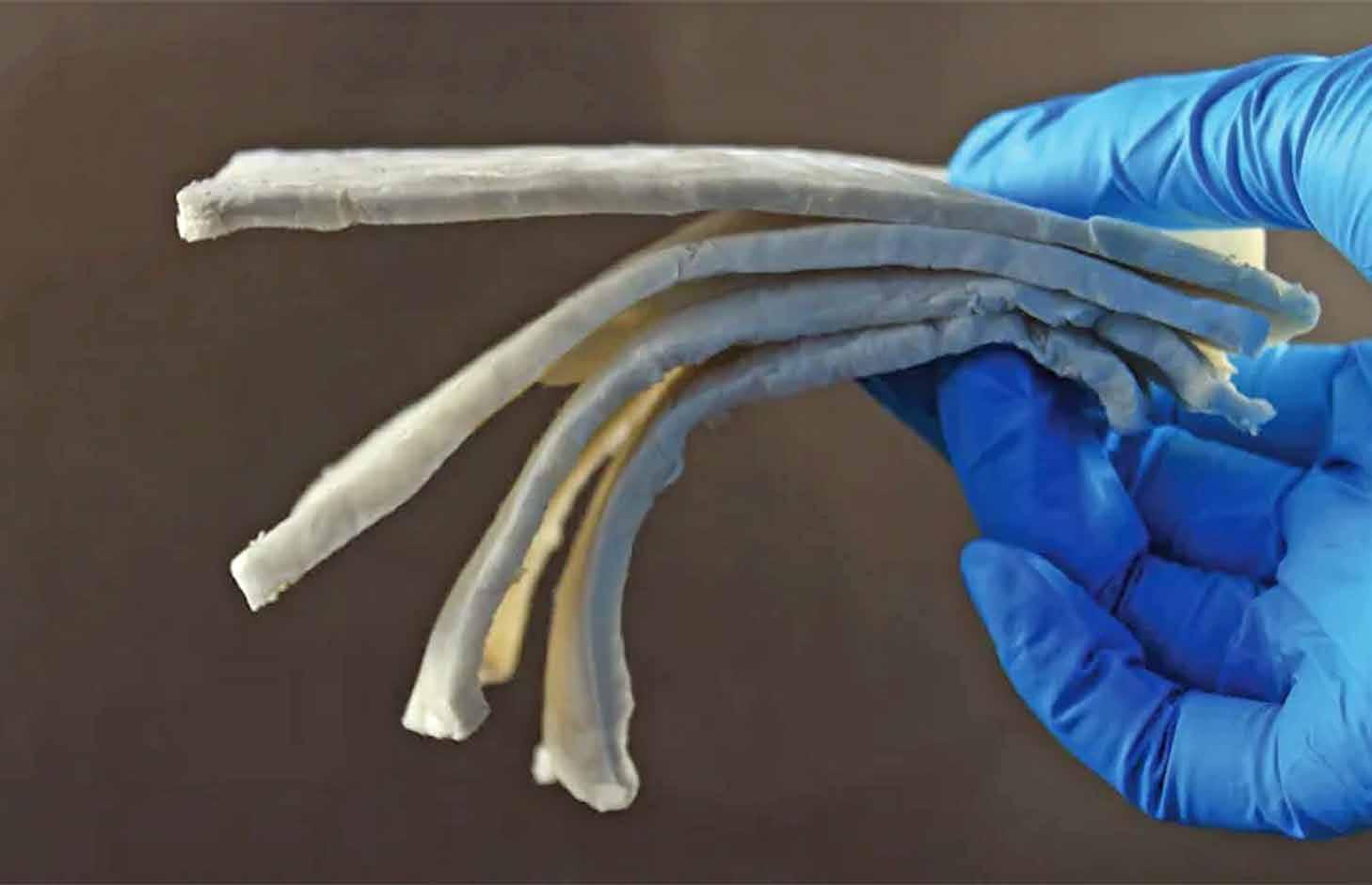
26 minute read
News
from IM20205EN
Samples of the electromagnetic shielding material: a composite of cellulose nanofibers and silver nanowires (Image: Empa)
The world’s lightest shielding material
Advertisement
Electric motors and electronic devices generate electromagnetic fields that sometimes have to be shielded in order not to affect neighboring electronic components or the transmission of signals. Conventional shielding is often too heavy or too poorly adaptable to the given geometry. Therefore, a light, flexible, and durable material with extremely high shielding effectiveness is needed. Researchers now have used nanofibers of cellulose as the basis for an aerogel, which is a light, highly porous material. Scientists of Empa, the Swiss Federal Laboratories for Materials Science and Technology, Dübendorf, Switzerland, now developed aerogels based on cellulose nanofibers that can effectively shield electromagnetic radiation over a wide frequency range. Cellulose fibers are obtained from wood and due to their chemical structure, enable a wide range of chemical modifications.
Ultra-light fine structures
The researchers now have succeeded in making a composite of cellulose nanofibers and silver nanowires, thereby creating ultra-light fine structures that provide excellent shielding against electromagnetic radiation. With a density of only 1.7 milligrams per cubic centimetre, the silver-reinforced cellulose aerogel achieves more than 40 dB shielding in the frequency range of high-resolution radar radiation (8 to 12 GHz); virtually all radiation in this frequency range is intercepted by the material. The composition of cellulose and silver wires is, together with the pore structure of the material decisive for the shielding effect. To create pores of optimum size and shape, the researchers pour the material into pre-cooled molds and allow it to freeze out slowly. The growth of the ice crystals creates the optimum pore structure for damping the fields.
More at Empa>
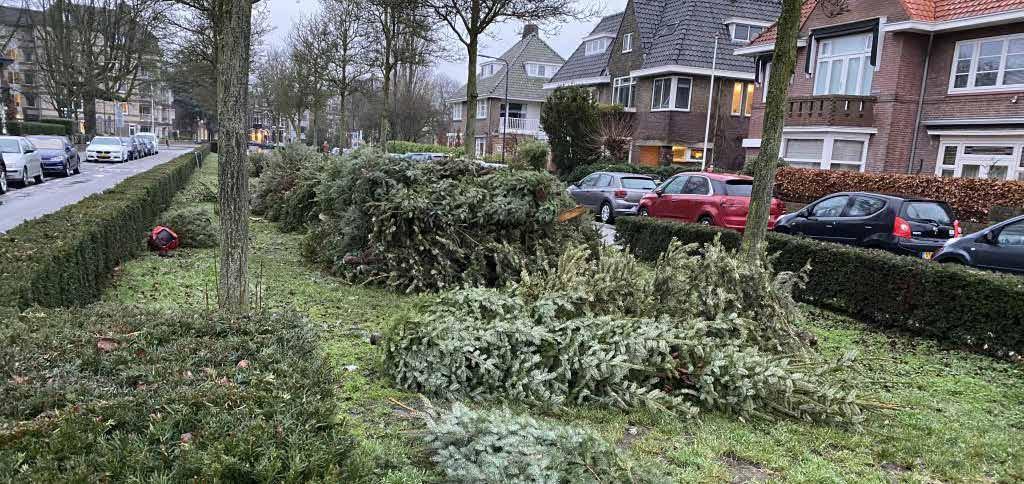
Christmas may be the happiest time of the year, but not the most sustainable. Therefore CoE BBE (Center of Expertise Biobased Economy) is studying a way to make Christmas more sustainable. The research focuses on the processing of pine needles from old Christmas trees into biopolymers to make biobased, circular Christmas bauble.
Every year, three million Christmas trees are planted in the Netherlands. The vast majority eventually finds its way to Dutch living rooms and remains there, often for about four to five weeks. In the past ten years, the Christmas turnover of the Dutch market leader Intratuin has doubled to 135 million euros in 2019. Christmas decorations are increasingly becoming a fashion item that is only used for only one year. The majority of the discarded trees are collected by the municipal authorities and composted or incinerated. Christmas decorations that go out of style are often thrown away. What to do with all that biomass that is released in the first weeks of January? For that reason CoE BBE starts a project, with the aim of developing a circular and biobased Christmas bauble; including packaging. The project is divided into a technical and an economic part. In short, the aim of the technical research is to find out how biomass from used Christmas trees can be processed into a biopolymer and how a Christmas bauble can be produced with it. CoE BBE will carry out this part of the research and finance it together with production companies. The economic part of the research focuses on the target group and the creation of biobased awareness.
More at CoEBBE>
WE KUNNEN NIET ZONDER NATUUR
Word nu lid op natuurmonumenten.nl en ontvang 4 x per jaar het magazine Puur Natuur


Summers are getting warmer. Therefore cities are struggling increasingly with locally occurring heat zones, the so-called Urban Heat Island-effect. An urban heat island is an urban area or metropolitan area that is significantly warmer than its surrounding rural areas due to human activities. The temperature difference is usually larger at night than during the day, and is most apparent when winds are weak. The heat island effect is already a major problem in many countries. Advancing climate changes are bringing more and more southern heat to the cities, leading to progressively hotter and drier summer months. In addition, cities are becoming increasingly crowded and compact and more and more ‘closed’ spaces are emerging. And so there is a clear link between urban morphology, use of materials and microclimate. Urban planners and architects have therefore started thinking about new, smart and robust solutions for climate-friendly adaptations in the city. For example, the Technical University of Munich is investigating new possibilities to use the climate-active properties such as thermal storage capacity and hygric

Hygric properties (water absorption capacity) to reduce the heat island effect. But there’s more. One of the new research directions of the Climate Active Bricks project is the development of a
method in which walls are not oriented in a flat plane, but in a geometry that generates shadow. Digital manufacturing techniques are used for this. As a result a robot will eventually position these ‘selfshading’ bricks exactly in the right place, creating a geometry with such a shadow pattern that the wall becomes less hot due to solar radiation. The TUM researchers want to use this phenomena in combination with the climate-active (thermal and hygric) properties, to create relatively cool zones. According to the researchers, this can make an interesting contribution to a more comfortable and healthier design of cities.
The TUM recently released a video online in which the project is explained (see video).
More at TUM>

