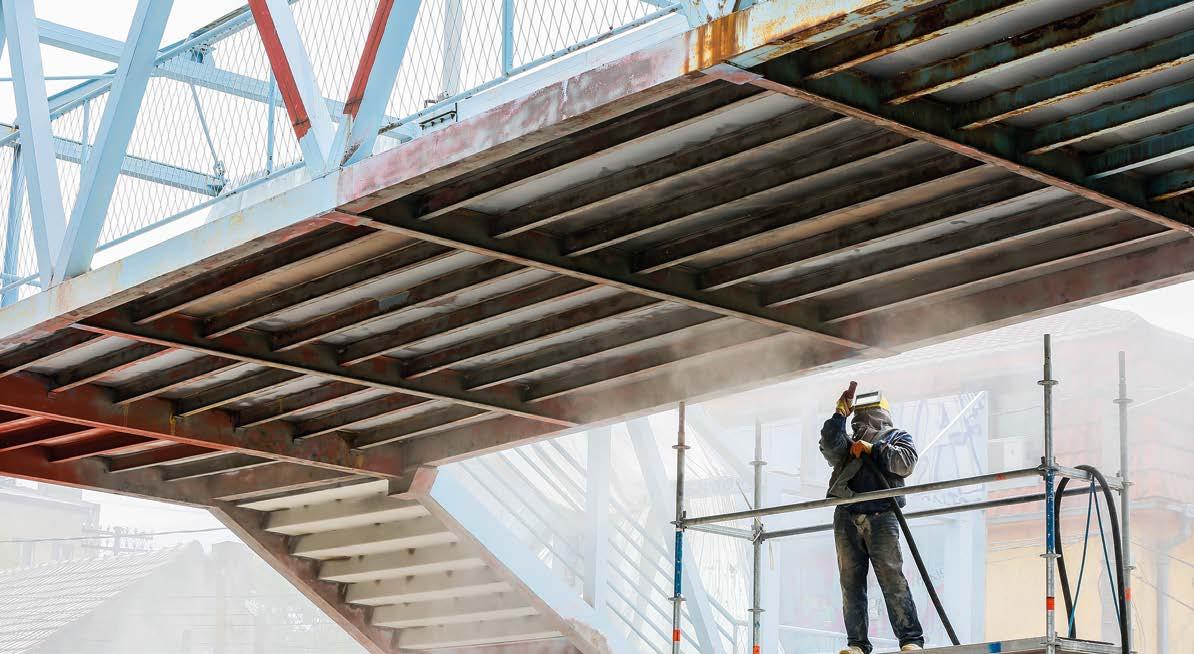
6 minute read
INSPECTION LOGBOOK
Coating Inspections - Inspection of Steel Surface Preparation, Part 5
Massimo Cornago
NACE International Certified Coating Inspector, NACE CIP PEER Reviewer cornago@ipcm.it
Following the previous article, “Inspection of Surface Preparation of Steel, Part 4”, and before we discuss other surface preparation systems and their related inspections, beginning with the abrasive blast cleaning process and its related inspection method, let us start by considering the appropriate international standards: NACE, SSPC, and ISO (the latter of which will be covered in another article). For many years, the industry has referred to the NACE and SSPC surface preparation standards as if they were exact equivalents, although they actually contained some wording differences. In 1990, the two associations formed a joint task group with the express purpose of setting joint, identically worded standards for steel abrasive blast cleaning. Such joint standards were published in October 1994 and they soon began to be commonly used in the industry at a global level. Recently, NACE and SSPC have merged and changed their name into AMPP: Association for Materials Protection and Performance. For the time being, however, the standards still maintain the old denomination that we will describe here below.
White metal blast cleaning (NACE1/SSPC-SP5)
The NACE1/SSPC-SP5 White Metal Blast Cleaning standard states that “when viewed without magnification, the surface shall be free of all visible oil, grease, dust, dirt, mill scale, rust, coating, oxides, corrosion products, and other foreign matter.” Acceptable variations in appearance that do not affect surface cleanliness include variations caused by the type of steel, original surface condition, thickness of the steel, weld metal, mill or fabrication marks, heat treating, heat-affected zones, blasting abrasives, and differences due to the blasting technique. When coating is specified, the surface shall be roughened to a degree suitable for the specified coating system. Immediately prior to coating application, the entire surface shall comply with the degree of cleaning specified. SSPC-VIS1 may be specified to supplement the written definition. In any dispute, however, the written standards shall take precedence over visual standards and comparators.
