
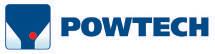
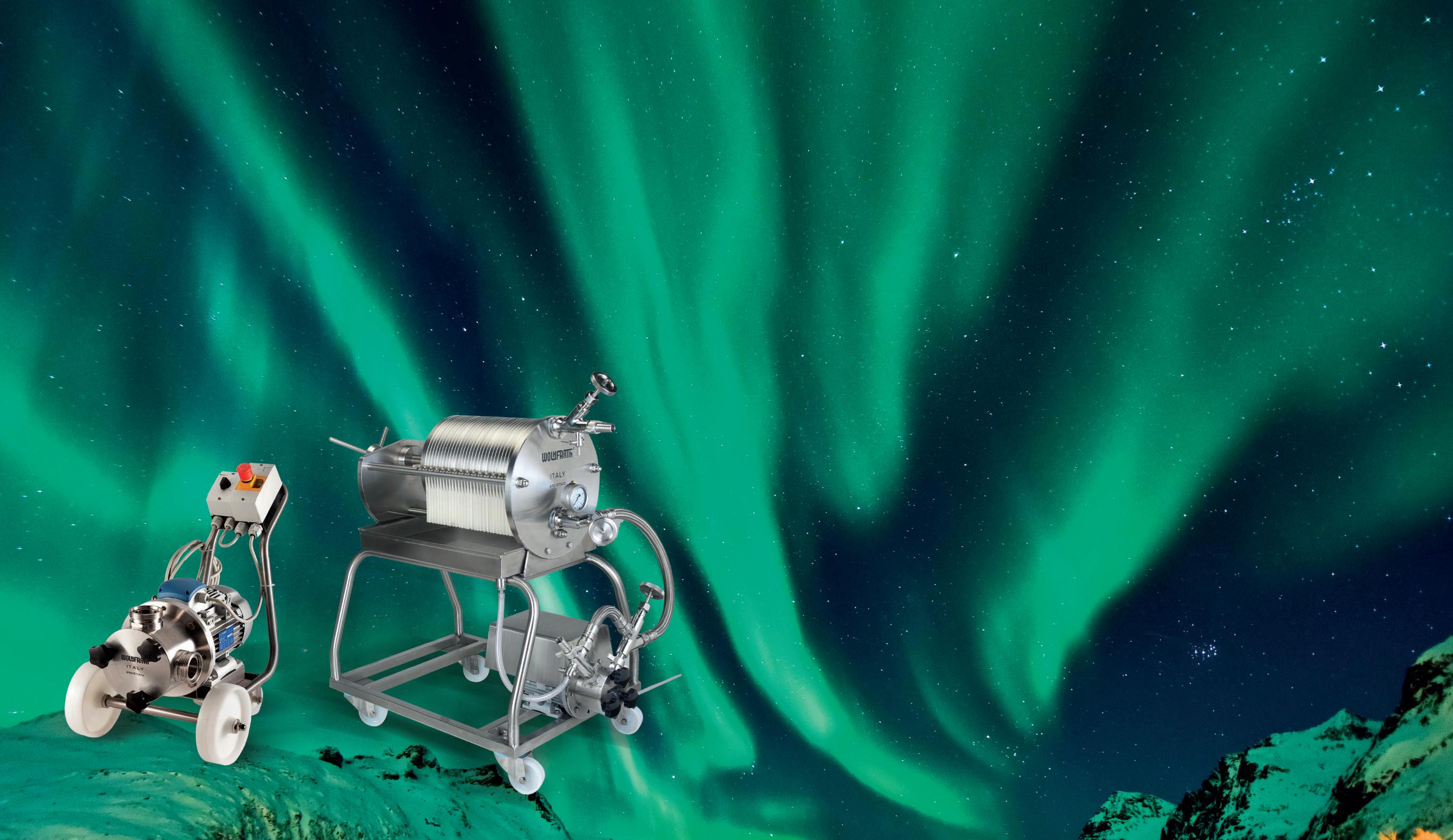
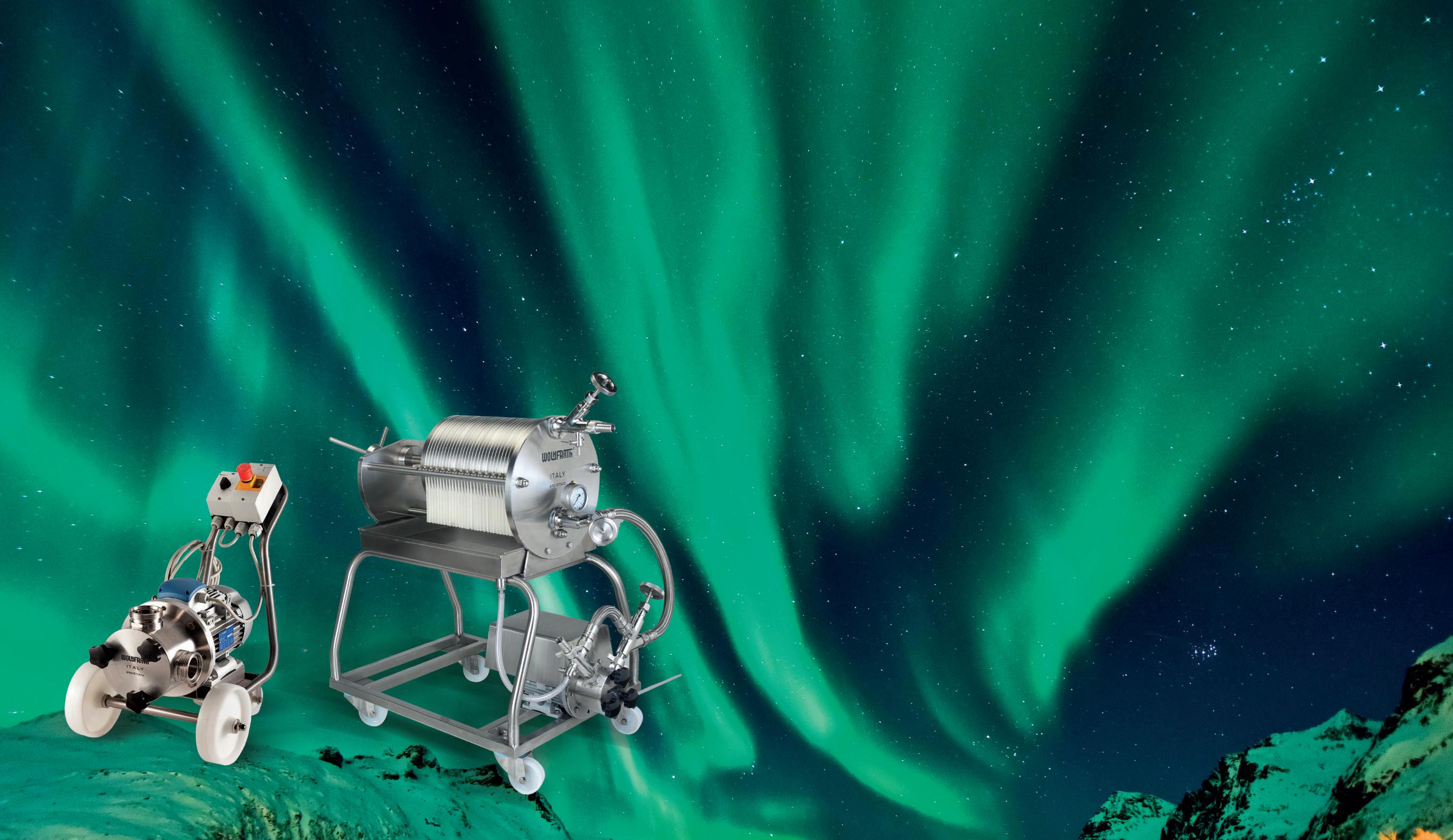
The environmental monitoring specialists, for your consumers’ safety
The environmental monitoring specialists, for your consumers’ safety
Achema Preview
Achema Preview
“The
The healthcare sector in the world will exceed 8 trillion euros in 2025, if the estimates of Pharmintech Monitor, the document issued on Pharmintech, the exhibition held in Milan last Spring, are confirmed. It is clear that the multiple and intertwined emergencies underway globally - from war to inflation, climate change and energy crisis - make any forecast uncertain. Yet in this gloomy context, pharma currently ap pears to have good stability and prospects for fur ther growth. Within the overall health sector, which is supposed to advance from now to 2025 with an average rate of 1.9% per year, the pharmaceutical industry stands out for its vitality, so much so that it grew by 7.9% in 2021 and justifies estimates for an increase of 3.9% per year over the next three years. These numbers are higher than those estimat ed before the advent of the pandemic. It is therefore fairly easy to deduce that the fight against coro navirus has played a decisive role in the evolution of this industry. Of the 1,113 billion euros that ex press the world value of the international pharma ceutical market in 2021, 78.3 billion are attributa ble to vaccines alone. However, other life sciences are also growing - nutraceuticals, cosmeceuticals, biotechs, biomedicals - niches destined to expand, with expected double-digit growth rates over the next three years. Back to the impact of Covid19, the Pharmintech Monitor highlights that, starting from 2020, not only has the demand for products linked to the production of vaccines increased, but also
that for therapies against the acute phase of the disease, as well as the treatments of Covid long-term symptoms. Research & development on therapeutic vaccines and experimental treatments has also been drastically intensified. But the whole supply chain, up to the pharmacy, was crossed by completely new dynamics that led operators to rapidly change to adapt to a scenario never seen before. This reactivity made it possible, after the initial loss, to quickly re-establish the continui ty of production and the capillarity of distribution: from the supply of active ingredients to the phar macist’s shelf close to home. On the other hand, especially in hospital pharmaceuticals, medicines for therapies considered “temporarily” less urgent have slowed down. The situation is expected to re turn to greater balance by 2023. The next few years will be featuring above all an exponential increase in demand from less advanced but faster-growing countries. The fastest-growing rates of the pharma ceutical industry between 2016 and 2025 are in Ni geria (+239.2%), Chile (+165.9%), India (+122.7%), Bangladesh (+121.5%) and Poland (+115%), com pared to a world average rate of +66% with Italian growth, in 10 years, accounted for + 28%. So phar ma is on the move all over the world, but in some countries the growth will be disruptive.
by Alessandro BignamiGaskets obtained from Texgraf® sheets in flexible expanded graphite, reinforced with stainless steel tanged foil, thickness 0.1 mm.
Ideal for use at high temperature and pressure, with thermo-mechanical shocks; in the presence of saturated and superheated steam and chemically aggressive fluids, with the exception of strongly oxidizing agents.
Efpia, the European federation of Pharmaceutical industries and Association complied a report about the Pharmaceu tical Industry in Figures 2022 that reveals a keystone of the Europe an economy at a pivotal moment in its history.
Nathalie Moll – who joined the Eu ropean Federation of Pharmaceu tical Industries and Associations (EFPIA) as Director general in April 2017 – argues that thank’s to this report is possible to get a sense of
just how pivotal the research-based industry is to Europe’s economic and health future.
Thanks to advances in science and technology, the research-based phar maceutical industry is entering an ex citing new era in medicines develop ment. Research methods are evolving and we have many promising pros pects on the horizon, with groundbreaking cell and gene therapies be ing increasingly available. The in novative pharmaceutical industry is driven by, and drives, medical pro
by Eva Degress. It aims to turn fundamental research into innovative treatments that are widely available and acces sible to patients.
Already, the industry has contribut ed to significant improvements in patient well-being. Today’s European citizens can expect to live up to 30 years longer than they did a century ago. Some major steps in biopharma ceutical research, complimented by many smaller steps, have allowed for reductions in mortality, for instance from HIV/AIDS-related causes and
In 2021 year the world come through a Global Financial Crisis and a huge pandemic but EFPIA companies have more than doubled production, increased exports and build up a pharmaceutical industry which is vital to Europe’s economy.
Vecchis
several cancers. High blood pressure and cardiovascular diseases can be controlled with antihypertensive and cholesterol-lowering medicines; knee or hip replacements prevent patients from immobility; and some cancers can be controlled – or even cured –with the help of new targeted treat ments. European citizens can expect not only to live longer, but to live better quality lives. Yet major hurdles remain, including Alzheimer’s, Multi ple Sclerosis, many cancers, and ra re diseases.
As well as driving medical progress by researching, developing and bringing new medicines that improve health and quality of life for patients around the world, the research-based phar maceutical industry is a key asset of the European economy.
The research-based pharmaceutical industry can play a critical role in re storing Europe to growth and ensur ing future competitiveness in an ad vancing global economy. In 2021 it invested an estimated 41,500 million in R&D in Europe. It directly employs some 840,000 people and generates about three times more employment indirectly – upstream and downstream – than it does directly (PwC, Econom ic and societal footprint of the phar maceutical industry in Europe, June 2019). However, the sector faces re al challenges. Besides the addition al regulatory hurdles and escalating R&D costs, the sector has been severe ly hit by the impact of fiscal austerity measures introduced by governments across much of Europe since 2010. There is rapid growth in the market and research environment in emerg ing economies such as Brazil, China and India, leading to a gradual migra tion of economic and research activi ties from Europe to these fast-grow ing markets.
During the period 2016-2021 the Brazilian, Chinese and Indian mar kets grew by 11.7%, 6.7% and 11.8% respectively compared to an average market growth of 5.8% for the top 5 European Union markets and 5.6% for the US market (source: IQVIA MIDAS, May 2022).
In 2021 North America account ed for 49.1% of world pharmaceutical sales compared with 23.4% for Europe. According to IQVIA (MIDAS May 2022), 64.4% of sales of new medicines launched during the peri od 2016-2021 were on the US market, compared with 16.8% on the Eu- ro pean market (top 5 markets).
All new medicines introduced into the market are the result of lengthy, costly and risky research and devel opment (R&D) conducted by pharma ceutical companies.
By the time a medicinal product reach es the market, an average of 12-13 years will have elapsed since the first synthesis of the new active substance.
The cost of researching and develop ing a new chemical or biological en tity was estimated at 1,926 million ($ 2,558 million in year 2013 dol lars) in 2014 (DiMasi et al, Journal of Health Economics, January 2016). On average, only one to two of every 10,000 substances synthesised in laboratories will successfully pass all stages of development required to become a marketable medicine. In 2020 the pharmaceutical industry invested more than € 39,600 million in R&D in Europe. A decade of strong US market dominance led to a signif icant shift of economic and research activity towards the US during the period 1995-2005, a trend that has been exacerbating since 2015. Ad ditionally, Europe is now facing in creasing competition from emerg ing economies: rapid growth in the market and research environments in countries such as China and Ko rea are contributing to the move of economic and research activities to non-European markets. In 2021 Chi na nearly equalled Europe as orig
(e): EFPIA estimate
inator of new active substances launched for the first time on the world market, with respectively 18 and 19 new substances, far behind the US leading with 35 on a total of 95. The geographical balance of the pharmaceutical market – and ulti mately the R&D base – is likely to shift gradually towards fast-growing emerging economies.
According to Eurostat data, the phar maceutical industry is the high tech nology sector with the highest add ed value per person employed, signif icantly higher than the average value for high-tech and manufacturing in dustries. The pharmaceutical indus try is also the sector with the highest ratio of R&D investment to net sales. According to the 2021 EU Industrial R&D Investment Scoreboard, health industries invested about 188.7 bil lion in R&D in 2020, accounting for 20.8% of total business R&D expend iture worldwide.
Recent studies in some countries showed that the research-based phar maceutical industry generates about three times more employment indi rectly – upstream and downstream
– than it does directly (PwC, Eco nomic and societal footprint of the pharmaceutical industry in Europe, June 2019). Furthermore, a signifi cant proportion of these are valua ble skilled jobs, for instance in the fields of academia or clinical science, which can help maintain a high-lev el knowledge base and prevent a Eu ropean “brain drain”.
“Take the number of people em ployed in our sector: among all the data packed in this report, this is one of the numbers that translates most readily to people”, comments Nath alie Moll. “Of course, the 840,000 individuals directly employed in Eu rope’s pharmaceutical sector is not the whole picture.
There is a significant multiplier ef fect which includes all those peo ple, companies and partners provid ing services to the industry whose jobs we rely on; from plumbers to academics, CROs and SMEs, caterers to logisticians”.
The world pharmaceutical (prescrip tion) market was worth an estimat ed 1,062,707 million ($ 1,256,863 million) at ex-factory prices in 2021. The North American market (USA &
Canada) remained the world’s larg est market with a 49.1% share, well ahead of Europe, China and Japan. Distribution margins, which are gen erally fixed by governments, and VAT rates differ significantly from coun try to country in Europe. On average, approximately one third of the retail price of a medicine reverts to distrib utors (pharmacists and wholesalers) and the State.
All this informations contained in the 2022 report, can be a good start ing point to figure out how pharma can contribute both to health and wealth in a key moment for policy development on the continent.
“We must take a long-term stra tegic view of where we are as a re gion and where we are goin”, says Nathalie Moll. “Company leaders and life-science investors, who can invest in any industry in any country or re gion, need to have confidence in the long-term outlook: in the innovation ecosystem, in access to talent, in the market. Despite the clear and posi tive contribution of the pharmaceuti cal industry to Europe’s economy, we are facing a number of challenges. Es calating costs and regulatory hurdles are making R&D more difficult, while the impact of fiscal austerity meas ures introduced across Europe since 2010 continue to affect today’s rev enues and influence key decisions on bringing innovation to market. At the same time, we have seen the growth of Brazilian, Chinese and Indian mar kets outstrip growth in the top 5 Euro pean markets. Our global competitors have prioritised life sciences and we must respond with similar ambition.”
“That’s where Europe’s pharmaceutical and industrial strategies come in. It is vital that Europe rises to the challenge and develops the policies needed to ensure the European phar maceutical sector is an innovator and world leader”. l
The OQEMA Group is an internationally active distribution company for the chemical basic and speciality chemicals based in Germany since 1922. We are a family business by tradition and by conviction. Always reliable. Always responsive. Always present.
OQEMA in Italy is based in Assago (MI) and Rivanazzano Terme (PV), also known as Elettrochimica Valle Staffora. We continue to be a distribution and marketing of chemical products with a strong imprint of reliability, attention to safety, quality and sustainability.
Born in 2013 as part of CSV Life Sci ence Group, CSV Active comes as a reli able and skillful partner in the research and marketing of Fine Chemicals In termediate, API sourcing and services for the pharma-chemical market. The staff’s many years experience enables to rely upon a network of highly qualified providers mainly coming from the Far East, who are capable of complying with any technical and regulatory re quirements. To date, CSV Active main ly works in Europe, especially on the Italian market. Initially established as trading company, for the purpose of identifying at first intermediate pro viders and later on Active Pharmaceu tical Ingredients and to deal with their marketing, over the last few years, CSV Active has reorganized to rapidly meet market changing requirements.
