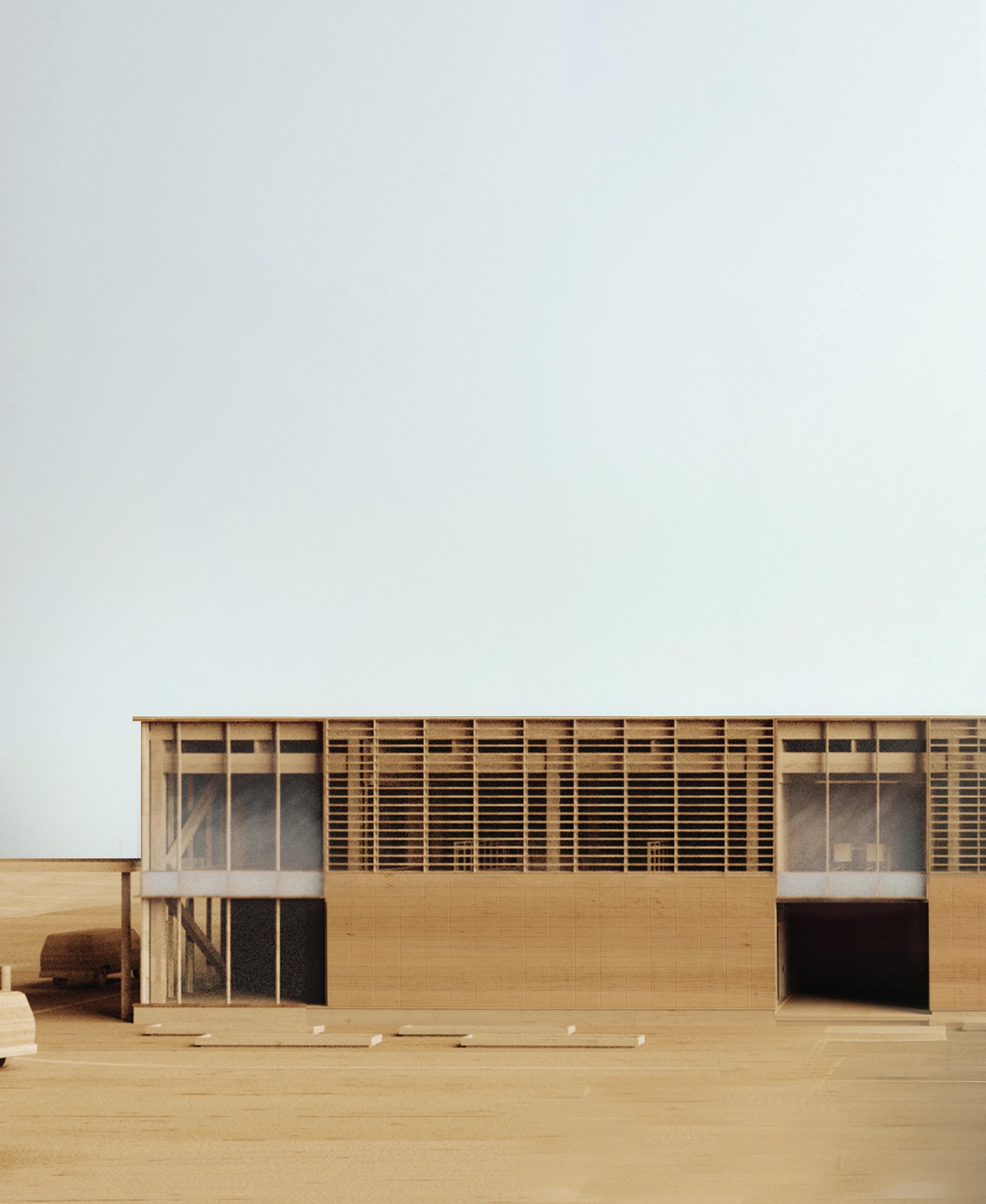
14 minute read
CHALK RIVER LABORATORIES
INNOVATION HUB
THREE NEW BUILDINGS AT THE CHALK RIVER LABORATORIES CAMPUS DEPLOY MASS TIMBER AND AN IPD TEAM TO DELIVER INNOVATIVE RESULTS.
PROJECTS Canadian Nuclear Laboratories (CNL) Site Entrance Building, Support and Maintenance Facility, and Science Collaboration Centre, Chalk River, Ontario ARCHITECT HDR, as part of CNL IPD NB Poly Party Team TEXT Leland Dadson PHOTOS Kevin Belanger, courtesy CNL IPD NB Poly Party Team, unless otherwise noted In February 2020—during simpler pre-pandemic times—I had the rare opportunity to visit the construction sites for a series of three projects by HDR at the Chalk River Laboratories Campus, about 200 kilometres northwest of Ottawa. The innovation taking place at Chalk River relates not only to nuclear energy, but also, surprisingly, to two trends in architecture: mass timber construction and integrated project delivery (IPD) team processes.
Science of Tomorrow The Chalk River campus sits on unceded Algonquin Anishinabek territory, on a picturesque 3,700-hectare plot at the edge of the Ottawa River. The site is relatively remote—a choice that was likely strategic when the facility was established in 1944. Today, security remains a critical concern, given the sensitive nature of work and material on site. Chalk River Laboratories has had a rich and complex history of nuclear research since its establishment under the purview of Atomic Energy of Canada Limited (AECL), a federal Crown corporation. Canadian Nuclear Laboratories (CNL) now manages and operates the site on behalf of AECL. Among other things, Chalk River Laboratories was engaged in the operation and sales of CANDU reactor technology, as well as the production of a meaningful percentage of the world’s supply of radioactive isotopes for medical use.
Today, it is among Canada’s key sites focused on technological innovation to support clean energy technology, including materials research and sustainable power generation. For instance, Chalk River’s vision for a Clean Energy Demonstration, Innovation and Research Park (CEDIR) is focused on advancing low-carbon hybrid energy generation systems, including small modular reactors. That spirit of innovation also shows in the campus’s recent approach to planning and architectural development.
Fostering a Campus In 2017, CNL engaged HDR and Urban Strategies to develop a master plan for the campus, envisaging how, in parallel with its broadening research, the physical fabric of Chalk River Laboratories might become more like a university-style science and technology campus. Despite the secure nature of the work on site, there was a goal to foster a sense of public space that would support Chalk River’s academic-based community of researchers. Toward this goal, the plan considered key metrics such as walkability, health, security, safety and wellness. Ultimately, the master plan recommended investment in site infrastructure, and the addition of several new buildings, which would be coordinated with the decommissioning of aging facilities.
HDR was retained as the lead architect for the first phase of this work, which included the construction of three key buildings, all of which are now complete or underway.
The completed 4,650-square-metre Site Entrance Building serves as the public face for the Chalk River Laboratories, with a smaller front volume providing refined spaces to welcome both visitors and staff, and a larger section behind that supports procurement, warehousing and logistics services across the entire Chalk River site.
The similarly sized Support and Maintenance Facility provides flexible open space, allowing a consolidation of resources to support both maintenance and manufacturing activities. When I visited, this building was at an earlier point in construction, providing the tour with a very clear reading of its structural elements in isolation.
The Science Collaboration Centre was not yet out of the ground in early 2020, but is now well underway. This will be largest of the three buildings, providing six storeys of multi-use space that includes large, open plan studios. Once complete, it will act as the campus heart, offering the site’s most outward architectural expression of innovation.
Mass Timber Fortune Early concept schemes for the three buildings proposed sculptural forms that would not look out of place on a forward-looking university campus. They would be poised to capture architectural design awards—but perhaps not yet grounded in the spirit of innovation of Chalk River Laboratories.
The introduction of mass timber as a structural element—at the suggestion of the client—was clearly a turning point in the evolution of the buildings’ design. HDR design principal Donald Chong was no stranger to wood. Prior to joining HDR, Chong was one of three partners at Williamson Chong Architects (now Williamson Williamson), and he shared the Professional Prix de Rome for the firm’s research project, Living Wood. The prize enabled the firm to travel internationally to visit manufacturers and designers working on the cutting-edge of crosslaminated timber (CLT) technologies.
Chong built the sustainability case for Chalk River by highlighting mass timber’s ability to both divert carbon (by replacing materials such as concrete and steel) and to sequester carbon (a function inherent to the natural growing process of trees). A Sankey diagram served to illustrate the impact—using metric tonnes of carbon as a measure that could be easily understood by all parties—and helped to secure roughly $4 M in funding through the Green Construction through Wood (GCWood) program, administered by National Resources Canada (NRCan).
