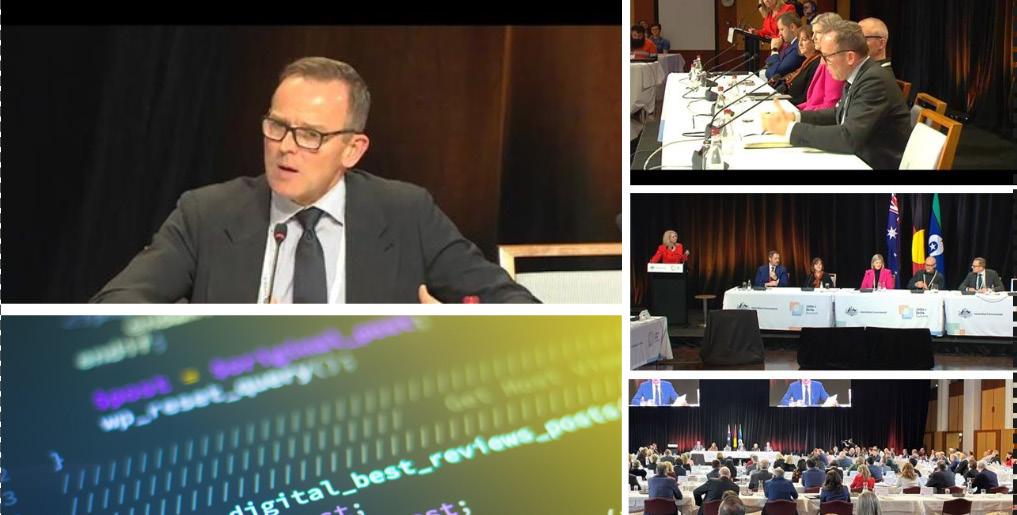
13 minute read
Industry News
Manufacturing: misunderstood,
mismeasured & miscommunicated By Christine Powis
Advertisement
When Dr Jens Goennemann addressed the Jobs and Skills Summit last month, he didn’t pull any punches, telling attendees they did not understand manufacturing.
The Managing Director of Australian Manufacturing Growth Centre said it was wrong to think of manufacturing as a sector and nor was it all about making finished goods. Rather, he told them, it is a capability that cuts across every sector where anything is being made.
“This misunderstanding is compounded because we also use outdated measures,” he said. “These measures ignore roles in pre-and post-production, although these roles account for more than half of manufacturing jobs and are higher-paying, more resilient manufacturing jobs, which are also a growth category and where women’s participation has tripled.”
The misunderstanding, Goennemann told Industry Update, has had a profound impact on all aspects of Australia’s manufacturing capability—from ways many manufacturers think of their own businesses, to how government policy works, and to the way Australians, especially job seekers, think of manufacturing as a career—or not!
“If you get it wrong from the start how can any policy be well informed— it’s impossible. If policy makers and the public believe manufacturing is production, or assembling products from overseas, then we will not extract maximum value from manufacturing.
“So, subsidies to assemble cars designed and engineered overseas will never have a lasting impact – because we don’t engage in all steps of their manufacture.
“Whereas, if an industry department has a project proposal, for example with AMGC, where we take $57m to create $1.6bn revenue and along the way create 4,000 local jobs with local manufacturers, that’s policy at its best—informed by profound research and real, impactful outcomes.”
Australian Bureau of Statistics (ABS) figures show manufacturing employs about 900,000 Australians, yet AMGC has found the ABS doesn’t count crucial roles in pre- and post-production.
Based on AMGC data, manufacturing employs circa 1.3 million Australians (3.5 times the mining sector) which creates an average of 3.5 jobs—in food and other retail, childcare, education, and support services.
“We mismeasure it, so we end up miscommunicating it and portraying jobs as blokes in overalls and hi-viz— not the case but it’s what the public thinks and what our children are led to believe.”
Goennemann believes the mismeasurement creates a distorted picture which not only affects government policy but has led to worker shortages: manufacturers are having trouble finding people for roles from talented skilled labour to digitisation experts.
