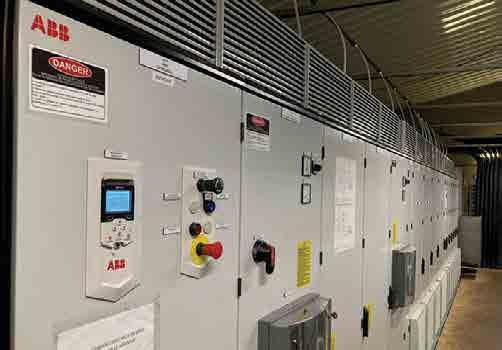
7 minute read
Pacific deep sea mining gets green light, Greenpeace slams decision
Thecontroversial practice of deep-sea mining could begin in the Pacific as soon as this month after the International Seabed Authority (ISA) gave the go-ahead to The Metals Company to commence mining the sea floor.
The ISA granted permission for Metals Company subsidiary, Nauru Oceans Resources Incorporated (NORI) to start exploratory mining in an area between Mexico and Hawai'i known as the Clarion Clipper Zone. The initial mining test phase is scheduled to conclude by the end of the year.
The company hopes it will pave the way for "NORI’s application to the ISA for an exploitation contract" said The Metals Company in a statement.
The trial will see NORI's offshore partner Allseas test a system consisting of a nodule collector on the seabed and a riser system that will bring the nodules to the vessel at the surface, Hidden Gem. The company is anticipating collecting around 3600 tonnes of polymetallic nodules during the trial.
The Metals Company says that both the Allseas systems will be monitored by independ- ent scientists from a dozen research institutes from around the world, who will analyse the environmental impacts.
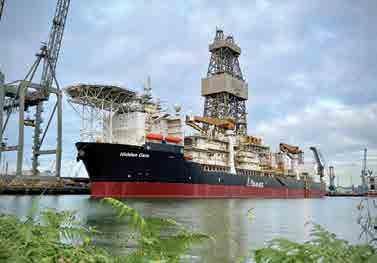
The Metals Company CEO and Chairman Gerard Barron welcomed the ISA decision and said that his team had worked tirelessly to achieve the result.
"With this green light from the ISA, the team of world-class engineers from Allseas and scientists from some of the world’s leading deep-sea research institutions that we’ve brought together can begin technology trials and our impact monitoring campaign. We have a couple of exciting and no doubt challenging months ahead of us. The environmental and operational data and insights from these trials will be an important step in ensuring the safe and efficient collection of polymetallic nodules to supply critical battery materials for the clean energy transition,” said Barron.
The decision has been slammed by environmental campaigners, with Greenpeace Aotearoa describing it as the start of a new and highly destructive extractive industry that will prioritise profit over people and biodiversity, and threaten the ocean's health and people's way of life.
"Deep sea mining is now right upon our doorstep and is a threat to each and every one of us. The ocean is home to over 90% of life on earth and is one of our greatest allies in the fight against climate change. Greenpeace will not stand by quietly as deep-sea mining companies begin to plunder the seafloor and decimate biodiversity for profit," said Greenpeace Aotearoa seabed mining campaigner James Hita. Read more: www.industryeurope.net
SLM Solutions and Danish Technological Institute Collaborate to Revolutionize Metal Additive Manufacturing
Today,SLM Solutions, the leading metal additive manufacturing technology provider, announced a game-changing collaboration with the Danish Technological Institute (DTI) to scale up the industrialization of additive manufacturing. This partnership is set to revolutionize the metal additive manufacturing industry by developing new outstanding parameters for SLM® machines and the NXG XII 600.
With their recently acquired SLM®280 2.0, DTI is developing faster process parameters for stainless steel 316L and copper alloy CuCr1Zr to support cost-effective production, taking advantage of SLM Solutions' importance of open architecture. The material development collaboration will create new application opportunities for advanced components, where electrical and thermal conductivity are crucial, and sturdy components out of stainless steel can be manufactured with lightning-fast processes.
“We are thrilled to be collaborating with DTI on high-productivity solutions for 316L and CuCr1Zr. DTI will follow the SLM Solutions standards of material development and qualification, enabling us to provide material parameters of the same high quality as any other new SLM® material parameter,” said Christoph Wangenheim, Head of Additive Material Products & Development at SLM Solutions.
The partnership between DTI and SLM Solutions is the natural next step in their long-term relationship. “The collaboration with SLM Solutions is extremely interesting for us. With SLM Solutions' expertise in special alloys for additive manufacturing, this collaboration gives us a unique insight into future possibilities,” says Ellen M. J. Hedegaard, Business Manager at DTI.
The development allows the copper alloy CuCr1Zr to be printed in varying layer thicknesses and creates new business cases where AM will be used for advanced components where electrical and thermal conductivity are important. With up to 92 % IACS after heat-treatment, CuCr1Zr still features very high electrical conductivities at up to 300 MPa ultimate tensile strength. SLM Solutions' stainless steel 316L, on the other hand, is an austenitic high-chromium steel with excellent processability on SLM Solutions' additive manufacturing machines. 316L is often used in applications requiring good mechanical properties and excellent corrosion resistance, especially in chloride environments. DTI will develop faster process parameters for stainless steel 316L, enabling the possibilities of printing components at a lower price.
