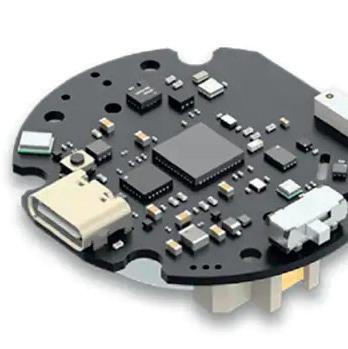
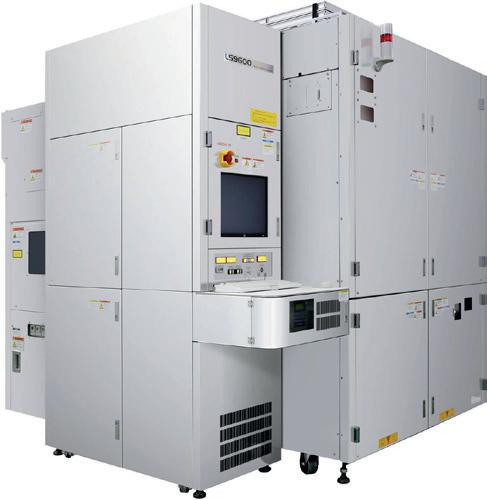
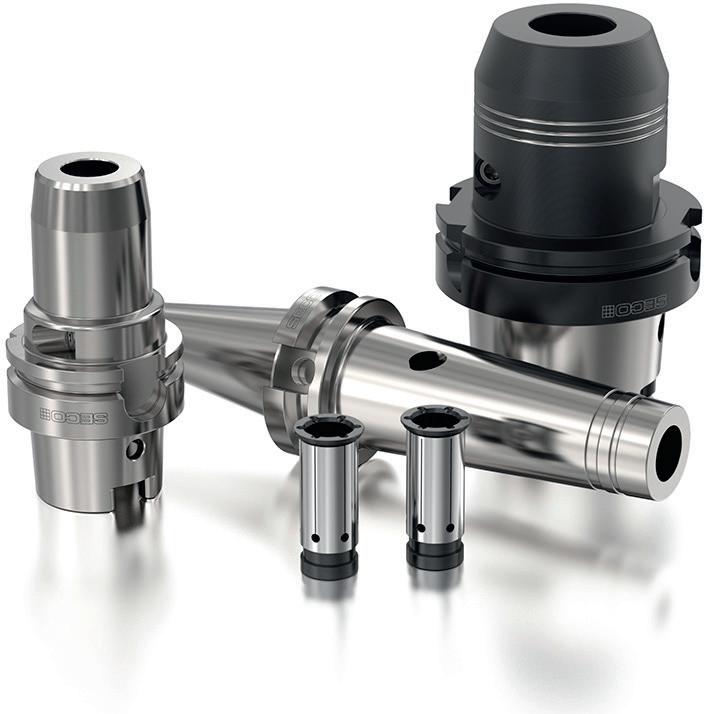
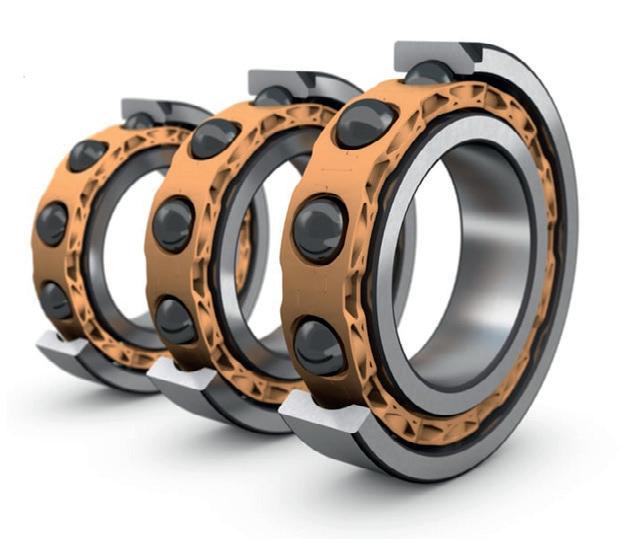
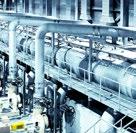

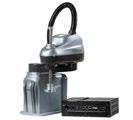
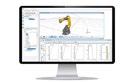
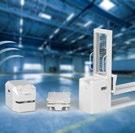

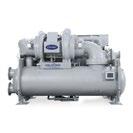
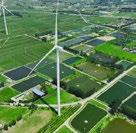
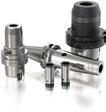
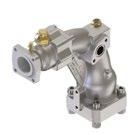
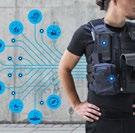
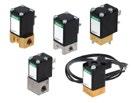
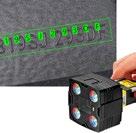
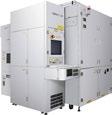

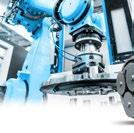
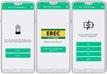
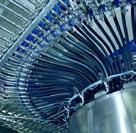


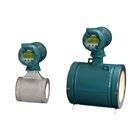
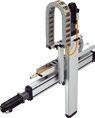
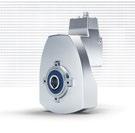
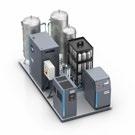
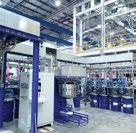
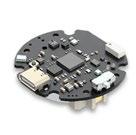
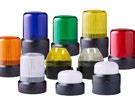
Next to industrial and digital revolutions, 3D printing is another technology changing the world. It is an ultramodern manufacturing technique that can be found almost everywhere and not just as tooling in factory settings.
While today’s 3D printing carries some impressive capabilities and is a widespread mode of production used by manufacturers across nearly every industry, it was not always like that. 3D printing has come a long way since additive manufacturing technology was introduced back in the 1980s. To understand this futuristic method, it is helpful to understand the history of 3D printing, what have come before it, and where are we at with this industrial revolution.
Additive manufacturing started in the 1980s when Chuck Hull invented a process called, stereolithography, now known as 3D printing. He discovered the method, which used UV lasers to create 3D objects layer by layer, after becoming frustrated with the long production times of prototyping. This sparked the next wave of manufacturing practices, and in 1986, he successfully patented his invention, eventually becoming the father of 3D printing. Thus, commercialized availability of additive manufacturing and 3D printing for manufacturers was born.
Since the invention of the first 3D printing rolled into the spotlight, it has been subject to rapid and endless innovation and development. A niche technology, it has opened possibilities for start-ups to present reasonably-priced 3D printers, with major multinational corporations like HP and GE entering the 3D printing space.
3D printing technology has offered various solutions to help tackle the shortcomings that traditional manufacturing methods have for decades. The global 3D printing market is projected to grow from US$18.33 billion in 2022 to US$83.90 billion by 2029, at a CAGR of 24.3% in forecast period, 2022-2029, exhibiting a CAGR of 24% during the forecast period, reports Fortune Business Insights.
According to the market research firm, the rapidly increasing digitalization, growing adoption of advanced technologies, such as Industry 4.0, smart factories, robotics, machine learning, and others fuel the demand for online 3D printing for simulation purposes. These technologies increase the chances of broader adoption and greater utilization of this technology across industries, including aerospace, automotive, healthcare among others.
We have witnessed the continued evolution of 3D printing in the past year as it transitions from mostly prototyping to widespread use in manufacturing at scale. The great paces made on the technology front mean that today’s printers can provide manufacturers with parts that are faster to develop, more accurate, lower cost, and closer to the point of application. Here are some of the important techniques of 3D printing technology today:
Stereolithography (SLA): Stereolithography is an additive manufacturing process using a vat of liquid UV-curable photopolymer resin and a UV laser to build parts a layer at a time.
Digital Light Processing (DLP): Digital Light Processing displays the image of the 3D model onto the liquid polymer. The exposed liquid polymer hardens and the build plate moves down and the liquid polymer is once more exposed to light. The process is repeated until the 3D model is complete and the vat is drained of liquid, revealing the solidified model.
Selective Laser Sintering (SLS): Selective Laser Sintering is an additive manufacturing technique that uses a high-power laser (for example, a carbon dioxide laser) to fuse small particles of plastics, metal (direct metal laser sintering), ceramic or glass powders into a mass that has a desired 3-dimensional shape.
Inkjet Binder Jet: A binder jetting machine will distribute a layer of powder onto a build platform. A liquid bonding agent is applied through inkjet print heads bonding the particles together. The build platform will be lowered and the next layer of powder will be laid out on top. By repeating the process of laying out powder and bonding, the parts are built up in the powder bed.
Selective Deposition Lamination (SDL): SLD is a 3D printing process using paper. The process involves layers of adhesive coated paper (or plastics or metal laminates) that are successively glued together with a heated roller and cut to shape with a laser cutter layer by layer. A roller with the material moves each new sheet of material over the last and repeats the process until the object is completed.
Electronic Beam Melting (EBM): EBM is like laser melting, but working with an electron beam instead of a laser. The machine distributes a layer of metal powder onto a build platform, which is melted by the electron beam. The build platform is then lowered and the next layer of metal powder will be coated on top. The process of coating powder and melting where needed is repeated and the parts are built up layer by layer in the powder bed.
Fused Filament Fusion (FFF): FFF is an additive manufacturing technology, it is now the most popular 3D printing process, and in FFF a continuous filament of a thermoplastic material is used. Through a moving, heated printer extruder head, molten material is forced out of the print head’s nozzle and is deposited on the work piece layer by layer to form the desired Product.
Every manufacturing company knows that having a vision before you have even started the process of prototyping is where the treasure lay. When great concepts are combined with technology, the possibilities can take form. Some companies have succeeded connecting the competences of 3D printing to solve the 21st century’s most perilous issues. IMARC Group released its top 3D printing companies in the world:
Stratasys Ltd is one of the top companies that are at the forefront of 3D printing technology. It caters to various enduse industries, including aerospace, automotive, medical start-up, as well as tech giants. It also provides decades of knowledge, consulting, training, workflow management, and end-to-end support.
3D Systems, Inc. has been leading the additive manufacturing innovation since its inception. Its portfolio includes hardware, software, and material solutions that span from plastics to metals, and is backed by industryspecific engineering expertise housed in the application innovation group. It also offers a combination of solutions, expertise, and innovation that helps users defy conventional
manufacturing limitations and maximize the value of additive manufacturing.
Materialise NV has combined the largest group of software developers in the industry with one of the largest 3D printing facilities in the world to enable new users for the extraordinary potential that 3D printing offers. The company has created a range of software solutions and 3D printing services to form the backbone of the 3D printing industry.
EOS is a worldwide provider for industrial 3D printing of metals and plastics. The company brings responsible manufacturing solutions via industrial 3D printing technology to manufacturers across the globe. Today, the company’s industrial 3D printing systems make it possible to respond quickly to the demands of volatile markets and address trends like the increasing customization of end products.
ExOne has been the global leader in industrial 3D printing systems company in the United States for more than 20 years. It uses Binder Jetting technology, an additive manufacturing process, to selectively join a binding agent with industrial-grade powder particles. It also created a
Stratasys composite-ready 3D printers are designed for manufacturers to supplement traditional fabrication technologies with high-strength composite 3D printing. Source: Stratasys
custom finished product from a 3D CAD file using metal, sand, or ceramic materials.
Voxeljet AS is a global innovator and technology driver for advanced 3D printing systems and solutions in production environments. The company is equipped with state-of-theart binder jet components and seamlessly integrated into partially or fully automated production systems. It is also sustainably shifting the economic parameters and possible applications of additive manufacturing in the industry.
