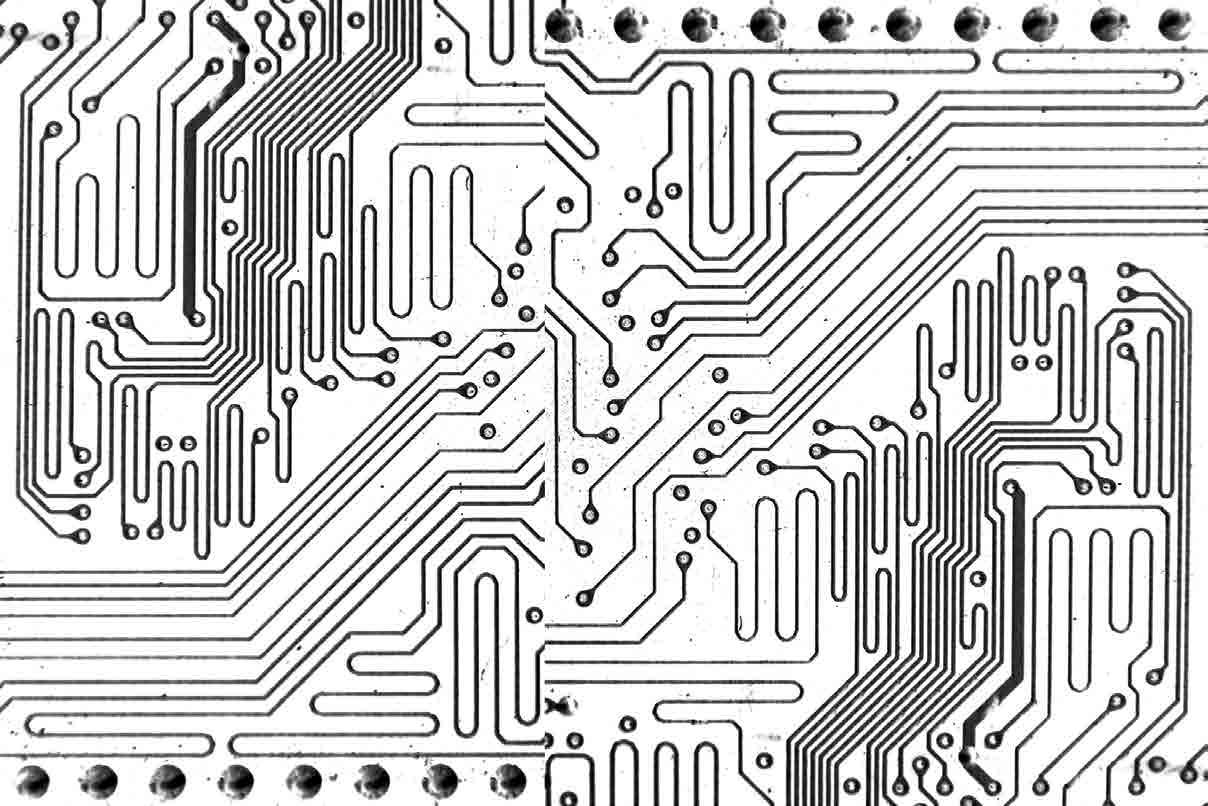
5 minute read
DGT ronik - PCB ASSEMBLY EXPERTS
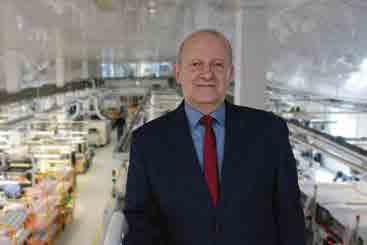
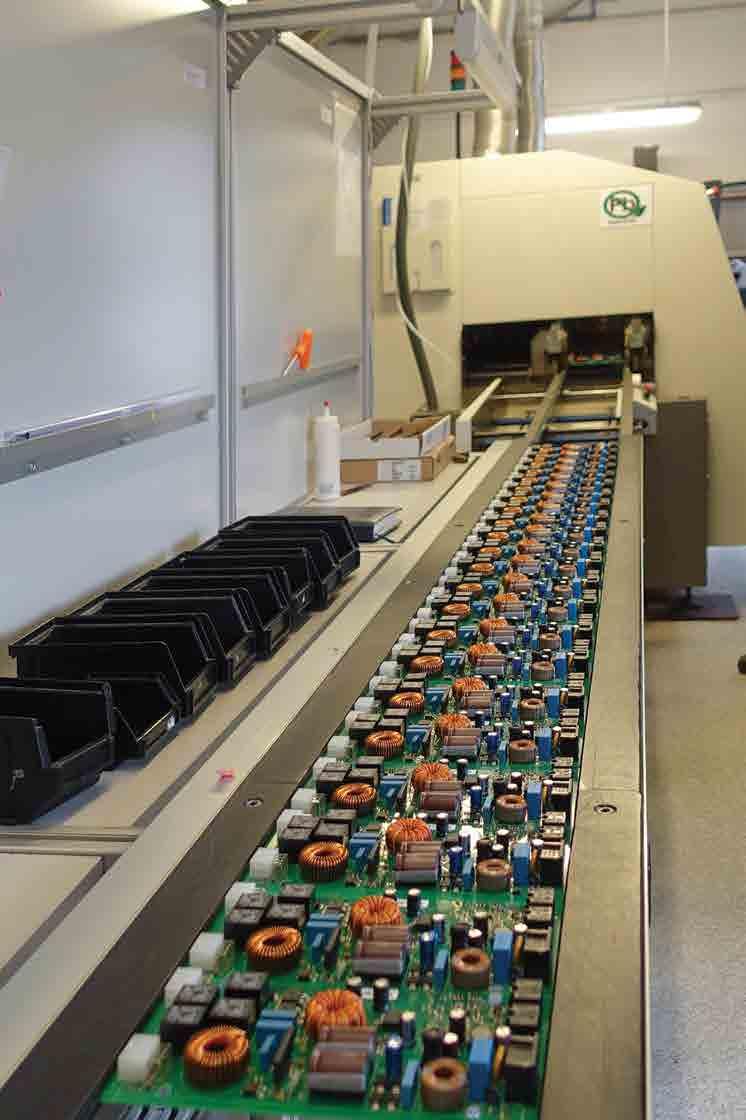
DGTronik, a company from Straszyn near Gdansk, Poland, provides comprehensive electronics assembly solutions. It implements projects involving electronics with densely arranged SMD components in sizes from 01005 and micro BGA. Dariusz Balcerzyk speaks with Mr. Krzysztof Izewski, the founder and long-term CEO, a member of the DGTronik’s Management Board, a company, which is a part of the DGT capital group. At DGT, Mr. Izewski ran for 12 years the company’s Technology Division, including the design office. Currently, he is focused on managing DGTronik.
