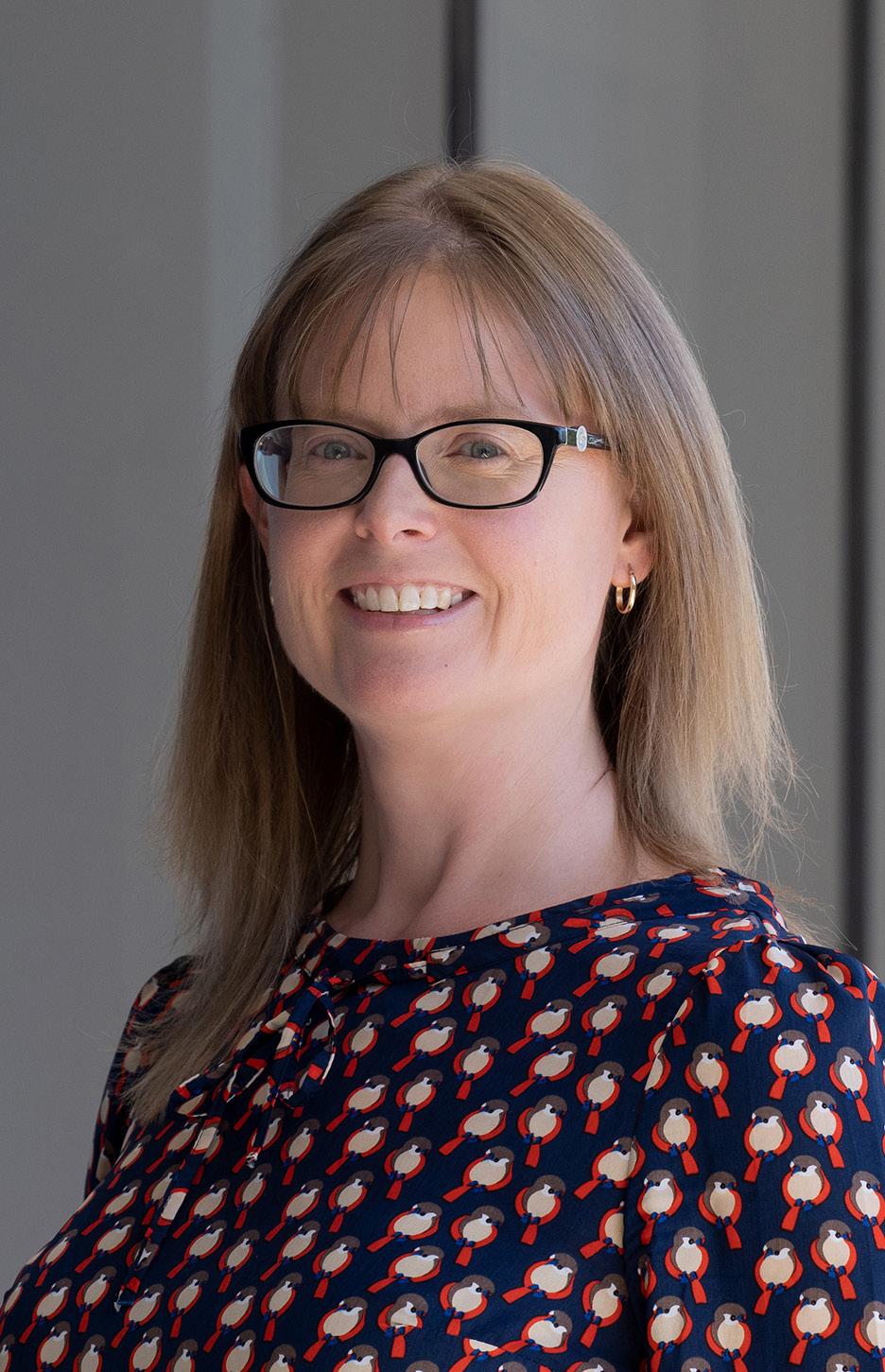
12 minute read
Women in Manufacturing
The age of disruption for manufacturers
By Margie Smithurst
Advertisement
When Meighan Heard, executive director at Mitsubishi Electric Australia, spoke on a panel of industry experts at the Smart Manufacturing Conference in September, she was the only woman (apart from female federal and state politicians) to take the floor.
