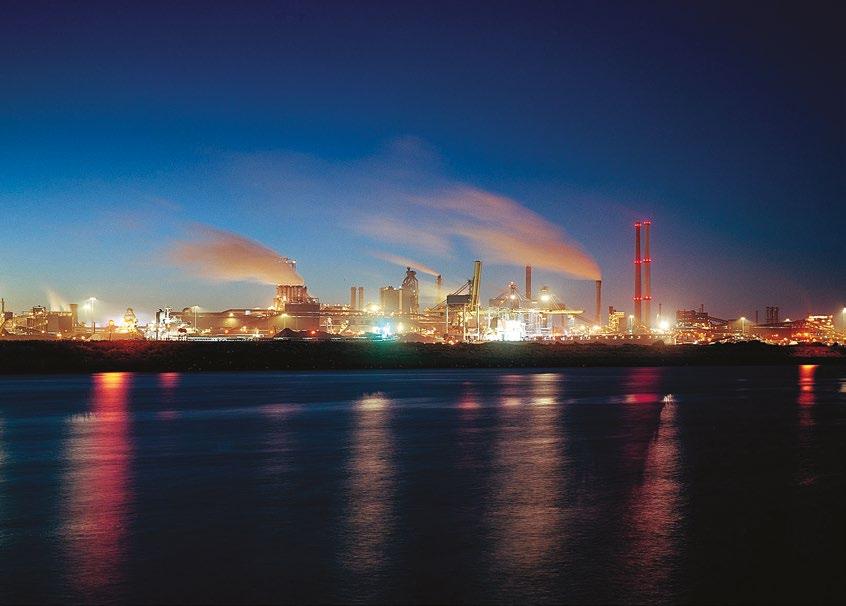
6 minute read
Iv-Industrie takes substantial steps towards a cleaner TATA Steel
There is much to do for the Netherlands’ most important steel producer. TATA Steel in IJmuiden aims to produce steel responsibly and thus make a positive impact on the immediate environment. Roadmap Plus is an accelerated route to achieving this goal, and Iv-Industrie is delivering a vital contribution to this process. The Pellet Factory, also called PEFA, will be equipped with a dedusting installation (part of the DeNOx and dedusting installation) and will reduce lead emissions by approximately 70 percent by 2023. As a result, emissions of heavy metals will also be reduced by more than 55 percent and of particulates by roughly 35 percent.
TATA Steel, therefore, faces a significant and necessary sustainability challenge. Not only in terms of CO₂ emissions and other substances but also the environment and nuisance to the (immediate) surroundings. Introducing a dedusting installation is a significant step towards cleaner production and limiting nuisance for local residents and the environment. In addition, it will also positively affect flora and fauna in the area. Rick de Jong is the Programme Director on behalf of Iv-Industrie & Consult. Rick is responsible for finding a solution with, among others, Project Manager Don de Jong and Paul van der Werf (Senior Lead Engineer - Piping & Mechanical). In the PEFA, iron ore is pre-processed into round balls (pellets), which are then introduced into the production process in the Blast Furnace. The pellets form an important raw material for the production of pig iron.
We want to play a greater role for TATA in the future.
In addition to carbon dioxide (CO₂), the entire production process also releases a considerable amount of nitrogen (N2). Therefore, nitrogen emissions (NOx) must also be significantly reduced. The solution: a cleaning installation connected to the PEFA. “It’s a kind of dust & gas scrubber”, explains Rick de Jong. “In the preliminary phase, we examined workable solutions. This is one of them. There needs to be a ‘system’ in the middle that removes the pollution. This can be achieved in various ways. This new cleaning installation is a filter and a washing installation in one. A washer, also known as a scrubber, is like a water shower.”
