
9 minute read
HIGHLIGHT OF THE MONTH
GSB International as a Digital Pioneer-Quality Assurance in Times of the Pandemic
© GSB
Edited by GSB International
Düsseldorf, Germany1 info@gsb-international.de
1First published in Besser lackieren 6/2021
Aquality community lives from its network. This was the case before Corona, this is the case during Corona and this will also be the case after Corona. GSB International is active in the field of quality assurance for the coating of aluminium and steel components. Its quality focus is on exterior applications in the fields of architecture and industry. The special feature is that GSB monitors the complete supply chain, by assuring the quality of chromium and chromium-VI-free pretreatment chemicals, of powder coatings as well as liquid paints, and of coating companies. At the beginning of the pandemic, the auditing of the coating companies was a big challenge. Normally, all coating companies that carry one of GSB’s prestigious quality seals are audited twice a year, unannounced, by independent testing institutes. In times of Corona, it is of course difficult to carry out on-site inspections while complying with all hygiene regulations. In addition, the member companies are spread all over Europe. Different regions naturally go hand in hand with different hygiene rules and containment measures. In awareness of the ongoing pandemic, GSB drew up a concept as quickly as possible. The most important factor in this was the safety of the employees from the companies and the testing institutes. A pilot test was launched immediately and an audit was conducted via video conference. In this type of audit, employees at the sites show the auditors the relevant areas using a mobile device. In the meantime, online audits have become part of everyday life. This form of testing was used at companies where on-site audits are not possible due to the pandemic. In this way, the outstanding quality of GSB-compliant coatings can be secured despite the pandemic. In addition to testing, training is particularly important for GSB and its members. Employees of the member companies must regularly attend GSB training courses. Within the framework of these training courses, the GSB association’s team provides knowledge related to quality assurance in accordance with the quality regulations. In addition, highly up-to-date topics, such as technical innovations and legal changes, are regularly included in the curricula. GSB has also switched to video conferencing for this format. What is particularly appreciated here is that in some cases very long business trips are no longer necessary. The member companies can thus actively prevent the shortage of skilled workers without having to invest valuable time in traveling. Coincidentally, the publication of the new edition of GSB quality regulations coincided with the start of the pandemic. These have been completely restructured in countless hours of work. Important information can now be found significantly faster. This is ensured not least by the fact that the documents have been optimized for use on digital devices. As a result, it is always possible to call up the latest information directly in the production facility. Furthermore, glossaries have been included, as they are known from textbooks. This makes it much easier for trainees and newcomers to get started. To ensure that all those who work with the GSB quality regulations on a daily basis can immediately familiarize themselves with the new edition, the GSB offered online introductions. These were so popular that it was able to offer additional sessions on several occasions. Over the course of 2020, the association instructed a total of more than 125 employees of the member companies in its new quality regulations – in German and English, of course. In order to further expand GSB’s digital leadership, the Board of Directors, the Quality Committees, and the Head Office are working closely together. A collaboration that GSB reliably maintains via video conferencing, even in times of restrictions. Cooperation with simultaneous interpreters is particularly important at this point since many nationalities are represented in GSB’s team and, in this way, cooperation is possible without a language barrier. The meeting participants select the language in which they want to hear the meeting via a button. But despite GSB’s advanced digital solutions, everyone is naturally looking forward to the time after the pandemic, when face-to-face meetings and trade shows will be possible again. Meanwhile, the member companies are taking the opportunity to present themselves and their projects on GSB’s social media pages and benefit from its big number of followers.
Werner Mader, Managing Director, GSB International.
HIGHLIGHT OF THE MONTH
IM GROUP Launches Unique Machine for Automated Application of Ring Latches to Liquid Paint Pail Lids
From an interview with Antonio Riggio and Silvio Cimenti
IM Group - San Gillio (Turin), Italy
Tecnopails, an IM GROUP brand specialising in the production of automated systems for packaging paint containers, has developed the world’s first automated system for coupling ring latches and lids.
ipcm® has recently announced the rebranding of Inkmaker1 , which has officially become IM GROUP, an international industrial group of six brands specialising in solutions for the paint and ink production chain.
1 https://www.ipcm.it/en/open/ipcm/2021/69/42-46.aspx IM GROUP’s latest innovation is the result of the know-how of one of these six brands, Tecnopails. Acquired by the group in December 2019 and specialising in the design and manufacture of automated equipment for dosing, sealing, and labelling paint pails and containers, Tecnopails has developed a unique machine capable of automatically applying rigs latches to the lids used to seal paint pails.