“I did make the observation to the organisers at one point — where are the other women on this agenda?”
The challenge, she says, is to identify women in the industry who are ready, able and confident enough to stand up and speak in a public forum.
“I always think there must be more women who are capable of speaking up, so where are they?”
For women in the sector, Heard’s lead is a strong one to follow, and her observations at the conference contributed to a broader analysis of some of Australia’s manufacturing challenges.
IU: During the Smart Manufacturing Conference, you observed that we are in an age of disruption. How does this rapidly changing situation play out in the manufacturing sector?
Meighan Heard: We continue to operate in an age of significant disruption. Technology is changing rapidly, the geopolitical environment is quite uncertain, there are massive challenges in the sourcing of critical parts and components, and we are all affected by the situation which continues to unfold in China. This means we need to be prepared for the unexpected, constantly on our toes when making decisions and ready to change course at short notice.
IU: What is the impact of this disruption on the workforce in the manufacturing sector?
Meighan Heard: Mitsubishi Electric is both a manufacturer and a supplier to the manufacturing sector. With a factory in Sydney and purchasing arrangements with Mitsubishi Electric factories across the world, we have experienced and continue to experience the same challenges as other manufacturing companies in Australia. It is an uncomfortable and difficult environment to work in. There continue to be significant pressures associated with securing sufficient stock to meet demand. This leads to a level of stress and fatigue in the workforce, and no doubt this has been experienced across the board. It’s a credit to our teams that they have been so resilient and maintained a good sense of humour during this time.
IU: How does Mitsubishi Electric manage the relationship with its customers in this challenging environment?
Meighan Heard: This can be very difficult. Our customers want to know when stock will be available and when their order will arrive. Sometimes it is very difficult to know. We do our best to communicate openly and transparently about the status of orders and the availability of parts and equipment. Sometimes that information isn’t perfect but we’ve learned it can be better to share imperfect information to allow our customers to make decisions, rather than not share any information at all.
“We need to make it easier … for SMEs to explore the opportunities and take the next steps“
IU: What are your observations regarding the take up of automation in Australian manufacturing companies?
Meighan Heard: There is still some reluctance in Australian companies to embrace the opportunities presented by automation but this is changing. Until recently, there has been a strong concern from the community that introducing automation, robotics and other Industry 4.0 technologies into manufacturing companies will result in unacceptable job losses. The environment is now better for Australian manufacturers to explore and make this change. With unemployment so low and the need for skilled workers so high, it’s essential that we consciously ensure people can move from low skilled manufacturing jobs to higher skilled roles where there is a greater need in the community. Automation means that this can happen without losing (and potentially gaining) productivity in manufacturing.
IU: Are we making progress?
making progress. Covid has been a game changer. It has forced manufacturers to consider the alternatives and encouraged all of us to do things differently.
There is still a challenge in helping SMEs determine which Industry 4.0 technologies will best suit their needs and support their business objectives. We need to make it easier for the owners of SMEs to explore the opportunities and take the next steps in their companies – they are busy people! Some of the investment decisions are quite difficult and we need to provide the right support to help these companies understand the options, analyse potential solutions and determine which solutions are best for their business. AusIndustry offers some great programs for small businesses and the Advanced Manufacturing Growth Centre provides excellent support, including through its Manufacturing Academy. I’m excited by the opportunity to work with SMEs as they grow and achieve their goals by making smart decisions about what to implement.
Meighan Heard, Executive Director Mitsubishi Electric Australia
IU: Mitsubishi Electric is a Japanese company. Are there elements of Japanese business techniques that can support the change that needs to occur?
Meighan Heard: The concept of kaizen continues to be relevant and important for businesses that seek to embrace Industry 4.0 technologies and solutions. Kaizen is about continuous improvement over a long period of time. It involves making the work environment more efficient and effective by improving everyday procedures and activities and involving the workforce in the process. One helpful way for companies to consider approaching investments in new automation technology might be to apply this technique. It’s rarely necessary or practical for businesses to implement everything all at once. Instead we make ongoing continuous and
The age of disruption for manufacturers
Continued from previous page
incremental changes that make a difference and become stepping stones for the next investment. Applying kaizen can keep us focused on the need to constantly improve and evolve. It’s a practice I apply to both my professional and personal life, and was a strong attraction in my decision to join Mitsubishi Electric.
