plastic a la
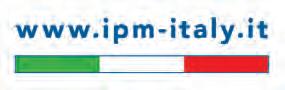
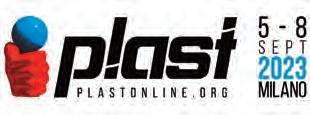


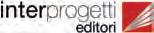
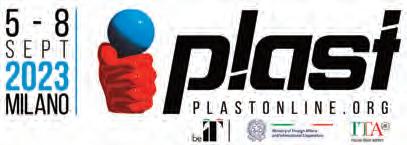


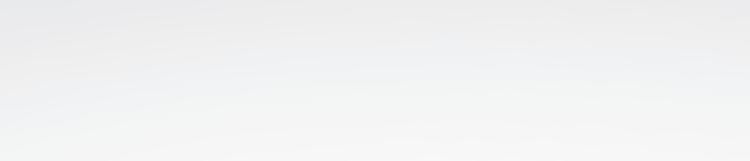

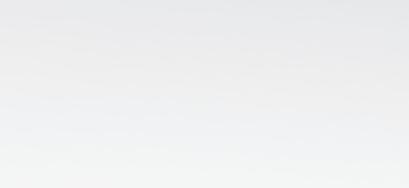
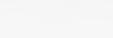
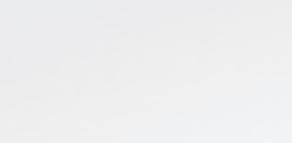
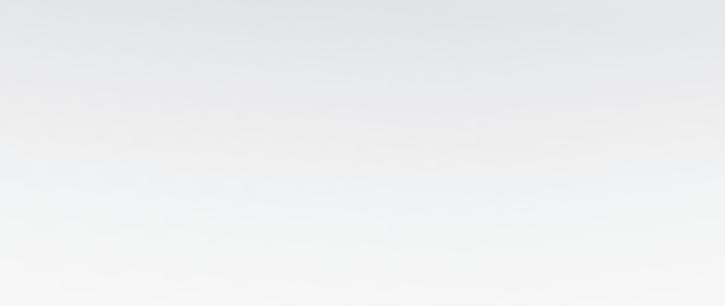

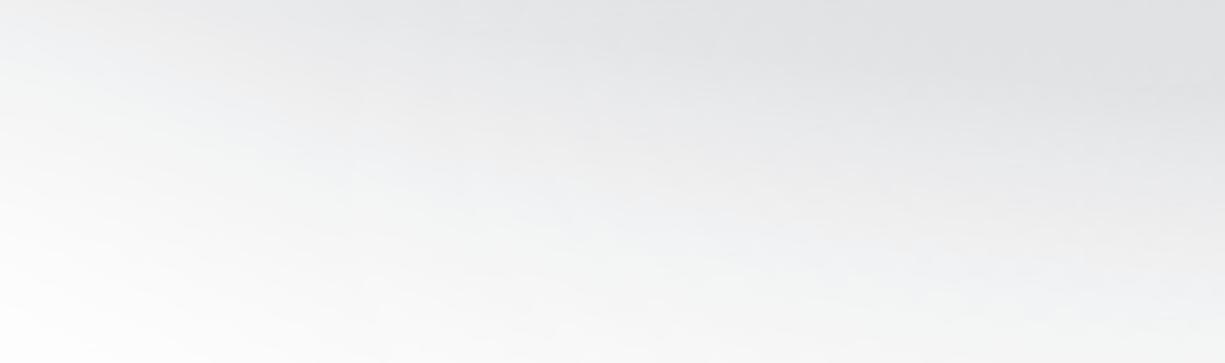
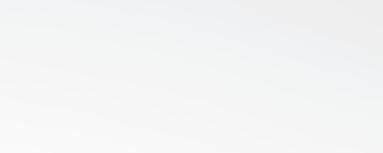
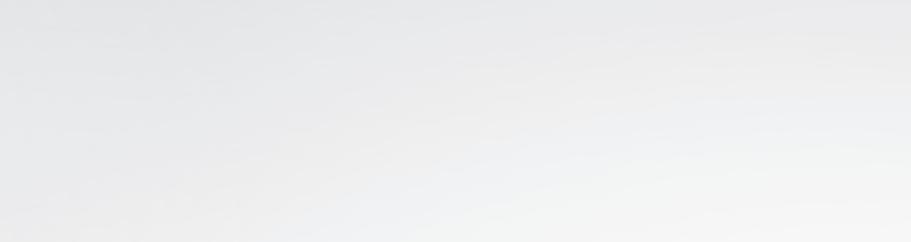
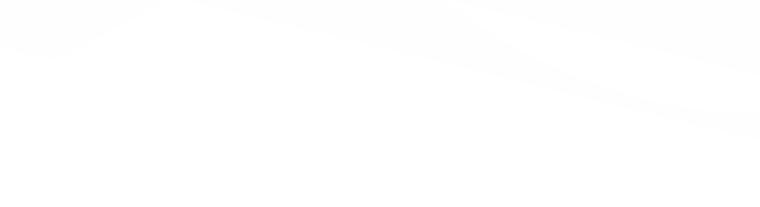

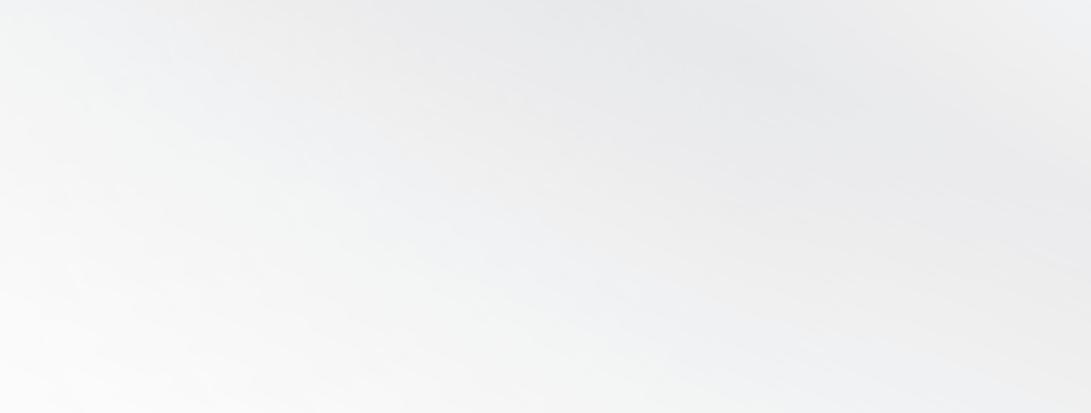
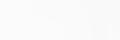
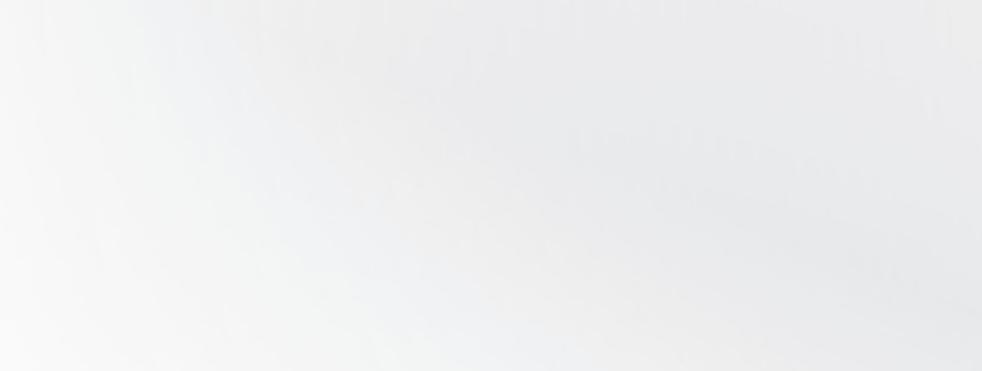
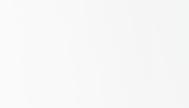
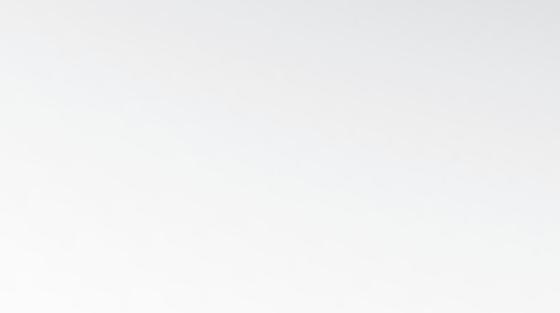
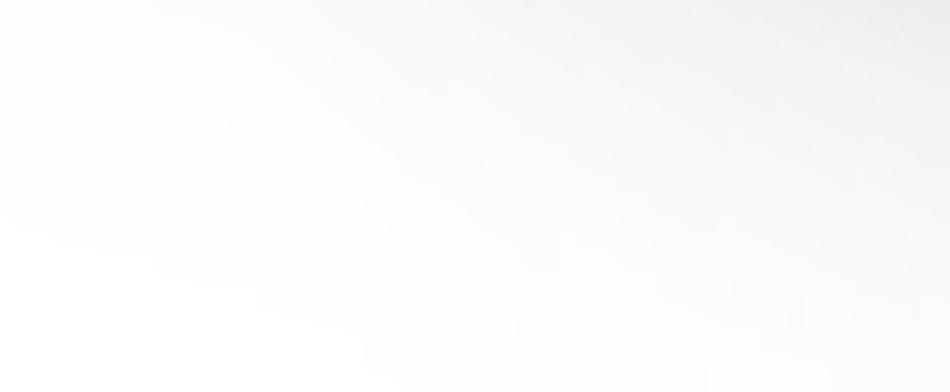
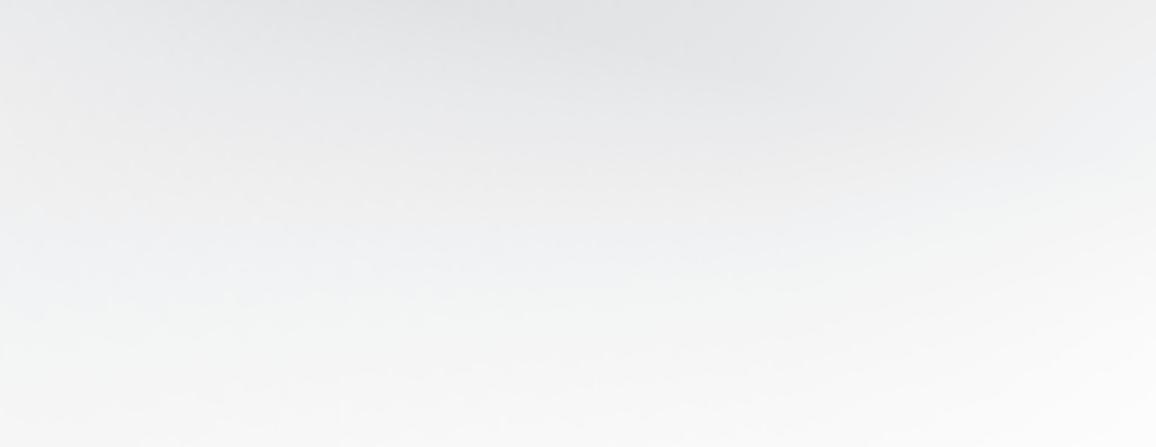
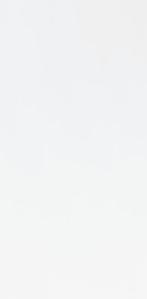

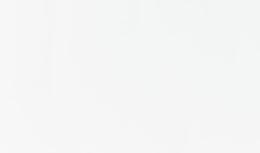
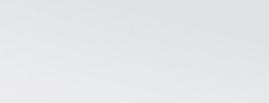


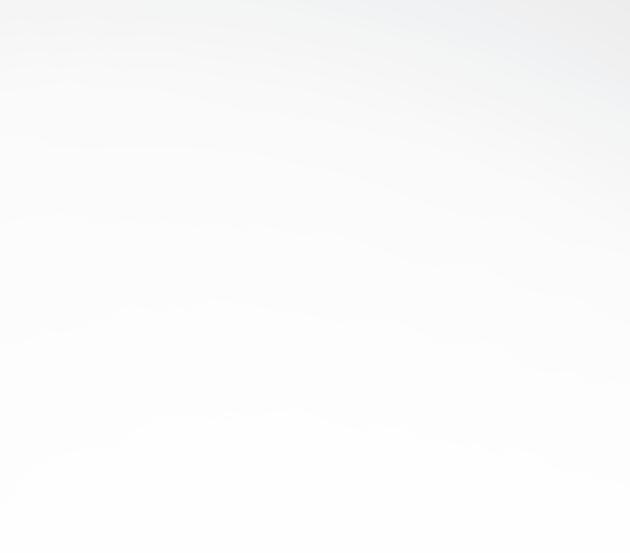

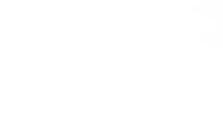
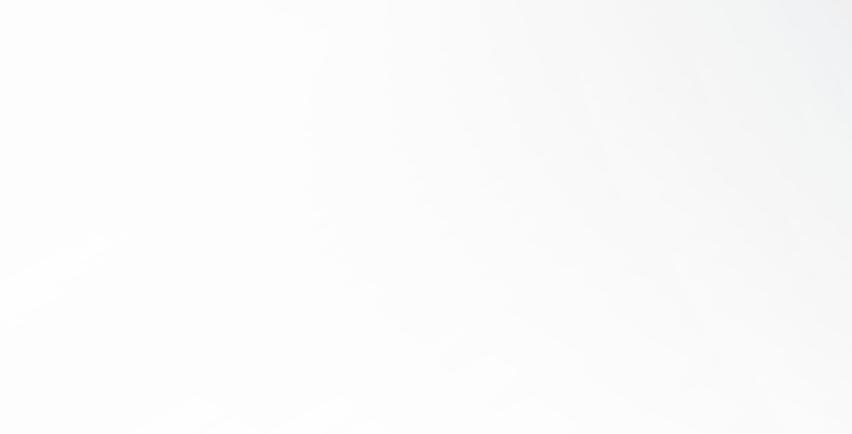

