
5 minute read
Less is more BASF
LESS IS MORE
Reduction of waste and greenhouse gas emissions
All Images supplied by: BASF SE
Circular economy means decoupling growth from resource consumption. BASF aims at moving towards a circular economy, among others, by increasingly using recycled and renewable feedstocks. Made from these two new circular feedstocks, BASF now also offers plasticizers.
With its ChemCycling™ project, BASF is aiming to manufacture products from chemically recycled plastic waste on an industrial scale. BASF cooperates with partners, who use a thermochemical process called pyrolysis to transform plastic waste into a secondary raw material - pyrolysis oil. This oil is fed into BASF’s production network at the beginning of the value chain and then allocated to selected sales products according to a third-party certified mass balance approach. These sales products carry the name suffix “Ccycled™”. BASF now offers its trusted non-phthalate plasticizer Hexamoll® DINCH also as Hexamoll® DINCH CcycledTM .
Plasticizers made from renewable raw materials
Another method is the so-called biomass balance (BMB) approach. Here, renewable raw materials such as bio-naphtha or biogas derived from organic waste or vegetable oils are fed in at the beginning of BASF’s production network and are allocated to certain sales products according to a third-party certified mass balance

approach. These biomass balanced chemicals save fossil resources and reduce CO2 emissions at the same time. The plasticizer portfolio of BASF includes the following biomass balance products: Hexamoll® DINCH BMB, Palatinol® N BMB (DINP), Palatinol® 10-P BMB (DPHP), Plastomoll® DOA BMB (DOA/ DEHA).
The mass balance principle is similar to that of green electricity
Here, too, consumers cannot be certain that the electricity they use in their homes was generated from renewable energy sources. However, they can be sure that the share of green energy in the overall electricity grid increases due to their decision to purchase it.
Sustainable success with little effort
Besides saving fossil raw materials and decreasing CO2 emissions by using either recycled or bio-based feestock, the two approaches have another advantage for manufacturers: the products have the same specifications and technical properties as the regular plasticizers. Therefore, neither sampling nor additional release testing for these plasticizers is necessary. Transportation and warehousing can also be done together with the regular plasticizers. That way, it takes little effort to switch production or to manufacture special editions.
The new plasticizer portfolio goes hand in hand with the goals of VinylPlus®, the sustainability program of the European PVC industry. As a member of European Plasticizers, BASF actively supports VinylPlus® and is committed to the sustainable use of plasticizers and soft PVC.
You can find further information on the new plasticizer portfolio on the BASF website: www.plasticiziers.basf.com
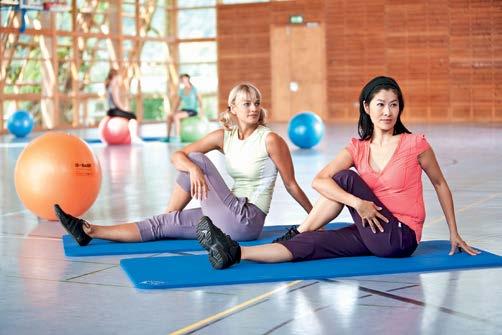
All new plasticizers can be transported, stored and even processed together with the regular plasticizers. That way, it is easy to launch special sustainable editions of typical PVC consumer products such as flooring or wallpaper. By introducing the new plasticizers of the Biomass Balance and ChemCyclingTM portfolio, BASF helps to save fossil raw materials and contributes to the reduction of plastic waste and to the use of renewable raw materials. Those are compelling characteristics for many end-consumer applications today.
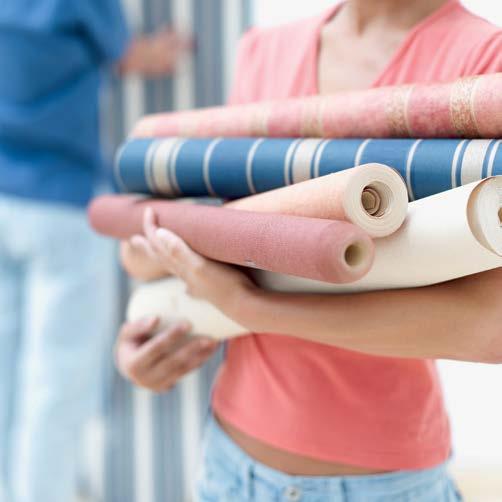
The plasticizers of the Biomass Balance and ChemCyclingTM portfolio have the same product properties as the regular plasticizers but have a lower CO2 footprint. Therefore, they can be used as sustainable alternative in already established customer formulations, such as Hexamoll® DINCH in children’s toys.
