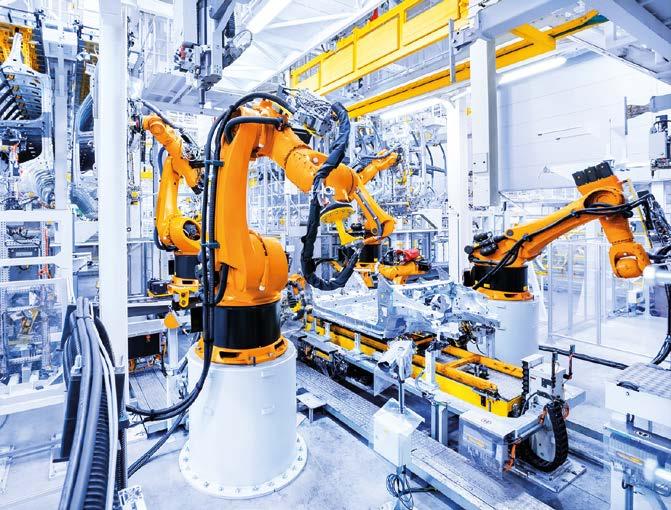
14 minute read
BRAND NEW
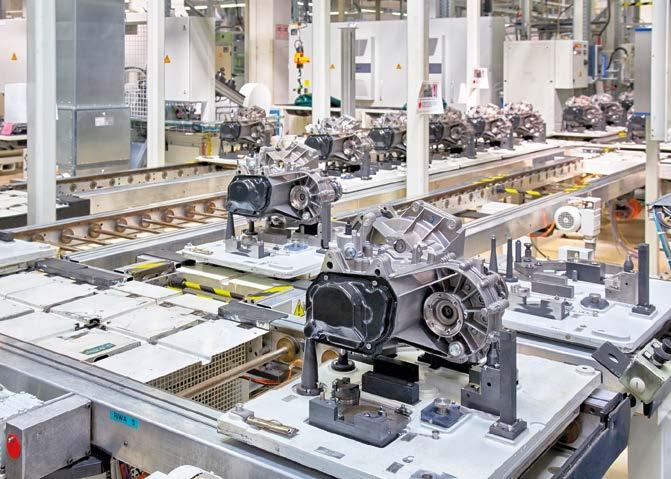
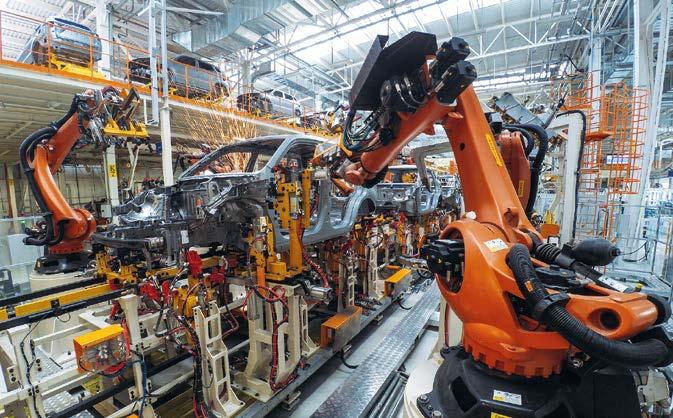
© Cortec
© Cortec
Cortec’s Biobased Rust Preventative VpCI-277 Preserves Metals During Storage and Transport
The new rust preventative launched by Cortec saves time and reduces the use of additional materials.
Cortec has announced that it has recently developed the new ready to use rust preventative VpCI®-277. Specifically designed to preserve metals during storage and transportation, the product combines film-forming additives with Vapour phase Corrosion Inhibitors in order to provide multi-metal corrosion protection. It can provide corrosion protection for up to two years of indoor storage or during shipments when combined with VpCI packaging materials, leaving a dry and non-tacky film on the metal surface. Cortec’s new solution contains a biobased corrosion inhibitor in a non-flammable and low VOC solvent carrier, so it can assist for example automotive manufacturers that need rust preventatives with drier films and low VOCs to meet their solvent-based specifications. The rust preventative VpCI-277 is also suitable for robotic assembly of precision components which require tight tolerances, helping to maintain a clean preservation process through the absence of oily residue. Moreover, it does not contain chlorinated compounds, chromates or nitrites. It can be applied by spray or dip and left on metal parts during further processing or shipment, not requiring removal. Usually, rust preventatives need to be applied and removed several times because the metals risk flash corrosion when sitting in temporary storage. Furthermore, the parts have to be washed before entering the next phase of the manufacturing process. VpCI-277 allows to streamline processes by eliminating steps, improving tact time and reducing the use of additional materials and cost. VpCI®-277 conforms to ASTM D1748 (Humidity), ASTM D1735 (Water Fog), MIL-C-83993 (Water Displacement), and NACE RP0487-2000 (Selection of Rust Preventives) standard test methods.
