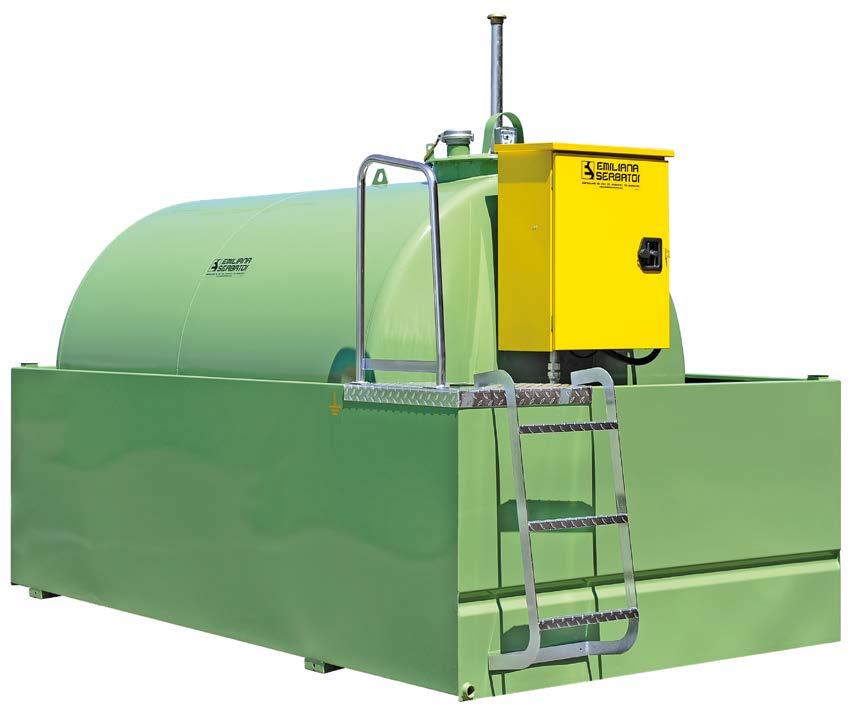
11 minute read
FOCUS ON TECHNOLOGY
SPECIAL ISSUE ON ACE & OFF ROAD VEHICLES
Emiliana Serbatoi’s New Water-Based Top Coat Halved Drying Times and Increased Production Throughput
Monica Fumagalli ipcm®
Reducing the duration of coating processes is one of the most frequent requests received by paint manufacturers from applicators. Emiliana Serbatoi turned to Inver, belonging to multinational group Sherwin-Williams, for the development of INVERPUR/R, a water-based top coat capable of halving drying times even at room temperature and thus doubling its production capacity related to its world-famous tanks.
Production times are among the biggest costs of a company. Emiliana Serbatoi (Campogalliano, Modena, Italy), a company known globally for the production of tanks for the storage, transport, and dispensing of fuels and liquids in general for agricultural and industrial use. “This is why,” states Gian Lauro Morselli, the founder of the company in 1983 together with his father Giancarlo and its current president, “we are always on the lookout for innovative solutions that can reduce our products’ delivery times to increasingly demanding local and international markets.” Moreover, in 2015, the firm switched from solvent-based to water-based paints and, since then, the drying times of its tanks have increased due to the inherent peculiarities of this particular coating technology. Based on a well-considered management decision aimed at sustainability, however, it chose not to install a drying oven in its coating department, which would have certainly reduced
One of the latest products made by Emiliana Serbatoi (Campogalliano, Modena) and coated with INVERPUR/R.
