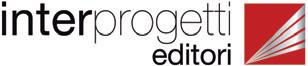
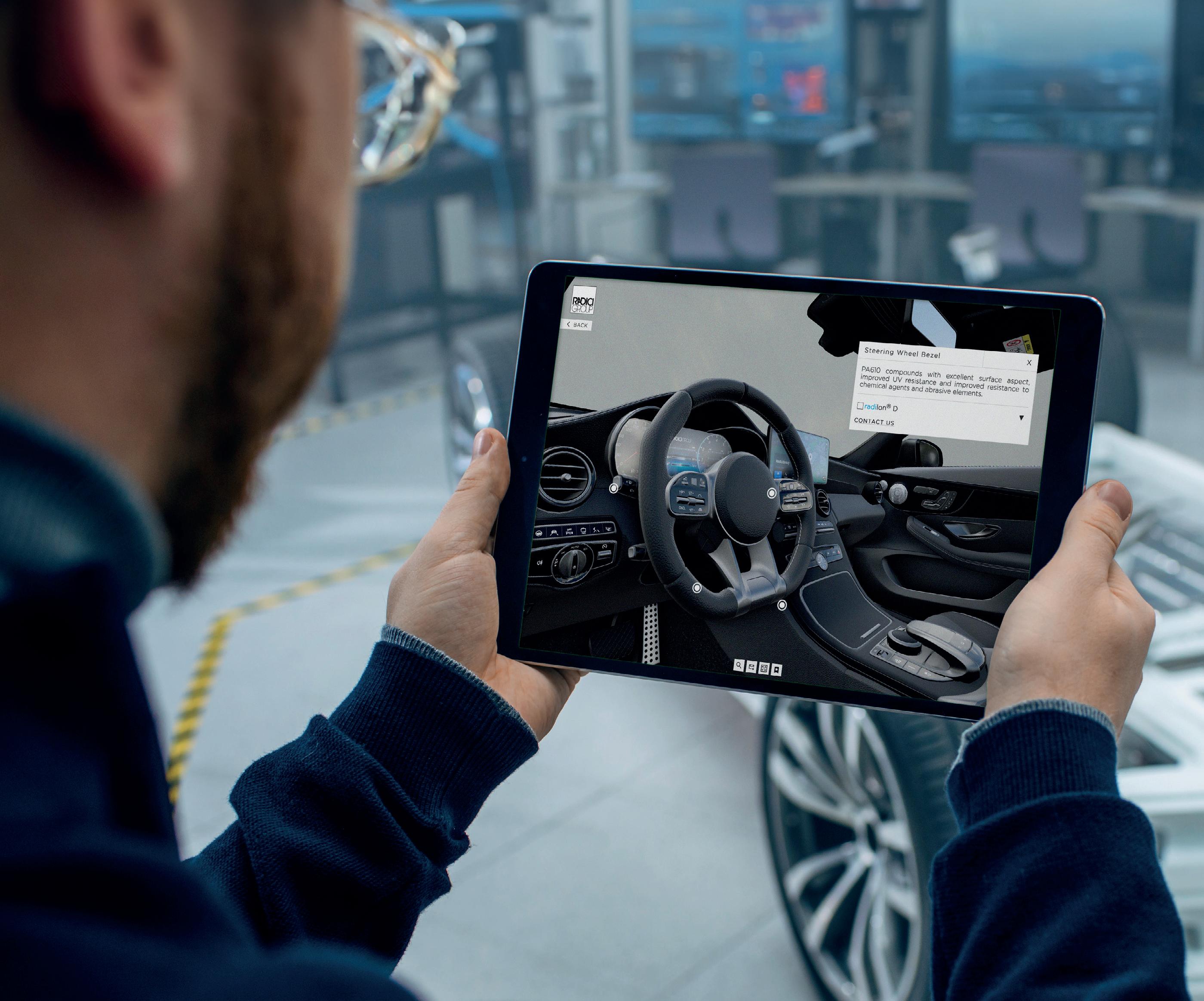
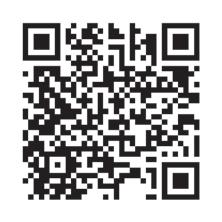
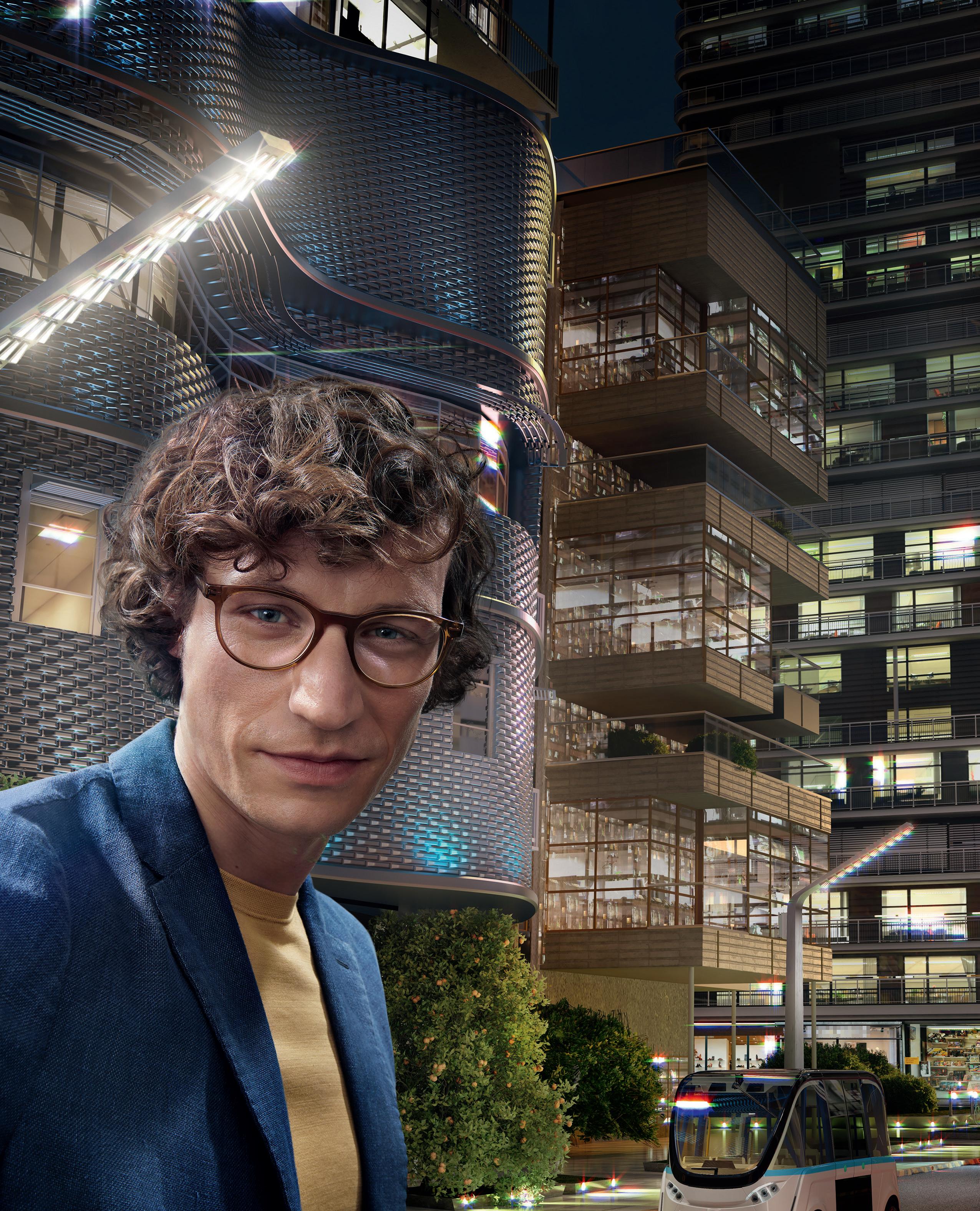
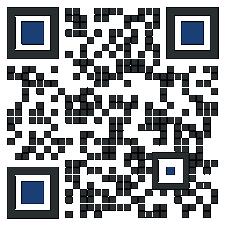
Fakuma
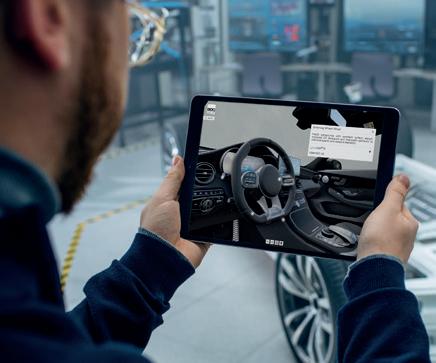

Fakuma

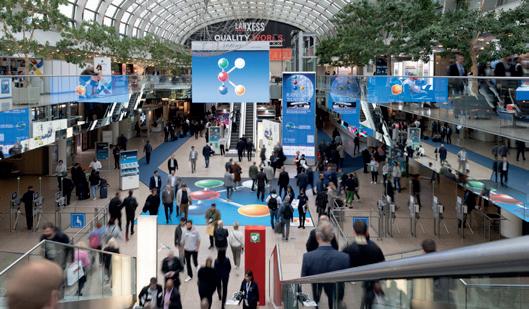
Fakuma
Smart and flexible solutions to increase efficiency
Fakuma 2024 The green side of technical compound
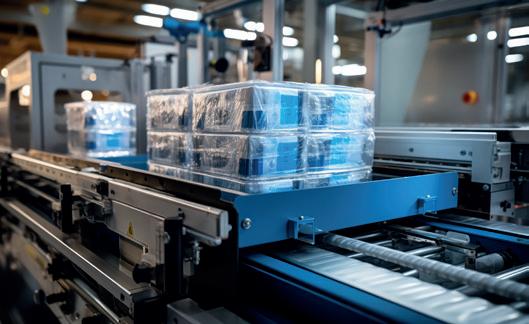
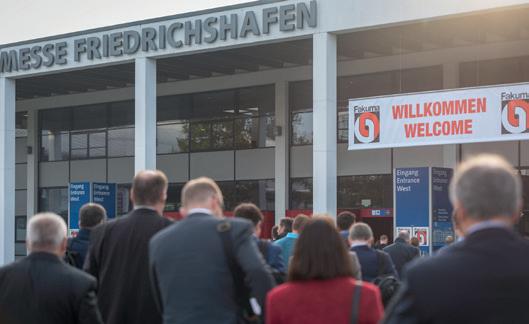
Fakuma 2024 A reality focused on every need
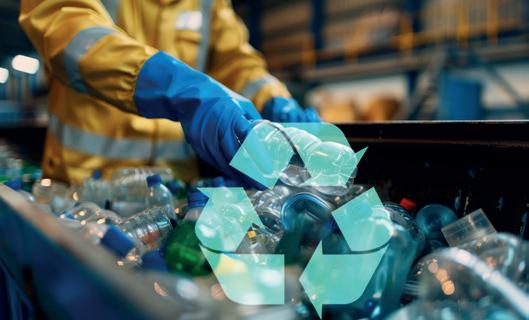
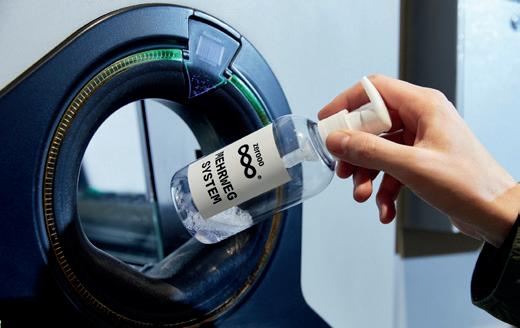
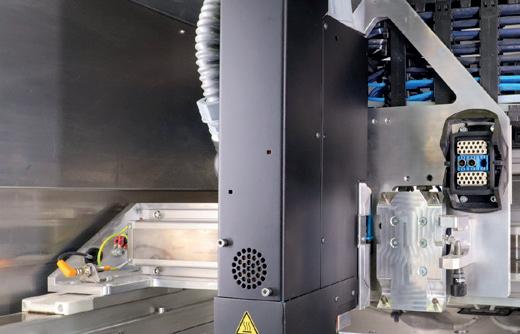


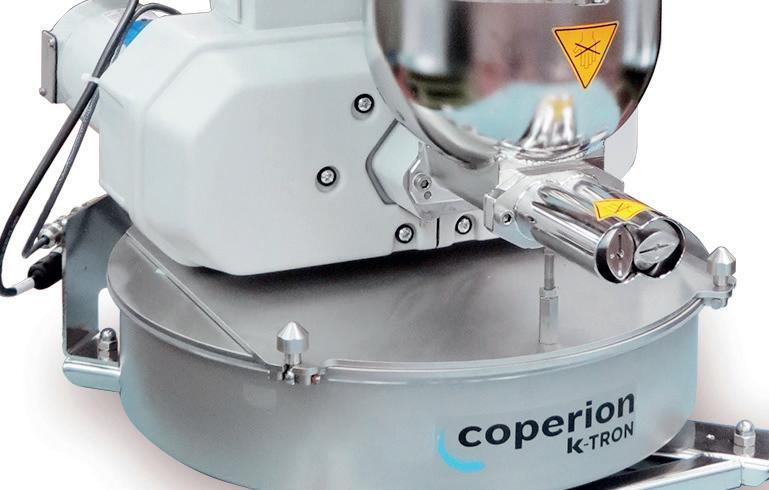
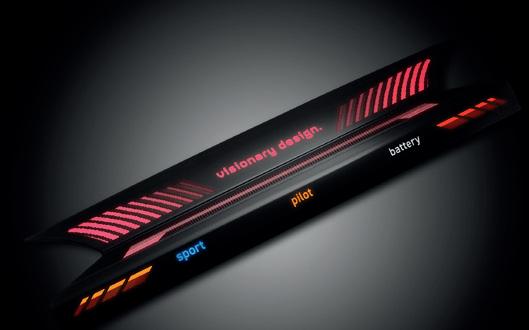
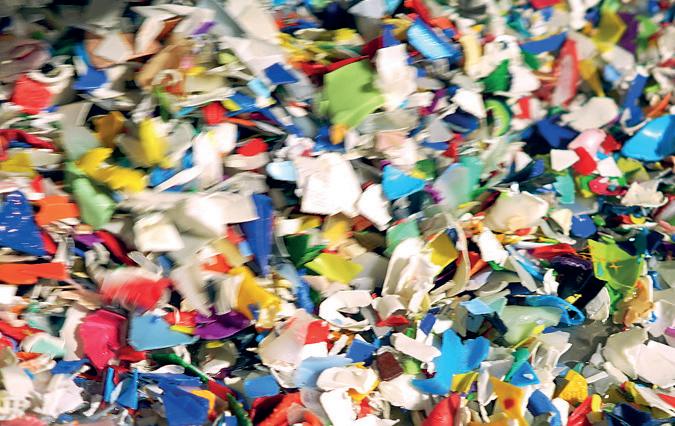
Fakuma
Fakuma
Fakuma
Smart and flexible solutions to increase efficiency
Fakuma 2024 The green side of technical compound
Fakuma 2024 A reality focused on every need
The plastics industry has shown, and continues to show, mixed signals both globally and nationally, with Italy demonstrating some particularly interesting results. Italian exports of machinery for plastics processing had a positive year, especially in Europe (+9.2%) and Asia (+8.1%), with significant growth in China (+12.4%). The American market also saw major increases, with a 20.2% rise. However, certain non-EU regions experienced declines, such as the Far East (-1.3%).