IU: What are your reflections on the presence of women in the manufacturing sector and how are women represented in manufacturing at Mitsubishi Electric?
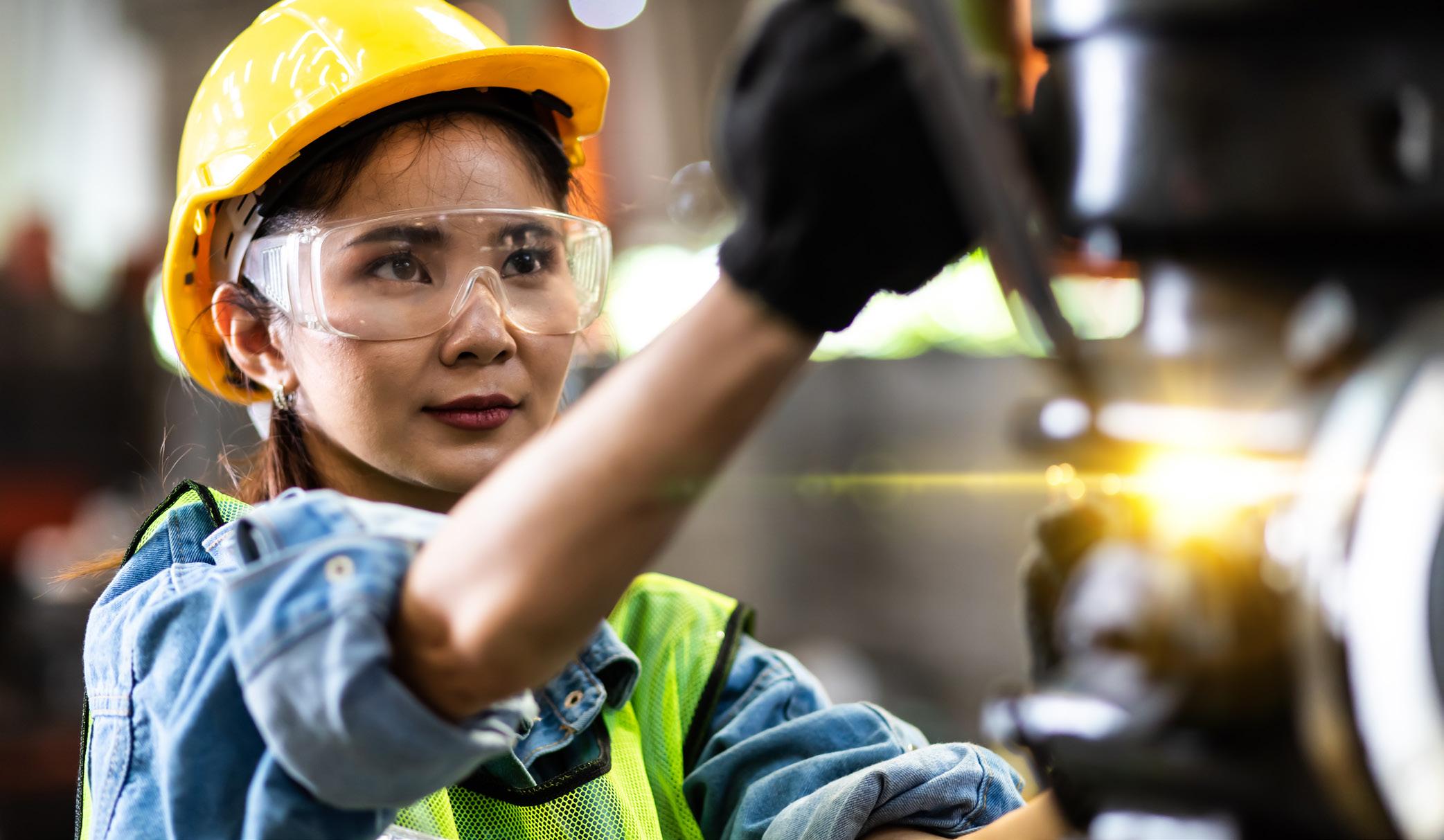
Meighan Heard: One of the things I love about our automation team is that we have a female leader who has worked in automation for 25 years. Rebecca Gatenby is a qualified electrical engineer who joined our team as a university graduate. She is extremely experienced and knowledgeable about our products and the automation industry.