Recent generations have been losing interest in manufacturing, says Goennemann, because we keep hearing manufacturing is shrinking and don’t know about the variety and expertise it often involves. “We get it wrong before the work begins,” says Goennemann, “and it impacts the pipeline of people looking to a manufacturing career, but manufacturing indeed can offer a job for anyone, of any skill set, from any background.”
He says misconceptions about manufacturing are deeply wired in Australians so that we favour finished goods and production lines when thinking about manufacturing. Finished goods are easier to understand, and great for ribbon-cutting photo opps. But all 141 manufacturing projects co-financed by AMGC have a digitisation component— they’re high-tech businesses.
Scaling up
Rather than a dearth of research, ideas, or the capability to turn them into reality, the capacity to scale up is the biggest problem for many Australian manufacturers, and therefore a focus of AMGC’s support. Of the 47,000 manufacturers in Australia, about 90% are small businesses employing less than 20 people— who often wear several hats.
“It’s difficult for small businesses to scale up to international sales where they could have 7.5 billion global customers, not 25 million locals,” says Goennemann. “Yet that is what an Australian company is doing with carbon fibre wheel rims.”
Importantly, building scale in manufacturing is among the 36 outcomes from the Jobs and Skills Summit to which the government has already committed.
The government also committed to support jobs growth and resilience in the clean energy supply-chain by increasing Australia’s value-adding, clean energy manufacturing industries.
AMGC research shows that 95% of Australia’s manufacturing exports are generated by just 5% of local manufacturers. This means that even a small uplift in growing the scale of local manufacturers could have an immense impact on jobs and GDP.
Cleaner, Greener. More sustainable aluminium for your projects.
Capral now offers lower-carbon aluminium with a certified CO2e content of 8kgCO2e/kg AL or below. Make a responsible choice; choose locally extruded, lower carbon aluminium from Capral.
For more information visit: capral.com.au
Goennemann expects AMGC’s mantra is sinking in, and there will be good results from the summit.
Bespoke bodies for Australian trade vehicles
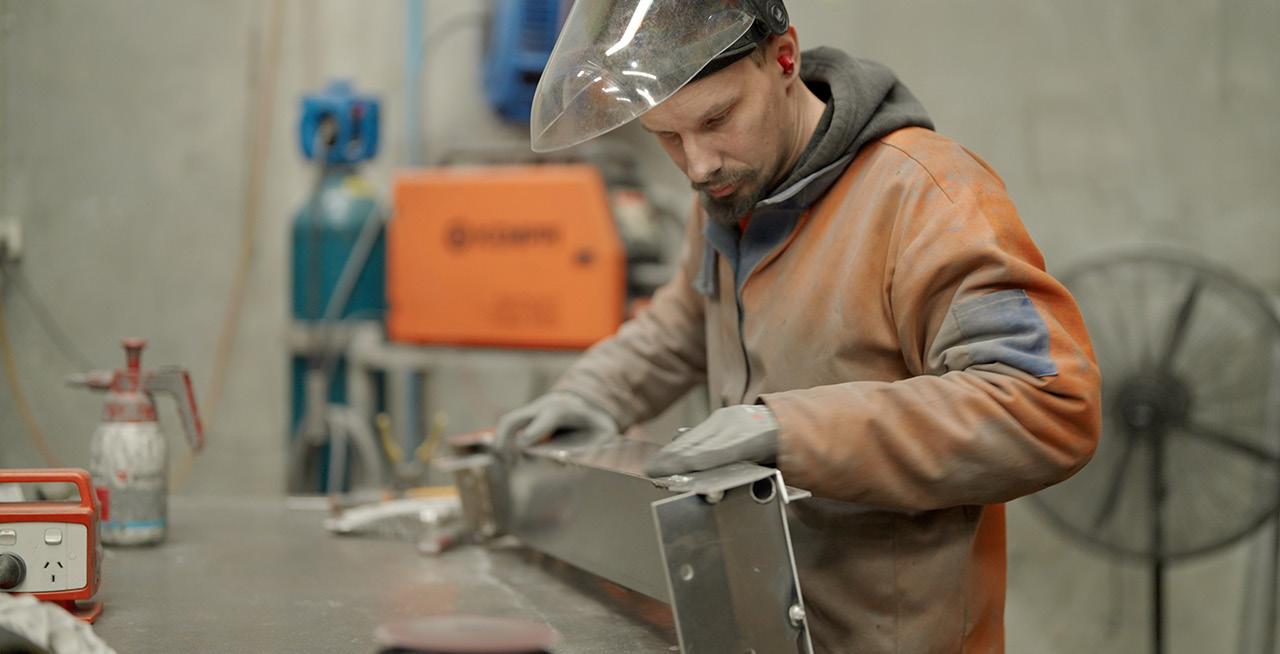
When Andy Park and his business partner began a Perth metal fabrication business 20 years ago, they looked for a gap in the market where they could apply their creativity.
