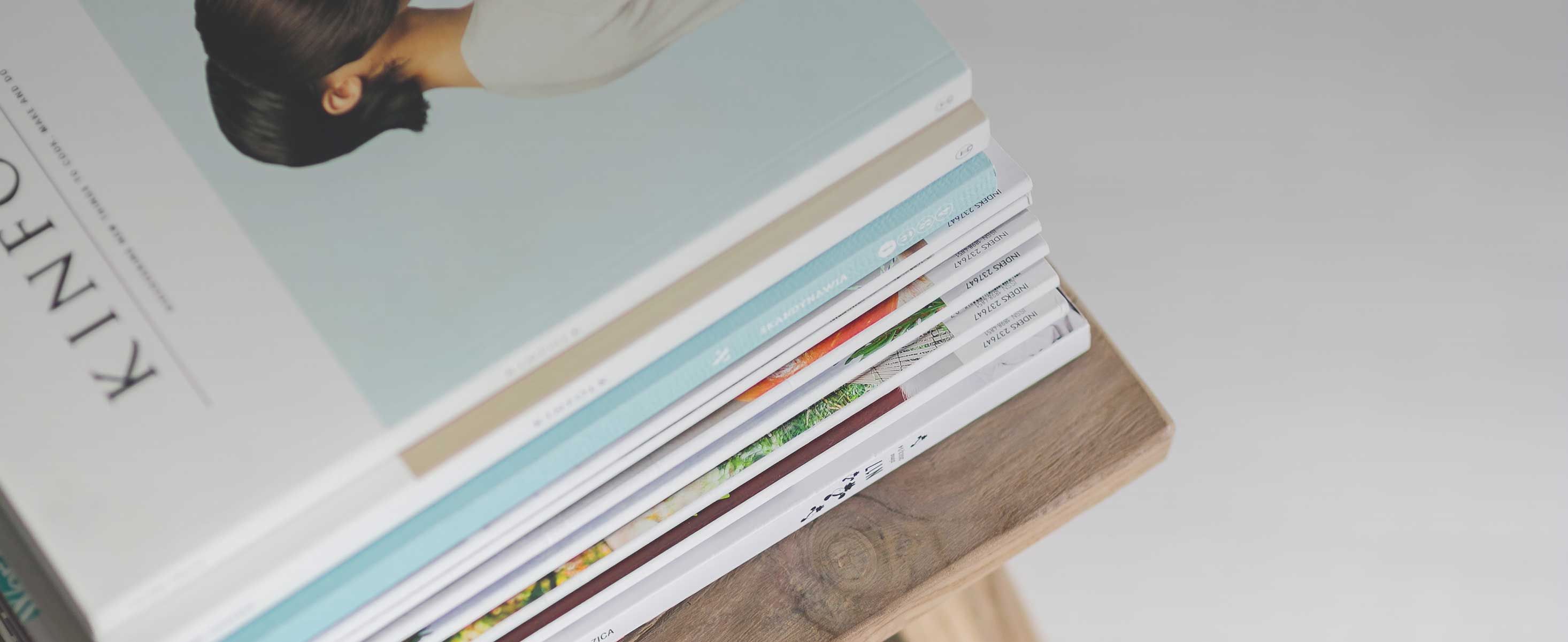
4 minute read
Responding to ongoing vehicle availability challenges
It has been referred to as ‘the perfect storm.’ The COVID pandemic caused the demand for vehicles to decrease significantly. As a result, the overseas manufacturers of semiconductor chips needed to support the automotive industry decreased production or shifted to chips for entertainment products that were in high demand during lockdown. Once the economy started to improve, getting access to the chips proved exceedingly difficult because they had been allocated to consumer electronics by the overseas chip suppliers.
Current projections
This has not been an easy situation to resolve. The semi-conductor chips were manufactured overseas, and domestic production has not been able to make up for the shortages. With vehicle availability shortages now expected to continue into 2024, most manufacturers are taking measures to keep supply flowing. Some are making vehicles without chips for certain (non-safety related) features. The manufacturer may provide incomplete vehicles that are safe to drive to be installed later by a dealer.
1. Operating budget increases
2.
Even with these measures, there have been many cases where organizations are promised a nineto-12 month wait time for a vehicle, only to have the order cancelled nearer to the expected delivery time.
