management
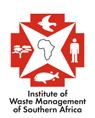

Innovation
How the construction industry is capitalising on recycled polystyrene
Sustainability
Local and international industries merge to tackle marine litter
management
Innovation
How the construction industry is capitalising on recycled polystyrene
Local and international industries merge to tackle marine litter
Investment
Realising value from Africa’s waste stream
Technology
Harnessing the power of renewable energy resources
Heavy industry is a critical part of our economy. But disposing of the waste they produce in a way that’s safe for people and the environment takes years of expertise, scientific savvy and biochemistry knowledge.
Not just anyone can do it. That’s why EnviroServ employs the most highly-qualified professionals for the job.
Like our Industrial Services Manager Henco Swart. With eight years’ experience in the Hazmat and Industrial Services field and dozens of projects planned and executed, he takes pride in helping to run a compliant operation. In his leisure time, Henco participates in fire challenges, which encourage firefighter fitness, completing events while dressed in full protective gear. The skills and commitment required in this job are closely related to his own work – protecting lives and preventing the destruction of property and our natural environment.
Because expertise is important, but so is having employees who live the EnviroServ values of passion and integrity, who are dedicated to working towards delivering waste solutions that are environmentally responsible and effective.
Waste’s founder and CEO, Dr Phetole David Sekete, discusses how the company has grown from humble beginnings to become one of the largest waste treatment companies in the country. P6
Every new year, many of us ponder how to become a better person than we were the previous year. Typically, we undertake to eat/drink less and exercise more, but I’m yet to hear of anyone with the new year’s resolution of generating less waste than the year before.
WasteCon 2018 is set to be held during 15 to 19 October 2018 at Emperors Palace, with the theme being ‘Implementing the Waste Hierarchy’ – indeed a very appropriate theme for people with a new year’s resolution to generate less waste.
The waste hierarchy consists of two spheres of responsibility. First, there is the responsibility of the generator of waste – that is us – to avoid the generation of waste and also to reduce the waste we do generate. The objective of these two actions is to give less waste to the service authority (municipality), which means putting less waste on your sidewalk on collection day.
This can be achieved without much cost to the generator, through a simple focus on buying items that are packaged in recyclable material, refusing extra packaging material such as carrier bags when only buying one or two items, and buying only the quantity of fresh vegetables needed at the time. The waste that the average homeowner puts out for collection consists
mainly of packaging material and food wastes, and both can easily be reduced. The other sphere of the waste hierarchy is the responsibility of the service authority. Their main objective is to divert as much collected waste as possible from landfill.
This can be done by recovering the recyclables, either via source separation or via a materials recovery facility, chipping and composting garden waste, composting or digesting (anaerobically) organic (food) waste, crushing builder’s rubble to be used as fill material and, finally, if there are sufficient quantities of waste, the application of thermal technologies.
n o longer can we reach the end of another year and look back only to realise that we have done nothing to reduce our waste footprint
Only the waste that remains after all the above diversion alternatives have been applied should be landfilled. This is what integrated waste management is all about.
Unfortunately, recent studies conducted in the Southern Cape have shown that, when applying the relevant norms and standards, all the above diversion alternatives are financially more expensive than disposal, except for the crushing of builder’s rubble. That is perhaps why so few of these diversion technologies have been implemented at our municipalities. But implementing these technologies is the right thing to do and the costs associated with doing the right thing are justifiable, since we only have one Planet Earth. No longer can we reach the end of another year and look back only to realise that we have done nothing to reduce our waste footprint. The current water crisis in Cape Town is a reminder for us all to be proactive with waste management. Please attend WasteCon 2018 and let us join hands in implementing the waste hierarchy in Southern Africa.
1
The official magazine of the
Trade and technical print magazines remain the most powerful method for getting your message across in the South African b2b market.
2
A 2016 report by Neilson found that for every one dollar spent on advertising in magazines, four times as much money came back to the advertiser, giving magazines “the highest ROI of all marketing media”.
3 A 2015 report from Neilson concluded that magazines yield the highest ROI of all media, using just 10% of ad expenditure.
4
The Entertainment and media outlook: 2016 - 2020, published by PwC South Africa, found that South Africa’s b2b market, including magazines, directories and online resources, made R9.5 billion in 2015 and is forecast to grow at a 4% CAGR to reach over R11.6 billion in 2020.
5
In a survey looking at consumers’ behaviour in the US, international research company Toluna found that 80% of respondents indicated a clear preference for reading print on paper.
6
Hubcast, a cloud print solutions company, published a recent research paper titled 10 reasons why print isn’t dead, why marketers need to print. The report explores the following reasons for a resurgence in print over the past year:
• Print is easier to read and navigate
• Print readers retain information better
• Digital reading fosters skimming
• Print is tactile
• Print is more credible
• Digital reading can have negative health implications
• Millennials love print
• Print is sustainable (more so than screen reading which requires electricity and fossil fuels)
• It is easier than ever to print globally
7
E-commerce giant Amazon, originally started as an internet-only retailer, has since begun building more and more physical bookstores and other retail outlets so that consumers can touch, feel and more fully experience their products.
• ReSource (quarterly) promotes integrated resources management, with a focus on waste management and cleaner production. It is the official magazine of the Institute of Waste Management of Southern Africa (IWMSA) and is endorsed by 12 industry associations.
• IMIESA (monthly) is the official magazine of the Institute of Municipal Engineering of Southern Africa (IMESA), focusing on infrastructure development, maintenance and service delivery.
• Water&Sanitation Africa (bi-monthly) is the official magazine of the Water Institute of Southern Africa (WISA), dealing with the preservation, treatment and provision of water.
• www.infrastructurene.ws is a leading news hub for infrastructure development and service delivery, linked to social media platforms.
We are market leaders in combining our print products with multimedia offerings to create content marketing campaigns across print and digital platforms.
Book a cross-platform package with print at its centre, and enjoy:
• greater credibility
• more reach and engagement
• extended brand awareness with your target market.
Publisher Elizabeth Shorten
Editor Candice Landie
Assistant editor Liesl Frankson
Managing editor Alastair Currie
Head of design Beren Bauermeister
Designer Ramon Chinian
Chief sub-editor Tristan Snijders
Sub-editor Morgan Carter
Contributors Roelien du Plessis, Susan Oelofse, Jan Palm, Fhumulani Ruth Ramukhwatho, ROSE Foundation
Client services & production manager Antois-Leigh Botma
Financial director Andrew Lobban
Distribution manager Nomsa Masina
Distribution coordinator Asha Pursotham
Printers United Litho Johannesburg
Advertising sales Jodi Haigh
Tel +27 (0)11 467 6224
Cell +27 (0)83 710 9788 jodih@lantic.net
Publisher No.9, 3rd Avenue
Rivonia, 2191
PO Box 92026, Norwood 2117
Tel +27 (0)11 233 2600
Fax +27 (0)11 234 7274/5
www.3smedia.co.za
Annual subscription subs@3smedia.co.za
R200.00 (incl VAT) South Africa
ISSN 1680-4902
Institute of Waste Management of Southern Africa
Tel: +27 (0)11 675 3462
Email: gail@iwmsa.co.za
All material herein is copyright protected and may not be reproduced either in whole or in part without the prior written permission of the publisher. The views and opinions of authors expressed in the magazine do not necessarily reflect those of the publisher, editor or the Institute of Waste Management of Southern Africa.
Welcome to 2018 and the industry’s first issue of ReSource for the year. As a former editor of ReSource myself, having worked on the publication six years ago, I am thrilled to be back at 3S Media. I am joined by assistant editor Liesl Frankson who was phenomenal in helping to put together this issue.
The water scarcity crisis in Cape Town is just that, a crisis; so it comes as no surprise that sustainability is, once again, doing the rounds as an industry buzzword. Sustainable water solutions, sustainable recycling initiatives, sustainable energy sources, and sustainable buildings – all of which have a common thread: protecting and preserving the Earth and its resources. It is for this reason that we chose to kick-start 2018 with a strong sustainability issue.
On our agenda is Jasco Park, located in Midrand, Gauteng, which started out as a small, smart technology solutions provider before realising the opportunity to become a leader in the field of renewable energy, by harnessing its expertise on a solar project at its own head office complex (page 27).
Another sustainable project worth mentioning is the Elon solar PV water-heating system, which uses solar photovoltaic technology but does not require expensive batteries or inverters. It is currently being tested at a new 430-unit residential property development in Mokopane, Limpopo, and, according to the manufacturer, delivers increased reliability, reduced costs and requires little maintenance (page 28).
One of the most-talked-about new buildings to open its doors in Cape Town recently was the Zeitz Museum of Contemporary Art Africa (Mocaa) located in the V&A Waterfront. Originally an old grain silo complex, this was once the tallest building along the Cape Town skyline. The mammoth task of redesigning these silos into a functional exhibition space of the highest possible quality called for a solution that would be unique to Africa, which came in the form of innovative construction products that make use of recycled polystyrene (page 26).
And no sustainability issue would be complete without drawing attention to Aurecon’s significant milestone of becoming the first consultancy to
achieve 50 Green Star ratings in South Africa (page 29). Now that’s one for the record books! It seems, however, that despite the progressive steps we take in the waste management industry, there are still some challenges that continue to plague the sector. One such challenge is the proper storage and disposal of hazardous wastes such as used oil. Alarming statistics from the ROSE Foundation reveal that with nearly 11 million vehicles on South Africa’s roads and more than 3 000 registered workshops – not to mention unregistered and backyard mechanics – there is a huge volume of used oil being generated in the automotive sector, not all of which is correctly stored or disposed of (page 23).
As for this issue’s cover story, in a bid to achieve environmental and community sustainability and excellence, Buhle Waste provides scholarships and has even introduced a graduate recruitment programme to engage the country’s youth in economic participation, encouraging future leaders to remain cognisant of their contribution to environmental sustainability (page 6). “We need the help of the people if we are to achieve our zero-waste-to-landfill objectives. We need the pillars of our business to operate in a synergistic fashion if we are to continue to hold true to our values of beauty, love and respect,” says Dr Phetole David Sekete, founder and CEO of Buhle Waste.
Our business has been raised on the belief that our homes and cities must be beautiful spaces; a love for our people and work should be fostered; and a respect for our environment needs to be maintained. We strive for beauty, love and respect in all that we do,” says Dr Phetole David Sekete, founder and CEO of Buhle Waste.
In 1997, family man and medical practitioner Sekete recognised that the township in which he was living was plagued by poor service delivery; waste was piling up in the sewerage system and rubbish heaps were strewn along the streets –and these areas had become the playgrounds of children. Sekete’s medical practice was full of patients who were suffering from ailments caused by this mismanaged waste. Dedicated to preventative healthcare, Sekete committed himself to bringing efficient waste management to the townships around South Africa.
Buhle Waste is a secondgeneration family business that is 100% black-owned and -managed. The company strives to achieve excellence in all of its business activities in the communities in which it operates. Buhle Waste strives to be an embodiment of ubuntu, knowing that it takes a community to help raise a business.
Buhle Waste began in the dusty streets of Katlehong with a single truck and seven staff members, managing the waste of the local communities in an effort to bring a sense of beauty and pride to their environment. Over the years, the company has gained experience through the trials of business hardships and successes; it now operates nationally with over 350 staff and a fleet of over 70 trucks, with offices, warehouses and/or treatment plants in the Gauteng, Free State, Limpopo and Mpumalanga provinces.
