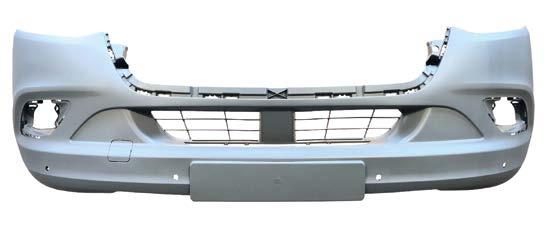
10 minute read
HIGHLIGHT OF THE MONTH
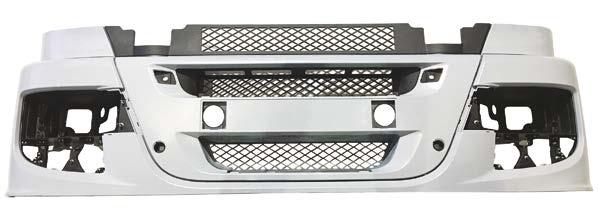

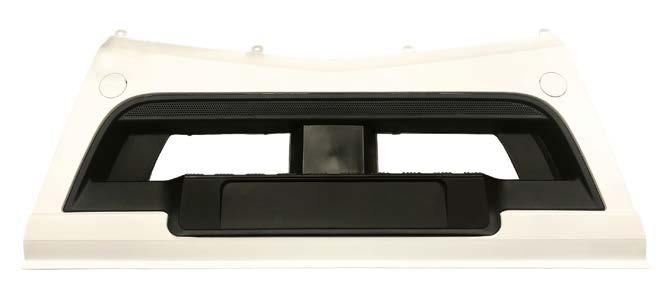
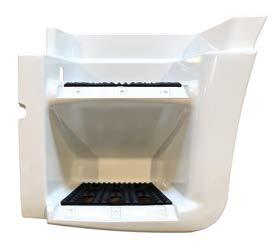
Bumpers manufactured by Poliplast Srl (Albiate, province of Monza e Brianza, Italy).
FOCUS ON TECHNOLOGY
SPECIAL ISSUE ON ACE & OFF ROAD VEHICLES
User-Friendly, Self-Learning Robot Programming Simplifies Production Management for Real-Time Delivery of Automotive Spare Parts
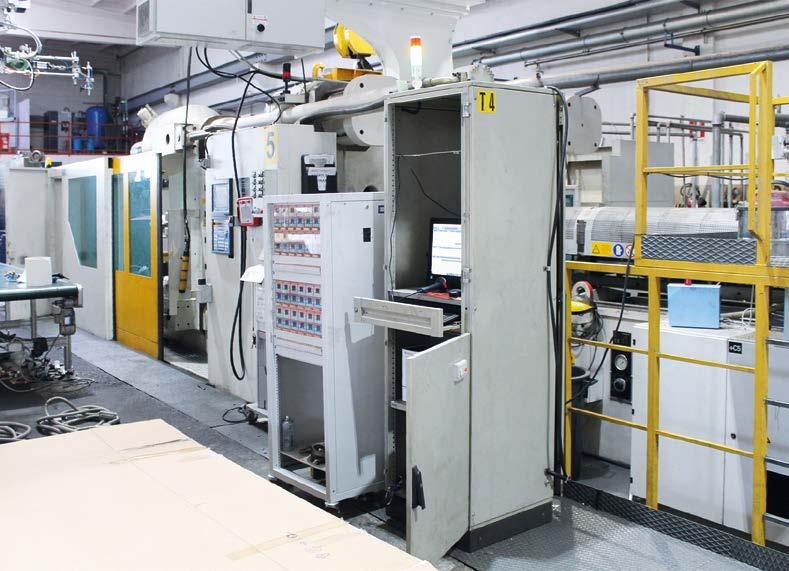
Monica Fumagalli ipcm®
Poliplast, a long-standing company in the field of plastic parts for commercial and industrial vehicles, has equipped its flame hardening and coating stations with three Lesta robots capable of guaranteeing fast application and optimum performance. This is a strategic aspect in production environments characterised by the constant need to replenish aftermarket companies’ stocks.