Hewlett Packard (HP) Enterprise Company aims to create technology that makes life better for everyone, everywhere across the globe. HP Personalization has partnered with 3D printing to make any idea, large or small, simple, or complex, a reality. Furthermore, HP MJF 3D printing technology can unlock new possibilities that complement CNC, injection moulding, as well as additive manufacturing, and powderbased technologies.
SLM Solutions Group is one of the leading providers of industrial metal 3D printing machines focused on metal additive manufacturing and multi-laser technology. They find applications across end-use industries including,
aerospace and defense, automotive, energy, healthcare, tooling, and research.
EnvisionTEC offers a wide variety of 3D printing systems with the ability to mass-produce polymer parts. ETEC printers deliver parts with exceptional accuracy, superior part properties, fine feature detail, and a smooth surface finish. They also provide scale and cost that are competitive with traditional manufacturing techniques like injection moulding.
CleanGreen3D is an Irish company that bought the assets and IP of the former Mcor Technologies Limited, an innovative manufacturer of the world’s most affordable, full-colour, and eco-friendly 3D printers. It makes use of ordinary business letters and A4 papers as build material. Its vision is to make 3D printing more accessible to everyone by rendering durable, stable, and tactile models.
Optomec, Inc. offers production equipment and digital solutions such as 3D printed metal, 3D printed electronics, for the digital age. It aims to reduce lifecycle costs for long-term asset management. The company also enables customers to not only print full 3D parts but also add materials onto existing 3D parts that were produced using conventional manufacturing methods.
Groupe Gorge specializes in high technology and is imbued with a strong entrepreneurial culture. It is one of the leading players in its high-tech markets and operates around the world in innovative and growth sectors such as drones, robotics, engineering, and protection systems. Moreover, the company is enabling major players to find routes to successful production processes by providing 3D printers and new premium materials.
Ultimaker is the market leader in desktop 3D printing that has built an open and easy-to-use solution of 3D printers, software, and materials. It is increasing business flexibility and continuity by 3D printing parts with software trusted by over 800,000 users. Their easy-to-use FFF desktop 3D printers can save time and money while streamlining the workflow and delivering the quality results that are expected.
Renishaw plc is a systems manufacturer and solutions provider for additive manufacturing or 3D printing. It is one of the leading manufacturers of advanced metal additive manufacturing systems and an expert provider of customer-tailored solutions. The company makes use of thin layers of materials to create complex shapes, which cannot be produced by “traditional” techniques such as casting, forging, and machining.
Beijing Tiertime Technology Corp. Ltd strives to deliver additive manufacturing solutions to a wide variety of fields, such as science, mechanical engineering, industrial design, low-volume manufacturing, and education. The company is China’s first 3D printer manufacturer that launched the nation’s entry into the additive manufacturing age with the Inspire industrial line.
XYZprinting, Inc. is one of the leading global providers of comprehensive 3D printing solutions. The company offers desktop 3D printing products and services and is venturing into the industrial additive manufacturing arena. Moreover, XYZprinting is backed by the world’s leading electronic manufacturing conglomerate, New Kinpo Group, which earns more than US$36 billion in revenues annually and has more than 8,500 engineers in research and development across four continents.
With favourable balance sheets and a multitude of latest offerings, 3D printing industry is expected to accelerate adoption in manufacturing processes and make meaningful advances in 2023 and beyond.
These are a few trends that are expected to dominate this year:
Lower cost of 3D printing: One of the major trends in the 3D printing industry is the decreasing cost of 3D printing technology. As 3D printing becomes more accessible, prices are decreasing and the technology is becoming more affordable. This will make it easier for businesses and individuals to utilize 3D printing technology and will offer a new world of options.
Improved speed and quality: Speed and quality are two of the most important aspects of 3D printing. It is becoming faster and more accurate with new advancements coming in. This will enable businesses to create better products more quickly and efficiently and will lead to a greater level of customization for consumers.
Increased use of materials: In the past, 3D printing was limited to plastics and metals. However, as 3D printing technology continues to evolve, an increased use of materials, such as ceramics, polymers, and even food items are likely to happen in the future. This will open a new world of possibilities for 3D printing and will allow businesses to create products that were not previously possible.
The development of multi-material 3D printing allows to produce objects with multiple materials and properties. This technology has the potential to greatly expand the range of applications for 3D printing, including the production of functional prototypes, customized medical devices, and even consumer products.
There has also been a trend towards the development of more advanced 3D printing technologies, for instance: 4D printing and 5D printing. 4D printing involves the use of materials that are capable of changing shape or properties over time in response to external stimuli, such as heat or moisture. 5D printing, on the other hand, involves the use of multiple 3D printing techniques to create objects with complex structures and functions. These technologies have the potential to significantly expand the capabilities of 3D printing and could lead to the development of new and innovative products.
Widespread adoption: As 3D printing becomes more affordable and accessible, it is expected to be adopted by a larger portion of the population. This will open new prospects for individuals and companies to utilize 3D printing technology, as well as lead to new innovations in the industry.
A reduction in carbon emissions is to be expected, as parts now require less transportation. Parts can now also be produced more sustainably as it is easier to customise the materials and dimensions of a part, leading to waste reduction. On that note, its on-demand production capabilities will also ensure that one can only manufacture parts that they need when they need them, resulting in minimal parts wastage and excess.
Shift from process automation to workflow automation: The promise of large-scale industrial 3D printing requires us to automate not only each individual process but also the flow between them. This is what we call workflow automation.
Fred Vancrae, CEO of Materialise, explained, “We see the same requirement in a medical industry where workflow automation is needed to address the dramatic increase of customized 3D printed solutions. The good news is that the ability to meet this need is growing thanks to the creation of software platforms that allow manufacturers to define their own unique 3D printing process. Several companies including Materialise now offer these solutions to customers allowing them to automate not just the individual 3D printing processes but the entire 3D printing workflow from order intake to delivery and everything in between.”
Smart distributed manufacturing: Smart distributed manufacturing that is enabled by 3D printing when done in a strategic way can be a successful recipe, rather than an ad hoc response to problems with global supply chains, Fred Vancrae emphasized. “3D printing enables design optimizations that provide weight performance, time saving and supply chain benefits that are impossible to achieve with traditional manufacturing methods. In many cases, these benefits create cost advantages that impact the overall end-to-end manufacturing costs from design to delivery. In fact, the ability to reduce the overall manufacturing costs is cited as the most important benefit of 3D printing but that does not necessarily mean that the 3D printing process itself is cost efficient. Increasing material and energy prices have only driven up the costs even more,” he stressed.
“There are several factors that determine the cost of 3D printing parts. This comprises of the materials required, production time per part, and the type of printer. However, there are two important ways to reduce this,” Fred pointed. “The first step is by working more efficiently to increase production capacity. Software plays a major role in this by making it possible to optimize the build. We can also tune the printing process to make it more efficient and repeatable,” he indicated.
“The second step is using tools and improve quality; but quality comes at a cost. Looking at certified manufacturing in the medical or aeronautics industry for example, we see that up to 70 percent of the production cost is in quality control. 3D printing continues to transform the factory floor, as companies increasingly turn to the technology for large-scale production. But to accelerate this adoption, the industry will have to make extra efforts to reduce the cost of 3D printing,” Fred added.
Data security and data integrity: Data security is important in any form of manufacturing whether traditional or smart in both cases as addressed by Fred Vancrae in his video about the biggest 3D printing trends for 2023.
“Companies share their unique designs with contractors and suppliers and they want to know that their design data remain secure. With 3D printing, manufacturers may want to plan and scale up the production of their 3D printed parts into thousands or even millions. They need to optimize and fine-tune their unique printing process to make it efficient, reliable, and repeatable across multiple production sites. A smart production process ensures that all 3D printed components have the same quality no matter where they are produced. Creating such a process is complex and time consuming but it allows companies to leap ahead of the competition. That is why in addition to data security and data integrity, the close and secure link between the design on one hand and the production parameters on the other hand is becoming top of mind for companies that embrace digital manufacturing,” he revealed.
The adoption of 3D printing technology reaches new heights each year. Over the last thirty plus years, it has become an integral part of the manufacturing industry. The future is bright for 3D printing technology in 2023, as it will help companies scale up their operations into volume production and advance their overall utilization.
More than 80 employees in 35 different countries, ensuring a strong relationship with main local media. Mepax distinguishes itself through its extensive media knowledge and ability to select the best international online/print advertising options. PR can be translated into 35 languages.
45,000 published articles in 2021: EMEA: 48% - Asia: 31% - Americas: 21%. Most of the articles are published in the top 1000 media worldwide.
With a proven process set for more than 200 active customers, we can adapt to all specific client needs with the highest reliability. We have developed in house the most advanced PR dedicated ERP, enabling transparency and real-time full online reporting. International media management is then made easy, fast, and efficient for optimal results.
www.mepax.com info@mepax.com
OMRON’s has announced the availability of new EtherCAT models in the i4L SCARA robot series. The compact i4L robots now offer even stronger performance at the lowest total cost of ownership. Robotic Integrated Controller allows synchronized multi-robot applications with EtherCAT models.
The i4L SCARA delivers quality along with scalability and integration flexibility well above its class. Thanks to a compact design and small footprint it is simple to install. The i4L offers easy integration with unique Ethernet or EtherCAT connectivity in the base, and together with the robotic integrated controller users can deploy multiple robots and reduce set up complexity and programming time. Its speed makes it ideal for material handling tasks, while freeing human resources for other tasks that maximize productivity.
“Thanks to the EtherCAT models, we have taken our SCARA robots to the next level. They can be implemented in a wide range of applications allowing for more productivity within the workplace,” Fernando Vaquerizo, Fixed and Cobots Product Marketing Manager at OMRON Europe, comments.
Key features and benefits of the i4L include:
• 5 kg payload capacity
• 350 mm, 450 mm, and 550mm reach options with table and wall mounting options
• Robotic Integrated Controller NJ-R for multi robot applications with EtherCAT models
• Stand Alone Ethernet models
• Fast cycle time with an unprecedented range of movement and repeatability
• Exceptionally powerful built-in servos to handle payloads with ease
• Advanced and robust industrial design
• Lowest total cost of ownership
For more information, please visit the i4L compact SCARA robot product page
Edge learning technology simplifies character reading applications to improve quality control and traceability.
Cognex Corporation, the leader in industrial machine vision, has expanded the capabilities of its In-Sight® 2800 vision system to include optical character recognition (OCR). The new ViDi™ EL Read tool, powered by edge learning technology, deciphers human-readable characters on reflective, low-contrast and non-flat surfaces with ease.
“The In-Sight 2800 with edge learning redefines ease of use, allowing anyone to deploy AI-based applications regardless of experience level,” said Lavanya Manohar, Cognex Vice President of Vision Systems. “ViDi EL Read replaces complicated programming with example-based training, making it simple to set up OCR models to read characters on challenging surfaces and even multiple lines of text simultaneously.”
Companies across all the industries we serve have been looking for an easy-to-use OCR solution and are enthusiastic about this new offering. Food and beverage producers can easily read expiration dates, even on curved surfaces, to verify freshness and prevent consumer recalls. Medical device and pharmaceutical companies can verify dates and lot codes to ensure vaccine efficacy and compliance with medical standards. Electric vehicle manufacturers can quickly locate and read the alphanumeric text laser etched
on the bottom sides of EV batteries to improve traceability, and logistics facilities can decipher codes and text on a variety of package types to ensure proper routing and prevent rework.
