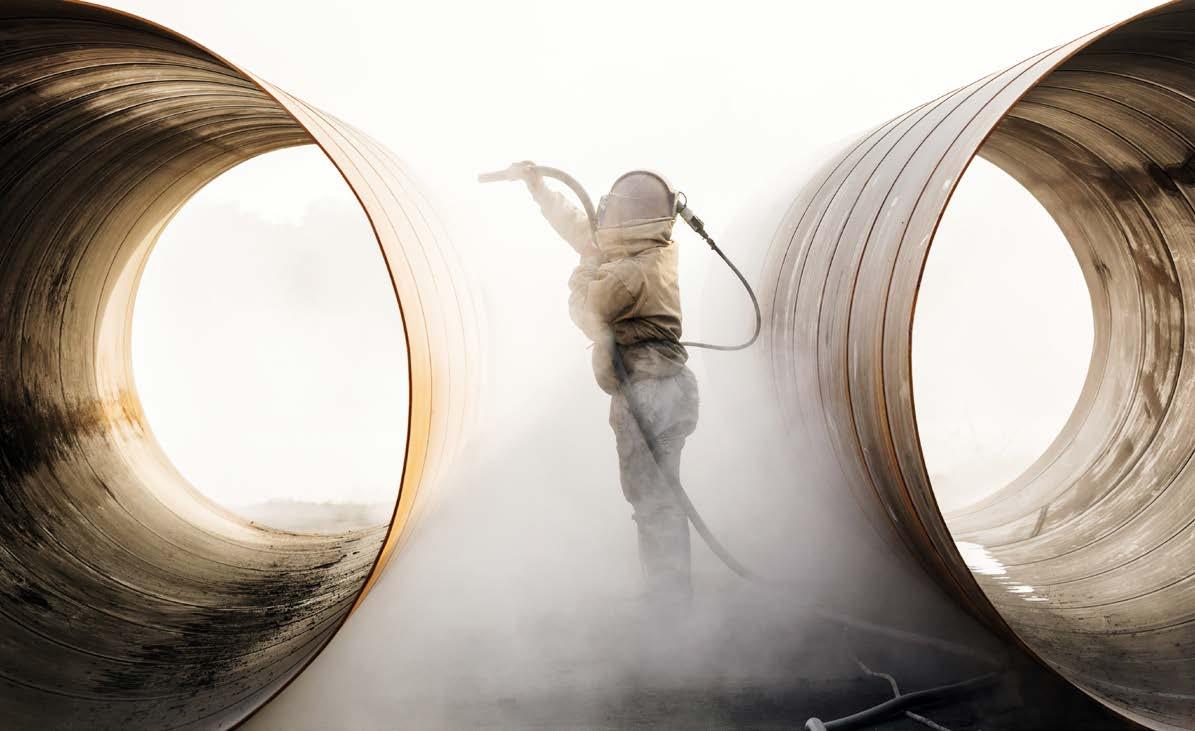
7 minute read
INSPECTION LOGBOOK
© Adobe Stock
Coating Inspections - Inspection of Steel Surface Preparation, Part 3
Massimo Cornago
NACE International Certified Coating Inspector, NACE CIP PEER Reviewer cornago@ipcm.it
As mentioned in our previous article1, we will now discuss other surface preparation systems and their related inspections to be carried out during the works themselves, starting with the inspection of hand tool and power tool cleaning operations based on the appropriate standards.
Initial steel conditions
The amount of time, work, and effort required to achieve any particular degree of surface preparation largely depends on the initial conditions of the surface to be cleaned. It is necessary to take into consideration the amount of “rust”, “old paint”, “contamination”, and “active corrosion” or “pitting” traces on the surface to be protected. Although many different initial conditions can be found, SSPC has divided them into four construction conditions based on the rust grade classification of SSPC-Vis 1 “Visual Standard for Abrasive Blast Cleaned Steel” and three maintenance conditions based on SSPC-Vis 3 “Visual Standard for Power- and Hand-Tool Cleaned Steel” for already painted surfaces.
Inspection of hand and power tools
Hand cleaning tools include wire brushes, non-woven abrasive pads, scrapers, chisels, knives, and chipping hammers. When hand tool cleaning is included in the project specifications, the Coating Inspector
1 https://www.ipcm.it/en/open/protective-coatings/2021/37/46-47.aspx. Editor’s note: In this article, we delve into the NACE Standard No. 5/SSPC-SP 12 “Surface Preparation and Cleaning of Metals by Water-Jetting Prior to Recoating”, which has been edited and replaced with the following standards in 2012 and 2017: NACE WJ-1/SSPC-SP WJ-1 Waterjet Cleaning of Metals—Clean to Bare Substrate (WJ-1) NACE WJ-2/SSPC-SP WJ-2 Waterjet Cleaning of Metals—Very Thorough Cleaning (WJ-2) NACE WJ-3/SSPC-SP WJ-3 Waterjet Cleaning of Metals—Thorough Cleaning (WJ-3) NACE WJ-4/SSPC-SP WJ-4 Waterjet Cleaning of Metals—Light Cleaning (WJ-4). However, we chose to do so because the earlier standard is still internationally recognised and used.