Then, badgered by an electrician friend, they built the first Bull canopies and were soon creating a small run of bespoke canopies. They had identified a need in the vehicle build-up market for a standardised, scalable solutions for heavy industry vehicles used in mining, and by emergency and utilities services.
They worked at perfecting Bull Motor Bodies’ manufacturing processes and automated production. The team designed a new way of fabricating vehicle canopies to streamline the process, shed excess weight and create a more stylish body. The resulting AeroBody range led to interstate contracts with large fleets.
But managing director Park says they realised there was scope for their business to innovate further.
“In 2007, we decided to take all we’d learned so far and start again with design. We invested in 3D software and looked at the whole thing differently.
“How would a car manufacturer make this product? How could we use new technologies?
They wanted to use their essential material, aluminium, more smartly, using engineering, adhesives and new processes.
Using a clever mix of technology, premium aluminium and automotive plastics, they created a range of strong yet lightweight, stylish chassis-mounted modules to suit all light utilities on the market.
Fast forward to 2013, and Bull Motor Bodies opened its first interstate operation in Queensland and then its national distribution centre in 2018.
Today, a generation on from its modest start, Bull Motor Bodies is a preferred provider for some of Australia’s largest fleets. Bull has literally built up more than 13,000 vehicles.
Bull motor bodies withstand Australia’s harshest conditions. For instance, their bespoke northwest mining utilities run 24 hours on offroad corrugated tracks.
Bull’s biggest client sector is mining: the company builds directly for large mining companies and businesses servicing the mining sector.
“We work long and hard with our big clients to understand what their technicians do on-site, what tools and weights they carry, what terrain they travel over and how it’s going to be compliant,” says Park. “We sit with them, visit their sites, talk to their people and try to understand what works, what doesn’t, what is essential and what is nice to have.” Bull provides design concepts for review before creating prototypes to trial in the field for evaluation, with feedback informing final designs. Its bespoke solutions draw on a wide range of standardised and proven parts, saving its clients time and money.
Park says the Bull team found aluminium the best medium to work with from its earliest days.
In 2007 Bull looked for a supply partner which ticked the right boxes as to who they were and what they could do and offer.
“We knew we needed lots of extrusions; we needed an experienced Australian company with local die-making facilities able to turn things around quickly, with the capability to advise us on aluminium use. An Australian company that could service us as we grew.”
Capral Aluminium matched their brief and has become the most important part of Bull’s supply chain, providing more than 30 unique and standard extrusions along with aluminium sheet in different thicknesses, grades and widths.
Park believes that the ability to design custom extrusions with Capral is part of what differentiates Bull motor bodies in the market.
“It takes all the complexity out of the day–to–day build but adds all the smarts of the design into it.”
As a long-term Capral customer, reflects on the relationship as more of a partnership, commenting that transparency has become one of the great benefits to both parties.
“We have cooperation as to future needs, warehousing and logistics so we work more as partners rather than a distant supplier. Capral is the most important part of our supply chain.”
Park stresses that a highly skilled, stable workforce capable of crafting high-quality vehicle bodies has been central to Bull’s success.
“Every time we touch any part of our work, we are thinking how it could be better and what we can improve. We have a culture of innovation; everyone feeds back, and in, we push forward.
“We live and breathe crafting our products; we are all dedicated
to making sure our products are perfect when they go out the door. The laser-cutting, 3D designs and extrusions give us a head start.
