
Municipal Feature
Tshwane’s R30 million illegal dumping problem
Organic Waste
Turning fruit waste into energy
Green Building
The concrete solution to plastic waste
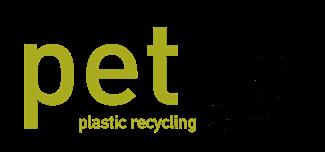
Helping
collectors turn passion into profit
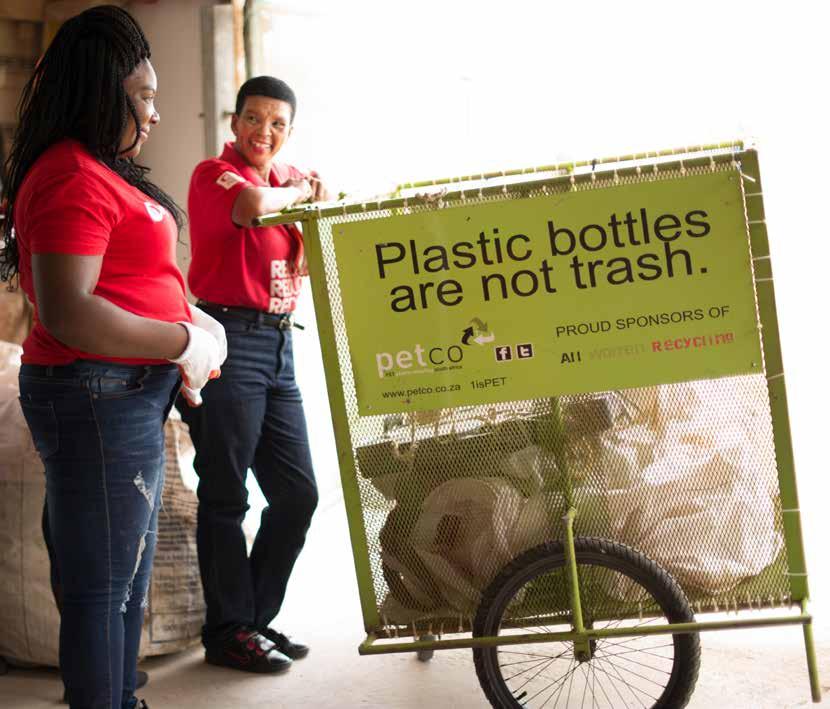
Panel Discussion
As
Tshwane’s R30 million illegal dumping problem
Turning fruit waste into energy
The concrete solution to plastic waste
Helping
As
Vertical single-stage submersible motor pump for wet installation, with free-flow impeller (F-max), stationary or transportable version. Electrical submersible Motor sizes ranging from 1.1 kW to 10.2 kW.
- Pumping station
- Waste water containing long fibre
- Waste water treatment (Including sludge and solid substances treatment and recirculation)
- Municipal and industrial waste water
- Fluids containing gas
- River water transport
- Storm water transport
- Service water
- Grey water
Editor Nombulelo Manyana
Managing editor Alastair Currie
Head of design Beren Bauermeister
Designer Lizette Jonker
Chief sub-editor Tristan Snijders
Contributors Sathisha Barath, Emma Bleeker, Brendon Jewaskiewitz, Stan Jewaskiewitz, Nick Mannie, Anton Nahman, PaulaAnn Novotny, Suzan Oelofse, Garyn Rapson, Michelle Roux, Chris Wiid, Eckart Zollner
Production & client liaison manager
Antois-Leigh Nepgen
Production coordinator Jacqueline Modise
Group sales manager Chilomia Van Wijk
Distribution manager Nomsa Masina
Distribution coordinator Asha Pursotham
Printers Novus Print Montague Gardens
Tel +27 (0)21 550 2300
Advertising sales Joanne Lawrie
Cell +27 (0)82 346 5338 joanne@3smedia.co.za
Publisher Jacques Breytenbach
3S Media
46 Milkyway Avenue, Frankenwald, 2090 PO Box 92026, Norwood 2117
Tel +27 (0)11 233 2600
Fax +27 (0)11 234 7274/5 www.3smedia.co.za
he growing urban population is inevitably increasing the amount of waste generated, thus also prompting an increase in waste volumes going to landfill sites.
Annual subscription subs@3smedia.co.za
R200.00 (incl VAT) South Africa
ISSN 1680-4902
Institute of Waste Management of Southern Africa
Tel +27 (0)11 675 3462 Email iwmsa@iwmsa.co.za
All material herein is copyright protected and may not be reproduced either in whole or in part without the prior written permission of the publisher. The views and opinions of authors expressed in the magazine do not necessarily reflect those of the publisher, editor or the Institute of Waste Management of Southern Africa.
© Copyright 2021. All rights reserved.
Novus Holdings is a Level 2 Broad-Based Black Economic Empowerment (BBBEE) Contributor, with 125% recognised procurement recognition. View our BBBEE scorecard here: https://novus.holdings/sustainability/transformation
Not only is landfilling unsustainable, with most South African major cities set to run out of landfill airspace by 2030 but, if it is not managed effectively, it can be detrimental to the environment and human health. Cities need to start seeing waste as a valuable resource and adopt sustainable waste management habits that promote the three Rs: reuse, recycle and recover.
This includes promoting separation of waste at source, funding sustainable mechanisms of waste disposal, educating the public on waste management, and developing an effective Integrated Waste Management Plan.
The good news is that the South African government has already started upping the ante by updating key legislation in order to promote circularity within the waste sector.
The updating of the regulations around plastic carrier bags and plastic flat bags will promote circularity in waste management and product development by ensuring that these plastic bags are made up of household, industrial and commercial waste diverted from landfills. The bags must be made from a minimum of 50% post-consumer recyclate from 1 January 2023, 75% of recycled materials from the start of 2025, and comprise 100% post-consumer recyclate from 1 January 2027.
Additionally, the ongoing conversation around extended producer responsibility schemes also outlines a new approach to
waste management in South Africa, which places greater responsibility on the producers and manufacturers of waste.
We have also seen a positive rise in initiatives set up by various companies to play their part in reducing waste to landfill – from Woolworths scrapping plastic bags in 50 of its stores, to Coca-Cola South Africa and BanQu launching an innovative payment platform to empower informal waste reclaimers.
All of these initiatives seem to be signalling a dawn for the South African waste sector and ushering in a generation of ecowarriors determined to tackle our waste crisis. In this issue, we take a look at how the waste management sector is adapting to all of these changes and what the various players in the sector are doing to manage waste more effectively.
As we approach the mid-point of 2021, a third Covid-19 wave remains a distinct possibility. We must remain vigilant, while also getting on with things and taking courage from our own resilience. As writer
Sherrilyn Kenyon said, “Life
isn’t
finding shelter in the storm. It’s about learning to dance in the rain.”
In my experience, one of the positive sideeffects of the pandemic, with respect to our sector, has been a general increase in awareness of health- and waste-related matters on the part of the public. Various degrees of isolation and a heightened awareness of Covid-19-related waste has resulted in many thinking further than the kerbside on which the weekly black bags or bins are put out for collection.
Some well-publicised waste management failures over the last few years have also contributed to this increased ‘waste’ awareness. This surely presents an opportunity for both government and the waste industry, which will hopefully result in a greater focus on health and waste management, and increased participation in finding solutions on the part of the general public.
We have been grappling with a severe ‘waste crisis’ for some time now, with government policy and departmental objectives over the last few years often being out of alignment with the reality of waste in South Africa. There has been an overwhelming tendency to eschew the need for engineered sanitary landfill facilities in favour of other philosophies more aligned with the waste hierarchy or circular economy. This has been done without recognising that an effective transition takes years to achieve, and that circular economy (and zero waste) approaches require not less, but
more – and better – waste management. While I believe there is absolutely no debate over the need to embrace a circular economy and strive towards zero waste production and resource efficiency, this transition is not automatic; it will take time to properly develop the required technologies, governance and business models.
For the myriad waste streams currently in existence, it will be of utmost importance to substantially improve the management thereof, in order to protect human health and the environment – the primary purpose of waste management. The management and treatment of all these ‘waste’ streams will have greater importance, as these materials are discarded and then repurposed with higher value, while also recognising that there will always be residual waste to contend with.
While engineered, sanitary landfills (even if only for emergencies) will always be the last resort for any waste management system, no matter how advanced it might be, the available evidence around the world has shown that the availability of environmentally safe landfills is crucial.
Acknowledging the need, it makes sense, then, that the design, construction and operation of our waste management facilities and engineered landfills should be of such a level as to ensure
As I am sure most of you will be aware, Gail Smit and Ann Oosthuizen both officially retired at the end of March and will be assisting with the transition of the new persons taking over their roles over the next few months.
Both these well-respected ladies have played a pivotal role in the leadership, direction and everyday operations of the IWMSA for a number of years, and I cannot understate their value. They have tirelessly ensured that we live up to the expectations of our members and the waste sector. Nothing was too big or too small for them to tackle, and we owe much of where we are today to their efforts. On behalf of the IWMSA, I would like to say a huge thank-you for your commitment over the years and wish you all the very best in the coming years.
In closing, I would also like to take the opportunity to welcome our new executive manager, Nicolle de Bruyn, to the IWMSA. I am sure she will step into the role with great enthusiasm, and look forward to working with her on Council. Welcome to the team!
Organisations and individuals across South Africa are rethinking the recyclability of packaging, educating and uplifting communities, and creating revenue streams among waste reclaimers, while also boosting the circular economy and the environment.
The national polyethylene terephthalate (PET) extended producer responsibility body, PETCO, is recognising excellence in reuse, recycling and waste minimisation among businesses, organisations, community groups and individuals within the South African PET plastic industry, through their environmental awards initiative.
The winners for 2021 are recognised for embracing extended producer responsibility, contributing to driving PET recycling and reflecting the principles of sustainability practices, the circular economy, SMME development, and the advancement of women in the value chain.
Among this year’s eco-warriors are 13 individuals and organisations that have been lauded for their environmental efforts. Announcing this year’s winners of the annual PETCO Awards, CEO Cheri Scholtz said these recycling champions had seen the environmental and economic value of postconsumer PET recycling.
“Their success shows that PET plastic waste is not trash,” she said.
The category winners in this year’s recycling awards include a company that started in a backyard, a company turning traditionally unrecycled material into pallets made from 97% recycled PET (rPET), and a reclaimer so determined to start a recycling business that he sold his car.
Loretta Waterboer (45) started LW Recycling and Trade in 2013, operating out of her backyard in Fisantekraal, where she collected small quantities of any recyclable material she could find, including PET plastic bottles.
With just her one little trolley and no other equipment to assist her, she
made do with what she could while working a full-time job as a domestic worker.
“I remember the first load I ever took to a buyback centre –I only managed to get R21.00. I was genuinely disappointed, but I decided to not give up because I had faith,” said Waterboer.
For Waterboer, the idea of starting a recycling business started with a trip to the local library on a rainy Tuesday afternoon.
“I was actually going to search for jobs at the library when I saw that there was a bus waiting next to the building. When I asked what was going on, they told me they were trying to fill the bus with people to go to a workshop.”
Little did she know, it was a PETCO workshop, where they were teaching women about starting their own recycling business.
“I left there feeling excited and motivated to start doing something that would not only bring me money but also help the community.”
In February 2014, after she had been operating her small-scale business from her backyard, Waterboer decided to quit her job and focus all her energy on her business. She also enrolled as a full-time student, doing a two-year diploma in early childhood development.
“While I was studying, I still continued with my recycling business. I would pick up my recyclables on campus and, even on my daily commute from Fisantekraal to Atlantis, I would make the bus driver stop along the way so I could pick up my waste stuff.
“Everyone looked at me like I was crazy, because people see this as a humiliating job, but I knew at the time that recycling was putting bread on my table. So, I didn’t worry about what people thought,” said Waterboer.
Waterboer started LW Recycling and Trade in 2013, operating out of her backyard
Despite the challenges, her remarkable passion, humility and determination paid off. In 2015, she officially registered her business and was collecting all kinds of waste from the streets of the Fisantekraal neighbourhood.
Just two years later, in 2017, after she had approached Garden Cities the year before about giving her a space to work from in their site yard, they approached her and entered into an enterprise development agreement with her. They gave her an 81 m2 area, which she uses for storage. “They even helped me with resources, like transport and electricity.”
Today, LW Recycling and Trade is still collecting and recycling waste from that premises and is the only accredited and registered recycling company in Fisantekraal. Waterboer is also the only woman recycler in the Durbanville area.
Although she still uses her trusted trolley and her “God-given legs”, she now also has a waste baling machine – gifted to her by PETCO – which she says has helped her collect more waste.
Waterboer is not only proud of what she has accomplished but believes that it’s very important to prioritise waste management, as it keeps the community clean and saves the environment from pollution.
“I’m feeling very overwhelmed and still
LW Recycling and Trade works with women and the youth within the Fisantekraal community, helping them start their own recycling companies
cannot believe that I won the award. But I’m proud of it and I’m proud of myself. I know I’m going to go very far,” says Waterboer.