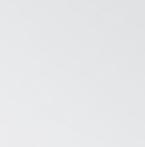

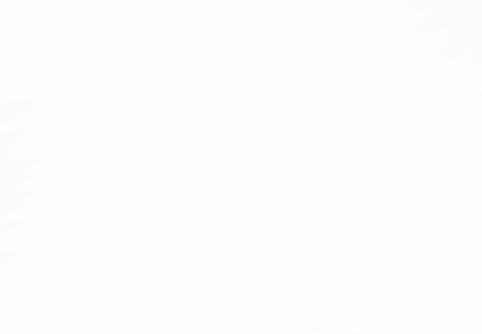
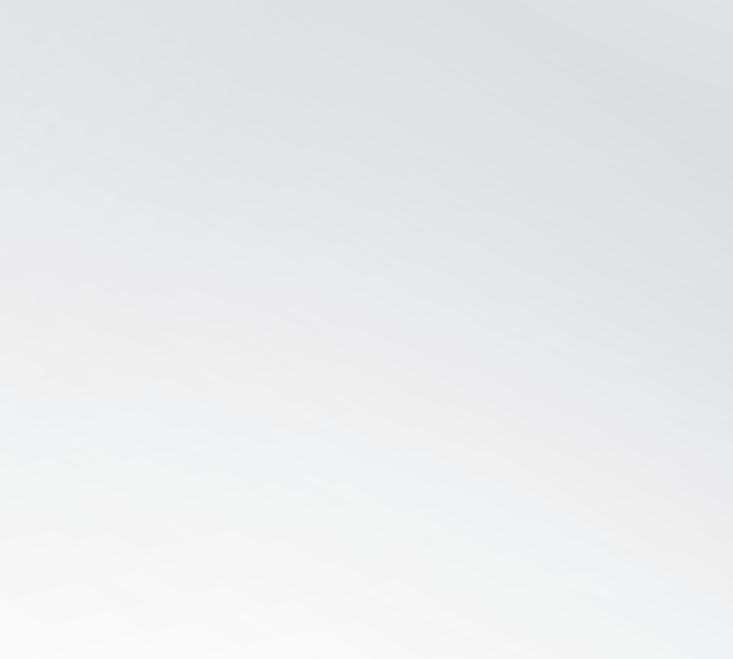
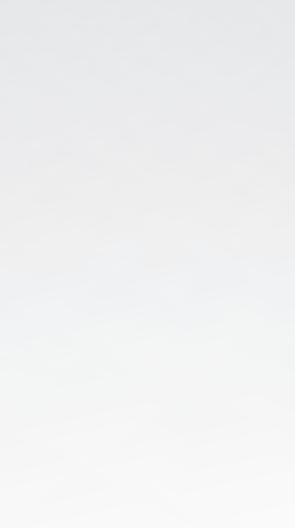
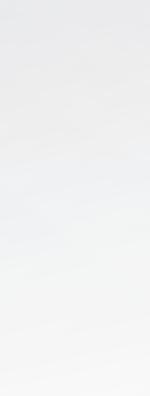
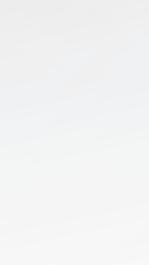
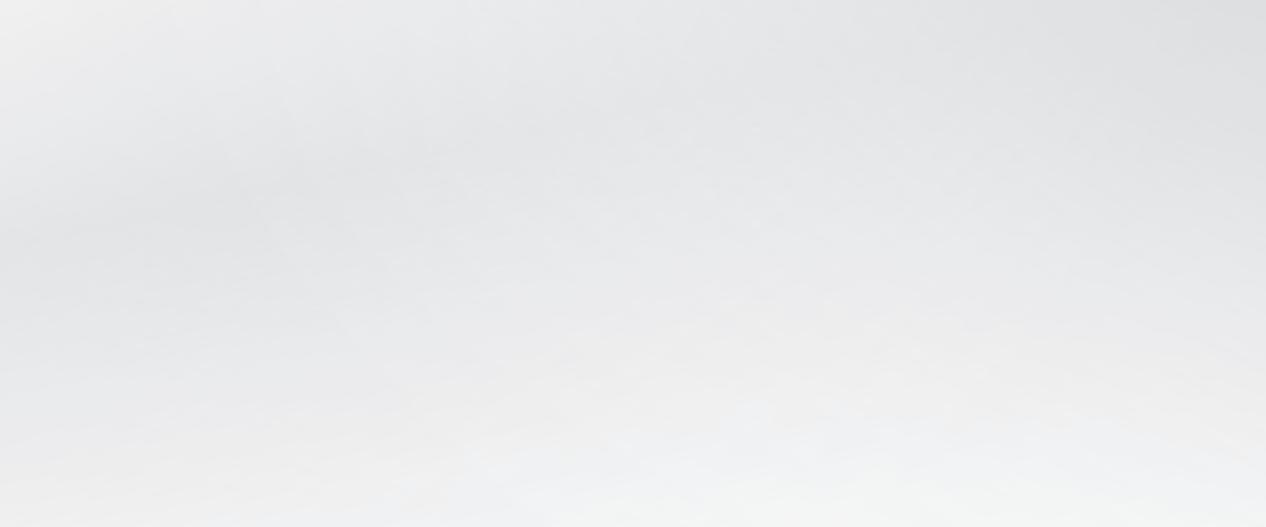
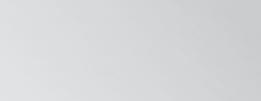

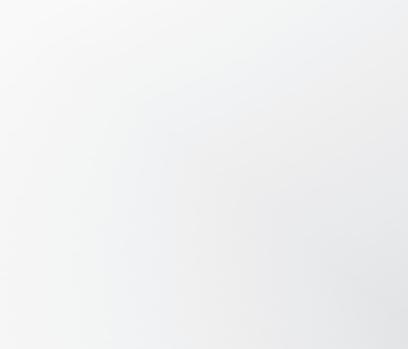
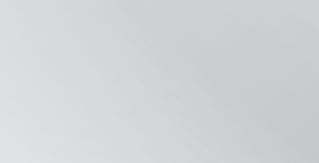

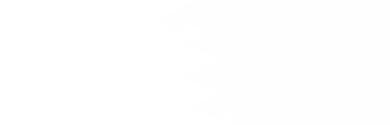
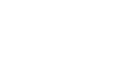
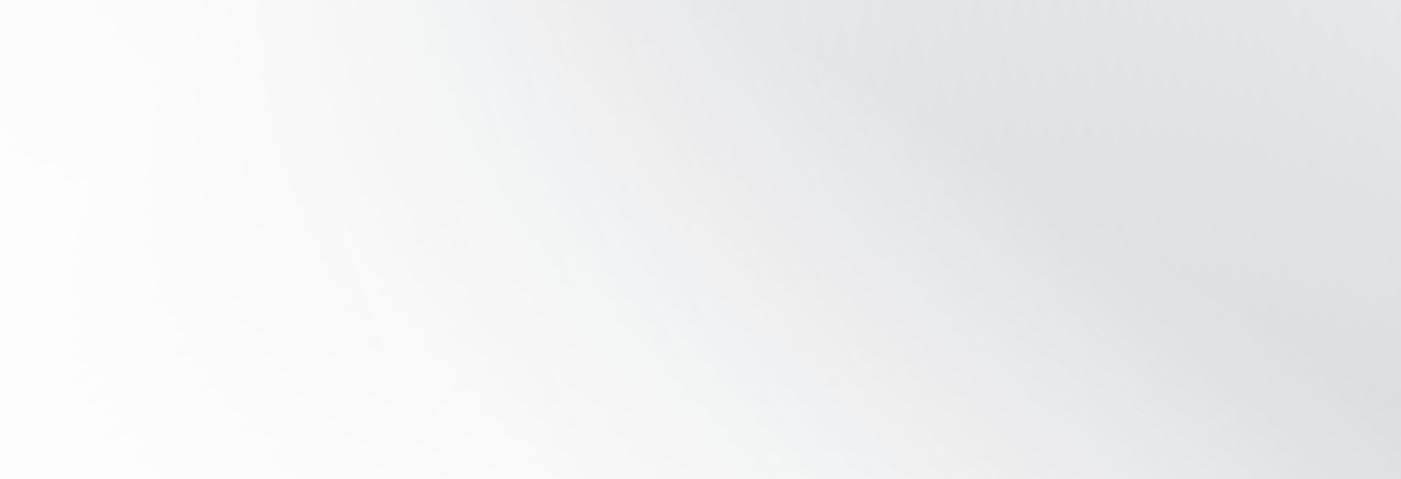
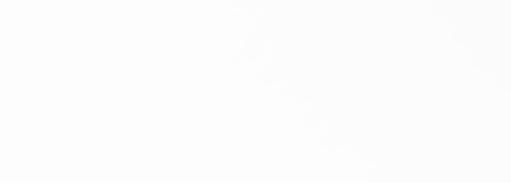
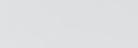

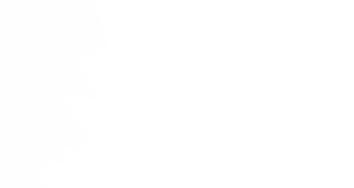
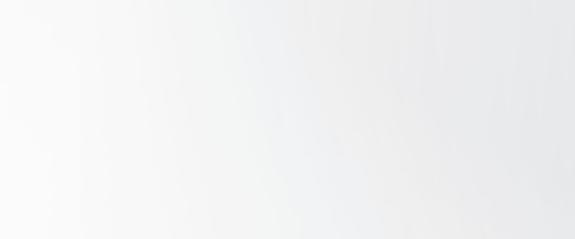
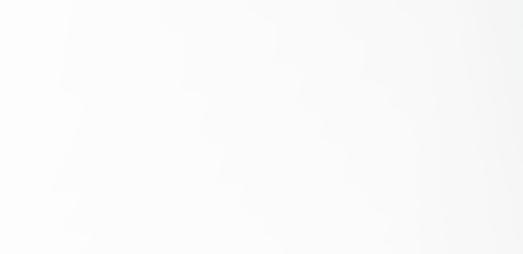


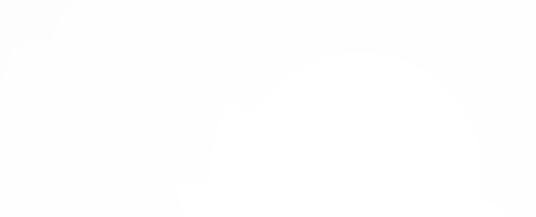

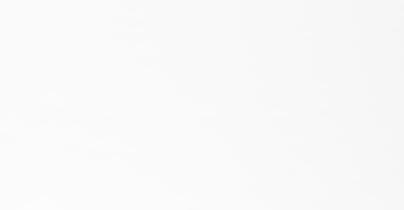
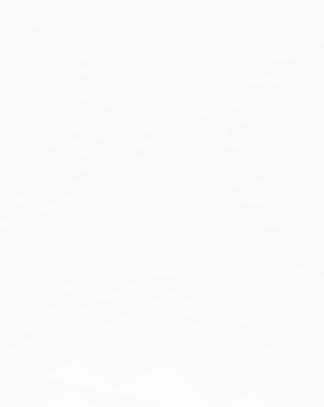

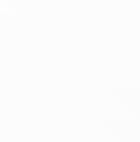
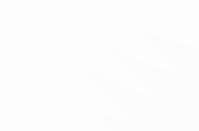
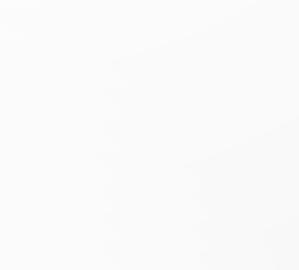