As a sector, one adjustment we might want to make is to establish a formal association for Women in Manufacturing. In doing so, we could be inspired by NAWIC (the National Association of Women in Construction) which has been operating for a long time. NAWIC is a powerhouse in terms of advocacy and connectivity for women in construction. They have awards nights to celebrate the achievement of women in the industry and a long running mentoring program. We don’t seem to have anything equivalent in manufacturing, so it begs the question, should we?
IU: Do you have anything else you want to add regarding the topic of women in manufacturing?
Meighan Heard: If we want to see another step change in our ongoing quest for gender diversity and equal opportunity in the sector, we need to challenge the status quo and keep trying to look at things differently. As part of this, I’d like to see the sector engage in a meaningful conversation around part-time and flexible work for traditional male roles (such as trades) in construction and manufacturing.
While we have achieved big steps forward in providing flexibility and options for women navigating a career path and parental responsibilities, we don’t talk anywhere near enough about giving the same opportunities to men who take on the role of primary carer. This is a personal issue for me as my husband, who is a qualified electrician, has held the primary carer role in our household for almost 12 years. When our first child was born, his colleagues in the construction sector said he would never work on a construction site part-time. I just can’t accept this is not possible. If women can hold and job share senior positions in law, accounting, teaching and nursing, it must be possible to implement these models for leading hands and supervisors on construction sites. So where are these opportunities for men? Perhaps, as women, we need to take up this challenge and advocate for this to change.
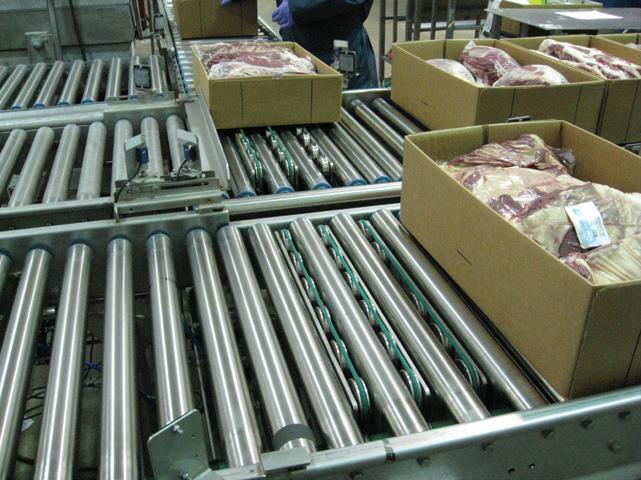