Waterboer also works with women and the youth within the community, helping them by providing resources and knowledge on how to start their own recycling companies.
“I always tell them: let’s do this together, and I am here to assist you wherever I can. But people get discouraged because they feel this job is humiliating and they are better than this.
“You really need to have a passion for this –don’t worry about everything else. With this job, you don’t spend money to make money. You pick it up for free and are able to put food on the table, but also help save the environment.”
For more information about PETCO and the 2021 PETCO Awards winners, follow this link: www.petco.co.za.
www.petco.co.za
CATEGORY: Environmental Education and Awareness Initiative Winner: Giving Them Wings Foundation NPC (Nelson Mandela Bay, Eastern Cape)
CATEGORY: Top Woman in Collection and Recycling Winner: Loretta Waterboer of LW Recycling and Trade (Fisantekraal, Western Cape)
CATEGORY: Recycling Partnership Gamechanger Joint winners: African Reclaimers Organisation (ARO) and the Bordeaux South Homeowners Association (Johannesburg, Gauteng)
CATEGORY: PET-repreneur
Joint winners: Mandlenkosi Nkosi of Man Recycling (Boksburg, Gauteng) and Matsobane Mawasha of Circular Green (Zebediela, Limpopo)
CATEGORY: Best Community Recycling Initiative Joint winner: The ReTrade Project (Nelson Mandela Bay, Eastern Cape)
CATEGORY: Best New End-Use Products Winner: Palletplast (Pty) Ltd (Blackheath, Western Cape)
CATEGORY: Design for Circularity Winner: The Mpact Versapak Company (Paarl, Western Cape)
CATEGORY: Media Spotlight Winner: Pippa Hudson, Cape Talk Radio (Cape Town, Western Cape)
CATEGORY: Best Community Recycling Initiative Joint winners: Belville Recycling and Trolley Project (Cape Town, Western Cape)
CATEGORY: Recycling Partnership Gamechanger Joint winner: GreenUP (Stellenbosch, Western Cape)
CATEGORY: Local Authority Recycling Innovation Joint winner: City of Cape Town (Cape Town, Western Cape)
CATEGORY: Local Authority Recycling Innovation Joint winner: Department of Agriculture, Rural Development, Land and Environmental Affairs (DARDLEA) (KwaMhlanga, Mpumalanga)
During 2020, South Africans recycled 1.1 million tonnes of paper and paper packaging, putting the country’s latest paper recovery rate at 73% – up from 68.5% in 2019. This is according to paper recycling association RecyclePaperZA, which states that South Africa has kept 19 million tonnes of paper out of landfills over the past 15 years, enough to cover 3 456 soccer fields.
“This is a fantastic achievement, but there is always room for improvement. With more companies moving to paper packaging for their products, consumers need to play their part too,” says Anele Sololo, general manager, RecyclePaperZA.
Sololo believes that it is a good time for citizens, schools and businesses to be more proactive in terms of waste and recycling. “By recycling, we not only reduce the burden on our landfills and support livelihoods, we are also more mindful of the waste we create and where it should be going,” notes Sololo.
“In a world where packaging pollution clogs its waterways and rubbish lines the streets, recycling is something that citizens can do to bring about a cleaner South Africa.”
In order to tackle South Africa’s rising e-waste challenge, key local and international stakeholders have joined forces to launch an ambitious project set to bring about economic opportunities while ensuring workable and safe solutions for the management of e-waste.
Rooted in the global Sustainable Recycling Industries (SRI) programme, the local chapter of the SRI project aims to build capacity for sustainable e-waste recycling, by supporting related national initiatives and implementing pilot ventures.
The SRI project in South Africa involves various stakeholders including The Appliance Bank (TAB) – a training programme for unemployed men that gives them the technical skills needed to repair damaged and customer-returned small appliances.
TAB will provide a two-year training programme for unemployed men to establish their own sustainable businesses. The men repair the donated household appliances and sell them for a profit in their communities. The pilot project is kicking off in iLembe, KwaZulu-Natal.
The first phase of the SRI programme was implemented between 2013 and 2018 and it is now in its second phase (2019 to 2023). The overall development objective of the SRI programme (Phase 2) is to create favourable framework conditions, which enable the development of a sustainable recycling industry for e-waste and any related waste streams.
The City of Cape Town (CoCT) is appealing to the public to take part in its organic food waste project, aimed at diverting food waste from landfills. The pilot project will be trialled to assess its efficacy and potential for further roll-out.
The food waste diversion project will operate from four CoCT drop-off sites in Belhar, Killarney, Hout Bay and Woodstock, and will have four pop-up sites in the Cape Town CBD, Claremont CBD, Durbanville and Somerset West.
Participants will be issued a 5 ℓ bucket with an information leaflet, to fill with organic food waste,
temporarily storing it in the fridge or freezer; when the buckets are filled, the waste can be taken to the designated site where the bucket was received.
The bucket will then be decanted, cleaned and reissued to the individual. The project will run until 30 June, with 200 participants per site.
Alison Davison, head: Waste Minimisation, CoCT, says it is among the various strategies being trialled to divert food waste from landfills, including a garden waste programme and a home composting container programme.
To minimise packaging waste ending up in landfills, Woolworths announced that 50 of its stores will switch to being plastic-free.
Woolworths said it will no longer sell single-use plastic bags, as part of its vision is to steer towards zero packaging waste to landfill. The retailer said that, while it encouraged customers to bring and use reusable bags, stores will also sell a recycled bag manufactured locally. The bag retails at R6.49.
These stores, based mainly in Gauteng and the Western Cape, take Woolworths to over 200 stores in Southern Africa free of single-use plastic bags. This is a significant achievement at a time when we have had so many supply uncertainties.
In the face of the worsening effects of climate change, increasing energy prices in South Africa, and a more challenging business environment, companies have been left with no choice but to improve their operations and strive to become more energy efficient.
Barry Bredenkamp of the South African National Energy Development Institute (Sanedi) explains that this trend is demonstrated by the increased number of Section 12L Energy Efficiency tax incentive applications Sanedi has received since March 2020.
The 12L tax incentive, according to the Income Tax Act (No. 58 of 1962), provides an allowance for businesses to implement energy efficiency savings. The savings allow for a tax deduction of R0.95/kWh saved on energy consumption. From March to May 2020, the number of applications more than doubled.
Bredenkamp says that part of the reason for the update since March is that people finally had time to consider their energy bill and carbon tax payable during lockdown alert level 5.
“Large power users, and South Africans in general, are well informed about our energy landscape and have finally woken up to the reality of the carbon tax. They know that there are things they can do to reduce power use and costs.”
According to the Event Greening Forum, the typical conference attendee produces 1.89 kg of waste each day, of which 1.16 kg will end up in a landfill. Carmen Wagener, operations director of Reed Exhibitions Africa, says the company’s waste reduction policy is continually being reviewed and fine-tuned to implement solutions wherever possible.
Reed Exhibitions Africa’s greening policy and procedures already include seeking out and recommending venues that have a sound greening policy, as well as monitoring the carbon footprint of events and implementing steps to counteract them.
Reed is also constantly stepping up its energy saving and fine-tuning waste management, with a view to reused or recycle waste wherever possible. The planned update of all its green guidelines will take effect this year, as in-person gatherings are allowed to return to the events calendar.
These will set a benchmark against which the company can meet and improve its efforts as new solutions come to market.
One of the major drives is to promote the use of printed fabric graphics to clients and going digital by promoting digital signage at exhibitions, electronic brochures and e-ticketing where possible.
These challenges manifest as the ineffective utilisation of municipal resources (financial, equipment, capacity), non-compliance with environmental legislation, no or poor levels of service delivery, and potential environmental and human health impacts. The legal requirements for municipalities to provide refuse removal services have evolved and become more demanding over the years. Municipalities often refer to ‘unfunded mandates’ that have been added with the implementation of the National Environmental Management: Waste Act (No. 59 of 2008). The overlap of functions between districts and local municipalities has also been mentioned as a challenge that results in a lack of accountability, hampering solid waste management in small municipalities1
The South African waste sector has experienced a surge in waste regulation since the Act came into effect on 1 July 2009. The sector has moved from a situation of limited waste regulation to the current state, which advocates for moving waste up the waste management hierarchy, away from disposal, towards more sustainable alternative waste management options, with regulatory control instituted on most waste management activities. According to many, this increase in
Reports dating back to 2007 and 2008 show that municipalities in South Africa are faced with four broad challenges, namely: financial management, equipment management, labour management, and institutional behaviour.
By Dr Suzan Oelofse*
regulatory control has introduced a compliance burden, which has increased both operational and capital costs for the waste sector. The cost of landfilling municipal solid waste is a case in point, which saw an increase associated with the introduction of new landfill barrier requirements. Experts in the design of landfills have indicated that the cost of compliance with the new requirements is close to double when compared to the Minimum Requirements of 1998.
The increase in the cost of landfilling in itself is not necessarily a bad thing. An increase in the cost of landfilling is important to make alternative treatment options more attractive and to encourage municipalities and industry to explore alternative waste management options towards ‘saving’ landfill airspace for residual waste (with associated higher disposal tariffs). The real problem is that compliance with the new requirements is generally not a priority for many municipalities.
A shortage of landfill airspace in Gauteng and the Western Cape was the main trigger that resulted in action towards waste diversion away from landfill to alternative waste treatment technologies (AWTT) in these provinces. For example, a ban on organic waste disposal in the Western Cape has seen an increase in investment in composting facilities, and the shortage of
landfill airspace in Gauteng saw investment by the Gauteng Infrastructure Funding Agency in feasibility studies for AWTT in all three metros in Gauteng.
Municipalities perceive moving waste up the waste management hierarchy as an ‘unfunded mandate’. The Constitution of South Africa outlines the waste management mandate of municipalities as refuse removal, refuse dumps and solid waste disposal. A consequence of this situation is that municipalities are slow to initiate waste separation-at-source initiatives, resulting in only 7% of urban households and 2.6% of households in towns and rural areas showing regular recycling behaviour in 2015. Common operational challenges faced by municipalities include littering, illegal dumping, service backlogs, service interruptions resulting from breakdowns associated with ageing vehicles, inadequate plant and equipment, and insufficient waste management infrastructure. Many municipal landfills are nearing the end of their designed lifespan; while the development of new infrastructure such as materials recovery facilities, buyback centres, and drop-off centres to divert waste away from landfill, and the introduction of sustainable AWTT options, are lagging behind. Many municipal by-laws assign ownership of waste to the municipality, which hampers private sector
involvement in waste separation-at-source initiatives and investment in infrastructure. The sharing of costs and benefits associated with the sale of recyclable materials is a sticking point that should be resolved to unlock these situations.
Municipalities spend between 20% and 50% of their annual budget on municipal solid waste management2, of which 50% to 90% is typically allocated to waste collection. The average operating and capital expenditure on solid waste per municipality in KwaZuluNatal in 2017/18 was R107 664 193 and R37 308 905 respectively3. The costs of providing waste removal services vary significantly between municipalities, and nonpayment of waste services by residents and businesses therefore has a direct impact on a municipality’s ability to render services. In addition, municipalities are expected to provide services to poor households even if they cannot afford to pay.
Municipalities are in a position to recover the cost associated with waste collection and management services through the collection of rates and taxes, and by charging gate fees for the disposal of waste at landfills, but full cost accounting is not widely implemented. In addition, the Policy for the Provision of Basic Refuse Removal Services to Indigent
Households requires municipalities to provide waste collection services to non-paying indigent households. This service is often financed through cross-subsidisation, by charging a higher collection fee in affluent areas, or by linking the tariff to the property size or value. Therefore, households are unlikely to be willing to pay an additional fee for the collection of source-separated recyclables. Adding a service for the collection of source-separated waste is likely to increase the costs of collection, depending on the format of the collection system, but will also result in landfill airspace savings. In addition, investment in appropriate infrastructure and equipment to support waste diversion from landfill is required.
Government is looking to industry to support the development of capital infrastructure through private sector investment, but municipalities are reluctant to enter into public-private partnerships due to the complex administrative and legal processes required to establish such partnerships. Municipalities need to build the required capacity and competence to establish, manage and maintain partnership agreements to create an enabling environment for the much-needed investment in infrastructure.
In conclusion, it is clear that municipalities face many challenges, despite national
policy and strategies providing the enabling environment for moving waste up the waste management hierarchy towards recycling and AWTT. To effect the required change, municipalities will have to get their house in order and create an enabling environment for private sector support and investment in recycling and AWTT infrastructure.
*Dr Suzan Oelofse is a principal researcher at the CSIR, with expertise in integrated waste management.
