FIDGET PAW
A paw shaped fidget toy with rolling balls and a soft sponge to allow students with dyspraxia to feel less overwhelmed whilst at university.
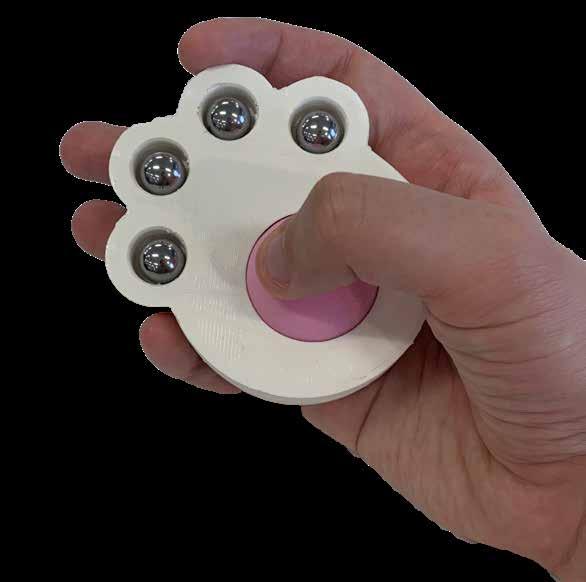
A paw shaped fidget toy with rolling balls and a soft sponge to allow students with dyspraxia to feel less overwhelmed whilst at university.
I chose to focus on students with Dyspraxia as it is a personal area to me. I have dyspraxia and university at first was challenging. Dyspraxia is a “common disorder affecting fine or gross motor co-ordination among children and adults” (Grant, 2017). Six to ten percent of people in the UK have dyspraxia (Walker et all, 2018). The amount of university students with specific learning difficulties (dyspraxia, dyslexia, asperges syndrome, ADHD or dyscalculia) are increasing. Students with Dyspraxia can easily feel overwhelmed especially when in new and unknown situations and this can affect their well-being.
From interviews, I found out that one student with dyspraxia feels “trapped and he “can’t get out” when in a large crowd. Another student with dyspraxia, gets overwhelmed “when [they] can’t concentrate when [they] need to or when [they] can’t do a basic task”. One person said, he has “pride in what [he does] and that willing to suceed can be overwhelming” and “when [he feels] overwhelmed, [he calls] people to calm down.”
A fidget toy allows students with dyspraxia to fidget with when they are in overwhelming situations such as a large crowd or in a lecture. It also allows students to focus better in the lectures. By fidgeting, they would be able to relieve themselves of excess energy and give them something else to focus on (Ashworth, 2019). Fidgeting would also provide physiological stimulation to bring their attention and energy to a level that would allow their minds to be better focussed on the lecture or university work. The paw shape fits in the hand nicely and for people cats or dogs can help calm people’s nerves when they stroke the animal. The fidget paw has diffferen materials and textures.
The fidget paw would need to be made of a durable material as they would need to withstand fidgeting for long periods of time and be durable when knocked against the body. The fidget paw would have to made of a smooth material as it would be held in your hand and would need to be smooth to hold and feel nice in the hand. A type of plastic would be good for this, for example ABS plastic, which is what Lego pieces are made of, ABS plastic is a durable material that is robust and can withstand continuous and a lot of playing with. ABS is more prone to warping so PLA plastic could also be used as this is stronger and stiffer than abs but has poor heat resistance properties.
Some of the component parts would need to be bouncy and flexible as when they are squished and fidgeted with, they would need to bouncy back. For example, polyurethane foam (see fig 3), which is what stress balls and squishes are made of, can be squashed and return to its original shape.
A trackball mouse has a similar mechanism to the outside balls of the fidget paw, the ball slots into place and can be freely moved around and not fall out. I would need to implement this mechanism in the paw so the ball does not fall out and be easily lost. The ball material and the main body of the paw would need to have enough friction to stay in place but not be rough to feel when you move the ball around. A small steel ball bearing would be suitable as it is smooth and and weight of it allows it to be rolled smoothly.