Sherwin-Williams’ FIRETEX FX6002 To Be Applied on the Y-Towers
The intumescent coating developed by Sherwin-Williams will offer fire protection to Amsterdam’s tallest buildings.
The intumescent coating FIRETEX® FX6002 developed by Sherwin-Williams, winner of the 2021 Queen’s Award for Enterprise: Innovation, has been selected as part of a system that will maximise fire protection for a major residential and hotel development project in northern Amsterdam. The Y-Towers are two 100m-high towers under construction in the Overhoeks district. After completion, expected by 2023, they will become the tallest buildings in the Dutch capital. The tallest one will host the Maritim Hotel Amsterdam, that includes 579 rooms, a Skybar, conference centre and a events space, while the second tower will house almost 300 residential apartments. FIRETEX FX6002 results particularly suitable for this project, as it can be applied off-site and enables operators to transport steelwork in few hours, rather than days. In addition, it can be applied direct to metal without the need for a primer or topcoat in some environments while retaining the highest levels of durability: up to 120 minutes of fire protection and long-term corrosion protection. To increase fire protection, Sherwin-Williams will also provide the epoxy blast primer FIRETEX C69, the methacrylate intumescent coating FIRETEX FX6002 and a topcoat of Acrolon™ 7300 polyurethane. “For the Y Towers project, a just-in-time delivery method requires beams to be delivered after they are coated off-site. This will help to reduce the exposure, backlog and time delays associated with application on-site. Through our partnership with Sherwin-Williams, the FX6002 system can be fully applied at the paint shop and moved on site and installed within one day, enabling the construction to move at a quicker pace with fewer bottlenecks,” stated the General Manager of Maeg Costruzioni SpA Alessio Ortolan, the steel fabricator for the construction works. “As a result, the quick curing of FX6002 should lead to less damage to the steel when moved, as we know beams will be fully cured when lifted on-site.” “This project demanded the highest specification standards for skyscraper buildings. FX6002 is helping fabricators across Europe to offer high-quality passive fire protection, while also reducing bottlenecks and project costs. We are proud to have been involved to ensure the highest level of fire protection measures are in place where the lives of people and safety of property are at stake,” commented Valter Volta, Sherwin-Williams Regional Sales Manager for South East Europe. Sherwin-Williams’ fire protection coatings have been also used in other construction projects in Europe and Asia, such as The Shard and the Leadenhall Building in London, as well as Azerbaijan’s Flame Towers.