In the aftermarket industry, characterised by huge quantities of products and fluctuating, intermittent demand, careful stock management is crucial. Generally, it is achieved by optimising production flows through plant engineering and IT solutions aimed at simplifying every process stage, in order to respond quickly and flexibly to customers’ real-time delivery requests. Poliplast Srl (Albiate, Monza e Brianza, Italy) is a long-standing company that has been active in the automotive aftermarket sector for over fifty years. “We have been producing plastic parts for commercial and industrial vehicle bodies since 1969,” states Alessandro Pozzoli, the production manager and a member of the third generation of the family at the helm of the company. “We started out manufacturing metal bumpers. Then, we switched to processing a more malleable material, that is, polyurethane, although our production process was still much more complex than the current one, which involves injection moulding polypropylene.” Today, Poliplast offers a very extensive spare parts catalogue, ranging from bumpers to corner protectors, from grilles to body mouldings and cross beams, from rearview mirrors to wings, from deflectors to headlights. “We have six manufacturing lines with different dimensions, which allow us to produce range from components that are a few centimetres large up to 2-metre long bumpers for industrial vehicles”. Investment in new production technologies has always characterised the history of this company, committed to pursuing production quality and environmental sustainability. “With the aim of improving the management of our production flow, machine ergonomics, product quality, and, last but not least, the environmental impact of our processes, we have been collaborating for about a year with Lesta Srl (Dairago, Milan, Italy), which specialises in the design and production of automated systems for plastic, metal, and wood coating and its related programming software packages.”
Restocking management
Poliplast carries out its entire production cycle in-house. As Pozzoli points out, “The development process of a new product starts from reverse engineering, which allows us to faithfully reproduce the 3D geometry of the sample by scanning it. The drawing obtained will be the basis for the mould design phase”.
© ipcm
© ipcm
For its automotive spare parts, Poliplast uses moulds ranging from 1000 kg to 30 tonnes in weight.
A detail of the moulding department.
