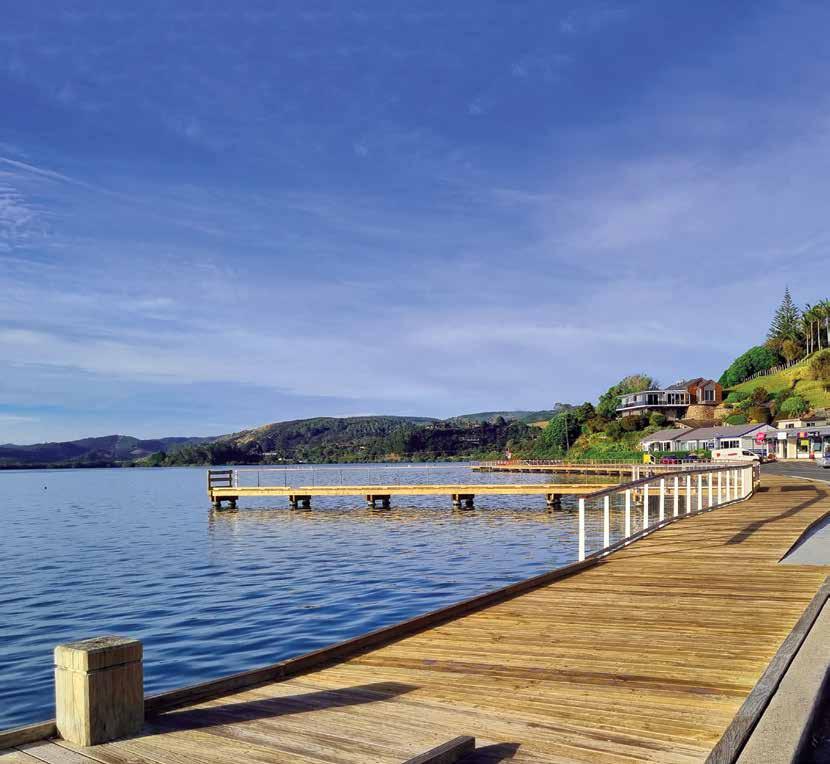
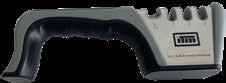
If you currently employ or supervise an ITAB apprentice, the existing support for you and your apprentice will continue unchanged (provided the apprentice remains a financial member of ITAB) until the apprentice has either:
In April 2020, the reform brought together New Zealand’s Institutes of Technology, Industry Training Organisations (ITOs) and Polytechnics as subsidiaries under a new organisation named Te Pūkenga.
The change aims to create a vocational education system that combines the functions of all of these organisations so that apprentices can easily move between on-the-job and off-the-job learning and online study.
According to Nick Matthews, Industry Pathways and Apprenticeship Manager, New Zealand Certified Builders, the forming of Te Pūkenga means every apprentice, regardless of what pathway they enrol into, has access to offsite training at a campus of Te Pūkenga.
“This means ITAB’s point of difference has been removed and is one of the reasons why the ITAB Board elected to remove the Industry Partnership and phase it out.”
▶ Completed their training and graduated from the ITAB Programme.
▶ Decides to withdraw or transfer to an alternative training programme.
If an apprentice decides to withdraw from ITAB, their training will be supported for the duration of their apprenticeship by the Institute of Technology or Polytechnic that they are currently enrolled with.
ITAB will no longer be available to new apprentices enrolling after 31 December 2022. ITAB will be phased out over the next 2 – 3 years while existing apprentices complete their apprenticeship training.
ITAB is an industry partnership between New Zealand Certified Builders and ITO’s nationwide. While ITAB will no longer be available from 1 January 2023, NZCB remains committed to quality training and support of Carpentry Apprentices.
NZCB will launch a new membership service, replacing ITAB, which is exclusively available to NZCB Business Members.
If you want to know more about these changes, please visit www.nzcb.nz for the latest updates.
A government review of vocational education in 2019 has resulted in an overhaul of how apprenticeship programmes in the building industry are managed.
Adapting your building or specifying habits to MBIE’s ‘Clause H1 – Energy efficiency’ is easier with Kooltherm. Here’s an insulation product that lets you achieve or exceed new standards in any New Zealand climate zone.
MBIE’s Building for Climate Change provisions were established in 2020 to help the building and construction sector achieve its contribution to New Zealand’s emissions reduction targets.
Specifically, Clause H1 will make new homes and buildings warmer, drier and healthier, with less impact on the climate. The new provisions represent the most significant changes in over a decade to energy efficiency requirements in the NZ Building Code.
▶ New climate zones: The changes introduce six new climate zones to reflect the specific weather experienced in different parts of New Zealand. Insulation requirements are prescribed for each zone.
▶ Thermal bridging: The recognition of thermal bridging impacts, where insulation effectiveness is compromised through heat loss or gain through building elements and penetrations, is a vital step in improving the overall performance of building envelopes.
While these changes are significant, New Zealand will still lag significantly behind international insulation standards. For example, the NZ changes achieve little over half the prescribed requirements for homes in the UK.
Kingspan is a global leader in developing and supplying high-performance building envelope technologies and systems. Our acquisition of Thermakraft in late 2021 means we can offer proven, innovative integrated insulation and building membrane systems. Using our systems makes meeting the required changes easy, allowing you to achieve international best practice levels without compromising ease-of-build and cost-effectiveness.
Kingspan Kooltherm is a closed-cell phenolic insulation with exceptional insulation and fire performance properties. Thickness for thickness, Kooltherm dramatically outperforms glasswool and other bulk insulations. It achieves a product R-value of 2.5 at just 50mm.
