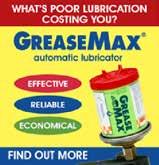
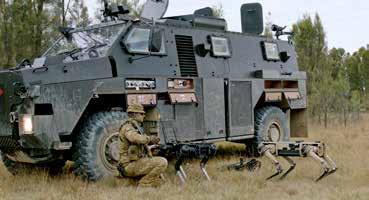

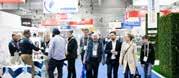
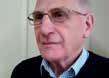
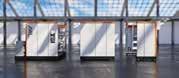
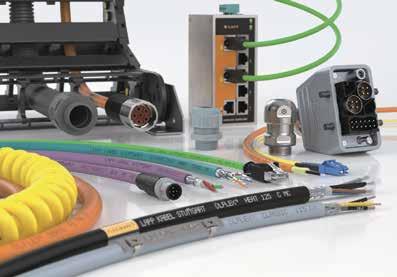

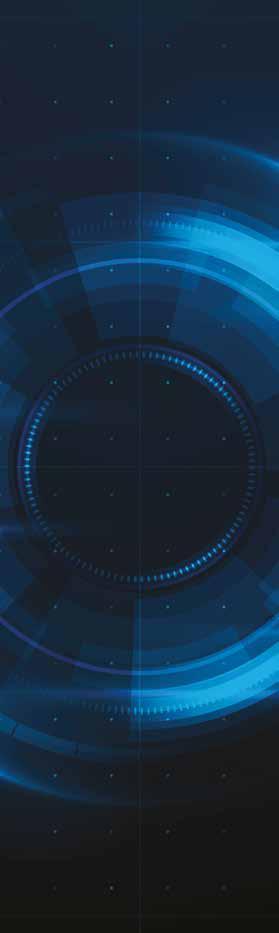


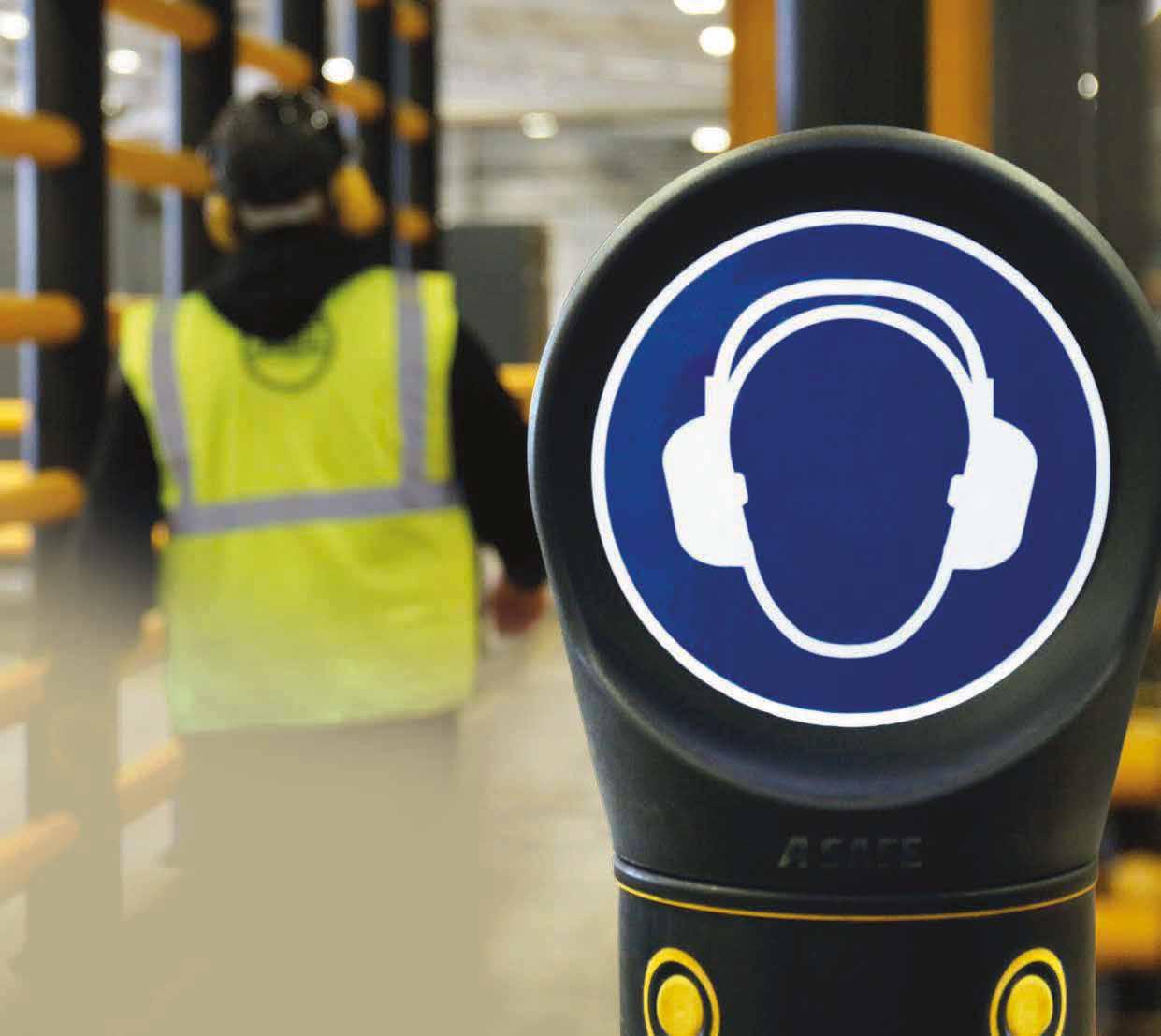
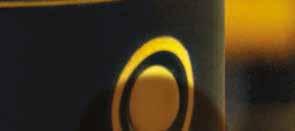
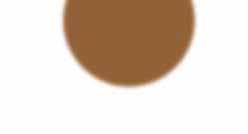
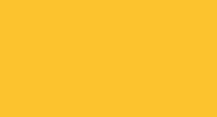
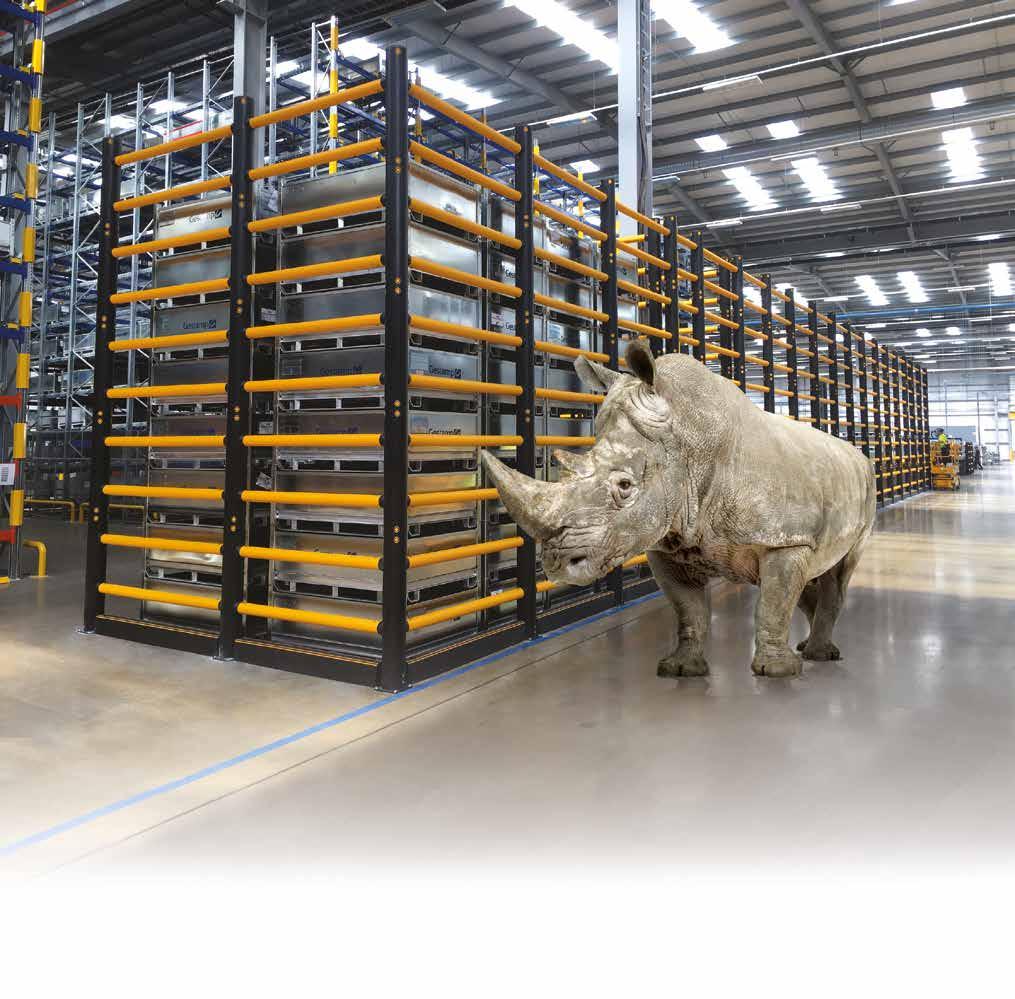
Far too big for any booth, a specially assigned 1,000 sqm area within our Sydney store, has been set aside to demonstrate how technical advancements in modern machinery will increase your business's efficiency and profit.
More than ten brand-new cutting-edge machines gathered from around the world will be on display and used over the three days.
Head CNC Machinist, Danny Sims from Brad Jones Racing, will be on hand to share his experiences, as well as representatives from UNIMIG Welders, Brobo Machinery, Bramley Manufacturing Equipment, Sutton Cutting Tools, Pilot Air Compressors and more.
This is a strictly RSVP event, so please confirm your attendance quickly to avoid disappointment
All FUTURE VISION attendees go in the draw to win one of 5 x $1,000 gift cards!
Robotic Automation Systems
5-Axis, 3-Axis and Vertical CNC Machines
CNC Plasma Cutters
Synchro Pressbrakes
Automated Lathes
Water Jet
After going into voluntary administration last October, dessert manufacturer Sara Lee is set to be sold to the same family that bought Darrell Lea from its administrators in 2012 and made it viable.
Sara Lee’s Australian and New Zealand businesses will be sold to a private company owned by Klark and Brooke Quinn by the appointed administrators, FTI Consulting.
The administrators said the sale was a competitive process that has saved more than 200 jobs.
“Staff and consumers have rallied behind the business during this tough time, and we are so grateful to the loyal workforce and management team who have made this process a
success while they have continued to produce amazing products,” said administrator Vaughan Strawbridge.
“We have enjoyed working with the
Sara Lee team and are pleased to see them come through this process. Many staff have been with Sara Lee a long time and we have seen their passion for
Sara Lee is based on New South Wales’ Central Coast and has produced frozen desserts, pies and ice cream there for more than 50 years.
In the early ‘50s when an American firm wanted to import Sara Lee product, founder Charles Lubin set about revolutionising his business and fresh product which then did not freeze well. By ‘53 Lubin had created a new food production and freezing process which suited shipping.
By 1988 the company had 126 different product lines including cheesecakes which sold at a rate of 50,000 every day.
Tindo Solar, Australia’s only current manufacturer of solar panels, has announced plans to build a $100m gigafactory to meet local demand and offset the influx of cheap Chinese panels.
The company plans to use government funding to get the factory up
and running, including via the $15bn National Reconstruction Fund and Australian Renewable Energy Agency.
CEO Richard Petterson said production would begin in mid-2025 and be able to manufacture 7,000 panels a day at full capacity - about a third of Australia’s solar panel daily
Haigh’s has announced it’ll build a new $130 million factory at Salisbury South in Adelaide to double its chocolate making business to 2000 tonnes a year.
It’s the largest single investment in the Australian family company’s 108 year history, and includes 9000 square metres of new production facilities, plus warehousing and online orders space and $36 million worth of European-made equipment.
“This project represents a
significant milestone for Haigh’s…, allowing us to meet increased demand and interstate growth opportunities, including entering new markets,” said Chief Executive Alister Haigh.
The company, which employs 800 people, says the facility will be operational in the second half of 2025 and create hundreds of new jobs.
“Not only will this project directly create new jobs and opportunities at this site, it will facilitate employment growth across our retail
sovereignty and “affirms our energy independence”.
“Tindo Solar envisions playing a pivotal role in meeting the considerable demand, contributing to the estimated 22,000 PV panels expected to be installed daily to achieve our decarbonisation targets,” said Petterson.
“It is critical Australia moves quickly and ensures we enjoy the benefits of the energy transition by creating hundreds of jobs and a domestic renewables manufacturing industry.”
Petterson also said Tindo shouldn’t be the only solar panel manufacturer in the country and called on governments to “get the settings right”.
In an interview with the AFR, Petterson said that Chinese panels needed replacing after 10 years but Tindo’s panels, with a 25 year guarantee, “are designed to last 30 years”.
Petterson said more than 90 per cent of rooftop solar panels in Australia came from China, and in the last year there’s been an influx of cheap, imported panels in the market.
“Australia is a dumping ground for cheap panels,” he told the AFR.
demand.
The factory, at a yet to be announced site on the east coast of Australia, would make up to 1.9 million panels a year.
Petterson said the move “goes beyond mere manufacturing”, it bolsters Australia’s domestic
Around 3.4 million Australian households now have solar panels installed and Tindo, which is based in Adelaide, began manufacturing solar panels in 2011.
Tindo Solar tindosolar.com.au
business Australia-wide creating up to 250 new jobs in the medium and long term,” explains Chief Operating Officer, Peter Millard.
Haighs currently produces 1000 tonnes of chocolate across two existing manufacturing sites in Mile End
and Parkside.
The company spent $15 million in 2018, including on updating its cocoa processing plant at Mile End There are 21 Haigh’s stores across Adelaide, Sydney, Melbourne, and Canberra, as well as online.
Defence: A Growth Industry for Manufacturers.
Industry Update is pleased to launch its Defence Industry section, which will now be in every edition.
Australian manufacturers have long played a role in supporting defence policy, but now, as a riskier Indo-Pacific strategic situation looms, they need to take on a larger and more agile role - if at least for sovereign capability.
Already, large multinational defence manufacturers such as BAE Systems and Lockheed Martin work with Australian companies, providing mentoring and access to the latest technologies.
Australian manufacturers are also stepping up to directly provide defence with innovative technology to enhance its capability. Industry Update will be looking to cover those stories in each edition, as we have in this edition with SME Technology.
The Defence Industry news section of this edition shows how broad the manufacturing base for defence is: from the first locally manufactured guided missiles, to using Australian steel in the AUKUS submarine hulls, to electrifying Bushmaster vehicles, and innovative drone trials.
Other local defence contractor companies are taking advantage of increasingly sophisticated 3D metal and composite printers from international companies such as Markforged.
In terms of collaboration and international exposure for our local innovations, groups of regional defence industry manufacturers, such as the 100 or so that make up the Hunter Defence group of which our new Defence Industry editor, Tim Owen, is chair, are important. We’d like to hear from more of them.
The Chair of the Committee investigating Australia’s transition to electric vehicles (EVs) has called for submissions, saying one of the committee’s foci will be EV battery manufacturing.
Committee Chair Mr Tony Zappia MP said the number of EVs sold in Australia more than doubled last year “to 7.2% of all new cars sold in 2023, up from less than 3% in 2022”.
Broadly, the enquiry will investigate the necessary resources, systems and infrastructure for the transition and the impacts of moving away from traditional vehicles. It will explore opportunities such as fuel savings and affordability for people in outer regions to make this shift beneficial for all.
“Our focus will also be on the future of EV battery manufacturing, and we will consider challenges on electricity consumption and demand and our limited EV supply compared to other countries,’ said Zappia, who holds the seat of Makin,
Welcome to the first edition of Industry Update in 2024. This year the magazine will develop its Defence Industry content, ably assisted by regular columns from retired Air Commodore Tim Owen, who chairs the 100-strong Hunter Defence manufacturing network.
In this edition, we feature one of the innovative companies in that network, 3ME Technology, who have been electrifying Defence Bushmasters with their BladeVOLT lithium-ion battery system technology.
The Hunter region is just one part of Australia contributing to the country’s sovereign defence industry growth, and the magazine will also profile other companies in strong defence industry locations elsewhere, such as South Australia.
As the federal government implements its commitments to a more robust local defence industry, looming strategic concerns mean a more agile sector is also needed (see the Ai Group / Strategic Defence Studies
report on page 28).
Better communication between defence and industry, and a greater focus on strategic rather than economic concerns would lead to a more dynamic and resilient local defence industry in future, argues the report.
One of the perks of being editor / writer of this magazine is the chance to visit manufacturing sites and see how the process works. In this edition, we profile Weathertex, the external cladding company, which has operated from the same factory in Heatherbrae outside Newcastle for decades.
The invigoration of their turnover and branding over the past few years is a real manufacturing success story.
As well, businesses should be aware of the insidiousness of ‘invoice scams’ (p20), where company emails are being hacked and invoices sent via emails that look remarkably similar to suppliers’ ones. St.George advises making the effort to check any unusual bank account details over the phone.
South Australia, in the House of Representatives.
The Committee is calling for submissions to make recommendations on these aspects of the transition and on any or all of its terms of reference listed below by Friday, 22 March 2024.
The Committee’s terms of reference are:
• the establishment of resources, systems and infrastructure to support transition to EVs
• opportunities for expanding EV battery manufacturing, recycling, disposal and safety, and
• other opportunities for Australia in the automotive value chain to support ongoing maintenance of EVs
• the impact of moving from internal combustion engine vehicles, including fuel excise loss, existing auto industry component manufacturers and the environment
• the opportunities for fuel savings, such as by combining EVs with
other consumer energy technologies and savings for outer suburban and regional motorists
• the impact on electricity consumption and demand
• the impact of Australia’s limited EV supply compared to peer countries
• any other relevant matters
The new inquiry builds on the National Electric Vehicle Strategy released in April last year which laid groundwork for this new inquiry.
The National Electric Vehicle Strategy aimed to increase the supply of affordable and accessible
electric vehicles (EVs); to establish resources, systems, and infrastructure to enable rapid EV uptake; and to encourage increased EV demand.
It also follows other parliamentary inquiries into ‘Australia’s transition to a green energy superpower’.
Find out more about the Committee’s scope and make a written submission (by Friday 22 March) at the inquiry webpage.
Inquiry Webpage
Small and medium enterprises are an intrinsic and vital aspect of Australian manufacturing.
Run by smart, hard-working individuals, SMEs contributed $506 billion to the economy in 2021-22, equivalent to a third of Australia’s GDP .
Many have the potential to become the big businesses of tomorrow, propelling productivity growth across the broader economy.
The key to this is enabling science-based collaboration that allows ambitious SMEs to adopt new technologies and scale up their operations.
If we’re to become a sophisticated manufacturing sector able to meet complex needs, more of our SMEs need to onboard great Aussie ideas and get them to market.
That’s why I commissioned Industry Innovation and Science Australia (IISA) – the Government’s independent advisor on industry innovation – to review industry-research collaboration and identify ways to improve linkages.
Published in November, the IISA report found the Government’s supply-side, or “technology-push” strategies and investments have helped create a solid innovation and startup ecosystem.
Instead, the report’s focus was on the need to complement supply-side initiatives with “demand-pull” policies to encourage more SMEs to become more entrepreneurial and
technologically savvy.
For these enterprises, increasing aggregate market demand for products or services that have commercial or societal impact is likely to spur innovation and commercialisation.
The report proposes a range of actions to achieve this – and to remove or lower other barriers to a more efficient innovation process.
The IISA’s key findings and recommendations will ensure a more uniform and consistent approach by industry to innovation.
As such, it will guide our government’s actions in the years ahead.
In the meantime, we continue to progress other policies and program initiatives designed to grow Australia’s industrial capability.
The cornerstone of our industry transformation strategy, the National Reconstruction Fund Corporation, officially commenced in September, with the Board meeting for the first time.
In November, I signed off on the NRFC’s investment mandate with Finance Minister Katie Gallagher. And this month [February} we appointed Ivan Power aS the NRFC’s new chief executive officer.
Mr Power has worked in global investment for more than 25 years, and during his time at Macquarie Group built a strong track record in working with early-stage startups.
The NRFC’s mandate requires
that it operate on a commercially self-sufficient basis and to deliver a positive rate of return to taxpayers.
The Corporation will provide finance in the form of equity, loans, or guarantees to crowd in private investment to enable bigger firms operating in sectors where Australia has natural and competitive strengths to expand and scaleup.
These sectors that the NRFC will prioritise include renewables and low emission technologies; medical science; transport; value-add in agriculture, forestry and fisheries; value-add in resources; defence capabilities and enabling technologies.
At the end of December, the NRFC had had about 200 approaches from businesses seeking investment information.
I encourage people who want to learn more about the fund to visit the nrf.gov.au website.
In the same week, I signed off on the NRFC’s investment mandate, our new Industry Growth Program opened its doors for business for the first time.
This $392 million initiative will help startups and SMEs navigate the so-called “valley of death” – the often difficult period when a new product or process is in development and not yet capable of generating revenue.
Eligible startups and SMEs will be able to apply for grant funding ranging from $50,000 to $5 million from early this year (2024).
Besides providing matched grant funding to eligible businesses, the program will also offer specialist services for SMEs seeking investment, market testing, and networking advice.
By enabling small businesses to scale up, the IGP will grow the pool of Australian businesses able to apply for NRFC funding.
The Government accepts small businesses face challenges in taking up technology opportunities.
With this IISA report, however, I am confident we can enable greater collaboration at the SME level to accelerate the growth of diversified manufacturing in Australia.
Early leak detection
Easy hose changes
Pump thick sludge easily
No corrosion issues
Only one wearing part
Very easy servicing
Australia is being gripped by a silent crisis. It is happening in our city centres, in our suburbs and in our regions.
One by one, businesses by business, doors are being closed and companies shuttered.
Australia is in the midst of an insolvencies crisis.
It is a crisis that is hitting our manufacturers and our construction industry particularly hard.
This crisis is disproportionately affecting small and family businesses, which represent over 90% of businesses in Australia’s industry structure.
The latest data demonstrates that since the government changed hands in May 2022 there has been a surge in manufacturers and construction companies going insolvent.
According to the official Australian insolvency statistics, released by ASIC on 10 January 2024, manufacturing insolvencies
have steeply risen.
The data shows that just half way into the 2023-24 financial year, 243 manufacturing businesses have already become insolvent. Alarmingly, this number is around three times higher than the same period just two years ago.
We are seeing a tripling of insolvencies across Australian manufacturing businesses and we are yet to see any substantial response from the government.
This comes as Labor’s muchvaunted National Reconstruction Fund has failed to support a single manufacturer with a single cent almost a year after it was passed by the Parliament.
The new Labor Government has been in office for nearly two years promising to “make things here” but instead we have seen business after business go to the wall.
The dire state of the construction industry has also been revealed with
1,387 insolvencies over the six months to December 2023 compared with 565 over the same period in 2021.
More construction companies have gone insolvent in the year to date than the entire 2021-22 Financial Year (1,284). Bankruptcies in the construction industry are now roughly twice the pre-Covid level and this follows a 30 per cent rise in construction input costs (November 2023 ACIF Forecasts).
There are dire consequences to this crisis.
Supply chains can be disrupted, costs can increase for consumers, and one crisis can fuel another if we consider the impacts to the need to build more homes across the country.
We are seeing iconic business after iconic business enter voluntary administration and we are not talking about it enough. A perfect storm of rising input costs is crushing Australian manufactures and construction companies.