OCR applications can be time-consuming to set up, requiring hours of programming by highly trained engineers, preventing many companies from automating this type of inspection. Using the ViDi EL Read tool, models are set up and deployed directly on the device in minutes with as few as 10 sample images. The accuracy of the results is measured by a confidence score that is displayed below each of the trained characters offering real-time, visual feedback and reassurance of reliable traceability across the supply chain.
The In-Sight 2800 vision system was first released in April 2022 designed to solve complex classification applications. Additional tools are currently in development and scheduled for release in coming months.
www.cognex.com
Typical SelectaFlot flotation system by ANDRITZ.
International technology group ANDRITZ has received an order from Lipy Paper Mills Ltd. to supply wastepaper processing systems to the mill in Changine, Modonpur, Kanchpur, Sonargaon.
These are the first ANDRITZ RCF (Recycled Fiber) lines for Bangladesh. Start-up is scheduled for the third quarter in 2023.
ANDRITZ will supply key equipment for two RCF lines, featuring a total capacity of 150 t/d and processing LOCC (Local OCC) and MOW (Mixed Office Waste) as raw material for production of testliner, writing and printing paper.
“ANDRITZ convinced us because of its energy-saving technology for screening and flotation and its focus on minimum fiber loss. In addition, with the Ultra High Dispersion we’ll be able to keep steam demand at a low level. All these topics are strategic development targets for an aspiring company like Lipy Paper Mills,” Shahiar Hasan Khan, Deputy Managing Director, Lipy Paper Mills says.
Lipy Paper Mills Ltd. is an aspiring company, established in 2016 by Lipy Group, a family-owned Bangladeshi enterprise and successful player in the paper market.
www.andritz.com
The new line of Thomson miniature lead screws is available in 2-, 3- and 4-millimeter diameters and with a handful of additional options to provide flexible linear motion solutions for space-conscious applications.
Thomson Industries, a leading manufacturer of linear motion control solutions, has introduced a line of miniature lead screws and nuts. This new offering extends the Thomson lead screw product line to include 2-, 3- and 4-millimeter diameters.
“ OEMs are increasingly demanding components for smaller assemblies, and we are pleased to announce that Thomson high-quality lead screws and nuts are now available in diameters smaller than six millimetres. This provides our customers with additional flexibility to design more compact systems and is part of the ongoing expansion of our miniature offerings,” said Saurabh Khetan, Thomson Product Line Manager – Lead Screws.
The new Thomson miniature lead screw line is available with either standard or anti-backlash lead nuts to optimise positional accuracy, friction and repeatability. The antibacklash lead nut design reduces friction between the nut and screw threads in order to optimise efficiency while still eliminating play between the lead screw and nut.
Customers can specify a variety of lead options and end machining capabilities for maximum flexibility in final assembly and precision at a miniature scale. As with all Thomson products, a wide variety of customisation options are available. For ease of mounting and integration, Thomson also offers oversized end machining options such as journals and even a brand new, integrated coupler design, which allows customers to easily mount the lead screw onto various shaft diameters without the need of an additional coupling component.
The smaller screws are ideal for a wide range of applications but are especially valuable in emerging medical technologies and analytical equipment.
For more information on Thomson miniature lead screws, visit https://www.thomsonlinear.com/en/products/leadscrews/mini-lead-screws
www.thomsonlinear.com
Hitachi High-Tech Corporation has announced the launch of the LS9600, a new system for detecting particles and defects on non-patterned wafer surfaces. It features a new highoutput, short-wavelength laser that improves throughput at the sensitivity levels required for the mass production of cutting-edge semiconductor devices by ~2.6 times compared to our previous generation systems.
By introducing this product, Hitachi High-Tech will continue to help to improve yields and reduce inspection costs associated with customers’ mass production of semiconductor devices.
Non-patterned wafer inspection systems are used for applications such as controlling the condition (cleanliness) of non-patterned wafers to manage particles and defects in semiconductor device manufacturing equipment. Due to the shrinking of semiconductor devices, the defects of interest (DOIs), which impact yield during the manufacturing process, have also become smaller in size. As a result, there is a growing need for high-sensitivity inspection that can detect DOIs of 20 nm and smaller across the entire surface of non-patterned wafers. In addition to high-sensitivity inspection to improve yield, there is also a strong demand for high throughput, which leads to lower inspection costs.
This system achieves both high sensitivity and high throughput by implementing the following new technologies.
The deep-ultraviolet laser has a higher output and shorter wavelength than legacy systems, which increases the amount of light scattered by microscopic defects, thereby achieving a higher degree of sensitivity.
The new optical detection system features a larger surface area to capture light scattered by DOIs compared to the legacy systems. In addition, its newly developed highsensitivity sensor has improved the detection rate of weak scattered light by around 20%.
Improved scattered light data-processing algorithms deliver higher sensitivity, together with higher throughput due to high-speed, real-time data processing.
By using this product, as well as our wafer optical inspection systems, and electron beam-based products such as a traditional CD-SEM*1 and DR-SEM*2, Hitachi High-Tech is working to meet customers’ various needs in processing, measurement, and inspection throughout the semiconductor manufacturing process. We will continue to provide innovative and digitally enhanced solutions to our products for the upcoming technology challenges, and create new value together with our customers, as well as contributing to cutting-edge manufacturing.
*1 CD-SEM (Critical Dimension-Scanning Electron Microscope): An equipment for measuring the microscopic circuit patterns on semiconductor wafers. Used for inspections on semiconductor devices development and production lines, these systems are essential for yield management.
*2 DR-SEM (Defect Review-Scanning Electron Microscope): An equipment for reviewing the microscopic circuit patterns and defects on semiconductor wafers. Used for inspections on semiconductor devices development and production lines, these systems are essential for yield management.
www.hitachi.com
Elements’ system-level modelling can be used across a wide range of industries, from robotics to aerospace, and from automotive to energy generation.
Hexagon’s Manufacturing Intelligence division has today introduced Elements, new simulation software that helps engineering teams understand the behaviour of systems that are becoming increasingly complex in modern products. Using the software, teams can evaluate the performance and feasibility of new design concepts quickly to inform more efficient product development and reduce risk and cost.
Elements addresses the growing importance of integrated, multi-disciplinary system development and end-to- end workflows. Customers in every industry are demanding technologies that consider many physics domains and tackle mechatronics challenges in a robust way, fuelling a growing trend towards system-level engineering. Achieving this requires the integration of all relevant engineering disciplines, control systems, and thirdparty supplier systems to understand how the domains interact, and how a design decision in one discipline impacts others.
Systems engineers can easily learn to use the Elements software, using its drag-and-drop environment to model any physics type or logic and analyse systems by intuitively connecting blocks – regardless of whether they represent electrical, hydraulic, mechanical components – to solve system-level engineering problems. It is based on the Modelica language, which is an open and widely used standard for building fast, flexible, and customisable models.
Systems modelling is indispensable in the early design phases because little information is required – often a CAD model, equation, or lookup table is sufficient and a 3D mesh is not required. Elements further speeds up engineering development because it also ensures that system-level models compute quickly and efficiently by optimising equations and code for fast calculation, but with no loss of fidelity.
As the design develops, and components and subsystems are detailed in specialist simulation software, the components can be routinely integrated into a larger system through full compliance with the FMI standard and Hexagon’s proprietary SmartFMU technology. SmartFMU unlocks the Functional Mock-up Unit (FMU) for supported Hexagon products so that changes can be made directly in the Elements system-level model without having to go back to the specialist Computer Aided Engineering (CAE) software and its expert user. This helps to avoid resource bottlenecks, time-consuming switching between applications, and versioning problems.
Elements combines user-friendly drag-anddrop modelling with comprehensive multiphysics simulation – e.g. mechanical, hydraulic, control, and many others.
Hexagon’s roadmap will see its best-in-class CAE technologies readied for easy and productive use with Elements. At launch, the software provides SmartFMU connectivity with Adams multibody dynamics software and Easy5. Future plans are likely to include workflows with Cradle CFD thermal-fluid dynamics and Actran acoustic simulation products, among others.
Both standard FMI support and the novel SmartFMU plug-and-play capabilities offer immediate value and address challenges of system complexity, including those for transportation electrification; for example:
• Helping automotive engineers to find optimal solutions to vehicle range optimization issues by considering a vehicle’s energy use under different driving conditions, taking into account eDrive design, regenerative braking, climate control, ADAS safety requirements, and battery choice.
• Improving the flexibility and accuracy of industrial robotics by designing control systems that take detailed mechanical system vibrations and interactions from multibody dynamics simulation into account.
• Right-sizing heavy battery systems in new eVTOL aircraft designs by helping engineers understand the power draw during take-off and landing, safety margins, and thermal management system controls.
• Implementing safer, more sustainable long-life battery systems by using Elements to design control systems that balance the improved performance of lithium-ion batteries at elevated temperatures with the impact heating has on cell degradation.
Landing gear simulation in Elements uses Hexagon’s unique SmartFMU capability to provide enhanced integration with its Adams software.
Elements was developed in close cooperation with Maplesoft, building upon its powerful maths engine to optimise system equations and deliver fast efficient simulation to Hexagon’s customers. Chris Harduwar, VP of Strategic Solutions at Maplesoft, commented: “We are excited to begin this long-term collaboration with Hexagon, which has an impressive vision and track record of innovation. By combining the tried-and-tested Maplesoft system-level modelling technology with the extensive Hexagon CAE portfolio, engineers in many industries benefit from new productivity-boosting solutions that significantly reduce simulation effort.”
“Elements offers engineers an easy way to explore behaviour of systems quickly and find better solutions to problems using simulation, before committing designs to subsequent resource-intensive engineering processes. We look forward to a long-term collaboration with Maplesoft, using its powerful and open technology foundations to realise synergies with our extensive Hexagon CAE ecosystem portfolio and deliver valuable capabilities to our customers,” Mahesh Kailasam, General Manager for Design and Engineering Software at Hexagon, commented.
To learn more about Elements, please visit hexagon.com/products/elements
www.hexagon.com
Ultra-compact and rugged wireless routers enhance connectivity to remotely located equipment and systems in demanding utility, infrastructure and transportation applications.
Westermo has expanded its range of industrial cellular routers designed to provide resilient data communications for remote sites. The new Merlin 4400 series of ultra-compact and rugged LTE Cat 4 wireless routers has been developed specifically to support extremely secure remote access to equipment and systems within demanding utility, industrial and trackside applications. High connection security gives users the confidence to expand their IP networks to include remote assets, helping to increase visibility and ultimately improve operational performance.
Resilient and reliable high-speed data communications are essential to the digitisation of the rail network, the implementation of smart grids and improving the operational performance of utilities. Network security is a fundamental requirement in these applications and to defend against increasing cyber threats, the Merlin 4400 series is equipped with a complete set of cybersecurity tools as standard.
These include a TPM (trusted platform module) chip that keeps cryptographic keys secure, Secure Boot functionality ensuring the routers boot using only trusted software, and virtual private network (VPN) and stateful firewall support for data security and user authentication.
The Merlin 4400 series offers high-speed data network connectivity, with support for Ethernet and RS-232/485 communications to ensure suitability for a broad range of applications. The Merlin 4400 is ideally suited to replace traditional modems when migrating to an IP infrastructure. Serial (RS-232/485) ports enable connection to legacy devices and equipment, while a built-in industrial protocol gateway enables seamless connection to multiple devices using different communication protocols.