References:
1 Statistics South Africa (Stats SA) 2016. The state of basic service delivery in South Africa: In-depth analysis of the Community Survey 2016 data. Statistics South Africa. Pretoria. 120 pp. Report No. 03-01-22 2016. ISBN 978-0-621-45302-7
2 Dukhan, A., Bourbon-Séclet, C. and Yannic, N. (2012). Linking public and private action for sustainable waste management. Private Sector and Development, 15 (October): 9-11. https://issuu.com/objectifdeveloppement/ docs/magazine_proparco_psd15_uk
3 Municipal Demarcation Board (MDB) (2018). Municipal powers and functions capacity assessment 2018. National report: Executive summary
A recently completed project funded by the Waste Research, Development and Innovation Roadmap set out to understand the root causes for the dominance of landfilling as a waste management option in South Africa. By Anton Nahman*
The National Environmental Management: Waste Act (No. 59 of 2008) and National Waste Management Strategy (NWMS) call for the increased diversion of waste away from landfill towards reuse, recycling and recovery. This is in line with the waste management hierarchy, according to which waste should first be avoided, reduced, reused, recycled or recovered –with disposal as a last resort. It is also in line with the concept of a circular economy, which is central to the recently updated NWMS.
However, the majority of waste generated in South Africa is still disposed of (either to landfill or to a communal/own dumpsite, or illegally dumped). This represents a significant loss of valuable resources that could potentially be recovered and recycled for further processing. Disposal of waste also gives rise to significant social and environmental externalities, while many municipalities are rapidly running out of landfill airspace.
In a recently completed project funded by the Waste Research, Development and Innovation Roadmap, we set out to understand the root causes for the dominance of landfilling as a waste management option in South Africa, and to identify relevant solutions for addressing the issues and increasing the diversion of waste from landfill towards alternative waste treatment technologies. Based on consultation with experts and stakeholders, a wide range of barriers to investment
in alternative waste treatment were identified. Some of the issues identified include:
1. Legislative barriers
• Municipalities are mandated to collect and dispose of waste; KPIs for municipal waste managers are therefore based on the quantities of waste disposed.
• Legislation inhibits private sector participation or investment in waste diversion or beneficiation activities, or makes it a long and complex process to get projects off the ground.
2. Low cost of landfilling relative to alternative treatment technologies, such that there is no incentive to divert waste from landfill
• Many landfill sites are unregulated, unlicensed and/or non-compliant, and therefore the cost of landfilling is artificially low.
• Lack of full cost accounting or cost recovery for waste services.
• Externalities (social and environmental impacts) associated with landfill disposal are not internalised in tariffs.
• High capital and operating costs are associated with alternative treatment technologies.
3. Lack of funding to upgrade landfill infrastructure, or to invest in alternative treatment technologies
4. Perceived lack of benefits from alternative waste treatment technologies
• Where there is still airspace available, there is no immediate benefit from diverting waste.
• Failure to properly understand or account for the benefits, which are often long term or indirect in nature.
• Market prices for recyclables are too low relative to the costs of collecting and recovering.
• The fluctuating market price of virgin materials (linked to global commodity prices) relative to recycled materials means there is no guaranteed market for recycled materials, which disincentivises investment in recycling infrastructure.
• In many cases, there is a lack of markets for recyclables, or for the end-products produced from recycled materials.
• Some recycled materials (or the end-products produced from such materials) are unable to compete in the market, because virgin alternatives tend to be cheaper (particularly when oil prices are low).
5. Behavioural and institutional issues
• Government has not created a sufficiently effective enabling environment.
• Producers don’t take responsibility for their products at end of life.
• It is difficult to change deeply entrenched behavioural patterns among waste generators.
• Institutional issues exist within municipalities.
• A lack of effective communication, collaboration and partnerships pervades the value chain. During the project, we identified a broad range of solutions to these issues, and for
stimulating investment in alternative treatment technologies. Given the complex nature of the problem, and the broad range of issues to be addressed, no single type of intervention will be effective on its own – nor will actions by any one role player be effective in isolation. Instead, implementing the waste hierarchy and transitioning to a circular economy will require a coherent set of mutually reinforcing regulatory, economic and other interventions, with actions required by all relevant role players – including the various tiers of government (from national to local), industry, waste generators, etc.
In particular, the outcomes of the study make it clear that a landfill tax, which is often discussed as a potential ‘silver bullet’ for diverting waste from landfill, would not be effective, and would in fact end up doing more harm than good. A number of prerequisites need to be in place before a landfill tax can be considered, including:
• licensing of landfill sites, and compliance with permit conditions as well as norms and standards
• viable alternatives to landfill disposal (e.g. options for recycling) to enable a change in behaviour without stimulating an increase in illegal dumping
• effective access control, functioning weighbridges and adequate reporting systems, to enable accurate monitoring and reporting of waste quantities
• capacity to monitor and control illegal dumping
• full cost accounting, and cost-reflective gate fees and waste tariffs, to enable cost recovery
• municipalities must be in a sufficiently sound financial position for payment of the tax. Indeed, addressing these issues would in and of itself increase the cost of landfilling (and thereby result in a diversion of waste from landfill), even in the absence of a landfill tax. In this way, the potential negative impacts of such a tax (e.g. stimulating an increase in illegal dumping, negative impacts on municipal finances, etc.) can be avoided.
Strictly speaking, environmental taxes (such as landfill taxes) are only appropriate for addressing specific market failures, such as externalities. The externalities associated with landfill disposal are a relatively small driver of the current gap between the costs of landfilling and alternative treatment technologies. Environmental taxes are not appropriate when there are underlying structural issues – e.g. pervasive underpricing of waste services due to unlicensed or non-compliant landfill sites, lack of full cost accounting, tariffs set below the levels required for cost-recovery, etc. These issues need to be addressed before a landfill tax could be considered.
*Anton Nahman is a senior researcher at the CSIR, with expertise in integrated waste management.
According to GreenCape’s 2020 Market Intelligence Report for the Waste Sector , opportunities in waste organics, electronic waste, waste plastics and builder’s rubble have the potential to add considerable value to the economy.
By Dr Linda Godfrey*
The short answer to the headline is no.
In a 2013 thematic investment review ‘No time to waste’, the Bank of America Merrill Lynch identified South Africa as one of five emerging markets with “exciting opportunities” in the waste sector1.
The other countries presenting significant opportunities included Brazil, China, India and Russia. In particular, the bank noted that the fastest growth was coming from emerging markets, and new opportunities around secondary raw material and energy recovery from waste. In the case of South Africa, the bank noted that declining landfill space would make recycling a “cost-effective necessity”.
However, the review also acknowledged that the biggest challenge facing the South African waste sector in its move away from landfilling was the low cost of landfilling, which “renders alternative technologies and practices financially unsustainable”.
A recommendation to address this price failing was to build capacity in full cost accounting of waste management within municipalities. In 2014, Engineering News featured an article, ‘South Africa begins waking up to the economic potential of waste recycling’, noting that the costs that can be avoided by diverting waste from landfill, and the benefits associated
with recovering the resources currently lost to landfill, are significant.
Nearly a decade on, I would argue that this potential has not yet been realised in South Africa. While recycling rates have increased between 2011 and 2017, the disposal of waste to landfill, often to uncontrolled or controlled dumpsites, remains the dominant technology solution for the end-of-life management of waste in the country. This is despite extensive policy that supports the implementation of the waste hierarchy and, more recently, the circular economy.
According to GreenCape’s 2020 Market Intelligence Report for the Waste Sector 2 , opportunities in waste organics, electronic waste, waste plastics and builder’s rubble have the potential to add considerable value to the economy. The report notes that private sector investments have grown, both in number and scale, which is likely to accelerate in the next three to five years. It also notes that key drivers to unlocking these opportunities include legislation, extended producer responsibility (EPR), government initiatives, the increasing cost of disposal, and dwindling landfill airspace.
The R109.6 billion of investment announcements made at the 2020 South Africa Investment Conference saw little promise of investment in the waste sector, amounting to only 0.2% of the total announcements.
While significant opportunity exists in the South African waste sector, this opportunity has not yet been realised, and public and private sector investment has been slow to materialise. Why is this the case, when the potential clearly exists?
According to the Africa Waste Management Outlook 3, waste management project finance and implementation face a number of constraints in Africa, and are often considered high risk; owing to:
• insufficient future cash flow
• improper evaluation of project life-cycle costs
• low probability of success during appraisal
• lack of ability to pay back loans
• lack of cost control, operational expertise and risk management
• lack of/inadequate cost recovery options
• lack of effective governance frameworks
• administrative and operational flaws, suggesting that even with suitable finance from the central government or funding bodies, with no repayment requirements, a project will fail owing to unsuitable institutional, policy and service conditions.
The reality is that most municipalities in South Africa are struggling and not in a position to direct public sector funding into major waste management investments. With the economy stalling, even pre-Covid-19, and with significant government funding redirected during
2021 to the national pandemic response, national government is also struggling to make a case for significant investments in waste infrastructure.
The reality, given the state of the South African economy, is that government does not have the financial resources, on its own, to unlock the opportunities of this sector.
It is going to need significant private sector investment, both across value chains and opportunity waste streams. As noted by the OECD4, investments by businesses will be a key factor in unlocking a circular economy. This means that if we are to unlock the opportunities of the waste and secondary resources sector, we have to look to the private sector.
However, government has a crucial role to play in unlocking this private sector investment. As noted by the OECD, “Governments have used several financing mechanisms, including grants, loans and tax exemptions that support investments made by business”.
Yet, out of the suite of economic instruments available, the South African government has tended to lean towards punitive instruments such as taxes and EPR fees, further enforced through legislation, as opposed to incentives. The OECD notes that several countries have used funds originating from environmental charges and taxes to
finance waste management investments. In South Africa, there are currently a number of environmental taxes being implemented by National Treasury, some of which have direct relevance to the waste sector.
These include taxes on plastic bags (fossilbased and bio-based), tyres and incandescent light bulbs, and related taxes such as the carbon tax and sugar tax. Estimated revenue from the first three of these taxes for the 2020/21 financial year totalled R1.08 billion5
Imagine if all of that revenue were reinvested back into unlocking private sector investment opportunities in implementing the waste hierarchy...
Contemplating why private sector investments have been slow to materialise in the South African waste and secondary resources sector, I’m left with more questions than answers:
• Do we have the right policies in place?
• Have we created an enabling environment for the private sector to thrive?
• Have we done all that we can in terms of economic incentives?
• Are we sending clear policy signals regarding future opportunities?
• Have we harnessed the opportunity of green public procurement?
• Are we reducing investment risks through demonstration?
• Have we created fertile ground at local government level?
The recently published third National Waste Management Strategy6 reconfirms the potential of the sector. The question is: what do we need to do differently this time to fully unlock this opportunity?
*Dr Linda Godfrey is a principal researcher at the CSIR, with expertise in integrated waste management
References:
1 BofA Merrill Lynch Global Research (2013). No Time to Waste–Global Waste Primer.
2 GreenCape (2020). Market intelligence report – Waste, https://www.greencape.co.za/ assets/Uploads/WASTE_MIR_20200331.pdf
3 UNEP (2018). Africa Waste Management Outlook, https://wedocs.unep.org/ handle/20.500.11822/25514
4 OECD (2019). Waste management and the circular economy in selected OECD countries, https://doi. org/10.1787/9789264309395-en
5 National Treasury (2021). Budget Review 2021, http://www.treasury.gov.za/documents/ national%20budget/2021/review/FullBR.pdf
6 DEFF (2021). National Waste Management Strategy 2020, http://sawic.environment.gov. za/documents/12777.pdf
Inefficient waste management, the collapse of infrastructure, corruption, health and safety, climate change and pollution have necessitated that serious action be taken to protect our constitutional rights and the environment.
By Stan Jewaskiewitz*
Few municipalities across South Africa comply with the waste regulations and local government lacks the responsibility or commitment for proper waste management, as well as the monitoring and licensing of facilities.
The impacts of landfill sites include odour, wind scatter, regular fires (smoke), and pollution (air, soil and water). The effects of these increase where communities live close to landfills.
Compliance to permit conditions is critical in mitigating the impacts of landfill sites. Many municipal landfill sites are not licensed, while licensed sites do not always operate according to their permit conditions. Poorly operated landfill sites impact on the environment and can cause nuisances and health risks to communities living nearby.
South Africa has, by and large, some of the most advanced legislation and regulations governing the management and disposal of municipal solid waste (MSW). MSW comprises mostly domestic, commercial and industrial wastes, excluding hazardous wastes. The guidelines for the disposal of wastes to landfill (first edition) were published in 1994, followed by the second edition in 1998, namely Department of Water Affairs & Forestry, Second Edition, 1998. Waste Management Series. Minimum Requirements for Waste Disposal by Landfill. These are still in force today.
Waste management is also governed by the National Environmental Management: Waste Act (No. 59 of 2008), as amended, the waste classification and management regulations (R634), and the norms and standards for disposal of waste to landfill (R635 and R636).
Within the last two decades, there has been a concerted effort by the various regulatory authorities and other institutions to promote good waste management practices in accordance with the legislation via conferences, seminars, workshops and numerous training courses.