Following the new European regu lations also implemented in Italy in 2014, AIFA issued a legislative decree that made the importation of drugs or active ingredients a production activ ity. Thus the company has therefore organized itself in a more structured way, by introducing a new office – the Quality Unit – and adopting a system complying with GMP.
In 2019 AIFA, following an inspec tion, authorised CSV Active as Phar maceutical Workshop, also approv ing the 5 products presently availa ble in the catalogue: omega 3, thi opronine, azithromycin, fluconazole and camphor. Always focusing on customer care quality and relying up on the Group, CSV Active has reached an agreement with an external ware house, also authorized by AIFA, for
the storage of products, managing to guarantee end customers suitable storage and maintenance of the re quired temperature conditions. Bene fits for customers are more than these. In fact, there are many services that Active is able to offer: from suppli er qualification audits, which ensure the suitability of the active ingredi ents, to constant staff training, which makes our staff always oriented to wards the management of quality is sues. Suppliers themselves, by choos ing CSV Active, know they can rely not only on a business partner who car ries out inspections and defines the regulatory aspects for authorization, but also on a company responsible for maintaining their qualification status and always updated on Italian and Eu ropean regulations.
GSK PLC announced the first recipient of the Target the Future Think Tank Challenge £70,000 (equivalent to approximately $100,000) grant to the HealthTree Foundation, a non-profit organisation help ing patients learn more about their health and become their own best advocates. Their proposal, the “HealthTree Equity and Diver sity for Multiple Myeloma Program,” will improve access, education and support for underserved communities and minority patients. Tania Small, Vice President, Global Head of Oncology Medical Affairs and Head of R&D Diversity, Equity and Inclusion at GSK, said: “The response to this challenge showcased an abundance of innovation, creativity and ingenuity, which we need to address patients’ unmet needs. We see great potential in the HealthTree Foundation’s pro posal, which goes beyond the science to improve access, equita ble care and quality of life for the multiple myeloma community.” GSK’s grant will help support the HealthTree Foundation as it devel ops digital delivery tools to distribute information on treatments and trials, facilitate digital communities and expand outreach ef forts to support, educate and provide more equitable care to mul tiple myeloma patients.
Jenny Ahlstrom, Founder and CEO of the HealthTree Founda tion, said: “I am alive today because I had the right information and treatments, and we must extend that access to communities of colour. GSK saw problems and created a programme to target a better future.”
Specifically, the Target the Future grant from GSK will aid in the expansion of two of the following initiatives at the HealthTree Foundation:
- “Black Myeloma Health”: Outreach from the HealthTree Foundation will expand to spotlight Black patients with multiple myeloma and their experiences through video journaling and distribution of new educational brochures with information about relevant treatments and resources.
- “HealthTree for Mieloma Multiple”: The organisation’s efforts to support multiple myeloma patients will increase through de ployment of Spanish-speaking patient navigators who will help people get answers along their treatment journey in their na tive language.
A research and innovation infrastructure for the development of Digital Healthcare, Biopharma, Artificial Intelligence, and Big Data will be created with the contribution of Next Generation EU.
The University of Brescia has signed an agreement with Antar es Vision Group, an Italian prod uct and chain quality traceabili ty and control multinational, and with Dompè Farmaceutici Spa, a leading Italian company in the bio-pharmaceutical sector, for the development of an integrated system of infrastructures that will expand by approximately 2,000 sq.m. the Technological Multisec tor Service Centre in the building owned by the University inside the North university campus. The project, the result of a pub lic and private partnership which has collected EUR 19.5 million in funds, known as L.I.G.H.T. Lifes cience Innovation Good Health care Technology – will develop healthcare technologies pursuing three important goals:
• AI and Big Data Main Hub: largescale analysis, storage, and con struction of platforms for sharing the data collected, creation and update of websites.
• Digital Health Care Hub: devel opment of a smart hospital with geo-referenced rooms and beds equipped with sensors and com munication systems for continu ous monitoring, development of telemedicine digital technologies, and for improved remote control of the patient, creation of drug tracking solutions that aim to protect the quality and integrity of the medicinal products them
selves and reduce administration errors or counterfeiting.
• AI Biopharma Hub: develop ment of a fully integrated struc ture based on artificial intelli gence that can design, synthe sise, and define the activity of new drugs and bio-pharmaceuti cals, in collaboration with the EX
principles.
It aims to reach goal no.9 “In dustry, innovation and infrastruc ture” as its purpose is to design an infrastructure where public and private entities exchange ideas and experiences for a new open innovation system, with three targets: a) increasing the con tact and meeting points between basic research and industrial re search to create new solutions for health and well-being; b) set up new innovative undertakings; c) revise the curricula for the train
“Technological Innovation In frastructures - adds Prof. Mari na Pizzi, Vice Chancellor for re search represent vital initiatives for Italian research that must prove that they are able to integrate to an increasing degree in the years to come, following the PNRR (Italy’s recovery and resil ience plan), with significant ef fects for the entire national re search system and its technologi cal transfer into products that cit izens can use”.
The L.I.G.H.T. infrastructural pro ject is consistent with the 17 Sus tainable Development Goals of the 2030 Agenda signed by the mem bers of the UN and focuses on the Green New Deal.
It is in line with goal no.3 “Good health and well-being” as it aims to develop new techno logical solutions for healthy and ill patients, and to design a smart hospital prototype. It complies with the principles of goal no.5 “Gender equality” as all governing bodies of the infra structure will be designed in con formity with the gender equality
ing of new professional figures in the medical field and in the field of new technologies for health.
A strong partnership between public and private entities “The main goal of the initiative is to strengthen the collaboration between the University of Bres cia and private companies aiming at a more in-depth integration of basic research skills with skills in industrial and experimental research”, states the Chancellor, Prof. Maurizio Tira. “Moreover, the project will have a significant impact on knowledge that can be applied to the digital transition of healthcare providers”.
”We are proud to partner with the University of Brescia in this pro ject that, thanks to its concrete ness, we believe can trigger a vir tuous circle of contacts and part nerships among various entities in our country. In the words of Emidio Zorzella, Chairman and CoCEO of Antares Vision Group, “We have always believed in research, in innovation, and in a multidis ciplinary approach as a driver for growth, transformation, and sus tainability”.
”The collaboration between pub lic and private entities and open innovation have, for some time, been one of the driving forces of the research carried out by Dompé farmaceutici” commented Marcel lo Allegretti, Chief Scientifc Of ficer of the Milan-based compa ny. “I believe that our EXSCALATE platform, which is based on arti ficial intelligence and supercom puting, can make a significant contribution towards the success of the initiative, producing new knowledge, accelerating drug dis covery times, and consolidating the scientific network with new partners”.
Catalysts used, consist of precious or noble metals.
The high efficiency of our filtration systems, guarantees: • Fast pay-back
Catalysts used, consist of precious or noble metals. The high efficiency of our filtration systems, guarantees: • Fast pay back
• Environmental safety
• Low operational cost
• Environmental safety • Low operational cost • Highflexibility
Catalysts used, consist of precious or noble metals. The high efficiency of our filtration systems, guarantees: • Fast pay back • Environmental safety • Low operational cost • Highflexibility
TheMott laboratoryallowsyou to carry out filtration tests to optimizetheselectionoffilter media thanks to thehigh tech equipment available
TheMott laboratoryallowsyou to carry out filtration tests to optimizetheselectionoffilter media thanks to thehigh tech equipment available
TheMott laboratoryallowsyou to carry out filtration tests to optimizetheselectionoffilter media thanks to thehigh tech equipment available
Installation support Post installation support
Useoneof ourpilot plants to test onfieldthefiltrationefficiency and ability of oursystems
commissioning
ASCO Filtri S.p.A. - This and much more H.Q.
H.Q.
Asco FiltriS.p.A.
Asco Filtri S.p.A. Viale delle Scienze, 8 20082 Binasco (MI) Italy info@ascofiltri.com
Viale delle Scienze, 8 20082 Binasco (MI) Italy info@ascofiltri.com
Asco FiltriS.p.A.
Viale delle Scienze, 8 20082 Binasco (MI) Italy info@ascofiltri.com
On 9 June, ISPE President and CEO Thomas Hartman, and ISPE Foundation Board Chair Antonio Moreira, PhD, visited Gilead’s headquarters in Foster City, California to present Joydeep Gan guly, Senior Vice President, Corporate Operations, with a rec ognition award for his support in developing a critical and diverse pool of talent necessary for accelerating the delivery of transformational medicines to patients worldwide. They were thrilled to also meet with Abbey Kim who was part of the inaugural ISPE Foundation Diversity Internship Program
at Gilead Sciences in 2021, where she now works as an auto mation engineer.
Thomas was invited back to join in on the celebration of Gile ad’s 35th anniversary on 22 June, which also marked the open ing of both the Gilead Sciences Park and their Wellbeing Center. The ISPE Foundation said it is proud to partner with companies such as Gilead Sciences, and leaders like Joydeep, to champion programs that create opportunity, diversity, and success with in the global pharmaceutical industry.
Chiesi Farmaceutici Spa (Chiesi Group), the international research-fo cused pharmaceutical and healthcare group, entered into an agreement with Allinaire Therapeutic, LLC, a company founded by BioMotiv, to ac quire the world-wide rights to a portfolio of therapeutic monoclonal an tibodies (mAbs) against endothelial monocyte-activating polypeptide II (EMAP II) for the potential treatment of PAH.
EMAP II is a non-classical cytokine which impacts apoptosis, cell inju ry, endothelial cell function and inflammation. Based on the pioneering work by the scientific founders, Matthias Clauss, PhD and Irina Petra che, MD, and their colleagues at Indiana University and National Jew ish Health, Allinaire and their network of preclinical and clinical scien tists, have demonstrated a pivotal pathogenic role of EMAP II in car diopulmonary diseases, including PAH, chronic obstructive pulmonary disease (COPD), and viral-induced acute lung injury. They developed an ti-EMAP II mAbs which are currently being progressed in early phases, as a potential disease-modifying treatment for PAH and are the sub ject of this partnership.
PAH is a rare disease with an incidence of 2–5 per million adults.. PAH is a progressive disorder characterised by high blood pressure in the arter ies of the lungs that can lead to right heart failure. Current approved med ications mainly address the symp toms of this rare condition and there is an unmet medical need for novel approaches that could delay, or re verse, the disease progression. “This agreement is further evidence of Chiesi’s commitment to seek out novel treatments for conditions with a high unmet medical need such as
PAH” commented Thomas Eichholtz, Head of Global R&D of Chiesi Group. “We believe that an anti-EMAP II mAb is a promising novel approach for the treatment and slowing of disease progression for patients with PAH. The partnership with Allinaire is further evidence of Chiesi’s fo cus on innovation and desire to accelerate our entry into biologics and thus diversify our therapeutic platforms”.
According to Douglas W.P. Hay, CEO and CSO of Allinaire, “We have made excellent progress in our anti-EMAP II mAb program at Allinaire, work ing with a multi-disciplinary team of experts in EMAP II science, bio logics, and cardiopulmonary disease therapeutics. We are extremely ex cited to be partnering with Chiesi, a world-class global pharmaceutical company with a long-standing and successful track-record in this ther apeutic area, to advance this novel class of medicines”. Allinaire will receive an upfront payment, future milestone payments and net sales royalties.
The agreement with Allinaire follows Chiesi’s recent €85m investment to build the Biotech Center of Excellence Plant in Parma (Italy), ded icated to the development, production, and distribution of biological products. In recent years the group has also undertaken a series of new strategic partnerships with external partners, including Moderna and Cy clica, to strengthen their work in bi otechnology.
The development of biological products has continued to increase over the last 10 years. On the glob al market, the sector has grown at an annual rate of more than 12% in the last 30 years and will dou ble by 2030.
Stevanato Group S.p.A., a leading global provider of drug contain ment, drug delivery, and diagnostic solutions to the pharmaceu tical, biotechnology, and life sciences industries, announced the publication of its Sustainability Report 2021. The report showcas es the Group’s holistic approach to sustainable development and highlighted strong guidance aimed at pursuing goals pertaining to economic sustainability, its responsibility to innovation and new products, employees, and the environment.
This is the first year that Stevanato Group publishes a report on its approach to sustainability, comparing its performance to the Global Reporting Initiative (GRI) Standards. The Company is striving to provide comprehensive and transparent information to demonstrate its unwavering commitment to sustainability. The report covers Stevanato Group’s rapid response to the COV ID-19 outbreak, as the Company increased production capacity to support its customers’ efforts to combat the global crisis. As part of this effort, Stevanato Group provided glass vials and syring es to approximately 90% of existing vaccine programs, accord ing to estimates based on public information (WHO, EMA, FDA); as well as plastic diagnostic consumables for the detection and diagnosis of COVID-19.
“As we approach one year since the Company’s IPO on the New York Stock Exchange, we are united in our commitment to support ing our customers on the single-minded goal of enhancing the in tegrity of medicines to help people live a better life,” said Franco Moro, Chief Executive Officer of Stevanato Group. “To do this, we have collaborated with our partners and the scientific community, and invested in R&D, to make greater strides toward better eco nomic, environmental, and social sustainability – for our Company, customers, and the communities we live in.”
In 2021, Stevanato Group focused on areas that were of high materiality for the Company as well as key stakeholders. In line with its business strategy, primary attention was given to two main areas: product quality and responsibility, and research & development and innovation. Other focus areas were closely as sociated with human resources, such as occupational health & safety and human capital management and development, high lighting the importance of Stevanato Group’s policies toward people. The report also illustrates the positive results and dif ferent actions taken to improve sustainability towards the en vironment, reducing water consumption and waste in Stevana to Group’s productions.
27.9 -29.9.2022
Venite a scoprire l‘ingegneria dei processi meccanici in tutta la sua ampiezza e dinamicità alla più grande fiera internazionale dei beni strumentali. Toccate con mano gli oggetti in esposizione. Cogliete questa occasione di approfondimento professionale e di scambio tra esperti.
Novità di quest’anno:
L‘industria di processo incontra l‘industria dell‘imballaggio. Aspettatevi l‘intera catena del valore, dalla produzione al confezionamento dei prodotti.
Una combinazione di proposte pronta a convincervi! powtech.de/become-visitor
Sponsor onorari
Parallelamente a FACHPACK – La fiera europea del settore dell‘imballaggio, della tecnologia e della lavorazione
La fiera leader per il trattamento e l‘analisi delle polveri e dei solidi sfusi
Agrowing bio-based chemi cal industry is critical to the transition towards a carbon neutral and circular bioeco nomy to extend the lifecycle of products, minimize waste, efficiently use renewable raw materials and devel op bio-based products (BBPs).
“We started in 2005 with the bioeco nomy and now we have 30-35 coun tries, including China as of May 2022, and maybe the same number of re gions with bio-strategies,” says Christian Patermann, co-founder and hon orary chair of the World Bioeconomy Forum’s advisory board. “But what is missing is the breakthrough in the minds of decision-makers and the pop ulation at large. I don’t expect that very
soon. The bioeconomy works very slow ly, but steadily.”
The European Commission defines the bioeconomy as “using renewable bio logical resources from land and sea like crops, forests, fish, animals and mi cro-organisms to produce food, mate rials and energy.” The circular bioeco nomy involves extending the lifecycle of such products by recycling or reus ing them.
Patermann, points to the potential of bio-based rhamnolipids for detergents; HFDA for nylon, coatings and adhe sives; aniline for aromatics; and poly ethelene glycol for additives and sur factants found in many chemical plat forms today. “These products directly and indirectly reduce fossil carbon us
age all over the world,” he says.
According to Cefic’s position paper, biobased products are still a small part (2.5%) of the overall European bioeco nomy, which has a turnover of approx imately €2.4 trillion. About 50% of this is generated by food and beverages, around 25% from agriculture and for estry, and the remaining 25% in the pharmaceutical, pulp and paper, tex tile, fuels and energy sectors.
For Patermann, the pursuit of circularity needs to go hand-in-hand with the de velopment of the bioeconomy. For ex ample, the toxicity of substances, such as some textile dyes, is not reduced or
Christian Patermann, co-founder of WorldBioeconomy
Forum outlines how to make broader use of renewable biological resources: “The bio-based sector works very slowly, but steadily”.Photo by Croda Christian Patermann, co-founder and honorary chair of the World Bioeconomy Forum’s advisory board
eliminated by recycling or biodegrada bility. Plus, a lot of recycling processes need enormously large volumes of wa ter and energy. In order to reduce the toxicity of chemicals and make natural resources for recycling climate-friend ly, microorganisms, enzymes and oth er biological resources can be utilised. “The innovation element, which in volves biological resources, can never be replaced by circularity,” Patermann says. “It’s something in addition. For that reason, we need both. They might not be integrated, but they should be linked together.”
To this end, Europe is striving for a circular, sustainable bioeconomy and eventually, a bio-based circular econ omy as well, he adds. “Bio-based cir cularity is very evident in quite a few products and processes of the chemi cal industry.”
The use of non-food crops and secondand third-generation feedstocks (bio waste and residues) is particularly im portant given the disruptions to glob al food, feed and fuel supplies with the war in Ukraine, notes Patermann. He predicts the food versus fuel debate will end as the bioeconomy focuses on ma terials that are not in direct competi tion with food and feed. “The next five years will be very decisive.”
Are there enough non-food feedstocks to go around? “If we really exploit the enormous
amount of waste, in particular urban waste – which has been completely ne glected up to now – we have a tremen dous canopy of opportunities,” Pater mann states. “And that’s just the be ginning… The volume of urban waste cannot be compared to anything you have in a rural area.”
There is also an opportunity for the “repatriation of value chains and supply chains,” Patermann says. For ex ample, northern Germany is cultivat ing Russian dandelion to supplant rub ber trees from Southeast Asia in areas where food crops cannot grow to sup ply the automotive industry with a re newable source for tires.
Biological resources cannot yet replace all raw materials, but they might one day, Patermann adds, noting the po tential of enzymes, fungi and other mi croorganisms in the chemical industry. He estimates that more than half of the chemicals in raw materials still need to be discovered in order to find bio-re placements.
Engaging the private sector in the bioeconomy
How can the private sector be incen tivised to invest and innovate in the bioeconomy? “The best incentive is a successful showroom of innovative, af fordable products to show the value of using waste and biomass to create new products,” Patermann responds.