Kooltherm has exceptional fire performance, demonstrating low flame spread and smoke emission. Since it is a thermoset material, it hardens and chars in fire situations, giving off very little smoke, unlike thermoplastics, such as polystyrene, which melt, soften, and give off thick black smoke. Used either internally or externally, Kooltherm is ideal for continuous insulation to mitigate thermal bridging and achieve NZ compliance and above. It does this without necessitating adjustments to frame thicknesses or truss heights.
Lightweight and easy to install, Kooltherm products are easy to handle on-site without requiring huge piles of insulation bales. Moreover, concealing ceiling truss chords with layers of traditional insulation can be avoided with Kooltherm, which makes ceiling spaces safer.
Kingspan is ready to support your move to H1 Energy efficiency standards. To find out more, visit www.kingspaninsulation.co.nz or call 0800 806 595.
•
ITM recently hosted a series of ITM LBP training days where builders could get down-to-earth answers to some of the hard questions that commonly come up. Here's a summary of the training days' feedback about accountancy issues from
• Goodie bags • Spot prizes • Major prize
Codewords | On-Site Learning
Thursday, August 18th 8am-4pm Claudelands Events Centre Hamilton
Wednesday, July 6th 8am-4pm Trentham Racecourse Wellington
Register at: ITM.CO.NZ
Thursday, August 25th 8am-4pm Addington Racecourse Christchurch
spouse or partner who works in the business, helping reduced significantly in certain situations.
Q:
A: A straightforward solution is to use what we call a "Workplace Wellness Bonus". This allows you to provide gifts to your employees (and yourself) of up to $300 every three months, tax-free.
The most common method is to use gift vouchers. However, there are some exceptions to keep in mind. You cannot give vouchers for food or drink as these fall into the category of "entertainment" and are taxable, albeit at a lower rate than normal PAYE or other types of expenses.
Also, you can accumulate the quarterly $300 gifts and pay them in one lump sum of $1200 at one time, if you adjust for FBT annually, otherwise the gifts must be paid out in quarterly instalments.
A: There's a common myth that buying an asset before the end of the financial year will save you lots of tax. Unfortunately, this is not always the case.
Buying assets such as vehicles and equipment (over $1,000) doesn't immediately reduce your tax. You can claim depreciation on these items, but this happens over a number of years.
Buying your new gear before March 31st means you can claim a percentage of the depreciation in the following financial year. There may be some advantages if you have strong cash reserves in your company account.
But if you're using your overdraft facility to make the purchase, it could compromise your cash flow. The key is, don't run yourself short of funds thinking you're saving tax!
A: We offer services like cash flow management and growth strategies in addition to all the usual things you must do to satisfy the IRD. We provide a monthly or quarterly accounting service that provides realtime feedback on your business performance, cash position and tax obligations so you always know exactly where you stand.
For further information on Kiwitax services, go to www.kiwitax.co.nz
Q: Should I continue as a sole trader, or will I
How can I give my employees regular bonuses?The team at Kiwitax are ready to help answer your questions on business improvements, tax and accounting.
A: DriSpace is made up of three brands: DriStud, VENT and ProctorPassive. DriSpace systems offer a range of wall and roof underlays with Vent products.
▶ DriStud: A New Zealand building product brand servicing residential and commercial sectors. The product range includes several CodeMarkTM Certified products, such as Fire Retardant Wall Wrap, Fire Retardant and non-Fire Retardant Roof Underlays and Window Flashing Tape. We also have Self Supporting White Faced Foils!
Available as a 2740mm x 36.5m, 100m2 roll –minimum order of 36 rolls, printed here in New Zealand meaning short lead times. With seven colours to choose from, and a maximum of two colours per custom print.
Q: What is the benefit of VB20 as a Cavity Batten?
A: BRANZ Appraised VB20 is an easy-to-handle 1.8m length batten with a self-adhesive strip for temporary fixing. Offering airflow in the wall space, reducing the risk of moisture build-up and condensation, and when installed horizontally and continuously, VB20 offers vermin proofing to the bottom of the drained cavity. Dually beneficial, VB20 can be used in the roof cavity as specified in DriSpace Systems.
A: No corner moulds are required! CodeMarkTM Certified Cool Tape self-seals around fasteners when properly installed; therefore, only one layer is required on the sill. Unless you live in Antarctica (anywhere -6°C), no primer or heat gun is needed.
A: Yes! Installed with black side facing upwards, CodeMarkTM Certified DriStud RU24 is the best DriStud Roof Underlay to use on sheds.
▶ VENT: Particularly important with the upcoming H1 insulation change, VENT products offer a variety of solutions for passive ventilation systems in the roof cavity and wall space. From Roll Panel/Eaves Baffle Vent, Over Fascia Vents for Skillion and Trussed Roofs and ventilation and drainage battens for roof and wall –designed to create unimpeded airflow.
▶ ProctorPassive: ProctorPassive offers a variety of airtight membranes, ranging from high vapour permeable self-adhesives, UV resistant membranes and vapour retarder and convection barriers.
A: DriStud Wall Wrap is CodeMarkTM Certified and available for custom print – a great way to promote
For more info, visit www.DriSpace.co.nz or scan the QR code to view the product catalogue.
Q: Can I order
your business!The use of DriSpace products in this house helped ensure an energy-efficient, well-ventilated home, reducing the chances of condensation. Protor Passive Wraptite-SA is a self adhering airtight and vapour permeable membrane for wall and roof applications.
Q: I have a BLP-H type bracing element, but I don't have access to both sides of the framing. Can I install both the ply and GIB® plasterboard onto the same side of the frame?
A: Unfortunately, you cannot. Doing so would significantly reduce the performance of the bracing element.
We suggest you check with your designer to see if a single-sided bracing element would provide enough bracing units; if not, perhaps some additional bracing could be added elsewhere to compensate for this.