At Poliplast, production management is organised on a weekly basis. “We make reorders based on the customer orders of the last two months. It is a complex sector characterized by fluctuating demand that we are able to manage thanks to a constant optimization of production processes. An essential aspect of our industry is in fact the speed of deliveries and, consequently, of restocking, optimized by real-time control of the entire production flow, starting with the supply of raw materials and components necessary for the processing of our products”. The production structure
During the weekly programming phase, the main objective is to organize the production sequence trying to limit the setup times as much as possible between one process and the next one, so as to be able to restore stocks more quickly and flexibly. The production department in Albiate is equipped with four injection moulding machines of different sizes, with clamping forces of 14,000, 18,000, 20,000, and 23,000 tonnes and capable of handling moulds with a weight from 1,000 kg to 30 tonnes.
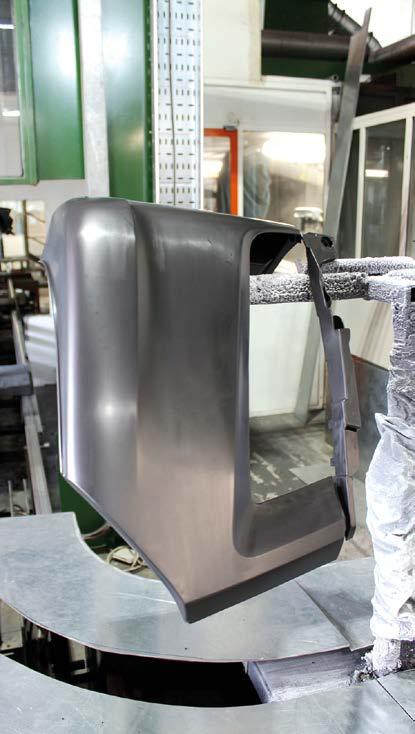

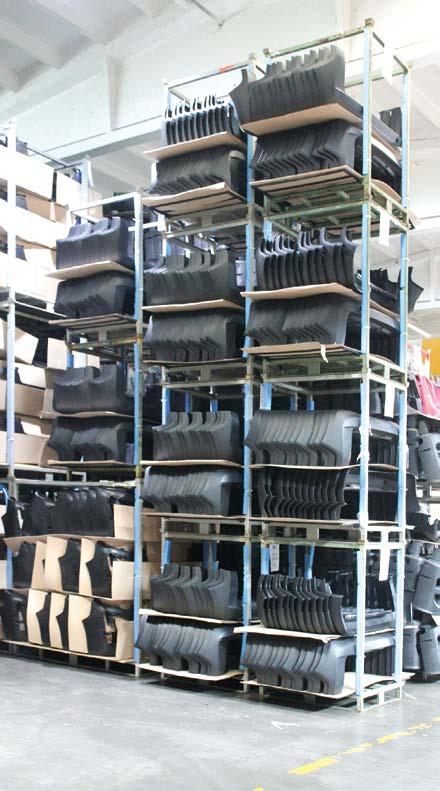

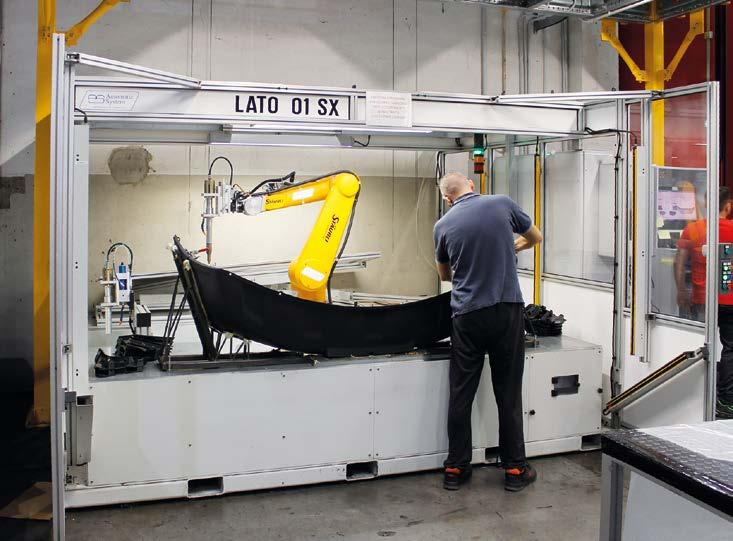
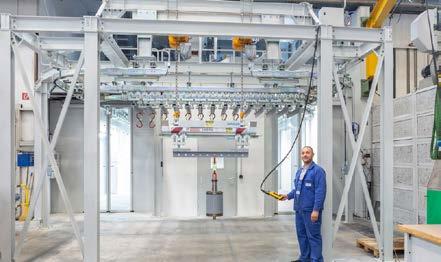
© ipcm
From top left clockwise:
A plastic bumper after the moulding stage.
The semi-finished products warehouse.
Ultrasonic assembly in the robot station.
© ipcm
The inverted conveyor.
“In order not to compromise the effectiveness of the moulding operation,” explains Pozzoli, “each machine must have sufficient clamping force to keep the mould closed to counteract the plastic’s pressure that develops inside it.” After moulding, the parts that do not require further processing are unloaded from the machines and sent to the warehouse. On the other hand, the components that have to be sent to the assembly and coating departments are stored in the semifinished products warehouse to be picked up later. Ultrasonic assembly takes place in three stations, of which two are manual and one robotic. The parts to be painted, where required, are first masked to protect the areas that do not need to be painted, and then loaded onto the inverted conveyor that takes them to the three robot stations
© ipcm
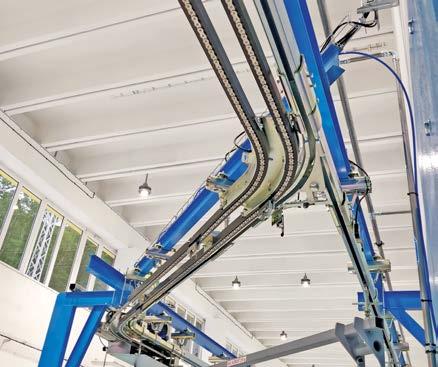
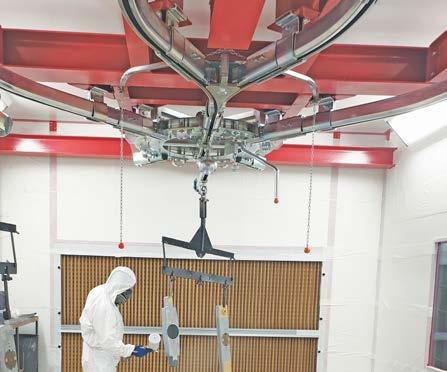
A component waiting to enter the flame hardening station.
– one for flame hardening and the other two for coating – and to a conventional hot-air oven for drying. “Flame hardening and coating are usually the last steps in order to avoid compromising the coating’s quality due to excessive handling, before packaging and final storage,” notes Pozzoli.