IPD Serendipity Perhaps serendipitously, this development roughly aligned with the introduction of Integrated Project Delivery (IPD) to the project, through the involvement of constructor Chandos, a pioneer in the field. IPD is a process in which the project’s owner, contractor, designers, key consultants and trades explicitly agree to share in the project’s risk and
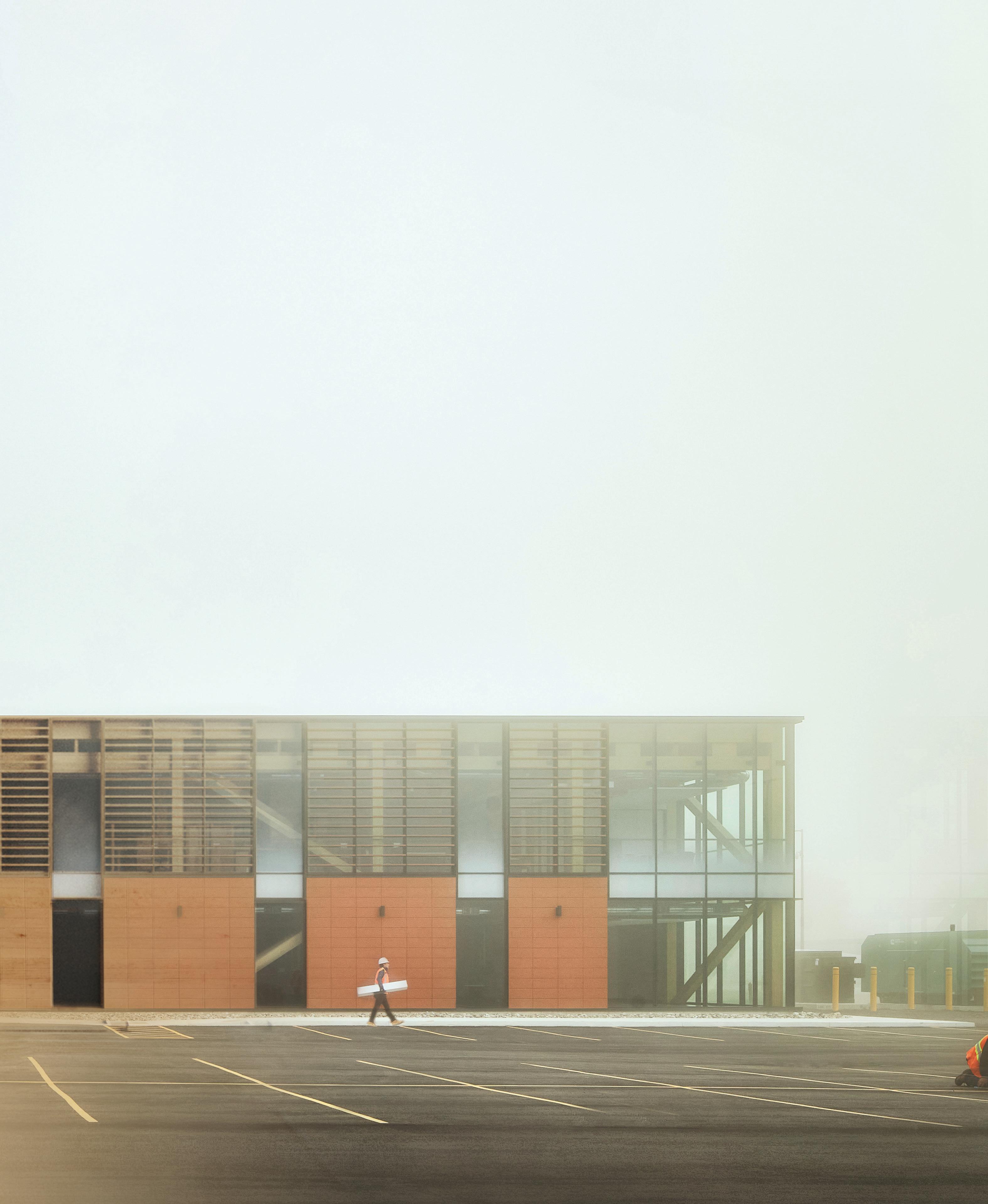
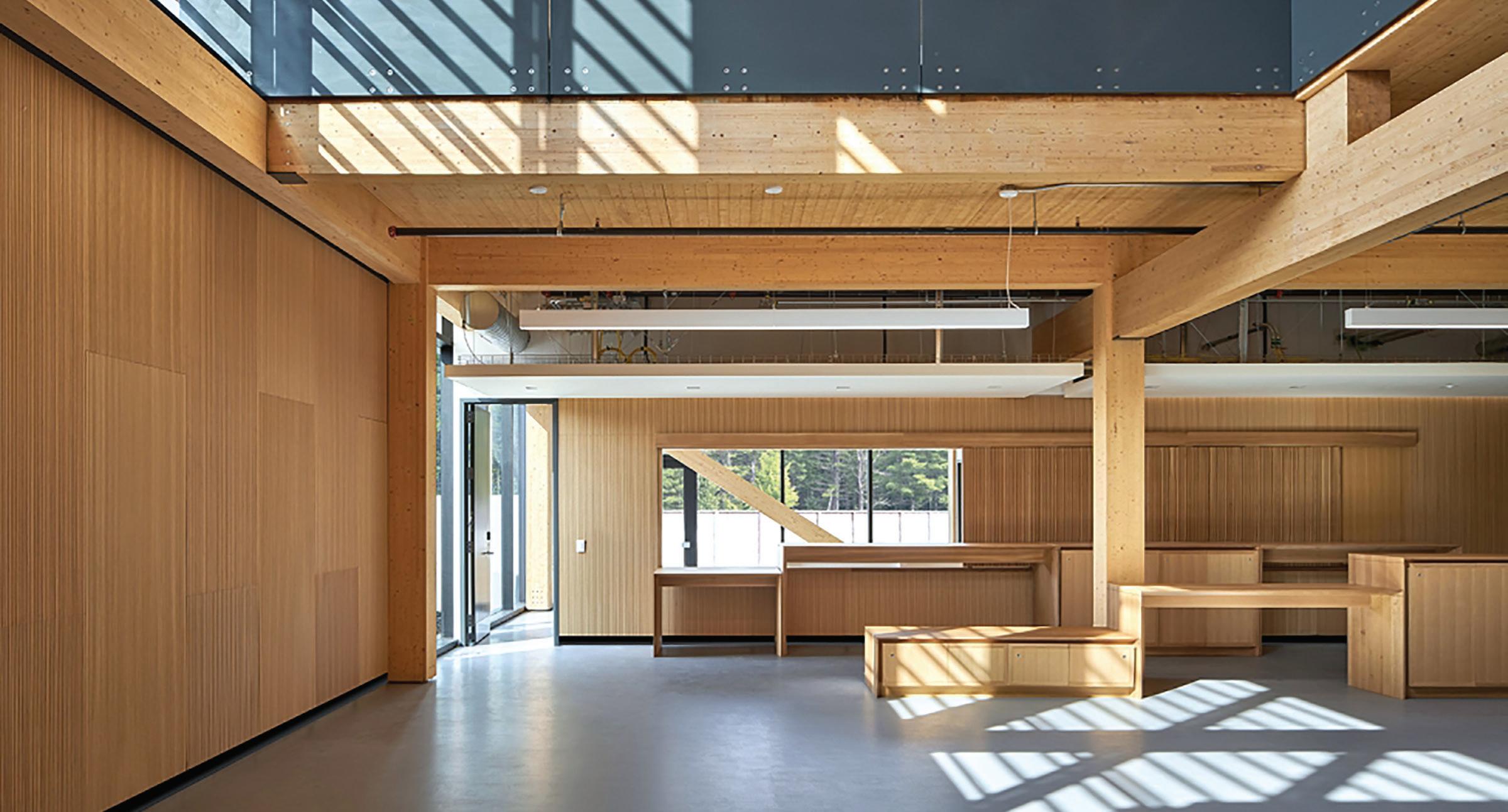

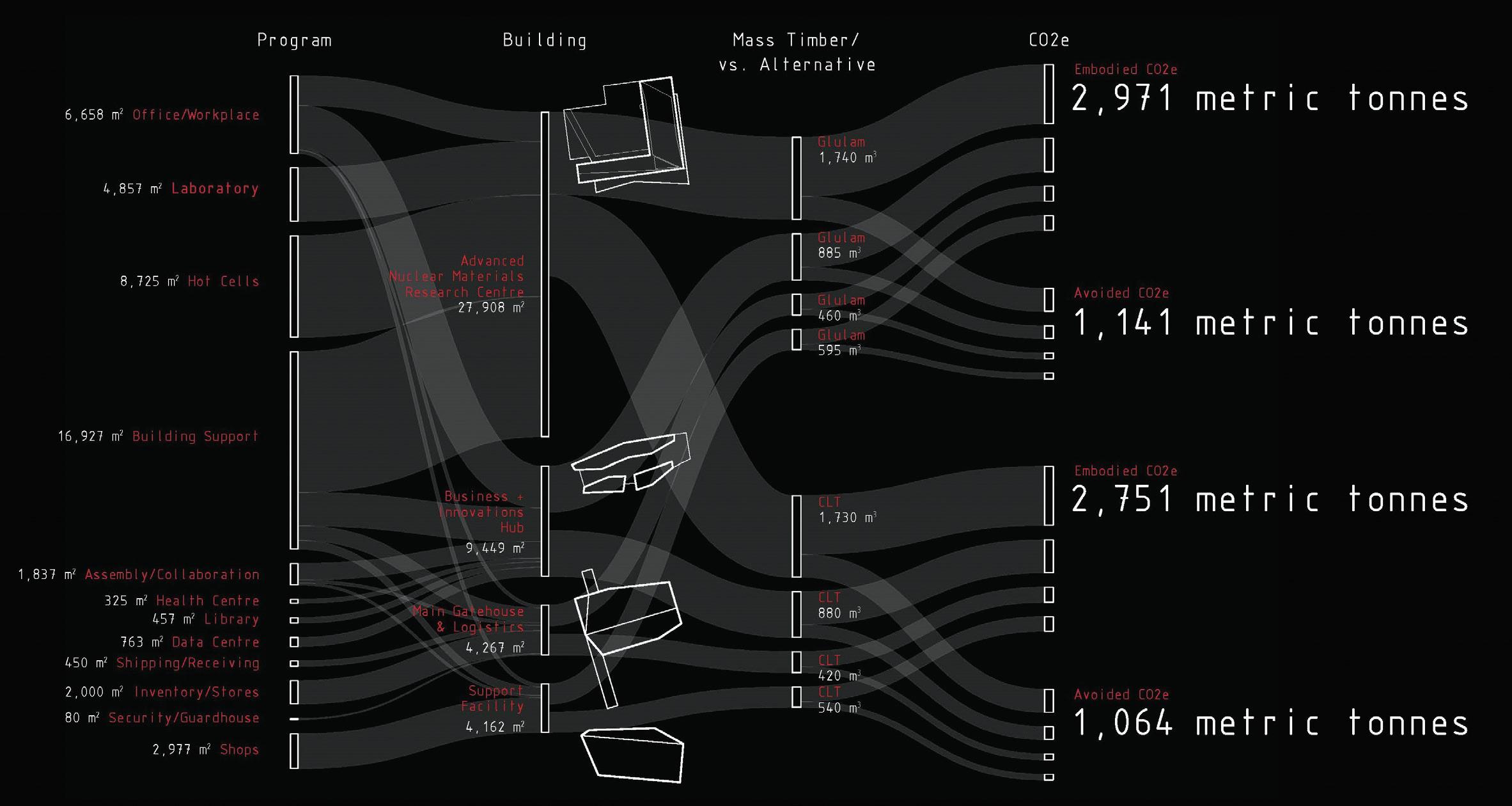
PREVIOUS SPREAD An image of the Site Entrance Building blends model and photograph, showing the accuracy inherent in working with an IPD process and prefabricated mass timber. OPPOSITE TOP Inside, dropped ceilings are minimized, acting as service trays for principal HVAC system components. OPPOSITE BOTTOM The carefully considered spacing of columns allows for a flexible configuration of the building’s work and collaboration spaces. ABOVE Early in the IPD process, architect Don Chong made the case for mass timber by using a diagram that indicated the carbon-reduction impact of using wood.
reward. If managed effectively, it creates a collaborative and transparent mechanism for decision making—particularly for complex and innovative projects, such as those at the forefront of wood construction technology.
Paired together, IPD and mass timber served to advance the project in ways that were mutually beneficial to all parties involved. In fact, Chong argues that mass timber and IPD needed each other to succeed. It was through the IPD “big room”—a physical or digital space wherein the whole team gathers, breaking down large decisions into smaller ones in a decision matrix, and then putting proposals to vote—that the case for wood was validated.
Though not necessarily binding, the decisions made through this collaborative process speak to a trust in the group’s wisdom, a factor inherent to the success of IPD. It is this trust that fosters an engaged team, with all parties invested, both metaphorically and contractually.
In the case of Chalk River, the team collectively found that the premium on the cost of wood (compared to steel or concrete) was offset when broadening the comparison to consider factors such as fire protection, interior finishes and speed of construction.