A: GIB Fire Soundseal® is only intended for use as specified within GIB® Fire Rated and GIB Noise Control® systems. It will maintain the fire rating and noise control performance of these systems, so depending on the system, it will perform up to 240 FRR.
If substitution takes place, obtain verification from the supplier of the alternative product.
A: There are a few things that may cause fastener popping. It could be framing movement or shrinkage, framing not properly aligned, causing additional pressure on fixing points resulting in board or fastener movement, or simply fasteners being over-driven or driven in on an angle.
To fix this, ensure the GIB® plasterboard is pressed firmly back to the framing and then place an additional fastener 50mm from the popped screw.
A: Firstly, the GIBFix® One is a water-based adhesive, and the GIBFix® All-Bond is a solvent-based adhesive.
Secondly, the GIBFix® One can be used in temperatures as low as 10°C whereas the GIBFix® All-Bond can be used in temperatures as low as 5°C.
Please note that water-based adhesives rely on the evaporation of water to cure; this means that when bonding surfaces together that are both impervious to water (such as steel framing and a moistureresistant plasterboard), the curing times will likely increase.
For this reason, GIBFix® All-Bond is the recommended adhesive for fixing GIB Aqualine® to steel framing and GIB® Rondo® metal ceiling battens.
For assistance on any specific GIB® product or system questions, don't hesitate to get in touch with the GIB® Helpline on 0800 100 442 or visit www.gib.co.nz
Q:
A: Engineered for durability, fibre cement is fireresistant, rot-resistant and resistant to moisture damage, making it the ideal low-maintenance alternative to traditional building materials. Hardie™ cladding products are resistant to cracking and warping, so hold paint well, extending the time before repainting, and you can paint it a large variety of colours, including darker shades.
A: Linea™ Weatherboard can be conceal-fixed, and gun nailed in wind zones up to and including Very High (VH), making for a quick install and a tidy finish with less work for the painter.
Face nails are only required at window/door jambs and corners or across the whole wall when in an Extra High (EH) wind zone. Unlike other weatherboards, you must predrill and nail through the lap when face nailing. Afterwards, you can hand nail or use a nail gun with the appropriate alignment tip.
or HomeRAB™
A: Simply use the 4.5mm, 6mm, or 9mm PVC Z Flashing. Ask your friendly ITM store for a copy of the Product Identification Guide by James Hardie for a full list of our products and accessories.
A: On hard surfaces (concrete, paving, etc.), you must maintain a gap of 100mm from the bottom edge of the cladding to the ground surface.
On soft surfaces (dirt, bark, etc.), you must maintain a gap of 175mm from the bottom edge of the cladding to the ground surface.
Q: I’m struggling to understand the fire requirements of my project. Can you help?
A: Of course! James Hardie has a comprehensive fire and acoustic manual and a range of solutions to meet 30, 60, or 120-minute fire ratings. You can find the manual at www.jameshardie.co.nz or call the helpful Technical Team on 0800 808 868.
A: James Hardie recently released interactive design models to bring the Technical Installation Manuals to life. You can find these on the James Hardie website and use them on your phone or tablet by downloading the Workingspec app.
A full suite of Technical Installation Manuals can be found on our website in PDF form, or you can order them through the “contact us” tab. We also have a highly knowledgeable and experienced Technical Team that can assist you on 0800 808 868.
A full suite of Technical Installation Manuals can be found on www.jameshardie.co.nz in PDF form, or you can order them through the “contact us” tab.
Q: Why would I choose James Hardie’s products for my next project?
Q: How do I nail off Linea™
Q: When joining RAB™ Board
Pre-Cladding end to end on a tall wall, how do I flash the joint?
Q: How do I get more information about how to install James Hardie’s products?
James Hardie have been helping create homes for New Zealanders for over 83 years – but that doesn’t mean we don’t get questions from homeowners, builders, and designers about our products. So here are a few common questions to help you on your next James Hardie project.
A: How much will depend on the width and depth of the gap you’re filling. Check the PDS for consumption or try the handy Sika Sealant and Consumption Guide - scan the DOWNLOAD QR code below to view the PDF.
A: Sika highly recommends that you do, but understand that as busy tradies, that might not always be possible. Make sure you keep the can on the gun until you can clean it, or replace the empty can immediately with a new Sika Boom can (to stop any air from entering the gun and curing the leftover foam inside the gun). And don’t forget, you can use the handle on the gun to hang it in your vehicle and keep the can upright. Scan the VIDEO QR code below to view a YouTube video on How to clean your Sika Boom Gun.
A: SSD means when preparing your concrete before applying repair mortars, it needs to be saturated with water, which gets absorbed into the concrete leaving the surface damp to the touch with no surface water. This is important, so the concrete doesn’t suck the moisture away from your freshly applied mortar and end up as a crumbly repair!
A: Yes. Sika BlackSeal Elastic is the premium product with the backing of BRANZ Appraisal (No. 770 [2018]) as a damp-proof membrane. Some people like to get a bit creative with using Sika BlackSeal in all sorts of places, but it’s only designed as a below-ground damp-proof membrane – i.e. behind retaining walls and basement walls which are then backfilled against. It should NOT be left exposed to UV. If you want to know how to do it correctly, do the free online course: scan the ONLINE COURSE Sika BlackSeal Elastic QR code below to take the course and learn how to correctly apply below ground waterproofing membranes.
A: Short answer – no.
The longer answer, silicones aren’t paintable, but many other sealant technologies are, such as modified sealants (like Sikaflex MS or Sikaflex AT Façade) and polyurethanes like Sikaflex-11 FC. Remember to test the paint on the cured sealant first and check the PDS for acceptable paints. Also, be aware that if your sealant is painted and moves (yes, they do move!), it may restrict the natural movement capability of the joint or cause some undesirable cracking or visual effect on the paint.