For further information:
https://pages.s-w.com/FX6002-gb-en.html
© Sherwin-Williams
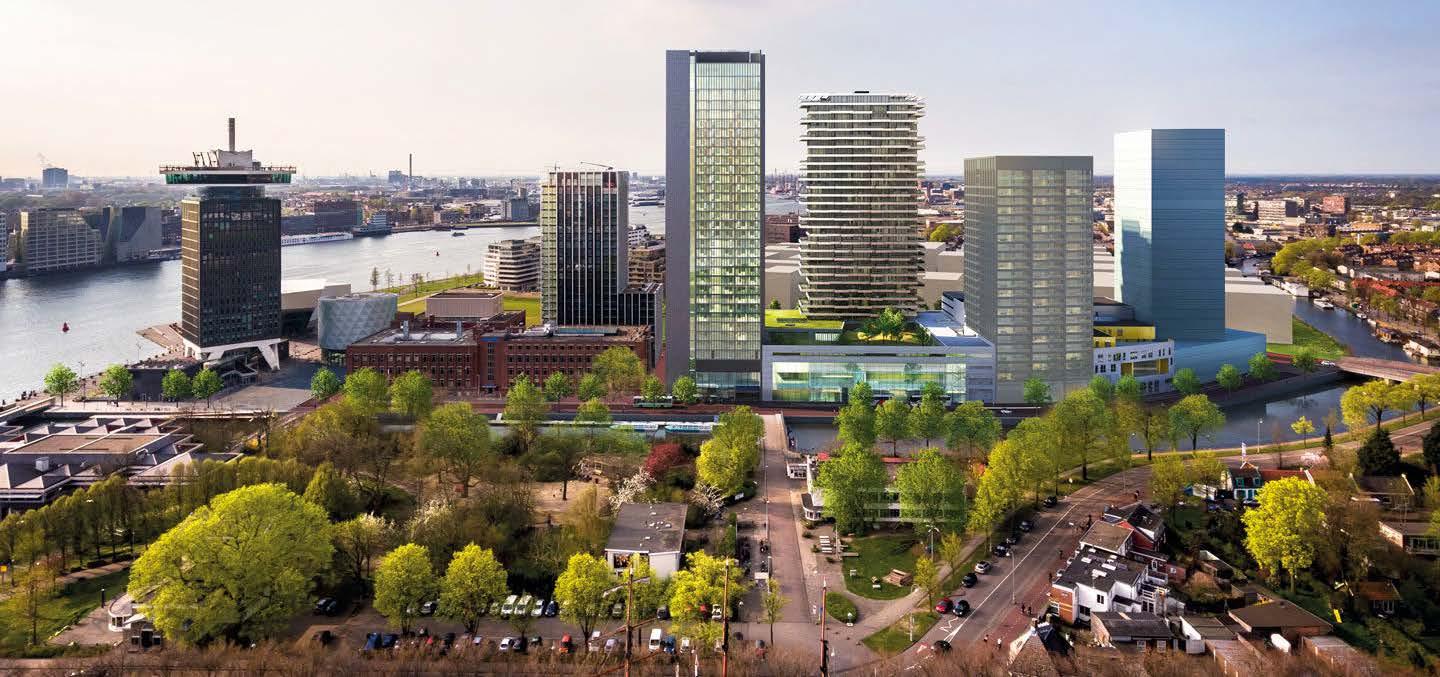
© Matthias_Ibeler
BASF Signs a Wind Power Supply Agreement with Ørsted
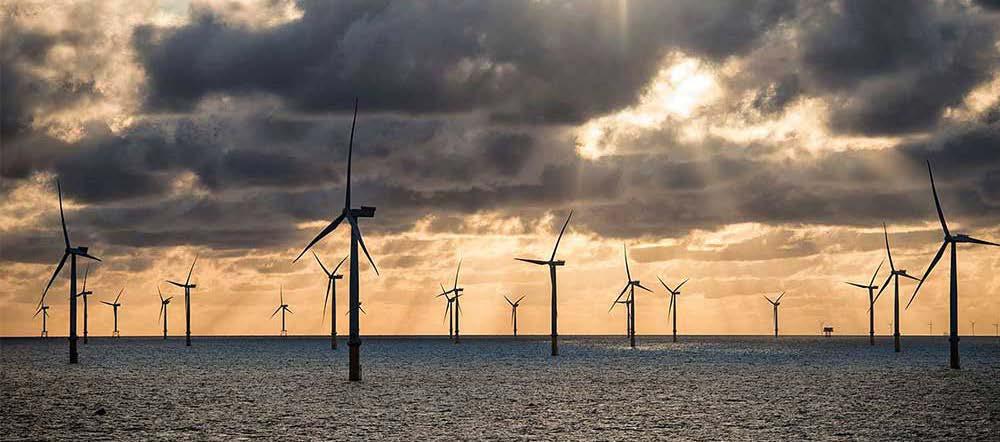
BASF and Ørsted have concluded a 25-year fixed-price corporate power purchase agreement (CPPA), under which BASF will offtake the output of 186 megawatts from Ørsted’s planned Borkum Riffgrund 3 Offshore Wind Farm in the German North Sea.
BASF has signed a power purchase agreement with Ørsted that will help the company cover the increased electricity needs of low-emission technologies. It also represents a step towards BASF’s ambition of becoming carbon neutral by 2050.