“We will need, at least for certain peri
od of transition, some public help like the U.S. BioPreferred Program,” which facilitates public procurement of biobased products. It’s also important to level the playing field for all stakehold ers and offer equal access to new mar kets, he adds. The bioeconomy should first be in troduced in school, then continue at the university level with green chem istry curricula, Patermann says. Master courses in green chemistry are already available in Austria, Finland, France, Latvia and Switzerland. The chemical industry can also collaborate with uni versities and offer its personnel lifelong learning. For example, Cefic or ganises green chemistry boot camps. Processes involving bio-based feed stocks play an increasingly important role in the bioeconomy. For example, an enzymatic process for the interest erification (rearrangement of fatty ac ids) of oils and fats avoids production of harmful trans fatty acids. In addi tion to eliminating these artery-clog ging substances, the process reduces the use of toxic chemicals and water, prevents vast amounts of by-products and reduces waste.
“The chemical industry is one of the last industrial branches in Europe that still has a strong lead globally,” Pater mann concludes. “With its influence today, it should work much harder to build up sustainable future developments through education, training and funding for green chemistry. That would be very good for Europe and the plan et. The chemical industry has the pow er to do that.”
l (Source: Cefic)
“The chemical industry should work much harder to build up sustainable future developments through education, training and funding for green chemistry. It has the power to do that”
The mix of numerous innova tions and expert-to-expert dialogue makes Powtech the networking and knowledge platform for process techni cians and engineers. Decision-mak ers and buyers will find competent advice here for their investment decisions. From 27 to 29 September 2022, trade visitors will experience the latest equipment and systems for mechanical processes for the processing, analysis and handling of powder, granulate and bulk solids
in four halls, including the state-ofthe-art Hall 3A. This year’s trade fair duo, Powtech and Fachpack, expects over 1,600 exhibitors from Europearound 500 of whom will be exhib iting at Powtech in the field of me chanical processing technology and analysis. Both trade fairs bring together the entire value chain from process to technology to packaging. The respective ticket is valid for both trade fairs.
Powtech brings together the global innovations for mechanical process
ing technology as well as for the anal ysis and handling of powders, granu lates and bulk solids. Plant planners and operators from almost all indus tries, including food and feed, chem icals and pharmaceuticals, construc tion, recycling and ceramics, come together to update their knowledge, examine state-of-the-art process technology and prepare and make investment decisions. Trade visitors experience three days of high-quali ty technology live in action, inspira tion and exchange at eye level, and a varied supporting programme.
“Powtech has always been the exhibition where process engineers and production managers from every in dustry have found very concrete solu tions to their requirements and also their problems,” says Heike Slotta, Executive Director NürnbergMesse.
At Powtech 2022, trade visitors will experience the latest equipment and systems for mechanical processes for the processing, analysis and handling of powder, granulate and bulk solids
“When networking on the stands, but also through the specialist forums, where presentations on current is sues in the industry take place on an ongoing basis and leading man ufacturers and users share compact best practices.”
This year, visitors to Europe’s lead ing trade fair exclusively for powder, granulate and bulk solids technol ogies will also benefit from syner gies created with the simultaneous staging of Fachpack, trade fair for packaging, technology and process ing. With one trade fair ticket, visi tors gain access to both events and the expected more than 1,600 ex hibitors.
Shaping the future together Whether mixing, crushing, agglom erating or separating material that has a powdery or lumpy aggregate state in the course of the manufac turing process - the systems and machines are decisive for the pro duction processes of many indus tries. In dialogue with visitors and exhibitors, future topics of modern production will be discussed in the open atmosphere of Powtech in four halls, including important sustaina bility topics such as resource effi ciency, recycling or CO2-neutral pro duction, but also topics relating to the working world of tomorrow and attracting skilled workers and talent.
In lectures, seminars, live demon strations, guided tours and special shows, powder and bulk solids pro fessionals from every sector will re ceive useful practical knowledge from top-class speakers. Bulk solids practitioners meet in the Expert Fo rum “stagetalks”. Here, for example, the focus will be on innovative pro cesses for modern battery and energy storage production. In the food sec tor, one topic will be protein shifting in the drying of vegetable protein sources. For users from the pharma ceutical industry, the Pharma.Manu facturing.Excellence forum will offer inspiration on the subjects of phar maceutical processing and pharma ceutical packaging.
The special show “Dust recognises boundaries – free trade doesn’t” by the VDMA Group Air Purification and Drying Technology shows how the air in production facilities can be kept clean. The topic of explosion protec tion will not be neglected either. In the outdoor area of Powtech there will be daily controlled live demon strations on explosion protectionincluding spectacular bang and fire effects. At the joint stand “Inno vation made in Germany”, nation al start-ups and young companies will show interesting innovations in the industry.
Longstanding exhibitors need no persuading
One thing is certain: trade fairs like Powtech will continue to be a key tool for business success in the fu ture. This view is also shared by long standing Powtech exhibitors who can hardly wait for the fair to take place in 2022. They include Rain er Zimmermann, CEO of AZO GmbH & Co. KG, one of the world’s most experienced companies in the au tomated handling of raw materials, who says: “Two years of pandemic and enforced breaks have shown us that there is no substitute for per sonal contact in the trade fair en vironment. We are therefore even more delighted that Powtech, the leading fair for bulk solids and pow der technology, can also take place again this year. Barely any other event offers AZO such a good op portunity to present our expertise in the automated handling of raw materials. And this year, the par allel Fachpack show offers visitors yet another opportunity for person al exchanges about our AZO prod ucts and solutions.”
Gerold Rogge, Regional Sales Man ager/Key Accounts of Coperion K-Tron GmbH, a globally operating supplier of process equipment, is full of praise for the leading trade fair for mechanical processing tech nology: “Without a lot of ‘bells and whistles’, visitors have direct ac cess to the ‘who’s who’ of bulk sol ids technology. They can discuss up coming projects directly with quali fied stand personnel, which can of ten result in solutions being found there and then. And that’s exactly what makes these face-to-face dis cussions better than the virtual ex perience. Finally, we will also be able to offer a hands-on display of our latest developments to the profes sional community.” l
This year, visitors to Powtech will also benefit from synergies created with the simultaneous staging of Fachpack, trade fair for packaging, technology and processing (Photos by NürnbergMesse)
In addition to the transforma tion towards a climate-neu tral chemical industry and the perennial topic of digitalisa tion, the current global po litical situation also poses massive challenges for the process industry.
do we shape the necessary political framework and incentives? Which fi nancial instruments are required? These questions will be addressed at the opening event of Achema enti tled “Climate-Neutral Chemical In dustry“ on 22 August 2022 from 5 pm
Northern Lights, and Ernst Rauch, Chief Climate and Geo Scientist of Munich Re, joining the panel.
Green Innovation Zone shows solutions for a more sustainable future The challenges and solutions for
Which technologies can be used to achieve defossilisation? How to se cure and enhance regional and glob al supply chain networks? And what hurdles must be overcome in the dig italisation of the industry? Achema 2022 offers answers and solutions to these and many more questions. Europe aims to become climate-neu tral by 2050. In line with this tar get, the chemical industry is work ing on technologies to achieve this goal. What are the opportunities, challenges, and obstructions? How
at the end of the first exhibition day. After the welcome address and open ing of Achema by Klaus Schäfer, Chief Technology Officer of Coves tro AG and Chairman of Dechema e.V., Martin Brudermüller, President of Cefic – The European Chemical Industry Council and CEO of BASF SE, will present the perspective of the European chemical industry in his keynote speech. Open questions will be discussed in the subsequent panel discussion, with Martijn Smit, Business Development Director of
a more sustainable future are al so addressed by the “Green In novation Zone”: this special area brings together pioneers, experts and solution providers from indus try, politics, and science with de cisionmakers and users. The Green Innovation Zone highlights green innovations and the challeng es faced by the process industry on its way to climate-neutral pro duction. Five areas in particular will be in the spotlight at Ache ma: climate-neutral production,
The transformation towards a climate-neutral chemical industry, the topic of digitalisation, the global political situation, the difficulties of the energy sector and supply chain networks. The world’s leading show for chemical engineering, process engineering and biotechnology will offer answers and solutions to these and many more questions.
circular economy, industrial wa ter, sustainable chemistry, biobased economy.
“The process industry will have to electrify its facilities across the board and use hydrogen as an en ergy source in the medium term if it wants to live up to its responsibili ty for sustainable value creation,” adds Frank Jenner, Global Chemi cals & Advanced Materials Indus try Leader at EY, the main green in novation partner of Achema 2022. “The industry is already going to great lengths and it’s a huge chal lenge, but it can be done.”
“With this year’s Achema – perhaps more than ever – we are sending out
Digital Hub and Digital Lab offer digitalisation at your fingertips
The topic of digitalization has fi nally claimed a top spot on the agenda of the process industry. The new exhibition group “Digital Hub“ contributes to this: it is the cen tral meeting point for digital ex perts and all participants interested in or actively involved in the digital transformation of the pro cess industry. The exhibition area with a central stage puts digital showcases of the process industry in the spotlight and offers the lat est insights from experts and solu tion providers and facilitates fu ture-oriented discussions.
hensive showcase of the latest tech nology trends in our industry to find and tackle solutions together.”
a signal that technological cooper ation across industry boundaries, but also across national borders, is indispensable for solving the sig nificant crises of our time“, says Thomas Scheuring, CEO of Dechema Ausstellungs-GmbH. Björn Mathes, Member of the Board of Dechema Ausstellungs-GmbH, adds: “As an industry platform, we can create a nucleus in our lecture formats and in the discussions at the stands, in which the industry works together on a solution.”
A total of six use cases for the con nected and digitalized laboratory will be presented at the Digital Lab Action Area – the smart lab of tomor row to experience, touch and try out. Equipment and software manufac turers will demonstrate cross-manu facturer digitalization solutions us ing relevant practical examples. The spectrum ranges from Cobot-assist ed work processes for sample prepa ration and analysis, user-oriented process control with Laboratory Ex ecution Systems, to horizontally and vertically connected yet modularly adaptable equipment solutions with the perspective of shared laborato ry infrastructure and seamless inte gration between sample input and quality-assured analysis results. In novative software and device solu tions are supported by the Labora tory & Analytical Device Standard (LADS) for OPC UA. “Digitalisation, sustainability, security of supply – the challenges ahead are enormous and can only be overcome together and across sec tors”, says Thomas Scheuring. “Let us therefore use Achema in August 2022 as the world’s only compre
This year, for the first time, Ache ma will fully integrate the congress into the exhibition programme. All congress sessions will take place ei ther on stages directly in the exhibi tion halls or in the immediate vicini ty of the exhibition groups. Another change to the Congress is that there will be five theme days instead of three this year. Daily highlight ses sions within the respective themes will emphasize additional topics, en suring that all topics driving the pro cess industry are addressed.
“True to the Achema motto 'Inspir ing Sustainable Connections', we are bringing together what belongs to gether,“ says Dr Andreas Förster, Ex ecutive Director of Dechema and or ganiser of Achema. “Application and research go even more hand in hand at Achema 2022 thanks to the clos er thematic and spatial integration of the exhibition and congress pro gramme.“
On Monday (22 August 2022), the theme “Hydrogen Economy“ will kick off the event. The “Fossil Free Produc tion“ theme day on Tuesday (23 Au gust 2022). The focus topic of Ache ma, “The Digital Lab“, will be part of the Wednesday (24 August 2022) theme day on “Perspectives in Labo ratory & Analytics“. The continuous hot topic “Digitalisation in Process Industry“ can be found as part of the new exhibition group “Digital Hub“ (Hall 12.1) and also as a focal point of the Congress programme agenda on Thursday (25 August 2022). The last day of the congress on Friday (26 Au gust 2022) will focus on “Novel Bio processes and Technologies”. l
Steriline is presenting a Robotic Vial Filling and Capping Machine under isolator (RVFCM50) and a Robotic Nest Filling Machine under double-wall isolator (RNFM5).
After four years, Achema, the in ternational trade show for the pro cess industries that attracts visi tors from all over the world, is back. Steriline is presenting a Ro botic Vial Filling and Capping Ma
can be checked in real-time dur ing filling operations and the rec ipe parameters can be met.
Once they have been properly filled, the vials are moved to the second robotic arm for the stop
Hall 3.1Booth E69
erations while vials are positioned on the weighing cells with a refill function.
This is controlled through sophisticated software based on feed backs from the high-precision weighing cells the filling pumps are equipped with, which are tasked with autonomously adjust ing refilling interventions.
protects the operator at the same time. This new robotic line will al low the customer, a Contract De velopment and Manufacturing Or ganization (CDMO), to further dif ferentiate its offer, processing a wide range of packaging solu tions, and to add toxic products to its own portfolio. After the successful delivery in 2021 of a pilot line for the pri mary packaging of small batch es, the customer’s order for this line comes as a testament of its
Robotic Vial Filling Machine 2: Steriline Robotic Vial Capping Machine
satisfaction with Steriline’s solutions and services.
The RNFM5 under dou ble-wall isolator can process every container that comes in nested form, including syringes, vials and cartridg es. It is equipped with a statistical weight-checking system at the filling station and with Steriline’s patent ed smart bung system at the capping station.
chine under isolator (RVFCM50) and a Robotic Nest Filling Ma chine under double-wall isolator (RNFM5).
The RVFCM50 can process up to 2,400 pcs/h. Once vials are washed and depyrogenated, the first of three robotic arms grasps two vials at the time and places them under the filling heads, which are linked to two peristal tic pumps that potentially allow infinite capacity filling. This step happens directly on two weighing cells, so that the filling volume
pering process and then to the third robotic arm for capping. Whenever the check sensors de tect any non-conformity during filling, stoppering or capping, the process can be repeated to guar antee the conformity needed ac cording to the company’s “robot ics zero-loss philosophy”. This methodology, applied at the filling, stoppering and capping steps, aims to avoid any product loss in the fill-finish process. The philosophy mainly relies on ro bots that allow smooth filling op
In addition, the zero-loss philoso phy also relies on sensors that de tect and report to the technician missing or incorrectly positioned stoppers or caps, with the possi bility of repeating the closing op erations, which reduces this type of waste associated with stand ard solutions.
The machine was designed to manage highly potent drugs po tentially dangerous for people and, for this reason, it is equipped with an isolator that ensures the sterility of the processed vials and
It answers to the client’s need to introduce a new production line to start the commercialisation of a new biotech drug. Its output is up to 10,000 pieces/h with a double-wall isolator solution that guarantees the sterility through out the entire process and the maximum safety for operators. This solution perfectly satisfies all the requirements for the produc tion of extremely sensitive drugs, such as biosimilars and monoclo nal antibodies, in addition to bi otech drugs.
Antares Vision Group is an outstanding technology partner in digitalization and innovation to guarantee the safety of products and people, business competitiveness and sustainability through a unique and comprehensive ecosystem of software and hardware solutions for the life science industries: inspection systems and automatic machines to ensure product quality, track & trace at line, plant, corporate and government level for regulatory compliance and end-to-end traceability, integrated data management within the production process and the supply chain.
EXPERIENCE THE POWER OF TRUSTPARENCY®
WE ARE READY FOR ACHEMA. JOIN US AND EXPERIENCE THE POWER OF TRUSTPARENCY®
Today, Italvacuum manufacturing capabil ities include a wide range of original and patented equipment and systems including single and double stage vacuum pumps, dy namic horizontal and rotative vacuum dry ers and static vacuum tray dryers complying with the main international regulations (ATEX, UL, PED and ASME) and with the lat est FDA and cGMP norms.
ing out semi-industrial and laboratory scale drying tests on customer’s products.
Project Engineering: technical know-how and a thorough knowledge of the needs of the chemical and pharmaceutical industries have enabled Italvacuum engineering services to build up unparalleled expertise in vacuum processes.
Thanks to over 80 years of experi ence, Italvacuum is one of the lead ing manufactur ers of vacuum pumps, as well as a world-wide ref erence point in the engineering, manufac ture and supply of vacuum dryers, ensuring top-tier performances for the treatment of wet powders from filtering and centrifug ing processes. Considering the importance of the use of Italvacuum installations, that are quite of ten exploited in the production of Active Pharmaceutical Ingredients (APIs), Fine Chemicals and Intermediates, the compa ny mission has always been to provide the customers with the utmost in quality, in novation and safety.
Italvacuum is able to pro vide turn-key installa tions and also tailor-made equipment and solutions, according to customer’s process requirements. Ital vacuum presence all over the world, with a continu ally growing number of in stallations in both consol idated and emerging markets, is a tangible sign of the company’s reliability. Customer care, for Italvacuum, means sup porting the customer from the very first contact. Italvacuum offers the opportunity to conduct pilot drying trials and involves the customer in system design and manu facturing. Once the system is up and run ning, Italvacuum also provides all the tech nical support the customer may need to en sure year after year of fault-free operation.
Pilot Trials: the Italvacuum facility compre hends a full range of pilot systems for carry
After Sales Service: with highly qualified personnel, Italvacuum After Sales Service provides the following assistance: 1) sched uled preventive maintenance; 2) technical assistance; 3) service spare parts; 4) sys tem upgrading and overhaul.
Italvacuum is very glad to participate, after 4 years, at Achema, world’s leading trade show for the process industries.
The company will exhibit all its portfolio of vacuum solutions:
- Saurus939 Vacuum pump with VVB and VVC models;
- Criox System 350 liters, Double-cone ro tary vacuum dryer with electric lump break er units;
- Planex System 150 liters, Horizontal pad dle dryer with eccentric agitator;
- CosmoDry System 150 liters, Horizontal paddle dryer with concentric agitator, - Multispray System E0,9 model, Vacuum tray dryer with extractable shelves; - LaboDry System ESL 2 model, Laborato ry dryer.
Antares Vision Group provides a unique, com prehensive ecosystem of solutions to guarantee the safety of products and people, business com petitiveness and sustainability through digital ization and innovation: inspection systems and automatic machines to ensure product quali ty, track & trace at line, plant, corporate and government level for regulatory compliance and
end-to-end traceability, integrated data manage ment within the production process and the supply chain.
Antares Vision Group is the technology part ner for the digitalization of products and sup ply chains through a comprehensive ecosystem of software and hardware solutions: inspection, traceability, data management.
Ecosystem of solutions to guarantee the safety of products and people
Texpack is a manufacturer of packings, tapes, twisted ropes, cloths and sleeves, for thermal insulation for static use, and produces special packings and braided packings with dynamic use for pumps and valves. It produces and markets industrial gaskets of different types and sizes, offering a complete range of sealing systems and products for high temperatures.
Texpack® is a manufacturer of packings, tapes, twisted ropes, cloths and sleeves, for thermal insulation for stat ic use, and produces special packings and braided packings with dynamic use for pumps and valves. It produces and markets industrial gas kets of different types and sizes, of fering a complete range of sealing systems and products for high tem peratures. 9TX. Spiral-wound gaskets
5100. PTFE semi-finished products
The semi-finished product catego ry includes PTFE pipes, bars, tubes, tapes, ribbons, whasers and sleeves.
The same can be filled (during pro cessing with PTFE powder a percent age of specific components is insert ed) glass, graphite, copper, bronze, molybdenum, coal. These special compounds improve the mechanical and thermal strength of virgin PTFE.