With many applications typically requiring installation in demanding environments, the Merlin series has been designed to cope with extreme operating temperatures and high levels of electrical magnetic interference. The Merlin 4400 series has IEC 61850-3 Class 1 approval, allowing deployment in medium voltage substation automation applications, while EN 50121-4 approval enables use in rail trackside applications. Outstanding reliability and an extremely long operating life (mean time between failures of 1,600,000 hours) helps to minimise expensive maintenance trips and lowers network operating costs.
With networks increasing in size and complexity, the Merlin range has been designed to support both the system integrator and user by being easier to install, operate and maintain. When coupled with Westermo’s zero touch deployment software Activator, the Merlin routers provide cost-effective, reliable and consistent onboarding within large-scale projects. This allows configuration from a central server, which reduces the potential for errors and saves considerable time.
“The increasing need to gain access to remote sites for monitoring, management, diagnostics and support creates a greater reliance on the availability of reliable and secure data networks. The Merlin 4400 range of cellular wireless products meet this requirement, supporting the most demanding industry applications, while providing the advanced functionality needed to maximise connectivity and reduce installation time without affecting security,” explained Dermot Mannion, product manager, Westermo.
Read more: www.westermo.com/products/routers/ wireless-routers/merlin-4407-t4-s2-lv
www.westermo.com
Over the last 5 years, SANY Renewable Energy’s market share has been increasing steadily to 7.75% where it now has been placed among the TOP 5 onshore wind power manufacturers in China. Globally, as the wind power sector of SANY Group, SANY Renewable Energy has been on the list of the TOP 500 global new energy enterprises for many years, ranking 136th in 2022.
In recent years, with substantial investments in R&D, SANY Renewable Energy has established a global R&D network in major cities in China and an R&D center in Spain. As part of the wave of SANY’s intelligent and digital transformation, SANY Renewable Energy is one of the pioneers in promoting China’s 5G wind power technology to the world. Its intelligent manufacturing bases produce in-house wind turbine blades and generators to ensure the high quality and efficiency of the manufacture of intelligent WTGs, which guarantees SANY being a reliable global provider in the renewable energy industry.
Under the background of a low-carbon future featuring a carbon emissions peak and carbon neutrality, SANY Renewable Energy explores the low-carbon development of the manufacturing industry through intelligent products, manufacturing, and operation, contributing continuously in terms of the global environment and climate protection.
After the technology accumulation and R&D innovations, SANY Renewable Energy has formed diverse packaged wind farm solutions that manage the entire life cycle of wind power projects: From digital R&D platform modular product design and automation technology manufacturing process, to wind farm design, EPC, intelligent O&M, and servicing, SANY’s value-maximized wind farm solutions are available to adapt to various geographical and climatic conditions to address the need of all the investors for a optimize business case.
As an established brand in the heavy equipment industry and a well-known excavator and crane manufacturer, SANY is working on expanding the horizons of what the brand used to be known for - The future we build is not only about stronger roofs and higher walls, but also a cleaner sky for future generations.
www.sanyglobal.com
The new innovative solution for oil-free heat pumps and chillers enhances the systems’ efficiency and reliability. The oil-free centrifugal market is growing exponentially around the world driven by a need to reduce system running costs, complexity, and system size.
The new Danfoss OFC check and stop valve incorporates a damped nozzle check valve, stop valves and diffuser function to address the major application pain points.
The nozzle check valve remains open at minimum flow, closes quickly if there is a system stop generating refrigerant backflow, and improves stability during surge, closing and opening for enhanced compressor reliability.
Decoupled stop and check functions allow fast access and improve reliability of sealing. The lock ring design prevents unintentional ball valve closes.
The OFC valve has a built-in sight glass which provides direct visibility of proper check valve functioning, and the builtin pressure port connects to a high pressure cut out as an added safety measure.
Minimizing pressure losses is critical to ensure optimum system efficiency. This is even more important at part-load conditions needed to meet the latest efficiency guidelines. Optimizing the flow path within the valve improves flow capacity and reduces pressure drops by up to 70% compared to using an alternative piston type valve, axial wafer valve or swing wafer.
Reduced system complexity, installation, and maintenance costs
Production planning is much simpler as the OFC valve is an all-in-one solution. There is no need to combine multiple components and store spare parts in inventory. Installation is fast and easy, allowing companies to start production quickly with shorter lead times. The OFC valve can be set
up in three positions, either vertically, horizontally or at a 45-degree angle in order to optimize space and minimize piping.
The new OFC valve is compatible with the Danfoss portfolio of TT and TG Turbocor® compressors - the world’s first oil-free magnetic bearing compressor for the HVAC industry.
“At Danfoss we are continually developing components for efficient oil-free systems,” said Frank Ford, Director of Product Management at Turbocor®. “With the OFC check and stop valve, customers can avoid high pressure drops and unstable performance.
Through our innovative approach we have patented the check valve design used in the centrifugal compressor discharge line. There is no other product on the market today that has the capabilities of our unique OFC check and stop valve.”
Victor Marinich, Global Segment Director at Danfoss Air Conditioning said: “We are dedicated to supporting HVAC professionals by providing solutions that overcome the challenges they face. The OFC check and stop valve is just the latest in a line of new products within our extensive oil-free portfolio. We will soon be introducing ETS 175/250/400/500 L electric expansion valves dedicated to oil-free and hightemperature applications. They are complementing the recent releases within our portfolio of expansion valves and
accessories such as the EKF stepper valve driver and the EKE 2U power module, and a brand new superheat controller platform—EKE 100— which will be released in 2023. All that together support reliable, high-performance oil-free systems.”
www.danfoss.com
“Following major strategic partnerships concluded early this year, the race was on to implement them on the ground. We’re pleased that it’s in Switzerland, the country where our solution was designed, that Wearin’ is applying its unique IoT and artificial intelligence technology at the service of the connected human.” – Jonathan Brossard, Conextivity Group CEO.
Since the beginning of October, all the agents at the security company SOS Cash & Value have been equipped with the intelligent vest from Wearin’, the startup whose Internet of Things (IoT) technology is specifically designed to reinforce the safety and efficiency of its mission-critical teams on the ground.
The high-tech vest that SOS Cash & Value’s security guards wear at all times during their mission throughout Switzerland is equipped with environmental and biometric sensors connected to the monitoring center based at the security company’s headquarters in Vernayaz (Valais). The Wearin’ dashboard integrated into the center’s warning system provides real-time information on the situation on the ground. It continuously displays the data from the sensors whose algorithms correlate biometry, movement, acceleration and positioning in the vicinity and in the armored vehicle, which is also equipped with a specific sensor. An alarm is automatically triggered when the system detects an abnormal situation such as a security guard falling over (Man Down detection), or the stress caused by an incident such as an attack on a vehicle. The alert and communication system between the agents and the monitoring center enables the SOS Cash & Value mission leaders to decide on the actions and measures to secure and intervene with the emergency services and police forces at the scene of the incident.
The Wearin’ solution comprises two scalable platforms, one physical and one digital, that communicate with each other in real time.
“This personal equipment is revolutionizing the world of private security”, explains Pierre-Yves Glassey, CEO of SOS Cash & Value. “It’s cutting-edge and provides an ingenious and reliable solution, tailored by Wearin’ to our company’s specific needs, and based on our experience and standards in security. This high-tech bulletproof vest provides a security guard with exceptional safety.”
The technology developed by Wearin’s R&D engineers in Morges (Vaud) was successfully tested on a European scale in May 2022, during first-aid drills in the event of a major disaster. It is intended for organizations whose staff is called upon to coordinate risky activities and interventions on the ground, such as police forces, firefighters and first responders, or lone workers in the logistics or construction sectors.
“Our IoT technology is unique on account of its ingenuity as well as its integrability and modularity,” specifies Alvaro Goncalves, Wearin’s Technical Director. “We implement it as a turnkey end-to-end solution, on two platforms that communicate permanently with each other: on the one hand, the physical platform of the smart vest worn in the field by the customer’s staff and, on the other hand, the digital platform that is easily integrated into the customer’s monitoring system. The digital platform collects and centralizes the data transmitted by the vests’ sensors. These data are processed by artificial intelligence and then displayed via an application on a security dashboard used by
the operators in the engagement and monitoring centers. Both platforms are modular and scalable. Our solution is designed to be adapted very easily and quickly to the customer’s own needs and technological capabilities.”
The SOS Cash & Value Security Manager notes the data security guaranteed by the solution: “This is a crucial point for the SOS Surveillance Group, to which SOS Cash & Value belongs. Our group wants to take the lead in reinforcing our agents’ security, which is the priority. Since the encryption used by Wearin’ to encode our data is of the highest industrial standard, we are protected against any criminal intent to decrypt them.”
Jonathan Brossard, CEO of Conextivity Group to which Wearin’ belongs, is pleased to implement the solution as a world first with a Swiss customer: “Three years almost to the day after the creation of our startup, and following strategic partnerships concluded early this year with leading suppliers such as Airbus with its Secure Land Communications (SLC) division, the race was on to implement the solution on the ground. We’re pleased that it’s in Switzerland, the country where our solution was designed, that Wearin’ is applying its unique IoT and artificial intelligence technology at the service of the connected human.”
https://wearin.tech/
ASCO Series 209 proportional valves offer superior precision, flow and power consumption for medical devices, hydrogen fuel pumps, food equipment and more.
Emerson introduced the ASCO™ Series 209 proportional flow control valves, which offer the highest standards of precision, pressure ratings, flow characteristics and energy efficiency available in a purpose-built, compact architecture. With this combination of size and performance, Series 209 valves allow users to precisely regulate the flow of fluid in a wide range of devices that require exacting performance, like those found in the medical equipment, food and beverage, and heating, ventilation and air conditioning (HVAC) industries.
Accuracy, response time and repeatability are critical in high-precision flow control applications, such as controlling tool speed in dental chairs, the flow of steam in coffee makers, water flow in cooling systems and hydrogen flow in fuel cells. Series 209 valves have low hysteresis (less than or equal to 5%), excellent repeatability (less than or equal to 1%) and high sensitivity (less than or equal to 0.2%) that contribute to their precision.
“Proportional valves are key components that can significantly impact equipment performance and efficiency,” said Shivam Chauhan, commercial product marketing manager, Europe, the Middle East and Africa at Emerson’s discrete automation business. “We designed the ASCO Series 209 valves to deliver the highest level of performance in a small footprint, giving our customers the flexibility and confidence to engineer products that drive innovation, foster sustainability, lower costs and improve people’s lives.”
The low power consumption and fast response time (less than or equal to 15 milliseconds) of Series 209 can extend battery life in devices powered by them and optimize system performance and efficiency. An improved internal design prevents metal-on-metal contact that causes clicking, which allows valves to operate at extremely low sound levels that are crucial for occupant comfort and wellbeing in medical, commercial building and food service and hospitality environments.
Series 209 valves meet global approvals, including Underwriters’ Laboratories (UL), United Kingdom Conformity Assessed (UKCA) and European Conformity (CE) and include a range of options that tailor valves for specific applications. For instance, Series 209 valves can be cleaned for critical applications like oxygen therapy devices and come in different coil configurations that add flexibility and simplify installation. And a selection of elastomers ensures compatibility with various media, including elastomers free of silicone that can withstand alcohol and sulfur in demanding applications like painting and powder coating as well as elastomers approved by the United States Food and Drug Association (FDA) for food and beverage applications.
Series 209 valves join Emerson’s comprehensive offering of industry-leading proportional valve technology.