In addition, buyers have been paying a premium to get vehicles since the crisis began. Fleet buyers must expect inflated prices until the situation is resolved but there are indications that the inventory situation is improving with new inventory levels increasing 1.5 per cent from October to November 2022 and nearly 37 per cent compared to October 2021.
It is far too early, however, to see actual consequences of these increases.
Impacts on fleet
This unprecedented situation has impacted fleets around the world. An unreliable supply and increased prices of new vehicles has resulted in many challenges.
Older vehicles staying on the road longer means an increase in the number of services and repairs needed. Older vehicles are typically less fuel efficient and fuel costs will be higher.
2. Capital budget increases
Naturally, capital requirements do not increase when there are no replacement vehicles to purchase. As vehicles do become available, however, inflation is pushing acquisition prices up.
3. Maintenance and repair service increases
The cost of maintenance is a starting point for the impact of delayed replacement on an organization.
As a fleet ages, the need for maintenance increases. Current facilities and staff may have to be augmented to accommodate these increases.
4. Safety decreases
Vehicle manufacturers are constantly investing in safety technology and new vehicles are safer vehicles. Delaying the introduction of new vehicles means the retention of older (less safe) vehicles.
Finding solutions
There is no crystal ball to predict how or when this will end. There is no magic wand to fix the current vehicle availability issues. Fleet managers have reported a number of creative practices to help in the short term.
In one example, an organization was forced to make the difficult decision to retire assets with excessive maintenance costs while retaining several units that were in marginally better condition than the rest. Before disposing of the assets, however, they retrieved much-needed items such as winter tires to reuse on retained assets.
Another organization had never rotated vehicles between departments. As a result, vehicles had a wide range of accumulated mileage. They instituted an unpopular vehicle rotation program in order to smooth utilization and reduce the need for replacements.
Many organizations continue to emphasize the importance of a multi-year replacement plan even if strict adherence to the plan is currently impossible. Understanding the impacts of delayed replacement and adjusting the plan as those delays happen puts the organization in an informed position when vehicle supplies increase. These and other local solutions may ease the pain to an extent, but a coherent and comprehensive plan is needed to address the damage done and the continuing challenges ahead.
How to respond
There is no ideal solution. Inevitably, fleet professionals have to act counter to what they know is best practice to meet the priority goals of their organizations. Accepted practice is to replace vehicles at an optimum point in their lifecycle where the total cost of ownership (TCO) is minimized. This is not possible if replacement vehicles are unavailable. Where delayed replacement is inevitable due to vehicle availability (or lack thereof), fleet managers should take the following steps to ensure that informed delayed replacement takes place.
1. Understand when vehicles will actually be available
There are few guarantees right now so use relationships with trusted suppliers to ensure you know the truth. Generous promises and rosy predictions will not help. An organization can only make a workable plan when they have accurate information on vehicle delivery dates (as grim as they may be).
2. Evaluate the short- and longterm costs and impacts
Once accurate information is available, it is possible to assess the consequences of vehicle replacement delays. Organizations should consider financial, safety, staff, and policy impacts. Additional operating costs to fuel and maintain older vehicles may be the easiest to quantify. Safety may be impacted by delaying the introduction of newer, safer vehicles. Employees may be negatively impacted by having to maintain and operate older vehicles and policies may have to be updated to show new lifecycles or rotation guidelines.
3. Educate decision-makers on these impacts
The information gained in the previous assessment needs to be shared with decision-makers who may control access to the budget increases needed and who may approve the policy changes.
4. Explore the least costly options
With a realistic view of the situation and ongoing impacts, decisions can be made that take overall costs into account and minimize their impact on the organization.
5. Implement wisely Flexibility and innovation need to be part of any implementation plan. A dogmatic adherence to a 20-year replacement plan will fail – the replacement vehicles are simply not available. Organizations that are willing to adjust that plan as circumstances warrant will be more successful in overall cost control.
As the fleet industry struggles with these unprecedented challenges, it is more important than ever to reach out to industry colleagues and share ideas and solutions. Vehicle availability and price inflation will not be resolved overnight so a longer-term strategy is needed to weather this perfect storm. FM/SP
By Matthew Wiedmeyer