Team:
Dr.ing. Architekt Philipp Lionel Molter, (projectleider) Associate Professorship of Architectural Design and Building Envelope; Prof.dr.sc. ETH Kathrin Dörfler, TT Professorship Digital Fabrication; Dipl. ing. Julia Fleckenstein; Ata Chokhachian, M.Sc. Climateflux
Video
Hét expertisecentrum voor materiaalkarakterisering. Integer, onafhankelijk, objectief onderzoek en advies. ISO 17025 geaccrediteerd.
Wij helpen u graag verder met onderzoek en analyse van uw innovatieve materialen. Bel ons op 026 3845600 of mail info@tcki.nl www.tcki.nl
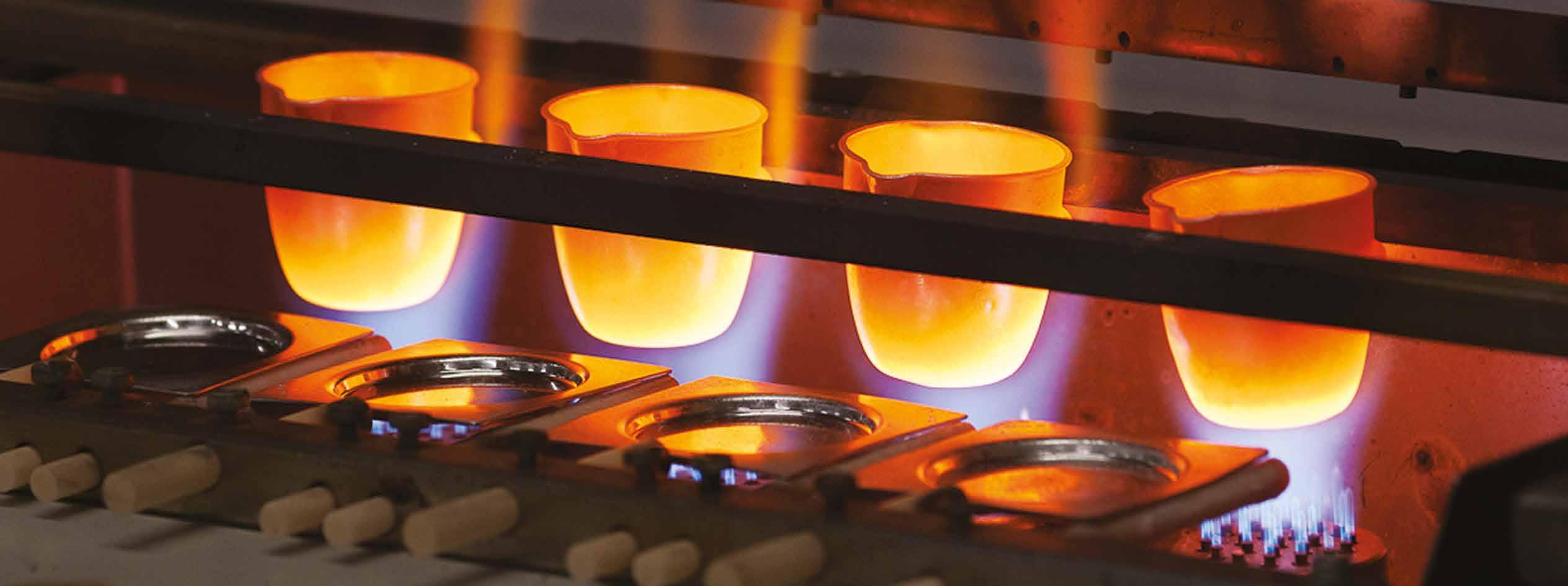
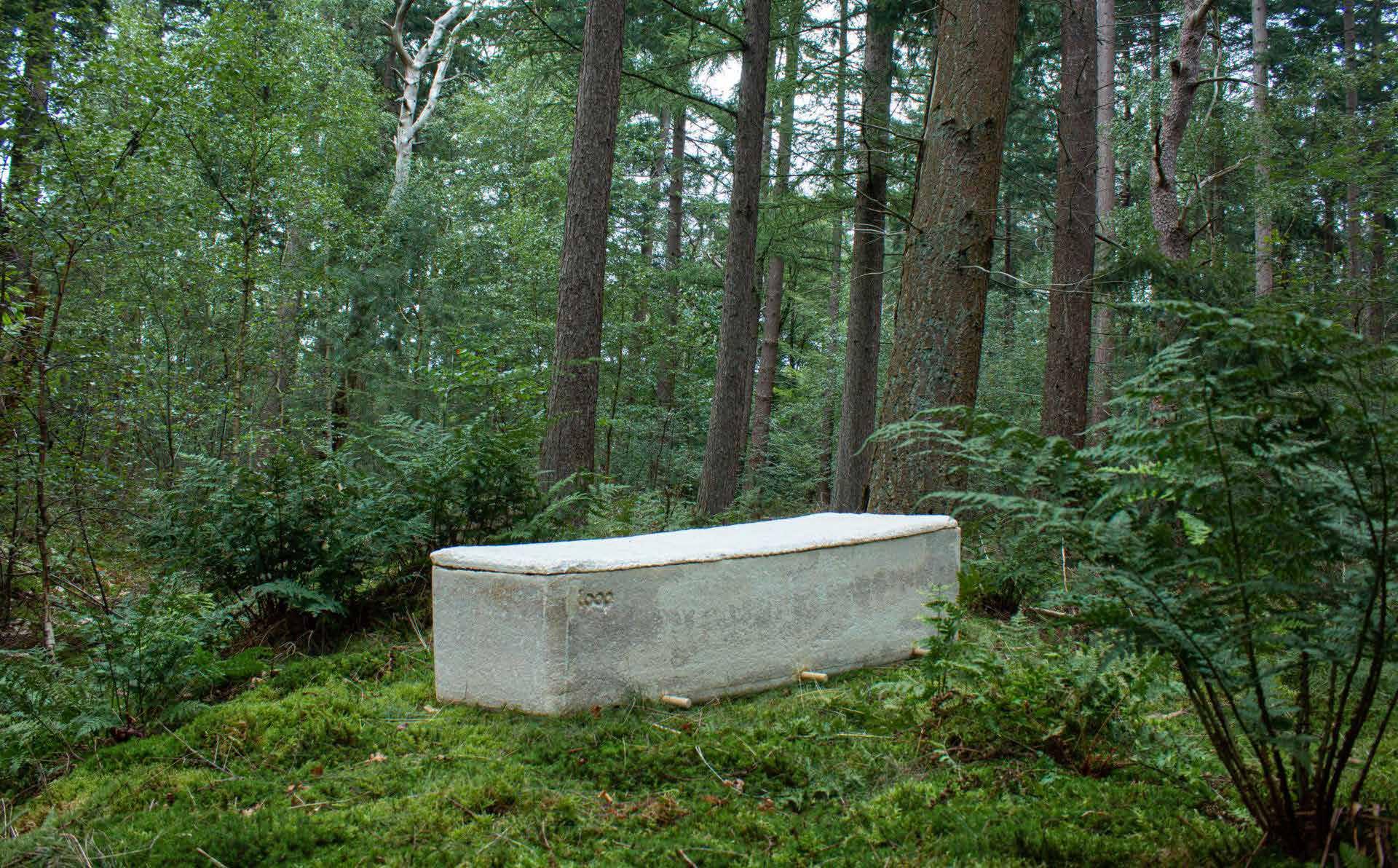
TU Delft start-up develops ‘living coffin’
The TU Delft student start-up Loop has developed a living coffin made from mycelium. The Living Cocoon helps the body to ‘compost’ more efficiently, removes toxic substances and produces richer conditions in which to grow (new) trees and plants. After extensive testing, including in collaboration with two major funeral cooperatives CUVO (The Hague) and De Laatste Eer (Delft), this new form of burial is ready to be applied in practice. The first of the initial limited batch of ten Living Cocoons was already used for a funeral last september. Mycelium normally grows underground in the complex root structure of trees, plants and fungi. It is a living organism that can neutralise all kinds of toxic substances and provides nutrition to everything that grows above the ground. Mycelium can also help break down a human body. The speed at which a body composts generally depends on various conditions, but experience shows that it can take over a decade. The varnished and metal parts of a coffin, as well as synthetic clothing, can persist for even longer. Loop expects that their coffin will be able to complete this entire process in two to three years, because it actively contributes to the composting process. In that process, not only are the waste products from the human body converted into nutrients, the quality of the surrounding soil is also improved,. Practical tests conducted by Ecovative in America have shown that the coffin is actually absorbed by nature within 30 to 45 days, under normal Dutch conditions.