Mutually Beneficial Beyond the initial confirmation to proceed with mass timber, IPD also allowed for critical collaboration between trades, suppliers and the design team to help de-risk the material selection. While wood construction is ancient, mass timber is relatively nascent, and requires early, detailed, and ongoing information regarding price, supply, and available technology in order to take advantage of key benefits, such as speed and accuracy of construction.
Nordic Structures acted as the trade partner in the integrated team, and early on, toured the team through its dedicated forest lot and factory operation. Throughout the process, they continued to provide a depth of knowledge that would otherwise have been absent from the team. This included such details as offering analyses of the grain structure within their black spruce tree stock, which informed explorations into routing out material from structural members. During design and construction, Nordic worked within the studio-like IPD big room, collaborating closely with key members, such as structural engineers LEA Consulting, to optimize the design to the specificities of their supply chain.
Another early example of big room collaboration was in establishing the spacing of the column grid. By seeking input from all parties—from the mass timber supplier to the furniture systems manufacturer—the team optimized the grid to best meet spatial, structural, envelope, services, and fabrication requirements simultaneously. Whether through IPD or a different contractual relationship, early interaction with suppliers such as this is crucial for the success of any mass timber project. This was true before the pandemic—and is even more true now, as the wood market continues to experience price volatility.
On the other side of the equation, as a new industry, mass timber also allows for a reconsideration of many current construction practices—often for the better. By rethinking sequencing and staging requirements, the construction timeline could be optimized. For instance, the team benefitted from the fact that structural mass timber members and panels can be lifted in place directly from a flatbed truck, with no intermediate staging zone required. Moreover, a successful IPD process demands a high level of precision and accuracy, from the extensive
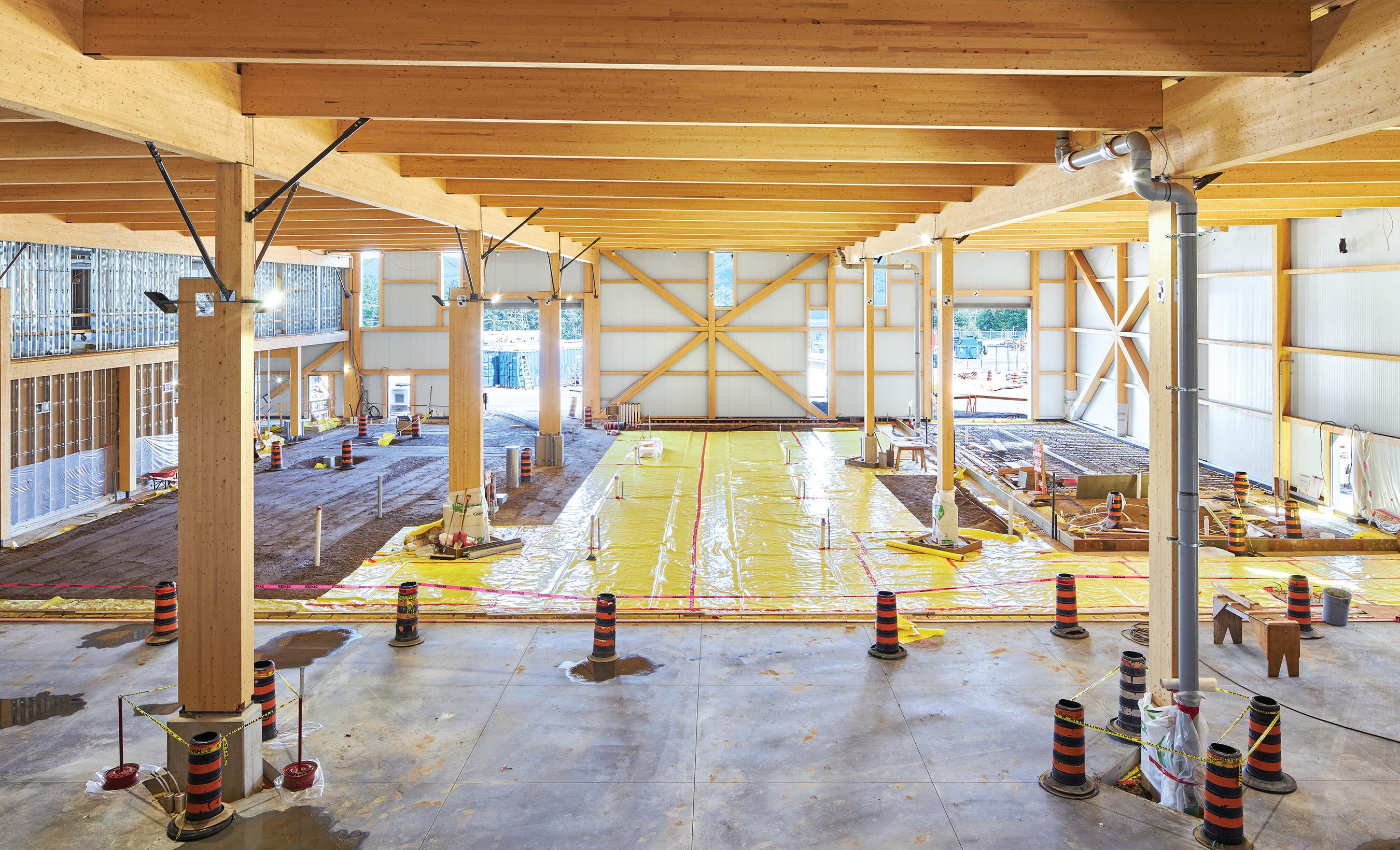
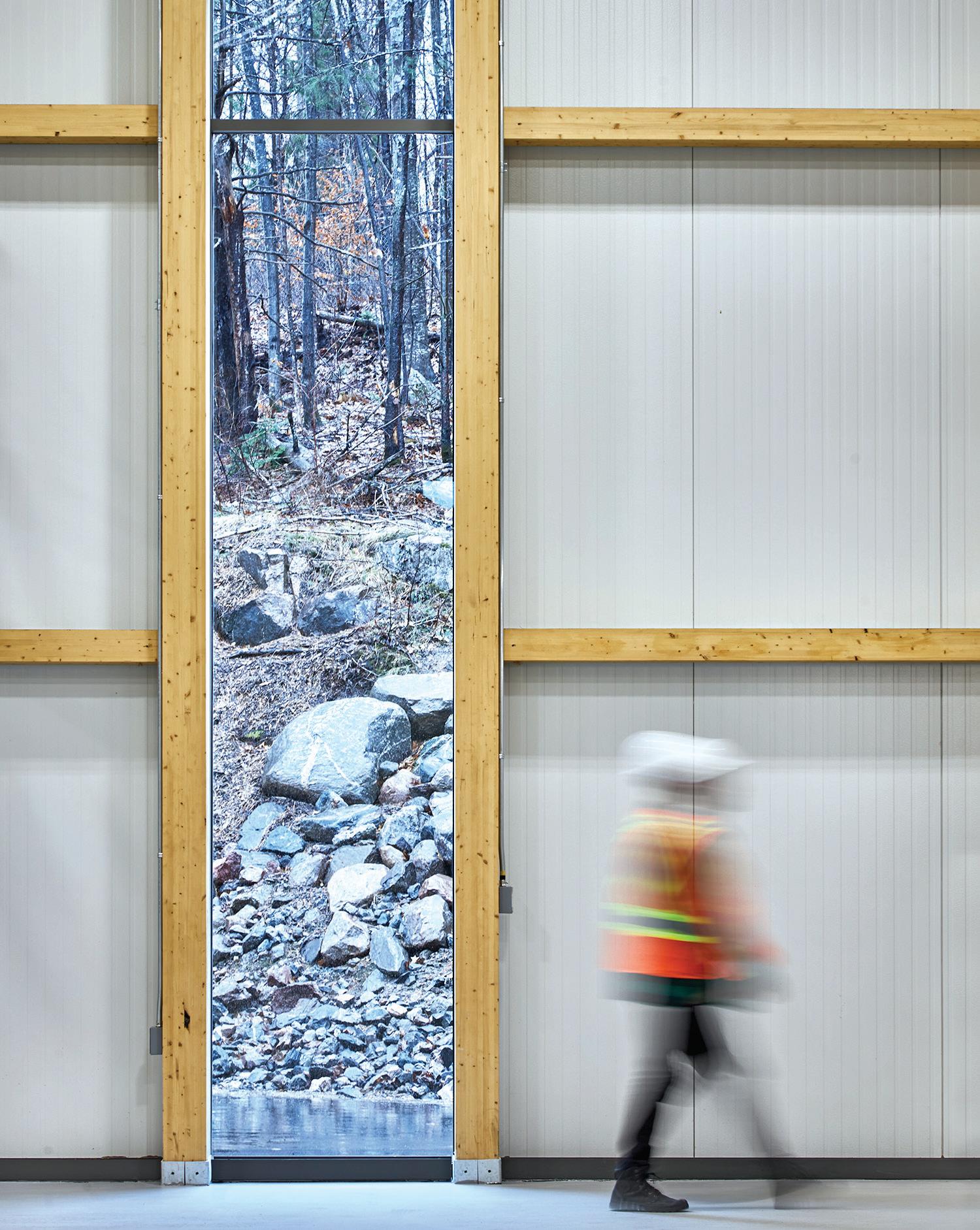
© 2020 KEVIN BELANGER © 2020 KEVIN BELANGER
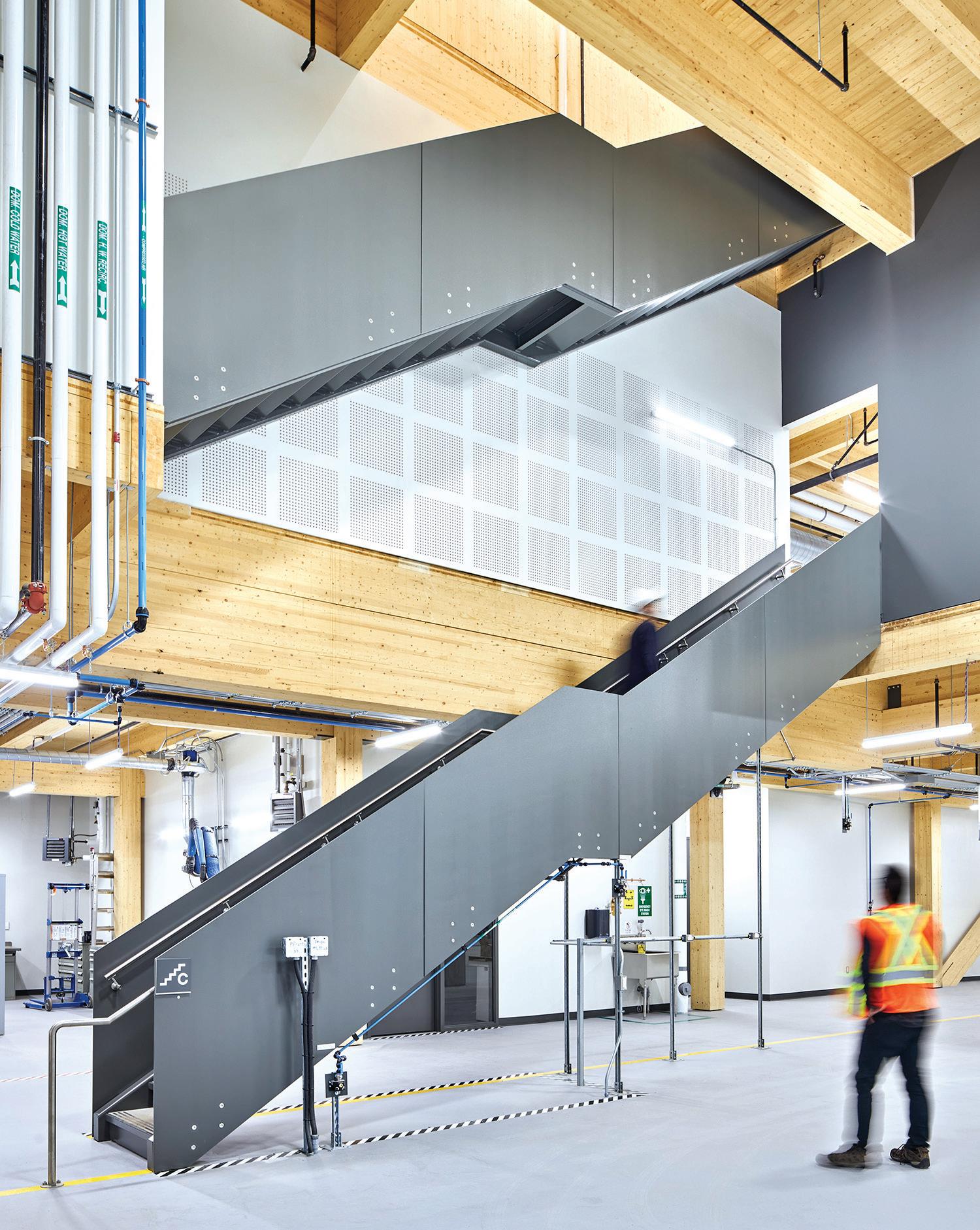
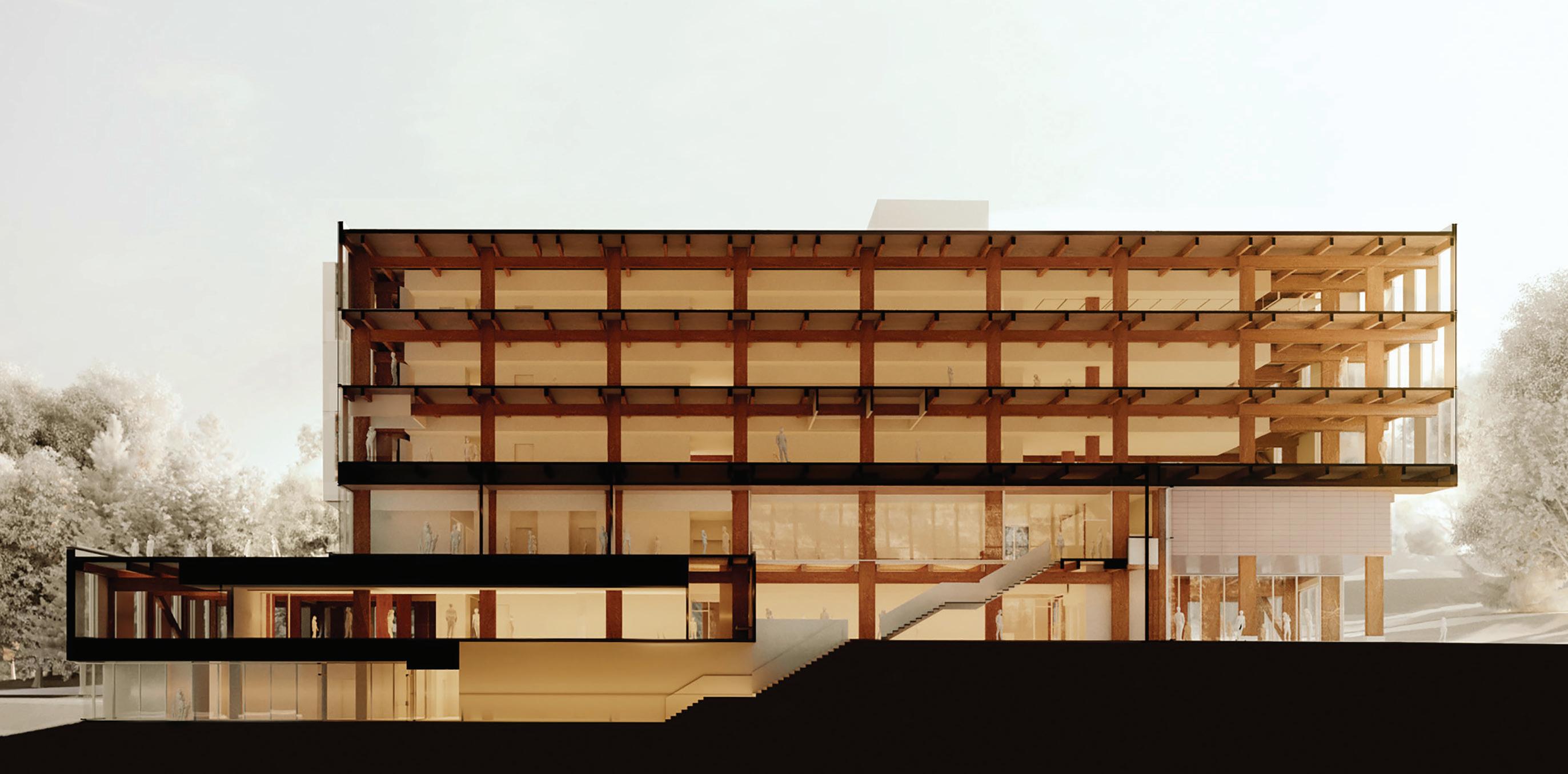
OPPOSITE, CLOCKWISE FROM TOP The Support and Maintenance Facility’s mass timber structure can be clearly seen during construction; office spaces are located in a loft above part of the maintenance and manufacturing area; a slit window provides a view of the Boreal forest surrounding the campus. ABOVE Construction on the largest of the three buildings—the Science Collaboration Centre—is currently underway, with completion expected in 2023.
digital planning stage through to erection. Mass timber is particularly suited to capitalizing from such a demanding coordination process, since the material is prefabricated to very tight tolerances. These types of opportunities encouraged all team members to keep an open mind, and fostered a spirit of innovation throughout the project.
Innovation through Rationalization The integration of mass timber in these three buildings oriented HDR’s design towards rectilinear compositions, focused on building systems and elements. The resulting buildings deliver a high degree of structural legibility, beginning with the articulation of their timber systems. Regular grids of columns also set these buildings up as flexible, futureproof structures that can easily accommodate changes in use.
Above the glulam columns, a system of girders, beams, and purlins is carefully orchestrated to allow for the unimpeded integration of building services tight to the timber deck. To minimize operational energy use, the designs opted to avoid using raised access floors or dropped ceilings for distributing services—the solutions most commonly chosen in mass timber structures. Instead, the three buildings leave mechanical and electrical elements exposed, in keeping with a tradition exemplified in Canadian works by the likes of Barton Myers, Ron Keenberg, and Carmen Corneil.