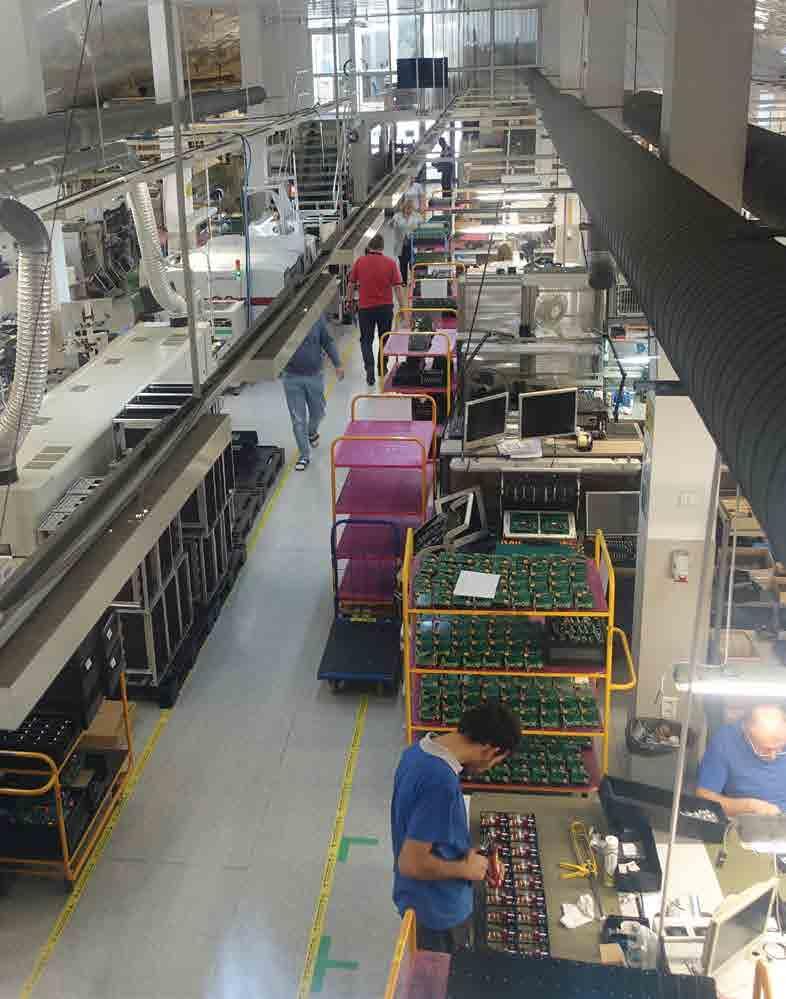
The history of DGTronik dates back to the early 21st century. What are the origins of the company?
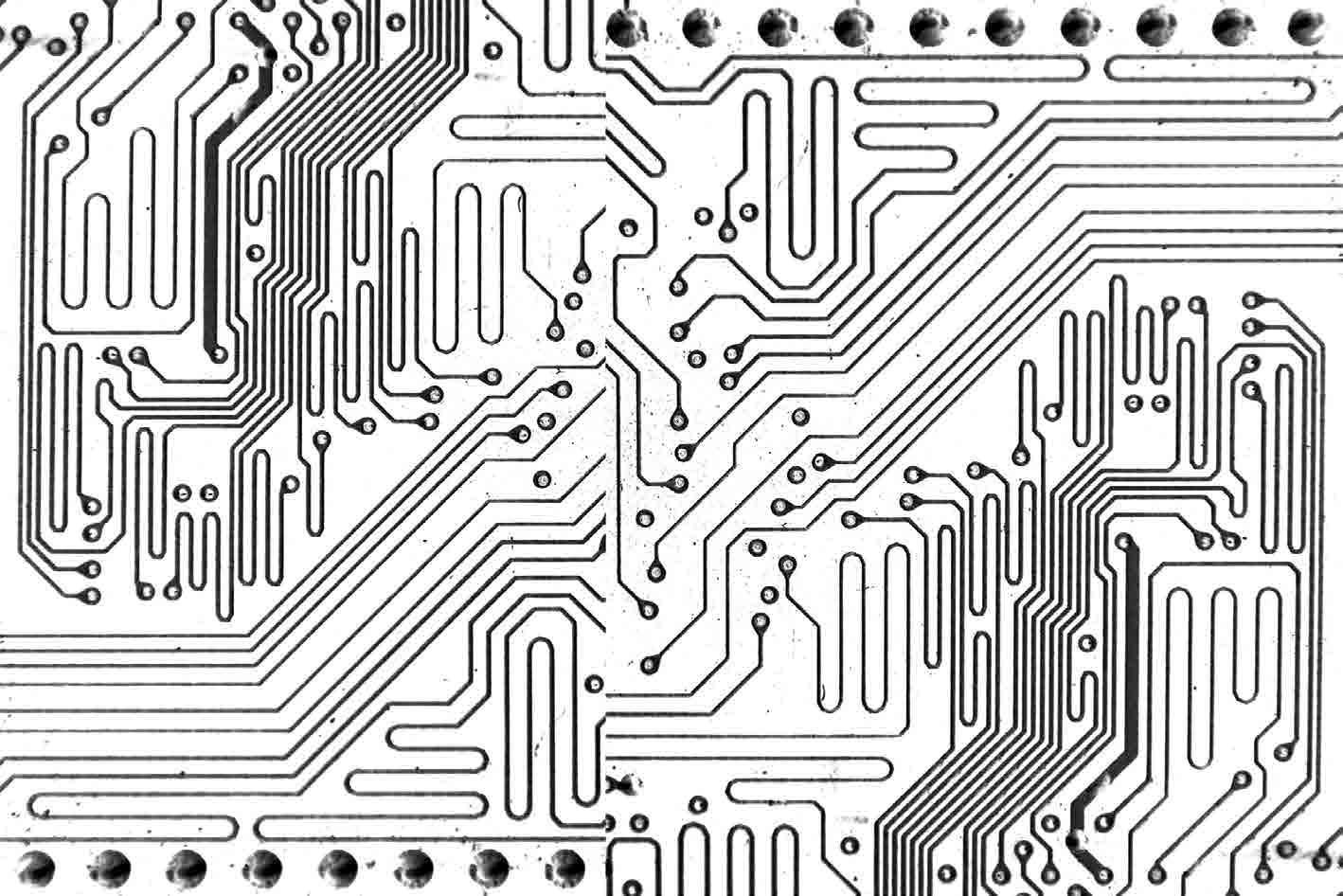
DGTronik was established in February 2002 as a result of the transformation of the DGT’s Production Office into a limited liability company. This decision was taken due to the growing potential of the Production Office, which at some point has significantly exceeded the assembly needs of DGT. So we did not start from scratch but already had a great production infrastructure and a very experienced team of specialists, especially in the field of difficult projects. All we needed were customers. Our participation in trade fairs, our attractive prices, especially for foreign companies, our wide offer and sound experience in assembling difficult prototype series made our order portfolio quickly grown.
