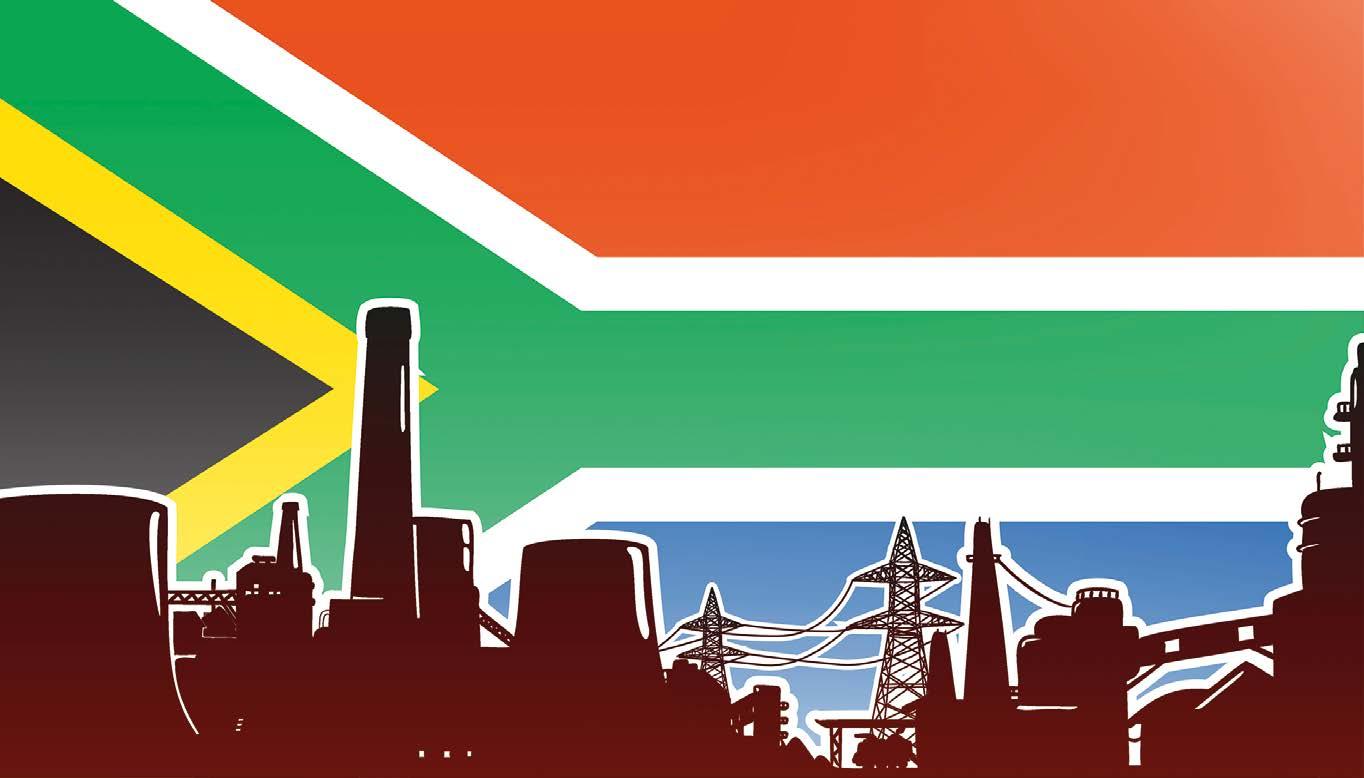
7 minute read
MARKET CLOSE-UP
Corrosion Under COVID-19 in Southern Africa
Greg Combrink
President of CorrISA, Corrosion Institute of Southern Africa, and CEO of Corrosion Hub (Pty) Ltd. gregc@corrosion-lab.co.za
The Market Close Up’s interviews continue with a clear analysis of the corrosion industry’s situation in South Africa, in the light of the health crisis and the current economic issues.