“This supply agreement with Ørsted is another important step in securing additional renewable energy for BASF,” says Dr. Martin Brudermüller, Chairman of the Board of Executive Directors of
BASF SE. “BASF wants to reduce its CO2 emissions by 25% by 2030 compared with 2018. To achieve this ambitious goal, we will have to replace large amounts of fossil energy with renewable energy within the coming years. Ørsted can provide the required additional quantities through the construction of new wind farms to support us in our energy transformation.”
Ørsted’s offshore wind farm – for which the company has recently secured planning approval from the German Federal Maritime and
Hydrographic Agency (BSH) – will have a total installed capacity of 900 megawatts and go into full commercial operation in 2025.
As the agreement will run for 25 years, it is the longest CPPA for offshore wind ever announced and an important step in enabling
Ørsted to take final investment decision on Borkum Riffgrund 3, which is expected towards the end of 2021. Borkum Riffgrund 3 was the world’s first large-scale offshore wind farm to be awarded with a zero bid. This was made possible by several cost-drivers, including the installation of next-generation wind turbine technology, very favourable site conditions and high wind speeds, and anticipated revenue-stabilising power purchase agreements with industrial partners such as BASF. “In the common fight against climate change, it’s partners like BASF that will make the difference. The chemical sector has a challenging path towards decarbonisation, but it will also make one of the biggest contributions. For this reason, countries like Germany must respond to the enormous demand for renewable electricity by urgently making more seabed available for offshore wind projects and by increasing its ambitions for deploying large-scale renewable energy sources such as offshore wind power. Offshore wind in the North Sea and the Baltic Sea is an abundant source of green electricity that can be unleashed through clearer and more ambitious policies. With our vision of a world that runs entirely on green energy, we aim to further accelerate the build out of renewable energy and support partners like BASF in realising their climate ambitions”, says Mads Nipper, CEO of Ørsted.
The path towards decarbonisation
BASF is working on scaling up low-emission technologies to industrial dimensions.
On this path, beyond 2030 BASF expects to implement technologies such as CO2-free methods for the production of hydrogen and electrically heated steam crackers, which will significantly increase BASF’s demand for renewable power. Ørsted is also pursuing ambitious decarbonisation goals. More than ten years ago, the company started its own transformation, from being one of the most coal-intensive energy companies to being the most sustainable energy company in the world. Ørsted has the target and plan of becoming carbon-neutral in its energy generation by 2025 and of reaching full value chain decarbonisation by 2040, as the world’s first energy company with scientifically validated plans. By 2030, Ørsted aims to have installed 50 gigawatts of renewable energy capacity. Of this, 30 gigawatts will be offshore wind power.
For further information: www.basf.com
About Ørsted
Ørsted AS (formerly DONG Energy) is a Danish multinational power company based in Fredericia (Denmark) which develops, constructs, and operates offshore and onshore wind farms, solar farms, energy storage facilities, and bioenergy plants. It employs 6,672 people and is the largest energy company in Denmark. The company adopted its current name on 6 November 2017 in honour of the Danish scientist Hans Christian Ørsted who discovered electromagnetism and laid the foundation for the modern generation of electricity, which is at the core of Ørsted’s business. As of 2020, the company is the world’s largest developer of offshore wind power, accounting for 29% of global installed capacity and producing 88% of their energy from renewable sources. With its vision of a world that runs entirely on green energy, the company has a goal of net zero generation by the year 2025 and no carbon emissions by 2040. Ørsted ranks as the world’s most sustainable energy company in Corporate Knights’ 2021 index of the Global 100 most sustainable corporations in the world, and is recognised on the CDP Climate Change A List as a global leader on climate action.