should verify that all the tools are clean (completely free of contaminants such as grease and oil) and of the appropriate type, size, and shape to enter the area to be cleaned. Indeed, hand tools should be in such a condition that they can be safely used for effective cleaning operations without gouging the steel surface. Wire brushes with too many lost or bent bristles should be rejected. Scrapers should be sharp and made of tempered tool steel. Chipping hammers should have a blunt edge. Power tools for surface cleaning are classified as impact cleaning tools, rotary cleaning tools, and rotary impact cleaning tools; they may be pneumatic or electric. When power tool cleaning is included in the project specifications, the Coating Inspector should verify that all the tools are appropriate for the substrate and the material to be removed, they are capable of producing the specified finish without driving rust and scale into the surface (e.g. dull tools), and they can be safely and effectively operated in the work space available. Since worker fatigue is often a severe problem during prolonged use of power tools, the operator’s preference may also be a factor in determining the appropriateness of a power tool. The Coating Inspector should verify that the tools used are capable of guaranteeing the required cleanliness level. The manufacturer should be consulted about their recommended operating speed. For power tools that contain abrasive media (i.e. non-woven abrasive, rotary wire brushes and coating abrasive discs or flap wheels), it should be verified that the tool is compatible with the size and speed rating of the abrasive media themselves. For air-driven tools, it should be verified that the air supply is clean, dry, and adequate and that moisture separators and filters on air lines are in place. Air-driven tools should also be properly lubricated and they should contain hoses of the appropriate length and diameter for correct and optimal operation: long lengths of small diameter hoses should be avoided.
Testing for surface cleanliness
The Coating Inspector should verify that the specified level of surface cleanliness is attained. SSPC has developed written and visual standards that are used together to verify the cleanliness degree of surfaces by the non-abrasive blast cleaning methods of “solvent cleaning”, “hand-tool cleaning”, and “power-tool cleaning”. The written standards (SSPC-SP 1, 2, 3, and 11) describe the various degrees of surface cleanliness.
Visual Standard SSPC-Vis 3
The Visual Standard (SSPC-Vis 3) is a book containing colour prints illustrating the various hand and power-tool cleaning results over various rust grades of structural steel. It is intended to supplement the written descriptions. The determination of the initial condition(s) of the steel surface to be cleaned should be done by comparing it to the seven photographs representing the different options as follows: • Condition A: Steel surface completely covered with adherent mill scale; little or no visible rust. • Condition B: Steel surface covered with both mill scale and rust. • Condition C: Steel surface completely covered with rust; little or no pitting visible. • Condition D: Steel surface completely covered with rust; pitting visible. • Condition E: Previously painted steel surface; light coloured paint applied over blast-cleaned surface, paint mostly intact. • Condition F: Previously painted steel surface; zinc-rich paint applied
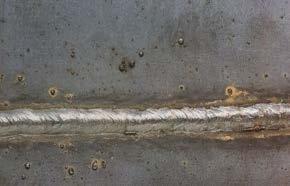
CONDITION A CONDITION B CONDITION C CONDITION D
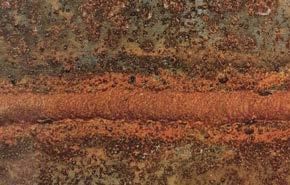
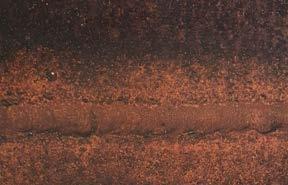
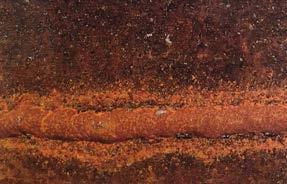
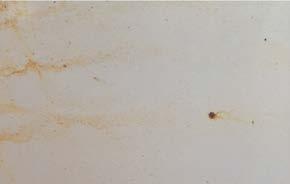
CONDITION E CONDITION F CONDITION G BSP3/SD
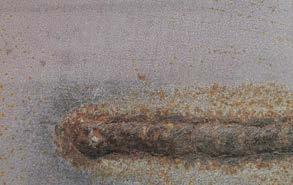
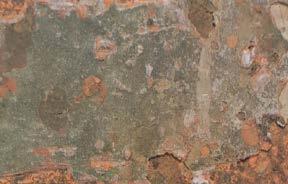
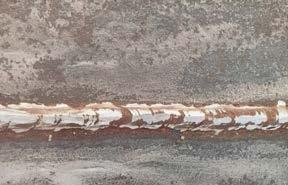
The Visual Standard SSPC-Vis 3’s pictures illustrating the various hand and power-tool cleaning results over various rust grades of structural steel.
over blast-cleaned steel, paint mostly intact. • Condition G: Paint system applied over mill scale bearing steel; system thoroughly weathered, thoroughly blistered, or thoroughly stained.
