
4 minute read
CHARGING AHEAD ADVANCING BATTERY TECHNOLOGY HAS INCREASED THEIR SAFETY, SUSTAINABILITY, AND USAGE
Twenty years ago, the most popular battery type found in commercial and industrial applications was a flooded lead-acid battery. It was the go-to for general purpose applications such as fleet vehicles. It was also standard for industrial equipment with minor variations, depending on its usage such as voltages (6V to 80V or more), post or terminal mountings, cell and plate composition like lead, cadmium or calcium. Still, the “little black box” of power remained static. These conventional batteries exist to this day along with both slight variations such as sealed, gel and no-maintenance options to full-blown smart batteries and everything in between.
Traditionally, industrial vehicles and equipment have used the common lead-acid battery known for its performance, relatively low-acquisition costs, and minor maintenance requirements like fluid top-ups (either water or sulphuric acid). These hardworking powerhouses are what most think of when you mention a battery. They’re commonplace and offer good performance, although they have significant drawbacks such as safety concerns related to handling and storage. For example, their shelflife is six-to-12 months, depending on battery type and storage conditions. As well, there’s the possibility of acid leaks, exposure to hazardous materials such as lead terminals and the potential for fires or explosions due to poor ventilation during charging, which is the result of off-gassing.
These traditional models work for most applications, especially when constrained by budget. Some of the first steps in battery evolution came in the form of sealed batteries, which reduced spillage and explosion risks due to the reduced off-gassing when charged correctly (overcharging still poses a risk) and combined with their limited maintenance requirements. For example, there are no fluid top ups needed and only charging between uses.
Industrial Vehicles
Combination battery and charger options have become commonplace in forklift and automated vehicle applications. This eliminates the need for an external charger, freeing up valuable floorspace and reducing the downtime required to disassemble and set up the charging operation. It also means not tying up valuable operator time with maintenance functions. Rather, it frees them to perform value-added, operational functions. This combination solution also addresses the risk of potentially misusing the incorrect charger with the battery.
One of the most significant advances in commercial battery technology is the use of lithium-ion batteries. These have become more widely known, a development driven by their use in electric cars and a growing public acceptance of alternative vehicles. Lithium-ion batteries have countless applications in the industrial space, from forklifts in warehouses to robotic equipment in manufacturing and UPS backup power stations across many sectors.
These batteries are lighter than conventional lead-acid batteries and can store more energy in a smaller space. They also require less maintenance, as they do not need to be topped up with water and don’t produce gas while charging. This makes them more convenient, safer to handle, and cost-effective to use. Additionally, lithium-ion batteries have longer shelf-lives and can hold their charge for longer, making them a great backup option for applications where needs are inconsistent. The lithium-ion battery’s quicker recharge time, as compared to conventional lead-acid varieties, make for a solid option during unexpected demand spikes. This has led to an increase in their use in forklifts and other industrial vehicles such as bucket trucks in utilities fleets, as they are more efficient and environmentally friendly.
Another technology that is impacting batteries in industrial vehicles is the use of wireless connectivity, a service provided by companies such as E-Motec and TI Automotive. With the increasing digitization of industrial vehicles, wireless connectivity has become a critical component in battery management systems. This allows for real-time monitoring of the battery’s health, including its charge level, temperature, and other important parameters. The data can be used to optimize the charging and discharging of the batteries, leading to increased efficiency and longer battery life.
Batteries In The Cloud

Artificial intelligence (AI) cloud-based battery management systems are increasingly popular, with manufacturers that include NXP and the well-known European automotive brand Bosch. These systems allow for the remote monitoring and management of batteries, a great option to use in remote locations. This is particularly useful in large manufacturing or warehouse facilities that use multiple forklifts and other industrial vehicles. By monitoring the charge level of the batteries, technicians and operators can ensure that the vehicles are always ready for use, reducing downtime and increasing operator efficiency. The seamless communication and integration between battery, motor, operator, and technician provides real-time data and activity which can help with emergencies or accidents in remote areas or in lone-work scenarios. Additionally, this data can be used to schedule maintenance, especially during seasonal slowdowns, to avoid downtime and improve the battery life.