Q: Do I have to clean my
my
#PRO300SM25KA
• Ideal for underlay, subfloor, cement sheet, weatherboard, and decking applications.
• Designed to drive 40mm–75mm (8–12 gauge) screws.
• This kit includes: PRO300 attachment, extension pole, rugged toolbox, Makita® FS2300 screwgun fitted with MAA3G2 adaptor.
• The PRO250 is the preferred attachment for decking applications.
• Designed to drive 40mm–65mm (8–12 gauge) screws.
• This kit includes: PRO250 attachment, G2 extension, pack of deck clips, rugged toolbox, Makita® FS2300 screwgun fitted with MAA3G2 adaptor.
#PRO250G2DC2KA-S
• The PRO250 is the preferred attachment for decking applications.
• Designed to drive 40mm–65mm (8–12 gauge) screws.
• This cordless kit includes: PRO250 attachment, G2 extension, pack of deck clips, rugged toolbox, DeWalt® DCF622N screwgun (skin only) fitted with adaptor.*
• 10g x 50mm
• Box of 2000
• For subfloor, mid floor, timber-to-timber, timber flooring.
1:3
For scaffolds with a width of 800mm and wider, multiply the scaffold width by 3 to determine the maximum platform height for this width scaffold. If your required platform height exceeds this height, outriggers are required to increase the scaffold width.
For scaffolds with a width of less than 800mm, a 1:2 ratio applies to ensure stability.
Example: The 800mm wide Staffy Tough Tower can raise its platform up to 2.4m (3 x 0.8m = 2.4m) before outriggers are required. The 1.4m wide Staffy Tough Tower (TUT1400) can raise its platforms up to 4.2m (3 x 1.4m = 4.2m) before outriggers are required. The 0.75m wide Staffy Sprint Tower has a maximum platform height of 1.5m (2x 0.75m = 1.5m).
Note: The width-to-height ratios are a guide only. Other circumstances like high winds, uneven ground or type of work may require you to use outriggers.
A. If your scaffold is set up against a building, then one pair (2) outriggers are sufficient. Install them on the two external corners of the scaffold so that they run off at a 45-degree angle.
Four outriggers are required if your scaffold is used completely free standing, for example, in the middle of a warehouse.
Tip: Staffy Outriggers are telescopic. Set them up slightly extended and simply retract them when moving the scaffold. There is no need to dismantle them from the scaffold, and this saves time and increases safety during the move.
A. A certified scaffolder has to assemble any scaffold structure that exceeds an overall height of 5m. Any scaffolds where the highest platform exceeds 5m must be notified to WorkSafe NZ/Council 24-hours prior.
The Tough Tower 800 (TUT800-5). This one is 5m tall with a reach height of 6m and a platform height of 4m.
A. There is a common misunderstanding that handrails are only required if your work platform exceeds a specific height, e.g. 900mm, 1m or even 2m. There is no particular height that demands the use of handrails. Rather, it is your assessment of the likelihood and extent of injury by not installing a handrail in a specific situation. Assess the risk and then manage it.
Q. When is it necessary to use outriggers with my scaffold?
Earlier this year, Laminex challenged the way New Zealanders do walls and introduced a modern range of interior decorative wall panels called Surround by LaminexTM
Q: What is the panel thickness?
A: All profiles are 12mm thick except Classic VJ 100, which is 9mm thick.
Q: What is on the back of the panel?
A: All profiles come with a low-pressure melamine back except Classic VJ 100, which has a raw back.
Q: Can Surround by Laminex Panels be used on or to make cabinets?
A: Surround by Laminex is NOT suitable for cabinetry making. It can, however, be used as a decorative feature around a fixture such as a shop counter or kitchen island. A toe kick is recommended.
Available in classic and contemporary profiles, panels transform spaces by adding warmth and texture. The decorative front is conveniently pre-primed with water-based paint – ready to be finished and applied with a chosen paint colour.
Challenging the way New Zealanders do walls. 1 Since the launch, there has been significant interest and many questions relating to this new, innovative product range – including; Q:
Q: Can Surround by Laminex Panels be used on Ceilings or as flooring?
A: Surround by Laminex is NOT suitable for any ceiling or floor applications.
Q: Can the panels be used outside or in alfresco areas?
A: Surround by Laminex is NOT suitable for use in any exterior applications.
Q: How do the panels fit together?
A: The panels are easily attached together using the smart tongue and groove system.
Q: Why do I need to allow for a 10mm expansion gap when installing panels?
A: Surround by Laminex can be installed in interior applications, including; Hallways, bedrooms, playrooms, living areas, laundries1, bathrooms1, kitchens1, around kitchen islands2, around commercial counter tops2 and adjacent to fireplaces3
A: Surround by Laminex is made from Medium Density Fibreboard (MDF). MDF responds to the surrounding environment's humidity and temperature, affecting the product's moisture content, resulting in panel dimensional change.
A: Fill all nail/screw holes and imperfections with a compatible wood filler. Lightly sand the entire panel. Apply two coats of water-based paint. Follow all paint manufacturer's directions, including if the pre-finished base primer is suitable for the intended base finish.
A: All panels come in two sizes: 2400mm X 1200mm and 3000mm X 1200mm.
A community-led development in Mangonui (Northland) brings 500 metres of new boardwalk, two viewing platforms, swimming steps, a new jetty and pontoon, and additional parking to the picturesque harbourside town.
produced to their requirements,” says Northpine GM Bruce Larsen. “The engineers had specified some custom large-dimension products, including big structural members. We had to cut these to fit the brief, and we're one of the few sawmills that will cut bespoke.”
The design was by Rob Brown of Shorewise Engineering Consultants in collaboration with the Mangonui Community Group, whose brief was to create a cost-effective boardwalk that would unify the town's popular waterfront, improve safety, and stand up to heavy use.