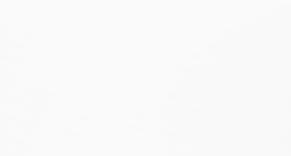
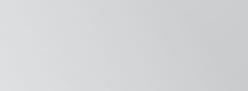
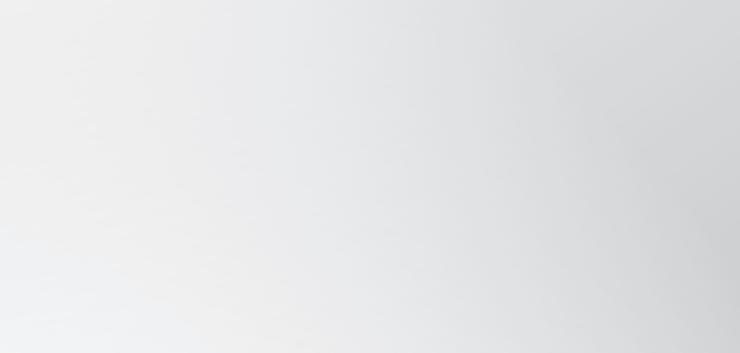
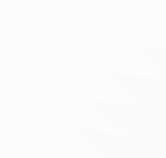

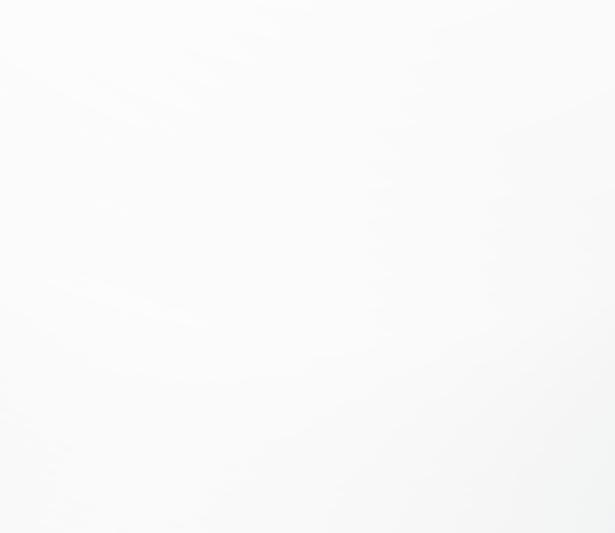
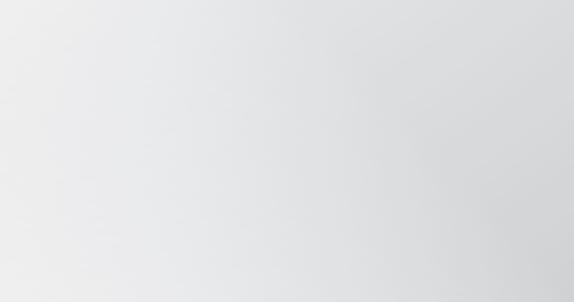


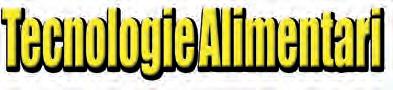
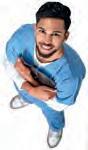
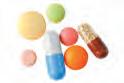
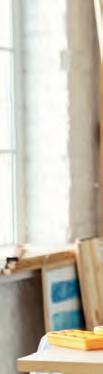
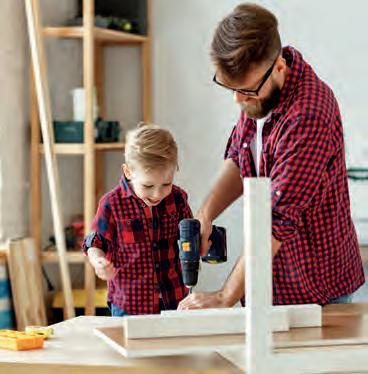

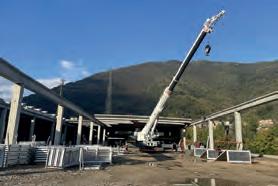
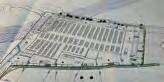
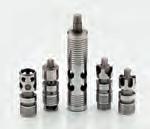
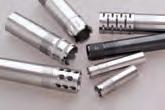
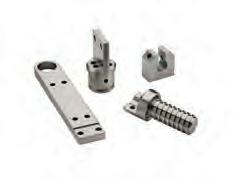
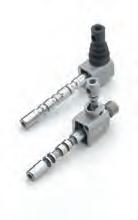
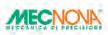


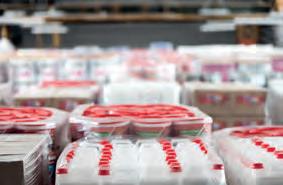

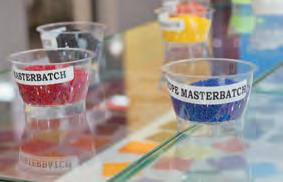
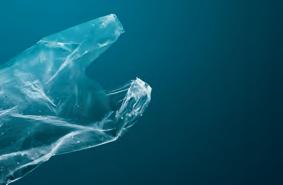
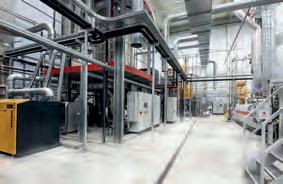
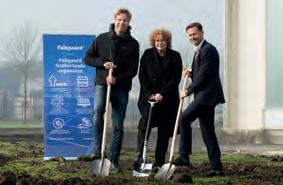

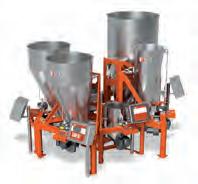
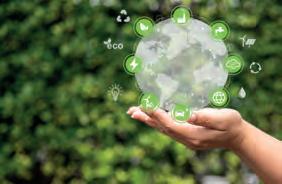