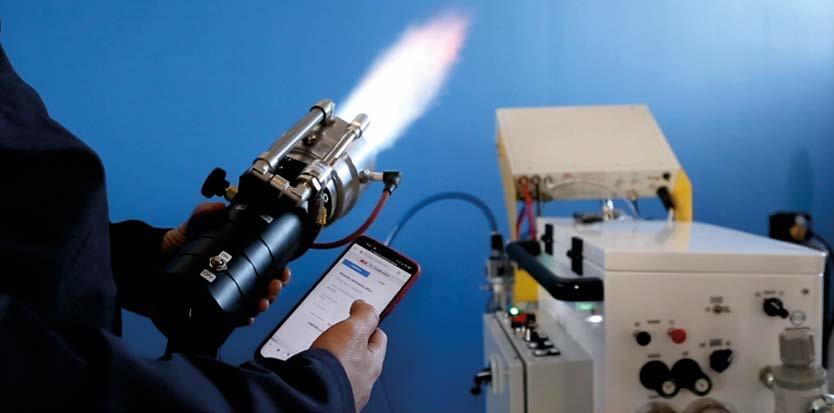
U.S. Government to Fund Corrosion and Biofouling Research for Marine Energy Devices
The Office of Technology Transitions is funding research to optimise non-toxic coatings for control of biofouling and corrosion on marine energy devices and facilities.
The Office of Technology Transitions of the U.S. Department of Energy (DOE) is funding the Pacific Northwest National Laboratory (PNNL) project to scale up, field test, and optimise the non-toxic, durable and convenient coatings for control of biofouling and corrosion on marine energy devices and facilities. The project is based on a patented technology developed by the PNNL, the Superhydrophobic Lubricant Infused Composite (SLIC), which provides antifouling performance and durability while decreasing hydrodynamic drag without involving toxic materials. So, it can help to prevent biofouling of water power civil works in both freshwater and marine environments. The objectives of the research include a final laboratory-based performance test that will measure SLIC’s saltwater-based durability, friction and compatibility with other paint and primer types. Researchers will collaborate with experts from the coatings industry (such as from BioBlend Renewable Resources, Dry Surface Technologies, Prometheus Innovations and Lorama Group, as well as PNNL’s Marine and Coastal Research Laboratory and Taylor Shellfish Farms), in order to co-develop blends of SLIC with solvents, curing agents, binders and pigments to assess tensile strength, shelf life, cure time, and any impact on other performance metrics. The federal funding of $529,000 has been issued through the Technology Commercialization Fund (TCF), a programme aiming at helping national lab-based research and development projects on energy. “President Biden is serious about making sure America corners the clean energy market – and that means we need to work with our nation’s savviest entrepreneurs to fast-track solutions from DOE’s National Labs into commercial-ready technologies”, stated Jennifer Granholm, Secretary of Energy. “These projects will help us deploy game-changing innovations that position us to win the clean energy race, while creating jobs and opportunity across every pocket of the country”.
For further information:
https://www.energy.gov/technologytransitions/
and www.pnnl.gov
© Shutterstock
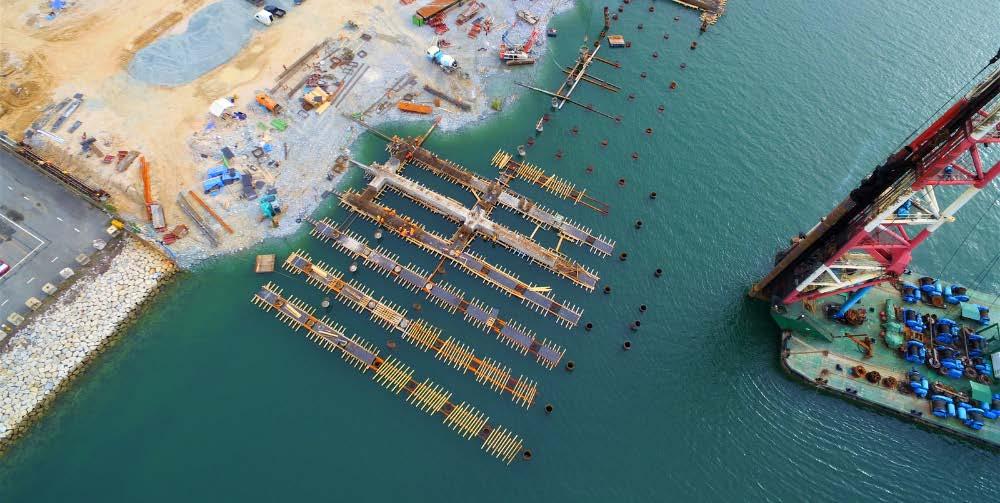
TITANTECH Presents Its New Catalogue of High-performance Anti-corrosion and PFP Coatings
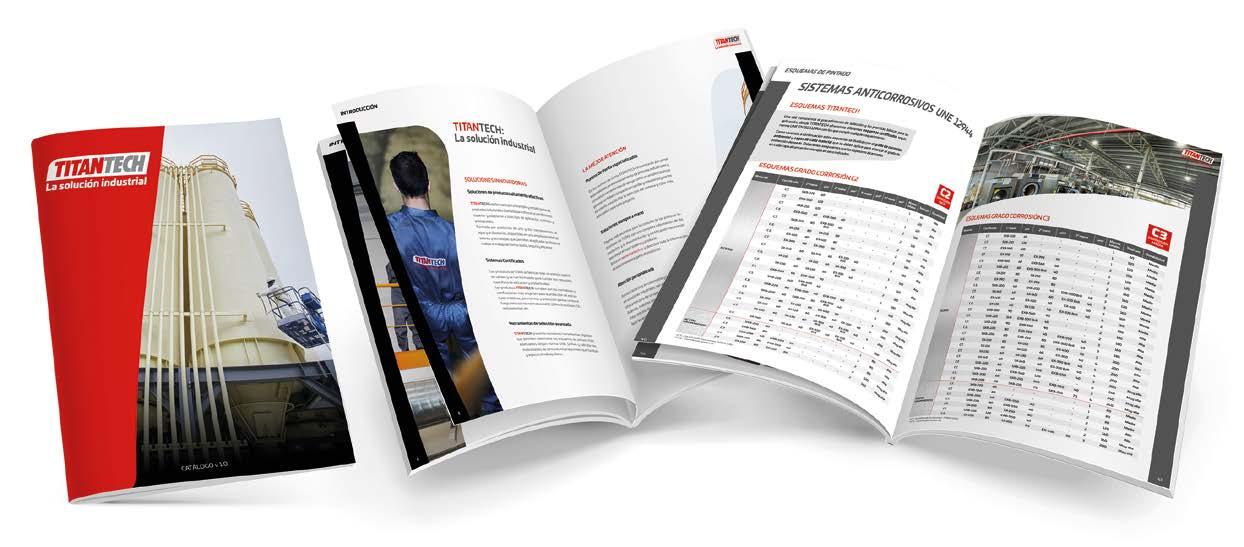
TITANTECH has presented a new catalogue of coatings for corrosion and fire protection of metal structures, floors and wooden surfaces.
In the “catalogues” section of TITANTECH website, the new coating brand of AkzoNobel, it is available a new online catalogue designed to provide a consultation tool to professionals who are searching for the best coating solutions for corrosion and fire protection of metal structures, wooden floors and surfaces in industrial environments or with high technical or hygienic requirements.
This new publication, however, it is not simply a catalogue, rather it is a guide that allows to consult the most suitable solutions of anticorrosive primers and enamels, floor and intumescent coatings, as well as paints, lacquers and solvents for wood. It is also possible to access additional technical information such as, for example: • regulations and certifications: TITANTECH coatings comply with regulations and certifications related to protection of steel structures, flooring and passive fire protection according to ISO 12944, to reaction to fire according to EN 13501-1 and to the slip and fire resistance of structures according to EN 13381-8; • coating systems: TITANTECH, in addition to guaranteeing useful tools for choosing the most suitable paints for each intervention or situation, offers also the possibility of obtaining up to 120 certified coating systems based on ISO 12944; • the list of defects with causes and TITANTECH solutions, accompanied by photos and detailed technical and practical explanations; • the glossary: a dictionary, complete with information and technical data to understand the characteristics and performance of the paints.
The new catalogue of TITANTECH’s coatings business line represents a guide and a working tool containing a renewed and wide assortment of high-quality paints, specifically designed to structures and capital goods. It offers optimal and innovative solutions with certified products and coating systems that meet the needs of the most demanding customers.