Corrosion is a very diverse issue. In general, it crosses over traditional disciplinary boundaries and influences all aspects of life and industry from the construction and local infrastructure industries, health sciences, biotechnology, agriculture through the electronics and road and sea transport and power generation industries to the more sophisticated industries such as manufacturing, aerospace, petrochemical and nuclear industries in the scientific and engineering aspects thereof. This diversity is also of course, present in Southern Africa. However, the sophistication and elegance of counter measures are often provided at either a very basic level where for instance purely a coat of paint will have a vast effect on the retardation of corrosion or at a higher even more sophisticated level where for instance exotic materials and sophisticated surface treatments are the order of the day to provide the required level of mitigation and prevention. Typically, in the Southern African context preventative measures can generally be classified to be one of or even combinations of the following measures: • Application of organic coatings • Electrochemical in nature (cathodic and anodic protection) • Selection of materials (use of more corrosion resistant materials for specific environments)
© Corrosion Hub © Corrosion Hub
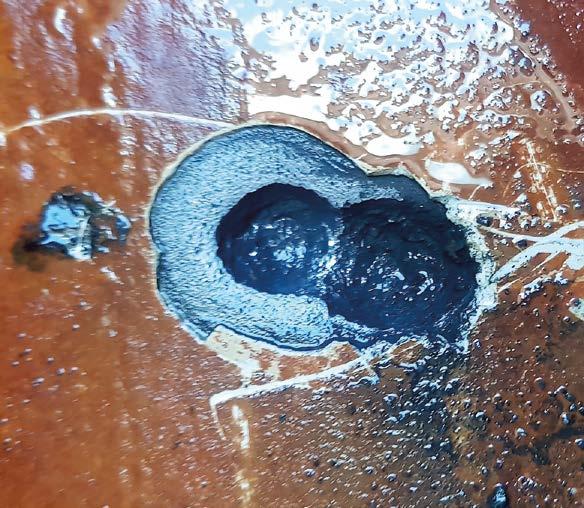
Internal corrosion of a steel pipe in seawater environment.
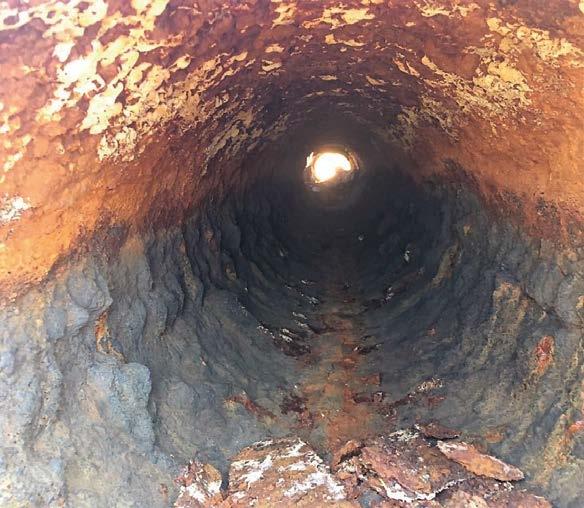
• Use of metallic coatings (cladding, galvanizing, anodizing, sherardizing, other diffusion coatings, thermal sprayed, CVD and PVD to name a few) • Use of inhibitor technology (water treatment, modifying the environment, Vapour-phase Corrosion Inhibitors (VpCI)) • Design against corrosion (water shedding structures and selfcleaning structures and also plant operation processes). In many cases in Southern Africa the first port of call is using organic coatings where a wide variety of options exist some manufactured locally and others sourced from foreign sources. Often this is coupled with supplementary preventative mechanisms. Thus, one may find that an at-risk object is protected firstly by a suitable organic coating system that is supplemented by the use of Vapour Phase Corrosion Inhibitors. Corrosion is driven by thermodynamics and given enough time and exposure most metals will indeed interact with their environment chemically resulting in loss of desired properties. The rate at which this occurs is the domain of the corrosion specialist engineers and scientists and most of the mitigative measures mentioned above act in a way to retard the rate of corrosion reactions. In the RSA the direct costs of corrosion are estimated to be around 5% of the country’s gross domestic product (GDP) equating to around R260 billion wastage annually. If one considers the indirect cost too this amount easily doubles (if not more) with collateral damage, loss of production, increased insurance costs being significant contributors to the indirect costs. Furthermore, damage to the environment
Microbiologically influenced corrosion (MIC) in Circ Piping 11 seawater cooling system power plant.
