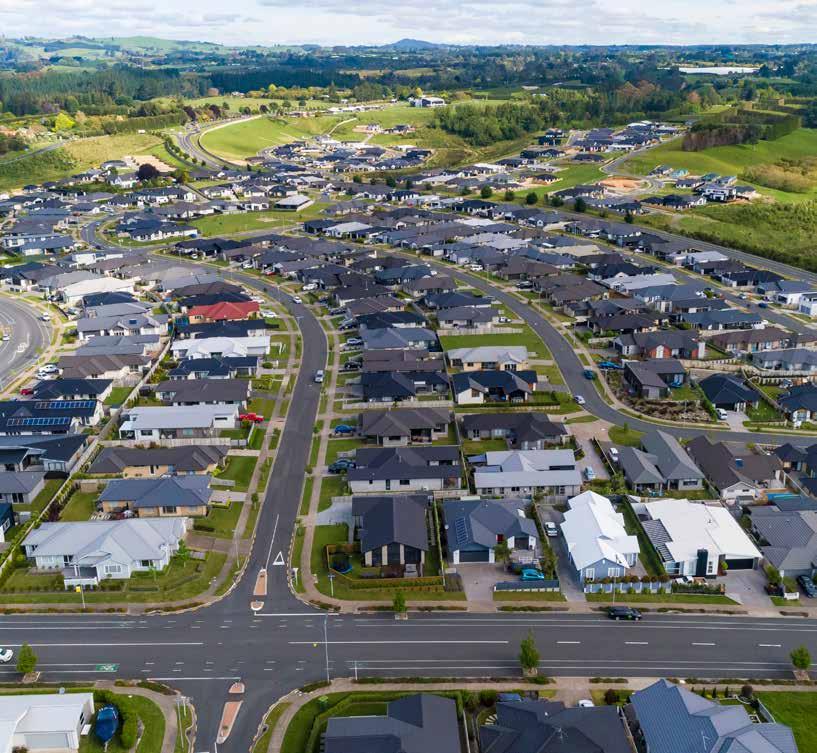














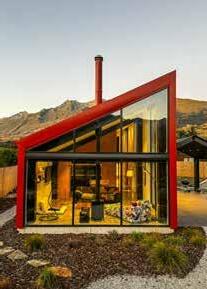





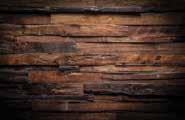



a granny flat or tiny house without the red tape:
How easy will it be?
The government's plan to simplify granny flat regulations could profoundly affect the building industry, opening up a new stream of opportunity for residential builders.
Under the proposed changes, people will be able to build a small, secondary self-contained dwelling on their property without needing resource consent, making the whole process easier and more costeffective.
The government says the proposals will "make it more affordable for families to live the way that suits them best," and "unlocking the space in the backyards of family members opens the door to new ways of living."
Announcing the changes, NZ First leader Winston Peters said the concept of a granny flat wasn't just for seniors.
"They're also increasingly popular with families whose university-age children can live at home but maintain some privacy and independence, or families who want to provide extra support to a loved one."
A discussion document detailing the proposed changes was released in June and includes a range of options for setbacks, including one that
requires no minimum setback, meaning the second dwelling could be built right up to boundary lines, thus maximising the space available for building.
The proposals apply to small (60m2 or less), detached, self-contained, single-storey houses for residential use with a principal residence on-site, and the two will be held in common ownership.
According to Stats NZ, the median floor size of a new home consented in 2022 was 126m2. A second dwelling would be just under half the size.
Bill McKay, a senior lecturer in the School of Architecture and Planning at the University of Auckland, says that a dwelling of that size could easily have two bedrooms, a living room, kitchen, dining and a bathroom.
Also included in the discussion document is the proposal to add a new schedule to the Building Act to allow "simple standalone houses" up to 60m2 to be exempt from a building consent, provided the dwellings conform to certain "conditions and criteria" yet to be determined.
The coalition government announced a raft of planning law changes in July aimed at significantly reducing the cost of building in New Zealand. The main thrust is to free up more land for development to reduce section costs and make it easier and cheaper to develop the land into housing.
The reforms will remove council powers over urban boundaries and development standards. Councils' ability to set fixed urban-rural boundaries will be abolished, as will their powers to mandate minimum floor area sizes or balconies for developments.
In announcing the proposed changes, Housing Minister Chris Bishop said current requirements imposed by some councils can significantly increase the cost of new apartments and referred to a 2015 report showing that in the Auckland market, balcony size requirements increased the costs of an apartment by between $40,000 to $70,000 per unit.
He said the government was "unshackling the developers and unshackling the house builders from the red tape and the planning rules that stymie development."
Bishop said the changes would ultimately "flood the market with development opportunities, and over time, drive down land prices and the cost of housing."
"People often complain to me about all these 'shoebox apartments', and I agree that they won't be the right housing solution for everyone. But you know what is smaller than a shoebox apartment? A car or an emergency housing motel room.
"We need change. After inflation, house prices have increased by more than any other OECD country in the past 30 years."
The existing National Policy Statement on Urban Development (NPS-UD) only requires councils to "live-zone" feasible development capacity to meet three years of demand at any one time. Under the new regulations, the government will require the 24 city, district, and unitary councils representing our largest cities to zone for 30 years of housing growth, freeing up vastly more space.
House zoning targets will be set for councils; urbanrural limits will be scrapped; mixed-use zoning will be encouraged; minimum floor sizes and balcony requirements for apartments will be abolished; and the government will more tightly define highdensity transport corridors eligible for development.
The government is taking steps to make remote building consent inspections the default standard throughout New Zealand.
Building and Construction Minister Chris Penk announced in July that the government will seek feedback on the move, saying a video conferencing approach will reduce travel times and delays in getting a building consent.
"Remote inspections offer significant productivity gains that make it easier and cheaper to build. However, the use of remote inspections is currently inconsistent across the country, with some councils being reluctant to use it," he said.
Penk said the move would also lower transport emissions, lead to better record-keeping and documentation, and reduce the time wasted by increasing flexibility for inspectors and building professionals alike.