We need a proper economic plan that pushes productivity up and drives prices down.
Until we do, the insolvencies will continue to trend in the wrong direction and 2024 will set a new low water mark for Australian industry.
The government has announced supply commitments with Esso and Woodside to boost domestic supply of gas and make the energy system more reliable for Australian manufacturing, other businesses and households as Australia transitions to low-cost renewables.
More than 260 PJ of extra gas will be available between now and 2033 through two enforceable supply commitments under exemptions within the Gas Code of Conduct. This would be sufficient to power east coast, gas-fired power stations for around two and a half years.
This in addition to the commitments made by Senex and APLNG in November 2023 and brings the total volume of gas secured through Gas Market Code commitments to 564 PJs.
The reliability and affordability of the increasingly renewable grid needs gas to peak and firm power supply. The goal is for this code and these commitments to ensure industry and households can benefit from continued downward pressure on wholesale electricity prices brought by solar.
Madeleine King, Minister for Resources said gas is Australia’s insurance policy for the energy grid as we move to cleaner, greener renewables.
“Gas is also indispensable in the processing of critical minerals and technologies such as wind turbines and solar panels,” she said.
“Importantly, this agreement underlines the continued importance of the Bass Strait in supplying and supporting the east coast energy network.”
Minister for Climate Change and Energy Chris Bowen said gas is critical to supporting a lower-cost, more renewable grid as ageing coal exits, and to support Australian manufacturing.
“The Albanese government’s Gas Code has now delivered commitments for gas supply that’s equivalent to what is needed for powering eastcoast gas power stations for five years.
Making the announcement, the Labor government pointed out that this supply comes under the code that the LNP “disgracefully refused to support”.
“Peter Dutton and his No-alition should be ashamed for having risked these commitments and energy security for households and businesses with their lack of support for the Code in the Parliament,” said Minister Bowen.
The two new supply commitments will directly feed into southern demand centres previously
identified as being at risk of seasonal shortfalls and ensure there is sufficient domestic supply to keep downward pressure on gas prices.
Other exemption applications under the Gas Market Code are being assessed. The mandatory Gas Market Code of Conduct came into force in July 2023 and will be reviewed no later than 2025.
Australia has the potential to contribute at every stage of photovoltaic manufacturing according to a just-released ‘roadmap’ called ‘Silicon 2 Solar’, which its writers say offers a credible framework based on techno-economic analysis for each stage in the solar PV supply chain – from raw material processing to module manufacturing.
This roadmap to build a strong domestic photovoltaic manufacturing industry was developed by the Australian Photovoltaic Institute (APVI), Deloitte and a group of key industry stakeholders, with the support of the Australian Renewable Energy Agency (ARENA). Collaborating stakeholders included the Australian Centre for Advanced Photovoltaics (ACAP), AGL, Aspiradac, Energus, Siemens, SunDrive, Tindo Solar and 5B.
The map examines four key steps in the supply chain, from polysilicon production through production of ingots and wafers, followed by the manufacture of solar cells and modules. Each stage in the chain involves challenges but the roadmap shows Australia has the capacity to participate successfully in each stage.
ARENA CEO Darren Miller said ‘Silicon 2 Solar’ is a clear vision for Australia’s role as a manufacturer of cutting-edge solar technology across the supply chain, leveraging some of Australia’s competitive advantages in the sector.
“Australia has already demonstrated its capacity to manufacture advanced technology in other sectors. Solar PV represents an enormous opportunity to apply our skills to a sector that will play a critical role in Australia’s clean energy economy.
“A number of Australian companies have already stated their ambitions to develop local manufacturing of solar PV at scale, and ‘Silicon 2 Solar’ illuminates the policy and
investment pathway to make these bold plans a reality,” Miller said.
The roadmap focuses on Australia’s potential to manufacture today’s leading solar PV technology based on crystalline silicon solar cells. It also shows Australia has the potential to commercialise more novel solar technologies as they reach technical and commercial maturity.
Australia is a major contributor to world R&D of solar PV and a major market for solar PV but now has only a small domestic manufacturing capability and relies on other markets for a supply of low-cost solar PV modules.
As Australia ramps up solar PV installations from current levels of approximately 5GW per annum, it
will be critical to maintain reliable and diversified sources of supply. By contributing towards global supply chains, Australia will reduce the potential risk to its energy transformation and play a greater role in the world’s net zero ambitions.
ARENA recently released its white paper on the incredible potential of ultra-low-cost solar for Australia and the world. At the forefront of the white paper is ARENA’s 30-30-30 vision for cheap solar in Australia, which represents 30% solar module efficiency and an installed cost of 30 cents per watt by 2030.
In the eleven years since ARENA was established, the agency has shifted the renewable energy landscape in Australia. Since ARENA funded the first generation of largescale solar farms in 2016, the cost of electricity from solar farms has dropped from between AUD$140 and178/MWh to as low as AUD$50/ MWh today.
To read the roadmap and find out more, visit arena.gov.au
The $392 million Industry Growth Program to help startups and small businesses commercialise and scale up has been officially launched by the federal government, fulfilling its announcement in its May 2023 budget. Grant funding of up to $5 million for eligible companies is now open,
and businesses can apply for advice on grants by visiting www.business. gov.au.
The funding was launched against the backdrop of a report from Industry Innovation and Science Australia Board which found that SMEs wanting to scale up are confronted by many barriers.
Industry Innovation and Science Australia Chair, Andrew Stevens, said it’s hard for businesses to compete when they’re small.
“While we outperform in the creation of start-ups and small businesses against other OECD countries, our industry structure is overly skewed to small businesses with less than 20 employees.”
Julie Collins, Minister for Small Business said Australia’s small businesses are known for their ingenuity and innovation — especially “how adaptive, resilient and passionate they are”.
“The Industry Growth Program will help turbocharge this innovation. This is good for jobs, good for our economy and good for
Australia’s small businesses.”
Minister for Industry and Science Ed Husic said the Industry Growth Program will help meet the long-term challenge for the Australian economy “to scale up our businesses”, and it will potentially steer some businesses to further support from the National Reconstruction Fund.
“The Industry Growth Program is designed to commercialise great ideas and know-how, build stronger Australian businesses and put them on a pathway for potential support by the National Reconstruction Fund,” Minister Husic said.
The report advises the government to identify businesses with the impetus, ideas and risk appetite to deliver novel products and services. It also outlines steps organisations can take to commercialise research results which would help expand and diversify the economy and create well-paid jobs at the same time.
The Industry Growth Program will support project areas prioritised by the National
Reconstruction Fund and includes:
- A national advisory service: business growth and commercialisation experts to guide those looking for investment, market testing, business models, and networking.
- Matched grant funding ranging from $50,000 to $5 million for eligible startups and innovative SMEs.
“The outcome we need right now is the scaling of small businesses into medium-sized businesses,” said Stevens. “This will build sovereign capability and economic complexity in Australia.”
Businesses can apply for expert advice now by visiting www.business.gov.au
The future of Australian steelmaking is on the agenda, with the federal government spending $200 million in grants to steelmakers and projects which will help transform the energy system and keep Australian producers internationally competitive while creating jobs.
In the first round of the Powering the Regions Fund (PRF) has granted $136.8 million to BlueScope Steel in New South Wales and $63.2 million to Liberty Steel Australia in South Australia.
BlueScope will put the funds towards relining and upgrading its No. 6 Blast Furnace at the Port
Kembla Steelworks to maintain domestic production, reduce emissions, and support pathways to producing even lower-emissions steel.
Liberty’s funding will go to the purchase and commission of a low-carbon electric arc furnace (EAF) to replace its existing traditional blast furnace at the Whyalla Steelworks. The new stateof-the-art EAF will support the manufacturing of green steel and help achieve Liberty’s aim of carbon neutrality by 2030.
The Minister for Climate Change and Energy Chris Bowen said the $200 million investment in the steel sector aimed to secure its long-term future.
“Steel is essential for our energy transformation. Ninety percent of the materials that go into making a wind turbine are steel and cement, and we’re going to need a lot more of it.”
“Total steel demand for the energy transformation from 2022 to 2050 will be almost 5 billion tonnes, accounting for 75% of the total material
requirement – and that steel will increasingly be green steel.”
The Minister said the government wants to make sure products vital to Australia’s economic future, such as green steel are made here, but this will require innovation and new ways of processing iron ore that decarbonise the steel industry.
“Regions like the Illawarra and Whyalla have been industrial powerhouses for generations, making the steel used in building our houses, infrastructure and industry while creating jobs, and we want to see this continue.”
BlueScope will add about 250 workers to its site during the blast furnace upgrade and will help secure the local workforce over the long term, including the thousands of jobs at the Port Kembla Steelworks.
Liberty’s shift to green iron and steel will increase its workforce by around 24% over five years and help provide many existing employees with retraining and new skills.
Australian composites manufacturer Omni Tanker, in collaboration with international aerospace giant Lockheed Martin and the University of New South Wales (UNSW) has developed a world-leading solution for the transport of cryogenic and liquid cargoes of hydrogen and helium, including into space.
With support from the Advanced Manufacturing Growth Centre (AMGC), the collaborative partnership builds on Omni Tanker’s expansive composite capabilities developed for use across its industrial transport portfolio.
The company currently leads global manufacturing in lightweight, composite road tankers for caustic materials that are used and sold locally and exported to Europe, and North America from its Sydney base.
Pairing Omni Tanker’s capabilities with Lockheed Martin’s extensive aerospace experience led to the development and manufacture of two new tanks including a:
• Type 4, fluoropolymer-lined, carbon fibre composite tank, and a
• Type 5, liner-less, carbon fibre composite tank.
The tanks can store and transport liquid hydrogen, as well as oxygen, hydrogen peroxide, and hydrazine at high pressures under extreme cryogenic temperatures as low as -269ºC.
As a result of the successful project, operational-scale demonstrator versions of the tanks for Lockheed Martin’s LM2100 satellite have now been manufactured at Omni Tanker’s advanced manufacturing facility located in Sydney’s west.
Omni Tanker CEO and Founder Dr Daniel Rodgers said the $1.59 million project has taken the company’s world-leading capabilities to new heights.
“By leveraging Omni Tanker’s capabilities, we have been able to translate our composite road tanker technology to the global space sector – where performance, weight, and cost are of paramount importance,” said Rodgers.
“Omni Tanker can develop and deliver composite pressure vessels to meet demanding technical requirements quicker and at a lower cost than exotic materials, such as titanium, which are widely used in the space sector.”
Christopher Hess, Lockheed Martin Australia’s Head of Industrial Development said, “The global strategic environment is constantly evolving, and Lockheed Martin is committed to working with industry, through exemplary partners such as Omni Tanker, UNSW, and AMGC, to deliver a world-leading space capability.”
Dr Jens Goennemann, Managing
Director of AMGC, said the project demonstrates the importance for manufacturers to look beyond their current businesses.
“With the assistance of AMGC, Omni Tanker has done what more manufacturers should do: seek ways to leverage their capabilities across adjacent opportunities, in this case moving from road tankers to spacecraft,” said Goennemann.
“It’s generally not rocket science –except in this case it is.”
Together, the project participants identified a new application for Omni Tanker’s patented OmniBIND solution which links an interior thermoplastic tank to a lightweight composite exterior tank.
The use of a nanoengineered additive product, developed by UNSW, prevented matrix cracks usually present at extremely low temperatures in pressure vessels storing liquefied hydrogen.
“The collaborative efforts with Omni Tanker and Lockheed Martin Space have been pivotal in transforming this cutting-edge technology into practical commercial applications,” said Professor Chun Wang, UNSW’s Scientia Professor.
“As a result of extensive nano-engineering efforts, we now have composite
structures that can withstand the extreme cold of liquid hydrogen without experiencing microcracking or hydrogen gas leak,” said Professor Wang.
Dr Luke Djukic, CTO at Omni Tanker, said the project represented a significant step forward for the company and a strategic leap in sovereign capability.
“These new material technologies are well-matched to the high-end pre-impregnated composite materials typically used in aerospace yet offer a more economical production method from materials that are readily available,” said Djukic.
“In developing these new products and processes onshore, we have established significant sovereign capability at Omni Tanker. We look forward to leveraging this capability as we move our tanks into operational use across the transport and aerospace sectors here and abroad,” said Djukic.
The $1.59m co-funded project received co-investment from the Advanced Manufacturing Growth Centre to the value of $700,000, while in-kind contributions totalled $194,000.
In the rapidly evolving landscape of Australian manufacturing, 2024 presents a myriad of challenges that demand strategic solutions. Manufacturers across the nation are grappling with issues ranging from security and privacy concerns to the need for skilled professionals and navigating increased regulations. In this article, we delve into the top six issues impacting Australian manufacturers and provide insightful strategies derived from industry expertise.
As the manufacturing sector undergoes digitisation, the heightened concerns around security and privacy necessitate a proactive approach. Utilising data-driven insights allows manufacturers to make informed decisions based on real-time information. By analysing data, businesses can identify potential threats, assess vulnerabilities, and implement targeted security measures. This proactive stance ensures a robust cybersecurity strategy, safeguarding sensitive information and maintaining trust in an increasingly digital environment.
The challenge of aging capital and reliance on outdated technology requires a strategic evaluation. Trusted advisors can provide financial insights and strategic guidance to seamlessly integrate new technologies. Modernising equipment and processes enhance efficiency, reduces downtime, and opens avenues for automation. By strategically allocating resources for technology upgrades, manufacturers can future-proof their operations, stay competitive, and
ensure long-term sustainability.
With supply chain disruptions on the rise, a holistic approach is needed to optimise operational efficiency and secure funding opportunities. Conducting feasibility studies and financial modelling assists manufacturers to identify vulnerabilities in their supply chains. By understanding the financial implications of potential disruptions, businesses can develop contingency plans, diversify suppliers, and leverage technology to enhance visibility and traceability. This proactive approach ensures a resilient supply chain capable of withstanding unforeseen challenges.
Gaining access to skilled professionals is vital in an industry where expertise is indispensable. Active engagement with trusted partners can address the challenge of acquiring and retaining skilled talent, fostering long-term growth. By prioritising ongoing training and development, businesses can nurture a workforce that adapts to evolving industry demands, fostering innovation and competitiveness.
Manufacturers are grappling with increased regulations and shrinking profit margins. A strategic approach, beyond mere compliance, is essential. Through in-depth financial analysis and strategic planning, manufacturers can identify areas for operational efficiency, cost reduction, and process improvement. This
proactive stance not only ensures compliance but also positions the business for sustainable growth in a challenging regulatory landscape.
The challenges faced by Australian manufacturers in 2024 require a collaborative and strategic approach. Explore the possibilities and navigate the complexities with us.
Contact your local William Buck advisor to unlock the full potential of your manufacturing business.
William Buck williambuck.comAre you grappling with the challenges of the evolving manufacturing landscape? The William Buck Hour is a complimentary discussion to provide manufacturers with strategic planning that could reshape your future.
Following the session, our advisors will conduct an in-depth analysis of your business leveraging commercial insights, professional experience and best practice standards.
The end result? A fresh perspective and a targeted strategy, empowering you to move forward with confidence.
Your success is our priority. Let’s unlock the full potential of your manufacturing business together.
If your accounts department or company receives an invoice with an unfamiliar bank account number, then no matter how authentic the invoice looks, make a phone call to the company and talk to someone directly to verify their bank details.
That’s the advice of St.George Bank, which says it is seeing an increasing number of ‘invoice scams’ where, in some instances, eye-wateringly large amounts are being transferred to scammers.
This type of scam is the most common kind of fraud against companies, and called a business email compromise (BEC) - or a ‘payment redirection scheme’ - where cyber criminals use compromised email accounts to impersonate trusted senders and trick the target into making fraudulent payments, or give up sensitive information.
The Australian Competition and Consumer Commission (ACCC) estimates Australian businesses lose $224 million a year this way.
Industry Update spoke to Matt Kelly, Head of Manufacturing and Wholesale NSW & Regional General Manager at St.George Bank, who gave a recent example where a company was emailed an invoice for $2.5 million from a known supplier. Initially, the recipients noticed the different banking details and did try to call someone at the company to check.
The problem was, said Kelly, key people from the company were away at the time, and instead of continuing to try to talk to someone directly, the person dealing with the invoice sent an email instead.
That email went to the scammers,
who told the sender the bank details had changed.
So $2.5 million was then transferred to the scammers’ overseas bank account. Thankfully, authorities had a watch on that account and the transfer was able to be stopped, said Kelly.
But not long after that incident, St.George dealt with yet another example where a different company did exactly the same thing in the same circumstances of receiving false banking details, but without making a verification phone call –this time sending $1.5 million to a false account overseas.
Luckily, St.George was able to get all the money back for them, said Kelly, despite it already being in transit.
The potentially devastating scam is now so common that St.George is working with Eftsure, which uses B-2-B payment protection software to detect unusual bank account transactions, and alerts users to any incorrect or fraudulent bank details before the payment is made.
Eftsure says it is working to provide a solution that reviews all payment files uploaded into the St.George platform.
In 2023, Eftsure says it saw the average number of fraud attempts detected each week against businesses increase nearly three-fold, and says cybercriminals are becoming more sophisticated, infiltrating both the target organisation’s email systems and those of a supplier’s.
“We’ve seen some organisations
targeted multiple times, with various invoices totalling millions of dollars per attempt,” Mark Chazan, the CEO of Eftsure, told Industry Update
“However, that doesn’t mean that fraudsters are only targeting large payments or large organisations –Eftsure has prevented fraudulent payments ranging from the millions to only a few hundred. Everyone from small not-for-profits to massive corporations are fair game in the eyes of scammers.”
Chazan says the company prevented “directly targeted frauds” for approximately 17% of customers in 2023, and by blacklisting the fraudulent accounts and alerting other customers of the same suppliers, has indirectly stopped frauds for hundreds more customers.
Chazan says the software “uses a mix of automation and multi-factor verification to mitigate payment fraud risks. The system adds a technical layer of security and includes ‘cleaning’ an organisation’s vendor data, streamlining their vendor onboarding, ensuring changes to vendor details are correct and ultimately also verifying payments immediately before processing.”
“When a payment is about to be made and the payment details don’t match those on Eftsure’s unique database of millions of suppliers, the users are presented with easy-to-understand traffic-light-style alerts inside their online banking screen.
“This helps organisations avoid releasing funds to fraudulent or incorrect accounts thereby ensuring
payments are made to the correct payees. While Eftsure’s solution minimises risks across the entire procure-to-pay process, it also acts as a final guardrail to ensure that payments don’t go to the wrong people, even if a cyber incident has already taken place.”
Fundamentally, human error is at the core of almost all successful scams.
“An organisation’s people are its biggest vulnerability,“ says Chazan. “Regular training is critical for raising awareness and counterbalancing these weaknesses – that includes more tailored training for those with access to especially sensitive data or processes.
Or as Matt Kelly from St.George puts it, “you really have to have stringent policies with your accounting department that mean you call and verify with someone you know at the company that their bank details have changed. Don’t respond to the email address because that could be a fraudulent party.”
Disclaimer: This information is general in nature and has been prepared without taking your objectives, needs and overall financial situation into account. For this reason, you should consider the appropriateness for the information to your own circumstances and, if necessary, seek appropriate professional advice. |
© St.George Bank - A Division of Westpac Banking Corporation ABN 33 007 457 141 AFSL &Australian credit licence 233714.
In today’s fast-paced industry, going green is not just a choice – it’s a must. The latest quarterly update of Australia’s National Greenhouse Gas Inventory in March 2023 revealed that emissions were 465.9 million tonnes of carbon dioxide equivalent in the year to March 2023. Industries globally are grappling with the urgent need to curtail their carbon footprint, with many groundbreaking production
equipment solutions that promise to redefine our approach to sustainability.
Sustainability is no longer just about reducing carbon emissions; it’s a broader commitment to energy conservation. Businesses now recognise that green practices should not only help the planet but also contribute to financial health. Many companies
have set ambitious targets for carbon emission reduction, aiming to align with sustainability commitments and foster a low-carbon economy. The collective efforts seek to drive industry-wide sustainability, making a positive impact on both the environment and society.
Aligned with this commitment to sustainability and innovation, companies have proactively implemented measures to minimise their carbon footprint. The focus lies in enhancing energy efficiency, adopting renewable energy sources, and developing sustainable solutions. The provision of energy-efficient products empowers businesses to simultaneously reduce energy consumption and carbon emissions.
In the pursuit of a sustainable future, knowledge plays a pivotal role. Sophisticated tools like Atlas Copco’s Carbon Emission Calculator have emerged as game-changers, providing industries with a realtime insight into the environmental impact of their operations. These tools go beyond numbers; they serve as guides for businesses navigating
the complex world of reducing carbon emissions.
The Carbon Emissions Calculator empowers decision-makers by offering insights into carbon emissions across various industrial processes. Armed with this data, companies can pinpoint areas of inefficiency, identify opportunities for improvement, and make informed choices that align with global efforts to combat climate change.
Commitment to sustainability
Atlas Copco is committed to sustainability and innovation. The company has implemented measures to minimise its carbon footprint by enhancing energy efficiency, adopting renewable energy sources and developing sustainable solutions. Their sustainable solutions go beyond green products. Atlas Copco has set science-based targets to reduce greenhouse gas emissions in line with the goals of the Paris Agreement.
Maintains a safe area reducing the risk from cable tripping hazards and ladder falls from spring reels
Keeps the power socket in safe location at all times educing wear and tear and risk from electrocution ovides power when and where it’s needed and out of s way when not required
•
•
•
Safe, easy and secure operation for staff/operators equiring minimal training
Reliable 240v 10amp supply directly at your workspace
work area reducing the risk from cable
Removing the need for ladders with spring cable reels emoving the risk of a ladder fall
Keeps the power socket in safe location at all times educing wear and tear and risk from electrocution e operation for staff/operators equiring minimal training
Reliable 240v 10amp supply directly at your workspace
•
•
•
Maintains a safe work area reducing the risk from cable tripping hazards and the impact on personnel and the service area.
Removing the need for ladders with spring cable reels educing the risk from a ladder fall
Keeps the power socket in safe location at all times educing wear and tear and risk from electrocution
Safe, easy and secure operation for staff/operators equiring minimal training
Reliable 240v 10amp supply directly at your workspace
Safe, easy and secure operation for staff/operators equiring minimal training
rea reducing the risk from cable
Keeps the power socket in safe location at all times
Quiet and smooth operation not creating issues during ovides power when and where it’s needed and out of s way when not required
In the intricate dance of global supply chains, the COVID-19 pandemic cast a glaring spotlight on the vulnerabilities of overseas sourcing, prompting a re-evaluation of traditional practices.
In recent decades, Australian businesses have been drawn to offshore suppliers, enticed by lower costs and perceived efficiencies. However, the pandemic, plus other ongoing geopolitical tensions in Europe and the Middle East, have laid bare the risks associated with this approach.
There is a growing awareness of the untapped benefits of prioritising local Australian suppliers for critical components.
According to a 2023 report by the Capgemini Research Institute*, 71% of surveyed Australian businesses stated they were actively investing in regionalising and localising their supplier base to help insulate them against global risks.
The report also found that by
2025, procurement from offshore suppliers is expected to drop by 7%.
Australian manufacturers can be competitive preferred suppliers against overseas counterparts, but is a like-forlike part price comparison fair?
These simplistic comparisons significantly diminish the added value Aussie-base producers represent to you, and in turn, your customers.
Consider the following benefits gained from purchasing within Australia:
Greater shelter from adverse global economic events and foreign exchange movements: Australian manufacturers offer a shield against global economic uncertainties and foreign exchange fluctuations. Offshore supply chains are prone to disruptions caused by wars, natural disasters, and regional conflicts, often leading to unexpected shortages.