because of product leakages due to corrosion can take decades to completely rehabilitate. Because of the complex nature of corrosion mechanisms where oft times several mechanisms may be occurring at the same time and in fact one mechanism can result in the establishment and acceleration of a secondary mechanism, it is imperative that the mechanisms are clearly understood and also how they are interdependent so that the root cause of the problem can be addressed as opposed to only the symptoms. Thus, education is of paramount importance to the Southern African industry. To this end the 61-year-old Corrosion Institute of Southern Africa has an array of courses aimed at not just increasing awareness but also training engineers, scientists, technicians, technologists and applicators how to recognize corrosion and its underlying causes and how to take appropriate action to mitigate and prevent reoccurrence thereof. In early 2020 Southern Africa along with the rest of the world was caught unawares to how life in general and also our industries would change. In the words of Neil Young “Rust never sleeps” and this is indeed true when the literal meaning is taken and the fight against it is one of keeping a constant wary eye out for signs of its occurrence followed by a rapid addressing of the problem whilst it is still a small one. This requires constant vigilance and a constant laborious intervention, however the new rapidly introduced COVID-19 protocols restricting our movement and physical interaction resulted in less people actually physically being at their place of work with many jobs being changed from ones requiring actual site attendance
© Corrosion Hub © Corrosion Hub
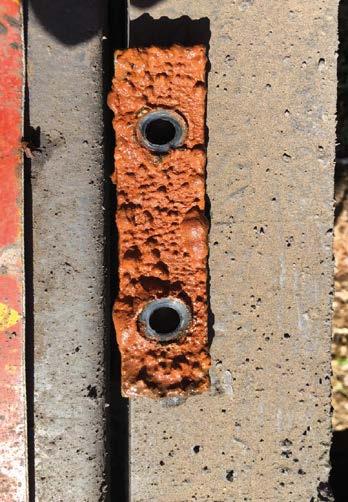
Corrosion coupons after exposure inside a raw fresh water pipeline for 12 months. Closer view of a corrosion coupon exposed in raw fresh water for 12 months.

to ones where people worked remotely from home. This has resulted in a huge upheaval in addressing corrosion matters and how we in the corrosion industry should do business. In many cases maintenance including addressing issues of corrosion have been put on the back burner in the interests of reducing the risk of people contracting COVID-19. The effect of this reduced maintenance will in many cases not be immediately felt but will rather take several years to manifest especially if a catch-up process is not implemented at the first available opportunity. But this will still be more costly than had the issues been addressed at the early stages of development. Another negative development has been the rapid and exorbitant increase in costs. Manufacturers have in most sectors seen huge increases in commodity prices resulting in massive increases in costs for produced goods. In some cases, prices have increased by more than 200%. COVID-19 has had a domino effect on prices. Higher manpower and other input costs are being experienced at every stage of manufacturing and supply as production costs have increased significantly. Worldwide production rates are at a low and shortages are the order of the day. These shortages have also contributed to slower production in Southern Africa as items and commodities (such as steel) needed for manufacturing of finished goods are just not available in the quantities needed. Another contributor to the issue of slower production (and subsequently higher input costs) is shipping (especially by air freight) that is now provided at extremely high premiums and shipping is slower as transportation opportunities to the Southern African subcontinent are a lot less than before. This is especially the case in the RSA due to additional restrictions being applied by our trading partners due to the very real fear of contracting the “South African Strain” of COVID-19. As a result, only a very limited number of carriers service the Southern African region and, in most cases, items shipped from some countries are firstly unloaded at intermediate ports before being transferred to a carrier that flies to the RSA. After the first wave, many South African industries implemented different strategies to continue to operate in a competitive way and many thousands of jobs were shed or redefined as “work-fromhome” positions. This of course raises the question of whether staff can work productively at home for the specific job they are doing. From a pro point of view working from home means less traveling, less expenses for the company for rentals and related costs, also the work environment for some people at least, is a more relaxed environment but on the opposite side the cons also appear. Are the staff as productive as they need to be, is the home environment not perhaps a distraction and of course one can’t in many cases just pop down to the warehouse to check if the inventory shown on the system is correct etc. Thus COVID-19 protocols have resulted in a new working dispensation for many jobs that can be converted to one that can be performed remotely. It will of course evolve to encompass more and more tasks as the AI (Artificial Intelligence) and IoT (Internet of Things) develops, however at this stage fighting corrosion has not yet reached that level where it can
in most cases be performed remotely. It is also at this stage unlikely that coating applicators will be replaced within the next five years by machines. However, with the ingenuity of man to create things to make life easier, it is not an unthinkable thing to foresee that thereafter many aspects that can be performed by machines which in turn can be deployed remotely will indeed be performed by such machines. In my opinion the lockdown due to COVID-19 has hastened the rate of changeover for remote deployment of machines and the use of the IoT.

I predict that in the short term a 5-to-10-year transition period will prevail but very soon driven by technology, even the corrosion industry will enter the 4th industrial revolution with much AI becoming more and more part of life in the South African corrosion industry. ‹
© Corrosion Hub
A mousehole in anodized aluminium after 25 years service.
