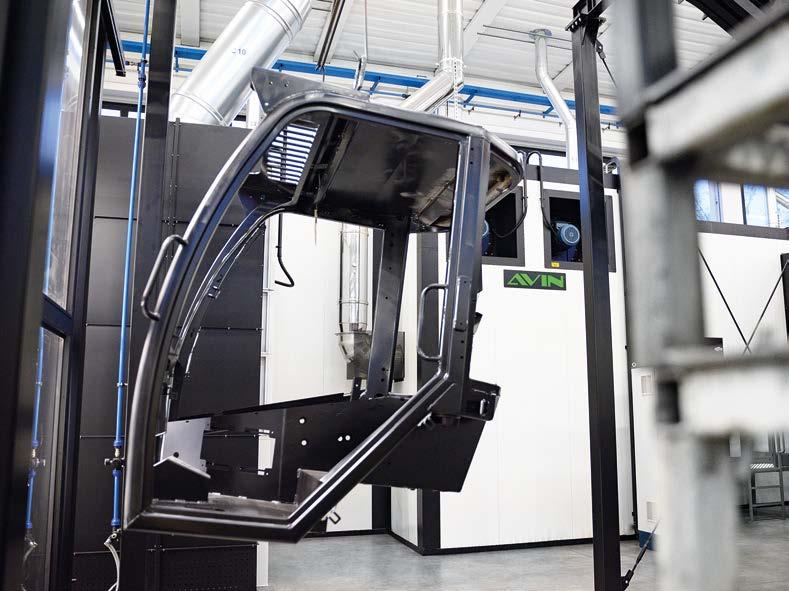
3 minute read
BUSINESS CARDS
© Riccardo Sottoriva
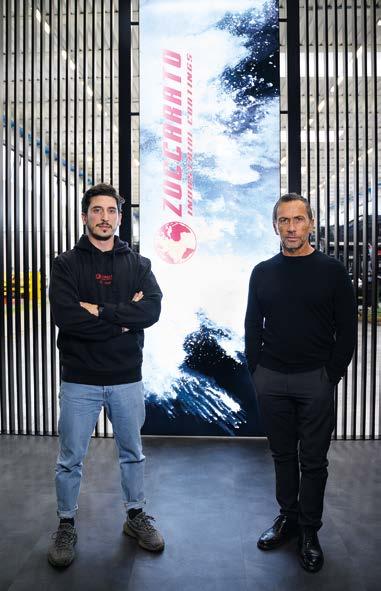
The new line has enabled Zoccarato to increase its production rates in terms of top coat application.
© Riccardo Sottoriva
From left, Vittorio and Alessio Zoccarato.
The products are then transferred to the cataphoresis tank, with a capacity of 70 m3, where they remain submerged for 6 minutes while a patented system eliminates any air bubbles that might remain in the underroofs of the components. Cataphoretic coating is then followed by two cleaning stages and baking at 190 °C in a drying oven with vertically opening automatic doors.
Coating over 1,100 cabins per week
Zoccarato’s evolution has always been characterised by investments aimed at increasing production rates, expanding the company’s offer, improving the quality of its services, and optimising internal processes. While the use of the best technologies guarantees high functional and aesthetic properties, however, these also require constant monitoring. “Avin had already maintained and upgraded our other plants several times, so we were perfectly aware of its professionalism and availability. The decision came naturally to rely on this partner once again and the results were not long in coming: in the first month after the line’s startup, we painted 800 cabins and today we are able to treat 1,100 cabins per week on one shift. And the plant is also structured for a further increase in production volumes or for two-shift production, as is already the case with the other lines,” concludes Alessio Zoccarato with great satisfaction.

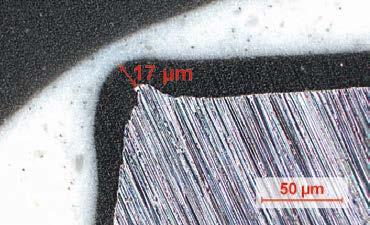

FOCUS ON TECHNOLOGY
SPECIAL ISSUE ON ACE & OFF ROAD VEHICLES
Balfor Revolutionised Its Entire Production Flow with a New Cartesian Powder Coating System
Gabriele Lazzari ipcm®
Thanks to the installation of a new Cartesian manual powder coating plant with an automatic parts transfer system built by Eurotherm, Balfor is now able to carry out painting cycles tailored to each one of its parts. It has thus optimised its entire production flow and increased the volume of its coated batches, while at the same time decreasing work shifts and consumption.