In 2011, the CSIR developed and published a good practice guide: Municipal waste
management – good practices. Edition 1. CSIR, Pretoria. ISBN No: 978-0-7988-5596-9, March 2011. This guide (or toolkit) was intended to assist municipalities with improving their waste management and disposal practices.
So, where did it go wrong?
Despite the legislation in place, the technical guidance and training provided, there are many landfills that are still not licensed or, if licensed, are not operated to any standard.
The photographs accompanying this article show the typical conditions still encountered on many municipal landfill sites across South Africa. As can be seen, none of these sites comply with any standards whatsoever!
An audit of some 127 landfill sites, spread across all nine provinces, was carried out in 2019 by a private organisation in collaboration with the relevant authorities. In the audit, it was found that 78% of the municipalities did not comply with the minimum requirements for landfill; only 22% complied. It also found that the compliance of landfill sites marginally improved between 2015 and 2018; this significantly declined thereafter.
The findings also show that there is a
lack of political will to sustainably manage wastes by way of reuse, recycling and reducing, and to maintain and properly manage waste management infrastructure. There is also a lack of adequate waste management expertise among those responsible for the proper management of wastes.
The poor management and operation of landfill sites can be ascribed to various factors, including:
• corruption
• lack of leadership and responsibility
• lack of waste management expertise
• outright disrespect for the relevant legislation and the environment
• insufficient funds or budget available for the proper development of infrastructure (landfills), landfilling management and operations, and rehabilitation
• misappropriation of funds or budget
• lack of political will
• low priority accorded to waste management and landfills in particular.
It has also been shown that, in the case of all illegal landfill sites (sites with no licence or operation plan) and those that do not comply with the minimum requirements, municipalities continue to use these sites for waste disposal regardless. These sites continue to create a risk for the environment and the health of people in the surrounding community.
In order to address the various issues as discussed above, consideration should be given to the following:
• The community needs to become involved with the functions of waste management within the municipality. This would increase the transparency of municipal processes and thereby improve the management of wastes.
• Municipalities should be forced
to comply with their democratic responsibilities to create monitoring committees for the communities where they can provide input and operations can be critically analysed. Municipalities should also be forced to comply with their constitutional responsibilities with respect to sustainable landfill operations and management, and to demonstrate improvement on an annual basis.
• Relevant provincial departments should play a more active role in monitoring, law enforcement and licensing authority to improve waste management and landfill operations at local government level, in order to comply with their constitutional responsibilities.
*Stan Jewaskiewitz is a technical director at Envitech Solutions.
The following are required for producers: PLASTIC
Existing producers to register with the Department of Forestry, Fisheries and the Environment from 5 May and no later than 5 November 2021 (as per the amended EPR regulations released on 15 January 2021).
Join or form an EPR scheme that includes the entire value chain. Be accountable for the operation and performance of an EPR scheme.
Pay the appropriate fees to the EPR scheme.
Fulfil monitoring and reporting obligations –to begin Q1 2022.
Growth in South Africa’s population and increased urbanisation has led to an increase in per capita waste generation. This places stress on current landfills and results in litter in the environment.
As a pro-active response to the growing national concern around waste and its impact on society and the environment, South Africa has recently published the Section 18 Regulations to the National Environmental Management: Waste Act on 5 November 2020, which refers to the Extended Producer Responsibility (EPR) aspect of the National Environmental Management Waste Act (NEMWA). The regulations will come into effect on 5 May 2021.
In essence, this new legislation makes EPR mandatory for all producers and importers of packaging. It changes how producers, brand owners, retailers and importers design, make, sell and keep their products in the recycling loop as far as is practicably possible. Any company or brand that makes or imports any form of plastic packaging for distribution is required to pay an EPR fee. Strict targets have been set by Government, for yearly collection and recycling, that need to be met over the next five years. Prouders can either join an existing PRO or allocate funding for the implementation of an independent EPR scheme.
EPR will see an investment in collection infrastructure. Not only will this provide consumers with more convenient recycling facilities, but a concerted recovery effort at the pre-consumer or post-industrial phase. Intensive consumer awareness campaigns will also help to drive behaviour change.
All companies involved in the value chain have to work
together to ensure that less waste goes to landfill. Instead of supporting the outdated, linear approach of producing, using and discarding plastic packaging waste that continues to hold value after it has been used, our focus is now on developing a true circular economy within South Africa – where the value of waste is never lost but is kept within the economy by ensuring that these materials are reused and recycled into many new and useful materials.
Luckily, South Africa's plastics industry is well positioned for this next stage of environmental legislation. We have four voluntary, industry-led PRO’s that have been running for many years now and have impressive track-records of collection and recycling successes, namely PETCO for PET, Polyco for polyolefins (PP, HDPE, LDPE/LLDPE and Multi-layer), the Polystyrene Association for polystyrene, Southern African Vinyls Association for PVC.
Each of these PROs collect voluntary EPR fees from their members, and use the revenue they generate to support the collection, sorting and recycling of recyclable materials by informal waste pickers, small and medium-sized collectors and large-scale mechanical recyclers.
The new Section 18 regulations are a welcome step forward towards a more collaborative approach between government and industry. As an industry, we are committed to continue working closely with government as this process unfolds. We urge you to start the process now by engaging with the relevant plastics industry PRO’s listed below. Reporting against the gazetted targets starts in Jan 2022.
The EIE Group provides best-in-class materials handling and industrial equipment. CEO Gary Neubert expands on the Group’s total solutions offering for the waste management and recycling industries.
in the waste management and recycling segments?
management. There are a large range of forklifts, with each one being designed for specific jobs.
Please expand on EIE Group’s total solutions offering for the waste management sector.
GN 600SA Holdings has been a household name in waste management solutions for the past 53 years. Urbanisation has resulted in the overproduction of waste, negatively affecting the environment. It is for this reason that we align ourselves with the best-quality products to ensure optimal usage under extreme conditions. Our product offering includes refuse compactors, hooklifts and skiploaders.
How does 600SA fit into the EIE Group?
600SA forms part of the EIE Group and the JSE-listed enX Group of companies. 600SA offers a complete solution for all materials handling needs, providing life-time value for its customers. Our Cleaning and Waste Division specifically focuses on the waste management and recycling industry.
What are the key products marketed
Our Oracki and Usimeca refuse compactors are designed for refuse collection companies and municipalities operating in urban waste collection. Different volume options are available. The ORV series, which works on the principle of container loading or manual loading, can meet the requirements of our customers at the highest level.
Our VDL skiploaders are specifically developed around the concepts of reach and stability. The hexagonal lifting arms can be operated independently, offering maximum flexibility. The buckling shape of the lifting arms also contributes to efficient manoeuvring in confined spaces. Even inclined containers are easy to lift and place.
We support the recycling industry with the latest addition of our VDL hooklift. It boasts quick and convenient loading, tipping and unloading, with a high degree of operational reliability and efficiency.
The user-friendly design also offers hydraulic and pneumatics operation from inside the truck cab.
What are some of the common mistakes in selecting a forklift?
Choosing the right forklift is important for your business. It affects everything from operation costs and productivity to employee morale and stock
Your business environment will influence the type of forklift, tyre selection and fuel type. Consider the floor surface and conditions the forklift will be working in.
Load capacity should be taken into consideration. What stock will the forklift be handling, what is your average load weight, what is the heaviest load you need to lift, and what is the width of your loads? The type of load also matters, as there are specific forklift attachments that can enhance a standard forklift and help you move the load more efficiently. There are three types of fuel options – electric, gas or diesel. Electric forklifts will cost more initially, but you will reap the rewards over time, as they have a longer lifespan and cheaper consumption compared to other types of forklifts. Operating very quietly and producing no emissions, they are recommended for working indoors or in cold climates. Gas or diesel forklifts can lift much bigger loads and move faster. Diesel forklifts are recommended if the forklift will be used for heavy lifting or outdoors.
We offer a wide variety of CT Power forklifts to meet customer requirements. Our services include long- and short-term rentals, service and maintenance contracts, sales of new and used equipment and parts, load testing, and battery bay management.
The city of Tshwane has prioritised its resources to eradicate the increasing number of illegal dumping sites across various regions in the metro. This has seen over 2 300 illegal dumping sites cleared in as little as two months.
he occurrence of illegal dumping is an ongoing problem across all nine provinces of South Africa. Moreover, these dumping sites are now on the increase. In Tshwane, there are approximately 671 illegal dumping hot spots – and those are just the ones that have been identified. They are mostly sited in townships like Soshanguve, Atteridgeville and Mamelodi.
The severity of the illegal dumping problem the City of Tshwane is battling can be seen as you drive through Atteridgeville, located to the west of Pretoria. One is immediately greeted by rows of trash as you enter the township. Every second corner is littered with waste, has been recently cleared, or has someone unloading their bin on to the massive heap already there.
According to Dana Wannenburg, MMC: Environmental and Agricultural Management, the City of Tshwane spends over R30 million per year to clear and clean these illegal dumping sites; however, Wannenburg says it feels like fighting a losing battle.
“Local municipalities do their best to inform and educate residents about the dangers of illegal dumping and the importance of using the available waste removal services; however, it is so disheartening to our officials who clean up an area, at great expense, and go back just two days later to find it filled with
dumped refuse again,” says Wannenburg. “The cost involved in the cleaning of these illegal dumping sites is excessive and could honestly be better utilised in delivering other desperately needed services.”
The City of Tshwane launched a campaign in November 2020, which focused its resources on clearing more than 600 illegal dumping sites across the municipality. The campaign garnered good results, with Executive Mayor Randall Williams even sharing that, although eradicating these illegal dumping sites was a mammoth task, the City of Tshwane was making great progress.
The campaign also included liaising with the Chief of Police, the Deputy Chief of Police responsible for Specialised Policing, and with the Tshwane Metro Police Department (TMPD) By-law Enforcement Unit regarding enforcement of waste management by-laws.
The following key actions have thus been instituted:
1. The Chief of Police issued a directive to instruct all uniformed TMPD officers in every region to proactively enforce the by-law and apprehend suspects when they see them.
2. The TMPD will provide weekly statistics on the number of illegal dumping cases reported, the number of incidents they
responded to, and the number of incidents proactively identified and addressed.
3. The TMPD will also inform the Waste Management Division in the Department of Environmental and Agricultural Management of reported illegal dumping incidents for these to be cleared.
Any person found guilty of illegal dumping is now liable to a maximum period of imprisonment of three years or a R60 000 fine, or both, as determined by a court.
The metro could further recover remedial and administrative costs as applicable, as well as the costs of cleaning up the illegally disposed waste from the offender.
“Transgressors know very well that what they are doing is illegal, but it just seems that they have no regard for the law. You can clearly see the sign that says no dumping, and yet they dump right under it,” says Wannenburg.
Wannenburg adds that the City of Tshwane had also started with educational projects to help people understand the financial, health and environmental impacts of these sites.
“A lot of the dumping is caused by backyard dwellers or households that have a lot of members living there, where one dustbin is not enough because it gets filled up quickly and they have to remove it from their yards,” he says.
catch the culprits, but it now needs the public to help combat illegal dumping by reporting these perpetrators.
“These criminal activities negatively impact the lives of community members. These sites serve as a breeding ground for all kinds of things that can cause life-threatening diseases. We are at a point where we need these communities to help us help them. By first reporting, and also to let us know how we can solve this illegal dumping problem, because we have tried different things and it seems that it’s not working. So, it’s really up to them now.”
How the public can address the issue of littering and illegal dumping:
• Talk to the person directly.
• Report those orchestrating dumping activities to the authorities.
the addresses of alleged perpetrators.
• Educate and be a good example to the children in your communities.
An alternative solution
Wannenburg says the metro is also investigating new ways to solve the dumping problem, where larger skip containers will be placed near the illegal sites for the community to use.
“We will then be able to see if this will help to prevent community members from dumping on open land.”
He adds that it is important to note that in a number of instances where skips are placed on illegal dumping hotspots, people still do not use the skips – opting instead to dump on the ground around it. “We have also found that skips get vandalised and are sometimes
cut up completely to be sold for scrap metal – which inevitably increases the drain on our resources,” states Wannenburg.
The City of Tshwane also believes that residents have to realise that illegal dumping affects everyone – not just residents in the immediate vicinity of the dumping sites.
“So, while we’re out cleaning and clearing, we rely heavily on residents to put an end to this practice. It is up to all of us to safeguard our environment for our children and the generations to follow. We are thus pleading with residents to assist the municipality by guarding against any illegal dumping practices in communities and to make sure that, once we have cleaned the area, they help us to keep it clean.”
The impact of Covid-19 on South Africa’s ailing economy has resulted in a huge loss of jobs.
Gauteng, in particular the City of Johannesburg – the country’s centre of economic activity – has been adversely affected.
The recent Statistics South Africa unemployment rate results bear this point out. The latest unemployment rate figures revealed an increase of 32.5%, with 7.2 million jobless people; however, despite the scientific confirmation of such a fact, one needs to drive around the city to witness first-hand the negative impact of unemployment.