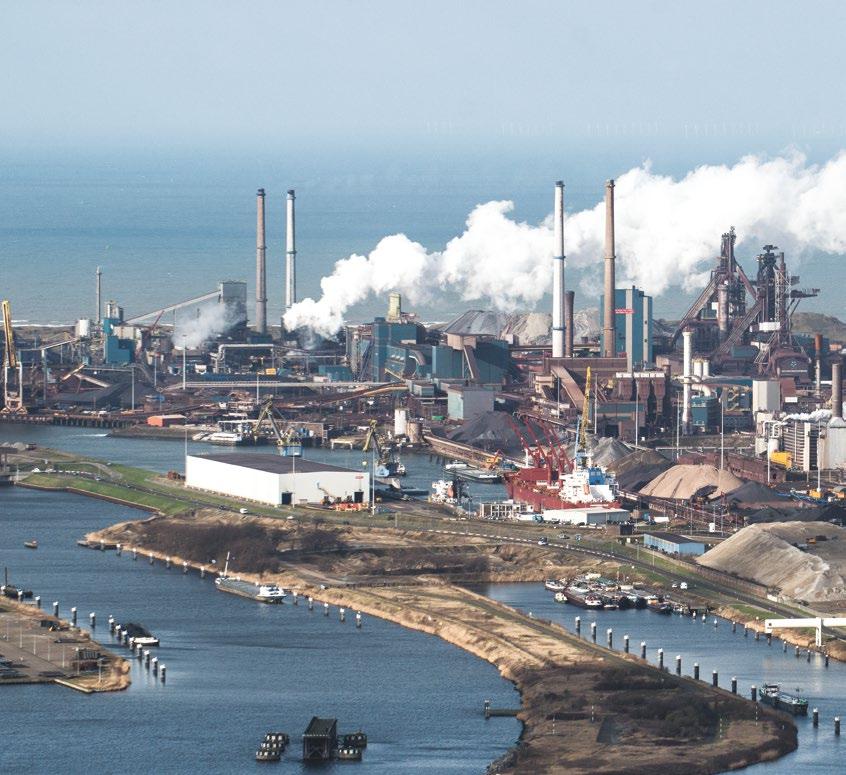
Roadmap Plus:
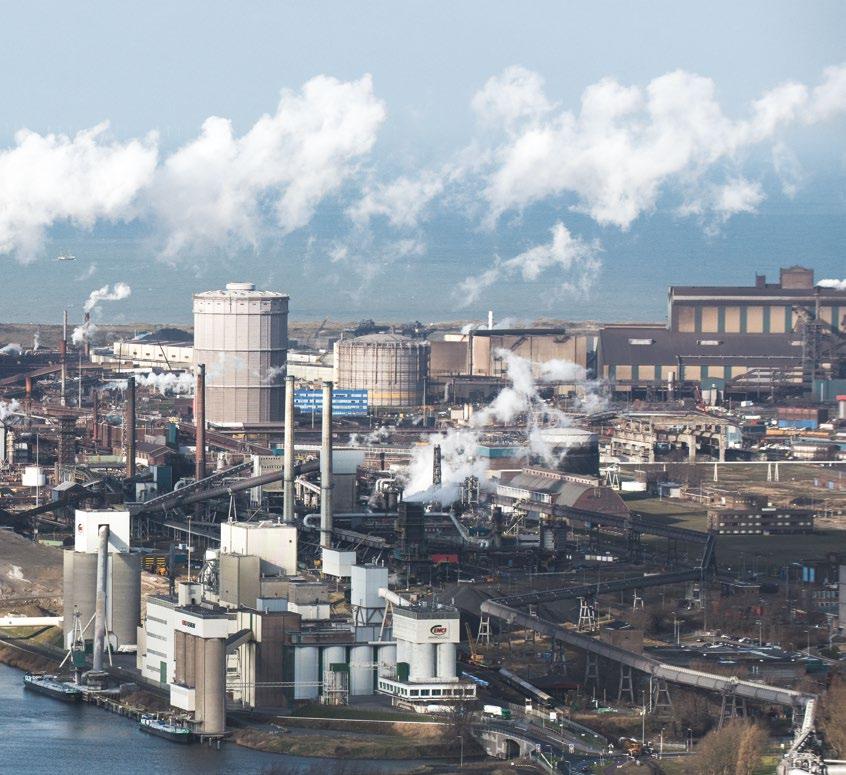
The Roadmap Plus was launched in 2019 to accelerate the realisation of Tata Steel’s (climate) goals and is the company’s roadmap to reduce emissions and nuisance for local residents. The introduction of the dedusting installation and the DeNO x installation forms part of this roadmap. The aim is to complete all projects within the Roadmap Plus by 2023, not in 2030. Only the DeNOx installation will be operational in 2025. In addition to sustainability projects around the Pellet Factory, greening and nuisance-limiting measures are also taking place at the Blast Furnace, the coke plant, the cold rolling mill, the steel factory, and the scrap yard and the sinter plant. Many of the dozens of projects within the roadmap are already underway. The Roadmap Plus is expected to be fully completed in 2025.