Small areas of dropped ceiling are present mainly around the core, where principal services—including main duct lines and fan coil units—are grouped. The minimal dropped ceilings act as service trays, and allow for easy side access for servicing or for future adaptation. An array of distribution lines—including ducts, sprinklers and conduit—then run throughout the floorplate. They are aligned parallel to the purlins, and above the larger structural members, in what are essentially service troughs framed by the layered timber structure. Beyond creating an aesthetically appealing and spatially optimized solution, this decision had the added benefit of allowing for more exposed wood structure, saving time and money by reducing finishing and coordination requirements.
Much of the buildings’ structure can be read on the exterior. On the nearly complete Site Entrance Building, the columns clearly establish a visual order that informs the organization of the façade, while the beams and roof structure evoke a building entablature behind the glazing. Drawing inspiration from projects such as Mies van der Rohe’s IIT College of Architecture and Peter Behrens’ Turbine Factory, the elevations are a thoughtful, ordered composition of glazing, ceramic tiles and insulated metal panels. The minimalist façade treatment allows for a strong legibility of the structure, and is in keeping with the concept of flexible open space behind.
Campus as Opportunity for Iteration One key advantage of working through a collection of campus buildings is the ability to iterate, learning from previous designs. Aided by the rigorous tools of IPD, HDR worked to refine their designs, details and techniques as they progressed from the Site Entrance Building, to the Support and Maintenance Facility, to the Science Collaboration Centre. This had a notable impact on the evolution and refinement of the timber construction systems used.
This process is particularly notable in the development of the buildings’ column design.