The number of people begging or advertising their skills to potential employers is rising unabated. The long winding queues for unemployment insurance and social grants bear testimony to the scale of unemployment facing the country. Although an atmosphere of despair is pervasive as a result of joblessness and the outbreak of Covid-19, strides are being made to address the employment challenge.
The City of Johannesburg’s waste management company, Pikitup, has introduced its co-production model to contribute to efforts aimed at reducing the current 32.5% unemployment rate.
Cllr Mpho Moerane, MMC: Environment and Infrastructure Services, City of Johannesburg, launched the new co-production model at the company’s Southdale depot on 3 February 2021.
The co-production model entails that Pikitup should deliver on its waste management and minimisation mandate in conjunction with local communities or residents. This approach gives credence to Pikitup’s long-held view that it cannot achieve the highest standards of cleanliness possible without the participation and involvement of local communities.
In terms of the model, each ward in the city will be capacitated with 15 Expanded Public Works Programme (EPWP) employees, who will assist with waste management activities.
The model’s approach entails the appointment of cooperatives, non-profit companies and exempted micro-enterprises to ensure improved waste management services in the City of Johannesburg. A total of 48 such companies will in turn appoint the above-mentioned number of employees on a rotational basis. They are meant to assist Pikitup with litter picking, street cleaning and rendering education and awareness programmes to residents about the value of a clean environment and the value of recycling, as well as the identification, clearing and/or reporting of illegal dumping when it occurs.
Moerane said the work of the appointed cooperatives, non-governmental organisations and micro-enterprises was critical in ensuring that Joburg rids itself of the tag of being a dirty city. He also stated that the EPWP workers who would be employed would also be responsible for recording and reporting incidences such as potholes, dysfunctional traffic lights, leaking pipes, and the monitoring and managing of illegal dumping spots.
The co-production model has created about 2 025 jobs in all the regions of the city.
During the launch, Moerane emphasised the importance of taking ownership of the city’s cleanliness by all who reside in it. “It is easy to blame the government for everything each time our city is littered with trash; however, as we launch this programme to help enhance the cleanliness in our streets, it is important for us to note that the responsibility to keep our city clean remains with all of us,” he said.
The city is fast running out of landfill airspace and Pikitup’s four landfill sites collectively have less than five years’ worth of landfill airspace remaining. The dire need for communities to adopt responsible waste management through
recycling is an imperative to reduce waste that ends up at landfill sites.
The education and awareness creation aspect of the jobs that the appointed employees are charged with is anticipated to contribute immensely to the preservation of the remaining landfill airspace.
Currently, recycling efforts are gaining traction in high-income areas of the city and Pikitup has a target of diverting the following waste streams away from the landfill sites: 50% of green waste during FY 2020/21, 85% of builders’ rubble by 2021, and 85% of dry waste. This effectively means that 1 720 984 t of such waste must be diverted away from landfill.
It is against this backdrop that these education and awareness campaigns seek to raise awareness and encourage local residents not to include such waste in their bins but dispose of it in Pikitup’s waste disposal facilities situated in all the seven regions of the city.
The additional resources will also ensure that the street cleaning activities of Pikitup will be improved to assist ensuring that 9 000 km of streets will be kept clean. However, it must also be emphasised that such a reality is only possible if residents refrain from dumping waste illegally, as well as littering.
During 2018, the Western Cape Department of Environmental Affairs and Development Planning took a policy decision to introduce a 100% ban on organic waste to landfill by 2027, with a 50% target by 2022. While this has had a huge impact on many businesses, some have taken it as a welcome push towards achieving their zero waste goals.
Organic waste, which forms approximately 37% of the waste stream in the Western Cape, is a resource that has inherent economic value, if it’s separated properly and used either for compost, nutrient extraction or as an energy source.
Zero Waste Technologies has partnered with Elgin Fruit Juices on a biogas plant that will accept the disposal of organic waste.
Diverting this waste from landfill will not only save landfill airspace but will help to reduce the amount of greenhouse gas emissions.
Zero Waste Technologies, a subsidiary of GCX, and Elgin Fruit Juices have thus partnered on a biogas plant that will accept the disposal of organic waste.
The partnership
According to Hein Fourie, operations director of Zero Waste Technologies, the Elgin Biodigestion Plant was built in 2013 with the sole purpose of
processing the fruit waste from Elgin Fruit Juices’ normal factory operation and producing biogas, which is rich in methane. The biogas is then used to generate electricity for use on the plant.
“The plant, however, had a number of problems within its first year, which prohibited it from producing gas at a sustainable scale,” says Fourie.
In 2017, Elgin Fruit Juices was strongly considering closing the plant. This is when Zero Waste Technologies was brought in to assist
with ironing out some of the technicalities required for the digester to start producing gas.
The initial focus was on providing a consulting service on how to run/ operate the biogas facility. Fourie asserts that once they started seeing a disconnect, the decision was made for Zero Waste Technologies and Elgin Fruit Juices to form a collaboration.
This new agreement meant that Zero Waste Technologies would take over managing the operation of the anaerobic digester. This is a 50/50 partnership where both companies are equal partners. Elgin Fruit Juices provides the assets, while Zero Waste Technologies provides operational services.
Zero Waste Technologies specialises in providing advisory services to clients on how to go ‘zero waste’. The company is focused on alternative waste project development such as waste-to-energy (W2E) and other viable and sustainable interventions. It also currently operates biogas facilities and is building a solid pipeline of W2E facilities across the country.
When organic matter, such as food scraps, is broken down in an anaerobic environment, it releases a blend of gases – primarily methane
and carbon dioxide. This creates biogas that can be converted to electricity and heat.
The plant, located at the Elgin Fruit Juices factory in Grabouw, Western Cape, uses an anaerobic digester to convert approximately 60 tonnes/day of organic waste into methane-rich biogas.
The biogas is then used to generate steam in a biogas boiler, which is used by Elgin Fruit Juices to produce its products.
The Elgin Biodigestion Plant creates a digestate that is high in nutrient value. There are ongoing investigations into how to beneficiate this valuable digestate through setting up a composting facility as well as a semi-commercial farm, which could create sustainable employment for the local community.
The goods from the farm will then be sold back to the very food retail stores that generate the organic waste in the first place.
“This would mean that carbon-negative energy is created – a circular economic system – and an
impoverished community is being empowered,” Fourie adds.
The plant is currently operating at 50% capacity, with it rapidly ramping up to 80-100% in the next few months.
Fourie explains that Zero Waste Technologies and Wasteplan have designed a truck that will be responsible for the collection and transportation of organic waste from designated sites in the Western Cape to the facilities. Previously, no service existed that solely collected organic waste, seeing as a full wheelie bin is heavy and difficult to transport on a bakkie.
“In response to this, we designed a truck specifically to collect organic waste and deliver it to the Elgin Biodigestion Plant. The truck can lift the organic waste wheelie bins. We wanted a vehicle that is robust yet small enough to ride down the narrow streets of Cape Town but also
big enough to transport substantial amounts of organic waste. This truck should begin operating in August this year,” says Fourie.
The truck is expected to be arriving within the next two months; delays were caused due to Covid-19. The truck will service shopping centres, restaurant and university hostels.
The beneficiation of waste has significant financial incentives for companies. In the case of Elgin Fruit Juices, the correct operation of its biodigester will decrease the cost of production through a reduced reliance on coal for steam production, as well as remove the cost of waste disposal.
Other business benefits include:
• coal cost savings: R2.2 million per annum
• carbon footprint reduction: approximately 2 600 tonnes CO2e through coal fuel replacement only
• landfill waste reduction: 18 250 tonnes per annum
• carbon footprint reduction: 36 540 tonnes CO2e per annum through landfill diversion
• savings in waste disposal: between R150-600/ tonne depending on type of waste.
Making a success of the biogas projects will further play an important role in the industry, which has not yet reached its potential in South Africa generally due to poor management.
More than 60 000 waste reclaimers in South Africa earn a living by collecting packaging waste, with many being unable to find work or formal employment. Much of what reclaimers collect is sold through small buyback centres before ultimately reaching large recyclers.
“Waste reclaimers who collect waste packaging perform one of the toughest, yet most important, jobs in the circular economy and, up until now, they have remained mostly invisible and unbanked,” says David Drew, director: Sustainability at Coca-Cola Africa.
The development of the innovative, blockchainbased BanQu solution will provide a platform to “financially empower waste reclaimers and small buyback centres across South Africa”.
BanQu is a blockchain-based software platform and economic identity technology that enables a secure and immutable platform for creating economic opportunities for people around the world living in extreme poverty. The first of its kind, BanQu is being used in 40+ countries across more than a million last-mile-first-mile beneficiaries today.
Major brands like AB InBev use BanQu in their sourcing and circularity value chains in Africa and Latin America. In February 2020, BanQu launched is first African office in Johannesburg.
It has also become the leading platform for ensuring Covid-19 supplies are reaching the most vulnerable nations and communities in the Middle East and North Africa region.
BanQu creates a permanent, personal record of the transactions for each waste picker, enabling them to demonstrate their earnings in order to access credit. It also enables cashless transactions that reduce the risk associated with cash for both reclaimers and buyback centres, and enables direct financial support for waste reclaimers.
By recording the contribution of the informal sector as a whole to the recycling value chain, the platform is set to improve both understanding and recognition of the important contribution of waste reclaimers and buyback centres.
Coca-Cola selected BanQu as a partner based on the impact they have achieved to date and their track record of working with small-scale farmers across Africa.
Since the launch in mid-February, the system has already registered over 300 waste pickers and recorded over 4 900 transactions, totalling over 200 000 kg of recyclables.
Ashish Gadnis, CEO, BanQu, says the platform helps both individual waste reclaimers as well as small buyback centres.
“BanQu’s automated online supply chain tracking and payment system uses blockchain technology to track and trace recycled
Coca-Cola in South Africa and BanQu are rolling out an innovative payment platform to financially empower informal waste reclaimers and buyback centres in an exciting boost to the local recycling sector.
material across the value chain, providing price transparency for both buyers and sellers. Reclaimers don’t require expensive smartphones – the system sends a simple SMS when a payment is processed.”
The payments solution is also fully integrated with mobile money applications, enabling reclaimers to withdraw cash from ATMs or store their earnings in secure e-wallets.
Most importantly, the new technology enables waste reclaimers to develop a financial record and promotes their financial inclusion into the economy. Waste reclaimers can build a financial history – an economic passport that validates their existence in a global supply chain. The platform enables a traceable, transparent and, most importantly, equitable value chain that empowers waste reclaimers as well as buyback centres.
For small buyback centres, many of them operating in township areas, BanQu enables owners to better understand their businesses
using automated recording and tracking of transactions. Geolocation capabilities provide valuable data in real time about types of materials collected in particular areas.
For brand owners such as Coca-Cola, the platform provides a useful tool, as the company supports and empowers waste reclaimers and meets its World Without Waste targets to collect
and recycle a bottle or can for each one it sells by 2030.
“From a sustainability perspective, this is a very exciting and innovative technology that not only benefits those working in the recycling value chain but is a step change in our collective understanding and our ability to support this critical part of the circular economy,” says Drew.
The roll-out builds on BanQu’s successes in other African countries and in Latin America.
“BanQu is deeply rooted in a simple fact that millions of the poorest work tirelessly in our landfills, recycling centres and our streets, and they deserve a better future. We are thrilled with this partnership and look forward to scaling it,” concludes Gadnis.
• Waste Collection Optimisation
• Waste Transfer Station design
• General Waste Landfill design
• Hazardous Waste Landfill design
• Landfill Rehabilitation
• Landfill Auditing and Monitoring
Contact Numbers
Telephone:+27 (0)21 982 6570
Fax:+27 (0)21 981 0868
• Landfill Closure
• Leachate Treatment
• Regional Waste Studies
• PPP Involvement in Waste Management
• Alternative Technologies for Waste Reduction
• Integrated Waste Management Plans
Physical Address
60 Bracken Street, Protea Heights South Africa, 7560
Postal Address
P.O. Box 931, Brackenfell South Africa, 7561
The countdown to extended producer responsibility (EPR) scheme implementation commenced in May 2021 following the gazetting of Section 18 of the Waste Act in November last year. ReSource speaks to Anton Hanekom and Shabeer Jhetam* about the implications and opportunities for their sectors.
Long before the latest round of EPR developments, various voluntary producer responsibility organisations (PROs) were already successfully spearheading change in the recycling sector. Within the plastic packaging segments, prime examples include PETCO for PET, Polyco for polyolefins (PP, HDPE, LDPE/LLDPE and multilayer), the Polystyrene Association for polystyrene, and the Southern African Vinyls Association for PVC. The Paper and Packaging EPR schemes also include the metals, paper and glass PROs.
“Overall, these PROs have done an exceptional job, achieving a collection rate of around 58% for all paper and packaging. The collection rate for plastics alone is around 45.7%. These are commendable results that compare with some of the better performing countries in the world,” says Jhetam.
