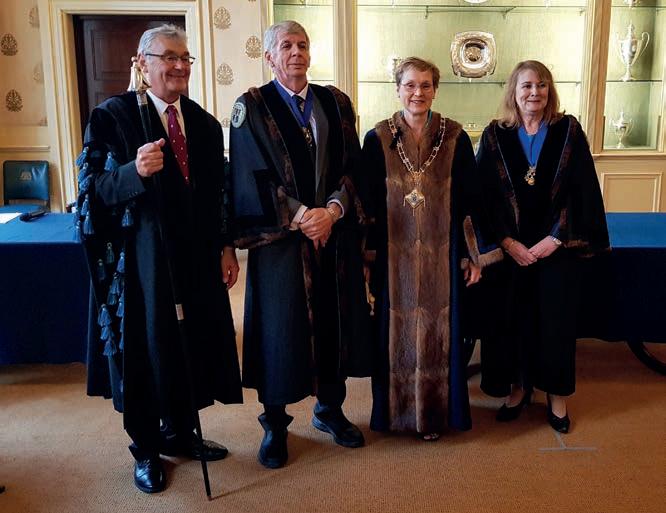
15 minute read
7
AMUSF news roundup
Wendy with Senior Warden, Jackie Smith - right - and Junior Warden, Malcolm Hopkins and - left - Beadle, Roy Theobald
WENDY HAS HER DAY
Wendy Shorter, the AMUSF’s director or training, has officially been installed as the 637th Master of the Worshipful Company of Upholders and only the third Lady Master in over 650 years.
The ceremony, which should originally have taken place on April 1 2020 but was postponed because of the Covid-19 pandemic, took place on Tuesday September 15.
Said Wendy, who also owns the Wendy Shorter Interiors upholstery and soft furnishings training centre: “Coronavirus interrupted everything for all of us, so my installation had to be postponed. “Anthony Demby continued as Master until my own ceremony when I was installed at a very much pared down event than would normally happen. The COVID restrictions meant we were only able to meet in small groups without any formal dining. Therefore, the ceremony took place with just 19 court members and six guests: my daughter Louise, two of our friends, Susie and Malcolm Bay, two new Liveryman: Dennis Tate and his girlfriend Molly and Stefan Koschek, as well as Master Furniture Maker David Woodward. “The ceremony was held at Saddler’s Hall in the City of London and, for the first time in our history, was also Zoomed to members of the Livery who were unable to attend in person.” Wendy was installed by the Immediate Past Master, Anthony Demby and she in turn then installed Jackie Williams as Senior Warden and Malcolm Hopkins as Junior Warden. Added Wendy: “My first task as Master was to clothe into the Livery, Lt. Dennis Tate RN, who my husband Steve and I had pleasure in proposing to the Company earlier in the year. We first met Dennis last year on a visit to the submarine base in Plymouth. Wendy Shorter with husband Steve Blake “As we were unable to dine at Saddler’s Hall due to the ‘rule of six’ COVID restrictions, we went to the Manicomio Restaurant in Gutter Lane. All in all, a very different installation, but one very much more personal to me!”.
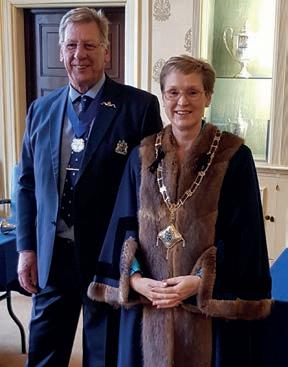
THE AMUSF HAS AN ALL-NEW WEBSITE!
With more and more people now visiting our website, we’ve developed an exciting and up-to-date new site – www.AMUSF.org – offering a host of new features.
Said association manage Manjeet Upple: “We are hoping to have much more interaction from our members, particularly regarding the newsletter. The layout will be completely different, making it exciting to read and more visually appealing.
We’d love to showcase live videos of members and their work and perhaps feature any fascinating projects they may be working on.
“We also hope to give the magazine a greater online profile. Full members can now read the magazine on the website which we hope will, in turn, attract more subscribers. Our social media sites are also linked to the main website so members can see what’s happening from there, as well as on their phones.”
