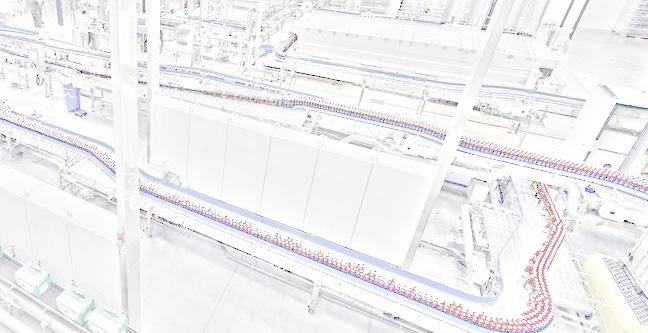
6 minute read
SPECIAL ARTICLE
How Inspection Solutions Help Maximize Food & Beverage Productivity
Raymond P. Shead. Product Marketing Manager. FILTEC, Torrance California, USA
Advertisement
Container inspection systems are a key manufacturing component for the food and beverage industry. They help improve both quality and productivity by detecting defects quickly to reduce waste and downtime, while protecting consumer health, legal compliance the brand name.
Auratectm Pressure Inspection
Empty Can Inspection Fill Level Inspection
QuadViewTM Closure Inspection Compact Inspection Enclosure
Full Pack Inspection Vision Enclosure
INTELLECT also provides complete connectivity from the plant floor (PLC, SCADA) to manufacturing execution systems (MES) with flexible open integration tools. Communication protocols include Modbus TCP/IP, OPC UA and OMAC Weihenstephan. Inspection data is logged by each INTELLECT solution and transferred to the MES platform for further analysis and plantwide reporting.
Figure 1: INTELLECT Advanced Intelligent Inspection Platform Inspection Solutions Overview The food Introducing FILTEC Inspection and beverage industry prides itself with Technologies quality, safety and brand image. As they often operate at tight margins, it is To meet the needs of today and the imperative they run efficiently using future, inspection systems need to be the latest inspection solutions. These modular so that they can be combined solutions help maximise quality through to provide a range of solutions at each continuous, high-speed container in- stage of production. Each solution perspection that provides process visibility forms critical inspections of every conand analytical tools to deliver consistent, tainer using fast sensing and high-speed high-quality products. The tangible image capture to either accept or reject benefits from these solutions also in- them according to quality standards clude: FILTEC’s INTELLECT Container In- The elimination of substandard con- spection Platform (Figure 1: INTELtainers at source LECT Advanced Intelligent Inspection - Reduced product give-away with precise Platform ) addresses these needs with fill level measurement its comprehensive family of unique - Consistent product appearance and inspection solutions that integrate correct, compliant labelling measurement, inspection and control - Reduced closer and seamer jams and technologies to examine each container. line downtime Intelligent INTELLECT modules utilise - Prevention of incorrectly pressurized three principal technologies to inspect containers from being shipped and track each container: vision, photon - Elimination of low fill level and in- and sensors. Vision modules inspect each complete packaged cases container for fill level accuracy, closure integrity, label attributes and many Inspection solutions significantly reduce more properties. Photon technologies substandard quality at each stage of measure container fill levels when the production, while value-add produc- content is not visible, while Sensor tivity is increased through reduced modules examine each container for downtime, product give-away and ex- damage and the presence of foreign pensive non-recyclable rejects. objects. Powerful processors perform each inspection with speed and precision to ensure that the quality specifications and productivity goals are met.
Choosing an Inspection Solution
Losses at any stage through production can result in irrecoverable rejects and value add losses. Therefore, the criteria for selecting a particular type inspection solution may include a range of considerations including the incoming container quality, fill level variation, capping integrity, label appearance and packaging integrity. The choice of an inspection solution also depends on the location where there are unacceptable line losses, or where there is a productivity ‘bottleneck’.
FILTEC’s family of intelligent INTELLECT solutions solve a multitude of inspection challenges from the de-palletizer/de-crater through to the filler, closer, pasteurizer, warmer, cooler, labeller and packing operations.
Precise Inspection Modules
INTELLECT modules are factory calibrated prior to shipment then verified on site for accurate, repeatable measurement. Their rugged design coupled with robust calibration algorithms ensures that each inspection and measurement is insensitive to product composition variation. There is zero electronic drift, resulting in precise, reliable measurement performance, helping build operator confidence and high system utilization for best results.
Available Food & Beverage Inspections
The following inspection solutions and their benefits represents some of the more common ones that are in use today:
- Empty Can Inspection (ECI): Is an intelligent automated machine vision system that tracks and inspects every incoming container to prevent damaged or contaminated cans reaching the filler and seamer. Vision technologies examine the shape, and condition of the empty cans such that only highquality cans enter the process. This ensures that the downstream filling and seaming processes can work at the highest efficiency to reduce downtime due to jams and increase production efficiency.
- Vision Sorting Solution for Empty Bottles. Vision technologies examine the shape, size and condition of bottles so that only correct, high-quality bottles enter the process. This ensures that downstream filling, closure and labelling processes work properly and at the highest efficiency.
- Filler Management Solution: For cans and bottles comprises four applications that includes fill level, filler valve monitoring, sampling and filler performance analytics. The Solution tracks each container through the filler and closer or seamer and inspects the fill level, removing each non-conforming container. Quantitative Analysis application analyses the fill level performance of each filler valve to pinpoint faulty and non-performing filler valves (Figure 2) .
