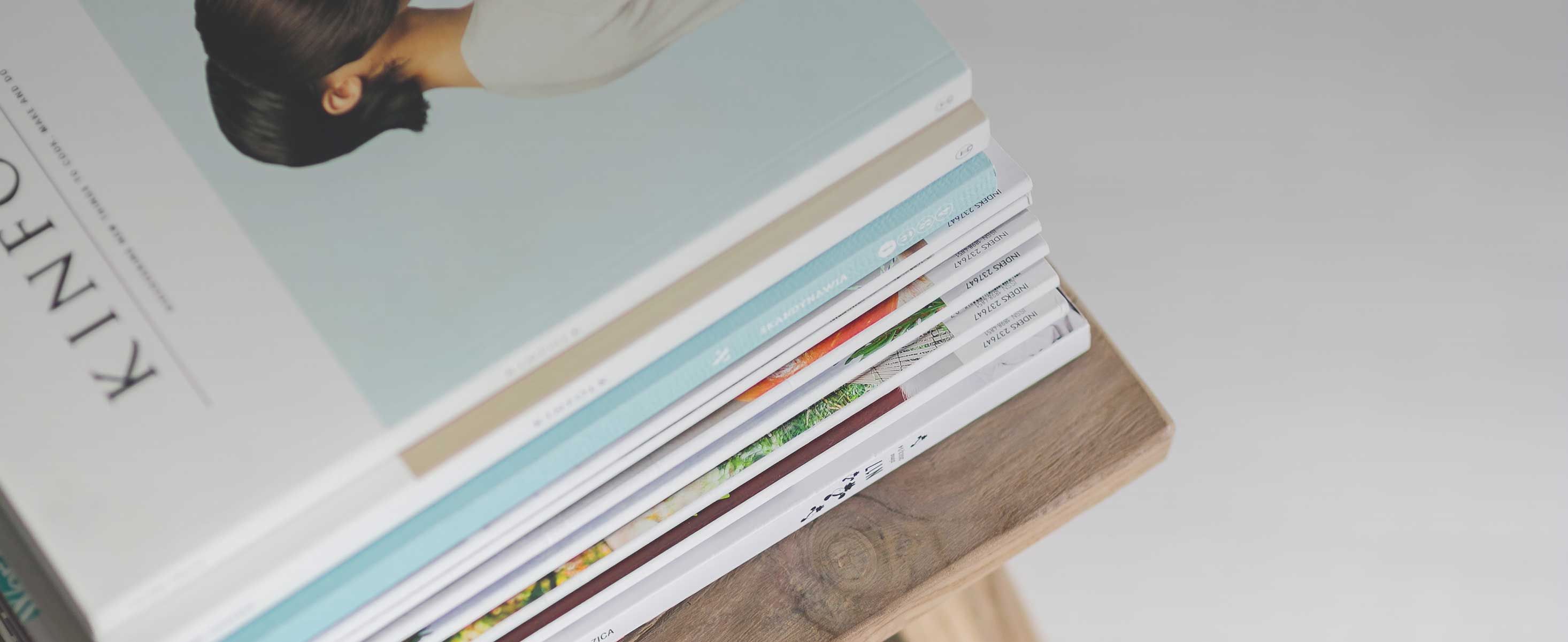
2 minute read
WHAT IS THE DIFFERENCE BETWEEN DYNAMIC AND STATIC IMBALANCE?
There is a good reason why rotating parts need to be balanced prior to use. An imbalanced part, being rotated at speed, causes unwanted vibration that increases proportionally as the square of the rpm of the rotor increases. (Doubling the rpm produces four times greater force of imbalance) This vibration will likely shorten the lifespan of the part, as well as the other components around it. On top of the possibility of damage or even catastrophic failure, this can also cause an excessive amount of noise, making it harmful to the hearing of those around it. In order to achieve better operation, longer service life, and not having to fix or replace mating parts you need to make sure that these rotating parts are balanced within their particular tolerance.
WHAT IS IMBALANCE?
Advertisement
Before understanding the difference between static and dynamic balancing and imbalance, you must first understand what imbalance is with respect to rotating bodies. Imbalance is the misalignment of the center of mass from its axis of rotation. Imagine a cylindrical rotor. Its nominal shape would consist of a large cylinder in the center with two smaller cylindrical shafts protruding from each end. Each of these sections is perfectly concentric.
Now, if you were to add a large piece of material to the outside of the cylinder in one place you would be changing that rotor’s center of gravity. There would be more mass in the location of the added material than there would be anywhere else along the cylinder.
If you were to now rotate that rotor along its axis of rotation down the center of the cylinder you would have excess centrifugal force in the area of the added mass. This would cause the rotor to want to pull away in the direction of said mass, causing vibration as it rotates. This is your imbalance. In order to bring the part back into balance you must either offset that material 180 degrees from it in the same plane of rotation, cancelling out the added centrifugal force, or remove the material causing the shift in center of gravity. Either way, you want to return the center of gravity back in line with the center of rotation.
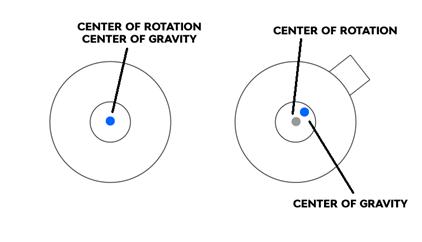
Static Imbalance
In “static” imbalance, only gravity or weight force is involved. Static Imbalance is essentially a heavy spot at a point outside of the center of rotation of the rotor. It is called static because it is present even when the part is not rotating. If the rotor is placed on frictionless rollers or “knife edges” and a weight is applied at the center-of-gravity line (between the two ends), the weighted portion, acted upon by gravitational force, would immediately roll to the bottom. This would be the heavy part of the rotor being pulled down by gravity until the heavy spot is at the bottom. You can see a part’s static imbalance on a balancing machine by setting it on the bearings and letting the heavy part rotate downward just using gravity. Static imbalance can be corrected with single plane balancing. Balancing the rotor, without rotation, may be accomplished provided the rotor is a narrow, inflexible type.