
16 minute read
PRODUCTS
HOW SHARPE ENGINEERING KEEPS THEIR COOLANT CLEAN
Demand for Australian-made metal components is increasing, a positive development, but scaling production also means using more coolant.
Advertisement
Industrial coolants, widely used in metalworking and CNC (Computer Numerical Control) cutting processes, are a major expense.
Their unique chemical composition makes them prone to contamination and degradation.
Replacing them is a messy and timeconsuming task.
Disposal costs are high and expected to rise further in the face of today’s environmental regulations.
But dirty coolants are also linked to other, less obvious costs. For example, fine metal shavings in coolant can lead to increased tool wear.
Oil in coolants causes bacteria to proliferate.
Bacterial growth in collection tanks does not only deteriorate the coolant, but produces a distinctive foul odour which is a WHS issue for metal manufacturing industry workers.
Tramp oil also contributes to quality problems later during processing (e.g. painting), and can trigger skin irritations.
Some companies use skimmers and filters in an effort to prolong the life of coolant and cutting fluids. These technologies are quite basic and
When working in hazardous locations, such as during heatwaves or extreme weather conditions, extra consideration is made to protect materials against corrosion.
This applies for example when working with steel structures, like pipes, tanks and bridges.
This is where the use of cathodic protection (CP) systems becomes crucial.
Corrosion is a natural process where metals are gradually degraded and destroyed by chemical and electrochemical reactions with their environment.
Galvanic and impressed current CP systems are used to control the corrosion of steel in structures and involve voltages and currents being introduced into the structures. cannot remove tramp oil and fine metal shavings due to their small particle size.
A better way to clean your coolant;
Family-owned business Sharpe Engineering has been providing quality engineering and manufacturing solutions in Queensland since 1995.
The company’s clients include operators, contractors and service providers across Australia’s significant resource and energy sectors.
As the business expanded across its three workshops, equipment was getting bigger and with that, coolant volumes were increasing.
Currently, Sharpe’s biggest machine requires a 1,700 litres coolant tank, while the other units are attached to 600 – 700 litre tanks.
In Brisbane the company operates 12 machines alone.
Jon Sharpe, General Manager at Sharpe Engineering, explains why coolant treatment is a problem.
“Particles enter the coolant system, and these fine metal shavings affect the quality of the coolant fluids over time.”
“We had to dispose of our coolant every year to keep it at a good consistency.”
Sharpe Engineering is currently paying almost $1 per litre with a specialised waste disposal company. situated in hazardous environments where there are explosive liquids and gases, creating a risk of an explosion occurring if electrical voltages and currents are not managed carefully.
“It’s clear that using galvanic or impressed current CP systems in hazardous areas needs to be handled carefully,” explained David Celine, Managing Director of Omniflex.
“The approach required to manage this must be well-documented and systematic, detailng all electrical circuits and materials present, to comply with regulations and standards.”
“There are international standards governing the installation and use of electrical equipment in hazardous areas, which all equipment located in hazardous areas must comply with,” said Mr Celine.
Jon Sharpe -, General Manager at Sharpe Engineering
Due to rising cost, it made perfect sense to investigate the Alfa Laval Alfie 500 separator, to clean the coolant.
“The Alfie rips all the oils and particles from the coolant.”
“And the right coolant treatment has a great effect on the quality of work and staff morale,” Jon Sharpe added.
Centrifugation works with G-force to achieve solid-liquid separation faster and more efficiently than filtration, skimmers, and lamella separators.
Centrifuges can remove sub-micron particles down to 2-3 microns whereas filters are limited to 8-10 microns.
The coolant is pumped up from the tank and centrifuged in the separator bowl at speeds of 6,000–10,000 rpm.
Centrifugal force pushes the solid particles out to the periphery of the disc stack.
Unfortunately, these standards don’t specifically discuss CP systems in hazardous areas.
This perpetuates a lack of understanding within the corrosion industry on how to quantify the dangers presented, and how to mitigate these dangers in accordance with the requirements of the standards.