The evolving design of the structural columns was informed by the thinking that led to a simplified distribution of building systems through the x and y dimensions of the ceiling. Over the course of the three projects,
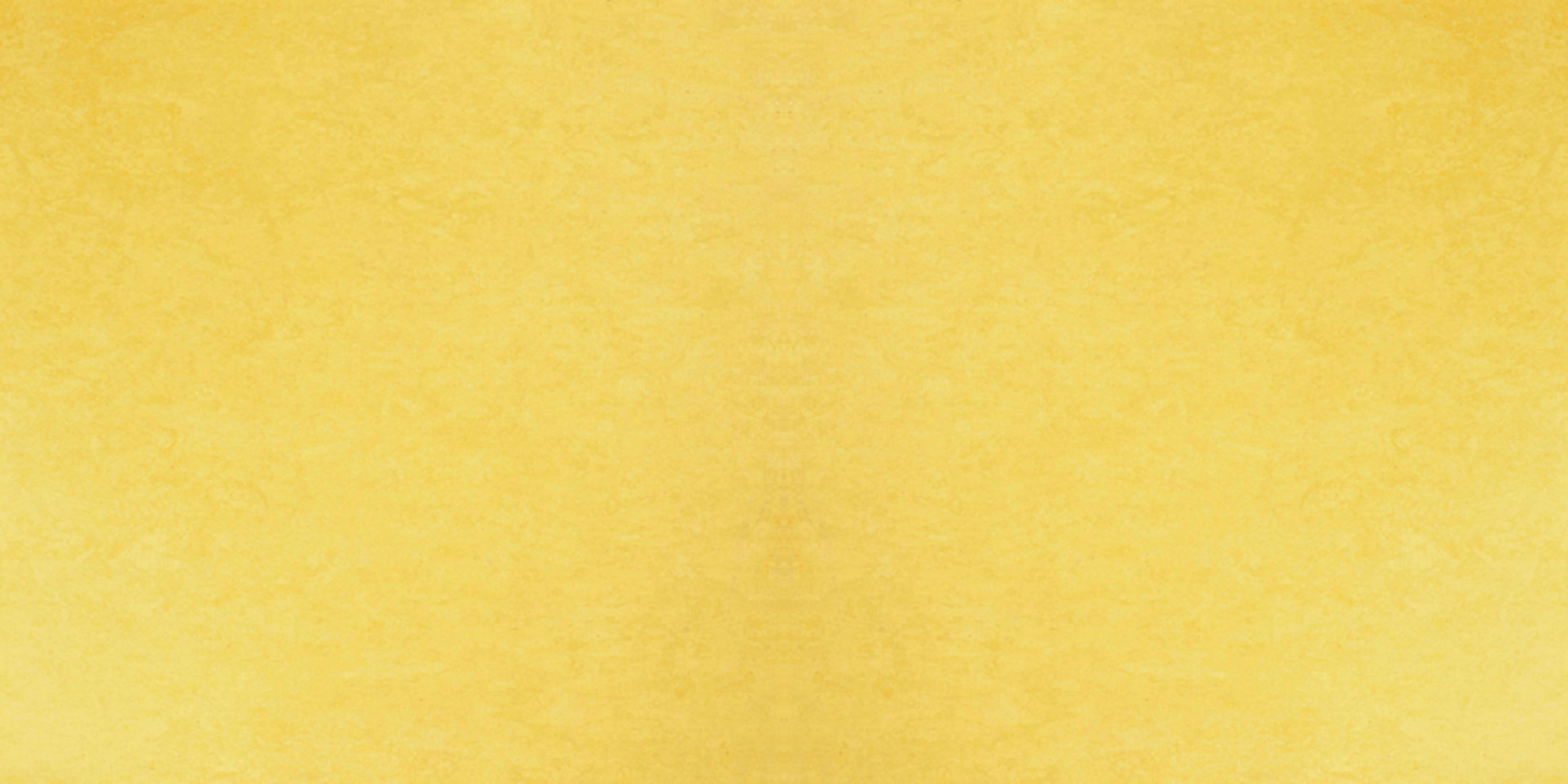
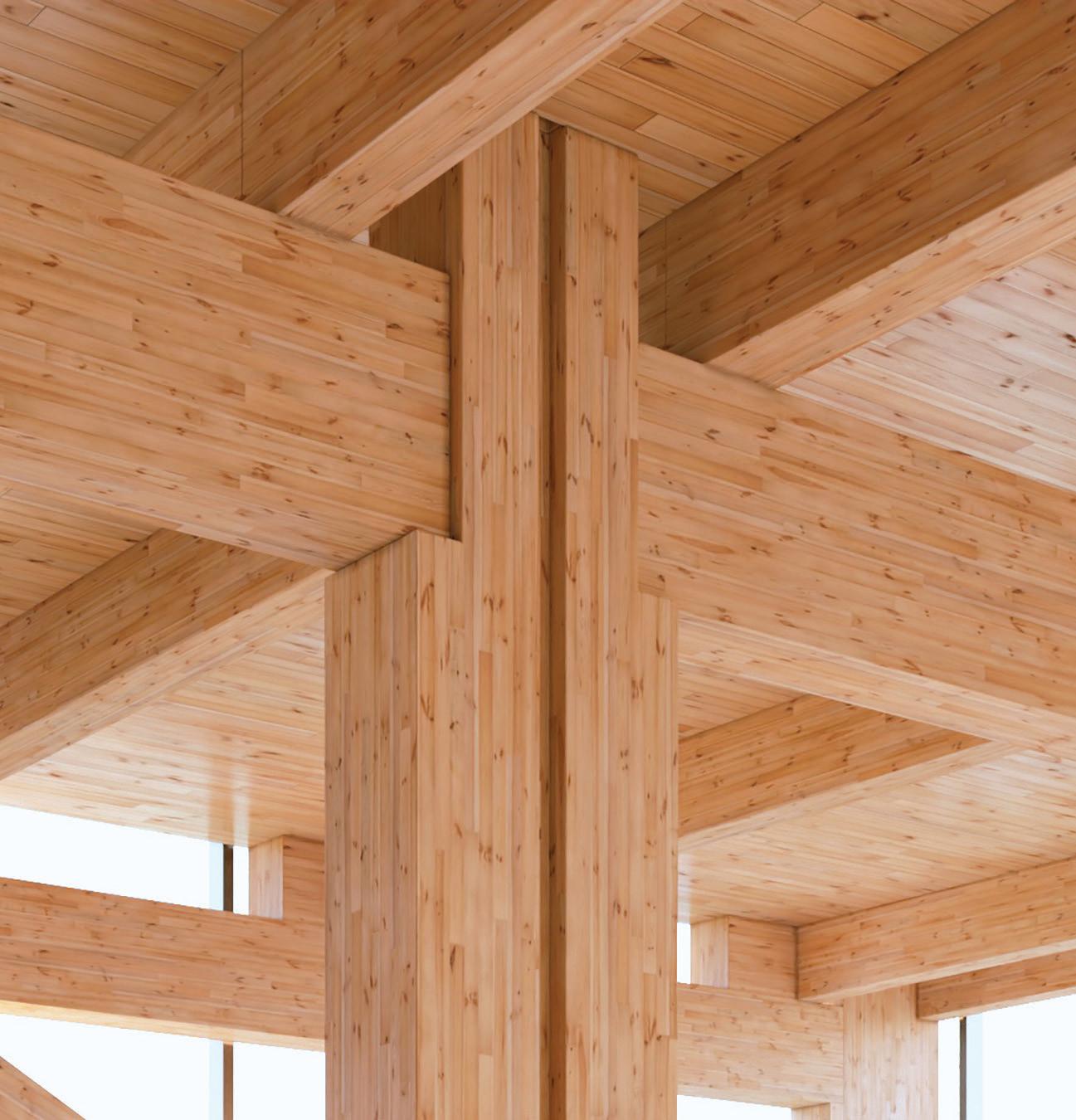
HDR © 2020 KEVIN BELANGER
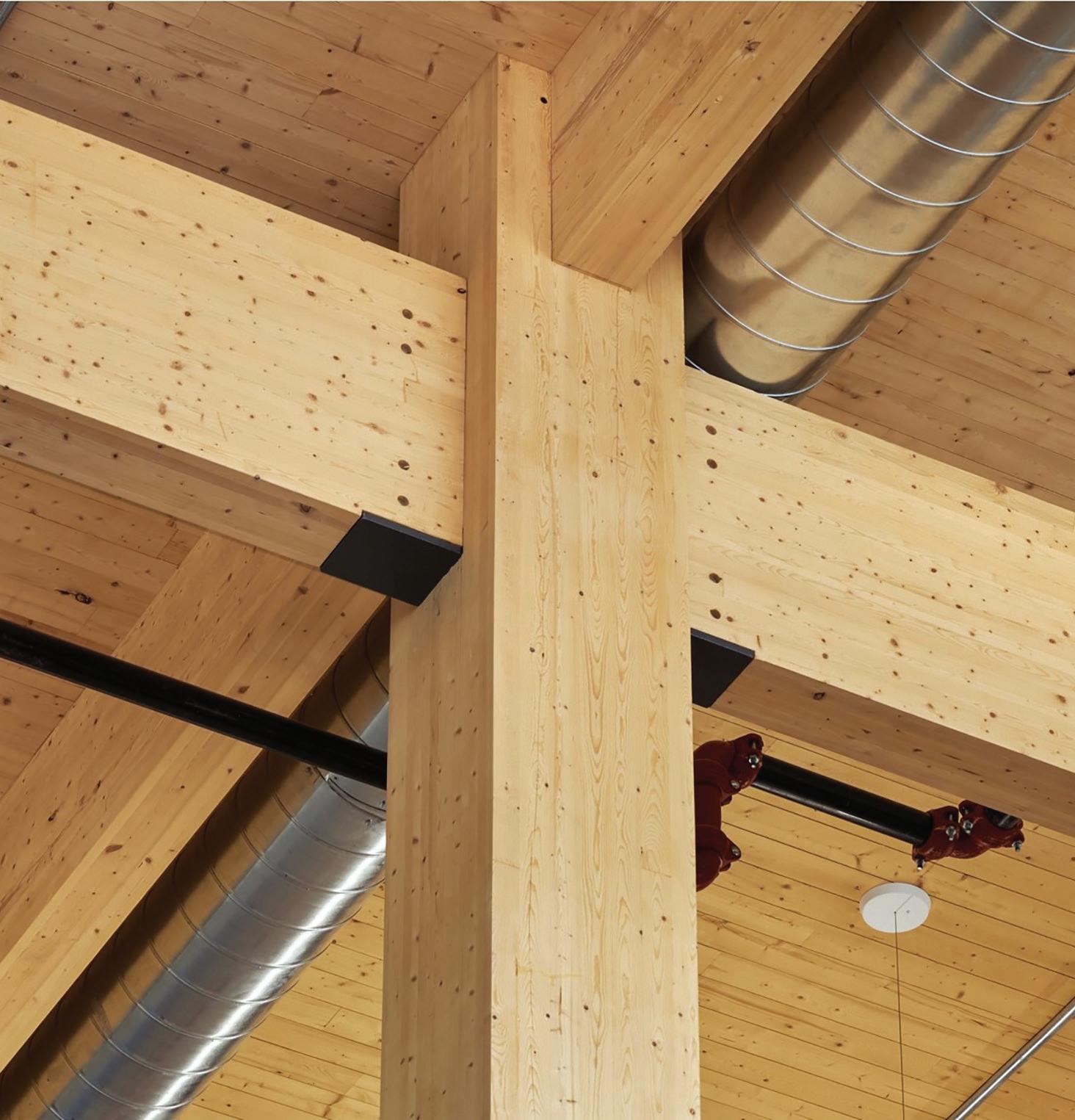
ABOVE The structural column design in the Science Collaboration Centre, at left, has been refined since the initial structural columns were built in the Site Entrance Building, at right. In the newer column design, notches provide bearing support for the beams, while a vertical channel allows for surface-mounted conduit, which continues along the ceiling in a service pathway framed by a pair of purlins.