“Our dedication to our community and our respect for our environment have continued to form the foundation of our business operations to this day. Infused in our foundation of operations is the perseverance, resilience and dedication to achieve success for our clients,” notes Sekete.
“When we first began operations in 1997, it
was a tense time for black businesses, which had very little access to capital because of the conservative financing mentality of the banks. In addition to that, the pressures from the larger, white-owned corporations within the industry, who were resolved to minimise any new entrants into the business, were taking their toll on our business operations and ability to expand in scale and scope,” he explains.
Sekete believes that without government interventions, namely BBBEE, the waste industry may not have changed much by today and the sector would have remained in the hands of very few companies who controlled the market share of the industry.
“Today, we find a relatively fragmented industry with lower barriers to entry, overall – there is greater economic inclusion, leading to a spurring in the economy. In addition, the flood of new entrants into the market contributes to a
more competitive environment – this has been beneficial to the companies, individuals and entities that rely on our services,” he continues.
As a business, Buhle Waste has continued to evolve and adapt to the changing circumstances; like the environment it serves, the company has taken on its most resilient characteristics –innovation forms a pillar of the business and its continued growth and success.
The company has continued to invest in technologies that will assist it in achieving its zero-waste-to-landfill goals while simultaneously differentiating its value proposition in the market. In its early years, the company was heavily dependent on other, larger waste management companies that were involved in the treatment and disposal of waste. Today, Buhle is one of the largest waste treatment companies in the country.
“To achieve our zero-wasteto-landfill vision and minimise our environmental impact, we have invested in green technology that has no emissions and reduces waste from treatment. As such, we invested in a steam treatment injection (STI) technology that utilises a steam injection chamber, as opposed to incineration, for treating medical and hazardous waste at high temperatures to sterilise and shred the waste, rendering it non-hazardous and safe to handle.”
“Our commitment to environmentally sustainable technology and ensuring that its benefits are seen throughout the country is further highlighted in our investment in a treatment technology in Seshego, Limpopo – our flagship treatment site,” Sekete notes.
The Converter is a revolutionary technology that, in using friction from rotating shredder blades in a sealed chamber, generates heat to sterilise and destroy hazardous waste, rendering it non-hazardous. The machine reduces the original input by about 70% in volume and 60% in weight. The waste by-product retains a calorific value that is greater than that of coal, allowing us to explore ways in which this by-product can be used to generate energy – it converts waste into a refuse-derived fuel that presents a wealth of opportunities on a continent that is energy starved. This technology is an essential component in Buhle Waste’s mission to achieve zero-waste-to-landfill by 2025.
It is imperative that we, as a collective within our communities, collate our resources and intellect to achieve the great positive impacts of beautifying our communities and ensuring environmental sustainability,” Sekete adds.
The STI is based in Gauteng, making Buhle Waste the first waste management company to have an incinerator and non-burn technology on the same premises. The company’s capacity to treat waste is greatly increased, while its transportation impact is reduced.
“We manage general, industrial, hazardous, chemical, sanitation and medical waste. Our management of multiple waste streams allows us to be an ideal partner to businesses in managing their waste on-site –our clients leave the waste for us to handle while they go about their business of serving their own clients. We feel this is a partnership that ensures our clients’ success because they are not overly encumbered by the burdens of their waste,” he explains.
“It is our mission to achieve our goals through the investment in technology and our people.
“It is with this in mind that we provide scholarships to students who wish to study towards achieving environmental and community sustainability and excellence. We have further introduced a graduate recruitment programme to engage our youth in economic participation and encourage future leaders to remain cognisant of their contribution to environmental sustainability. We need the help of the people if we are to achieve our zero-waste-to-landfill objectives.
“We need the pillars of our business to operate in a synergistic fashion if we are to continue to hold true to our values of beauty, love and respect,” he concludes.
+27 (0)11
info@buhlewaste.co.za www.buhlewaste.co.za
While much of South Africa’s packaging waste problems can be overcome by recycling, only 5% of South Africans recycle. This leads to questions around why more people aren’t participating.
According to Mandy Naudé, CEO, Polyco, one of the most significant reasons is the mindset of the public towards recycling. At a recent event held by Polyco to highlight how South Africans can make waste work, Naudé said: “We want to transform people’s perception of waste by teaching them that used packaging has value and creates opportunities across the country.” Since 2013, Polyco has invested over R29 million in more than 45 projects
around South Africa to grow the collection, separation, sorting and recycling of post-consumer polyolefin plastics. One of these projects, Destination Green Recycling, received a R100 000 grant, which was put towards the purchase of a trailer, floor scale and bailer.
This has enabled the community of Tembisa – and those living beyond its borders – to earn an income via the youth-led and -focused organisation’s mobile buy-back service, which generates 5 t of recyclable waste on average per month.
Similarly, residents in Langa, Cape Town, have recycled 64 t of glass, paper, plastic and metal cans and, in exchange, have collectively received R59 000 through the Packa-Ching project spearheaded by Polyco.
People should be able to recycle plastics in their own homes, and new-build houses should come with the technology ready-installed.
That’s the view of a major British waste and recycling company, which says the technology already exists to allow plastics to be either pelleted or turned into useful items.
While most plastic recycling is done by big companies and involves collecting waste plastics from homes and industry to be shredded and processed, the process has been developed to allow domestic plastic shredders, much like household kitchen waste disposals.
BusinessWaste.co.uk’s Mark Hall foresees a future where householders can just toss unwanted plastics down a chute in their kitchen, and it’s shredded and collected ‘behind the scenes’.
“While this is possibly not suitable for every household, it’s something that can easily be wheeled out into executive homes first, and then generally across the housebuilding industry,” he says. The potential for the technology is enormous, according to Hall. But for those who want to take the entire concept to
its logical conclusion, waste plastics can be shredded and converted into other plastic products in the home. “Plastic pellets are easily converted into the ‘ink’ for 3D printers and, from there, the sky’s the limit,” says Hall.
People already experimenting with everyday household plastic waste say they’re turning out plates, bowls, cups and other items in their own homes and garages. “The technology’s there, it’s getting cheaper by the day, and there’s a willingness to use it,” says Hall.
Energy-efficiency
Some 70% of organisations are paying more attention to energy efficiency than a year ago and 58% are expecting to increase investments in 2018. This is according to the 2017 Johnson Controls Energy Efficiency Indicator survey of more than 1 500 facility and management executives in the US, Canada and 10 other countries.
Cost reduction remained the most important driver for investments globally, with 77% rating it as a very or extremely significant factor in driving investments. Neil Cameron, GM: Building Efficiency – Africa, Johnson Controls, says cost reduction is an issue for investments in South Africa too. “As we see the steady rise in the cost of electricity, this is driving businesses and consumers to look towards technology that delivers energy efficiency.”
When asked about planned investments over the coming year, on-site renewable energy leads with 57% of organisations planning to invest. Energy storage is gaining momentum as well, with 48% of organ isations planning to make investments in 2018.
“In South Africa, despite the significant increase in our cost of electricity, it is still far cheaper than overseas markets, which results in a slower uptake of renewable energy. Environmental issues and working towards a zero-carbon footprint are currently the chief reasons for companies investing in renewable energy in South Africa,” adds Cameron.
Only around 5% of South Africans recycle; to improve on this, it is imperative to change people’s attitudes
Businesses are looking towards technology, like on-site renewable energy, to deliver energy-efficiency cost savings
Electricity is significantly cheaper in SA than most overseas markets, which slows renewable energy generation uptake
Switching
In today’s facilities management market, achieving green building status has become vital. In line with this, many companies have invested in the design, construction or refurbish ment of their buildings. To do this, they have updated everything from the types of bricks and cement used to the functioning of their cooling and heating systems.
However, despite the amount of capital that has been invested into cre ating a clean and healthy work structure, using green building practices, many companies are unaware of what type of cleaning and hygiene products they or their contractors are using, and whether or not these cleaning products meet Green Star Eco standards.
building’s GBCSA (Green Building Council of South Africa) status. “However, this status can easily be increased by using cleaning products that meet the Green Star Eco profile,” confirms John Coetzee, CEO, Green Worx Cleaning Solutions.
“After six months of using truly green cleaning products, companies can qualify for 3.5 points towards their next GBCSA assessment. Companies that use cleaning products that meet the Green Star Eco profile will inevitably benefit the health of their building, staff, visitors and, above all, the environment.”
Common cleaning products used in companies consist of petrochemicals, which emit dangerous volatile organic compounds
Common cleaning products consist of petrochemicals, which emit dangerous volatile organic compounds. According to the Environmental Protection Agency’s Office of Research and Development, these chemicals have a negative impact on waterways as well as human health. Using these cleaning products will decrease a
Health and environmental benefits are not the only reasons why green cleaning products are a better option. “Switching to these products can reportedly reduce the volume of cleaning products by as much as 50% and reduce the acquisition cost of cleaning products by 30% to 50%,” adds Coetzee.
“This affords companies effective cleaning solutions at reduced costs and risk. The increase in health and safety has the potential of reducing staff absenteeism and job injuries, as well as increasing alertness, resulting in better job performance.”
Forty municipal councillors from Mpumalanga municipalities received in-depth training on the recycling of packaging material thanks to a two-day workshop arranged by Packaging SA.
The main focus of the workshop was to educate the councillors, in a ‘train the trainer’ format, on how plastics, glass, metals and papers are recycled in South Africa and the importance of recycling in our economy, as part of local government support strategy interventions. The workshop, which was hosted
18 Mpumalanga councillors attended recycling training and received certificates of completion
at the Plastics|SA head office, was a joint initiative of the South African Local Government Association (SALGA) and the Department of Agriculture, Rural Development, Land and Environmental Affairs, and the Department of Environmental Affairs.
Charles Muller, executive director, Packaging|SA, says the workshop is an excellent example of the first fruits being reaped as a result of a concerted effort to improve public-private partnerships. The councillors, who
are all responsible for the Climate Change, Environmental and Waste Management portfolio in their respective municipalities, learnt specifically about certain recycling processes and products made from recycled materials through presentations delivered by PRASA, Tetrapak, TGRC, MetPac-SA, PETCO, Polyco, SAVA, Plastics|SA and Destination Green Recycling.
Once the theory was completed, it was time for a practical, hands-on experience, where the municipal councillors visited a recycling collector and the Tufflex recycling facility.
“The feedback we received from our government colleagues was that the training they received was hugely beneficial,” says Muller.
“Not only are they now empowered to promote recycling initiatives in emerging and potential recycling companies within their communities, but we have also equipped them with the necessary skills and knowledge to further uplift their communities through job creation and ensuring that valuable waste with high recycling value stays out of our already burdened landfills and oceans,” he concludes.
CAIA has launched its Responsible Care ® in Action programme to develop an increasingly powerful ethic that will reshape the global chemical industry.
The Chemical and Allied Industries’ Association (CAIA) has devised an ongoing Responsible Care® programme designed to elicit both attitudinal and behavioural change in its membership. The Responsible Care® in Action programme will be launched in April 2018 under the theme‘Sustainability’.
“The programme will ensure the strengthening of the implementation of Responsible Care® in South Africa and a continued growth of awareness,” says Deidré Penfold, executive director, CAIA.