Auckland’s Daniel Smith (32) from Structured Builders has won the coveted title of New Zealand’s top apprentice at the NZ Certified Builders (NZCB) Apprentice Challenge sponsored by ITM. Roy Devereux (23) of Devereux Builders from Otago won second place, and Courtney Willan (28) of Edgecity Builders from Auckland (north) came in third.
The NZCB Apprentice Challenge National Final took place at NZCB’s annual conference in Wellington on 21-22 June, where 20 regional finalists from across the country competed for the top prize. Apprentices were judged on examples of their work, dedication towards their apprenticeship, and a presentation to hundreds of NZCB member builders attending the conference.
As well as the title of New Zealand’s top apprentice, Daniel Smith returns to Auckland with a $10,000 prize package from ITM and the Ken Read Memorial Trophy. The second-place winner heads home with a $7,000 prize package from Milwaukee Tools NZ, and the third place-getter leaves with a $5,000 prize package from Winstone Wallboards.
Promising signs for the next generation of builders
NZCB Chief Executive Malcolm Fleming says that the talent seen in New Zealand’s next generation of builders at the national final is a great sign for the future of the construction industry as it grows and adapts to meet evolving needs.
“The apprentices that competed in this year’s NZCB Apprentice Challenge demonstrated enthusiasm for the carpentry trade and a high level of skill, which is incredibly promising for the future of the industry.
“To ensure that we continue to grow the number of qualified builders in New Zealand and meet the demand facing our sector, it’s vital we support our apprentices and provide them with opportunities to put their skills to the test and thrive,” says Mr Fleming.
NZCB also runs The NZCB Apprentice Network, an initiative launched in 2023 and free to all apprentices employed by NZCB member builders. The NZCB Apprentice Network offers wraparound support to apprentices throughout their apprenticeships. It provides access to mental health and wellbeing support, deals and discounts for trade tools, and ongoing access to professional development and networking opportunities. The initiative is also designed to equip employers with tools and resources to enable them to create a supportive workplace.
Adesanya Close is a new development in Palmerston North offering highquality rental accommodation. Designed by Houston Architects, the seven two-storey homes feature distinctive architectural elements, including the use of Cemintel Territory Woodlands. This durable fibre cement cladding mimics natural timber while minimizing maintenance.
It only needs a wash every year to stay looking good
Cemintel Territory Woodlands in Teak was chosen for its natural woodgrain appearance without the high maintenance of real timber. As a CodeMarkcertified fibre cement wall cladding system, Cemintel Territory offers the aesthetic of timber with minimal upkeep. Having used Cemintel in previous projects, the architects knew it was a reliable choice. "We'd used Cemintel before, and what we like about it is that it keeps the timber woodgrain look without weathering," says Wayne Houston of Houston Architects. "It's not easy to maintain actual timber, so we really like the fact that Cemintel keeps looking good over time."
Femi Adesanya, Director of The Stylebender Limited, appreciated the low maintenance of the Cemintel cladding. "We don't need to do heavy maintenance like painting for the next 15 to 20 years — all we have to do is wash it every year," says Femi.
This was the first project where the builders used Cemintel, and the developer was pleased with the hands-on approach of the technical team, who visited the site to demonstrate the installation. Houston Architects had confidence in specifying the product, knowing any issues would be resolved.
"We were able to specify confidently, knowing wherever it was specified, any problems would be overcome," says Wayne.
An attention-getting cladding
The result is seven stunning homes with a unique cantilever design and combination cladding, offering a refined look to the build-to-rent development. The low-maintenance Cemintel Territory Woodlands cladding ensures the homes will look good for many years. "I'm very pleased with the Cemintel cladding. I'd use it again quite happily," says Wayne. "We've even had comments from people in Palmerston North — 'What's that product? We love it. We want to use it'."
For Femi, the cladding and overall design met the brief perfectly. "We're extremely happy. The homes have come out beautifully," he says. "I haven't met anyone who has seen the homes and hasn't commended the project in terms of architecture, materials, uniqueness of the whole concept, and above all, the thoughtfulness of providing quality accommodation for those who want to live in good homes but can't afford to buy yet."
Extreme weather events have highlighted the woeful condition of the infrastructure essential for New Zealand cities and communities to function. Ageing water, sewage, energy, and transport networks have all been shown to be vulnerable. So what can we do about it?
Central government and councils are struggling with the ramifications of decades of underinvestment in infrastructure, and communities are reeling from unprecedented rate increases to fund urgent upgrades.
The storms in 2023 left many communities devastated, with no water, power, communications, internet and no way of getting help due to widespread flooding, slips and road washouts.
Even one of the basics of our needs – clean water – is a major concern with alarming reports of contaminated public water supply in some regions.
The recent Havelock North Campylobacter water contamination tragedy, where over 5,000 people became ill and people died from associated causes, highlights a systematic failure in our water infrastructure.
A Ministry of Health drinking-water standards review outlined that compliance with drinkingwater standards in many parts of New Zealand is ‘unacceptably low’.
Upgrading infrastructure won’t happen overnight, but it is essential for the future of our economy and the well-being of all New Zealanders. A key United Nations sustainable development goal is building resilient infrastructure.
The goal states that “economic growth, social development and climate action are heavily dependent on investments in infrastructure, sustainable industrial development and technological progress.”
While builders have little control over major infrastructure like water supply, sewage systems, energy supply, transportation networks or communications, a number of things can be done to build extra resilience into a new build.
Some examples include:
▶ Carefully evaluate the section for risk of land movement, flooding, exposure to strong winds or risk from sea level rise.
▶ Ensure foundation design, drainage, and stormwater systems can cope with extreme weather events.
▶ Incorporate passive solar design to reduce the need for supplementary heating/cooling.
▶ Use solar panels to minimise dependence on the national grid.
▶ Choose energy-efficient appliances.
▶ Make provision for rainwater harvesting and storage.
Given the unusual weather events over the last few years, people planning to build a new home are acutely aware of the shortcomings of our national infrastructure and the need to plan for a future where climate change will inevitably affect their homes. Builders should be proactive in having candid conversations about these issues with customers.