© Boeing
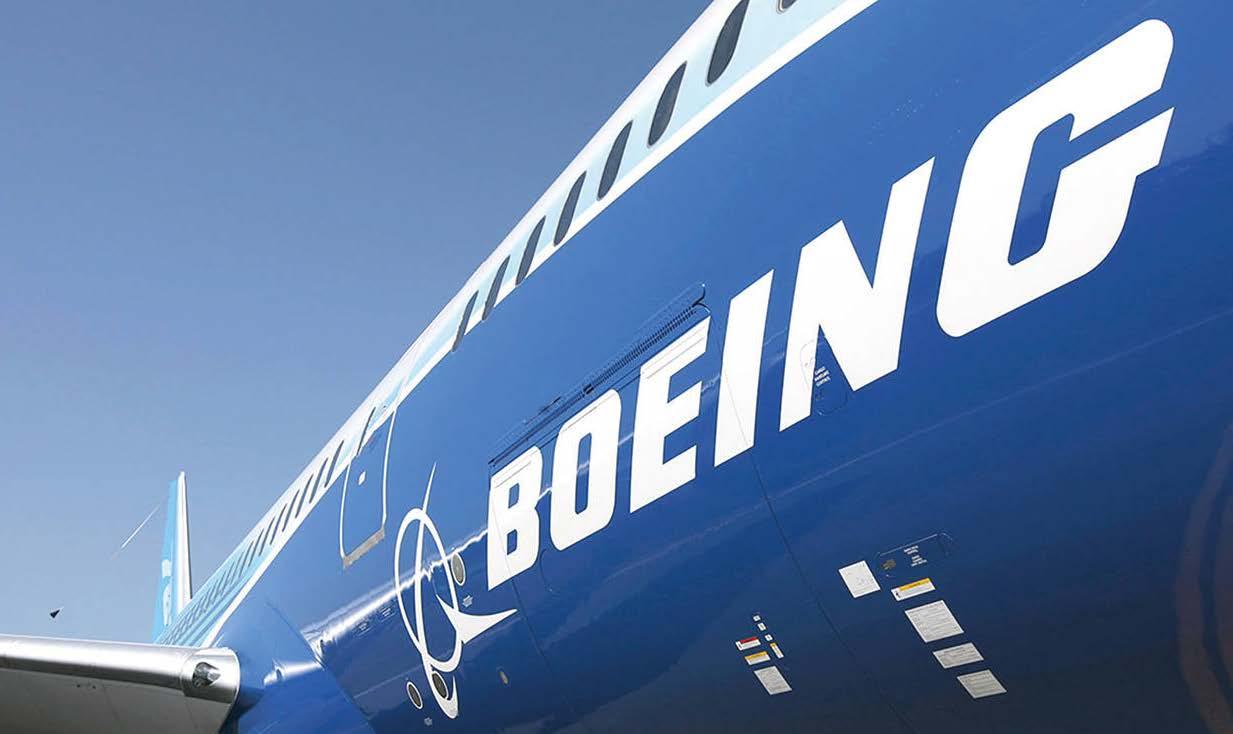
Savroc and Boeing: Partnering for a Sustainable Aerospace Manufacturing
Savroc and Boeing have signed a Purchase Contract to partner on the use of TripleHard® chromium coating technology.
Savroc Ltd and Boeing have signed a Purchase Contract to collaborate on the use of TripleHard® technology, a non-toxic trivalent hard chromium coating developed by Savroc. This coating is more environmentally friendly than many other protective coatings commonly used in the aerospace industry. This partnership underlines the industrial participation agreements that promote Finnish companies’ work packages that increase the competitive offering of Boeing products around the world, generating more and more economic benefits in Finland. “Collaborating with Savroc underscores our shared mission to deliver unsurpassed product offerings that do right by our customers, our planet, and future generations,” said Maria Laine, vice president, Business Development, Boeing Defence, Space & Security. “This partnership serves as a guidepost across the industry of how we can collectively deliver on our commitment to climate action and sustainable aerospace.” “We are proud to partner with Boeing to enhance our mission of providing technology-based solutions to customer needs while being responsible for the environment,” said Osmo Jahkola, Chief executive officer at Savroc. “Savroc and Boeing share a common pioneering spirit that focuses on a cleaner future by providing the right solutions today”. Savroc Ltd is the pioneer of the trivalent hard chromium technology. Savroc technology center is located in Kuopio, Finland. The center is equipped with the latest technology for coating industry research & development. In 2015 Savroc Ltd was selected as one of the 25 most promising Nordic cleantech start-ups by Nordic Cleantech Open.