The DGT, a company, which is an essential part of our capital group and thanks to which we have entered the market, deserves a special mention. The company specialises in the construction and production of integrated communication systems. They were applied, for example, to create systems for handling national emergency numbers ‘112’ and ‘999’ systems in Poland. It was on the DGT products that we learned how to assemble 18-layer PCBs with SMD elements in BGA housings with 1650 leads.
What are the DGTronik’s main areas of activity?
The area of our activity has remained unchanged since the very beginning of the company’s operation and includes contractual electronic assembling supplemented with the commissioning, testing and marking. The assembly applies to packages or entire devices. We also provide additional, outsourced services, e.g. coating, potting or X-ray tests. The assembly service is complemented by the purchase of components and printed circuit boards (PCBs). It is worth mentioning that we can also carry out assembly of electronics for the automotive industry.
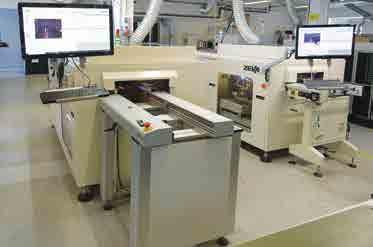
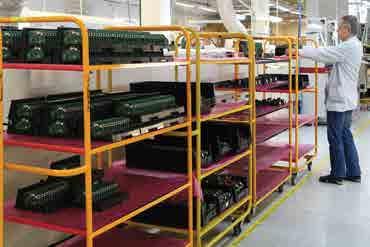
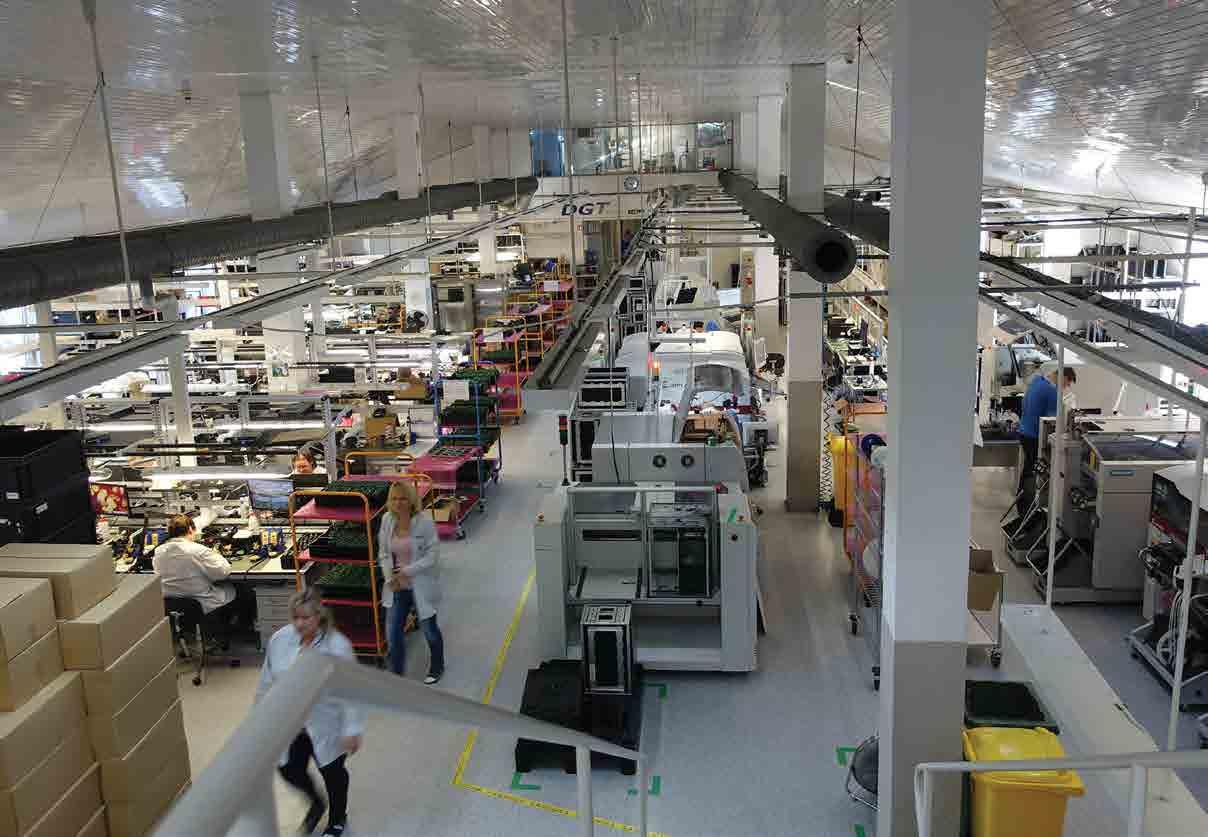
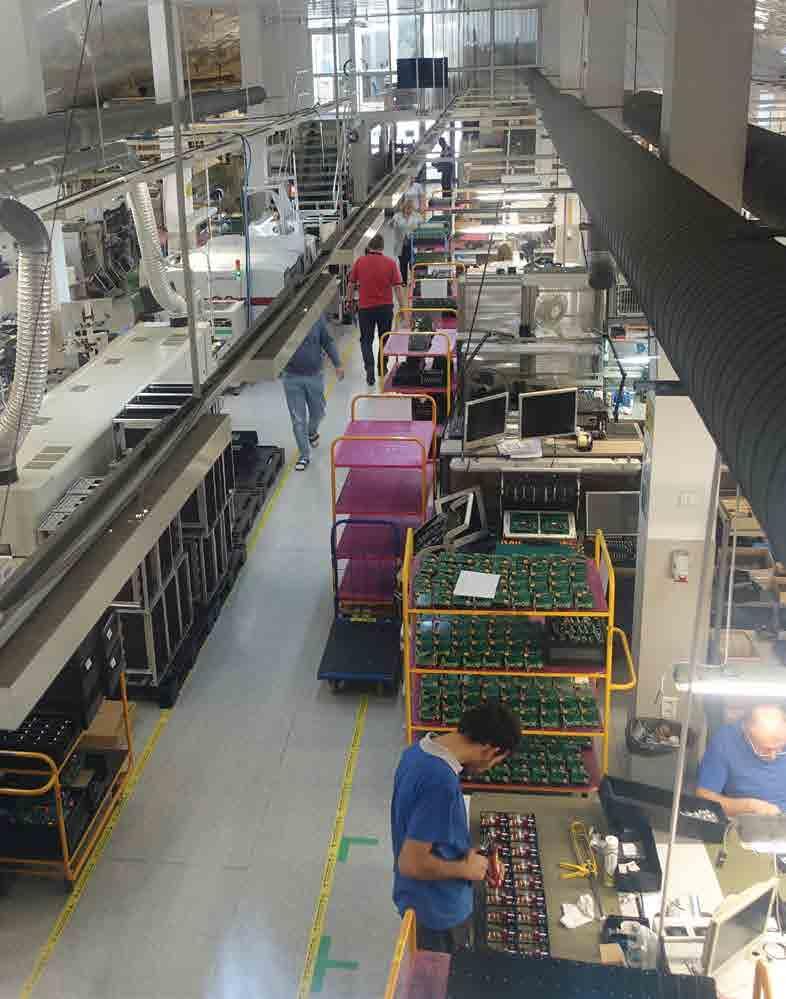
Looking back on past 21 years, what would you consider the secret of the DGTronik market success?
Three elements have determined our continuous presence on the market: being a part of the DGT capital group, taking special care of customer trust and paying the utmost attention to the quality of the services offered. It takes a long time to build a customer trust, while it can be lost very quickly. Therefore, the service timeliness of implementation and its quality are crucial. The last 30 months have been a period of great test for us when it comes to our cooperation with partners. The pandemic has broken supply chains and only close relationship with our clients and their understanding of the situation, allowed us to function.
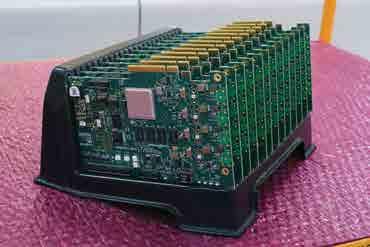

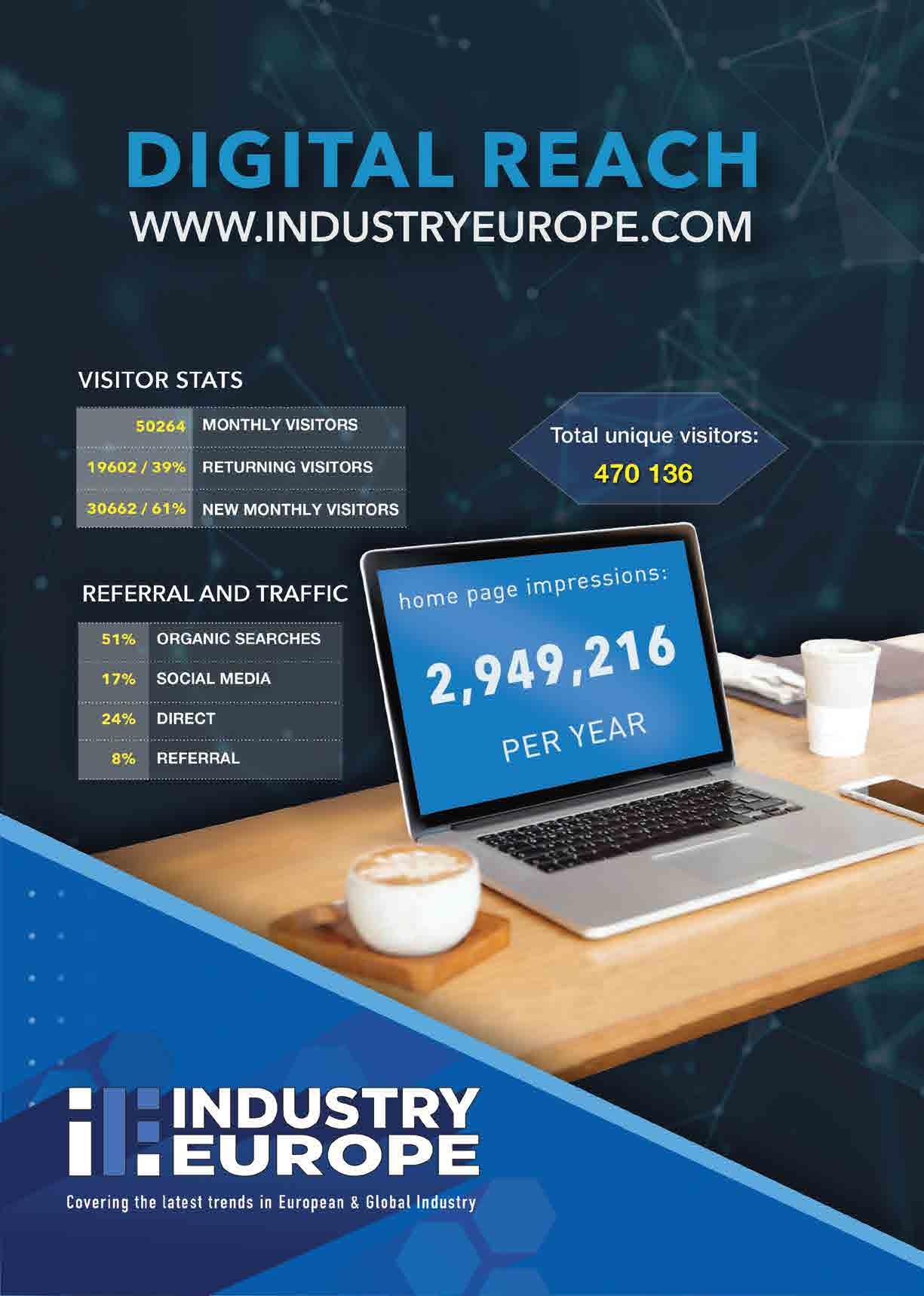