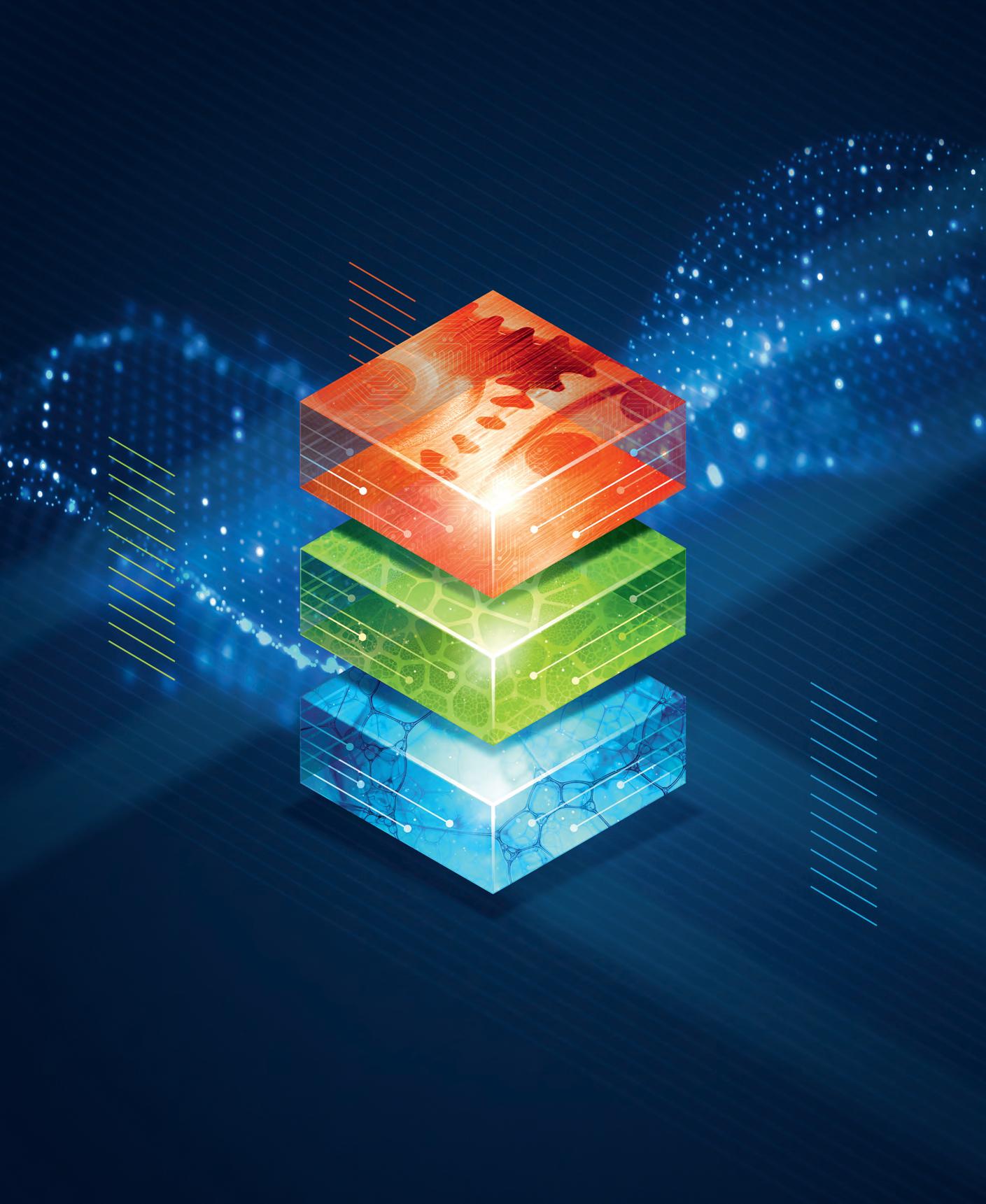
The global production of plastics has reached 400 million tons each year with projected 35 billion tons produced by 2050, as announced during the United Nations Climate Change Conference (COP27) held in November 2022. This numbers are consequences of a rapid urbanization and changing lifestyles which have encouraged the expansion of plastics application in a wide range of industries such as food and beverage, automotive, electronics and electrical, home appliances, and healthcare. The consumption of plastics, especially single-use plastics, poses a huge challenge to our environment. Meanwhile, the industry, for its part, strives to intensify innovations toward a circular economy for sustainability development.
This is compounded by data from the Ellen MacArthur Foundation that by 2050 the world’s oceans could contain about 937 million tons of plastic compared to 895 million tons of fish by 2050. Also contributing to these exorbitant numbers is the Coronavirus pandemic that began in 2020, which has pushed single-use plastic use up 300 percent. These findings must confront the plastics industry with the need to find urgent solutions to ease the burden on the planet, and the circular economy model has been identified as the best option.
The circular economy concept aims to reduce the amount of plastic waste generated by applying a “closed-loop” system in which plastics are produced, used, and reused in a continuous cycle to avoid leakage to the environment.
One of the major strengths of the circular economy is increasing recycling rates. Post-industrial and post-consumer waste
must be recycled in order to be reused. Recycling technologies have seen tremendous improvements in speed, efficiency and savings.
The adoption of the circular economy in the plastics industry presents multiple opportunities for recycling technologies, plastics production systems capable of processing recycled materials, and new materials with recycled content or from renewable sources. It also offers opportunities for manufacturers of finished plastic products eager to meet market trends and consumer preference for environmentally friendly products. According to the United Nations Environment Program, by 2030 the circular economy could generate an additional $4.5 trillion in annual economic output.
According to PlasticsEurope, in addition to the known solutions, it will need to harness the power of innovation, technology and eco-design-based solutions to significantly increase the amount of reuse and recycling, by designing for recycling/circularity and developing more cuttingedge recycling technologies.
To talk about all this and much more there will be Fakuma 2023, trade fair for injection molding, which will be held in Friedrichshafen from the 17th through the 21st of October: an opportunity to address the issues of digitization, process automation and energy efficiency that are high on the agenda along with the circular economy and sustainability. New products and future-oriented business models are also expected.
Eva De VecchisIn 2023 IPM has faced the critical issues of the international markets, and especially the devastating consequences of the climate crisis that have affected Romagna. Investing in research and innovation, as well as in well known economic – commercial reliability, the company continues to grow and win prestigious awards.
“Making predictions for the future is difficult”, explains Silvia Geminiani, CEO of IPM, a company that designs and manufactures high-tech machines and plants for the extrusion and packaging of plastic pipes and pro-
files. IPM is a company with solid roots, the same roots that allowed it to cope with the flood that hit a large area of Emilia-Romagna last May, with heavy consequences for Lugo di Romagna, the city where the company is located.
These are the same roots that have provided the strength to go on and help the employees who have lost their homes, cars, memories in just a day: “the fruit of a lifetime of work.”
Nevertheless, IPM continues its growth by moving toward ever-increasing technological evolution, increased productivity, constant research and development, and strong technical assistance to customers. Relying on these qualities the Romagna-based company will recover, rise up again, roll up their sleeves with a positive spirit.
Silvia Geminiani, what results and goals did IPM achieve in the past year?
“Technological evolution is increasingly important in extrusion lines for the production of plastic pipes and profiles. As for the machinery we produce, IPM has always focused on:
- Technology and consequent increase in productivity, while maintaining very high quality standards. In particular, we have improved the plant efficiency by automating those steps that previously required the manual intervention of several operators. I am referring to the automation of the line end by means of specifically designed machines or robots, which take care of the collection, packaging (according to the customer requirements) and palletizing of the pipes, ready for storage in the warehouse.
- Continuous Research and Development to monitor carefully each stage of the production cycle to identify critical issues, taking appropriate action and paying special attention to the “green” aspect (for example, we have converted several hydraulic belling machines into electric machines, which are
more precise and environmental friendly, thus containing energy consumption as much as possible).
- Customization of manufactured machines according to the needs of each customer. In addition IPM has upgraded the technical assistance services for our customers such as the IPM META LINK: it consists of structured and efficient services for the remote technical assistance involving trouble shooting, commissioning, start – up, daily production setting.
When the operator scans by the smartphone the QR code displayed on the machine, he automatically sends the call to our Service –Customer Assistance, then he will be able to show immediately and precisely the problem to our technicians by means of the Smart Glasses (thus avoiding misunderstandings and time spending to send emails and photos). IPM META LINK allows the operator to receive prompt answers from our qualified technicains, to minimize downtime, to get support without any delayed expensive technical intervention due to distance. It is possible to select the language also, thus removing any communication barrier.
How do you evaluate your partecipation to Exhibition K2022 and the contacts you developed in the months that followed?
“Our partecipation in Exhibition K2022 in Düsseldorf, which is the world’s number one trade show for our industry, marked the return to normal life we had been waiting for long, the joy of face – to – face meetings, the shaking hands, and the exchange of ideas and projects with customers from all around the world, after three years disrupted by the pandemic.
We welcomed a lot of customers who wanted to invest and the negotiations brought about plenty of orders, which even exceeded our highest expectations”.
Last January IPM was awarded the CRIBIS Prime Company, which recognizes companies that are able to maintain high economic and commercial reliability and are punctual in payments to suppliers. What does this achievement mean for you?
“We are proud to have received this award once again: CRIBIS Prime Company reasserts our highest business reliability and ontime payments to suppliers, confirming our
Silvia Geminiani, CEO of IPM: “Thank you to all those who helped and are still struggling to make our region rise up again”IPM partners, from left: Bruno Barabani, Silvia Geminiani and Claudio Argnani
constant commitment to improvement. This certificate reassures our customers and business partners that we IPM are a reliable and professional partner. Last March, IPM srl received the prestigious title of “Champion of Export 2023,” an award given by Statista GmbH (a German company specialized in market research and business data analysis) in cooperation with the Italian economics magazine Il Sole 24 Ore, to reward the 250 Italian companies with the highest level of exports in relation to turnover. This is an important achievement of great satisfaction. We have long driven our strate-
gies toward exports, believing strongly in Made in Italy, and our choice has increasingly proved to be fundamental and successful. We want to thank all our customers who have chosen IPM, our partners who have always supported us, and all the cooperators who daily walk with us on the path of continuous growth”.
After five years, the Exhibition Plast is back. What do you expect from this fair?
In September we take part in Plast 2023, after the COVID pandemic cancelled the 2021
edition. The Italian market has always been important for IPM, especially in recent years, thanks to the fiscal incentives of the Industry 4.0 plan.
As always, we participate with enthusiasm, presenting our latest innovations especially in the field of the line end automation.
Do you think that the role of women and of female entrepreneurs in the plastics industry is expanding?
“I must admit that our field is still male-dominated. Lately, however, as in all sectors, there is an increase in female entrepreneurship as well as a greater presence of women, and I am really happy about that. In fact, I believe that women are skilled and represent an important development opportunity for our country and for the cultural growth of the society, that is the reason why this increase has to be supported more and more.
What are your predictions for the current year? What are the next goals you would like to achieve?
“I think everyone, especially we entrepreneurs, we all are in need of stability today.
IPM has recently designed a new series of belling machines for PVC-O, Oriented or BI-Oriented pipes, ranging from diam. 50 mm up to diam. 630 mm. What is PVC-O? PVC is a polymer whose molecules oriented at random.
In PVC-O, under certain conditions of pressure-temperature-velocity, stretching the material results into the ordering of the molecules, thus forming a laminar (layered) structure that significantly improves the physical and mechanical properties of PVC, providing exceptional characteristics and additional extraordinary competitive advantages, while maintaining the characteristics of the raw material of origin. In biaxially oriented PVC pipes, stretching occurs in two directions: radial and axial.
This results into a biaxially-oriented PVC system, which gives the pipe greater performance and strength (allowing significant savings in raw material when compared to a conventional PVC pressure pipe).
It is worth saying that the proven quality of PVC pressure pipes, their excellent technical-economic ratio, as well as their high durability, safety and recyclability, have made this type of pipe the ideal solution for the conducting all types of pressure fluids. Fields of application:
- Pressurized supply systems for drinking water
- Irrigation systems
- Pressurized sanification systems
It is really difficult to make any predictions. Macro-economic changes such as inflation, volatility of financial markets together with the consequences of the war in Ukraine, as well as the impact of the energy crisis are of great concern to any companies that are facing looming recession, difficulties in sourcing many materials (especially electronic components), shortage of skilled labour in addition to rising prices and consequent reduction of the margins.
Unfortunately, the difficulties that began with
the pandemic in 2020, the energy crisis and the economic impact of the current war have been affecting all of Europe, forcing companies to work with more and more technological and quality machinery, optimizing production processes as much as possible with a view to better energy efficiency. All this is creating a market that is increasingly complex and difficult to organize and to manage. Furthermore, the climate change that is still disrupting our country, is putting us all to the test.
In our area Romagna we have just experienced a nightmare: the overflowing of rivers and canals, caused by the enormous amount of water that fell in a very short time. Incalculable damages, countries and companies have been still flooded for 15 days. Many of our employees have lost their homes, cars, memories, and all that remained of a lifetime of hard work.
IPM has luckily escaped the disaster: and that is the reason why we have been trying to help our employees who have been most affected, rolling up our sleeves and restarting work immediately, with the positive and resilient spirit that sets us apart. Thank you to all those who helped and are still struggling to make our region rise up again”.
- Other underground applications for the use of non-potable water under pressure (reuse of recovered water, fire-fighting networks...).
Now, the company presents the belling machine BA 630 BIAX for PVC-Oriented and BI-Oriented pipes. The belling cycle consists of several stages: the first and the second concern heating of the pipe end, the third one involves the forming and the cooling. The heating takes place in special ovens equipped with shortwave heaters that start to heat the pipe instantly as soon as they are turned on.
The high-frequency heat waves pass through the air without heating it, with no loss caused by air currents or heat rising. A special device allows optimization of heating by preserving the tube surface from burning and overheating. The result is a precisely and
homogeneously heated pipe end. The heating temperature is sligthly above the glass transition temperature so that the socket can be shaped without any loss of the bi – orientation and its advantages.
The belling group is particularly heavy duty and reliable because of the remarkable deformation forces involved.
Thanks to the use of pressurized air and of the cooling by water spray, the socket that is obtained has a well-defined, dimensionally correct and stable profile, while safeguarding a high production capacity of the belling machine.
The belling machine BA 630 BIAX, like the entire range of machines model BA BIAX, allows the processing of pipes produced according to standards EN 17176, Ansi/Awwa C909 and Astm F1483, AS/NZS 4441, CAN/CSA -B137 and ISO 16422.
Asia’s Regional Comprehensive Economic Partnership (RCEP), the world’s largest free trade agreement enforced in January 2022, offers a bountiful of possibilities for the plastics, rubber and petrochemicals sectors in various aspects, giving Asia’s advanced and emerging markets a much needed economic boost.
Asia’s trade growth was severely impacted by the pandemic. Slower growth and rising prices, as well as lower demand from recession-ravaged United States, China, Europe, and other trade partners, have also affected growth in Asia. Nonetheless, the region’s GDP is expected to grow by 4.4% in 2022 and rise to 4.9% by 2023, according to the International Monetary Fund (IMF) 2022 regional economic outlook data.
Thus, bolstering trade is a strategy that is expected to accelerate recovery. FTAs signed by Asia’s advanced and developing economies, as well as emerging markets, provide a much-needed economic boost for the region.
The Association of Southeast Asian Nations (ASEAN), which represents a market of more than 600 million people with a total combined GDP of US$3.2 trillion in 2019, has seven trade agreements, including the Regional Comprehensive Economic Partnership (RCEP), which was signed in November 2020 and took effect in January 2022.
RCEP is a free trade agreement (FTA) between the ten member states of ASEAN (Brunei, Cambodia, Indonesia, Laos, Malaysia, Myanmar, the Philippines, Singapore, Thailand, Vietnam) and its five FTA
partners (Australia, China, Japan, New Zealand and Korea). It is the world’s largest FTA, covering 30% of the world’s GDP and population, as well as approximately 30% of total global trade, and is the first FTA among the largest economies in Asia Pacific. Asia’s trade growth was severely impacted by the pandemic. Slower growth and rising prices, as well as lower demand from recession-ravaged United States, China, Europe, and other trade partners, have also affected growth in Asia. Nonetheless, the region’s GDP is expected to grow by 4.4% in 2022 and rise to 4.9% by 2023, according to the International Monetary Fund (IMF) 2022 regional economic outlook data. Thus, bolstering trade is a strategy that is expected to accelerate recovery. FTAs signed by Asia’s advanced and developing economies, as well as emerging markets, provide a much-needed economic boost for the region.
The Association of Southeast Asian Nations (ASEAN), which represents a market of more than 600 million people with a total combined GDP of US$3.2 trillion in 2019, has seven trade agreements, including the Regional Comprehensive Economic Partnership (RCEP), which was signed in November 2020 and took effect in January 2022.
RCEP is a free trade agreement (FTA) between the ten member states of ASEAN (Brunei, Cambodia, Indonesia, Laos, Malaysia, Myanmar, the Philippines, Singapore, Thailand, Vietnam) and its five FTA partners (Australia, China, Japan, New Zealand and Korea). It is the world’s largest FTA, covering 30% of the world’s GDP and population, as well as approximately 30% of total global trade, and is the first FTA among the largest economies in Asia Pacific.
Currently the world’s fifth largest economy, ASEAN is expected to become the world’s fourth-largest economy by 2030, with a consumer market worth more than US$4 trillion. This expansion will be aided further by RCEP. For example, RCEP members account for 40% of ASEAN’s investments, while non-ASEAN RCEP members account for 24%.