According to the Circular Economy Network (CEN), Italy excels in circular economy practices, ranking first among the top five EU economies. Resource productivity is high, generating €3.7 per kilo of materials, surpassing the EU average. The country leads in waste management, with 71.7% of packaging waste recycled in 2021, and has strong results in WEEE recycling. However, material consumption has increased, and reliance on imported materials remains a challenge. In addition to this, a survey of SMEs revealed that 65% are adopting circular economy strategies, with the recycling of critical materials like copper and rare earths seen as essential for the future. Overall, both in Italy and abroad, the sector is increasingly adapting to sustainability challenges, with a growing focus on transitioning towards a circular economy. Roberto Bertaggia, Petcore Europe Executive Director and the Association’s past president also addressed this in an inter-
view with La Plastica Oggi e Domani. He noted that the European PET market has changed significantly in recent years, with an increasing focus on recycling. Many companies now view recycling as an opportunity, especially with the integration of chemical and mechanical technologies. So, what should be done next? Effective communication to consumers is key to promoting recycling culture and combating misinformation. Understanding the surrounding environment and opportunities is crucial for action and engagement.
One way to do this is by attending the 29th Fakuma International Trade Fair for Plastics Processing in Friedrichshafen from October 15th to 19th, 2024. This leading international event will emphasize sustainability and the circular economy. The fair will focus on energy efficiency, recycling, and the use of renewable raw materials, with numerous innovative solutions aimed at improving material circularity and reducing waste. Technologies promoting design for recycling and the development of more sustainable plastics, including post-consumer and post-industrial recycled polymers, will be showcased. A key highlight will be the “Fakuma Roundtable,” where experts will discuss the importance of digitalization in achieving sustainability goals.
Eva De Vecchis
The most important challenge in the coming years for high-performance plastics industry lies in meeting the needs of increasingly critical applications, while reducing the environmental impact. Carrying out such a complex task requires a great capacity for innovation and research, as well as an important industrial history. Over these years, RadiciGroup has demonstrated this, by strongly focusing on innovation and sustainability, developing engineering polymers containing mechanically recycled or bio-based polyamide capable of offering in many cases performances comparable to virgin materials. At Fakuma 2024, sustainability will once again be the Group’s central message, as explained by Erico Spini, Global Marketing Manager of the RadiciGroup High Performance Polymers Business Area.
E-mobility, solar power, hydrogen, electrical/electronic and consumer-goods market. These are some of the industrial sectors
RadiciGroup High Performance Polymers is innovating by using new materials, including those with a lower environmental impact, keeping the required performance even in the most demanding contexts.
by Alessandro Bignami and Eva De Vecchis
Mr. Spini, your air intake manifold made of 100% recycled Renycle® was recently awarded by the Society of Plastics Engineers (SPE). What about the features of this material?
“The air intake manifold is made of 100% Renycle®, the RadiciGroup brand that identifies engineering polymers obtained from mechanically recycled nylon. The air intake
manifold is a high technology application typical of the automotive sector, where glass-fibre reinforced nylon has almost completely replaced metals over the years.
RadiciGroup supplies both PA6-FV and PA66-FV polymers for various engines of motor vehicles worldwide. However, there is an ever-increasing demand for a reduction in the environmental impact of materials, the
Erico Spini, Global Marketing Manager of the RadiciGroup High Performance Polymers Business Area
The air intake manifold made of 100% Renycle®
challenge therefore was to use a 100% mechanically recycled polyamide material, the result of a careful process involving the selection, cleaning and control of raw materials to ensure very high quality consistency. Together with our partner Marelli, which produces the component itself, we developed this 100% mechanically recycled polyamide material. While Marelli is responsible for the functionality of the final product, we are responsible for the material performance and quality constancy, which can be compared to the one of top-of-the-range materials. We took part to the Society of Plastic Engineering contest because we thought it was a highly innovative and sustainable project on a critical application.
Marelli, on its turn, optimized the component as against the specific application, focusing on stringent performance requirements: high burst pressure, pressure pulsation and pro-
longed vibration tests subjected to thermal cycles, thermal shocks. Particular attention was paid to NVH (Noise Vibration Harshness) analysis with the aim of ensuring, among other things, acoustic performance in line with the other materials used today. RadiciGroup also tried to maximize the environmental benefits. Emission reduction allowed by the use of recycled material is dramatic, since its production cycle does not foresee high environmental impact phases, such as fossil fuel extraction and polymerization”.
Are there still investments in material innovation for the internal combustion engine?
“The main driver, again, remains sustainability. The development of new materials for high temperature powertrain, for example, is less required than a few years ago. The real challenge will be to introduce alternatives to existing materials, the measurement of envi-
ronmental impact a new variable. Today, however, development activities for new materials in the powertrain segment are almost completely from internal combustion engines to electric traction engines, where the functional requirements are very different”.
In Western markets, however, there has been a slight slowdown in the growth of e-mobility
“Undoubtedly China is the leader in the electric car market today. According to the latest data, the sale of electric vehicles – both full and plug-in – has reached 50%. They are designed with an important focus on aesthetics, Internet connectivity and, of course, price. The situation in the West, on the other hand, still shows some critical points, as we know: from consumer concerns about car’s autonomy - also in the light of the still insufficient infrastructure and charging stations - to the still high selling prices. It will take time,
“The Radiflam® family has some characteristics that make them particularly interesting: high impact resistance at low temperatures, easy and safe component moulding, safety for the integrity of the electrical parts”
but the trajectory seems clear and irreversible. The acceleration will probably come with the introduction of new technologies, such as those expected in the coming years for the development of very high-performance batteries”.
Last July, you dedicated a webinar to the sustainability strategy of the RadiciGroup High Performance Polymers Business Area: what innovations did you present on that occasion?
“Regarding mechanical recycling, both post-industrial and post-consumer, we described three applications of our polyamides in as many industrial sectors: the automotive industry, for which we showed the air intake manifold recently awarded by SPE; the consumer goods industry; the electrical/electronic industry. As for bio or partially bio materials, we illustrated a product that is already in our range: polyamide 610, called Radilon® D, which showed excellent results in reducing environmental impact. We also talked about some products in development, in-
cluding polyamide 56, particularly suitable for the automotive and electrical/electronic industries. In fact, it can be formulated in a flame-retardant version”.
What are the renewable sources you use the most for your productions?
“For polyamide 610, the bio-based raw material is represented by castor oil seeds. Castor oil, once extracted, is processed to obtain the molecule needed to produce the
material. The bio part of polyamide 56 derives from lysine, which in turn comes from agricultural products such as corn, sugar cane or from waste not useful for human consumption”.
Is the cutting-edge plant you built in China already producing the desired results, also considering the growing demand for electric cars in the country?
“This plant represents absolute excellence for us and hosts our main productions for that market. So far, the program has been respected and we are optimistic about the future of the building, which was designed and built to meet a demand destined to grow strongly in the coming years”.
Which are the most innovative trends of the plastics market in China?
“In addition to materials for the electric car industry, another sector in which China is leading the way is solar energy. The Government invested heavily in supporting the production of electricity from photovoltaic panels. This area offers us a couple of interesting applications, especially those related to PV connectors, for which we developed flame retardant materials based on red phosphorus. RadiciGroup and its partners have developed and tested the material, belonging
to the Radiflam® family. This type of products have some characteristics that make them particularly interesting: high impact resistance at low temperatures, easy and safe component moulding, safety for the integrity of the electrical parts (absence of corrosion)”.
What is your main message at Fakuma 2024? Is there any previews scheduled for the European market?
“The first message we will communicate in Friedrichshafen is once again related to sustainability, connected with the latest novelties in the Renycle® range and to solutions derived from renewable sources. For this purpose, we will emphasize our PA610 offer, together with an overview of the products still in the experimental phase. Another focus will be e-mobility, a sector on which car man-
ufacturers are increasingly focusing their investments: here RadiciGroup has developed some innovative solutions that complement the current range of flame retardant products known under the Radiflam® brand. I am referring to products based on PBT (Radiflam® B), and on PPA (Radiflam® Aestus), both halogens - free. The two materials, also orange-coloured for applications with electrical parts under high voltages, will allow a targeted choice based on specific requirements, such as the need to ensure good electrical insulation at high temperatures, to get component better dimensional stability and so on. For the electric car, the challenge of the future is to manage more energy for a more efficient and high-performance battery and for fast charging.
Finally, at Fakuma, RadiciGroup will be focusing on the hydrogen industry, which has an excellent potential, especially in the field of high-purity materials for fuel cell components, that in the future will be used mainly for large vehicles (trucks and buses). In addition, materials from the Radilon® family (for blow molding and injection molding processes) suitable for the production of “liners” for
hydrogen tanks, both for use in the industrial and in transportation sectors, will also be presented. Technical features required: high impact resistance at very low temperatures, low hydrogen permeability, easy processability”.
To ensure a sustainable development of the European PET industry and to prevent unfair competition practices from jeopardizing the continent’s future, it is essential to engage in dialogue with the European parties involved and be open to new technologies.
PET market in Europe has changed. While until a few years ago, we could talk about a scenario featuring a prevalent production of virgin PET and the topic of recycling was still little known, now, the goal of manufacturing a recyclable con-
tainer with a percentage of recycled material has become a reality and is increasingly evident, as Roberto Bertaggia, Petcore Europe Executive Director and the Association’s past president explains. Yet the focus on recycling must be constant and, to best convey the theme, it is as important to take political actions as it is to have clear and correct communication towards the consumer.
Roberto Bertaggia, what do you think has changed over the years within Petcore Europe and, more generally, in the Eu-
ropean PET market?
“Much has changed over the last 8/10 years. As far as the Association is concerned, it has grown exponentially both in terms of members and activities. Until a few years ago, the members were a few dozens, now they are about 160 (including 9 associations) and Petcore represents 400 companies, 500 production sites in Europe, 27,000 people employed in the sector, 4.5 million tons of market, 1.5 billion euros turnover, more than 150 recyclers. Operations are carried out through 9 working groups
that embrace all sectors of interest, covering the main recycling issues and involving our entire industry, from bottles, to trays to labels, developing guidelines to facilitate recycling and circularity (‘design for recycling and circularity’). The same big virgin PET manufacturers now are looking at recycling as an opportunity and not as a danger, not just thinking of a merely chemical recycling, but also of novel technologies that can offer ideas for a further use of mechanical recycling. These key changes aren’t free from dangers: the European Union must understand that safeguarding local industry and prevent unfair competition is not “protectionism”, but it means to ensure a safe future to a society whose goals are ambitious and that is asking industry to make them happen”.
Many companies in Italy are preferring chemical to mechanical recycling. Are there actually advantages in terms of environmental and economic impact in choosing one over the other?
“My professional background has always led me to make objective judgments based
on scientific data rather than emotions. Mechanical recycling requires an investment that is certainly lower than the one required by ‘at scale’ chemical recycling plants, in some cases the differences are meaningful (even by a 10 factor).
Even production schedules are different, faster for mechanical recycling plants than for chemical ones. Talking about environmental impact, clearly, mechanical recycling, starting from post-consumer bottles as raw material, features a lower energy consumption and CO2 production requirement than a PET polymerization process, which concerns both virgin PET and chemically recycled PET. Let’s however underline how chemical recycling, if on the one side is similar to virgin PET in terms of consumption, on the other is fully independent from non renewable resources. Moreover, chemical recycling as against mechanical recycling has the advantage to start from difficult raw materials, as well as from materials mechanically hard to recycle (for instance containers with covering or multi-layered colours, or the waste of polyester fabrics, at least for the most difficult fractions). The two mechanical and chemical technologies are complementary, not antagonistic and
“The two mechanical and chemical technologies are complementary, not antagonistic and the development of recycling and circularity is showing this more and more clearly”
the development of recycling and circularity is showing this more and more clearly”.
Can PET packaging play a key role in achieving Europe’s climate neutrality goals, especially through recycling?
“First and foremost, when we talk about climate neutrality and the role that PET can play in this context, we should distinguish and properly communicate to the consumer the meanings of ‘recyclable’, ‘recycled content’ and ‘circularity’: this is essential to ensure transparent communication. Countries that have a strong knowledge of recycling market and technologies, such as Italy, must become politically active in promoting the culture of recycling and correct information: plastic bottles do not end up in the sea or rivers by their own initiative but because there is a lack of awareness that the post-consum-
er bottle is a resource and not waste.
The spreading of scientifically incorrect concepts such as ones relating with the release of potentially dangerous substances (such as bisphenol A) from PET bottles must also be fought at a legal level for a higher protection of scientifically correct information, to prevent phenomena similar to flat-earthism from having the right of citizenship. PET, which is approved for food use, does not pose any health risk: this is not my statement but that of DG Sante, the Commission that deals with public health and food contact at European level”.
We can say that today being sustainable is not a choice, but a duty. What are the priorities that a company must give itself to define itself sustainable?
“In my opinion, priorities are simple, but should be pursued firmly and constantly and are:
1. A business management including the use of renewable energy or at least a plan to achieve a high degree of independence from fossil fuels.
2. The reuse of resources (for example water).
3. A focus on products that is not only aimed at post-consumption (which is still important) but that takes inspiration from a sustainable products design (such as containers designed to facilitate reuse and/or recycling).
4. A scientific dissemination plan of recycling culture, conservation and saving of resources aimed at collaborators and the society we deal with”.
must ensure that they continuously support the development of modern “design for circularity” concepts.
2. Collaborate actively with the European institutions in defining the methodologies for measuring the results obtained and the controls to be carried out, for example, for recycling certifications (an initiative already recently launched in collaboration with DG Sante).
3. Harmonizing recycling standards and measuring them within the supply chain. We have also just started this project, always in collaboration with the European institutions.
What are Petcore Europe’s plans for the near future? And what are the most complex challenges to face?
“The challenges I see for Pectore as a supply chain association are new and old at the same time and are:
1. Bringing greater harmonization within the industry that allows for a coordinated approach to the issues of circularity and sustainability (through our working groups, for example, in the bottles and trays sector), to enable the entire PET industry to achieve the goals set by legislators. Our working groups are a reference point for the industry and we
4. We have recently started LCA (Life Cycle Assessment) evaluation projects that allow us to have a scientifically valid methodology to evaluate products placed on the market.
The new working group on polyester textiles has a very ambitious but achievable goal: to reuse polyester fibre waste as a raw material for chemical recycling.
The reason why Petcore Europe is gathering more and more members is inherent to the ability to meet society’s needs and requests and to propose realistic and practicable solutions and this is, and will remain, our task”.