Our partners value the quality of our services and a very flexible approach to their needs. We are able to cooperate substantively with the client, pointing out technological or design errors and proposing corrections. Our customers greatly admire the pace of modernization of our production base and the pace of adapting the company to new market requirements. Some customers, visiting us after a few years, cannot believe that it is still the same company.
What is the DGTronik current position on the market?
DGTronik holds the rank among the top ten Polish companies.We employ 107 people and our financial turnover in 2022 is estimated as PLN 22 million (EUR 4.7 million). Exports share 80 per cent of the company’s sales. Main foreign destinations are: the USA (36 per cent) and European markets – 44 per cent (including the UK -12 per cent).
Can you explain the process of the electronic component selection? How electronics are tested in the production process?
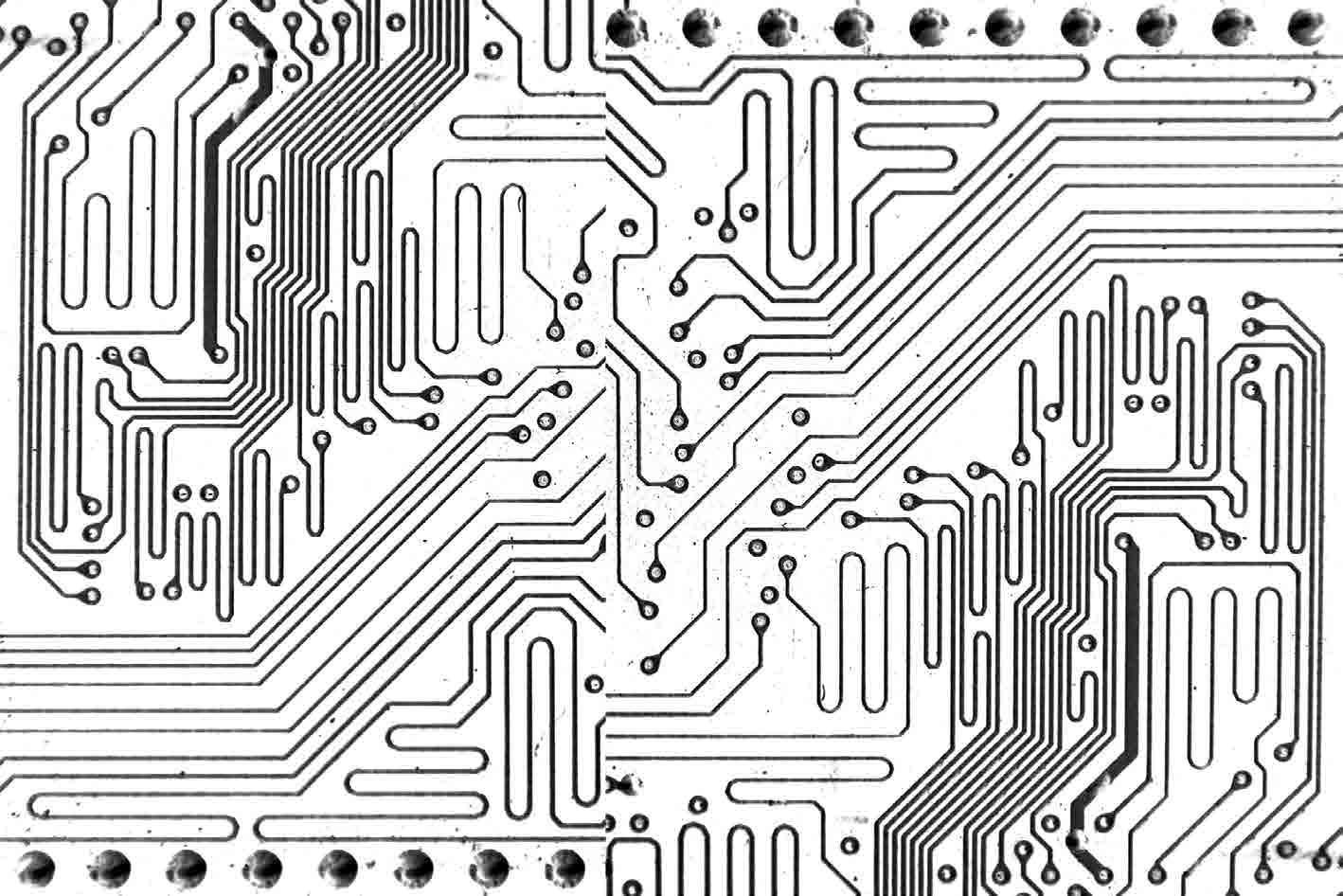
There are several types of contractual electronic assembly services. It can be assembled from materials provided by the client, or with the purchase of materials by the service provider, or with the purchase of materials by the client and the service provider.
