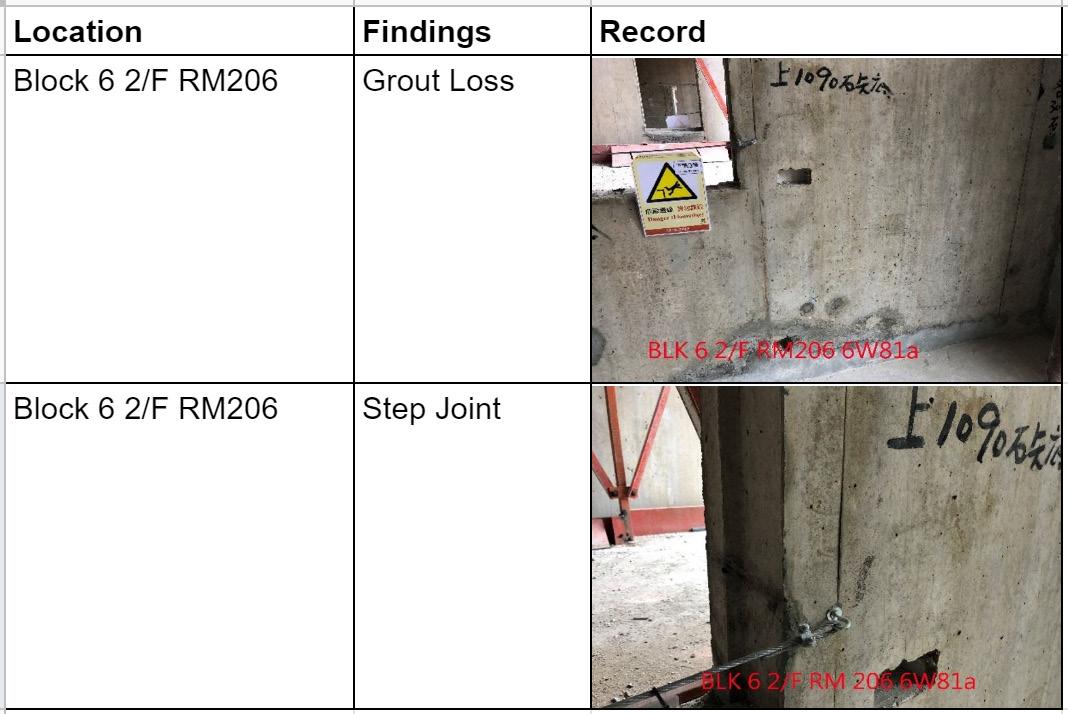
5 minute read
01
from Portfolio
by Jessie Kwok
Work Experience on Site
I have 5-6 years of experience in construction management. After architecture and urban design study in university, I listened to seniors' advice and worked at the main contractors to learn how to build a building. I know what happens after drawings came out and before buildings been delivered to users. During my work experience, I worked on three big projects: Fire Service Training School, Hong Kong Children's Hospital, and Pak Tin Estate Phase 11. I took part in small projects, such as the renewing of dormitories of Hong Kong University and Linnan University, etc.
Advertisement
There are three most essential points of construction management: time, money, and quality. I mainly took part in quality control and record progress. Matters were numerous on-site, and sometimes I also need to handle the transaction problems of workers.
I need to know the progress of architecture. To build a building, workers tie rebars, erect mouldboards, pour cement, and demolish mouldboards. After erecting the walls, I would go to check the quality of the concrete surface. Only the surface of the concrete is fair and neat can apply upper layers to the walls. According to the orders of a specific trade, I would contact different subcontractors to start construction and installation on time.
The progress was designed into different phases, base, underground, transfer floor, and above ground. Project managers called it milestone progress. Every floor had a schedule. The time of trades also needed records. Every week, progress meetings were held. On a workday morning, the foreman reported new conditions of the site: the subcontractors on-site and the workload of the workers on their duties.