Solvay, a global expert in essential chemistry, announces the opening of its groundbreaking Alve-One production unit in Rosignano, Italy. This marks a new milestone with the launch of a significant European production facility for Alve-One, a chemical blowing agent eco-designed to transform the thermoplastic foaming industry.
Solvay’s Alve-One unit aims to address the growing demand for safer and more sustainable blowing agents in various consumer and industrial uses, globally. These include automotive, footwear, building & construction, and consumer goods, aiming to reduce carbon footprints in foamed end-products while enhancing overall health and safety standards to protect both people and the environment.
“The inauguration of our Alve-One production unit in Rosignano reflects Solvay’s dedication to delivering innovative and sustainable solutions that directly benefit our
customers and society”, said Etienne Galan, President of the Soda Ash & Derivatives business at Solvay. “This facility equips us to effectively address our customers› evolving needs, while also fostering a positive environmental footprint. It marks a pivotal advancement in our mission to lead transformative change across multiple industries, guaranteeing our customers access to top-tier solutions that meet their highest expectations”.
The inauguration ceremony took place in Rosignano, Italy, with esteemed guests including customers, partners, and Italian authorities. Among the attendees are key players operating in the thermoplastic foaming industry, including those in artificial leather for automotive and fashion, wallcovering, packaging and insulation materials, footwear, yoga mats and other sports apparel sectors.
Alve-One solutions have received official recognition as a sustainable alternative for
foamed thermoplastics from various organizations. These include the International Chemical Secretariat (ChemSec), the Solar Impulse Foundation, which acknowledged it as an Efficient Solution, Inovyn, which honored it with an Innovation Award and France Chimie, which awarded it with the Pierre Potier Prize.
> estrusori > dosatori > componenti > trasporto pneumatico > sistemi completi
+ Sistemi di controllo completi per impianti di movimentazione materiali
+ Comprovato leader globale nelle soluzioni di dosaggio nei processi produttivi
+ Componenti altamente qualificati garantiscono affidabilità ed efficienza nei sistemi di movimentazione materiali
+ Sistemi di controllo all’avanguardia progettati per esigenze tecnologiche esistenti e future
Montenegro S.r.l. Via Volturno, 37 20861 Brugherio (MB)
Tel: +39 039 883107
Fax: +39 039 880023 info@montenegrosrl.it
Quando si tratta di progettare un sistema di processo per garantire affidabilità, risparmio energetico ed efficienza, sulla scelta dei componenti non guardate altrove, cercate su www.coperion.com/it/componenti
The circular economy involves recycling, reusing, and repurposing of products to extend their usable lifetime.
Among the oil and gas industry’s conventional products, plastic is the most relevant to the circular economy. Increasing demand for circular economy solutions in the oil and gas industry, especially regarding plastics, presents several long-term opportunities for companies. Companies can invest in the production of circular polymers, thereby making it easier to recycle plastics. Moreover, there is a considerable scope to increase their recycling capacities, allowing them to fulfil ESG goals by reducing virgin plastic production, says GlobalData, a leading data and analytics company.
GlobalData’s thematic report, “Circular Economy in Oil and Gas”, discusses the need for circular economy in the oil and gas industry to address plastic pollution. It also highlights the role of major oil and gas companies, such as ExxonMobil, Shell, and TotalEnergies, in their efforts to establish circular economy for plastic as a commodity.
“The use of plastics has skyrocketed in the last few decades and has accelerated plastic pollution in the soil and aquatic environments”, said Ravindra Puranik, Oil and Gas Analyst at GlobalData. “As awareness about the ill effects of plastic use grows among consumers, several countries and some enterprises are taking steps to remedy the situation, while ensuring the economic activity re-
mains unaffected”.
Plastic is an essential commodity in today’s economy. Overuse and mismanagement of plastic upon end-of-life results in a huge amount of waste, leading to pollution. This calls for efficient recycling of plastic waste. In 2019, less than 10% of the plastic waste generated was recycled compared to the 460 tons of the commodity produced that year.
“Several economies are taking steps to limit their plastic pollution and encourage circularity”, Puranik continues. “The European Union has set specific targets to reduce the use of single-use plastic in its jurisdiction. Countries in other regions, such as Japan and Australia, have also set targets to eliminate plastic waste generation”.
The ill effects of plastic waste and the non-renewable nature of fossil fuels used its production has prompted efforts to achieve sustainability with plastics.
This involves reducing plastic waste from going to landfills, being incinerated, and largely being mismanaged. There is a need to improve plastic waste and facilitate recycling, extending its usable lifetime. This can alleviate demand pressure on virgin plastic that annually enters the market.
“Companies are working to find suitable alternatives, to minimize the dependence on plastic made from conventional methods”, Puranik concludes. “The use of bioplastics is an emerging trend in the industry. Bioplastics are produced using alternative feedstock such as agricultural waste. Industry leaders such as BP, Shell, and TotalEnergies, have set themselves targets for plastic recycling. Companies are pursuing approaches such as mechanical recycling, chemical recycling, besides bioplastic production to support their ESG commitments”.
The Tetra Laval Group Board has appointed Pietro Cassani as President & CEO of Sidel from 15 July 2024. Pietro will be based in Parma, Italy. The appointment follows the decision by Monica Gimre to step down after more than five years as President & CEO of Sidel and 41 years in total with the Tetra Laval Group. Pietro has been CEO of the Marchesini Group for
the past eight years, and before that spent over 10 years as Group General Manager of SACMI. In total he has over 30 years of business and engineering experience. He holds an Engineering degree from the University of Bologna, and a Master of Business Administration degree from the SDA Bocconi School of Management.
PepsiCo and GreenDot announced aN agreement to support investment to recycle plastic waste back into recycled materials that can be used for PepsiCo’s snacks packaging. GreenDot, a holistic solution for plastic circularity provider, has been expanding its German sorting and recycling
activities and developed additional assets in Austria and Italy. The group now also incorporates advanced recycling in its portfolio to be able to supply circular polymers to brands and converters.
This collaboration comes at a critical time as PepsiCo Europe aims to eliminate virgin fossil-based plastic in all its crisp and chip bags by 2030.
“We are happy with this new collaboration which now goes beyond EPR licensing and establishes a new business model and closes the loop between waste plastic and recycled content in packaging”, says Mark Vester, EVP for Business Development and the German Business at GreenDot.
“This agreement is an important milestone for the industry”, states Laurent Auguste, CEO of GreenDot. “It further paves the way towards a circular economy of plastic packaging, with the support of a new type of long-term collaboration between key players of the value chain. I wish to congratulate PepsiCo for their vision, leadership
and for walking the talk, in line with their goal to increase the recycled content in their packaging and to reduce their carbon footprint. GreenDot will invest in developing plastic packaging to packaging recycling capacities, including advanced recycling of polyolefins, providing needed solutions at scale for the food industry”.
“The partnership is critical to scaling our operations and working together towards our shared goal of creating a circular economy for packaging”, says Archana Jagannathan, Chief Sustainability Officer at PepsiCo Europe Advanced and mechanical recycling are part of a broader suite of recycling we are leveraging to bring us one step closer to this goal. Closing the loop between plastic and recycled content is a central part of our PepsiCo Positive agenda. We aim to reduce the waste we send to landfill in our direct operations and across our value chain”.
PepsiCo and GreenDot are currently collaborating on new snacks packaging for Sunbites crisps which contain 50% recycled plastic film packaging. This new packaging was launched in the UK and Ireland in late 2023, and the company is expecting to expand this further.
Zeon expands the ACM production capacity up to 20 Ktpa
Zeon Europe GmbH – the European subsidiary of Zeon Corporation, Japan, a worldwide synthetic rubber producers, focuses on the new development of its acrylic rubber (ACM) products. Acrylic rubber ACM is a specialty oil-resistance rubber for high temperature application up to 180 °C. It is commonly utilized in the automotive sector for oil sealing, gaskets, turbo hose, fuel hose cover, and air duct achieving a broad range of OEM specifications. Not only for combustion engines, e-mobility is opening new yet challenging opportunities. With 20.000 tons per year capacity from 4 locations in 3 countries, Zeon commits to be the most reliable acrylic rubber supplier and the number one producer of ACM worldwide.
By virtue of the polymer, ACM’s current application is indeed dominated by the usages in the combustion en-
gines. The electrification of mobility has brought new challenges and opportunities to the whole sector. Equipped with its long experience and know-hows, new ACM developments and compound studies, Zeon – with the application technologists in the frontier – is ready to intensify the development partnership to generate tailored solutions. Already now, ACM based gaskets are used in e-axle, the combination of motor, axle, and gearbox in a unity.
Considering the full package of functionalities, costs, and the business continuity plan (BCP), especially in the current uncertain market situation when BCP becomes a decisive factor, ACM can be the best choice. Zeon expanded the ACM manufacturing capacity by building a new plant in Thailand, that started to go on stream in 2022.
“We have been introducing a new grade with a broader service temperature range and an acid resistance type as a potential solution for the so-called Worst Case Oil issue”, explained Marcus Santoso, Commercial Manager ACM of Zeon Europe.
Exhibition space at K 2025 is in high demand the world over. The coming K will focus on the industry’s relevant fields of action: circular economy, digitalisation and social responsibility.
K 2025 will follow on from an extremely successful event in 2022. After the official registration deadline in late May one thing is certain: all renowned companies in the international plastics and rubber industry will take part in this their leading trade fair held in October next year. Demand for stand space is high and all 18 halls of Düsseldorf Exhibition Centre and the outdoor premises will be fully occupied again.
“K 2025 will provide the complete overview of a plastics industry undergoing transformation and again have a plethora of impressive innovations in store”, explains Erhard Wienkamp, Managing Director at Messe Düsseldorf. “We know that many of our exhibitors are already preparing their product innovations and presentations at full speed. Düsseldorf will once again provide forward-looking impetus for the entire plastics and rubber industry”.
More than 3,000 exhibitors will participate in K 2025 from 8 to 15 October and introduce the global expert audience to their ranges in the areas of:
• Raw materials, auxiliaries.
• Semi-finished products, technical components and reinforced plastic parts.
• Machinery and equipment for the plastics and rubber industry.
Especially well represented again will be the suppliers from Germany, Italy, Turkey, Austria, Switzerland and the USA while the number of producers from China, India and Taiwan has increased yet again.
Green, smart and responsible
“The Power of Plastics! Green – Smart –Responsible” reads the slogan of K 2025, which is complemented by three core messages “Shaping the circular economy”, “embracing digitalisation” and “caring about people”. This places the focus on the three most relevant fields of action for the sector: Circular Economy, Digitalisation and People. The latter involves corporate social responsibility just as much as future career perspectives for young professionals in the plastics and rubber sectors.
K in Düsseldorf is a trend barometer and innovation forum for the global industry. Every three years the latest developments
celebrate their debuts here, innovative and pioneering technologies are presented and international networks established. The exhibitors’ ranges at their stands are complemented by K’s special formats. The special show organised by Plastics Europe Deutschland, will also reflect the three focal themes of K 2025. At the Science Campus the latest activities and results of university and science organisations will be presented again – here research and business are dovetailed. Organised by the plastics and rubber machinery association within the German machinery and equipment Manufacturers’ Association (VDMA) a large Circular economy Forum is planned to feature on the outdoor premises where exhibitors demonstrate the pivotal importance of technology for implementing the circular economy in the plastics industry. A Hotspot on the theme of rubber will be the re-designed Rubberstreet under the auspices of the wdk e.V. (Trade Association of the German Rubber Industry) in Hall 6. Here, exhibitors will be showcasing the innovative operational excellence of rubber and thermoplastic elastomers.
With Formnext Chicago, Mesago Messe Frankfurt is bringing the successful Formnext trade fair concept to the USA, the world’s largest AM market. From 8-10 April 2025, Formnext Chicago will showcase the entire industrial process chain for Additive Manufacturing.
“We see huge potential in US companies that have not yet encountered Additive Manufacturing (AM) or are not utilizing the benefits of this technology”, explains Sascha F. Wenzler, Vice President Formnext. “Our focus is on the various user industries to which we want to provide solutions. This will further raise awareness of the opportunities offered by Additive Manufacturing across the industry. We also intend to promote AM technologies and significantly increase our exhibitors’ business contacts”.
With Formnext Chicago, Mesago Messe Frankfurt is expanding its strategy of regionally adapted formats in relevant AM markets, based on the highly successful original Formnext event in Frankfurt. Examples to date include the Formnext + PM South China in Shenzhen, China, and the Formnext Forum Tokyo, Japan.
Agenda
Fakuma
15 - 19 October 2024
Friedichshafen, Germany fakuma-messe.de
Recycling conference
24 October 2024 Warsaw, Poland www.eplastics.pl/konferencje
Automotive Plastic Part Design
5 - 7 November 2024
Troy, USA www.ets-corp.com/lectures/ registration.htm
Formnext Chicago is being organized by Mesago Messe Frankfurt in collaboration with AMT (the Association for Manufacturing Technology) and Gardner Business Media. AMT is the organizer behind IMTS, the largest manufacturing trade fair in North America. Gardner Business Media is North America’s leading media company focused on machining, plastics processing, and other manufacturing technologies.
“Formnext was early to recognize the significance of the US market for the AM industry and announced the 2025 Chicago event back in 2021. The AM community’s global growth is evi-
Ecomondo 5 - 8 November 2024 Rimini, Italy www.ecomondo.com
Formnext 19 - 22 November 2024 Frankfurt, Germany www.messefrankfurt.it/it/fiera/ formnext
Chemical Recycling Europe Forum
27 November 2024 Brussels, Belgium
https://chemical-recycling-europe.prezly.com/
dence of the high demand for the successful format. Other suppliers, such as Rapid + TCT, confirm our assessment of the potential of the local AM sector, but are now holding their event at the same time as Formnext Chicago”, says Douglas Woods, AMT President. “We see Formnext Chicago as a great opportunity for the US application industries because it covers the entire additive value chain from material suppliers, software, and production systems to post-processing and quality assurance. This clearly differentiates the new format from existing 3D Printing or rapid prototyping events in the US market”.
Mecspe 5 - 7 March 2025 Bologna, Italy www.mecspe.com/it
Formnext 8 - 10 April 2025 Chicago, USA www.formnextchicago.com
Chinaplas 15 - 18 April 2025 Shenzhen, China www.chinaplasonline.com/ cps24/becomeanexhibitor/eng
SPS Italy 13 - 15 May 2025 Parma, Italy www.spsitalia.it
Greenplast 25 - 27 May 2025 Milan, Italy www.greenplast.org
K 8 - 15 October 2025 Düsseldorf, Germany www-k-online.com
The focus of Fakuma 2024 is on digitalization, automation, flexibility, energy efficiency and sustainability. Therefore, the international trade fair for plastics processing will be an opportunity to receive tools and solutions for the challenges of efficiency, the conservation of resources and sustainability.
