
6 minute read
The Good Plastic Company: A Champion of Sustainability & the Circular Economy
By Sarah Peiper
The Good Plastic Company, a leading international manufacturer of sustainable surface materials, recently announced its expansion into North America. Founded by Dr. William Chizhovsky in 2018 to address the scourge of plastic waste, the company is committed to helping its partners make a tangible commitment to sustainability and the circular economy. The company’s flagship product, Polygood, comprises a range of 100% recycled and recyclable plastic panels made from post-consumer and post-industrial waste. The brand has completed over 750 international projects showcasing solutions for furniture, surfacing and design elements and now looks to continue the momentum as it enters the North American market.
Countertops & Architectural Surfaces recently sat down with Dr. William Chizhovsky to learn more about how The Good Plastic Company aims to make a sustainable impact on the surfacing industry.

C&AS: What is Polygood?
Chizhovsky: Polygood panels are stylish, durable, lightweight, waterproof and extremely versatile — a sustainable plastic material designed with specifiers, designers, architects and the circular economy in mind. Each panel is composed of a single type of recycled plastic, ensuring simple recycling and robust, long-lasting quality. We choose to work with polystyrene plastic, a durable material that minimizes resource usage in recycling and manufacturing processes, aligning with eco-friendly principles.
We take pride in being the sole manufacturer of a recycled plastic material that holds both Cradle to Cradle certification and an Environmental Product Declaration, demonstrating our commitment to quantifying the environmental impact of our products. Our VOC certification has an A+ rating.
C&AS: What are the material specifications?
Chizhovsky: We offer the largest panels crafted from recycled materials currently accessible, available in dimensions of 2800 mm by 1400 mm and thicknesses of 12 mm and 19 mm, with custom sizes also available. Our collection includes over 100 colors and customizable finishes, empowering designers to imbue their creations with personality and charm. Additionally, we cater to bespoke design requests, particularly within the commercial/retail sector, ensuring tailored solutions for every client.
C&AS: Can you tell us a little about the production process? Where do you source the plastic waste?
Chizhovsky: We operate within expansive recycling plants across Europe, where our two manufacturing facilities are located. Our suppliers are in the Netherlands, Germany, Poland and other countries.
Our distinctiveness stems from our ability to produce Polygood using post-consumer and post-industrial plastic waste. Managing post-consumer waste poses challenges due to its diverse nature; sorting through various types of refuse can be complex.
Over two years, we’ve developed technology that allows us to process different types of plastic effectively. We receive plastic in its raw form, which has already been sorted by type and thoroughly cleaned. Subsequently, we subject it to controlled pressure and temperature to melt and mold it into panels. We refrain from adding any external components to the sheets, ensuring they consist solely of 100% recycled plastic, thereby maintaining the highest quality standards.

C&AS: How is the material fabricated? What tools are required to cut or shape it? Can it be thermoformed?
Chizhovsky: Polygood is quite easy to work with. It’s most closely related to the solid surface category. The material can be cut using standard CNC machines and hand tools; it can be glued, drilled, sanded and polished to achieve various finishes such as gloss, matte and so on. Additionally, Polygood can be thermoformed to create various beautiful design objects — a completely standard process with this material.
We provide a workability guide, and our technical team conducts workshops to make it easier for clients to understand, although difficulties rarely arise.
C&AS: How does this material compete in terms of performance with other materials like solid surface, which is already widely popular and often contains recycled elements like stone or glass?
Chizhovsky: Standard applications using Polygood include interior design, furniture, wall cladding, flooring, installation booths and even outdoor facades. We offer various coatings for our panels, including anti-scratch, fireresistant and UV-resistant options.
The material’s competitive edge lies in our production of panels crafted from recycled plastic. This not only reduces CO2 emissions but also minimizes resource consumption compared to the production of virgin materials. However, materials containing partially recycled plastic often rely on recycling their own production waste, which fails to address the broader issue of plastic waste.
In our case, we exclusively use 100% recycled plastic, a fact verified by certificates. Our business model revolves around large-scale production.
C&AS: Where is the material made, and how is it distributed?
Chizhovsky: Presently, we operate two plants in Europe and are poised to inaugurate a third in America next year, which is slated to be our largest facility yet. Our reach extends globally, encompassing projects in the Middle East, Japan, Europe, Africa and Asia. With over 1000 projects underway, we’ve established local distributors with on-site warehouses. Additionally, stock became available in April in the United States with distribution out of North Carolina. Orders are fulfilled swiftly, typically within two to eight weeks.

C&AS: What are your go-to-market plans for North America?
Chizhovsky: North America represents a colossal market, and we’re witnessing a significant demand for sustainable materials, offering us unparalleled growth opportunities.
We’ve already established a team with an office in New York, and now we’re actively seeking partners and exploring stock opportunities. Our next step
involves the construction of a manufacturing plant, alongside acquiring the necessary equipment. Additionally, we’ve initiated the search for local raw material suppliers.
However, the most crucial aspect is demand. We need designers, architects and fabricators who will champion sustainable practices within the industry. They’ll take the lead, while we’ll also emphasize the importance of using our materials. It’s a symbiotic relationship where they take the first step, and we amplify the message about the significance of our material usage.
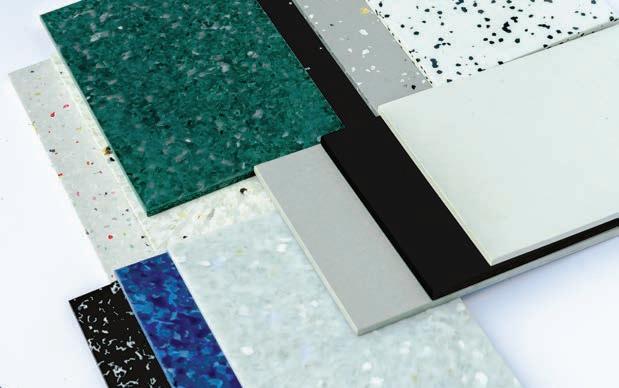
C&AS: What are your plans to scale, increase production, broaden applications, and improve the product further?
Chizhovsky: With the addition of our third manufacturing facility in North America, our production capacity will see a minimum threefold increase. We can manufacture as much as necessary, as we produce our own equipment. Moreover, there is a plentiful supply of plastic waste available.
However, the pivotal factor lies in the demand for our product, compelling individuals to transition from traditional, unsustainable materials to more environmentally friendly alternatives. This shift not only drives our growth but also fosters a more sustainable future.
To learn more about The Good Plastic Company and see all the available Polygood panel designs, visit www.thegoodplasticcompany.com.