
8 minute read
SUSTAINABILITY MATTERS Waste: Environmental Hazard, Latent Asset, or Both?
By Max Le Pera & Jessica McNaughton
A central pillar of Sustainability Matters is to suggest ways and incite conversation around how we can weave into the fabric of the industry the four R’s of environmental sustainability: Reduce, Reuse, Recycle and Reform. As we continue the journey with a holistic focus, it is clear that not all strategies are endemic to each business. Furthermore, as we move to construct a more defined framework around Leadership in Energy and Environmental Fabrication (LEEF), a concept we introduced in the previous issue, we insist that some efforts require teamwork. Waste is one of these conundrums that is profound in size and poorly understood, yet it continues to grow at a rate many times faster than the expended efforts to remediate it.
Waste comes in many forms: excess water usage, lights we forget to turn off when we leave a room, office workflows that heavily rely on paper products, or a lack of protocols to recycle within an organization. But dig deeper, and you’ll find more subtle forms of waste such as cardboard, lumber, yield loss, cutout remnants and material samples that end up in the trash. While businesses may ignore these waste streams’ impact, the waste summation of everyone — fabricators, distributors and manufacturers — is alarming.
The solid surface industry may have the highest degree of the circular economy because sheets can be hard-seamed together, and yield loss can be kept at a minimum — for the popular colors at least. Further, due to the nature of this material, it requires carbide tooling, which is relatively easy and less expensive. Converting cutouts and remnants into something of value is quite possible. Finally, the repairability of solid surface means the life of this material is easily extended. Every effort to reuse anything otherwise destined for a landfill poses a win for the environment.
At the local level, some fabricators are doing what they can and addressing the problem in their own way – every effort counts. For example, material otherwise destined for the dumpster can be donated to organizations such as Habitat for Humanity or passed along to paving companies that grind the material down to aggregate for roads and landscaping. Additionally, for solid surface, some of you may be creating cutting boards, signage and other marketing materials that can be easily made from remnants and cutouts. While all these efforts are fantastic, they represent only a nano-fraction of the waste remediation policies we need.
Further, as we look beyond solid surface into the other two main engineered materials categories — quartz and mineral surfacing — we see a distinct step change in how effective the four R’s are represented. These materials have a hardness about them that, on the one hand, gives them performance benefits that are so appealing, but on the other, makes reusing, recycling and reforming a significant challenge.
The massive quartz waste, for example, starts at the manufacturing level. Given the profound proliferation of the quartz category since 2006, when quartz, for the first time, took the crown away from natural stone as the best overall choice for countertops, the world has seen an explosion of quartz manufacturing facilities whose manufacturing, research and development of the material, has raced to innovate designs, but in the process created an abundance of out-of-spec material and slow-moving and discontinued colors. Add fabricator yield loss that often winds up in a dumpster, and the tonnage is almost incalculable.
The mineral surfaces category, which includes sintered stone, porcelain and ultracompact materials, is rapidly growing, although relatively smaller by volume than quartz. The value proposition is becoming clear that mineral surfaces are the next big surfacing category whose application, colors and aesthetics steadily increase every year.
Sintered stone, for example, is purely a mineral mix and can be reground back into its base mix and reformulated into new slabs. This is unique to sintered stone, unlike large format porcelain, which can use inks and dyes that compromise its ability to be reground into a pure mix. Porcelain can also use mineralbased colorants, which would be reground, but many manufacturers do not make this claim. Recycling and reclamation programs are all impressive in theory, but in reality, the programs’ implementation needs attention. Fabricators will need to bin and sort the offal from quartz, mineral surfaces and stone to keep them separate for individual processing, depending on if there are resins or if it is a mineral composition like stone or sintered stone.
In addition, regrinding does not come without concerns, including respirable crystalline silica, which, while safe to consumers when installed in a slab form, would need proper safety and protection equipment and infrastructure in place. Any facility constructed must have the appropriate systems and machinery to keep all operators and occupants safe. Both stone and engineered stone like quartz have crystalline silica; some sintered stones do not, and some new quartz formulations, like that introduced by Breton (Bioquartz), do not have crystalline silica in their mineral mix.
Back to this idea of teamwork. Viable, sustainable solutions that combat waste is front and center. The problem emanates from the cost of conversion for engineered materials. That is, what it costs to reuse or reform waste in terms of skilled labor alone, exceeds any realized value. Hence, little to no effort is invested, and the waste stream gets wider and deeper.
Industry teamwork, however, could be a viable solution for waste remediation. Oftentimes, a process does not become economically feasible unless done at scale. Engineered waste could likely fall into this category. Where one fabricator trying to convert all engineered waste into something of value is not in the least viable, perhaps a regional specialized processing center, for example, can repurpose (a combination of reuse and recycle) the materials at scale. Why scale? Mainly because a processing center would be highly operationally leveraged due to the nature of the material and the large scale and volume needed to reach and surpass break-even. Such a theoretical plant could make quartz bricks, create aggregate for paving, and a host of other assets that help to minimize waste accumulation and, at the same time, reduce demand for new materials and thereby preserve natural resources.
If we all banded together to support the operation, perhaps fabricators could get rebates based on the tonnage they contribute. After all, the operation’s raw materials could be included at a negative cost on their financials. For example, the operation charges to pick up the waste — the very raw material they need to make a new product — hence a negative cost. As an incentive to guarantee their supply chain, a discount or rebate could go to the fabricators who contribute their waste and are proactively part of an industry-wide solution — theoretically, a huge win/win.
Yes, this is big-picture thinking, but it’s necessary because the dilemmas grow and increase in severity without it. Participating in this sort of venture or anything similar would be crucial to being a LEEF. As we design the constituent parts of the certification, actions like these are highly aligned. A good next step is perhaps forming an industry waste alliance network with participants at every level — manufacturing, distribution and fabrication — to brainstorm and participate in solutions that significantly mitigate the waste dilemma and create an economically and environmentally viable solution.
While the industry is evolving and iterating, and materials are becoming healthier and safer for people and the planet, the surfacing industry is woefully behind in contributing to environmental health. In its inadvertent stockpiling of slabs, partial slabs, remnants and waste across thousands of fabrication shops, material manufacturing and distribution facilities should look at ways to mitigate adverse environmental impacts. With seemingly little to no economically viable solution to reuse, recycle or repurpose at the moment, perhaps the awareness we drive here is a first step in calling all parties to the table to start the conversation. There is much truth applicable here; it does, in fact, take teamwork to make the dream work.
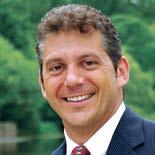
Paul “Max” Le Pera is the president and founder of Proprietary Ventures, LLC, a boutique-style global firm devoted to researching, discovering and deploying disruptive and sustainably oriented proprietary products and technologies. He serves on the ISFA board of directors as vice president of standards. He can be reached at paul.l@proprietaryventures.com.

Jessica McNaughton serves as president at CaraGreen, a provider of sustainable building materials, including many alternative surfacing materials. She has 20 years’ experience in sales, marketing, business development and strategy. Previously the director of sales and marketing at CaraGreen, Jessica has maintained her status as a LEED Accredited Professional since 2009 and she hosts a podcast, Build Green Live Green. She can be reached at jessica@caragreen.com.