5100L. PTFE sheets
PTFE plate, polymer belonging to the class of perfluorocarbons (PFC), re sulting from homopolymerization of tetrafluoroethylene. The same plates can be made with the addition of other stabilizing and thinning components, to expand their application range.
5211. Jointex red
High quality jointing sheet made with pigmented, quartz fillers. It is an innovative replacement material for asbestos seals and conventional products in PTFE. Its special produc tion process ensures that the Join tex® gaskets have excellent creep re sistance and tightness with a wide range of temperatures and pressures.
tion of alkaline substances and is usually supplied with bi-adhesive film which facilitates application.
Visit Texpack at Achema. Hall 8.0 Stand G61
TEXPACK® Srl
Via Galileo Galilei, 24 - 25030 Adro (BS), Italia
Phone: +39 030 7480168 - Fax: +39 030 7480201 info@texpack.it - www.texpack.it
High quality jointing sheet made of PTFE with pigmented glass sphere fill ers. It is an innovative replacement material for asbestos seals and con ventional products in PTFE. The ma terial offers valid mechanical prop erties which enable a high sealing capacity to be achieved and main tained over time. It has excellent chemical resistance and good com pression strength, and does not age.
6803G.
Texgraf® flat gaskets are obtained from a sheet of flexible expanded graphite into which a tanged foil with a thickness of 0.1 mm made of AISI 316 has been inserted.
The spiral-wound gaskets are made of metal tape with a specially shaped pro file coupled with a filler tape (graph ite, ceramic or glass fibre, PTFE or mica), both uniformly wound with constant winding tension. The unique metal pro file has an elastic action that guarantees a perfect seal under all fluctuating tem perature and pressure conditions. They can be assembled to a centring ring that may be external, internal or both.
3350 - 3360. Valve and flange covers
5700.
Envelope gaskets consist of an en closure, commonly called an enve lope, which can be made from the more common virgin PTFE and filled PTFE (silica, graphite or other). The thickness of the envelope is usually 0.5 mm; this makes the gasket par ticularly suitable for the chemical, pharmaceutical and food industries.
6804G. Metaltex
Metaltex represents a Texpack evo lution in the assembly technology sector, guaranteeing a longer gasket lifetime. In fact, Metaltex belongs to the Texpack family of flat gaskets reinforced with graphite, which fea ture a special characteristic that in creases seal performance: the pres ence of an inner reinforcement ring.
Made of brown and black PTFE-coated glass fabric (with or without pH test strip). Valve cover and flange cover are made of a brown PTFE-coated glass fab ric with thickness 0.254 mm or 600 g, black. Harnesses for side fasteners and flame retardant Velcro. A pocket with a hole can be inserted on request, in which the pH test strip can be applied to check the leak, by the change of colour.
5500.
A self-modelling gasket tape made of soft and flexible non-sintered ex panded 100% PTFE. Texlon® resists chemical products with the excep
6610I.
Jointing sheets made of cellulose fi bres, mineral fibres and fillers, NBR based elastomer binder.
This is a packing composed of pure PTFE yarns, which is impregnated yarn-byyarn with PTFE dispersion, and formed using a diagonal braiding method. This packing has a low coefficient of friction on the shaft and a high resistance to chemicals.
Mott & ASCO combined have over 80 years of fil tration and flow control experience in critical in dustries including specialty and bulk chemical pro cessing. Mott & ASCO pro vide complete site needs for filtration ranging from
disposable filter media to semi automated systems, through coalescing tech nology and fully automat ed self-cleaning catalyst recovery filtration skids. In addition to the standard range of filtration products, the company’s engineering
Hall 8.0Booth H22
To expand the already wide range of hydraulics Salvatore Robuschi will present at Achema a new series with open channel impeller available in both horizontal and vertical versions. The pump is intended for sugar mills, fertilizer production, the paper industries and all situations where an open impeller with wide passages is required. It is suitable for viscous liquids even containing dis solved gases, offers a low NPSH and guarantees good performance and stability even with high dry matter content.
division provides complete filtration packages to en gineering companies and end users alike, designed and manufactured according to all the main con struction codes and stand ards (ASME VIII Div 1&2, PED etc.) building on the
combined resources of an engineering team. To sat isfy the requirements of the oil & gas and petrochemi cal sectors, ASCO Filtri and Mott can also provide pres sure vessels and systems with U-Stamp 1&2 and/or CE Stamp.
CO.RA. Srl is leader in “made in Italy” production in solid handling systems for finished and semi-finished products for the chemical and phar maceutical field of the solid, oral and sterile production ar eas; is at 360° available to the customer for engineering and design, construction, in stallation and assistance ser vices, its expertise which al ways puts customer satis faction first, together with, CO.RA. creates the applica tion tailored and suited to individual needs. The experience gained in over 30 years of activity, make the company an ideal partner who is able to offer a range of transversal products, from components and fittings for the chemical-pharmaceutical all the way to solid handling plants, ensuring assembly, testing, maintenance and as sistance. CO.RA. offers a vast portfolio of products particu larly specialized in connec tion and interface systems
between machine A and ma chine B, within the process. The production is based on the standardization of the products but at the same time the distinctive factor is in the ability to understand the needs and specificities of the customers and adapt or design the CO.RA. product able to respond exactly to the needs. The staff follows the customer and the process from the analysis of needs, to the installation and test ing of the product/system up to the periodic maintenance. The processes of technical design, processing, testing and certification of the prod ucts respect the quality pro cedures, the most careful and strict certification bodies in compliance with the Phar macopoeia directives (FDA). The goal is to ensure that CO.RA. products contribute and guarantee, within the chemical, pharmaceutical, to the production of reliable and quality pharmaceuticals.
Hall 3.1Booth A69
The Filtration Division of the energy management company Eaton will be exhibiting at Achema numerous solutions for the Life Sciences and In dustrial Processing segments. A special focus will be on the new gener ation of BECO CARBON™ depth filter sheets containing activated carbon and the Simplex 72X pipeline strainer range. The upgraded Beco Carbon depth filter sheets containing activated carbon offer particularly high adsorption properties for the demanding filtration of liquids. Having the activated carbon bonded directly into the filter elimi nates the need for manual dosing and separation of the otherwise typical ly loose activated carbon and the challenges that go along with it. With their strong decolorization abilities and adsorptive removal of undesired by-products, along with taste, odor and color correction, they are ideal ly suited for use in the fine chemical, pharmaceutical, cosmetic, food and beverage, and biotechnology industries. Beco Carbon depth filter sheets are available in the versions ACF 02 with an activated carbon content of 1,000 g/m² (macroporous) and ACF 07.10 with 420 g/m² activated carbon content (meso/macroporous). They are available in all common filter sizes and formats as well as stacked disc cartridges and small disposable cap
sules. The product program thus cov ers the requirements from laboratory to production scale.
The new Simplex 72X strainer range consists of a total of six standard siz es from one to six inches for industrial pipelines. It features improved O-ring seals and allows removal of solids down to 40 µm. In particular, they support the protection of industrial plants where chemical, petrochemical and water pipelines can be temporarily shut down for cleaning or replacement. A duplex solution is also available for contin uous processes. The improved sealing and surface finish properties com ply with the Pressure Equipment Directive (PED), EN13445 and AD 2000 pressure vessel codes.
In addition to the product highlights Beco Carbon and Simplex 72X, Eaton will also be showcasing other filtration solutions for life sciences, such as membrane filter cartridges and housings, depth filter media, stacked disc cartridges and housings, and filtration systems for laboratory applications.
IMA Active will have a corner dedicated to Continuous Manufacturing, that underpins the improvement of pharmaceutical products in terms of potency, effectiveness and safety by means of accurate process control.
IMA Pharma is world leader in the design and manufacture of automatic machines for the pro cessing and packaging of phar maceutical products thanks to a high technological profile and the ability to offer tailor-made solutions to satisfy the most so phisticated requests of the mar ket, thanks to highly special ised divisions: IMA Active (Solid Dose Solutions), IMA Life (Asep tic Processing & Freeze Drying Solutions), IMA Safe (Packaging Solutions) and IMA BFB (End of Line Solutions).
At Achema 2022, visitors will have the chance to discover what’s new from IMA for the pharmaceutical industries.
IMA Active will have a corner dedicated to Continuous Manu facturing. Continuous Manufac turing underpins the improve ment of pharmaceutical prod ucts in terms of potency, effec tiveness and safety by means of accurate process control.
IMA Active have been cultivat ing their own knowledge and are ready to welcome the demand for innovation, working together with companies and stakehold ers to design the future of phar maceutical manufacturing and taking the lead in the future of pharmaceutical technologies for OSD (Oral Solid Dosage) forms.
IMA Active’s belief in and knowl
edge of Continuous Manufactur ing have grown stronger thanks to intensive R&D work carried out on two fronts.
A more disruptive front of IMA Active R&D consists in the part nership with Continuus Pharma ceuticals, a spin out of Novartis MIT centre, leveraging a novel production platform called Inte grated Continuous Manufactur ing (ICM). ICM enables seamless end-to-end continuous manu facturing processes that incor porate API formation steps with final drug product formulation.
IMA Active supports ICM in the development of EMC (Extrusion Moulding Coating Technology) to create the final dosage form. While on the other R&D front IMA Active work on continuous processes by revisiting current technologies, embracing a con cept of Continuous Manufactur ing more closely related to con ventional solid forms.
This initiative aims primarily to introduce continuous equip ment into the market that can be integrated with convention al technologies, even in an ex isting plant, in order to improve the production performance.
Continuous direct compres sion line and continuous direct encapsulation
IMA Active can supply either
fully integrated lines or unit op erations to combine with each other offering maximum flexi bility in new or existing plants. This initiative quickly pro vide Continuous Manufacturing solutions that can be integrat ed with conventional technol ogies, even in existing plants, capable to manufacture existing drugs with higher performance. The tablet press or the capsule filler are fed continuously with consistent mixture of product, from a feeding blending unit installed upstream them. The whole system is managed by Maestro, IMA Active modular or chestration layer. The flexibility of Maestro makes it easy to inte grate any kind of unit operation so the entire Continuous Manu facturing Line can be managed as a single system.
CROMA continuous tablet coat ing equipment is sized to work downstream a medium-speed tablet press. CROMA is a mod ular unit operation that can be configured as a single module or in combination of more modules either in series or in parallel and the product flows continuously throughout the modules, with no steps. Such combinations al low to process all kind of tab lets at different throughput and coating weight gain. The ma chine is fitted with highly inno vative technologies for process monitoring and control, like PAT tools and sources of process an alytical data that can facilitate decision-making and follow-up action.
Hall 3.0Booth F49
ACCELA CTC 500 continuous coater by Thomas Processing completes the IMA Active range of continuous coating equip ment. ACCELA CTC 500 is the ultimate technology by Thom as Processing, who have been pioneers in continuous coat ing since 1993. It is designed to manage high production throughputs in a range of 1001,000 kg/h of large batch sizes of tablets to process in contin uous mode. Advanced design of ACCELA CTC 500 provides phar maceutical manufacturers with an improved manufacturing pro cess to eliminate material waste and reprocessing during startup and shutdown. Thomas Process ing’s ACCELA CTC 500 is the only coater on the market manufac tured with an integrated cooling chamber that eliminates the need for additional cooling sys tems, reducing the footprint of the equipment and streamlining the coating process.
MG2 will show two machines representative of its divisions Packaging and Processing. For the first time, the company will host the coexhibitor Universal Pack.
After months of waiting and postpone ments, MG2 is preparing to fly to Ger many. The Pianorese company, world leader in the design and production of capsule fillers and packaging ma chines, will show two machines rep resentative of its divisions Packaging and Processing: these are BliStar and FlexaLAB.
BliStar is a blistering machine de signed to optimize the primary pack aging of capsules and tablets in blis ters for both pharmaceuticals and nutraceuticals. It is characterized by both ergonomic design and electron ic control that guarantee fast size change over by recalling a recipe and it can manage up to 150 blisters/ minute with maximum dimensions of mm 90×140. BliStar is a tile that ex pands MG2 proposal, to allow its cus tomers to create a complete packag ing line, starting from the capsule fillers to the end-of-line machines. FlexaLAB is a capsule filling machine specifically designed for R&D labo ratories, small batches and special productions, suitable to dose several pharmaceutical oral forms, with pro duction speed up to 3.000 capsules/ hour. At Achema, FlexaLAB will be equipped with two dosing units spe cially designed for trending applica tions: the Microdose unit suitable for powder micro-dosages (includ ing API without excipients) from 0.5 mg and the liquid filling unit which can manage cold liquids, hot-melt liquids and suspensions up to 70°C. This is how MG2 introduces itself on
the German market which has been also the scene of a recent success: the supporting activity to industrial ize a pharmaceutical product for in halation purposes, carried out for an important CDMO, the Aenova Group.
The capsule filling machine, which is installed in the Münster plant, is a Planeta 200 equipped with a powder low-dosages unit (from 5 mg to 40 mg) and the MultiNETT system that controls 100% in-process net weight of each filled capsule.
MG2 technology is not the only one present on the stand, which also hosts the partner Universal Pack, an Italian company based in Romagna which boasts over 50 years of experience in the production of vertical packaging machines for single-dose packaging. Universal Pack cooperates in the USA with MG America, the historic sub sidiary of MG2. The company will show the Alfa Flexi vertical pack aging machine, able to produce a wide range of stick-packs. This ma chine is designed for powders and liquids processing, at low and high dosage, to guarantee high standards of flexibility. This solution is made possible thanks to the combination of different modular components, which allow the company to offer us er-friendly technology to the market, ideal features for those custom ers with easy and fast format change needs. The Alfa Flexi vertical packag ing machine combines minimum di mensions, ergonomic and flexibility to make the role of the operator as
easy as possible.
MG2 and Universal Pack are ready to welcome visitors to Achema with their top-level technological offer, an expression of European and es pecially Italian industrial excellence in the sector of processing and pack aging machines for the pharmaceuti cal and nutraceutical fields.
A robotised integrated line for packaging blisters in cartons will be presented by Marchesini with labelling machine complete with incorporated checkweigher for dynamic weighing and control of cartons.
At Achema, Marchesini Group will be presenting a wide selec tion of machines and lines devel oped for the pharmaceutical in dustry with innovative features in the areas of Industry 4.0, sus tainability, safety and product traceability.
In centre stage on stand G3 in hall 3.1 will be a state-of-theart solution for the packaging, serialisation and traceability of blister products, developed in association with strategic part ner SEA Vision - a company spe cialising in vision systems.
Integra 720V, a robotised inte grated line for packaging blis ters in cartons, will be present ed with BL-A525 CW labelling machine complete with incor porated checkweigher for dy namic weighing and control of cartons. What makes this line innovative is the inclusion on board the machine of a new technology, unique on the mar ket: a complete software pack age that aggregates the blister to the carton.
This is a strategically important solution for all contexts where blisters are sold, distributed or separated from their original pack, whether by the end us er or by other players along the distribution chain, such as in hospitals, or in pharmacies in
many countries. Although reg ulators do not yet require the serialisation of individual blis ters, this technology is intend ed to provide suppliers with an added opportunity for protect ing consumers and combating the counterfeiting of pharma ceutical products, preparing for the future and its demands in advance.
The Integra line will be fur ther equipped with the Predic tive Maintenance solution devel oped by the Marchesini Group. The data of the sensors installed on board the machine (IoT) is collected, analysed with the aid of Artificial Intelligence (AI) al gorithms, transformed into in formation useful to the opera tor and displayed by means of a dedicated web platform, on dis play at the show. Checking this information will enable anoma lies to be identified and main tenance to be scheduled in ad vance, avoiding any failures. In addition to this new technol ogy for solid products, the Group will also be exhibiting two more innovative lines for the inspec tion and packaging of products in stickpacks.
First of the two, visitors will be able to view a line consist ing of a CMP Phar.ma inspection machine checking 400 vials per
Hall 3.1Booth G3minute: thanks to innovative in spection systems based on Neu ral Networks and Artificial In telligence (AI) technology, the new machine upgrades perfor mances, maximising flexibility and precision. The line is com pleted by an RL-F800 extreme ly high-speed labelling machine with a rotary star wheel infeed system and rotary roller convey or, designed by the Neri division, and a TM3 for bundling vials in trays, with counter function. On board the line, SEA Vision cam eras will provide optic control of tray contents. Secondly a line for packaging products in stickpacks, compris ing a Schmucker MT1300 12-lane stick packaging machine, a stack ing and counting system and an MA80 cartoner. Specifically, this line is designed to process PPbased packaging materials (with and without PE) such as 100% recyclable plastic monomaterials like OPP or BOPP with a metal lised intermediate layer.
Stand-alone machines on show Three stand-alone machines will also be exhibited, includ ing FSP05, an automatic solu tion for filling and stoppering RTU (Ready to Use) vials, car tridges and syringes in nests. This machine, produced by the
Corima division and already consolidated on the market, is presented with a new fill ing technology using “dispos able volumetric pumps” devel oped by Neoceram in associa tion with Marchesini Group. On show will be also a TUR BO-MEK 1000, a vacuum tur bo-emulsifier for processing liquid products, developed by Dumek, the Group brand spe cialising in processing solutions for pharmaceutical products. The machine, designed in accord ance with hygienic and cleaning design guidelines, is extreme ly flexible and is ideal for pro cessing a wide range of products, since it is equipped with an in ternal turbine and a second tur bine for the external recycling of the product.
Last but not least, the stand will host a solution by Dott. Bonapace, a company based in Cusano Milanino (Milan) that became part of the Marchesini Group in 2021. The machine displayed will be the IN-CAP SE automatic filling machine, able to process up to 3,000 capsules an hour and designed to dose various products (such as powders, liquids, pellets and tablets) into the same capsule, with over twenty possible com binations.
Ystral, the German machine and plant man ufacturer chooses the topic “Trends and Me ga Trends in Process Technology” for its trade show stand at the Achema 2022. With its themed trade show exhibit, the mixing and dispersion technology specialist intends to promote the exchange between different are as of the process industry. “Depending on the industry, trends in process technology often turn out to be very different for similar pro cesses”, says Dr. Hans-Joachim Jacob, Senior Expert Process and Applications at ystral. “This is often due to the fact that manufacturers do not know anything about solutions from oth er industries. For this reason, we would like to use our new booth concept to get users from different areas of the process industry –whether it is paints and varnishes, foodstuffs,
drugs or cosmetics – to learn from each other, and thus gain new inspiration for their day-today production.”
The trends presented at the ystral trade show stand include cleaning without cleaning agents, clean production processes without biocides or preservatives, cold chemistry, possibilities of process intensification and the realisation of intensive processes outside the tank as well as the development from co-grind to slurry man ufacturing and from batch to inline process.