This article is the third in a series of articles exploring the United Nations Sustainable Development Goals and how they affect building and construction in New Zealand.
Goal 9: Industry, innovation and Infrastructure.
For further information, visit sdgs.un.org/goals
Bring beauty to the exterior of your next project, with Dimond’s low maintenance range of roofing and cladding profiles. Style with durability and proudly displayed for the world to see.
dimond.co.nz
#032CT10+2
• Coarse toothing for fast and precise cuts
• Universal open-back fitting
• Pack of 10 blades + 2 extra blades free
• Comes in a multi-tool blade case
#032FT3+1
• Fine toothing for extra precise and clean cuts
• Universal open-back fitting
• Pack of 3 blades + 1 extra blade free
• Comes in a multi-tool blade case
#032CTL3+1
• Extended length of 67mm for deeper cuts
• Heat treated cutting edge for long-life
• Universal open-back fitting
• Pack of 3 blades + 1 extra blade free
• Comes in a multi-tool blade case
#035HCT3+1
• Heat treated cutting edge for long-life
• Universal open-back fitting
• Pack of 3 blades + 1 extra blade free
• Comes in a multi-tool blade case
#044BMT10+2
• For wood, nails, and screws
• Titanium coated for enhanced cutting performance
• Universal open-back fitting
• Pack of 10 blades + 2 extra blades free
• Comes in a multi-tool blade case
#032BM10+2
• For wood, nails, and screws
• Universal open-back fitting
• Pack of 10 blades + 2 extra blades free
• Comes in a multi-tool blade case
Resistant to weather, pests, and rot, Biowood Composite Cladding ensures long-lasting façades Builders save on upkeep costs and provide clients with a responsible, cost-effective solution
Achieve the timeless, elegant appearance of real wood. Builders can offer a warm, inviting design without sacrificing modern aesthetics.
Request a Sample: sales@bbi.net.nz
Combining the timeless beauty of natural wood with a versatile, responsible, and durable timber cladding alternative.
Biowood cladding is an innovative building material that combines the natural beauty of natural wood with durability and the low maintenance benefits of composite materials. Ideal for both interior and exterior applications, Biowood cladding stands out as a versatile and responsible option for modern and contemporary architecture and design.
Biowood cladding is primarily composed of wood flour and uPVC (unplasticised polyvinyl chloride), resulting in a product that mimics the appearance of natural timber while providing enhanced performance characteristics. The PVC component contributes to its durability, moisture resistance, and protection against pests and decay. While the wood flour, sourced from recycled or sustainably managed forests, gives the cladding its authentic wooden look and feel.
The aesthetic flexibility of Biowood cladding is a significant draw for architects and designers. Available in a spectrum of colours, finishes, and textures, it allows for customisation to achieve any desired look. Whether the goal is a rustic, natural charm or a sleek, modern finish, Biowood cladding can be adapted to meet these specifications. It convincingly replicates the grain patterns and textures of natural wood, offering an authentic appearance without the maintenance drawbacks associated with natural timber.
Biowood cladding is not only Global Green Tag certified but also embodies sustainability. It aligns builders and designers with greener building practices and responsible construction initiatives. Made from recycled wood flour and uPVC, Biowood cladding reduces waste and environmental impact through full recyclability while minimising reliance on virgin materials. Its manufacturing processes emphasise energy efficiency, further enhancing its eco-friendly credentials.
Compared to traditional wood, Biowood cladding offers superior durability. It is resistant to common issues such as rot, warping, and splitting, which can affect natural timber when exposed to the elements. This makes it particularly suitable for exterior applications, where it must withstand varying weather conditions. Additionally, Biowood cladding is resistant to termites and other pests that typically damage wood, ensuring a longer lifespan and reduced maintenance costs.
Maintenance of Biowood cladding is minimal, unlike natural wood, which requires regular staining, sealing, and repairs. It remains in top condition with occasional cleaning using water and mild detergent. This low maintenance requirement translates to significant time and cost savings over the long term.
The versatility of Biowood cladding makes it suitable for a wide array of applications, ranging from residential to commercial and public buildings. It offers a cohesive aesthetic for both interior and exterior use, commonly applied in wall cladding, facades, ceilings, and decorative elements. Its weather-resistant properties are ideal for outdoor use, while its attractive appearance enhances indoor spaces.
Biowood cladding presents a forward-thinking choice, blending the timeless appeal of wood with modern performance benefits. Its durability, ease of maintenance, and environmental credentials make it a standout material for responsible construction.
This is part two of some of the most frequently asked health and safety questions that get submitted to SiteSafe's safety advisor via the Ask an Advisor online form.
Q: What are the procedures for worker injuries at work?
A: Administer medical treatment as required. This may be first aid for minor injuries or a medical professional for more serious harm.
You should record any health and safety incidents and complete an investigation.
More severe injuries will have to be notified to WorkSafe, and the scene of the injury/illness kept secure until released by WorkSafe.
Use the Incident Investigation and Reporting form provided by Site Safe to record incidents and investigations.
Q: Is there a legal obligation when working on a residential roof to have two workers on the same roof to ensure job safety?
A: There is no specific requirement for two people to be on the roof at the same time for H&S reasons.
Q: What are the recommendations around wearing Hi-Vis around moving plant and other vehicles?
A: It is recommended that everyone who is in the vicinity of moving plant and vehicles wears hi-vis.
It's a matter of managing the risks. If a worker can implement safety measures that mean only one worker is required on the roof, this should be completed. If these measures aren't reasonably practicable then a second worker on the roof may reduce risk.
Q: What are the laws around ear protection?
A: There are no laws regarding hearing protection; these are covered by standards and practice guidelines.
Good practice is that the ear protection must reduce the noise to an acceptable level – so they must be manufactured to an acceptable standard and meet the noise reduction requirements.
This should be included in your standard operating procedure (SOP) for loading/unloading operations; hi-vis should not be relied on solely to control risk associated with these activities.