Mr Celine will be holding a presentation on hazardous areas and address the impacts this has on the design of CP systems referencing real-life examples.
It will be held in the coming Corrosion and Prevention annual event online,of cathodic protection specialists at the Australasian Corrosion and Prevention conference.
There they become trapped on the inner surface of the separator bowl, while the lighter oil is forced toward the centre, where it can then be drawn off.
Due to its high rotation speed, the centrifugal separator cleans up to 10,000 times more effectively than equipment based on gravity alone.
Since Alfa Laval Alfie centrifugal separator is installed in a bypass flow, cleaning can proceed both during production and when the equipment is idle.
Centrifugal separation dramatically reduces the volume of waste coolant to be sent to disposal and waste management facilities.
Find out more how Alfa Laval, the global leader in separation technology, can help your business save on coolant treatment.
CATHODIC PROTECTION IN HAZARDOUS AREAS DISCUSSED
www.alfalaval.com.au on corrosion and mitigation in the Southern Hemisphere, hosted by Omniflex.
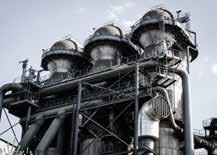
Omniflex designs and manufactures electronic products and systems for the automation and control industry worldwide, specialising in remote monitoring.
This includes industrial networking, remote I/O systems, utilities monitoring, process auto-mation systems, signal conditioning, and alarm and event management.
Omniflex www.omniflex.com
EPSON ECOTANK TOPS 50M SALES
Cumulative global sales of Epson’s EcoTank high-capacity ink tank inkjet printers recently topped 50 million units.
Epson first launched EcoTank high-capacity ink tank inkjet printers in October 2010, in Indonesia. The company then steadily expanded the territory over which EcoTank printers were sold, reaching 170 countries and regions by last year.
As well as selling more 50 million units, by saving on plastic, which is the main component of ink cartridges, Epson estimates that CO2 emissions are about 166,000 tonnes lower than they would have been if all these units had been cartridge printers.
By first establishing a presence in emerging nations and then making inroads into developed economies, Epson has seen its high-capacity ink tank models account for a growing percentage of the total inkjet market each year.
As a result, Epson, which boasts strong brand recognition and an extensive product line-up, has continued to maintain the top share in the global high-capacity ink tank printer market for 10 consecutive years.
Rapid changes in society touched
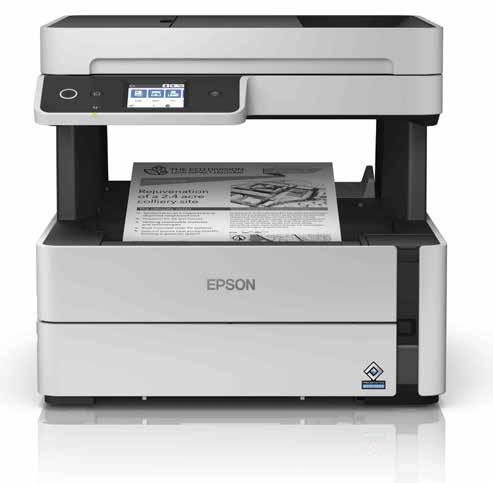
off changes in the office and education printing environments during the 2020 fiscal year. Epson’s goal in all segments now is to continue to offer far lower printing costs than its competitors and unrivalled environmental performance.
For more information on Epson EcoTank printers scan the QR code.
CONVEYOR COMPONENTS
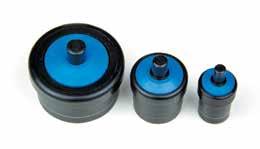

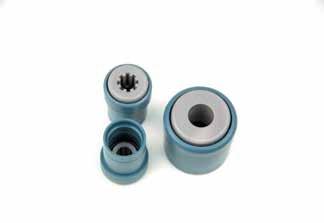
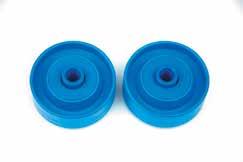
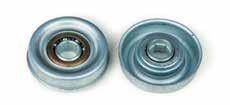

Range unmatched from any other Australian supplier. Performance and reliability unmatched and backed. No comparable products on the local market that can match it for quality and performance. Hard to beat price on any other European products. Solutions to most hard to source replacements. Complete roller range offered and assembled here.