- Compact Vision Closure Inspection for Bottles: Vision technologies identify all closure defects including skew & broken caps, skirt condition, bull nose defects and broken tamper bands. This helps ensure consistent, accurate and safe container closure.
- Vision Pressure Inspection for Bottles and Cans: Ultra high-resolution cameras and laser optics provide an accurate 3D topography image of the closure area. A sophisticated application detects any deformations in the closure due to pressure variation. The inspection and removal of leaking containers prevents sealing failures, product contamination and consequential collapse of packaged cases.
- Vision Shrink Sleeve Inspection: This inspection detects label quality defects including sleave positioning, bar code presence and label damage. This helps reduce waste by alarming and rejecting defectively labelled containers from proceeding further down the production line. - Full Pack Inspection: Inspection technologies are applied at the packing stage of manufacture to ensure that each pack has no missing or grossly underfilled containers that are also neither damaged nor leaking.
Return on Investment from Inspection Solutions
Automated inspection solutions improve operations through continuous, high-speed inspection of empty containers, full containers, labels and cases. They improve both quality and productivity through process visibility and process analysis that helps pinpoint maintenance requirements to optimize the process. For example, a Filler Management Solution (Figure 2) operating on a can line running at 1200 cans per minute can return an estimated $225,000/year just through reduced underfilling, reduced sampling time and reduced downtime.
- Vision Shrink Sleeve Inspection: This inspection detects label quality defects including sleave positioning, bar code presence and label damage. This helps reduce waste by alarming and rejecting defectively labelled containers from proceeding further down the production line. In summary, INTELLECT Inspection Solutions contribute toward greater value-add productivity. They help produce consistent, high-quality products with reduced waste and customer returns that protects both the brand and customer loyalty.
- Vision Glue-On Label Inspection for Bottles: Applications include paper, plastic and ceramic labels where the discrete neck and body labels cover part of the container. The inspection capabilities cover over twenty different label conditions, helpin produce uniform appearance and improved quality with the rejection of defectively labelled bottles
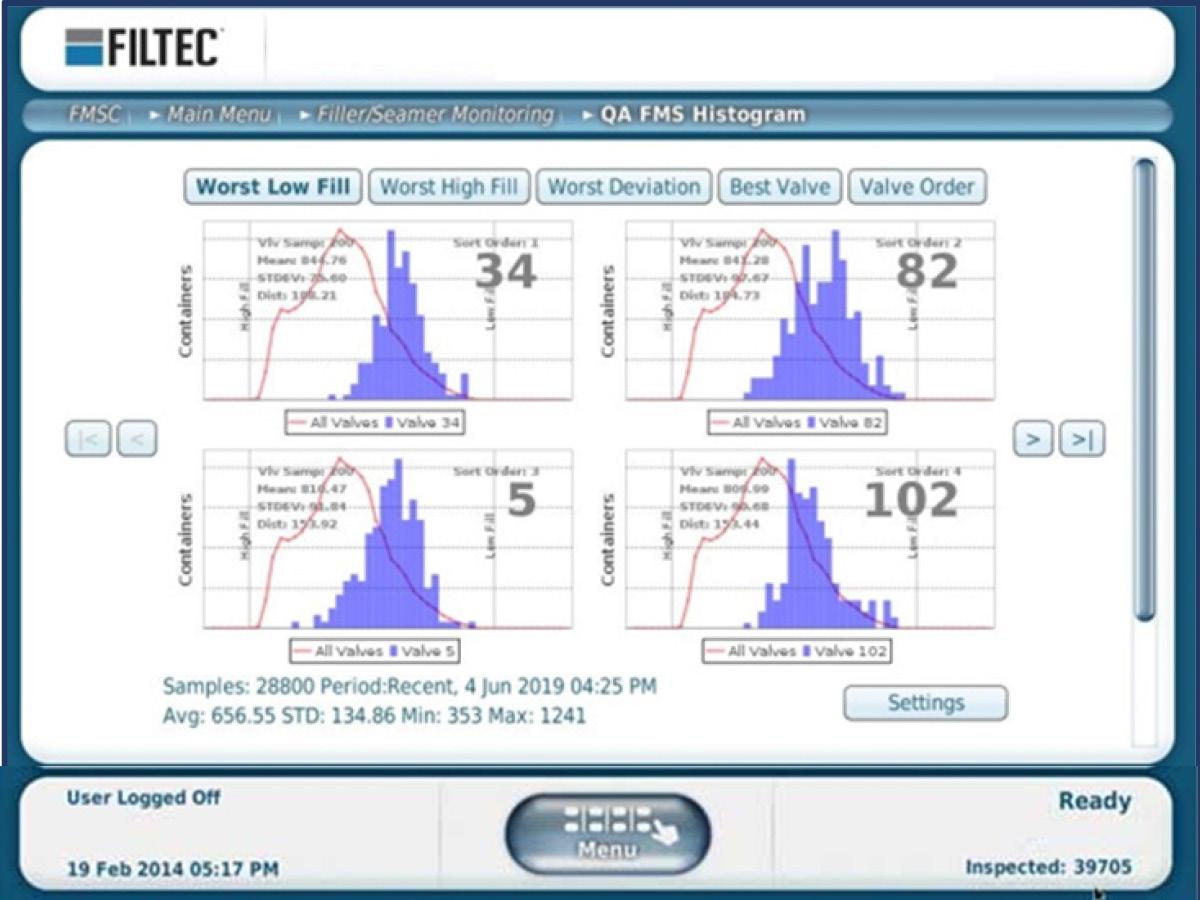