© Emiliana Serbatoi
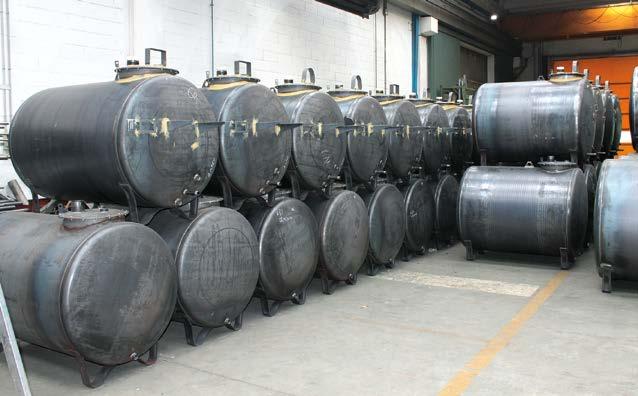
processing times. As the President explains, “this would have had a significant evintonmental impact, in contradiction with the green principles that have always been pursued by Emiliana Serbatoi, which considers environmental friendliness a priority – as is also demonstrated by the recent installation of a photovoltaic system, aimed at meeting our company’s energy needs.” The company, on the other hand, chose to continue to believe in the ability of its water-based coatings’ supplier to find the right solution for its needs and, in the end, it did. INVERPUR/R, the top coat developed by Inver1’s laboratory during the pandemic, meets the demand of all those applicators that, like Emiliana Serbatoi, choose to let their products dry at ambient temperatures, which are not always optimal because they are difficult to control, thus avoiding the oven. Since the 1960s, when the path that would have led to the foundation of the company in 1983 began, “Emiliana Serbatoi has stood out for its non-conformist choices such as this one,” the president says, “which have led it to become an international benchmark” to the extent that it has been called upon by governments all over the world to offer its expertise in the development of regulations for the complex sector of the manufacture and securing of tanks for petroleum products and liquids in general.
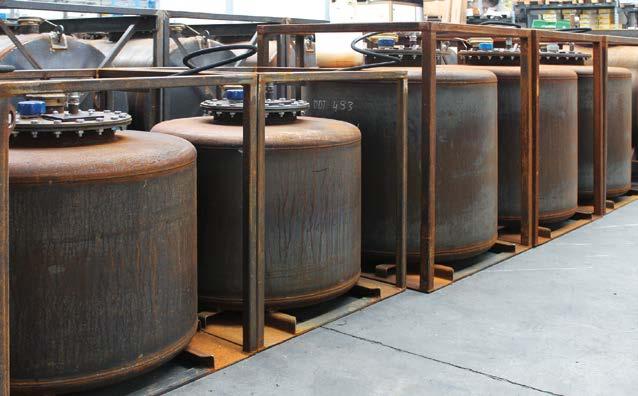
Emiliana Serbatoi: from farmland to oil tankers
Emiliana Serbatoi started its business with the construction of gravity tanks for diesel fuel (now no longer legally compliant) intended mainly for farms, quarries, and construction sites that needed fuel dispensers for their work vehicles in easily accessible areas. Hence, the urgent need to especially regulate the production of agricultural tanks, which at that time could reach a volume of up to 9,000 litres: the risk of accidents that would cause potential harm not only to people but also, in the event of a spill, to the soil and the surrounding environment was unacceptable. “Emiliana Serbatoi was the first company to obtain ministerial approval for its single-walled steel tanks equipped with a containment basin for the storage of diesel fuel,” says Paolo Cinquegrana from the firm’s marketing department. “These tanks were the initial core business of our company, which since then has also continued to collaborate with the Italian ministry of the interior first and then with foreign governments as well to make a technical contribution in the drafting of new environmental safety regulations.”
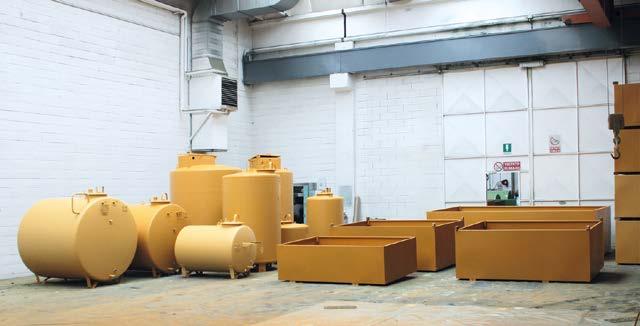
1 A brand of The Sherwin-Williams Company.
© ipcm
© ipcm
From top to bottom: - Some tanks waiting for mechanical pre-treatment before painting. - Brushed tanks. - The coating booth.