The recent increase in global firewood consumption, which stands at around 1.9 billion cubic metres according to research published by the Food and Agriculture Organisation of the United Nations (FAO)1, has also generated a spike in demand for both industrial and domestic wood-cutting machinery and equipment.
1 https://agriculture.ec.europa.eu/data-and-analysis/markets/overviews/market-overview-sector_en To cope with the growing demands of the market and optimise the coating process of its firewood cutting machines, Balfor has recently turned to Eurotherm Spa (Volpiano, Turin, Italy), a company specialising in the supply of tailor-made systems for all painting needs. It has thus completely revolutionised its production flow thanks to remote management, which enables it to monitor and adjust the whole coating process, and to the setting up of different stations within the new coating plant, which allows adapting the performed cycles to individual batch requirements and prioritising urgent tasks.
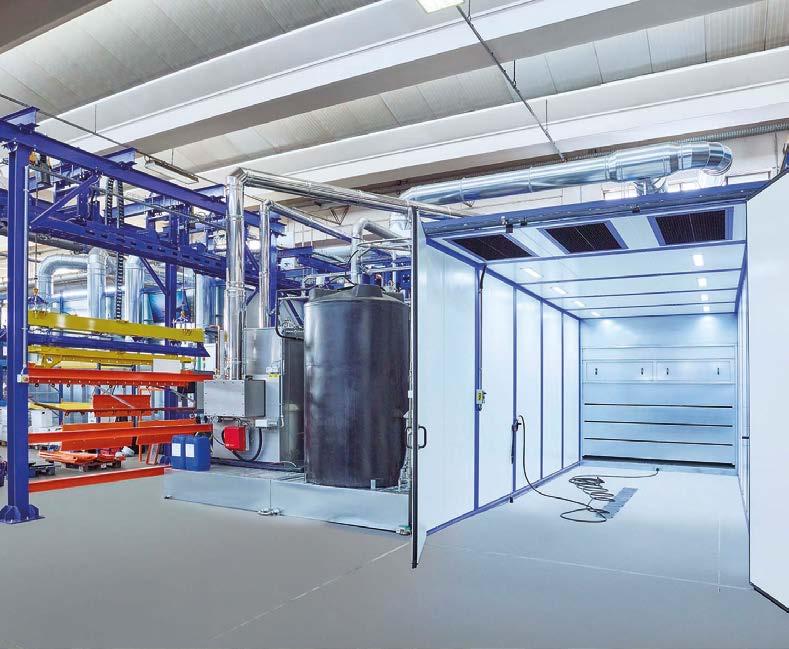

From artisanal production to international expansion
Mario Ballario e Mario Forestello, two craftsmen from Cuneo (Italy) who shared a passion for making wood-cutting tools, established the company as Ballario e Forestello S.r.l in 1979. Headquartered in Manta (in the province of Cuneo), it specialised in the manufacturing of hydraulic piston machinery for firewood processing. The company began expanding its portfolio in the early 1980s to include circular and band saws, providing farmers and lumberjacks with a viable alternative to hand hatchets. Ballario e Forestello’s production also started being exported abroad, thanks to a dealer network that still interfaces directly with customers today to understand their specific needs and devise tailor-made solutions. “Expansion abroad was a big boost to our business’ growth. In 1996, the company moved to a new plant in Verzuolo (Cuneo) to cope with the increasing production flow. It returned to Manta in 2008, when it further expanded its portfolio with large-scale firewood cutting plants and changed its name to Balfor S.r.l.,” recounts Gianluca Ballario, the son of Mario and the firm’s current CEO.
Machinery for the industrial and domestic markets
Balfor’s more than sixty-five employees now produce machinery and equipment used to turn tree trunks into logs for firewood, as well as special components for other agricultural tools.