
6 minute read
Build Confidence in Your Business by Evaluating Your Market Segments
By Ed Young, Fabricator’s Business Coach
I get a lot of questions from shop owners about how to price their products. They see advertisements from competitors touting incredibly low price-per-square-foot numbers and wonder if they have priced their products incorrectly.
“How are their prices so low?”
“Should my prices be that low?”
“How do I make a profit at that price?”
I also run across a lot of shop owners who want to close every quote opportunity regardless of the work. For them, it’s all about selling as much as possible. They think, “If the shop is busy, shouldn’t I be making money?”
Unfortunately, they are both asking the wrong questions. They should ask, “What kind of work makes the most money for my shop the fastest?”
To answer this question, you need to know how much money each order generates for your business (Throughput Dollars or $T) and how much cash the business burns daily (Operating Expense or $OE). Additionally, you need to understand how quickly you can fabricate and install different jobs.
Here’s an example of what happens when you ask the right question and use these metrics to get the answer:
I was working with a shop that was limping along at about break-even financially and had some unfilled capacity. Just filling the capacity would have added profit, but the owner was struggling with low-price competition in the area, hampering his ability to increase sales.
We analyzed his market segments: retail, kitchen and bath, contractors, etc. To do this, we calculated the $T as a percentage of the sales price for each kind of job. As expected, the $T percentage varied between the market segments and within each segment. However, there were a few surprises. Most of the contractor orders had a similar $T percentage as most of the retail jobs. The owner had expected the contractor work to have a lower percentage of $T. Through this exercise, he discovered he was doing better with the contractor work than he thought.
We then discussed which market segments he could get more sales from and what actions were required to get that work. There were various challenges with each market segment: high advertising costs, fierce low-cost competition for a couple of segments, and other issues. These challenges were significant barriers to increasing his sales volume.

Then the owner recalled one market segment he hadn’t evaluated yet. Recently, he had taken on some production builder work at a really low price because he needed to keep the shop busy. Sure enough, the $T percentage was the lowest of all the market segments. It was easy to see why he felt beat up by that customer.
Next, we discussed how many jobs of each market segment he could fabricate and install each week. The way we approached it was to ballpark fabrication and installation of typical retail jobs for an entire week and then do the same for the other market segments. We talked about how the various characteristics of the types of jobs impacted how many he could get fabricated and installed in a week.
The retail and contractor jobs were typically larger and more complex than the production builder jobs. This meant he couldn’t get as many retail jobs fabricated and installed in a week as the production builder jobs. The question was whether the higher $T for the retail and contractor jobs would make up for the lower quantity completed per week.
The aha moment came when we looked at the production builder work. As expected, the number of these jobs he could process per week was the highest of all. When we multiplied the typical $T for production builder jobs by the number of those jobs he could fabricate and install in a week, this segment outperformed all others. We had a winner! Not only was this work good for his shop, but he also knew how to get more of this work so he could fill his shop. We now had a recipe for this shop owner to start making a significant profit.
This rough calculation helped the owner understand how quickly each type of job generated $T relative to other types of jobs. While not true for every shop, in this instance, the simple production builder work generated cash faster than any other type of work this shop was doing. We also talked about how he might start to adjust his pricing to reflect this impact and start to drive total $T for the business even higher.
Another client recently sent me a note. She had bid on a sizable multi-unit job a year ago and had just learned she had won the bid, but now she was concerned about the ultimate profitability since this was an unusual job for her workflow. When she went through the same evaluation for her market segments, she realized this job could be quite profitable. Now she just had to focus on making sure the logistics for the job were managed well rather than worrying about profitability. Now she has the data and the confidence to bid on this type of work in a way that makes her company money.
Remember, you cannot take the results in this article and assume they are true for your shop. Each shop is different, and you have to do your own analysis. But knowing how to quantify the profitability of the various types of jobs you run can be the difference between successfully navigating this uncertain economy and not.
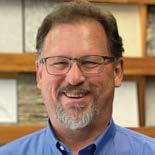