© IM GROUP | Photography Riccardo Cordera
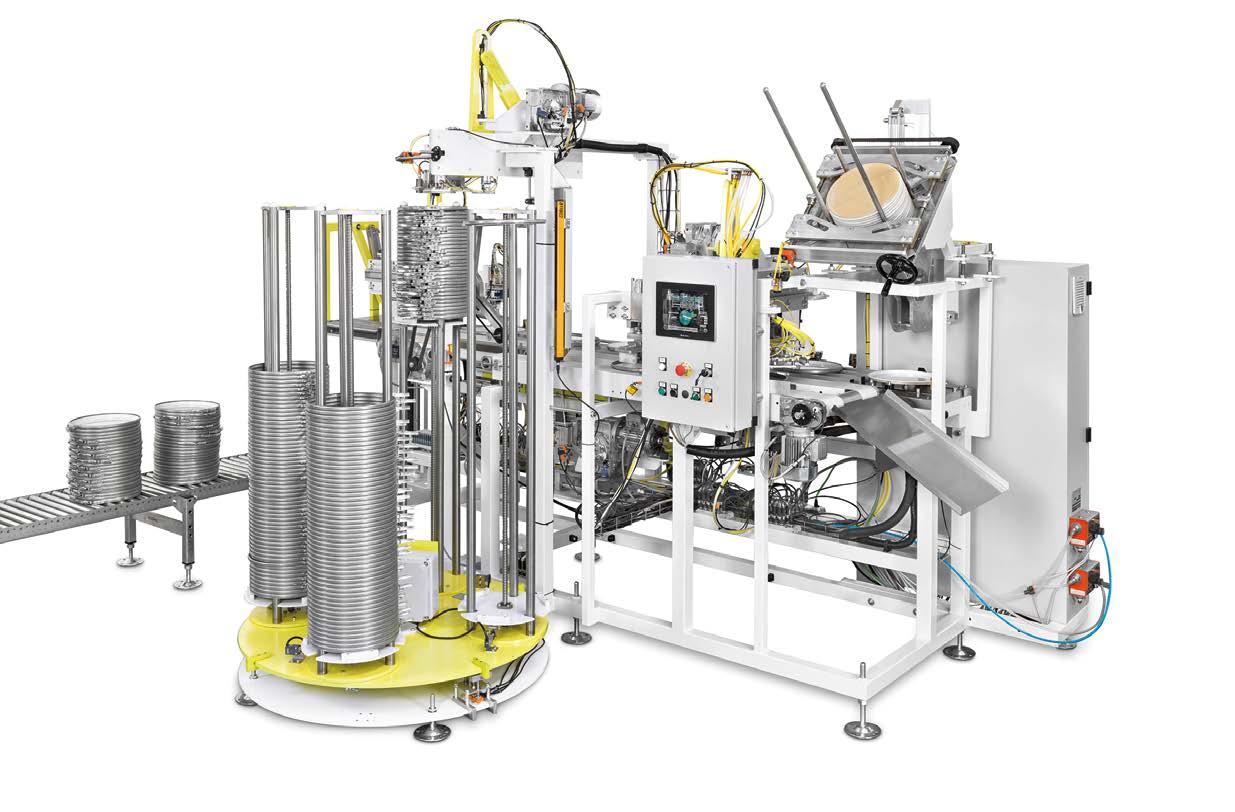

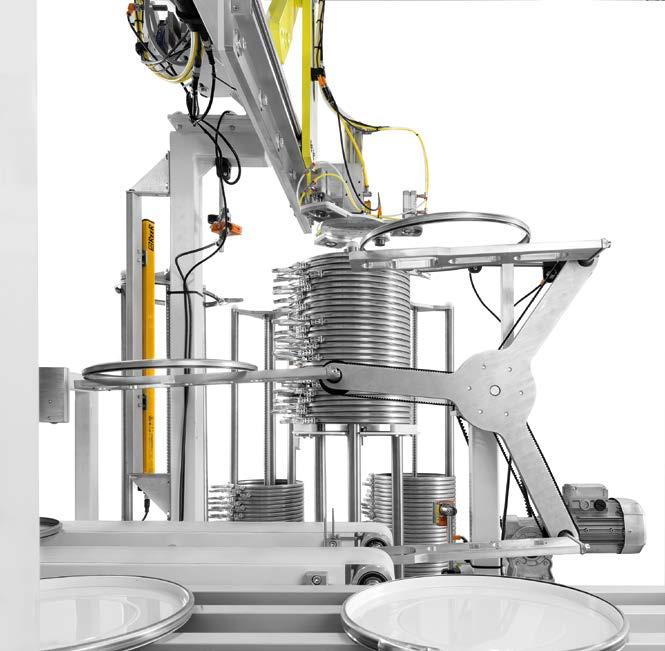
“Tecnopails has always stood out for its ability to create products tailored to customer needs. When it was established in 1974, there was no standard available and each customer had different needs. Although we now also offer a line of standard filling products, the focus on customisation that has always distinguished us continues to be part of our know-how and it is what has enabled us to develop a unique machine, for which there is absolutely no related literature. It actually meets the need of one of our customers, active in the production of paint containers, as it enables lids to be applied their corresponding ring latches automatically,” explains Tecnopails Operations Manager, Antonio Riggio.