Major disruptions to logistics, like the 2021 and current Suez Canal
disruption, are often more easily managed when businesses source their products and components from Australian suppliers.
During the global COVID-19 pandemic, disruptions in international supply chains were widespread. Australian manufacturers, however, experienced fewer interruptions, showcasing the resilience of a localised supply chain. Additionally, currency fluctuations that occurred during this time had a lesser impact on businesses sourcing locally.
Greater certainty of quality raw inputs and ethical sourcing: Committing to sourcing raw materials locally ensures a consistent level of quality and adherence to ethical standards.
Australian producers are bound by internationally leading employment and industrial relations laws, reducing the risk of unethical practices and modern slavery. This commitment to ethical sourcing enhances the reputation of businesses and ensures that products meet the highest quality standards.
Reducing lead times for your customers: Localising the supply chain in Australia significantly reduces lead times. This allows businesses to streamline their operations by minimising inventory stock holding and warehouse overheads.
Quicker lead times contribute to efficient working capital management.
Greater responsiveness and support to product design challenges: Local suppliers in Australia offer invaluable support in navigating product design changes and improvements. Leveraging local technical expertise expedites the development process, ensuring a competitive speed to market.
This advantage is particularly crucial compared to offshore suppliers who may face challenges in effective communication and collaboration due to an over-reliance on virtual meetings. Communicating with local suppliers in Australia also reduces language barriers and the challenges of significant time zone differences.
Dealing with a supplier wellversed in the Australian market: Long-standing local suppliers in Australia possess extensive knowledge of the domestic market. This
ensures that clients are not treated as minor customers and enables businesses to avoid competition for factory space with larger multinationals relying on offshore channels.
The familiarity with local market dynamics also facilitates better alignment of products with consumer preferences and regulatory requirements.
Quicker engagement with transportation and supply chain intermediaries: Local suppliers in Australia have established strong relationships with domestic transport companies, providing businesses with flexible speed-to-market options. This proves invaluable in situations where unforeseen delays may arise, offering a distinct advantage over foreign manufacturers.
In conclusion, the feat of achieving cost efficiencies coupled with a resilient supply chain will always be an ongoing balancing act for businesses. The upfront cost advantages of offshoring can often go unrealised in the face of poor responsiveness, long lead times and inferior quality materials. There’s no shortage of Australian based manufacturers who are ready and willing to cater to those looking to adopt local sourcing and production.
Secure your supply chain with Marsh Alliance
Marsh has been Australia’s leading producer of springs and metal components for over 70 years. Marsh Alliance produces from bespoke limited-run orders through to high-volume contract manufacturing. Over 90% of the factory volume is produced from Australian made raw inputs too and we strive to maintain product lead times within a few weeks of order (for goods made from locally sourced and stocked materials). Our inhouse Quality Assurance and R&D departments work to support our clients’ technical and product development needs.
*Source: Capgemini Research Institute, “Illuminating the path: Building resilient and efficient supply chains in the consumer products and retail industry,” 2023.
Marsh Alliance marshalliance.com.au
There aren’t many manufacturing businesses as exciting to visit as timber cladding company Weathertex, just outside Newcastle.
It’s one of the rare companies where the full, end-to-end manufacturing process happens on site.
When the factory’s in full flight, trucks deliver loads of hardwood eucalyptus logs, which become piles of wood chips then fed into huge high-pressure mason guns, (the only company left in the world to use such guns). These massive ‘guns’ turn the chips into pulp, which is then washed to remove all the sugars and starch, and a small amount of wax is added to form a wet lap, not dissimilar to soggy cardboard. The wet lap is then formed into sheets, the water squeezed out and the sheets heated in presses. There, they’re imprinted with the company’s signature surface styles, and then sent through to the final stages of becoming the external timber planks and panel cladding Weathertex is known for.
It’s a marvel to watch the whole process and owner Paul Michael never tires of it.
“The process is actually 85 years old, so a factory tour is a bit like walking around a museum.”
When Michael, who has an engineering background, bought the masonite factory with a business partner in 1998, it had been manufacturing Weathertex since 1964 but was still old school. Operators used sound and vibration to determine whether equipment and the production process was working properly, and the measuring equipment was analogue, with no computers or work stations.
Michael and his engineering team set about modernising the factory floor by computerising all the processes, although the machines remain the same as they were all those decades ago. Now, almost all of the production equipment and process parameters are now monitored by a computer system and displayed on monitors in the control rooms in the plant, the main office and online.
The factory runs continuously during the week, and supervisors meet each morning to assess and discuss the constantly incoming data, displayed on monitors in the main office.
But although Michael knew he could handle the engineering side of things, he realised the company needed a different shot in the arm in terms of sales.
Weathertex had always been the little brother to the large fibre cement manufacturers in Australia, which had been aggressively marketing products and built significant market share.
After the global financial crisis hit, Michael says a strategic review determined that they needed to change “from a manufacturing organisation that happens to sell the products it makes, to a sales and marketing business that happens to make the product it sells.”
“That change is where a lot of manufacturing businesses struggle, as they’re focused on the product not necessarily on the sales and marketing,” says Matt Kelly, St.George Bank’s Head of Manufacturing and Wholesale in NSW, who has worked with Weathertex for a number of years.
Michael says he knew he didn’t have the skillset to focus on that shift, so hired the former National Sales Manager for Bunnings Trade, Jason O’Hagan, now Managing Director of Weathertex.
It was a savvy move. Since coming on board in 2012, O’Hagan and the Weathertex team have significantly increased Weathertex’s annual turnover and equally importantly, the brand recognition and trust within the Australian building industry.
He did it by changing the focus of the sales effort to target architects, designers and builders - the pointof-sale customers - rather than the distribution end of the supply chain.
“It was all about getting back to basics and creating demand for the Weathertex product.”
The company also got a makeover of its website and catalogues, with O’Hagan making sure the brand trumpeted its sustainability credentials: a 100% natural product sourced from Australian hardwood timber, the “ultimate renewable building material”.
Weathertex also changed its tagline
to “A better choice, naturally”.
“The whole sustainability trend was kicking in with architects and designers, and people in general wanted to use more sustainable building products,” O’Hagan told Industry Update
Weathertex has long boasted a sustainable pedigree, but just how sustainable they were was brought home in 2008, when Kevin Rudd proposed a Carbon Pollution Reduction Scheme that would impact manufacturers.
After the mandatory audit of their carbon footprint, Michael and his team sat down and did the calculations, and were flabbergasted to work out that they had a “better than zero” carbon footprint.
“We know that 50 percent of timber is sequestered carbon, and so it turned out for every cubic metre of Weathertex we produce, we were sequestering 34 kilograms of CO2 emissions,” said Michael.
Weathertex engaged a third party certifier Global Greentag to verify its ‘green’ credentials and in doing so was the first cladding manufacturer globally to achieve Platinum Certification for its natural range of products. Weathertex was also voted the most trusted brand in the 2016 and 2018 Architecture and Design Brand survey, beating a number of respected brands within the building industry.
In a construction market where a lot of building materials are imported, Weathertex exports 20% of the company’s products, usually to medium-to-large sized family
It’s not bad for an Australian manufacturing business that employs only 150 people and still has room to ramp up its production as sales grow.
“We’re currently at 50% of our production capacity and we’re seeing plenty of upside in volume throughout Australia and around the world,” says O’Hagan.
The company has weathered financial ups and downs, but its relationship with St.George Bank has been a crucial and flexible mainstay for two decades.
“We wouldn’t be here today if it wasn’t for St.George,” says Michael. Weathertex established an initial relationship with the bank - which specialises in manufacturing finance - in Michael’s early days, when he was
going through the difficult process of buying out his business partner, an accountant, in 2003.
The big bank Michael was with at the time told him he couldn’t get refinancing unless he had an accountant working for him. But in order to make a deal and hire another accountant, they had to have the finance there. It was a catch-22.
“They made it impossible,” relates Michael.
“St.George provided Weathertex and Paul with funding since then, including through the GFC,” says St.George’s Matt Kelly.
Weathertex’s success, says Kelly, really lies in the way the company took the brand by the horns and grew it.
“Manufacturers always underestimate the value of the brand, and that’s one of their biggest challenges because that’s probably your biggest IP for a sale. If everyone recognises the brand, then obviously the profits will follow.”
Disclaimer : This information is general in nature and has been prepared without taking your objectives, needs and overall financial situation into account. For this reason, you should consider the appropriateness for the information to your own circumstances and, if necessary, seek appropriate professional advice.
In good news for drivers, there’s now an Australian-made spray product that keeps spiders, ants, and their nests out of vehicles. Called RoadBlock, it’s marketed at professional drivers such as truckies and delivery drivers, but is basically for anyone who fears an encounter with eight-legged guests – which
can happen mid-drive, and prompt alarmed and erratic driving.
“We believe RoadBlock is the first product designed specifically to keep spiders, ants, and cobwebs from taking hold in vehicles,” said Amanda Lintott, developer of the product, which she says is a powerfully effective spider and ant deterrent.
“Australia has thousands of species of spider, and plenty of them rather fancy a nice warm place to rest and nest. Only a few – funnel webs and redbacks – can kill people, but plenty of others can give a really painful long-lasting bite if you sit on them or try to give them the flick. And they are all frightening and totally distracting when they pop out unexpectedly,”
An Australian solution to Australian pests
RoadBlock barrier treatment is formulated and manufactured in Australia to be immediately efficacious, then provide up to three months’ barrier protection to keep spiders and ants –and their nests and webs – out of vehicles, minimising potentially dangerous distractions for drivers.
The long-lasting treatment, which is compliant with the requirements of the Australian Pesticides and Veterinary Medicines Authority (APVMA), is in a different category of potency from standard sprays, but safe to use on all automotive surfaces, says Lintott.
“We developed this to be the ultimate deterrent to a very common and frightening distraction that pops up often to frighten drivers generally, and particularly truckies, tradies, service techs, delivery drivers, forklift drivers, and others operating along the logistics and warehousing chain,” said Lintott, whose background is in the car industry.
In addition to being particularly applicable to professional drivers covering big distances yearly, traversing many spider and ant habitants, RoadBlock is:
• Suitable for use on all automotive surfaces of big rigs, rigid trucks, utes, vans, cars, bikes, RVs. 4wds, forklifts and mobile machinery
• Especially helpful where vehicles are parked on the roadside overnight, or in garages and sheds already hosting a peripatetic population of ants and spiders
• Easy to apply, with a 360-degree nozzle and straw applicator for hard-to-reach spider and ant preferred habitat and onboarding points, including side mirrors, wheel arches and grilles
• APVMA compliant, safe to use on all automotive surfaces, and contains no oil to degrade paint or cabin finishes
• Designed to keep unwanted insect passengers at bay and reduce the risk of accident or injury for
motorists.
A recent online poll by Lintott’s Autonomy Co, a car product brand, found 78 per cent of drivers had experienced a spider in their car, 79 per cent had had problems with cobwebs and a scary 23 per cent had come close to having an accident after discovering a spider in their car.
“The most common stowaways are huntsman spiders, which can grow up to 15 cm wide, but others include venomous redbacks and famously hairy wolf spiders,” said Lintott.
“Spiders are attracted to the warmth of engines and can often be found in the engine bay, door frames, or on the underside of the car. They get startled by vibrations when the car gets moving. If this happens at high speed, it can be a dangerous distraction but even at low speed it’s a lot of people’s worst nightmare.”
While a single arachnid is bad enough, spiders also have a habit of nesting in cars and leaving cobwebs around side windows, windshield-wiper arms and door handles which can obstruct vision and be tricky to shift.
Meanwhile, anywhere there’s food, there are ants.
“Ants also can give terrific bites, worse than a bee sting, as anyone who has been nipped by a bull ant will tell you,” said Lintott.
“Our research shows 11 per cent of drivers have experienced ant infestations in their car. Ants are hard to get rid of and can lead to costly repairs if they manage to infest electrical systems.
“While there are many products for homes and gardens, until now there has been nothing out there for vehicles. We are enthusiastic to expand distribution of this product throughout Australia, and to investigate manufacture of the formulation overseas for major markets there as well.”
Members of the Blind Manufacturers’ Association of Australia (BMAA), from small family-operated businesses to national corporations in the window furnishings industry, will get a marketing boost now they have joined the Australian Made club.
Australian Made Chief Executive Ben Lazzaro said the partnership was a win for local manufacturers.
“We are thrilled to partner with the Blind Manufacturers Association of Australia to support Australia’s blinds, awnings, and shutters manufacturing industry.
“Our Aussie makers create products that are made to some of the highest quality and safety standards in the world.
“Whether you’re purchasing curtains, outdoor blinds, shutters or indoor blinds — asking for the Australian Made option helps invest in thousands of
Australians at all stages of the supply chain,” Lazzaro said.
From local makers to retailers, Lazzaro said the flow-on effects from consumer purchases can be huge.
According to IBIS World, Australia’s window furnishings manufacturing contributes an estimated $842 million a year to the local economy and employs almost 3,000 people.
BMAA Chairman Gilbert Da Silva said the association is dedicated to promoting and strengthening the industry.
“Our partnership with Australian Made is a significant stride in showcasing the top-quality, Australianmade window coverings and shading systems that our industry provides.
“This strategic partnership not only strengthens our advocacy for locally made products but also underscores our unwavering dedication to the growth of Australian
manufacturing.
“BMAA will proudly display the Australian Made partner logo, symbolising our shared commitment to fostering a robust and thriving manufacturing industry in Australia.”
For more information on BMAA and Australia’s window furnishings industry, visit bmaa.net.au
To find genuine Australian Made products and support local makers,
As Australia ramps up its defence spending in line with federal government reviews, Australian businesses are increasingly being courted as part of the Defence Force’s commitment to building a robust and resilient domestic defence industry.
Already, numerous local companies working separately or with Defence
By Margie SmithurstPrimes, have pivoted to provide the defence industry with critical products from vehicles to equipment, artificial intelligence and robotics, and administrative services.
Industry capability programs, resources and training are on offer, and the Advanced Strategic Capabilities Accelerator (ASCA) is looking towards a more streamlined
Australia’s defence industry policy is out of date for the strategic challenges at hand, is challenged by a lack of coordination across government and industry, and has limited flexibility for local industry to respond to major conflict, according to a report released last December.
The report, by employer association Ai Group and the Strategic and Defence Studies Centre (SDSC) at ANU, looks at the defence industry in the context of Australia’s national defence strategy and argues that local defence industry needs to be seen as a national capability in its own right and not just a capability input.
Amid concerns of looming conflict in the Indo-Pacific, the report argues an “independent but internationally linked” defence industry would be an asset that gives local industry flexibility to respond and adapt to dynamic military capability needs, and reduces reliance on overseas industry and suppliers.
“Australia’s current defence industry settings do not reflect the demands of a world where Australia needs to be prepared for major conflict in our region,” it said. “The current policy paradigm reflects a world where substantial warning time was assumed, and the threat environment was less specific.”
The report says that Australia’s Defence Strategic Review (DSR) of
acquisition of innovative and disruptive technologies.
Australian innovations (eg, Sypaq’s cardboard drone - the Corvo Precision Payload Delivery System) are playing important roles in the Ukraine conflict, and other local companies such as DroneShield, Micro-X, Minelab and SPEE3D are contributing critical technologies to Ukraine’s defence.
Sending Australian-designed technology and equipment overseas is just one purpose of the industry though. Locally manufactured or designed equipment for use by the Australian Defence Force is another.
Industry Update has invited retired Air Commodore Tim Owen, the chair of Hunter Defence, to contribute regular editorials on the defence industry’s partnerships with local manufacturing. We very much look forward to his insightsboth locally, in the Hunter region, and more broadly in terms of the defence industry nationally.
Of course, businesses working with Defence are not just located in the Hunter region, so Industry Update would like to hear from, and will be covering, other businesses around Australia in defence industry partnerships.
2023 is “largely silent” on a “critical question” of what kind of defence industry is needed to support the national defence strategy, or even what the industry’s role is.
“The approaches that Australia has adopted in defence industry policy over the past decades indicate an emphasis primarily on economic considerations rather than strategic ones. If that is to change, government will need to rethink how it can more actively shape Australia’s defence industrial base.”
The report aims to map a path to prioritise the defence industry capabilities Australia must fulfil locally, and a method for building those capabilities to scale using the broad suite of industry policy tools and greater collaboration between government and business.
Releasing the report, Ai Group Chief Executive, Innes Willox, said the major question Australia’s National Defence Strategy must answer is how to ensure Australia has the capability – in terms of infrastructure, skills and intellectual property – to supply critical defence goods in Australia.
“Both international primes and local businesses in defence and the defence supply chain are critical to achieving that ambition. We need to build joined-up supply chains, both to deliver that capability more quickly and at a larger scale,” he said.
“A key problem this report seeks to address is a lack of coordination across many layers and dimensions of government and industry. A strong recommendation to address this shortcoming is the appointment of an [defence] Industry Capability Manager. If we need coordination, then there’s got to be a defence industry Czar, and the ICM is it,” Mr Willox said.
Professor Stephan Frühling, Strategic and Defence Studies Centre, said the conflict in Ukraine has demonstrated the importance of a defence industrial base that can surge and adapt, not just to support but also to reconstitute, expand and provide new capabilities during conflict.
“Other countries have built and manage their defence industrial bases as national assets for threatening times, and so … should Australia.”
The Ai Group/ANU report draws on observations from five peer countries: Canada, France, Israel, Sweden and the United Kingdom. The case studies identify how other governments think about the role of industry in defence, and how industry capabilities are built to meet government requirements.
The report, ‘Defence Industry in National Defence: Rethinking
the future of Australian defence industry policy’, offers five recommendations for the future of defence industry policy in Australia:
1. The Australian defence industry should be considered a capability in its own right and not just an input.
2. Defence industry should be embedded within and managed as part of Australia’s broader national industry structure and policy.
3. Defence industries should be strategically prioritised, then supported to achieve scale and surge capabilities.
4. Government should utilise the full range of policy levers at its disposal to shape defence industry outcomes.
5. Government should establish a Defence Industry Capability Manager to define the capability and capacity that the government needs to develop to assist industry to meet the level of preparedness determined by the government.
Introducing retired Air Commodore Tim Owen, chair of Hunter Defence, who will contribute Defence Industry editorials for Industry Update
North of Sydney sits one of the most industrially diverse regions in Australia, where manufacturing for the mining industry, agricultural systems, rail and bus transport and high-end engineering and fabrication are all key capabilities of the area.
We are talking about the Hunter Region, focused around the largest regional city in Australia, Newcastle.
The Hunter Region is also home to Australia’s key air combat, battlespace management and missile defence systems, centred around one of the RAAF’s major operational bases, Williamtown.
This has driven the development of a sophisticated industry network in advanced aerospace, maritime manufacturing, cyber security, simulation and smart technologies.
Hunter Defence, as it is called, and chaired by retired Air Commodore Tim Owen AM, represents over 100 companies in the Hunter region competing for prime and supply chain contracts in the defence space.
It prepares them for these opportunities and helps them articulate their value proposition and capabilities to government and major defence industry players.
Owen had a long and decorated career in the RAAF, with over 30 years’ operational, staff and command experience. He commanded at every operational level within the Air Force and was the key commander for the Australian military’s Intelligence, Surveillance and Airborne/Space Reconnaissance assets in the latter part of his career. He was made a Member of the Order of Australia in 2007 for his efforts in this field.
Owen was also the head strategic planner for the INTERFET intervention in East Timor and held the position of Director General of Strategic Planning for the RAAF. He served on exchange with the US Air Force and was also posted to London as the Australian Air Force Adviser. Owen was assigned as the Deputy Commander of Australian Forces in Iraq and Afghanistan in 2008/2009.
He has a wealth of experience, and he has agreed to pen an ongoing defence bi-monthly editorial for this publication.
In his current role of the Chair of Hunter Defence, Owen set up the Hunter Defence Task Force. It is a collaborative task force focused on demonstrating the capability of established Hunter defence industry suppliers to Australian Department of Defence and primes (eg, BAE Systems, Lockheed Martin) and upskilling local small and medium enterprises (SMEs) to become ‘defence ready’.
This work involves understanding regional defence capabilities and capacities, aligning them with opportunities, encouraging SMEs to form advanced capability groups, educating the companies as to the requirements of contracting into Defence and synergising broader product offerings via closer collaboration.
The Task Force meets monthly and is made up of the key industry cooperatives in the region, plus the TAFE, University, Masters Builders Association, the NSW Government and the regional airport.
The Chair and Task Force members work to articulate to government and major world-wide defence primes the value proposition of the industrial capability of the SME base within the Hunter and surrounding regions, and run programs, funded by the federal government, to educate and prepare regional industry within the Hunter catchment to compete for defence
contracts in their own right or as subcontractors to the major primes.
This monthly work by the Task Force includes understanding what defence capabilities are generated regionally, aligning local industry capabilities and capacities with upcoming opportunities, and encouraging SMEs within the region to form advanced defence capability groupings and synergising broader product offerings by closer collaboration.
Fortunately for the region, Owen has strong links with all levels of government. For example, he meets regularly with the Minister for Defence Industry to discuss issues of defence prime/regional SME opportunities, AIC requirements and Defence legislative, project and process changes.
Additionally, Hunter Defence conducts ongoing quarterly SME/ prime defence industry forums, with presentations also conducted on an ‘as required’ basis by defence primes with respect to current project status and emerging opportunities.
Hunter Defence also participates on behalf of, and in company with, Hunter SMEs at all key national Defence Trade Exhibitions and selected international exhibitions where the manufacturing capabilities of the region have opportunities for contracts in the global supply chain.
These include Avalon, Land Forces, Indo Pacific and the recently initiated Cyber and Space conferences.
Hunter Defence has for the last 12 years conducted an annual Defence Conference and Exhibition, where regional companies have the opportunity to engage with politicians at both a federal and state level, hear from the highest levels of Department of Defence about upcoming capability requirements, discuss possible contract opportunities with the key defence primes who attend and hear from SMEs who have been successful in gaining contracts in defence. It is rated as one of the best conferences in Australia for defence industry.
When compared to other regions within Australia, Hunter Defence is the gold standard in terms of presenting manufacturing and contract opportunities to Australian industry and working closely with them to upskill to meet the demanding requirements of delivery to the Australian and international departments of defence.
We very much look forward to Owen’s insights as a key defence manufacturing contributor to Industry Update
Utilities top spot in 2021) was initially used to electrify heavy underground mining trucks, which ran on carcinogenic diesel fuel.
3ME, which is owned and partly staffed by Defence Force veterans, then turned to applying the same technology for Defence.
“While our focus in mining is very much decarbonisation and efficiency, our focus in Defence is first and foremost, the defence capability needs, providing Defence with a ‘capability enhancement’ such as silent watch, export power distribution, improved vehicle performance and logistics simplification, and the added benefit is obviously the efficiency and decarbonisation of those assets,” 3ME Technology CEO Justin Bain told Industry Update
“We’ve been able to support Defence both through electrification / hybridisation of vehicles like the Bushmaster, but also a range of mobile power and energy requirements. There’s growing power and energy demand in Defence for edge communication systems, electronic warfare systems, robotic systems and directed energy systems.”
The company is understood to be the only one in Australia so far to have delivered medium-to-large electric armoured vehicles and integrated high kW lithium-ion mobile energy solutions to the Australian Defence Force and industry partners.
The benefits of having a hybrid Bushmaster, dubbed the Stealthmaster, which can refuel in the traditional way if needed,
are manifold, explained Bain, who served in Afghanistan operating Bushmasters and has dealt firsthand with power and energy challenges on the battlefield.