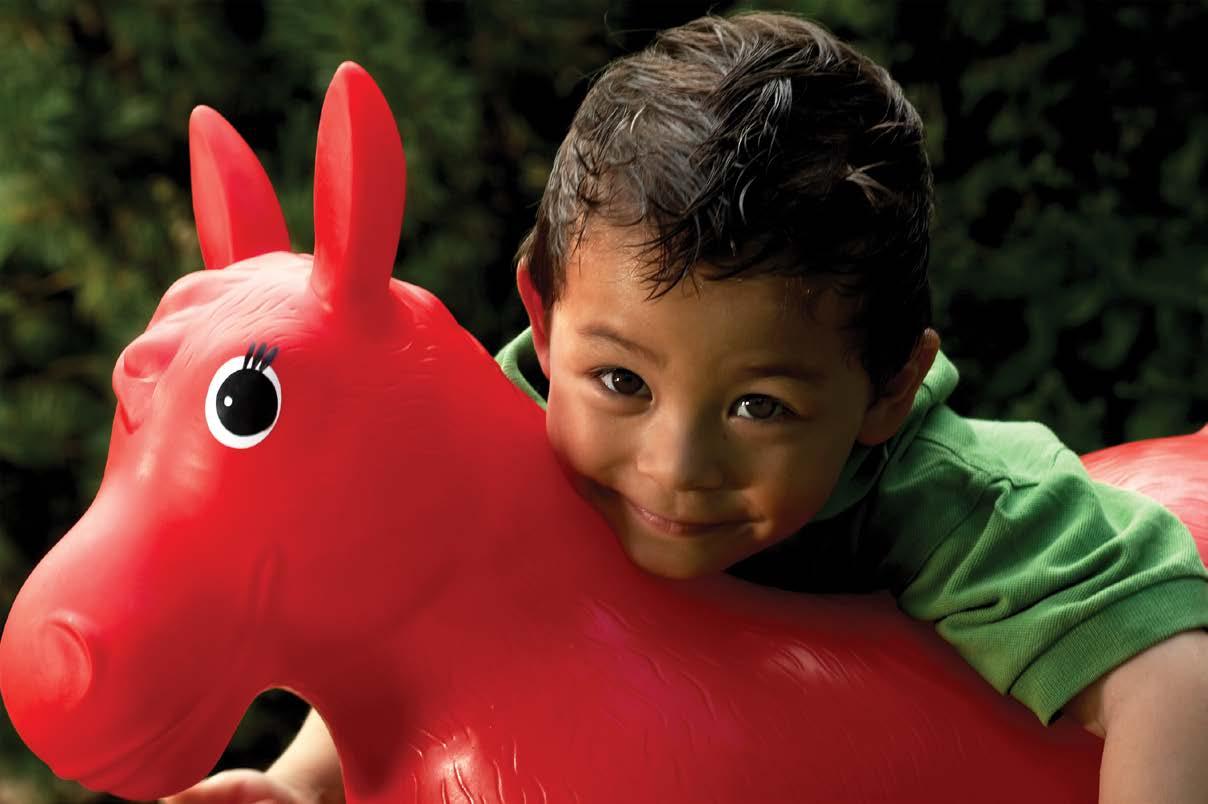
Interview with Diana Brunnenkant, Head of Commercial Marketing Plasticizers Europe, BASF SE:
What systems does BASF have in place to increasingly use recycled and renewable feedstocks?
We at BASF aim to move towards a more Circular Economy, thus making the most of the limited resources of our planet. We have therefore launched a new Circular Economy Program. By the year 2030, BASF aims to double its sales generated with solutions for the Circular Economy to €17 billion. To achieve this, we are concentrating on three action areas: circular feedstocks, new material cycles and new business models. Circular feedstocks comprise of recycled as well as renewable feedstocks. We expect that 250,000 metric tonnes of feedstock will come from recycled sources by 2025. Regarding renewable raw materials, we already use around 1.2 million metric tonnes annually and we want to increase this further in the future. Two of the main contributors will be the ChemCyclingTM project and the Biomass Balance approach (BMB).
Which of these approaches do you apply in the plasticizer business?
Plasticizers are mostly used in flexible PVC articles in many different applications, ranging from industrial to consumer products. As we serve so many different industries, we decided to offer plasticizers based on both concepts, ChemCyclingTM as well as Biomass Balance, and therewith to meet the different needs of our various customers.
What is the ratio of Biomass Balance and CcycledTM plasticizers? Are both approaches given the same focus and what are the individual advantages?
In the plasticizer business, we focus on both concepts equally as both serve different target groups and show different advantages. In the production of biomass balanced plasticizers, bio-naphtha or biogas is used instead of fossil resources. Biomass balanced plasticizers have a lower carbon footprint than the conventional ones and help save fossil resources. In the manufacturing process of the CcycledTM plasticizers, we use pyrolysis oil obtained from previously non-recycled plastic waste instead of fossil resources. The resulting products contribute to the recycling of plastic waste and the substitution of fossil feedstock.
Where do you see the biggest demand coming from (sector-wise, and geography-wise)?
From a geographical point of view, we currently see a strong pull from the European market as political regulations as well as consumer demands are increasingly focusing on sustainability. At the same time, we also see a rising interest from other regions, e.g. Asia, where sustainability topics gain in importance. From a segment point of view, we currently see strong interest coming from industries that produce sensitive applications or that are close to end-consumers. In general, there is high interest in these solutions, both to keep up with political developments and to differentiate from the competition.