Responsible Care® is an international voluntary initiative under the guardianship of the International Council of Chemical Associations (ICCA); CAIA, as the overarching body that represents the chemical and related industries in South Africa, is the initiative custodian in South Africa.
Through Responsible Care®, CAIA promotes the improvement of the safety, health and environmental performance of the chemical and allied industries in South Africa. CAIA members sign the Responsible Care® pledge that commits them to the guiding principles of this initiative and they undergo regular self-assessments and thirdparty audits to ensure compliance.
On a global level, the ICCA’s Responsible Care® Leadership Group (RCLG) identifies problems, shares solutions and provides assistance to member associations in developing and enhancing their current programmes through capacity building. Each of these functions has a specific role to play in ensuring that Responsible Care® becomes and remains deeply integrated into the industry.
Members of the ICCA RCLG include representatives from national associations, chemical manufacturing companies and logistics service providers around the world that are committed to Responsible Care®. CAIA envisages
knowledge expansion and practical implementation of the initiative after the programme has been launched. This will see the spreading of the Responsible Care® ethic beyond chemical manufacturers and their trade associates, says Penfold. “Our aim is that Responsible Care® will no longer be limited to performance improvement only, but that the initiative will develop into an increasingly powerful ethic that will help to reshape the global chemical industry for the future.
“The components of the programme are aimed at specific audiences that are crucial to the well-being and progress of the chemical industry, including executives and government officials, operational managers, the workforce and Responsible Care® industry auditors,” says Penfold.
Improving performance, communication and accountability Companies, through their national associations, commit to working together to continuously improve the safety, health and environmental performance of their products and processes, thereby contributing to the sustainable development of local communities and society as a whole. Responsible Care® is thus managed by industry and focuses on improving performance, communication and accountability.
The launch of the Responsible Care® in Action programme will be attended by RCLG chairman Patrick Vandenhoeke, together with other interested African delegates who will be sponsored by the ICCA. “CAIA looks forward to the successful launch and implementation of the programme, and the inevitable revamping of the Responsible Care® initiative,” says Penfold. “This year will be
a busy one for CAIA and we will explore every opportunity to further safety and sustainability in the chemical industry, as well as the interests of our members and their employees.
“We are already hard at work to make it one of CAIA’s most successful years ever by reviewing the management practice standards and associated audit guidance documents in our industry, reintroducing our Process Safety Forum in KwaZulu-Natal, keeping an eye on environmental management, and policy and/or legislation development, among other things.
“I am looking forward to another year of close collaboration with our members, promoting the Responsible ® initiative for a safer and greener industry, expanding our advocacy efforts and working with government to the best advantage of all,” says Penfold.
2018 CAIA calendar
www.caia.co.za/wp-content/uploads/2017/12/ CAIA%20Calendar%202018.pdf
A study conducted by Unisa’s Department of Environmental Sciences and the CSIR, presented at WasteCon 2016, sheds new light on how income levels affect the composition of food waste across five areas in the City of Tshwane.
By Fhumulani Ruth Ramukhwatho, Roelien du Plessis and Susan Oelofse*
Food waste is generated throughout the supply chain, including at household level. Household waste contains a fairly large percentage of food in developing countries. This study assessed household food wastage in five selected areas in the City of Tshwane Metropolitan Municipality (CTMM). The main goal of the study was to assess food waste by income level and the reasons for wasting food. Household food wastage was assessed using questionnaires during face-to-face interviews. A total of 210 households participated in the study. Results
showed that high-income households wasted the most food. The main reason why food is wasted, as reported by the respondents, is that they prepare too much porridge and rice.
The chi-square test is a test that is often applied to categorical data, i.e. data that is grouped into categories, which may or may not be ordered, and for which the number of occurrences within each category is counted or expressed as a proportion of the total. (For categorical data, the data is recorded as a category, as opposed to numerical data that is recorded as measurements, which could, for example, be averaged for different groups in the data.)
The chi-square test determines whether differences in proportions between groups may be attributable to random differences between the groups or whether they represent a consistent, non-random pattern of differences. The chi-square test uses the chi-square probability distribution (x2) to calculate the probability value (or p-value). Such probability values could be calculated using pivot tables and the chisquare. The test function in Excel or a
package can be used for this.
In this study, the statistical software SAS was used to apply the chi-square test and determine the relevant p-values.
There were more female respondents (58%) than male (42%); the summary of respondents’ demographic profile is shown in Table 1. More than 90% of respondents had some form of education (e.g. certificate, diploma and degree), while only 1% were unschooled (no form of education, no certificates).
Most of the respondents who participated in this study were from two-member households (28%); however, the majority of the respondents (55%) had a monthly income of over R10 000. Age and gender are two relevant personal characteristics whose effects on food waste have been hotly debated in the literature reviewed.
Chi-square results for the different income categories and questions related to food wastage are shown in Table 2. Any p-value of <0.05 is considered statistically significant, i.e. an indication of an underlying consistent, non-random pattern. Any p-value of >0.05 is considered not statistically significant. Table 2 shows that the majority of the respondents had a monthly income of over R10 000, followed by respondents receiving a monthly income ranging between R500 and R5 000, and respondents with a monthly income of R6 000 to R9 000. The chi-square results show that there were statistically
significant differences at (p < 0.05) in the values of questions regarding whether respondents wasted food. The results indicate that 75 out of 115 (65%) high-income respondents admitted to wasting food, compared to 17 out of 52 (32%) low-income households and 31 out of 43 (72%) middle-income households. It can therefore be concluded that middle and highincome households are more aware of their food wastage than lowincome households in this study.
As presented in Table 3, 29% of respondents with a monthly income of R10 000+ wasted food because they bought too much. There was not much difference between income categories: 28% of respondents in the R6 000 – R9 000 and 21% in the R500 – R5 000 categories wasted food for this reason. Twenty-seven per cent of respondents with a monthly income of R500 – R5 000 wasted food because of special offers, and only 11% with a monthly income of R10 000+ wasted food for this reason. Respondents (43%) with a monthly income of R10 000+ wasted food due to cooking too much. Twenty-six per cent and 29% of respondents with a monthly income of R6 000 – R9 000 and R500 – R5 000, respectively, wasted food for this reason. Ten per cent of respondents with a monthly income of R500 – R5 000 wasted food because of poor storage. The study found that respondents
with a monthly income of R500 –R5 000 had the highest percentage (8%) of food wastage because of food residue. The range between the categories, however, was very small and ranged between 7% and 8%. Respondents with a monthly income of R6 000 – R9 000 and R10 000+ had the lowest percentage (7%) of respondents who wasted food because of food residue. The highest percentage, 12% of respondents with a monthly income of R6 000 – R9 000, wasted food because of fruit and vegetables going off. There was no statistically significant difference in the results of the questions on the reasons for wasting food.
It is, however, notable that, overall, (75 out of 210) 35.7% wasted food due to cooking too much, (56 out of 210) 26.7% buy too much food, and (37 out of 210) 17.6%
respond to special offers that result in food wastage.
As presented in Table 4, households with a monthly income of R500 – R5 000 had the highest percentage of respondents who composted their food waste (6%). Two per cent of respondents with a monthly income of R6 000 – R9 000 composted their food waste and only 1% of those with a monthly income of R10 000+ did so. It can, therefore, be concluded that there is a correlation between income level and food waste disposal methods, and the difference between income levels was statistically significant. Households with a monthly income of R6 000 – R9 000 had the highest number (35%) of respondents who fed their food waste to pets. Households with a monthly income of R10 000+ had the lowest percentage (4%) of feeding food waste to
high-income respondents (75 out of 115) admitted to wasting food, compared to 17 out of 52 (32%) lowincome households, and 31 out of 43 (72%) middle-income households
Households with a monthly income of R500 to R5 000 had the highest number of respondents who composted their food waste (6%)
Globally, 30% to 50% of food produced for human consumption is wasted. It covers 6% of the Earth’s surface and 20% of the total landmass
Studies found that the main driver of food wastage is cooking too much. Households prepare more than their family members can consume
If the country avoids wasting food, this could go a way towards alleviating hunger in South Africa and improving global food security more generally
• 30% to 50% of food produced for human consumption is wasted globally
• This equates to 250 km3 of water and 1.4 billion hectares of land use wasted
• Developing countries waste about 120 kg to 170 kg of food per capita per year
• Developed countries waste about compared to 280 kg to 300 kg of food per capita per year
• About 50% of food grown is lost before and after it reaches consumers
pets. Ninety-five per cent of respondents with a monthly income of R10 000+ relied on the household garbage bin for their food waste disposal, followed by 75% with a monthly income of R500 – R5 000, and 63% with a monthly income of R6 000 –R9 000. Overall, 175 out of 210 (83%) of households dispose of their food waste to the household garbage bin.
The study found that the main driver of wasting food is cooking too much. Households prepare more than their family members can consume. This may be a symptom of South African culture, where provision is made for the unexpected visitor. Changing practices relating to culture may prove to be challenging but, given the large majority of responses, it may be worthwhile to raise awareness of this situation with the public at large.
(175 out of 210) of households dispose of their food waste to the household garbage bin
Composting as an
The study presented three methods that respondents could employ to dispose of their food waste. The majority of the respondents (83%) in this study relied on the household garbage bin, i.e. municipal waste collection services.
Fourteen per cent of respondents fed their food waste to pets and 3% of respondents composted food waste for their garden. There is, thus, huge potential to increase household composting as a means of diverting food waste away from landfill.
Test result:
The findings of this study reveal that several recommendations can be made that will lead to better management of households’ food waste in the CTMM and possibly in all other municipalities in South Africa. These are:
• Households should try to prepare only the amount of food that they can consume. This may require education on portion sizes and general meal planning for households.
• The household garbage bin as the main food waste disposal method provides an opportunity for CTMM to raise awareness on composting as an alternative to landfills. The CTMM may consider using food waste as a biofuel input material for biodigesters to generate gas for electricity. The CTMM must prohibit food waste from being disposed of with general waste in the municipality bins because it ends up at the landfills, contributing to environmental pollution; household food waste should be stored and collected separately for recycling. It is recommended that food waste separation at source be started in household kitchens.
• This is an opportunity for the CTMM to raise awareness of reducing household food waste and educate people on the impacts of food waste. Additionally, the CTMM needs to encourage households to recycle food waste and raise awareness about the benefits of doing so.
Acknowledgment: The Unisa Masters and Doctoral Support Programme funded this research.
*Fhumulani Ruth Ramukhwatho is a researcher in the Department of Environmental Sciences, Unisa; Roelien du Plessis lectures at the Department of Environmental Sciences, Unisa; and Susan Oelofse is a researcher at the CSIR’s Natural Resources and Environment Department.
For the full version of this paper, including a reference list, contact the lead researcher at 4humulani@gmail.com
Arecurring theme throughout the conference covered the tremendous opportunities presented by Africa. The continent is frequently referred to as a sleeping giant, and this is especially true for waste. As Ruben Janse van Rensburg, sustainability manager, HP Inc. Africa, pointed out: “By 2040, Africa is expected to have the largest workforce population in the world, exceeding China and India combined.”
