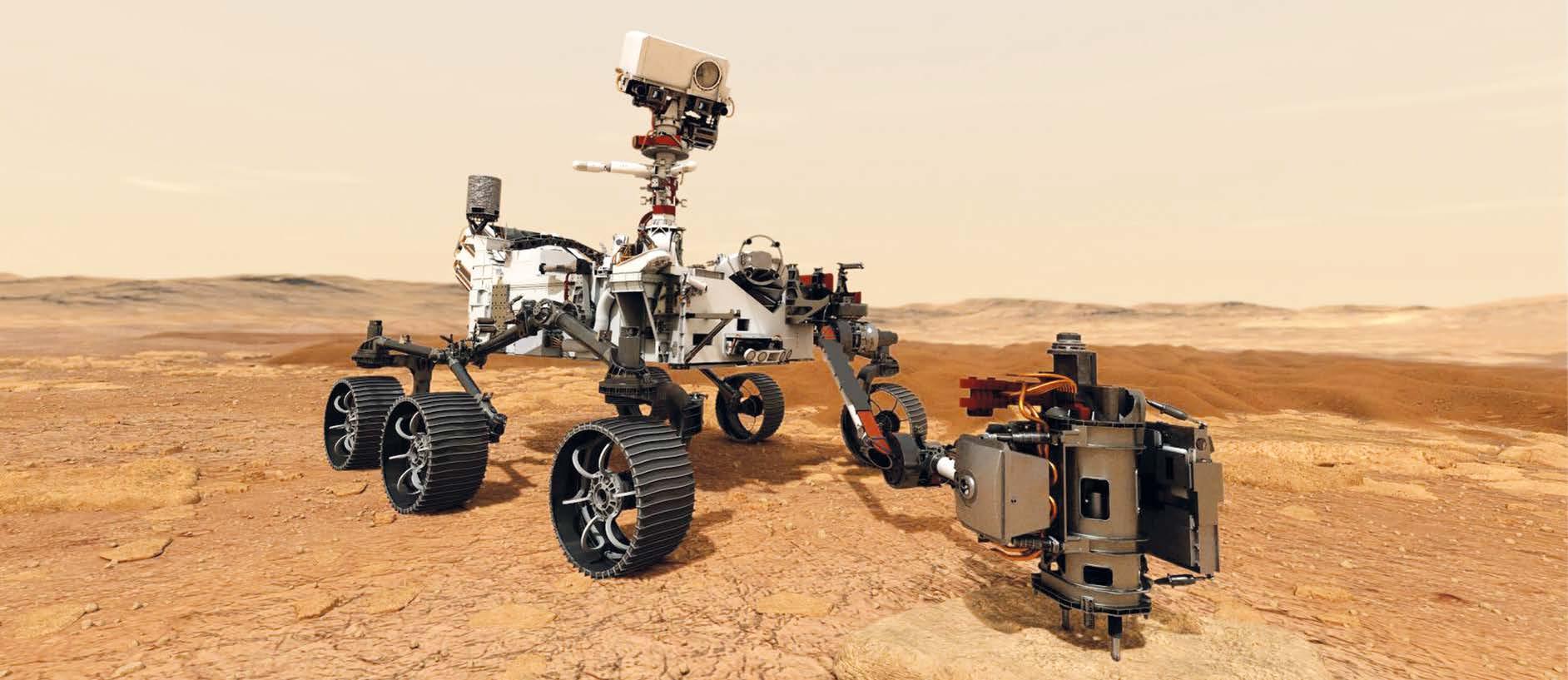
10 minute read
IPCM IN REVIEW
Painting Cars for Mars
DC Agle
Jet Propulsion Laboratory, Pasadena CA – United States agle@jpl.nasa.gov
What does NASA do to get a rover ready for Mars? JPL’s paint shop does a thousand different paint jobs a year. And while every piece of spacecrafts that comes through the shop is important, one headed for the Red Planet adds a little extra oomph. After four-and-a-half months and a painstaking work of masking and coating, the Perseverance rover was ready for its mission to the Mars. This is the story of how it was built and coated.