In order to quantify the positive impact on soil quality, Loop is set to join forces with researchers from Naturalis to conduct further research into the increase in biodiversity that this form of burial can help to achieve.
Exhibition at Cube Design Museum
An example of a potential future design of the Loop Living Cocoon is on display at the (Re)Design Death exhibition in the Cube Design Museum in Kerkrade The exhibition is devoted to the theme of saying goodbye, dying, mourning and remembrance and can be seen until 24 January 2021.
TU Delft>
More at Loop>
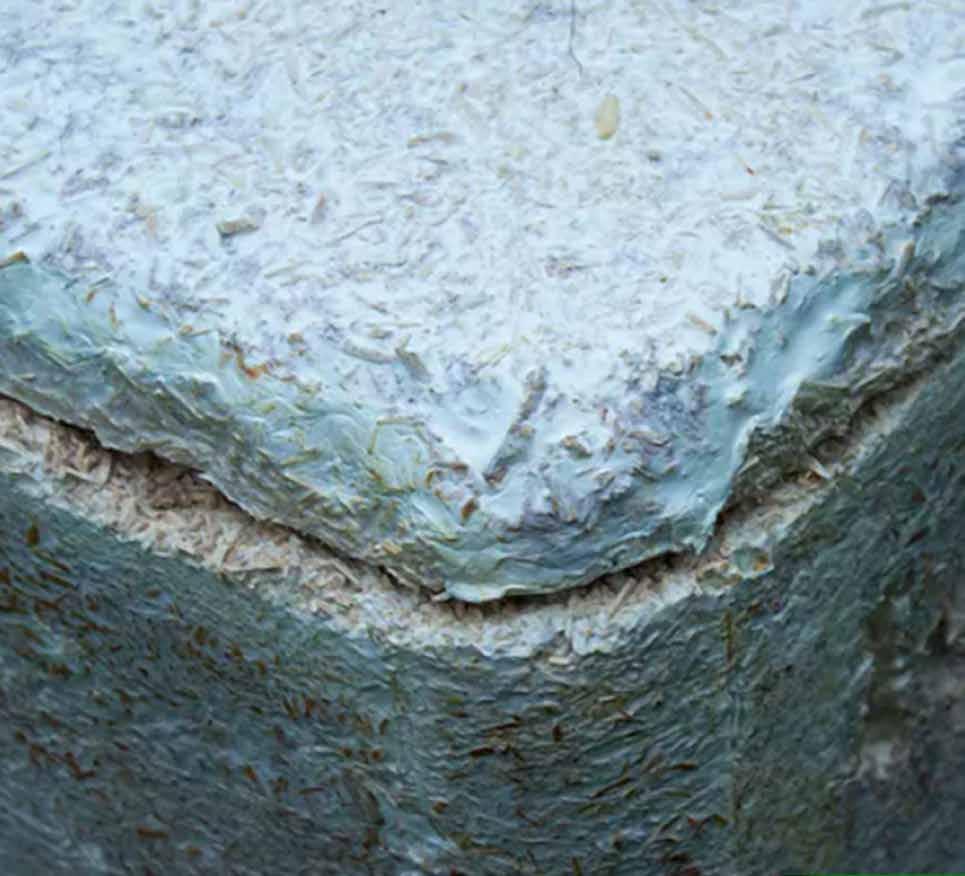
Voeg informatie toe aan de Kennisbank Biobased Bouwen
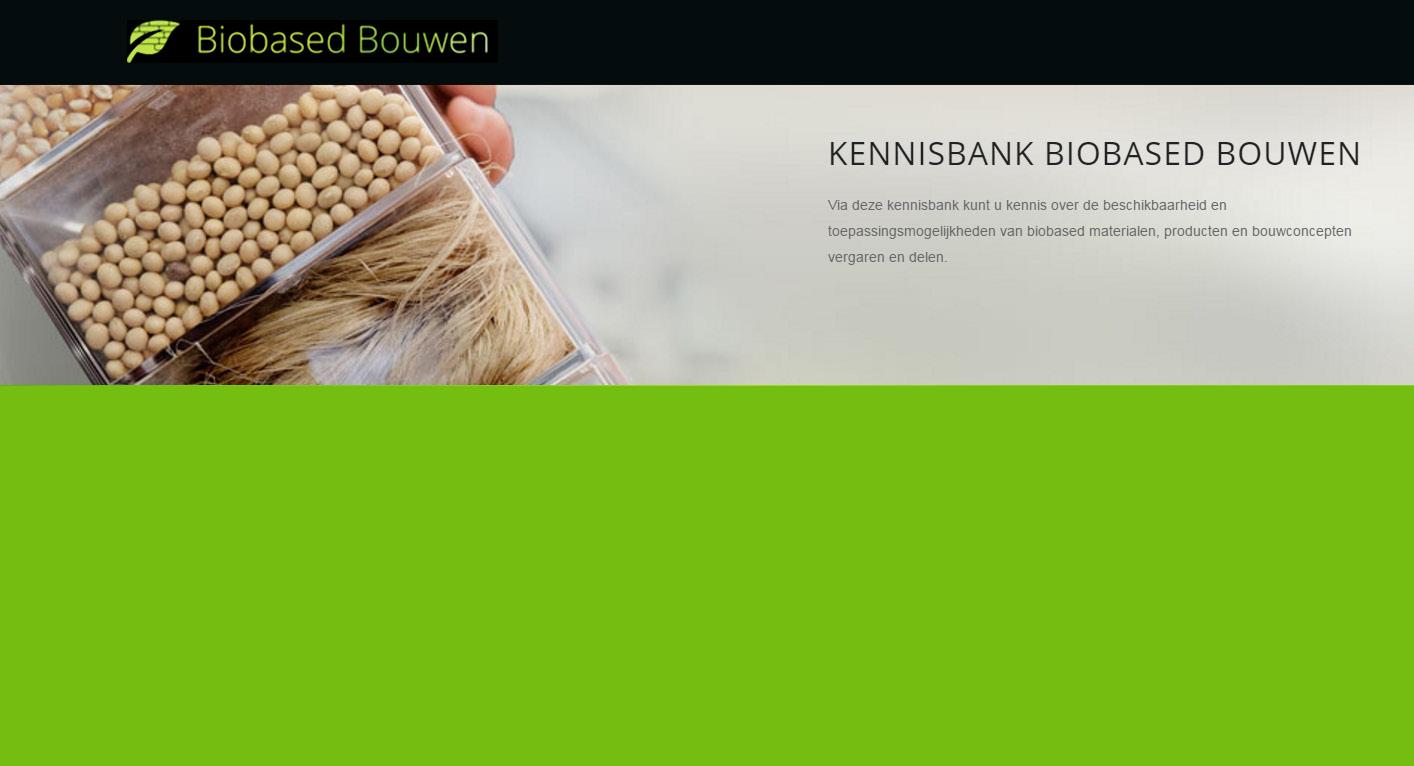
De Biobased Economy speelt een belangrijke rol in de duurzame ontwikkeling van Nederland en biedt nieuwe kansen voor het bedrijfsleven. Via de kennisbank kunt u kennis vergaren en delen over de beschikbaarheid en toepassingsmogelijkheden van biobased materialen, producten en bouwconcepten. Samen versterken we zo de biobased economie.
Ruim dertig partijen in de bouwsector ondertekenden de green deal biobased bouwen. Deze producenten, architecten, adviseurs en kennisinstellingen delen hun kennis rond kansrijke mogelijkheden van biobased bouwen. Ook de ministeries van Binnenlandse Zaken (Wonen en Rijksdienst), Economische Zaken, en Infrastructuur en Milieu ondersteunen de green deal.

Easy-to-repair glass speaker wins Dyson Award 2020
Six industrial design engineering students from Delft University of Technology have won the Dutch edition of the James Dyson Award with Ammos: a fully recyclable home audio system that produces crystal clear sound with a sheet of glass. With their sustainable design they hope to stimulate recycling and give everyone the chance to easily repair their audio system. Electronic waste is growing at speed. Harmful to the environment and bad for your wallet. Last year, more than fifty million tons of electrical appliances were thrown away
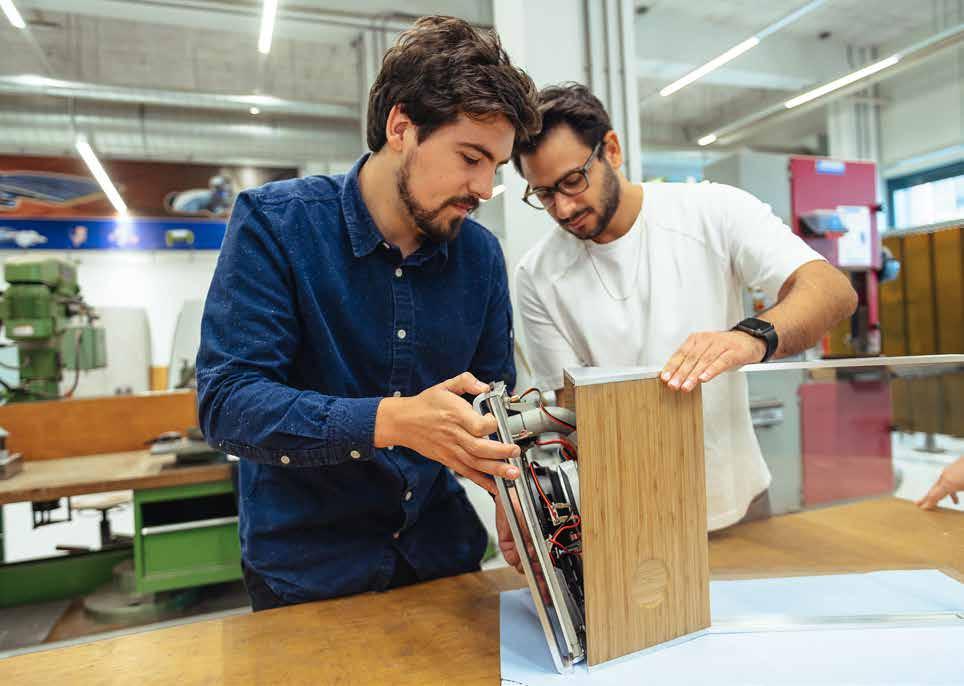
worldwide. More than seven kilos per person. As demand for modern appliances grows, the mountain of e-waste keeps growing. Students at TU Delft’s Faculty of Industrial Design (IDE) realised that things could be done better. With the development of Ammos, they aim to start a counter-movement to the current throw-away culture. A glass speaker that you can repair yourself with just one screwdriver.
Glass
The big problem for consumer electronics is twofold. Firstly they’re often difficult, if not impossible to repair. Secondly, they are very difficult to recycle. Current speakers, for example, include parts made from rare metals. In collaboration with the Delft startup, DeNoize, the students set to work on the most important element of their Ammos design: the highly recyclable material that is glass. While DeNoize is developing soundproof glass for buildings, the design students turned this concept on its head. What if we let the glass generate sound? With only ecologically sound materials such as bamboo and no compounds such as glue, Ammos is not only sustainable in
production, but also easy to disassemble if you want to replace parts.
How does it work?
Ammos amplifies sound by vibrating a thin glass plate with the help of small actuators placed invisibly close to the edge of the glass. Thus the glass produces medium to high frequencies from 200 to 20,000 Hz. A small subwoofer in the base produces low frequencies of 20 and 200 Hz for a full sound spectrum. The speaker can be connected via Wi-Fi and Bluetooth and has USB-C, 3.5 mm audio cable and power support as inputs. The bamboo front panel has a haptic touch surface that allows easy operation.
A winning design
The jury was impressed by Ammos’ design, with a long lifespan due to the high-quality components and timeless design. The product consists of secondary materials that have been chosen for durability, user quality and because they are ecologically sound. The aluminium printed circuit boards, for example, provide better heat dissipation, longevity, recyclability and are non-toxic. Ammos also stands for reparability. No glue is used, all fastenings can be undone with a
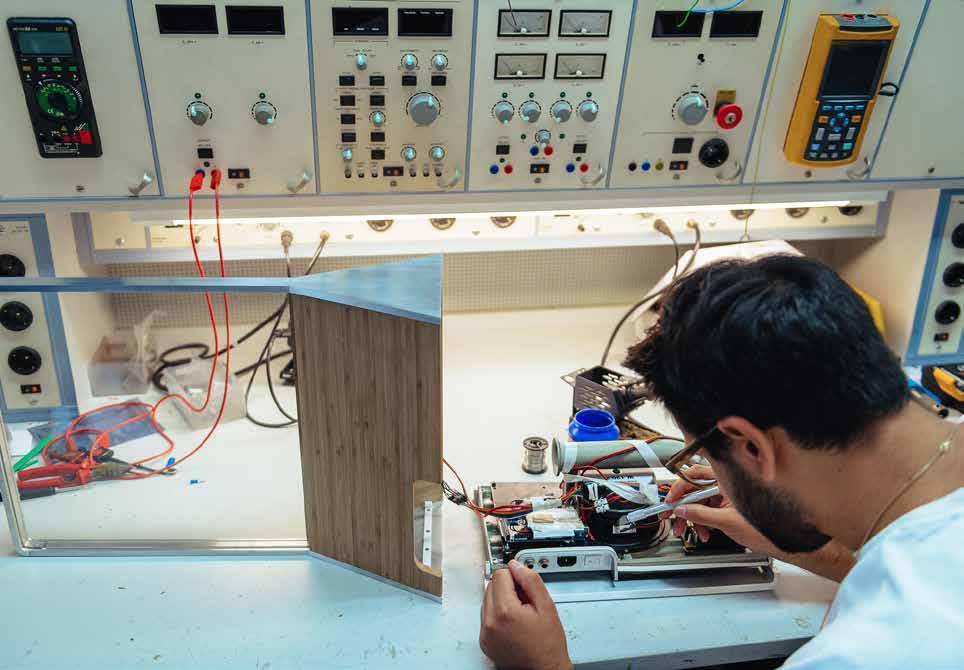
single screwdriver and all electronics are accessible by removing only six screws. Critical components can be replaced more easily and cheaply, for example in case of a crack in the glass plate.
Text TU Delft>
Video