For more about Emerson’s ASCO Series 209 proportional flow control valves, please visit: www.Emerson.com/Proportional
Mobile robots are everywhere, from warehouses to hospitals and even on the street. Their popularity is easy to understand; they’re cheaper, safer, easier to find, and more productive than actual workers. They’re easy to scale or combine with other machines. As mobile robots collect a lot of real-time data, companies can use mobile robots to start their IIoT journey.
But to work efficiently, mobile robots need safe and reliable communication. This article outlines the main communication and safety challenges facing mobile robot manufacturers and provides an easy way to overcome these challenges to keep mobile robots moving.
Before we begin, let’s define what we mean by mobile robots.
Mobile robots transport materials from one location to another and come in two types, automated guided vehicles (AGVs) and autonomous mobile robots (AMRs). AGVs use guiding infrastructure (wires reflectors, reflectors, or magnetic strips) to follow predetermined routes. If an object blocks an AGV’s path, the AGV stops and waits until the object is removed.
AMRs are more dynamic. They navigate via maps and use data from cameras, built-in sensors, or laser scanners to detect their surroundings and choose the most efficient route. If an object blocks an AMR’s planned route, it selects another route. As AMRs are not reliant on guiding infrastructure, they’re quicker to install and can adapt to logistical changes.
The first challenge for mobile robot manufacturers is to select the most suitable wireless technology. The usual advice is to establish the requirements, evaluate the standards, and choose the best match. Unfortunately, this isn’t always possible for mobile robot manufacturers as often they don’t know where the machine will be located or the exact details of the target application.
Sometimes a Bluetooth connection will be ideal as it offers a stable non-congested connection, while other applications
will require a high-speed, secure cellular connection. What would be useful for mobile robot manufacturers is to have a networking technology that’s easy to change to meet specific requirements.
The second challenge is to ensure that the installation works as planned. Before installing a wireless solution, complete a predictive site survey based on facility drawings to ensure the mobile robots have sufficient signal coverage throughout the location. The site survey should identify the optimal location for the Access Points, the correct antenna type, the optimal antenna angle, and how to mitigate interference. After the installation, use wireless sniffer tools to check the design and adjust APs or antenna as required.
Mobile robots need to communicate with controllers at the relevant site even though the mobile robots and controllers are often using different industrial protocols. For example, an AGV might use CANopen while the controller might use PROFINET. Furthermore, mobile robot manufacturers may want to use the same AGV model on a different site where the controller uses another industrial network, such as EtherCAT.
Mobile robot manufacturers also need to ensure that their mobile robots have sufficient capacity to process the required amount of data. The required amount of data will vary depending on the size and type of installation. Large installations may use more data as the routing algorithms need to cover a larger area, more vehicles, and more potential routes. Navigation systems such as vision navigation process images and therefore require more processing power than installations using other navigation systems such as reflectors. As a result, mobile robot manufacturers must solve the following challenges:
• They need a networking technology that supports all major fieldbus and industrial Ethernet networks.
• It needs to be easy to change the networking technology to enable the mobile robot to communicate on the same industrial network as the controller without changing the hardware design.
• They need to ensure that the networking technology has sufficient capacity and functionality to process the required data.
Creating a system where mobile robots can safely transport material is a critical but challenging task. Mobile robot manufacturers need to create a system that considers all the diverse types of mobile robots, structures, and people in the environment. They need to ensure that the mobile robots react to outside actions, such as someone opening a safety door or pushing an emergency stop button, and that the networking solution can process different safety protocols and interfaces. They need to consider that AMRs move freely and manage the risk of collisions accordingly. The technology used in sensors is constantly evolving, and mobile robot manufacturers need to follow the developments to ensure their products remain as efficient as possible.
The safety standards provide guidelines on implementing safety-related components, preparing the environment, and maintaining machines or equipment.
While compliance with the different safety standards (ISO, DIN, IEC, ANSI, etc.) is mostly voluntary, machine builders in the European Union are legally required to follow the safety standards in the machinery directives. Machinery directive 2006/42/EC is always applicable for mobile robot manufacturers, and in some applications, directive 2014/30/EU might also be relevant as it regulates the electromagnetic compatibility of equipment. Machinery directive 2006/42/EC describes the requirements for the design and construction of safe machines introduced into the European market. Manufacturers can only affix a CE label and deliver the machine to their customers if they can prove in the declaration of conformity that they have fulfilled the directive’s requirements.
Although the other safety standards are not mandatory, manufacturers should still follow them as they help to fulfill the requirements in machinery directive 2006/42/ EC. For example, manufacturers can follow the guidance in ISO 12100 to reduce identified risks to an acceptable residual
risk. They can use ISO 13849 or IEC 62061 to find the required safety level for each risk and ensure that the corresponding safety-related function meets the defined requirements. Mobile robot manufacturers decide how they achieve a certain safety level. For example, they can decrease the speed of the mobile robot to lower the risk of collisions and severity of injuries to an acceptable level. Or they can ensure that mobile robots only operate in separated zones where human access is prohibited (defined as confined zones in ISO 3691-4).
Identifying the correct standards and implementing the requirements is the best way mobile manufacturers can create a safe system. But as this summary suggests, it’s a complicated and time-consuming process.
A reliable and easy-to-implement standard since the 1980s, communication-based on CAN technology is still growing in popularity, mainly due to its use in various booming industries, such as E-Mobility and Battery Energy Storage Systems (BESS). CAN is simple, energy and cost-efficient. All the devices on the network can access all the information, and it’s an open standard, meaning that users can adapt and extend the messages to meet their needs.
For mobile robot manufacturers, establishing a CAN connection is becoming even more vital as it enables them to monitor the lithium-ion batteries increasingly used in mobile robot drive systems, either in retrofit systems or in new installations. Mobile robot manufacturers need to do the following:
1 - Establish a reliable connection to the CAN or CANopen communication standards to enable them to check their devices, such as monitoring the battery’s status and performance.
2 - Protect systems from electromagnetic interference (EMI), as EMI can destroy a system’s electronics. The risk of EMI is significant in retrofits as adding new components, such as batteries next to the communication cable, results in
the introduction of high-frequency electromagnetic disturbances.
5. Accessing Mobile Robots Remotely
The ability to remotely access a machine’s control system can enable mobile robot vendors or engineers to troubleshoot and resolve most problems without traveling to the site.
The challenge is to create a remote access solution that balances the needs of the IT department with the needs of the engineer or vendor.
The IT department wants to ensure that the network remains secure, reliable, and retains integrity. As a result, the remote access solution should include the following security measures:
• Use outbound connections rather than inbound connections to keep the impact on the firewall to a minimum.
• Separate the relevant traffic from the rest of the network.
• Encrypt and protect all traffic to ensure its confidentiality and integrity.
• Ensure that vendors work in line with or are certified to relevant security standards such as ISO 27001
• Ensure that suppliers complete regular security audits.
The engineer or vendor wants an easy-to-use and dependable system. It should be easy for users to connect to the mobile robots and access the required information. If the installation might change, it should be easy to scale the number of robots as required. If the mobile robots are in a different country from the vendors or engineers, the networking infrastructure must have sufficient coverage and redundancy to guarantee availability worldwide.
Benefits of Remote Access.
As we’ve seen, mobile robot manufacturers must solve many communication and safety challenges. They must establish a wireless connection, send data over different networks, ensure safety, connect to CAN systems, and securely access the robots remotely. And to make it more complicated, each installation must be re-assessed and adapted to meet the on-site requirements.
Mobile robot manufacturers are rarely communication or safety experts. Subsequently, they can find it timeconsuming and expensive to try and develop the required communication technology in-house. Enlisting purposebuilt third-party communication solutions not only solves the communication challenges at hand, it also provides other benefits.
Modern communication solutions have a modular design enabling mobile robot manufacturers to remove one networking product designed for one standard or protocol and replace it with a product designed for a different standard or protocol without impacting any other part of the machine. For example, Bluetooth may be the most suitable wireless standard in one installation, while Wi-Fi may provide better coverage in another installation. Similarly, one site may use the PROFINET and PROFIsafe protocols,
while another may use different industrial and safety protocols. In both scenarios, mobile robot manufacturers can use communication products to change the networking technology to meet the local requirements without making any changes to the hardware design.
Authors: Mark Crossley, Daniel Heinzler, Fredrik Brynolf, Thomas Carlsson
https://www.hms-networks.com/
Carrier has announced that it has expanded its award-winning AquaEdge® 19DV water-cooled centrifugal chiller capacity range in North America. With capacity now up to 1150 tons, the AquaEdge 19DV can accommodate customer requirements of higher capacity applications such as commercial high rise and mixed use buildings, large manufacturing factories and healthcare facilities.
The AquaEdge 19DV is the ultimate innovation in chiller technology and utilizes a refrigerant with an ultra-low global warming potential of ~1. Carrier is a part of Carrier Global Corporation, the leading global provider of healthy, safe, sustainable and intelligent building and cold chain solutions.
“The AquaEdge 19DV is built on the legacy of Willis Carrier’s breakthrough invention of the centrifugal chiller, which is celebrating its 100th anniversary this year,” said Tom Franaszek, Director, Global Product Management, Watercooled Chillers, Carrier Commercial HVAC. “The 19DV’s unique EquiDriveTM two-stage back-to-back compressor design improves efficiency and operating range, continuing Carrier’s technological leadership in centrifugal chiller design.”
The AquaEdge 19DV was designed to minimize environmental impact while also providing industry leading efficiency. It also provides free cooling, a strategy for leveraging natural air temperatures, which can result in thousands of dollars in energy savings per year while reducing maintenance costs and mechanical room space. The efficient design supports Carrier’s 2030 ESG goal to reduce its customers’ carbon footprint by more than 1 gigaton.
Additional features include a variable frequency drive (VFD) that protects the chiller against abnormalities in the power quality being delivered to a system. In addition, every 19DV is supported by Carrier’s BluEdge™ service platform, providing actionable analytics and real-time dashboards. Carrier Service automatically trends, predicts and analyzes performance, allowing for a strategic approach to preventive maintenance and providing an intuitive way to monitor plant energy consumption.
The innovative AquaEdge 19DV first launched in Asia in 2016 and was subsequently introduced to other regions, earning a reputation for reliability and efficiency. The chiller has amassed an impressive list of more than five international accolades including earning gold in the U.S.based Consulting-Specifying Engineer Product of the Year Awards, Boilers & Chillers category.
To learn more about the Carrier AquaEdge 19DV watercooled centrifugal chiller, visit www.carrier.com/19DV www.carrier.com
Manufacturers must overcome specific machining challenges cost effectively. With this goal in mind, Seco offers its comprehensive range of Hydraulic Chucks and accompanying Reduction Sleeves in three versions, each able to accommodate several tool shank size variations for reduced tooling inventory. With 360° tool-shank holding strength and precise centering, the Hydraulic Chucks and Expansion Sleeves ensure reliability, along with exceptional machining performance and maximized tool life.
Easy to use and versatile
For simple, easy-to-use, versatile tool holding, the three versions of Seco Hydraulic Chucks include the HC Conventional, HCR Reinforced and the HCS Slim. The HC Conventional version delivers precision holding for drilling, reaming and light milling. As a universal solution, the HCR Reinforced version provides effective holding for all applications from HSM to HPM and for all kinds of tool shank types like Cylindrical, Weldon and Whistle Notch. The HCS Slim holder version is ideal for accessing deep, narrow part cavities during 5-axis machining at high speeds.