Trade liberalization is at the heart of the RCEP framework, and it will be accomplished through gradual tariff reductions with significant exemptions in sensitive and strategic sectors. Concessions under the RCEP are expected to eventually eliminate tariffs on more than 90% of goods traded among member countries.
Moreover, it is anticipated that RCEP tariff concessions will increase trade among members while diverting certain trade from non-member nations. Lower import prices are likely to lead to higher imports as a result of lower tariffs.
RCEP also aims to align ASEAN’s existing FTAs and partnerships with the other five partner economies in a bid to reduce trade barriers and improve investment regulations. As a result, the economic benefits of RCEP
are expected to be immense. According to the UN Conference on Trade and Development (UNCTAD), intra-RCEP trade was already worth approximately US$ 2.3 trillion in 2019, and the RCEP’s tariff concessions would upsurge intraregional exports within the bloc by nearly 2% to an estimated US$42 billion.
Furthermore, the RCEP will have a favorable impact on nearly all major industries, ranging from manufacturing to chemicals. Chemicals, for example, are expected to gain US$1.7 billion, for a total increase of
approximately US$6.4 billion, of which US$4.5 billion is due to trade diversion. The plastics and rubber sector is expected to add US$0.5 billion in trade, resulting in a US$1.6 billion increase in trade, with trade diversion accounting for an estimated US$1.2 billion.
Meanwhile, beyond the RCEP, the global plastics and rubber trade has already shown strong growth from industries that rely on these materials, such as medical devices, automotive, construction, electronics, consumer goods, and others.
RCEP is envisioned to enhance market access and ease the flow of provisions like medical devices
The plastics value chain has been subjected to a number of disruptive events, prompting Asian companies and businesses to implement strategies to make their business models resilient to supply chain disruptions. The RCEP’s trade liberalization and preservation of multilateral trading systems can generate different trade opportunities for ASEAN and non-ASEAN member countries, thereby accelerating the region’s economic recovery.
Petrochemicals, which are essential in the production of raw materials such as polymers used in packaging, electronics, construction and other applications, are expected to trade strongly within the RCEP alliance.
Notwithstanding the supply disruptions and geopolitical volatility, the International Energy Administration (EIA) predicts that the petrochemicals sector will secure more than a third of global oil demand growth by 2030
and nearly half of demand growth by 2050. China is one factor expected to influence this growth.
The colossal country is expected to generate significant petrochemical demand, rising to 780 million tonnes per year by 2030, according to the NPC Economics & Technology Research Institute (ETRI). Meanwhile, Thailand’s petrochemical industry, which is the largest in ASEAN, satisfies demand for petrochemical feedstock, such as naphtha and olefins, particularly in China, which is its largest export market, says Kungsri Research.
The global health crisis that affected the supply of personal protective equipment (PPE) and diagnostic health products, which are abundantly made of plastics or rubber, in the previous years has brought access to medical devices to the forefront more than ever before. RCEP is envisioned to enhance market access and ease the flow of provisions like medical devices.
Asia, the largest producer of pharmaceuticals and medical equipment, is expected to grow at a CAGR of 4.4% from 2022 to reach approximately US$225 billion in 2030, with Thailand, Singapore, Malaysia, and Indonesia as revenue drivers and zones for investment and business opportunities. The Indo-
nesian medical device market is set to be among the fastest growing in Asia, with a market value of US$1.9 billion by 2026.
Because of the region’s burgeoning consumer market, integrated supply chains and comparatively lower cost of labor, the ASEAN automotive sector has emerged as a manufacturing hotspot for both OEMs and vehicle parts suppliers. The automotive sector’s inclusion in the RCEP is deemed to be complementary.
According to the University of Duisburg-Essen’s CAR Institute, an estimated 41.8 million vehicles will be sold in RCEP countries by 2030, accounting for 46% of global market share, and counting.
The huge potential brought by RCEP bodes well for the plastics and rubber sectors, as the automotive industry is the third largest user of plastics after packaging and construction, and a major consumer of rubber. Thailand, which is Asia’s automotive node, plays a key role in the automobile value chain. Several global companies have established facilities in the country for development, design, and other production-related activities since the 2000s.
Today, Thailand is home to several major Japanese automobile manufacturers, as well as approximately six Chinese electric vehicle brands. Meanwhile, Singapore is capitalizing on its electronics and semiconductor capabilities, as well as its stronghold in advanced materials and equipment manufacturing, to serve the global and regional automobile markets.
An estimated 41.8 million vehicles will be sold in RCEP countries by 2030, accounting to 46% of global market share
OQ, the Oman-based energy transition enabler that specializes in PP and PE grades for flexible and rigid packaging solutions, continues building on a longlived trading partnership between its home country and India as the company greets familiar faces at the PlastIndia event in New Delhi this week.
Oman’s total trade with India almost doubled last year and was estimated at USD$9.9bn in 2021-2022 compared to USD$5.4bn in 2020-2021. OQ believes the trade opportunities will only further prosper as India’s population, its demand for plastic products and countries’ collaborations continue to grow momentum. An advantageous prospect of a free trade
agreement between the two countries is in the works, with discussions at an advanced stage.
The Indian sub-continent is one of the fastest-growing regions for polymer demand with a CAGR of 6 per cent projected for the 2022-2030 period. In addition in 2023 India is expected to become the most populous country in the world – and with rising income levels being seen across the region, demand for plastic products is set to increase exponentially. Harnessing years of success and confidence in the face of challenges, OQ is primed for demand and ready to take action in support of their close partnership with India.
Palsgaard has started work on a major expansion at its specialist Netherlands factory for high-grade PGPR emulsifiers. PGPR (polyglycerol polyricinoleate) is a co-emulsifier primarily used in chocolate production to control flow, reduce viscosity and optimize moulding and enrobing.
It also reduces fat content in mar-
garine spreads and is a highly effective, plant-based colour-dispersing aid that replaces petrol-based waxes in plastics.
Scheduled for completion in 2024, the €18 million expansion to Palsgaard’s Netherlands plant, which also makes specialty ingredients for margarine and bakery, will double the company’s global capacity to produce PGPR, demand for which is growing by 10% per year.
The facility achieved CO2-neutral production (Scope 1 and 2) status in 2018. The energy-saving design of the new extension includes an additional 1500m2 of solar panels and complete electrification of PGPR production, along with three new reactors and a new downstream processing line.
“As well as almost doubling our PGPR capacity to 11500 MT annually, this expansion will substantially increase storage capacity for raw materials and finished goods, which will secure business continuity in times of supply chain disruptions”, spiega Palsgaard Netherlands Site Director Joris Dhont.
Palsgaard’s new Chief Executive Of-
ficer Helle Müller Petersen, who recently joined the company from Arla Foods, led the ground-breaking ceremony on 7th February.
She commented: “Visiting our facilities around the world and meeting Palsgaard employees is a priority for my first 100 days as CEO, so seeing work start on the PGPR factory extension in the Netherlands has been a great opportunity to learn more about Palsgaard’s unique DNA”.
“We are already market leaders in PGPR and the world’s only commercial source of fully sustainable emulsifiers”, added Kim Bøjstrup, Chief Operations Officer who also participated in the ceremony. “Our expanded Netherlands plant will continue to manufacture the highest quality, palm-free PGPR products”.
Palsgaard is also investing heavily in its main production site in Denmark and is currently installing a new 30,000 MT spray cooling tower. This facility will be supported by the construction of multiple new reaction, distillation, and esterification plants. The €125 million investment will double its production capacity by 2024.
Plastics Europe supports the overarching objective to end plastic pollution by 2040 through a circular economy. According to the association, a global agreement that provides guidance and supports global harmonization of standards would be the basis for an inclusive transition of the plastics system.
In early March 2022 in Senegal, the fifth session of the United Nations Environment Assembly (UNEA) adopted Resolution 5/14 with the goal of developing, by 2024, a legally binding international instrument on plastic pollution, including in the marine environment, called Inc-2.
Our goal must be to end plastic pollution by 2040 through a circular economy where all plastic applications are reused, recycled, and responsibly managed during and after use while enabling a lower greenhouse gas emissions plastic economy.
PlasticsEurope support an international agreement including ambitious measures and an enabling framework to facilitate this global transformation of the plastics systems. These measures should include the creation of a market pull for circular plastics, the rapid global expansion of collection, sorting and recycling as well as a financing system supporting the massive investments needed for facilitating this change.
To achieve the goal of ending plastics pollution by 2040 through a circular plastics
economy, the association support a set of core obligations and measures to ensure the envisioned system transition. Plastics Europe is convinced that an ambitious global agreement that provides guidance and supports global harmonisation of standards is the basis for an inclusive transition of the plastic system for all stakeholders.
We need a holistic approach to stop plastics pollution. One that is built on sustainable plastic production and consumption with waste prevention, reuse, reduce and repair, and the development of a circular economy. In addition to the global scale up of known solutions, we will need to harness the power of innovation, technology and
eco-design-based solutions to significantly increase the amount of reuse and recycling, by designing for recycling/circularity and developing more cuttingedge recycling technologies. The current global challenges need to be addressed with globally harmonised measures that can be nationally implemented recognising national and local circumstances and enabling policies.
PlasticsEurope supports the need to increase the use of circular feedstocks thereby reducing the dependence on fossil feedstocks used for the production of plastics products. In order to achieve sustainable production through feedstock diversification, high recycling rates and investment are needed to secure circular feedstock availability.
“We consider the setting of recycled plastic content targets as a highly effective option to support investment in the roll-out of segregated collection and recycling infrastructure”, reads on the association’s website. “Such targets can help to create a market demand for recyclates across all plastics applications (for example in packaging, consumer goods, or the automotive sector).
To safeguard effective plastic pollution prevention, a robust and competitive business case for plastic waste-based feedstock streams is essential to unlock and safeguard constant and significant waste and recycling infrastructure investments at scale”.
To ensure faster systemic change, it is also essential to use the existing assets of plastics production while diversifying feedstock sources. From that perspective, PlasticsEurope supports the increased use of all kinds of circular feedstocks, including recycled feedstock from plastic and other wastes, sustainably sourced biomass, and captured carbon feedstocks (CCU), which will help to reduce the reliance on fossil feedstocks and considerably lower GHG emissions and the waste footprint of the plastics system. In order to achieve sustainable plastics production through feedstock diversification, high recycling rates and investment are needed to secure circular feedstock availability. “In order to enable and drive the transition towards a circular economy − declares Plastics Europe − we need for an appropriate regulatory framework on a national level that should include the following measures”:
• create demand drivers for the transition to circular plastics production, e.g., via legislative targets for circular plastics based on national circumstances;
• recycled plastics content targets per industry sector to create a demand driver for waste management and recycling;
Reuse, refill or other new business models can be effective ways of saving resources, reducing the generation of waste and improving the environmental footprint of plastic products
• secure circular feedstock availability e.g., through recycling rate targets combined with collection and sorting of plastics waste; • financial incentives to promote essential investments in circularity and support the development of innovative technologies (e.g. innovations in recycling, carbon capture);
• re-use targets for specific packaging applications.
Design for circularity is an essential obligation to end plastic pollution. PlasticsEurope believes that the global agreement should focus on the following core levers for a systemic change:
• Reuse and Refill: In certain instances, reuse, refill or other new business models and alternative delivery systems are effective ways of saving resources, reducing the generation of waste and improving the environmental footprint of plastic products.
• Sustainable consumption of plastics applications: Plastics Europe supports the vision of enabling the sustainable consumption of plastics applications globally and sees tackling plastic pollution on an application level as the most effective lever to reach the objectives of the agreement.
• Design for Recycling/Circularity: this is an additional valuable tool to support the sustainable consumption of plastic applications in a circular economy. Plastic Europe supports the development of Product Design Principles, based on LCA assessment, to increase recycling and where possible reuse. Design for Recycling (DfR) criteria
Plastics Europe support the important objective to globally develop waste management systems, thus preventing pollution and laying the ground for a circular economy
need to be application specific and must aim to support an inclusive transition. Currently, no globally aligned methodology for the evaluation of plastic applications is available. Nevertheless, the association consider the development of such a methodology for driving sustainable consumption on an application level as a core objective of the future agreement.
Universal access to integrated waste management systems (collection, sorting and treatment) for all wastes, not only plastic waste, is crucial to prevent littering
important objective to globally develop waste management systems, thus preventing pollution and laying the ground for a circular economy. Additionally, there needs to be fully agree on the importance of involving citizens, the informal sector, and consumers in the design of the collection systems. The transition towards a global circular economy for plastics can be supported by targets on recycling rates. To achieve sufficient plastics recycling, Plastics Europe call for a clear pathway towards a market environment supportive of a circular economy, including through a global ambition to transition away from waste treatment approaches
ble plastics waste towards more environmentally sound waste management approaches like recycling.
Although the term “bioplastics” is widely used, it can often refer to two entirely different properties of plastic materials, namely plastics using a bio-based feedstock (origin of carbon) and plastics that are intrinsically biodegradable under one or more environmental conditions (end-of-life).
An approach that differentiates between biobased plastics which are part of a transition to non-fossil feedstock in plastics production and biodegradable or compostable plastics applications is important and possible.