DTI is a leading research and technology institute with over 30 years of experience in additive manufacturing. Their modern facilities in Aarhus offer 3D-printed components in a range of metal and polymer materials, utilizing a wide variety of additive manufacturing technologies to tailor a solution that perfectly fits the customers' needs.
With this ground-breaking partnership between SLM Solutions and DTI, further industrialization and increased use of metal-based additive manufacturing will take a significant leap forward. Industry will get a front-row seat to witness the future of additive manufacturing.
SLM Solutions is a publicly-traded Company headquartered in Germany, with offices in Canada, China, France, India, Italy, Japan, Singapore, South Korea, and the United States. Further information is available on www.slm-solutions.com
and control system technology for steel mill in France
in terms of thickness tolerances, flatness and surface characteristics via precise process control and equipment lifecycle management.”
“ABB will bring a combined MOM4Metals and RGC/AGC automation solution specific to metals processing to our modernization project at Contrisson,” said Frédéric Geoffroy in charge of process and automation department at ArcelorMittal Construction. “This stands out from standard automation and digital solutions and we are pleased that our needs can be met by one supplier with whom we have a long standing relationship at and beyond this site. ABB successfully revamped the drive of the cold rolling mill previously.”
“For ArcelorMittal Construction France, leader in the field of steel building envelopes, ABB supports us through its business solutions and allows us to offer our customers innovative solutions based on decarbonized and sustainable steel.”
Ain Contrisson, France, as part of a modernization project. The solutions, which include ABB Ability™ Manufacturing Operations Management for metals (MOM4Metals), Roll-Gap (RGC) and Automatic Gauge Control (AGC), will help the world’s largest steel producer to bring productivity to a new level, improve quality and performance.
ABB MOM4Metals product, based on precise data analytics, improves information sharing, production planning, execution, reporting, asset monitoring and operational performance optimization. It is designed for and used in various metal production processes from rolling mills to processing lines delivering clear benefits over generic industry-agnostic MES platforms.
ABB is also modernizing advanced RGC and AGC technologies to reduce thickness deviations and off-gauge length. The project is expected be completed in the first quarter of 2024.
“ArcelorMittal Construction has placed its trust in ABB know-how and solutions for cold mill applications,” said Frederik Esterhuizen, Global Business Line Manager for Metals at ABB. “Through discussions with the customer we have been able to utilize our deep metals expertise to refine the ABB solution to meet their needs. ABB solutions enable cold rolling mills to improve and maintain performance and meet quality requirements
Technology is a decisive factor in determining the quality of rolled products. ABB’s rolling mill solutions, including metals specific electrical, process automation and control technologies, leverage over 100 years of metals industry expertise to enable increased speed, reduced non-rolling time and threading problems while allowing for precise process control in terms of strip surface, flatness, thickness, off-gauge length and more to deliver improved strip quality, productivity and resource efficiency.
ABB’s Process Automation business automates, electrifies and digitalizes industrial operations that address a wide range of essential needs – from supplying energy, water and materials, to producing goods and transporting them to market. With its ~20,000 employees, leading technology and service expertise, ABB Process Automation helps customers in process, hybrid and maritime industries improve performance and safety of operations, enabling a more sustainable and resource-efficient future. go.abb/processautomation
ABB is a technology leader in electrification and automation, enabling a more sustainable and resource-efficient future. The company’s solutions connect engineering know-how and software to optimize how things are manufactured, moved, powered and operated. Building on more than 130 years of excellence, ABB’s ~105,000 employees are committed to driving innovations that accelerate industrial transformation.
Sweden's H2 Green Steel has raised €190 million in its latest round of financing, as its push to replace fossil fuels with green hydrogen in steel production gathers pace.
The company is constructing its first steel mill in the northern Swedish town of Boden, with an aim to produce 5 million tonnes of green steel per year by 2030.
The financing round was co-led by three new investors; Singapore's sovereign wealth fund GIC, Swedish pension fund AMF, and German automotive firm Schaeffler, as well as existing investor Altor Equity.
Also participating in the equity raise is new investor Swedbank Robur Alternative Equity and existing shareholders Vargas, Kingspan, FAM, Marcegaglia, IMAS Foundation, Cristina Stenbeck and Daniel Ek continue to support the company with additional equity funding.
"This financing milestone is a real statement of confidence in H2 Green Steel. Despite the uncertainty in global markets, a venture like ours, with both a strong business case and a strong sustainable purpose, is clearly attractive to investors.
"This financing round has allowed us to combine leading industrial companies and global financial institutions, with investors with a strong Swedish participation, creating the investor-base that will set us up for success," said Henrik Henriksson, CEO of H2 Green Steel.
After its launch in February 2021 and the close of its series A equity round in May of the same year, the company received a permissibility permit for its operations in Boden in record time, securing a 14 TWh agreement for renewable electricity and initiating groundworks and construction.
H2 Green Steel has already pre-sold about 60% of its initial volumes, which is a testament to the high demand for decarbonised steel. Customers represent a broad range of sectors including steel service centres, pipe and tube manufacturers, automakers, white goods companies and construction products.