Kamp C the first to print an entire house in one piece
This summer, at Kamp C, (the provincial Center for Sustainability and Innovation in construction at Westerlo, Belgium) a building was printed with the largest 3D concrete printer in Europe. The 90-square metre dwelling was printed in one piece with a fixed printer. According to the parties involved this is a world first. The project is supposed to demonstrate the possibilities of the 3D concrete printing to the construction industry. The printed house is three times sturdier than a house built with quick build bricks. The material’s compressive strength is three times greater than that of the conventional quick build brick. This first house is a test. The researchers will now check whether solidity is retained over time. Besides the fibres in the concrete, the amount of wire-mesh reinforcement


used is extremely limited. As a result of the printing technology used, formwork was redundant, saving an estimated sixty percent on material, time, and budget. In the future, an entire house could be printed in just under two days. If you add up all the days, it took just three weeks to print the house at Kamp C. The 3D concrete printer, which Kamp C bought from the Danish pioneer 3D Printhuset, is 11.4 x 10 x 10 m in size and can print a building up to 8.3 m high, 9.5 m wide and 9.5 m deep.
The house at Kamp C is a demo building that aims to show the techniques and opportunities of 3D printing as much as possible, such as strongly curved walls, different wall types, while avoiding thermal bridges. The house is part of the European C3PO project, which stands for ‘Co-creation: 3D Printing met Ondernemingen (Enterpises)’. The project aims to accelerate the introduction of this innovative technology in Flanders. Eight partners, from both the scientific and business world, join forces: Beneens, ETIB / CONCRETE HOUSE, Groep Van
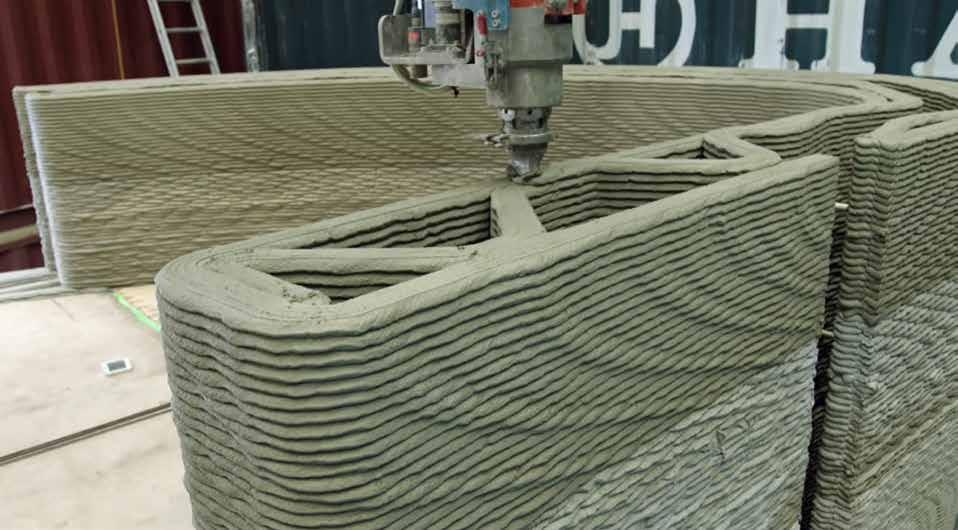
Roey, Thomas More, Trias architects, Ugent and Vicré. Saint-Gobain Weber is also participating in the project. The house was printed with support from ERDF (the European Regional Development Fund).
More at Kamp C>
Photography: Kamp C & Jasmien Smets

Schuttebusbrug wins national steel prize 2020
The Zwolle Bus Bridge has won the Dutch National Steel Award 2020 in the category ‘Infrastructure.’ The the S-shaped Schuttebusbrug (bridge) was designed by ipv Delft for ProRail and the municipality of Zwolle. The bridge was built by BAM Infra.
The National Steel prize has been awarded every two years since 1971 in five categories: Non-residential construction, Industrial construction, Residential construction, Infrastructure, Characteristic steel building components. The Schuttebusbrug is an S-shaped bus bridge on the west side of Zwolle station. In the run-up towards the project, the project team considered different material options. From the point of view of costs, feasibility and maintenance, the choice was made for a main span in steel with concrete abutments. The main span is a tubular steel beam (box girder) with cantilevering steel wings. From a structural point of view, this is the most logical option. There is a concrete pressure layer on top of the steel construction. The steel main span of over eighty meters is located above the track and has the double shape of a S curve. The box girder runs both in width and height, in the middle of the span it is 3.66 meters wide and 3.75 meters high. At the ends, the box girder is 4.55 meters wide and 2.67 meters high. The steel used is S355, the weight of the 110 meter long box girder is 1,000 tons.
The bottom of the S-shaped bridge is covered with bamboo, so that the bridge fits in well with the new, green environment of the station. The bridge construction consists of a central box girder with the deck overhanging. The light aluminum bridge edge is, among other things, equipped with integrated lighting for the roadways. From the side, this produces a three-layer image: the dark gray box girder at the bottom, the wooden slats above it and a slender, light line at the end. All necessary (technical) facilities have been integrated into the design: vehicle barriers, shielding the overhead line, lighting, rainwater drainage and soundproofing.
The bus bridge opened on 9 February, 2019 and was commissioned on 17 February, 2019. The bridge is only accessible to regular buses and emergency services.
According to the jury, the winning design was chosen because of its clear line and sleek design with a pleasant, soft appearance. According to the jury, the Schuttebusbrug is unique because of its shape, the use of steel and the method of inserting the steel main span above the tracks and finally the torsion-resistant design, which makes the slim appearance of the 245-meter-long bridge appear to float.
The Schuttebusbrug was designed ipv Delft for ProRail and the municipality of Zwolle. The bridge was built by BAM Infra. The Belgian steel constructor Victor Buyck Steel Construction made the construction and there was collaboration with Setzpfandt Beratende Ingenieu-
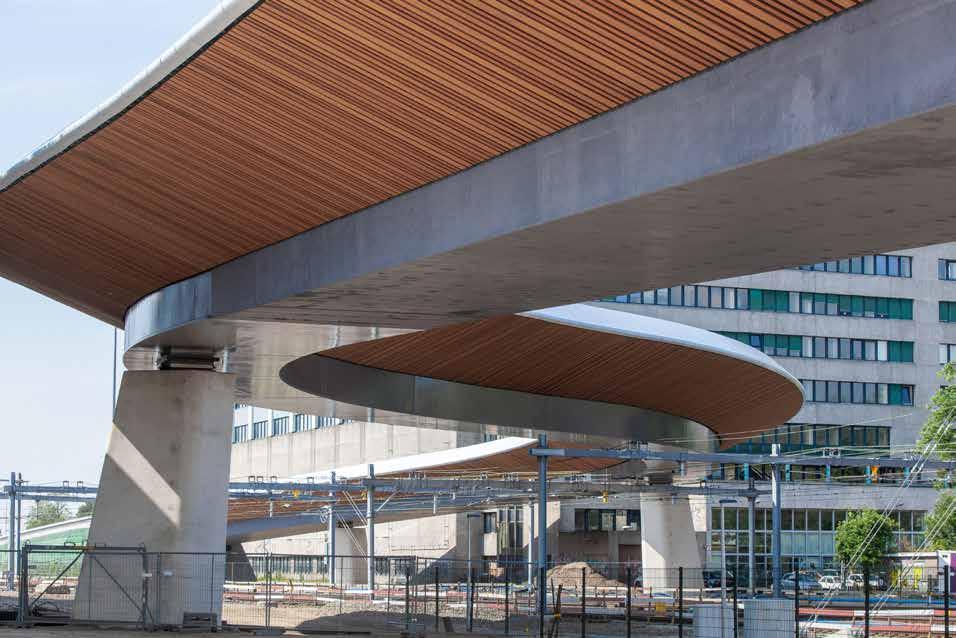
re, who developed the structural design together with engineers from BAM.
Nationale staalprijs (Dutch)>
ipv Delft> Winners in the other categories are:
Diamantbeurs, Capital C, Amsterdam (category Non-residential building)> Rhenus New Logic III, Tilburg (Industrial building)>
Residential building Fenix I, Rotterdam (Residential building)>
Kunstobject de Zwerm, Eindhoven (Characteristic steel building parts)>
The winner of the National Sustainability Award for Steel 2020 is the project ‘Renovation of shops Hoogstraat 168-172, Rotterdam.’>

