
6 minute read
Flax fibre composites in F1
from IM20205EN
McLaren and the Swiss company Bcomp are developing F1’s first natural fibre composite racing seat. The composite material is based on two fibre strengthened composites, developed by Bcomp, with salient properties in terms of temperature resistance, strength, weight, vibration damping and safety. The latter because of the crack behaviour of flax fibre composites. As opposed to carbon fibres, this natural fibre composite has a ductile fracture behaviour with blunt edges, thus improving safety without sharp carbon fibre shattering and toxic carbon fibre dust. And last but not least: using natural fibres instead of carbon, the CO2 footprint can be drastically reduced.
Since the introduction of the FIA Formula 1 World Championship in 1950, motorsport has seen teams constantly pushing the boundaries of technology, making it the birthplace of innovation. For instance, in 1981, the McLaren Formula 1 team was the first to apply the aerospace fighter plane practice of using carbon fiber to replace aluminum in creating the chassis. The McLaren MP4/1 was met by skepticism in the paddock that season, but carbon fiber was quickly adopted by all of the F1 teams. Now McLaren is thinking of a new material innovation. The reaceteam wants to start replacing carbon fiber in some parts of its F1 cars with a new organic composite developed by Swiss natural fiber supplier Bcomp Ltd. Carbon fiber accounts for 70 percent of an F1 car by weight, but Bcomp’s renewable natural fiber material is lighter still. It also has the advantages of being cheaper, stronger, and more vibration dampening, which are all appreciated benefits. Furthermore, using Bcomp’s natural flax fibers in place of conventional carbon fiber is expected to result in a 75 percent lower CO2 footprint for the specific part; a racing seat in this case.
Advertisement
CO 2 -neutral
Flax is primarily used in the production of linen. It is grown without competing directly with food crops. Flax is a CO2-neutral raw material and its fibres are biodegradable. At the end of the bio composite material can be ground down into a new base material or thermally
Flax fibres
recycled without residual waste, rather than end up in landfill.
AmpliTex
Bcomp was founded in 2011 by material science PhDs from EPFL. (École polytechnique fédérale de Lausanne.) The team started with a mission to create lightweight yet high performance skis. The
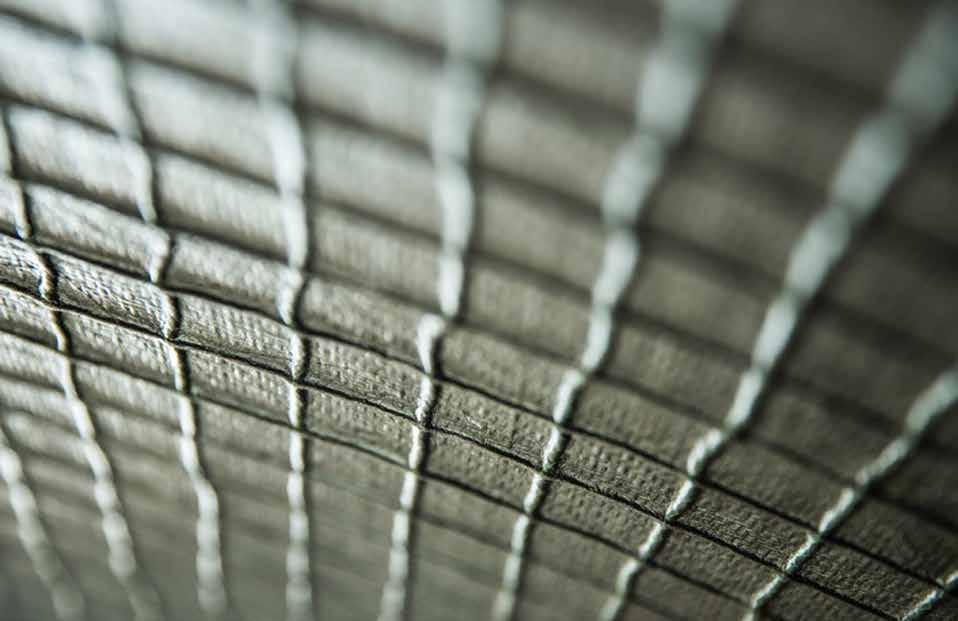
so-called bCores were launched and successfully adopted by some of the biggest names in freeride skiing. At the time, Bcomp used flax fibres to reinforce the balsa cores and improve shear stiffness. And still, Bcomp’s composites are based on natural fibres. Seveal years ago, Bcomp launced ampliTex, range consists of extremely lightweight, high performance natural fibre reinforcement fabrics. According to the company this type of composite offers improved safety with non-catastrophic crash behaviour, high vibration damping, specific bending stiffness and fatigue resistance and more.