When electrified, the Stealthmaster has better torque, faster acceleration (like a big,
(US, UK) with the intent to align common vehicle and battery architectures for electrification and hybridisation”.
The additional power and energy on board from the batteries means the vehicle can run as a mobile field hospital or command post for several days. A recent trial in Brisbane
armoured Tesla), and a better ability to move around less detectable by traditional heat and acoustic sensors. With the hybrid capability, the system can be re-charged (electricity) or re-fuelled (diesel) and enables more efficient driving and superior range.
Larger land and maritime vehicles will need to be hybrid, he says, so they can meet operational range requirements, have the option to both charge or refuel whilst taking advantage of the simplified and more efficient drivetrain.
“That’s also the approach that’s being taken by our allies in the US Dept of Defense and the UK’s Ministry of Defense. We are progressing collaboration with our close allies
combined with lithium-ion batteries and carrying explosives, so safety has been our top priority. We’re pleased to continue collaboration with Australian Defence Science Technology (DST) and EV Fire Safe in this area.”
Export expansion plans
The fact that a quarter of its staff are veterans has meant a commercial advantage in translating Defence’s requirements quickly, says Bain.
“We have operational understanding that we combine with our technical expertise to support rapid prototyping, development and delivery. We don’t stop there as we understand the importance of through-life support to Defence assets and routinely have our staff on Defence bases supporting trials and training.”
Demand for 3ME’s dual-use technologies and proven capabilities with heavy-industry hybrid vehicles has attracted international attention, and the company’s now looking at increasing its exports and establishing operations in North America (and is pleased to be a part of Investment NSW’s ‘Going Global’ Export Program.
“As we know, the mining industry can be boom and bust and defence programs can change and be cancelled, so it’s certainly advantageous when a company has a diversified, resilient offering in mutually beneficial markets.
“We are a good example of an Australian SME getting global demand pull,” says Bain.
Hunter region advantages
Being based in the Hunter region, with its mining and energy innovation history, has been a big advantage, says Bain.
found the vehicle had enough power to run medical equipment for eight days without a generator.
Also, says Bain, electric vehicle systems have a lot fewer moving parts and components, “so the supply chain is simplified, which is great for logistics and survivability.”
The safety of the battery system is a key focus.
The company has focused on inherently safe lithium-ion systems meaning they won’t catch fire (thermal run-away), and have been designed to meet stringent international safety standards (IEC Ex) for deploying equipment in areas where an increased risk of fire or explosion exists.
“You’ve got soldiers in vehicles
There are also plenty of universities and TAFEs to draw skilled students from, and local like-minded companies to collaborate with – assisted by the strong presence of two local manufacturing associations, Hunternet and its sister entity Hunter Defence.
But there are other bonuses, says Bain.
“More importantly, it’s an awesome lifestyle in Newcastle – it’s got great beaches and it’s a great place to live, and we’ve been able to attract great talent into the business.”
Eleven Australian manufacturing and training companies have signed up to provide a drone prototype as part of an Australian government initiative which supports capabilities for the Australian Defence Force.
Contracts worth $1.2 million have been signed for the prototype of an ‘unscrewed aerial system’ (UAS) drone to be demonstrated in April. The contractors will also give detailed plans as to how they can quickly deliver the drones at scale for use by the ADF.
The initiative is part of the ADF’s Sovereign UAS Challenge which is run by the Advanced Strategic Capabilities Accelerator (ASCA).
“ASCA’s first Innovation Incubation Challenge will support some of our brightest minds in developing sovereign drone technology that can advance the future capabilities of the ADF,” said Minister for Defence
Industry, Pat Conroy.
Australian agencies including Defence use small UASs for training, photography. survey and surveillance tasks. Compared with bigger surveillance equipment, small UASs are versatile, cost-effective platforms that provide almost realtime situational awareness at lower altitudes than larger surveillance alternatives, in an expendable and general-purpose frame.
Contractors include AMSL Aero, Autonomous Technology, Bask Aerospace, Boresight, Crystalaid Manufacture, DefendTex Military Products, Edinburgh Drone Company, Geodrones Australia, Ichor Autonomy, SYPAQ Systems and V-TOL Aerospace.
ASCA was established In May 2023 as part of the government’s election commitment to foster innovation that creates capabilities for the Australian Defence Force.
Minister for Defence Industry
Pat Conroy says there are plans for Australian-made steel to be used in constructing Australia’s nuclear-powered submarines at Osborne Naval Shipyard, South Australia.
Australian steel manufacturer
Bisalloy Steels and the Australian Submarine Agency have signed a contract for the qualification of Australian steel for use on Australia’s future SSN-AUKUS submarines. Based in Unanderra, NSW, Bisalloy Steels will perform the advanced heat treatment process on the raw plate steel to produce high-grade, submarine-pressure, hull steel that meets or exceeds both UK and US standards. The raw plate steel will be supplied by BlueScope, based in Port Kembla, NSW.
The qualification of the steel to both the UK and US standards will increase the resilience of the AUKUS trilateral supply chain. All elements of the construction of the SSN-AUKUS subs will be subject to a comprehensive qualification process involving more than 4,500 tests, slated for completion in the first half of 2025.
Minister Pat Conroy MP said the
Minister Conroy said investments in developing small, smart UASs will not only advance a sovereign drone industry and create highly skilled jobs but will increase the operational effectiveness of Australia’s military.
“This initiative is another
qualification of Australian steel is a vital step in the government’s strategy for acquiring the AUKUS submarines.
“The strength and quality of Australian steel will keep Australian submariners safe in the SSN-AUKUS nuclear-powered submarines for decades to come, just as it does today on our Collins Class submarines.
“Crucially, this contract will support jobs in an industry which is not only of strategic importance but also a source of innovation and employment, and part of the Australian fabric.”
The Defence Industry Department stresses its commitment to supporting Australian industry in the AUKUS trilateral supply chain and sees Australian products at the forefront of submarine construction in the $15 million contract.
As well as being used for qualification purposes, the steel produced under this contract will be used to develop the welding procedures, and used in early production demonstration activities before Australia’s first SSN-AUKUS submarines are built later this decade.
example of how the Albanese Government is getting on with the job of providing the ADF with stateof-the-art technology while supporting the local defence industry, including small and medium sized enterprises,” he said.
Defence’s largest operational air base, the RAAF Base at Amberley in Queensland, is to get a critical infrastructure upgrade with $4 million invested by the Australian government.
RAAF Base Amberley is home to the Royal Australian Air Force’s F/A-18F Super Hornet and EA-18G Growler fleets.
The investment will support the RAAF’s Super Hornet and Growler fleets by upgrading Amberley’s external fuel tank workshop, communications support works, and electrical repairs and maintenance works.
These projects will support fuel quality testing for the Hornet and Growler fleets, as well as upgrade electrical infrastructure and deliver base infrastructure in support of deployable ICT communications equipment.
The upgrade will support the
country’s critical capabilities for keeping Australians safe by ensuring the Australian Defence Force has facilities that are fit for purpose.
Works have already begun and will create opportunities for local trades, construction and other businesses, and this will include participation by Indigenous companies.
Assistant Minister for Defence, the Hon. Matt Thistlethwaite MP, said the Albanese Government recognises our Defence sites must be equipped to meet current and future operational and capability requirements.
“These projects, to be delivered by local businesses, will create opportunities in the trades and construction industries and deliver over 100 jobs.
“The government will continue to invest in foundational estate and infrastructure, which is critical to the capacity of our Defence Force.”
“Wars have been won or lost primarily because of logistics,” said Dwight Eisenhower. The world is rapidly changing fuelled by supply chain challenges and rising costs, forcing nations to find new ways of manufacturing components. The Defence industry is constantly challenged to be ahead of the curve when it comes to protecting the front line.
US company Markforged is working with Australia’s defence industry to add 3D printing technologies to the force’s ships and bases, allowing spare parts to be printed on demand on land and at sea.
Markforged already has additive manufacturing equipment aboard nine US Navy surface ships, including three US aircraft carriers and four submarines, as part of US Navy Command’s NAVSEA plan to
transform digital capacity.
In July 2022, a Markforged X7 3D carbon-fibre printer was installed on a Virginia class nuclear-powered submarine, the USS New Hampshire, and has been performing well.
Sailors use the 3D printing technology with the Markforged Digital Forge software platform, to quickly manufacture components and perform maintenance and repair, without the need for extensive training or equipment.
The US Army’s Markforged composite printers have been used for personal protective equipment, window wiper brackets for military vehicles, tools, and low volume production parts. For example, a regiment saved $375,000 AUD by 3D printing a no-longer-available hatch plug that sits on top of a vehicle in
the intelligence community, Secure Bits founder Nick Owen has said that Markforged has helped them reach more customers, more broadly.
“We’re used to everything being word of mouth and people coming to us because we’re the only ones that do it. Markforged has been essential in that lead generation and helping industry find us.”
Since launching the FX20 in Australia, Markforged has seen Australian manufacturers adopt its technology into their existing workflows on shop floors. Six months after launching the FX20, Markforged shipped and established a two-digit network of FX20s in Australia and New Zealand.
low light scenarios allowing the driver to see at night.
Australian defence force and industry
Additive manufacturing is growing as a feasible Australian defence technology, with adoption and testing happening in deployable and strategic circumstances.
The technology’s ability for self-reliance and mobile on-demand and sophisticated manufacturing are a key advantage.
Last year, Markforged launched its largest and most capable composite 3D printer, the FX20, in Australia, with its Continuous Fibre Reinforcement printing process designed for high-strength end-use parts in aerospace and defence.
Sydney’s Garden Island Naval base now has both composite and metal Markforged printers.
In terms of supplying to Australia’s aerospace industry, Markforged is working towards getting CASA quality-standard approval of its parts-printing process.
Markforged also works with local businesses, such as veteran-owned Secure Bits, which provides defence with critical infrastructure for data centres, as well as composites, metals and rapid prototyping; and defence contractor, XTEK, which supplies defence products such as drones, and develops its own composite armour.
While the company is primarily oriented to Defence, government and
In addition to producing customised parts and components, additive manufacturing is also being used to produce tooling and fixtures for existing manufacturing processes. Traditionally, producing tooling and fixtures can be a lengthy and costly process, requiring specialised skills and equipment.
With 3D printing, however, manufacturers can produce these items quickly and easily using CAD software and a 3D printer. This has led to improved efficiency and reduced costs in many manufacturing processes.
Markforged has more than 10,000 connected printers globally. All these systems, including both composites and metal solutions, are connected through the company’s Digital Forge, the company’s digital manufacturing workflow composed of software, printers, and materials working seamlessly on a unified platform.
Markforged markforged.com
The federal government will spend $400 million to continue developing, in cooperation with Boeing Defence Australia, the MQ-28A Ghost Bat — the first combat aircraft to be designed, engineered and manufactured in Australia in more than 50 years.
The Minister for Defence Industry Pat Conroy said the funding will develop the unique Australian technology that allows the Ghost Bats, which are collaborative combat aircraft (CAA), to work together with each other and with crewed aircraft as one team to achieve their mission.
“Designed to act as a loyal wingman, we’ll be able to protect and support our military assets and pilots and undertake a wide range of activities across huge distances, and importantly, in contested environments, including performing combat roles, including performing combat roles.”
Minister Conroy said the Ghost Bats could potentially support aircraft such as the Super Hornet, the
Wedgetail, the F-35 and P-8 Poseidon.
“This technology has the potential to turn a single fighter jet into a fighting team, a single fighter into a fighting team, with advanced sensors that are like hundreds of eyes in the sky. Ghost Bats and other drones of the future that the Air Force is working on right now will function like smart phones, to be upgraded often with new and advanced features.”
“This project demonstrates that, with appropriate support from government, Australia’s defence industry can continue to be a world leader and a key source of jobs.
The continuation of the program also secures over 350 jobs across Australia and will ensure ongoing work for hundreds of suppliers, supporting the local defence industry and other employers.
More than 70 per cent of the MQ-28A Ghost Bat delivery program is being directed towards Australian industry content, delivering substantial benefits to local companies and highly skilled workforces.
“More than 200 Australian companies have already contributed to the MQ-28A program, including more than 50 small and medium enterprises within the supply chain,” said Minister Conroy.
The funding decision follows a Defence Strategic Review recommendation that options be
developed for collaboration and technology sharing with the US, and Defence signed a CCA development project arrangement with the United States in March last year. Minister Conroy said Australia’s agreement with the United States promises to share this technology and turbo-charge its development.
Lockheed Martin Australia and the Defence Department have signed a $37.4m contract to start the first local manufacturing of Guided Multiple Launch Rocket System (GMLRS) missiles from 2025.
The government says the contract will enable an initial small batch of GMLRS missiles to be manufactured in Australia, an important first step towards establishing domestic missile manufacturing on a larger scale.
According to the government, it will also facilitate the transfer of technical data from the US, establish processes for engineering certification, and begin to build the technical skills of an Australian workforce.
“This work is a clear demonstration of the ongoing collaboration between Australia and the United States on Australia’s Guided Weapons and Explosive Ordnance Enterprise – a key outcome of the Australia-United States Ministerial Consultations in July 2023,” said Acting Minister for Defence and Minister for Defence Industry, Pat Conroy.
Under the contract, Lockheed Martin Australia will begin
preparation for a state-of-the-art guided weapons production capability at the Defence Establishment Orchard Hills in western Sydney.
“We are excited about this strategic endeavour to bring advanced factory technology to Australia,” said Tim Cahill, Executive Vice President Missiles and Fire Control, Lockheed Martin.
“Lockheed Martin will transfer the technology and service delivery
as is in many of our US advanced weapon factories – accelerating the development of manufacturing capability in Australia for Lockheed Martin weapons,” said Cahill.
The objective of the Guided Weapons Production Capability (GWPC) Risk Reduction Activity contract is to have Australian involvement in the manufacture of GMLRS, All Up Rounds (AURs) and Launch Pod Containers (LPCs).
“The GWPC Risk Reduction Activity contract will provide a mechanism for swift knowledge and technology transfer and serve as a risk mitigator and pathfinder to future manufacture in Australia of the Lockheed Martin suite of guided weapons.”
In readiness for making the missiles in Australia, a team of Lockheed Martin Australia engineers will be sent to the US for specialised training at Lockheed Martin’s guided weapons production facilities.
“This partnership exemplifies our enduring commitment to innovation, growth and creating a strategically important capability,” said Ken Kota, Vice President, ADSCO, Lockheed Martin.
“Our team looks forward to ongoing collaboration with the Australian Defence Force and defence industry to accelerate the development of advanced guided weapon manufacturing capabilities in Australia”.
Previously known as AUSPACK, APPEX 2024 is Australia’s largest processing & packaging event and will run from March 12-15 2024 at the Melbourne Convention and Exhibition Centre.
Run for the industry, by the industry, APPEX is one of the most important events of the year for the processing & packaging industry according to Event Director Jon Perry.
“APPEX is relevant for any business that has a requirement to pack and wrap products including businesses from pharmaceutical, cosmetics and beauty, non-food and household goods, e-commerce businesses, retailers and logistics and warehousing businesses,” Perry said.
Taking over the entire 20 bays of the MCEC, APPEX 2024 focus is on sustainability, efficiency and automation for Australian manufacturers.
Perry believes APPEX will be the largest-ever showcase of equipment, technology and innovation in machinery, ancillary equipment, automation,
materials and packaging, logistics, robotics, food processing and industry services.
“For manufacturers looking to boost their production lines through new machinery, automation and technology, APPEX is the place to be.” Perry stated.
The APPEX exhibition is divided into four easy-to-navigate zones.
These zones include IT & Services, Materials & Packaging, Packaging Machinery and Packaging & Processing Machinery.
The 2024 Event Program is jampacked with live seminar sessions, demonstrations, and networking events throughout the four-day event.
With each day comes a different agenda including: the Food Industry Solution Series, Meat Industry Day, Women in Processing & Packaging event, ’ecoporium’ by Ball & Doggett Live Experience, the Matthews’ Retailer Engagement Hub, Result Group’s Sustainability Corner and much more.
Held on Wednesday, March 13
during APPEX, Meat Industry Day is an initiative led by the Australian Meat Processor Corporation (AMPC) partnering with the Australian Meat Industry Council (AMIC) and Meat & Livestock Australia (MLA).
Meat Industry Day promises a curated blend of educational content, a showcase of cutting-edge processing and packaging technology, and the latest industry developments. It provides a unique opportunity for both sectors to forge connections, foster development, and engage in business activities including an exclusive networking event.
The APPEX Women in Processing & Packaging event will be led by Louise Weine, CEO of NAWO. Weine will present on ‘Achieving gender balance in Packaging and Processing: Systemic Change that Works’, followed by an indepth panel discussion with four key female leaders. Ticket proceeds will go to the Good Friday Appeal.
Visitors can expect to find a series
of daily educational and insightful sessions at the APPEX Seminar Theatre. Sessions include the Food Industry Solution Series hosted and curated by Barry McGookin, Robotics Australia - exploring the role and future of robotics in processing and packaging for manufacturers - and the International Packaging Press Organisation (IPPO).
The Food Industry Solution Series will run on Day 1; Tuesday, March 12 and Day 3; Thursday, March 14 of APPEX and is designed to showcase what’s available to manufacturers interested in bringing innovation into their businesses to improve their competitiveness in the market.
Day 1 sessions will cover Sustainable Energy, Sustainable Packaging, Inventory Management, and Global Packaging Trends. Followed by Day 3, which will include Sensors for improved efficiency, Digital packaging, AI and food manufacturing and Robotics.
The Seminar Theatre will also host an afternoon of sessions with the International Packaging Press Organisation (IPPO) which has partnered with APPMA to add a global perspective the IPPO Forum will present ‘Packaging Perspectives: Global Trends Driving Change’.
APPEX 2024 stands out as a must-attend event for all businesses across packaging, processing, and manufacturing. More than just an expo, it represents the future of the processing and packaging sector. Notably, APPEX will move to a threeyear rotation, with its next return to Melbourne scheduled for 2027.
APPEX is free to attend, and registration is essential.
Owned and presented by APPMA.
Incorporating AUSPACK.
Beckhoff Automation, one of Australia’s leading PC-based control specialists, will use APPEX 2024 as a platform to highlight its Vision range. The aim of Beckhoff Vision is to bring vision and automation technology together through system integration for all environments.
With Beckhoff Vision, real-time image processing can be easily integrated and synchronised with all machine and plant processes. In addition, Beckhoff Vision components deliver a robust and attractive design, scalability and long-term availability.
“It’s really exciting that we have the opportunity to showcase physical hardware at this year’s show. The range consists of cameras, optics, illuminations, complete units, software and accessories - not forgetting training and support which form part-and-parcel,” said Nick Psahoulias, Managing Director for Beckhoff Australia.
The complete Vision system is applicable for industrial use and offers a host of benefits, including:
• Synchronising with all control processes.
• Consistent interaction with all other components.
• Implementation of standard automation applications.
• Illumination integrated units can be integrated or sold separately.
Perhaps one of the biggest benefits of them all is the cost savings.
“By directly integrating Vision project planning into your environment, you can reduce engineering and hardware costs while enjoying easy system integration and commissioning,” says Psahoulias.
Vision hardware unpacked
Cameras: “In a nutshell, these IP65/67 area scan cameras use colour and monochrome CMOS sensors with up to 24 megapixel resolution to generate high-quality image materials for industrial image processing.”
A wide portfolio of established Sony sensors with 3.45 µm and 2.74 µm pixel pitch is available for different vision tasks and image analysis functions. With their high frame rates and rapid 2.5 Gbit/s image data transmission, these industrial cameras are ideal for automated visual inspection tasks and precise product tracking in EtherCAT-synchronised applications.
Optics: “These robust industrial-grade lenses offer a host of benefits.”
The high-resolution lenses found in the VOS2000 and VOS3000 series
can be used universally thanks to the C-mount connection thread. They are ideal for use in harsh industrial environments thanks to their robust and easy-to-mount design.
In addition to being easy to adjust, the focus and fixed aperture can be easily and precisely locked using compact screws. Similarly, both lens series feature a broadband anti-reflection coating for the visible spectrum (VIS) and near infrared region (NIR) from 420 nm to 1050 nm, which is perfectly adapted to the multicolour LED illumination.
Illumination: “Illumination supports EtherCAT-based applications,” says Psahoulias.
The multicolour LED illumination in three designs – area, ring, and bar light – produces constant illumination conditions for consistently high-quality images. This provides an indispensable basis for precise evaluations when processing images. The illumination creates the best possible contrast between the inspection feature and its surroundings – even in spectrally adjustable pulse mode.
Vision Unit Illuminated (VUI): Says Psahoulias: “This is a compact unit that consists of a camera, illumination and focusable optics, complete with liquid lens technology.”
It significantly reduces installation and commissioning labour and, thanks to focus adjustment during runtime, it is particularly well-suited for work with changing component heights, as is common in logistics applications. What’s more, all functional components are
encased in elegant IP65/67 anodised aluminium housing.
Accessories: “We support the range with pre-assembled cables and vision-specific accessories,” he explains.
When it comes to pre-assembled cables, Beckhoff combines power supply, signal and data communication in one connector. Hybrid cables are also available in application specific sizes, and performance classes.
Vision-specific accessories include products for mounting the hardware and accessories for extended use of the optical components.
TwinCAT Vision: “This is software for industrial machine vision,” explains Psahoulias.
TwinCAT Vision is an integrated image processing solution. This addition underscores the increasing importance of image processing as a quality factor across mechanical engineering, particularly in applications like Industry 4.0, quality optimisation and track-and-trace.
“We are so excited about showcasing TwinCAT Vision, amongst various other stand-out offerings to visitors at the expo. This will be our first time showcasing and we are excited to engage with members of industry.”
Visit Beckhoff Automation at APPEX (stand D025) from 12 to 15 March 2024.
Beckhoff beckhoff.com
Before buying a new air compressor, take the time to fully analyse current and future application needs. ‘One type or size fits all’ definitely does not apply when choosing a compressor to meet the exacting demands of any application.
Most compressor suppliers can assess and recommend a compressor and system to match business needs.
In workshops and smaller, specialised applications, the ‘piston type’ reciprocating clunker can be replaced with smooth and quiet orbital or rotary-screw models that are far more energy-efficient and available in a wide range of kilowatt capacities. These tank-mounted, integrated compressed air delivery systems offer far more control and far less maintenance requirements than outdated piston compressors.
Even at this lower end of air demand, it’s advisable to assess the functionality and output required by an application. The right choice will ensure a compressor fully caters to immediate needs and well into the future while minimising energy bills.
In industrial applications, the choice of compressor, system configuration and in-line components is even more critical as demand levels are far more diversified.
With the capital cost of the equipment and increasing energy costs of running the compressor, matching the equipment to application needs can save thousands of dollars and engender a short-term payback period based on pre-calculated savings.
Major compressor supply
companies with vast experience around the world in a wide variety of specialised applications, such as Kaishan Compressors Australia, can conduct detailed assessments of type, size and system configuration to provide detailed recommendations for replacement or new installations.
Rotary screw, single or two-stage, permanent magnet motors, fixed or variable speed control, oil free, high pressure, low pressure, sealed cabinet, corrosion resistance, mobile, receiver type and capacity, filter types, aftercoolers, air dryers, reticulation system and configuration etc; it’s a lot to take in and specify to create the ideal solution for any application. So call in the experts to ensure the right choices create a compressed air system perfectly matched to your current and projected needs and a system that uses the best technology to ensure cost-saving, energy-efficiency for the life of the compressor.
1. Rotary-screw compressors
A direct drive, energy efficient range of rotary-screw compressors for multiple industrial applications offering variable speed drive, from 18.5 to 400kW.