PRECISION ENGINEERING & LOCAL EXPERTISE mrtaustralia.com.au EXCLUSIVE DISTRIBUTION RIGHTS JOINT AUSTRALIAN / GERMAN OWNERSHIP
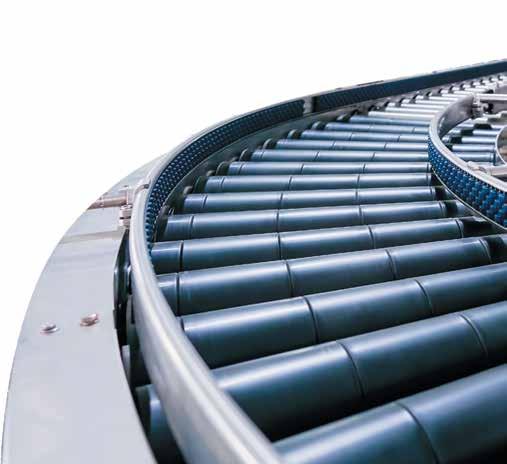

Backplane Systems Technology is proud to present iBase’s VINO2100, an intelligent face mask and body temperature detection system powered by Intel® OpenVINO-based iVINO AI recognition software.
The VINO2100 is an all-in-one platform featuring a 7th Gen Intel® Core™ i7-7600U processor and a 21.5” IPS LCD Touch Panel with IP65 Front-Panel Waterproof Protection.
It uses a high-precision thermal camera for body temperature measurements ranging from 35°C to 42°C (95°F to 107.6°F), the precision of ±0.3°C.
This real-time automated system features face mask recognition with 90+% accuracy in 50ms speed and can be used to intercept people not wearing a face mask and who fail body temperature test.
It supports sound/light alarm and access gate control for one by one walkthrough inspection.
The face mask detection function can be disabled if not required.
Saving up to nearly half its weight and 42% mass intertia, Treotham’s black guide roller with ball bearings has proven to be big news for packaging and labelling technology.
Unlike handheld thermometers that need an individual to take a person's body temperature, VINO2100 provides noncontact and efficient temperature checks and facial mask detection to allow or deny the entry of people in buildings and event venues.
With Artificial Intelligence (AI) Technology, it does not require human observation or intervention to assist frontline workers to perform epidemic prevention and control. Measuring 537.8 x 329.26 x 71.95mm, the fanless system has 8GB of DDR4 memory and 64GB SSD storage.
A desktop mounting stand and the high-precision thermal camera are optional in the package.
Key Features
The key features of iBase’s VINO2100 is Face Mask Recognition with 90+% Accuracy in 50ms Speed.
There is capacity for Body Temperature Test with Measurement Range from 35°C ~ 42°C (95°F ~ 107.6°F), Precision of ±0.3°C and RealTime Detection for Multiple People.
There is also Built-in Intel OpenVINO-Based iVINO AI Recognition Software and High-Precision Thermal Camera.
It has IP65 Front-Panel Waterproof Protection and Supports Sound/Light Alarm and Access Gate Control. As fully assembled systems with a tube made of aluminium, carbon or PVC, the ball bearings prove their worth as guide rollers for deflecting films or labels, or for conveying goods. Marcus Semsroth is Head of the xiros polymer ball-bearing division at igus GmbH. Semsroth points out that by using wear-resistant high-performance polymers and thin-walled tubes, they provide a weight saving of up to 48% compared to metallic solutions.
PHASE POWER METER GIVES ACCESS TO REALTIME ELECTRIC USAGE WITH 3 PHASE POWER MEASUREMENT

ICP Australia is proud to introduce ICP DAS’ PM-3133-RTCP2000P Series Modbus RTU, 3-Phase Power Meter, with Rogowski Coil CT.