“We set the deflection limits to avoid the vibration issues associated with people walking, cycling and running on public boardwalks,” says Rob. “We specified an SG8 pine size that we knew would meet the project's requirements for strength, cost and deflection limits.”
When United Civil Construction (UCC) won the tender, they chose Waipu-based manufacturer Northpine to supply the structural timber. “It was right at the time of Auckland's long Covid lockdown, and getting materials was difficult,” says the project manager at United Civil. “We went to see Northpine, and they pulled out all the stops to provide the product we needed to get underway.”
“The timber was high-spec, very dense, and everything was to be bolted and screwed in. The structural engineers specified 350mm deep joists as part of the design, and it creates a very solid structure – people run on it, scooter, cycle, and it doesn't vibrate.”
Northpine supplied their specialist Northbeam range for bearers, joists and decking. “Our quote was part of United Civil Construction's tender and was
The properties of mature Northland-grown radiata aided in creating these large structural members. “Some of the large dimensions, like 350 x 150, are as big as you can go and still meet the standards for structural compliance,” says Bruce. “It's all about the raw material – denser northern timber can meet the specs.”
Watch the short video on www.youtube.com. Search for ‘Mangonui Waterfront Walkway’.
Northpine products are BRANZ Appraised and independently verified by Grade Right. Founded in 1999, Northpine is based in Waipu, with a distribution centre at Silverdale which dispatches to ITM stores around New Zealand.
For more information: call 0508 432 115 or email northbeam@northpine.co.nz
The current shortage of products means builders are increasingly turning to alternatives. This can be potentially problematic, and MBIE has recently released specific guidance on what products can be substituted for plasterboard.
It has been well documented that Aotearoa New Zealand is currently facing a shortage of plasterboard and other commonly used building products. This is mainly due to supply chain issues associated with the downstream effects of COVID-19 and elevated demand levels.
Consequently, there is an increased possibility that some building products specified as part of a building consent may need to be substituted with a similar or comparable product.
The Building Code sets the minimum performance requirements that all building work must meet. However, it does not prescribe which materials, building methods or products to use.
Designers and homeowners can choose the product that fits their requirements if they can provide evidence that it complies with the relevant performance requirements of the Building Code.
MBIE recently released the guidance document Product substitution – plasterboard for building consent authorities (BCAs), designers, contractors and building owners to better support them in using building products that differ from those initially requested by owners and specified in building consent applications.
It outlines a pathway to product substitution and compliance for plasterboard and other wallboard products and is best read in conjunction with the more general Product substitution guidance published by MBIE in November 2021.
The guidance was developed with BCAs to manage the approval of plasterboard substitution in a more nationally consistent manner.
In addition, MBIE has published the Step-bystep guide for plasterboard product substitution, showing the roles played by manufacturers, designers, building consent officers and builders.
The plasterboard product substitution guidance lays out a three-step approach consistent with MBIE’s broader product substitution guidance:
1. It encourages people to consider the legal context, particularly any additional obligations and compliance-related matters that might arise from a product substitution.
2. It points to the broader implications of using a different product than specified, including whether it is fit for the same purpose and still meets the owner’s needs.
3. It talks people through how to implement changes to consent - for example, if substituting the product requires a minor variation or for more complex changes, it might trigger an amendment to the building consent.
In summary, it also:
▶ outlines and encourages the use of the minor variation process for substituting plasterboard
▶ lists those products that can be substituted as a minor variation
▶ explains what should be considered when substituting plasterboard that has:
▷
standard performance requirements when used as lining only
▷ additional performance requirements such as a substrate lining in areas subject to water splashes, such as bathrooms and kitchens, or as an element within a fireprotection system, a sound-rated system or a bracing system
▷ advises what can be done in the design stage to avoid the need for product substitution - the consideration of other products and construction methods.
▷ provides an appendix of links to additional product information that may be useful to show compliance with the Building Code.
A designer or builder who wishes to substitute a building product should ensure that:
▶ the customer is informed about and has agreed to the substitution taking place
▶ they provide adequate evidence so the BCA can be satisfied on reasonable grounds that the building work will continue to comply with the Building Code
▶ they are on site to talk to the building control officer (or are available in the event that it is a remote inspection) about the proposed substitution and provide documentation if this is requested.
Failure to provide sufficient information may lead to delays in assessing variations or rejection of the application or require an amendment to the building consent to be applied for.
Most designers will try to avoid specifying products likely to be substituted during construction.
As a reminder, however, designers should check on the availability of products in short supply and consider whether any of the following are more readily available and could be suitable alternatives such as:
▶ Other readily available plasterboard products.
▶ Non-plasterboard panel systems such as plywood.
▶
Alternative construction systems.
by Paul Hobbs Principal Advisor, Building System Assurance, MBIE CARPENTRYThis article is relevant to these classes:
1. Does a building owner need to be made aware that a consented building product is to be substituted with another product?
a) Yes b) No c) Maybe
2. When should the BCA be made aware of a product substitution?
a) After the product has been substituted b) Before the product substitution takes place c) While the product substitution is taking place
3. What needs to be in place before a minor variation can be approved? a) Relevant technical information b) Applicable installation details c) Approval from the BCA d) All of the above
Answers: 1.a 2.b 3.d
This article is from Codewords Issue 109.
Log-in to the LBP portal lbp.govt.nz and update your Skills Maintenance activities.
For years, the most significant query we had at bbi® from customers looking at our interior lining solutions was, ‘Are these rated for bracing?’. Well, after so many ‘not yets’, the answer is now a resounding ‘Yes!’.
bbi® RedLine® and BlondeLine® Birch have now been tested using the P21 method for bracing. They can now be used for interior linings where bracing is required under the new PlyBrace™ System, which also includes the bbi® AraucoPly® 7mm DD F8, tested right down to a 200mm wall size.