“We do a thousand different paint jobs a year at JPL, from components as small as a pill to entire spacecraft fuselages,” said John Campanella, coating expert at NASA’s Jet Propulsion Laboratory in Pasadena, California. “I have worked on the first Mars rover Pathfinder, the Deep Impact mission, GRAIL, Juno and Cassini, and I think my paint is just about everywhere in the solar system. When we finished off the Mars 2020 chassis, we had to get everything as close to perfect as we can get it.” While there are thousands of steps that could be chosen to start a story about producing an SUV-sized, nuclear-powered six-wheel-drive vehicle for the Red Planet, we will begin ours four-and-a-half months before Campanella and his colleagues trained their highly-trained paint guns on the rover.
© NASA/JPL-Caltech In mid-April 2018, more than 20 freshlymachined, large, shiny chunks of 7050 and 7075 aluminium that would make up the primary structure of the chassis were collected in a clean room in Building 18 at JPL, along with about a hundred smaller secondary parts. Over the following four-and-a-half months, Mars 2020 engineers and technicians planned, measured, examined, consulted, drilled and fastened until those many parts became a single Mars rover chassis. “The plan called for 610 rivets, 730 washers, 644 nuts and 964 mechanical fasteners to hold the rover chassis together,” said Stephen Pakbaz, lead engineer for the Mars 2020 chassis assembly. “That means there are well over 1,000 holes in the Mars 2020 rover. But in almost all cases we don’t just drill once for each hole; we drill three or more times - entirely by hand.” Each hole in Mars 2020’s chassis began its life as a hand-drilled pilot hole. Next, a larger bit is introduced to expand the hole slightly. Then a final drilling of the same hole takes place. “We drill holes in steps because it gives us the best chance to catch any errors, stresses the metal less, and the increments make it easier to drill by hand,” said Pakbaz. “It’s detailed work and at times can be tedious, but everyone knows what is at stake.”
Prep Work
At the end of 5,000 engineering hours of assembly, involving more than 3,000 drillings and well beyond a thousand rivet and fastener applications, the rover’s chassis was complete. But it still was not ready for the paint guns of Campanella’s team. There are locations on the rover’s chassis where paint is strictly verboten - places where electronics boxes have yet to
Your Leaders in Zero Liquid Discharge
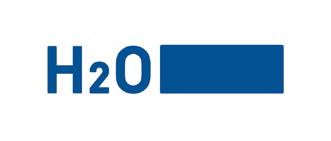
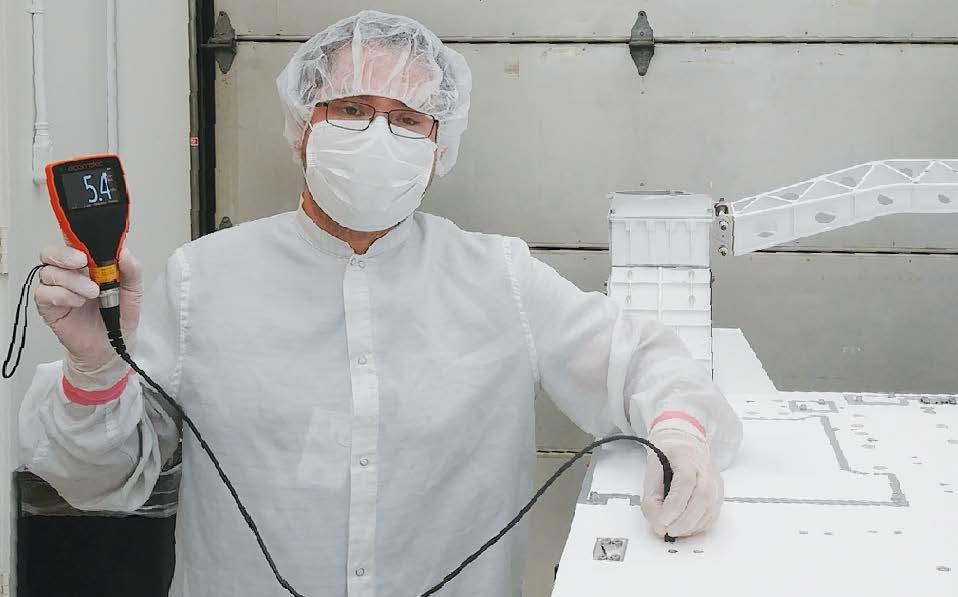
Industrial Wastewater Treatment
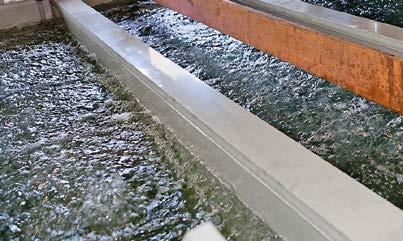
© NASA/JPL-Caltech