“The new Section 18 regulations contained within the National Environmental Management: Waste Act (No. 59 of 2008) are a welcome step towards a more collaborative approach between government and industry,” he continues. In
terms of Section 18, any company or brand that makes or imports any form of packaging will be required to pay an EPR fee per tonne, which will be different for the various material streams. In addition, strict collection and recycling targets have been established, which need to be met by industry over the next five years, starting from January 2022.
The initial Section 28 regulations proposed and subsequently withdrawn by government were going to be applied as an EPR tax. However, it wasn’t clear whether all the taxes collected would be effectively channelled back into EPR activities. In Hungary, for example, where a mandatory EPR tax was imposed, the collection rate fell by around 10% during the first year. This supports the viewpoint that an industry-managed EPR scheme is far more proactive and effective.
To date, the plastics industry’s voluntary PROs have been able to use the revenues they generate to support the collection, sorting and buyback of recycled materials via informal waste
pickers, small and medium-sized collectors, and large-scale commercial recyclers. The regulation of an official EPR scheme simply formalises the process. It also ensures that‘free riders’ will be a thing of the past.
“As industry-affiliated bodies, we remain committed to working with the DFFE as this process unfolds. For those plastic producers who are not yet members of one of the four plastic industry PROs mentioned, or Fibre Circle for paper, The Glass Recycling Company for glass or MetPac-SA for metal packaging, we urge you to get in touch with the relevant organisation,” Jhetam advises.
“As in the past, we believe that managing an EPR scheme through an industry PRO works best. In terms of the regulations, however, individual producers can establish their own independent EPR scheme, so a PRO is not a requirement,” Hanekom explains.
For EPRs to work effectively, though, everyone across the value chain needs to get involved – from the raw material supplier to the end user. That requires a major mindset shift, making consumer education a very important component of successful EPR implementation. Plastics|SA’s drive to create waste ambassadors supports this, as do competitions like the annual Caroline Reid Award, which recognises eco-champions.
Adequate collection infrastructure also needs to be in place. Currently, for example, around 34% of South Africa’s population is not serviced by formal waste management services. Where domestic waste is sent to landfill, there is also no mandatory requirement at present for separation at source.
“Enforcing this is a key factor in increasing volumes and establishing a permanent shift from dumping to recycling,” says Hanekom. “We also need to make it easier for consumers to recycle. Among the more high-tech examples are the reverse vending machines you see at some shopping centres that pay out instant cash for various packaging waste deposits. We also need more buyback centres nationally.”
The industry waste management plan submitted in 2018 included a proposal for a municipal infrastructure fund, and the setting up of SMMEs, among other initiatives. “Hopefully a lot of this will be carried over into the EPR in terms of supporting community projects that can move
informal waste pickers higher up in the waste value chain,” Hanekom continues.
The implementation of the EPR schemes will influence how packaging is designed in future. Here, Packaging SA already has a design guideline for recycling.
“Some products are more easily collected and recycled. Others need more end-of-life research and development (R&D),” says Jhetam. “These factors will almost certainly influence how the future EPR fee scale is developed.”
Reaching a point where packaging is 100% recyclable will hinge on joint initiatives between brand owners and manufacturers. At the end of the day, the packaging needs to be fit for purpose. In some cases, that may result in an R&D breakthrough that extends the product’s
packaging life before it eventually needs to be recycled. A case in point is the development of returnable plastic soft drink bottles that can be refilled and resold up to seven times.
“The proven track record achieved by our voluntary PROs makes us confident that this is the preferred route for EPR implementation. We’ve helped grow members from disadvantaged communities into vibrant business owners. Now the formalisation of the EPR will enable us to grow and sustain these initiatives on a far broader and greater scale,” Jhetam concludes.
• Existing producers to register with the Department of Environment, Forestry and Fisheries from 5 May and no later than 4 November 2021
• Join or form an EPR scheme that includes the entire value chain
• Be accountable for the operation and performance of an EPR scheme
• Pay the appropriate fees to the EPR scheme
• Fulfil monitoring and reporting obligations, commencing January 2022
South Africa’s amended Plastic Bag Regulations, coupled with the new Extended Producer Responsibility (EPR) Regulations, are raising concerns about double taxation in the plastic bag sector.
By Garyn Rapson, Paula-Ann Novotny & Emma Bleeker*
Historically, retailers provided plastic carrier bags to consumers for free and incorporated the cost into the price of goods; however, studies conducted by the former Department of Environmental Affairs and Tourism in 2002 shed light on a serious plastic waste problem, noting that, unlike other waste types, plastic had no organisation dedicated to its disposal and recycling.
In 2003, under the ambit of the Environment Conservation Act (No. 73 of 1989), the Plastic Carrier Bags and Plastic Flat Bags Regulations (‘Plastic Bag Regulations’) were published. These were followed by the introduction of a plastic bag levy in 2004 under the Customs and Excise Act (No. 91 of 1964).
It was an indirect tax on the movement, manufacture or consumption of goods and services, which in this case retailers (specifically, supermarkets) charge on every sale of a plastic bag.
The Plastic Bag Regulations prohibit the manufacture, trade and commercial distribution of domestically produced and imported plastic carrier bags and plastic flat bags unless the bags comply with the ‘Compulsory Specifications’ (such as a minimum thickness of 24 microns), subject to certain exclusions.
These design specifications were intended to make plastic bags more environmentally friendly and reusable. It became an offence
for manufacturers, traders, and commercial distributors to contravene the Plastic Bag Regulations, and these regulations remain in force today.
In 2019, the Department of Forestry, Fisheries and the Environment initiated a review of the Plastic Bag Regulations to see how they could be improved. On 7 April 2021, Minister Barbara Creecy published the amended Plastic Bags Regulations, which included the introduction of a definition of ‘post-consumer recyclate’.
This was defined as: “material generated by households or commercial, industrial or institutional facilities, in their role as end-users of the product, which can no longer be used for its intended purpose, and includes returns of material from the distribution chain, as well as inhouse scrap that already contains postconsumer recyclate content”.
The amended regulations set goals for the minimum percentages of post-consumer recyclate that plastic bags should contain at certain intervals until they achieve a 100% post-consumer recyclate content by 1 January 2027.
The amended regulations include:
• a minimum of 50% post-consumer recyclate from 1 January 2023
• 75% of recycled materials from the start of 2025
• 100% post-consumer recyclate from 1 January 2027.
The Plastic Bag Regulations are considered upstream regulations, as they regulate the production and composition of products. Downstream regulations regulate the waste implications associated with products after their consumption, or what is referred to as their ‘post-consumer phase’.
South Africa recently published its own set of downstream regulations, known as the EPR Regulations, under the ambit of the National Environmental Management: Waste Act (No. 59 of 2008), which aim to promote a circular economy.
Arguably, the new downstream regulations also capture the plastic bag sector. The new EPR Regulations are aimed at drastically reducing the amount of waste that enters landfill sites. Essentially, they require producers, manufacturers, importers and brand owners to include an increasing amount of recycled material in their products.
The EPR Regulations apply only to products and their related waste streams identified by the Minister in the Government Gazette They envisage that all producers of identified products and their related waste streams will establish and implement an EPR scheme or join an EPR scheme established by a producer responsibility organisation (PRO) on behalf of its producers.
The EPR scheme for the paper and packaging sector and some single-use products applies to identified products that include an array of paper and paper packaging material, plastic packaging, biodegradable and compostable packaging, single-use plastic products (including if compostable or biodegradable), glass packaging, and metal packaging. In terms of this scheme, packaging is defined as any material, container, wrapping or corrugated cases used for the containment, transport, handling, protection, promotion, marketing or sale of any product or substance. It may be primary packaging containing the actual product, or secondary or tertiary packaging, typically containing products already packaged in primary packaging.
It can be argued that plastic bags fall within the ambit of this definition, as they are secondary or tertiary packaging used to contain, transport, handle or protect goods and can be branded for marketing purposes.
A producer, in terms of the proposed amendments to the EPR packaging scheme, is obliged to comply with the EPR Regulations if it places more than 10 tonnes of plastic bags into the market annually. Depending on whether the brand operates/is domiciled within South Africa, the liable producer could be the manufacturer, converter, brand owner, licensed agent, importer or retailer. The lack of clarity on who bears the responsibility as the ‘producer’ leaves much to be desired.
A notable consideration for producers is that an EPR fee is chargeable on identified items, which will fund the relevant EPR scheme. This fee must be indicated as a separate line item on every invoice and cash sale receipt for each purchase (or be publicly available on the PRO’s website in terms of the proposed amendments).
This raises the question of whether this EPR fee will be charged on plastic bags in addition to the existing plastic bag levy of R0.25.
Other obligations for producers in terms of the EPR Regulations include having to submit information about the ‘life cycle’ of their products, reduce the consumption of natural resources,
and show that products are designed to be more environmentally friendly. Under the EPR Regulations, offenders found guilty of noncompliance can be imprisoned for up to 15 years or fined, or both.
Producers of plastic bags now face potential additional obligations under the EPR Regulations, which could see a double ‘taxation’ on plastic bags.
The advantages of both the Plastic Bag Regulations and the EPR Regulations applying to plastic carrier and plastic flat bags are that they are the only waste type to be regulated both up- and downstream.
However, some plastic bags that do not fall within the scope of the Plastic Bag Regulations do fall within the ambit of the EPR Regulations, such as garbage bags. The implications of applying both sets of regulations to the producers of plastic bags are yet to be seen.
*Garyn Rapson, Paula-Ann Novotny and Emma Bleeker are environmental law experts at Webber Wentzel.
In a world where society and business are challenged with environmental, economic and health impacts, the focus to preserve what we have and reduce waste, coupled with climate change, is taking centre stage.
By Nick Mannie
While all these challenges are evolving in various forms daily, business leaders are being forced to re-assess their business strategy while considering sustainable business practice. This calls for deep introspection of the entire supply chain and product value chain. It may sound daunting and mind-boggling at first; however, the assessment is key to unlocking value in the business where you would least likely have found it.
This means it is time to rethink and reconfigure processes and practices in the business. As a business, you want to maximise the product value, reduce waste – or even possibly iron out waste generation – use fewer resources to produce the product, and seek alternative materials in the production process. This requires going back to the drawing board and engagements with team members to get to a sustainable solution.
The starting block is with business leadership and the team to map out the attributes needed to work towards creating a new normal and introducing the circular economy. The ‘sticky notes’ on the chart to the right show some attributes that you need to consider, discuss and incorporate into the planning of a circular economy approach. While some may
seem to be common terms, there is a lot to unpack around each term to understand your business approach towards circular economy implementation.
In unpacking this map, it is also crucial to understand the barriers to achieving success in the circular economy. These include but are not limited to:
• resistance to change
• lack of skills to undertake and implement the process
• institutional capacity
• funding and access to finance
• no collaboration or cooperation among peers in the sectors
• no investment into innovation and research
• lack of credible data to make good business decisions.
These barriers will vary depending on the stage in which your business is and how ready the business and its teams are to transition to the circular economy.
In a developing country like South Africa, urbanisation is on the increase and the pressure to develop is unfolding at an immense
rate, which means there is a greater impact on resources and infrastructure requirements. Investment into policy change and programmes that promote a circular approach will be required if we want to limit waste, pollution, climate impacts and resource constraints. Habits and mindsets will require education and awareness to heighten the awareness of why the shift to a circular economy approach is needed now and not later.
Which material is having the biggest impact to the environment?
South Africa is already experiencing the adverse effects of climate change and faces multiple challenges in relation to this phenomenon over the next decade.
By Eckart Zollner*
Since 1990, South Africa’s average temperature has risen at a rate of more than double that of global increases, already resulting in more frequent droughts and extreme weather events. Alarmingly, the country has seen a sevenfold increase in its fossil-fuel CO2 emission levels since 1950, with 80-90% of these emissions resulting from the burning of fossil fuels. When expressed as gross emissions per individual, each South African was responsible for emitting 9.8 tonnes of CO2e (carbon dioxide equivalent) in 2015.
Our reliance on coal contributed an average of 91.8% of total carbon dioxide emissions between 2000 and 2015, with other significant emitters being transport, livestock and manufacturing waste.
GHGs (greenhouse gases, which include water vapour, carbon dioxide, methane, nitrous oxide and ozone) can absorb and emit radiation at a certain level, causing the greenhouse effect, which leads to the warming of the earth’s surface. This has a major adverse impact on the environment, causing climate change that results in weather extremities like storms, flooding and droughts – all of which impact farming productivity and food security.
With the world’s 13th largest emitting country for fossil-fuel emissions and a domestic economy powered by coal, South Africa’s private sector needs to step up and take responsibility for its contribution.
This involves complying with the Carbon Tax Act (No. 15 of 2019), gradually reducing emissions-producing activities and phasing in cleaner technology. With 15 coal-powered power plants across the country, it’s likely to be an extensive process to reduce dependence
on coal, which only emphasises the need for private sector organisations to take charge in powering South Africa’s greener future.