“Complicated tool holding systems not only require special care and training to avoid operator injury, they add extra time and costs,” said Seco Product Manager Yves Heitz. “Seco Hydraulic Chucks and Reduction Sleeves eliminate the risk as well as any extra maintenance to allow users to get in the cut faster while gaining tool holding versatility with less required tooling.”
For added flexibility to accommodate a wide range of cutting tool sizes, 05FHC slotted Reduction Sleeves for the Hydraulic Chucks allow one holder to handle various shank diameters. They provide through-tool or peripheral cooling capabilities and work with either metric or inch-size tools.
Low runout and high precision
According to Heitz, at high spindle speeds, controlling tool holder runout is imperative. When machining at speeds up to 25,000 rpm for example, Seco Hydraulic Chucks and Expansion Sleeves minimize runout and the vibration it causes. Users gain worry-free tool holding without the added cost of specialty holders.
To keep vibration under control, Seco Hydraulic Chucks incorporate internal reservoirs in which oil generates strong 360° tool clamping forces and acts as a natural vibration dampening system – engaged with the simple turn of a hex screw. Additionally, reduction sleeves compress uniformly and completely around tool shanks for precise centering and holding strength.
The slotted reduction sleeves come in sealed and peripherical coolant versions, and the Hydraulic Chucks support all Seco round tools. The holders are compatible with all common machine tool spindle interfaces, including HSK, DIN, BT, BT Taper/face, CAT, CAT
Taper/face and cylindrical straight shanks. Metric shank tools clamp directly in chuck IDs, while inch shanks are held through use of the reduction sleeves.
For more information on the features and specifications of the Seco Hydraulic Chucks and Reduction Sleeves, please contact a local Seco representative or visit https://www.secotools.com/article/m_7244
Heavy-duty robots require robust, precise and dynamic gears with a high load-bearing capacity and a long-lasting design. A home match for cycloidal gears from Nabtesco. The compact robot gears are designed for high performance, durability and reliability. That makes them ideal for heavy loads.
For use in heavy-duty robots Nabtesco, the largest manufacturer of cycloidal gears and Number 1 in robotics, offers an extensive range of products for high-performance gear systems with torque ratings of up to 28,000 Nm. The heavy-duty gears are characterised by extreme precision, maximum robustness and a compact design, and can easily handle the heaviest loads.
High torque capacity combined with minimal backlash and a compact design
In cycloidal gears, power transmission is achieved by cams and rollers. This design ensures continuous contact and even distribution of forces within the gearbox, which produces high rigidity. As a result, it is possible to transmit very high torques with maximum precision (hysteresis loss < 1 arc.min). The increase in backlash remains negligible throughout the entire life cycle. Furthermore, their special design achieves excellent behaviour with respect to dynamics, load capacity and compactness. Even high reduction ratios can be achieved with only two or three gear stages. The integrated main bearings absorb both axial and radial loads and bending moments, and provide for high moment rigidity and resistance to shock loads (up to 500% of the rated torque).
Incidentally: The integrated main bearings allow Nabtesco gears to withstand 250% higher bending moments than conventional planetary gears of a comparable size. This eliminates the need for additional external bearings, which
allows a more compact robot design with maximum precision, dynamics, load capacity and rigidity.
The world’s largest precision gearbox
With a torque rating of 28,000 Nm the RV-2800N is currently the largest and most robust precision gearbox in the world. The XXL gearbox features an optimal combination of performance, torsional rigidity and compactness, which opens up entirely new applications for robots that in the past were possible only with hydraulic or spindle solutions. This is the case, for example, when moving large panes of glass, sheet steel, machine components or even entire motor vehicles. In such applications, heavy-duty robots also benefit from good load conditions as a result of the reduced weight and lower inertia.
Nabtesco cycloidal gears: An ideal solution for heavyduty robotics
Whether for the automotive sector, steel industry, sheet metal handling, metalworking or aircraft construction: In all applications requiring exact robot-based positioning of heavy and large components, high-torque gears from Nabtesco are in demand. The robust precision gears, which are available with a solid or hollow shaft, guarantee safe handling and pin-point positioning – in combination with maximum reliability and a long life.
www.nabtesco.com
How FIRALP, a French company of public works and specialized sectors (Energy, Civil engineering, High voltage, etc.), monitors its charging stations using advanced diagnostic features to increase availability and optimize maintenance activities.
As sustainable mobility has become a priority for many countries, notably in Europe where the parliament just voted to end sales of petrol and diesel cars by 2035, e-vehicles have grown into a booming market.
According to a new report by specialized site EV-Volumes, global EV sales reached 6.75 million units in 2021, 108% more than in 2020. This volume includes passenger vehicles, light trucks and light commercial vehicles. Moreover, the number of electric vehicles on the road should reach at least 145 million units by the end of the decade as per the International Energy Agency (IEA) estimates.
At FIRALP, the move to electric vehicles has been underway for several years now. However, 2022 marks a decisive shift, with more than 100 electric vehicles ordered and charging stations already installed in the branches. The deployment of dual-energy pods is also continuing, as is the order for a dozen gas (CNG) trucks. This renewal meets environmental expectations and anticipates the restriction of the most polluting vehicles in low-emission mobility zones by 2025.
To support its transition to electric vehicles, the group, through its subsidiary EREC, has chosen PcVue Solutions for the supervision of its charging stations.
EREC Technologies is a national specialist in process management and has been a PcVue partner for over 20
years; it supports its customers in the maintenance and operation of turnkey solutions in electricity and automation.
The project began in 2020 with the aim of managing internally the hundred-22kW charging stations of FIRALP’s fifty branches, with an open and flexible solution.
The tests carried out during the lockdown, allowed communication configuration with the charging stations of various manufacturers. OCPP was the selected protocol to monitor the stations for it ensures interoperability.
The charging stations also rely on Load Management Systems which required several firmware updates in order to obtain the desired performance.
Several information are reported in the PcVue application: power delivered by station during charging in time, end-ofcharge event, alarms, start/stop of charging. In addition, 10 WebVue clients provide access to reports visualizations for a better use of the stations. A BMS supervision of the head office, the Château, is also coupled.
As of today, access to the charging stations is free, but each branch has a portal to control it. The number of charging stations is currently sufficient for the number of e-vehicles, but the strong desire of the FIRALP group to expand their fleet of e-vehicles may make access to the stations increasingly difficult.
In the coming months, FIRALP will receive an order of more than 100 electric vehicles to complete their fleet, thus requiring the implementation of resource optimization tools. It is in this context that the innovative mobility solutions offered by the PcVue platform were presented to the FIRALP group.
Digitizing the Queue Ticket Machine: how PcVue makes life easier for EV car drivers!
The main problem that EV car drivers may encounter concerns the cars remaining connected even after a full charge, making the charging station inaccessible for other waiting vehicles.
To solve this challenge, PcVue Solutions offers a solution that allows e-vehicles drivers to sign in with their cell phone when they arrive at parking lots and to indicate the desired charge rate. PcVue stores this information regarding the charge need and rate and when a charging station becomes available, the PcVue platform is able to notify the driver on his mobile of the charging station to use.
Once the vehicle is connected, PcVue will trigger the charging. A configurable time-out is also available if the driver decides to finally not charge his vehicle, in that case PcVue move to the next charging request available in its ticket queue.
The mobile application dedicated to vehicle charging stations is realized without a single line of code thanks to PcVue’s bot functionality. It allows the creation of a mobile graphic interface adapted to the client’s needs, both functional and graphic.
In the FIRALP context, it will be possible for the driver receiving the charging authorization on his mobile to transfer it to a third person in case of unavailability, or simply to postpone it.
These mobile and intelligent solutions allow the three parties involved: vehicles, charging stations and drivers, a perfect match between availability, charging and time.
Adopted by all the employees, “Absolutely no one wants to go back to thermal vehicles”, says Jerome Dorne, head of studies and execution, about 40 new charging stations of various powers and from various manufacturers, as well as a hundred electric vehicles have been ordered by FIRALP. One of main ambition is to have a solution ensuring MOC (Maintenance in Operational Condition) that is to say an obligation of maintenance contract for each installation of a charging station.
In the near future, EREC would also like to become an installer for several other customers.
Towards even greater energy efficiency Finally, the energy performance of FIRALP’s assets has always been the subject of innovation: the Montereau-surle-Jard site, south of Paris, is already covered with 600 m2 of photovoltaic panels managed by the Departmental Energy Syndicate. The next new buildings will also be equipped with them. The Group plans to go one-step further by recovering solar energy for its own consumption. The principle is to use the energy produced by the panels of its truck shelters to power the heating and air conditioning of buildings or to charge electric vehicle terminals.
“Our objective is to control the energy of our buildings, whether it comes from the panels or from the ENEDIS network, an expertise mastered by our subsidiary EREC. These actions should reduce the footprint of our buildings by 10%” emphasizes François Chapel, real estate manager at FIRALP.
In addition to self-consumption, the next high tension site in Meyzieu, near Lyon will experiment with energy storage using recycled batteries. It will be the first site to be built with low-carbon asphalt. A composition based on Landes pinesap will also be tested.
In 2021, FIRALP has carried out a full carbon assessment to calculate the direct greenhouse gas (GHG) emissions generated by the Group’s activity. After the time of measurement, 2022 will be a time for experimentation and action.
To carry out this low-carbon approach, the Group has relied on the firm Oksigen. Following the assessment, 4 priority actions were defined to act on the carbon footprint (concrete, recycling, alternative energies and carbon calculator) and working groups were set up. The goal is to reduce their CO2 emissions by 10% by 2025 and by 20% by 2030.
• About one hundred 22kW terminals
• About 50 agencies
• About 40 new charging stations of various powers and from multiple manufacturers by 2023
• A hundred vehicles ordered in 2022
• A smart mobile application to optimize charging
www.evchargingcontrol.com https://www.pcvuesolutions.com
Branded as Inktrasyst®, the new system, is the top of the range of Inkmaker’s ink-transferring technology and was installed with pre-blending, storage, transfer, and inline automatic-viscosity adjustment for process colour; CMYK + White in 3 different series. The system is powered by IMPRIMO, the latest of Inkmaker’s legendary software; for managing ink stock, formulation blending, real-time storage monitoring, instant-accurate transferring and automatic inline ink-viscosity adjusting, as well as consumption and traceability by work order—a result of IM GROUP’s increased investment in Industry 4.0 technology and IIoT R&D.
As part of several key objectives related to sustainability, Inkmaker’s new system had to abide by the concept of environmental protection. Inkmaker achieved this by maximising current operations towards automation thus reducing human intervention; as well as reducing carbon emissions and wastage; achieving absolute inksupply consistency; activating automatic ink traceability; implementing an always-fresh-ink-blend-to-demand facility and applying bridging-to-printing machinery. Manpower was also reduced for the moving of ink—between ink room and presses—thus further reducing operational costs.
“Traditionally operators would manually refill the ink tray and adjust the viscosity. However, with the Inktrasyst, the ink always arrives at the press in its optimum condition. Additionally, the viscosity is automatically consistent throughout the printing process; this not only increases confidence in achieving a perfect final print out, but also the leftover ink is reduced to practically zero, which is an incredible saving for the environment,” explained Lau Kar Seng, General Manager of Inkmaker Shanghai and board member of IM GROUP.
“We are proud to be part of this environmental-upgrade project, with this major installation, we are able to contribute Inkmaker’s technology to the green-environment target of Beijing—one of the largest economic and technological development areas in China—and with this our commitment, of achieving a greener and more sustainable world, is gaining momentum,” concluded Roberto Guerra, CEO Asia Pacific of IM GROUP.
www.inkmaker.com
With the new GEMÜ app for smartphones and tablets, products can be clearly identified, operated intuitively and product information can be called up conveniently. Furthermore, the entire GEMÜ product range is now also accessible from your trouser pocket.