2. Two-stage rotary-screw compressors
All the benefits of single stage with significantly higher efficiency gains and energy saving performance. With added variable speed drive,
these compressors can return more than 50% savings over conventional machines and 37 to 400kW.
3. Permanent-magnet, variable-frequency compressors
Systemic optimisation of the airend with advanced permanent-magnet drive motor and integrated variable speed drive technology provides greater air output for far less energy input and 15 to 250kW.
4. Oil-free (air-cooled) rotary-screw compressors
Zero-class, oil-free compressors are used where air quality is paramount for quality control and production processes. Typical applications include food processing and packaging, medical and scientific applications. They offer totally integrated function control at 90-200kW.
5. Low-pressure, rotary-screw compressors
These three-bar, low-pressure compressors are designed for textile, cement, flue gas, desulfurisation and pneumatic conveyance and similar applications. They deliver high-efficiency performance with low energy costs at 55-250kW.
6. Compact, tank-mounted, plug-in compressors
Superseding old piston-type, reciprocating technology, these fully integrated compressed air systems use advanced rotary-screw or scroll orbital technology to deliver quiet, efficient operation for modern
workshops and specialised applications and 4.5-15kW.
7. Custom-designed and built
Highly specialised applications require suppliers such as Kaishan Compressors Australia to provide custom-designed adaptions or project-specific compressors to meet the needs of harsh environments and critical processes such as marine and mining operations.
System design and installation
No matter which compressor type meets needs, the design and configuration of the delivery system is critical to efficiency and running costs. From the compressor’s location in a plant to the reticulation system and in-line components including receivers, filters, dryers, separators and coolers etc, Kaishan’s global experience, products and know-how can greatly assist from application assessment stage to full system design and installation.
Continued compressor efficiency
Regular checks and servicing of the compressor and system will ensure maximum operating efficiency, minimal downtime and long product life.
Kaishan deploys a fleet of trained and experienced compressed air technicians to maintain Kaishan and all other makes and models of compressors all around Australia.
Kaishan
kaishan.com.au
Wireless industrial networking technologies and their associated benefits have been embraced by manufacturers as they modernise, simplify and smarten up factories.
Newer communication protocols and technologies such as EtherNet/IP™, RFID and Bluetooth are making their presence known on the factory floor.
In the past, trailing communications cables proved problematic for two reasons. Firstly, cables were often damaged or disconnected during operations and, secondly, this led to more maintenance costs and higher operating expenditure. So wireless technologies became an attractive alternative.
Unpacking the EXW1 SMC Corporation recently launched the EXW1 Compact Type series, a compact and lightweight wireless communication module for use on a robot or moving fixture.
“APPEX 2024 is the ideal platform to showcase the latest edition to our wireless portfolio,” comments Jozef Ceh, Group Manager, ANZ,
Integrated Solutions.
“This comes as the first new addition since the EX600-W wireless, which has enjoyed resounding success in the local market.”
Pointing to the key differences between the EX600-W and the EXW1, Ceh notes that the EX600-W is modular, while the EXW1 is a Compact-type Wireless System.
“Advances in wireless technologies by SMC means that the EXW1 now offers around 86% volume reduction and 87% weight reduction.”
The IP67 rated EXW1 series makes use of 2.4 GHz ISM frequency band and offers frequency hopping every 2 milliseconds. It supports a faster wireless communication of up to 1 Mbps and an external antenna allows for easy installation within metal-shielded locations and locations with an obstructed line of sight.
“Introducing wireless communications eliminates the high costs associated with traditional network infrastructure and the cumbersome commissioning process. Other than the immediate efficiencies gained through the physical layer,
cables and is easy to integrate into existing setups.”
The base unit is connected to a standard industrial Ethernet connection such as Ethernet/IP™ or PROFINET®. The base can wirelessly communicate and control up to 127 remote units in a range of up to 10 meters.
“The EX600-W is frequently found in an array of applications and sectors – from food and beverage to packaging, and more.”
the functional upside is a wireless ecosystem that is futureproof, easy to expand and no additional IP addresses are required,” says Ceh.
“The EXW1 Wireless Base Module is compatible with CC-Link and EtherCAT® protocols and the EtherNET IP Wireless Base is not far from release. The series offers a reach of 100 meters (when used with a remote unit) and is also compatible with the EX600-W.”
Ceh does believe that while the additional upgrades to the new EXW1 Compact Modules are welcome, the brand-new Remote Wireless IO-LINK Master Remote module will redefine connectivity.
“It integrates all the standard features and benefits of IO-Link into a wireless network, while offering both Class A and Class B port specification — making this product a game changer.”
The EX600-W still holds its place in the range.
“The EX600-W can manage up to 1280 outputs and 1280 inputs. This decentralised wireless fieldbus system bypasses the need for network
AMS the cherry on top
SMC’s new-generation Air Management System (AMS) is the perfect accompaniment to a wireless fieldbus system.
“This series monitors when production stops and automatically decreases the pressure — reducing power consumption. It’s compatible with our wireless fieldbus systems and comes standard with one IO-Link master port on all AMS modules.”
Ceh says that in today’s modern manufacturing era, incorporating wireless technologies just makes sense.
“Wireless offers a simple and elegant solution. Where possible, look to replace legacy systems with wireless alternatives to save you on time and costs in the long run.”
The EXW1 will be showcased at APPEX 2024 from 12 to 15 March at SMC’s stand E121
Space is valuable and time costs money - so if you can maximise your storage facilities and speed up handling procedures you’ll reap multiple benefits. Leading packaging suppliers around the world are doing just this thanks to the narrow aisle and versatile capabilities of the Aisle Master range of articulated forklift trucks.
Manufactured by the Irish specialist Combilift, the Aisle Master VNA range was designed to replace a combination of other forklifts, such as counterbalance and reach trucks, that have traditionally been found in many warehousing operations.
Some drawbacks of this traditional system include the amount of space needed by reach trucks to work within aisles of racking. As counterbalance trucks are best for outside operations such as offloading, switching from one type of truck to another results in double handling, which is time-consuming, not overly efficient and which carries the risk of product damage.
With the universal one truck
solution that is the Aisle Master, loads can be taken directly from the yard to indoor storage facilities and this “truck to rack” capability vastly increases productivity. Unlike other classic VNA trucks, Aisle Masters do not need super flat floors to work on, and thanks to large rubber tyres they are at home on semi-rough or less than perfect terrain.
With the ability to operate in working aisle widths of just 1.6m, Aisle Masters can increase storage capacity in the existing warehouse by 50% compared with counterbalance or reach truck operation. In times of growth for example, optimising racking layouts according to the trucks’ abilities can avoid the need to extend current premises or relocate – both of which are costly, disruptive and involve a great deal of bureaucracy. “Improving and not moving” is also a much more sustainable course of action and accords with many companies’ wish to reduce their carbon footprint.
Aisle Masters are available with various power options and with lift
capacities of up to 3t. The impressive lift height of up to 15m also enables every centimetre of vertical space to be used for optimum pallet density in the warehouse.
UN1F1ED2 Global Packaging Group, with headquarters in Massachusetts, has a number of subsidiaries in Europe including a site in Ireland. Its four Aisle Masters have ensured maximum storage density, with 3,000 pallet spaces now accommodated in a relatively small warehousing area in its premises. The trucks move easily within the 1900mm aisle-widths and the very limited turning space at the end of the aisles. A further by-product is improved productivity and faster operations.
Warehouse and Logistics Manager Tomas Bernotas: “We have been able to reduce the number of forklifts thanks to the trucks’ ability to pick from racking and load directly to HGVs in the yard, speeding operations across the twelve hour shifts that the trucks put in. Inside, their
manoeuvrability enables them to move easily around the machinery in the production areas to take semi-finished or finished products to and from the storage bays.”
Combilift’s Aisle Master models will be at APPEX 2024 at stand A172.
Combilift
Packserv has always championed the cause of Australian manufacturing and is a strong advocate for buying local and supporting Australian food growers and producers.
Throughout the past year, as we all navigated demanding economic conditions, Packserv has been hard at work, developing a new range of machinery.
The first machine off the line in their new range is a new high-speed filler which is set to be unveiled at APPEX this year.
Designed and manufactured locally in Australia using high quality stainless-steel and aluminium, this new machine is constructed from the latest cylinder actuators from SMC Technology, the first time they’ve been used in this type of application.
In a departure from conventional designs, Packserv moved away from compressed air and also from the standard single stream of container movement in the development of this equipment.
The new machine is completely electronically controlled and
features twin-lane indexing. The twin-lane system allows alternating filling of containers in various sizes with nozzles seamlessly shifting between lanes. This innovative design, which is adaptable to its environment, not only doubles production, but also minimises downtime and enhances efficiency.
Packserv recognised that to build the machine they had in mind, they would need to develop a state-of-the-art operating system and the University of Technology Sydney (UTS) was an ideal partner to assist in developing this innovative system. Onboard technology provides real-time accessibility for remote diagnostics, technical support, servicing, and preventative maintenance. Additionally, the machine boasts a closed-loop cleaning system which saves valuable operator time and cuts down on product changeovers.
“Now, more than ever local FMCG manufacturers and packers need
to be at the forefront of innovation and as efficient as possible to keep up with the demands of Australian consumers to be competitive with imported products from overseas,” said Nathan Wardell, Managing Director of Packserv.
“Many manufacturers have faced challenges with supply chain issues, delays with parts, limited support, and downtime dealing with international suppliers of machinery. There are so many benefits of using a local onshore supplier who can support your manufacturing.
“Utilising the latest digital technologies, we are able to give SME manufacturers access to equipment that will allow them to compete at the highest levels of quality manufacturing” added Wardell.
To learn more and to see Packserv’s packaging machinery in action, visit Packserv at Stand E100 at the APPEX expo.
Global warming is a worldwide struggle and an energy efficient product is a prime requirement.
Over the years, ELGi has focused on improving their specific power consumption (SPC) and improved flow (FAD).
Keeping ‘best in class’ life cycle cost (including power) in mind, ELGi has developed their new air-cooled, direct drive series with Permanent Magnet Synchronous Motor (PMSM).
Fixed speed machines’ performance is measured at 100% load, no matter what the customer demand is.
ELGi has developed a PMSM machine which offers superior efficiency at lower load to maximise the saving.
ELGi has designed their own robust, IP55 rated motor by leveraging the induction motor’s capacity. In the unlikely event of needing it, they can service the airend and motor separately which isn’t possible with most permanent magnet machines available in the market.
Why IE5 ‘plus’? For motors, only IE5 regulation is available, and ELGi is exceeding the regulation. That’s why they claim their motor efficiency is best in class.
Why PMSM? Induction doesn’t exceed IE4 and ELGi needed something better than that so chose synchronous technology. There are many options, but ELGi chose PMSM as it has the lowest losses. The technology is very precise, it receives input and gives feedback as well, which means ELGi can provide a ‘best in class’ efficient compressor.
controller and gives variable output.
VFD can run at lower turndown as well. And the drop in the efficiency from 100% load to lower load in PMSM technology is the least against all other technologies.
The compressor is fitted with an intelligent thermal valve system (ITV) for effective thermal management, which works intelligently with inputs from ambient and lube temperature sensors through a Neuron IV
ITV reacts instantly to temperature change and reduces thermal stress on the oil. By optimising the oil temperature and reducing the load on the airend, that enables energy savings.
The machine comes with an optional Air~Alert, which is an IoTenabled monitoring and alert system compatible with ELGi’s range of air compressors.
Data analysed and delivered by Air~Alert from your compressor enables you to improve your compressor’s energy efficiency and
uptime. Air~Alert also allows 24x7 remote monitoring from anywhere in the world.
Along with all the features, ELGi is making sure it’s optimally priced, and to give peace of mind to customers, they are also providing a superior warranty.
ELGi will be at booth number B155 at APPEX 2024, Melbourne.
Mouser Electronics has opened a new customer service centre in Melbourne to support its growing number of customers across Australia and New Zealand.
“This is an exciting time for our business as we expand into Australia to better serve our customers in this part of the world,” said Mark Burr-Lonnon, Mouser’s Senior Vice President of Global Service & EMEA and APAC Business.
“Melbourne has a thriving tech community and manufacturing base with a large amount of activity, especially in the original equipment manufacturers (OEMs) and electronics manufacturing service (EMS) sectors. This office gives us a strong local presence to serve customers with best-in-class service and support.”
Australia is home to a growing number of tech companies and start-ups and is considered a world leader in silicon-based quantum computing.
Mouser’s new service centre in Melbourne will have a team of
members onsite to personally assist with orders and respond to customer calls.
This will be Mouser’s 12th office in the APAC region. Mouser’s other APAC locations include Hong Kong, Shanghai, Bangalore and Pune, India, Republic of Korea, Malaysia, Philippines, Singapore, Taiwan, Thailand and Vietnam. The Melbourne office will be Mouser’s 28th service centre location worldwide.
About Mouser
As a global authorised distributor, Mouser offers the widest selection of the newest semiconductors, electronic components and industrial automation products.
To help speed customers’ designs, Mouser’s website hosts an extensive
library
Weld Australia has called for a guaranteed pipeline of local steel work in the renewable energy sector, with an incentive scheme similar to what the US is doing with the Inflation Reduction Act (IRA).
The group, which has sounded alarms about a shortage of welders in Australia, wants the federal government to enact a national policy framework that attracts the investment needed for sovereign renewable energy manufacturing.
It is calling for a mandated 60% of local content of Australia fabricated steel, by kilogram.
Citing mining billionaire Andrew Forrest’s decision to put $54 million into a new battery manufacturing plant in the US, the welding organisation says Forrest is cashing in on the significant benefits and tax incentives on offer under President Biden’s $550 million IRA.
These are “incentives that Australia’s governments seem
unwilling to entertain,” said Weld Australia.
It wants the federal government to consider the same framework, citing figures from thinktank Climateworks that estimates $625 million worth of investment is needed to decarbonise Australia’s industry and energy system by 2050.
“Our governments must stop prevaricating over our response to the IRA and enact equivalent policies and legislation that encourage private investment and secure a pipeline for local business. The alternative is that Australia remains a dig and ship economy until we run out of ore—and options, ”said Geoff Crittenden, CEO of Weld Australia.
“We must grow our manufacturing capability at a rapid pace if Australia is to have the resources to meet net zero targets. And yet, the federal government has so far failed to allocate funding, or enact any kind of industry policy, tax incentives, or legislation,” said
Crittenden.
The organisation pointed to speculation about whether the global supply chain can deliver on Australia’s requirements for the renewable energy transition, citing Vestas, a large wind turbine
The leader in high quality power, data transmission and automation systems that are used in mobile industrial applications.
Born as the exclusive distributor for VAHLE, Nilian has conscientiously expanded its partner selection to also include Brevetti Stendalto, Gain Electronic
and more recently Carl Stahl (Kromer). This ensures that our clients receive a diverse product selection from some of the worlds best innovators and
manufacturer, needing to build a local plant to guarantee supply.
Weld Australia
weldaustralia.com.au
In 1984, two Aussie friends with experience in engineering and magnetic applications came up with ideas for a range of magnetic products including clamps for steel workpieces. The partnership was named Serpent and Dove and was incorporated two years later.
Although small permanent magnetic configurations had been used to hold pieces of steel together, at that time none had been configured to the approximate size and proportions of the old and familiar engineer’s square (image 1).
Using ferrite magnet material bonded between two steel side plates which acted to extend the magnet poles and create a strong field across the gap between them, the original Welder’s Magnetic Square was born (image 2). The original versions even had centimetre and millimetre graduations printed on the label to assist users in approximating positions.
It featured 90 and 45 degree angles, or, if two were hinged together as a magnetic pair, any desired angle could be achieved.
From there, a natural product
evolution resulted in various sizes, such as the Compact Welder’s Magnetic Square, The Big Daddy, the Chunky as well as Compact Double among others. In addition, the range of ever-useful Drag-On Magnetic Handles (image 3) for handling a single steel sheet from stacks or into processes was developed in the mid-‘90s.
Serpent and Dove also developed the original Welder’s Magnetic Earth Clamp based on our design 88 mm diameter ferrite ‘Pot’ magnet. It featured a spring-loaded copper electrode capable of carrying up to 800 amps of DC current for firm electrical connection to the job. Later a 350 amp model with a brass electrode was introduced and various improvements and insulations were patented over time (image 4).
These new products quickly found acceptance, not only in Australia but
and, as is evident, picks up less than half the mass of typical steel swarf!
with help from Austrade were also exported in significant quantities to North America and sold extremely well through a nationwide distribution network. In the early ‘90s Serpent and Dove developed the very first Magnetic Wand pick-up tool for
swarf and steel chip collection and clean-up around machines and lathes. That product soon won a silver medal at the prestigious Plant Engineering Product of the Year Awards in Chicago in the Maintenance Tools and Equipment division (5).
The picture (image 6) below illustrates the significant difference between Serpent and Dove’s Magnetic Wonder-Wand at the top and that of an inferior copy which employs a very poorly designed internal magnetic element. The inferior wand is almost twice the weight
Naturally, it did not take long for these products to be extensively copied and soon the market was inundated with a host of inferior, second-rate products. Some Serpent and Dove products were patented using the once-upon-a-time Australian Innovation Patent system which has unfortunately been discontinued. (Apparently this low-cost avenue, which was a boon to small Australian innovators and businesses, was abused by multinationals and others who initiated large quantities of possibly spurious applications in attempts to establish innovation priority over competitors!)
In more recent years Serpent and Dove received patents for its Yellow Mag ll Pilot Ladder Magnet used worldwide to anchor pilot ladders to ship hulls during pilot transfer. The first Pilot Ladder Magnet was a Serpent and Dove product and was, once again, soon copied. However, in keeping with the company’s ‘product evolution’ philosophy, an improved, lighter and more flexible product was developed and has been patented.
Alongside Serpent and Dove’s innovative product development, the company has for many years also offered a range of magnetic separation products for food, chemical and mining industries and has become particularly strong in the supply of magnetic lifting systems in Australia.
A long association as representative of Mag-Autoblok Tecnomagnete of Italy with its superb suite of Permanent-Electro Lifting Magnet products for steel loads from a few kilograms to in excess of 40 tonnes, has positioned Serpent and Dove (now Serpent & Dove—Applied Magnetics Pty Ltd) as a leading authority. Large and small systems have been installed by many Australian heavy fabricators. In addition, the same technology powers work-holding systems for milling and grinding applications.
Australian Trellis Door Company has acquired an interest in EBS Entrance Solutions (EBS) which pioneered Thermospeed, Australia’s first insulated, thermal-efficient rapid-roller freezer door.
EBS’ range of industrial and highspeed cold storage and freezer doors lead the market in performance, reliability, durability, low maintenance and safety.
Typical applications where temperature-controlled doors are required include fresh food, meat and beverage processing facilities, warehouse and logistics centres, pharmaceutical and medical facilities, supermarkets.
Any business needing to move more product out the door does have options. As frequency of parcel movement increases, any level of automation can only assist.
Handling freight and moving customer orders in greater numbers has certainly accelerated in recent times, and finding quicker, smarter ways has always been key to success. Certainly the rapid growth in e-commerce has exponentially multiplied the rate at which parcels need to get out the door and at ever-faster turnaround times.
Often we get a request to assist in sometimes quite simple, “low-target” solutions to lift performance to get the customer through a perceived temporary situation.
However most customers are very receptive to receiving an alternative and longer term solution that will give them broader and more sustained scope for growth.
Other products in EBS’ wide range include insulated, sectional overhead doors, cold storage doors, dock levellers, insulated roller shutters, PVC doors and curtains among others.
Services provided by EBS’ qualified technicians include installation, repairs and maintenance of all their products, nationally across Australia and New Zealand. EBS is headquartered in Carrum Downs in Melbourne, Victoria, and exports across the globe.
ebssolutions.com.au
By providing “the alternative solution”, Adept Conveyor Technologies shows the customer much greater potential by looking in broader terms rather than just the temporary or initial request.
It takes just one phone call.
6-8
1/116
www.adeptconveyor.com.au
Understanding manufacturers’ needs, and knowing these are not all the same, are among the keys to success for East West Engineering which, lately, has been increasingly supplying manufacturers with off-the-shelf and customised materials handling equipment.
As a manufacturer itself, Sydneybased East West Engineering leverages its own experiences as it designs, develops, fabricates, and certifies a vast range of material handling equipment.
When the East West Engineering team needs equipment to improve its manufacturing processes and no off-the-shelf solution will do the job or is not certified for the right capacity and safety standards — it creates the equipment it needs. A new range of trestles is just one example.
Like many manufacturers, East West Engineering kept staff busy in the early days of Covid, by looking at inhouse improvements and housekeeping.Its production team works with loads that vary in size, shape and weight and the company saw that sometimes it didn’t have the ideal equipment to safely support them ergonomically.
“At the time we were working on
a 7m steel spreader beam weighing over 1000 kgs that needed to be supported in the optimal position whilst our fabricators worked on it,” says East West Engineering owner and Head Product Designer, Ron King.
“Once the trestle prototypes were successfully tested and certified, suddenly all our staff were putting in their orders for a set in their production bays.”
The ATS Trestles, now widely adopted by metal finishing and other manufacturers, highlights the adaptability of East West Engineering in responding to industry needs.
“When global supply chains were impacted during COVID, we noticed an increase in orders for products such as stillage cages and forklift attachments because manufacturers had to source local products. And demand for these products has continued,” says King.
East West Engineering consistently introduces new products from its purpose-built facility in Sydney. This is where the company’s product designers, engineers, fabricators, assemblers, painters and customer support team are based. With over
spreader bars ideal for manufacturers handling smaller loads. The new CEXL1726 spreader bar (with load connection points of 1700, 2150 and 2600mm), was selling well with manufacturers asking for more lower-capacity options, so the company developed a smaller model to suit working in tighter spaces.
Used in East West Engineering’s own fabrication and assembly bays, the AW Welding booms extend the reach for welding tasks with greater control and safety, while minimising non-arc time activities and removing trip hazards. Its articulated model AWB36 moves 180 degrees so welders can access more areas and tilts for optimal welding gun positioning. For more flexibility, the AWH30 Welding boom can be fitted up with an optional post, base and wheels.This saves time otherwise wasted on moving equipment and is ideal for jobs that don’t fit in designated areas.
Mobile gantry
300 standard products — in various sizes and capacities — and a library of over 9,000 custom designs under its belt, East West Engineering’s own user experience allows it to stay ahead of the curve. What starts as a bespoke solution for in-house or client needs often evolves into a standard product, such as the floor-mounted bin tipper designed initially for the food industry.
The company stocks materials and sub-assemblies to ensure swift production lead-times and offers custom builds and variations on standard products to meet the demands of its customers. Cages and waste bins, for example, can be modified to suit different loads or space constraints.
“Because we’re prolific manufacturers, our economies of scale often mean we can offer the best product for the job at the most competitive price,” says King.
Bestsellers includes:
Spreader and lifting beams
Centre-lift and end-lift models safely lift and precisely move heavy, awkward loads. Understanding that every lift is different, East West Engineering added a 5 Tonne
Mobility gives flexibility to move heavy equipment and materials around the worksite without having to install permanent overhead cranes. Mobile gantry cranes can also be used in more than one work area or facility and for lifting jobs that don’t have overhead crane access. They can also run on rails for heavier equipment or materials.
Trestles
A must for manufacturers, these sturdy, adjustable trestles provide load support during welding and other assembly processes.
Forklift attachments
East West Engineering offers over 100 standard forklift attachments that make forklifts more versatile and capable of more precise material handling tasks. Attachments allow you to lift, tip, turn, pull, position, grab, store and handle any load with a forklift. This includes work platforms, goods cages, jibs, fork spreaders, dirt buckets, roll prongs, bin tippers, hydraulic forks, rotators, hydraulic clamps and push pulls.