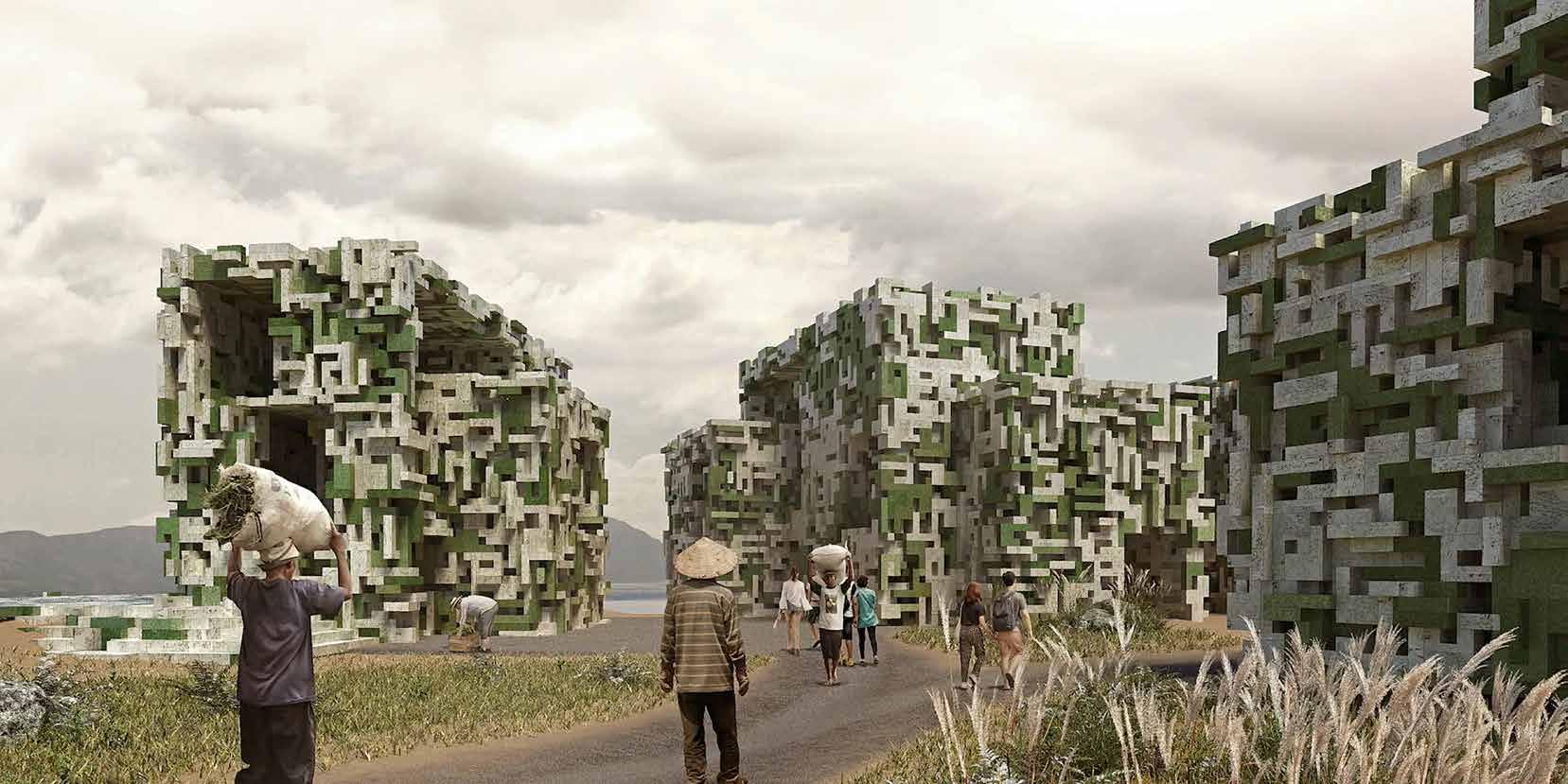
Algae as a building material
Students from the Bartlett School of Architecture at University College London have investigated the use of algae as a building material when mixed together with clay. The research focused on the east coast of China, where so-called algae blooms are common and cause a lot of nuisance. This has led to a concept in which various building materials were developed based on algae. These algae can be mixed with clay in different proportions and then pressed. This resulted in building blocks of different shapes and densities, which, according to the researchers, opens up completely new possibilities in terms of design. The type of algae the project proposes to use green macroalgae, which despite being naturally-occurring, is harmful to natural environments and marine life. Notorious are so-called algae blooms, where the algae multiply explosively, emit toxic gases and destroy marine life. The Bartlett researchers’ idea was: can anything useful be done with that enormous growth of algae? For example, could it be made into construction material? And so the Ningbo Eco Village project
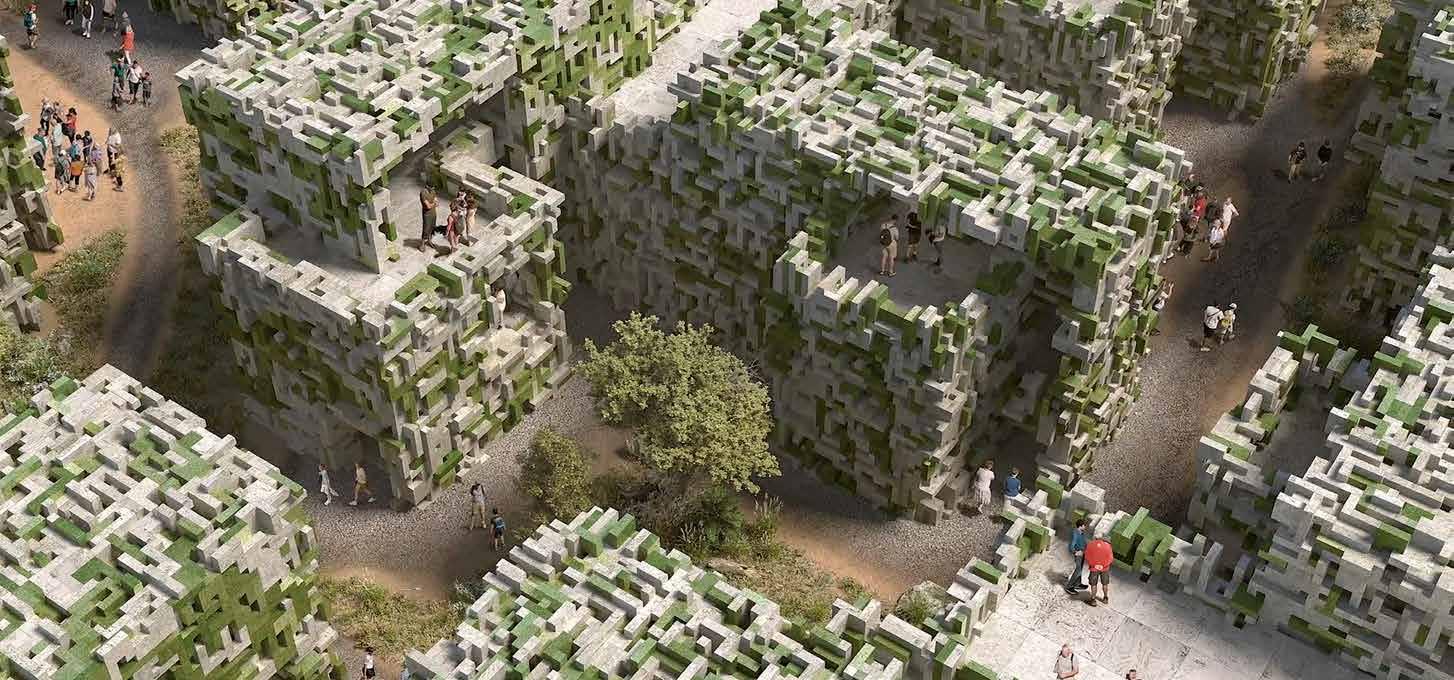
was born. The environment of the site is rich in these algae, and in this way alternative building materials will find and use an alternative destination to obtain housing units. The team succeeded in creating a light, rigid building element (block) by compressing and hardening green macroalgae, mixed up with white clay, with clay playing the role of a naturally derived structural aggregate. Furthermore, a interlocking component system was developed, with which a newly devised design language can be given shape.
Project name: Algae Anatomy Team: Bryan Law, Dinel Mao, Jie Song Studio: Research Cluster 5&6 Tutors: Daniel Widrig, Guan Lee, Adam Holloway

Video Different building blocks of algae. Issuu publication ‘clay: algae atonomy’>