In the case of materials entrusted by the customer, the control is limited to checking the quantity and quality of the elements. The production date and the condition of technological packaging are important. When we buy the materials needed for assembly processes, we rely on supplies from proven and verified suppliers.
In turn, the material list that we receive from the client must contain all the key parameters of the elements for the project.
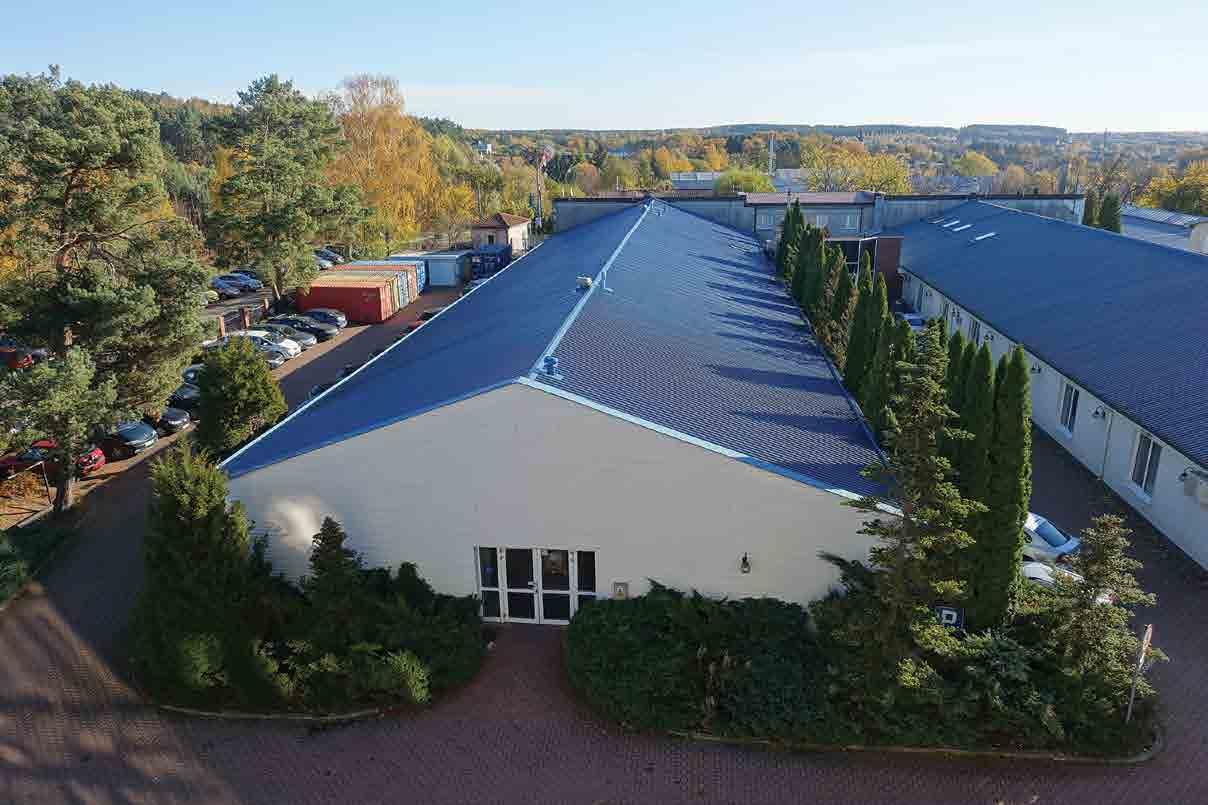
Testing, on the other hand, is a very important competence of a company providing assembly services. If we are commissioned to provide a service for only a PCB package, then the quality control is carried out on SMT assembly lines (automatically, AOI) and TH lines (optical inspection manually) and the final check at the Quality Control Office. If only a PCB package with a test is ordered, in addition to the previously mentioned checks, there is an additional test carried out on the tester and software provided by the customer. And when we are dealing with the assembly of a complete device with start-up and configuration tests, apart from the tests taking place on the SMT and TH assembly lines, there are also package tests, very often on pin testers, and tests of the assembled device. Testers and test software are provided by the customer.
What kind of investments that increase the DGTronik’s production capacity and its competitiveness have been recently implemented?
The last 5 years have been crucial when it comes to modernizing the production infrastructure. We replaced two old SMT assembly lines, replacing them with analogous, but more modern ASMPT SIPLACE machines. We also replaced soldering ovens and paste printers. We paid particular attention to the verification of all elements of the process, which is why each line was equipped with a solder paste controller (SPI) and an automatic optical inspection device (AOI). Solder paste printers received individual air conditioners. We supplemented the through-hole assembly process with two selective waves from Vitronic Soltec Zeva M+. The repeatability of the process carried out by automatic machines is impossible to achieve in manual operation. This reconstruction of the production base significantly increased our production capacity, while guaranteeing high quality of services.
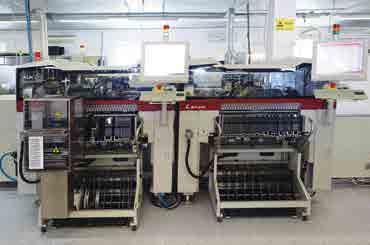
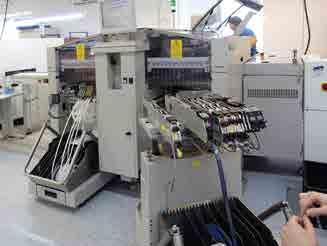
Furthermore, while looking for a chance to expand our offer with new services, we received an interesting inquiry from our client about the possibilities of laser marking of his products. The client wants to move away from the traditional sticker-type nameplate in favour of laser printing. We are currently testing selected laser markers and integrating them into our IT system. Further development and investments are related to the expansion of the production area that we are planning.