Thanks to this testing, bbi® can now offer bracing and lining solutions in both light and dark finishes, in economic Poplar core or Premium Hardwood cores. bbi® even offers RedLine® and BlondeLine® Birch in the Plus range with a matt UV coating on both sides for ease of finishing.
bbi® RedLine® is available in three types under the PlyBrace™ System:
▶
bbi® RedLine® Poplar Core
▶
bbi® RedLine® Plus Matt UV Coated Poplar Core
▶ bbi® RedLine® Premium Hardwood Core
bbi® BlondeLine® Birch is available in two types under the PlyBrace™ System:
▶
bbi® BlondeLine® Birch Poplar Core
These products make for a great aesthetic in your interior space and are available in varying thicknesses and lengths.
bbi® PlyBrace™ is easy to install when you follow the installation guidelines in the bbi® PlyBrace™ Technical Document. All products in the PlyBrace™ range are fixed in precisely the same way. This makes installing bbi® PlyBrace™ quick and easy. By removing the need for stopping and sanding, your project can be finished much faster!
The bracing ratings, also available in a handy table in the bbi® PlyBrace™ Technical Document, can be plugged into any bracing calculator to give you what you need for installation.
▶
bbi® BlondeLine® Plus Birch Matt UV Coated Poplar Core
For more details or to download the bbi® PlyBrace™ Technical Document, go to www.bbi.net.nz
TimberTech is a premium, composite decking product that takes stain and fade resistance to an entirely new level. With the texture and feel of real wood, this is the ultimate in low maintenance, aesthetically pleasing decking solutions.
TimberTech composite decking combines post-consumer recycled plastic, virgin plastics and reclaimed wood fibre from the US Woodworking Industry. Up to 80% of the capped composite deckboards are made of recycled content, making it a sustainable and responsible option. TimberTech have also invested in a state-of-the-art recycling plant that is committed to increasing the amount of recycled content in their products without compromising on providing industry leading warranties. Visit www.timbertech.nz for more info. Call 0800 786 883 or email info@psp.co.nz to request a sample.
Protected Backed by industry leading warranties.
Durable Resists mould, mildew, and moisture damage.
Beautiful Texture of real wood grain.
Low maintenance No annual sealing or staining.
Enduring Resists stains, scratches and fading.
Recently a colleague posed a question: Currently I have a Design AoP 2 licence. Do I need to apply for a Design AoP 3 licence to be able to carry out design work under the new Medium Density Residential Standards (MDRS)?
The answer is that you may need an AoP 2 licence if the design work comes within the definition of restricted building work (RBW), but not a Design AoP 3.
The reason the answer is ‘may’ and not ‘must’ relates to differences in the height limits in the definition of RBW in the Building (Definition of Restricted Building Work) Order 2011 compared to those in the Medium Density Residential Standards (MDRS).
Clause 6 of the Order states the kinds of design work that are restricted building work. These are ‘the preparation of any drawing, specification, or other document, according to which:
a. the primary structure of a house or a small-tomedium apartment building is proposed to be constructed or altered; or
b. any external moisture-management system attached to or forming part of a house, or a small-to-medium apartment building is proposed to be constructed or altered.’
The terms ‘house’ and ‘small-to-medium apartment building’ are defined in clause 3 of the Order.
A house means ‘a free-standing, fully detached building consisting of a single residential unit – or a single residential unit and 1 or more residential facilities’.
A small-to-medium apartment building means ‘a building that:
a. contains 2 or more residential units or residential facilities
b. does not contain parts that are neither residential units nor residential facilities
c. has a maximum calculated height of less than 10m.’
It is in the last part of the definition of small-tomedium apartment building that the differences with MDRS arise.
Clause 3 of the Order provides the following further definition: ‘maximum calculated height, in relation to a building, means the vertical distance between the highest point of its roof (excluding structures such as aerials, chimneys, flagpoles, and vents) and the lowest point of the ground’.
The MDRS however, allow for a maximum building height of 11m plus 1m for a pitched roof. This exceeds the maximum calculated height provided in the Order.
If the design work comes within the RBW definition, a designer will have to be licensed and hold a Design AoP 2 licence.
Generally, Design AoP 1 licence holders are restricted to Category 1 buildings, AoP 2 to Category 1 and 2 buildings and AoP 3 to Category 1, 2 and 3 buildings.
However, if the building is a small-to-medium apartment building that exceeds 10m from its highest to lowest points, it would fall outside of the RBW definition. The design work would not have to be carried out by an LBP.
Caution is still advised, even if the design work is not RBW.
First, LBP designers can be held responsible and accountable for their work, even if it is not RBW – the broadest disciplinary charge under the Building Act is negligence and incompetence.
The specific charge (section 317(1)(b) of the Building Act) relates to building work, not RBW. Building work is defined in section 7 of the Act. It is much wider than RBW and it would include design work relating to an MDRS structure that is higher than 10m.
Second, the disciplinary regime focuses on competence. One way of assessing an LBP designer’s competence is by checking the AoP licence they hold as defined in the Building (Designation of Building Work Licensing Classes) Order 2010.
Interestingly, the height limits in Category 3 buildings in the Order fall outside the definition of RBW – perhaps future-proofing them should the definitions of RBW be extended in the future.
Be wary of carrying out work outside of your competence – for example, a designer with a Design AoP 1 licence developing a consent for an MDRS building with a high risk matrix score or near the upper limits in the allowable height. This is another disciplinary charge under the Act (section 314 and 317(1)(h) of the Building Act) and another reason for caution.
It’s also worth noting that a designer who works outside of their personal competency may run into issues with their professional indemnity cover and their civil liability to their clients.