Immediately prior to painting, one should open the section of SSPC-Vis 3 about the condition determined in the previous step and select the photograph that represents the specified cleanliness level. For SSPC-SP3 and SSPC-SP11, it is also necessary to identify the specific power tool to be used to clean the steel surface.
• SSPC-SP3 Power Tool Cleaning (Power Wire Brush) • SSPC-SP3 Power Tool Cleaning (Sanding Disc) • SSPC-SP3 Power Tool Cleaning (Needle Gun) • SSPC-SP11 Power Tool Cleaning to bare Metal (Needle gun or Rotary Flap) • SSPC-SP11 Power Tool Cleaning to bare Metal (Non-Woven Disk).
Thus, if Rust Grade B steel is to be cleaned to SSPC-SP3 with a sanding disc, the photo to be used is “BSP3/SD”: it should be compared to the cleaned steel to help determine whether it meets the written standard or not. It should also be noted that variations from the photos might occur in the texture, shade, colour, tone, or amount of mill scale or pitting.
Hand tool cleaning (SSPC-SP2)
Hand tool cleaning is a method of preparing surfaces by the use of non-powered hand tools. It removes all loose mill scale, loose rust, loose paint, and loose detrimental foreign matter. It is not intended to remove adherent mill scale, rust, or paint; mill scale, rust, and paint are considered adherent if they cannot be removed by lifting with a dull putty knife.
Power tool cleaning (SSPC-SP-3)
Conventional power tool cleaning is a method of preparing steel surfaces by the use of power-assisted hand tools. Conventional power tool cleaning removes all loose mill scale, loose rust, loose paint, and loose detrimental foreign matter. It is not intended to remove adherent mill scale, rust, or pain; mill scale, rust and paint are considered adherent if they cannot be removed by lifting with a dull putty knife.
Power tool cleaning to bare metal (SSPC-SP11)
This method includes several types of power tools that provide bare metal surfaces. When viewed without magnification, the metal surfaces prepared in compliance with this specification should be free of all visible oil, grease, dirt, dust, mill scale, rust, paint, oxides, corrosion products, and other foreign matter. Slight residues of rust and paint may be left in the lower portion of pits if the original surface is pitted. When painting is specified, the surface shall be roughened to a degree suitable for the specified paint system. The surface profile should not be less than 25 micrometres (in fact, this is the only surface preparation standard to determine a minimal profile level).
In the next article, we will have the opportunity to discuss other surface preparation systems and their related inspections to be conducted during the works themselves. ‹
© Adobe Stock
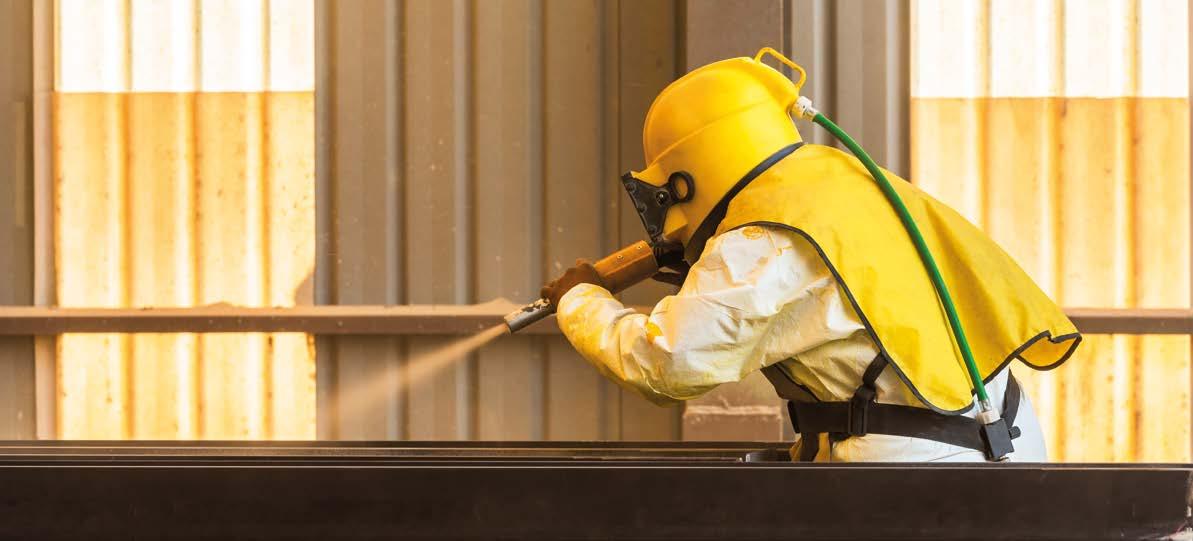