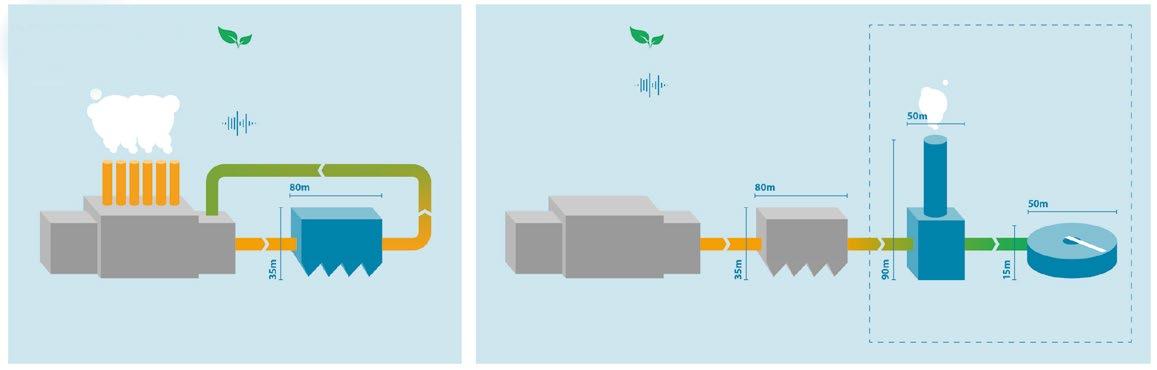
The ‘cleaning installation’, a so-called DeNOx installation, delivers a considerable impact. Until now, substances such as sulphur, metals and lead were directly expelled via the chimney, causing elevated pollution levels. A filter and a scrubber will now be placed between the chimney and the PEFA to capture much of these emissions.
It works as follows: the first step is installing the dedusting installation, for which Iv provided the engineering and design, including the preparatory studies. This installation is connected directly to the PEFA and must do exactly what the name suggests: dust removal, thus reducing emissions of heavy metals, dust and lead. The flue gases are transported to the dedusting installation via a special pipe. The dedusting installation will be operational in 2023, and TATA expects the emissions of all these substances to be reduced by no less than 80 percent.
How can we make them last another five years?
The size of the installation is impressive, both inside and out. It is 80 metres long and 35 metres tall and contains no fewer than 6,000 filter bags that filter all substances. The pipeline from the PEFA to the dedusting installation is 140 metres long with a diameter of 6 metres: comparable to a tunnel tube of the North-South metro line in Amsterdam.
This is followed by the DeNOx installation, which should reduce nitrogen dioxide emissions by the same amount and is linked to the dedusting installation. Here the flue gases are washed from the PEFA by the aforementioned ‘water shower’. The water from the DeNO x installation is then forwarded to a water treatment system. The interventions surrounding the PEFA are an essential part of TATA’s Roadmap Plus. If all goes according to plan, the DeNO x installation will be ready by the end of 2024 or early 2025.