Search engine optimisation is another area being improved to ensure the site takes a more prominent ranking, ideally ensuring when someone puts ‘upholstery’ into their web browser, the AMUSF site comes at, or near, the top of their search.
But the biggest change is a new online payment system: students can now register and pay for their courses online. Said Manjeet: “This is a real step forward for us as it will automatically update our database with each student’s details. It all adds up to a lot less paperwork for us at head office.”
Full members will also be able to pay online although the association plans to maintain its ‘personal touch’ by contacting everyone individually.
Also offering greater functionality is the page featuring the popular fabric buying scheme. In the past, this just carried a basic list of participating companies, but members can now narrow their searches to see which company sells what. They can also click on the name of each individual fabric company and be automatically linked through to its website.
Searching for members has also changed from a postcode only facility to one which can be done by town, postcode
or name, making it easier and more flexible for users.
Said Manjeet: “We were also keen to ensure information about training centres is kept refreshed and up-to-date with links straight to their websites. Prospective students can also search for their closest centre rather than just see each centre’s location on a map.”
Finally, the association’s email addresses have changed to reflect the fact its members include soft furnishers as well as upholsterers. The core ‘@upholsterers’ part of the address has been changed to @AMUSF.
SNIPPETS
• Although not an AMUSF member, it’s good to hear about businesses in our sector which have been investing in the future, despite a difficult year. South
West Upholstery spent £65K refurbishing its showrooms during lockdown, re-opening its doors to the public in early September.
The company, which specialises in bespoke furniture upholstery and soft furnishings for domestic and commercial clients, remains a family business and is based on
North Street, Southville.
• FOR SALE – and with a possible student project in mind – is this
Edwardian chaise longue with turned legs and brass castors (with brown china wheels for sale), priced £275. For more information, contact Derek Caplen of Dee Cee Upholstery on 023 8055 5888.
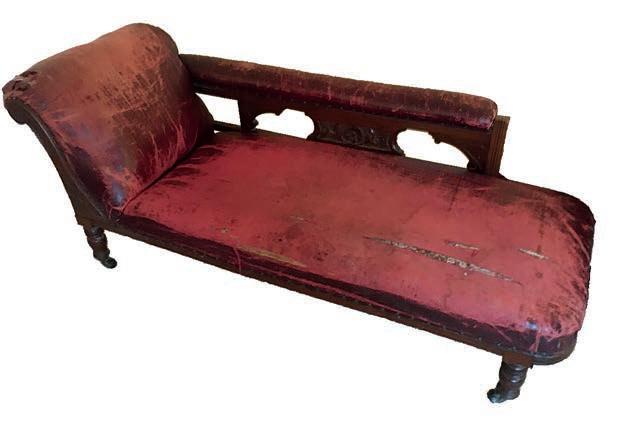
AMUSF news roundup KEEPING STANDARDS IN CHECK
Darren Colvin, a regional technical design manager with Plumbs, has joined the AMUSF team of verifiers.
Darren, who has worked as an upholsterer since 1987, joins the association’s team of five other verifiers, ensuring the work of students meets expected standards at AMUSF approved training centres.
Based at Brixham in Devon, Darren spent 16 years at FIRA working with and training its network of technicians before joining Plumbs earlier this year. He now works with the company – which has been celebrating its 60th anniversary in 2020 – overseeing and supporting upholsterers and loose cover makers from Wales to Norfolk and all points south.
Said Darren: “Plumbs works with over 100 independent upholsterers around the country and my job is to help and support them and ensure there is a good flow of work to sustain their business. The company has actually been incredibly busy since the first lockdown restrictions were eased, so we are always looking for more people to partner with. I spend a lot of time visiting upholsterers each week and the fact that I have spent many years in the trade myself means I have a good understanding of their business and what’s involved.
“I originally trained at the London College of Furniture and then worked as an upholsterer for Collards in Romford before setting up my own business doing upholstery and restoration work. I then joined FIRA as a technician and went on to train other upholsterers to do technician work, handle complaints and undertake repairs.
“I think that experience plus my technical knowledge and the work I now do with Plumbs is not dissimilar to the role of verifier which is essentially a quality control role, maintaining standards and offering advice and support. “Its great to see the AMUSF training schools developing and bringing on our upholsterers and keeping the skills alive. There’s been
Darren Colvin a real resurgence in upholstery in recent years after it dropped off during the early 2000s when people were more into ‘disposable’ furniture. Now, its good to see that people are once again becoming concerned about sustainability, enduring pieces and the skills involved.