© ipcm

© Emiliana Serbatoi
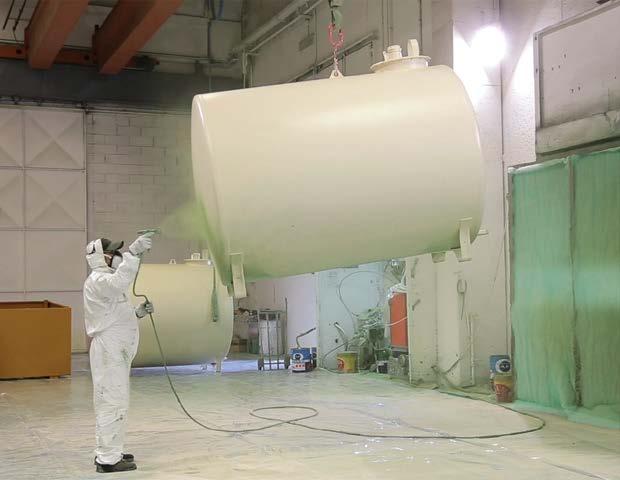
An INVERPUR/R top coat application phase.
© Emiliana Serbatoi
In the 1990s, a new figure emerged in the agricultural sector, that of the contractors who used their own machinery to work the fields to order. “With this came the need to build transportable tanks that followed the contractors’ vehicles and were capable of safely transporting diesel fuel. In addition to our established line of storage tanks, we therefore started manufacturing transport tanks, which have in turn evolved into a series of plastic transportable tanks. Actually, polyethylene products now account for 50% of our production, with sheet metal tanks accounting for the other 50%,” indicates Cinquegrana. The company has now achieved an annual production of 18,000 plastic transportable tanks made with 25 proprietary moulds and 4,500 iron tanks. It has also significantly diversified its target markets beyond agriculture, which still remains among the priority sectors, to include the industries of construction, oil and gas – for example, it was approached to supply a container station to be mounted on an oil tanker – automotive, transport, shipping, aviation, industrial equipment, gardening, and food. “We have also developed a department devoted to special tanks, particularly for the chemical and pharmaceutical sectors, for which we are receiving more and more requests,” notes Gian Lauro Morselli. “This is further proof that we are not afraid to go against the tide: our competitors are currently focusing on standardising their production, while we are going in exactly the opposite direction with our constant search for innovative products.”
The production structure
In the second decade of the 2000s, the company revised its production structure. As Morselli explains, “with the Campogalliano site alone, Emiliana Serbatoi was no longer able to cope with increased market demands. Therefore, we decided to insource some processes such as the construction of tank casings and to acquire another company in San Donà di Piave (Venice, Italy), which carried out the same production as us and had an in-house coating department, but was no longer able to cope with manufacturing costs. We then decided to only perform our sheet metal processing operations there and close the paint shop, in order to concentrate the finishing processes in Campogalliano and thus have greater control over our coating quality, while avoiding unnecessary additional handling and, consequently, longer delivery times. This decision also led us to expand our product portfolio, which now range from 50-litre to 80-m3 tanks, with no limit on customisation.” The acquired Venice-based company took the name of Espa Enerlab and it now manufactures finished tanks that it then sends to the Campogalliano plant. “However, it is thanks to the experience that San Donà’s technical staff had in the field of painting that we heard about Inver and its water-based paints for the first time,” adds Filippo Cucchierato, the technical manager of Emiliana Serbatoi. “Before employing these products into our coating process, we carried out a number of tests that gave very good quality results compared with the products we were using at the time and with which we were experiencing durability problems. In fact, we needed paints that would give the coatings a high degree of resistance not only against the chemicals present in the fuels contained in our tanks, but also against the severe weather conditions to which our products are often subjected.”