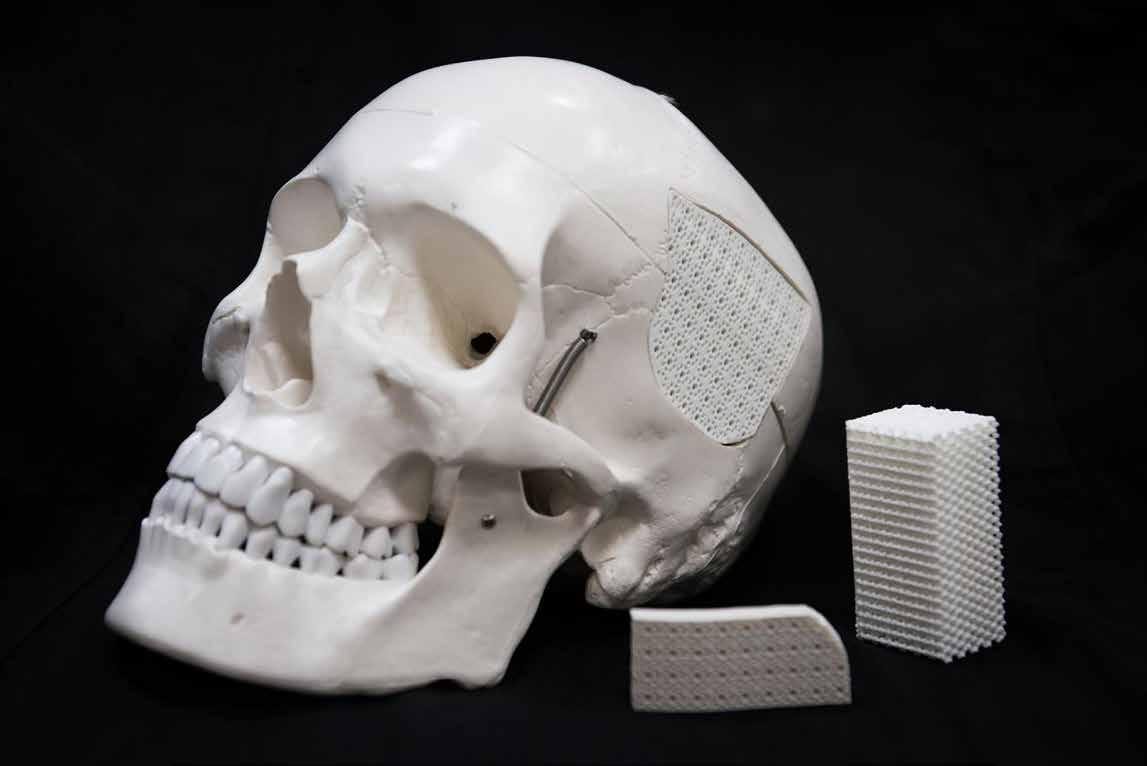
Eggshell-based surgical material for skull injuries
A bioactive polymer-ceramic composite for fixing implants and restoring bone defects in the skull was developed by an international group of materials scientists from the NUST MISIS Center for Composite Materials, Moscow, Russia. An innovative composition of the material based on eggshell-derived bioceramic provides increased strength and biointegration of implants. The results of the work were published in the international scientific journal Journal of Asian Ceramic Societies, titled ‘Designing of porous PMMA/diopside bone cement for non-load bearing applications.’
Polymethylmethacrylate (PMMA) is a synthetic polymer used by surgeons as a ‘bone cement’ due to its self-curing and strength properties. But this material is bioinert by its nature, therefore it has a weak chemical and biological interactions with living tissues and hardly integrates with bones. Scientists are actively investigating PMMA in order to optimize it for wider application in various biomedical fields, for example, ensuring reliable fixation of artificial joints/implants, dental fixators, closure of cranial defects in various injuries, etc.
The team of the NUST MISIS Center for Composite Materials has solved this problem by modifying polymethylmethacrylate adding diopside, a material from the category of silicate bioceramics. It is known for such properties as lack of toxicity to living cells, biodegradability and the ability to stimulate osteogenesis - the formation of bone tissue on its surface.
For the production of composites, diopside obtained from eggshells was used. The developers proposed to optimize the material by adding bioactive ceramics to the PMMA polymer matrix. As a result, a porous composite PMMA/diopside material was obtained. During the experiments, different proportions of diopside - 25, 50 and 75 % were used.
The samples containing 50 % diopside have shown the best result - they have demonstrated a four-fold increase in compressive strength, and after four weeks of in vitro testing have shown a good ability to deposit bone minerals on their surface. At the same time, the scientists have found that the mechanical properties of the obtained porous composites correspond to the properties of the spongy bone of the human body.
MISIS>
The original article is online>
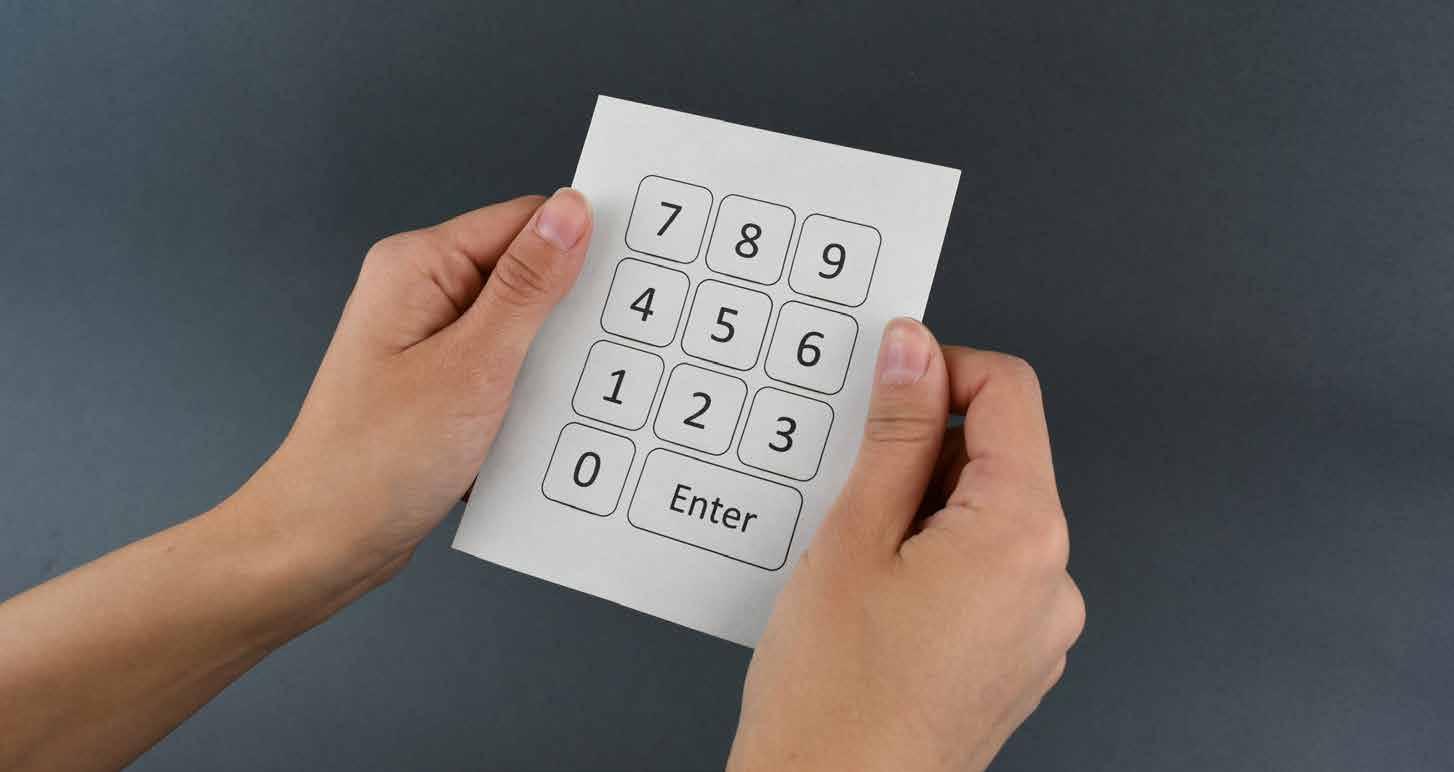
Foldable keyboards out of any paper
Engineers of Purdue University (West Lafayette, VS) developed a simple printing process that renders any paper or cardboard packaging into a keyboard, keypad or other easy-to-use human-machine interfaces. This technology was published in the Aug. 23 edition of Nano Energy, titled ‘Moisture-insensitive, Self-powered Paper-based Flexible Electronics.’ According to Ramses Martinez, assistant professor in Purdue’s School of Industrial Engineering, it’s the first time a self-powered paper-based electronic device is demonstrated. The scientists have unveiled a new printing process that can turn just about any piece of paper or cardboard into a waterproof, foldable keyboard that even doesn’t require a power source, since they harvest the energy from their contact with the user1 . The Perdue scientists developed a method to render paper repellent to water, oil and dust by coating it with highly fluorinated molecules. This omniphobic coating allowed the team to print multiple layers of circuits onto paper without getting the ink to smear from one layer to the next one. (A surface is omniphobic if, in addition to being water-repellent (hydrophobic), it is also oil-repellent (oleophobic).)
According toe Purdue this technology is compatible with conventional large-scale printing processes and could easily be implemented to rapidly convert conventional cardboard packaging or paper into smart packaging or a smart human-machine interface.
Martinez envisions this technology to facilitate the user interaction with food packaging, to verify if the food is safe to be consumed, or enabling users to sign the package that arrives at home by dragging their finger over the box to properly identify themselves as the owner of the package. Additionally, the team demonstrated that simple paper sheets from a notebook can be transformed into music player interfaces for users to choose songs, play them and change their volume.
More at Prudue>
1 Watch the video ‘Harvesting the World’s Mechanical Energy: Triboelectric Generators Capture Wasted Power’>
Video
MAKE IT MATTER
MAKE IT MATTER is compiled in collaboration with MaterialDistrict (MaterialDistrict.com). In this section new, and/or interesting developments and innovative materials are highlighted.
Le Pavé
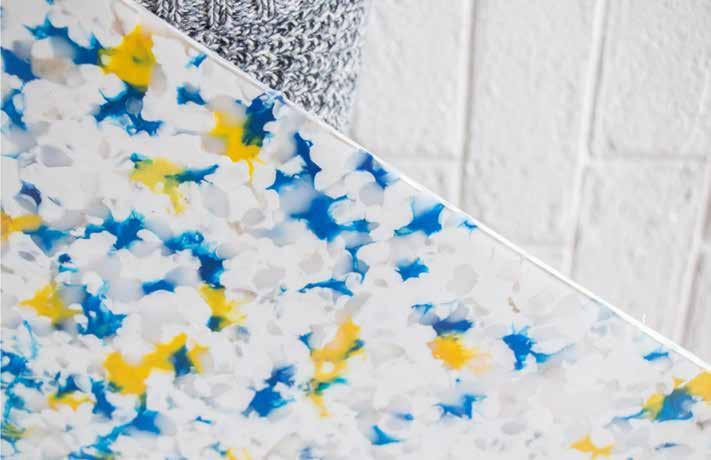
The material Le Pavé comes in panels made from plastic waste. It is certified safe, locally produced, recycled, recyclable and fire-resistant. It’s composed of 100 % plastic waste; all of which is made possible by a patented thermocompression technique. With Le Pavé each panel is unique, the aesthetics are the result of a unique process, which, like marble or wood, allows the substance of the material to express itself.
More at MaterialDistrict>
Remake ceramics