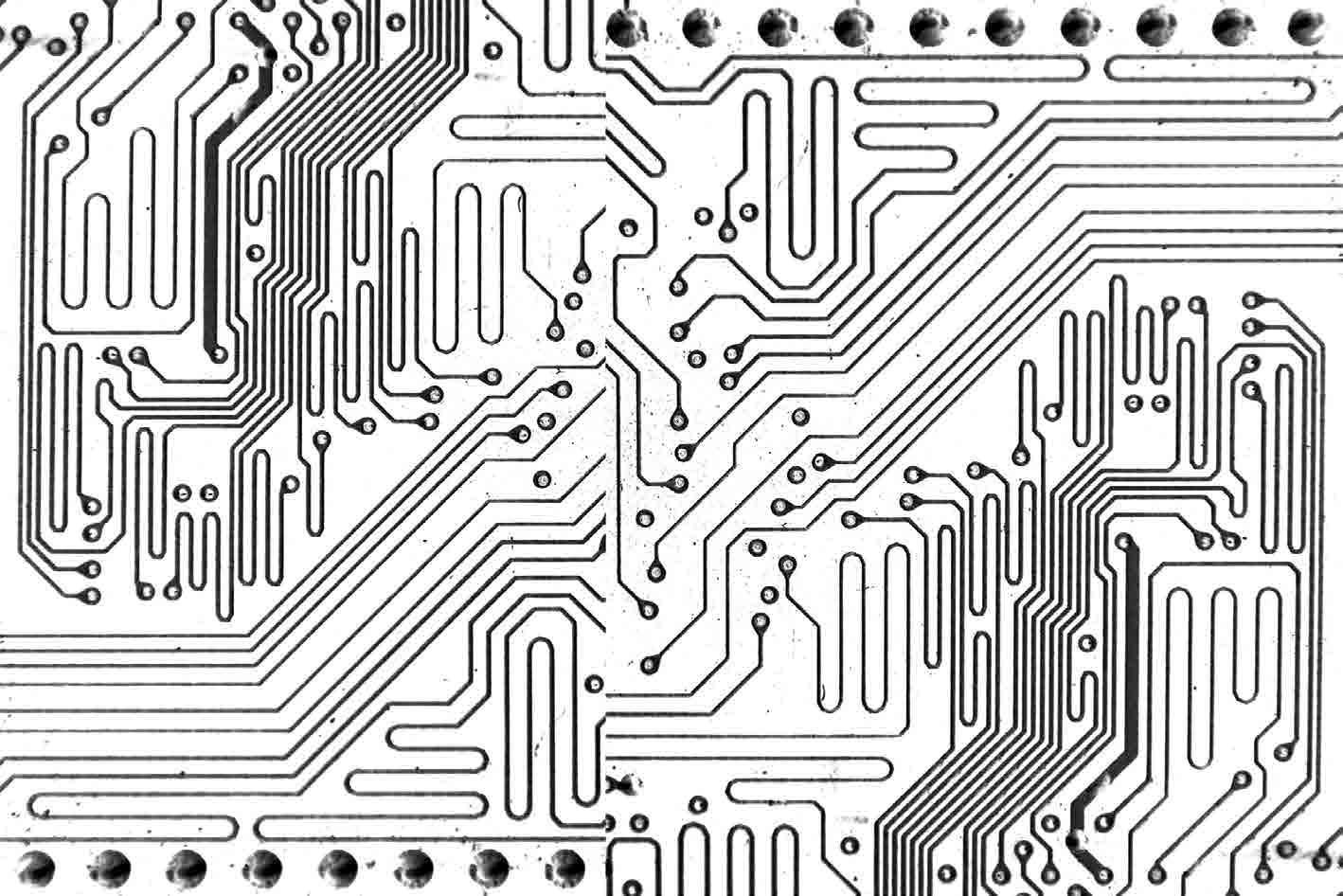
What are the company’s vision andmission for the coming years?
It is a vision of the company providing services at the highest, worldclass level, friendly to employees, effectively protecting them against the harmful effects of certain technological processes and ensuring a friendly working atmosphere. For the sake of our specialists, we do not want our employees to be present at some particularly onerous parts of the technological process, which is why we are planning automation in this area.