Construction Progress
Construction Schedule A Site Wak Defects Record

A Concrete Defects Rectification Schedule
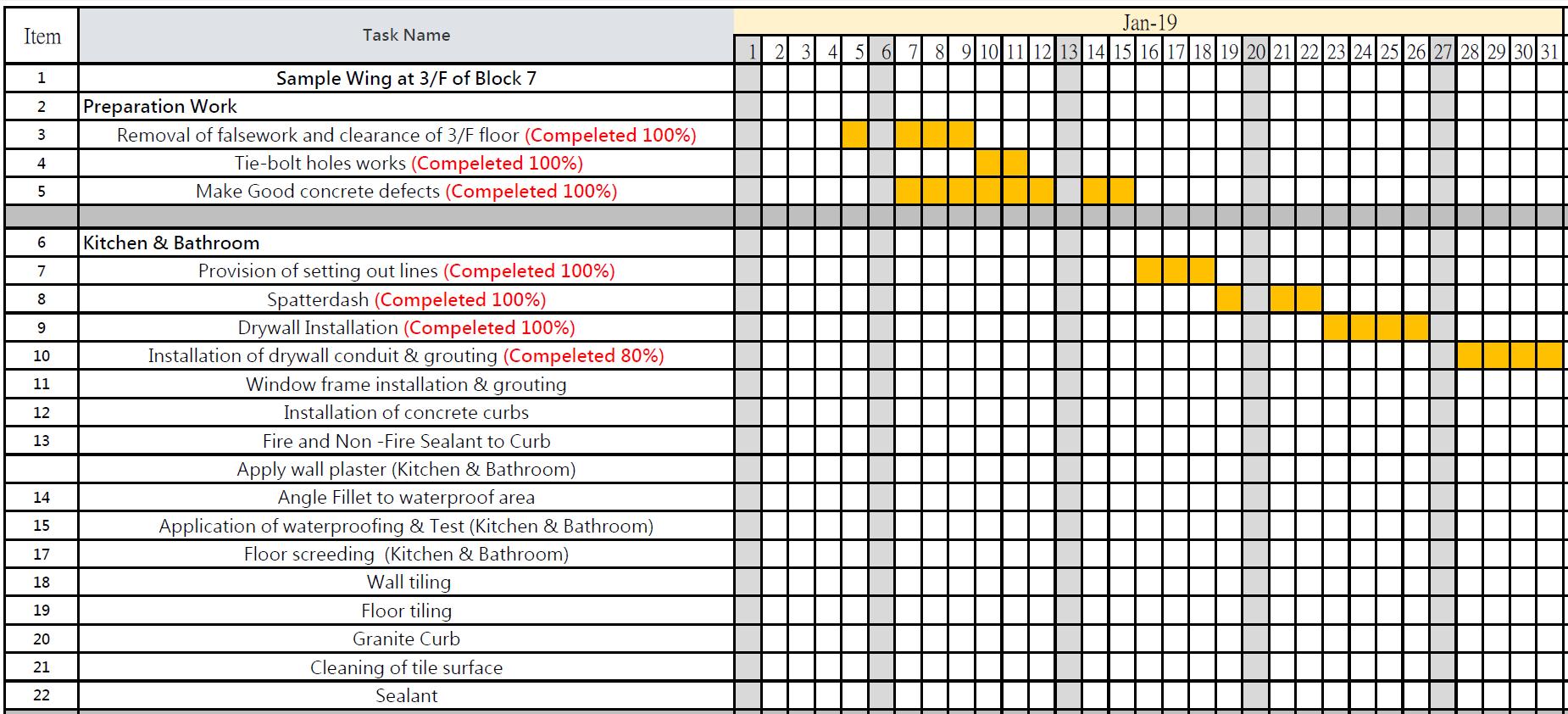
Before starting a new trade, I must make sure architects approve the drawings; the materials' certification is available and recognized; the methodology is practical. Colleagues of QS told the project team the chosen subcontractors. In addition, I would check if there were enough workers got license issued by the council of construction.
When starting a new trade, I would fill record the date in the progress file. A methodology meeting is a must thing. Telling coordinators and subcontractors details of contractor got twice the result with half the effort. A methodology meeting includes instruction of materials and facilities, preparation, construction flow, accepted standard and rectification measure. Safety officers and environment officers must be present. If the trade used materials about green architecture, I would also report it to QS Department, and they could apply supernumerary fees from the government.
