
4 minute read
HVAC in cleanrooms and laboratories
What’s involved in planning and specifying HVAC for cleanroom facilities? Heatwave Mechanical’s Maksim Manko explains
What does the process look like, from design to completion?
When our clients plan on constructing or adding to their cleanroom facilities, we sit down with them and discuss specific technical requirements, to produce a brief or short specification – eg. humidity and temperature ranges, quality assurance requirements to determine the cleanroom classification and pressure cascading.
We also go through space requirements, in particular where to position the HVAC equipment (eg. air-handling units, chiller), and see how to lower their capital expenditure costs through value engineering.
From here we will work through the engineering/design aspects – fresh-air requirements, heat-load calculations, air-flow distribution according to ISO classification, room pressure analysis – consulting the client through each phase of design to ensure we are working towards the best possible solution. heatwave.co.nz
Once we have developed the solution, we work with our client and other contractors, eg. panel installers and electricians, to ensure the installation is as smooth as possible. Quality assurance throughout the installation is important, as the testing and commissioning phase –setting up the HVAC systems for a cleanroom are extremely important and require 100 percent accuracy regarding humidity and pressure cascading.
Once commissioned, the job isn’t done – close monitoring of the BMS and system performance is necessary for the first few weeks, and regular service/ maintenance of the equipment post-completion, to ensure the client’s assets continue to perform at their best and ensure a longer life-cycle.
What are the general requirements for these spaces?
Humidity and temperature control, pressure cascading (difference in pressure between various rooms/spaces), keeping the air-change-rate high to remove particles/dust with the use of HEPA filtration.
Constant monitoring, logging and data exporting is required for many of our clients, having strict Quality Assurance requirements for their overseas exports.
We also design and build heating or chilled clean water systems for use inside cleanrooms – with soft water or reverse osmosis treatment.
What challenges are typically involved in projects like this?
It is important to consider future capacities and more stringent Quality Assurance requirements for each of our customers and the systems we build for them – as our client’s market share grows and they continue to develop more technical products and they want to know their new cleanroom systems are flexible and capable of meeting such requirements.
Some clients will even need specific exhaust systems eg carbon filtration, wash bays and local exhausts of high-temperature machines – we need to make sure these don’t adversely affect the standard of the cleanroom or its air-pressure requirements.
A lot of our projects involve the expansion of existing cleanrooms – we strive to ensure the cleanrooms are always operational and there aren’t long shutdowns to integrate new systems – sometimes this may require the use of a temporary air handling unit while we remove a smaller old air-handling unit and build a new, higher spec air-handling unit in its place and integrate it without disruption.
From an engineering perspective, cleanrooms can be challenging projects to design. We recently had a process heating water system for an ISO-8 cleanroom which had 2x closed loops and 1x open loop, high temperatures, various heat exchangers, and many variables (potential scenarios) that we needed to consider in our design. This was one of the most technical projects that I have been involved in, to date – a very enjoyable project for our engineering and installation team to be involved in.
Heatwave is a one-stop-shop for design and build projects, HVAC/cleanroom piping and beyond – we have our in-house engineers, duct fabrication workshop, installation teams, project management and maintenance department, www.heatwave.co.nz
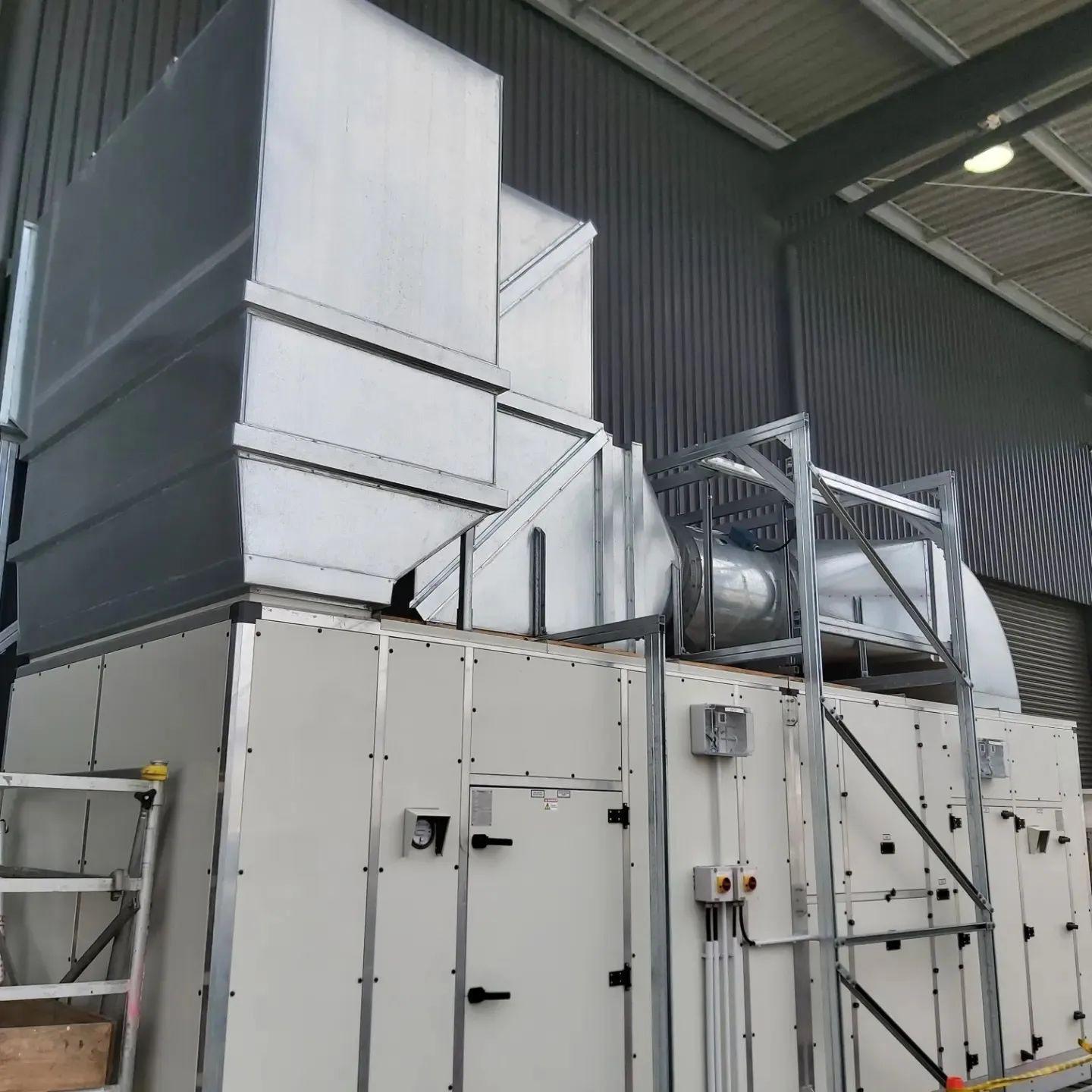