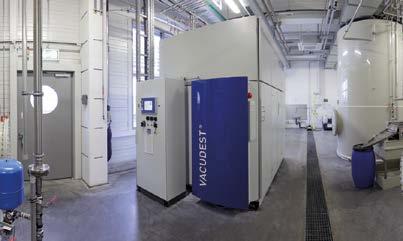
JPL mechanical technician Eduardo Castro uses a paint meter to measure the paint thickness on the Mars 2020 rover chassis. The reading on the meter indicates a thickness of 5.4 thousandths of an inch.
be bolted on, wiring harnesses are still to be run and attachment points for hypersensitive science instruments that require bare metal surfaces to perform their best. “Any good paint job is preceded by a great tape job,” said Campanella. “I wouldn’t freestyle flames on a Camaro, and we sure don’t freestyle Mars rovers.” Numbering more than 600, the pieces of masking tape for the rover came in all shapes and sizes. Many were smaller than a coin, but a few were about the size of a bagel, and one (covering where fibre optic cable channel will go) was shaped like a serpent and as large as a microwave oven. All were applied by hand and smoothed out to prevent bubbling. “One hundred and thirty-five temporary sheet-metal stencils also were applied during this time,” said Ryan van Schilifgaarde, a support engineer for Mars 2020 assembly. “They mask larger locations on the rover that require a more rigid cover during this part of the build.” The masking team measured success by the millimetre, and more than one application of masking tape had to be recut and reapplied after a visit from Quality Assurance. But with five Mars 2020 engineers logging 500 hours over seven days, the task was finally complete. On Aug. 6, 2018, the Mars 2020 rover chassis - festooned with metal overlays and masking tape, and then covered in sterile antistatic wrap - was gingerly forklifted 150 yards from Building 18 to JPL’s paint shop.
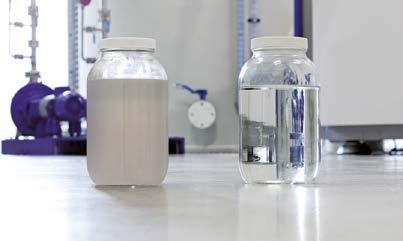
A “Martian” painting
“With any spacecraft, after you get the static wrap off and inspect the rover, you start with surface prep - abrading the surface with sand paper so the paint will adhere better,” said Campanella. “To prevent any chance of corrosion or oxidation, the rule is, once you start sanding, you have six hours to complete everything - sanding, priming and painting.” As spacecraft paint jobs go, the Mars 2020 rover was big, and occupied much of the paint room. Because of the rover’s size, Campanella worked with just two other people, and this small team took on the rover in stages. They painted the top deck first, then let things cure for a day before tackling the sides. Another day off and they finished with the Simple Principle
Effective Result
Leading companies rely on vacuum distillation systems for the sustainable treatment of industrial wastewater.
Do you want to benefit from a zero liquid discharge production with VACUDEST aswell?