The second stap was the development of the powerRibs technology, which matches the performance of carbon fibres for motorsport bodywork and other thin-walled shell elements. Inspired by the thin veins on the back of leaves, Bcomp’s proprietary powerRibs technology provides a three-dimensional grid structure on one side of the seat, which is then used to reinforce Bcomp’s optimally spun and woven flax fibre reinforcement fabric, ampliTex. Made by twisting flax fibres to form a thick yarn, the powerRibs act as a backbone to the ampliTex flax fabric that is bonded to it. According to Bcomp, PowerRibs add maximal stiffness at minimal weight by creating a 3D structure on one side of a thin walled shell element. This enables using less base material, decreasing weight, costs and consumables in production. The proprietary technology is perfect for high-performance appli-


Flax fiber composite details in the McLaren racing seat
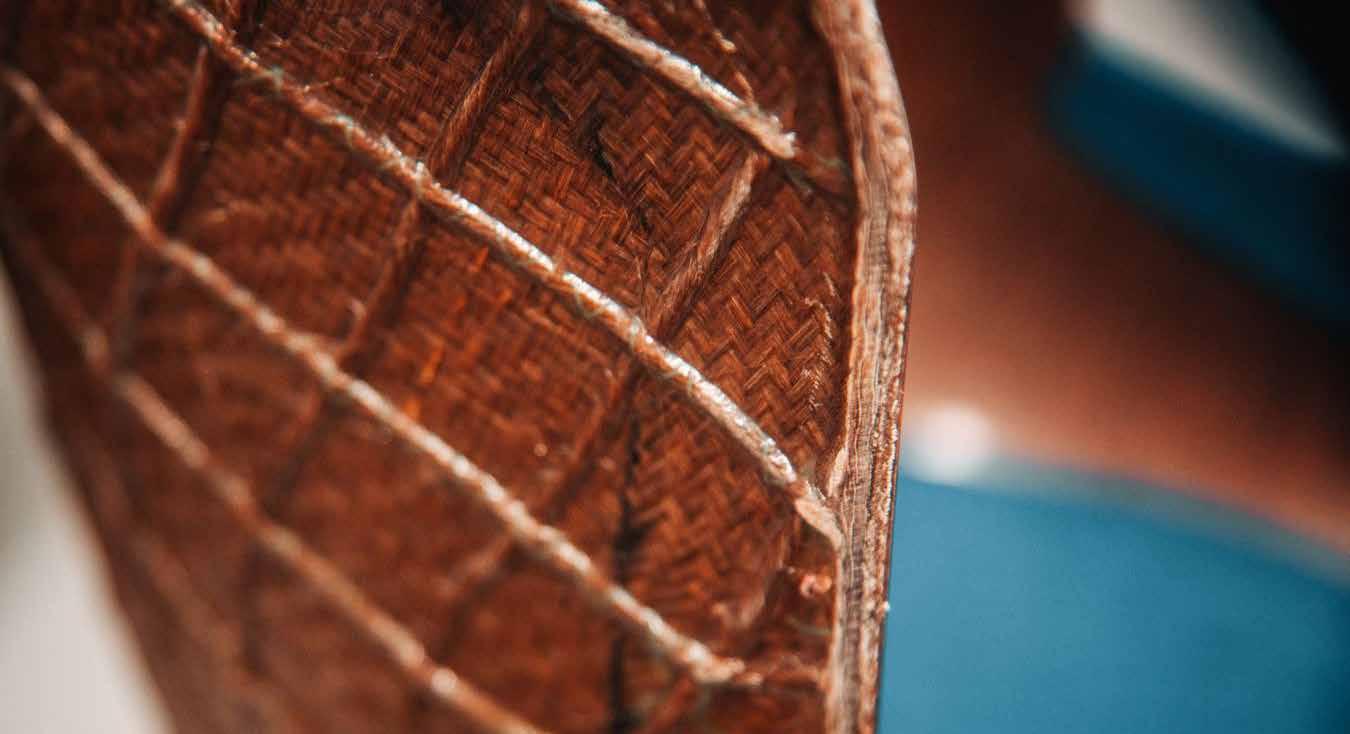
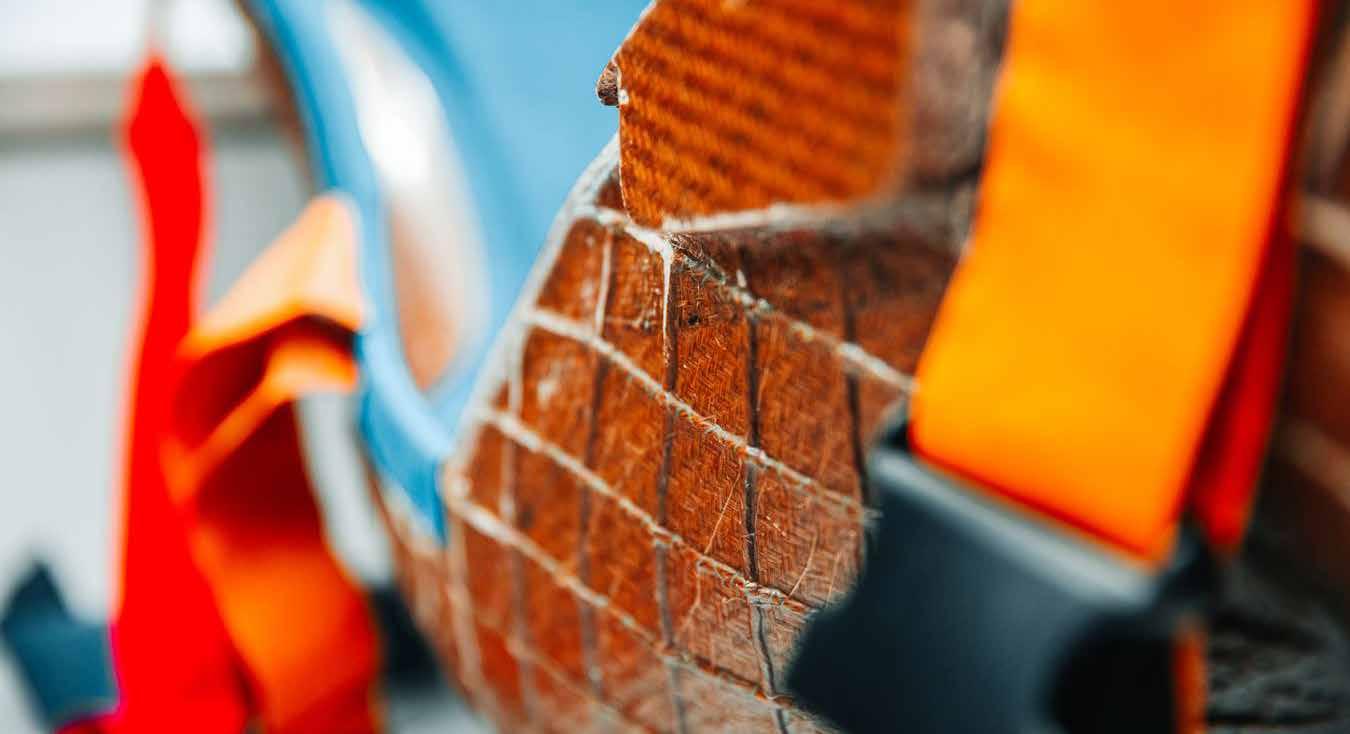
cations such as replacing or reinforcing carbon fibres in motorsport bodywork or decreasing weight in automotive interior panels.