Finally, remember, the LBP Scheme and areas of practice are designed to recognise the competence of designers so that consumers can choose the right person for the job. The scheme relies on designers using their licence responsibly to ensure quality compliant homes are built.
by Faye Pearson-Green Building Practitioners Board MemberThis article is relevant to these classes:
1. What is the maximum calculated height of a small-to-medium apartment building under the Building (Definition of Restricted Building Work) Order 2011?
a) Less than 10m b) 11m plus 1m for the pitched roof c) 10m or higher
2. What is the maximum height of a small-to-medium apartment building under the medium density residential standards?
a) Less than 10m b) 11m plus 1m for the pitched roof c) 10m or higher
3. How is the maximum calculated height measured under the Building (Definition of Restricted Building Work) Order 2011?
a) The vertical distance between the upper surfaces of the floors of the lowest and highest storeys. b) The vertical distance from the lowest storey floor to the upper-most ceiling in the building.
c) The vertical distance between the highest point of its roof (excluding structures such as aerials and chimneys) to the lowest point of the ground.
Answers: 1.a 2.b 3.c
This article is from Codewords Issue 109.
Log-in to the LBP portal lbp.govt.nz and update your Skills Maintenance activities.
•
The biggest story in the construction industry over the last 12 months has been about material shortages, labour shortages and constant price rises. It's frustrating and contributes to increased stress for both the builder and the client. Projects are delayed, and budgets are strained.
Despite press coverage about lengthening supply chain timelines, most clients have an unrealistic expectation that their projects won't be affected. So delays to their move-in date can make them frustrated. While supply issues seem to be improving in the past 4-6 months, they are not over. Then, while material supplies are improving recently, the time it takes to secure the first Council inspection is double the historical average! (Infometrics July 2022).
Sometimes one problem can lead to another, and timelines are further pushed out. For example, a product specified on the consented plans may suddenly be unavailable or severely delayed. A decision is made to substitute an alternative material to keep the project moving. Unfortunately, this may require the architect to prepare amended drawings, which takes time and then apply for an amendment with Council, which takes more time. Most Building Consent Authorities are already straining at the seams, and these substitution amendments add more fuel to the fire.
The net effect of these supply and price pressures is forcing down profits and putting additional strain on business cash flow. Suppose you are not keeping up with this situation through regular project budget and timeline reviews. In that case, you can be sucker punched by an apparent sudden change in your financial situation. In reality, it doesn't happen suddenly, and it builds up over time and then comes to a head - a bit like the build-up of cholesterol in the arteries causing a heart attack.
Consider the building company in the table on the next page. It's a fictitious company, but a real example of the significant effect that project delays can have on a company's bottom line. The company, in this example, turns over around $1 million per year. I spread the Income, the Cost of Sales and Overheads evenly over six months. The top chart shows a Gross Margin of 18% and a Net Margin of 6%.
The lower chart shows what happens when a project is delayed by one month during months 2 and 3. In reality, projects often have multiple, smaller delays, but for ease of calculation, I have lumped all the delays in 1 month. Income is halved across months 2 and 3, and the Cost of Sales is not quite halved
because you often have employees to pay during delay times. (Not everyone has only contractors on a "no work, no pay" basis). Overheads continue uninterrupted, so the Net Margin goes from +6% to -20% over this delay period. Over the six months, the total Net Profit drops from $30,000 to $3,000, which comes straight out of the owner's pocket. The Net Margin drops from 6% to 1%.
As you can see, project delays can significantly affect profitability and subsequent cash flow in a construction business. If margins are thin, these effects can be even more severe.
So, what are some things you can do to prevent or manage these situations? The following are some suggestions to think about. In the interests of brevity, I will list various strategies. If you want more information on these and how they can be implemented into your business, please email me and I can advise you further.
▶ Know your numbers and monitor them regularly.
▶ Plan for the worst.
▶ Use the right contract terms.
▶ Educate the client on what may happen and what you will do about it.
▶
Don't be too greedy on the amount of work you go for.
▶ Buy and store key materials.
▶ Seek higher deposits and bill ahead.
These are a few ideas that you should consider implementing into your business plan in 2023. The current business environment requires you to approach your operation differently than in recent years.
By putting a more proactive plan in place, you will be better prepared to handle these challenging times and reach the end in a stronger position.
by Andy Burrows Business Advisor, Mentor and CoachAndy specialises in working with the owners of construction related businesses to build systems and profitability into their operations.
For further guidance on adapting your business plan to maximise your success, contact me at andy@tradescoach.co.nz or visit my website: www.tradescoach.co.nz
The Red Stag Group’s long-standing vision is to be an industry leader, aiming to achieve the best in everything they do. This focus is applied to workplace culture, environmental and safety standards, product manufacturing processes and use of technology.
Red Stag has developed an Environmental Product Declaration (EPD) to help to showcase the environmental credentials of their wood products. The EPD also provides life cycle data for calculating the impacts of wood products at a building level. This data may be used by specifiers and developers to calculate and present the environmental impacts of particular construction projects.
This EPD allows the represented products to qualify for points under green rating tools, such as the Green Star rating tool of the New Zealand Green Building Council (NZGBC).
The EPD measures and documents the impact on the environment in terms of:
The Red Stag Timber sawmill site has been in a constant state of improvement since 2003. Modernisation of processes with state of the art systems and equipment offer higher efficiencies and lower impact on the enviroment.
In the early days, some timber preservation was carried out off-site, incurring transportation costs and carbon impacts. Investment into on-site closedloop preservation plants has eliminated the need for double-handling and produces higher quality products with a lower environmental impact.
Additional new boilers at the new Energy Centre generates more energy from burning wood waste. This energy, by means of steam, is used to operate the kilns.