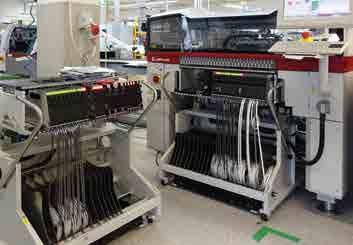
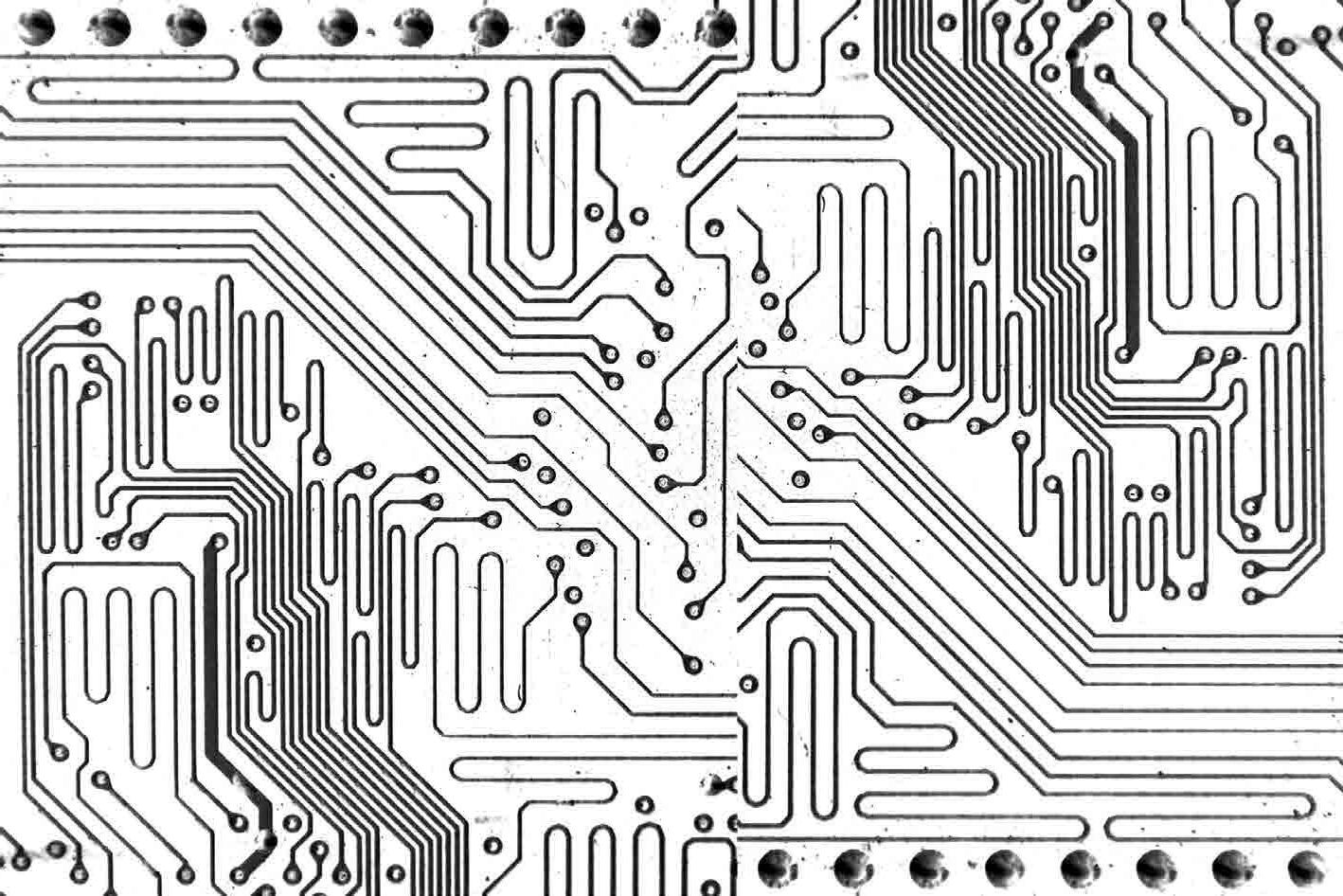
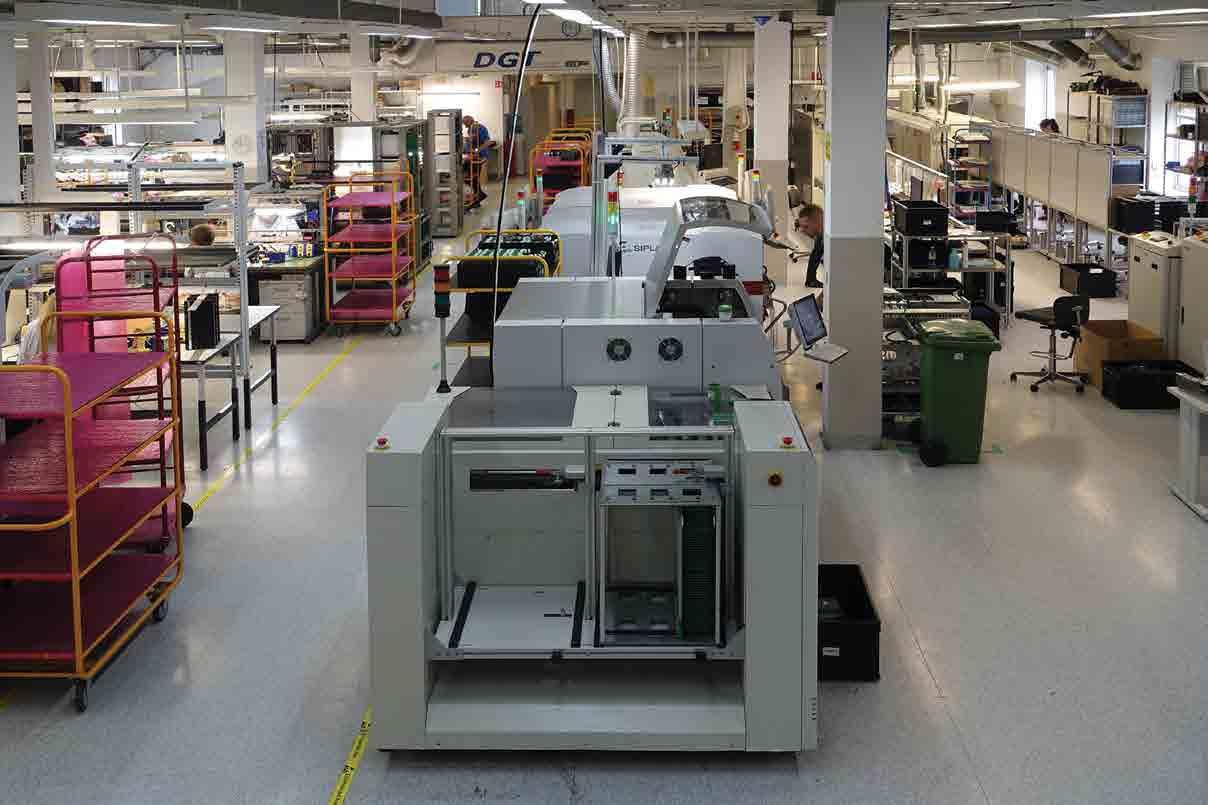
Another important element that fits into the organizational vision and mission is being an environmentally friendly company. The beautiful location of our headquarters is an additional stimulus forcing pro-environmental thinking. We are trying to reduce gradually the carbon footprint of our production cycle and use technological materials with negligible harmfulness to the environment.
Next part is the provision of production capacity for the needs of our capital group, especially for the DGT company, and the successive increase in the value of sales of services for our current customers. They increase their orders striving to locate all their production in one place - at us. We must be ready for such scenarios and secure the necessary production capacity in advance. n Visit