
5 minute read
Escher heading towards the ‘finale’ in China: mechanical completion of Crystallisers in sight
Escher Process Modules, a subsidiary of Iv-Groep, is making its final sprint toward the finish line in China. In Lianyungang, to be precise. At Shenghong Refining & Chemical Corporation’s new gigantic petrochemical complex, 24 Crystallisers will be put into operation over a few months. These Crystallisers were designed, tested and produced from A to Z by Escher. The finish line of this prestigious project is now in sight.
The Crystallisers were developed to crystallise paraxylene. The chemical, a colourless liquid, is a raw material needed to producte PET bottles (which is easily recyclable and therefore more sustainable) and clothing, among other things. As a result, China will become less dependent on imports: a must in one of the fastestgrowing economies in the world.
You can compare it to a slush puppy machine, except you shouldn’t drink this.
It was no surprise that Shenghong ended up at Escher a few years ago, given that only a few companies globally have the specific knowledge and competence to make such Crystallisers. The tanks used for this purpose must comply with complex and strict manufacturing requirements. More so than with other process vessels. The extensive knowledge and experience that Escher has accumulated over the decades are in full bloom in China. INEOS (formerly BP) in Geel, Belgium, has had five of these Crystallisers for almost a quarter of a century. And these are still working effortlessly for the time being.
How does a Crystalliser work? Each tank is filled with a 250,000-litre mixture of xylenes (ortho-xylene, metaxylene and para-xylene). By way of a double wall through which coolant flows, the xylene mixture is cooled over almost the entire length of the tank. The cooling of the tank’s contents enables crystals to form on the inner wall, and due to the high crystallisation temperature, the crystals formed mainly comprise para-xylene. The crystals are then scraped from the inner wall by a revolving scraper and discharged from the Crystalliser via the underside.
The liquid is continuously added from above to ensure the tank’s contents remain consistent. Finally, the crystallised para-xylene is separated from the rest of the liquid in three steps until all that remains is pure paraxylene. This is a continuous process. “You can compare it to a slush puppy machine”, says Project Manager Marcel Veenendaal. “Except you shouldn’t drink this.”
The gigantic petrochemical complex will commence production fully within a few months. The 24 process vessels made by Escher form an essential part of the facility. “The tanks are situated in the main flow of the complex. So, if the Crystallisers fail to work, the whole plant will come to a standstill,” explains Marcel. “Physically, it’s a small part of the petrochemical plant, but it forms an essential link.”
In short: a project comprising much responsibility and complexity. It is with good reason that so many checkpoints have been incorporated. For example, the socalled ‘cold commissioning’, running the tanks with water to see if the system works, is now scheduled, preceded by the ‘mechanical completion’. In other words: the completion of the system’s installation. This is another milestone that brings us closer to the finish line. Operations Manager Rob Emmen: “The client has asked us to be present there for this. Even though the entire engineering process has been completed, including the production and installation of the process vessels, it’ll still be a special moment.”
This is familiar work for Escher Process Modules. Still, now that the final sprint is underway, Rob agrees that the forthcoming completion is creating some healthy tension. “If these phases go well, we will move on to the so-called ‘hot commissioning’. This entails filling the tanks with process liquids for the first time. It’s a thrill to be there to witness this. Only after a few minutes will it be known whether the Crystalliser is working properly; roughly an hour later, we can measure the quality of the product via samples. The moment you see that it works always gives a special feeling.” A Mechanical Engineer and an E&I Engineer (Electrical & Instrumentation) from Escher will go to China to be present for the test phases. The large plant is expected to start production next year, with which the project will be largely finished for Escher. However, this project is a milestone in itself as it is by far the largest project the company has taken on, even Iv-wide.
Next year! That sounds soon, and it is. Rob could see, from his experience, that the pace in China was finally gaining momentum. “In China, they are particularly good at building fast. With our experience and background, we find it vital to guarantee the quality, so we need to be there for this last phase.”
Escher’s deep-rooted knowledge has, therefore, played a crucial role in this project. Over the years, the company has built up a considerable track record which proved very useful for this assignment. The five Crystalliser tanks in Geel are the most concrete example; however, knowledge has increased considerably in recent years.
“The Crystalliser tanks for INEOS in Geel is an excellent reference. Since these, we have improved our product and optimised the process,” explains Marcel. But lessons have indeed been learned along the way.
The biggest challenge was putting everything that seemed to fit together perfectly and seamlessly on paper into practice. Rob: “You have to imagine: the tank itself and the rotating scrapers were manufactured at different locations,
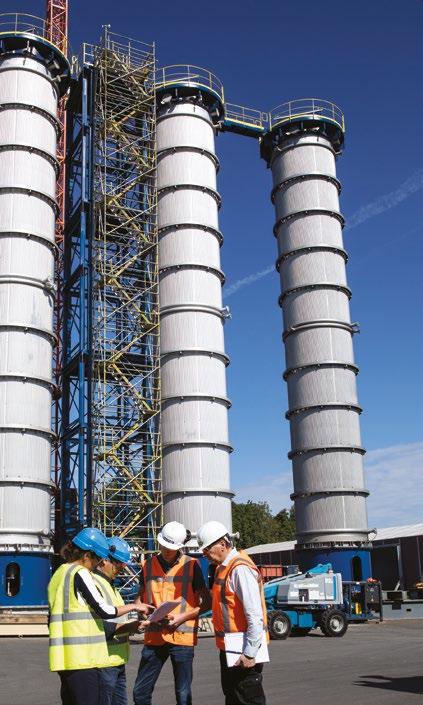
which means temperature differences must also be taken into account. Five degrees can make a substantial difference with, for example, the length because of shrinking or expansion. So these are the aspects that need to be kept in mind.”
But such cases also occur in the welding process. When welding the jacket, the exterior wall of the process vessel, heat is released, through which minimal deformations can occur. These deformations should be limited as much as possible. Of course, this was considered in the design process, says Marcel. “You can’t be ahead of everything or tackle everything in the preliminary phases. But fortunately, we do have highly skilled people here who can prevent this as much as possible.”
According to both gents, the Shenghong project is one of Escher’s most prestigious projects. “The ‘proof of the pudding’ will be the concluding phase in China. Fortunately, we already tested six units during manufacture, which went well without any problems, so we are confident that all will go well.”
Rob hopes that this project will put Escher back on the map. “We have realised a gigantic project with a relatively small team. That is very impressive. And at the same time, it creates expectations. So that’s nice, bring it on.” •