“This has to be good for the upholstery sector, but my concern is that it is still difficult for businesses to access apprentices and this will remain so until there are more college courses available to facilitate their training.
“It makes the work of AMUSF training centres all the more important, although we do need to see those students go on to set up their own businesses in upholstery and loose cover making if we are to sustain the future of the craft.
“It means the role of our verifiers is incredibly important to ensuring the quality of their work and encouraging them. If our craft is to live on, these are the people who have the potential to take it forward.” Darren can be reached at Dcolvin@plumbs.co.uk or on 07736 936879.

Industry roundup FURNISHING SECTOR’S ROLLER COASTER 2020
As U&SF went to press, England was in the grip of a second lockdown after what has been an unprecedented year for everyone – and an extraordinary one for the furnishings sector.
After the original Spring lockdown when many businesses had no choice but to temporarily ‘shut up shop’, the year looked a lot more promising by October when a good proportion of furnishing retailers and manufacturers were hoping to meet their budgets by the end of the year. For despite many weeks of zero takings, a surprise surge in consumer spending over the late Summer/Autumn period saw orders pouring in – but quickly led to problems with supplies, lead times and deliveries.
Yet only weeks earlier, the British Furniture Confederation (BFC) had been so concerned about the return to trading post-lockdown, that it had announced a four week Autumn campaign to encourage sales. Its ‘Buy the Best, Buy British, Save Jobs’ campaign launched in furnishing stores nationwide from September 19 to October 18, aiming to make people aware of the jobs at stake and encouraging them to seek out British made goods.
It was an indication of how nervous the sector was feeling over the Summer. But by early October, both the British Furniture Makers (BFM) and National Bed Federation (NBF) were warning of the sudden surge in sales causing supply shortages and putting a squeeze on furniture production and pricing.
While the BFM reported shortages of foam and particle board impacting the production of furniture in the run-up to Christmas, the NBF warned of disruptions to pre-Christmas deliveries. It said price rises were unavoidable as manufacturers faced increasing difficulties getting hold of raw materials. Spring units, foam and timber were among the components particularly affected.
BFM md, Nick Garratt, said: “The squeeze in supply in both the foam and particle boards markets has possibly been exacerbated by a post-lockdown spike in demand for furniture.”
He said factories were being put on reduced allocations of foam block, so affecting production capacity in the critical pre-Christmas delivery period.
NBF executive director Jessica Alexander said the bed industry was experiencing the same problems: “The supply chain is under unprecedented pressure as demand outstrips the ability for factories to make products fast enough. Price rises and rationing are both becoming increasingly widespread and impacting large and small companies, high end and budget sectors alike.”
The AMUSF itself acknowledged similar challenges after the association’s AGM in October when there were discussions about the difficulties in obtaining essential supplies and materials. There were concerns that with so many members working as sole traders or small artisan-style businesses, there wasn’t the buying power to compete with larger businesses, leaving many ‘at the back of the queue’ when it comes to prioritising the distribution of limited goods.
It’s something which chairman Jerry Appleyard has undertaken to look into by examining possible opportunities for group buying along the lines of the association’s successful fabric buying scheme.
The shortages reported across the furnishings sector have been all the more frustrating given a level of trade which represented an extraordinary about turn in consumer spending.
In October, the NBF published the results of a snap poll conducted among its Retail Champions (retailers who stock at least 50% of beds made by NBF members) which suggested that eight out of 10 (80%) of those taking part were doing better than last year.
Said NBF marketing and membership manager Simon Williams: “After a devastating Spring when retailers were forced to shut up shop for the lockdown, the bounce back in sales has taken everyone by surprise. The furnishings sector as a whole has been an unexpected beneficiary of a pivot in spending from holidays to the home and it would appear that bed retailers are among those enjoying a boom that’s been described as ‘Christmas on steroids’.
“Most families have not been able to take their usual holidays this year and also spent a lot of time in their homes. This has both heightened their awareness of what needs replacing and provided the ‘spare’ cash to buy it.