With heavy lifting an everyday activity, storage of rigging equipment is important for a manufacturer like East West Engineering that prides itself on maintaining a
safe environment. A lack of suitable rigging equipment prompted the company to develop a range for its team. A hanging rack, trolley and secure storage cage that can be crane-lifted are now part of East West Engineering’s standard range.
Storage racks and trolleys are designed to store and transport long materials such as pipe, scaffolding, conduit, tubing and bar stock. The latest addition, APV100, was designed to meet the needs of an anti-fire sprinkler system installer that needed to transport pipes on site and through doorways. There’s also a heavy-duty, 4-metre rack APR12 that stores up to 12 tonnes so it’s ideal for manufacturers.One of these racks is being used by an infrastructure company involved in Victoria’s North East Link tunnelling project.
Used in most industries to securely store and transport materials, East West Engineering’s range varies in size and capacity with forklift pockets and crane lugs fitted to most models to ensure ease of moving
them on and off site.
Proper disposal and storage of waste and materials is a daily occurrence in manufacturing.East West Engineering’s range includes self-dumping, lever-release tipping, rollover, drop bottom, heavy duty, stackable, skip, bulk waste, crane, hopper and wheelie bins.
Forklift bin tippers allow efficient emptying of wheelie and mega bins whilst reducing the risk of workplace injuries caused by manual handling.
Equipment must be sturdy to safely tilt or dump from when handling mega bins, chep boxes, wheelie bins and drums. East West Engineering’s BKN125 model was designed to be easily customised to suit any bins and has been sold to metal recyclers, pet food and grain companies. New to this range is BKN130 Floor Mount Mega Bin Tipper with a stainless steel chute to suit food processing and agricultural production lines which need to be fed constantly to be efficient. The customer for this
bespoke version required modifying to fit their existing production line and removable safety barriers.
The company extended its range in response to demand from manufacturers wanting smaller, more affordable bulk-bag hoppers, and has found a new manufacturing customer segment has opened. Its bag-filling frames, stands that hook open a bulk bag, bulk bag lifters and hoppers enable more efficient material handling. East West Engineering’s range of accessories includes a clamshell gate for bulk dropping soil, sand, gravel or grain, slide valves that allow more precise dispensing of materials as well as reducing adaptors to allow fitment into existing systems.
Heightened awareness of hygiene during Covid was met with East West Engineering’s first manual boot washer. With increasing demand for this range, the company rapidly expanded the range which includes an automatic model ideal for the food industry with three brushes and pressured spray bars
activated by sensors when the boot is in position.
Safely transport and dispense cable reels to reduce risk of damage or injury. This new range enables handling cable reels by forklift and crane.
With every product designed for safe and efficient handling, East West Engineering’s success is rooted in its proactive approach to understanding manufacturers’ needs, continuous innovation, a commitment to customer support and delivering reliable solutions for material handling challenges.
“We regularly provide replacement compliance plates for attachments out in the field.It makes us proud when we receive request for some older gear such as a marrel skip bin made for Sydney Water in 1998 and a jib made in 1997. Twentysix years in the field and still getting the job done!” says King.
East
eastwesteng.com.au
Selecting the right electric stair climber needn’t be overwhelming, even for newcomers.
Electric stair climbers have been made since 1983, and are increasingly being enhanced courtesy of global manufacturers.
These devices are broadly categorised into upright and tracked models, with recent innovations introducing upright tracked climbers.
Upright stair climbers, resembling enhanced hand trucks, support loads from 110kg to 250kg, offering affordability, portability, ease of loading, and adaptability to various terrains.
Their main challenge lies in maintaining the load’s balance during operation—a task that demands some getting used to. Despite this, their agility and effectiveness across diverse staircases make them a preferred choice for many.
On the other hand, tracked climbers, which utilise caterpillar tracks for movement, cater to heavier loads starting at 300kg. These units are bulkier, pricier, and slower, with a reliance on ramps or lifting for loading.
Their advantage lies in their ability to significantly reduce manual effort, often allowing operation via a corded remote, thus transforming tasks that would typically require multiple people into solo endeavours.
The advent of upright tracked climbers seeks to merge the best of both categories, offering a lighter,
more cost-effective, and quicker alternative without the need for manual load balancing on stairs. However, this technology, still in development, presents certain limitations for specific uses or loads.
XSTO Australia, for which Tente is a distributor, prides itself on hosting the country’s most extensive
stair climber selection, backed by over two decades of specialised, in-house experience.
Their offerings range from economical models to cutting-edge innovations, enhancing both efficiency and safety. To enhance the decision-making process and ensure you’re fully equipped to use your stair climber with confidence and skill, they have curated an extensive collection of demonstration and training videos.
These resources are designed to guide users through the selection of the ideal stair climber for their needs and to provide them with the knowledge and techniques necessary for proficient operation.
With a full suite of services, including sales, training, repairs, and custom modifications, XSTO’s expert team can assist you in finding the perfect stair climber for your needs.
Tente tente.com.au
Door manufacturer, DMF International, has announced that Premier Doors Systems Pty Ltd (PDS), an industry leader in commercial doors, has acquired the company, combining to give over 100 years of experience in the specialist door market.
DMF says the strategic partnership of DMF and PDS increases the range of doors available, but also enhances nearly every element of the businesses, providing full manufacturing facilities in both NSW and VIC, leading to greater innovation, and creating more value for clients and partners.
DMF is a leading Australian manufacturer and distributor of high-speed and PVC doors. They provide doors for a variety of applications, including food processing plants, car washes, car parks, warehouses, pharmaceutical plants and hospitals.
They are also the authorised partner for EFAFLEX GmbH, a global leader in high-speed door technology, located in Bruckberg Germany.
DMF says the partnership allows it to supply and install a wide range of specialist doors for the Australian market.
• Diverse expertise: offering a comprehensive portfolio of doors, from rapid roll doors and folding doors to swing doors and PVC strip curtains.
• Customisable solutions: custom doors for unique business needs, collaborating closely with clients for large openings, extreme conditions, and specific security requirements.
• Unwavering quality: highest-grade materials and advanced manufacturing for doors that are durable, reliable, and long-lasting.
• Innovation: pushing door technology boundaries, investing in R&D to deliver cutting-edge materials, automation, and safety features.
• Exceptional service: with manufacturing facilities in both Sydney & Melbourne, DMF can exceed
lead time expectations, and provide comprehensive guidance from consultation through installation and beyond.
The collaboration between PDS and DMF boosts value for everyone involved. It strengthens DMF’s operations and partnerships with Australian suppliers, showing their dedication to excellence and will be
a partnership that “opens doors” to endless possibilities. Call DMF for a free consultation from one of our experienced team members.
At 80 years old, King Group’s Managing Director Ron Mileham is still very much in the game.
He continues to invent products, and offers a range of packaging and materials handling products through his company Pack King.
The company philosophy, he says, is to take a different path from competitors.
“We’ve been differentiating ourselves with unique products.”
“Basically, we solve problems, because the people who come to us with a problem are often too close to it – they can’t see the wood for the trees. So we step in, drawing on our experience with so many companies.
The latest of Mileham’s inventions is his Bendy Angles crate maker, which has just been patented.
It’s a “speedy way of making a crate,” says Mileham, allowing the user to make a crate out of a flat steel plate, bent to any angle to form the joints of the corners and the sides.
It comes in two sizes, with a larger version for DIY users, says Mileham.
“For example, if you’re putting a structure up outside your home, you’ll want to put brackets upthese can be set at any angle you want, and then you bend them at the angle that suits.”
Some of Mileham’s other inventions include the Drum Major, a multi-purpose drum trolley, purported to be one of the most
expensive in the world, but which hasn’t stopped it from being sold globally.
“The reason it’s so expensive - costing $2500 compared with others that start at $300 - is because it makes it so much easier to move a 200L drum,” Mileham told Industry Update
“It has an ergonomic design, it can load and unload drums from pallets, and when lying flat it acts as a drum decanting trolley. It has two or four wheel options, including a four
wheel angle position so there’s no load on the operator.
“The unique double torsion spring action isn’t found on any other drum trolley.”
Another Mileham innovation is the Eziloader Floor Level Loading Trailer, which as its name implies, lowers fully to the floor to allow any wheeled vehicle, especially those with very low ground clearance, to be wheeled on or off without the need for lifting.
Designed originally to enable walkie stackers to be loaded and unloaded for demonstration at clients’ premises, these floor level loading trailers have been used for removals, shop-fitting, vending machines, go-carts and much more.
Mileham says a lower-cost, open or closed top version is on the way.
Then there’s the Rapid Wrapper, a powered stretch wrapper, and can stretch-wrap extra long objects.
In order to save on warehouse space, it can be stowed away on racking securely due to slots in the base, and loaded using a straddle walkie stacker or forklift. The latest iteration offers variable speed control, soft start and ramp up timing.
In 2015, Pack King expanded into the US, establishing the King Group USA, which Mileham says sells the best unique and specialised Australian handling products into the US.
“The US market is huge but we only have a small part of it as Americans are quite parochial. Our products on the website do well however, because there’s probably nothing like them in the US.”
Mileham says he’d welcome more Australian products on his US site.
“We encourage people to get in touch with us if they want to enter the US market, then we can add them to our website.”
All products, whether here or in Australia, would still adhere to Mileham’s long-running credo.
“Pack King is not in the business of offering cheap products, rather we offer value for money, well designed and manufactured products that have kept customers coming back for over 30 years. We are still dealing with our very first customer.”
packking.com.au
Removing
Pulling
Loading
Following news of its phone-operated, retractable, 240v power-on-demand system, Conductix-Wampfler’s VersaReel Blue has been welcomed by Victorian wholesalers, architects and designers.
The Melbourne-based company has been busy educating electrical wholesalers in a soft, local launch ahead of taking the campaign to other states.
Local wholesalers now understand the VersaReel Blue is ideal for retail spaces, educational facilities, offices, and galleries as well as warehouses and more industrial environments. This tidy power supply, which has excited designers of educational facilities, suits any organisation that needs temporary, retractable power and also values safety and convenience.
By combining reliable cable reel performance with Bluetooth, Conductix-Wampfler has created a motorised electric cable reel which can be installed neatly at the ceiling or within a ceiling space. This obviates ladders, messy and hazardous cabling, and avoids wear and tear on cables. It also creates more possiblities for flexible use of space.
“Unlike Conductix’s traditional cable reels, the VersaReel Blue can be operated easily and securely by anyone using the password-protected app on their iOS or Android phone,” says Nick Banham, Southern Region Sales Manager Conductix-Wampfler.
The app enables users to remotely operate the reel to quietly lower a power outlet to a desired point in a classroom, library, retail space, office or gallery where outlets are
inconveniently at the perimeter. When it’s no longer needed, they can tuck it away just as easily.
“The VersaReel Blue’s professional, neat appearance, safety benefits, and minimal training requirements make it suitable for all sorts of organisations and staff,” says Banham.
As a specialist in mobile energy supply and data transmission, Conductix-Wampfler has a reputation for hard-wearing systems for
mining, bulk handling, factories and warehousing. Yet the VersaReel Blue’s professional aesthetic and simple operation takes this product to many more environments while retaining Conductix-Wampfler’s engineering which is known for durability and longevity.
What does the skipper do on a racing yacht? The traditional view of a seafaring captain or skipper is that of one person who makes every tactical and operational decision and who then issues commands to the crew to make it happen.
On a racing yacht there simply isn’t time for all that rigmarole. Each member of the crew has specific functions they perform, and they have trained as a group to work in precise harmony to achieve their common goal using their individual areas of expertise.
In these terms traditional centralised automation is the skipper (master PLC) standing on the quarterdeck (control room) bellowing out commands while decentralised
automation is the racing yacht where all the crewmembers (machine modules) perform their functions quickly and efficiently and in perfect synchronisation with the other crew members (machine modules).
Traditionally, automation systems have had rigid hierarchies that were based around centralised control, as per the well-known automation pyramid diagram. The sensors and actuators were always connected to the PLC. The PLC was always connected to the SCADA system and so it went. Unfortunately, this well entrenched automation model can be limiting. It requires lengthy decision-making paths, and it also ties all the automation together to a single, central point. This means that a single fault or maintenance activity can bring an
entire plant to a halt.
As technology has advanced, the previously rigid levels have had to become more flexible. We now have sensors that detect machine wear, RFID tags that tell the machine it is correctly configured for the next step and what it must do, and I/O modules that can decide independently to operate an actuator.
It is no longer possible to place the present and future of automation within the constraints of a traditional automation system because it is simply not able to deal efficiently with all the extra capabilities that are now achievable.
Decentralised automation lays the foundation for a new era of automation. It enables maximum flexibility, and it creates numerous benefits such as:
A small PLC or FLC (Field Logic Controller) can preprocess data, only passing on that which is necessary. PLCs can be integrated within HMI’s, they can be separate blocks or can be included in I/O system modules). FLCs are already integrated into many I/O modules. The PLCs and FLCs can be field mountable (IP67/69K) or suitable for use in cabinets (IP20). They minimise processing time and provide efficiency by cutting the amount of information that needs to be sent to a central point down to valuable and essential information only. This simplifies the installation.
Each different machine, or each
individual module is capable of fully independent operation. They can be pretested before installation and issues with one section will not delay the progress of other sections. Wiring is easy thanks to IP67 components and standard industrial quick connectors. Control cabinets can be scaled down or eliminated altogether so that significantly less wiring is required.
There is a significant reduction in the necessary central control capacities. By reusing existing modules design costs are also reduced and the reduced wiring and mechanical requirements mean lower personnel costs.
There is a significant reduction in the risk of failure because decentralised automation has a much lower dependency on a central control system. On-site machine condition monitoring allows early intervention when issues are detected before failure occurs. Module replacements in the event of a failure are fast, simple and require minimal configuration.
Decentralised automation allows users to respond dynamically to changing requirements. They can fine tune their equipment and process, even during production. Decentralised logic enables the testing of machinery and machine modules offline before delivery. By reusing existing modules, the design phase is shortened.
One of the benefits of self-diagnosis on machinery and plants is the reduction of load on the communication lines to the central control system. Information is not sent to the top level until an error or anomaly is detected. Modern smart sensors and local edge devices are designed to decide for themselves when an anomaly has occurred and IO-Link enables more data to be retrieved from the devices, providing more comprehensive coverage. Condition monitoring also makes maintenance more efficient. Rather than doing preventative maintenance to pre-empt issues that may not actually occur we can let the sensors and the machine tell us what needs to be done when it needs to be done.
Decentralised intelligence makes modular machine construction
considerably easier. Each module operates independently and supplies adjacent modules and, when required, a central control system with greatly simplified data via easy to use and service-oriented interfaces for control purposes. Modularity allows for simple and flexible expansion. IP67 field PLCs also allow modularisation of the control programs. Even security applications can be wired or controlled in a decentralised manner. The use of field mountable equipment eliminates the need for control boxes on the individual machine modules.
Ethernet based safety I/O modules provide personal protection at the machine module and enable local, field-based safety logic. By providing faster response times than centrally controlled safety systems, this can allow safety guarding devices to be mounted closer to the danger point, saving space, and improving ergonomics. Off site pre-testing, the elimination of control cabinets and the use of industrial quick connectors make installation easy and shorten commissioning times. By distributing safety logic in the field non-affected modules can continue to operate when an emergency stop of an adjacent process occurs. Safety Ethernet can be used for communication between units.
Decentralised identification technology allows direct communication with workpiece carriers and products, and you do not need to have a central database. The product tells the machine what to do. This setup offers a number of advantages from production through to after-sales such as faster processes through preprocessing directly at the application and complete transparency through comprehensive tracking.
Decentralisation may not be perfect for every situation, but in most cases it reduces wiring and hardware and cuts design time. It also reduces manufacturing and installation time, improves efficiency and minimises downtime.
As demonstrated with the racing yacht, having a single central control is often less efficient than having a well trained and coordinated team of experts on the job.
Centralised automation? It looks a lot like that outdated ship has sailed.
Turck
turck.com.au
Anew partnership between LAPP Australia and Wieland Electric is expanding LAPP’s ranges of electrical automation technologies, including multiple products in the functional safety category.
Wieland is a German-based leader which supports industries including building technology, engineering, wind power, EV charging, horticulture, and lighting and operates in more than 70 countries. Wieland products are developed for functional safety for machines, industrial networking, and power distribution.
“The partnership with Wieland is a natural fit for LAPP Australia, as we continue to expand our industrial IT, automation, networking, and electrical interconnection ranges,” said LAPP Australia Managing Director, Simon Pullinger.
LAPP Australia will sell more than 28,000 Wieland product lines, with 1,000 to be stocked locally in Australia, and the others to be air-freighted from Germany in one to three weeks, depending on the
product and destination.
Wieland is known for its functional safety products, where it has built up a global pedigree for reliability and performance. Functional safety refers to technologies that enable safe operation of machines and reduce the risk of equipment causing harm to people or property due to malfunction or incorrect operation.
“As industrial processes become more automated with more complex machinery, there’s an increased need to meet strict functional safety requirements. Wieland’s range includes electro-sensitive and mechanical safe sensors, compact relays, and powerful safety controllers to reliably support industrial clients in motion monitoring, analogue signal processing, industrial press control, and material flow,” says Pullinger.
“LAPP Australia has the in-house technical expertise to assist with specifying the right Wieland products for the job, as well as ongoing
E-stops, safety magnets and light curtains, left, safety relays, right, are just a few examples of Wieland’s extensive safety product ranges
support to keep everything running smoothly and operating to optimum efficiency,” he adds.
At the heart of each functional safety solution is Wieland’s SAMOS®
PRO COMPACT safety logic controller. The most compact and versatile in its class, this safety controller includes a large library of TÜV-certified safety functions, integrated status and diagnosis functions, and easy-to-use programming software.
“Wieland shares LAPP’s focus on customer service, and getting each application right, no matter how complex or unusual. Both
companies have extensive resources and highly trained personnel, which will provide direct benefits to the Australian market,” says Pullinger.
LAPP Australia is part of the LAPP Group, a leading global manufacturer of high quality German-manufactured cables, connectors, and industrial connectivity solutions for a broad range of industrial applications.
lappaustralia.com.au
Retailers need to adapt to consumers’ changing habits
Consumer behaviours are in flux, changing in response to economic factors and the adoption of new technologies.
“For businesses in the supply chain – including manufacturers, retailers and warehouse owners –it’s essential to adapt to changing consumer habits, or risk being left behind,” says Jason Wu, Business Development Manager, AutoStore Australia and New Zealand.
Wu points out that digital technology holds the key to helping retailers present shoppers with price comparison platforms, personalised discounts or vouchers, and loyalty benefits.
Not only do consumers want access to a wider range of goods; they also want to be able to select the payment and fulfilment method that suits them best.
“To secure customer loyalty, retailers need to focus on giving shoppers convenience and choice. It’s important to offer a variety of payment options, including mobile payment and buy-now-pay-later, as well as a variety of fulfilment
options, from same-day delivery to click-and-collect,” saidWu.
“For retailers, this means closing the distance between the warehouse and the shopper.”
Wu outlines how the supply chain
will need to adapt, to keep up with these changes:
1. Helping shoppers plan and budget: Wu points to the findings of News Corp Australia’s News Food Corp Network’s Trend Forecast – 2024 Special Edition, that two in three Australian shoppers are
planning their grocery shop in advance.
“For the grocer, this might be offering free access to recipes and meal planning templates via the store app or website,” says Wu.
2. Optimising warehouse space: Being able to offer consumers a wider range of products, available fast, means having more space to store those products. “Vertical cube storage systems increase storage density, without the need for a larger warehouse footprint,” says Wu.
3. Automating warehouse processes to achieve enhanced performance: The deployment of robotics and automation technology enables faster sorting, picking and order fulfilment, as well as more accurate inventory management.
4. Offering omni-channel fulfilment: Consumers are demanding greater flexibility and more choice when it comes to the fulfilment of orders. For retailers, this means integrating physical stores with
digital platforms, and supporting choice by offering delivery or click-and-collect shopping.
5. Ensuring same day delivery:
“For this to be feasible, many retailers will look to the establishment of smaller distribution centres – micro-fulfilment centres or dark stores - located in close proximity to customers or even inside existing grocery or retail spaces,” explains Wu. “This is the only way to close the gap between the warehouse and the customer, and avoid the costs associated with last mile shipping.”
6. Supporting seamless returns:
According to Shopify, the average return rate for ecommerce is 20% to 30%. “There’s growing pressure for Australian brands and retailers to offer free returns.Having a warehouse system in place that can handle returns efficiently, will be key,” adds Wu.
The AutoStore Automated Storage and Retrieval System (ASRS) comprises a vertical cube storage Grid and automated Robots which travel over the Grid, picking up or storing items in Bins housed in the Grid. Wu highlights how this solution
John Dee, a family-owned Australian beef producer, has partnered with Dematic to dramatically upgrade and automate its beef processing systems to meet the demands of the global beef market.
John Dee’s Warwick-based processing plant in Queensland, just two hours from the port of Brisbane, is instrumental in supplying premium beef cuts to more than 145 customers in over 37 export markets worldwide. Over the years, it has evolved from a local beef producer into a major beef exporter servicing a diverse range of international markets.
“We’ve been a beef processor in Warwick since 1945 and today we’ve transformed into a full-blown beef export and processing operation,” explains John Hart, Owner of John Dee, Warwick.
“In the early days, we sold full sets of meat parts, whereas today we break them up and send different components to Japan, Korea, Indonesia, Taiwan, the EU, and America.”
With growing demand, especially from international markets, John Dee faced a critical challenge. The company had outgrown its existing storage capacity, and manual operations were proving inadequate to meet the complexity and scale of their production.
“With the way we’re operating today, trying to get products into the right place at the right time, was becoming almost impossible to do by hand,” says Hart.
“In our previous manual operation, people had to understand all the
facilitates a number of benefits for warehouses:
• The Grid is modular and is easily customised, enabling 90% warehouse space utilisation.
• The Robots are designed to move in four directions, making it easy for them to reach any Bin on the Grid, and deliver a 99.9% picking accuracy.
• The Robots are self-monitoring (recharge automatically as required) and energy efficient, with 10 Robots using less energy than a standard vacuum cleaner.
• The ASRS is the fastest ‘Goods to Person’ system per square metre
- enabling order fulfilment times of less than a minute from order to shipping. At the company’s fastest site, the ASRS presents 12, 000plus Bins per hour.
• The AutoStore PickUpPort™ (a public-facing port that lets customers shop online and pick up their order directly from the AutoStore System) enables collection from the warehouse facility.
product codes and pick by hand out of a cold store. With over 10,000 cartons being produced a day, it became a logistical nightmare. A thousand cartons a year that would go out of date because they couldn’t be located.”
In response to these challenges, John Dee embarked on a multi-staged facility upgrade project, partnering with Wiley and Dematic to design and implement automated systems tailored to their unique needs.
At the heart of the transformation is the Dematic Multishuttle® meat buffer storage and handling system, a solution specifically designed to address the complexities of meat processing.
This modern system automates the storage and retrieval of product cartons, streamlining operations in sub-zero conditions. It manages products both chilled to -1°C and frozen at -20°C, reducing the reliance on manual labour in harsh cold store and freezer environments.
“Our advanced Dematic Multishuttle system provides a high performance, accurate, safe, and cost-effective automated order fulfilment and despatch processing solution for the meat industry, and we are very excited to see John Dee reaping the many benefits at their Warwick facility,” says Soeren Schauki, Business Development Manager at Dematic.