Other elements that can be included in SOP:
▶ Designated (and marked out) loading/unloading areas
▶ Designated (and marked out) pedestrian pathways
▶ Barriers to prevent pedestrians straying into loading areas
▶ Signage warning of operating machinery
▶ Induction level training for all staff and contractors on SOP
▶ Training for drivers and forklift operators
If fitted with radios, then they should not be worn where the radio would interfere with critical communications (verbal communication; alarms; audio alerts etc.).
For more information on health and safety help and advice in the construction industry:
Ph: 0800 SITE SAFE (748 372) Email: theteam@sitesafe.org.nz Web: www.sitesafe.org.nz
E L CE ES BTA L S L T CHN L GY O O
Exclusively available on the BL4040F these next-generation cells are designed with cutting-edge technology. Tabless lithium-ion cells remove the bottleneck allowing for a much more efficient method of power delivery.
Tabless cells avoid current concentration by connecting the entire end of the electrode to the end of the cell instead of the tabs. This improves battery efficiency, thermal management and overall battery performance. Elevate your workday with the high-output 40V Max 4.0Ah battery – where power, durability, and innovation meet to redefine excellence in tool performance.
BENEFITS OF TABLESS CELLS
• Higher power output with less internal electrical resistance in BL4040F –Up to 35% more power compared to BL4040
• Reduced temperature under heavy load due to a lower electrical resistance in BL4040F – Up to 45% cooler running compared to BL4040
• Higher productivity of connected tool
Experience the difference in every task as these high-output batteries drive your tools to new heights,effortlessly handling heavy load applications. Designed for high demand applications these batteries supply a higher output power enabling XGT tools to continuously perform heavy duty applications.
applica
High Output battery, designed to produce up to 35% more power versus the standard 4.0Ah battery (BL4040)
With Tabless cell technology, BL4040F runs up to 45% cooler versus the standard 4.0Ah battery (BL4040)
Written by Ben Rickard, Construction Risk Expert, Builtin Insurance Brokers
This one happened in Australia, but they have very similar workplace safety laws; in fact, ours were modelled on theirs. So, what happens in Australia clearly indicates what could be coming here. In this case, the company was convicted and fined AUD20,000 for failing to provide and maintain a safe system of work. The director was also individually fined AUD20,000 for failing to take reasonable care as an officer of the company.
Essentially, the director was found to have verbally abused, intimidated and threatened a subcontractor over four years. The bullying came to a head during the 2020 Covid lockdown. The court found that the company and the director should have provided a safe system for identifying, reporting, investigating and stopping inappropriate workplace behaviour, including bullying.
A property developer was found guilty under the Resource Management Act of deliberately altering a protected tree. The offence was committed after a tornado in June 2021, and the judge noted that it was a reckless and opportunistic act. The developer was fined $96,000.
An individual was found guilty of breaching the RMA by failing to comply with an enforcement order issued by the Environment Court. This related to the dumping of tonnes of waste material that posed a serious and ongoing risk to the environment from asbestos exposure and lead and zinc leaching into groundwater. A fine of $20,000 was imposed, along with an order to complete 200 hours of community service.
Two related South Island companies were fined $270,000 and ordered to pay reparations of $130,000 following the death of a man after his vehicle was struck by a runaway trailer.
WorkSafe found that the companies did not have a system to ensure that vehicles were kept in good
working order or that drivers visually checked their vehicles before use. In addition, staff had inadequate training, instruction, supervision, and experience in safely using company vehicles and trailers.
This conviction follows another case from 2022 for inadequate management of trailer safety. In that case, a nine-year-old girl was killed when a trailer’s safety chain failed, disconnecting it from the truck towing it and sending it into the path of an oncoming vehicle. An investigation found the tow ball and coupling were severely worn down.
In this case, the contractor was convicted for unlawfully carrying out earthworks without best practice erosion and sediment control measures in place, in breach of the Resource Management Act. The judge found the company was “highly culpable” and had “deliberate disregard for the rules and the environment”.
A worker at a timber processing company sustained serious injuries when his hand struck the blade of a docking saw he was operating. The company was charged with failing to ensure effective guarding or controls for the safe operation of the saw. They agreed to an Enforceable Undertaking that involved a total spend of over $110,000. This included making financial amends to the victim, totalling $46,977 and donating $10,000 to the local fire brigade.
Statutory liability insurance ensures that if a contractor breaches legislation, such as the Resource Management Act, Building Act, Fair Trading Act or Health & Safety at Work Act, they won’t be financially burdened by the resulting costs, which can be significant. Additionally, if the contractor is prosecuted under that legislation, they won’t need to bear the significant legal defence costs.
From a WorkSafe perspective, contractors as PCBUs are responsible for health & safety on their worksite. Any accident could result in a WorkSafe investigation, prosecution and
potential reparations awarded to the injured person. While statutory liability insurance can’t legally insure health & safety fines, it will cover legal costs and reparations.
The cover is for unintentional breaches; if the offence committed is deliberate or with the knowledge that it would breach the law, it will likely be excluded from coverage.
Builtin is New Zealand’s Construction Risk Management Expert. For more information, visit builtininsurance.co.nz, email Ben Rickard at ben@builtin.co.nz, or call the team on 0800 BUILTIN.
ADOS Builders Glue Pack #4490 - 500ml, #4492 - 1L
• Bonds similar and dissimilar products.
• Suitable for over painting, drilling, tapping, sanding, planing, sawing.
• 100% water resistant, excellent chemical, abrasion and high impact resistance.
• Easy to use. 1:1 ratio, ensures correct mixing each time.
$50 EXCL GST 500ml
CRC Metal Armour #1754703- 350g, #1754729- 1L
• 85% Zinc-rich primer and sealer
• Bonds directly to bare metal or most surfaces, including painted surfaces.
• Ideal for interior and external applications and anything requiring painting post rust treatments.
ADOS Builders Fill #7074 - 1 Litre
• Repairs gaps, cracks, holes and dents
• Can be used on variety of surfaces
• Exceptional adhesion and stops sagging.