“We don’t lose people. When they join us, we look after them, and they hang around. It’s a good place to be.”
Park’s focus is on pushing the business forward by making things easier to do, making Bull a better place to work and producing designs others only dream about.
“We challenge ourselves daily to be more sophisticated as a supplier.”
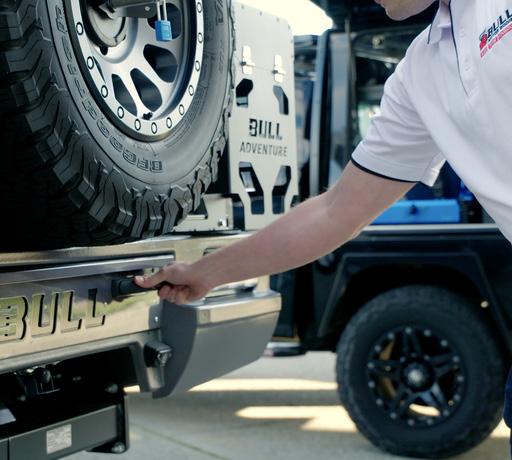

Capral
Deputy Leader of the Opposition and Shadow Minister for Industry
Sussan Ley
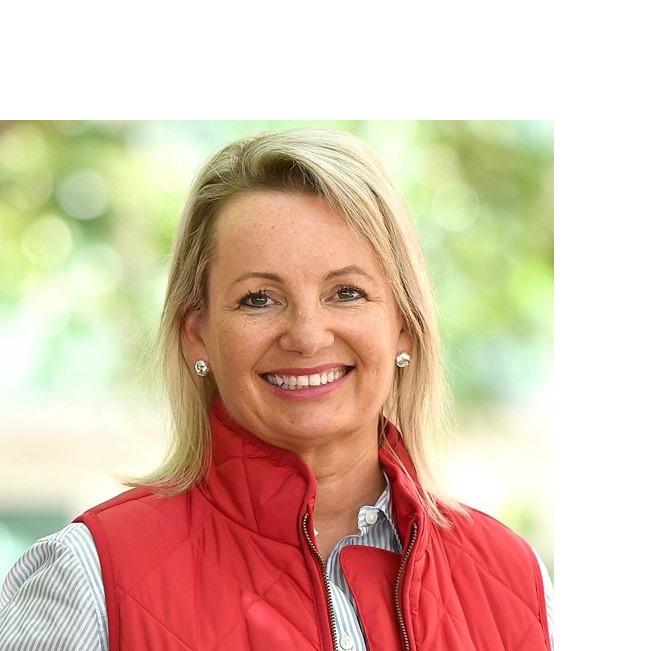
As the federal opposition considers our next set of industry policies, I want to take this opportunity to thank the manufacturers of Australia and let them know my door is always open to hear what is going on in their neck of the woods.
Australian manufacturers have walked a difficult road through this pandemic. They have had to pivot all the way. Manufacturers have had to run workshops and change the way their businesses operate. They’ve had to split rosters, divide up teams and separate production lines.
Manufacturers have faced supply chain shocks and unpredictable hits to margins. It has been tough. But equally manufacturers have been up to meeting these challenges the pandemic has posed to our nation.
Manufacturers changed their products to help Australia mask up and stay sanitised. They built new capabilities and shifted to support sovereign need over business sense.
It’s no stretch to say Australian manufacturing kept the nation moving.
Manufacturers have come through a storm — many survived thanks to the support of government assistance through programs like JobKeeper.
This was always the plan. We needed to insulate our economy from the shocks so we could grow through the post-pandemic period.
With the major impacts of the pandemic behind us, many manufacturers now face new risks and a cost-of-business crisis that isn’t just brewing – it’s erupting. As the Federal Treasurer himself has said, storm clouds are on the horizon.
Travelling across the country in recent months, I’ve heard a great deal from manufacturers and small businesses.
Inflation is hitting all parts of our economy. We have rising energy costs, an inability to get skilled workers, soaring input costs and massive supply chain disruptions. These are serious problems that need serious solutions.