The industry will meet in Friedrichshafen for the 29th Fakuma internati onal trade fair for plastics processing from the 15th through the 19th of October 2024. For many companies, the autumn highlight is one of the most important trade fairs and will once again be a celebration of plastics. Career Friday will take place for the first time this year with the objective of inspiring young people for careers in the plastics industry. The “Fakuma Roundtable” will be held for the second time, addressing this year’s topic of “Digitalization – Top or Flop?”.
Efficiency will be a key topic at Fakuma 2024 – on several levels and from a variety of perspectives. Increased efficiency in terms of materials and energy consumption is crucial, as are process efficiency and the efficient operation of production systems, because in light of current shortages of qualified personnel, consistently high levels of quality can only be achieved reliably and efficiently with easy-to-use control systems and digital assistance. As a result of the new Energy Efficiency Act, German plastics processors will be challenged to a much greater extent to realise their full potential. Fakuma exhibitors will provide tools and solutions for the chal-
lenges of efficiency, the conservation of resources and sustainability.
Career Friday for pupils, students and entry-level employees will be a new feature this year in keeping with the motto “Mould Your Dreams, Mould Your Future”. Together with the trade fair advisory board, trade fair promoters P. E. Schall are launching this campaign to inform young people about a broad range of career opportunities in the plastics industry. The event will be held as an integral part of the trade fair on the 18th of October 2024. Career Friday will provide the target group with the unique opportunity of meeting Fakuma’s international exhibitors in person at their booths and finding out first-hand about exciting career prospects. The exhibitors will offer young visitors insights into the world of plastics processing, product development and new technologies. In dialogue with industry experts, interested parties will receive exciting
background information on plastics processing and insights into work processes.
The overall focus of Fakuma is thus on digitalization, automation, flexibility, energy efficiency and sustainability. The establishment of closedloop material flows, product optimization targeted at recycling and the processing of recyclates for high-end applications will also be at the top of the agenda this year. Innovations in the field of injection moulding technology are being eagerly awaited – systems with all-electric drives that make machines flexible and powerful and raise them to a new level of efficiency. Fakuma will also provide new impetus for the aspects of holistic product design and the further development of recycling and degradability. Design for recycling – this goal is taking shape to an ever-greater extent in product manufacturing. Future-proof solutions for packaging, recycling compounds and alternatives to metal are therefore just as much in focus at the trade fair as machines for grinding and crushing, cooling systems and energy-efficient mould temperature control technology, systems for process monitoring and data acquisition, as well as innovations from the field of industrial 3D printing. The increasing use of renewable instead of fossil-based raw materials will also be a key topic.
HALL B3 - STAND 3208
The Italian company continues to invest in innovation to produce increasingly cutting-edge solutions. The R&D laboratory benefits of several state-of-the-art instruments involved in the design and development of its products.
Interconnected control room for remote assistance
Moretto, the Italian company based in Massanzago (Padua) expert in the production of automations for the plastics processing industry, will be present at Fakuma 2024 (at Hall B3 - Stand 3208) with several novelties. Moretto considers fundamental to invest in innovation, research and testing activities to design and develop future-oriented solutions. The laboratory of the R&D department consists in several state-ofthe-art instruments such as rheometers for viscosity control, a gas chromatograph for acetaldehyde control, a DSC for crystallinity control, professional sound level meter, fine dust measurement, infrared cameras, professional highspeed cameras (10,000 frames per second), temperature and airflow control, chilled mirror hygrometer for humidity measurement, anemometers and portable testing tools. In addition, Leonardo, the Supercomputer with a mathematical simulation software capable of calculations of:
• Load-bearing structures such as mezzanines, mechanical strength;
• Thermodynamics for controlling heat distribution;
• Fluid dynamics with analysis of air and fluid flows;
• Electromagnetism for electromagnetic energy analysis;
• Sound analysis, precision of acoustic impact on devices.
Moretto involves this high technological equipment in the design of its automations. They have been essential in the product development of Flowmatik, Kruise Kontrol, X Dryer, X Comb, X MAX, Kasko, and automatic One Wire 6. The challenge goes on with new products such as Gravix DGM 20, Kasko Filterless, X Comb 12, 6050 Hyper Cut grinder and Navigator 9001.
Gravix, high performance doser that elevates precision in micro-dosing: digital electronics, double eyelid shutter device, self-learning for a compact doser with great benefits for customers.
Kasko Filterless, a system suitable for plastic granules and/or regrind conveying with the same performance as a filtered system, while avoiding maintenance and filter cleaning.
X Comb 12, the smallest dryer in the market has a constant performance, -50 °C Dew Point, and very low energy consumption. Moretto offers the smallest dryer with OTX (Original Thermal eXchanger) hopper and
X MAX, the biggest dryer capable of 20,000 kg per hour suitable for large productions, extrusion and/or compounding guaranteeing constant efficiency. Moretto dryers range consists of 49 models offering a wide and complete product range in dehumidification. X Comb is the latest of 16 patents in drying. GR 6050 Hyper Cut, a newly designed, low speed grinder will be introduced in the market.
A starve feeding granulator suitable for grinding waste pieces, sprues and blowed parts with 15 movable blades. The engine power is transferred on a single mobile blade and three standard fixed blades. The 160-degree grid increases the GR productivity while reducing consumptions. GR 6050 Hyper Cut is 5.0 ready and second to none.
Navigator 9001, a control system developed by Contrex, a company of Moretto group, for blown film production. It is 5.0 ready allowing film production to start automatically in just 5 minutes compared to 25-30 minutes required by conventional automations available on the market. Navigator 9001 ensures double-digit energy savings for film production.
MOWIS, a proprietary supervision platform that simplifies the management of complex systems and provides an immediate view of the plant status for maximum benefits in terms of productivity, traceability, elimination of human error, and optimization of production costs. To enhance the after-sales service, an interconnected control room ensures remote assistance of the more than 2,200,000 units already installed worldwide. With 115,000 machines produced each year, Moretto is a short supply chain company that manufactures more than 75% of its components in-house in adherence to Smart Factory 4.0 criteria.
Many other technologies dedicated to the plastics processing industry will be on display at the exhibition. Products with high technological content capable of raising the quality standard, increasing production efficiency and energy savings of the supplied systems.
In a record-breaking year, Campetella Robotic Center will be exhibiting at Fakuma 2024 with solutions for complete automation lines and to meet the demands of a growing need to automate secondary packaging processes.
Campetella Robotic Center - an italian company specialized in the production and application of industrial robots and automation systems for plastic material injection molding - will participate at Fakuma 2024. On the occasion of the event, La Plastica Oggi e Domani interviewed the CEO Elia Campetella to find out how this year is evolving for the company and to know about the solutions it will bring to the fair.
Elia Campetella, how has 2024 been evolving for Campetella Robotic Center and what are the biggest challenges faced?
“This year the company has experienced an extraordinarily positive evolution, despite a somewhat slow start. 2024 turned out to be the best year ever for us. Our ability to quickly adapt to market needs and provide customized solutions has strengthened our competi-
tive position. We face the future with optimism, ready to consolidate the success achieved and explore new growth opportunities.”
What are the main application fields of your robots: are there some that, in your opinion, require your solutions more than others?
“The main industries our robots are addressed to are the packaging and the medical ones, where our solutions are particularly requested. In the packaging industry, our robots offer the efficiency and precision needed to manage high production volumes in short cycle times. Our technologies allow to significantly optimize packaging processes, improving speed while reducing errors. This is crucial for companies like ours, that have to face growing and variable demand.
As far as the medical field is concerned, however, our experience translates into robotic solutions that guarantee high standards. Our robots are employed in applications ranging from the production of medical devices to the assembly of sensitive components, where safety and quality are compulsory conditions. Our technology allows us to satisfy the strict regulations of this field and guarantee the highest product reliability.
Our ability to provide highly customized and cutting-edge systems has allowed us to stand out in these two markets and to face their challenges successfully, strongly contributing to the development and global competitiveness of our customers”.
Campetella values sustainability. Speaking of which, at the beginning of 2024 your company took part in the RENEE project, which aims to give new life to obsolete machines or their components by regenerating them so that they can be reintroduced into the production cycle. How is the project progressing?
“The project is progressing towards its ambitious goals and their consequent technological challenges. Campetella takes part in one of the 4 pilot projects financed by the program, together with Emotors, Decathlon and Arcelik. During these first months of the year, we have collected information about the product to be subjected to the remanufacturing cycle, that is the robot, and above all, we have studied the process which, up to now, is completely carried out by hand.
“In
the next months, Campetella will focus on the analysis and study of the most effective technologies to improve the remanufacturing process and make it sustainable from both an environmental and economic point of view”
Campetella has been following this practice for some time now, recovering old robots to be able to reuse some parts, especially the most long-lasting ones, and send the no longer usable materials to recycling processes. In the next months, we will focus on the analysis and study of the most effective technologies to improve the remanufacturing process and make it sustainable from both an environmental and economic point of view”.
What are your expectations on the Fakuma show, which will be held in Germany from 15 to 18 October 2024, and which solutions will you focus on?
“Over the last five years Campetella has managed to successfully increase its market share in Germany and Austria. In market segments such as food packaging, highspeed automation, caps and closures and IML technology, we succeeded at successfully equipping the largest manufacturers with the Campetella robots.
The local after-sales customer service in Germany and Austria ensures quick and easy assistance for the robots’ entire life cycle. Campetella means to be a unique partner for the creation of complete automation lines, from parts picking at the IMM to final packing in boxes or pallets. At Fakuma 2024 Campetella will exhibit two SCARA robots, called Spin, designed and developed
over time for the end-of-line packaging. The plastic packaging market needs answers to face the great challenges it is featured with. Campetella provides customized automation solutions that help its customers win these challenges and this is precisely what we would like to prove to our customers, both prospects and loyal ones, at Fakuma 2024”.
About the SCARA robots, can you tell us about their features and why you decided to spotlight this product too?
“The European market’s need to automate secondary packaging processes is strongly increasing and our SCARA robots are precisely intended to best satisfy this demand by guaranteeing the highest performance, in terms of both speed and precision. Campetella SCARAs are the perfect choice for end-of-line handling and palletizing, due to their many benefits:
• Long Vertical stroke with minimum footprint on the ground
• Maximum dexterity and flexibility with its 5 axes and free programming
• Either Palletizing or boxing of coils coming from more lines”.
How do you envision 2025 both for Campetella and, in general, for the industrial automation systems for the plastics injection molding field?
“We are optimistic about 2025 because, regardless of economic cycles, the trend of industrial robotics is growing. In fact, it is a crucial sector for advanced economies, particularly for those operating in the plastics injection molding market.
The new regulations regarding packaging and disposable products require the molding processes to change and that will necessarily lead to an evolution of production technologies, which will strongly involve industrial automation”.
Haitian International will be presenting its new generation of machines and showcasing complete solutions including peripherals.
clamping force regulation (HT·OptiForce), which reduces the clamping force from 500 kN to 80 kN, resulting in energy and material savings.
Another electric ZE1500V produces 1.2 g cable clamps (16-cavities) from PA6.6GF30.
The machine is equipped with a real-time monitor that visualizes the filling process. The dryer, material feed and temperature control unit are made by Haitian and are in-
This year’s Fakuma 2024 in Friedrichshafen is all about efficiency. This includes various aspects such as materials, processes, energy and more.
At Hall A1 - stand 1103, Haitian will be presenting its smart, flexible solutions designed to increase productivity and help companies remain competitive in a dynamic market. A total of six machines will be on display, three of them at its own stand and three more machines at the stands of Gollmer Formen GmbH (A2 - 2213), Nonnenmann GmbH (A11101) and TST DE GmbH (A1-1512).
All the exhibits at Fakuma represent the 5th generation of machine technology. This is characterized, among other things, by energy savings of 20-40% compared to its previous version and features innovations such as the HT·XTEND Smart Features. Smart machine functions in terms of process stability and machine efficiency, which are included in the standard configuration of all machines
almost without exception.
Peripheral devices from the affiliate Haitian Smart Solutions will also be presented for the first time in Germany. The peripheral devices impress with their simple and seamless integration into the new Haitian control system.
“We were already able to give many customers a sneak preview at our Open House in June. I agree with many of our guests, that this is the biggest technological leap we have made so far. I am even more excited to be able to present our current portfolio to a wide audience at Fakuma.” Niels Herz, Sales Manager Germany at Haitian International Germany regarding Fakuma 2024.
An electric Zhafir Zeres series with medical package, producing 8 cavity syringe cartridges (1.5 ml), is equipped with a laminar flow box, pneumatic quality flap and conveyor belt. Part of the process is the automatic
tegrated into the controller.
The servo-hydraulic world bestseller, the Haitian Mars series, comes with a clamping force of 200 tons and produces frisbee discs from 100% recycled PP. The machine showcases the function HT·Inject, which ensures greater process stability during injection. The entire production cell and peripheral system is fully provided by Haitian.
With its product philosophy “Technology to the Point”, Haitian continues to focus on solutions that are designed to drive efficiency and flexibility.
In the face of increasing competition, growing demand for sustainable solutions and a growing shortage of skilled labor, Haitian’s machines and production cells are designed to simplify operation, increase productivity and reduce energy consumption.
Caldara Plast believes in the second life of plastic: a possibility that today can no longer be considered a second choice but the first choice of environmentally conscious companies.
Large production capacity, speed and availability are the most suitable terms to describe this Lombardy-based production company. Caldara Plast is increasingly convinced that the use of regenerated plastic material must increasingly be the first choice of companies that care about the environment. Caldara guarantees its customers compliance with all legal authorizations for waste collection and storage, as well as with all relevant European and international regulations (RoHS, REACH, etc.). The company is also ISO 9001:2015 and ISO 14001:2015 certified.
Caldara Plast wants to let stakeholders know that plastic is a versatile material, recyclable and reusable countless times in the production process, thus reducing the environmental impact. The world production of plastics in increasingly and the recycling of plastics al-
lows a reduction of up to 90% of CO2 emissions compared to its production. Caldara Plast’s mission is to give a second life to waste, which today can no longer be considered a second choice but the first choice of companies that care about the environment. For an increasingly greener future. Because the future belongs to companies that care about the environment.
It is the choices of companies that underline their green vocation. Caldara Plast customers know that, for the same price, they are choosing a regenerated compound that will help them to be more sustainable too.
Under the guidance of brothers, Massimiliano, Attilio and Alessandro, Caldara Plast is increasingly distinguishing itself on the market as an industrial recycling company
capable of providing a 360-degree service: from recovery of waste material, scraps, offcuts etc. to the supply of regenerated compounds, including the line of “Caldara 2nd Life” certified products. On the recovery side, the company offers suppliers the possibility to give a new life to production waste. On the compound side, the company offers customers regenerated compounds, such as industrial-grade granules and modified raw materials, all produced according to their needs. Caldara Plast is a valuable partner for customers that want to develop new formulations, thanks to the specific skills of the company’s specialised technicians able to meet all their needs.