“The further development of process technol ogy is of course also characterised by mega trends such as Smart Factory, digitalisation or modularised fabrication”, says ystral’s Pro cess Engineer Jacob. “However, the trends in mechanical process technology selected by us mainly aim at making visitors to the trade
show aware of possibilities which they did not know anything about up to that point – and providing them with some eye-open ing insights.”
Ystral will show how, against the background of these trends, altered process-related requirements can be implemented with innova tive mixing and dispersion technologies. The company will present amongst others the inline powder wetting and dispersing machine Ystral Conti-TDS, as well as the Ystral Jetstream Mixer. Furthermore, the mixing and dispersion tech nology specialist will introduce the newly de veloped powder dispersing system Ystral BATTTDS, which reduces the manufacturing times for the production of lithium-ion-electrode slurries in battery production from currently between two and six hours to just a few minutes.
AMI Codes-II O3
Colorimetric standard method according to DIN 38408-3, no sensitivity loss in absence of ozone.
AMI LineTOC
Early trend detection without laboratory measurements. Automatic System Suitability Test (SST) and calibration at minimized maintenance.
AMU Pharmacon
Conductivity transmitter according to USP <645> in a standardized design and integrated temperature compensation.
Swan Analitica Srl ∙ IT-16167 Genova www.swaninstruments.ch swan@swananalitica.it
Coesia, a group of 21 companies specialized in innovative indus trial and packaging solutions, is participating at Achema, an in ternational trade fair dedicated to the process industry with man ufacturers and service providers from over 50 countries present ing their products for chemical, pharmaceutical and biotech re search and manufacturing). Six companies from the GroupFlexLink, GF, HAPA, MGS, Norden and Volpak - present their latest innovations in terms of packag ing machinery, printing and fac tory automation, which are aimed at improving production efficien cy and the digitalization of op erations, as well as reducing the ecological footprint of packaging for the pharmaceutical sector. Coesia offers a complete portfolio of solutions and services for cus tomers who are facing the new market challenges, increasingly oriented toward greater sustaina bility and the digitization of pro
cesses in the Pharma sector.
In particular, Coesia is progres sively focusing on digital tools and services to optimize the ef ficiency of machines, lines and entire factories, and deliver ad vanced support to customers.
The latest Coesia Digital innova tions are:
• OptiMate, Coesia’s new smart HMI, developed to expedite op erations such as format change, troubleshooting, maintenance or technician training, and to facil itate access to guided procedures and digital documentation di rectly on the machine. OptiMate is installed and visible on Hapa and Enflex (a brand of Volpak) solutions at the Coesia booth.
• PerforMate, Coesia’s IIoT plat form for real-time machine mon itoring. Working as an entry point to many innovative servic es, PerforMate allows improved control, enhanced collabora tion, and performance boost of customers’ entire machine pool.
Sustainability remains one of the fundamental pillars of Coesia’s strategy. Indeed, the majority of the machines on display are able to handle sustainable mate rials, such as paper films or mo no-materials. The Coesia Shelf of Sustainable Solutions, pres ent at the stand, is dedicated to sustainability and eco-sustain able packaging offered by the Coesia companies in the Phar ma industry.
The six Group companies join ing the exhibition
Enflex, a Volpak brand, is pre senting the F-11, a machine that manufactures, fills and seals flat flexible pouches specifical ly designed for the pharmaceu tical industry. The F-11 is suita ble for packaging a wide range of products, such as pharmaceuti cal powders, pills, medical devic es, over-the-counter medicines, wipes and swabs.
The experts at FlexLink, a lead ing company in the field of au tomated manufacturing and ma terial flow solutions, are on hand to discuss how industrial auto mation can improve high-value
Hall 3.0Booth D73
pharmaceutical manufacturing processes and increase the ef ficiency of medical packaging.
FlexLink’s X45 conveyor system is designed for high through puts that require special atten tion and offers several functions.
GF, an expert in turnkey solu tions for the primary packaging of injectable drugs in vials, am poules, cartridges, syringes and bottles, presents the AV-E in spection machine: fully auto mated and developed to treat vi als, bottles and cartridges filled with injectable solutions and ly ophilized products. It is the ideal solution for meeting the require ments of GMP (Good Manufactur ing Practice) and to ensure that the products are essentially free of foreign particles.
Hapa showcases two solutions that offer printing and inspec tion capabilities integrated on the same machine through a common workflow. This inno vation substantially reduces the time spent on system integra tion and validation.
The technicians and experts at MGS, a Coesia Company that de signs and manufactures custom ized and cutting-edge packaging solutions in the Life Science sec tor, are available to show cus tomers and visitors how to solve unique packaging challenges and achieve seamless production.
Norden, a leader in the supply of high-performance systems for tube filling as well as cartoning, offers numerous machine mod els and various technologies to meet every production need.
all
OQEMA is an international ly active distribution com pany for basic and special ty chemicals based in Ger many since 1922; it is, tra ditionally and conventionally, a me dium-sized family-run business (the "German Mittelstand"). A feature that OQEMA is convinced can also bring advantages to larger customers, with faster decision-making processes that support the business better.
In Italy, OQEMA is based in Lombardy, with offices in Assago (MI) and Riva nazzano Terme (PV), where the man agement offices, logistics and ware houses are located. Here it was for merly known as Elettrochimica Valle Staffora, a company operating in the chemical raw materials distribution sector since 1930 and which has been working from the very beginning to find solutions to improve our quality of life and that of future generations.
The Group's first 3 years in Italy Thanks to a team of experienced pro fessionals, Elettrochimica Valle Staffo ra gained a prominent position in the chemical raw materials distribution sec tor, combining professionalism, quali ty and innovation with its widespread presence in various production sectors. Since 2019, Elettrochimica Valle Staffora has become OQEMA EVS and it has expanded its international distribution offer in the food, cosmetics, pharma ceutical, rubber and resins, chemical industry, water treatment, paint and coatings and livestock sectors.
Today, OQEMA is a Group with a turno ver of more than 1.3 billion Euro, with 29,000 customers, distributing 14,000 products throughout Europe and em ploying 1,300 people in 45 locations in 23 countries.
Whoever tries something completely new must be able to constantly break with tradition. Never before in the history of the company has a mem ber of the founding and owner family left without being replaced by anoth er family member.
Peter Overlack's departure marks the beginning of a new management era: the new Executive Board now con sists of three people none of which are members of the Overlack family. While this involves a natural and grad ual detachment from executive leadership continuity on the one hand, it also represents an opportunity for the best people to take the reins and work diligently and efficiently, regardless of personal disagreements and share holder disputes.
In any case, Peter Overlack will remain quite close to the company, just like his family, in his role as a member of the Supervisory Board, while, Patrick Barth els has become Chief Executive Officer of the OQEMA Group on 1 July 2022. Hartmut Kunz will remain in charge of finance, administration, marketing, le gal, IT, compliance and digitalisation. He has been involved in the complete overhaul of the company’s IT solution over the last few years and therefore still has a lot on his plate. Philipp Junge is joining the Exec utive Board as a fresh face. He pre viously worked at Lanxess, where he spent the last 14 years and held vari ous active leadership roles. The chal lenge of working in a characteristical ly mid-tier environment was a particu lar incentive for him. He has made the move to the OQEMA Group and began as Chief Operating Officer (COO) on 1 June 2022.
The OQEMA Group is divided into HUBs, eight in total. Italy is headed by Mat thias Mirbach as HUB Director of South ern Europe, which recently expanded to include France, where the OQEMA SAS and OROSOLV units operate. With this step, the possibilities for syn ergies in the organic, inorganic and spe
OQEMA is a Group with a turnover of more than 1.3 billion Euro, with 29,000 customers, distributing 14,000 products throughout Europe and employing 1,300 people in 45 locations in 23 countries
OQEMA EVS has was formerly known as Elettrochimica Valle Staffora, a company operating since 1930 in the chemical raw materials distribution sector. Since 2019, it has expanded its international distribution offer in the food, cosmetics, pharmaceutical, rubber and resins, chemical industry, water treatment, paint and coatings and livestock sectors.
cialty sectors in France, Spain, Portugal, Italy and North Africa have increased.
The leading figures of OQEMA Italy OQEMA EVS's Board recently welcomed Renato Quinto, sales, purchasing and logistics manager. Renato has years of experience in the chemical and plas tics industry in Group such as Arkema. “I have embarked on this new adventure driven by the Group's potential. I found a stimulating environment in a multinational but people-oriented context, where attention to customer needs and passion for one's work are
spread coverage all over Europe. In the long term, OQEMA aims to become one of the top five-ten chemical distribu tion companies in the world.
How will it be possible to achieve these goals? Innovation, flexibility and excel lent service to constantly increase cus tomer satisfaction. Flexibility, focus on service, readiness and speed: in aiming for growth, OQEMA wants to consciously create or maintain structures that al lows the Group to quickly develop cus tomised solutions for its customers.
“We will make sure that the increasing development of our expanding busi ness does not make our work processes become too rigid or regulated. We be lieve that employees should always be able to make decisions on site for our customers. We have an invisible ‘flexi bility watchman’ who keeps an eye on us and tells us if we are becoming too slow or too complicated” comments the OQEMA Group Board.
ious European countries (Presence) must be as climate-friendly as pos sible (e.g. completely zero-emission warehouse in Austria).
In the Product area, efforts are be ing made to review and optimise the product portfolio in the direc tion of greener, more environmental ly friendly and bio-based raw mate rials. In Germany, there is already a strong bio-based portfolio in the Fla vour and Fragrance division. Reuse, recycle, reduce: the three ‘R’ of sustainability are assigned to the Plan et aspect. The circular economy within chemicals will play an important role in achieving the sustainability goals. OQEMA's long experience and resourc es dedicated to processing and distrib uting chemicals for recycling will allow the Group to be recognised as a lead er in the recovery and reuse of a wide range of chemicals and energy storage applications.
an important strong point” comments Renato Quinto.
In addition to Quinto, the Board in cludes Chairman Matthias Mirbach and Laura Cellerino, Director and CFO. “I started working with Elettrochimica Valle Staffora and I was able to con tribute to the integration of the com pany into the OQEMA Group, starting from rebranding at the end of 2020, and all the way to the implementa tion of policies and strategy. Working with the talented and skilful people who were already in the company has led to excellent results over the past two years and I am convinced that we have laid down a solid foundation for our growth” says Laura Cellerino.
The Group's Vision for the short term Within 2027, OQEMA aims to consol idate its position in the distribution sector and grow, in order to reach a turnover of 2 billion Euro, with 2,0003,000 employees and with a wide
In the summer of 2022, the OQEMA Group will be celebrating its 100th birthday, giving us the opportunity to take stock of this first century and giv ing us another reason to look towards the future. How can we become even more sustainable? Which internal and external values must be strengthened in the coming decades?
The Group will continue to plant seeds to watch them grow and, with the mot to “Planting Seeds”, has defined six fundamental areas that are reflect ed in the anniversary campaign: Peo ple, Presence, Product, Planet, Perfor mance and Planting.
Committed and motivated employees have always been an important success factor (People) for OQEMA, to be supported to actively realise their po tential with development plans, focus ing on diversity and promoting mental and physical health. The Group's headquarters in the var
In order to develop in the distribu tion market, it is necessary to recog nise growth opportunities and exploit them consistently (Performance). This is what OQEMA is able to do. Anoth er highly competitive factor is profit ability, which provides the necessary funds for investments and ensures the strength to constantly put customer needs at the centre of the company's actions.
Last but not least, the heart of the 100-year project: Planting. A green er and more sustainable world can be achieved not only by adapting prod ucts and optimising supply chains and warehouses, but also by simply plant ing trees. In 2021, the Overlack fami ly acquired the Lappen nursery, which they have now relaunched under the name Baum & Bonheur.
And with this in mind, for the OQEMA Group's 100th anniversary, mighty trees will be planted at each of the Group's locations to make a significant contribution to climate protection. l
OQEMA’s long experience and resources dedicated to processing and distributing chemicals for recycling will allow the Group to be recognised as a leader in the recovery and reuse of a wide range of chemicals and energy storage applications
Nitrogen oxide abatement plant at Radici Chimica Novara
Setting concrete environmen tal sustainability objectives for abating direct greenhouse gas emissions and leveraging investments and state-of-theart technology. This is the approach that has always guided world leading manufacturer RadiciGroup in operat ing its businesses with a wide range of products: chemical intermediates, pol yamide polymers, high performance en gineering polymers and advanced tex tile solutions.
RadiciGroup’s strategy has paid off, al lowing the Group to reach ambitious
goals: between 2011 and 2020, overall Group greenhouse gas emissions were cut by 70%, falling from about 700,000 metric tons per year of CO2 equivalent to 200,000 metric tons. These results were largely achieved through the action implemented by the Group’s Specialty Chemicals Busi ness Area at its plants in Novara, Italy, and in Germany, which are the heart of RadiciGroup’s chemicals business. Here the Group produces an essential inter mediate for synthesizing polyamide 66, adipic acid, whose production process releases nitrous oxide as a by-product.
Nitrous oxide in itself is not particular ly problematic (in fact, it is used in the medical sector as an anaesthetic and in the food industry as a spray propel lant, in cans of whipped cream, for in stance), but, if it is released into the at mosphere, it has a much higher green house gas effect than carbon dioxide. At the Radici Chimica site in Novara, a multiyear investment budget of over EUR 10 million was dedicated to lower ing these emissions through three im portant undertakings: in 2004, putting into operation a three catalyst bed re actor, designed and patented by the
In the past decade, RadiciGroup slashed greenhouse gas emissions by 70%. The next target is -80% by 2030. Radici Chimica Novara plays a key role in reducing Group environmental impact.
company, to decompose nitrous oxide into nitrogen and oxygen, the two el ements it is composed of, thus mak ing it innocuous for the atmosphere; in 2013, installing an EnviNOx plant to decrease the release of nitrous oxide formed in the production of nitric acid, and, in 2021, a further improvement in the emissions abatement system asso ciated with nitric acid production. Since activating the last plant just 9 months ago, more than 35,000 metric tons of CO2 equivalent have been cut. All the above-mentioned actions have enabled Radici Chimica Novara to re cord a nitrous oxide emissions level less than 10 ppm, a value close to zero. “We are the only Italian manufacturer of adipic acid, a basic chemical interme diate for numerous industries, as well as polyamide 66, our own sector. The investments we have made to improve the environmental performance of the adipic acid production process have al lowed us to achieve significant results and make our business increasing ly more sustainable,” Maurizio Radici, vice president and COO of RadiciGroup, stated. “We decided to implement initiatives for emissions abatement long be fore it was required by law. As a matter of fact, we started studying the avail able technologies at the end of the 1990s and advocated for setting up the European Emission Trading System
(ETS) in the Italian chemical industry in 2011, two years before it became law.”
Furthermore, in Germany, in 2001, RadiciGroup built from scratch an ad ipic acid plant that uses Best Availa ble Techniques, including an advanced thermal abatement system for nitrous oxide. Additionally, by the end of 2022, an EnviNOx plant is scheduled to be in operation, so as to bring the plant’s di rect greenhouse gas emissions down to zero, by reducing nitrous oxide emis sions associated with nitric acid pro duction.
“We are convinced that our companies will grow only if they stay in harmony withalltheirstakeholders,AngeloRadici, president of RadiciGroup, emphasized. “As regards minimizing environmental impact, we will continue to invest from the perspective of continuous improve ment, so that our recent installations in the Specialty Chemicals business ar ea will enable us to further abate total Group greenhouse gas emissions and by 2030 arrive at a reduction of around 80% compared to 2011. Moreover, con cerning energy, on top of an innova tive trigeneration plant, all our Bergamo sites use self-produced renewable energy or draw electricity from the grid, with the ambitious objective of 100% self-produced renewable source energy. Radici Chimica Novara is directly con nected to a high-efficiency cogenera
tion plant that runs the site and fully covers its energy needs.”
President Radici continued: “Besides our commitment to energy issues, we invest in innovation and the devel opment of new recycling and circular economy projects, trying to take tan gible action towards a sustainable fu ture for our companies and the commu nities where we operate.”
Other significant investments in emis sions abatement have been carried out at the RadiciFil site in Casnigo (BG) and at Radici Yarn in Villa d’Ogna (BG). RadiciFil installed a thermocompression system that slashes steam consumption by the production plant, while Radici Yarn set up a trigeneration plant that uses a high-efficiency system to pro duce not only electricity and steam, but also cold water needed for the produc tion processes, resulting in a drop in water usage of 30% in 2021. l
Ellab provides world-leading validation, monitoring and cali bration solutions and services, as well as GMP consulting, to life science and food manufacturing companies. The company serves both small and large companies within the Life Science and Food industries and have solutions for almost all applications such as sterilization, freeze drying, en vironmental chamber testing, depyrogenation, warehouse mapping, pasteurization, con trolled temperature units (CTU) and many more.
Ellab develops unique and inno vative solutions based on input from close interactions and dia logues with customers. The goal is to help the customers over come challenges and increase their productivity by providing reliable and efficient solutions. The main services can be split up into the following categories: - Commissioning, Qualification and Validation Services
(CQV), for on-site projects, temperature mapping qualifications and commissioning tasks. The qualification and validation teams of Ellab aim to assist you with meeting indus try requirements and guidelines to ensure safe and high-quality products. The company covers a wide array of applications and tasks, from all kinds of temper ature mapping, IQ, OQ and PQ’s to alarm testing and shelf map ping – just to name a few. Ellab’s highly trained technicians are well versed in the requirements from government agencies such as the FDA, EU and ICH. To re duce the turnaround time, Ellab works with its efficient report ing tools, but also accepts and works with whatever report, protocol and/or SOP templates that customers desire. Allowing Ellab to draft documentation de signed specifically for custom er’s project and procedures.
- Consulting and Engineering
Services, for sparring, project management and support. Ellab’s consulting teams have the vast experience required to ad vise the customer on its projects and processes. All Ellab’s con sultants are GMP experts capa ble of increasing operation reli ability and ensuring compliance while decreasing costs. Ellab thrives in supporting customer development and production, as well as managing its projects to eliminate deviations and bottle necks. With Ellab as consulting partner, the user gets access to experts with crucial knowledge of: implementing cost reduc tion measures, implementing preventative measures, setting up and executing master plans, managing project scopes, times cales and tasks, providing com missioning, validation or quali fication reports as proof of com pletion, conducting a wide array of relevant studies, audits, as sessments and tests, performing data analysis and error-checks, and much more.