• Will not shrink like common air drying fillers
• Will not rot and is waterproof
$27
CRC Zinc It #2085- 350g
• Zinc-rich 95% highest purity zinc in the dried film, fuses directly to iron or steel surfaces
• Same advantages as hot-dip galvanising.
• Excellent adhesive qualities forms a tough coat for long-term protection
• High film build in one step.
• Ideal for use after rust treatment including CRC Rust Converter. $17
$20
GST 350g
• Corrosion Protection Factor 72 (up to 6 years outdoors, depending on conditions).
When completing and issuing records of work (RoWs), licensed building practitioners (LBPs) have certain obligations.
The Building Practitioners Board (the Board) continues to receive a high number of complaints about LBPs not issuing RoWs when they are required. Not providing a RoW is a poor reason to come before the Board, so please ensure your records are up to date.
You can read more information on how RoWs should be used in Know your stuff: For the record which was in Codewords 71 (March 2016: www.lbp.govt.nz/for-lbps/ codewords/know-your-stuff-for-therecord/ or scan the QR code.
Each LBP who carries out or supervises restricted building work (RBW) must, on completion of the RBW, provide a RoW to the homeowner and territorial authority (the local council). This requirement is set out in section 88 of the Building
Act. It is also a disciplinary matter for LBPs if a RoW is not provided when required – meaning that you could be disciplined by the Board.
A RoW is designed to be a documented record of who carried out or supervised RBW under a building consent.
It protects you by listing only what you did, removing future uncertainty when multiple contractors have performed or supervised RBW on one site. For this reason, the accuracy of the record is important as it will remain with the building records for the life of the building. It serves as an enduring and accurate record of RBW undertaken on-site.
If you were asked today what work you carried out on a project 12 years ago, would you be able to accurately describe that work?
When you have completed your portion of RBW onsite, you should:
▶ complete a RoW. If you do not have the RoW template, you may download it from www.lbp.govt.nz or scan the QR code.
▶ ensure the record is sufficiently detailed so it describes each aspect of the RBW you either carried out or supervised (your role could include a combination of supervision and doing work).
▶ provide a copy of the RoW to the homeowner and the local council.
You could face disciplinary action by the Board if you do not provide a RoW when one is required. You must not withhold a RoW for non-payment of work under a building contract or simply because you are in dispute with the client.
Failure to provide a RoW is a disciplinary matter for which the Board has zero tolerance.
For a more detailed overview of these requirements, refer to the Board’s decision regarding Complaint No. C2 01170 on the LBP website or scan the QR code.
Whether an LBP is a subcontractor or is employed, they are still accountable to the Board. The Board does not deal with payment or contractual disputes, but it does determine whether the LBP has met their obligations under the Building Act.
Not knowing the owner’s name is not a defence for failing to provide a RoW, as there are ways of finding such details. It is also important to remember who the RoW is for. While it might be a common practice to give it to the main contractor, it is a practice that carries the risk that it may not be passed on to those who require it - the owner and the local council.
A recent Board disciplinary decision found that the above are not good reasons for failure to provide a RoW. The respondent was fined $1000 and ordered to pay costs of $500, even though he had given the RoW to the main contractor, who then failed to pass it on.
1. What is the reason for a Record of Work?
a) To ensure the homeowner doesn’t do anything they’re not supposed to.
b) To record who carried out the restricted landscaping and electrical work on a particular job.
c) To record who carried out or supervised restricted building work on a job.
2. Why should you add full details to a record of work?
a) The law requires you write at least 150 words to complete it.
b) MBIE says you must.
c) It can protect you by listing only what you did, excluding other people’s work.
3. How long after you finish your work should you provide a copy to the homeowner and the local council?
a) On completion of the RBW.
b) By the time the code compliance certificate is applied for.
a) Less than one year.
This article is from Codewords Issue 119. Log in to the LBP portal lbp.govt.nz (or scan the QR code below) and update your Skills Maintenance activities.
When conflicts arise between parties involved in a building project, finding the right resolution is crucial. As licensed building practitioners (LBPs), you encounter disputes that require careful handling. This article covers some methods for resolving these issues.
Mediation and self-resolution: Mediation is a common approach in Aotearoa New Zealand. It involves bringing disputing parties together to discuss their concerns and find mutually acceptable solutions. As an LBP, consider suggesting mediation when faced with disagreements related to building work.
Consumer rights: If you're dealing with consumerrelated disputes, understanding consumer rights is essential. Encourage clients to understand and assert their rights and seek fair outcomes.
Formal complaints, arbitration, and adjudication: In more complex cases, formal complaints, arbitration, or adjudication may be necessary. These processes provide structured ways to address disagreements and reach decisions.
Disputes Tribunal and courts: When other methods fail, the Disputes Tribunal or courts become relevant. These legal avenues allow parties to present evidence and seek binding resolutions.
Determinations: A determination allows the Ministry of Business, Innovation and Employment (MBIE) to thoroughly review and consider the facts and make a legally binding decision. As an LBP, you can apply for a determination, and you can participate in someone else's determination if you were involved in the disputed project.
Remember, choosing the right approach depends on the specific circumstances. Prioritise effective communication and collaboration to achieve satisfactory outcomes in building-related disputes.
Using determinations wisely: when to apply and when not to
Understanding when to use a determination is essential. Here are some key points to consider:
Disagreements with authorities: You can apply for a determination if you disagree with a decision made by a building consent authority or territorial authority under the Building Act or Building Code. For instance, if you receive a notice to fix or if the authority refuses to issue a building consent, code compliance certificate, or certificate of acceptance, a determination may be appropriate.
Not a mediation service: While determinations are increasingly sought after due to communication breakdowns, they are not a mediation service. Parties unable to communicate professionally should seek other avenues for resolution.
Resource Management Act: Determinations cannot address matters related to the Resource Management Act (except under Section 224(f), which pertains to specific subdivisions).
Contractual disputes, damages, and liability: Determinations do not cover contractual disputes or attribute liability or award damages.
Council decisions: Determinations are not intended as an alternative pathway for decisions made by councils. However, a determination can confirm, reverse, or modify decisions made by council.
Workmanship Disputes: Determinations are not suitable for disputes related to workmanship. Workmanship disputes may be resolvable under the Construction Contracts Act 2002.