Increased government investment in education, throughout most of the continent, except South Africa, will see a rising middle class in Africa. This is likely to increase Africa’s purchasing power and stimulate an increase in the number of opportunities for economic growth. One of these is the opportunity to leapfrog the developed world’s mistakes in terms of realising the value of waste.
“Africa has an opportunity to start looking at the bigger picture in terms of product design and the recovery of materials for recycling. Lessons can be learned from Europe and other developed regions that have been now sits with the problem of dealing with toxic materials products that have reached their end-of-life in terms of a linear consumption paradigm. Africa has access to information on recycling those materials and has the opportunity to sidestep the problems that have been dealt with arisen elsewhere, by adopting a mental shift toward a circular-economy paradigm,” Janse van Rensburg explained.
o n 5 to 6 o ctober 2017, the c S i R and the d epartment of Science and Technology ( d ST) hosted their annual i ndustrial d evelopment c onference. The session on waste valorisation for improved industrial competitiveness looked at new ways to realise value from a frica’s waste.
In his presentation, Janse van Rensburg used the example of the EU’s Green Public Procurement policy to illustrate how market shifts and consumer preferences are driving the new circular economy mindset. “If HP Inc. wants to sell to European governments, our products need to have 15% post-consumer recycled plastic con tent; this, in turn, drives a change in how man ufacturers design and manufactures products,” he said.
Recycled plastics used in HP products cannot be contaminated with toxic or otherwise harmful substances. This creates demand for ‘clean’ recyclable plastic. “Since we participate in large tenders in Europe, where sustainability or recycled content could be as much as 40% of the awarding criteria –price could be as low as10% to 15% – we now need to look for reliable sources of clean plastic like recovered products and even drinking bottles which could be in Africa, which we then can send to plastic recycling facilities,” Janse van Rensburg added.
The next speaker was Dr Sarushen Pillay, environmental technology manager, Sasol. He focused on how, by following a three-step process, innovation can be used to overcome waste challenges in a large organisation such as Sasol. These three
steps are: 1) having clear goals, 2) having support from leadership and decision-makers within the organisation, and 3) having teams with diverse skills.
“A high-pressure environment creates immediate focus. If you have management support at the highest level, it also allows you to drive these ideas forward,” Pillay explains. “Also, saying that we want something better than incineration or landfilling is not a clear goal; it doesn’t set a timeframe, or an economic target for the team to chase. A clear goal states what’s needed by what date, at what cost, in order to drive the right behaviour.”
“Lastly, what we were lacking was multiskilled, diverse teams. We’ve got a waste research group, so we gave them the job to find new ideas for our waste streams and we found that that’s not the way to do it. What you really want is to bring people from all parts of the organisation to innovate in this space. you can’t rely on just a waste group,” he added.
The final team composition included chemists, engineers, scientists and even a zoologist. Pillay’s three-step process has led to two successful cases at Sasol, where the organisation was able to change the way it approached two different waste streams, so that it could reduce costs while implementing the waste management hierarchy.
“We had attempted to implement the waste management hierarchy at an earlier stage but we found that only when we were faced with unusual new challenges and deadline pressure were we able to focus
Ruben Janse van RensbuRg Sustainability manager, Hewlett-Packard Africa
DR saRushen PiLL ay Environmental technology manager, Sasol
and really apply the hierarchy as a fundamental principle, rather than as a ‘check-box’ exercise,” Pillay explained. Of the two case studies, the first was a project to find a new way to deal with spent caustic without discharging treated effluent still containing salts into the Vaal system. The deadline for the project was mid-2018. “One of the members of our team was from our Secunda facility. He pointed out that the spent caustic was a highly basic waste stream, while there was a highly acidic waste stream in Secunda. He suggested that one waste stream be used to treat the other. “We were able to scale the whole process from laboratory to pilot and engi neering in four to five months, because we had support from management to drive the project,” he said.
PRoFessoR bRuCe sithoLe Chief scientist in biorefinery research, CSIR
“Forestry produces many tonnes of waste. Indeed, the yield extracted from a tree is only about 47%. Waste takes the form of sawdust, sludge, bark, fly ash and so on. This is not acceptable or environmentally sustainable,” explained Professor Bruce Sithole, chief scientist in biorefinery research for the forestry industry at the CSIR. His team has found different ways to realise value from these different waste streams, so that as much as 95% of milled trees is used, all while high-value secondary industries with the potential to create entrepreneurial opportunities and jobs are stimulated.
• Africa is the largest continent – larger than China, the US, India and all of Eastern Europe combined
• It covers 6% of the earth’s surface and 20% of the total landmass
• Algeria is the largest country in Africa –roughly a quarter of the size of the US or China, and about 70% the size of India
• Lagos is the largest city in Africa, currently the seventh largest in the world, and it’s projected that it will be the largest by 2100
• Africa has the largest population of people between 15 and 25 years of age
• By 2040, Africa is expected to have the largest workforce population in the world, exceeding China and India combined
• It’s estimated that the African workforce will swell by 163 million inside the next 10 years
• By 2050, Africa will account for 25% of the world’s workers
• With the notable exception of South Africa, 20% of government spending in Africa goes to education
The second case study came about in response to one of Sasol’s service providers refusing to accept one of its acrid waste streams due to odour complaints. “One of our junior organic chemists did not see this waste stream as waste but rather as a molecule. He pointed out that if we mixed it with caustic and methanol (two products produced by Sasol), it would make an odourless ester. It worked. Again, we were able to quickly work the concept, to do the laboratory work, the piloting and, by doing the engineering in parallel, we were able to develop a concept that could be implemented quickly,” Pillay explained.
The Sasol case studies are inspiring because relative crises were turned into opportunities. Equally, if not even more, inspiring is the work being done at the CSIR for making the local forestry industry less wasteful through beneficiation.
One of the projects that Sithole’s research focuses on is extracting xylose from waste cellulose in sawdust to make xylitol – a sugar-substitute that retails for R150/kg, and is not locally produced. As all of South Africa’s xylitol is imported, it represents an opportunity for local businesses.
“Another example is our work with pine sawdust waste. Pine waste is full of lipophilic extractives and these can be extracted and used in a variety of cleaning and polishing agents. Similarly, there is no local production of these materials,” Sithole explained.
Lastly, and perhaps most impressively, research is being done on how to extract the most value from the remaining fibres by extracting the relevant materials and refining them into nanocrystalline cellulose.
“If you look at cellulose’s structure, it’s comprised of crystalline and non-crystalline agents. By using strong acid, we can break up those nanocrystalline agents and extract these crystalline fibres. This technology was first created
in Canada a few years ago,” explained Sithole. “The most interesting thing about these nanocrystalline fibres is that their tensile strength is stronger than that of stainless steel. And under wet conditions, the material displays iridescence. Material applications include paint, films, hydrogels and others.” “In our laboratories, we are developing these applications. For example, if you take a plastic polyacrylic acid, add 4% of this material, it changes its properties and becomes a hydrogel. If you immerse it in water, it expands 98%, making it a high-performance composite,” adds Sithole. He noted that there are only about four or five companies worldwide producing this type of material. The current way of doing the extraction is expensive, as it uses expensive dissolving wood pulp as a starting material – thus the nanocrystalline cellulose sells for about US$1 000/kg. The CSIR is investigating a more cost-effective means of extraction of nanocrystalline cellulose directly from wood state, which would give rise to a competitive local industry. In the end, the industry will be extraction well over 95% value from harvested trees.
“One of our junior organic chemists did not see an acrid waste stream as waste but rather as a molecule. He pointed out that if we mixed it with caustic and methanol, it would make and odourless ester.”
One of the biggest challenges in the local forestry industry is scaling production. In South Africa, there are about 400 sawmills scattered around the country. It would not make financial sense for all of them to produce these secondary products on a large scale. Sithole believes that the CSIR can develop a mobile extractor that can be used to go from plant to plant, collecting the necessary materials that would then travel to a central point. “That is one thing we are looking into,” he said. “We have a facility in Durban called
“Africa has the opportunity to sidestep the problems that have arisen elsewhere by adopting a mental shift toward a circulareconomy paradigm.”
the Biorefinery Industry Development Facility, funded by the CSIR and DST. This world-class facility, which is central to the major biomass in the region, has highly trained specialists in advisory and technology development roles. In addition, we have pilot plant equipment that enables us to upscale these technologies to be ready for uptake by industry. We are also heavily involved in human capital development in industry and now we have a growing network of partnerships and collaborations,” concluded Sithole.
Innovation can be leveraged to derive the maximum value from industrial waste streams. The estimated value of South
One of the projects that Professor Sithole’s research focuses on is extracting xylose from waste cellulose in sawdust, to make xylitol – a sugar-substitute that retails for R150/kg, and is not locally produced
Africa’s available resources from waste is equal to one entire GDP point. yet, recycling rates are low – about 10%. The only factor limiting this figure is people’s imagination.
By focusing, and taking the necessary steps, the waste hierarchy can be effectively implemented to create value from waste, in turn stimulating new industries, creating jobs and boosting South Africa’s (and Africa’s) international competitiveness. In the next decade, this will not only be a ‘nice to have’; it will be a necessary mind-shift to create sustainable jobs for Africa’s growing workforce.
According to the latest statistics, a massive 21.6 million tonnes of waste was generated in South Africa in 2011. A key challenge is that 90% of all SA’s waste is disposed of in landfill sites. With the country fast running out of landfill airspace, it is imperative to find responsible disposal solutions.
Unlike many developed countries around the globe that operate within a regenerative system, called a circular economy, South Africa only recycles 10% of its waste. Pollution, global warming and resource scarcity have led to the rise of circular economies that focus on the repurposing and reuse of products that would typically be destined for landfills.
However, due to several factors, the country still employs a predominantly linear or ‘take-makedispose’ approach. Considering that most of our waste is destined for landfills, the promotion of responsible disposal practices remains crucial for environmental sustainability.
According to Averda, one of South Africa’s largest waste management providers, under-pricing in the industry is a significant barrier to the development of green waste management solutions. This is compounded by a high number of unlicensed or non-compliant waste handlers who undercut prices by skirting legislative requirements.
Reg Gerber, national landfill manager at Averda South Africa, says reputable waste management companies often guide their clients on how to reduce waste. “We develop strategies with our clients that enable them to divert significant portions of their waste away from landfills. This includes a rebate system to incentivise recycling. However, when disposal is necessary, reputable providers can be trusted to ensure that this is managed responsibly,” he explains.
The construction and management of landfill facilities are subject to strict governmental regulation aimed at reducing their environmental impact. When consumers employ unlicensed or non-compliant providers, they have no control over where their waste ends up, which is bad for the environment.
Mismanaged landfills and dumps present a number of risks to the environment including air pollution and groundwater contamination. When rain falls on landfill sites, the organic and inorganic constituents are dissolved, forming a leachate, which can contain toxic metals such as ammonia, organic compounds and pathogens. Any leakage can result in groundwater contamination.
To prevent contamination, Averda’s landfill facilities are built with containment barriers designed according to the strictest legislative requirements. Bar riers include a leachate collection layer that traps the contaminant, preventing it from reaching groundwater supplies. As part of the management process, waste is sorted and treated, so that it can be disposed of in a facility that has been de signed to mitigate its specific environmental risks.
example, is a Highly Hazardous, Class 1 landfill site, which is South Africa’s only landfill to be constructed to the standards prescribed by the new Waste Classification and Management Regulations for Class A containment barriers. In accordance with legislation, the company continues to monitor its facilities for 30 years after closure.