How the latest lockdown in England will now effect trading remains to be seen with most industry watchers unwilling to forecast just where the COVID rollercoaster might take us next and what 2021 is likely to hold.
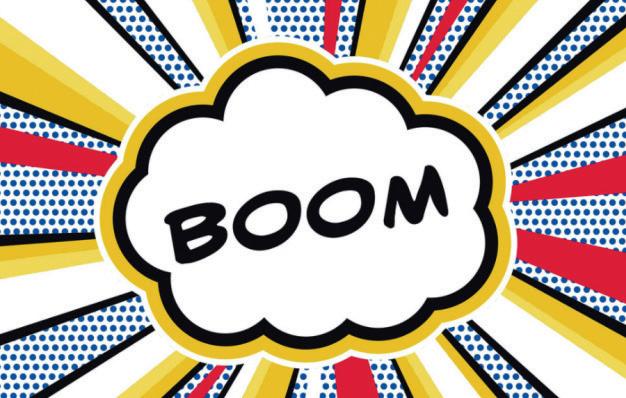
Add a unique touch to your designs this winter!
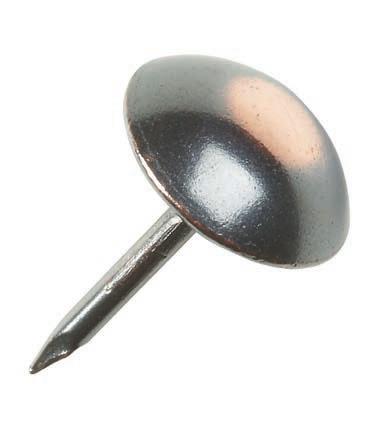

Sofa Legs & Sofa Feet I Upholstery Nails I Brass Castors I Upholstery Supplies I Sewing Threads
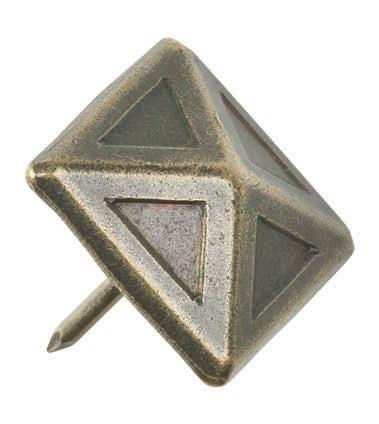
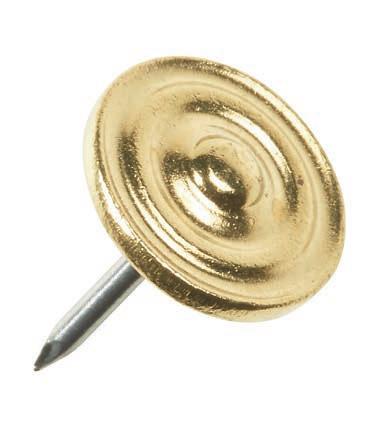


The most extensive range of Decorative Upholstery Nails in the UK Small pack sizes available across the range www.heico-direct.co.uk

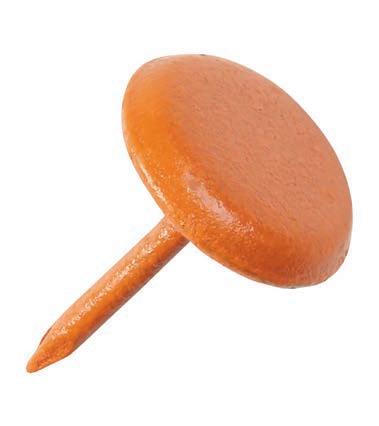
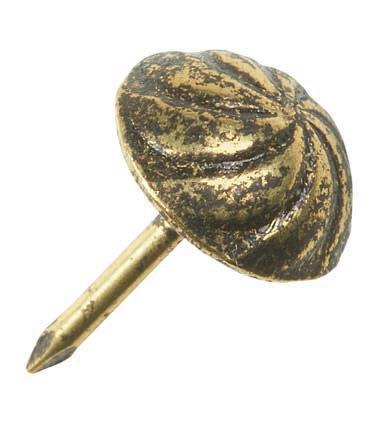
ALL AT SEA
Steve Cotton, FIRA International’s technical specialist for flammability and physical upholstery, answers your flammability questions.