Plastics Europe welcomes technical global standards developed by International Organizations for Standardization, such as ISO 17088 - Specifications for compostable plastics or ISO 16620 – Specifications for bio-based plastics. Biodegradation of a plastic material is a systems property that “requires both plastic material properties that allow for biodegradation and suitable conditions in the receiving environment such that biodegradation can take place” (Scientific Opinion of the European Commission’s Group of Chief Scientific Advisors; Biodegradability of plastics in the open environment, 2020). There is a need for clear differentiation between certified compostable plastic applications supporting organic waste recycling and environmentally biodegradable plastic applications. In fact, these two plastic application types have different biodegradation needs, end-of-life receiving environments and linked to the aforementioned aspects, sustainability value proposition. This distinction in terms and potential labelling is key to avoid misunderstanding and confusion. Environmental biodegradation shall never increase litter or be an excuse thereof.
The Council of Experts met for the first time to discuss plans for the international plastics and rubber industry’s most important trade fair, K 2025, to be held Oct. 8-15, 2025, in Düsseldorf. The Exhibitors’ Council assists Messe Düsseldorf with its preparations in the run-up to K 2025 and provides consultancy on basic conceptual and organizational matters.
Comprised of representatives from exhibiting industrial segments and from important industrial associations, the council covers the entire range of products and services presented at K 2025 – machine and plant engineering, plastics and rubber raw material and auxiliary production as well as the production of semi-finished products and industrial components made from plastics and rubber.
Ulrich Reifenhäuser, Chairman of the Management Board of the Reifenhäuser Group and Chairman of the VDMA plastics and rubber machinery association, will retain his position as Chairman of the Exhibitors’ Council.
Thorsten Kühmann, Director of the VDMA plastics and rubber machinery association, will retain his position as head of the communication committee.
Every three years companies from throughout the world present the latest technological developments, current solutions and visionary approaches here.
Highlighting impressive innovations and forward-looking impulses for climate protection, the circular economy and digitalisation, K in Oc-
tober fully met the high expectations last year. More than 3,000 exhibiting companies from 59 countries and to the tune of 177,500 trade visitors from 169 nations gathered at K 2022.
In 2023, Interplas, the UK’s largest and longest-running plastics trade fair, will celebrate its 75th anniversary. Among a number of exciting features and new developments is the return of
the PlastikCity pavilion, first introduced at Interplas in 2017, and following the success of the second edition in 2021, the fair’s organizers, Interplas Events Ltd, part of the Rapid News Group, and PlastikCity announce its return for Interplas 2023, Sept. 26-28 at the NEC in Birmingham.
The pavilion is designed to provide opportunities for high-quality UK & Irish suppliers that may not normally exhibit at the show, for example, suppliers who may not have the resources to occupy a large individual stand, or who wish to dip their toe in the water for the first time to assess the benefits.
Visitors will be able to connect with 20 exhibitors on the pavilion, with access to new products and services from UK companies.
“It’s a big year for Interplas with our 75th birthday celebration, and this pavilion is a great opportunity for smaller companies to join the party,” explained Duncan Wood, CEO of Interplas.
“The PlastikCity pavilion is a staple of the Interplas show and we look forward to seeing the wide range of suppliers our visitors can connect with”.
“We are excited to once again bring the PlastikCity Pavilion to Interplas, especially for this special commemorative edition of the fair,” added Carl Futcher, managing director of PlastikCity. “With over 100 of our partner companies exhibiting and another 20 SMEs participating alongside us in the pavilion, the fair promises to be one of the highlights of 2023 for the UK plastics industry”.
The 28th Fakuma international trade fair for plastics processing is being eagerly awaited in Friedrichshafen from the 17th through the 21st of October, 2023. The trade fair, which also serves as a technology and industry barometer for extrusion technology, thermoforming and 3D printing, will offer information on new solutions and provide fresh impetus for circular economy.
and forward-looking business models”, explains Annemarie Schur, Fakuma project manager at trade fair promoters P. E. Schall. “This trade fair with worldwide recognition will make the significance of plastics and their special importance a topic of discussion for everyone. Plastics will have to meet the challenges of both the present and the future. This is why Fakuma 2023 is an ideal platform for new products and technological solutions, as well as for expert discussion of upcoming spheres of action”.
The entire injection molding industry awaits the arrival of the 28th Fakuma international trade fair for plastics processing wich will be held in Friedrichshafen (Germany) from the 17th through the 21st of October, 2023.
As a recyclable material, plastic is an indispensable constituent of everyday life – in the private sphere, for business and in technology. Innumerable consumer and industrial products would be inconceivable without plastics. Plastics manufacturers and plastics processing companies rely on top-quality, durable high-tech solutions for a
wide range of industry sectors such as power generation with solar modules, e-mobility components, the construction sector, the packaging industry, technical components, lightweight design and automobile manufacturing, medical technology and the furnishings industry. At the same time, plastics represent a challenge in terms of the consumption and reuse of natural resources.
“Many Fakuma exhibitors are addressing the topics of advanced machinery for the production and reuse of plastics, optimised processes for production and processing, improved materials, newly designed products
The industry sector is being confronted with a variety of far-reaching tasks – amongst others the goal of decreasing greenhouse gas emissions, reducing energy consumption and improving operations at manufacturing and processing companies. At the same time, the transformation to circular economy must be implemented in all its facets. In any case, digitalisation and automation are triggering significant transformation processes which act as beneficial drivers: they support the efficient use of all resources in the production, processing, utilisation and reuse or recycling of plastics. AI-based solutions will also be increasingly helpful in this regard. “In many respects, Fakuma 2023 will provide important and valuable stimuli for the positive advancement of
thought and action in functioning circular economies”, says Bettina Schall, managing director of trade fair promoters P. E. Schall.
“The practice-oriented trade fair format in a familiar working atmosphere is an appropriate setting for technical discussions, objective clarification and the demonstration of implementable solutions for a circular economy”. As the world’s leading trade fair highlight for injection moulding, Fakuma also serves as an industry and technology barometer in the fields of extrusion technology, thermoforming and 3D printing. Suppliers and users will explore the exciting, future-oriented topic of plastics from all sides for five days at this well-established industry meet. High levels of internationalism, the quality of the expert discussions and the event’s concrete practical relevance mean that forward-looking solutions can be expected for the tasks being faced by the industry sector. Not least of all, the world-
class expert presentations at the exhibitor forum promise to provide important impetus for the relevant topics of plastics, the circular economy, efficiency and sustainability. The dates are set for Fakuma 2023: the industry sector will meet in Friedrichshafen from the 17th through the 21st of October, 2023.
“The technologies presented at Fakuma are ready for series production. The trade fair visitors know this”, notes Markus Hanetseder, vice president of product management, marketing and communications at Engel. “The trip to Friedrichshafen pays off for them very quickly”. He stresses the fact that Fakuma’s high levels of innovative power and great dynamics are the basis for a world-class trade fair audience. As a result, trade visitors will experience trailblazing, future-oriented solutions at this year’s industry event on Lake Con-
Digitalisation and automation support the efficient use of all resources in the production, processing, utilisation and reuse or recycling of plastics
stance. As the world’s leading trade fair highlight for injection moulding and as an industry and technology barometer in the fields of extrusion technology, thermoforming and 3D printing, Fakuma 2023 is being eagerly awaited. The issues of digitalisation, process automation and energy efficiency are just as high up on the agenda as circular economy and sustainability. Enhanced machines and optimised processes will also be exhibited. New products and forward-looking business models are expected as well. The exhibitor forum with world-class expert presentations will deliver inspiring impetus for all relevant topics.
“Fakuma is internationally recognised as a business platform for innovations throughout the value creation chain”, observes Bettina Schall, trade fair promoter and managing director of P. E. Schall GmbH & Co. KG. “We cordially invite all industry players to visit Fakuma 2023 in Friedrichshafen. It’s the ideal platform for discovering new products and technological solutions, as well as for personal and professional dialogue concerning present and future challenges”. Fakuma 2023, with its practice-oriented format and informal atmosphere, will be an essential milestone for finding solutions to the demanding tasks currently faced by the industry.
As a recyclable material, plastic is an indispensable constituent of everyday life –in the private sphere, for business and in technology
The ALPLA Group, together with its joint venture partners Ecohelp and UPT, has opened its first PET recycling plant in Romania after a construction time of nine months and investment of around 7.5 million euros.
Around 18,000 tonnes of post-consumer-recycled PET (rPET) per year – the packaging and recycling specialist ALPLA, Ecohelp SRL (Romania) and United Polymer Trading AG (Switzerland) begin production at their joint recycling plant in Targu Mures. The three companies invested around 7.5 million euros in the construction and equipping of the plant on an adjacent site to the existing Ecohelp site in Targu Mures. Now, the first extrusion line for the production of high-quality rPET granulate from PET flakes has entered into operation. The joint venture partners have hosted the official opening ceremony last May.
“The growing importance of local recycling
processes calls for increased commitment in the region”, says Georg Lässer, Director Business Development, Procurement and Sales Recycling at ALPLA. “Together with our partners, we combine strengths, increase the processing quality of the recycled PET material and ensure the long-term supply of the southeast European market”. Expansion potential has already been identified – the plant has space for a second extrusion line, which would double capacity.
The joint venture, which was established in autumn 2021, combines the skill sets of the three companies involved. ALPLA brings its
At the new plant, the joint venture Ecohelp and UPT produces recycled PET granulate based on bottles from household waste for the production of new preforms and bottles
Copyright: ALPLA
many years of expertise as a global recycling specialist and packaging manufacturer, while United Polymer Trading (UPT) has an extensive distribution network for plastics and recycled material. The local company Ecohelp supplies the material in the form of recycled PET flakes based on PET bottles from household waste. The food-grade rPET granulate obtained from this process then serves as the starting material for new preforms and bottles.
“The collaboration is a great example of how to improve local recycling and ensure sustainable economic development. We are filling a gap in the market for high-quality recycled material in Romania and neighbouring countries”, says Mihail Moloiu, General Manager at PET Recycling Team Targu Mures. The new recycling plant has created around 20 new jobs. ALPLA is investing 50 million euros a year until 2025 in the ongoing expansion of its recycling activities. With its activities for the production of high-quality recycled materials, the global company is promoting complete recycling in as many parts of the world as possible. In total, the annual production capacity of ALPLA’s recycling companies and collaborations around the world amounts to approximately 203,000 tonnes of rPET and 74,000 tonnes of rHDPE.
Copyright: ALPLA
Epax has reported close to total circularity for its marine biomaterials, thanks to a strict zero-waste policy. In 2022, 96.7% of by-products resulting from the manufacture of Epax’s marine oil ingredients were used to create other valuable resources, including animal feed, fertiliser and biogas.
The achievement is announced in the Norwegian marine lipid specialist’s first annual Environ-
ment, Social and Governance (ESG) Report, in which it commits to increase the figure to 98% by the end of 2023. To its knowledge, Epax is the first Omega-3 ingredients supplier to set itself biocircularity targets or to report on its progress in the area.
The ethos of circularity – also known as the circular economy – is to minimise the use of raw materials, maximise product
reuse and recycling, and make new products from waste and by-products. Currently, just 7.2% of all materials input into the entire global economy are used to create new resources at the end of their useful life.
Epax’s ESG report also provides an overview of other measures the company has taken to minimise its environmental impact, promote social responsibility across the supply chain and improve corporate governance. These have already resulted in a 33% reduction in fuel oil use since 2019 and a 13.3% cut in CO2 emissions since 2020.
The new ESG strategy builds on Epax’s first environmental stewardship policy, EcoVision, which it launched in 2010 as part of a commitment to responsible and sustainable operating practices.
“Epax has a long-standing commitment to sustainability, and an
Krall Kunststoff-Recycling can now prove that the CO2 equivalents of the PMMA, PET and PC regrinds produced there from post-industrial plastic waste are up to 95% lower than those of corresponding virgin materials. One key to this particularly high contribution to sustainability is the extensive use of solar energy generated in-house. The calculation of the carbon footprints, which was carried out at a renowned institute, was based on the international standards DIN EN ISO 14040 / 14044 on “Life Cycle Assessment” and DIN EN ISO 14067 on “Carbon Footprint of Products”.
“The documentation of greenhouse gas savings gives our customers and partners a valuable aid for proving and evaluating their own environmental measures”, comments Markus Krall, company founder and managing director. “The high values that apply specifically to our regrinds make a particularly positive contribution to this”.
As a further confidence-building measure, Krall has already demonstrated in the course of an audit by TÜV Rheinland Cert in 2022 that the quality management system anchored in the company fulfils the extensive requirements of ISO 9001 in all areas, from purchasing to goods
exceptionally high level of biocircularity is a key element of our plans for the future”, said Bjørn Refsum, CEO of Epax. “This is increasingly important as consumer demand grows for sustainably produced omega-3 products and full ingredient transparency. To our knowledge, we’re the first supplier in the sector to report on our progress towards full circularity, but we hope that others will now do the same”.
The report sets out 12 goals to be achieved by 2030, including 100% renewable energy usage in Epax’s Ålesund factory by 2025, using 80% less potable water by 2025 compared to 2021, and achieving an absolute reduction in CO2 emissions year-on-year to 2030. The goals align with five specific UN Sustainable Development Goals (SDGs): clean water and sanitation (SDG 6), decent work and economic growth (SDG 8), responsible production and consumption (SDG 12), climate action (SDG 13), and life below water (SDG 14).
receipt, preparation and storage to distribution and dispatch of the goods.
TÜV Rheinland Cert also confirms that the company complies with the strict criteria of the Ordinance on Specialised Waste Management Companies. This certification is tailored to the specific conditions in the industry and at Krall covers the storage, treatment and recycling of waste from technical plastics, polyolefins and composite materials. It certifies the technical and expert knowledge as well as the reliability of the management and the responsible persons in the company.
Rapid urbanization and changing lifestyles have encouraged the expansion of plastics application in a wide range of industries such as food and beverage, automotive, electronics and electrical, home appliances, and healthcare. It is no surprise that the global production of plastics has reached 400 million tons each year with projected 35 billion tons produced by 2050, as announced during the United Nations Climate Change Conference (COP27) held in November 2022. Plastic consumption – especially for single-use plastics – has created