“We develop a closure plan prior to the development of our landfill sites. This is essential to ensure we have the resources required to monitor and maintain our facilities on an ongoing basis following their closure,” explains Gerber.
Gerber adds, “We have a number of landfill sites that are designed and managed to deal with specific waste streams. Our site in Vlakfontein, for
Properly managed landfill facilities are supposed to adhere to Minimum Requirements for Waste Disposal by Landfill as prescribed in government regulations that came into effect in 1998. The regulations include specifications regarding site selection, design standards, operational practices, closure processes and monitoring. It’s important for consumers to understand that sustainable behaviour not only requires reducing one’s waste but includes responsible disposal methods. Employing reputable waste management providers will not only ensure that the impact of your waste is minimised, but it could also reduce under-pricing in the industry, paving the way for sustainable waste management solutions.
While local government focuses on housing, water, electricity, and road infrastructure, waste management is falling behind as the least prioritised municipal service in most municipalities. This is alarming because the country only recycles around 10% of its waste at present.
With Johannesburg, Tshwane, and Cape Town all having less than 10 years of useful landfill life left, the pressure is on to find alternative waste treatment technologies (AWTT), says Nicola Liversage, business unit director: Environment, Aecom Africa.
South Africa’s eight Category A metropolitan municipalities have the highest population
numbers, and, therefore, generate the largest waste volumes of between 10 million and 20 million tonnes of waste a year, of which the bulk is landfilled.
Landfilling at an average density of 1 t/m3 means that municipalities need an annual landfill space of about 10 million m3. While some municipalities like eThekwini boast a useful landfill life of 120 years, others, such as Johannesburg, Cape Town and Tshwane, have a limited useful landfill life of less than 10 years.
AWTT crucial for diverting waste to landfill
“Therefore, the need to investigate AWTT is crucial for diverting waste from landfill,” highlights Liversage. Johannesburg, the eThekwini Metropolitan Municipality, Cape Town, and the Sedibeng District Municipality have all completed AWTT feasibility studies, while the Drakenstein Local Municipality in the Western Cape has finalised a waste-to-energy feasibility study. AWTT feasibility studies are also under way in Tshwane and Ekurhuleni. Materials recovery facilities (MRFs) have been established in some municipalities in
Waste management is the least prioritised municipal service in most South African municipalities
order to recover recyclables. However, these are hampered by the low rate of recovery of recyclables. The absence of separating waste at source means facilities are operated as ‘dirty’ MRFs with high contamination rates and lower recovery rates, compared to ‘clean’ facilities with low contamination rates.
In addition, some South African municipalities are piloting separation at source, but with a minimal response. In the EU, on the other hand, separation at source has been key in enabling the diversion of waste from landfill by means of recycling, composting, and incineration. In South Africa, waste incineration is still smallscale, used mainly for the thermal treatment of healthcare and some hazardous waste.
e nvironmental authorisations a stumbling block
With regard to the challenges facing waste management in South Africa, Liversage points
Eight to ten million tonnes of waste a year is landfilled
to environmental authorisations, permitting, licensing and social issues as the main stumbling blocks. “In fact, it can take up to 10 years between identifying a suitable site and actually commissioning a landfill,” she adds.
Although the capex and maintenance costs of technologies for treating waste are substantial, landfilling remains less expensive than AWTT. However, the cost of landfilling may be even higher at the end of the day, given the cost of managing a landfill upon its closure. The life of a landfill may stretch to about 50 years after it closes. In addition, the absence of carbon taxes means that landfilling continues to dominate waste management in South Africa compared to AWTT, which is increasingly the norm in the EU.
It is estimated that 65% of waste produced in South Africa is recyclable and could theoretically be diverted from landfill and recovered to be reprocessed or repurposed, according to a 2012 report by the Department of Environmental Affairs
Some municipalities have established materials recovery facilities
It can take up to 10 years between identifying a suitable site and commissioning a landfill
South Africa is aiming to reach a target of 20% waste division (by weight) by 2019
b ased on global trends, by diverting waste away from landfill, South Africa could increase the revenue from this sector
The ‘business as usual’ approach to waste management (approximately 90% going to landfill) generates an industry that is estimated to be worth R15 billion in revenue and provides 298 337 people with employment, primarily in the recycling and reclamation sector, according to a 2014 report by the Department of Science and Technology
The National e nvironmental Management: Waste Act (No. 59 of 2008) and the National Waste Management Strategy (2011) mandate municipalities to implement alternative waste management to divert waste from landfill and minimise environmental degradation
In 2014, the Department of Science and Technology estimated that an additional R17 billion/year worth of resources could be unlocked if 100% of the identified 13 waste streams could be recycled
It is estimated that South Africa generates an average of 120 million litres of used lubricant oil per year. This is a large amount of used oil that, if not collected and recycled responsibly, could make its way into our environment. Submitted by the Recycling Oil Saves the Environment (ROSE) Foundation
With nearly 11 million vehicles on South Africa’s roads (according to latest eNatis statistics) and more than 3 000 registered workshops – not to mention the unregistered and backyard mechanics servicing many of these vehicles – there is a huge volume of used oil being generated in the automotive sector.
Service centres and mechanical workshops, as used oil generators, are urged to gather and store their used oil for responsible collection by a ROSE-registered oil collector who will visit the site, remove the oil and take it to be recycled in an environmentally compliant and safe manner. Collectors must always issue their clients with a safe disposal certificate, which is now required by law under the National
Drain oil into a clean container with a tight-fitting lid, such as a reusable combination drain pan or storage container
Ensure that the oil is stored in a container with a secure lid so that it cannot spill out. Empty oil containers and drums make effective makeshift storage vessels for used oil. However, do not use a container that previously held chemicals such as cleaners, solvents, fuels, paint or bleach
Always clearly label used motor oil containers
For those running businesses that generate high volumes of used oil, the ROSE Foundation can supply tailor-made, cubeshaped 1 000 ℓ mini tanks, which make maximum use of available space and hold more oil. To make things even easier, the collections require no handling of the containers. Sealed couplings are used to pump the contents straight into a tanker truck so there is no spillage or leakage
Keep these containers in a place that can be accessed by an accredited used-oil collector and keep the surrounding area clear and clean. Ideally store them under cover and away from heat or the sources of an ignition
“The legislation in place in South Africa means that responsible waste management within a business environment is no longer just a nice thing to do but a necessary thing.”
Some oily can- or bottle-waste-generating businesses in South Africa discard their related wastes along with the domestic refuse and are not properly storing them for safe disposal or recycling
Keep oil-change pans free of water and ensure your storage containers are tightly sealed and covered to protect them from rainwater. Oil that is contaminated with water is far more difficult to recycle – requiring several laborious and costly processes to separate the water from the oil before it can be recycled
Ensure no mixing of used oil with other fluids such as antifreeze, transmission fluid, petrol, diesel etc. Mixing may make oil non-recyclable as well as hazardous and flammable
Build a bund wall around bulk used-oil storage tanks so that in the event of a spill or leak, the used oil will be contained. In the event of an oil spill, it is necessary to contact a used-oil collector
Environmental Management: Waste Act (No. 59 of 2008; NEMWA).
According to Bubele Nyiba, CEO, ROSE Foundation, many businesses also over look the matter of related wastes. This is especially the case when it comes to used oil filters, oily rags, sawdust used to soak up oil and empty oil containers.
Some oily can- or bottle-waste generating businesses in South Africa discard their related wastes along with the domestic refuse and are not properly storing them for safe disposal or recycling.
Nyiba explains that this is largely due to a lack of knowledge on the available alternatives rather than a disregard for the law.
“DIy mechanics can drop this waste off at their nearest approved municipal garden refuse site (a
list is available from the ROSE Foundation). Usedoil collectors can also be asked to take this away with them if possible,” advises Nyiba. The ROSE Foundation has dedicated service providers that collect oily containers from service stations in the major metros of Johannesburg, Cape Town and Durban. Nyiba explains that the safe disposal of hazardous waste has become a critical issue for businesses in South Africa, with specific measures of accountability clearly being laid down in the NEMWA and the National Waste Information Regulations.
“There is a worldwide shift towards sustainable business practices in order to protect our environment. The legislation in place in South Africa means that responsible waste management within a business environment is no longer just a nice thing to do but a necessary thing,” he concludes.
Pellets or Fluff as alternative fuels
AMANDUS KAHL USA Corp. 105 Hembree Park Drive, Suite L · Roswell · GA30076 · USA 001-770-521-1021 · sales@amanduskahlusa.com · akahl.us
AMANDUS KAHL GmbH & Co. KG SARJ Equipment Corp. 29 Golfview Blvd · Bradford · Ontario L3Z 2A6, CANADA 001-905-778-0073 · rbmacarthur@sympatico.ca
Representatives from the Global Plastics Alliance (GPA) recently met in Penang, Malaysia, as guests of the Malaysian Plastic Manufacturers, with the aim of accelerating and advancing the Declaration of the Global Plastics Associations for Solutions on Marine Litter, also known as the Joint Declaration.
According to Douw Steyn, sustainability director, Plastics|SA, more than 19 countries from across four continents are currently participating in this joint initiative, including Canada, Colombia, India, Japan, Malaysia, Russia, South Africa, Thailand, Turkey, the USA, Vietnam and Europe.
“Marine litter is a complex problem that requires creative thinking and a holistic approach. There is no single solution and it is, therefore, important to hear the many different perspectives on the issues facing the industry,” Steyn says.
“It was hugely encouraging to see so many plastic manufacturers from across the globe come together with the objective of finding ways to keep used plastic out of the environment and to further improve the sustainability of these
energy- and resource-efficient materials,” he adds. One of the highlights of the meeting was updating the Joint Declaration that was launched for the first time in March 2011 at the 5th International Marine Debris Conference. Seventy plastics associations representing regions from across the globe became signatories of the Declaration, and now recognise and acknowledge the important role they have to play in fighting marine litter. Africa’s voice in these matters is represented by Plastics|SA, Packaging SA and Ghana, which also recently became a signatory.
“Plastics|SA is proud to be one of the first signatories and is actively supporting projects in six key areas aimed at contributing to sustainable solutions, namely education, research, public policy, sharing best practices,
plastics recycling/recovery, and plastic pellet containment,” Steyn says.
“We have launched various successful cleanup and recycle initiatives, such as our annual International Coastal Clean-Ups, Operation Clean Sweep, and sponsoring litter booms and initiatives such as the Aqua Amazing schools education programme as part of our commitment to reducing plastics litter in the environment.”
Commenting on the success of the latest GPA meeting, Callum Chen, secretary-general, Asia Plastics Forum, said: “The continued growth of the GPA proves that this industry is committed to providing solutions to ensuring a more sustainable future. As a united group, we are leading the deployment of hundreds of marine litter prevention programmes in all regions of the globe. While it is clear that there is much to do, it is equally obvious that our combined efforts are building momentum.”
The Zeitz Museum of Contemporary Art Africa (Mocaa) at the V&A Waterfront is one of the most-talked-about buildings to have recently opened its doors in Cape Town. Even the building materials used have garnered interest.