The Smart Power Meter PM-3133RCT gives you access to real-time electric usage for three-phase power measurement.
With its high accuracy (<2%, PF=1; Input Current >50A), this series can be used to both low voltage primary side and medium/high voltage secondary side and enables the users to obtain reliable and accurate energy consumption readings from the monitored equipment in realtime under operation.
These compact size and cost-effective power meters monitoring equipment with Rogowski Coil CT is "rope-style" Current Transformer which delivers "Easy Installation" features for large window size (55 ~ 185mm) and mechanical flexibility for from a customer enquiry. The technical specifications of our classic aluminium rollers were already very convincing, but black visible parts were desired for one labelling series,” Semsroth said.
“This soon resulted in a product that met the customer’s requirements in terms of technology, price and appearance.”
Since the roller doesn’t reflect light, it allows for easier collaboration with camera systems.
In the online tool, the user only has to specify the outer and inner diameter as well as the length of the roller, the load, the tight space. It operates over a wide range of input voltages 10 ~ 500 VAC which allows universal compatibility.
Also, with 2 channels built-in relay outputs, it can be linked with sirens or lightings for alarm messages.
It also supports Modbus RTU, Modbus TCP, or CANopen protocols for easy integration.
Key Features
Its multiple key features include BiDirectional Energy and True RMS Power Measurements. There is also Energy Analysis for 3P4W, 3P3W, 1P3W, 1P2W, with Current Measurements Up to 500 ~ 4000 andVoltage Measurements Up to 500 V.
Its Rogowski Coil Soft CT is for Easy Installation and W Accuracy Better than 2% (PF=1 Input Current >50A).
There is Total Harmonic Distortion (THD) feature with RS-485 or Ethernet (PoE) Communication and Supports Modbus RTU/TCP Protocol.
Finally it also has Built-In 2 Power Relay Output (Form A) and IEC 61010-1
TREOTHAM’S LABELLING TECHNOLOGY GETS NEW LOOK

and EN 61010-1. load case, and the ambient temperature.
If the user follows the second step, they can select their guide roller based on the deflection, weight and price data – all directly from Treotham.
Treotham Automation is a leading supplier of high-quality electrical components and products to a wide range of industrial markets.
Treotham Automation 1300 657 564 www.treotham.com.au
SELECTING THE RIGHT SEIFERT COOLING SOLUTION FOR YOUR ENCLOSURE APPLICATION
The selection process for determining appropriate cooling for your enclosure and protecting the equipment inside needs to be thought thru. Here are some points to assist in the process of evaluating cooling requirements.
Consider the size and build style of your enclosure; it needs to be a minimum IP54 (ingress protection, where 5 = solids - dust protected and 4 = water - protected from water splashed at all directions. We recommend this IP rating as a minimum.
The functionality of Seifert precision air conditioners works on a split system, dual air circuit principal.
The internal cabinet circuit recycles clean cool air within a pressurised zone. The external air circuit relies on drawing and exiting air to atmosphere.
What’s your enclosure fabricated from. If it is stainless steel, we recommend a stainless steel air conditioner. Stainless 304 as standard and 316 for harsher environments.
For a guaranteed supply of safe and reliable conveyor belts for your material transport needs Kinder Australia’s K-Commander series has it covered. A poorly tracked conveyor belt can lead to a number of productivity and safety issues. Damage to the conveyor belt when it misaligns or tears, as well as the conveyor structure can become a major problem. This becomes a significant safety risk. Conveyor belt misalignment may lead to material spillage and may increase the risk of accidental slipping or personnel becoming entangled. Material spillage can then damage idlers and can cause conveyor rollers to seize. The ideal scenario whereby a conveyor belt tracks "true" in the centre, involves idlers and pulleys being aligned, leveled and square to centre line prior to loading the belt. It should be pivoting and rotating freely when the belt is tracking. Other options include fixed tracking solutions without rotating structure.
For mild steel applications as standard Seifert units are powder coated RAL7035 - a light grey finish as standard.
For outdoor environments we recommend the dedicated OC series of Outdoor units or the Slim Line Pro series. By default, these units are IP56.