Properties
While the mechanical properties of flax make it an attractive renewable raw material for high-performance composites, the tubular structure of flax fibres provides low density and high stiffness, which affords the opportunity to reduce weight while simultaneously improving vibration damping, as well as resistance to breakage, torsion and compression. Furthermore, it’s safe. According to Bcomp, it’s not prone to brittle fracture and splintering when it breaks, like cabon fibre does. This property is enhanced further by the structure of Bcomp’s powerRibs which stiffen and confine the damage zone. The composite of ampliTex and powerRibs is not as fragile, and while it still breaks, the softer debris remains attached to the main structure with the help of the powerRibs, which help dissipate the energy. The ductile fracture behaviour of natural fibre composites opens the door to other possibilities too. One of the most spectacular, but equally dangerous, aspects of an on-track incident are the
shards of carbon fibre that result from a collision. Not only do they present an immediate risk to the drivers, they are notorious for causing punctures and leaving a driver’s race in tatters. By using natural fibre composites in other areas of the car, such as front wing endplates and the floor, it’s possible to reduce carbon fibre debris and therefore the risk of punctures.
Reducing costs
Even, there’s more. With a budget cap set be introduced from 2021, many F1 teams will need to reduce costs while maintaining and improving performance - no mean feat in a sport where, typically, a team can pursue more development routes the more resource it has
Natural fibre reinforced satellite panel
Together with the European Space Agency (ESA), Bcomp
Ltd has developed the first natural fibre reinforced satellite panel. The project is the result of a close collaboration between Bcomp Ltd and experts from the European Space
Agency, RUAG Space and IRS Stuttgart, funded under the
ESA General Support Technology Program. The bio-composite satellite structure panel has been developed within the framework of ESA Clean Space Initiative. According to
Bcomp, it demonstrates the versatility of Bcomp’s proprietary powerRibsTM and ampliTexTM natural fibre technologies, even in the most extreme environments.
According to the ESA, bio-composites create new opportunities for ‘Design for Demise’ - the intentional design of the space system hardware, such that it will completely burn up upon re-entry at the end of its mission. This makes it safer for humans, ground infrastructure and the environment.
The bio-composite satellite panels meet the high requirements in terms of temperature resistance, strength, weight and vibration damping.
More at Bcomp>
available. Teams are going to have to work even smarter, and with Bcomp’s ampliTex and powerRibs solutions reducing raw material cost by up to 30 % compared to traditional carbon fibre, this significant saving can free up budget to explore other ways of improving car performance.
Expectations
According to McLaren, the natural fibre composite racing seat is just the beginning. This seat is the first step in the successful application of natural fibre composites in F1. By working with Bcomp, McLaren expects to identify other components that can be replaced

with a sustainable alternative that has equivalent weight and performance.
More at McLaren>
Bcomp>
Photography: McLaren/Bcomp
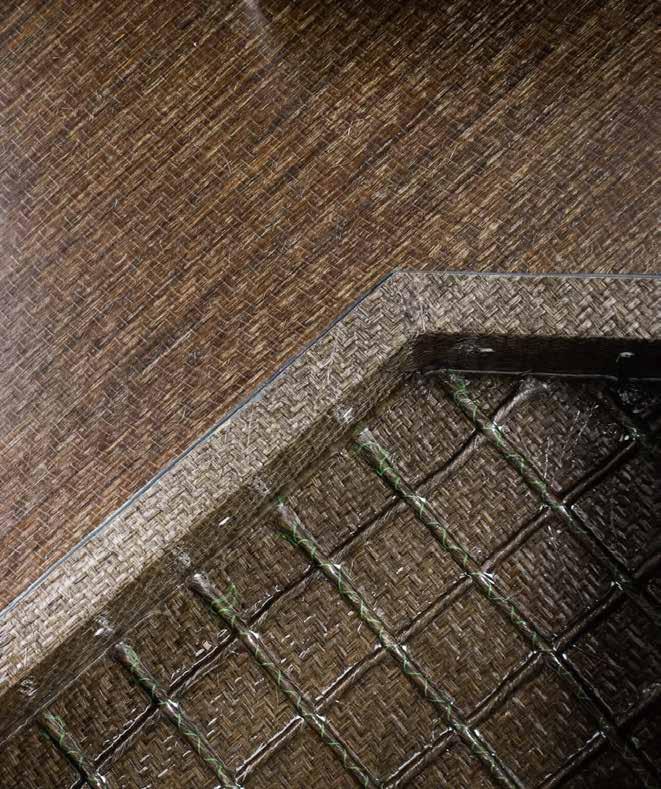