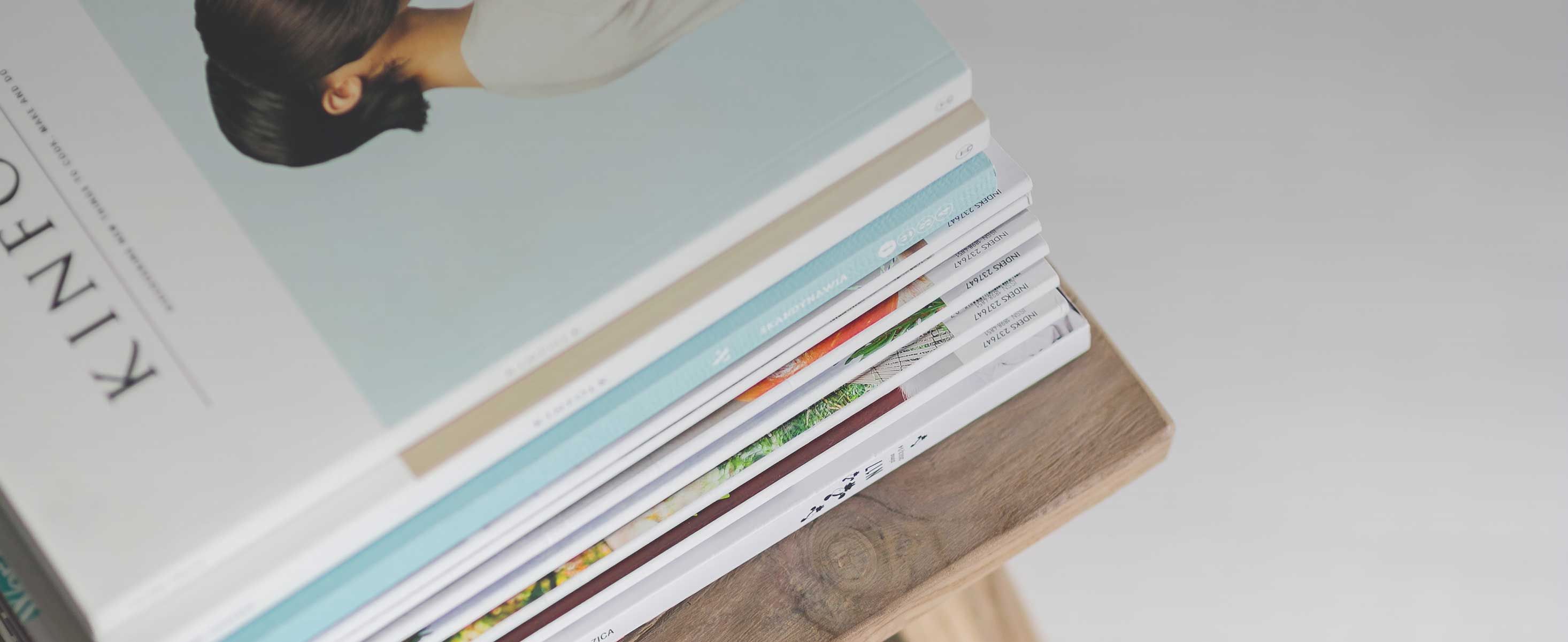
2 minute read
DYNAMIC IMBALANCE
Some balancing machine manufacturers refer to “dynamic” imbalance as any type of rotating imbalance, but technically speaking, dynamic imbalance is strictly a “couple” caused by two equal forces in two separate planes, 180 degrees opposite each other.
Assume the rotor is placed on frictionless rollers. Because each weight is 180 degrees opposite each other, no one point would roll to the bottom, since this rotor is balanced statically. If this same rotor is revolved to an appreciable speed, each weight would cause a centrifugal force which, being in separate planes, would cause a rocking motion tending to displace the rotor. The direction of the rocking motion would change as the location of the weights changed during their rotation about the rotor shaft. This type of unbalance is called pure dynamic unbalance.
Advertisement
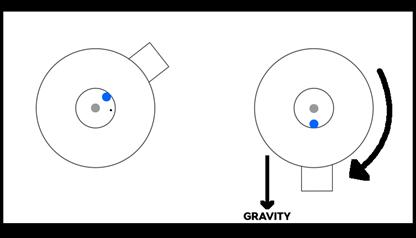
To observe this action, place a pencil on a table and push with one finger in one direction, as you push with another finger in another plane in the opposite direction. The pencil will tend to rotate “end-for-end”. This action is restricted in a rotating rotor by the bearings that hold the rotor in one plane – however, this tendency to turn “end-for-end” is still present and it is this force which causes the rotor to vibrate.
Combined Static And Dynamic Imbalance
Rarely does pure dynamic or static imbalance occur. More often, parts tend to have a number of imbalances throughout their composition, at different planes along its axis of rotation. Imagine a heavy spot one inch from the left end of the cylinder at the top (relative to the machine operator) and another heavy spot one inch from the right end, but toward the bottom. Because of these “heavy spots” the part will try to pull the rotor in the direction of their respective centrifugal forces. This is also referred to as “couple.” Dynamic imbalance can only be determined while the part is rotating.
This asymmetric distribution of mass about the axis of rotation causes vibration when the part is rotating. It is this vibration which is measured by sensors on our dynamic balancing machines and sent to the ProBal data acquisition board to be turned into useful data for the computer to display. The ProBal system of balancing separates these forces into their component parts; dynamic couple and static force. The computer then gives you the location and amount of imbalance to be corrected. The advantage of separating static and dynamic in balancing is that the operator can make his corrections in any plane he desires. Often the operator may choose a plane of correction but finds after finding the angle of the imbalance that he could make his correction easier in some plane other than that originally chosen. This is done by either adding or removing material in the correction planes to realign the center of mass with the center of rotation. When achieved, this should eliminate the excess centrifugal forces and lessen the unwanted vibration.
ProBal Dynamic Balancing has a long history of making the process of balancing rotating parts faster and simpler. Our balancing software is arguably the most user-friendly in the industry. All the information needed to find and correct dynamic and static imbalance is displayed for you with easy-to-understand graphics and simple to adjust settings to make sure the calculations accurately reflect reality on the machine. Our system drastically cuts setup time, as well as having a sample time in mere seconds. Our goal was to give the operator an easier time making corrections and less time needed to interpret the data.
To learn more about why owning one of ProBal’s Dynamic Balancing machines will help your company to become more productive and efficient visit our machine information pages or contact us to see how we can best put together a turn-key solution for your balancing needs.