For indoor applications maybe the Compact series or the Slim Line series. Again, they are available in mild steel powder coat finish or stainless steel. These units are rated to IP54.
When establishing the required cooling capacity to suit an enclosure we take into consideration the following- Maximum ambient temperature.
Where the installation location is, indoors or outdoors -
Maximum internal temp – that is the required internal temp of the enclosure to be maintained at – In most applications it is around 35ºC. In order to install any one of the K-Commander® series, the belt needs to be monitored in order to identify any problem areas that cannot be solved by making adjustments. The K-Commander Exceed Series is an all-direction belt tracking solution featuring flexible 360o rotational capability, with its separate axial and rotational function allowing for the double axis pivot bush. While the K-Commander Exceed Series P has been designed to use in two steps. The first stage focuses on the inner shell, which contains the shaft and an engineered pivoting bush allowing the axial movement of the tracker. A flexible EPDM rubber boot protects the inner shell. The second stage focuses on the roller bearings, which allows the rotational movement of the tracker. The roller bearings connect the inner shell and the outer shell and are protected by a labyrinth seal. The installation of the K-Commander Control Series is only for the return side, being the most critical surface of the belt in order to maintain belt alignment.
What the power supply source is - 240V AC or 400V AC (3 phase).
Solar load on the enclosure, are sun shields fitted and Thermabreak installed- These need to be considered.
Thermal dissipation of equipment. Probably the most complex part of the equation and generally the hardest to define. Sometimes the data sheets of equipment will identify thermal loads in Watts or British Thermal Units (BTU’s).
Can take a bit of investigation. We are happy to assist in this area. These are the main criteria for selecting a suitable cooler.
To assist, refer to the Seifert web page “Cal-cool-ator”.
By answering the above questions and a few additional, it will assist with fine tuning an appropriate cooling solution for your application.
Alternatively, we are happy to work thru the process of establishing a suitable The unique engineered action of the central ball and socket link is encased in a rubber covered steel tube. This protects the internal mechanics and ensures that the belt runs true. The K-Commander Direct Series are a pivoting base style, available in both trough and return applications automatically providing belt centering. The outboard servo rollers cause the idler frame to pivot as they contact the belt edge and this swivel action causes the belt to realign automatically. To further aid belt tracking, Kinder Australia offer rubber lagged rollers (trough and return) as an option for your belt tracker. The results are better tracking performance (especially in heavy duty applications), Increased roller durability against the constant scuffing nature roller shells in trackers experience and increased belt training response. Made of highly wear-resistant polyurethane, the K-Commander® Tracking Discs fit both flat and vee return rollers as well as selected troughing rollers. Ideally, they are located in pairs prior to the tail pulley to help align the conveyor belt, and so eliminating spillage from miscooling solution in consultation with you.
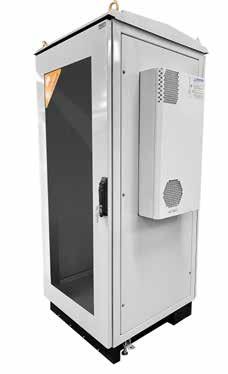
Seifert Systems Pty Ltd 03 9801 1906
K-COMMANDER CONVEYOR BELT TRACKING FOR ALL-ROUND SAFETY
www.seifertsystems.com.au
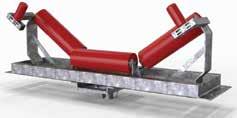
tracked belts.
They are easy to install with a split on one side to slip over the roller – no need to remove the roller.
Finally, the K-Commander® Guide Series INV is an all-purpose conveyor belt alignment idler ideally suited to short centred or reversing conveyor applications.
The two inverted vee rollers put pressure down onto the belt, promoting centralised belt training.
The universal frame adjusts to all types of mounting structures and is installed just after the head pulley, or prior to the tail pulley. They are suitable for reversing belt and are available for all belt widths.
So there are many customised options, which can assist any belt tracking needs using the K-Commander series.
Kinder Australia Pty Ltd www.kinder.com.au