With Remake ceramics, Breda (The Netherlands) based Fabrique Publique reuses broken pieces of ceramics, saving them from the incinerator, and makes it a valuable resource for new products. The first tests with recycled ceramics were applied to a set of tableware called ‘Future history’, containing 5 and 10 % recycled material. In further research, tests with higher percentages of recycled content were carried out, as well as tests with smaller/bigger type of grains and specific colours.
More at MaterialDistrict>
Space-defining-surfaces

Design studio Giles Miller Studio developed textured wall tiles made of various materials, like ceramics, wood, and metal. The tiles manipulate the relationship between light and material to create subtle yet complex aesthetics.
More at MaterialDistrict>
Recycled pet felt wall-cover

To improve the acoustics, mostly the reverberation time will be shortened. The RTS acoustic panels, made by RTS-Preidel, Alblasserdam, The Netherlands, ensure optimum absorption and are easy to process. The total system of the RTS acoustic panel (full-colour) consists of a felt plate that is installed on a cavity filled with absorption filling. The material is made from recycled PET and 280 bottles are used for the production of one sheet.
More at MaterialDistrict>
Lightweight acoustics
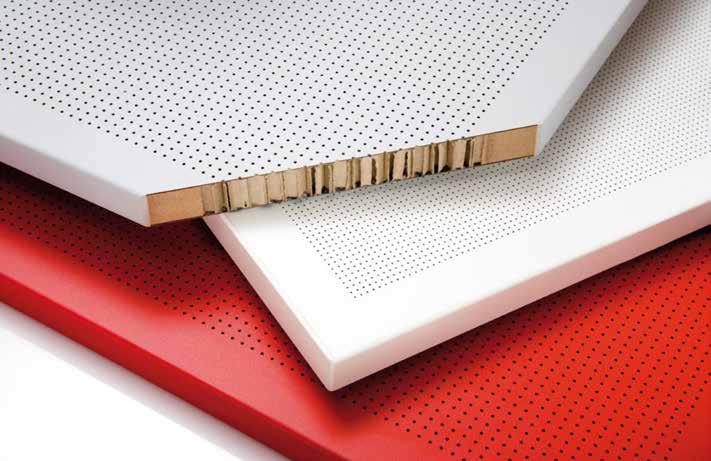
Modern architecture and design increasingly use more materials such as glass, steel and stone that meet the requirements of more open offices and meeting facilities. These hard surfaces reflect sound and contribute to an increase in sound levels and a decrease in productive environments. Lightweight Acoustic Trend panel counteracts the noise. The material is made of pressure laminates and wood veneer, perforated with more than 320,000 perforations per square meter.
More at Material District>
Robotic precision in manufacturing parametric design

Designed by researchers of the University of Stuttgart, the BUGA Wood Pavilion celebrates a new approach to digital timber construction. Following biomimicry principles, the pavilion consists of 376 segmented timber shells. Each polygonal segment is built up from two plywood panels and features unique finger joints (more than 17,000) on the sides to make them fit together like an enormous jigsaw puzzle.
More at MaterialDistrict>
HeartFelt-baffles
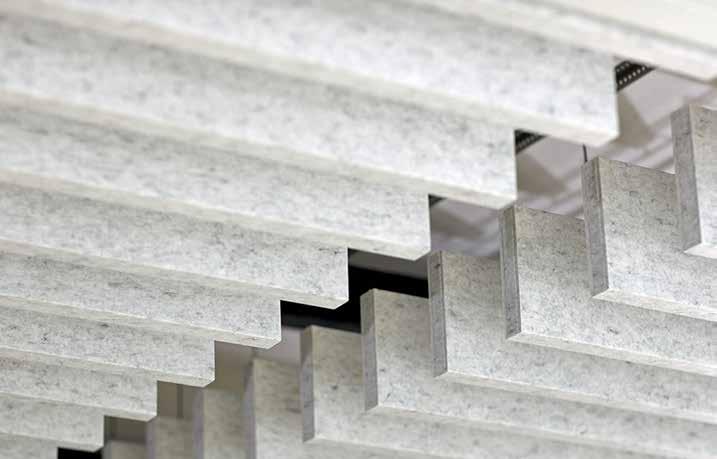
The HeartFelt modular acoustic felt system for ceilings and walls was developed by Hunter Douglas Architectural. The lightweight HeartFelt acoustic baffles for ceilings are made from non-woven thermoformed PES fibres, each measuring 40 to 100 mm in width and are available in 100-500 mm height, with a maximum length of 2000 mm. HeartFelt Baffles won the 2020 Red Dot Design Award in the Product Design category.
More at MaterialDesign>
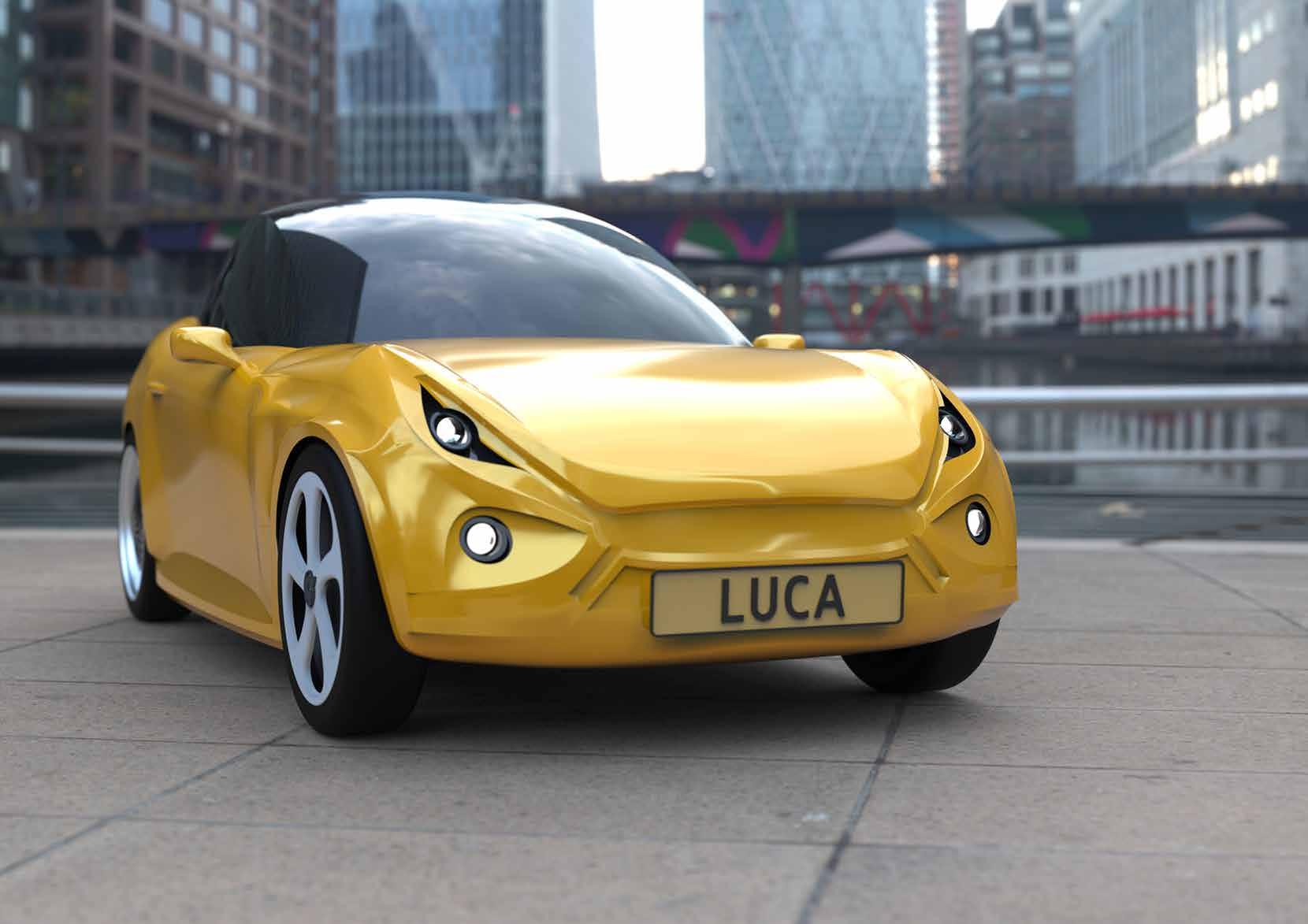
Presenting Luca: a car made of recycled waste
Every year mankind produces 2.1 billion tons of waste, worldwide. In order to demonstrate this material can be reused this waste in a useful manner, a TU/ecomotive student team developed a car made almost entirely out of waste. The result is a sporty-looking electric car called Luca with a base of flax and recycled plastic, a large part of which was even fished out of the ocean. The body, finish, windows and interior are also made of recycled materials, including PET bottles, the hard plastic ABS and household waste. October 8th, the car was officially be unveiled.
Luca is a compact car with two electric motors in the rear wheels. It can reach a top speed of 90 kilometers per hour and has an action radius of 220 kilometers. The consumption can be converted to about 180 kilometers per liter of gasoline. In addition to the efficient engines, this is due to the low weight: the car weighs only 360 kg without batteries. This is over half as light as comparable cars. In addition, the car only needs sixty kilos of batteries as opposed to hundreds of kilos for other electric cars.
Plastic from the oceans
Luca’s chassis consists of a unique sandwich panel developed by the students in collaboration with several companies. The exterior is made of flax fibers combined with plastic which was fished from the ocean. Although this was often in
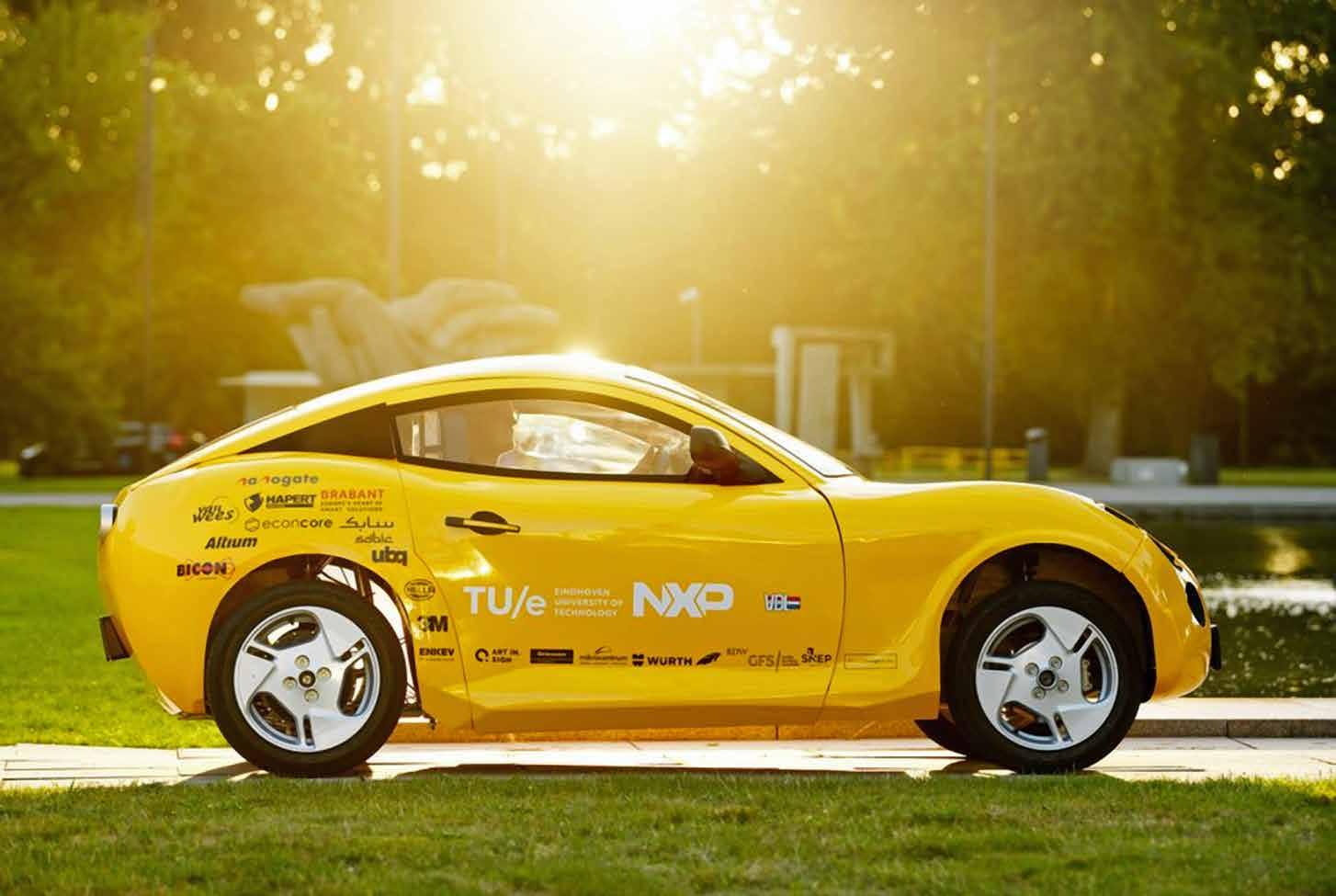
the ocean for several years and consists of different types of plastic, it is able to give the chassis sufficient strength when combined with the natural fibers. The core of the material is made of recycled PET bottles. PET can be recycled no more than ten times, so its lifespan can be greatly extended by using it in a car. After all, ten cars last longer than ten plastic bottles.
Coloured film
However, the implementation of waste doesn’t stop there. The car’s body, for example, is made of recycled ABS, a hard plastic used in many consumer products such as toys, televisions and kitchen products. The car gets its yellow colour from a wrap - a coloured film - instead of paint. This film can also be removed without leaving any residue. This leaves pure plastic and makes the final recycling process a lot easier. The side and rear windows are also made of recycled material. The recycling process immediately gives the windows a luxurious black tint, so sustainability can be anything but boring.