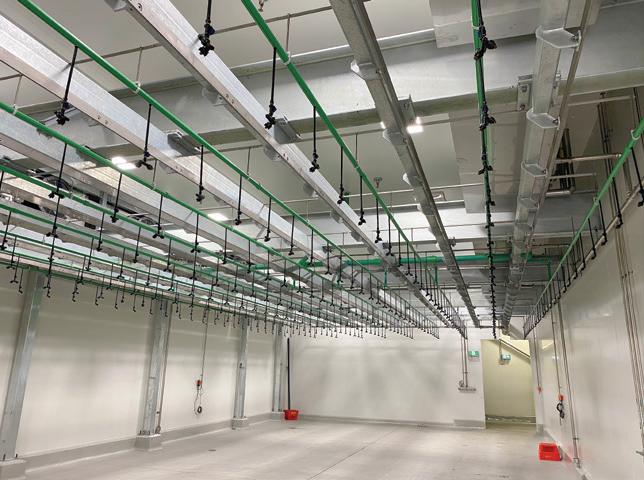
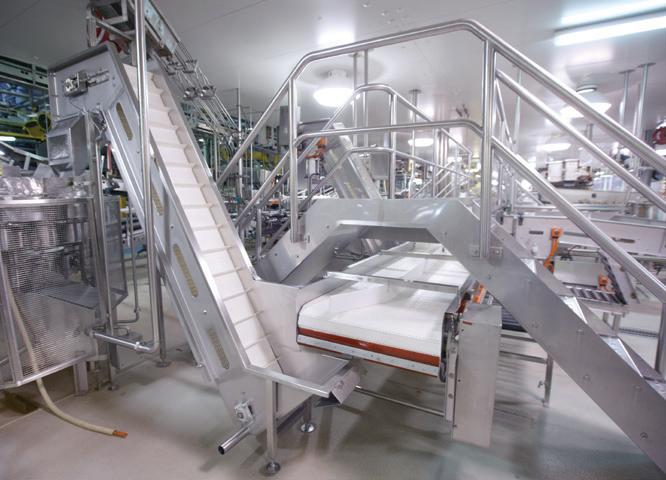
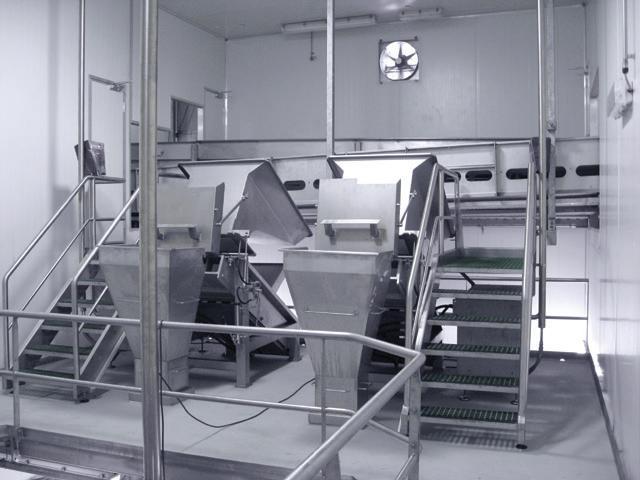
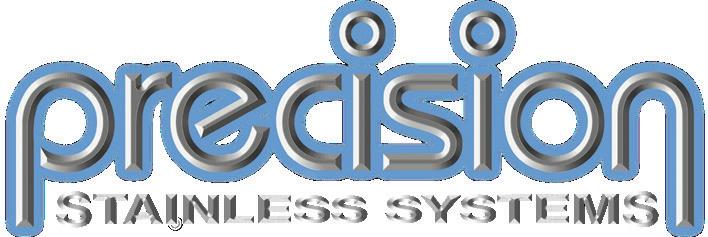
Breathing fire into uniform safety at RMIT
A$2.3 million modular, flame test chamber is one of the first of its kind in Oceania and will be used by researchers and research students in partnership with industry at RMIT’s Brunswick, Victoria, campus.
Called Flash-Fire Laboratory for Advanced Manikin & Material Evaluation (FLAMME), this insulated steel chamber which is roughly the size of a shipping container houses a mannequin which can withstand the force of 12 ‘super-power’ jet flames without getting burnt.
There is high demand for such a facility to test uniforms, according to Professor Rajiv Padhye, the Director of the Centre for Materials Innovation and Future Fashion at RMIT. Australian industry has been shipping items to Canada for testing, which can mean long waits to get the results back.
“We could test the fire resistance of uniforms for firefighters, as well as soldiers, gas platform workers and steel foundry workers,” he said.
The chamber is designed to be used for textiles, but Associate Deputy Vice Chancellor Learning and Teaching, Professor Robyn Healy says RMIT hopes to also test the flammability of building and automotive materials.
Outside the FLAMME test chamber is an operating room with a large viewing window so users can watch combustion tests in progress and adjust tests.
“This new facility will allow manufacturers both locally and from across the Asia Pacific to be there during the testing and make adjustments to the testing protocols where needed,” she said.
Protecting firies
Victoria is one of Australia’s most bushfire-prone areas, with 1.5 million hectares of land burnt in the 20192020 bushfire season alone. With the state about to enter another fire season, Healy said it was crucial to ensure Australian firefighters and volunteers have the highest quality uniforms to protect them.