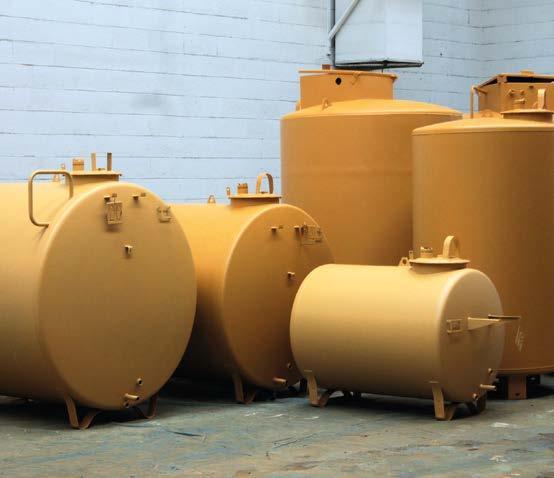
Coated tanks in the drying phase.
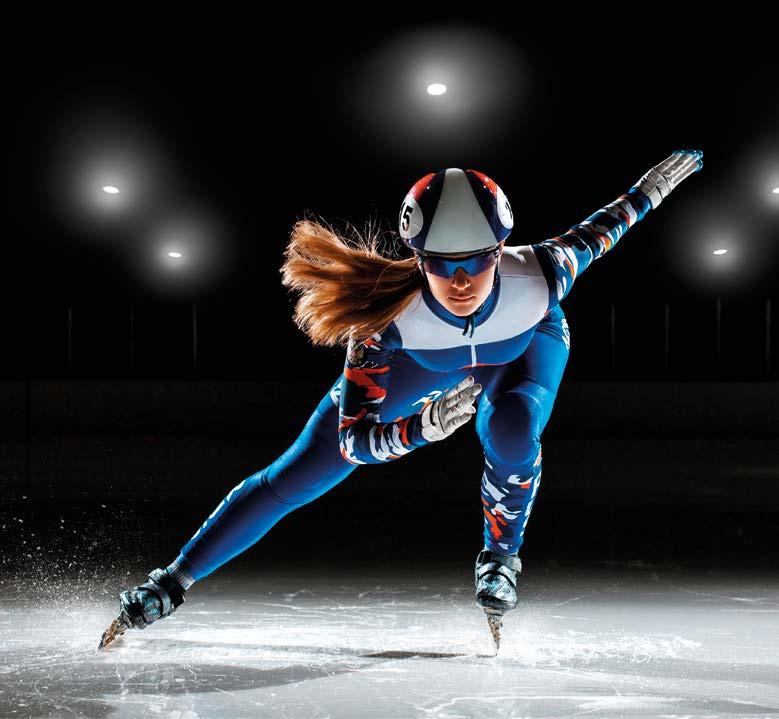
© ipcm
The competitive edge provided by the fast-drying top coat
Once the tanks reach the Campogalliano plant, they are degreased and mechanically pre-treated to remove any residues of dust and contaminants left by previous processes and then sent for painting. “In our manual coating booth, we use an airless gun to apply two coats of primer, also supplied by Inver: one on the most difficultto-reach areas such as welds and undercuts and one on the entire surface of the tank,” says Cucchierato. “The product is then left to dry at room temperature and, once dry, it receives a coat of INVERPUR/R, followed by drying in the booth at room temperature, aided if necessary by mechanical ventilation. While the entire cycle used to take 48 hours, thanks to the coating developed by Inver it now takes just 24 hours, leaving the tank to dry overnight. We can thus cope with a high production rate of 15 to 25 tanks per day, with delivery times of 3 days. We apply different colours, but the predominant one is a green shade called “Emiliana” because it is the typical tint of our products: it accounts for 80% of the paints we use, whereas customised colours on request account for the rest. Inver’s cooperation has also proved to be optimal in the management of batches, from the largest ones to the smallest ones needed to meet the most particular requirements.”