- Field Calibration Services, for equipment calibrations and adjustments on location. Ellab’s field calibration services are perfect for whenever off-site calibrations stop being an op tion. This could be due to the hassle of transporting sensitive measuring equipment or due to sensors being locked in crucial processes – either way, Ellab’s calibration technicians have the solution. With the portable equipment, the company can see to customer’s calibrations anywhere, anytime. Ellab exclu sively uses high-end calibration hardware and software to ensure that the calibrations and adjust ments are accurate and well doc
umented. All Ellab’s calibrations come with reproducible, trace able and compliant certificates that are saved to company’s cloud and can be printed when ever necessary. Field Calibra tions drastically reduces down time for measuring instruments and eliminates shipping costs and risks. All Ellab’s calibration equipment is traceable to AC CREDIA to ensure the traceabil ity to measurement standards of physical quantities includ ing temperature, humidity rel ative, CO2, dew point, pressure and electrical quantities.
Training is also a pillar of Ellab’s business: the compa ny offers specialized training courses within Ellab Academy both in headquarters and online and gives the customers the opportunity to agree on the training course best suited to their needs.
For further information visit the website www.ellab.com.
Flexibility, full availability to wards the client in all phases of the project, top work develop ment, cost transparency, prac ticality and professionalism are the ingredients that made S4S (www. s4ssrl.it) a company standing out for the designing and building of systems for controlled atmosphere environ ments designed for production areas. Today the company is focusing on en
vironmental and energy control-related issues. The meaningful know-how in the pharma and chemical fields, today ex tending also to the food and electronic fields, top availability towards the cus tomer in all of the planning steps, the capability of meeting the needs ensur ing the best possible results are the keys to the success of S4S srl, a company dealing with the development of con trolled atmosphere systems designed for Cart for LAF area
clean rooms and production areas, as well as for “turnkey areas”. The compa ny works in the name of enthusiasm, in a dynamic and constructing work envi ronment, often facing highly custom ized and challenging projects.
Process and needs within the production area The development of an environmen tal monitoring plan represents one of pharmaceutical companies’ most com plex activities. Generally, the "design" of the activities is entrusted, by proce dure or internal management, to a sin gle professional often as QA or QC. Over time, it has been understood how im portant this role is and therefore dif ferent figures have been involved such as engineers and production managers. Building an environmental monitor ing plan means first of all knowing the classified environments, the ma chinery and materials present inside, the air flows, the external and inter nal flows of material and personnel as well as the processes.
Environmental monitoring is the ac tivity that more than others requires a transversal commitment, in which S4S know-how and skill become fundamental, always acting as a partner within companies. All laminar flow hoods op erate on the principle of low turbulence forced air flow. Using this principle, a stream of air is introduced horizontal ly or vertically along the bench’s entire
S4S designs and develops clean room and production area systems, offering industry a high level of skill and flexibility.
work area. During this procedure, ambi ent air is introduced into the work area as a laminar flow stream and flows hori zontally or vertically for suspended sub stances with top performance. This air stream captures the particles directly from the source and transfers them without backflow away from the cleanroom via the air exhaust duct. The choice of vertical or horizontal flow should be based on the amount and geometry of the items located in the work area.
The analysis of the surrounding envi ronment and air flows is key for con tamination control. For this reason, S4S, before the machines are put into operation, offers a control service in side your premises, to better optimize the air flows and the control of con tamination, thanks to a technique that analyzes the air flow and its power. Laminar flow hoods avoid particle con tamination in the filling or packag ing product operations. Laminar flow hoods are installed on existing produc tion lines. Vertical flow modules can be mounted on mobile structures and moved from one area to another. The lateral conduction of the clean air flow and the protection of the work area is achieved by means of PVC curtains or side panels.
In 2011, the company’s year of founda tion, the idea was to create a firm that, taking advantage from previous and di versified experiences in the engineer ing field in the design for third parties and in the validations in the pharma ceutical world, could expand the com pany’s know-how.
Marco Pizzi, the company’s managing director, tells us how they came into play with the desire to expand their skills to pursue continuous improve ment. Through a continuous exchange of know-how, resulting from an open and constructive relationship, encour
aging collaborations and feedbacks, they grew up and developed new skills. An increasingly creative, reactive and flexible teamwork was built up. The large, very bright, colorful and welcom ing work spaces of the headquarters im mediately convey their way of interfac ing and tackling each new project. En thusiasm, opening, listening skills, availability, flexibility as well as a solid expertise grown on field, make S4S an ideal partner for the pharma industry.
S4S deals with the construction of machines for contamination control, for pharmaceutical environments, air showers for personnel and materials and offers a whole series of related ser vices such as design, planning, basic and detailed engineering, concept en gineering, construction and commis sioning, equipment, validation, requal ification of machines and environ ments. S4S team is ready to work to offer turnkey solutions as a single a re liable provider, taking the responsibil ity and control of the order in bulk, as well as dealing only with one or more parts of it. From design to production phase, from installation to validation, S4S is ready to listen, analyze and de sign the right solution. The company follows all stages of the work, actually
behaving as if they were a department within the client company, and this al lows to anticipate critical issues by im plementing a precise and timely prob lem solving strategy. Often, there are questions, doubts, needs from the cus tomer, even during construction, which are faced through an open dialogue and constructive discussion aimed at satis fying the request and identifying, when necessary, the best possible solution. Dealing with a competent team capa ble of solving problems not previously addressed makes the difference. It is a winning and loyal approach, tes tified by the trust of customers who have kept working with the group for a long time; the relationship with them does not end with the completion of the work. We boast relationships with long-standing customers who return for subsequent projects as a result of past positive experiences. Quality is fundamental in S4S work: it means meeting all requirements, ensuring top results not just in terms of construc tion and development goals but even in terms of economic outcome, offer ing transparency in costs. The project is followed step by step, the verifi cation is addressed through internal procedures at all stages of construc tion and completed during installation with inspections and validations of the equipment installed, the customer is never forgotten. The goal remains to continue a path of growth, focusing on continuous change following requirements, devel oping new skills. This enables to come as a cutting-edge company able to an ticipate future needs in different and always new areas. By the way, S4S is constantly looking for new professional figures to be included in its staff, young people capable of integrating in to the corporate operational fabric and at the same time contributing to cor porate growth with innovative propos als and ideas. l
Piller, as a supplier of power protection equipment, is rapidly expanding its client base in India’s booming Pharmaceutical manufacturing sector.
Piller Power Systems, the glob al sustainable power technology infrastructure supplier, is rapid ly expanding its client base in India’s booming Pharmaceutical manufacturing sector.
As an established trusted part ner and supplier of power pro tection equipment to the phar maceutical sector, Piller clients include top ten companies in the India pharma industry. Both domestic and international firms with manufacturing capac ity in India rely on Piller pow er conditioning, UPS protection with battery backed and kinetic energy storage solutions which are configured for specific ap plications in pharma manufac turing.
Shailendra S Bais, Piller India Director, says: “India is known as the world’s pharmacy and forecasts for manufacturing growth prove it. India’s domes tic pharmaceutical market val ue is expected to reach US$42 billion in 2021, likely to reach US$65 billion by 2024 and fore cast to expand to US$120-130 billion by 2030. Piller focuses on establishing long term part nerships because it understands that building a facility and pro viding vital utility infrastructure for pharmaceutical manufactur ing represents a company’s sin gle biggest cost and is heavily regulated from the outset.”
The number of deployments of Piller’s latest UB-V electronical
ly coupled UPS at Phar maceutical manufacturing sites in India is grow ing. The UB-V Series, built on the renowned reliability of UNIBLOCK™, is a highly flexible elec trically coupled UPS sys tem. The UB-V provides from 1MW to 3.24 MW of UPS protection in one single-module. UB-V UPS operates equally well at low and medium voltage. The growth of internation al Indian players such as Zydus Cadila, Cadila Healthcare and Sun Pharmaceuticals, Alembic Schott Glass sets alongside big investments in new manufactur ing capacity by the global phar maceutical giants such as Pfiz er, GSK, Sanofi, Abbott Labora tories, Merck and Roche. “Drug manufacturing in In dia is undergoing rapid expan sion. Domestic and internation al firms with manufacturing ca pacity in India use Piller rota ry power generation, back up, battery backed and kinetic ener gy storage solutions,” said Bais. Inside India’s booming phar maceutical base the stakes could not be higher. Already the world’s largest producer of generic drugs and maker of half the world’s vaccines, India has 3,000 drug companies and 10,500 manufacturing units. India is already the largest pro vider of generic drugs global
ly and forecasts point to ma jor expansion in manufacturing base capacity. The Indian phar maceutical sector supplies over 50% of global demand for vari ous vaccines, 40% of generic de mand in the US and 25% of all medicine in the UK. Globally, In dia ranks 3rd in terms of phar maceutical production by vol ume and 14th by value. India’s new pharmaceutical pro duction capacity can rely on clean, stable and conditioned power provided by Piller’s scal able, flexible power infrastruc ture.
More than 7000 kinetic energy storage devices and over 6000 high power UPS units installed in the world
Piller was founded in Hamburg, Germany in 1909 by engineer Anton Piller. Employing around 1000 people worldwide, Piller is
headquartered in Osterode, near Hanover, Germany, with subsid iaries across Europe, America, Asia and Australia. Piller occu pies a unique position, being the only company to produce both types of electrically cou pled UPS technologies and with kinetic energy storage or bat tery options. The company al so manufactures aircraft ground power units, 50/60Hz frequen cy converters, static trans fer switches and specialist ma rine generators. With more than 7000 kinetic energy storage de vices and over 6000 high pow er UPS units installed, Piller has more than 300 service personnel taking care of clients across 24 countries. The Piller group is a wholly owned subsidiary of the multi-disciplined global UK en gineering and industrial group, Langley Holdings Plc. In 2016, Piller acquired Active Power Inc., the flywheel energy stor age specialist.
Gli eccipienti e le materie prime distribuite da Faravelli ti aiutano a raggiungere la formulazione farmaceutica perfetta, proprio quella che stai cercando: funzionale, sicura, efficace, performante.
La formula che rende ogni cliente soddisfatto e felice.
“Accompagniamo con competenza globale e sensibilità locale i nostri partner verso scelte innovative, per formulare il futuro con ingredienti e soluzioni affidabili e sostenibili”.
Nuova Guseo has specialized in the design and manufacture of fixed body mixers, generally made from a stationary container, with variable geometric shape within which the content is moved from rotating parts, the mixing elements.
Nuova Guseo has estab lished itself over the years by designing and manufacturing plants and equipment for fine and ex
tra fine grinding, mixing systems, devices for solids handling, con tainment systems for the treatment of highly active products. Today the company is a reliable point of reference in the field of sol id handling and containment, main ly for the chemical, pharmaceuti cal, food and cosmetic sectors.
Detail of the ribbon agitator
From the theoretical point of view the mixing can be defined as an op eration that allows to obtain ho mogeneity in a polyphase system (ex., dust compounds, emulsions, suspensions). the mixing can be applied to systems solids (pow ders) or liquids (to obtain solu tions, emulsions, suspensions). The result of a mixing process de pends on variables related to the
substances to be mixed, from the characteristics of the mixer used and the mixing conditions.
Regarding the character istics of the substances (density of powders, form of particles, humidity, friability, flowability, the characteristics of mixers (type of mixer, dimensions and shape of the mixer, construc tive characteristics), the mixing conditions (order of adding substances, speed and time of agitation, volume occupied by powders), there are different types of mixers that can group into two categories: 1) fixed body mixers rotating; 2) body mixers. Nuova Guseo has specialized in the design and manufacture of fixed body mixers, generally made from a stationary container, with vari able geometric shape within which the content is moved from rotating parts, the mixing el ements.
These configurations guarantee a good mixing, ease of loading and unloading, and possibility of mix ing powders and liquid additives. The main types of fixed body mix ers are horizontal mixers and ver tical mixers.
Horizontal mixers are widely used for several applications in mining, food stuff, chemical and pharmaceutical industries. The series MG RB con sist of a U-shaped horizontal tank flanged above the lid, equipped with
loading and inspection doors, with single shaft ribbon screw and are configured for batch-type mixing. Mixing takes place by means of a ribbon agitator that causes product to move following crossed lines, conveying it to the centre of the containment tank to facilitate its unloading, obtaining high quality mixtures and maintaining the phys ical properties of the product.
Due to the proven effectiveness of the mixing action, this equip ment guarantee a reduced overall height and an easy maintenance and cleaning activity, thanks to the total opening of the lid. above the mixing tank.
In the lower part there is the dis charge mouth with a pneumati cally operated pad valve to avoid dead spots of unmixed material. The RB mixers series can be man ufactured in the single or double shaft version and with usefull vol umes up to 10,000 liters.
By adding a “V” shaped hopper, se ries MG TS, it is possible to work continuously avoiding discharging intervals.
The horizontal mixers can also be implemented with product trans fer devices at loading and unload ing and can be easily integrated into complete process lines.
The vertical mixers, series MG VP, consist in an upper cover, suitable to support the drive unit, flanged to the upper part. On the upper cover are allowed at least the charging and inspection doors, this one protected by limit switch that does not allow starting when door is opened.
Conical-shaped body in rugged con struction at the bottom of which is placed the discharging mouth equipped with discharging valve. These mixers are widely used es
pecially in the chemical-pharma ceutical field, and are character ized by the total discharge of the processing batch from the bottom of the mixing tank. The simultane ous motion of suitable transmis sions allows the agitator to per form two movements: to rotate on its own axis and to orbit along the inner conical vessel wall.
In this way the agitator, which generally consists in a worm screw, conveys product from bottom to the top and creates a horizontal motion flow.
Besides, the conical shape of the mixing vessel allows to obtain a different motion speed of parti cles which depends on their dis tance from the bottom where par ticles moves more speedily.
Vertical mixer grants particular advantages:
• low power consumption because the mixing screw does not act on the whole product simultaneously;
• dust seals not immersed into the product;
• minimum heating of substances;
• soft mixing action;
• total emptying without product retention;
• easy to be thoroughly cleaned.
In relation to the volume of the mixer and the application field, two different configurations are available: with mixing reel with out bottom support (up to a useful capacity of 2000 liters) and with a reel supported on the bottom (from 1000 liters up to 7000 lit ers useful capacity).
The vertical mixers can be implemented in various ways with spe cial washing devices, nozzles for introducing liquid additives, with product transfer devices at loading and unloading, bagging and weigh ing systems and can be easily inte
grated into complete process lines. Similar to the series VP, the series VPS enables the best ratio of over all dimensions/loading volume thanks to their truncated-conical shaped body.
A shaft on which a conical spiral is applied causes mixing movement.
The spiral brushes the inner walls of the vessel and conveys product from bottom to the top.
Integral with the same shaft a sec ond central spiral conveys product from the top to the bottom inten sifying mixing and favouring nec essary times reduction.
The slow movement of the mixing paddle, completely driven from the vessel outside, makes this mixer suitable for treatment of fragile and heat sensitive products.
The VPS model can be also used for treatment of dry product (both in powders and in granules), wet or sticky materials, as well as low or medium viscosity liquids.
The vertical mixer can be also con figured for vacuum drying pro cesses series VP/ V, they are de signed and manufactured for the treatment of substances with sol vents or water, combining the ac tion of mixing with that of dry ing, For this purpose, the verti cal dryer is equipped with an in sulated filter, heating/cooling jacket, vacuum-resistant product discharge valve and are config ured to be integrated into a spe cial process line: the unit has to be implemented with heating/ cooling group, pre-condensation group, vacuum pump, post con densation-group.
For use in classified areas (with the presence of hazardous gas and/or dust mixtures) the equip ment is manufactured in compli ance with the 2014/34 EU Direc tive (ATEX). l
BEA Technologies offers solutions for the microfiltration of liquids and compressed gases dedicated to the specific needs of the life science industries: Pharmaceutical, Medical and Cosmetic.
Pharmaceutical companies and those involved in life science have gone beyond traditional business models and are oper ating at worldwide scale nowa days. The challenges for the pro duction of new medicines and active substances are requir ing increased research and more strict cooperation with suppliers to design and realize new pro duction lines and more flexible and efficient new equipment. BEA Technologies is aware of these new demands and put its knowledge at disposal to reach the quality and safety levels re quired by current regulations. The filtration technologies pro posed by the company are final ized to reach the best Quality –price rate for sterilization and clarifications of products, ac tive substances for pharmaceu tical use and utilities.
BEA Technologies offers solu tions for the microfiltration of liquids and compressed gases dedicated to the specific needs of the life science industries: Pharmaceutical, Medical and Cosmetic.
The expertise in typical appli cations such as fermentation, sterile filtration of liquids, fil tration for injectables, filtra tion of process fluids and gel atins has allowed the develop ment of products with specific performances tailored to needs of industry and laboratory ser vices and a highly professional technical assistance.
Each product is the result of con stant technological research, of the careful selection of materi als, of a controlled production process, and it is verified and accepted after specific tests. BEA Technologies is organized
to provide: complete traceabili ty of product; validation guides for each filter element; compli ance with USP-class VI, USP wa ter for injection; wide range of filtering membranes PES, N66, PVDF e PTFE; interchangea ble configurations and EndCaps; customization of filters and housing, guarantee of high quality as the Production pro cess is entirely Made in Italy.
An innovative line of filter ing systems designed to as sure safety in High Potent API (HPAPI) applications. The sys tem is made to achieve double containment, with the filter el ement contained in a capsule, enclosed in a second steel or plastic housing. A practical and effective solution to replace in sulators.
Complete line of capsules and filter elements
BEA Technologies offers a com plete line of filter elements for all the needs of the Life Sci ence industry, which includes the main types of pre-filters and innovative filter elements in nano- fibers, available car tridge and with the most widely used interchangeable GND caps. The filter elements are provided with the necessary documenta tion: validation guides, to com plete the Regulatory Files and marked with a barcode on the labels for a quick and safe recognition.
To select a manufacturer as a supplier, with a high technical
skill and a structured organi zation makes the difference in critical moments. It means to have certified pharma products, checked and in compliance with the regulations, but also being able to count on the advice of an expert partner. Essential el ements for companies accus tomed to face future scenarios with a “focus” to “risk base thinking” that really want to be prepared for the challenges of the future markets.
A fast intervention makes the difference when it comes to as sistance.
That’s why BEA Technologies of fers a team of qualified experts, able to support companies both in the selection phase and in the after-sales.
Services available to the cus tomer: filtration tests in the in ternal Lab an field tests at the customer’s site to size the sys tem and optimize the filtration process; support in the valida tion of processes, with custom izable specific validation pro tocols; international techni cal assistance; fast and relia ble delivery times, confirmed at time of order; customer service available for all commercial re quirements.
filtration
Legislative constraints, typical problems, process complexity: each application has its own characteristics, which must be carefully considered in the selection phase of the most suit able filtration system.
For each industry and applica tion of the life science sector, BEA Technologies suggests one or more dedicated products.