Fig 8
I had to make sure that the steel balls would stay in place in the holes and not fall out. The top has a sight curve which is the same diameter of the balls. The steel ball bearings are small balls in the top 4 pads of the paw as when it was one big ball in the centre it was too heavy, so making it smaller would have less weight in fidget paw. Using chrome steel ball bearings was the best choice for the balls as all the other balls I tested (wood, foam, 3D printed PLA, plastic) did not have the same effect as the steel ball bearing. They was either too rough in texture or too noisy when you moved the balls.
Fig 10
1. Wire rod is cut to length, slightly larger than the volume of the finished ball
2. It is then cold forged in steel dies to produce a cold headed ball
3. flashing removes the equator and poles giving the steel ball a rough finish
4. heat treating through hardens the chrome steel ball
5. the ball is ground to achieve the approximate size.
6. lapping gives the smooth finish as the ball is polished to the exact size
• the sizing of the different ball bearings
• the weight of the ball bearings
Ball bearings are the most common type of bearings and are found in many every day objects, such skateboards, blenders, bicycles, DVD players and photocopiers. This type of bearing is typically used in applications which have a high
• Steel production has a number of impacts on the environment, including air emissions (CO, SOx, NOx, PM2), wastewater contaminants, hazardous wastes, and solid wastes.
The main body of the frame has thin walls with uniform thickness and is shelled out so it can be injection moulded. The sides have a slight draft angle so it can be removed from the mould easier. It is also split into two parts (a male and a female) so a mould can be created of each and then sloted together using the pins and holes. The holes are slightly bigger (3mm) than the pins (2.5mm) so they can be slotted together. The bigger pegs for the small steel ball bearing reduce the need to have the smaller pegs on the outside edge near the top.
They are many environmental issues associated with plastic, for example, plastic can be hard to recycle. However, you can get biodegradable plastics that can be degraded into CO2, water and biomass. This includes polylactic acid (PLA) which is made from the starch of plants. In the process of injection moulding, scrap plastic pieces can be re-melted and fed back into the process so there is limteted material waste
1. Hopper feeds the plastic polymer into a heated barrel and screw
2. The screw melts the plastic.
3. It would then inject the liquid plastic into a temperature controlled split mould tool that creates the shape of the product.
4. This is then cooled and the plastic moulded product is removed.
Injection moulding is good for manufacturing high volume, identical products at a high-quality finish in a short space of time.
For example, injection moulding is used in the production of Lego pieces, made from ABS. These need to be durable and identical so they can be slotted together. Plastic is more robust than other materials, such as wood or metal, and safer for children to play with.
Injection moulding can also be used to creat large scale products such as chairs and other furniture items.
• The edges need to have a slight draft angle
• The mould can be expensive to make - only used in the production of high quantity products
• walls have to be uniformed thickness to provent inconsitancys
• The mould would have to be designed and filled to ensure even spread of the polymer while it is still in its liquid state.
The design is a simple ball shape (30mm in diameter) which would be easy to create a mould from to produce the polyurethane foam
Polyurethane foam emits toxic fumes if burned. Some blowing agents in polyurethane produce greenhouse gases that have negative effects on the atmosphere. Some polyurethane foam contains non-renewable fossil fuels that adversely affect the environment. Polyurethane is inherently more eco-friendly than most other plastics. It also doesn’t contain any chemicals that interfere with endocrine and hormone systems.
1. Mould is cleaned and sprayed with a silicone lubricant.
2. inserts and frames are put into place and the mould is clamped shut
3. Polyurethane foam (a liquid in 2 parts - polyol and isocyanate) is poured into the mould. The foam will expand so the mould doesn’t need to be completely full.