Features of INVERPUR/R
“The top coat developed in our laboratory,” says Sherwin-Williams’ sales representative Michael Benedini, “is a water-based, twocomponent polyurethane acrylic resin. The main challenge faced
Fast. Powerful. Consistent.
Become a winner with Atotech’s efficient paint removal processes
Master Remover® 7000 paint removal process, together with Master Remover® ESPRIT integrated equipment, provides a powerful in house solution for powder paint removal.
Free of hazardous solvents
• Fast powder paint removal • Simplified operation and control with Master Remover® ESPRIT plug and play equipment • Consistent performance, all day everyday • Efficient use of energy and space
Table 1: INVERPUR/R speed of drying.
100 µM WFT (≈ 50 µM DFT) 150 µM WFT (≈ 70 µM DFT)
Drying conditions RT 40 °C 60 °C RT 40 °C 60 °C
INVERPUR 25% 72870
Tack-free time >8 h >1 h 30 min >8 h >1 h 35 min
Dry-to-handle time >8 h >2 h 35 min >8 h >3 h 40 min
INVERPUR/R 30% 40301
Tack-free time 3 h 20 min 10 min 3.5 h 20 min 10 min
Dry-to-handle time 4 h 30 min 10 min 4.5 h 50 min 15 min
An example of a tank with customised colours.
© ipcm
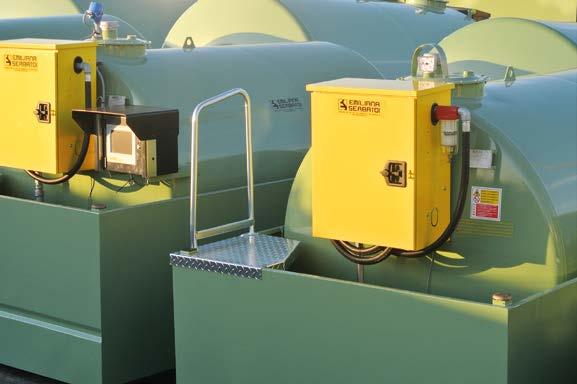
when creating the most suitable coating system for Emiliana Serbatoi’s needs was its high quality standard, combined with its processing time requirements to cope with peak production. We conceived a waterbased, two-component product that works perfectly both in optimal conditions such as those of a drying oven with pre-set temperature parameters and in less than perfect conditions such as ambient ones.” “Thanks to the development of INVERPUR/R,” emphasises the Modenese company, whose headquarters are located just a stone’s throw from the A22 motorway exit, a genuine gateway to Europe, “we were able to increase production capacity without integrating a drying oven, doubling shifts, or expanding our production space. We appreciated the professionalism of Inver’s team in its consultancy service and its willingness to carry out the many tests we needed. We chose this supplier because of its large corporate structure that ensures an average daily production of 80,000 kg of paint, but we would like to underline that we have never received a negative response even when we ordered just a few cans of a tint. Lastly, the fact that it stores in its warehouse the equivalent of the volume of paints we need for one and a half months’ work is also indicative of our two-way, consolidated relationship of trust.”
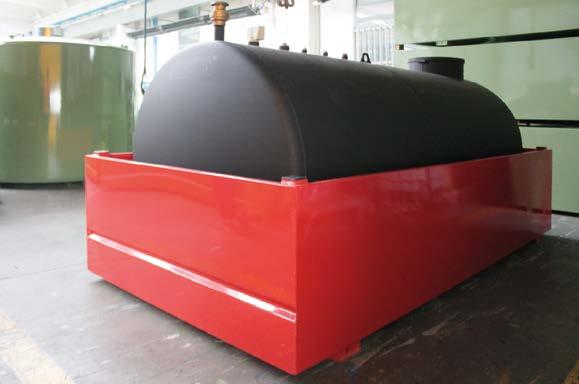
Emiliana green is the most used tint.