GUAFLON™ ULTRA is ultimate certi fied sealing solution from Fluortecno for flanged couplings that require electric conductivity. This unique PTFE (poly-tet ra-fluoro-ethylene) matrix allows electrostatic charges to freely move from the inner white layer in Guaf lon SBTM to the outer layer in Guaf lon EXDTM thus avoiding the creation of sparks. Guaflon ULTRATM avoids the need of expensive and hassling earthings for piping and equipment; still, this special seal segregates the process fluid from any contamina tion of black particles.
Characteristics: inner white core in Guaflon SBTM (PTFE charged with Barium Sulphate - modified and sta bilized formula); approvals and cer
tifications FDA 177.15.1550 and UE 10/2011.
Outstanding chemical resistance: suitable for all chemicals within the range PH 0 – 14; suitable for use in Food&Pharma environments outer re inforcement in black, conductive and antistatic.
Mechanical properties: The exclusive isostatic and simultaneous moulding of the two materials provides the seal with a natural, multidirectional stability thus granting an excellent sustainability of thermal cycles and a superior resistance to permeation due to the barrier effect of the dou ble sinterization.
Electrical Properties: all laboratory trials have shown that GUAFLON UL TRA gaskets, when compressed with
variable clamping, possess a superfi cial resistivity of 30 - 130 Ohms thus granting the equipotentiality of the two ends.
Within the production process, the electric pump is the less complex and flashy element, but it actually repre sents its heart, as it pumps into the plant the product to be processed or as it collects the finished product to be sent to packaging machinery. For over 50 years, Bruno Wolhfarth has been meeting the needs of its customers operating in the food, pharmaceutical, and chemical industries, offering us er-friendly, easy to maintain and clean solutions, that at the same time are reliable and long lasting. Plant manu
facturers and end users know the im portance of the pump within the pro cess, waiting either for a spare part or a maintainer for repair. Wolhfarth’s pump strong point is the simple disassem bling and maintenance. The pump can be easily disassembled and reassem bled even when installed by unskilled personnel. Either stainless-steel 316L or titanium for pumps working with corrosive acids are used. Machining from the solid bar, without casting or welding, guarantees the durability and the surface finish, also complying with
the strictest standards in the food and pharmaceutical sectors. Flexible elas tomer impeller enables a strong suc tion and the most powerful models can treat gently both creamy products such as yoghurt and the thickest ones, such as honey and jams. The ATEX-compli ant version is available for use in areas at risk of explosion. The impeller and gasket materials are suitable for use in contact with food in compliance with current regulations. For detailed infor mation and offers, please write to: in fo@wolhfarth.it.
The series TCHM of Pompe travaini consists of mon oblock single-stage cen trifugal pumps with closed impeller. Built according to ISO standard 2858 and 5199 these sturdy and reliable pumps are available at low price coupled with the easy operation of monobloc units. The series TCHM is of the highest quality, with at tractive prices to the chemi cal and industry in general.
Technical Details:
• The connections are flanged to UNI2223-2229 NP16 standard. Liquids up to 140 °C can be han
dled. These pumps can cov er a wider range of duties and applications than or dinary monoblock pumps and those pumps which are stamped out of sheet metal.
• Shrouded type impellers are suitable for handling either clean or contaminat ed liquid.
• The pump casings, impel lers and casing covers are the same as for TCH series. This reduces inventory costs and the provision of spare parts at reduced prices.
• Capacity up to 500 m3/h and head up to 10 bar. Thanks to new acquisitions, international sales offic
es, and a broad network of agents and distributors, Pompetravaini has become a global authority in the pump industry that exports its products worldwide to over 80 countries with the guarantee of a solid experi ence of more than 90 years of history.
real digital trans formation is possi ble only with every stakeholder’s par ticipation”. Davide Ferrara, Sintetica Digital Affairs Cor porate Executive Director, was invit ed as speaker to “Digitalization and Pharma 4.0 in Life Science” event, organized by SPS Italia and ISPE Ita
lia on April in Milan. He gave his take to the discussion by communicating to the audience his direct experience for the creation of a 4.0 roadmap in a medium-sized company. To do that, Ferrara did not just talk about tech nologies and systems, but above all about digital awareness and focus on
people. “Digital is the enabling technology, but what matters is to transform the way of do ing business, the organization, the processes. And this can be done only by involving all departments”. Dur ing the event, that took place in the wide spaces of Bovisa’s MADE Com
Sintetica is one of the most advanced medium-sized pharmaceutical companies in digital transformation. The IT Corporate Executive Director of the Swiss Company took part to SPS Italia and ISPE Italia round table about “Digitalization and Pharma 4.0” and said: “Active involvement of People is important as much as technology”.
Alessandro Bignami
petence 4.0, we had the opportu nity to discuss some of the topics touched upon in the presentation with the manager.
Davide Ferrara, can you briefly in troduce Sintetica?
Sintetica is a medium-sized compa ny based in Canton Ticino, that cel ebrated 100 years in 2021. It has a long and successful history in the field of pharmaceutical research. We produce aseptic drugs and are lead ers in the production of injectable solutions such as local anesthetics and analgesics, products therefore intended primarily for intensive care and for the operating room. These drugs are mainly used by anesthe tists and health workers in hospitals. Three years ago the company was ac quired by a fund that further broad ened the growth outlook and laid the foundations for a new phase of accel eration leveraging digitalization and innovation.
What’s your size today?
We’re more than 300 people overall, spread in four main legal entities: two in Switzerland, one in Germa ny and one in UK. Our products are distributed worldwide with a mod el that provides both a “Business to Consumer” channel with direct sales to hospitals and pharmacies and a “Business to Business” channel, where we operate thanks to multiple strategic distribution partnerships.
When did you join the company and what skills did you bring?
I joined Sintetica about three years ago, after twenty years of experience in the pharma industry with one of the top management and strate gic consulting firm. I spent major ity of my career supporting or lead ing transformation programs world wide with many pharma multination
al companies. In Sintetica, I was giv en the task to coordinate the whole digital transition program as Corpo rate IT Director. I found a compa ny strongly focused on people’s val ue and innovation, two elements in tune with my approach to digitaliza tion. Technology plays a key role in terms of digital transformation pro grams since it can enable change and accelerate growth, but the empha sis must be placed on transforma tion. Previous experiences taught me that when people are not really in volved and fully engaged in this kind of large transformation program, it is difficult to be really successful. The ability to overcome change re sistance and the experience in deal ing with natural defensive attitude
towards new technologies and in novation becomes fundamental. From this perspective, it is crucial to support the program with con crete initiatives aimed to facilitate the change not limiting them just to communication or training activ ities. It is necessary to intervene deeply on the way of working, to facilitate continuous alignment to wards company objectives, stimu late a more and more rooted digi tal awareness. These aspects aren’t less important than technologies and are even more complex than technologies, for which we can at least rely upon system integrators. In the end, what counts are a clear vision and the capability of inte grating technical and business skills
“We have set an extremely ambitious program considering the systems and technologies we are implementing and the timescales we have set to achieve the individual objectives. 2022 will be a turning point”
throughout all the digital transition program steps.
How far did you arrive with your digital transformation journey?
We are just over halfway. We have set an extremely ambitious pro gram considering the systems and technologies we are implementing and the timescales we have set to achieve the individual objectives. 2022 will be a turning point, as four of the five initiatives we have launched in this transition phase will be fully operational. It is a first and important program checkpoint, which can already generate an im portant breakthrough. We expect to integrate all the company process es on a single integrated platform. It is an evolution that I consider even more significant after listen ing to ISPE Italia’s survey, accord ing to which many companies, sim ilar to ours in size, are still wonder ing how it is best to move on the digital issue.
How did the pandemic influence your path?
It was not an easy challenge. In some ways, it accelerated the change that we had already start ed. For everybody, it was a dramat ic period, but I also like to look at the positive effects for the compa ny’s evolution. I think for instance about the lesson we learned about smart working. Today companies are realizing that home work is not incompatible with business objec tives and it can even promote an increased productivity.
Of course, it cannot involve any business task and must be analyz ed also according to local regula tions, but it proved to be a virtuous tool. Another inheritance of this terrible emergency features a more commercial nature and regards new
ways to do business and the possi bility to involve customers through digital channels. These experienc es will bear fruit even when the pandemic will be completely be hind us. Companies that, in front of these changes, proved to be more reactive over the next years will be seeing an increase in their compet itive advantage.
Does the digital offer peculiar opportunities for the pharma in dustry?
Yes it does, since the pharma indus try is subject to regulations that can not be compared to the ones of other
No, it doesn’t, if this system of rules offers a real improvement towards product quality, process transpar ency and integration. On the con trary, regulation is appreciated by the most virtuous companies and, thanks to the fat it so strict, it pro tects the patient and subsequently the pharma manufacturer. Look at counterfeiting. The ISPE survey itself reveals that about one out of five drugs purchased on the inter net is counterfeit. This jeopardizes the patient’s health and the cred ibility of the industry. And it ex plains well why every step towards more controlled and traceable pro cesses can only be viewed favora bly by both industry and clinicians community.
What do you expect over the next few months?
industries and that unavoidably in volve a specific approach to digital transformation, that must take in to account of validation procedures and test protocols Industry specific.
I think for example about the need of transparency, data integrity and compliance in general. With this in mind, technology is also a valid al ly to respond to the requirements of the complex regulatory appara tus that regulates the industry and is constantly evolving.
There’s the need of complying with regulations and validating every innovation: doesn’t it curb change towards new technological and IT systems?
We are living a very dynamic phase of our company history and in this year, several initiatives will bring some initial results. We aim at be ing pioneers in digital transforma tion, at least among the pharma ceutical companies of our size. The whole company management team is involved in this transition and in the coming months, with comple tion of the various initiatives, ma jority of company’s employees will be involved as well. We tried to overcome the usual way of working according to which departments express business requirements and the IT area selects and develops appropriate solutions.
All of them are an integral part of digital evolution and are invited to feel it their own and to appreciate its benefits, so that to give an active contribution and feeling like actors of change. I’m convinced that only a wide participation and engagement allow to realize the potential of dig ital transformation. l
“In Sintetica, all are an integral part of digital evolution and are invited to feel it their own and to appreciate its benefits, so that to give an active contribution and feeling like actors of change”
Tecnologia, esperienza e innovazione per la rigenerazione degli oli lubrificanti, la purificazione dei solventi e i servizi ambientali per l’industria.
25 siti operativi e più di 850 persone: soluzioni sostenibili per oltre 35.000 clienti in più di 60 Paesi.
Itelyum Regeneration / Itelyum Purification / ImTraS / Itelyum Ambiente / Aeco / Amsia / Area / Carbo-Nafta Ecologia Castiglia / Centro Risorse / De Luca Servizi Ambiente / FEr.Ol.Met / Idroclean / Innovazione Chimica / Intereco / Keoma Labio.Lab / Neda Ambiente FVG / Riraee / Rimondi Paolo / SAM / Sepi Ambiente.
ITELYUM:
il nuovo nome dell’economia circolare.
An innovative rotating cleaning nozzle with a special flat fan design developed by Lechler, saves time and money through uniform co verage when cleaning tanks. In a series of tests, it was capable of reducing the clea ning time by 40% and fresh water consu mption by 30% in comparison to conventional spray balls.
re are mechanics, chemistry, time and tem perature (Sinner Circle).
The cost associated with this nozzle is paid off quickly, especially when you compare the significant reduction in lower operating costs. More efficient cleaning systems will also
Reliable cleaning processes reduce the risk of claims Hygiene is absolutely essential to ensure the quality and uniformity of goods that are manufactured, filled and packaged. In dustrial cleaning processes such as Clea ning in Place (CIP) provide a long-term con tribution in maintaining the required hy giene levels and protecting manufacturers against expensive claims which can dama ge their reputation. The required cleaning jobs must be performed quickly and more or less in between production. Longer downti mes result in higher costs.
With modern cleaning processes, the focus is no longer on effectiveness but efficien cy. Optimally matched factors achieve the desired cleaning result with the economical use of resources. The main four factors he
become increasing important in production plant as well in the future. The goal is to show how the cleaning result is affected by gradually increasing the operating pressure and the size of the tank. The results will be used by Lechler for further optimization of the rotating cleaning nozzle.
In order to increase process reliability even further, the rotating cleaning nozzle can al so be optionally combined with a rotation monitoring sensor.
Renowned plant manufacturers have pla ced their trust in the nozzle technology and know-how of Lechler company for many ye ars now. Reduction in the costs for energy, natural resources and additives is an impor tant argument in the industry.
Lechler never focuses on just the individual nozzles but always on the overall process.
Endress+Hauser continues on the path to growth. Over the past five years the number of employees at the Reinach lo cation in the Swiss canton of Basel-Landschaft has grown by 20 percent to more than 2,000. At the same time, the number of units pro duced has significantly increased and
the digital solutions portfolio has ex panded. In order to simultaneously meet the new demands of the work environment, vocational training posi tions and digitalization, the measure ment and automation technology spe cialist invested 60 million Swiss francs in the Reinach campus. After beginning work on the foun
dations in 2019, Endress+Hauser will celebrate the opening of the nearly 150-meter-long building in Reinach on 1 July 2022. The construction plan included the use of available prop erty and an existing building locat ed on Kägenstrasse. The new facili ty, which boasts more than 25,000 square meters of space, equivalent to around four soccer fields, was built with roughly 19,000 cubic meters of concrete and 2,200 tons of rein forced steel and other materials. The new building is home to En dress+Hauser Flow, the product center for flow measuring technol ogy, as well as Endress+Hauser Dig ital Solutions, which is responsible within the Group for all issues
re
For Endress+Hauser, the expansion of the campus in Reinach is a commitment to Switzerland as a business location. The company is creating more space for the production of flow measurement technology and the development of IIoT solutions.
lated to digital communication and automation solutions. The first wave of employees has already moved in to the facility.
With the new building, Endress+Haus er is responding to the ongoing de mand for high-quality instrumentation and solutions for Industrial Internet of Things (IIoT) environ ments in the process industry. Liq uids and gases must always be mon itored, measured and settled with a high degree of accuracy. This is be ing driven, among other things, by increasingly strict government reg ulations and growing requirements on quality and environmental pro tection around the world. Endress+Hauser Flow has reacted to this development, expanded its portfolio and doubled the number of units produced over the past decade. The consequence is continuous ex pansion of the production capacity and the creation of additional jobs. With the most recent developments,
the family company is making a clear commitment to Reinach and the Ba sel region where the Group is firm ly rooted.
As a result of the expansion, around 1,050 employees will move across all buildings. The additional space will create more collectively used workspace. “In the spirit of ‘New
Work’, we are implementing activi ty-based working. Different work ar eas will be available for different ac tivities, meaning that our employ ees can choose the space best suited to their individual tasks,” says Mirko Lehmann, Managing Director of En dress+Hauser Flow. Special coworking zones such as In novation Labs or project zones fur thermore offer different departments
Among
The heart of the heating system is a stratified tank that stores waste heat
the opportunity to collaborate on longer-term projects. Employees can choose between a permanent or shared desks. Bright, friendly spac es and a modern infrastructure have a positive impact on the work envi ronment as well.
Learning-conducive training environment
For Endress+Hauser, laying the ground work for the future also means invest ing in the employees of tomorrow. The new building brings training and edu cation into the heart of operation and offers sufficient space for areas con ducive to learning with workshops, labs and training rooms, thus allow ing an increase in the number of ap prenticeship positions and vocational careers. To date, 43 apprentices have been trained in eight areas. Beginning in August, nearly 50 apprentices will be trained in 11 vocations. This num ber is expected to grow over the next five years.
Around 4,000 annual visitors can look
forward to the new plant tour and hos pitality concept. This concept con sists of a redesigned reception ar ea and a new visitor center includ ing “Flow Experience”, an integrat ed 2,000-square-meter area where the Endress+Hauser brand and flow instru ment portfolio can be experienced be fore taking a tour of the plant.
Sustainable energy concept Endress+Hauser is furthermore using the new building to align its ongoing business growth even more closely with its ecological and social re sponsibilities. In light of the goal of the Endress+Hauser Flow sustain ability strategy to operate its build ings in Reinach in a CO2-neutral man ner by the year 2030, high value is being placed on climate-friendly facilities management. As part of the energy concept, for example, waste heat is stored in a stratified storage tank for warm water and then used for heating. A comprehensive ener gy monitoring system using instru
ments from the company’s own portfolio also helps to continuously optimize op eration of the buildings. Large photovoltaic systems were installed on the roof of the new building, which boast a peak capacity of 365 kilowatts, enough to cover the annual electricity needs of around 75 sin gle-family homes. In Rein ach, Endress+Hauser now has photovoltaic systems covering more than 3,700 square meters with a total peak capacity of roughly 1 megawatt, making the company one of the larg est solar power producers in the Basel region. The roof is also home to two bee colonies and various bee-friendly flowers, a project that contributes to the preservation of bi odiversity as these small insects are considered central Europe’s most im portant plant pollinators.
Measurement and automation technology for process and laboratory applications
Endress+Hauser is a global leader in measurement and automation tech nology for process and laboratory applications. The family company, headquartered in Reinach, Switzer land, achieved net sales of approx imately 2.9 billion euros in 2021 with a total workforce of more than 15,000.
Endress+Hauser was founded in 1953 by Georg H Endress and Ludwig Haus er. Ever since, the company has been pushing ahead with the development and use of innovative technologies, now helping to shape the industry’s digital transformation. 8,600 pat ents and applications protect the Group’s intellectual property. l
Terranova pneumatic and electronic instruments for automation and control can be system integrated into turn-key systems for various industrial sectors.
TERRANOVA® engineers and manu factures pneumatic and electronic instruments for Automation and Control, which can be system in tegrated into turn-key systems for various industrial sectors: Chemi cal, Oil & Gas, Pharmaceutical, Fo od, Power and Naval. ISO9001, ATEX, IEC-Ex, PED and SIL certifi cations guarantee the products to be compliant with the up-to-date technical standards. The consoli dated activity of Terranova in Italy is integrated by a growing export activity in many foreign countries, managed by an international ly selected and well-trained Sales Network. Terranova products are available in standard (Carbon Ste el, Low temperature Carbon Steel, 316 & 321 Stainless Steel,) and special alloys (Hastelloy C, Duplex, Monel, Titanium, Inconel, etc.) all compliant to NACE latest require ments. The product range is inclu ding pressure, differential pressu re, level and temperature electro nic transmitters. The working prin ciples of transmitters are also quite wide to better fit the application:
torque tube, buoyancy, hydrosta tic pressure (piezoelectric, ceramic and capacitive) & resistive for the measure of level or interface level; piezoelectric, ceramic and capa citive for the measure of pressu re and differential pressure, ther mo resistance or thermocouple for the measure of temperature.