The thermoplastic granules are intended for the automotive, furniture, household appliance and electrical industries both in Italy (70%) and internationally (30%). The main compounds produced by the company are sinLAC ABS, sinBLEND PC/ABS, sinCARB PC, sinSTYR PS, sinMID PA6 E PA66, sinTRON PPS, sinPOM POM, sinGLASS PMMA, sinKRYL SAN, sinTER PBT, sinPET PET. The great market demand for regenerated products and the desire to make them more and more recognisable, has led Caldara Plast to certify the quality of its materials. Thus, since 2020 the company obtained the “PSV - Plastica Seconda Vita” (Plastic Second Life) and GRS (Global Recycle Standard) mark issued by the IPPR (Institute for the Promotion of Recycled Plastics) for a series of products. These certifications guarantee the customer complete traceability of all components of the finished product and ensure that they contain a minimum percentage of recycled plastic, as well as meet strict environmental and social parameters in the production chain.
Caldara will participate at Fakuma 2024, pavilion B5, booth 5011 to talk about the green side of the technical compound. For more information: info@caldara.it www.caldara.it.
Plastore’s real strength lies, above all, in its strong relationship with its customers and in listening attentively to every request. To fully understand every commercial and technical need, it dialogues with companies to propose the ideal solution or provide viable alternatives aimed at achieving immediate and tangible savings.
Next fall 2024 will be a very significant season for the plastics industry. On one hand, the international scenario remains uncertain and subject to ongoing tensions; on the other hand, the industrial sector hopes to change this negative trend through continuous technological innovations and changes in application sectors, from household to medical, from electronics to automotive.
From October 15 to 19, Fakuma 2024 will open its doors in Friedrichshafen, Germany. This is the most important trade fair of the sector at European level. This event will offer a concrete overview of the current market situation, providing a valuable opportunity for networking and gathering opinions
and perspectives on industry development and new international scenarios. Fakuma will also be an opportunity to know Plastore more closely, an Italian company that is a leader in the trade of plastic granules. With over 38 years of experience, Plastore offers customers the best solutions for purchasing plastic granules.
Plastore (with a warehouse of over five thousand square meters located in Villamarzana, Italy) is a unique and innovative company offering a wide selection of polymers immediately available in stock and ready for delivery. With more than 1,400 different types of granulated materials, Plastore maintains a constantly updated assortment, complete with detailed technical data sheets freely available
on its website www.plastore.it. This represents a real “Plastic Outlet Store” that is always open and accessible, allowing customers to make purchases at the best market prices.
Plastore’s success is not only based on its vast warehouse and variety of products; its true strength lies in the direct and continuous relationship with its customers. The formula is simple: Plastore listens carefully to every request to thoroughly understand each commercial and technical need, engages in direct dialogue with companies to propose the ideal solution, and, if necessary, it provides valid alternatives to achieve immediate and tangible savings in a complex and often confusing market like the one of plastics.
When it comes to “after-sales service,” Plastore refers to build up a relationship of trust and loyalty, always positioning itself as the sole interlocutor. It is a true partner to whom the solution of various “plastic problems” can be entrusted, offering certainty in a historically unstable and complicated time like the present.
Plastore’s staff is always available and responds with professionalism and promptness to every request, leveraging vast technical expertise and efficient logistics. Plastore knows how to put itself in the customers’ shoes, creating the right empathy to always find personalized and effective solutions suited to different needs.
Plastore will be at Fakuma (Hall A5 – Stand 5122) to offer a unique and personalized purchasing experience. Everyone will be welcomed by one of the most experienced agents in the field of plastics: Mr. Plastore, the cartoon character who has been accompanying our advertising communication for years. He perfectly embodies our philosophy of experience, dynamism, trust, and results, and our mission to help customers succeed.
Filtec is a company that stands out for its Italian craftsmanship, demonstrated through in-house production and total quality control of its systems. Yet, the company never stops thinking about the future by playing an active role in the world of the circular economy and environmental sustainability.
Aleading company in the field of filtration and granulation of plastics based in Veneto, in Badia Polesine (RO). With over three decades of experience, Filtec is highly specialized in providing customized and innovative systems, capable of responding to specific management, production and consumption optimization needs of its customers. Founded in 1993 by the Baracco family, Filtec has quickly gained a prominent position in the sector, introducing high-tech solutions in the market, such as the first Water Ring pelletizer and the prototype of the Underwater pelletizer. These products are still part of the company catalogue and have been constantly updated to keep up with the evolution of technologies
and the changing needs of the market. Together with the granulation systems, the products range offers single or double plate screen changers, water filtration and cooling systems, vented vibrating screens, centrifuges.
What makes Filtec unique is its Italian craftsmanship, which manifests itself through internal production and total quality control of its systems. This approach allows the company to guarantee a maximum level of reliability and to offer a complete and always available customer service, both in the presale and post-sale phases. With more than 700 customers worldwide,
400 suppliers and 1,600 global installations, Filtec has become a point of reference in the sector. Thanks also to its cutting-edge tools, it is able to develop customized and innovative solutions, representing a real partner for its customers.
But Filtec is not only a machinery manufacturer: its commitment extends to environmental issues. By offering solutions for the recycling of plastics and participating in the “Are You R” project, Filtec plays an active role in the world of circular economy and environmental sustainability. In detail, “Are You R” aims to raise awareness about plastic recycling among the world population, telling daily stories of reuse and recycling.
From 15th to 19th October 2024 Filtec will exhibit at Fakuma in Friedrichshafen (Stand A6-6405 – Hall A6) and it will bring its virtual showroom, an innovative platform that offers customers and visitors an engaging experience: simply with a monitor and a couple of clicks it allows to explore the products range, discover their characteristics, and understand the potential of Filtec systems. A virtual visit to discover the company’s portfolio, aimed at offering customers a realistic vision of Filtec entire offer, showing the company desire to adopt innovative technologies to support sales.
In order to anticipate market trends and meet the needs of an increasingly aware customer, Friul Filiere has patented FFC: a compound formed from a mixture of thermoplastic material and natural fibers, lightened by cell expansion, to create high-precision, high-quality profiles.
Innovation, sustainability and reliability. These will be the main themes that Friul Filiere will present during the Fakuma, from 15 to 19 October. At stand 6208 in Hall A6, it will be possible to see an upgrade of Friul Filiere extruders, which are already appreciated by the market for their reliability and flexibility. This upgrade is equipped with a brand-new operator panel and state-ofthe-art software that facilitate the man-machine interface. Friul Filiere’s commitment to the environment is shown by developing technologies that reduce the environmental impact of production processes and end products. This allows profiles and tubes to be manufactured using recycled and recyclable materials, thus contributing to the reduction of waste and the promotion of a circular economy. With this in mind, Friul Filiere’s innovative approach not only respects the environment, but is also a strategic choice to anticipate market trends and meet the needs of an increasingly demanding and informed customer.
FFCTM represents a significant innovation in the field of profile production for the furniture and interior design industry. It is a compound patented by Friul Filiere, formed from a blend of thermoplastic material and natural fibres, lightened by cell expansion, to be extruded using state-ofthe-art technologies, special single-screw or counter-rotating twin-screw, to create high-precision, high-quality profiles.
The most significant aspect of this patent is the possibility of using MDF waste from previous processing, instead of natural fibres. Recovering MDF not only helps to reduce environmental impact by minimising waste and CO2 emissions, but also offers significant cost benefits. In fact, turning waste into raw material reduces disposal and production costs, making the process not only sustainable but also very cost-effective. The benefits of FFC are:
• Extrusion speed: Friul Filiere’s plants ensure an extrusion speed of 1.1 m/min
• Moisture resistance: Unlike wood, FFC profiles do not absorb moisture.
• Nailability and screwability: They can be easily worked with nails and screws.
• Versatility: They can be worked with the same tools used for wood.
• Flexibility: They are ideal for applications that require flexibility while maintaining a robust and durable structure.
• Lightness and efficiency: All the benefits of PVC, but lighter, cheaper and definitely more sustainable.
Other sustainability-related highlights that visitors to Friul Filiere will be able to ask more about during Fakuma are:
• Light Thermal Break. This is the third evolutionary step of Friul Filiere’s thermal break technology, an innovative concept that allows extruded profiles to achieve significantly higher levels of thermal insulation, while significantly
The FFC compound represents a significant innovation in the field of profile production for the furniture and interior design industry
lightening their weight (approx. 30%), with obvious benefits in terms of application performance and environmental sustainability. Furthermore, the finished profile is 100% recyclable, as it has no polluting residues. This advanced technology allows a quick ROI due to raw material savings and increased productivity.
• Agricultural Industry. Friul Filiere has introduced innovative solutions to support cultivation. These include plants equipped with multi-layer heads for the production of irrigation pipes, produced with up to 70% recycled material; or even the complete project of co-extruding thermoplastic material bands on greenhouse coverings, which allows to eliminate the use of iron eyelets generally used for fixing them to the ground.
• Automotive Industry. The replacement of EPDM with TPV represents significant progress in both environmental and economic terms. TPV, being totally recyclable, offers a more sustainable solution than EPDM, which is more difficult to recycle after its use. In addition, TPV offers better performance in terms of durability and weather resistance. This shift not only improves the automotive industry’s ecological footprint, but also helps reduce production costs in the long run.
Euroviti knows how to offer its customers extensive support in extrusion and injection processes, not only as a supplier of mechanical parts, but also by improving the efficiency of their industrial processes by creating custom plasticizing unit designs.
Established in 1992 Euroviti is a leading manufacturer of injection and extrusion plasticizing units. Thanks to the avant-garde vision of its founder, Giuseppe Barrale, with a wealth of experience in the world of screws and cylinders, he did not limit himself to creating a simple spare parts factory but wanted to become a true technological partner for his customers.
The uncompromising quality of its products, combined with thirty years of experience, has allowed Euroviti to grow steadily, increasing both its turnover and the number of staff needed to support its expansion not only in the local market, but also in its numerous export markets in Europe, the Middle East and South America. These areas are also growing thanks to the company’s constant participation in the most important international trade fairs in the sector, such as K Show, NPE in Orlando, Plast Milano, PRSE and, most recently Fakuma. Events that allow constant contact with new market realities and customers from every continent. This year Euroviti will be at Fakuma 2024, Hall B3 - Stand 3308.
Among the other market players, this company distinguishes itself by offering extensive support to customers in the extrusion and
injection processes, not merely as a provider of mechanical parts but also by helping in the selection of materials and aiding everyone in need of optimization of their operations. Enhancing the efficiency of their industrial processes even with the creation of entirely cus tomized plasticizing unit designs in a client-focused approach that has fos tered long-lasting relation ships with numerous cus tomers and business partners worldwide.
One of the latest examples of a successful project involved a Japanese injection moulding machine from a leading international packaging company. The issue arose with transparent pieces produced using a sandwich-type mould and an original plasticizing unit equipped with a barrier screw for processing polypropylene (PP) which, due to contractual obligations, was mixed with a 1.5% clarifying additive needed to ensure excellent transparency of a globally recognized sweet box cover. The moulded pieces had whitish streaks and veins, making the product unacceptable and compromising the look of the packaging. The challenge was to remove them.
After a thorough analysis of the original screw design and production cycle time, Euroviti technical team implemented a comprehensive design overhaul. While competitors or the OEM itself were suggesting to entirely replace the plasticizing unit, Euroviti focused
exclusively on redesigning the screw which led to more efficient and cost-effective solution. The modification of the barrier shearing gates, the pitches adjustment, and the addition of a mixing area result in the creation of a customized HPB-mixing design, tailored to address the client’s specific issues. Elimination of product non-compliance due to streaks, securing that the moulded pieces met the required quality standards, and enhancing transparency levels with a visually appealing and flawless product were all achieved. Moreover, this solution, along with proper machine settings, allowed a 30% reduction in feeding time and a 9–11% improvement in total cycle time. This injection moulding project, as well as many others with single screw extruders, confirms that while addressing the immediate challenge, it is possible to solve and improve other elements. On top of that, it proves there is still a lot of work to be done in educating and convincing about how much of a difference a dedicated and correct screw design can make. Even a small single screw, if made correctly, can make a big difference. To stay constantly updated and learn about the successful case histories, visit the website at www.euroviti.com.
The Circular Economy Report confirms that plastic continue to be critical and irreplaceable material for almost every sector of the European economy with significant advances in circularity, but challenges remain.
Plastics Europe today published its biennial “The Circular Economy for Plastics: A European Analysis” report. Its data provides an overview of European plastics production, conversion, consumption, and waste management, and includes an analysis of plastics production from non-fossil sources, and recycling technologies. The 2024 edition of this report is a contribution towards a better understanding of the circular economy for plastics, and its evolution over the years. It provides an overview of European plastics production, conversion into products and components, consumption, waste management. It also addresses the different recycling technologies and plastics production from non-fossil based resources, i.e. bio-based and bio-attributed and carbon captured plastics. The report shows 2022 estimated data. The study’s central finding is that circular plastics now account for 13.5% in new plastic products manufactured in Europe. This means that the European plastics sys-
tem is halfway towards the interim ambition – established in the ‘Plastics Transition’ roadmap – to use 25% of plastics from circular sources in new products by 2030. However, the report’s data also highlights several major challenges that will undermine the Plastics system’s progress towards circularity; including growing rates of incineration with energy recovery (+15% since 2018) of plastics waste needed as circular feedstock/that could have been recycled.
“Our latest ‘Circular Economy for Plastics’ report provides essential insights into the transition of the plastics system”, said Vir-
ginia Janssens, Managing Director of Plastics Europe. “This edition is also broader in scope and contains more in-depth data than ever before. Whilst the data confirms the shift to circularity is firmly established and picking up pace, it is frustrating that we still incinerate so much plastics waste when this potential feedstock is desperately needed by our industry to accelerate the transition. Without urgent action to increase the availability of all circular feedstocks for plastics we cannot maintain the current rate of progress and realise the ambitions of our ‘Plastics Transition’ roadmap and the EU Green Deal”.
The European plastics system is halfway towards the interim to use 25% of plastics from circular sources in new products by 2030
The plastics circular economy is a sustainable model where plastics remain in circulation longer; their use is reduced1, and they are reused and recycled at the end of their life span. It allows to retain the value of plastics waste as a resource, whilst reducing CO2 emissions and preventing plastics from ending up in landfill, being incinerated or polluting the oceans. In total, 26.9% of European plastics waste is now recycled meaning that, for the first time, more plastics waste is recycled than is put into landfill; an important milestone in Europe’s plastics circularity journey. However, to meet the growing demand for plastics manufactured from circular feedstocks, we need to massively upscale the collection and sorting of post-consumer plastics waste, and increase the availability of biomass and captured carbon. The data also highlights that the uptake of circular plastics is not uniform but varies by industry sector. The strongest demand comes from the packaging, building and construction, and agricul ture sectors. However, others, including automotive and electricals and electronics, are falling behind.
The report found that in 2022, circular plastics were
produced from several sources: the largest source (13.2% of all plastics produced) was mechanically recycled, while only 1% came from bio-based feedstock, and 0.1% was chemically recycled.