QI have started working within the marine industry and want to know what fire regulations I have to adhere to when upholstering the inside of boats?
AUpholstered furniture in boats must comply with the IMO’s (International Maritime Organisation) Fire Test Procedures Code (FTP code). This is similar to the domestic and contract requirements and the tests are based on the old BS 5852 (Methods of test for assessment of the ignitability of upholstered seating by smouldering and flaming ignition sources) test methods.
However there are a number of differences and therefore materials that are compliant with the FTP Code must be used. There is a list of laboratories on the IMO website that are accredited to carry out this testing if needed. FIRA International’s sister company, Warringtonfire, is able to carry out the testing of textiles and furniture according to IMO FTP Code, Resolution MSC.61(67), Annex 1 Part 7-9). For more details email info.warrington@warringtonfire.com
QI have furniture from the 1930’s that was passed down to me through my family. The sofa suite is really nice but very tired. Could you tell me what fire standards I need to adhere to if I want to get my sofa suite reupholstered?
AAs the furniture is pre 1950 then it is not covered by The Furniture and Furnishings (Fire) (Safety) Regulations 1988 (FFFSR) and can be re-upholstered in non-compliant period appropriate materials.
However, if versions of the materials are available which meet the requirements of the FFFSR then these must be used; or if re-upholstering with modern materials, these should all be compliant with the relevant Schedules from the FFFSR.

QI have a rented property that I have decided to furnish for the new occupiers. Can I use second-hand furniture and will it still comply with regulations? Also do curtains and cushions and other soft furnishings need to be fireproof?
AAll second hand furniture that was manufactured after 1950 is covered by The Furniture and Furnishings (Fire) (Safety) Regulations 1988 (FFFSR) and therefore can only be sold if it is compliant and has the permanent label attached to it.
Curtains for domestic properties do not need to meet any flammability regulations -however cushions do fall under the FFFSR so would need to be compliant. Essentially any product that is upholstered, i.e. has an upholstery filling and cover material would be covered in some way by the FFFSR so would need to be compliant.