Torque tube level transmitter
SST50 and SST70 series SMART le vel transmitters are microproces sor based instruments that com bine the analog signal advanta ges (4-20mA) together with the flexibility of digital communica tion (HART®, FF, PA) protocol. The transmitter series SST70 measures liquid levels, density and interfa ce levels in closed or open vessels. It converts buoyant force exerted by a displacer immersed in a li quid to a proportional current si gnal thanks to a mechanical for ces transmission device based on a torque tube and a piezoresisti ve sensor.
Temperature transmitter
SST52 and SST72 series SMART temperature tran smitters are able to ac cept 3 wires Pt 100 ohm resistance thermometers and total accuracy is de pending on class of the sensors utilized such as DIN A, DIN B, 1/4 DIN, 1/10 DIN, etc. Based on these readings the mi croprocessor genera tes the 4-20 mA analog output “two wires system” and displays the pressure measurement on the LCD. Some of the main characteri stics of this microprocessor-based transmitter, are: wide rangeabili ty; automatic temperature com pensation; digital communication using HART, PA or FF protocol.
Differential pressure transmitter
SEX71A current to pres sure converters are ba sed on a force balanced system with electronic feedback: measuring the output signal, by means of a piezoelectric sen sor, and computing it with dedi cated SMT electronics, a reliable and high perfor ming instrument is obtai ned. An extraordinary ac curacy less than 0,25% (comprehensive of non linearity, hysteresis and repeatability er rors) is reached by this converter, 4 times better than what typical ly found on the market. The con verter is provided with intrinsic sa fety approval.
Pneumatic indicating controllers, regulators, recorders
Differential pressure transmitters
SST57B and SST7TB series SMART differential pressure transmit ters can be remotely configured by a universal hand-held termi nal (HHT) or by a PC with a de dicated interface and Terranova software. Moreover, it is possible to locally configure the instru ments (zero and span) by me ans of 2 push buttons and to di splay the data on the wide LCD display. The SST57B transmit ters measure differential pres sure with spans from 1,125 to 20000 mbar with a static pressure up to 100 bar. Thermal drift is compensated using the tem perature signal generated by a PTC thermistor integrated in the sensor itself.
Ideal for the control of temperatu re, pressure and level, in industrial or process plants as the indicating controller is used for control of li quid, gaseous or vaporous media. The instrument senses the tempe rature, pressure or level of the mea sured medium directly, displays the operating value, compares the me asured variable with the set point and puts out a pneumatic standard signal of 0,2 to 1bar or 3 to 15psi. This output pressure actuates final control element, the pneumatic valve. Four control forms are avai lable: ON-OFF, Proportional + Inte gral + Derivative. The units could be also used for remote control of process operations as pneuma tic transmitter (output 0,2÷1bar or 3÷15psi) or receiver controller (in put 0,2÷1bar, 3÷15psi).
The chemical industry is pro ducing a huge variety of chemicals by using various processes. Most of the time, however, basic chemicals are reacting with each other to obtain the desired finished chemical. While some chemical reactions require heat in order to take place (endothermic), some others, on the contrary, release a fair amount of heat once initiated (exothermic). Because their process
es require thermal flexibility and sta bility, heat exchangers are essential for chemical and petrochemical com panies. Heat transfer systems used in the chemical industry can be based on different concepts and technologies and use a wide range of heat transfer fluids. The majority of chemical com panies will use mineral oils or water to carry, dissipate or exchange heat in their processes. However, regardless of the thermal fluid in use, heat trans
fer systems will lose efficiency over the years because of fouling. Foul ing is the accumulation of undesira ble material such as varnish, sludge, algae, scale, insoluble salts and min erals on the internal surface of heat transfer systems. The following article provides more information on fouling and suggests how to prevent this phe nomenon from causing efficiency loss in heat transfer systems.
For all of the challenges heat transfer
Losing heat? Can’t cool it down? Seems like the heat transfer system needs a tune-up. Time has come to take back control of the heat exchangers and cooling towers.*Global Market Manager Chemical Industry, Klüber Lubrication Photo ©shutterstock / Red_Shadow
systems can pose, the tribology spe cialist Klüber Lubrication has devel oped highly efficient solutions which can help to restore the full efficien cy of water circulation and cooling systems.
Get more out of oil circulation systems
Regardless of whether they are designed to heat or cool down process es, most oil-circulating heat transfer systems in chemical and petrochem ical facilities still use group I miner al oils in this heavy-duty application. Group I mineral oils are derived from crude oil. The refining process uses a solvent which leaves impurities and hydrocarbon molecules of different sizes in the mixture. Some heat trans fer systems can use up to a hundred thousand liters of oil as a transfer me dium, which makes group I mineral oils with their affordable price attrac tive for chemical companies. In most cases, heat transfer systems are far from being perfectly designed. In the majority of the systems, the oil is subject to considerable stress, due to an intense localised heating source in combination with low flow velocity. The oil can also come into contact with the air in the expansion tank, causing it to oxidize and de grade faster. Group I oils contain un saturated hydrocarbons and asphal tene components that react with ox
ygen, provoking degradation at high temperature.
Pushing group I mineral oils to their performance and service life limits in heat transfer systems will most like ly lead to varnish or carbon build up throughout the circulation sys tem, which will definitely cause foul ing and over time affect system effi ciency. The tribology specialist Klüber Lubrication is well aware of the chal lenges heat transfer systems can rep resent for chemical companies, and has developed a comprehensive range of products and solutions for this ap plication. The highly refined and hy drotreated base oils used in these products offer much better stabili ty at high temperature and make ex tended service life possible.
Meeting the requirements perfectly Modern heat transfer systems are op erating in harsh conditions and may require a special thermal fluid or spe cial compliance features such as NSF H1 registration for incidental con tact with food. Technology advance ment in heat transfer fluids has re sulted in consumers today having a wide range of options to choose from according to their needs. Ther mal fluids based on different chemis tries like polyalphaolefin, polyalky lene glycol or silicone can show nu merous advantages in certain appli cations and could be the right alter native where conventional mineral oils are not suitable.
Detailed analysis, monitoring and maintenance
If you have recently noticed damage caused by a group I mineral oil to your system, and realized how poor the ef ficiency of your heat exchange sys tem has become over the years, you should know that a suitable cleaner/ conditioner for example from Klüber Lubrication can restore the system’s efficiency without the need for dis mantling or prolonged shutdown. Ef ficient, headache-free operation of heat transfer systems begins with a
Limestone deposits, usually composed of calcium and magnesium, are a plague on the operational efficiency of air compressors, heat exchangers, vacuum pumps, boilers, cooling towers and other equipment in touch with water (Photo ©shutterstock / High Simple)
If not properly treated, sediments, sludge and deposits that accumulate cause a loss of efficiency and increase energy consumption. In the photo beside washing and after cleaning the encrustations and rust with chemicals (Photo ©shutterstock / Paradorn Kotan)
good oil monitoring program. Just like blood testing can be useful to analyse health issues, an oil sample from the heat transfer system can reveal crucial information to help prevent eventual failures, safety issues, and even fires.
No tolerance for intruders in water circulation systems
For processes where the heat is not that critical, or where cooling is need ed, most chemical companies will rely on water circulation systems. Fouling also occurs in water circulation sys tems, as non-distilled industrial wa ter contains mineral salts that can
Scale deposits, usually calcium and magnesium compounds, affect the operating efficiency of air com pressors, chillers, exchangers, vac uum pumps, boilers, cooling tow ers and other water-wetted equip ment. If not properly treated, sed iment, sludge, and scale building up in the recycled water leads to a loss of efficiency and increases energy consumption. Poorly maintained systems can also harbor legionella bacteria, which pose a health risk to those working near such equipment. Every year, the chemical industry loses billions of dollars in revenue
bring it back to top operating effi ciency. Klüber Lubrications offers a complete range of high-performance descalers, which are enhanced with wetting agents, corrosion inhibitors and degreasing compounds. These are designed to penetrate and re move encrusted limescale, rust, dirt and corrosion byproducts from wa ter-wetted inner surfaces of commercial and industrial processing equip ment. Some high-technology des calers also contain active dyes that changes color in order to let the op erator know when action is required. However, not all descaler chemistries are suitable for all kinds of metal sur faces. For example, special attention has to be paid to electroplated and aluminium surfaces, as tradition al descalers based on mineral or or ganic acids could attack and damage these surfaces and components. It is therefore advisable to contact a spe cialist like Klüber Lubrication before cleaning a water circulation system. The tribology expert provides techni cal service, develops efficient clean ing procedures and can even assist maintenance teams on-site in clean ing operations.
bond to metal surfaces. The differ ence between water and oil circulat ing systems is the fouling factor, a mathematical value (usually referred to as Rf or Rd) that quantifies the the oretical resistance to heat flow due to the build-up of a layer on the internal surfaces of heat exchangers. It is a ra tio between the transfer coefficient of a clean heat exchanger and the same unit after a fouling problem has set in. The standard fouling factors for common liquids and gases are spec ified in a formal list, which is easily accessible on the internet.
due to equipment downtime and in creased power consumption, caused by limescale build-up clogging the pipes of the production equipment.
Back to top operating efficiency in a quick, safe and easy way Considering that equipment like cool ing towers only offers an efficiency of 70 to 75 %* from the outset, it is easy to imagine how poor the effi ciency becomes once a 3-6 mm lay er of scale has built up. Water-based descalers provide a quick, safe and easy way to clean the equipment and
As a long-standing partner of the chemical industry, Klüber Lubrica tion has developed a variety of high ly efficient products for all applica tions in heat transfer systems. These highly efficient heat transfer fluids, cleaners/conditioners and descalers can help to get back the efficien cy of water circulation and cooling systems. Taking into account the in dividual requirements and specific conditions of the application, Klüber Lubriation will provide not only the right products, but the company also offers all kinds of services required in order to optimise the efficiency of the process. l
Process Service srl è una società di ingegneria, che dal 1986, opera nell’erogazione di servizi di consulenza e progettazione, con una elevata specializzazione negli impianti chimici e farmaceutici. Process Service è in grado di accompagnare il cliente lungo tutto il corso di un progetto sia nuovo che di revamping. Sviluppo del processo e dell’ingegneria di base-Ingegneria di dettaglio-Supporto al procurement-Gestione cantiere-Precommissioning-Commissioning e avviamento.
Via Alcide De Gasperi 111 20017 Rho (MI) Tel: 02 939 09 272 Fax: +39 02 939 06 328 info@process-service.it www.process-service.it
ACHEMA ....................................................................... 11
ANTARES VISION GROUP 14, 25, 26
ASCO FILTRI ............................................................ 13, 30
BEA TECHNOLOGIES 54, 3rd COVER BRUNO WOLHFARTH .......................... 56, BACK COVER FLAP
CEFIC 16
CHIESI FARMACEUTICI ..................................................... 14 CO.RA. 30, BACK COVER
COESIA GROUP 36 CSV LIFE SCIENCE ............................................... COVER, 10
DOMPÈ FARMACEUTICI 12
EATON ........................................................................... 31
EFFEBI .......................................................................... 55 EFPIA.............................................................................. 6
ELLAB 2nd COVER, 44
ENDRESS+HAUSER........................................................... 64
FACHPACH 18
FARAVELLI .................................................................... 49 FF.GI. 23
FLUORTECNO ................................................... 56, INSERTO GSK 11 IMA 32 ISPE ............................................................................. 14
ITALVACUUM 26
ITELYUM ....................................................................... 61
KLÜBER LUBRICATION 68
LECHLER ................................................................. 62, 63
LIFEBEE 27
MARCHESINI GROUP........................................................ 34 MG2 33
MONTENEGRO ................................................................ 19 MOTT & ASCO 30 NUOVA GUSEO ................................................................ 50 OQEMA 9, 38 POMPETRAVAINI ........................................................ 1, 57 POWTECH 15, 18 PROCESS SERVICE 71 PVS GROUP ................................................................... 37 RADICIGROUP 42 S4S ........................................................................ 41, 46
SALVATORE ROBUSCHI 30, 45
SINTETICA ..................................................................... 58
STERILINE 24, 57
STEVANATO GROUP .......................................................... 15 SWAN ANALITICA 35
TERRANOVA INSTRUMENTS ....................................... 31, 67 TEXPACK 5, 28 TM.I.P.
RIVISTA DELL’
MANAGING DIRECTOR: Simone Ghioldi REDACTION: Alessandro Bignami (a.bignami@interprogettied.com), Eva De Vecchis (e.devecchis@interprogettied.com)
GRAPHIC LAYOUT: Studio Grafico Page Vincenzo De Rosa, Simona Viapiana - www.studiopage.it TRANSLATIONS: Elena Marzorati COLLABORATORS: Gherardo Marchini, Jonathan Venditti
INTERPROGETTI EDITORI S.R.L.
Via Statale 39 - 23888 La Valletta Brianza (LC) Redazione, vendite e abbonamenti Tel./fax +39 039 5153705 www.interprogettied.com
SALES DIRECTOR: Marika Poltresi SALES: Simone Ghioldi (vendite@interprogettied.com)
ADMINISTRATION: amministrazione@interprogettied.com
© Copyright Interprogetti Editori Srl
The columns and news are realised by the editorial team. All rights reserved – All reproduction, even partial, of published material without the publisher’s consent is strictly prohibited.
SUBSCRIPTION RATES:
Italy: ordinary mail delivery EUR 45.00, COD delivery EUR 48.00
International: ordinary mail delivery EUR 60.00, express delivery within Europe EUR 70.00 Express delivery to Africa, America, Asia: EUR 85.00
Express delivery to Oceania: EUR 100.00 Single copy: EUR 10.00
The VAT on subscription prices as well as on the price of single copies is paid by the publi sher pursuant to article 74, sub-section 1, point C of the Italian DPR n. 633 of 26th Oct 1972 and subsequent amendments and additions. It is therefore not possible to issue invoices.
Registered at the Court of Milan on 7 May 2010 no. 259 Managing Director: Simone Ghioldi Printed on July 25th 2022 at Aziende Grafiche Printing S.r.l. Via Milano, 5 - 20068 Peschiera Borromeo (MI)
Information to be given to the data subject - art. 13, legislative decree 30th June 2003, no. 196. Personal data are processed, with or without the help of electronic means, by Interprogetti Editori S.r.l. - Via Statale 39 - 23888 La Valletta Brianza (LC), Italy, to send you the magazine requested and for the operations connected. The processing of data will be carried out by the persons who have been committed by the controller the task of performing the pro cessing operations connected with recording, modification, processing of personal data and printing, fulfilment and delivery of magazines, commercial and fiscal issues, accounting and call center activity. With reference to art. 7, Italian legislative decree 196/2003, you have the right to access to your data, modify, update or cancel data or to object to their processing for direct marketing purposes, by writing to the controller, and ask for the list of data processors.
Publisher’s information to public – art. 13, legislative decree 30th June 2003, no. 196. With reference to Italian Personal Data Protection Code and art. 2, point 2 of Code of Conduct for the processing of personal data in the exercise of journalistic activities, Interprogetti Editori S.r.l. informs that the place where personal data, images and photos are kept is La Valletta Brianza (Italy). Data can be used by journalists, free-lance journalists, persons in the role of trainee journalists and persons who carry out processing for the publication or occasional circulation of essays, articles and other intellectual works for the purpose of the exercise of their journalistic or similar activities. The processing of data will be carried out by the persons mentioned above and by persons in charge of printing and publishing activities. With reference to art. 7, Italian legislative decree 196/2003, you have the right of access to your data, modify, update or cancel data or to object to their, by writing to Interprogetti Srl, and ask for the list of data processors. It is understood that the provisions concerning professional secrecy in the journalistic profession shall be left unprejudiced as related to the source of the information if a data subject requests to be informed of the source of the personal data processed by journalists.
Protezione ambientale
design e costruzione di impianti per il recupero dei VOC (solventi, idrocarburi leggeri e pesanti, etc.) e per il trattamento di effluenti liquidi, gassosi, morchie e fanghi.
Produzione design e costruzione di impianti per la produzione di composti chimici (adesivi, colla per pannelli, resine, PU e PVC per processi di rivestimento, derivati del legno come tannino, estratti della frutta come pectina, formaldeide e suoi derivati etc.).
40 anni di esperienza nella progettazione e fornitura di impianti per processi chimici, energetici e protezione ambientale personalizzati per soddisfare le esigenze del cliente.
TM.I.P. S.r.l. Termomeccanica Industrial Process
Tel. +39 0187 513.410 • Fax. +39 0187 515.352
Visita il nostro sito www.tmip.termomeccanica.com
A reliable company for non-conventional processes and solutions…
Ultimate certified sealing solution for flanged couplings that require electric conductivity.
This unique PTFE (poly-tetra-fluoro-ethylene) matrix allows electrostatic charges to freely move from the inner white layer in GUAFLON SB TM to the outer layer in GUAFLON EXD TM thus avoiding the creation of sparks.
GUAFLON ULTRA TM avoids the need of expensive and hassling earthings for piping and equipment; still, this special seal segregates the process fluid from any contamination of black particles.
• Inner white core in GUAFLON SBTM (PTFE charged with Barium Sulphate - modified and stabilized formula). Approvals and certifications FDA 177.15.1550 and UE 10/2011.
Outstanding chemical resistance:
• Suitable for all chemicals within the range PH 0 - 14
• Suitable for use in Food&Pharma environments
• Outer reinforcement in black, conductive and antistatic GUAFLON EXDTM
Sealing granted in all circumstances
Sealing effectiveness relies on type of fluid, type of flange and thickness
All data present in this brochure are based on laboratory trials. Properties and applications listed in this brochure are standard. Singular, peculiar applications cannot be extracted from the listed data without conducting specific analysis and evaluations. In presence of steam and/or particularly aggressive fluids, maximum operating temperature must include a 25% safety margin. We therefore encourage to contact Fluortecno technical office for further clarifications.
Pic. A shows the perfect multidirectional sinterization of the two materials. In all traction trials the eventual rupture does not take place along the sinterization surface.
(200 Nm for 1hr. at 250°C)
GUAFLONTM ULTRA
The exclusive isostatic and simultaneous moulding of the two materials provides the seal with a natural, multidirectional stability thus granting an excellent sustainability of thermal cycles and a superior resistance to permeation due to the barrier effect of the double sinterization. BEFORE AFTER
All laboratory trials have shown that GUAFLON ULTRATM gaskets, when compressed with variable clamping, possess a superficial resistivity of 30 - 130 Ohms thus granting the equipotentiality of the two ends.
Electric resistance (flange tightening load 5 kN)
Electric resistance (flange tightening load 10 kN)
Electric resistance (flange tightening load 15 kN)
Electric resistance (flange tightening load 20 kN)
Via delle Imprese 34/36 - 24041 Brembate (BG) - Tel. 035 48.74.077 www.guastallo.com - E-mail: FT@guastallo.com