Effective as of 1 June 2019, the Carbon Tax Act, together with the Customs and Excise Amendment Act (No. 13 of 2019), are intended to reduce GHG emissions in a manner that is sustainable yet compelling. In a further attempt to encourage businesses to reduce their carbon emissions, an initial levy of R120 per tonne of CO2e will be charged over the threshold of taxfree allowances.
The Act gives effect to the polluter-pays principle for large emitters and forces businesses to take these costs into account for future production, consumption and investment decisions, encouraging them to adopt cleaner technologies and production methods in the next decade.
Framed to roll out in three phases, the Carbon Tax Act will only be applicable to scope 1 emitters in the first phase. The first phase will run from 1 June 2019 to 31 December 2022, and the second phase from 2023 to 2030. In relation to a business’s operations, sources of GHGs are classified according to the level of phases over making less emissions-intensive operational choices.
In the first phase, direct emissions from the stationary combustion of fossil fuels (such as diesel generators) are taxable, while the second phase will address scope 2 emissions, which are gases that escape through venting or from landfills; the third phase will address indirect emissions.
However, the outbreak of the global Covid-19 pandemic last year and subsequent lockdown saw the first filing of carbon tax returns for
the 2019 reporting period deferred by three months, to 31 October 2020, as part of the Covid-19 relief mechanisms for taxpayers. Currently, the country’s heavy GHG emitters are scrambling to register for carbon-offset projects as the deadline looms for the payment of carbon tax in June this year.
The pandemic did not permit carbon tax to be a primary focus for businesses throughout last year, and it is expected that this year’s filing of carbon tax returns will likely feel like a hurdle to most businesses, as the economic climate remains tough and cash flows are constrained.
This has raised concerns within the industry that the Carbon Tax Act – much like the Protection of Personal Information (PoPI) Act (No. 4 of 2013) – lacks teeth to achieve its purported objectives. The PoPI Act has faced questions about its ability to fully protect individuals’ data privacy due to the evolving nature of technology, the continuous quantity of data created, advanced cyber fraud, and the non-adherence by responsible parties to the ethical use of personal information. The PoPI Act has faced criticism that, on its own, it lacks the legislative impact required to regulate technology companies in a time of unprecedented data collection and processing.
Similarly, it is questionable whether the Carbon Tax Act will be effectively adhered to by industry, especially given that the entry threshold for liability is currently set so high that it essentially targets extremely large polluters and for the moment excludes ‘medium-sized’
polluters. Furthermore, it has been argued that developing projects that comply with carbon credit regulations is a complex, timeconsuming process.
However, organisations – regardless of size –need to start gearing towards adherence, as non-compliance with carbon tax laws will have detrimental effects on the environment and organisations’ bottom line.
The initial phase of the Act offers significant opportunity for relief in the form of tax-free emissions allowances ranging from 60% to 95%, including a basic tax-free allowance of 60% for all activities, plus a 10% process and fugitive emissions allowance. There is also a maximum 10% allowance for companies that
use carbon offsets to reduce tax liability, as well as a performance allowance of up to 5% for companies that reduce the emissions intensity of activities.
Furthermore, a 5% carbon budget allowance is provided for reporting compliance and a maximum 10% allowance for trade exposed sectors. The legislature takes into consideration the need to balance aggressive measures to address climate change. This is coupled with the need to soften the financial impact on sectors such as manufacturing and heavy industry.
To take advantage of these discounts and allowances, and adequately calculate tax liability, businesses in the manufacturing sector will need to assess their emissions and get a clear picture of their carbon footprint.
Fortunately, this is not something organisations need to figure out on their own, as there are numerous carbon tax analysis tools available on the market. If businesses haven’t already done so, it is advisable to look for home-grown solutions that are designed specifically for local conditions to make tax compliance easy. Process or emissions data simply needs to be fed into the carbon analytics tool to generate an automated report that details emissions by source. The tool can also calculate an exact tax liability amount and provide a solid foundation for carbon reduction in manufacturing in a way that minimises the impact on the bottom line.
Using bioremediation to treat ground impacted by chlorinated hydrocarbons (CHCs) essentially requires building a bioreactor below the ground; therefore, direct observation of results is not possible. Rather, the process must be scientifically monitored through specialised tests to serve as the integral lines of evidence needed to assess the health and performance of the biobarrier. By
Michelle Roux and Sathisha Barath
The monitoring of this biobarrier, which is a living system, is done using specific in situ and laboratory tests. These tests will give insight into the key prevailing conditions that are required to maintain the biobarrier’s health and achieve the expected results in terms of CHC degradation. The characterisation of the affected ground will determine which geochemical conditions are most relevant to be included in the ongoing project assessment.
situ monitoring of redox and pH
For instance, certain microbes responsible for the degradation of the dense non-aqueous phase liquids (DNAPLs) will only thrive in an anaerobic environment – in which case a vital aspect of monitoring will be focused on checking for oxidation-reduction (redox) conditions.
Acidity in the groundwater must also be carefully checked, as the microbes require a pH level in a range from five to seven. As they break down CHCs, the microbes generate volatile fatty acids that reduce the pH level of the groundwater and could undermine their effectiveness. Where pH levels are found to be
too low, a ‘buffer’ can be added to raise them to within the optimal range.
It is also necessary to check other geochemical parameters such as the levels of nitrates and sulfates. This helps to identify and understand the complex geochemical dynamics in the aquifer and possible presence of other microbes in the aquifer that could influence remediation reactions; these other microbes can compete for the injected food source. Information on these factors enables the practitioner to adjust the food supply to ensure that the dehalorespirators are still well supplied.
Regularly sampling and measuring the total organic carbon (TOC) in the aquifer is crucial, as this is an indicator of the substrate (food) on which microbes survive and thrive. The TOC levels should be measured both spatially and temporally to determine whether more substrate needs to be injected and where. Aquifers – and even zones within a single aquifer – will differ in terms of their hydraulic properties and flow velocities.
During the characterisation phase, prior
to full-scale implementation, specific measurements should be undertaken to provide insights into the aquifer dynamics that will later influence substrate migration. The focus needs to be on the zone being treated and on ensuring that the substrate is finding its way to the targeted area and is being retained in the treatment zone for long enough that the microbes can utilise it efficiently.
This highlights the importance of making allowance in the project conceptualisation and characterisation phase for identifying preferential groundwater flow paths in the aquifer, which leads to flow heterogeneity within the system. These flow paths could take the injected substrate in unintended directions and deprive the microbes of an adequate food source.
Groundwater samples also need to be analysed to measure the concentration changes of CHCs within and downgradient of the biobarrier over time. Samples are collected every few months from carefully located monitoring holes. Indeed, the frequency and timing of the sampling regime can be viewed as a science in itself. Similarly, the sampling methodology is
Bioremediation of chlorinated hydrocarbons using emulsified vegetable oil substrate: Practical approaches – a four-part series
South Africa is seeing valuable innovations in the use of bioremediation to treat industrial sites impacted by chlorinated hydrocarbons. This groundbreaking work is particularly urgent as the country makes more use of groundwater resources – a receptor that is vulnerable to contamination from surface sources of pollution. In this four-part series, SRK Consulting discusses the current advances it is making locally and how these will benefit efforts to clean up legacy impacts in the subsurface environment. In this, the fourth article in the series, the authors examine how the success of an enhanced in situ bioremediation (EISB) system is best monitored and evaluated.
In the ground covered to date, the first article provided an overview of why EISB is an effective option for degrading chlorinated hydrocarbons. In the second article, the focus was on the use of emulsified vegetable oil as substrate for EISB, while the third article highlighted some lessons learnt in the practical implementation of this technology.
critical to the accurate measurement of aquifer conditions. The selection, layout and placement of the sampling pumps – whether at the bottom of the hole or across a fracture –become a terrain for experienced scientists and specialists. Incorrect choices could lead to drastically skewed results, providing a misleading picture of actual processes under way.
Monitoring results must show that the relevant end products are being formed from bioremediation’s metabolic pathway. This includes monitoring for methane, ethene and ethane – measured as a dissolved gas in water samples.
The sampling of groundwater in these projects, however, comes with special challenges. Bringing a sample to the surface would expose it to the atmosphere and thus potentially alter its pH and redox condition. Therefore, specialised in situ geochemical probes are used to sample the groundwater at depth to deliver an accurate reflection of the pH and redox conditions under which the microbes are living. Despite their cost, these probes
pH/redox probe used for in situ monitoring of geochemical parameters
are vital to effective monitoring, acting as the practitioner’s ‘eyes and ears’.
Highly specialised groundwater sampling and analysis are also required to ensure that the correct microbial species are present in sufficient quantities in the biobarrier. This calls for DNA testing – usually conducted by commercial laboratories abroad – with samples needing to comply with stringent requirements to avoid any kind of contamination. The Covid-19 pandemic has complicated this process even further, as samples must reach the laboratory within a certain timeframe. Logistical delays due to Covid19 lockdowns can lead to samples expiring in transit – and costly resampling of the aquifer.
Accurate data, it should be remembered, is the foundation of the complex endeavour that bioremediation represents. As a living entity, the biobarrier we create to degrade CHCs is constantly changing – demanding that practitioners make regular interventions to correct and maintain the specific conditions required. Without ongoing monitoring and technical input guiding appropriate and timely action, whole sections of the biobarrier can begin to die, potentially threatening the success of the project.
• Bioremediation has been used in the USA and Europe over the past 50 years or more for treating ground impacted by chlorinated hydrocarbons, and the technology holds great potential for South Africa.
• There is a growing level of scientific innovation and practical experience in this field locally, informed by a global knowledge base.
• Local project experience – alongside extensive laboratory and on-site testing – has allowed South African experts to develop fit-for-purpose solutions to deal with both chlorinated ethanes and chlorinated ethenes.
• Successful bioremediation depends on a thorough investigation and understanding of the chemistry and geological matrix of the source material.
Michelle is a principal hydrogeologist and contaminated land scientist in SRK Consulting’s Durban office, with more than 14 years of experience in hydrogeology, microbiology, contaminated land characterisation and management. Her specialisation includes project management, groundwater assessment and remediation, and bioremediation in situ treatment design. Her work includes conducting contaminated site assessments, developing and implementing long-term groundwater monitoring projects, and developing site conceptual models for DNAPL and LNAPL sites. Michelle holds an MSc Geohydrology, and a BSc (Hons) Microbiology.
As a senior hydrogeologist at SRK Consulting’s Durban office, Sathisha has more than 11 years of experience in land contamination, remediation and groundwater projects. Her specialisations include enhanced in situ bioremediation of chlorinated hydrocarbons, site characterisation of LNAPL and DNAPL sites, and soil and groundwater remediation of contaminated sites. She holds an MSc Hydrogeology and a BSc (Hons) Geology.
As
part of its commitment to achieve net zero carbon emissions across its supply chain, products and operations by 2039, Jaguar Land Rover’s venture capital
and mobility arm has invested in a lithium-ion battery recycling and materials company.
company, Battery Resourcers turns spent batteries and production scrap directly into new, battery-ready cathode active material with significant reductions in cost, emissions and energy consumption.
Founded in 2015, the company makes EV-grade, finished cathode active materials that perform as well as industry-leading brands.
Battery Resourcers, a sustainable technology firm, holds the exclusive licence for an innovative closed-loop process that integrates battery recycling, refining and materials engineering to convert scrap end-of-life batteries into new materials that can be used to make new batteries.
The investment in Battery Resourcers plays part of the plan for Jaguar Land Rover to establish sustainable solutions for end-of-life batteries, minimising waste and creating a circular economy across the battery supply chain.
Based in Massachusetts, USA, Battery Resourcers operates the world’s most efficient lithium-ion battery recycling process. A vertically integrated recycling, refining and materials engineering
The innovative technology will recycle and produce cathode active materials such as nickel manganese cobalt oxide (NMC), nickel cobalt aluminium (NCA) and lithium iron phosphate (LFP) batteries. The business has also filed intellectual property around graphite recovery and purification, which will enable it to return both the cathode and anode active materials back to manufacturers of new batteries.
The investment from InMotion Ventures and other strategic partners will fund the development of a commercial-scale processing facility, with the capability to process 10 000 t of batteries annually, along with the expansion and enhancement of the production and analysis facilities in Michigan, USA.
The announcement comes as Jaguar Land Rover defines its future strategy: a sustainability-rich reimagination of modern luxury, unique customer
experiences and positive societal impact – with the aim of achieving net zero carbon emissions across its supply chain, products and operations by 2039.
This investment showcases the company’s vision to establish new benchmark standards in efficient scale and quality by accelerating investments in circular economy supply chains.
Sebastian Peck, managing director of InMotion Ventures, says the company is very excited about the company’s investment in Battery Resourcers.
“Battery Resourcers is part of the plan for the business to meet its obligation for end-of-life batteries, minimising energy use and waste, achieving full circularity for its recycled battery materials, and securing future sustainable supplies of rare materials. We look forward to working with the Battery Resourcers team.”