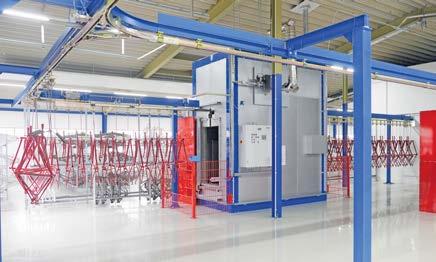
Investing in Lesta self-learning robots
The flame hardening and coating robots and the new paint management unit were among Poliplast’s most recent investments. “This choice was motivated by the need to replace our previous robots, which were still working but outdated, with latest-generation systems that could simplify our operators’ work, being lighter, more manageable and, above all, user-friendly.” “We installed three robots from our LEBOT MV A6
series, one for flame hardening and the other two for coating,” indicates Lesta technical sales expert Luca Ghidoni. “They are 6-axis self-learning articulated robots with a wrist capacity of 4 kg, ± 3 mm repeatability, and maximum speed of 1,000 mm/s. They can record their axes’ movements in real time and reproduce them automatically. Their arms are made of aluminium to offer greater ease of use, thanks to the lightweight and robustness characteristics of this material. Their movements are balanced by a compressedair hydraulic system that guarantees the least possible friction and smooth, unrestricted operations. The special feature of these robots is their flexibility: they can be placed in different workstations and they can apply both liquid, as in this case, and powder coatings on the most diverse materials.” Programming the application phase in an easy way

After flame hardening, the coating phase involves the application of a finish, in most cases white; besides it, the other colours used are black and seven different grey hues. “The two robots work simultaneously on the same component,” explains Pozzoli. “We deal with non-uniform surfaces, but we still need to perfectly cover all the internal and external areas of each workpiece: this is why the conveyor spindle rotates the parts as they pass from one robot to the next. “One of the most appreciated aspects by our operators is the ease of programming the robots: an operator grabs the joystick and follows the contours of the workpiece, while another operator manages the movement sequence from the control PLC. This is very simple: the operator presses the “start” button, performs the movement to be


The Lesta robots during finish application.
© ipcm
The flame hardening robot.
© ipcm © ipcm
The component exiting the drying oven.
repeated by the robot, and presses the “end learning” button to automatically record and save the new programme. All that remains is to check whether the programme thus conceived is adequate or whether there is something to change.”
Optimising consumption for greater sustainability
Poliplast partnered with Lesta with the aim of replacing and updating its equipment, but also with a view to environmental sustainability. “Poliplast has long had an afterburner that minimises emissions in compliance with environmental regulations,” states Pozzoli. “Lesta’s robots have enabled us to optimise paint consumption, thus reducing waste and, consequently, the afterburner’s activity. The integration of Lesta devices will further improve our ability to monitor consumption and will also help us assess more accurately our processing times and coating costs. In this way, we will be able to plan our production cycles with more certainty and precision and manage our warehouse stocks even more effectively.”
GLOBAL SOLUTIONS FOR WATER TREATMENT
with a complete service that includes system design manufacturing installation technical support chemicals
SPRAY BOOTHS WATER SLUDGE REMOVAL RESIN DEMINERALIZATION SYSTEMS REMEDIATION OF CONTAMINATED SITES BIOLOGICAL SYSTEMS BATCH TREATMENTS PHYSICAL-CHEMICAL SYSTEMS ADSORPTION FILTRATION REVERSE OSMOSIS MEMBRANE SYSTEMS EVAPORATORS BIOGAS BIOMASS SYSTEMS OIL SEPARATORS DESANDERS DESALINATION SYSTEMS PYROCHAR OTHER SYSTEMS CHEMICALS
INNOVATIONS: PRESENT&FUTURE
SPECIAL ISSUE ON ACE & OFF ROAD VEHICLES
VIANT – A New and Innovative Technology for Corrosion Protection
Edited by Chemetall
Giussano, Italy cristiano.laurita@basf.com
Conversion coating and primer in just one layer: VIANT is the new solution developed by the Surface Treatment global business unit of BASF’s Coatings division, operating under the Chemetall brand, to increase the coating quality and reduce the carbon footprint of the companies that choose to integrate it in their production processes. It can be applied in various industries, including ACE.