In the context of Roadmap Plus, this project has certainly inspired us to do more of this work. The basic and detailed engineering of the dedusting and DeNOx installation provides an excellent basis to help TATA achieve more in the field of sustainability and responsible production, says Rick de Jong. “In the future, we want to play a greater role in this for TATA. Also, in other project phases. For example, Front End Engineering Design (FEED) and feasibility studies. That would be the crowning glory of our collaboration with TATA.”
2023
Expected results:
-80% lead emissions
-80% heavy metal emissions -80% dust emissions
No increase in noise
Pellet factory Processes ore for the production of liquid pig iron Dedusting installation Cleans ue gases of heavy metal compounds and dust
2025
Work has already begun on that front. Iv is working on a study for the company’s future hydrogen plant. This plant is needed for, among other things, the production of ‘green steel’ in the new DRI Installation: Direct Reduced Iron. In short: the necessary and greener way of producing steel. A big step for TATA, the Netherlands, and European iron production.
“We are mainly involved with the entire logistical part of the project”, explains Rick. “A location has already been designated for the new DRI but is not currently available. For this, a crucial main road needs to be diverted, and several kilometres of new rail tracks will have to be constructed and diverted. Furthermore, there are also existing installations approaching their end-of-life phase. These will be rebuilt elsewhere in the preparatory phase. The repair phase costs a lot of time and would mean factories would be shut down for months, which is not feasible. So how can we make them last another five years? These studies will help us to provide answers to all these questions.”
In the coming years, Iv aims to play a key role in the enormous sustainability challenge that awaits TATA. Both in terms of studies and engineering. Rick: “We do many projects here, both large and small. All are important. TATA wants to innovate and become greener, and we’re helping them achieve that. This challenge for TATA is huge. I’m not somebody who easily sees a problem in something. I mostly see opportunities. If you know how to fix mistakes, you’ll get there. For us, the most important thing is staying sharp and continuing to make choices that enable others to continue.” •
Expected results:
-80% nitrogen oxides emissions
No increase in noise DeNO x - installation
Pellet factory Processes ore for the production of liquid pig iron Dedusting installation Cleans ue gases of heavy metal compounds and dust Gas scrubber Cleans the ue gases of salts and nitrogen oxides Water treatment Cleans the washing water
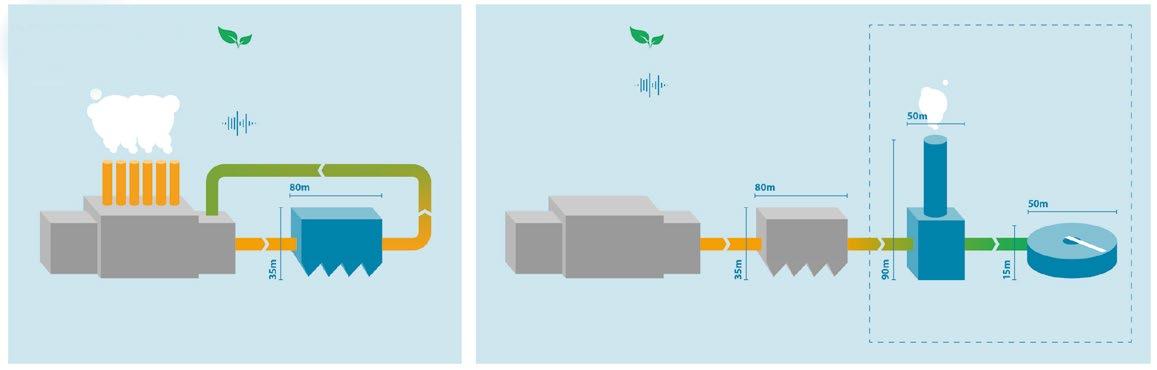