Originally an old grain silo complex consisting of forty-two, 33 m high concrete tubes – each with a diameter of 5.5 m – this was once the tallest building along the Cape Town skyline. The mammoth task of redesigning these silos into a functional exhibition space of the highest possible quality called for a solution that would be unique to Africa. The solution came in the form of innovative construction products that make use of recycled polystyrene.
Greenlite Concrete products were specified by the architects, owing to the fact that the structural engineers were concerned about excessive loading to the existing structure.
“The original concrete frame of the old silos building was built in 1924, making the building 94 years old,” explains Hilton Cowie, technical director, Greenlite. “The developers, therefore, needed a screed solution that would not put unnecessary load on the structure, yet
would not compromise on quality, strength and durability,” he continues.
Lightweight and easy to handle
Greenlite recycles post-consumer polystyrene back into beads through its recycling plants. “This material is then used as aggregate mixed with cement and additives to form insulated, soundproof, fireproof, water-resistant, lightweight concrete blocks and screeds,” Cowie notes, adding that more than 6 t of polystyrene was successfully recycled and diverted from landfill on the Mocaa project.
More than 2 000 m2 of lightweight screeds were installed – equating to around 200 cubes of Greenlight lightweight concrete being used at the Zeitz Museum Hotel. The total weight of lightweight screeds once installed was around 100 t, compared to the 400 t that conventional screed would have weighed. Adri Spangenberg, director, Polystyrene Association of South Africa, says
More than 2 000 m 2 of
that, with climate change looming and the rising cost of energy, using recycled polystyrene in building and construction applications is becoming an increasingly popular solution for architects and material specifiers. “Last year alone, more than 2 036 t of polystyrene was recycled countrywide for this use.”
A local smart technology solutions provider recently realised the opportunity to become a leader in the field of renewable energy, by harnessing its expertise on a solar project at its own head office complex.
Located in Midrand, north of Johannesburg, Jasco Park houses over 250 staff members, as well as a data centre and various other amenities. Jasco Power and Energy had a vision to use solar electricity to power much of its campus’s energy needs with the aim of cutting down on the costs of traditional power, reducing dependency on the national grid, and gaining valuable insights into clean energy deployments.
The solution began with the installation of a solar carport system in April 2015, leveraging the real estate available above the carports used by staff and visitors. Phase 1 of the project involved the installation of 53 kWp of solar panels, accompanied by two 25 kW inverters to generate up to 50 kW AC power during peak generation periods.
Jasco recently employed its expertise on a solar project at its own head office complex
Phase 2 saw the additional installation of a brand new solar carport system in the northern section of the Jasco campus. This upgrade saw the total PV generation of the campus increase to 150 kWp, with an increase in invertor output power to 125 kW AC.
According to Kevin Norris, consulting solutions architect, Jasco Power and Energy, the solar system remains ‘tied’ to the national grid, which enables seamless consumption between both the traditional power source and the new solar generation. Energy needs are primarily served by solar power and supported by the national grid where needed.
In this way, Norris explains that, in situations such as power outages, the solar system is not a backup to traditional power, but rather a complementary source of clean energy. In the event of power cuts, the campus still switches over to generators, to keep the data-centre operations running and ensure that staff are still able to work.
“Throughout the process, we used this project as an opportunity to create blueprints for our renewable energy programmes within our clients’ environments,” notes Dave Smith, managing director: Renewable Energy Division, Jasco.
“Our vision for this project is to showcase the opportunities presented by utilising solar energy, and demonstrate tangibly to our clients and encourage other corporates to embrace clean energy,” adds Norris.
By the end of the second phase, the team had effectively matched the campus demand with a reliable supply of new, clean energy. As a result
of this initiative, the company has reduced its maximum demand by 27% and its electrical consumption from the utility by 33%.
“Overall, we’ve reduced the carbon footprint by 50%,” reports Smith, adding that the payback timeframe is pegged at five to six years; if national energy tariffs and carbon taxes rise higher than inflation, however, that timeframe may be brought even further forward. At certain periods of time, such as at weekends, the campus actually becomes a net exporter of energy – selling energy back to the national grid and creating a new, growing revenue stream.
“Most importantly, it has also empowered us to have the right client conversations, as we clearly show them the positive impact of solar – not just from a business perspective, but more broadly in addressing macroeconomic and climate change issues,” concludes Smith.
A locally developed solar water heating system is blazing a path for renewable energy in South Africa. The solar project is showcasing major benefits for a local mining housing development.
The Elon solar PV water heating system uses solar photovoltaic (PV) technology but does not require expensive batteries or inverters.
It is currently being tested at a new 430-unit residential property development in Mokopane, Limpopo. According to the manufacturer, it delivers increased reliability, reduced costs and requires little maintenance.
“Renewable energy is playing an increasingly important role in property development in South Africa and around the world,” says Peter du Plessis, CEO Cranbrook – the property development company working with PowerOptimal to deploy the Elon Solar PV water heaters.
The Elon solar PV water heater consists of a switching unit that allows for the direct connection of solar PV modules to standard South African electric water heaters (geysers).
“The long lifetime and low maintenance of solar PV, combined with using water as a battery, creates an affordable, reliable, manageable and sustainable water heating solution suitable for a range of environments,” says Dr Sean Moolman, CEO, PowerOptimal. “Payback periods are in the range of four to six years,” he continues.
Dr Moolman notes that solar PV modules routinely last over 30 years, with manufacturers providing 25-year performance guarantees. “That’s opposed to solar thermal or heat pump systems that have much shorter lifetimes –typically 10 to 15 years – and require annual maintenance,” he explains.
k eeping costs down
The dramatic fall in solar PV module prices over the past few years has changed what is possible, with the practically unlimited energy from the sun.
Richard Fearon, director, PowerOptimal, says heating water with solar PV used to be a very expensive option but, through the company’s proprietary switching technology, it has become the most cost-effective and reliable way to heat water. “No inverter and no battery mean affordability and reliability. The water itself acts as the battery. This brings down the cost of energy produced by the Elon system to less than 90c/kWh, or about half of what typical residential electricity customers pay for electricity,” he concludes.
Johan Theron, technical director, and Sean Moolman from PowerOptimal
The Green Building Council of South Africa (GBCSA) confirmed that global engineering and infrastructure advisory company Aurecon was the first company to have 50 Green Star-rated buildings certified in South Africa. Aurecon fulfilled the role of green building consultant on these projects.
“Aurecon has been a leader in terms of delivering successful Green Star certifications, as well as collaborating with the GBCSA on the development of various rating tools, and guiding property developers, clients and other professionals in the built environment towards a greener future. I am proud to be able to confirm today that it is the first engineering consultancy in South Africa to have been responsible for 50 Green Star
Aurecon becomes the first consultancy to achieve 50 Green Star ratings in South Africa.
certifications,” says Manfred Braune, executive director: Certifications, GBCSA.
Not only does Aurecon offer ESD solutions for clients, but the company’s green credentials also extend to its offices. Aurecon’s Tshwane office at the Lynnwood Bridge Office Park was the first office building in Tshwane to receive a Green Star rating, and it was also the company’s first Green Star-rated building project in South Africa. The Lynnwood Bridge Office was officially opened in 2011, and the team’s skills and capabilities have continued to evolve ever since. Aurecon’s office in Cape Town opened in August 2011 and delivered the country’s first five-star rating.
Everyone thinks they know what buildings should look like. But the world is changing at an exponential rate and science fiction is fast becoming science fact.
Green design has now become a standard among tenants and property developers and it is changing the way engineers design buildings, as well as the way that clients approach projects.
Aurecon’s engineers design according to green building standards because it has become best practice within the sector. Green Star-rated buildings are no longer rare and tenants have come to expect the buildings they lease to be energy-efficient and sustainable. Aurecon has gone from promoting the importance of green building to clients to being brought in to share its expertise during the concept phase of projects, which is testament to how the industry has changed over the past six years.
Aurecon is a forerunner in identifying the opportunities this presents for clients and facilitating these changes. We question the status quo so that we might reimagine our physical spaces and infrastructure. We create value by rethinking the way that buildings are made. Beneficial for the environment, communityfocused and human centric – our engineering designs add value to our clients’ business operations and achieve their sustainability objectives.
It’s time to embrace radical change.
Environmental compliance is extremely important in the mining industry due to the fact that dust suppression affects the health and safety of not only mine workers, but of surrounding communities as well.
Mtion to supress dust. This is costly due to the fact that water only supresses dust for a short while, Rachelle Botha, environmental manager, I-CAT, points out. “Dust-suppression systems aid in the reduction of water usage – a current environmental issue, especially in the Western Cape.”
This, in effect, assists with water-use licence stipulations for mines, and reduces long-term costs due to excessive water usage. Dust suppression on mines is important in promoting environmental compliance due to the fact that dust fallout affects the air quality for mineworkers, surrounding communities and plant life.
“Dust-suppression systems aid in the reduction of water usage – a current environmental issue, especially in the Western Cape.” – Rachelle b otha, environmental manager, I-CAT
Mining operations are required to comply with the National Dust Control Regulations in terms of the National e nvironmental Management Air Quality Control Act (No. 36 of 2004), which make provision for dust-control management or air-quality control
“We keep on innovating and developing products that provide total dust-management solutions that comply with national and international ‘green’ standards.” –Wessel van der Westhuizen, project manager, I-CAT
Breathing in dust can result in a range of occupational illnesses and diseases, depending on the size and composition of the dust particles, the concentration in the breathing zone of the worker, and how often and how long a person breathes in the dust.
Most dust clouds contain particles of widely varying sizes. Hazardous dust is not always visible. A related impact of dust is safety, as high dust levels can reduce visibility, and thereby become a safety hazard. “Coal dust is a significant cause of underground explosions. Preventing underground explosions and their catastrophic consequences must always be a high priority in all mining operations, particularly underground coal-mining operations,” Botha highlights.
Complying with air quality control
Mining operations are required to comply with the National Dust Control Regulations in terms of the National Environmental Management Air Quality Control Act (No. 36 of 2004), which make
ity control. “These regulations ensure that mines comply in order to protect mineworkers and surrounding communities in terms of health and safety, as dust emissions are an air pollutant,” Botha stresses.
I-CAT is a leading designer and manufacturer of dust-suppression systems for mining operations. “We conduct extensive research and development on our products prior to placing them on the market. We test our products on numerous different soil samples in the field, and we have developed products that have shown very positive results,” asserts Wessel van der Westhuizen, project manager, I-CAT.
As an environmental solutions company, I-CAT has several divisions that focus on many aspects of dust management, such as road haulage, water, and legal and environmental compliance. “Most of our products are environmentally friendly, and are certified by Eco Specifier. We keep on innovating and developing products that provide total dust-management solutions that comply with national and international ‘green’ standards,” Van der Westhuizen reiterates.
“Quality is also key to our products. We have a great success rate due to our extensive research and development, coupled with the affordability of our products in comparison to some of our competitors’. Most importantly, we provide
RDC 20 is an innovative formulation of blended emulsified copolymers and ionic modifiers
an end-to-end, integrated dust-management solution that complies with industry regulations and standards.”
I-CAT offers five highly effective dust-suppression systems for mines. RDC 20 is an innovative formulation of blended emulsified copolymers and ionic modifiers. When sprayed on to the road surface, this water-soluble anionic polyelectrolyte polymer forms a durable cross-linked matrix. The matrix binds fine soil particles into larger heavier particles, which are less prone to becoming airborne.