Complex or technical matters: Determinations commonly deal with complex or technical issues. The information given by parties to the dispute is assessed, and the relevant regulations are applied to the facts. The outcome is a legally binding decision. For example, a determination might uphold, reverse, or modify a council's decision, such as refusing to issue a building consent or determining whether building work is compliant.
Remember, choosing the right approach depends on the specifics of each situation. As professionals, you play a crucial role in ensuring fair and effective dispute resolution in the construction industry.
Navigating disputes: determinations and effective resolution
Understanding the proper steps in dispute resolution is crucial. Here's what you need to know:
Prioritise practical solutions: Before seeking a formal determination, consider practical approaches to address routine complications and standard issues. Initiate with direct problem-solving methods and consult authoritative resources and precedents that offer guidance on comparable matters.
Check the facts: Gather accurate information.
Effective communication: Engage in clear, respectful communication with everyone involved.
Written agreements: Document any agreements in writing.
Mediation: When communication breaks down, consider mediation. An independent third party will assess the situation and help people reach an agreement. It's a constructive way to find common ground.
Code of ethics: As an LBP, adhere to your professional code of ethics. Act in good faith during dispute resolution, maintaining professionalism throughout the process.
Remember, choosing the right path depends on the specifics of each situation. Prioritise effective communication and ethical behaviour to achieve fair outcomes in building-related disputes.
"A determination can be useful if you disagree with a council’s
decision under the Building Act
or
Building Code,
but it isn’t the best option for everyone. There are other ways to try to solve your dispute."
A previous determination addressed an authority's decision to grant a minor variation for the substitution of external wall cladding. The matter to be determined was whether the change in cladding required a formal amendment to the building consent and a new or amended certificate of design work.
The LBP who designed the plans argued for the necessity of accurate building consent documentation to reflect the actual construction, including any changes to the cladding system. They believed the authority significantly deviated from the approved consent, requiring revised plans and an amended certificate of design work.
The LBP responsible for the building work viewed the substituted cladding systems as nearly identical, suggesting minor differences did not warrant a formal amendment.
The authority processed the cladding change as a minor variation without a formal amendment application, asserting that the designer's certificate of design work remained applicable for the original consent. The authority maintained that minor variations could be documented and added to the building file, transferring responsibility for compliance of restricted building work to the authority post-consent.
The determination concluded that the application for a minor variation did not meet the requirements of sections 45 and 45A of the Building Act 2004, as it lacked a new or amended certificate of design work from an LBP with the appropriate design license. Consequently, the authority's decision to grant the minor variation was reversed.
If you are considering a determination, it is worth looking through previous determinations about similar disputes. Finding a previous determination that has considered a similar issue may help you resolve your differences without having to go through the whole process. However, it is important to note that determinations aren't bound by decisions made in previous determinations, and two similar cases can have different outcomes as MBIE considers the unique circumstances of each case.
Previous determinations can also be a helpful resource when LBPs are unsure about a specific area of the Building Code or Building Act.
For more information on determinations, visit: www.building.govt.nz/determinations
To search for previous determinations for free downloads of determinations go to the Building Code Hub: www. codehub.building.govt.nz
1. What is a determination?
a) A decision in respect of consumerrelated disputes
b) It allows MBIE to thoroughly review and consider the facts and make a legally binding decision
c) Something carried out by a Disputes Tribunal
d) It brings the disputing parties together to discuss their concerns and find mutually acceptable solutions
2. When can determinations be used?
a) For Resource Management Act matters
b) To decide on contractual disputes, damages, and liability claims
c) For disagreements with building consent authorities or territorial authorities
d) For workmanship disputes
3. Can a determination reverse a council's decision?
a) No
b) Yes
This article is from Codewords Issue 119. Log in to the LBP portal lbp.govt.nz (or scan the QR code below) and update your Skills Maintenance activities.
Made in New Zealand For New Zealand. Plasterboard, locally made for over 95 years.
At Winstone Wallboards we are passionate about providing quality GIB® systems and technical support that make it easier for Kiwis to create exceptional interior living environments for generations to come.
LEARN MORE gib.co.nz
String Line 80m
#CM80FL
• Braided nylon for strength
• High stretch
• UV stabilised
$14
Steel Carpenter Square
#TWCS13
• 400mm x 600mm
• Black anodized quality steel body
$15
Snap Off Blades
#OLHB20
• 25mm
• 20-pack
End Cutting Pliers 205mm
#CH358
• High leverage cutting pliers with Xtreme Leverage Technology (XLT™) to make cutting easier
• Laser heat-treated cutting edges perform better and last longer
• Forged high carbon U.S. steel
Hand Saw 550mm
#GM328H22-ITM
• 7 point, 8 tooth, hardpoint
• For rough and heavy-duty cross-cutting
T-Square 1220mm
#TW1220HD
• Heavy-duty aluminum frame
• Easy read bold 2mm graduations
• Perfect length for drywall applications
$59
Utility Knife 25mm
#OLXHAL
• Snap off blade
• Auto-lock
• ComfortGrip, anti-slip grip
• Diamond ground hardpoint teeth for longer life and a fast cut $19
Staple Gun
#AP850B
• Heavy duty metal
• Power adjustment control system
• Nickel-plated finish for rust and corrosion resistance.
• 17 piece TCT kit
PermaPine, a leading supplier of treated timber in New Zealand, has expanded its offerings to include Micronised Copper Azole (MCA) treatment. Unlike traditional CCA (Chromated Copper Arsenate), MCA provides environmental advantages and better end-of-life options.
As New Zealand's leading supplier of CCA-treated posts, poles, and piles, PermaPine has long been committed to providing quality outdoor products for the New Zealand and Pacific Island markets.
PermaPine has recently commissioned a second treatment plant, which provides additional capacity and extends the capacity to "fixate" the timber preservative into treated product following treatment. Customers and end users benefit by receiving drier products.