In an economic situation that is fluctuating, uncertain and currently unfavourable for the manufacturing industry in general, and for the surface treatments sector in particular - since coating is one of the most energy-intensive operations in the production system - finding solutions capable of reducing energy consumption is essential. Chemetall, a go-to expert when it comes to the pre-treatment of metal surfaces, has introduced VIANT, a new process that combines conversion coating and primer in just one layer for the corrosion protection of steel in various industries, as for example Agriculture, Construction and Earth Moving (ACE). This solution is easy to operate and enables reliable corrosion protection on edges and inner surfaces. It does not need high voltage, special equipment, or a constant coating temperature for the coating process step. Instead, VIANT can lead to a shorter process chain, resource savings and reduced running costs. Let’s see how.
Energy-saving and environmentally sound process
The new coating technology can offer decisive advantages: at the top of the list are possible cost savings in electricity and simplified processes in various areas. This can be realised by combining pre-treatment and primer in one dip bath where cooling or heating is not required, so that the constant temperature control of the bath is not necessary.
© Chemetall The coating film can directly be applied onto the steel surface. The emerging of the wet coating film is driven by liberating ions from the metal surface rather than applying electricity actively. Due to the wide operating temperature range and a very low bath circulation, the process is very stable, and less electricity is required for powering the smaller circulation pumps. Additionally, you may turn off bath circulation between shifts without harming the coating chemical. Besides the savings in electricity, in water and chemical consumption, also the amount of wastewater requiring treatment can be reduced. This all is possible due to the lack of a dedicated conversion layer. All in all, the VIANT process is characterised by a better environmental balance compared to conventional technologies.
Interesting for many industries
Besides for the ACE industry, where the coating of inside surfaces with the same coating thickness and the same protection level as outside is a possible advantage, VIANT can be suitable for many fields
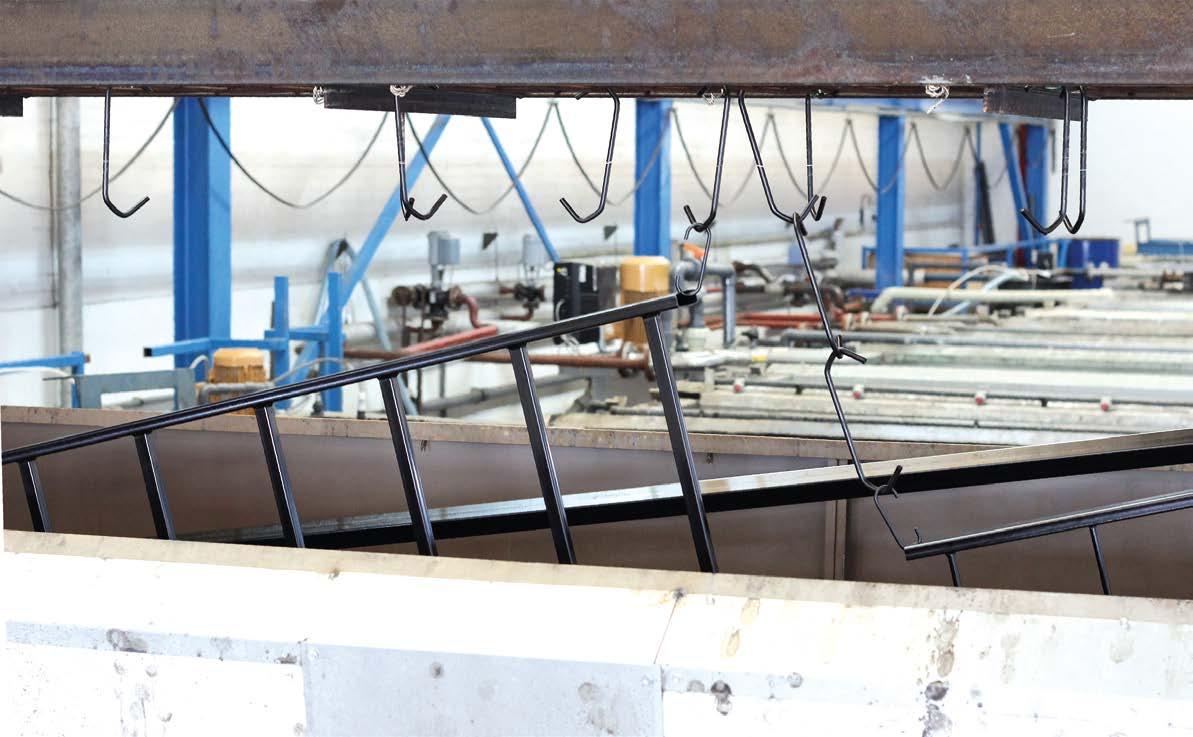
VIANT is the new process developed by Chemetall: it combines conversion coating and primer in just one layer for the corrosion protection of steel in various industries (opening photo). VIANT combines pre-treatment and coating in one dip bath where cooling or heating is not really required, so that the constant temperature control of the bath is virtually no longer necessary.