Looking to the future, Red Stag has gone beyond simply looking at ways to improve environmental performance and have extended to staff and visitors charging stations for EVs using the on-site electricity. This promotes the use of low cost pollution-free transport as well as giving flexibility to site visitors who may be coming from afar and needing to recharge for their trip home.
Over the longer term, Red Stag are looking at new ways of protecting kiln dried product without the use of plastic film. Until then, methods of reducing wastage of plastic wrap and strapping are being investigated and recycling is being encouraged.
Over recent years, Red Stag has made significant investments into plantation pine forestry for timber.
The carbon-sequestering nature of wood is a significant benefit of its use in construction. Trees extract carbon from the atmosphere and store it away for the tree's lifespan. Once harvested, the lumber continues to store carbon for the entire economic duration of the structure it has become part of.
Research has shown that over and above the many environmental benefits, in living spaces and working areas where wood is an integral component, the aesthetic and ambient qualities positively contribute to the well-being of the occupants. These inherent characteristics of wood offer contributions to the planet and to human habitation that are unmatched by any other building material.
Red Stag Timber products have a highly positive environmental impact compared to many alternatives.
Red Stag Timber utilises wood waste offcuts and sawdust from sawing and planing as a bio-fuel to generate electricity and provide thermal energy to dry timber.
Red Stag Timber is also a net exporter of electricity to the national grid to help power New Zealand’s growing energy needs. The Red Stag Energy Centre produces a total of 50MW of Energy, and up to 7.5MW of Renewable Electricity Generation– or enough to power 20% of the homes in Rotorua.
Utilising its own wood-waste as an energy source ensures that both CO2 emissions and landfill disposal requirements are minimised.
Timber products may undergo a preservation process where environmentally stable chemicals, all of which meet applicable safety guidelines are applied to meet and exceed all applicable treatment standards and to ensure a long and useful life in their intended application. Red Stag Timber was a pioneer in promoting the reintroduction of boron as a safe and effective preservative.
Treated timber products include those treated with boron, Light Organic Solvent Preservatives (LOSP) and Copper chrome-arsenate (CCA). No products declared within the company EPD contain substances exceeding the limits for registration according to the European Chemicals Agency’s ‘Candidate List of Substances of Very High Concern for Authorisation’.
At the end of its useful life, a timber product is removed from the building and may end up recycled, reused, combusted to produce energy, or landfilled. In New Zealand, the most common end-of-life method is landfill, especially for treated products, which have limitations for recycling and incinerating. The landfill scenario and other possible end of life scenarios are described in the EPD document.
Red Stag Timber has become a recognised market leader in terms of product innovation, manufacturing capacity and conservation having received the 2018 EECA award for large Energy User of the Year.
Over the past 15 years Red Stag has taken measures to improve the local and greater environment through various conservation and sustainability measures.
The full EPD document is available to view online - scan the QR code above or visit www.redstagtimber.co.nz/about-us
This sounds like an unlikely scenario, but it is precisely what happened to our client in the Auckland region a few weeks ago. A large tree was blown over in a storm, destroying the motorhome and severely damaging an adjacent vehicle. Fortunately, no one was hurt, and more severe damage was avoided, although a worker’s personal vehicle was also hit.
Unfortunately, the motorhome had appreciated in value by about $20,000 since it had been originally insured. While it is unusual for vehicle values to go up, we have seen this through increased pressure on global supply chains over the last few years, particularly in some trade vehicles and motorhomes.
Lesson: if your assets are increasing in value (including your home or other property), don’t wait to increase the sum insured.
This client had chosen to insure his tools for $10,000 because even though he owned substantially more than this, the likelihood of a larger claim was low since the tools are typically spread across multiple vehicles and sites.
The first claim was for tools stolen from a van. The quote to replace the stolen items came to $12,000, wiping out the $10k insurance cover. Nine days later, while the first claim was still being sorted out (client compiling proof of ownership and a complete list of the stolen items), a container was broken into, and more items were stolen. Unfortunately, because the first claim wiped out the sum insured, there was no money left on the policy for the second claim.
The amount of a claimed loss can be reinstated, upon payment of further premium, but only after the claim is settled.
Lesson: insuring a lesser amount than the value of your total tools can make sense when they’re spread around, but you take the risk if a claim is larger or multiple claims exceed your cover limit.
In this case, the builder had arranged contract works insurance for a new home build. It was a full build job, so he insured for the entire contract value. Late in the project, some appliances were
stolen. However, the homeowner supplied these appliances, and they were not part of the builder’s contract price.
Typically, a contract works policy will provide automatic extensions on top of the contract value for post-loss allowances. These allowances are usually specified in the build contract, and there are industry standard amounts that contract works insurance policies default to. If these amounts are changed in the contract, the policy can be updated to match them.
In this case, these amounts were removed from the contract works insurance application, so none were allowed for. One of those allowances is an extra amount to cover materials the homeowner supplies outside the original contract price. This is fairly common, for example, if the client wants to purchase their own whiteware, kitchen cabinets, or bathroom vanity. The policy should include a “principal supplied materials” amount to account for these so they are insured. In some cases the insurer gives an allowance of 10% to account for this, in others you need to specify the amount.
Lesson: Make sure you follow the requirements of your contract for these allowances. If the homeowner is going to supply some of the materials themselves (or perhaps even arrange their own subcontractor for some work), make sure this is allowed for in the contract works insurance.
Under cooking your cover can come back to bite you! Make sure you understand what’s in your policy and carefully consider the sums insured, both when you take it out and at renewal. If anything changes during the period, be sure to let your insurer know as well.
by Ben Rickard Trade Insurance Expert at BuiltinWritten on 7th October 2022. The information presented in this article is general and not intended to be financial advice for individual situations. It would be best to speak to an expert about your specific circumstances and needs.
It’s been a lousy month for underinsurance, with three claim examples that should remind everyone to double-check your cover is sufficient.