“Firefighters are constantly putting themselves in danger to protect the community. This combustion chamber will help develop and test textiles that are up to the task of protecting them from the dangers of fire,” she said.
Victoria State Manager for the Country Fire Authority’s ( CFA) Personal Protective Equipment and Clothing, Mark Tarbett, welcomed the new facility. “This new technology will offer our industry access to highly specialised services to assess the performance of innovative fire-fighting materials and emerging protective garment designs,” said Tarbett.
“This will ultimately lead to safer outcomes for people working in high-risk environments such as fire fighters and other emergency service personnel.”
Materials innovation
RMIT’s strong partnerships with the CFA, Fire Rescue Victoria and other firefighting and military uniform makers will encourage high demand for the facility.
The project has been supported with funding from the Australian Research Council, the Defence Science and Technology Group, RMIT, Deakin and Swinburne universities, and garment manufacturing company Bruck Textiles.
Healy said the facility underlined RMIT’s School of Fashion and Textiles’ reputation as a leader in textiles research and development, as well as its responsiveness to industry needs. “We are really excited to now have this chamber operational,” she said. “It opens up so many exciting new opportunities for research, student learning and industry partnerships, and provides a solution the industry has been crying out for.”
A fire-proof mannequin inside the insulated steel chamber. Credit: RMIT University.
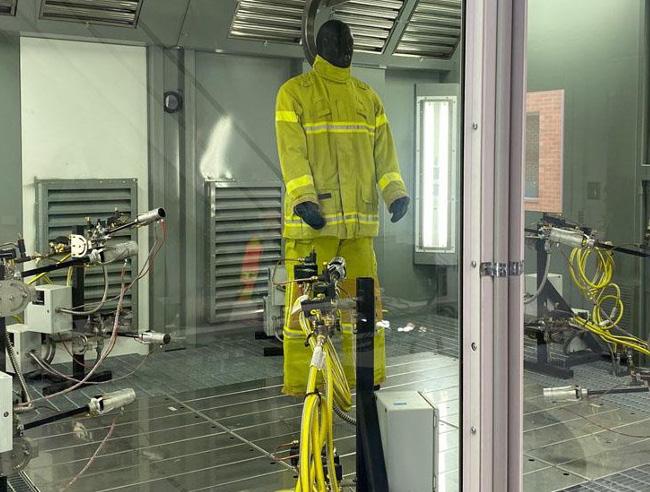
The ‘Shorts’ project: cobot design
Continued from page 25
Furthermore, if technology can make jobs more interesting and attractive to young people, then tech can help keep those industries alive and thereby keep people employed.
It’s especially true, says Roberts, if Australia’s goal is to have sovereign manufacturing capability then “robots and new tech can be part of the solution”.
Morale at Infrabuild is already up, with Thomas reporting staff as more than pleased to get the intense conveyor job off their roster. Sales
are also expected to go up, based on better quality to customers, who’ll appreciate not getting ‘shorts’.
“It didn’t matter how many bars were on the table, the cobot picked up all the shorts “
payback on the $360,000 project cost, which includes capital to industrialise, manufacture, install and commission a smaller, fit-forpurpose version of the cobot at its Sydney Bar Mill (that cost excludes the membership fee paid to be an ACC partner).
Having proven success with a big industrial robot, the smaller cobot will be scaled to have similar reach to a person’s arm.
“We’re looking for an integrator who can take all that research and results, and commercialise it,” says Thomas.
As a co-design between Infrabuild and the ACC engineers, the hook, which looks like a big boat gaffer, is now joint intellectual property. “Lots of integrators out there claim they can do a lot of things — but I haven’t seen any that can do the amount of R&D that ACC has done,” says Thomas.