The GEMÜ app offers numerous functions that make life easier in the world of GEMÜ valves, measurement and control systems.
New electrical GEMÜ products can now be initialized, configured, parametrized and localized via a Bluetooth connection. The GEMÜ app shows process values as well as status information in detail and provides support in setting parameters and error analysis. In the development of the app, particular attention was given to user friendliness in order to enable intuitive operation GEMÜ products. The new GEMÜ 1441 cPos-X positioner is the first product to be operated using the GEMÜ app.
GEMÜ products with a digital product label (QR code) or RFID tag can be clearly identified with the app. This means that users have the right product information and documents to hand directly in the plant. In addition, job-specific information, such as any product certificates acquired, can be called up. GEMÜ provides both the currently available documentation as well as the documentation at the time the product is delivered. This means that any changes or additions are immediately apparent.
The new GEMÜ app also enables easy access to general GEMÜ product information and documents – even when on the move. Users can quickly access datasheets, operating instructions, product flyers and further information to help them with product selection. The offline availability of the documents, which can also be used in plants without internet access, is particularly helpful.
Furthermore, the GEMÜ app offers users a way to make contact quickly and easily. There is a special highlight for app users at ACHEMA 2022 – they can book a day ticket free of charge.
Work is currently underway on further functions that will help plant operators and plant designers in the digitalization of the processing industry.
The GEMÜ app is available in German, English and French, and can be used both on Android and on iOS operating systems. The GEMÜ app can be downloaded from the Google PlayStore and from the App Store.
You can find further information on the GEMÜ app at www.gemu-group.com/app
A new high-performance two-piece polymer cage pushes SKF’s Hybrid deep groove ball bearing into new limits and gives more flexibility in the design choices.
SKF has developed a new hybrid deep groove ball bearing for high-speed applications. The new bearing is aimed at applications such as rail industry traction motors, as well as electric machines and drives. SKF already has three pilot customers, all of them OEMs.
A new lightweight cage helps to boost the limiting speed by at least 60% compared to traditional designs. Additionally, the polymeric cage helps to reduce friction, leading to quieter operation and allowing higher power density in the application.
“Our new cage design helps our customers to get more power from electric motors, which enables downsizing,” says Andreas Pichler, Business and Project Engineer at SKF.
By improving the efficiency of electric machines and drives, the new bearing can cut energy consumption, increase reliability and reduce the total cost of ownership.
Its two-piece cage is made from PEEK and PA66, making it 80% lighter than a brass cage. As well as running more quietly, the bearing operates at a lower temperature, which prolongs grease life and extends relubrication intervals. This can give engineers more flexibility in their design choices.
In addition, its limiting speed is twice that of a single-piece polyamide cage, and 60% higher than a brass one.
Rigidly connected cage bars ensure robustness, which helps to lengthen service life in harsh conditions. The optimised geometry also eliminates radial deformation from high centrifugal forces, the “umbrella effect”, that typically occurs on snap-type cages running at high speed.
The new bearing is targeted at OEMs in rail, off-highway vehicles, E-mobility, and industrial/electrical applications.
www.skf.com
Yokogawa Electric Corporation announces the release of the OpreXTM Magnetic Flowmeter CA Series. This new product series succeeds the ADMAG CA Series and is being released as part of the OpreX Field Instruments family. The products in this new series are all capacitance-type magnetic flowmeters that are capable of measuring the flow of conductive fluids through a measurement tube without the fluids coming into contact with the device’s electrodes.
In addition to this non-wetted electrode construction, this series features new functions that improve userfriendliness, maintainability, and operational efficiency. The new series is available from today in most major markets such as Japan, Southeast Asia, North and South America, Oceania, the Middle East and Africa, and will also be launched in Europe and China after qualifying for CE marking and obtaining the relevant certification for explosion-proof standards.
In plants, inspection is required for each instrument in order to maintain stable operation and product quality, so the efficiency of such inspections is an ongoing issue for production sites. As magnetic flowmeters have no structural components that hinder the flow of fluids and cause a loss in fluid pressure, they are widely used in plants to measure fluids with conductive properties. Large chemical plants and other such facilities can have hundreds of these instruments, and so it is important that their inspection and replacement as well as the collection of the data from each of these devices can be carried out efficiently.
In response to these needs, Yokogawa has revamped the ADMAG CA lineup of flowmeters, which were first released in 1995 and have been widely adopted by customers mainly in Japan, and developed the OpreXTM Magnetic Flowmeter CA Series, equipped with features to improve operational efficiency and maintainability, for release in a wide range of regions. This will help reduce the person-hours required
for customer instrument inspections and contribute to improved plant operational efficiency.
Features of the OpreX Magnetic Flowmeter CA Series
Capacitance-type magnetic flowmeters utilize electrodes that are mounted outside a ceramic measurement tube to measure the electromotive force generated by fluids passing through the tube, eliminating all direct contact between the electrodes and the fluid. This ensures stable flow measurement of fluids containing minerals that generate electrical noise when they collide with an electrode; fluids such as latex, a sticky insulating fluid that can adhere to the inside surfaces of pipes; and fluids such as deionized water and mizuame (millet jelly) that have low conductivity.
In addition to this non-wetted electrode construction, the newly released OpreX Magnetic Flowmeter CA Series has the following new features:
1. New and useful functions that improve userfriendliness and operational efficiency
Support for the widely used HART communications protocol has also been added, and a choice of nine languages is now given for the user interface, enabling swift and stress-free checking of displayed information. As an optional feature, measurement data can be saved on a microSD card for viewing on a PC, and instrument setting data that is saved on a microSD card can be copied to other devices. The display is now equipped with a backlight function that greatly improves visibility at night and in dark locations.
2. A device soundness analysis function that improves maintainability
Products in this series are equipped with a function that can analyze and verify that they are in sound operating condition
while mounted on a pipe. Inspection of magnetic circuits, excitation circuits, and arithmetic circuits, and the checking of device status alarms and soundness can be performed in as little as six minutes. When used in combination with Yokogawa’s FSA130 software (sold separately) and other maintenance tools, many additional items can be checked while a device is mounted on a pipe, and reports can be easily created.
3. Easily replaceable measurement tubes suiting a wide variety of purposes
Measurement tubes in eight sizes ranging from 15mm to 200mm are available for use with these flowmeters, suiting a wide range of purposes. As they have the same face-to-face lengths* as the ADMAG CA Series flowmeters, no additional work is required to replace an ADMAG CA Series flowmeter with a product from the OpreX Magnetic Flowmeter CA Series. The length from end face to end face required to mount a magnetic flowmeter on a pipe.
Chemicals, paper and pulp, mining, food and beverages, water and sewerage.
• Flow measurement for fluids with the following properties
• Fluids with insulators that are prone to adhering to measurement tubes • Fluids that include high-density slurry (solids)
• Fluids with low electrical conductivity
www.yokogawa.com
Bosch Rexroth has expanded its portfolio of linear robots for various applications in factory automation by adding new axis combinations and sizes. The much wider range of working areas and loads makes the Cartesian subsystems also suitable for applications like battery handling or intralogistics.
• Predefined linear robots for a wide range of working areas and loads
• ctrlX AUTOMATION as a shared automation platform
• Optionally available with preinstalled software for quicker commissioning and programming
From handling small parts to large masses: an extended range of Cartesian subsystems opens up new areas of application.
The linear robots can be selected and sized quickly and easily thanks to predefined axis combinations. They can then be configured and finalized online and ordered as preassembled subsystems – optionally with controllers for the new ctrlX AUTOMATION platform. Each multi-axis system is also available as a Smart Function Kit for handling or dispensing. Preinstalled software then allows even quicker commissioning and intuitive programming. This significantly reduces the engineering time.
The expanded range includes eight different axis combinations with 68 sizes. The products can be used in a variety of sectors such as automotive (including battery production), pharmaceuticals and FMCG. Applications range from pick and place, positioning and palletizing to feeding, shifting and loading and even dispensing tasks.
For use in intralogistics, including order picking and packaging, the new multi-axis systems cover large working ranges with stroke lengths of up to three meters in the X and Y directions and up to 1.5 m in the Z direction. The new load spectrum extends to up to 160 kg with three axes and up to 200 kg with two axes. The Cartesian robots are thus suitable for a range of tasks including handling individual parts, containers and boxes.
The preassembled multi-axis systems with the Smart Function Kit option for handling or dispensing require little
maintenance and achieve a high level of process quality and productivity. This is possible thanks to the special design properties such as rigidity, dynamics and repetition accuracy and the new ctrlX AUTOMATION platform which is particularly suitable for complex movements.
The standardized procedure for selecting and sizing a suitable subsystem can be carried out quickly and easily using predefined reference processes with LinSelect. While the design is finalized in the online configurator, the 3D CAD data can be retrieved, an inquiry started or the system ordered via the e-shop. In order to minimize installation times, Bosch Rexroth supplies the selected robot system in preassembled form. If required, it can be supplied with a complete energy chain and cable management. To make commissioning easier, the relevant axis parameters are stored in the motor encoder memory and can be read out automatically. Various attachment parts and interfaces make assembly easier.
The software add-on for the Smart Function Kits for handling or dispensing save users even more time. As part of the preinstalled software package, a wizard guides users intuitively through the commissioning process. The system is parameterized and the axes referenced automatically. Sequencing is carried out on a visual basis with the help of ready-to-use functional modules and can be completed in just a few minutes. Thanks to the flexible combination of hardware platform and innovative software, even complex line movements can be reproduced using simple graphic programming. Line integration can also be carried out easily with the help of suitable function modules.
www.boschrexroth.com
NORDAC ON/ON+ is a compact and Intelligent frequency inverter for decentralised use.
The innovative and patented DuoDrive geared motor reaches outstanding system efficiency.
Automatic bottling and conveyor systems in beverage and liquid food production set high requirements for energy efficiency, operational reliability, wash-down-capability and corrosion protection. As one of the world’s leading full-range suppliers for mechanical and electronic drive technology, NORD DRIVESYSTEMS knows the industry’s requirements and provides efficient, hygienic and reliable solutions for bottling and conveyor technology in beverage lines.
Easy to clean, energy-saving operation, high precision positioning, low operating costs: Drive systems used in automatic bottling systems for the beverage industry must reconcile various requirements – just NORD DRIVESYSTEMS’ area of expertise. The family company from North Germany is the global leader in drive technology and provides customised drive solutions with high energy efficiency, user-friendly plug & play technology, smooth surfaces and long service life.
The innovative and patented DuoDrive geared motor integrates a high-efficiency IE5+ synchronous motor into the housing of a single-stage helical gear unit, and with a system efficiency of up to 92% achieves one of the highest efficiencies on the market in this power class. Very high system efficiency is also achieved in the partial load range. The constant motor torque over a wide speed range allows for consistent version reduction and reduction of operating costs. Together with the simple plug-and-play commissioning, this results in a significant reduction in the Total Cost of Ownership (TCO) in comparison with existing drive systems. The unventilated, wash-down design with smooth surfaces meets the most stringent hygiene requirements and ensures optimum cleaning.