“The continent-wide roll-out of chemical recycling, as a complementary solution to mechanical recycling, is essential to meet ambitious mandatory recycled content targets for applications and industries that require high-quality plastics”, Virginia Janssens, Managing Director of Plastics Europe. “To incentivise the necessary investments and ramp up the deployment of chemical recycling in Europe we urgently need a green light and clarity from EU policy makers. We need legislative acceptance of chemical recycling and the adoption of a Mass Balance attribution method based on a fuel-use exempt model”.
The report also shows that Europe’s share of global plastics production decreased from 22% (2006) to 14% (2022). If this continues Europe will become increasingly dependent on imports and its ability to invest in circularity and support the tran-
The report shows that Europe’s share of global plastics production decreased from 22% (2006) to 14% (2022)
sitions of the many downstream sectors and value chain partners that rely on plastics, will be undermined.
“The European plastics system is too big, complex, and interconnected for any part of it to successfully deliver a competitive, circular and net zero system alone”, confirm Virginia Janssens, Managing Director of Plastics Europe. “We need to find better ways of listening, talking and deepening our collaboration. To boost this essential collaboration, we call on the European Commission to urgently establish a Clean Transition Dialogue to look at the roadblocks and solutions for creating a competitive circular plastics system in Europe together”.
ALPLA and zerooo have developed a standardised solution for cosmetics and care products. From September, the first brands will be presenting products in 300-millilitre PET bottles.
Zerooo stands for reusable packaging that fosters the circular economy in the cosmetics industry. The system offered by start-up SEA ME GmbH offers brand manufacturers safe, affordable and sustainable PET bottles, in addition to glass bottles, for the first time. Together with ten brand partners and packaging and recycling specialist ALPLA, the company has developed a fully recyclable solution. The reusable PET bottle, with a volume of 300 millilitres, is available in clear, milky white and brown versions. It is suitable for all caps and can also be used as a shatterproof alternative for toiletries in the shower. Further formats are planned. This reusable and fully recyclable plastic packaging is available in three colours and is suitable for all caps. A laser-engraved 2D data matrix code provides information on the contents of each bottle and its circulation.
From September, the first manufacturers in Germany presents cosmetics and care prod-
ucts in PET containers from the zerooo reusable system, with Austria following suit in October. In addition to SEA ME’s own brand, these include sodasan, i+m Naturkosmetik, Speick, Denttabs, 4 people who care and Aveo from Müller. Empties can be returned to the approximately one thousand collection points of zerooo retail partners for a deposit of €0.50.
As a globally active packaging manufacturer and recycling specialist, ALPLA is promoting closed ‘bottle-to-bottle’ cycles with its own plants. The company contributes its expertise as a system supplier and also supports customers with design. The zerooo reusable PET bottle was developed in tandem with the SEA ME GmbH team at ALPLA’s in-house STUDIOa design centre at the company’s headquarters in Hard.
‘With “Design for Recycling”, we are setting the course early on for optimum recycling and the longest possible service life. Every detail counts when it comes to shape, colour and material. The reusable system extends the life cycle of the plastic bottle, saves ma-
terial and reduces its carbon footprint,’ emphasises Alexander Tränkle, Industrial Designer at ALPLA.
‘With its wealth of knowledge, the ALPLA development team provided us with significant support in implementing the brand and reusable packaging requirements”, explains Mirko Waraszik, Director of Supply Chain and co-founder of zerooo at SEA ME GmbH.
“We are proud to have succeeded in integrating the individual serialisation of bottles directly into the production process for the first time. This innovation enables groundbreaking data applications for packaging in the context of reuse”.
Each zerooo reusable PET bottle is unique. A laser-engraved 2D data matrix code – the zerooo ID – provides information about the content and circulation history. “The digital labelling enables transparency and ensures the quality of the bottles. By combining it with the information from the label, it can also be complemented with further product data”, explains Jörg Schwärzler, Senior Technology Manager at ALPLA. The reusable PET bottle is compatible with all automatic return systems. At the end of their life cycle, the bottles and caps are sorted and recycled.
In terms of circular economy, Italy is on the right track and among the leaders in the EU. The country, however, together with small businesses, still has much to do to promote and improve circularity mainly due to its shortage of raw materials.
In Italy, households are not the only source of saving. Almost a fifth of what we produce comes from recycling: the circular material use rate is second only to France. Italy ranks first in terms of circularity of production among the top five EU economies: resource productivity is worth on average 3.7 euro per kilo, compared to the EU average of 2.5 euro per kilo. In short, the italian economic and production system loves circularity, and so do small and medium-sized enterprises: 65% said they are implementing circular economy practices, more than double compared to 2021.
The success of the Green Deal depends on circularity. And Italy has always played a leading role in Europe when it comes to circular economy. The data from the sixth report on the circular economy in Italy by the Circular Economy Network (CEN) and ENEA, were presented during the annual conference on
the circular economy, which took place at the Roman Aquarium.
For the first time, this edition of the Report adopted European Commission indicators to measure the circularity performances of the five largest economies of the European Union (Italy, France, Germany, Spain and Poland): production and consumption, waste, secondary raw materials, competitiveness and innovation, ecological sustainability and resilience. Even with these “new” indicators, Italy’s ranked first (45 points) in terms of circular economy, followed by Germany (38), France (30) Poland and Spain (26). Italy’s leadership is mainly due to waste management. We rank first for the waste recycling rate. Specifically, in 2021 we had a packaging waste recycling rate of 71.7%, 8% higher than the EU27 average (64%). In Italy municipal waste recycling grew by 3.4% between 2017 and 2022, reaching 49.2%. The EU average is
48.6%, Germany was the top recycler with 69.1%. We also lead the way in WEEE recycling: in 2021 it was 87.1% (minus two percentage points compared to 2017), with an EU average of 81.3%.
In 2022, resource productivity in Italy generated, for every kilo of resources consumed, 3.7 euro of GDP, +2.7% compared to 2018. The EU average in 2022 was 2.5 euro/kg. The figure for the other four main European countries is also lower than Italy’s.
As regards the circular material use rate, i.e. the ratio between the circular use of materials and the overall consumption of materials, Italy confirmed its position in 2022 with 18, 7%. Investments in some circular economy activi-
Italy’s positive result on circularity indices comes mainly from waste management where the country is first in Europe
ties in the EU27 amounted to 121.6 billion euro, 0.8% of the GDP, in 2021. Italy, with 12.4 billion euro (0.7% of GDP), ranked third, behind Germany and France.
Plus, a circular economy can have a positive impact on employment. In 2021, in the EU27, there were 4.3 million people employed in some circular economy activities, 2.1% of the total; in Italy 613,000, i.e. 2.4%, +4% compared to 2017; we ranked in second place after Germany, which employed 785,000 workers in these sectors (1.7% of the total).
The added value of the entire EU relating to some circular economy activities in 2021 was 299.5 billion euro, 2.1% of the total economy; in Italy it was 43.6 billion euro, 2.5% of the total (it was 2.1% in 2017). It also increased in Spain and Germany, while it decreased in France and Poland.
So, was everything okay? Not exactly. For instance, the consumption of materials in Italy in 2022 was 12.8 tonnes/inhabitant, lower than the European average (14.9 t/inhabitant) but growing (+8.5%) compared to the 11.8 t/inhabitant in 2018. Again in 2022, Italy’s dependence on imports of materials (46.8%) was more than double the European average (22.4%), although decreasing (-3.8%) compared to 2018.
Finally, as regards patents relating to waste management and recycling, in 2020, 0.46 were filed for every million inhabitants, i.e. a total of 206 in the European Union. In Italy only 21 patents (0.36 per million inhabitants): -25% compared to 2016. Taken together, the circularity trend indicators, based on the dynamics of the last five years, indicate a certain
difficulty for Italy in maintaining its leading position.
“A circular economy is key to accelerate the climate transition and increase business competitiveness”, said Edo Ronchi, president of the Circular Economy Network. “Even more so for a country poor in raw materials and above all, in the current context, characterized by low growth and the stringent constraints of repaying public debt. Italy can and must do more to promote and improve the circularity of its economy, with measures upstream of products to combat waste and consumerism and increase resource use and efficiency in production; promote prolonged use, reuse, repair and shared use of products; increase the quantity and quality of recycling and the use of secondary raw materials”.
Furthermore, 10% of companies intend to embrace circular economy strategies in the near future. The interventions carried out most often concern the use of recycled materials (68.2%), the reduction of packaging (64%), interventions to enhance product durability and reparability (53.2%). 70.4% of companies believe that moving towards a more circular economy could increase environmental sustainability and efficiency (35.6%), reduce production costs (61%) and boost innovation (34.2%). For 61% of the companies the benefits of circular economy measures include cost reduction. The survey confirms that small businesses can play a leading role in the transition towards a circular economy. But public policies need to be more oriented towards circular choices.
An important focus this year is upon small and medium-sized enterprises, the backbone of the Italian production system. With a survey carried out between December 2023 and January 2024 in collaboration with the CNA, presented at the CEN Conference, 800 small entrepreneurs were asked (49% in services, the remaining half in industry, of which 35,5% in manufacturing and 14.1% in construction) their views and what actions do they take concerning green policies. 65% of the respondents said they implement circular economy actions: more than twice compared to 2021.
In 2021, Italy had a packaging waste recycling rate of 71.7%, 8% higher than the EU27 average
In 2023 the European Commission identified 34 “critical raw materials” crucial to Italian economy. 17 were classified as strategic: copper is one of these. And it is estimated that its demand could double by 2050. The problem is that Europe has only 3% of global reserves, while the greatest concentration is found in Chile (31%), Peru (11%), Democratic Republic of Congo (9%). Hence the use of “secondary copper”: copper
can be recycled infinitely and is already recycled in significant quantities which need to be further increased. The same goes for other raw materials “rare earths”, some of which, used in permanent magnets, are also strategic for renewables, electric mobility and electronics.
Globally, approximately 85% of light rare earths and all heavy rare earths used come from China. Also in this case, the demand for rare earths could increase significantly, even tenfold by 2050. The world reserves of rare earths are concentrated, once again, in China (44 Mt), Vietnam (22 Mt), Brazil (21 Mt ) and Russia (12 Mt). The main supplier - around 80% - of refined materials to Europe? Always China. The same applies to copper: it is possible to recover rare earths from the recycling of end-of-life materials, a less polluting practice than the primary one which also allows access to sources with higher concentrations of rare earths than those found in nature. It is not a trivial issue: the economic activities that use rare earths are responsible for 11.4% of the turnover of the entire Italian manufacturing industry. Therefore, becoming independent from imports through the circular economy is more than a hope, a necessity.
“The indicators on the circularity of our country confirm Italy’s excellent performance on various aspects, including the recycling percentages and circular use rate of materials. However, the significant increase in resource consumption highlights the need for a paradigm shift in the economic model and lifestyles, to focus on the great potential of the circular economy in terms of more efficient use and management of resources in production chains, in cities and in the territories”, said Claudia Brunori, Head of the ENEA Department of Sustainability, Circularity and Adaptation to Climate Change of Production and Territorial Systems. “To have successful and long-lasting results it is necessary to revolutionize the way in which products are designed and manufactured, integrating circularity criteria into production processes”.
Vecoplan initiates a strategic partnership with Pla.to to offer its customers treatment solutions from a single source.
Vecoplan supports processors in implementing the circular economy. Europe wants to be climate-neutral by 2050. The circular economy for plastics makes an important contribution. The core element of the EU directive on packaging and packaging waste is the recycling rate. By 2025, member states must recycle at least 65% of their packaging waste. By 2030, the quota will increase to 70 percent. Chemical recycling is an important approach in the circular economy. It enables the reuse of plastic waste that is too complex to process using mechanical recycling methods but too valuable to dispose of. In chemical recycling, plastics are broken down into their chemical components and used as raw materials for the production of new plastics. This helps to reduce the consumption of fossil resources and prevent environmental pollution from plastic waste. At IFAT 2024, Vecoplan informed experts about the measures it intends to take to intensify its expertise in this area in the long term and entered into a close strategic partnership with Pla.to Technology.
“Vecoplan has more than 50 years of experience in the processing of recyclable materialsthe basis for the production of recyclates”, explains Martina Schmidt, Head of the Recycling - Waste division at Vecoplan. “We are definitely one of the pioneers in this field and can demonstrate a high level of innovation”. The chemical processing of plastics is also becoming increasingly important for the processing technology expert. Two years ago, Vecoplan laid the foundations for this with the introduction of a pioneering cleaning process and the commissioning of the “Cleanikum” - a demonstration and test facility near the headquarters in the Westerwald. But now the company is going one important step further.
Pla.to Technology, based in Görlitz, offers durable and wear-resistant cleaning processes for economical used plastic recy-
The efficient shredding and cleaning of used plastics is an important process step in chemical recycling
cling and already has 20 years of experience with established systems. This is the best basis for Vecoplan to enter into a strategic partnership in the field of cleaning. With the combination of Vecoplan’s high level of expertise in recyclable material processing and Pla.to’s experience in the various cleaning processes, customers will in future receive processing solutions from a single source. Over the past few years, the two partners have perfectly coordinated their proven technologies in various tests.
Martina Schmidt, Head of Business unit Recycling - Waste at Vecoplan
“We have had joint customers since 2007 and our systems complement each other perfectly to ensure a high level of customer satisfaction”, says Heinz Schnettler, General Manager of Pla. to. The two companies follow the same values and principles, and mutual trust plays a central role for both. “Only if we maintain an open and constructive working relationship can we react flexibly and creatively to the constantly changing requirements of our customers,” Martina Schmidt is certain.
Patents obtained by AIM3D protect both a topology of 3D printing extruders in the high-temperature and high-flow range, as well as a detailed technical solution in the field of pellet processing.
AIM3D, an expert of 3D printing with pellets using a 3D extrusion printer, has now been granted four patents in the USA and Europe. These grants of fundamental patents in the USA and Europe provide AIM3D with a far-reaching protection of technology and secure AIM3D’s pioneering role in the field of compact decentralized pellet extruders and material extrusion printing with high-temperature materials. The US patents also cover filament extruders (FDM printers) for high-temperature applications and high-flow hot ends. AIM3D emphasizes that it is generally open to licensing this technology. Since 2017, the start-up AIM3D, a spin-off from the University of Rostock (Germany), has been consistently focusing on 3D pellet printers as opposed to FDM (fused deposition modeling) printers, which process filaments instead of pellets. Significantly lower material acquisition costs for pellets and the inline recycling of reclaimed material form the basis for the high cost-effectiveness of this AM production strategy with 3D pellet printers. The development work on 3D pellet printing technology was reflected in four patent applications between 2016 and 2018, which have
now been granted in 2023. The patents protect both the topology of the 3D printing extruder as a whole and detailed technical solutions in the area of pellet processing.