Along with CCA treatment, PermaPine can now offer an alternative timber preservative called MCA. Micronised Copper Azole treatment will be offered to the market for products such as garden sleepers, roundwood, and landscaping products. Initially, these offerings will be "made to order" rather than purchased from stock; therefore, they will have slightly longer lead times.
MCA is a wood preservative with two active ingredients: Micronised Copper and Azole. Micronised copper is simply copper carbonate ground down to a fine size. The copper used is almost always from recycled copper metal. Copper is a common fungicide. Azoles are a family of synthetic fungicides originally developed for the human health and crop protection market. The azole used in MCA is also a finely ground particle.
The first commercial use of MCA was in the USA around 2007. MCA was accepted into the NZ Wood Treatment Standard (NZS3640) in 2012. MCA is commonly used to treat pine species in the US, and
is also used in Australia. MCA provides protection for H3, H4 and H5 applications, but until now, has been most commonly used for H3 applications such as decking, fencing, and pergolas.
MCA has some advantages compared to CCA.
▶ MCA has various environmental certifications, including being certified by Global Green tag, and National Green Building standard.
▶ Better end-of-life options, with some commercial boilers in NZ presently burning MCA-treated wood. For CCA, the disposal options through burning are limited to one commercial boiler.
▶ The ability to burn MCA-treated wood at the end of its life under specific conditions.
▶ PermaPine MCA treated product is backed by a 50-year warranty against insect and fungal attack when used and installed according to industry guidelines.
▶ CCA remains well-recognised and established as a preservative.
▶ Its long history of use globally and widespread availability make it a reliable choice
▶ CCA tends to be a more cost-effective preservative compared to MCA.
Slow grown hardwood is very stable, durable and resilient. Does this also apply to a quality Brand? The knowledge, skills and wisdom that come from decades of hard work, facing new challenges, and learning new ways of doing things, is irreplaceable. You can’t beat that kind of experience. SPAX has been a leader in innovative screw technology for the past 200 years. We started in 1823, the same year the modern nation of New Zealand took its first steps …
1823 Altenloh, Brinck & Co is founded as one of the world’s first companies to produce screws on an industrial scale.
1830 With the first exports, ABC becomes a household name in many sectors.
1840 ABC extends range to produce 400 different types of screws.
1857 Installation of the first steam engine so ABC no longer relies on waterpower.
1898 Further development of an automatic thread milling machine. The improved ABC screw point becomes a household name.
1907 ABC begins producing wood construction screws.
1967 ABC revolutionises timber construction with the SPAX universal screw. A huge global success, it becomes the modern universal screw for builders and craftspeople all over the world.
2013 SPAX Pacific becomes a subsidiary of the ABC Group
1823 The first missionaries settle in the Bay of Islands.
1830 New Zealand’s first town, Kororareka (now Russell) in the Bay of Islands is established.
1840 The Treaty of Waitangi is signed.
1857 New Zealand is at war with Maori resistance to British colonial rule.
1898 The first motor cars arrive in New Zealand when William MacLean imports two Benz vehicles.
1907 The modern nation of New Zealand becomes a dominion of the British Empire.
1967 Pounds, shillings and pence become dollars and cents as New Zealand switches to decimal currency.
2013 Initial Cross Laminated Timber production in New Zealand, with the first mass timber projects beginning.
Today, SPAX is still at the forefront of developing new technologies and new products that improve our buildings, building standards and sustainability. Progress doesn’t just happen - it takes courage and leadership to achieve it. Over the past 11 years, SPAX Pacific and the New Zealand building industry have achieved major milestones together. These include the adoption of Mass Timber construction, better engineering, and stronger, more sustainable building methods.
New Zealand is rapidly developing into a world leader in this field. Working closely together with ITM, our industry partner, we look forward to a bright future for the New Zealand building industry.
After all SPAX and ITM are both very stable, durable and resilient, just like slow grown hardwood!
Change is afoot for one of ITM's franchise owners in Taranaki, who has recently expanded their stores from one to three, including a sawmill, post mill, and a frame & truss plant.
Campbell and Hannah Mattson have owned Waitara ITM since 2006 and recently rebranded to North Taranaki ITM after launching two new locations in Waiwhakaiho and Inglewood to complement their Waitara offer.
The couple purchased the sites from Value Building Supplies and will be looking to offer an enhanced retail experience. They will use their newly acquired frame and truss plant, sawmill, and post mill operations to benefit their rural and trade customers throughout Taranaki and beyond.
Campbell says they had been actively looking to expand their offering for a while. He's excited to finally see it up and running, particularly the frame and truss plant, one of only three high-quality plants in Taranaki.
"We got to the point where we wanted to offer a lot more for our customers, the wider building industry, and the local community we are a part of here in Taranaki.
"The Covid period showed us that our supply chain is vulnerable to shocks. Milling our own high-quality, locally-grown timber to order, including niche sizes and lengths, and increasing stockholdings as the market changes gives our construction and farming clients much more security.
"Having the sawmill also allows us to work with our customers to create exactly what they need when it comes to specialty sizes that might be slightly outside the mainstream products available elsewhere."
The company's milled timber is seasoned and treated gently, as opposed to through high-impact treatments, meaning its cellular structure remains strong, stable, and of the highest quality.
It is a product they can offer at competitive prices for wholesale and retail customers, with its mill feedstock coming from a range of pine forests in Taranaki - many no more than 20-50km from the mill.
Sustainability is a key focus for the company, with processes in place to ensure the majority of its milled timber has an end purpose relative to its structure and quality.
Its Inglewood yard has a wide range of high-quality battens, posts, rails, and H3.2-H5 landscaping and structural timber products available for purchase regularly, with the operation milling approximately 25,000 logs per year. It's also set up to execute a range of specialist mouldings and profiles for various applications such as decking, cladding and timber screens.
At its Waiwhakaiho location, the team is building custom-made furniture from its locally sourced pine products, including chicken hutches, hot houses, gazebos, picnic tables and more.
In addition to ITM's pole shed offer, the North Taranaki team can supply high-quality custom kit-set and full-build pole sheds, with clear span options available. These sheds use a hybrid of rollform steel rafters and timber pole wall structures.
"These sheds are incredibly popular and are a vital product we have been providing farmers with throughout Taranaki and further afield.