a huge challenge to our environment. The industry now spares no effort to intensify innovations towards a circular economy for sustainability development.
Based on a report by World Bank, around 2 billion tons of municipal solid waste is being generated every year and this is expected to reach 3.5 billion tons by 2050. For the fast-growing regions of the world, such as East Asia and Pacific region, their plastic waste generations are expected to increase by 70% by 2050. It is imperative for the governments in this region to act fast. Another finding by the Ellen MacArthur Foundation claimed that the world’s oceans could contain around 937 million tons of plastic compared to 895 million tons of fish by 2050. The coronavirus pandemic that began in 2020 pushed single-use plastics usage by as much as 300%. These findings have put the plastics industry at task to come up with urgent solutions to alleviate the burden to the planet – and the circular economy model has been identified as the best option.
The plastics industry has long been applying the linear model, or “take-make-dispose” approach where plastics are produced, used, then disposed as waste, bringing challenge to waste management and environment protection. As a solution, the circular economy concept aims to reduce the amount of plastic waste generated by applying a “closed loop” system where plastics is produced, used and re-used in a continuous cycle to
By 2050 the global production of plastics will probably reach 400 million tons each year. That’s why plastics industries need to invest even more in the circular economy: to reduce the amount of plastic waste generated by applying a “closed loop” system where plastics is produced, used and re-used in a continuous cycle.
prevent its leakage to the environment. This model is seen as an appropriate way to address the core of the issue, especially for single-use plastics, as redesigning how plastic products are taken, made, used and reused to minimize plastic waste.
Packaging, for example, accounts for the largest segment of plastic applications. Circular economy as applied in packaging requires innovations in production technologies and materials to ensure that the plastic products are reusable, recyclable, or compostable. It also places responsibility to businesses engaged in plastic packaging to ensure that disposed items are collected, recycled or composted, for re-use as input in the manufacture of new product.
The vision for a circular economy includes reducing the need for single-use packaging and transitioning towards 100% reusable, recyclable or compostable to alleviate the plastic waste problem. In a study done by Nanyang Technological University in Singapore, it was found that reusable plastic bags are actually more environmentally-friendly than those from paper and cotton, but only in cities and countries with efficient waste management system.
O ne of the main thrusts of circular economy is the increased rate of recycling. Post-industrial waste and post-consumer waste need to undergo recycling in order for them to be re-used. Recycling technologies have seen tremendous improvements in terms of speed, efficiency and cost-saving advantages.
Recent trends in recycling indicate the growing interest in chemical recycling technologies, which break down plastics into building blocks to convert them into secondary raw materials that can be used to produce new raw materials. The growing popularity of pyrolysis, an advanced recycling technique where thermal decomposition of
materials at high temperatures in inert atmosphere is applied, has attracted attention especially since it has been found to be ideal in recycling polyethylene (PE) and polypropylene (PP). Chemical recycling is ideal for multi-layered or heavily contaminated plastic; another advantage is that the process can turn out high quality recycled material. BSH Hausgeräte GmbH for the first time uses BASF’s Styropor® based on a raw material made from chemically recycled plastic waste as a packaging material for selected large appliances of its luxury brand Gaggenau without compromising the protection properties for transportation. But the prevailing technology for plastic recycling remains mechanical recycling – which includes steps such as sorting, washing, shredding, grinding or granulating. Mechanical recycling has become better and more efficient in turning out good quality secondary materials. Digitalization, artificial intelligence and automation have contributed to more efficient recycling operations that many companies
The circular economy model is seen as an appropriate way to address the core of the issue, especially for single-use plastics, as redesigning how plastic products are taken, made, used and reused to minimize plastic waste
offering recycling technologies have added these to the capabilities of their machines. As the market for recycled plastics has been promising, recycling systems have been upgraded to meet rising demands. Bottle-to-bottle recycling has been taken to a higher level in processing post-consumer PET bottles to high-grade recycled PET (rPET) material, making it possible to produce bottles from as high as 100% recycled PET (rPET).
Also, bottle-to-bottle recycling has been able to meet the high safety standards required for food packaging with no risk of contamination. Another innovation is the development of techniques in recycling of multilayer flexible packaging that now, 100% of multilayer film production waste can be recycled. Processing technologies are now well able to adhere to the circularity targets. Injection molding systems, extrusion technologies and blow molding systems capable of processing recycled materials are the result of huge investments poured into R&D by companies to adapt to this trend. In the same manner, materials solutions geared toward improving the properties of recycled resins, such as additives and stabilizing agents, have been supporting the plastics industry’s bid for sustainability.
The adoption of circular economy in the plastics industry presents multiple opportunities for recycling technologies, plastics production systems that
The prevailing technology for plastic recycling remains mechanical recycling, which includes steps such as sorting, washing, shredding, grinding or granulating
are capable of processing recycled materials, and new materials with recycled content or content from renewable sources. It also offers opportunities for producers of finished plastic products who are eager to meet market trends and consumer preference for environmentally-friendly products. It is projected that by 2030, a circular economy could generate an additional US$4.5 trillion in annual economic output, according to the United Nations Environment Programme. Countries in Asia have started to provide the necessary framework towards a circular economy. China is spearheading this direction as the country has started its circular economy journey since the 1990s. One of the policies is the “Dual Carbon Goals”, which aims at bringing carbon emissions to a peak before 2030 and achieving carbon neutrality before 2060. Today, China’s strategy promotes circularity - reduce, recycle and reuse into the production processes as embodied in its Development Plan for the Circular Economy under the 14th Five-Year Plan covering 2021-2025. India has also adopted the circular economy route with its government implementing policies and projects which could potentially bring US$624 billion in annual by 2050.
Southeast Asian countries are also adopting the circular economy model with a framework approved by the ASEAN Economic Community (AEC) in October 2021. This opened up the region’s plastics industry to utilize the latest technologies in recycling and production systems that can very well process recycled materials to produce new products.
TotalEnergies and Intraplás are collaborating to bring sustainable solutions to the packaging market, without compromising on performance and food safety. Intraplás is launching commercial products using TotalEnergies RE:newable polymer – a range of the RE:clic portfolio - coming from renewable sourcing therefore allowing for a substantial reduction of the final product’s carbon footprint.
TotalEnergies’ world-class biorefinery in La Mède (France) allows to leverage a direct access to renewable feedstock for its drop-in RE:newable polymer range. The resulting polymer is warranted under the International Sustainability and Carbon Certification (ISCC PLUS) scheme, which uses a mass balance approach. As a result, the RE:newable range exhibits virgin-like properties suitable for high-end, demanding applications, while significantly reducing carbon emissions.
Intraplás technical and commercial expertise have been fundamental in bringing this innovation to the packaging market. As the converter’s facilities are ISCC PLUS certified, thus facilitating traceability from the material production through to the final application, Intraplás is able to provide high-performing, low-carbon, fossil-free products to its customers that need sustainable solutions in food packaging.
“Our RE:newable range is essential in achieving TotalEnergies’ ambition to produce 30% circular polymers by 2030. Our leading position as an integrated player on the market enables TotalEnergies to provide its customers with low-carbon, drop-in polymers from renewable sources in industrial quantities”, said Oliver Greinver, Vice President, Polymers Europe & Orient at Total Energies. “This collaboration with our long-term partner Intraplás is another
important milestone. Innovation is increasingly critical for companies to distinguish themselves in an increasingly competitive market”.
“If innovating is essential to create value, the sustainability of an innovative product is the best basis for responding to socio-environmental challenges. It is our commitment to offer to the market more eco-friendly packaging solutions”, said Marisa Alves, Chief Procurement officer of Intraplás. “We are increasingly investing in the incorporation of materials from renewable sources without compromising food safety, consumer well-being and product performance.
This collaboration with our partner TotalEnergies is in line with our goals to reduce our carbon footprint, and provide more sustainable packaging solutions to our customers, consumers and contribute to a better world”.
Following standardised testing procedures, Avery Dennison’s permanent adhesive is the first of its kind to receive a RecyClass Recyclability Approval. The laboratory findings show that this technology is compatible with the coloured high-density polyethylene (HDPE) recycling stream in Europe.
The technology is a white pressure senstivite label applied on an HDPE bottle, composed of a facestock and a polyolefin-based hotmelt adhesive. Separate evaluations were carried out both on a PE-based (PE Top White CF3050) and a PP-based (PP Caviated Top White CF3050) facestock.
According to the independent testing carried out by the Institut für Kunststofftechnologie und -recycling (IKTR), following the RecyClass Recyclability Evaluation Protocols, the technology is compatible with the given recycling stream if
the amount of adhesive represents 1% of the total packaging weight and that the facestock is either clear or white (The full list of conditions is available in the Approval Letters: Avery Dennison “PE Top White CF3050” and Avery Dennison “PP Caviated Top White CF3050”)
During the evaluation, the recycled material generated through recycling was successfully tested in high-value application such as HDPE bottles with up to 50% concentration.
With this approval, the plastic industry will benefit from additional understanding on adhesives and decoration technologies, and more specifically how their functionality can be paired with recyclability – aspects which will become increasingly important as the transition toward a circular plastic future accelerates.
A new study confirm that plastic recycling rate in Europe is still low and needs developments in technology and strategies to increase circularity. Mechanical recycling has been the reference technology for years but, in the near future, chemical recycling options are expected to give a great support to this industry.
According to a new study by several researchers from the Joint Research Centre (JRC) of the European Commission and the University of Gent and Maastricht, Europe’s plastic recycling rate is low, and new technologies and strategies are necessary to increase circularity. Together with further innovation in mechanical recycling (MR), chemical recycling (CR) technologies are expected to contribute to boosting plastic circularity, the study says.
This study uses a material flow analysis (MFA) at European level to provide quantitative estimates of the contribution of CR technologies to plastic recycling. Ten most used polymer types from five sectors are selected. A status quo 2018 scenario is modelled and compared to five potential future scenarios (in 2030) of plastic waste treatment, including one that only looks at improved waste collection, sorting, and MR technolo-
gies and four exploring developments of CR options.
The so-called ‘missing plastics’, i.e., plastic waste generated but currently not accounted for in statistics, is considered in one of the future scenarios. The MFA results are compared by calculating four circularity indicators namely end-of-life recycling rate (EoL-RR), plastic-to-plastic rate, plasticto-chemicals rate, and plastic-to-fuels rate. The results indicate that in the most optimistic scenario the EoLRR in 2030 is 73–80% (sum of plastic-to-plastic and plastic-to-chemical rates, excluding plastic-to-fuel rate), in which 41–46% is plastic-to-plastic from MR, 15–38% is plastic-to-plastic from CR and 19–35% is plastic-to-chemicals. The highest achievable plastic-to-plastic rate is estimated to be 61% (46% from MR and 15% from CR). In all future scenarios, the plastic-to-fuel rate is estimated to be 3–6%. The MFA results are also used to
estimate potential recycled content availability in 2030, which suggest that closed-loop recycling and processing the ‘missing plastics’ will be necessary to achieve the targets.
“We need more advanced recycling technologies next to other systemic views to achieve the quantitative targets and a qualitative circular economy”, said Steven De Meester, one of the authors of the study entitled “How much can chemical recycling contribute to plastic waste recycling in Europe? An assessment using material flow analysis modeling”.
In Europe, the current end-of-life recycling rate is around 18%, which mainly comes from mechanical recycling. The study suggests that chemical and solvent-based recycling technologies, together with further improvements in mechanical recycling, could lead to an overall end-of-life recycling rate (to plastics and chemicals, excluding
To provide resources of equal quality to primary resources, the quality of recycling needs to be considered
fuels) of up to 80% by 2030, with chemical recycling becoming complementary, not competitive, to improved mechanical recycling. The findings also suggest that capturing and treating “missing plastic”, i.e., plastic waste generated but currently not accounted for in statistics, when considered in one of the future scenarios, could significantly increase recycled plastic production and help reach recycled content targets in some sectors.
To provide resources of equal quality to primary resources, the quality of recycling needs to be considered. This includes not only aspects such as yield and footprint but also the material properties and substitution potential. “Quality means the materials should be suitable for the circular economy and should be able to substitute primary resources over a broad range of applications”, explained De Meester.
The chemical industry has already announced major investments of commercial scale covering different chemical recycling technologies in Europe and worldwide. However, one of the main barriers to scaling up these technologies is uncertainty about the method for calculating the recycled content of plastics. A clear mass balance method is key to overcoming this challenge. Mass balance is one of the well-known and widely used “chain of custody” models that gives a
high level of confidence that what is put in the process does come out at the end. It is already successfully deployed in other sectors, such as fairtrade cacao and coffee. EU rules supporting chemical recycling as a complementary solution to mechanical recycling are needed to attract investments into these technologies and help the EU meet targets for more recycled content. The findings of the researchers of the JRC and the University of Gent study should also be used by policymakers to support proposals for achievable recycled content tar-
EU rules supporting chemical recycling as a complementary solution to mechanical recycling are needed to attract investments into these technologies and help the EU meet targets for more recycled content
gets and to determine which recycling technologies can play a role in achieving these targets. Recycled content targets can incentivise the uptake of recycled content, leveraging the power of Europe’s single market. In conclusion, mainstream technologies alone will not be sufficient to achieve circular economy goals, and advanced recycling technologies are necessary to provide resources of equal quality to primary resources, also starting from a broader set of waste feedstock types.