“The system was completely operational at full speed on day one,
and the throughput of this system is unmatched.”
Operation of the four-aisle, 30-level Multishuttle is managed by Dematic Warehouse Control System (WCS) software that provides full track and trace, where each carton is followed throughout the supply chain, so losing product is no longer possible.
The WCS also controls the storage duration of all cartons, allowing John Dee to set the time each carton can remain in the system. This helps to improve the shelf life of the meat products and ensuring cold chain compliance is maintained.
The solution is designed for John Dee to scale up and increase its premium beef export market share.
One of the frozen aisles can also be switched to chilled in response to anticipated future growth and advancements in cold supply chain export markets across Asia.
“In working with Dematic, we ensured that our system would be able to adapt for the future growth of John Dee to increase capacity to match significant surges in demand, whilst also providing improved worker safety,” says Hart.
Since implementing the new system, John Dee has reduced its reliance on labour, which in a tight labour market has become difficult to source for harsh cold storage facilities. In doing so, John Dee has reduced occupational health and safety issues associated with employees working in a cold storage environment.
“The recent expansion of our Warwick facility is the largest single investment in the company’s almost 80-year history, and it is supporting our business growth and competitiveness during a time when beef exports are rising significantly,” concludes Hart.
To learn more about what the Dematic and John Dee partnership has achieved read the full case study.
BioNTech will build a state-ofthe-art clinical-stage manufacturing facility for new mRNA medicines at LaTrobe University’s Melbourne campus.
The site will manufacture new investigational mRNA therapies for serious diseases including cancer, which reflects BioNTech’s focus on developing investigational immunotherapeutic treatment methods including mRNA-based vaccine candidates, to fight diseases.
In December, BioNTech announced it was signing a multiyear partnership with Victoria to research, develop and manufacture new mRNA medicines and strengthen the local mRNA ecosystem and innovations.
Its goal is to treat up to 4,000 cancer patients over a ten year period in the region in clinical trials or with authorised therapies.
“The planned BioNTech
manufacturing mRNA facility will connect groundbreaking research and developments in mRNA vaccines and therapies with La Trobe’s research expertise, building on our already established national and global partnerships in cancer, cardiovascular and infectious disease,” said La Trobe Vice-Chancellor, Professor John Dewar.
At the press event of the announcement, the Victorian government also announced funding to establish a new Victorian Centre for AI in Medical Innovation at LaTrobe, which will sit alongside the new BioNTech facility.
“Complementing the planned facility, the Victorian Centre for AI in Medical Innovation will apply La Trobe’s world-leading expertise in AI and health to mRNA technology, helping accelerate the development of cancer vaccines and treatments,” said Professor Dewar.
University of Queensland (UQ) researchers have developed 4D printing technology that produces shape-shifting liquid metals for soft robotics, and which could lead to wider manufacturing breakthroughs.
4D printing is an extension of 3D printing, where solid objects are created using materials that can change shape when exposed to certain stimuli like heat, water or light.
At UQ’s Australian Institute for Bioengineering and Nanotechnology (AIBN), researchers are printing 4D structures using new liquid metal polymers that can be coaxed into performing a range of mechanical tasks with infrared lasers.
Lead researchers Dr Liwen Zhang and Dr Ruirui Qiao said the unique preparation methods developed by their lab allow them to produce 4D designs that are solid and durable while also being able to bend, grasp, lift, and release items five times their weight, or revert to a pre-programmed shape.
“4D printing takes traditional 3D printing and adds a new dimension –the dimension of time,” said Dr Zhang.
“Our method allows us to produce smart liquid metals that can be
customised, shaped and prompted to change over time without needing wires or circuits.
“This is a new era for robotics applications and a gamechanger for additive manufacturing.”
4D printed objects are usually prepared with a 3D printer using specific ingredients that give the finished product new qualities and abilities.
In the journal Nature Communications, Dr Zhang, Dr Qiao, and colleague Professor Tom Davis detail how they used spherical liquid metal nanoparticles to prepare printing resins that are responsive to near-infrared light.
This means lasers can be used to guide the materials to bend, grab and release items.
While the technology is in its early stages, Dr Qiao there was great potential to use it in the design of soft robotics, or technologies that mimic natural movements and interactions.
This could mean a number of applications across the aeronautical engineering and medical device sectors, including coronary stents, artificial muscles, and other devices that adapt and change shape inside the body.
More broadly, Dr Qiao said the ability to customise and shape materials
after they had been printed would lead to wider manufacturing breakthroughs and consumer innovations, from climate-reactive clothes and building materials to self-assembling furniture.
“4D printing is a rapidly evolving field that is really only limited by imagination,” Dr Qiao said.
“The specific nanoparticles we use allow our materials to react to lasers. Other 4D printed materials contain ingredients that react to
water, heat, acid, electric, or magnetic energy.
“The early signs for this technology are incredibly promising, and the wide range of potential applications give us encouragement to continue our research.”
The spherical liquid metal nanoparticle printing method used by Dr Zhang, Dr Qiao, and Professor Davis was published in Nature Communications.
DeepSouth, the world’s first supercomputer to simulate networks at the speed and scale of the human brain, is being built at Western Sydney University and should be operational by April this year.
Created by researchers at the university’s International Centre for Neuromorphic Systems (ICNS), this computer’s neuromorphic system mimics biological processes. It uses hardware to efficiently emulate large networks of neurons which spike at 228 trillion synaptic operations per second — rivalling the estimated rate of operations in the human brain.
DeepSouth differs from supercomputers which are typically power hungry, according to ICNS Director, Professor Andre van Schaik. Purpose-built to operate like networks of neurons, this supercomputer enables greater efficiencies and uses less power.
Prof. van Schaik says our former inability to simulate brain-like networks at scale has hampered advances in our understanding of how brains use neurons to compute.
“Simulating spiking neural networks on standard computers using graphics processing units and multicore central processing units (CPUs) is just too slow and power intensive. Our system will change that.”
Prof. van Schaik expects this platform to advance understanding of the brain and develop brain-scale computing applications in diverse fields including sensing, biomedical, robotics, space, and large-scale AI applications.
This will lead to advances in smart devices, such as mobile phones, sensors for manufacturing and agriculture, and less power-hungry and smarter AI applications. It will also enable a better understanding of how a healthy or
Science & Technology Australia (STA) has blasted the government’s December 2023 economic outlook, saying its $46.2 million cut to research commercialisation “undermines confidence” in R&D, and therefore undermines Australia’s future prosperity.
STA, which represents more than 115,000 scientists and technologists, urged the government and Education Minister Jason Clare to rethink the cut.
Australia’s Economic Accelerator (AEA), the country’s new research commercialisation fund will get $46 million less over four years which STA says is 7% of the capital allocated to the fund in the last Budget.
Science & Technology Australia President Professor Sharath Sriram called it a step in the wrong direction because the cut comes when Australia’s investment in R&D has plunged to a four-decade low, and when Australia needs to lift its investment in R&D.
“Australia urgently needs to invest more – not less – in R&D to generate the next wave of new jobs and income to secure the living
standards of our kids and grandkids,” he said.
“We cannot afford to undermine certainty and confidence – which are crucial to the willingness of Australian industry to engage in research commercialisation.”
“We urge the government and Education Minister Jason Clare to rethink this cut – especially as the government considers the final report of the Australian Universities Accord in the months ahead.”
“The Accord urgently needs to deepen Australia’s ambition and investments in R&D to secure Australia’s economic future – starting in the May Budget in 2024.”
diseased human brain works.
Western Sydney University’s ICNS team collaborated on this ground-breaking project with partners across the neuromorphic field including researchers from the University of Sydney, University of Melbourne, and University of Aachen, Germany.
The supercomputer is named DeepSouth partly in homage to
IBM’s TrueNorth system, which initiated efforts to build machines simulating large networks of spiking neurons, and to Deep Blue, the first computer to become a world chess champion. The name is also a nod to its geographical location.
DeepSouth will be based at Western Sydney University and is a key contributor to the growth of the region as a high-tech hub.
Growing from a handful of employees to seventy-five in a few years is testament to the enormous growing demand for MITS Alloy’s range of heavy-duty aluminium ute trays and canopies.
Based in Newcastle, the company was founded by Tim Lightfoot and Tony Brooks in 2015. Lightfoot’s existing business, Safety MITS, supplied maintenance equipment for heavy industries such as mining, earthmoving, transportation and associated industries. Together they identified the need for durable trays, canopies, toolboxes and service bodies for four-wheel drive utes that could stand up to the harsh abuse of heavy work and mine sites.
Initially manufacturing custom-designed products, the company evolved as it developed a range of standard modular trays and canopies to fit all popular ute brands and models — with a number of optional accessories to suit individual preferences. This flexibility of the modular design extends to being able to remove the tray and canopy and transfer it to another vehicle at time of sale if required.
A natural progression saw the company supplying the same high-quality products to the burgeoning recreational, off-road 4x4 market and more recently the fleet/trade market which has grown substantially.
Modern vehicles have an array of safety features including reversing cameras, parking sensors, autonomous braking and blind spot detection. Many of these driver aids are located in the rear bumper; this necessitated MITS to develop its own
harnesses, wiring and housings to ensure these work as per the factory settings once the new trays are fitted.
The demand for the trays and canopies over recent years necessitated the need for new premises. Serendipity intervened when a large factory across the road became available earlier this year. The facility has since been custom-designed for MITS operations and features a 2,000sqm space for fabrication, an 1,800sqm assembly facility and 900sqm powder coating area, enabling all work to now be done under the one roof.
The company’s expansion and move to larger premises corresponded with investment in new sheet metal equipment that has made possible the introduction of advanced manufacturing techniques, greater production efficiencies and broader manufacturing capabilities.
‘We already had a good relationship with Applied Machinery following our previous purchase of two Yawei press brakes. We’ve been impressed with the Yawei’s performance and reliability so a Yawei fibre laser was the obvious choice,” Lightfoot said.
“The 6kW high-power fibre laser is perfect for our mainly aluminium processing environment and has dramatically sped up our cutting. What used to take us 16 hours a day, over 5 days has now been reduced to just 23 hours a week over 3 days.
“We also have a much higher consistency of cut, a superior quality finish and our scrap rate has been significantly reduced,” Lightfoot said.
The auto-load/unload function
and other aesthetic enhancements.
“The Yaweis offer high performance at what is a very competitive pricepoint. Evidence of this is the fact that we anticipate a ROI on the fibre laser in just 12-18 months.”.
“The back-up and support from a local supplier like Applied has been great. We’ve always found the Applied team really easy to deal with; they have good tech support on the ground and get back to us quickly with a solution to any issue we encounter,” Lightfoot said.
The company has recently launched in the US where its products have found a ready market both in the recreational ‘overlanding’ side and also in more specialised areas such as police and fire and rescue vehicles.
has also been a huge time-saver for the company and reduced manual handling and minimised workplace health and safety risks. All cutting is done with high-pressure compressed air alone.
“Whilst the fibre laser has been great, it is our new Weber deburrer that has been the biggest timesaver — it takes all the sharp edges off parts quickly to give perfect surfaces and edges. We used to have
The company’s recent application for ISO 1001 certification is likely to see these specialised opportunities open up in the Australian market.
Recognition of MITS Alloy’s success and contribution to supporting employment in the local Newcastle area was confirmed recently with the company being named Manufacturer of the Year 2022 (50 employees or more) at the Hunter Manufacturing Awards.
The future certainly looks bright for MITS Alloy and Lightfoot sees the new factory and the new Yawei and
four guys working 16 hours a day cleaning parts by hand to ensure they were touchable. We can now do a week’s work of deburring in just six hours a week with just two staff –and the quality is far superior.”
Another benefit of the new equipment is that it has allowed MITS to produce more intricate parts and reduce weight; more detail can be put into products including logos
“YAWEI OFFERS HIGH PERFORMANCE AT A VERY COMPETITIVE PRICE POINT - WE ANTICIPATE AN ROI IN JUST 12-18 MONTHS.”TIM LIGHTFOOT, MITS ALLOY, NEWCASTLE, NSW
Dollar for dollar, the Yawei HLF series fiber lasers are in a league of their own, providing possibilities for all size companies across the laser cutting sector. Adding automation increases the value proposition further. Featuring high quality componentry they offer multiple benefits including high speed, extreme accuracy and consistency of cut, combined with low operating and maintenance costs.
Plus you get the expert advice and support that only a local supplier like Applied Machinery can provide. We’re a true machinery partner - just ask Tim Lightfoot.
Real Service. Real Support. Real People. That’s Applied Thinking.
Call:
Email: Visit:
03 9706 8066 sales@appliedmachinery.com.au appliedmachinery.com.au
industryupdate.com.au
The new cyber® kit line medium from Wittenstein’s Cyber Motor division rounds off a cohesive portfolio of frameless, torque-optimised servo motors in integration-friendly designs.
The new frameless motors are available in compact sizes with an outer diameter of 100 mm or 112 mm – as well as in three different lengths, namely 30 mm, 60 mm and 120 mm. A PT1000 and a PTC temperature sensor are integrated every time, to protect against thermal overload and enable constant monitoring of the drive temperature.
The modular motor system also provides enormous design flexibility due to the choice between small or large hollow shafts as well as voltage classes for 60 VDC and 600 VDC / 750 VDC.
Furthermore, the cyber® kit line medium is compatible not only with Wittenstein Cyber Motor’s cyber® simco® drive 2 servo drive but also with other standard servo drives worldwide.
The modularly configurable frameless motors in the cyber® kit line medium series are optimally adaptable to specific tasks and operating conditions owing to the large number of possible variants. This opens up numerous innovative design options for highly dynamic drive solutions in OEM machines.
The motors, which can also be used as direct drives, are both frameless and bearingless. With their compact dimensions and reduced weight, they are just perfect for direct, spacesaving integration into machines.
Thanks to the hollow-shaft concept cable, compressed air, vacuum, fiber optic and laser feedthroughs
for gripping elements or sensors, among others, can be elegantly implemented when only limited space is available. The frameless servo motors are no less impressive in use, setting benchmarks in terms of torque density and dynamics.
As far as performance is concerned, the cyber® kit line medium bridges the gap very neatly between the successful cyber® kit line small and cyber® kit line large series of frameless motors.
Collaborative and industrial robotics, machine tools, packaging technology, actuators for assembly, transfer and handling systems, testing and measuring machines or tasks in semiconductor manufacturing are typical applications for these highly dynamic and robust servo motors.
New encoder module for cyber® kit line small
Wittenstein has simultaneously introduced a new encoder module for the cyber® kit line small that can be built in as an option for four different feedback signals.
It provides >16 bit system accuracy as well as repeatability of <± 0.1° and ships in two versions: either with BiSS-C and SSI interfaces or for incremental and Hall signals. In combination with the cyber® simco® drive 2 servo drive, the frameless motors in the smallest series with an integrated encoder module are the perfect system solution for 48 VDC applications.
Greases are used as a method of lubricating with oil. The oil is held in a thickener which acts much like a sponge. Greases fail for a number of reasons but as the oil provides the lubricating properties of the grease, it is important to understand why both the grease and the oil fails.
Oil degradation caused by oxidation, which results in a permanent change to the oil molecules, will mean more frequent re-lubrication is required to replace both the degraded grease and any contaminants which the oxidation has created.
The main cause of oxidation is elevated temperatures. Generally the rate of oil oxidation doubles for every 150C above 700C. Therefore the life of the oil (and hence the grease) is halved for every 150C rise above 700C.
Degraded oils break down into by-products of the reaction that are harmful to bearings. These include carboxylic acids which will corrode surfaces if left in the system and sludge and varnish will form over time.
Higher temperatures also increase the rate of oil evaporation and bleeding from the thickener, which reduces the lubrication properties of the grease.
Additives that enhance the lubrication properties of the oil such as friction modifiers, corrosion inhibitors, antiwear agents, oxidation inhibitors, EP improvers and adhesion improvers have a finite life and become depleted in use. Once this occurs the grease and the oil in it can no longer perform to its original specification.
Other factors which reduce the grease and oil life and therefore the re-lubrication interval are:
• dust
• materials and by-products created by wear and lubricant degradation.
• humidity and condensation (daily or operational temperature cycles will cause the air trapped in the housing to become a condensate).
• water and process-related liquids
The limit for the absolute water content in mineral oil - the lubrication component of most greases - above which problems will occur, is 200 ppm
• vibration - high vibration will cause the grease to churn which will cause a grease life reduction. Vibration will also cause the grease to bleed more than normally, resulting in an increase in the hardness of the grease, limiting its
ability to correctly lubricate rolling contact bearings.
• strong air flow or reduced air flow through the bearing (drying of grease, oxidation, removal of microscopic oil droplets)
• the above factors will each cause a grease life reduction factor of between 0.4-0.7x the normal grease life in a single row spherical roller bearing. The reductions are cumulative for each cause and are in addition to the effect of temperature on the grease.
Continuous lubrication is the best preventative method to protect against the build-up of contaminated or degraded grease. If contaminants have built up in the housing then to fully remove them the housing must be opened and the bearings and housing thoroughly cleaned. An alternative is to purge the housing however whilst that may remove most of the contaminants it is unlikely to fully remove them all. If the contaminants are not removed then the bearing life will be decreased. It is more efficient and cost effective to use continuous lubrication to prevent the build-up of contaminated or degraded grease. Greasemax
Sydney Water relies on GormanRupp Grit Pumps at its Bondi wastewater treatment plant.
The plant has four channel-type grit inlets, and each has Gorman-Rupp six-inch Super T Series pump sitting on a moving bridge above these channels to vacuum up the grit that sinks to the bottom of the channels.
When the plant had to make a call on repairs to two of the pumps, it relied on Hydro Innovations as authorised Australian distributor for Gorman-Rupp pumps to do repairs with genuine parts to specifications in operations manuals. Repairs were turned around quickly because Hydro Innovations had all required parts on the shelf.
The Bondi plant has been using Gorman-Rupp pumps in this application for more than 30 years.
During this time, Gorman-Rupp has developed harder materials to cope with abrasive applications such as this where grit and sand are
pumped. Sydney Water was one of the first Australian organisations to recognise the benefits of these harder components in equipment which result in less downtime and longer intervals between repairs.
Being self-priming, pumps can be located above the water, in a safe, easily accessed position which enables quick, easy monitoring and repair. Cranes are generally not required to access pumps, and inspection covers allow operators to gain access to pump internals without removing the pump from the pipe system. A patented internal clearance adjustment system also allows one operator with just two spanners to safely adjust clearances in minutes to keep pumps at peak efficiency for the life of the installation.
Pumps are available in sizes from 50mm (suction and discharge) through to 250mm, with flows from just a few litres per second through
Hydro
hydroinnovations.com.au
rotect-Air provides a variety of in-line protection units developed for fluid and compressed air systems to tackle workplace health and safety issues as well as increase efficiency and ensure economical production.FluidReg® provides a constant and stable output pressure regardless of the inlet pressure. This preset, independent regulator can be used in any fluid system.
The in-line FluidReg® protects all equipment and components placed after it, ensuring they only receive the correct pressure. This is particularly important for liquid-dosing machinery because it prevents expensive loss of production. The specified pressure is factory set, ensuring safe, tamper-free operation.
The EcoReg® is made of Grivory® GV-5 FWA, which is an FDAcertified material that is ideal for critical application areas such as drinking water, food industry, medical industry and other fluids. The EcoReg® is NSF certified.
An independent diaphragm pressure regulator, the pre-set EcoReg® fluid regulator can be installed in all fluid systems. The pressure value has been factory set and cannot be changed, ensuring a constant and precise output pressure independent of the input pressure.
Check valve
Resistors are among the cornerstones of modern electronics. The small, but vitally important components are the basis for virtually every electronic circuit. Choosing the right value and power of the resistor is one of the challenges for today’s electronics designers, as incorrectly selected components can result in a device failure in the future.
Royal OHM, a Thailand-based company, is one of the leading manufacturers of resistors. Its products are available from TME.
SMD power resistors (SP series)
Widespread miniaturisation has extended to include not only integrated circuits, but also surface-mounted (SMD) power resistors. Royal OHM’s SMD power resistors are an interesting alternative to classic components that can dissipate significant amounts of energy.
In the TME catalogue, you will find models rated at 2 W, 3 W, 4 W, 5 W and 6 W. The components are available in the classic resistance variants from 0 Ω to 10 MΩ, and in various package sizes: 2010, 2512,
2817, 4320, and 4527. Besides, the resistors are designed to operate at temperatures from -55°C to 155°C with a tolerance of +/-1% or +/-5%.
Apart from the SP series, Royal OHM supplies classic surface-mounted (SMD) resistors, rated at 31.25 mW. They are available in
a wide range of resistance values (from 0 Ω to 10 MΩ) and are placed in 01005 packages (in the metric standard, this size is described as 0402). The low-power resistors are also designed to operate at temperatures from -55°C to 155°C, and their tolerance is in the similar range of +/-1% or +/-5%.
These SMD resistors are miniature components enclosed in a 01005 housing. In the metric standard, this format is designated 0402, i.e. the area of the base is enclosed in a rectangle with sides of 0.4mm and 0.2mm. Such compact elements are commonly applied in compact mobile devices (e.g. circuits of cellphones, tablets) and complex digital electronics systems (computer motherboards).
The presented resistors are distinguished by a wide thermal tolerance, reaching from -55°C to 125°C, as well as precise tolerance (±1% or ±5%). Their nominal power amounts to 1/32W – which fulfills the electrical requirements for most typical applications with room to spare.
To conclude, we wish to highlight that these resistors have been introduced into TME’s offer in all typical values (270 nominals in total), which encompass resistances from 0 Ω to 10MΩ
TME tme.com
Everything you need to keep it together
United Fasteners’ latest catalogue
United Fasteners has prioritised
user experience in the catalogue’s design. The intuitive layout and detailed product descriptions make it easier for customers to find the right solutions for their specific needs. Additionally, the catalogue features a comprehensive index and cross-referencing system for quick and efficient navigation.
In addition to the printed version, United Fasteners offers a digital flipbook version, accessible on its website.
This digital format allows customers to browse the extensive product range conveniently, access detailed specifications, and make product enquiries directly online, streamlining the procurement process.
United Fasteners has a wide range of technical resources available to download for free on their website, from conversion charts, assembly torque guides and much more.
With a focus on energy efficiency, BOGE has expanded its portfolio with the new SO-3 oil-free screw compressor that achieves peak delivery rate values at a lower specific power consumption.
With the introduction of the SO-3 oil-free screw compressor, BOGE has considerably improved the energy efficiency by eight percent.
This increase is based on an intelligent concept. The newly developed airend of the compressor convinces with its very low speeds and subsequently low compressor temperatures, as well as its extremely wear-resistant design.
The integrated IE4 drive motor also contributes to its efficient and cost-effective operation. Even though the screw compressor is very compact, the components are still easily accessible for maintenance purposes.
Specific sound insulation measures have been implemented to effectively reduce noise levels.
The compressor is available with frequency control and heat recovery, as required. BOGE thus offers maximum flexibility and additional options to increase efficiency. The heat recovery enables up to 94 percent of the applied energy to be used to heat the service water and for the heating system. The screw compressor heats the service water
up to 90°C.
Optimum adjustment to existing requirements
BOGE offers maximum flexibility (VSD and Heat Recovery) and additional options to increase efficiency.
The heat recovery enables up to 94 percent of the applied energy to be used to heat the service water and for the heating system. The screw compressor heats the service water up to 90°C,” explains Lutz Knoke Product Manager at BOGE to Zahid Rasool Managing Director BOGE Australia who was in Germany.
With options to connect adsorptions dryers and other accessories, the new SO-3 screw compressor
from BOGE is a customised solution for a variety of applications.