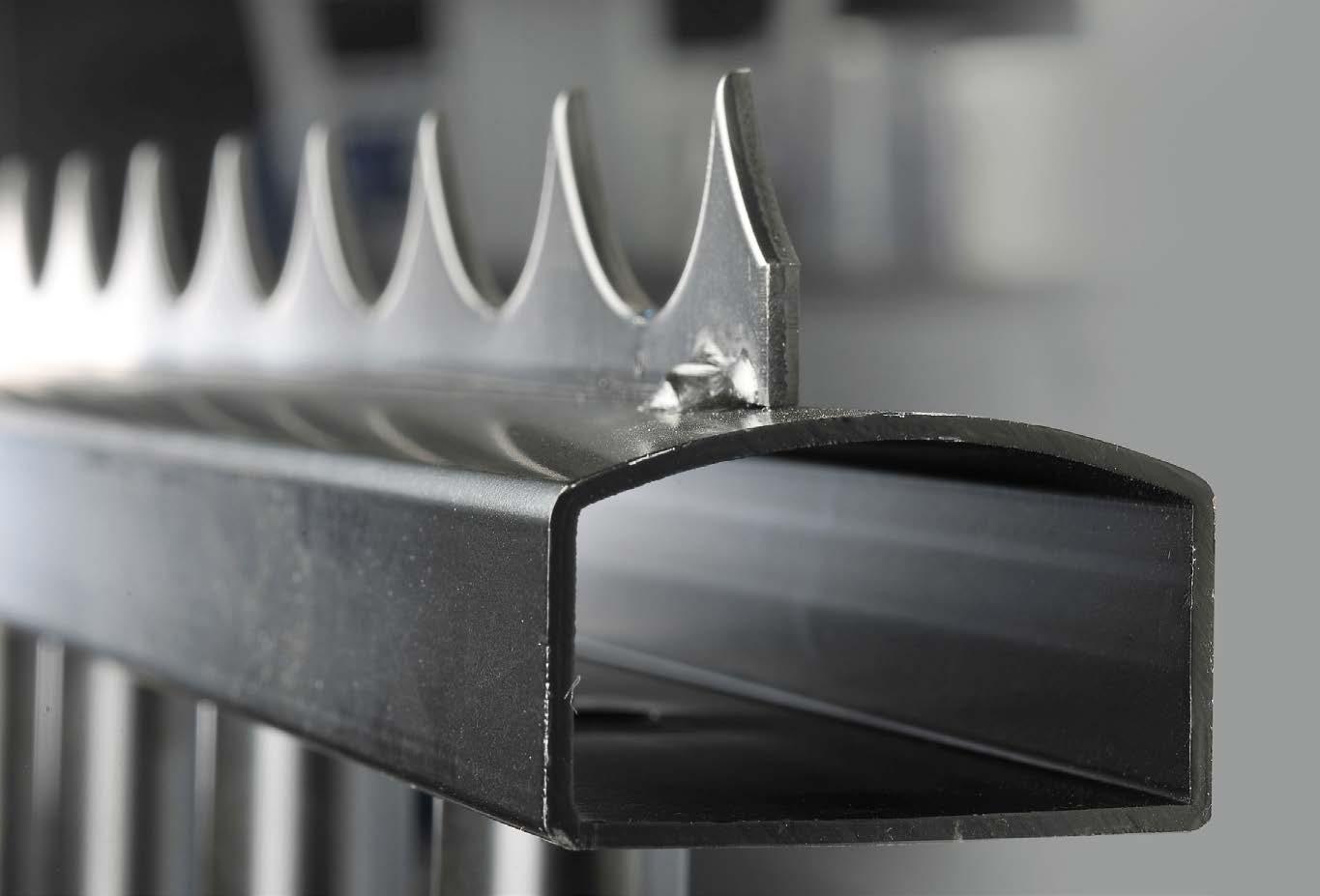