Previously we sought to support industry with partnerships. Our $1.3 billion Modern Manufacturing Initiative (MMI) did just that. These grants enabled manufacturers in sectors of comparative advantage and strategic importance to scale up.
The MMI initiative targeted manufacturers in defence, space, national security, food security, recycling, clean energy and importantly medical products, which have become crucial in recent years as we responded to the pandemic.
I welcome the Labor government’s commitment to this important initiative and am looking forward to seeing the projects which get underway over coming months.
An additional $52.8 million was committed to expanding the Manufacturing Modernisation Fund, and a further $107.2 million in our Supply Chain Resilience Initiative. These flagship programs were targeted and achieved in partnership.
Another key issue facing manufacturing is the cost of congestion at our ports.
According to the ACCC and the World Bank, Melbourne and Sydney ports are ranked in the lowest 15% for efficiency in the world. Out of 351 global ports, Melbourne ranked 302, Fremantle 326, Sydney 337 and Adelaide 339.
The ACCC has said it considers that industrial relations have played a pivotal role in inhibiting productivity and efficiency gains at Australian ports, exacerbating delays and increasing costs to Australian importers and exporters.
CEO of the Australian Chamber of Commerce and Industry Andrew McKellar said the Maritime Union of Australia maintains a choke-hold on Australia’s ports, trashing any measures that would encourage a more flexible and responsive workforce.
This is an issue on which we need to see action and an area we will be examining carefully. Yet our focus is not just in one sector – we are examining the pressures right up and down the supply chain.
On balance I think we got the settings right when it came to supporting Aussie manufacturers through the pandemic and I’ll be watching closely to make sure the balance is maintained as we face this cost-of-business crunch.
So thanks to all manufacturers for their hard work which kept Australia strong!
We have to keep at it … Because we aren’t out of the woods yet and we can’t afford to take a backward step when it comes to supporting Australian industry.
Green shipping with Treotham tech
Global shipping needs to reduce environmentally harmful emissions. With this goal in mind, the Spanish start-up bound4blue has developed a novel propulsion technology – fully automated sails that significantly reduce fuel consumption, by up to 40%.
A large proportion of ocean-going, coastal and inland vessels still run heavily on fuel oil and diesel. It’s a burden on the environment that’s no longer sustainable for shipping companies worldwide.
To help the international shipping industry achieve the common goal of climate neutrality by 2050, engineers are frantically developing greener drive technologies, such as electric motors or methanol- and ammonia-based fuels.
However, bound4blue from Barcelona is going in a completely different direction. Their idea is to use the power of the wind, combined with a novel drive system, to reduce fuel consumption.
To make this work, robust and durable components are needed that can withstand a harsh environment - such as igus’ plain and deep groove ball bearings
Lubrication and maintenance-free, the igus ball bearings are available from Treotham Automation.
Electric suction draws wind
The Spanish engineers’ invention consists of two complementary drive systems: wing sails and eSAILs.
The 20m high giant eSAILs are mounted on deck and automatically adjust to the wind – similar to a classic sail.
The wing sail looks like an aeroplane wing and is based on the same aerodynamic principles. The advantage is that it is a collapsible system that takes up little space on deck.
The column-like eSAIL comes with a special technical feature: an electric suction mechanism on the back of the sail draws in wind while the boat is moving.
This significantly reduces turbulence that is otherwise common. As a result, the airflow literally surrounds the sail, creating enormous lift with low drag.
That lift is up to seven times higher than that of a conventional sail, with minimal power consumption, and therefore strong enough to take the strain off the engines.
With the help of wing sails and eSAILs, fuel consumption can be reduced by up to 40%.
According to the company, a payback period of less than five years is therefore guaranteed.
To convince shipping companies of the benefits of this new drive system, the engineers also want to keep maintenance costs as low as possible.
The system has to withstand high loads, salty seawater, high humidity and changing temperatures for years – without frequent repair interventions.
These are demands that must be met not only by the largest but also by the smallest parts, such as the plain bearings. Hence, components from igus are used in the eSAIL.