Coconut- and horsehair
Waste has also been used in the interior. For example, Luca has two very comfortable custom-made chairs, the cushions of which consist of a combination of coconut hair and horsehair. The fabric around them is made of recycled PET but feels and looks like suede. The center console consists, among other things, of a plastic additive from household waste. In addition, there are even residual materials from Luca’s own production process: small pieces of flax with the plastic from the ocean are compressed into stylish, useful plates.
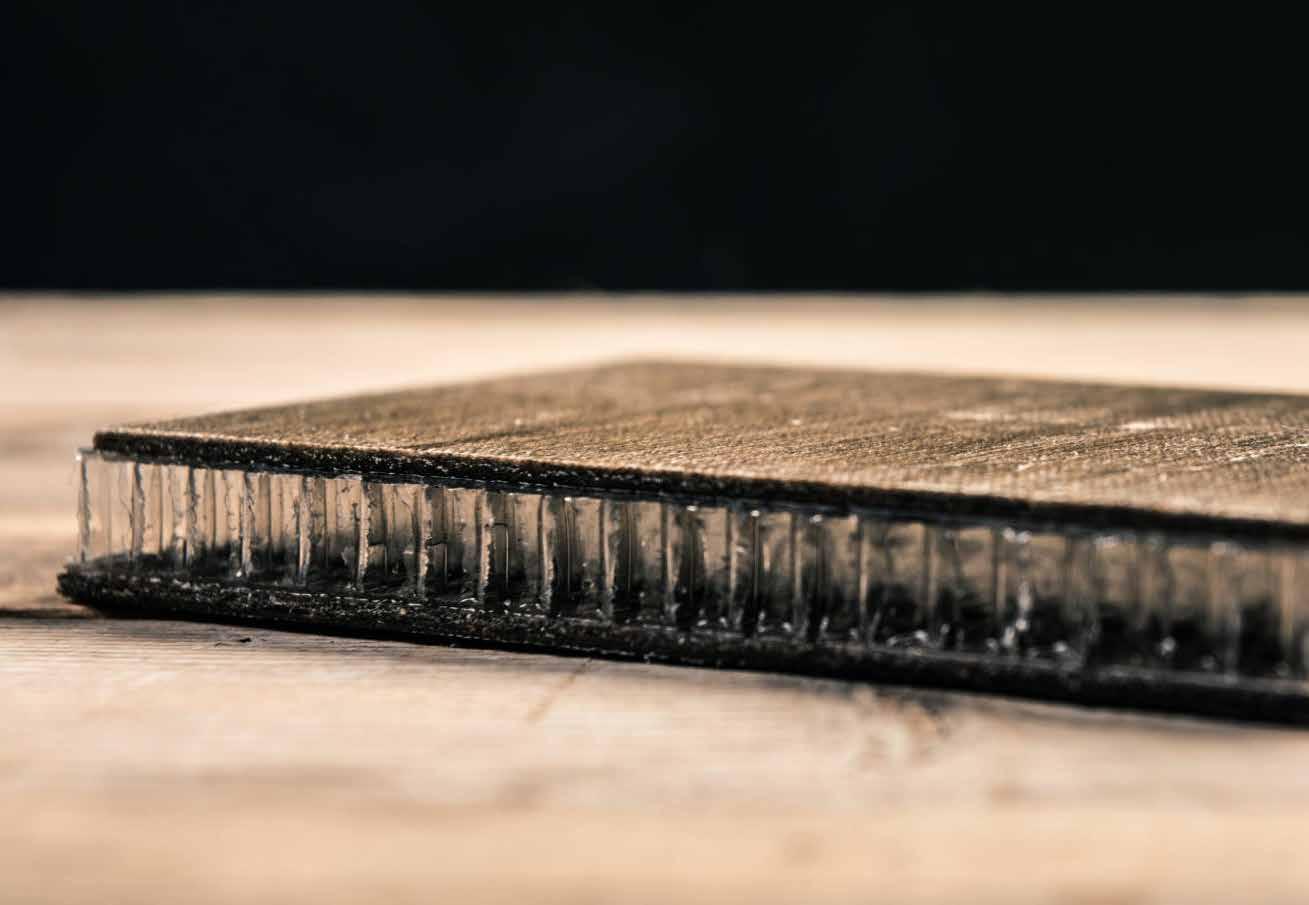
Photography: Bart van Overbeeke
More at TUE>
More about Luca at TU/ecomotive >
7de editie Ontmoet dé top van de lijmsector
Trends en ontwikkelingen voor industriële lijmverbindingen
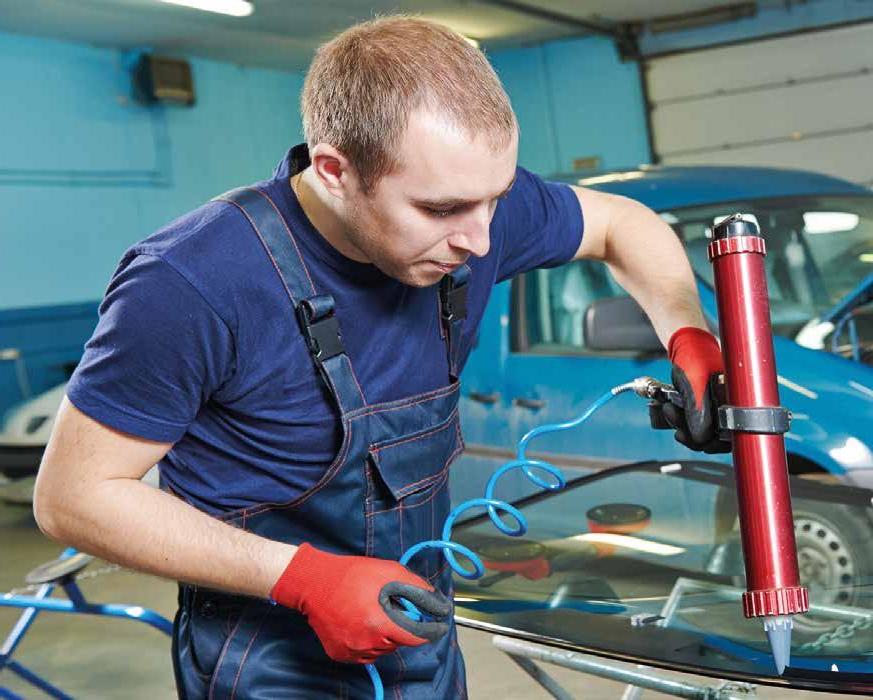