GreenGrip is a natural, polymer-based, durable gravel-road sealant. It is an environmentally safe alternative to chemically based products for semi-permanent gravel roads on mines and residential areas. It is water-soluble, and is incorporated easily into routine dust-suppression procedures, with no requirement for special equipment or handling precautions.
GreenBit is a natural binding agent combined with an emulsified bituminous product to create a durable gravel-road sealant. It is an environmentally safe alternative to purely chemically based products for permanent gravel roads on mines and residential areas. GreenBit was developed specifically for this application, and produces a durable, smooth and dust-free surface that eliminates the need for frequent maintenance. In terms of customisation, RDC20 and GreenBit comprise a fixed formula that can be adjusted for specific soil types, climatic conditions and traffic volumes.
“We have modified and adjusted this worldleading technology for application in the industrial and mining sectors in Africa,” Van der Westhuizen adds.“We also hold the sole distribution rights for an exciting new mist-nozzle system, developed and manufactured in Europe. It enables the user to have full control of the amount of water used –from minimal water usage, with no effect on the resource, up to higher levels of water usage that increase the level of moisture in the material, which is desirable in some cases. This system is easy to install and operate.”
The DustMonster product line provides outstanding results by creating an ultrafine mist that attracts dust, encapsulating airborne particles, and driving them to the ground.
Site inspections are conducted, whereby I-CAT gathers all of the necessary information from the client in order to compile a baseline of their current dust emissions. It then consults with the environmental department to determine the source of the dust being generated, which involves a full-scale analysis of the soil samples taken so as to be able to provide a tailored solution.
GreenGrip is a natural, polymerbased, durable gravel-road sealant
This includes daily, weekly and monthly client reporting. “We are in constant contact with the client. Most importantly, we have personnel stationed at the mines to look after the projects at hand, and to ensure that the client’s expectations are met.” At present, I-CAT has numerous projects running in South Africa for primary haulage roads and secondary roads.
GreenBit is a natural binding agent combined with an emulsified bituminous product to create a durable gravel-road sealant
“We have in-house capabilities to research and develop products to fit specific client solutions. Assessments are conducted on-site, and soil samples are extracted. Once these have been analysed, we customise the necessary products and service in accordance with the client’s requirements. Each case is different,” Van der Westhuizen emphasises.
TDS 2005 is a unique, environmentally friendly liquid gel used for dust suppression on tailing dams and large open soil areas. The unique properties of this liquid gel allow it to penetrate into the surface, creating a durable bond that binds the loose aggregate by forming a crust. Mines have a number of challenges in reducing windswept dust on and around their tailing dams and open soil areas.
I-CAT has acquired the sole distribution rights for sub-Saharan Africa for state-of-the-art low-pressure misting systems from Europe.
“We have several projects at iron ore and manganese mines in the Northern Cape, coal mines in Mpumalanga, as well as platinum and gold mines in the North West province. We have major projects running internationally in countries such as Australia, Botswana and Namibia, where the primary application is for road haulage on mines,” Botha continues.
In addition, I-CAT conducts a thorough report on the effectiveness of all systems supplied. “We conduct regular trials for mines on different soil samples. Trial and error is key to perfecting our products and systems,” Van der Westhuizen points out.
Botha concludes: “In the process of providing dust-suppression systems for various clients, not only in the mining industry, we have played a key role in the development of local communities. Our clients seek various environmental solutions and, in conjunction with that goal, we have been able to look after the interests of communities by complying with national environmental health standards. We have also been able to create employment for locals on particular projects in specific areas.”
Scientists at the University of Dundee, Scotland, have discovered that E. coli bacteria could play a crucial role in capturing and storing carbon dioxide.
Professor Frank Sargent and colleagues at the University of Dundee’s School of Life Sciences, working with local industry partners Sasol UK and Ingenza Ltd, have developed a process that enables the E. coli bacterium to act as a very efficient carbon capture device.
Sargent says reducing carbon dioxide emissions will require a basket of different solutions and nature offers some exciting options. “Microscopic, single-celled bacteria are used to living in extreme environments and often perform chemical reactions that plants and animals cannot,” he points out.
According to Sargent, the E. coli bacterium can grow in the complete absence of oxygen. When it does this, it makes a special metal-containing enzyme, called FHL, which can interconvert gaseous carbon dioxide with liquid formic acid. The
reaction happens quickly, over a few hours, and at ambient temperatures.
“This could provide an opportunity to capture carbon dioxide into a manageable product that is easily stored, controlled or even used to make other things. The trouble is the normal conversion process is slow and sometime unreliable,” he explains. “Not all bacteria are bad. Some might even save the planet,” he adds.
into empty oil and gas fields. What the scientists have done is develop a process that places the FHL enzyme under pressurised carbon dioxide and hydrogen gas mixtures to speed up the process. “This could be an important breakthrough in biotechnology. It should be possible to optimise the system still further and finally develop a ‘microbial cell factory’ that could be used to mop up carbon dioxide from many different types of industry,” Sargent notes.
While capturing carbon dioxide is a major issue, so is storing or recycling it. There are millions of tonnes of CO2 being pumped into the atmosphere every year. In the UK alone, the net emission of CO2 in 2015 was 404 million tonnes. There is then the question of where to store this once captured, with current suggestions including pumping it underground
Sargent adds that the E. coli solution’s ability to convert CO2 into a liquid that is stable and comparatively easily stored has major implications, especially since formic acid has several industrial uses, which include acting as a preservative and antibacterial agent in livestock feed, a coagulant in the production of rubber and, in salt form, a de-icer for airport runways. The results of
The 20 t excavator is currently being used during 24-hour shifts at the Agni Steels mini steel melting unit, commissioned in the Coega Industrial Development Zone of the Eastern Cape.
To cope efficiently with the demands of scrap metal handling, the HPE Africa workshop raised the cab of this machine and extended the dipper – both by 1 m. An orange-peel grab was installed, which provides a grab capacity of 650 dm³ and load weight of 920 kg.
The excavator, with the grab attached, has a maximum lifting capacity of 1.7 t (with a 70% safe working load) at a 4.5 m height and 6 m reach.
A super saver
“What’s notable about this robust machine is its low diesel consumption, which has been confirmed at 9.8 ℓ/h,” states Alex Ackron, managing director, HPE Africa. “Apart from this machine’s impressive productivity at the plant and its features for smooth and easy control, Agni Steels management is pleased with the swing speed,
HPE Africa works closely with its broad customer base to modify equipment, when necessary, to meet exact performance requirements
the long undercarriage design that ensures greater stability, and the auto idle facility that contributes to diesel savings. Other benefits are the non-common rail engine, which reduces service costs, and the Hyundai factory warranty of two years or 3 000 hours.”
Hyundai R200LC-9S excavators are fitted with six-cylinder, turbocharged, air-cooled Tier II engines to provide high power, reliable performance and economic operation.
A computer-aided power optimisation system ensures the optimum level of power and hydraulic flow for every application. The operator is able to select preferences for boom or swing priority, power mode and optional work tools. The operator cab ensures clear visibility on-site, greater safety and enhanced comfort. These excavators have ground-line access to all critical service and grease points for easy maintenance.
A new star is making its debut in the scrap metal handling sector thanks to a custom approach to business from High Power Equipment Africa (HPE Africa). The Hyundai R200LC-9S excavator has been specially modified for scrap metal handling applications by HPE Africa for its client Agni Steels SA.
The HPE Africa workshop raised the cab of this machine by 1 m and extended the dipper by 1 m, to ensure the machine can cope efficiently with the demands of scrap metal handling
A revolutionary new Wood Hog horizontal grinder, the 3400X is powerful, productive and versatile; this machine will be sure to turn heads! One of the most important features of the 3400X is its standard width of 2.6 m, making it within the legal transport width in any country, no matter what engine is used.
This model accommodates engines from 402 to 596 k, so it is ideal for a broad range of applications in a wide variety of markets. The size of the 3400X allows the same model, using a broad range of engines, to be configured for multiple applications without additional design considerations.
Brendan Moore +27 72 708 9091 brendanm@afrequip.co.za www.afrequip.co.za
Paul Harper +27 78 918 8281
paulh@afrequip.co.za
www.afrequip.co.za
Tracing its roots back to 1957, Morbark has cemented its position as a leading equipment manufacturer for the forestry, recycling and biomass industry. It’s no wonder that local solutions provider AfrEquip has added this world-class brand to its offering.
Leading the charge in AfrEquip’s local line-up is the Morbark 3200 Wood Hog. This aggressive, productive industrial-grade grinder is designed for wood and green waste recycling applications and can handle green waste, regrind, sawmill residue, pallets, and logs up to 60 cm in diameter with ease.
This machine was recently put to the test by AfrEquip client Biomass Producers Namibia, in a project that saw the Morbark 3200 used to clear invasive tree species that had overgrown the landscape on Namibian farm lands. The by-product of this process is sold as fuel to large industrial companies running boilers and burners to produce electricity.
“The Morbark 3200 has surpassed all the competition that the customer has worked with. This is due to the quality and productivity of the machine itself and the uncompromised backup that AfrEquip provides its customers,” notes Brendan Moore, Business Development Manager, AfrEquip.
Helping to get the job done, the Morbark 3200 features an integrated control system that automatically adjusts feed rates and monitors pressure and feed-wheel position to maximise production and engine efficiency.
The hammer mill includes a laser-cut upturn rotor that is factory-balanced with forged hammers, to offer unsurpassed durability and smooth operation.
The 3200 also boasts lower maintenance, more torque and better durability because the feed system’s internal planetary drive has no chains and sprockets. In addition, the machine has proven driveline protection systems to protect against damage from contaminants.
Further augmenting the AfrEquip arsenal is the Mobark 3400X Wood Hog, which provides 50% higher productivity at a <15% increase in premium. The 3400X features sloped infeed sides and an additional 60 cm infeed length when compared with the 3200, giving the operator improved visibility and loading efficiency.
In addition, it includes a hydraulic hinged door that allows for quick and easy access for changing grates; a hydraulically operated debris containment door; dust suppression; and a remote control with tethered backup system, among other things. The Mobark 3400X (wheeled) and 3400XT (tracked) hit the South African market at the start of 2018.
“Both machines come in diesel or electric configurations, as well as with wheeled or tracked undercarriage options,” Moore concludes.
Morbark 3200 options include
• Externally adjustable breakaway torque limiter
• Dust suppression system
• 12- or 16-knife chipper drum assembly
• Variety of grate sizes available
• Variety of conveyors available
• Thrower with extended discharge chute
• Automatic reversing fan system
• 5.5 hp air compressor with lockable enclosure
• Espar heating system for coldweather start
• Hydraulic rod puller
• Trailer to haul soft-start panel
EnviroServ Waste Management put out a call to candidates interested in becoming owner
drivers in the EnviroServ Employee Empowerment Scheme.
The goal was to assist these
would-be business people to manage their own transport company.
Seven years later, the owner driver scheme of this leading African waste management company has been hailed as a success, despite some stumbling blocks along the way. The scheme is in line with government’s BBBEE policy, as all businesses are 100% blackowned and -operated as sole proprietors with the vehicles registered in the owner drivers’ name.