For further information email info@fira.co.uk TESTING PORTAL FIRA International has launched a new portal to simplify testing.
The ‘E-TIC HUB’ is designed to give customers more control over their testing, allowing customers to: • Request quotes for all types of furniture testing with FIRA
International • Accept quotes and arrange for samples to be booked in • Follow the progress of specific tests, with full visibility of where the sample is in the testing process, with 24/7 access to check progress and alerts as each testing stage begins / ends • Access and direct download of test reports • Instant messaging with the experts at FIRA International Howard James, testing and technical manager, at FIRA International said: “This is just the first phase launch for the hub. We’re already working hard behind the scenes on the next release which will include a full reporting suite with details on test times and results analysis, the opportunity to schedule tests direct to machines in advance and invoicing functionality via the hub.”


KNOCKOUT MERCHANDISE

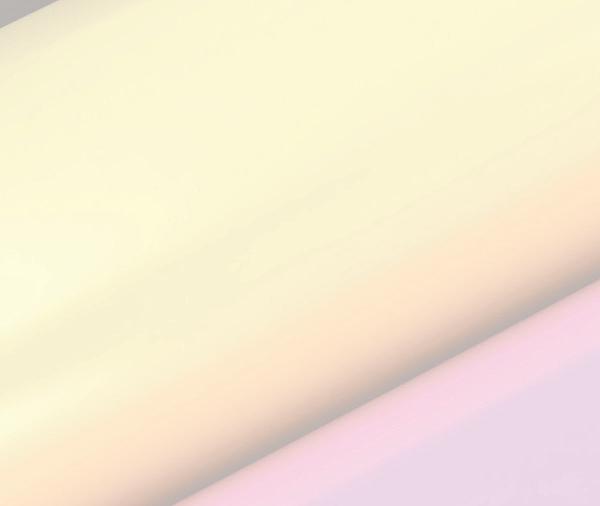
KNOCKOUT MERCHANDISE Our newest brand, headed up by Fiona Hope, formerly of Checkmate in Paddock Wood. For all your branded PPE, workwear, merchandise and anything else you can dream up with your logo on it! Get in touch to discuss any project. sales@knockoutmerchandise.co.uk 01892 839988
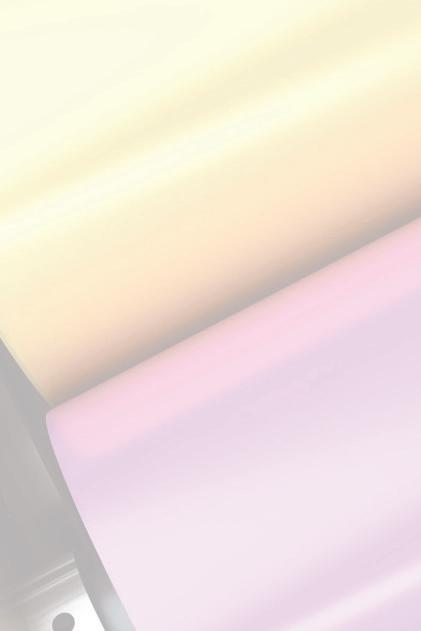
KNOCKOUT PRINT Now in its tenth year and continuing to grow. From brochures to banners, business cards to books, we have it all covered. We like to call it “local print at internet prices” which we feel sums us up pretty well! Whatever you need we have it covered! info@knockoutprint.co.uk 01892 823540

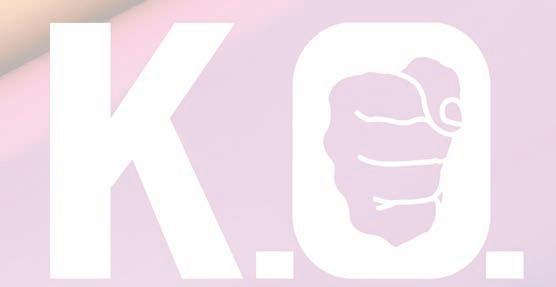
KNOCKOUT KNOCKOUT GRAPHICS PRINT

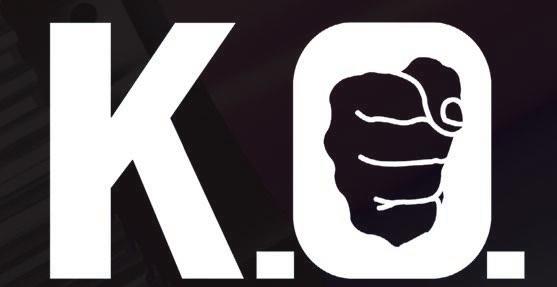

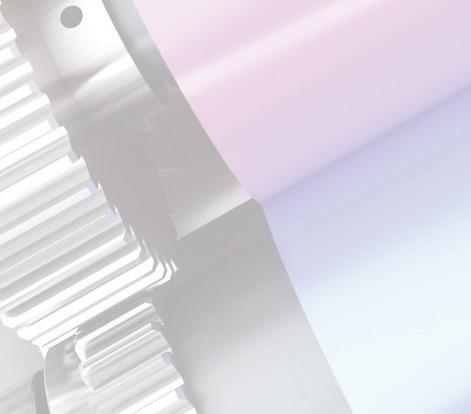
KNOCKOUT SIGNS & GRAPHICS
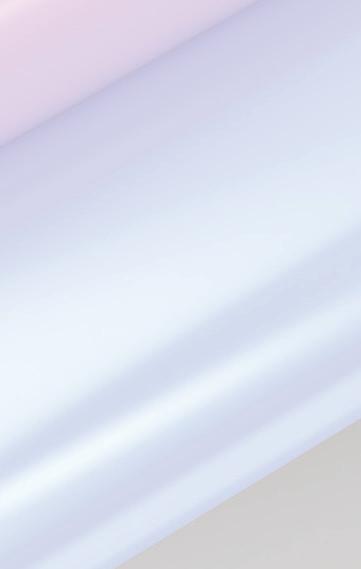
KNOCKOUT SIGNS & GRAPHICS A division of Knockout Print dedicated to the production of wide format printing such as banners, signage, vehicle graphics, exhibition panels and anything else on the larger side of things! Get in touch today! info@knockoutprint.co.uk 01892 823540