the column designs came to more tightly integrate vertical pathways for conduit distribution, completing the circuit with the z dimension.
The culmination of this process is the fluted column of the Science Collaboration Centre. Visually, it appears as a split column, which allows for conduit to be surface-mounted within a reveal on its face, in keeping with the exposed aesthetic of the ceiling. This vertical channel also has the advantage of connecting to a space on the ceiling between a pair of purlins. This pair has been reorganized from the Site Entrance Building system—in part to simplify erection and to optimize timber deck spans—but has an added benefit of providing an organized service pathway on the ceiling.
The innovation of the column design goes beyond this, by extending to its interaction with the structural beams. In the Site Entrance Building, the columns used a steel-chair-and-knife plate connection off the side of the columns to support the beams—a very typical connection detail. However, through a cost-benefit analysis, the team determined that the process of erecting the structure could be simplified if the connection was created through the articulation of the column itself. Taking cues from Japanese joinery and barn construction, the team introduced notches at the top of columns to provide the beam bearing support. The result is an elegant detail that simplifies fireproofing strategies and speeds construction.
The three mass timber buildings currently underway at the Chalk River Campus are a study of architectural innovation—in terms of both wood construction systems and the IPD project delivery method. The symbiosis between mass timber and IPD allowed for an active refinement of details that collectively inform an elegant, efficient system for building in wood.
What is the ultimate legacy for this project? Architect Don Chong sees the buildings less as specialized facilities, and more as prototypes for how mass timber can most effectively be deployed for standardized commercial and institutional structures. With an optimized prototype, Chong believes, mass timber buildings could become the brick-andbeam warehouses of the 21st century. HDR’s three buildings will doubtless expand the collective body of timber knowledge—even if few architects are able to visit them—with impacts that may go far beyond the security gates of Chalk River.
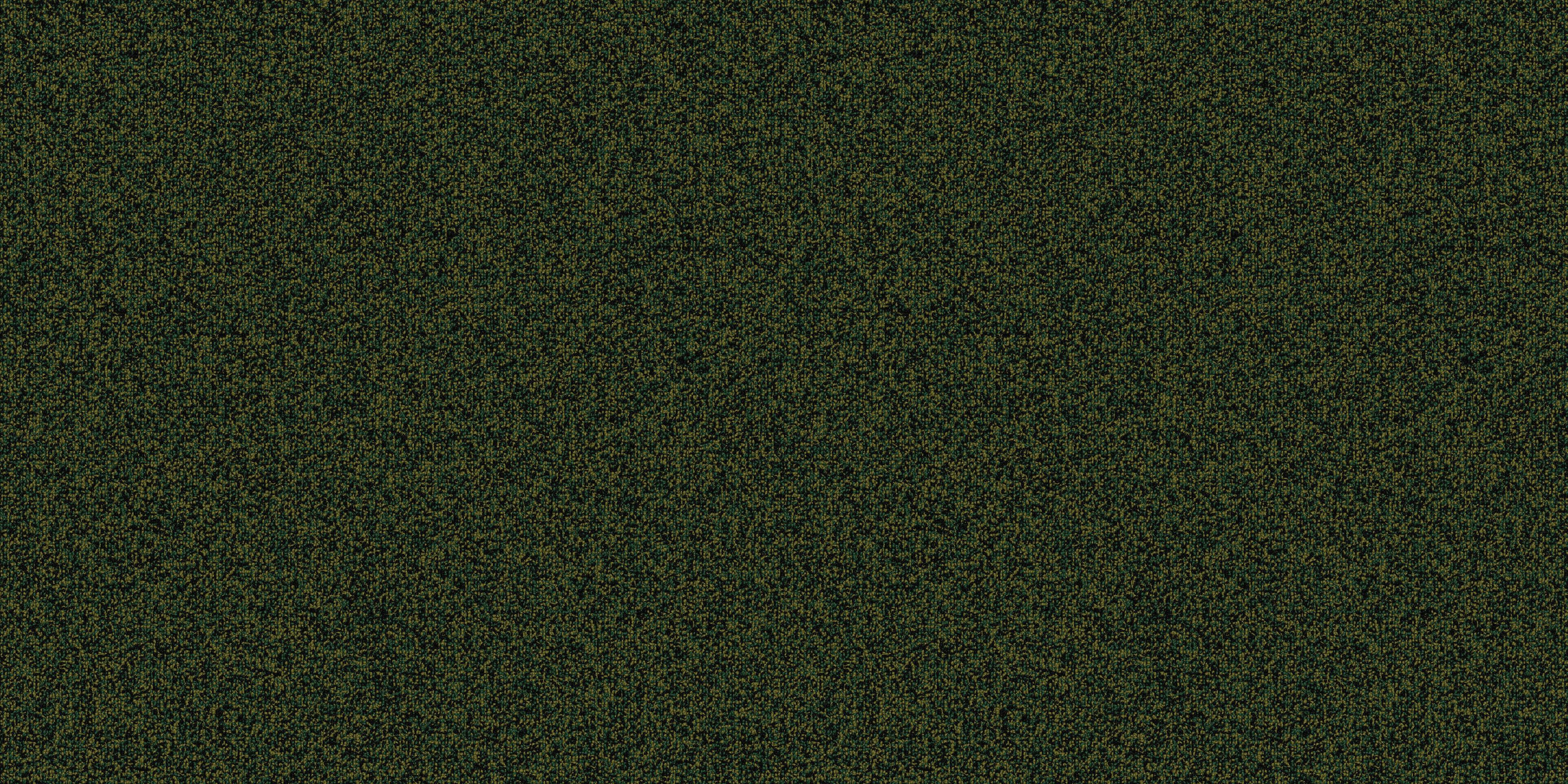
Architect Leland Dadson is a mass timber specialist at MJMA. He is involved with mass timber projects including the University of Toronto Academic Wood Tower (in association with Patkau Architects), and the Queen’s University John Deutsch University Centre Redevelopment (in association with HDR).