Has BASF made any investment to support the use of recycled and renewable feedstocks?
Indeed, we are highly committed to this topic, as you can see in particular by the investments made as part of the ChemCyclingTM project. So far, BASF invested €36 million – thereof, we invested €20 million into Quantafuel, a specialist for pyrolysis of mixed plastic waste and purification of pyrolysis oil, headquartered in Oslo, Norway. Furthermore, BASF invested €16 million into Pyrum Innovations AG, a technology company specialised in the pyrolysis of end-of-life tyres, headquartered in Dillingen/Saar, Germany. n
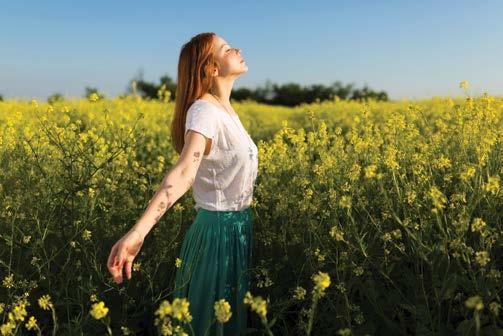
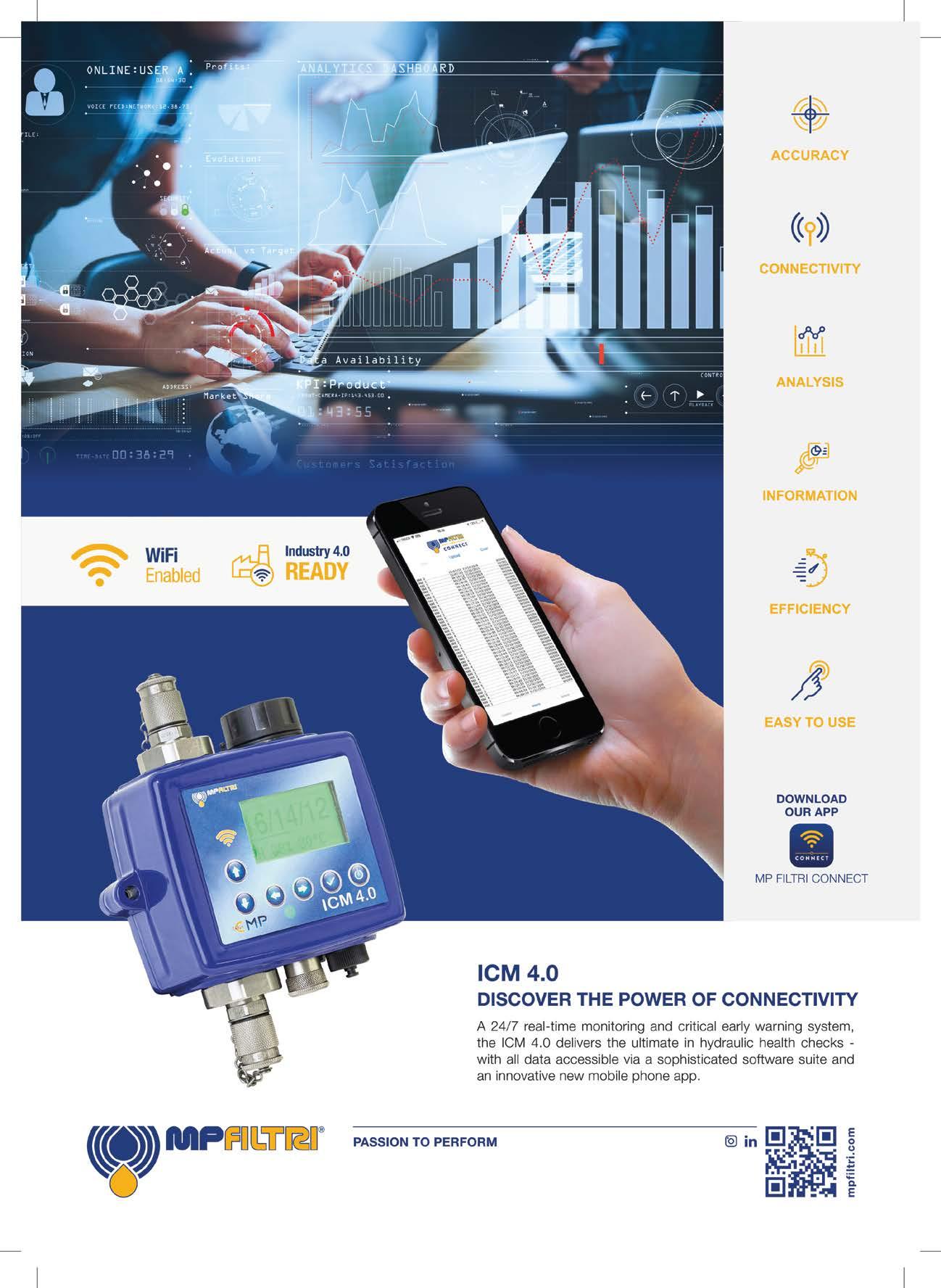