© NASA/JPL-Caltech
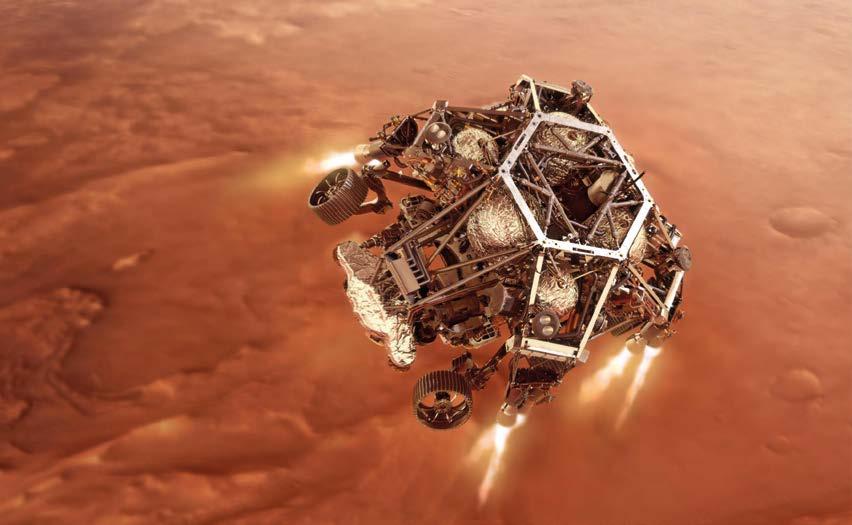
Engineers prepare the Mars 2020 spacecraft for a thermal vacuum (TVAC) test in the Space Simulator Facility at NASA’s Jet Propulsion Laboratory in Pasadena, California. In this illustration NASA’s Perseverance rover fires up its descent stage engines as it nears the Martian surface. The rover launched in July 2020 is collecting and storing rock and soil samples on the planet’s surface that future missions will retrieve and return to Earth.

© NASA/JPL-Caltech
front and back. Even with the job spread out, sanding and meticulously cleaning the results of said sanding ate up over two of the six available hours. “You can’t think about where it’s going or how much history it can make,” said Campanella. “We use the same paint guns on the same setting and fire them from the same distance and move at the same speed each and every time.” The primer and paint used on Mars 2020 are able to adhere to aluminium, and they have been proven through rigorous testing to be able to endure the jolts, vibrations, UV rays and other indignities of a trip to Mars, as well as be hearty enough to survive the Martian cold - all the while not outgassing organic compounds and other materials that could affect the mission’s science experiments. Less than five hours in and the three-layers’ application, the first painting session on the Mars 2020 rover chassis drew to a close: the rover’s chassis was coated with a blanket of paint between 4 and 6 mils (or thousandths of an inch). Ready to Bake
On Aug. 14, the Mars 2020 rover chassis was again carefully sheathed in antistatic wrap and transported “up the hill” to Building 144, where it would be baked in a vacuum chamber. “Cooking the chassis at 230°F (110°C) in a vacuum for three days not only hardens the paint, it literally bakes out contaminants from the paint that could possibly outgas in flight,” said Pakbaz. “Since Mars 2020 is an astrobiology mission, ensuring Mars samples have not been contaminated is paramount. Baking the rover goes a long way to making that possible.” On Monday, Aug. 20, the rover chassis came out of the oven. After inspection, it was again covered in sterile, antistatic film and returned to the clean room in Building 18 for some final touches and inspections. About two weeks later, on Sept. 5, a forklift gently carried the assembled, painted and baked chassis at no more than 3 mph back down the hill, a halfmile to JPL’s Spacecraft Assembly Facility High Bay 1, where it took its place next to the cruise and descent stages tasked with getting the rover safely to Mars. “When we are in the paint room, it is all about business,” said Campanella. “But now that our job is done, I wanted to make sure my team took a moment to let it sink in that they are part of a dedicated team of professionals working on a historic mission of exploration.” “It may not have flames or racing stripes,” he added, “but it still looks beautiful.” Mars 2020 launched from Space Launch Complex 41 at Cape Canaveral Air Force Station in Florida and landed on Mars in February 2021. It is currently carrying out its mandate to seek signs of ancient life and collect samples of rock and regolith (broken rock and soil) for possible return to Earth.