NORDAC ON/ON+: Decentralised frequency inverter with integrated Ethernet interface Beverage bottling is an area where the demand for decentralised drive technology is on the rise. NORD offers an optimal solution with the smart NORDAC ON/ ON+ frequency inverter. NORDAC ON/ON+ covers power ranges up to 2.2 kW and is characterised by an integrated Ethernet interface (ProfiNET, EtherNET IP and EtherCAT can be set per parameter), full plug-in capability and a very compact design. Decentralised inverters are ideally suited for integration into bottling and conveyor systems and thus save space as well the extensive motor cable wiring required for centralised frequency inverters.
The nsd tupH surface treatment is available for DuoDrive as well as for NORDAC ON/ON+. Thanks to a special method, the surface is made corrosion-resistant and harder and makes aluminium behave like stainless steel with regard to corrosion protection. This is not a coating, but a surface treatment that creates a protective layer which is permanently bonded to the substrate material. So nothing can detach or flake off. The drives are easy to clean and largely resistant to acids and alkalis. It is even possible to use high-pressure cleaners or apply aggressive media. nsd tupH treatment is available for most of NORD modular drive systems made from aluminium.
https://www.nord.com
Atlas Copco’s on-site nitrogen generation system has long been the preferred solution for high-pressure applications such as laser cutting and electronics manufacturing? an all-in-one solution that can handle the peak demands of applications as varied as fire prevention, pipeline services, and aviation tyre inflation.
Now, with the introduction of advanced components and additional models, users get even better performance and the flexibility to customise the package to their exact needs.
Atlas Copco’s nitrogen skid package is a complete highpressure nitrogen generation system built onto a compact and pre-commissioned skid. Its plug-and-play installation makes on-site gas production easy and seamless. The Atlas Copco nitrogen skid package comes in a 40-bar and a 300bar variant. Both now feature additional models, expanding the entire range to twelve models in total.
For customers that make the switch from purchasing gas to on-site generation, Atlas Copco’s latest nitrogen skid package offers continual unlimited supply and independence from vendors’ scheduled bulk deliveries, as well as the expense of ordering, transportation, and storage.
New, industry-leading components make up the nitrogen skid package
Atlas Copco’s continuous investment in compressed air and gas generation innovation has resulted in new, industryleading products and components that are now included in this next generation of the Atlas Copco nitrogen skid package:
GA oil-injected rotary screw compressor with VSD technology: The latest Variable Speed Drive compressors match their motor speed and power consumption to users’ nitrogen demand to deliver double-digit energy savings. This significantly reduces their operational costs and environmental footprint.
NGP+ PSA nitrogen generator: Atlas Copco’s premium nitrogen generation system operates with Pressure Swing Adsorption technology to offer a guaranteed gas purity of up to 99.999%. The NGP+ optimises its air consumption based on the actual nitrogen use to ensure energy savings at full and at low load. As a result, the recently expanded and enhanced range delivers superior performance combined with low cost of ownership.
• Nitrogen booster: The high-efficiency booster comes in a 40-bar version for on-demand nitrogen generation and in a 300-bar option for cylinder storage.
• Nitrogen storage: A 40-bar receiver and 300-bar cylinder racks are also offered.
• All components, including dryers and filters, are built to Atlas Copco’s quality standards. They are tested to work together for optimal, plug-and-play performance and reliability.
“Versatility has always been an important benefit of the nitrogen skid package and this latest generation gives users even more flexibility. With more models available, users can choose a nitrogen skid package that fits their exact needs along with the freedom to select and size their compressor, nitrogen generator, booster, and air treatment for a truly customised, top-quality performance. High purity, high flow, high-pressure nitrogen from one skid package. Selfproducing nitrogen has never been this easy,” said Ben John, Business Line Manager, Industrial Air.
For more information on Atlas Copco’s new high-pressure nitrogen generation skid package, please visit https://www. atlascopco.com/en-uk/compressors/products/nitrogengenerators/high-pressure-nitrogen-skid www.atlascopcogroup.com
The installation of the Inkmaker Easypaint 10v+24v water-based dispensing system designed for interior exterior and decorative paints including roof paints, water proofing, and wood staining was the result of a tripartite collaboration involving leading-edge technology from IM GROUP’s; Inkmaker Turin, Inkmaker Shanghai and PT Teko Tinting and Engineering. The installed system comes powered by Inkmaker’s IMAESTRO software which connects virtually to modern ERP systems.
PT Mowilex Indonesia, a leading producer of premium paints and coatings in Indonesia, with a workforce of over 1,000 team members and products distributed over 8,000 stores throughout the archipelago, compared several leading systems before settling on the optimal paint-dispensing solution:
“The Easypaint’s production speed, formula-dosing accuracy and detailed work-order traceability is impressive, the customised version, which Teko installed at our Cikande factory, is expected handle up to 70 tons per month, with 21 days of operation per month, translating into 3,3 tons per day,” explained Niko Safavi, CEO of PT Mowilex.
Having designated 50% of its new 6-plus-hectare factory at Cikande as a green area, Mowilex a pioneer in the development of environmentally friendly practices since its inception in 1970 looked for a system that could achieve its eco-friendly goals:
“Due to the high-precision dosing of the Inkmaker Easypaint we no longer require unnecessary extra stock, and can therefore eliminate unnecessary waste as well as having a cleaner production site,” concluded Safavi.
“The installation was particularly challenging for our team, deliveries were delayed and, due to lockdowns in Shanghai being at the peak of the Omicron variant, this limited the speed of our operations in Serang. Thankfully, being part of IM GROUP, we were able to tap into its collective knowledge and resources to best optimise our activities and minimise delays,” explained Michael Setiadi, Director of PT Teko Tinting and Engineering, Supply-chain.
“Mowilex is one of Indonesia’s most prominent paints and coatings brands, we are very proud that our Easypaint was able to meet its stringent requirements and that—with the combined expertise of Teko and Inkmaker—it is functioning beyond its expectations. We greatly look forward to future collaborations with the team at Mowilex,” commented Roberto Guerra, CEO Asia Pacific, IM GROUP.
www.im-group.com
Predictive maintenance in factories
Primarily by monitoring the movement of motors inside factories and industrial robots using various sensors, anomalies and failures of machinery and equipment can be predicted.
Factories and manufacturing sites need to prevent anomalies in machinery and equipment to minimize downtime. Productivity can be raised by predicting problems and performing maintenance preemptively, instead of reacting only after breakdowns have occurred. To facilitate this type of predictive maintenance, TDK has developed i3 Micro Module—the world’s first ultracompact sensor module featuring embedded edge AI.
The technical challenges of implementing predictive maintenance on the manufacturing floor
Generally, manufacturing sites are expected to operate their machinery and equipment at 100% capacity. This is because productivity can be held high by running at full capacity—in fact, many factories operate 24 hours a day, 365 days a year. Today, the concept of predictive maintenance is gathering considerable interest as a means to reduce the downtime of machinery and equipment. It refers to using sensors to monitor factory machinery and equipment in real time, predict anomalies and failures before they occur, and take preemptive action.
In contrast to traditional reactive maintenance, where actions are taken after failures or anomalies occur, predictive maintenance is believed to reduce the risk of failures, minimize manufacturing downtime, and extend equipment life. It is a major theme within the ongoing global movement toward smart factories*1, and is expected to be adopted in a variety of manufacturing settings.
In predictive maintenance, the real-time monitoring of equipment and machinery conditions using sensors is known as Condition Based Monitoring, which is considered to be a particularly key technology. Trying to achieve this, however, presents two major challenges. First, in factories, various sensors and analysis tools are generally provided as disparate systems, which complicates the collection and processing of data, thereby making it difficult to utilize the results of analyses. Secondly, due to wiring and other physical constraints, sensing at the positions desired by users is often unfeasible, hindering optimal condition monitoring.
Sensors, edge AI and networking integrated into an ultracompact sensor module solution
TDK has developed i3 Micro Module, the world’s first sensor module with built-in edge AI*2, overcoming the two aforementioned challenges.
i3 Micro Module integrates various sensors (vibration, temperature, sound, pressure etc.), edge AI, and mesh network*3 functionality into a single unit, facilitating data aggregation, integration and processing, which had been difficult in the past. Because it is an ultracompact, batterypowered wireless sensor module, users can achieve sensing at any desired position without physical constraints like wiring. This dramatically facilitates the prediction of anomalies in machinery and equipment, enabling an ideal Condition Based Monitoring implementation.
Numerous benefits are brought to the manufacturing floor, such as monitoring through visualized equipment information instead of relying on manpower, understanding the health of machinery and equipment to help extend their lives, and minimizing production downtime by preventing unexpected failures—thereby contributing to establishing an ideal predictive maintenance system.
The great potential of sensor modules empowered by edge AI
Battery-powered module products like i3 Micro Module require advanced technology to miniaturize and integrate sensors and wireless communications, and to optimally control everything inside the module in a power-efficient manner. The miniaturization and integration of such components and power-saving control were made possible by applying technologies cultivated through the vast experiences with electronic components and batteries, TDK’s core products. TDK has also long been conducting research and development on edge AI as an applied technology that builds on its sensor products, successfully developing the world’s first sensor module with embedded edge AI capabilities.
Kazuyuki Endo of TDK Corporation’s Next Generation Products & Solutions Group spoke about the future of i3 Micro Module. “We will continue to incorporate new sensing technologies and power supply technologies like solidstate batteries while we expand the range of applications, and integrate them into even smaller packages so that they can be embedded in all kinds of equipment. We also plan to further mature the embedded edge AI to enable it to continuously learn the situation at the point of installation and make autonomous decisions, thereby evolving the module to be able to support the types of advanced decision-making required at the forefront of integration.”
TDK is also envisaging offering i3 Micro Module to its customers as a solution that incorporates cloud integration. Through advanced software and hardware development and integration, TDK will continue to help bring next generation smart factories to life.
The future of i3 Micro Module: A module that supports advanced decision-making
TDK will continue to incorporate new sensing technologies and power supply technologies like energy harvesting and solid-state batteries while expanding the range of applications, and integrate them into even smaller packages so that the modules can be embedded in all kinds of equipment.
www.tdk.com
The new Bulletin 855R industrial beacons from Rockwell Automation can improve how industrial operators deliver warnings and status indications to workers on the plant floor.
The family of 110mm industrial round beacons offers enhanced performance compared to other beacon lines and can meet a broader range of signaling needs.
A single Bulletin 855R beacon can offer both audible and visual indication, which can help prevent confusion on the plant floor in the event of a critical machine or equipment condition alert. And with multiple light-pattern options and multiple mounting options, the beacons can be used for a diverse mix of signaling applications.
Operators can reduce maintenance costs thanks to the Bulletin 855R line’s use of maintenance-free LED technology. They can also drive down inventory costs by using one beacon family to signal up to three different machine or equipment conditions.
Other new features and functionalities of the 855R beacon family that can help operators get more from their investment include:
• The ability to provide up to 15 unique DIP switch selectable light patterns in groups of seven.
• Multicolor functionality, with the ability to produce up to seven colors in one device.
• Two profile options: “high lens” for traditional beacon applications or “compact lens” for space-critical installations.
• High-brightness functionality to maximize contrast in highambient-light environments or outdoor applications.
• An audible mounting base that’s compatible with all LED beacon modules and can produce up to three different audible outputs from a 32-tone table.
All 855R devices are available in 24V DC, 120V AC, or 240V AC global ratings. The 855R product family is certified to meet cULus, CE, KCC, RCM, UKCA and Morocco requirements for global applications. A high IP66/67 and UL Type 4/4X/13 ingress protection rating makes the product family suitable for indoor or outdoor industrial signaling applications.
The 855R beacon line is available now as separate components or as complete pre-assembled beacons to maximize flexibility.
www.rockwellautomation.com