The screw compressor is designed for applications that require large quantities of high-quality, oil-free compressed air. This ensures the compressor can be used in a variety of applications in different sectors, including the pharmaceutical, food and drinks industry right through to the textile industry, mechanical engineering applications and by industrial coating companies.
BOGE boge.com
The Workplace Health & Safety Show is back - bigger and better than ever with a refreshed look and feel.
Recently acquired by Australian events and exhibitions specialist, National Media, the show now boasts a revamped education program, rounding out its comprehensive offering. “We like to work in a space where we can really add value. Our events solve problems for the audience and create a platform where suppliers and vendors achieve their objectives,” explains Stephen Blackie, Commercial Director, National Media.
“Behind the show and on a larger scale you can see the impact it has
on the world. Health and safety are such a huge concern – one death is too many. We want to provide an event where organisations can find the tools, knowledge, best practise, technology, and equipment they need to create a healthy and safe place of work. Working on an event like this gives us a greater feeling of value and worth – that what we are doing is right for the world and the greater community, not only for the industry,” said Blackie.
“We strive to deliver an event that puts Australia on the global map as innovators and world leaders in health and safety. With this in mind, our end goal is to create the best safety event in the world,” he said.
The show will focus on delivering a highly relevant, finger-on-thepulse, free to attend education program, along with game-changing products and services.
According to Blackie, the show has grown by 25% and currently sits at over 130 exhibitors who will be showcasing the latest technology and products, much of which has never been seen before. Visitors will be able to touch and see demos of what’s new in Work Health and Safety solutions.
“Companies in this sector are incredibly innovative. We are particularly excited about the level of new technology that will be on show this year.”
This year’s show will also showcase the redesigned Spotlight Stages and Knowledge Centre, making them more comfortable, and geared-up for a great learning experience.
“We realise that in addition to all the great reasons visitors come to a show, networking opportunities, and meeting up with peers are also an important component. A signature of National Media events includes a central lounge where visitors can take a break or catch up on emails, and use the opportunity to network,” he added.
The 2024 show kicks off in Melbourne from 22-23 May, and then takes place in Sydney from 23-24 October, empowering visitors with the latest OHS tools, insights, and resources.
The 2024 Workplace Health & Safety Show will feature three theatre stages, including:
• A new Summit Stage, packed with more content. Already confirmed on the program are half-day summits on Worker Wellbeing, and Health and Safety in Construction.
• “Key areas of concern for our audience are the psychosocial laws and how workplaces can support their people. Meanwhile, the construction sector experiences a high proportion of injuries, accidents, and deaths. Our focus is on helping construction companies better understand the risks and improve their safety and compliance. This industry is modernising and faces constant changes, for example there’s new industrial
manslaughter legislation coming in July; key stakeholders need to be aware of how to navigate the new guidelines,” explained Blackie.
• The Spotlight Stage, showcasing a vast array of products and services available to the local market.
• The Knowledge Centre, where industry experts will explore workplace safety and health through interactive forums and talks on topics including safety technology, injury prevention and worker wellbeing, measurement of safety performance, and psychosocial hazards – among others.
The complete free education program will be available soon, at www. whsshow.com.au
The Workplace Health & Safety Melbourne Show runs alongside the AIHS National Health and Safety Conference 2024. Show partners and sponsors include the Victoria Chamber of Commerce and Industry, WorkSafe Victoria, SkyTrust and the Working at Height Association – to name a few.
The show is already over 80% allocated, with only a limited number of exhibition spaces remaining.
“Get in quick to be part of this exciting industry event,” said Blackie. “Register today for your free ticket and join the community of people building the world’s safest companies.”
When and where:
• Wednesday 22 – Thursday 23
May 2024 Melbourne, Melbourne Convention & Exhibition Centre
• Wednesday 23 - Thursday
24 October 2024, Sydney Showground, Olympic Park
WHSShow
whsshow.com.au
In industrial settings such as manufacturing, oil and gas operations, mining, agriculture, pharmaceuticals, and construction sites, the potential for exposure to hazardous substances looms large.
When chemicals come into contact with the eyes or skin they can cause severe damage within seconds.
Emergency safety showers and eye/face wash stations are crucial for prompt, efficient decontamination in the event of exposure to hazardous substances. That’s why they’re so vital in the workplace.
Spill Crew emergency showers and eyewash are designed to accommodate a wide range of industries and applications. This range of products includes combination showers with eyewash or eye/face wash, deluge showers, eyewash stations, eye/face wash stations and portable, gravity-fed units.
There are several requirements to make sure safety showers and eye/
face wash equipment complies with the Australian Standard AS 4775 including: flushing fluid flow rate required water temperature, valve control, nozzle design and performance, lighting, signposting, testing and maintenance requirements.
Spill Crew emergency shower and eyewash range are not only fully compliant with the standard but are independently tested for compliance by a NATA accredited laboratory.
Manufactured to withstand the harsh Australian conditions, Spill Crew shower and eyewash units are made from premium marine grade 316 stainless steel for superior corrosion resistance and durability, when compared to 304 stainless steel, also offered in the industry by others.
Built with high quality craftsmanship, the engineered OptiStream spray heads deliver a gentle, low velocity stream to the eyes and face to gently flush away contaminants.
The feature easy to clean filters, flow regulators and self-opening covers to protect flushing fluid from airborne contaminants.
The entire Spill Crew range of safety showers and eyewash is available now at Global Spill & Safety. High
levels of inventory of the entire range nationally are ready for immediate dispatch Australia wide.
Global Spill
ECD is an innovative company.
Since their development of the first 2-wire conductivity transmitter, ECD has been at the forefront of analytical measurements in water based applications.
Their innovation continues with the introduction of its new self-cleaning oil-in-water sensor, the OIW80.
The identification of oil in water and measurement of small quantities helps municipal water and wastewater facilities as well as industrial plants to quickly and accurately detect oil in water leak incidents.
Engineers at municipal water or wastewater facilities and industrial plants will find that the new OIW80 Sensor helps them to quickly, accurately and economically detect oil in water leak incidents that require fast response actions to prevent further contamination of drinking water, fouling of batch processes, damage to plant equipment and/or contamination of sensitive water ecosystems.
The sensor
The OIW80 Smart sensor is a
precision sensor that reliably measures oil in water over a range of 0 to 30 ppm (mg/L).
It can be factory preconfigured to measure oil in multiple ranges or easily set in the field, states the company.
A rugged, high-performance and responsive sensor, it operates over a temperature range of 5 to 45⁰C
and quickly detects oil, alerting plant technicians to leaks and spills in Industrial plants or of water treatment problems in downstream assets.
Designed for demanding and/ or dirty plant environments, the highly dependable sensor features a built-in wiper cleaning system to remove bio solids and films that
might cloud the sensor window’s visibility. The built-in ‘window wiper’ reduces the number of manual checks by technician and also reduces the frequency of scheduled cleaning maintenance.
Integration of the measurement into control and data acquisition is critical. ECD provides various options. The two-channel T80 Universal Transmitter or ECD’s eight-channel LQ800 controllers give plenty of scope. By utilizing the RS485/Modbus output, a wide range of compatible third-party controllers are also available.
A benefit of connecting ECD’s Smart sensors to the versatile ECD T80 transmitter or the ECD LQ800 controller, is that the sensor’s information is automatically uploaded to the analyser.
That device then configures the displays and outputs of the transmitter to the values appropriate to the oil sensor’s measurement parameters.
Technology is changing so much in our daily lives, including in how we get around. The electrification of vehicles, autonomous vehicles and connected systems within cities are no longer far off dreams, these technologies and a more connected automotive ecosystem are more of a reality in Australia than ever before.
In the early 2000s, electronics accounted for less than 20% of the total cost of a vehicle. In 2020 it was up to 40% and we expect electronics to account for about half of the price of a new car by 2030.
We’re also expecting to see 300 million electric vehicles (EVs) on global roads by 2030. Technology is pushing the transportation industry forward more quickly than many expected.
So, how do we ensure we’re ready? How do private companies, cities and the people building the infrastructure to support this transformation come together to make this a reality? What technology is on the horizon?
That’s what our team at DigiKey, along with our partners, are working to understand.
There are many ways technology has improved how we get around, the efficiency in which we do so and the safety of our cars. I’m excited about these advancements and how
they’re changing and improving transportation for all of us.
• Eliminating the need for a human driver – To maintain a competitive edge, many companies are looking toward driverless vehicles to cut costs and increase efficiency. With autonomous capabilities, we will see material transport and rideshare services operating with nobody in the driver’s seat.
• Battery Optimization – Similar to how AI learns your phone use, patterns and behaviours and charges your phone accordingly to best utilize your battery and increase its longevity, I expect this to be possible with car batteries in the future. Batteries are expensive, and an important factor that dictates the lifespan of a car, and these advancements will help keep EVs on the road for longer.
• Predictive maintenance – This is the ability to estimate, or predict, when maintenance should be performed on a vehicle. There are already sensors within cars and trucks, and I expect that we’ll continue to see more and more of this, monitoring the different parts of a vehicle – like the engine, brakes and any other moving component. If problems can be detected early and repairs can be made, this avoids costlier, and often time-consuming, catastrophic failures down the line.
• In-cabin assistance –Technologies utilized on the outside of vehicles for environment perception, such as machine vision and mmWave radar sensors, may also be used inside the cabin to monitor the driver’s heart rate, breath rate, head movements, eye movements, etc. to determine whether they are tired or unable to operate a vehicle safely.
• IoT and Cars – When you bring
your car to a mechanic, they will be able to connect to it via their phone, getting a full rundown of what’s going on before ever opening the hood of the car. They can start diagnosing problems faster and more efficiently.
The ability for vehicles to connect not just with each other, but also with mobile devices and smart ecosystems (smart cities, smart infrastructure, etc.) is an exciting prospect. Rather than rely solely on machine vision systems to perceive what’s around them, key objects within communication range can provide feedback to reduce computational burden and increase confidence in what the vehicle “sees”. These objects could include smartphones to identify pedestrians, traffic lights to manage traffic flow at intersections, and road signs to enforce traffic laws.
Furthermore, smart infrastructure has the potential to streamline how autonomous vehicles navigate from point A to point B. Beacons staggered along roads and streets can broadcast location data for vehicles to utilize when GPS signals are weak or lost entirely (e.g., when driving through tunnels or amongst tall buildings).
Smart parking meters can charge vehicle owners directly, based precisely on how long the space was occupied. Streetlights can increase their brightness as vehicles approach them to increase visibility and decrease their brightness the remainder of the time, to conserve energy. The possibilities are truly endless.
At DigiKey, we understand the importance of having the right products available to enable innovation. We have a huge selection of automotive products available in Australia, along with application details, articles and technical resources, that keep the smartest minds in the industry moving us forward. Through our partnerships with industry leaders like ADI, Texas Instruments and Microchip Technology, we provide Australian engineers and designers with topof-the-line integrated circuits, semiconductors and microprocessors.
DigiKey digikey.com
From boardrooms to workshop floors, we hear constant noise of ever-increasing change sweeping through the Australian manufacturing industry. There is no denying the landscape is evolving, and as leaders in this dynamic sector, we are compelled to ask not just what will change but, more crucially, what will remain constant.
In the words of Amazon’s Jeff Bezos, the important question that often gets overlooked is, “What’s not going to change in the next 10 years?” This perspective is not just a philosophical musing but a guiding principle for strategic business planning. What will not change is customers’ desire for cheaper products; better service; more convenient delivery; and better quality or value. So how do we position our offer to move the dial on these unchanging drivers?
Focus on the core
The aim is to thrive amidst the constant shifts. In the quest for growth, it is time to fortify your marketing foundations, introducing fundamental rigor and discipline. This is not a call for reinvention; it is a call for identifying and articulating the core within your go-to-market approach, spotlighting your high-value work that delivers exceptional results.
The high value but sometimes overlooked aspect of your offer
Many manufacturing and industrial businesses boast a strong heritage and technical legacy. Yet these strengths are often not brought to life via a compelling sales narrative or an inspiring look and feel. While technical products and widgets may be the heart of your offering, the arteries that supply lifeblood to your business are the often-overlooked value-added services – the behind the scenes engineering consulting, testing and QA or project management services that underpin your
I.M.Aclients’ product development.
Rich Australian manufacturing heritage is important as are good quality widgets, however they can’t do all the heavy lifting and be expected to make your offer distinct from your competitors. What will move the dial is your unique method and way of talking about the problems you are solving for clients. For example, through your consulting engineering or project management that are the high value and distinct parts of your core, but they need to be brought to the forefront. The opportunity is to reposition your brand, not as a mere product provider, but as a solutions provider, highlighting the tangible value you bring to your clients.
Here are some practical takeaways to refine your marketing approach in 2024:
1. Strategy framework: discovery and analysis
Insights lead to change, and change is what will propel your business forward. Conduct a thorough brand audit and market analysis, evaluating competitors and engaging key stakeholders. Craft a tailored marketing strategy aligned with your business objectives and market dynamics. This isn’t just about awareness; it’s about understanding
and responding to the insights and adapting the offer.
Your brand is not just a logo; it’s your promise to the market. Clarify your unique value proposition, craft a cohesive brand story, and create brand guidelines for consistency. Refresh the visual identity to reflect your positioning as a solutions provider. Your brand is your first impression – make it count. The famous Ren Jones quote says, ‘Marketing is the equivalent of asking someone on a date. Branding is the reason they say yes’.
Your website is your virtual storefront. Assess its usability, develop user personas, and redesign it with a focus on user experience. Showcase your expertise and problem-solving capabilities. Integrate SEO best practices to enhance online visibility. Your website should be a reflection of the solutions provider you are positioning yourself to be.
Your collateral is your voice when you’re not in the room. Review existing collateral, understand your audience’s preferences, and create
tailored materials for each market segment. Launch a suite of cohesive marketing collateral aligned with your new brand messaging. Every piece of collateral should echo the narrative of your solutions-driven approach.
A strategy is only as good as its execution. Launch the redesigned website, introduce the new brand messaging across all communication channels, and deploy targeted marketing campaigns. And a quick bit of advice – campaigns that use multiple channels are significantly more effective. Combine trusted industry publishing voices with social media, radio, and direct marketing. Don’t just be present; be omnipresent.
As we position ourselves for growth in 2024, let’s not get too distracted by the constant change. Instead, let’s focus on the things that will remain constant – our expertise, our commitment to excellence, and our unwavering focus on delivering value. It is not about chasing trends; but uncovering and then focusing on what really matters.
The government says more than 10,600 places for fee-free study were used in 2023 in areas of priority for the government including the health systems, early childcare, delivering SA’s infrastructure needs and building the defence force for AUKUS.The government says 2023 was the first time enrolments increased year-on-year since 2012.
Students taking up the free study included women in non-traditional fields (30%), veterans (13%), students speaking a language other than English at home (11%), people with a disability (9%) and First Nations students (5%).
Health-related courses have been popular with students, including the fee-free Certificate III in Pathology Collection, which recorded a 16% increase in enrolments since the introduction of the fee-free initiative, with 113 students enrolled in the course in 2023.
Other courses with strong interest include the Certificate III in Early Childhood and Care, Certificate IV in Plumbing and Services, Diploma of Nursing, and Certificate II in Electrotechnology (Career Start).
“We are thrilled with the response to fee-free TAFE and this has contributed to a return to growth in enrolment numbers over the past 12 months,” said TAFE SA Chief Executive David Coltman.
“With the support of state and federal governments, we have over 4,500 additional fee-free TAFE places for the next three years and it has been wonderful to hear the stories of many new students who have been able to enrol in study thanks to this initiative.”
In October last year, a new five-year National Skills Agreement was announced, with a $2.289 billion investment in training and skills for South Australia. That includes a boost for TAFE SA to fund extra training places, capital works upgrades and extra support services for students.
T
AFE NSW is equipping women for careers in the male-dominated supply chain industry and keeping NSW’s economy moving amidst a supply chain jobs boom.
The supply chain industry is forecast to grow by another 39,000 jobs over the next three years, yet Australian government data shows women comprise less than a quarter of the supply chain workforce.Western Sydney local Rayleen Woods discovered a passion for the supply chain industry after working as a forklift and crane operator for a large steel manufacturer and has since climbed the ladder at SCT Logistics Group to become a Regional Allocator.
Beginning her career in nursing, Woods’ switch to supply chain quickly provided opportunities, taking her from a temporary warehousing coordinator role to diving into study with two Certificate IVs in Warehousing and Logistics Operations and a Diploma in Logistics at TAFE NSW.
Her success was recently recognised at the Australian Supply Chain and Logistics Awards, the industry’s most prestigious awards ceremony, where she received the title of Highly Commended in the Future Leader category.
“When we talk about warehousing and logistics, it’s much more than loading and driving trucks. There is a large practical element for people who want a hands-on job but also many coordination and management opportunities,” said Woods.
“Supply chain is typically a male-dominated industry but is a very supportive work environment, and there is so much opportunity for women to develop a successful career and create a good work-life balance.”
Woods is now managing a large trucking contract in the Dubbo region and completing a Diploma in Logistics. She hopes her experience will encourage more women into the supply chain industry.
“The skills I gained at TAFE NSW have made all the difference in helping me get ahead in my career, and I use them in my job every day. My teacher Michael used his experience and networks to help me to explore available job roles and he supported me in applying for my current
Rayleen Woods accepts her ASCLA Future Leader award with TAFE NSW teacher Michael Farragher and TAFE NSW Director of Supply Chain Chris Greentree
position,” said Woods.
“There are also different study options at TAFE NSW to help you manage work and family while gaining the skills you need to grow your career.”
“TAFE’s course delivery options are helping make supply chain and logistics an accessible career option for more women. Their inclusion can lead to more innovative solutions, better decision-making, and improved performance in an industry that’s vital for global commerce,” said Woods’ teacher, TAFE NSW Teacher of Supply Chain and Logistics, Michael Farragher.
“Whether it’s operating a forklift or managing a supply chain, TAFE NSW is providing the latest in industry-specific training that equips students with the necessary skills to thrive in various roles within the supply chain and logistics sector.”
12-15 March 2024 | MCEC, Melbourne
Australasia’s Processing and Packaging Expo is an exhibition that will truly represent all sectors of the industry, including machinery, ancillary equipment, materials and packaging, food processing and industry services. It will provide a comprehensive range of all processing and packaging equipment and services under one roof..
appex.com.au
AMW 2024
17-19 April 2024 | ICC, Sydney
Australia’s premier manufacturing technology trade show, Australian Manufacturing Week (AMW 2024), promises to be a dynamic event that brings together professionals, companies and experts from many industries related to manufacturing, engineering and technology. Organiser AMTIL’s goal is that AMW 2024 is more than an exhibition. Rather, it is to be the centrepiece of a week-long celebration of manufacturing in Australia.
australianmanufacturingweek.com.au
Sydney Build Expo
1-2 May 2024 | ICC, Sydney
Now in its 8th year, Sydney Build is the best-attended Construction & Design Event in the whole of Australia. The two-day event showcases all the latest opportunities in NSW and Australia. The event connects all key players in the industry and attracts attendees from: contractors, architects, engineers, housebuilders, developers, government and construction professionals.
sydneybuildexpo.com
Foodservice Australia
19-21 May 2024 | ICC, Sydney
Don’t miss this chance to see the latest equipment, taste the food trends and find out what’s new in the industry. Discover over 450 exhibitors plus chef competitions, three conferences and plenty of free workshops and demonstrations.
foodserviceaustralia.com.au
ARBS 2024
28-30 May 2024 | ICC, Sydney
ARBS 2024, the Air Conditioning, Refrigeration & Building Services Exhibition, is Australia’s only international HVAC&R and building services trade show. ARBS provides the most
comprehensive range of HVAC&R and building services products and solutions in one location, allowing the entire industry to connect across three days.
arbs.com.au
Electronex
19-20 June 2024 | Rosehill Gardens, Sydney
Australia’s major dedicated expo and conference for the electronics industry, Electronex, returns to Sydney at Rosehill Gardens Event Centre in 2024. At Electronex designers, managers, engineers, technicians, manufacturers and system integrators can discuss their specific requirements with industry experts and see, test and compare the latest products and solutions to future proof their business.
electronex.com.au
CeMAT
23-25 July 2024 | MCEC, Melbourne
The CeMAT exhibition will be a onestop-shop of the leading technology and service providers in intralogistics, robotics and automation, warehousing, supply chain management and materials handling.CeMAT will showcase innovation and best practices in a wide variety of settings and sectors – from e-commerce to manufacturing, from the food industry to resources.
cemat.com.au
Australian Waste & Recycling Expo
24- 25 July 2024 | ICC, Sydney
Discover an exciting showcase of full circle innovative products and sustainable solutions to collect, process and recycle waste more smartly. Future critical areas include Machinery & Equipment, Software & Services, Bins, Vehicles, Food & Organics and more.
awre.com.au
LAND FORCES 2024
11-13 September 2024 | MCEC, Melbourne
A variety of exhibition and participation options are available and, as a centrepiece regional exhibition, the opportunities for business engagement at Land Forces will be considerable.In addition to hosting senior international military, defence, government, scientific and industry delegations from around the world, Land Forces will attract a comprehensive array of defence professionals and trade visitors at all levels.
landforces.com.au
Australian Manufacturing Week (AMW2024) is a huge event that will occupy more than 6,560 square metres of exhibition space at the Sydney ICC at Darling Harbour in April. More than 215 organisations have already taken stands to showcase the latest manufacturing technologies, processes, and support services.
AMW2024 is run by the Australian Manufacturing Technology Institute Limited (AMTIL), with the NSW Government as major sponsor. There will be seven zones on the show floor of Australian Manufacturing Week, each showcasing its own areas of expertise. These include:
• The Austech Machine Tools Zone will target the metalworking, machine tool and ancillary market in the global manufacturing space. The Austech Machine Tool Zone is proudly sponsored by Finlease.
• The Additive Manufacturing Zone will showcase techniques within Additive Manufacturing including stereolithography, selective laser sintering, material extrusion, sheet lamination, binder jetting, cold-spray processing, material jetting, directed-energy deposition, and among other advanced additive manufacturing technologies.
• The Australian Manufacturers Pavilion showcases the capabilities of Australia’s precision engineering and advanced manufacturing industry and the best in Australian manufacturing.
• The Manufacturing Solutions Zone will offer a concentration of optimised solutions to the most common challenges experienced by manufacturers. From materials handling and warehousing to integrated manufacturing
and safety solutions. Sponsored by The Execution Factor, the Manufacturing Solutions Zone incorporates everything from equipment for materials handling and logistics, to safety and software products.
• The Robotics and Automation Zone will feature the latest state-of-the-art equipment and processes for optimising manufacturing operations. There will be industrial robotics, automated solutions, instrumentation control systems, measurement, pneumatics, IOT solutions, industry 4.0 and digitalisation.
• The Weld and Air Solutions Zone will highlight advanced welding processes and provide high-quality interactive experiences that demonstrate the latest developments and applications in the welding sector. Welding is critical in metal fabrication and manufacturing. In fact, it is used in creating more than half of all products made in Australia today.
• The Plastic Technology Zone is a chance to see and feel the latest in plastics machinery, mould-making technologies, recycling materials, and the many plastics manufacturing processes. Plastic technology is a specialised branch of study which includes diverse types of chemicals that exhibit plasticity. Now is the time to register for your attendance at AMW2024. Don’t miss out: this is THE show not to miss!
Sydney ICC Darling Harbour , 17-19 April, 2024
To register, visit australianmanufacturingweek.com.au
australianmanufacturingweek.com.au
Decentralized automation solutions are shifting the coordinates of modern industrial production. We‘ll set you on course to success.