
3 minute read
Troubleshooting
Recently the question came up with regards to high main drive motor loads when making petfoods. This can be a good thing if your capacity is high as you simply back down just a bit and keep running. In the case where your motor load is elevated but your capacity is not as expected starts with evaluation of the situation. Extrusion moisture content is a big factor in this area. Too low water content and the extruder has to work harder, increases in steam and water inputs allows for easier flow and higher capacity as water addition acts similar but not as dramatic as adding oil in the system which is an option. The die also has an impact as the open area needed for capacity and the need for restriction to cook the food is dependent on the formula in many cases. Generally, 250 mm2 per tonne per hour is in the ball park but adjustments can increase capacity when it is seen that specific formulas cook easier thus lower motor loads or potential for increases in production rate.
Die design also varies on type of product made. Shaped products typically have a shorter land length and negligible taper behind the actual hole. This allows for a more defined shape being produced. Chunk products have the highest capacity when the land length, the final straight portion of the die hole, is backed by a taper inlet. Studies have shown this die design when everything is equally tested produced less rate but had the lowest motor load allowing for rate increases for the highest production possibilities. It should be noted shaped products as well as high protein formulas normally run at lower rates to achieve acceptable product. Starch sources also have an effect, corn normally achieves the highest possible extrusion capacity followed by wheat and then the rest of the possibilities.
Developments in restriction valves behind the die which creates the pressure in the barrel independent of the die allows for cook control while greatly increasing the possible die opening numbers for effectively increasing the production rate. Use of variable speed main drive motors with VFD, variable frequency drives, allow for screw speed changes which greatly increase the screw volume used over time with potential increases in production rate. Gradual rate increases with moisture and steam adjustments usually allow to push the system while keeping an eye on product characteristics should allow pushing a formula with a specific die to its maximum potential. Once achieved then mechanical changes might be the next move if increases are desired in production rates. What is your bottleneck?
The downstream equipment is what will control the extruder rate as dryer sizing as well as cooling and coating have maximum rates and thus production needs to be balanced for the line capacity.
Previously on Troubleshooting...
1. Density
An examination of product density and its relationship with moisture levels, heating, cooling feeder screw rate and automation.
2. Non-uniform and rough appearance
A guide to understanding the science involved in improving the art of making products of all the same size.
3. Extrusion dies
This article takes a look at aspects of the process including high, medium and low shear as well the adjustments required when producing feed for small mammals.
4. Dryers
The dryer is without a doubt one of the machines in the system which greatly impacts the bottom line.
5. The Extruder Barrel - Part 1
Forming extruders are used for some select products –thus this part of the discussion centres on single and twin designs.
6. Cook in the Extruder Barrel – part 2
As discussed last month, the extruder barrel has a number of functions, but the main goal is to finalise the cook, yield the desired shape with the density target.
7. Coating
The coating process has a few areas of importance, with this edition of ‘Troubleshooting’ exploring the most important of these.
8. Expanded cat food
Dry expanded cat food production is similar to dog food production, but there are some differences, with this edition exploring a choice selection of these.
9. Extrusion during operation
This month we discuss steam input into the conditioner. During the water addition process, the steam is usually in the two-bar range.
Innovations this month
February 2023
This month’s Production Showcase section features equipment and ingredients that will help in the production of petfood, taking you right from the recipe book, right up until until your product is ready to leave your factory door.
If you would like your product or service to appear on this page in a future edition of International Petfood magazine, then please contact us at editorial@perendale.co.uk

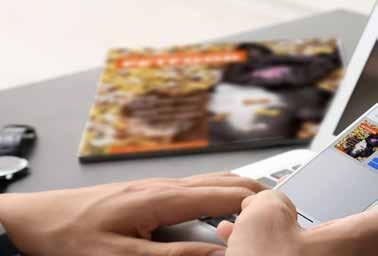
Continuous Coaters by Ottevanger https://www.ottevanger.com/en/products/coating/continuouscoaters/
The Ottevanger Continuous Coaters are perfectly suitable for adding and mixing liquids, evenly on pellets and/or extrudates. By dosing the liquids through a spray box, the product and liquids are slowly mixed together. The trough of the coater itself is executed in stainless or mild steel, with 50 mm thick insulated jacket. The heat tracing stimulates the absorption of the liquid and avoids contamination of the trough. The coater is equipped with hinged inspection hatches over the full length of the mixing trough, which allows easy access. Apart from oil and/or fat, also vitamins, enzymes etcetera can be added in small quantities. Dosing systems for these products are available upon request.
It has numerous features including Low power consumption, large doors enabling easy inspection/cleaning, rigid construction and variable heating system with insulated jacket and also has a low rate of wear.