According to chief executive Mike O’Kronley, Battery Resourcers is on the verge of revolutionising the lithium-ion battery supply chain.
“Being able to convert scrap and end-of-life battery materials into new active material that can be directly used in making new batteries drives increased profitability and stability for the lithium-ion battery ecosystem. Our investment partners share our vision and passion to scale this revolutionary process to support the battery material supply chain,” O’Kronley concludes.
Landfill leachate contains high concentrations of harmful contaminants, especially salts and organic content that pose a threat to the environment when not contained. ReSource speaks to Rob Holmes, managing director: TTM at Tecroveer, and Hugo du Plessis, senior project engineer at KSB Pumps and Valves, about combined technology solutions.
The formation of leachate is a chemical process that occurs in landfills as organic and inorganic materials leach out of the landfill space. Since it’s a highly toxic by-product, management and containment are legislative requirements and an environmental imperative. The key issue is the salt composition in the leachate, which can build up in potentially harmful concentrations.
“The historical practice of containment, treatment and recycling the leachate back into a landfill just tends to increase the salt content over time, exacerbating the problem,” Holmes explains. “This is because mainstream reverse osmosis processes employed to purify the effluent don’t actually remove the salts, but just separate them into a concentrate stream.
“Even though the leachate has been purified to a fair degree, with significant volume reduction, the dissolved salts in the brine effluent have not been extracted, since this requires an additional process stage. So, when, in this case, brine is returned to the landfill, there’s a resulting escalation in toxicity over time,” he continues.
Tecroveer is a water and wastewater plant design and contracting company with more than 40 years of experience in the municipal and general industrial environment, working with KSB as one of its preferred technology partners.
In recent years, Tecroveer’s traditional focus has evolved with the adoption of advanced technologies for industrial applications, water reuse, waste-to-energy, and now landfill leachate treatment.
“When it comes to leachate treatment, there’s conventionally been one type of technology to treat organics, and another one to deal with the salts. Tackling both at the same time requires unique and advanced treatment processes,” says Holmes.
“To target the opportunities and environmental priorities, we’ve partnered with European technology company Salttech, which has developed a proprietary dynamic vapour recovery
huge benefits for South Africa,” adds Holmes. KSB product examples that would typically be employed for a DyVaR process setup are the WKLn, ETA and ETAnorm range of pumps, all of which are made at KSB’s Germiston, Gauteng, factory.
KSB’s pump and valve solutions
Current and recent Tecroveer projects where KSB has supplied OEM solutions include a major bulk water supply and irrigation scheme in eSwatini, plus various municipal wastewater treatment works (WWTW) upgrades for South African municipalities that are ongoing. KSB has also supplied key products for various local WWTW waste-to-energy projects designed and commissioned by Tecroveer. Clients here include an automotive manufacturer, plus FMCG clients. At one site, this entails the extraction of biogas to run a 500 kW turbine generator. Another site currently being commissioned will have the potential capacity to produce up to 3 MW.
(DyVaR) process that does both simultaneously and very effectively,” says Holmes.
As an added advantage, the DyVaR solution comes in a containerised format that takes up a small footprint. It’s also designed to ‘plug and play’ with the existing process network. Essentially, leachate can be treated in a single step, removing high-quality water from the landfill, with the dissolved salts and organics having been separated and removed as a crystallised solid. The latter can then be safely encapsulated.
“We’re currently in discussions with private and public sector landfill owners, consulting engineers and specialist contractors, and believe that DyVaR technology will deliver
Further waste-to-energy opportunities in the public sector are being investigated on an ongoing basis, since Tecroveer believes there’s huge potential in this area.
“KSB is an expert solutions partner in all areas of water, wastewater and allied power generation projects, with a well-established South African manufacturing and supply base,” says Du Plessis.
“Our research and development teams are constantly responding to new opportunities that meet customer demands for greater efficiencies. Our ‘plug and play’ single- or dualpump stations serve as a prime example,” Du Plessis explains. These are supplied as
KSB’s Amamix submersible mixer series is a popular choice for biogas projects, alongside mainstream wastewater applications that include leachate treatment
a ready-to-connect package system with a fibreglass collecting tank for buried installation. Process capabilities range from 500 litres to 5 m3
“As a water and wastewater design company, selecting the right components and materials for the medium you’re dealing with is crucial. That’s why we trust KSB to deliver the right suite of products,” Holmes concludes.
KSB’s CK 800 packaged single- or dual-pump station serves a broad range of applications. These include the disposal of wastewater in the private, commercial, industrial and municipal sectors
Amarex submersible motor pump designed for handling wastewater
The DyVaR process system is housed in a container for ease of shipment and setup on site. This ‘plug and play’ functionality enables the technology to sync with the existing wastewater treatment setup. An added plus is that DyVaR is highly energy efficient
Plastic waste is an enormous global problem, with only 9.5% of plastics being recycled yearly. The other 90.5% is either incinerated, or ends up in landfills and the ocean.
By Nombulelo Manyana
numbers, South Africa has a severe housing shortage, with the housing backlog reportedly sitting at 2.3 million houses, and growing by around 178 000 houses a year. South Africa’s official unemployment rate has also risen to a staggering 32.5% between October and December 2020, with 11.1 million people currently out of work.
Although these statistics may seem shocking, the Centre for Regenerative Design and Collaboration (CRDC) believes that they also present a unique opportunity. With the introduction of what they call a new innovative technology, the CRDC will not only help mitigate the growing waste problem but will also create jobs, boost informal waste collection and solve some of South Africa’s other major problems by building houses, hospitals, schools and roads.
RESIN8 – which is the CRDC’s groundbreaking, regenerative solution to South Africa’s unmanaged plastic waste – is a breakthrough concrete modifier made from mixed plastic waste. It can take any type of waste plastics and convert them into high-value concrete modifier that perfectly simulates construction sand.
Deon Robbertze, manager: Business Development and Communications at CRDC, says the RESIN8 technology represents a “crossindustry collaboration between CRDC, leading plastic, waste management, construction industries and NGOs.”
CRDC is a global company with its roots in Costa Rica. Founded by Donald Thomson in 2010 as a volunteer-based beach clean-up programme, it is presently recognised internationally for its contributions towards sustainable product design.
CRDC comprises a diverse, multidisciplinary group of experts in the packaging and food/beverage industries, conservationists and award-winning designers working to create products, industrial
processes and economic models that provide socio-economic and environmental benefits.
The company also operates in South Africa, with a pilot plant based in Cape Town.
Through its net-zero-focused business model, REAP (Recover – Enrich – Appreciate – Prosper), CRDC has created collaborative relationships between diverse industries, where the waste stream of one can become the value stream for the next.
RESIN8 is a process that can turn any plastic –dirty or clean and in any form – into concrete modifier. The end results are environmentally friendly products that incorporate regenerated waste plastics, which would otherwise be destined for landfills.
Through the REAP process, all types of postindustrial and consumer plastic waste are recovered using different avenues, as shown in the figure below.
Then, while coexisting with them, natural systems can be regenerated and enriched.
Resources can be kept in use and their value appreciated while also being preserved.
A tonne of mixed plastic waste can, through the RESIN8 process, produce around 4 000 concrete blocks, while 1 000 tonnes will equate to 4 000 000 concrete blocks.
RESIN8 has multiple applications, namely concrete blocks and pavers, precast concrete and poured-in-place concrete.
It is the only material made from plastic waste that maintains or improves the performance of concrete products. It is tried, tested, in operation, has low capex requirements and can be scaled to regional remediated plastic waste volumes.
RESIN8 supports 12 of the 17 United Nations’ Sustainable Development Goals and is the 2020 Winner of the DOW Impact Award.
In Costa Rica, 400 houses have already been built in partnership with Habitat for Humanity and Costa Rica’s leading concrete company, Pedregal. Here in South Africa, Martin&East will be building about 4 000 Breaking New Ground homes over the next four years for the Western Cape Provincial Government, with the project set to have started around the end of March 2021.
Those houses will have RESIN8 in the concrete blocks, making them stronger and increasing
the thermal characteristics of the concrete blocks by 25%.
“This means that you will need less heating and cooling in that house. With climate change, that is another added value of the product,” said Robbertze.
The porous composition and gradation of RESIN8 improves both the mechanical and chemical bond to cement. It has numerous key benefits, which include the following.
Within concrete and construction:
• increase in strength
• 8% to 16% decrease in weight (with 5% or 10% RESIN8)
• increase in thermal properties
• same fire resistance as with standard concrete
• reduce cement industries carbon footprint. Environmentally:
• supports and grows the UN Sustainable Development Goals
• reduces carbon footprints by eliminating plastic to landfill and plastic pollution
• all types of plastic can be regenerated into RESIN8 – no separation required
• supports zero waste to landfill, extended producer responsibility and government programmes or initiatives.
• SMME and job creation from waste plastic collection, plastic shredding and transport
• cleaner cities and healthier environments
• helps support the building of better housing with a product that benefits the environment and society.
In terms of the last step in the process, Robbertze says that beyond creating better housing and infrastructure for those that need it, the aim is to ensure that jobs are being created for people living in informal sectors.
“It is absolutely critical to create jobs and build better infrastructure in this country. And we take our inspiration from nature – it doesn’t waste.”
CRDC’s full-scale plant, which is expected to use up to 1 000 tonnes of plastic waste per month and convert it into RESIN8, will be up and running by the third quarter of 2021. The company also plans to have 21 plants across South Africa in the next five years.
“Now that we have a zero-waste solution to our unmanaged plastics problem, we have a massive responsibility to make it happen at scale,” says founder Donald Thomson.
Venue: Digital event
Date: 8 to 10 June 2021
Website: www.enlit-africa.com
Enlit Africa, in partnership with ESIAfrica , invites you to learn, connect and engage with industry leaders and the community across a three-day, not-to-be-missed digital event on 8 to 10 June 2021.
Enlit Africa-Connect is a digital meeting place where you can connect, engage and network with your industry peers in real time or talk to a supplier to discuss your energy future. Watch cutting-edge content through live webinars, exclusive one-on-one interviews with the who’s who of the energy sector, compelling content from host publication ESIAfrica , product launches, technology showcases and much more throughout the year.
Venue: Gallagher Convention Centre, Midrand, Gauteng
Date: 29 June to 1 July 2021
Website: www.africanconstructionexpo.com
With thousands of built environment professionals from over 45 countries visiting every year, the African Construction and Totally Concrete Expo provides the platform for distinctive opportunities for business expansion, networking and learning.
The annual African Construction and Totally Concrete Expo is Africa’s mega construction and infrastructure show, and the biggest gathering of roughly 8 500 qualified buyers and sellers for the entire built environment value chain.
In 2021, the event will once again feature an exciting exhibition and robust workshop programme.
Venue: Gallagher Convention Centre, Midrand, Gauteng
Date: 1 to 3 June 2021
Website: www.aosh.co.za
Commemorating the 10th edition of Africa’s premier health and safety trade show, A-OSH Expo takes place, as before, at Gallagher Convention Centre, Midrand.
If you are serious about health and safety in the workplace, a visit to Africa’s foremost occupational health and safety (OHS) trade show is a must to put into your calendar for June 2021!
The show will be running alongside two shows: the highly respected security and fire exhibition Securex South Africa, and Facilities Management Expo, which showcases products and services associated with property and building management and maintenance.
Venue: Gallagher Convention Centre, Midrand, Gauteng
Date: 2 to 4 November 2021
Website: ifat-africa.com
IFAT Africa is the ultimate platform to showcase technologies and solutions for water, sewage, refuse and recycling for the sub-Saharan African market. The trade fair, taking place from 2 to 4 November 2021 at Gallagher Convention Centre, will give exhibitors and trade visitors the opportunity to experience the latest environmental technology, topics, trends, challenges and solutions.
It will also connect key industry players with senior buyers and decisionmakers in the region.
87% of marketing professionals use video as a successful marketing tool.
3S Media provides the interface to host, manage and broadcast live as well as on-demand webinars.
Our pla�orm ensures the highest quality video and audio technology. This ensures flawless digital broadcas�ng by using enterprise-grade streaming solu�ons.
Book your webinar today and participate in robust thought-leadership panel discussions and anchor desk interviews with captains of industry.
Novus Print (Pty) Ltd t/a 3S Media is a proud Level 2 BBBEE Contributor.
Marketers making use of video get 66% more qualified leads per year.
Video engages users for longer on a website. The average user spends 88% more time on a website with video content.
3S Media offers robust thought-leadership panel discussions and anchor desk interviews with captains of industry.
Webinars are ideal marke�ng pla�orms for product launches, training events and industry announcements. Our pla�orm ensures the highest quality video and audio technology.
Novus Print (Pty) Ltd t/a 3S Media is a registered member of National Treasury’s Central Supplier Database for Government.
Supplier Number: MAAA0016423
Unique Registration Ref Number: FFA60BC9-37E6-4596-89D9-A00025D4C50F