4. The polymer begins to expand to fill the mould. As the polymer expands, runners allow trapped air to escape
5. A bung is then inserted to maintain the iternal pressure
6. It is then removed from the mould and any excess foam is cut away
7. The finishing details are either sprayed or painted on.
The buttons would be made out of a foam, similar to that of a stress ball. Stress balls when squeezed return to their original shape. When you squeeze a stress ball, your nerves and muscles contract which would make them stronger, the strength improves the overall nervous system, which would reduce essential hormones and control your stress levels.
Stress balls can be painted many different colours, this would allow there to be flexibilty with the colours in the fidget paw
Both of the pieces have holes on both sides and are attatched together using wooden dowels as this would be easier to be produced on the CNC router. Glue would be applied on the outside wall so they stick together.
The wood would need to be sourced ethically and in line with guidelines set out by FSC, which tracks the origin of the timber. It is a reductive process so it would generate waste in operation. Most CNC routers have dust extraction which would take the dust out for recycling or incinerating.
1. File is created on CAD software such as solidworks or fusion 360
2. The file is sent to the CNC router
3. The CNC router would then cut the file according to what is set out from the 3D file and is completley automated.
4. For parts with geometries need different cutting heads, the tools can be automatically changed
• small and narrow points - Is there a CNC machine tool for this?
• CNC woodworking is affected by the grain, greeness and warping of the wood
• Some drawbacks associated with cost and size limitations but these can be resolved before the CNC machining process starts.
CNC machining is used in the production of wooden letter blocks (see fig 20). A tool would be used to cut out the letters and the general block shape out. The blocks would need to be varnished and sanded (so they are safe for children) and painted in different colours. The fidget paw would also need to be varnished and sanded and could also be painted different colours.
Fig 22
PET can be recycled repeatedly by washing and remelting for use in new products, this includes clothing fabric, carpets, upholstery and lanyards. Some lanyards can be made out of bamboo fibres.
The fidget paw has a hole in the middle of the two parts for it to be clipped onto a lanyard or used a keyring.
Polyester imprinted lanyards are most commonly used because of their cost, durabilty and flexability. Nylon imprinted lanyards can be used for holding ID badges, security cards in most business establishments. Nylon lanyards are thicker and shinier than polyester lanyards.
The attatchment would be the lobster claw clip as this would fit through the hole easier
Leeds Beckett would supply the lanyards and the fidget paw is an add on for students with dyspraxia.
1. Machines are fed with coloured threads
2. Cut into several straps then rolled on fixed size rolls
3. Rolls then shipped to factories that produce lanyards
4. For screen priniting, the lanyard material is layed out in rows
5. For full dye printing, the design is pressed onto polyester satin fabric then cut
6. Once printed, the lanyards can be assembled by sewing them into loops and adding the necessary components - break away clip and lobster claw clip
The fidget paw shape needs to be simplified for slip casting.
Slip casting is mainly used in the production of ceramic vases, bottles and bowls
• The moulds used for slip casting usually have a low toughness - They have a high porosity, which lowers the strength.
Low strength gypsum moulds wear out with time because the pores are eroded from the water that goes through them.
1. Prepare plaster mould (securing with rubber bands) and slip
2. Fill your mould with slip, wait 1525 minutes for the slip to thicken (longer wait = thicker walls)
3. Remove excess slip
4. Release your casting from the mould
5. Cut away the opening and smooth the piece down (Thompson 2007)
During slip casting there can be up to 15 percent waste, the majority of this can be recycled and put back into the system but if the parts have been fired, its no longer suitable for recycling. (Thompson 2007)
A paw shaped fidget toy with rolling balls and a soft sponge to allow students with dyspraxia to feel less overwhelmed whilst at university.
NOTE
Section view to show encapsulation of bearings Resistance and feel factor taken into account 1 FP 001 2 FP 002 3 FP 003 4 FP 004
SECTION A-A
SOLIDWORKS Educational Product. For Instructional Use Only.
• Ashworth, H. (2019). Why do we fidget? [online] BBC Science Focus Magazine. Available at: https://www.sciencefocus.com/the-human-body/why-do-we-fidget/ [Accessed 23 Nov. 2021].