Predictive analytics is another technology that is impacting batteries in industrial vehicles. Predictive analytics can be used to predict when applications. This can help to reduce downtime and improve the overall efficiency of the operation.
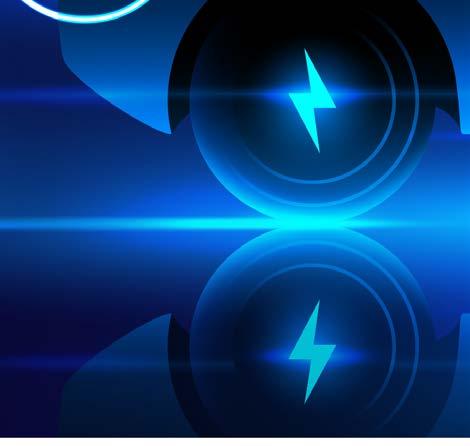

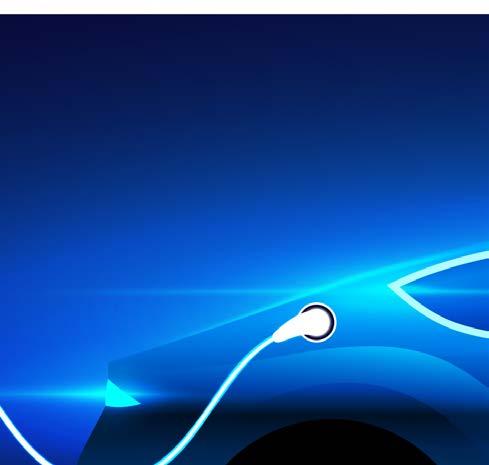
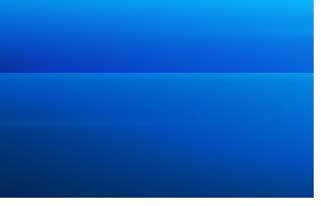
As battery technology has evolved, so too has battery recycling. No matter the type, batteries will eventually need to be disposed of. Conventional lead-acid batteries are easily recycled through smelting operations to recover valuable materials, such as lead and polypropylene; making these products over 90-per cent recyclable. This not only helps to conserve resources, but also reduces the environmental impact of batteries. With advances in technology, battery recycling is becoming more efficient and cost-effective, leading to a more sustainable use of batteries in industrial vehicles. The cost effectiveness of recycling newer battery technologies is still in its infancy. Still, the main materials can be recycled, including nickel manganese cobalt oxide, sodium-ion, lithium iron phosphate, lithium carbonate and lithium hydroxide. These are not widely used, and don’t yet offer comparable efficiencies as their lead-acid counterparts. Still, advances are on their way, both in North America and globally, as demand for spent lithium batteries grows.
The battery evolution continues to advance. Newer materials are coming onboard as they are refined and scaled to balance performance with cost. Zinc-manganese oxide, for example, has been researched by the US Department of Energy’s Pacific Northwest National Laboratory. These batteries may have large-scale energy applications such as for an electrical grid, gold nanowire gel electrolyte (researched conducted by the University of California) or organosilicon electrolyte (researched by the University of Wisconsin-Madison) which produces a less flammable or explosive option than the lithium battery. Batteries play an increasingly pivotal role as organizations look to more sustainable and mobile power options to flex based on changing business needs from environmental conditions to locations. Battery technologies, although stagnant for much of the last 100 years, have taken tremendous leaps forward as related technologies have evolved. This is especially true in transpor tation, with lithium batteries and the Internet of Things (IoT) incorporated into smart batteries to enhanced battery health monitoring.
BY MICHAEL POWER