The new business opportunity is driven by a shared passion that Campbell and Hannah have for igniting growth, impact, and improvement within the community. It fulfils a desire for them to contribute more widely to Taranaki and the future of its built environment.
Hannah says a key focus is to provide a service that removes much of the stress that often comes with building.
"We want to make building a positive, overall experience for everyone involved, from builders and farmers to homeowners."
Hannah, an interior designer, comes from a family that has built and continues to run a successful steel manufacturing business. She's seen first-hand how local businesses can positively impact the community. She hopes to do the same through North Taranaki ITM.
"This region has supported us a lot over the years, and we enjoy being immersed in how it is evolving and will continue to develop.
"We're focused on solving our customers' problems and removing as many barriers as possible to help people achieve what they need to achieve."
With one team of 70 across three locations, North Taranaki ITM has become Taranaki's largest and most diverse supplier of all things building. Campbell says he's incredibly grateful for the market power that being part of ITM brings and looks forward to passing that on to his customers.
"We plan to continue building on the strengths we have as a business, and combined with what the ITM brand has behind it, we know we have a great offer that has the potential to benefit a lot of people."
☐ Bay of Islands ITM Kaikohe 09 407 7600
☐ Bay of Islands ITM Paihia 09 402 7703
☐ Bay of Islands ITM Waipapa 09 407 8002
☐ Dargaville ITM 09 439 8730
☐ Far North ITM Kaitaia 09 408 3927
☐ Far North ITM Mangonui 09 406 0048
☐ Mangawhai ITM 09 431 4963
☐ Waipu ITM 09 432 0203
☐ Whangarei ITM 09 437 9420
☐ Albany ITM 09 415 6889
☐ Barrier ITM Tryphena 09 429 0466
☐ Dayle ITM Avondale 09 828 9791
☐ Dayle ITM East Tamaki 09 274 4942
☐ Dysart ITM Glen Innes 09 521 3609
☐ Hillside ITM Glenfield 09 443 8101
☐ MacClure's ITM Henderson 09 836 0088
☐ Mahia ITM Takanini 09 267 0234
☐ Matakana ITM 09 422 7525
☐ Thomsons ITM Papakura 09 294 9410
☐ Tuakau ITM 09 236 8226
☐ Waiuku ITM 09 235 7289
☐ Warkworth ITM 09 425 1021
☐ Weck’s ITM Patumahoe 09 236 3684
☐ Weck’s ITM Pukekohe 09 238 3678
☐ Western ITM Kumeu 09 412 8148
☐ Western ITM Swanson 09 832 0209
☐ Western ITM Whenuapai 09 416 8164
☐ Crighton ITM Greytown 06 304 7193
☐ Crighton ITM Seaview 04 568 3896
☐ Toa ITM Heretaunga 04 527 6800
☐ Toa ITM Porirua 04 232 5999
☐ Acorn ITM Hamilton 07 856 6789
☐ Cambridge ITM 07 827 0953
☐ Coromandel ITM 07 866 8848
☐ Dayle ITM Kopu 07 868 9829
☐ KKBS ITM Katikati 07 549 0689
☐ Matamata Post & Rails ITM 07 888 8189
☐ Mount ITM Mt Maunganui 07 575 3126
☐ Omokoroa ITM 07 552 5770
☐ Opotiki ITM 07 315 5984
☐ Otorohanga ITM 07 873 4841
☐ Pauanui ITM 07 864 8579
☐ Rotorua ITM 07 347 9423
☐ Taupo ITM 07 378 9899
☐ Tauranga ITM 07 541 1232
☐ Te Puke ITM 07 573 9993
☐ Thomsons ITM Hamilton 07 849 3674
☐ Thomsons ITM Whatawhata 07 829 8518
☐ Timmo’s ITM Te Awamutu 07 871 7545
☐ Tokoroa ITM 07 886 6611
☐ Turangi ITM 07 386 5736
☐ Whakatane ITM 07 307 0031
☐ Central ITM Carterton 06 929 7598
☐ Central ITM Feilding 06 323 3400
☐ Central ITM Marton 06 327 5458
☐ Crighton ITM Levin 06 368 4057
☐ Hometown ITM Foxton 06 363 8049
☐ Manawatu ITM 06 356 9490
☐ New Plymouth ITM 06 758 8939
☐ North Taranaki ITM Inglewood 06 756 7535
☐ North Taranaki ITM Waitara 06 754 8822
☐ North Taranaki ITM Waiwhakaiho 06 759 7435
☐ Stratford ITM 06 765 7800
☐ Blenheim ITM 03 578 3049
☐ Havelock ITM 03 574 1018
☐ Motueka ITM 03 528 7254
☐ Nelson ITM 03 548 5487
☐ Picton ITM 03 573 6888
☐ Takaka ITM 03 525 0005
☐ Ashburton ITM 03 307 0412
☐ Basher’s ITM Amberley 03 314 8311
☐ Darfield ITM 03 318 7474
☐ Dyers Road ITM Bromley 03 373 6049
☐ Geraldine ITM 03 693 9397
☐ Greymouth ITM 03 768 0441
☐ Hamptons ITM Waltham 03 374 3333
☐ Hillside ITM Hornby 03 349 9739
☐ Kaiapoi ITM 03 327 8829
☐ Kaikoura ITM 03 319 5447
☐ McMullan ITM Hokitika 03 755 8519
☐ McVicar ITM Harewood 0800 191 674
☐ ProBuild ITM Rolleston 0800 445 520
☐ Rangiora ITM 03 313 4862
☐ Timaru ITM 03 688 8074
☐ Waimate ITM 03 689 7427
☐ Dunedin
☐ Southbuild ITM Winton 03 236 6055
Thursday, 5th September
Addington Raceway 8am - 3:30pm
Wednesday, 18th September
Claudelands Events Centre
8am - 3:30pm
PALMERSTON NORTH
Friday, 11th October
Awapuni Racing Centre
8am - 3:30pm
AUCKLAND
Wednesday, 16th October
North Harbour Stadium
8am - 3:30pm