© Emiliana Serbatoi
Conclusions
“INVERPUR/R’s development,” explains Cesare Bonora, the GI Italy area manager of Sherwin-Williams, “started in 2019 to respond to the market’s needs for optimisation of coating times and processes following the switch from faster-drying solvent-based paints to waterbased ones. Indeed, the limitation of this technology lied in its drying time. Our R&D laboratory set out to researching new water-soluble, acrylic resins to develop this product, which, after being industrialised, has found one of its most successful applications in Emiliana Serbatoi. We have overcome one of the most difficult challenges: to create a top coat that, even in less than perfect ambient temperatures, guarantees drying characteristics comparable to those of conventional technology. Objective achieved!”

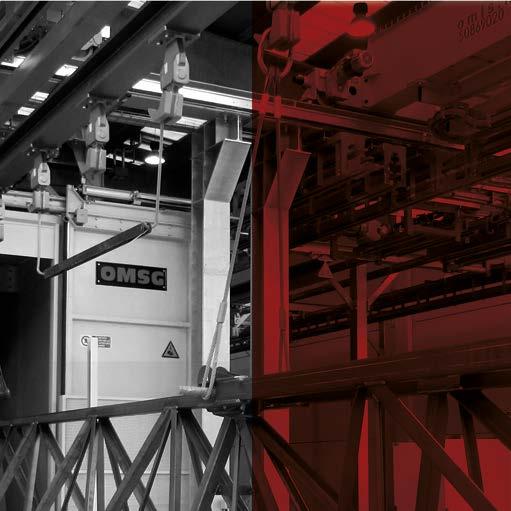
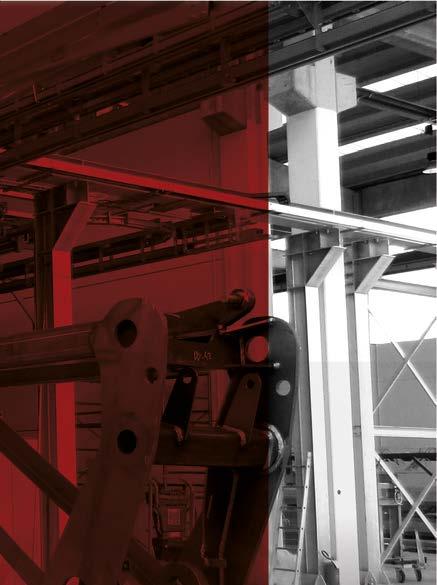
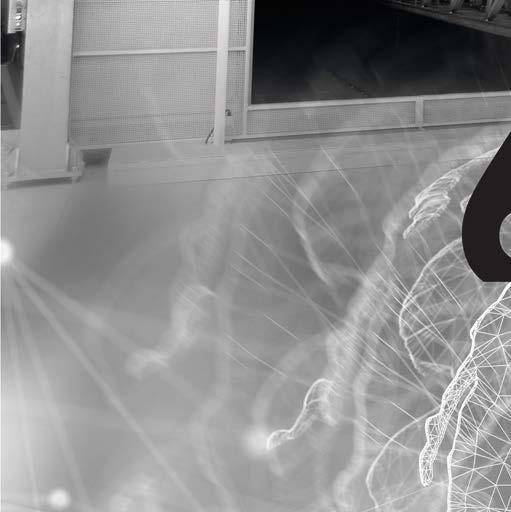
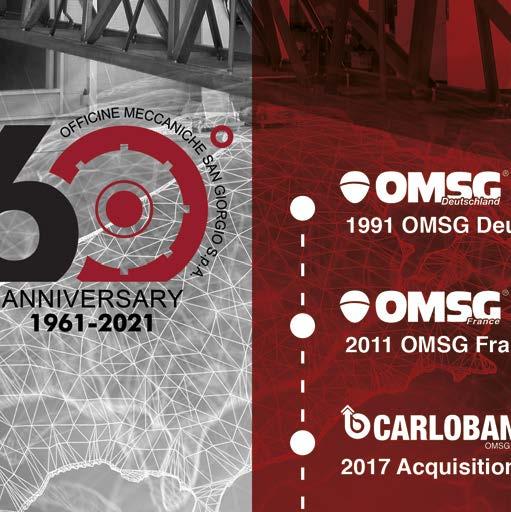
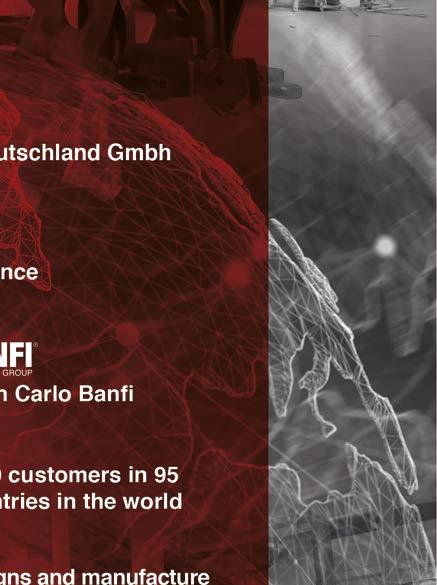

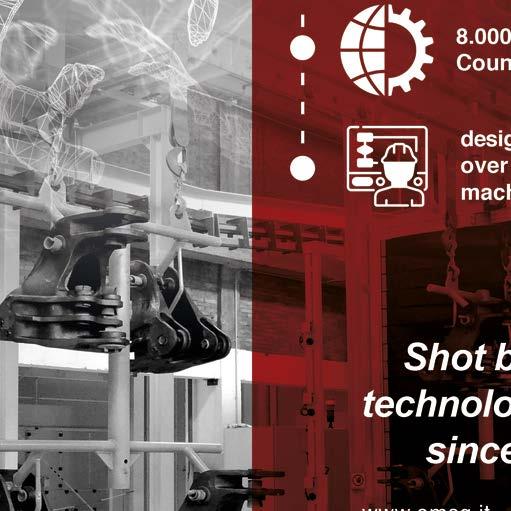
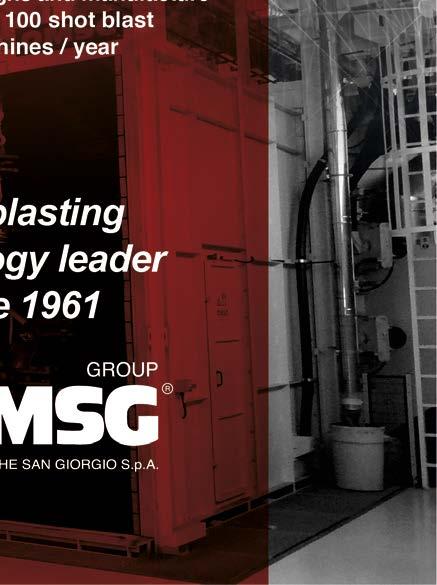
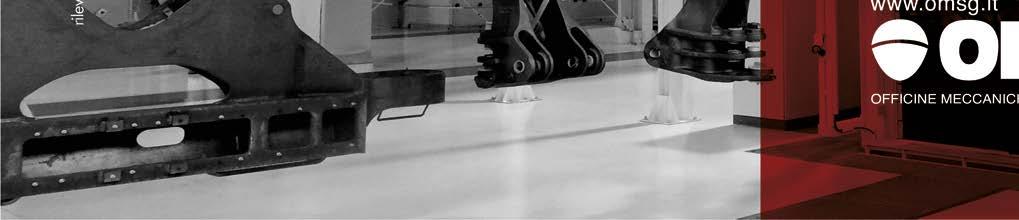