“The scheme was piloted for two years to ensure any teething problems were solved before we appointed more owner drivers,” says Mark Fisher, GM: Logistics, EnviroServ. In mid-2012, the search was on to find more
candidates and 200 applications were received.
To receive financial assistance from banks, owner drivers had to pass credit checks. “When this was completed, 25 drivers were deemed creditworthy and 23 put into operation,” he adds.
But the fledging scheme was put temporarily on the back burner after another owner driver scheme ran into problems that negatively affected the finance house, which then decided not to finance the drivers. This was a challenge for the waste management company, as no vehicles could be purchased.
It took a number of months before another finance house was found, and another two candidates were approved out of 40 applications.
In 2014, EnviroServ put an additional 10 owner driver vehicles on the road, bringing the total number to 33 vehicles. But in February 2015, the second finance house ran into problems and made the call to no longer finance owner drivers.
“After a long struggle and many doors being closed in our faces, we managed to find a finance house again this year for the owner drivers. At first, the long wait was regarded as the death of the scheme, but turned out to be a blessing in disguise. During the wait, the pool of owner drivers became financially stronger and more knowledgeable up to the point where they are now able to finance their own vehicles based on their own company’s financial strength,” Fisher says.
During the scheme’s seven years, there have only been a handful of drivers who did not succeed. “Reasons for this have included uncontrolled medical conditions that caused the driver
not to be able to renew his professional driving permit, fuel theft by employees of the owner driver that was so severe it caused him to go bankrupt, personal issues and one due to driving under the influence.
“There were also drivers who chose not to renew their contracts as they retired or wanted to use their vehicle elsewhere, although the market is tough and not everyone made it on their own,” explains Fisher. Two drivers successfully started their own business without working with EnviroServ.
“One driver has grown his business so much that he has purchased another vehicle, backend and trailer, and is employing seven staff members – proving that the ultimate goal of small businesses development that EnviroServ wants to achieve is possible.”
Four drivers received finance to run two vehicles simultaneously before the finance houses pulled out; however, they have successfully managed to run both vehicles to date.
“Our first owner driver managed to finance and fully pay off three vehicles in total and has currently got approval for vehicles number four and five based on his own business’s financial strength. This means he will be running three vehicles simultaneously,” says Fisher.
Many other owner drivers also enjoyed financial success. “Many are paying off home loans, school fees or putting their children through university – all thanks to the profit generated through their hard work,” he adds.
Fisher says the owner drivers have proved themselves to be hard-working individuals and managed to achieve the targets set by EnviroServ: “Due to this, we have improved our customer
service levels.” The scheme created an average of 95 job opportunities nationwide to assist in government’s key priority of job creation. “Each driver has a truck assistant to load the bins. In terms of our succession plan, we groom these
“one driver has grown his business so much that he has purchased another vehicle, back-end and trailer, and is employing seven staff members – proving that the ultimate goal of small businesses development that enviroserv wants to achieve is possible.”
Mark Fisher, GM: Logistics, EnviroServ
Rolls-Royce has signed a contract with tomato producer Tuinbouwbedrijf Marc Pittoors (TBMP) for the supply of a 7 MWe combined heat and power (CHP) plant.
The plant will be powered by two gas-fired gensets based on the new mediumspeed Bergen B36:45L6 engine and will provide heat and power to a new tomato greenhouse in Belgium. The contract also includes a service agreement for 10 years, with the gensets scheduled to go into operation around November 2018.
TBMP will use the generated electricity to power the greenhouse’s artificial lighting and the heat extracted from exhaust gases and engine cooling systems to heat up the facility.
In addition, cleaned engine exhaust gases will be injected into the greenhouse to increase the level of CO2 and boost plant growth.
Marc Pittoors, CEO, TBMP, says three factors were crucial for the tomato producer in taking this decision: electrical efficiency, expertise and optimum heat balance.
Pittoors notes that Rolls-Royce met all of the above criteria, having developed a gas engine in the early 1990s that pioneered leanburn technology, and by ensuring that 5 ha of greenhouse space is illuminated and 3.5 ha is not. “The greenhouse market is very important for us, and it’s a pleasure to sign a contract with a highly professional customer for this
TBMP’s tomato greenhouse will run more efficiently thanks to a 7 MWe combined heat and power plant fueled by two new types of medium-speed gas engines from Rolls-Royce
new generation of gas engines,” says Jeff Elliott, managing director, Bergen Engines, a wholly owned subsidiary of Rolls-Royce Power Systems and supplier of medium-speed engines.
Rolls-Royce will be supplying the complete CHP plant for this greenhouse, consisting of the power gensets, the exhaust gas systems – including a selective catalytic reduction system and heat exchangers – and the electronic control system.
In total, the technology achieves efficiency rates of more than 96%. Rolls-Royce has years of experience with CHP plants. Since 2005, it has delivered 52 CHP plants with a total installed capacity of 270 MWe for greenhouses in the Netherlands, Belgium, Russia and the UK.
22 - 24 MAY 2018
Now in its eighth year, A-OSH Expo has shown steady growth in industry support year-on-year, helping to match up the sector’s leading product and service providers with a keen audience that represents Africa’s OHS professionals and business leaders. Sven Smit, event director at Specialised Exhibitions Montgomery, says, “A-OSH Expo provides a platform for knowledge exchange and relationship building. The Expo facilitates networking between peers and discussions with the industry’s key associations, and provides a platform for the local OHS sector to source new products and services.”
A-OSH Expo is colocated with Securex South Africa 2018 – the only security and fire trade show of its kind on the African continent. Together, the two shows drew in more than 9 000 visitors in 2017, with over 2 500 attending A-OSH Expo 2017 from 24 countries over three days. A-OSH Expo will once again feature a number of highly popular free-to-attend seminar theatres, which provide in-depth content on critical industry issues. Exhibitors at the show will be able to increase their Exposure and strengthen their brand, reach a highly qualified expert audience, and showcase their newest products and services to thousands of current and prospective customers.
health and safety professionals in South Africa, with over 10 000 members. Neels Nortje, CEO, Saiosh, comments, “Saiosh has been involved with A-OSH Expo since its inception eight years ago, as both partner and exhibitor. We will once again be holding our annual OHS conference at Gallagher Convention Centre during A-OSH Expo 2018. It is truly advantageous for our members to be able to attend the conference and visit the Expo during the same time frame. For the OHS professional, this event has something for all interests and passions.”
More than 60 exhibitors have already signed up for the 2018 show (meaning that the show is already over 85% sold), which will be showcasing a full range of OHS products and services, including disaster management, fall arrest and working at height equipment, first aid products and services, health and safety consultancies, lifting and handling equipment, safety-related software, and hazardous materials storage.
More than two million non-fatal workplace injuries occur in south Africa every year, requiring three or less days off work.”
Key sectors represented include the government, mining, retail, telecommunications, beverages, aviation and banking.
Good business sense
The Saiosh stamp of approval
The event receives a seal of approval from the South African Institute of Occupational Safety and Health (Saiosh), which is recognised by the South African Qualifications Authority as the professional body to register occupational
Smit says, “Workplace health and safety for employees is their human right, but it also makes good business sense for employers as well. More than two million non-fatal workplace injuries occur in South Africa every year, requiring three or less days off work. In addition, good mental health plays a role in keeping employees happy and, therefore, more productive.
A-OSH Expo, Africa’s leading occupational health and safety (OHS) trade exhibition, is returning to the Gallagher Convention Centre in Midrand on 22 to 24 May 2018.
“With safer and happier employees equating to a reduced number of days lost due to workplace illness or accidents, as well as reduced staff turnover, it’s clear that employers need to play their part in improving staff health and, thereby, productivity. In tough economic times, this ultimately equates to a win-win for everyone.”
Visitor entrance to both A-OSH Expo 2018 and Securex South Africa 2018 is free. For more information, please visit www.aosh.co.za, or contact Specialised Exhibitions Montgomery on +27 (0)11 835 1565
Venue Emperors Palace, Ekurhuleni
Date 16 – 18 October 2018
Contact Ann Oosthuizen at ann@iwmsa.co.za
The countdown has begun to the next WasteCon conference. Every alternate year, the Institute of Waste Management of Southern Africa hosts the biggest waste management conference on the local industry calendar.
Venue Sandton Convention Centre, Johannesburg
Date 20 – 21 February 2018
Contact Maria Dippenaar at maria@energyindaba.co.za
With the last event in 2016 having been notable for the high quality of its technical papers and knowledgeable speakers from the local and international waste management industry, this year’s event promises the same high levels of input and engagement that have become a trademark of the event.
The Africa Energy Indaba conference seeks to provide an annual programme that shapes energy policy for the African continent. Key issues that impact the African energy sector will be discussed and debated at the event, based on discussions between leading global policy stakeholders, including African ministers.
Delegates will have the opportunity to discuss, debate and seek solutions to enable adequate energy generation across the continent. Those attending and speaking at the event will include industry experts, project developers, financiers, energy users, government officials and manufacturers.
WAste-to-energy conference
Venue Emperors Palace, Ekurhuleni
Date 22 – 23 March 2018
Contact Jerry Davison at jerry@vukanicomms.co.za
As the concept of waste-to-energy begins to take root in South Africa, the 2018 edition of the Waste-to-Energy Conference seeks to gather thought leaders, government officials and industry heavyweights under one roof to unpack this complex topic.
Attendees will have the opportunity to discuss the latest waste-to-energy conversion technologies and systems, and share solutions and best practices for tackling the waste problem before turning to landfills.
Venue Sandton Convention Centre, Johannesburg
Date 27 – 28 March 2018
Contact Cecilia Braxton at cecilia.braxton@terrapinn.com
Power & Electricity
World Africa is an annual conference aimed at Africa’s power and electricity industry. The conference brings together likeminded individuals who are committed to meeting the growing demand for energy on the African continent.
The conference serves as a platform where delegates can hear about the latest developments, innovations and investment opportunities that will help them succeed in the energy industry. It is colocated with Energy Efficiency World, Clean Technology World and a host of other associated events.
Venue Cape Town International Convention Centre, Cape Town
Date 15 – 17 May 2018
Contact Warda Jakoet at warda.jakoet@spintelligent.com
African Utility Week offers attendees the opportunity to discuss real commercial propositions and streamline their purchasing process by connecting African utility, municipal and commercial decision-makers with technology and service providers.
In 2018, the event will showcase the latest technologies and services in generation (incorporating fossil fuels, off-grid, nuclear and renewables), transmission and distribution (including metering), and new technologies (including storage, mini grids, micro grids, IOT and ICT systems).
Join us at the Gauteng Industrial Symbiosis Workshop
Date: Wednesday, 7 March 2018
Venue: Automotive Industry Development Centre (AIDC) 99 Hendrick Van Eck Street, Rosslyn, Akasia, 0200.
To sign up visit: www.ncpc.co.za or send an email to: ncpc@csir.co.za
IS is a resource efficient approach where unused/ residual resources (material, energy, water, waste, assets, logistics, expertise etc.) of one company are used by another. This results in mutual economic, social and environmental benefit.
Benefits of Industrial Symbiosis in your company are:
• Utilisation of assets
• Landfill costs
• Use of virgin resources
• Water usage
• Hazardous waste
• Transport
Take the first step and make the right connection.