The thermal separation of the housing and the division into an actively cooled and a heated area of AIM3D’s CEM technology lead to a short melting zone and uniform extrusion at high build rates (based on nozzle sizes of 0.3 mm to 0.6 mm). AIM3D has positioned its technology in this market segment and thus differs fundamentally from large-capacity pellet printers that rely on nozzle diameters larger than 1 mm. This becomes particularly evident in the processing of ULTEM 9085, a material that is of great importance in the aerospace sector, which can be processed by AIM3D’s patented pellet extruders in a material-friendly and reliable manner with high build rates and very good surface quality. The design of the extruder guarantees a short melting zone, which prevents degradation of the material, which would inevitably lead to process fluctuations and weak points in the components. In combination with the active filling of the extrud-
CEM extruder nozzle (nozzle sizes from 0.3 mm to 0.6 mm) for ExAM 255 and ExAM 510 from AIM3D
er’s feed area, this ensures a uniform static and dynamic pressure in the extruder, which in turn leads to uniform extrusion widths and therefore a high component quality. Beyond the processing of metal-filled composites (as mentioned by name in the patents), the system-specific patent claims also extend to the processing of thermoplastic polymers, as long as the system-specific elements are found in the systems and the processing of metal-filled composites (for example, MIM material) cannot be technically excluded. By using additive manufacturing processes, it
ULTEM component ventilation shaft from Alstom S.A. in cooperation with the company Replique
was possible to compare different designs and geometries and analyze the influence on the homogeneity of the extrusion technology (CEM technology) and on the process stability. The findings were incorporated into the basic extruder design of the CEM extruder via the nozzle and resulted in the application of the aforementioned patents. This was reflected in AIM3D’s industrial 3D printers ExAM 255 and ExAM 510.
The still “young” CEM printers have positioned themselves on the market alongside the widespread FDM printers. The 3D pellet printers ExAM 255 and ExAM 510 from AIM3D enable the use of standard pellets with or without fillers to generate robust 3D components. This ensures significantly greater cost-effectiveness for the users. With the Voxelfill strategy, AIM3D has now also overcome the inhomogeneous strengths in 3D printing. The CEM process enables the use of various materials: hybrid mul-
ti-material solutions with different Voxelfill materials and different materials for the contour or the structure of the inner walls are possible. This way, the material properties can be “customised”. Component weight, damping properties, elasticity or changes to the centre of gravity can be defined in 3D to suit the application. By selectively filling only certain volume chambers (selective densities), the component properties can be influenced in a targeted manner based on FE simulations. With Voxelfill it is possible to only fill the areas of a component that are absolutely necessary for the flow of forces. As a result, from the outside, these components look like conventional parts and can further benefit from applying conventional finishing processes. At the same time, however, the 3D printing process is carried out with reduced material and weight, right up to realising lightweight components. Especially when deploying fibre-reinforced materials, the use of Voxelfill offers an additional option for specifically aligning the fibres in the component to enhance the mechanical properties. In the flat
plane, the CEM process already offers very good options for controlling the orientation of the fibres. With the Voxelfill strategy, this affects the contour and the inner walls of the component. By injecting the material into the volume chambers (filling the voxels), the 3D component also receives fibres that are aligned along the Z axis, thereby further improving the mechanical properties.
AIM3D’s ExAM 510 system is predestined for use in industrial production. Reproducibility, that is, the repeatability of the process, is crucial for the construction of a 3D component. For a user, this is a key point to ensure consistent component quality, especially in the series production of small and medium-sized batches. Reproducibility is achieved primarily through the patented pellet extruder technology, which ensures gentle processing of the material and minimizes degradation of the polymers in the extruder.
Together, Coperion and Herbold Meckesheim offer solutions for mechanical recycling of post-industrial and post-consumer waste, chemical recycling, solvent-based recycling, and deodorization, tailored to the type of plastic being recycled.
Coperion and Herbold Meckesheim offer operators broad expertise in technology and process solutions for plastics recycling. Since their merger, both companies have continued to develop and optimally attune their technologies so that entire systems excel in operation with high efficiency.
For the STS 75, Coperion has raised the specific torque of the STS twin screw extruder from 11.3 Nm/cm³ to 13.6 Nm/cm³. The compounder thus achieves improved product quality and at the same time up to 20% higher
throughput in every application. Critical to this level of performance, along with process-technical modifications, is optimization of the drive’s key components. The new STS 75 Mc PLUS extruder is equipped with a high-power motor and a gearbox designed specifically for the high torque. Proven high-performance materials for the screw shafts ensure full torque transmission from the gearbox to the screw elements. The higher fill level in the process section is crucial to the improved compound quality that the STS 75 Mc PLUS achieves. It reduces both shear stress and melt temperature and improves mixing behavior. The result is an extremely gentle product handling at high throughputs. The process section of the STS
75 Mc PLUS is equipped with heating cartridges that generate heat very energy-efficiently exactly where it is needed.
STS extruders combine the advantages of substantially standardized and thus more cost-effective machine construction incorporating Coperion’s technical expertise. In the continued development of the STS 75 Mc
The new Coperion STS 75 Mc PLUS twin screw extruder achieves up to 20% greater throughput with improved product quality, at an increased specific torque of 13.6 Nm/cm³
Copyright: Coperion K-Tron, Switzerland
PLUS, Coperion has profited from the comprehensive experience gleaned from its highend ZSK Mc extruders. The new STS 75 Mc PLUS’s throughput increase of up to 20% makes it a particularly economical solution. Material costs per kilo drop and return on investment is reached much more quickly. Coperion retained the proven Do:Di = 1.55 ratio of outer to inner screw diameter unchanged, thus ensuring secure scale-up to other STS model sizes.
Coperion and Herbold Meckesheim realize plants for a wide variety of plastics recycling applications, excelling in their reliability and the high product quality they achieve. From mechanical processing – shredding, washing, separating, drying and agglomerating of plastics – to bulk material handling as well as feeding and extrusion all the way to compounding and pelletizing, such plants cover the entire plastics recycling process chain.
Coperion is an expert in all feeding tasks with its high-accuracy Coperion K-Tron K2-MLD5-T35 Quick Change feeder equipped with ActiFlow™ smart bulk solid activator and EPC (Electronic Pressure Compensation). The feeder is equipped with a 2415 vacuum receiver for refill. The T35/S60 quick change feeder (QC) on display is designed for applications requiring quick changeover of materials and convenience of fast cleaning. The QC feeder allows for fast removal of the entire feeding module with screws in place for replacement with a second unit. Twin and single screw feeding modules are available.
The ActiFlow™ smart bulk solid activator offers an innovative method to reliably prevent bridging and rat-holing of cohesive bulk materials in stainless steel hoppers without internal hopper agitation. The smart flow aid applies gentle vibrations to the hopper wall, hereby carefully activating the contained material with the optimal amplitude and frequency, automatically adjusted by the controller based on bulk material flow. It is designed specifically to work with Coperion K-Tron’s line of gravimet-
ric loss-in-weight feeders.
The 2400 Series vacuum receivers provide a high-capacity sequencing system primarily used where larger conveying rates or long distances are required, in applications with one or multiple destinations. They are designed to high quality standards for pneumatically conveying powder, pellets and granular materials for most industries. Conveying rates range from 327 to 6,804 kg/h (720 to 15,000 lb/h). The preconfigured size S ProRate PLUS single screw feeder, equipped with a 2410 receiver for refill is very robust and stands out for its good price-to-performance ratio. The ProRate PLUS line was designed as an especially economical solution for reliably feeding free-flowing bulk materials. Coperion has expanded the ProRate PLUS feeder line with a PLUS-MT twin screw feeder especially for feeding powders.
The ProRate PLUS feeder line with refill solutions are simple, robust and reliable
To meet the demands of the current market, Reifenhäuser Group shows blown and flat film technologies for the production of sustainable packaging.
The Reifenhäuser Group, the machine manufacturers specializing in blown and flat films, and its business units Reifenhäuser Blown Film, Reifenhäuser Cast Sheet Coating and Kdesign present their latest production technologies, such as EVO Aqua Cool water shock cooling, Kdesign’s market-leading KARAT cooling rings and the extensive range of applications for MDO cast films. All these solutions were exhibit by the Group at Chinaplas 2024.
Reifenhäuser EVO Ultra Stretch MDO unit enables blown film manufacturers to produce fully recyclable all-PE mono films - e.g. for barrier food pouches. Stretching gives the PE film sufficient stability to replace the usual PET film in the material composite. The necessary barrier effect is achieved with an EVOH content of less than five percent and therefore meets all requirements for complete recyclability. Ultra Stretch increases the barrier effect of the EVOH and reduces the necessary EVOH content while maintaining the same barrier effect. The all-PE mono film can be further processed and converted without any problems. Thanks to the patented position of
the stretching unit directly in the haul-off of the blown film line, the film is also stretched at the ideal time and with the first heat, which makes the process particularly efficient and stable.
Another highlight is Reifenhäuser EVO Aqua Cool, a blown film line that achieves particularly robust and highly transparent films thanks to water shock cooling - for example for medium to high-barrier food packaging or high-performance special applications such as medical infusion bags. Due to their formability, Aqua Cool films are also ideal for thermoforming applications, vacuum skin lidding films, or thanks to their optical properties for vacuum pouch packaging or lidding films. With water cooling, the extrusion directionfollowing the gravity of the water - runs from
Thanks to water shock cooling, Reifenhäuser EVO Aqua Cool enables particularly robust and at the same time highly transparent blown films
top to bottom from the die head. The bubble is first inflated to the required size and then passes through the EVO Ultra Quench water cooling and vacuum calibration chamber, which is unique on the market. Here, as much heat as possible is extracted through contact with water. The vacuum in the cooling chamber provides the necessary stability and ensures that the film tube leaves the cooling chamber almost dry.
Reifenhäuser cast lines can be used flexibly, e.g. to produce mono PP barrier film
Kdesign is part of the Reifenhäuser Group and offers market-leading technologies in the areas of cooling, measurement and calibration. Among other things, the KARAT cooling ring, which is known for highest performance, lowest film tolerances and easy handling, will be presented at the booth. Kdesign customers benefit from over 20 years of experience in retrofitting existing blown film lines and equipping new OEM lines. With an output capacity that is up to 50 percent higher than mid-range products and 25 percent higher than high-end competitors, the KARAT cooling ring enables a significant increase in productivity, while at the same time maintaining excellent profile tolerances and top film quality.
KARAT cooling rings from Kdesign are known for their high performance, minimal film tolerances and easy handling
Reifenhäuser Cast Sheet Coating has a range of applications for its MDO cast films. CPP/ CPE cast films are the standard for packaging films in the food and industrial sectors. They offer an optimal solution in terms of transparency (optics), printability, easy-tear performance and sealing. Thanks to their MDO (Machine Direction Orientation) stretching unit, Reifenhäuser cast lines improve the
properties of the film, for example to produce recyclable mono PP films with barrier functions for food or medical packaging. The barrier function is achieved by adding EVOH. The barrier effect is enhanced by the stretching process, allowing the proportion to be reduced to below the 5 percent mark relevant for recyclability. The mono-PP barrier film produced in this way can, for example, replace an aluminum barrier film in the packaging (which is currently still common on the market and is barely to recycle). The stretching unit also reduces the overall material consumption of the film. Other cast applications that are in great demand in China are sticky and nonsticky PP and PE protective films to protect products from damage during transportation. Reifenhäuser Cast Sheet Coating’s protection
Reifenhäuser EVO Ultra Stretch enables the production of monomaterial composites (all-PE film) for fully recyclable flexible packaging
The PAM automation option simplifies the operation of the system. Waste and energy consumption are significantly reduced and product changeovers are completed in the shortest possible time
film lines achieve both to perfection. The systems are very flexible and can also be quickly adapted to other applications.
In combination with PAM (precise, autonomous, mechatronic) - Reifenhäuser’s automation option for flat film lines - film manufacturers can take their production to a whole new level. PAM automatically calibrates coextrusion adapters and dies via high-precision actuators for optimum convenience, quality and productivity. The high degree of automation makes the machine operator’s work considerably easier, thus increasing line productivity and film quality. In addition, energy consumption is 99% lower compared to a thermal expansion bolt system, as the actuators only need to be supplied with power during the adjustment process and not permanently. The use of PAM also significantly reduces consumption of raw materials, as there is hardly any production waste due to time-consuming system start-up processes. Once recipes have been set, they can be saved and called up immediately at the touch of a button - even by inexperienced system operators.
The 22nd edition of the Automotive Awards highlighted the commitment of companies towards sustainable mobility. In this occasion Leonhard Kurz presented the front panel made with translucent polypropylene.
On June 2024, the 22nd Automotive Award Night took place, where all winners and nominees of the SPE Automotive Award 2024 were honored. The competition held everyone and a half years since 1992, is highly valued and supported by many companies in the plastics industry due to the high quality of the submissions and the objective evalua-
tion criteria. This year, the expert jury assessed a total of 43 components that showed a clear trend towards responsible design. With sustainable materials and technologies, the submitted innovations demonstrate that companies like Leonhard Kurz are actively working to make the vehicles of tomorrow more environmentally friendly in both production and operation. The
Fürth-based specialist for high-quality surface finishes was honored in two categories for its pioneering front and rear components.
With its innovative front panel, Kurz took fourth place in the ‘Enabler Technology’ category, subcategory ‘Materials & Technologies.’ The front panel, finished with Decopur®, is an outstanding example of bundled competence. The process technology and design come from Kurz, the material (translucent polypropylene) from raw material manufactur-
The front panel, finished with Decopur, is an example of bundled competence: the process technology and design come from Kurz, the material from SABIC, the tools from Kurz subsidiary Schöfer, and the machine from Engel Austria
er SABIC, the tools from Kurz subsidiary Schöfer, and the machine from Engel Austria. With the help of Decopur front panels with intricate geometries can be formed in the same machine clamping unit, decorated at the same time, and fully flooded with polyurethane in the next step. In the process, proven Kurz decoration technologies such as In-Mold Decoration (IMD), hot stamping, Print Mold Design (PMD) or insert molding can be applied with their usual design flexibility and quality and combined with a high-gloss, crystalline and durable finish. This results in smooth, aerodynamic, and hazard-proof surfaces with impressive depth effects and optional backlighting - perfect for automotive applications, as successfully demonstrated by the award-winning Integrated Front Panel at the SPE Automotive Award 2024. This component is characterized by its innovative, only 0.3 mm thick PUR coating. It is weather-resistant, durable, and self-repairing, making it ideal for outdoor use.
Most recently, Kurz has set itself the goal of further developing Decopur and making the technology behind it more efficient and flexi-
ble. On the one hand, the range of possible substrates has been increased, and on the other hand, Kurz has succeeded in significantly reducing material consumption, which also has an impact on production costs. The advanced process reduces energy consumption by combining several production steps into one, thus reducing the carbon footprint. “Decopur is a production-ready solution for the mobility of tomorrow and the next step towards even more efficient and scalable technologies for automotive manufacturing”, explains Martin Hahn, Head of Application, Technology & Innovation of the Business Area Plastic Decoration at Kurz.
tions only become visible upon activation. Additionally, the surface design allows for radar and 5G-enabled metallization, which supports car-to-X communication and paves the way for autonomous driving.