Scan the QR code to see NASA’s Mars 2020 Rover prepping
© Rich Vintage
Dörken Launches a Series of Webinars on “Soft Handling”
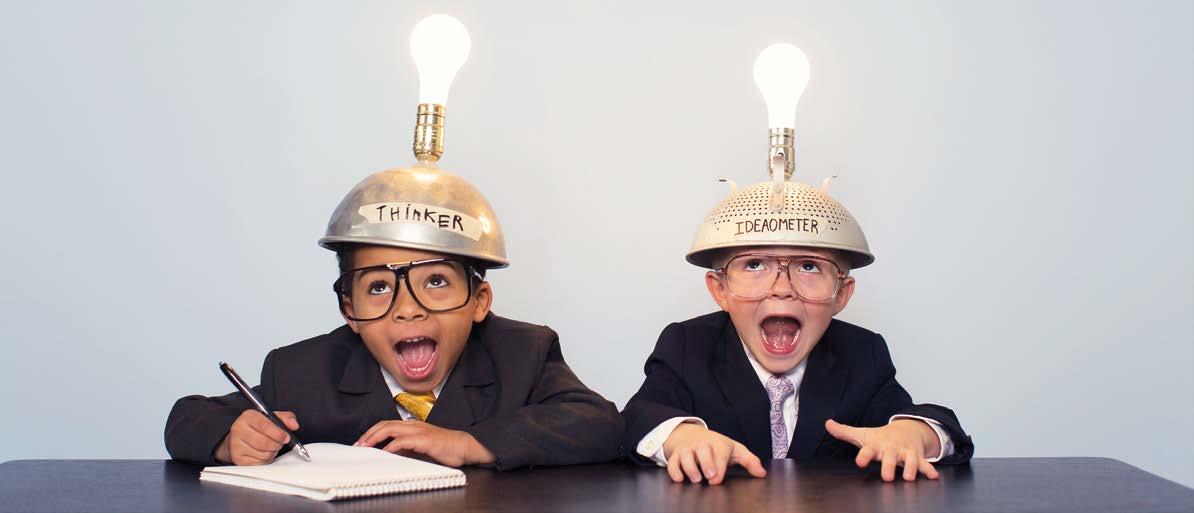
Starting from September, Dörken held a webinar series which addressed some of the most important questions on the subject of “soft handling”.
Dörken has decided to transfer its knowledge in a five-part webinar series on “soft handling” that provided information on the influence of the handling of parts throughout the value chain on corrosion protection, on by whom, when and how parts should be processed and on how to check the quality after the subsequent processes. The origin of this topic is the discovery by the German automotive manufacturer Daimler that bolts showed completely different corrosion processes at various positions on the car, despite originating in the same production and coating batches. All the webinars are held in English. The September webinars treated the following themes: • History of Daimler’s Quality offensives & special focus on soft handling issues in DBL 9440 • New version of the guideline of the Deutscher Schraubenverband & accordance with ISO 10683 for zinc flake coatings • Bolt production & coating process.
The next webinars will take place on: • Sorting, re-rolling of threads and patching – Scheduled: 05/10/21 • Packing, transport and assembly – Scheduled: 12/10/21 Dörken as well as external experts explain the different handling stages in the value chain. Dr. Pellkofer – head of Corrosion Protection and Surface Technology at Daimler Truck AG – provided exclusive insights into the Daimler history of the quality offensive and the Daimler DBL 9440 supplier specifications. Other speakers are Mr Bingeser (Richard Bergner Holding GmbH & Co. KG), Mr Mondin (Primat S.p.A), Mr Mauri (A. Agrati S.p.A.) and Mr Yazgan (R+FK Schulte KG). The series of webinar is part of the Dörken Academy, a project intended to pass on the bundled expertise and experience on the protection and coating of surfaces in seminars and training measures. As by the company motto, “Discover Expertise”, Dörken aims to transfer knowledge - including practical content - and improve dialogue, so it offers a platform on which people from different sectors and positions along the value chain can interact with one another. Subjects range from corrosion protection to structural coatings and on to pigment pastes and colour systems. Further information and registration options can be found in the “Academy” category of the company’s website. Here there are also listed further German and English language seminars and training offers.