Close up of the bars rotated
Australian Cobotics Centre
australiancobotics.org
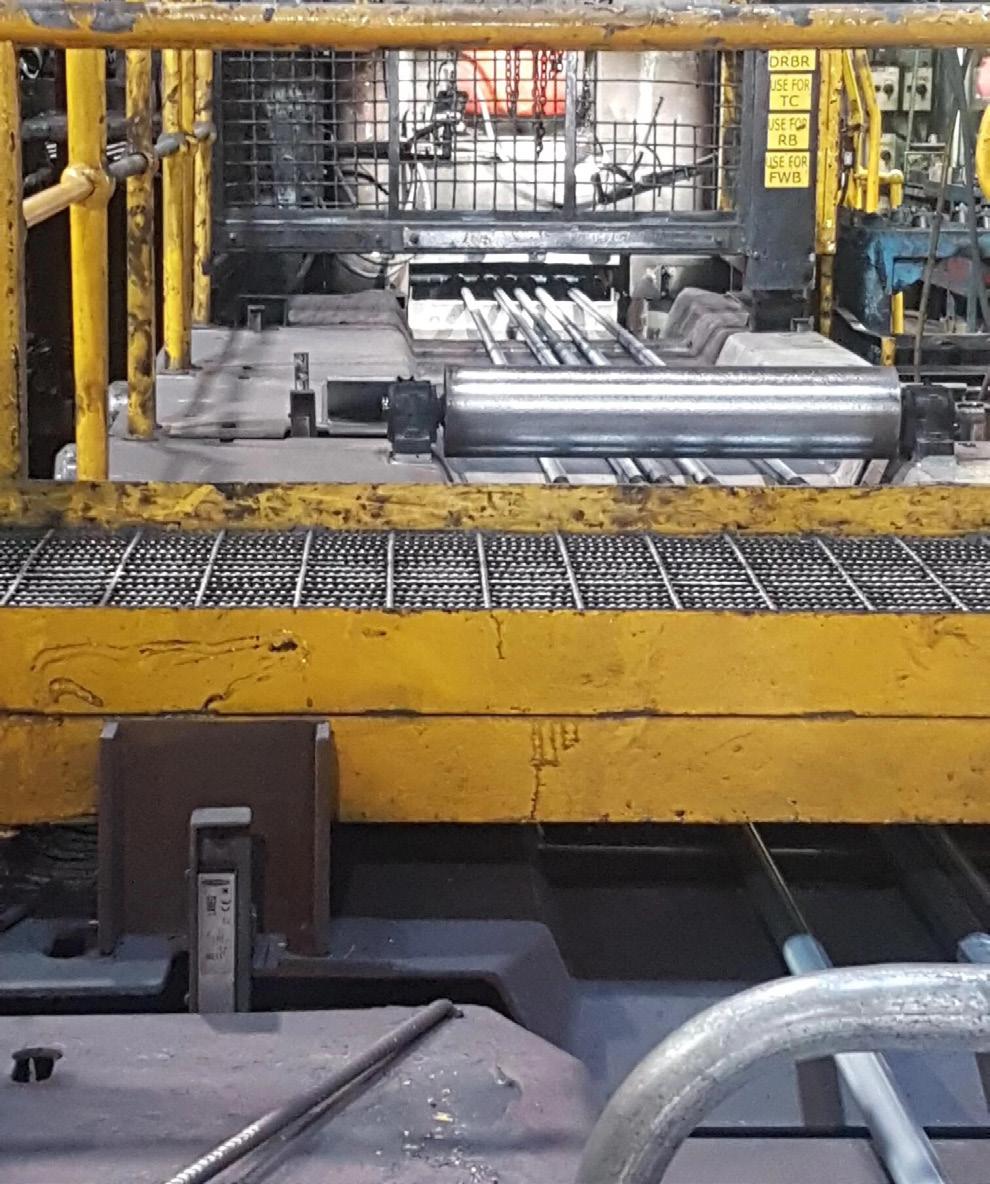
About the Australian Cobotics Centre
The ACC started in 2021 and is a collaboration between four universities and six industry partners. Together they aim to help Australian industry adopt collaborative robots to solve problems and improve capability in manufacturing. The ACC also trains researchers, engineers, technologists and manufacturing leaders in expertise needed to apply collaborative robotics technology. The research programs address the technological advances and the human and design factors to be considered when implementing new technology. This multi-disciplinary and multi-industry approach will result in improved safety, quality assurance, production efficiency, process innovation and workforce readiness across the industry. Funding for the Centre is via the Australian Government through the Australian Research Council’s Industrial Transformation Research Program and industry and university partners.