In addition to its trend-oriented design, the Kurz concept also impresses with its innovative and production-ready one-shot production process. This enables fast and cost-efficient production including finishing in just 60 to 70 seconds. Thanks to In-Mold Electronics (IME), it is also possible to integrate ultra-thin touch sensors in the same work step. In the manufacturing process, a 2K material mix of two different types of plastic - opaque and transparent, with targeted
In addition to the front panel concept, a Rear End Cover component from Kurz received the Nomination Award in the ‘Enabler Technology’ category, subcategory ‘Part & Component Design.’ This exterior concept for the rear end impresses with its revolutionary design. The futuristic design integrates fascinating 3D light effects with targeted light shielding, color gradients, and day/night designs. What’s more, the smooth, seamless surface and the sensor foils attached to the back enable convenient touch operation. Thanks to the Shy Tech design, the smart touch func-
light shielding - is used. Nevertheless, the component can be recycled and reused as a post-industrial compound. It is also possible to use recycled materials in production.
The Kurz subsidiaries Schöfer, Burg Design, and PolyIC, which were involved in the project, played a significant role in the development and component production of the advanced rear application. “Our Rear End Cover impresses with its visionary design, intelligent functions, and a cost-efficient and resource-saving multi-component layer structure”, says Martin Hahn. The honorable award for the component once again underscores KURZ’s innovative strength and pioneering design”.
Mixed plastic waste, raw material for chemical recycling
(photo: GreenDot)
Evertis launches Evercare™ brand, set to be a leading provider of specialty and innovative medical-grade films designed to provide superior performance and support regulatory compliance to the healthcare market. Evercare is built on over 65 years of trusted technical Evertis experience in developing PET and PETG films for regulated applications that meet sustainability credentials, and now compliant in meeting the rigorous needs of the healthcare industry.
Evercare sits in a vertically integrated Group that delivers a unique value proposition to healthcare customers in terms of innovation, sustainability and supply chain security. As film converters for packaging, Evertis is integrated with Selenis, a premium supplier of innovative copolyesters resins with solutions specifically developed, and certified for the medical value chain to further support patient safety. As a Group it fully understands and plays its part in circularity
whilst reducing the carbon footprint of its products.
Evercare PET and PETG drop-in solutions offer performance and sustainability advantages when compared to other materials. Their films facilitate the thermoforming process, provide improved mechanical and optical properties, and have a better resistance to sterilization. Manufactured in strict compliance with GMP standards and support regulatory compliance
needs, Evercare films are offered with declarations such as ISO10993, USP661.1, ISO11607, as well as change notification.
Similar to other industries, the healthcare packaging industry faces the challenges of improving sustainability. This is why the Evercare product range not only offers plug & play recyclable PET based solutions, but also two other sustainable options: bio-based and chemically recycled materials with up to 50% post-consumer recycled (PCR) content. All of these options take advantage of vertical integration with Selenis, meeting the same quality and regulatory standards and representing a great opportunity to lower carbon footprint.
For the last six months, the GreenDot Group and Shell Chemicals Europe B.V., a subsidiary of Shell, have been exploring ways to collaborate to try to deliver additional business outcomes across circular chemicals and polymers for Europe.
These discussions have now resulted in GreenDot supplying pyrolysis oil to
Shell Chemicals Europe B.V. since March this year. GreenDot is leveraging its 30 years of experience running an Extended Producer Responsibility (EPR) scheme in Germany to access plastics waste feedstock from households to produce pyrolysis oils.
Shell Chemicals Europe B.V. will use pyrolysis oil in their Market Development Upgrader unit (MDU), which is currently under construction at the Shell Chemicals Park in Moerdijk, Netherlands. The MDU is expected to start up later this year.
“We are happy to have supplied Pyrolysis Oil to Shell Chemicals Europe B.V. which will help to upgrade these pyrolysis oils and further develop the needed capacities in Europe for circular polymers”, said Mark Vester GreenDot Advanced Recycling Managing Director. “Only a few years are left for the first
recycled content targets for polyolefins packaging that must be met. Collaboration is therefore crucial for many industry partners to pull together in the same direction. With these volumes supplied and Shell Chemicals Europe B.V. covering the upgrade of these pyrolysis oils, GreenDot has taken another critical step forward in fitting together all the pieces of the jigsaw, that ultimately enable circular polymers to be delivered at scale”.
Shell Chemicals Europe B.V. will upgrade the pyrolysis oil to remove impurities and use the new cleaner feedstock to produce circular chemicals that can be further processed into circular polymers for use in plastics. These circular polymers can be used to make contact sensitive plastic packaging, which is designed for various contexts such as animal nutrition, food contact, medical devices, and cosmetic products.
Inaugurated a sorting facility for lightweight packaging designed for a circular economy
After less than a year of construction and a successful trial run lasting several months, the time has finally come: TriPlast, Europe’s most modern and Austria’s largest sorting plant for lightweight packaging, was officially opened by its owners ARA, Bernegger and Der Grüne Punkt together with Climate Protection Minister Leonore Gewessler and Governor Thomas Stelzer. The circular economy project in Ennshafen has an annual capacity of 100,000 tons and will create more than 60 new green jobs thanks to the investment of EUR 65 million.
For Upper Austria’s Governor Thomas Stelzer, the project embodies a win-win situation: “TriPlast benefits not only the environment, but also Upper Austria as a place to work and do business. TriPlast opens up great market opportunities for the industrial location of Ennshafen and
strengthens our position as a European innovation pioneer in the field of sustainable industry”.
TriPlast has a sorting capacity of 100,000 tons of plastic and metal packaging per year. This means that 50% of all Austrian lightweight packaging can be sorted. Packaging is processed in such a way that it can then be turned into recyclate and used to manufacture new packaging or other products. More than 20 different raw materials can be turned back into products such as shampoo bottles, canisters, films or components for the automotive and electrical industries. “With our strategic partnership and the cross-border joint venture, we are preparing Austria and the EU for the recycling quotas from 2025. TriPlast can process an incredible 20 tons per hour and is three times the
size of existing plants in Austria. We want to reduce Austria’s dependence on raw materials and provide the industry with high-quality raw materials”, emphasized ARA CEO Harald Hauke.
“The scarcity of resources in Europe requires a strategic reorientation and determined sustainable action”, said Laurent Auguste, CEO of Der Grüne Punkt. “This includes cooperation and investment in the circular economy of the future – such as the pioneering merger of TriPlast”.
DOMO Chemicals, a global expert in engineered technical materials, proudly inaugurates its newest plant in Haiyan, Jiaxing, Zhejiang, China. This significant milestone reinforces DOMO’s determination to meet rising demand in the Chinese market for its Technyl polyamide-based intelligent solutions.
The 14 millions of euros investment represents a potential doubling of DOMO’s commitment to the Chinese market, with
the new plant capable of increasing the current capacity of 25,000 tons of Technyl polyamides to 35,000 tons and eventually 50,000 tons in the long term. Covering an area of 40,000 square meters, the state-of-the-art facility underscores DOMO’s unwavering commitment to providing high quality products and services to its customers in key sectors such as automotive, electronics, energy, industrial and consumer goods.
“Our steadfast commitment to staying close to customers, both geographically and through innovative products, is at the heart of Domo’s success”, said Yves Bonte, CEO of Domo Chemicals. “We have strong and growing partnerships in crucial sectors like e-mobility and green energy in Chinese markets”.
Since 2016, Domo Chemicals has expe-
rienced robust growth in China, marked by a series of capacity expansions at its Jiaxing facility. With a 20% increase in annual sales, the latest expansion efforts have resulted in the groundbreaking of the new plant in Haiyan.
“We have built strong relationships with local and global customers in China”, confirms Denny Meng, Operations Manager. “This initiative is in line with DOMO’s commitment to innovation and customer focus as we seek to establish an Asia-Pacific application development center to strengthen our presence in new and emerging Asian industries and markets”.
DOMO Chemicals also continues to address some of the biggest trends shaping our world, such as urbanization, modern mobility, lifestyle and miniaturization. By using polyamide-based components instead of metal alternatives, weight can be reduced and efficiency increased, ensuring that electric vehicles consume less energy and therefore run longer.
MANAGING DIRECTOR: Simone Ghioldi
EDITORIAL STAFF: Alessandro Bignami (a.bignami@interprogettied.com), Eva De Vecchis (e.devecchis@interprogettied.com)
GRAPHIC LAYOUT: Studio Grafico Page Vincenzo De Rosa - www.studiograficopage.it
INTERPROGETTI EDITORI S.R.L. via Roggia Borromea, 16 - 22060 Carugo (CO) Tel.: +39 031 3665163 vendite@interprogettied.com - www.interprogettied.com
SALES DIRECTOR: Marika Poltresi SALES: Simone Ghioldi (vendite@interprogettied.com) ADMINISTRATION: amministrazione@interprogettied.com
© Copyright Interprogetti Editori Srl
The columns and news are realised by the editorial team. All rights reserved – All reproduction, even partial, of published material without the publisher’s consent is strictly prohibited.
SUBSCRIPTION RATES:
Italy: ordinary mail delivery EUR 45.00, COD delivery EUR 48.00
International: ordinary mail delivery EUR 60.00, express delivery within Europe EUR 70.00
Express delivery to Africa, America, Asia: EUR 85.00
Express delivery to Oceania: EUR 100.00
Single copy: EUR 10.00
The VAT on subscription prices as well as on the price of single copies is paid by the publisher pursuant to article 74, sub-section 1, point C of the Italian DPR n. 633 of 26th Oct 1972 and subsequent amendments and additions. It is therefore not possible to issue invoices.
Registered at the Court of Milan on 3th June 2010 no. 315
Managing Director: Simone Ghioldi
Print concluded on 27/09/2024 at Litogi, Milano
Information to be given to the data subject - art. 13, legislative decree 30th June 2003, no. 196. Personal data are processed, with or without the help of electronic means, by Interprogetti Editori S.r.l. - Via Maggiolino, 34F - 23849 Rogeno (LC) Italy, to send you the magazine requested and for the operations connected. The processing of data will be carried out by the persons who have been committed by the controller the task of performing the processing operations connected with recording, modification, processing of personal data and printing, fulfilment and delivery of magazines, commercial and fiscal issues, accounting and call center activity. With reference to art. 7, Italian legislative decree 196/2003, you have the right to access to your data, modify, update or cancel data or to object to their processing for direct marketing purposes, by writing to the controller, and ask for the list of data processors.
Publisher’s information to public – art. 13, legislative decree 30th June 2003, no. 196. With reference to Italian Personal Data Protection Code and art. 2, point 2 of Code of Conduct for the processing of personal data in the exercise of journalistic activities, Interprogetti Editori S.r.l. informs that the place where personal data, images and photos are kept is Rogeno (Italy). Data can be used by journalists, free-lance journalists, persons in the role of trainee journalists and persons who carry out processing for the publication or occasional circulation of essays, articles and other intellectual works for the purpose of the exercise of their journalistic or similar activities. The processing of data will be carried out by the persons mentioned above and by persons in charge of printing and publishing activities. With reference to art. 7, Italian legislative decree 196/2003, you have the right of access to your data, modify, update or cancel data or to object to their, by writing to Interprogetti Srl, and ask for the list of data processors. It is understood that the provisions concerning professional secrecy in the journalistic profession shall be left unprejudiced as related to the source of the information if a data subject requests to be informed of the source of the personal data processed by journalists.
is official distributor and service partner of Haitian and Zhafir products for Italy.
Hilectro robots:
Hilectro robots:
Automation working areas made by Hilectro, member of Haitian Group
Automation working areas made by Hilectro, member of Haitian Group
Haitian MM Italy is responsible for sales and assistance of Haitian / Zha r injection molding machines for thermoplastics for the Italian and Romanian market.
Haitian MM Italy is responsible for sales and assistance of Haitian / Zha r injection molding machines for thermoplastics for the Italian and Romanian market.
The company based in Brescia has contributed to the intense growth of the Chinese brand in Italy and is also responsible throughout Europe for the die-casting machine made by Haitian. With a structure of 4,000 square meters, it allows to optimize logistics operations to more easily manage the machines arriving from Haitian, also considering the addition of die casting technologies.
The company based in Brescia has contributed to the intense growth of the Chinese brand in Italy and is also responsible throughout Europe for the die-casting machine made by Haitian. With a structure of 4,000 square meters, it allows to optimize logistics operations to more easily manage the machines arriving from Haitian, also considering the addition of die casting technologies.
Haitian MM Italy company is able to deliver to the user a complete and turnkey package, which includes everything that revolves around the press: from the automation and robotics system (with relative CE certi cation of the working area) to the safety fences and to Formax peripherals. It also proposes itself as the single contact for the entire order, helping the customer to adopt a solution that respects of the parameters for Industry 4.0.
Haitian MM Italy company is able to deliver to the user a complete and turnkey package, which includes everything that revolves around the press: from the automation and robotics system (with relative CE certi cation of the working area) to the safety fences and to Formax peripherals. It also proposes itself as the single contact for the entire order, helping the customer to adopt a solution that respects of the parameters for Industry 4.0.
The sales network is made up of 20 sales man as well as the after-sales service with 30 technicians covering the Italian territory.
The sales network is made up of 20 sales man as well as the after-sales service with 30 technicians covering the Italian territory.
Haitian Jupiter V series: Space saving two-platen technology
Haitian Jupiter V series: Space saving two-platen technology
From 4,500 to 88,000 kN Large mold space, compact machine design
Energy-efficient servo-technology KEBA control technology
From 4,500 to 88,000 kN Large mold space, compact machine design Energy-efficient servo-technology KEBA control technology
Haitian Mars V series:
Servo-hydraulic solution
Haitian Mars V series: Servo-hydraulic solution
From 600 to 33,000 kN
From 600 to 33,000 kN
Best seller with over 400.000 sold machines
Best seller with over 400.000 sold machines
Electrical charging with higher energy saving rate
Electrical charging with higher energy saving rate
KEBA control technology
Zha r Zeres V series: Electrical solution with integrated hydraulics
Zha r Zeres V series: Electrical solution with integrated hydraulics
From 600 to 13,800 kN
From 600 to 13,800 kN
Over 30.000 installed machines
Over 30.000 installed machines
Available with Medical pack solution
Available with Medical pack solution
SIGMATEK controller
SIGMATEK controller
Zha r Zeres Multi series:
Zha r Zeres Multi series:
Electric bi-injection machine with second injection unit
Electric bi-injection machine with second injection unit
R-type (piggyback) - Vertical – Lateral or Parallel type
R-type (piggyback) - Vertical – Lateral or Parallel type
Zha r Jenius V series: Electric injection unit and two-platen servo hydraulic system
From 3.600 to 33.000 kN
Large mold space, compact machine design
Injection units with 1,2 and 4 spindle concept
SIGMATEK controller