OWNER CNL | BUILDER CSJV (CHANDOS SULLIVAN JOINT VENTURE) | ARCHITECT HDR | ARCHITECT TEAM DONALD CHONG, SUSAN CROSWELL, JUSTIN PURDUE, PAUL HOWARD HARRISON, JEREMY VAN DYKE, SOMAYEH MOUSAZADEH, MIN HOO KIM, SEBASTIAN WOOFF, SHELLEY GREENAWAY | STRUCTURAL LEA | MECHANICAL/SUSTAINABILITY INTEGRAL GROUP | ELECTRICAL/CIVIL JP2G | TIMBER NORDIC STRUCTURES | ENVELOPE (BUILDER) FLYNN CANADA | MECHANICAL/ELECTRICAL (BUILDER) JMR ELECTRIC | FRAMING/DRYWALL/CEILINGS (BUILDER) MARCANTONIO CONSTRUCTORS INC. | SYSTEMS FURNITURE (BUILDER) ADVANCED BUSINESS INTERIOR | BUILDING CONTROL (BUILDER) SIEMENS CANADA
SITE ENTRANCE BUILDING AREA 5,016 M2 | ESTIMATED BUDGET $30.6 M | COMPLETION SEPTEMBER 2020 | ENERGY USE INTENSITY (PROJECTED) 101 KWH/M2/YEAR
SUPPORT AND MAINTENANCE FACILITY AREA 4,800 M2 | ESTIMATED BUDGET $32.8 M | COMPLETION MARCH 2021 | ENERGY USE INTENSITY (PROJECTED) 143.3 KWH/M2/YEAR
SCIENCE COLLABORATION CENTRE AREA 8,918 M2 | ESTIMATED BUDGET $62 M | COMPLETION MARCH 2023 | ENERGY USE INTENSITY (PROJECTED) 130.4 KWH/M2/YEAR (WITHOUT DATA CENTRE); 373.8 KWH/M2/YEAR (WITH DATA CENTRE)
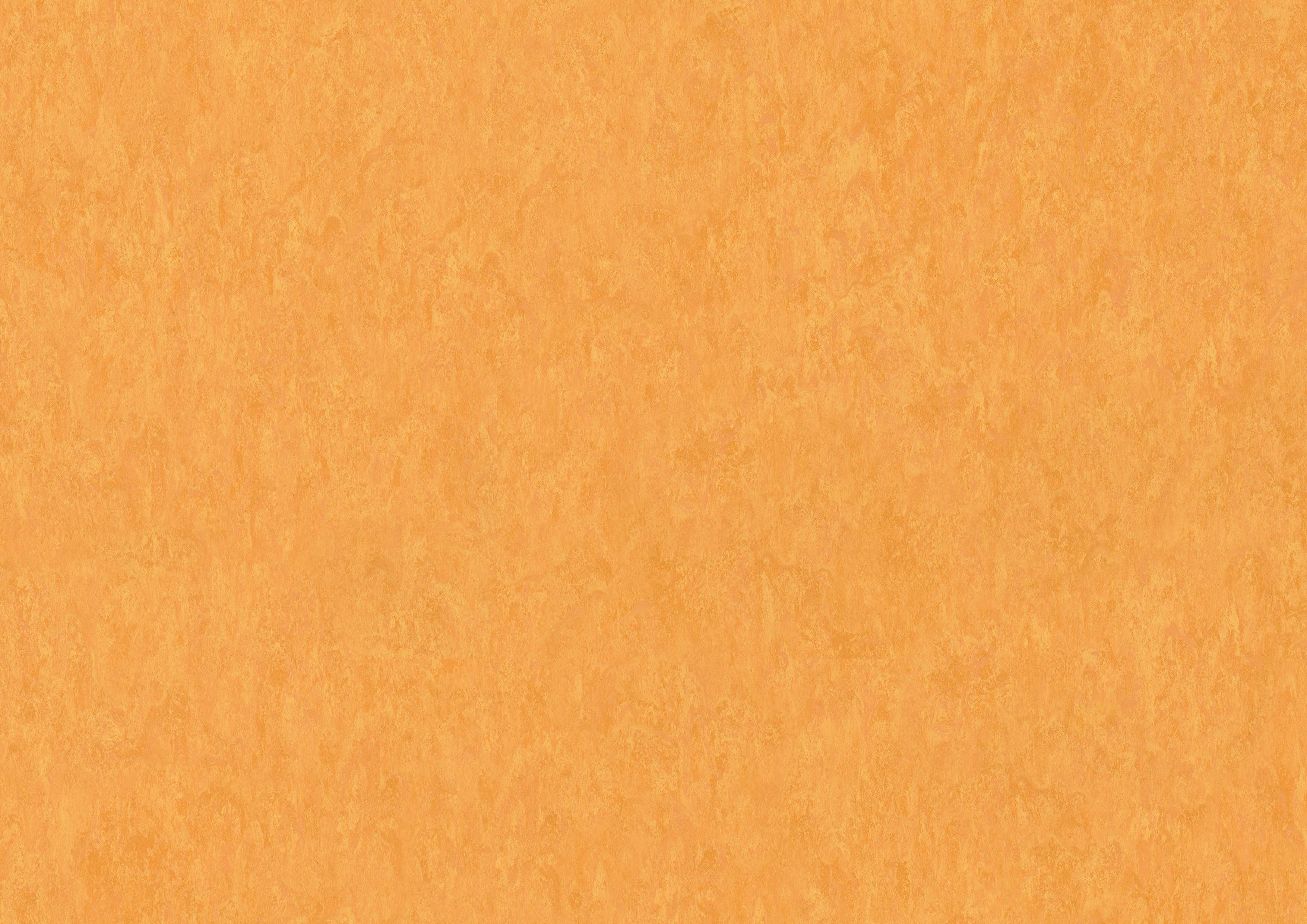
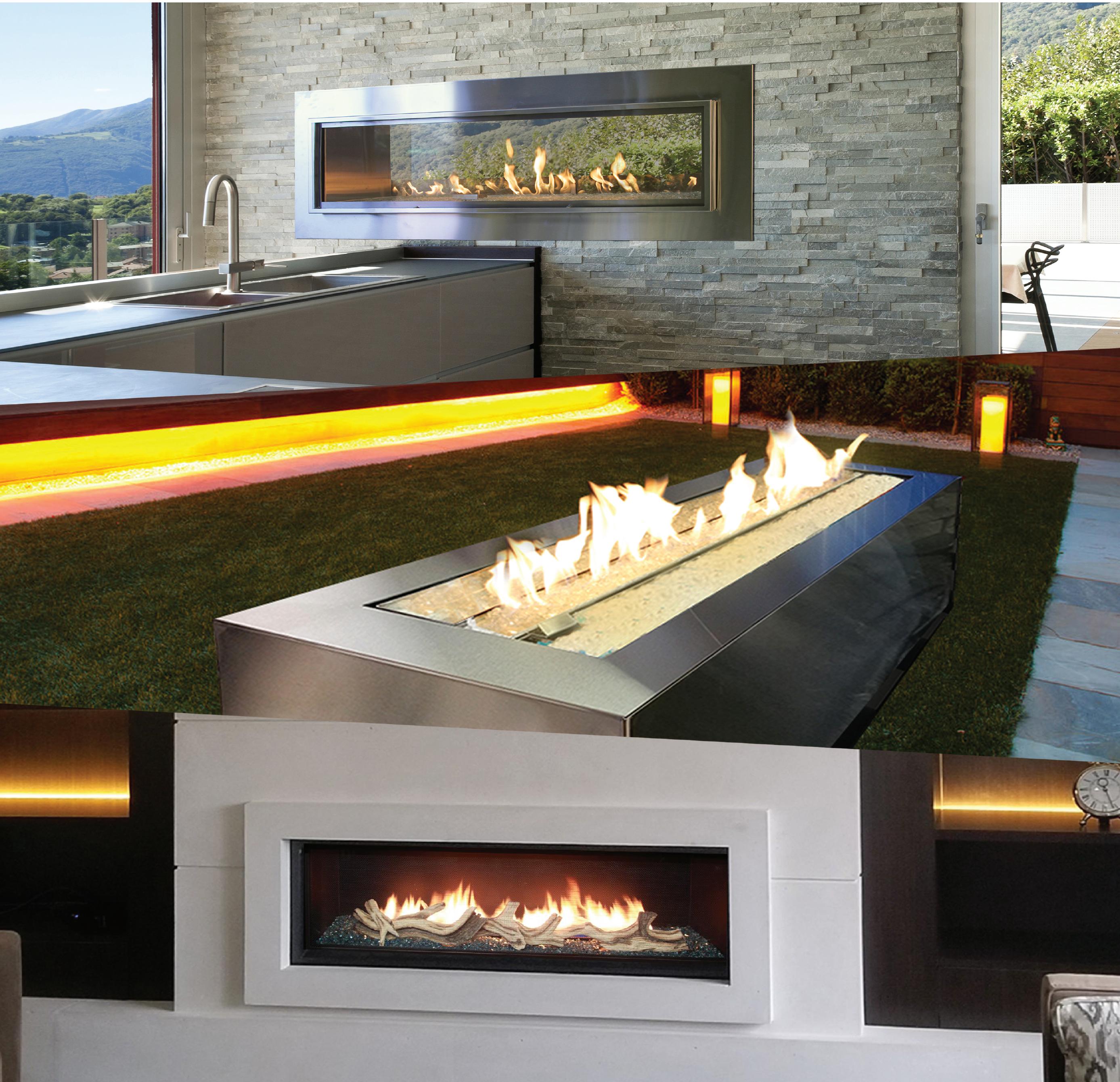