Near-white blast cleaning (NACE2/-SSPC-SP10)
The NACE2/SSPC-SP10 Near-White Blast Cleaning standard states that “when viewed without magnification, the surface shall be free of all visible oil, grease, dust, dirt, mill scale, rust, coating, oxides, corrosion products, and other foreign matter, except for staining. Random staining shall be limited to no more than 5% of each unit area of surface, approximately 58 cm2 (a square of 7.6 cm x 7.6 cm).” Staining may consist of light shadows, slight streaks, or minor discolorations caused by stains of rust, stains of mill scale, or stains of previously applied coating. Acceptable variations in appearance that do not affect surface cleanliness include variations caused by the type of steel, the original surface condition, the thickness of steel, weld metal, mill or fabrication marks, heat treating, heat-affected zones, blasting abrasives, and differences in the blast pattern. If coating is specified, the surface shall be roughened to a degree suitable for the specified coating system. Immediately prior to coating application, the entire surface shall comply with the degree of cleaning specified. SSPC-VIS1 photographs A SP-10, B SP-10, C SP-10, or D SP10 may be specified to supplement the written definition. In any dispute, however, the written standards shall take precedence over visual standards and comparators.
Commercial blast cleaning (NACE3/SSPC-SP6)
The NACE3/SSPC-SP6 Commercial Blast Cleaning standard states that “when viewed without magnification, the surface shall be free of all visible oil, grease, dust, dirt, mill scale, rust, coating, oxides, corrosion products, and other foreign matter, except for staining. Random staining shall be limited to no more than 33% of each unit area of surface, approximately 58 cm2 (a square of 7.6 cm x 7.6 cm).” Staining may consist of light shadows, slight streaks, or minor discolorations caused by stains of rust, stains of mill scale, or stains of previously applied coating. Acceptable variations in appearance that do not affect surface cleanliness include variations caused by the type of steel, the original surface condition, the thickness of steel, weld metal, mill or fabrication marks, heat treating, heat-affected zones, blasting abrasives, and differences due to the blasting technique. If coating is specified, the surface shall be roughened to a degree suitable for the specified coating system. Immediately prior to coating application, the entire surface shall comply with the degree of cleaning specified. SSPC-VIS1 may be specified to supplement the written definition. In any dispute, however, the written standards shall take precedence over visual standards and comparators.
Brush-off blast cleaning (NACE4/SSPC-SP7)
The NACE4/SSPC-SP7 standard defines a brush-off blast cleaned surface as follows: “when viewed without magnification, the surface shall be free of all visible oil, grease, dirt, dust, loose mill scale, loose rust, and lose coating. Tightly adherent mill scale, rust, and paint may remain on the surface.” Mill scale, rust, and paint are considered tightly adherent if they cannot be removed by lifting with a dull putty knife after abrasive blast cleaning. The entire surface should be subjected to the abrasive blast action. The remaining mil scale shall be subjected to abrasive blasting. Flacks of the underlying steel need not be exposed whenever the original substrate consists of intact coating. If coating is specified, the surface shall be roughened to a degree suitable for the specified coating system. Immediately prior to coating application, the entire surface shall comply with the degree of cleaning as specified. Visual standards or comparators may be specified to supplement the written definition. In any dispute, however, the written standards shall take precedence over visual standards and comparators.
Industrial blast cleaning (NACE8/SSPC-SP14)
The NACE8/SSPC-SP14 standard defines an industrial blast cleaned surface as follows: “when viewed without magnification, the surface shall be free of all visible oil, grease, dust, and dirt. Traces of tightly adherent mill scale, rust, and coating residues are permitted to remain on 10% of each unit area of the surface, approximately 58 cm2 (a square of 7.6 cm x 7.6 cm), if they are evenly distributed. ”Any traces of mill scale, rust, and coating are considered tightly adherent if they cannot be lifted with a dull putty knife. Shadows, streaks, and discolorations caused by stains of rust, stains of mill scale, and stains of previously applied coating may be present on the remainder of the surface. The shape, configuration, and design of structures can lead to areas of limited accessibility for blast cleaning. Examples include crevices around rivets or fasteners, and behind or between tightly configured back-to-back angles. Because of such limited accessibility, these areas are exempt from the 10% restrictions. However, all surfaces in limited-access areas shall be subjected to abrasive blasting and old coating, rust, and mill scale are permitted to remain on completion only provided they are well adherent as determined using a dull putty knife. Acceptable variations in appearance that do not affect surface cleanliness include variations caused by the type of steel, the original surface condition, the thickness of steel, weld metal, mill or fabrication marks, heat treating, heat-affected zones, blasting abrasives, and differences due to the blasting technique. If coating is specified, the surface shall be roughened to a degree suitable for the specified coating system. Immediately prior to coating application, the entire surface shall comply with the degree of cleaning specified. ISO 8501-1 or other visual standards of surface preparation may be specified to supplement the written definitions.
In the next article, we will discuss surface profile testing methods. ‹