Source: Cefic
To remain competitive, more and more processors are taking the recycling of plastics into their own hands. Vecoplan supports them with this process and proactively helps shape the change.
The HiTorc drive is distinguished by its high level of efficiency, the drive enables the machine to be started up under full load
Europe wants to be climate-neutral by 2050 – and the circular economy for plastics will make a telling contribution. The core element of the EU Packaging and Packaging Waste Directive is the recycling rate. By 2025, member countries must recycle at least 65% of their packaging waste, which will increase to 70% by 2030. The production of goods and commodities generates harmful emissions that increase the natural greenhouse effect. This inevitably leads to temperature changes with far-reaching consequences for the climate. Greenhouse gas emissions must therefore be reduced by at least 55% throughout Europe by 2030, and Europe intends to be climate-neutral by 2050.
“The circular economy is one of the tools that can be used to achieve these goals,” says Martina Schmidt, who heads the Recycling and Waste division of Vecoplan AG. Vecoplan is one of the leading suppliers of machinery and equipment for processing primary and secondary raw materials for thermal and material recycling. “In the field of product design and packaging, using recy-
cled plastics offers many possibilities for substitution,” says the Vecoplan expert. “According to the UMSICHT study by the Fraunhofer Institute, climate-damaging greenhouse gas emissions can be reduced by up to 50% if recyclate is used instead of new granulate from crude oil. We have to leverage this potential”. However, recycling is not only crucial for climate neutrality, it also conserves valuable resources and the environment. A wide range of industries in the plastics industry are undergoing a transition.
The aim is to increase the recycling rate and use the advantages of plastic in such a way that no damage is caused to the environment. The increasing demand in the various industries is leading to a tense supply situation and acting as a price driver.
Processors can quickly and cost-effectively satisfy the demand for high-quality recyclates by taking reprocessing into their own hands and following a holistic approach. “We work
closely with our customers in developing our solutions”, says Schmidt. “In the past, processors always came to us with new challenges, which motivated us then – and still does today – to actively shape this change”. The shredding of the materials is particularly challenging. For example, yarns, fibres and filaments are available in different thicknesses, in various and often extreme lengths and are made from various plastics. However, despite all their differences, they also share some unique mechanical properties – they are tough, wear- and tear-resistant and very elastic – which makes shredding all the more difficult.
“A homogeneous output material is optimal for all downstream processes”, says Schmidt. “That’s why excessive lengths and fine particles should also be avoided because they can cause disruptions or losses during the process”. In addition, to ensure effective downstream processing of the plastics, the characteristics of the input material must not be changed by the heat input that arises during shredding.
Vecoplan relies on its exceptional HiTorc drive to achieve the best possible energy efficiency during shredding. Thanks to eliminating mechanical drive elements such as belt and gear drives, flywheels and clutches, the direct drive is 10-15% more efficient. The HiTorc is dynamic, has a strong start-up phase, is low-maintenance and is insensitive to extraneous materials. “Our HiTorc is the Tesla among today’s drives”, comments Martina Schmidt.
To meet the high demands for the recycling of very different materials, Vecoplan revamped its proven, successful VAZ shredder series with the latest benchmarks in industrial design
Achieving the optimal coordination for the case at hand then continues with the selection of the ideal cutting unit, and here Vecoplan technicians work closely with their customers. “We develop shredders, which we individually coordinate through many tests in our technology centre. The test results are documented, made available to the customer and included in our database”, adds Schmidt. The database now includes more than 3,000 tests. Output material temperature, noise emission, torques and cutting forces are monitored and recorded in real time. Vecoplan also has an in-house laboratory for measuring moisture, testing material and determining grain size & density. Simple maintenance and the greatest possible ease of operation are essential aspects of all developments.
But, is there a perfect machine? “To answer this question, we first have to define what we mean by a perfect machine”, confirm Schmidt. “Is it a shredder that’s correctly configured for the usage scenario? And can it handle a few measures such as adjustments to the cutting force, a changed cutting geometry or output size? “Our shredders offer a high degree of flexibility
to meet these requirements”. Or should a perfect machine ensure stable processes and produce consistently high throughput and a homogeneous output material at all times? “Our customers also trust us to provide them with these machine features too”, says the Vecoplan expert.
To meet the high demands for the recycling of very different materials, Vecoplan revamped its proven, successful VAZ shredder series with the latest benchmarks in industrial design – and presented the series for the first time at IFAT in May 2022. The modular design of this single-shaft shredder particularly convinces users. The new shredder is also equipped with the Vecoplan Smart Center (VSC), Vecoplan’s powerful digitalisation concept for the maximum efficiency of shredders and systems. The integrated and intuitive VSC. control operating panel serves as a communication medium for the cutting-edge control of the machine and direct communication with Vecoplan. VSC.connect enables users to network their machines and access additional online services, such as remote service, key performance indicators and even a media database.
Coperion K-Tron announces the expansion of the original ProRate™ PLUS feeder portfolio with more solutions for feeding powders. A ProRate PLUS-MT twin screw feeder will be added to the product line that will be available end of April 2023. Together with the recently introduced ProFlow™ bulk solids activator the new twin screw feeder is an efficient solution for feeding powder additives in plastics applications. Last year Coperion K-Tron developed a completely new feeder line built on 100 years of feeding experience to provide a robust and reliable feeder for simple feeding applications in the plastics industry. The ProRate PLUS continuous gravimetric feeder line is an economical solution and offers a quick return on investment due to its good price-performance ratio and fast delivery times. The original product line featured three single screw feeders that are ideal for the feeding of pellets, granules and other free-flowing bulk materials in secondary plastics applications.
For more difficult to handle materials Coperion K-Tron is expanding the ProRate PLUS product line with a new twin screw feeder, the PLUS-MT. This gravimetric feeder with its horizontal agitator ensures that the two screws are always optimally filled with material. The twin screw technology also has the advantage of reducing pulsations and the screws have a self-cleaning effect. Twin screw feeders are ideal for difficult to handle powder additives such as talc, calcium carbonate or carbon black. The steep design of
additional vertical agitator. Should material bridging or ratholes still occur, one or more ProFlow bulk solids activators can be mounted on the hopper to promote material flow. The new ProRate PLUS-MT twin screw feeder can handle throughputs from 40 up to 1800 dm3/h [1.4 to 63.6 ft3/h], depending on bulk material characteristics. With individual bulk solids tests in our test centers, we can determine more precisely what the exact feeding range is for a specific bulk material.
Together with the new ProFlow™ solution, the scope of the original ProRate PLUS single screw feeders has been expanded to include moderate flowing powders and flakes. The solution is available for all four models (PLUS-S, PLUS-M, PLUS-L, PLUSMT) and can be installed on new equipment or as a “mounting kit” on existing feeders. The ProFlow bulk solid activator consists of an electromagnetic vibrating device, which activates the feed hopper to keep bulk ma-
terials moving. The device operates at an optimized frequency and amplitude to ensure minimal energy consumption and maximum product flow. Thanks to its smart electronic control, ProFlow only uses 3.6 Watts of electricity. Tests with a wide range of bulk materials have shown that ProFlow is an ideal solution for a variety of bulk materials. ProFlow has no wear parts and since it is mounted outside of the product contact area, there is no additional cleaning effort needed. For the smaller PLUS-S model, the ProFlow activator is implemented in conjunction with specially developed overflight screws.
The ProRate PLUS feeder line features a space-saving trapezoidal shape which allows up to six feeders to be easily grouped around an extruder inlet within a 1.5 meter [5 ft] radius. The four feeder models PLUS-S, PLUS-M, PLUS-L and PLUS-MT cover a wide range of throughputs. The ProRate PLUS feeders are capable of handling feed rates from 3.3 up to 4800 dm3/h [0.12 up to 400 ft3/h], depending on the material. Theoretically, a feeding
system with six ProRate PLUS-L feeders can feed up to 28.8 m3/h [1017 ft3/h] on a footprint of only 7 m2 [75 ft2].
ProRate feeders are highly standardized and include a variety of design features to optimize performance and ease of use. Simple access for cleaning and maintenance, even within a cluster, is provided thanks to a patent-pending rail system called “ProClean™ Rail”. ProClean Rail makes it possible to retract the base unit toward the rear of the feeder and rotate it for access to the feeding section and screw element while keeping the feeder in position. In addition, the bellows and screws use the latest magnet technology for simple but robust mounting. The magnet connections allow these parts to be released without tools while at the same time providing the required holding force for optimal and safe operation. All ProRate PLUS feeders are equipped with P-SFT load cells, featuring reliable Smart Force Transducer single wire weighing technology. Each feeder also comes equipped with its own prewired and pre-tested ProRate PLUS PCM control module. The PCM is mounted to the feeder stand, with adjustable height positioning. Most feeders only need a basic motor control unit (PCM-MD) while one feeder per group of eight is equipped with an advanced
Coperion K-Tron is expanding the ProRate PLUS product line with a new twin screw feeder, the PLUS-MT
version featuring an integrated user interface and line control functionality (PCM-KD).
ProRate PLUS feeders and the ProFlow bulk solids activator are suitable for use in hazardous locations rated NEC Class II, Div. 2, Group F & G and ATEX 3D/3D (outside/inside).
Preconfigured pneumatic refill solutions are available for each feeder size. Each feeder can be outfitted with either a filterless vacuum receiver for pellet applications or a vacuum receiver with a cartridge filter for applications where there may be dust that must be kept out of the air only line of the vacuum conveying system. Refill solutions include a compact support stand, level indicators, butterfly valves and electrical terminal boxes as well as one or more vacuum blowers as needed. The Series 4 MPC controller is ideal for up to 24 vacuum receivers on one blower with one back-up blower.
MANAGING DIRECTOR: Simone Ghioldi
EDITORIAL BOARD: Alessandro Bignami (a.bignami@interprogettied.com), Eva De Vecchis (e.devecchis@interprogettied.com)
GRAPHIC LAYOUT: Studio Grafico Page Vincenzo De Rosa, Rossella Rossi - www.studiopage.it
INTERPROGETTI EDITORI S.R.L. via Roggia Borromea, 16 - 22060 Carugo (CO) Tel.: +39 031 3665163 vendite@interprogettied.com - www.interprogettied.com
SALES DIRECTOR: Marika Poltresi
SALES: Simone Ghioldi (vendite@interprogettied.com)
ADMINISTRATION: amministrazione@interprogettied.com
© Copyright Interprogetti Editori Srl
The columns and news are realised by the editorial team. All rights reserved – All reproduction, even partial, of published material without the publisher’s consent is strictly prohibited.
SUBSCRIPTION RATES:
Italy: ordinary mail delivery EUR 45.00, COD delivery EUR 48.00
International: ordinary mail delivery EUR 60.00, express delivery within Europe EUR 70.00
Express delivery to Africa, America, Asia: EUR 85.00
Express delivery to Oceania: EUR 100.00
Single copy: EUR 10.00
The VAT on subscription prices as well as on the price of single copies is paid by the publisher pursuant to article 74, sub-section 1, point C of the Italian DPR n. 633 of 26th Oct 1972 and subsequent amendments and additions. It is therefore not possible to issue invoices.
Registered at the Court of Milan on 3th June 2010 no. 315
Managing Director: Simone Ghioldi
Print concluded on July 31, 2023 at Aziende Grafiche Printing S.r.l.
Via Milano, 5 - 20068 Peschiera Borromeo (MI)
Information to be given to the data subject - art. 13, legislative decree 30th June 2003, no. 196. Personal data are processed, with or without the help of electronic means, by Interprogetti Editori S.r.l. - Via Roggia Borromea, 1622060 Carugo (CO) Italy, to send you the magazine requested and for the operations connected. The processing of data will be carried out by the persons who have been committed by the controller the task of performing the processing operations connected with recording, modification, processing of personal data and printing, fulfilment and delivery of magazines, commercial and fiscal issues, accounting and call center activity. With reference to art. 7, Italian legislative decree 196/2003, you have the right to access to your data, modify, update or cancel data or to object to their processing for direct marketing purposes, by writing to the controller, and ask for the list of data processors.
Publisher’s information to public – art. 13, legislative decree 30th June 2003, no. 196. With reference to Italian Personal Data Protection Code and art. 2, point 2 of Code of Conduct for the processing of personal data in the exercise of journalistic activities, Interprogetti Editori S.r.l. informs that the place where personal data, images and photos are kept is Carugo (Italy). Data can be used by journalists, free-lance journalists, persons in the role of trainee journalists and persons who carry out processing for the publication or occasional circulation of essays, articles and other intellectual works for the purpose of the exercise of their journalistic or similar activities. The processing of data will be carried out by the persons mentioned above and by persons in charge of printing and publishing activities. With reference to art. 7, Italian legislative decree 196/2003, you have the right of access to your data, modify, update or cancel data or to object to their, by writing to Interprogetti Srl, and ask for the list of data processors. It is understood that the provisions concerning professional secrecy in the journalistic profession shall be left unprejudiced as related to the source of the information if a data subject requests to be informed of the source of the personal data processed by journalists.
In this issue, we spoke about...
Haitian MM Italy is responsible for sales and assistance of Haitian / Zhafir injection molding machines for thermoplastics for the Italian and Romanian market. The company based in Brescia has contributed to the intense growth of the Chinese brand in Italy and is also responsible throughout Europe for the die-casting machine made by Haitian. With a structure of 4,000 square meters, it allows to optimize logistics operations to more easily manage the machines arriving from Haitian, also considering the addition of die casting technologies.
Haitian MM Italy company is able to deliver to the user a complete and turnkey package, which includes everything that revolves around the press: from the automation and robotics system (with relative CE certification of the working area) to the safety fences and to Formax peripherals. It also proposes itself as the single contact for the entire order, helping the customer to adopt a solution that respects of the parameters for Industry 4.0. The sales network is made up of 20 sales man as well as the after-sales service with 30 technicians covering the Italian territory.
Hilectro robots: Automation working areas made by Hilectro, member of Haitian Group
Haitian JupiterIII series: Space saving two-platen technology
From 4,500 to 66,000 kN
Large mold space, compact machine design
Energy-efficient servo-technology
KEBA control technology
Haitian Mars K series: Hydraulic servoassisted machine for packaging with high injection performance of up to 1,000 mm/s
Zhafir Zeres Medical series: Electric machine equipped with medical package for cleanroom
Zhafir Zeres Multi series: Electric bi-injection machine with second injection unit R-type (piggyback)
Zhafir Jenius series: Electric injection unit and the two-platen servo hydraulic system From 3.600 – 33.000 kN
Large mold space, compact machine design Injection units with 1,2 and 4 spindle concept 15-inch SIGMATEK controller