For further information: www.savroc.com
Hempel Announces New Executive Group Management
Hempel announced a new Executive Group Management that will lead the way to doubling the company’s revenue to 3 billion euros by 2025.
Hempel announced a new Executive Group Management to lead its growth journey and get even closer to its customers. The new Executive Group
Management replaces the former matrix structure with a two-tier leadership, including an Executive Management
Board and an Operational Management Board. The new way of working gives Hempel a simpler organisational structure, with clearer roles and responsibilities, enabling future growth and closer alignment with customers. “I’m thrilled to announce today’s changes,” said Lars
Petersson, Group President & CEO. “My new leadership team will lead a new way of working at Hempel - we have organised our business in an even more customer-focused structure, which will unleash potential and energy from the organisation to deliver on our Double Impact strategy.”
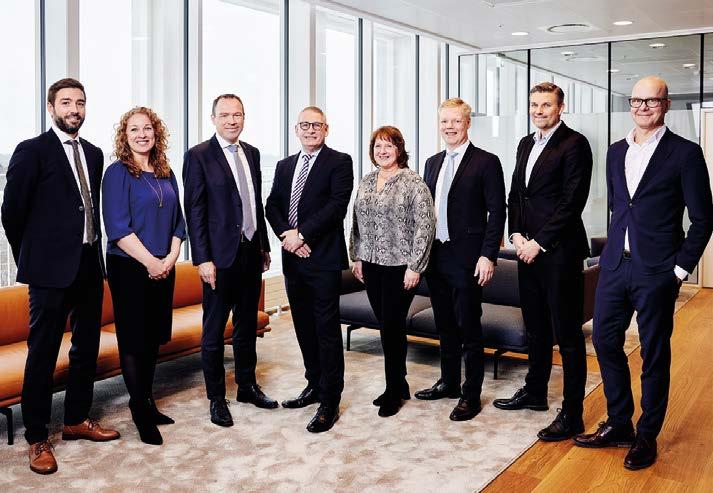
The new structure
Hempel’s commercial activities are now organised into key segments: • Marine, led by Executive Vice President, Alexander Enström; • Energy & Infrastructure, led by Executive Vice President, Michael Hansen; • Decorative, led by Executive Vice President, Joe Devitt.
Chief Operations Officer and Executive Vice President, Katarina Lindström, now heads up Technology & Operations; Chief Financial Officer and Executive Vice President, Lars Dollerup now oversees Finance & Digital; and Chief People & Culture Officer and Executive Vice President, Pernille Fritz Vilhelmsen is at the helm of People & Culture. Strategy & Transformation is also joining the EGM, headed up by Vice President, René Overgaard Jensen. “A year into our Double Impact strategy and we’ve made great progress,” continues CEO, Lars Petersson. “We’re on track, but from hereon in, the mountain gets steeper and we have changed the way we work to enable us to grow at a faster rate, and ready ourselves for scaling up the business with future acquisitions.”
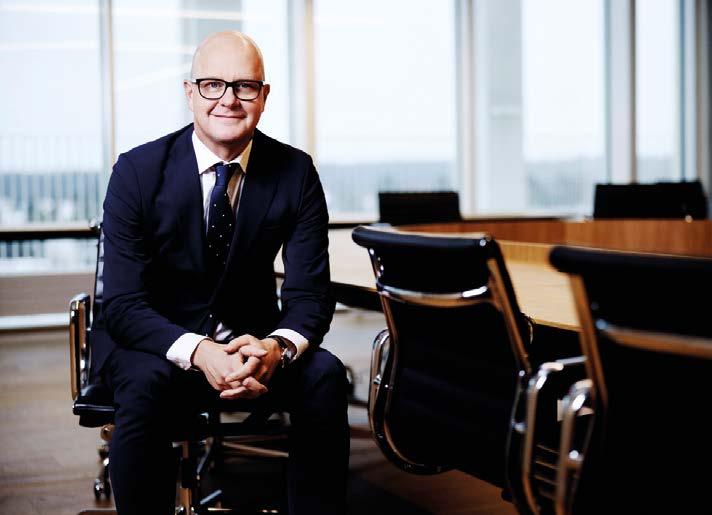
For further information: www.hempel.com
© Hempel
© Hempel Lars Petersson, Group President & CEO of Hempel.