Innovative drive
The need to design such a system arose from the fact that paint manufacturers prefer to be supplied with lids having their ring latches already applied: this operation is usually carried out manually by lids suppliers. Supplying lids having their ring latches already applied is easier and has a lower cost than supplying lids and ring latches separately. The bulk handling of ring latches is highly complex because they can be fitted one inside the other, and it requires doubled transport volumes. “The machines we have developed are totally Italian-made prototypes, the first in the world, designed in synergy with the customer that will have them installed at its premises at the end of July. They are twin machines, symmetrically arranged for reasons of space. Each machine is equipped with a graphic touch screen to make man-machine interface easy and intuitive. This system has two storage areas, where the operators can safely load lids and ring latches respectively, even if the machine is in use. The plant automatically picks up a ring latch and a lid, it couples them, and it arranges them in neat piles. As the thickness is greater in correspondence with the ring latch handle, it is necessary to misalign the handles in order to keep the piles vertical: the machine takes care of that as well. “Moreover, when the system picks up the ring latch from the storage area, it recognises the orientation of its handle autonomously, so that the ring latches do not need to be arranged with a precise orientation,” adds Riggio. “Our system ultimately enables paint container manufacturers to offer their customers a solution that optimises filling operations: their automatic packaging machine will simply have to place the lid with the ring latch on the container, open and close it to seal the pail. Regarding the new machines, what the operator has to do is packaging the ready batches”. However, IM GROUP’s system has also been designed to be integrated with other process plants and to be fully automated based on the Industry 4.0 principles. “The project specifications also included the ability to interface with
© IM GROUP | Photography Riccardo Cordera
the customer’s management system and the possibility of integrating and automating other process phases with an Industry 4.0-oriented approach, also opening up to various tax benefits. Our customer intends to automate the transport of the lids to the machine, which is currently carried out by operators: automating this step would mean that the machine that prints the lids feeds our machine directly. In future, the packaging of the stacks of already-coupled lids and ring latches could be automated as well. And all this will be made possible by the fact that we have designed the entire project for full automation,” says Riggio.
The beverage sector as a model applied to the world of paints
“One of the reasons why we were the first to develop this machine is because we had forty years’ experience in the industry, giving us the necessary know-how. Indeed, in the context of other tailor-made solutions developed in the past, we have started specialising in the handling of ring latches by developing a machine capable of picking up a ring from its storage area and putting it on a finished pail. It was intended for paint manufacturers buying pails and ring latches separately. However, such need has changed over the years: paint manufacturers have begun to demand for pails to be supplied with already-coupled ring latches and lids, and this has meant that the demand for these machines has diminished. At the same time, this has led pail producer to require the automation of the coupling process, in the presence of high enough volumes. Clearly, in terms of finances, access to this type of automation is limited, as the investment is only justified for large volumes. At the same time, our customer, a multinational company holding a very large market share, has in fact gained a considerable competitive advantage with it,” notes Antonio Riggio. “This system is now a flagship of the IM GROUP, as well as a technological milestone that allows us to demonstrate the experience and design capability behind our brand. It will probably remain a unique product that will never be manufactured on a large scale, but it is a perfect example of our technical ability to meet any customer needs or requirements,” confirms Silvio Cimenti, the Global Branding, Marketing, and Communications Director of the IM GROUP. “We want to position ourselves in the market as a total solution engineering firm, that is, a one-stop supplier able to serve the whole supply chain in the paint production sector, from dosing to packaging. The acquisition of Tecnopails is further proof of this, as it specialises in the final packaging operations, which we were not dealing with yet. We have completed about 90% of this project with our six different brands, now working together while each bringing its own specialisation, and we are actively working to add the missing pieces of the jigsaw to reach our goal of becoming a global supplier for the inks & paints industry.” “The paint sector is a few steps behind other industries that have experienced exponential growth, such as the beverage one, where players are used to approaching the market as sole suppliers. As such, IM GROUP’s supply chain completion project is highly innovative: we want to apply the successful model of the beverage sector to the world of paints,” concludes Antonio Riggio.

© IM GROUP | Photography Riccardo Cordera