The designers use cylindrical plain bearings made of the iglidur X material for the gear shafts and support rods of the sail.
The advantage compared to metal bearings is that the polymer bearings don’t corrode, even in direct contact
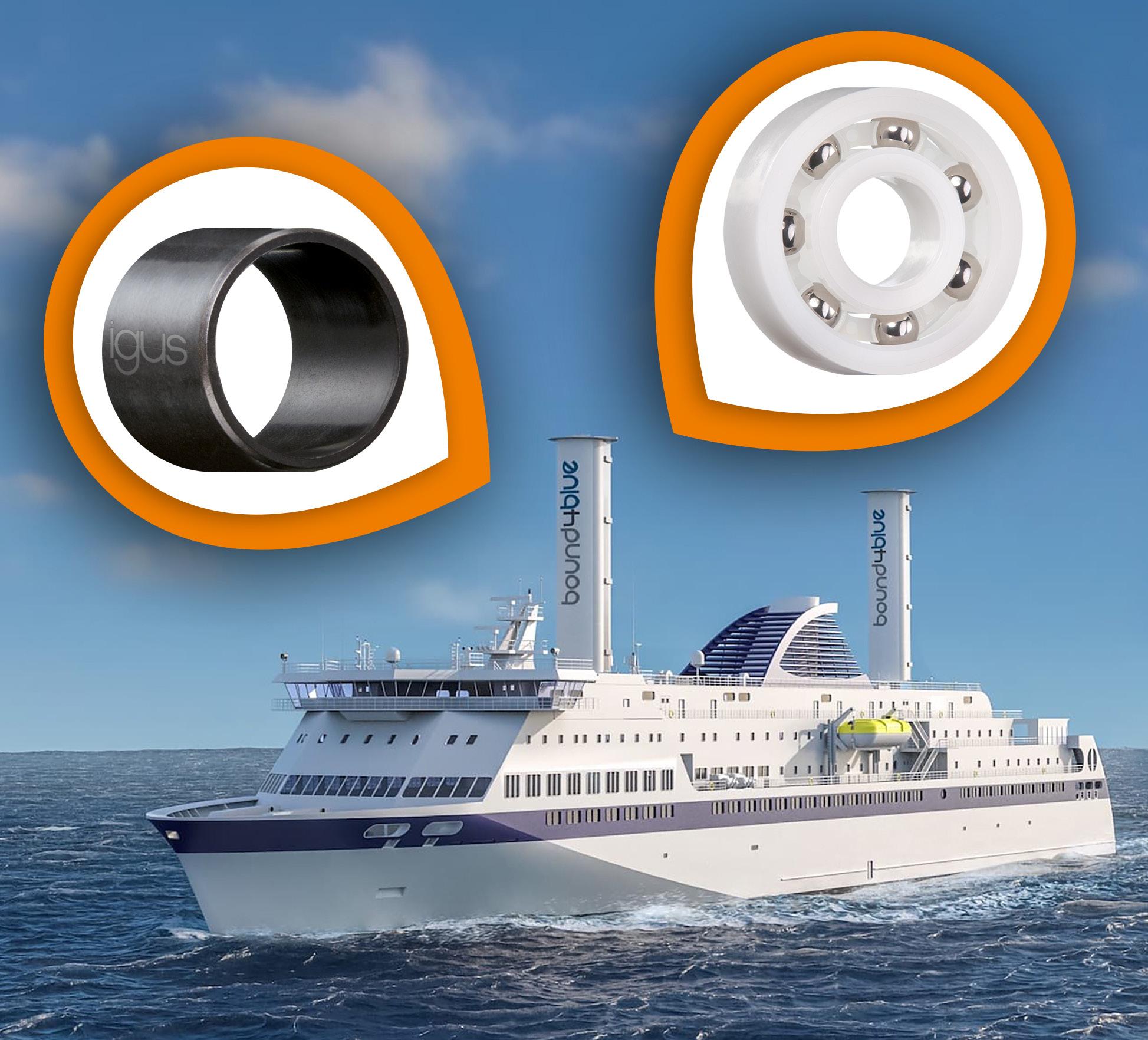