• D W Plastics. (2021). What are the manufacturing processes for plastics? [online] Available at: https://www.dwplastics.co.uk/manufacturing-processes-for-plastics/ [Accessed 24 Nov. 2021].
• Grant, D. (2017) That’s the way I think: dyslexia, dyspraxia, adhd, and dyscalculia explained. Chapter 3 Third edition. London: Routledge.
• Owen, A. (2015). Quality Foam Grades For Specific Comfort. [online] Foam for Comfort Blog. Available at: https://www.foamforcomfort.co.uk/blog/2015/12/quality-foam/ [Accessed 24 Nov. 2021].
• Stressballsuk.com. (2021). StressBallsUK.com. [online] Available at: https://www. stressballsuk.com/manufacturing [Accessed 24 Nov. 2021].
• The Crucible. (2019). You Will Be Slip Casting Ceramics With These 5 Easy Steps - The Crucible. [online] Available at: https://www.thecrucible.org/slip-casting-in-five-steps/ [Accessed 27 Nov. 2021].
• Thompson, R. (2007) Manufacturing processes for design professionals. London: Thames & Hudson.
• Walker E et al. (2018) “Dyspraxia in Clinical Education: A Review,” The clinical teacher, 15(2), pp. 98–103. doi: 10.1111/tct.12734.
• Fig.1 Rapid Direct (2021) ABS vs PLA [online] Available at: https://249261-772960raikfcquaxqncofqfm.stackpathdns.com/wp-content/uploads/2021/07/pla-vs.-abs-usefor-different-prints.png [Accessed 13/12/2021]
• Fig. 4 Francis, T (2014) The internal circuit of the Logitech wireless trackball M57 [online] Available at: https://www.researchgate.net/figure/The-internal-circuit-of-the-Logitechwireless-trackball-M57-Color-figure-available_fig8_262963170 [Accessed 13/12/2021]
• Fig. 10 indiamart.com (2014) Ball bearings [online] Available at: https://5.imimg.com/ data5/QG/NT/MY-15068885/imported-ball-bearings-500x500.jpg [Accessed 13/12/2021]
• Fig. 13 Toolcraft.co.uk. (2015) injection moulding process [online] Available at: https:// www.toolcraft.co.uk/plastic-injection-moulding/advice/help-injection-moulding-process. htm [Accessed 13/12/2021]
• Fig. 16 gd-admin (2021). PU Stress Ball Toys Foam Injection Machine. [online] Available at: https://www.machinepu.com/pu-stress-ball-toys-foam-injection-machine-product/ [Accessed 13/12/2021]
• Fig. 19 Thompson, R. (2007) CNC machining process from Manufacturing processes for design professionals, pg 183. London: Thames & Hudson.
• Fig 20 Amazon.co.uk. (2021). Skoolzy 30 Alphabet Blocks with Letters Colors. Wooden ABC Toddler, Preschool & Kindergarten Building Toy. Wood Reading Stacking with Carrying Tote : Amazon.co.uk: Toys & Games. [online] Available at: https://www. amazon.co.uk/Alphabet-Preschool-Kindergarten-Building-Stacking/dp/B00NY4TL36 [Accessed 14 Dec. 2021].
• Fig 22 Leedsbeckettmerchandise.co.uk. (2019). 15mm Lanyard. [online] Available at: https://www.leedsbeckettmerchandise.co.uk/Product/Details/16849/15mm-Lanyard [Accessed 14 Dec. 2021].
• Fig 25 Benjamin Hubert. (2014) Seams [online] Available at: https://catesthill. com/2014/09/17/ldf14-seams-by-benjamin-hubert-for-bitossi-ceramiche/ [Accessed 13/12/2021]
Figs 2 - 3, 5 - 9, 11 -12, 14- 15, 17- 18, 21 – 24 are all my own sketches and photographs