Because the site lack human resource, sometimes safety officers can't be present in methodology meeting. I got a certification in safety supervision. Safety is the top priority of a project.
I would not only held methodology meetings for quality control but also take photos and record the procedures. On the site, new quality problems and solutions may occur. If any new foreman entered our project team, I would transfer the information to newcomers.
Methodology meeting is a critical way to improve quality. Some trades need a long period of construction. Sometimes, holding just one meeting is not enough. When quality problems happened repeatedly, I would call foremen, subcontractors, and workers to held meetings twice, even more times. When I did the site walk, I would also check a worker randomly to ask if he or she knew the must-know knowledge about quality control.
When workers finished work, I would check the quality. Foremen are good partners, and they would tell the details and condition of the site. If quality problems happened, I need to find someone to do rectification and make a schedule. If the subcontractors delay, I will issue a formal alert letter. When contractors impacted the whole progress and had a bad performance, I would negotiate with the project manager to change a subcontractor.
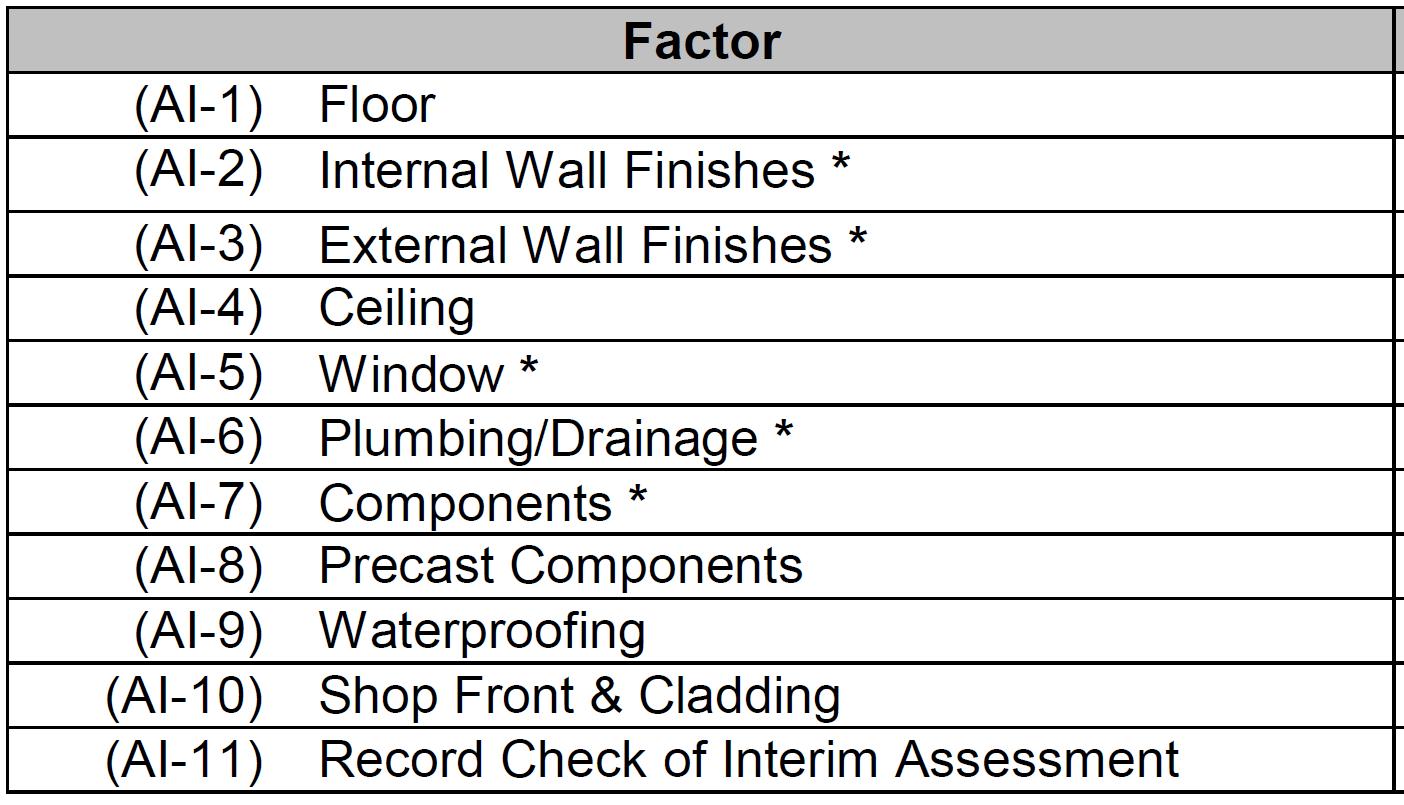
11 Items of Inspection
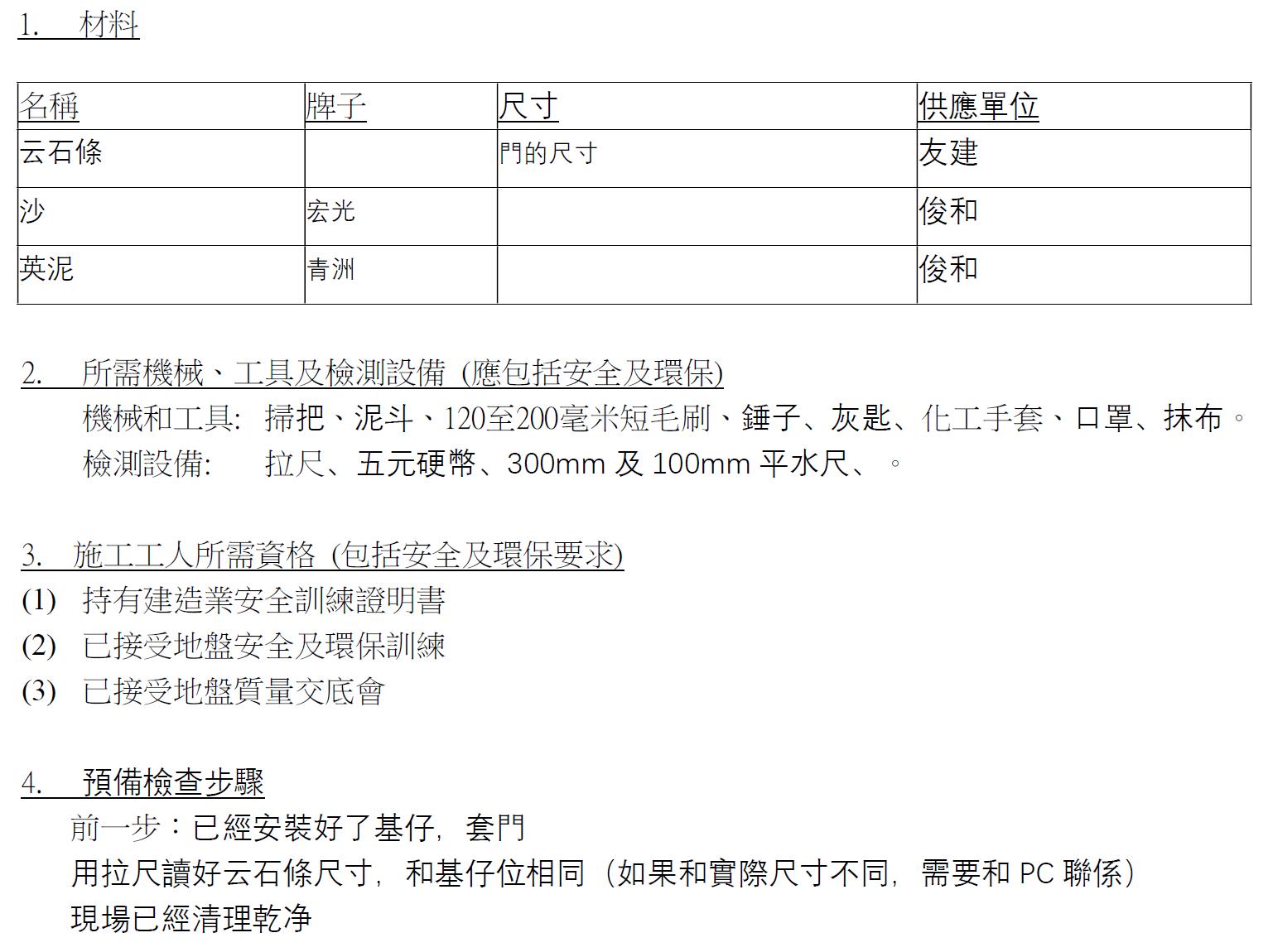
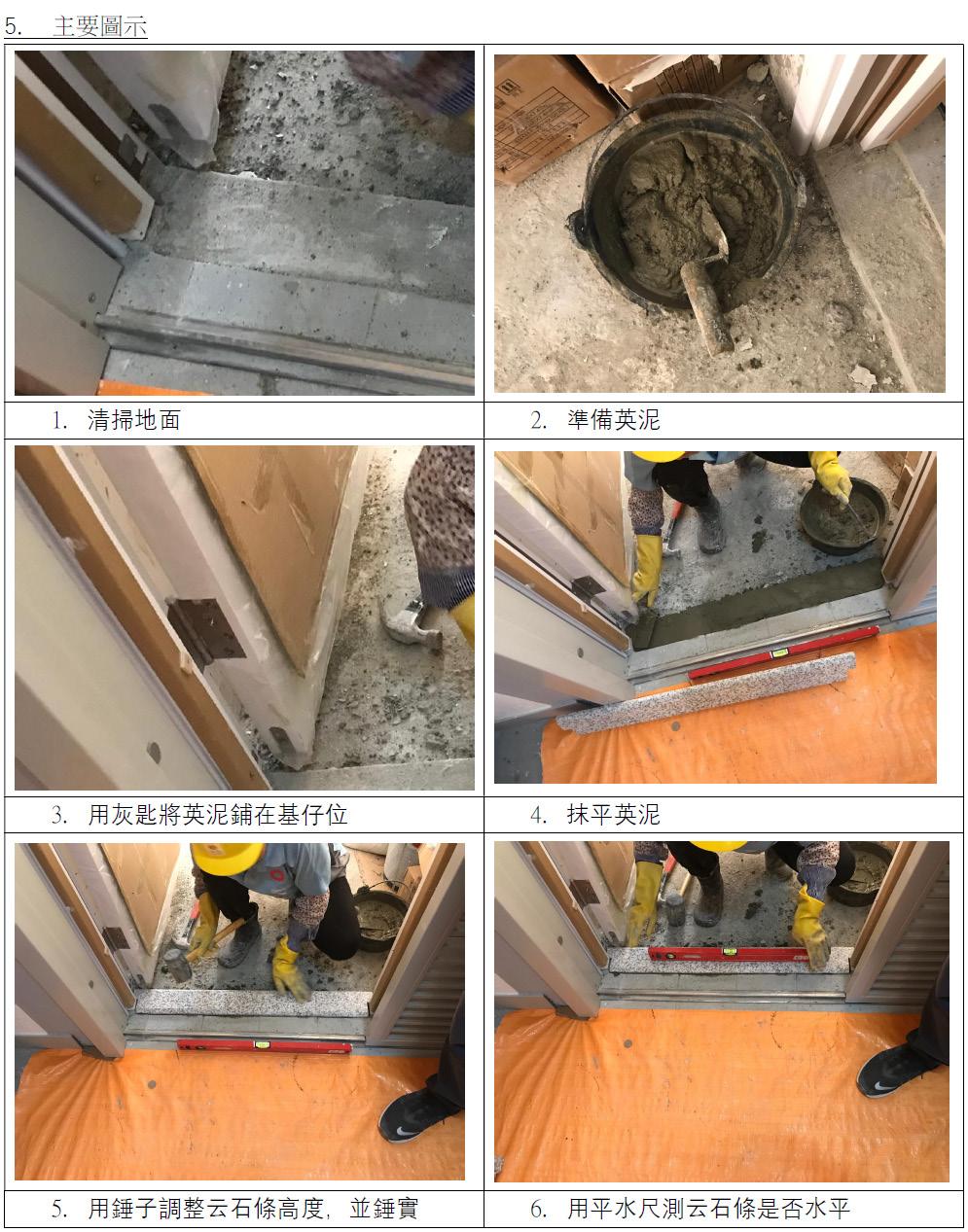
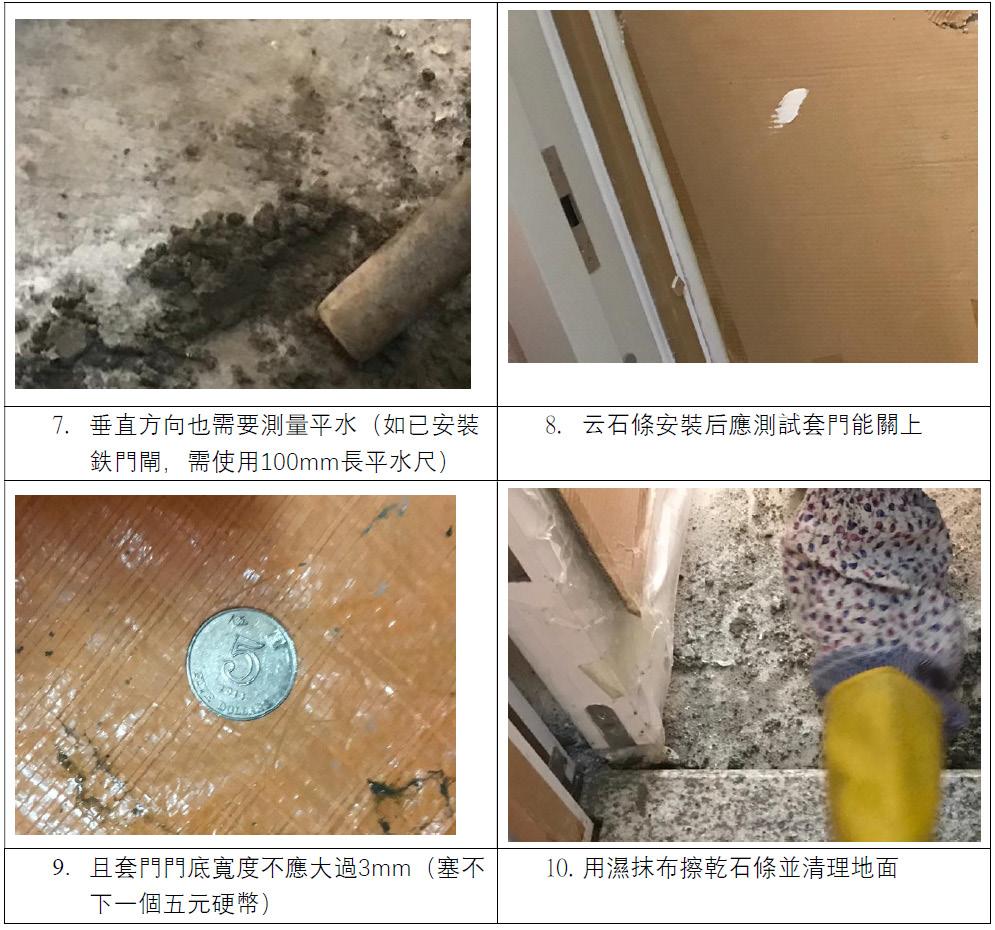
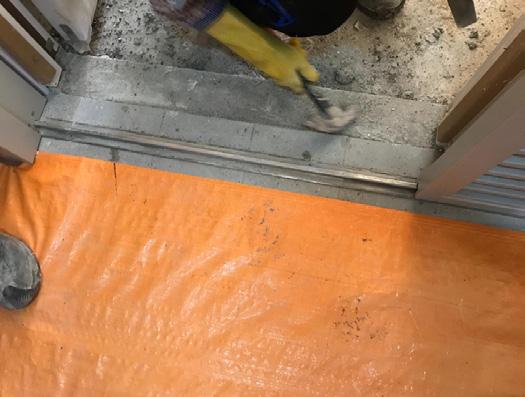
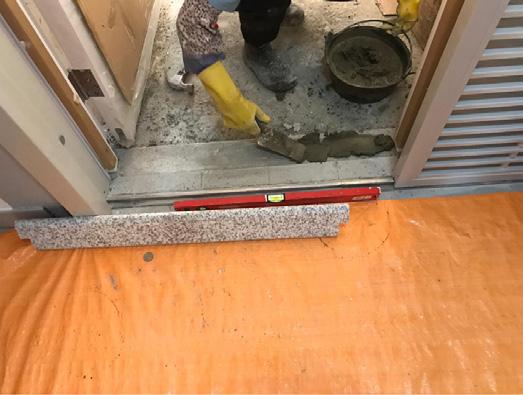
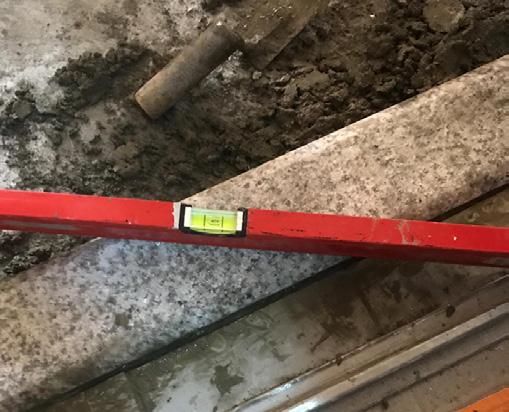
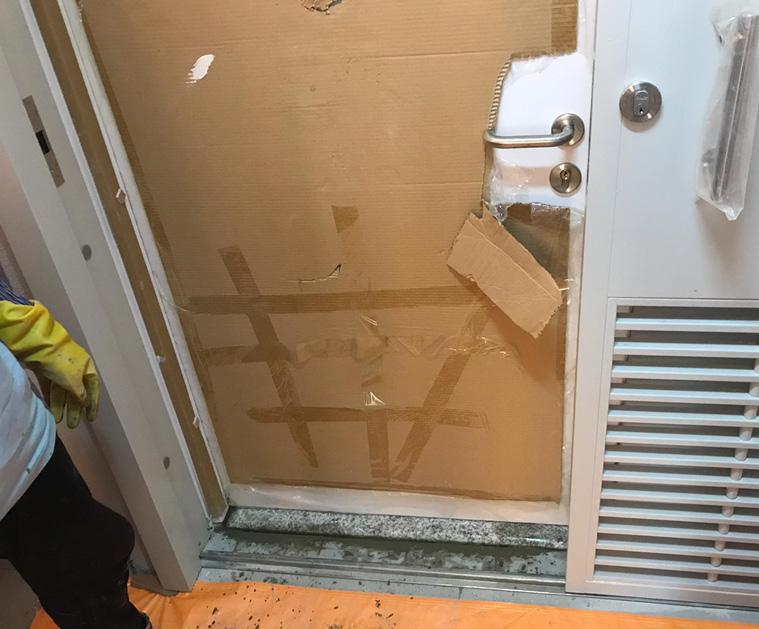
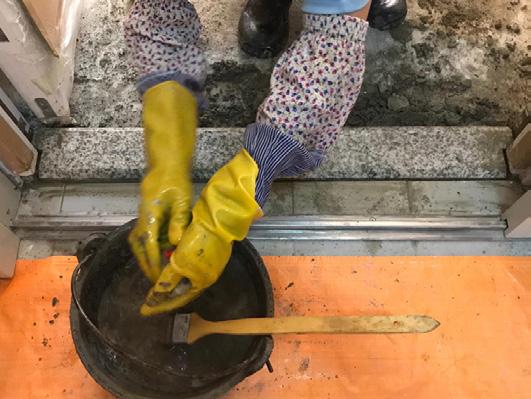
Architecture Coordination
In construction, problems are numerous every day. Sometimes I would go to the site by myself. Sometimes foremen help to check. Problems happened every day. One detail may conflict with another. Some design looked good in drawings may be a big problem of the whole construction.
In the site office, I worked among civil engineers and building service engineers. I always have meetings with clients and project team staff. Purchasing staff, safety officers, and environment officers also need to work together. A project was a giant nest. We are all involved and try our best to build a building together.
This is a drawing combined ceiling and layout plan. I discussed with the building service engineer and QS staff to modify the details.

On the right, there is a shop drawing depicts the components used in the construction of precast walls. In Hong Kong, precast walls are also called "drywall". On the site, workers call it "cookie wall." I asked industry manufacturers to figure out the function of each component. There are a lot of shop drawings different from bidding drawings.

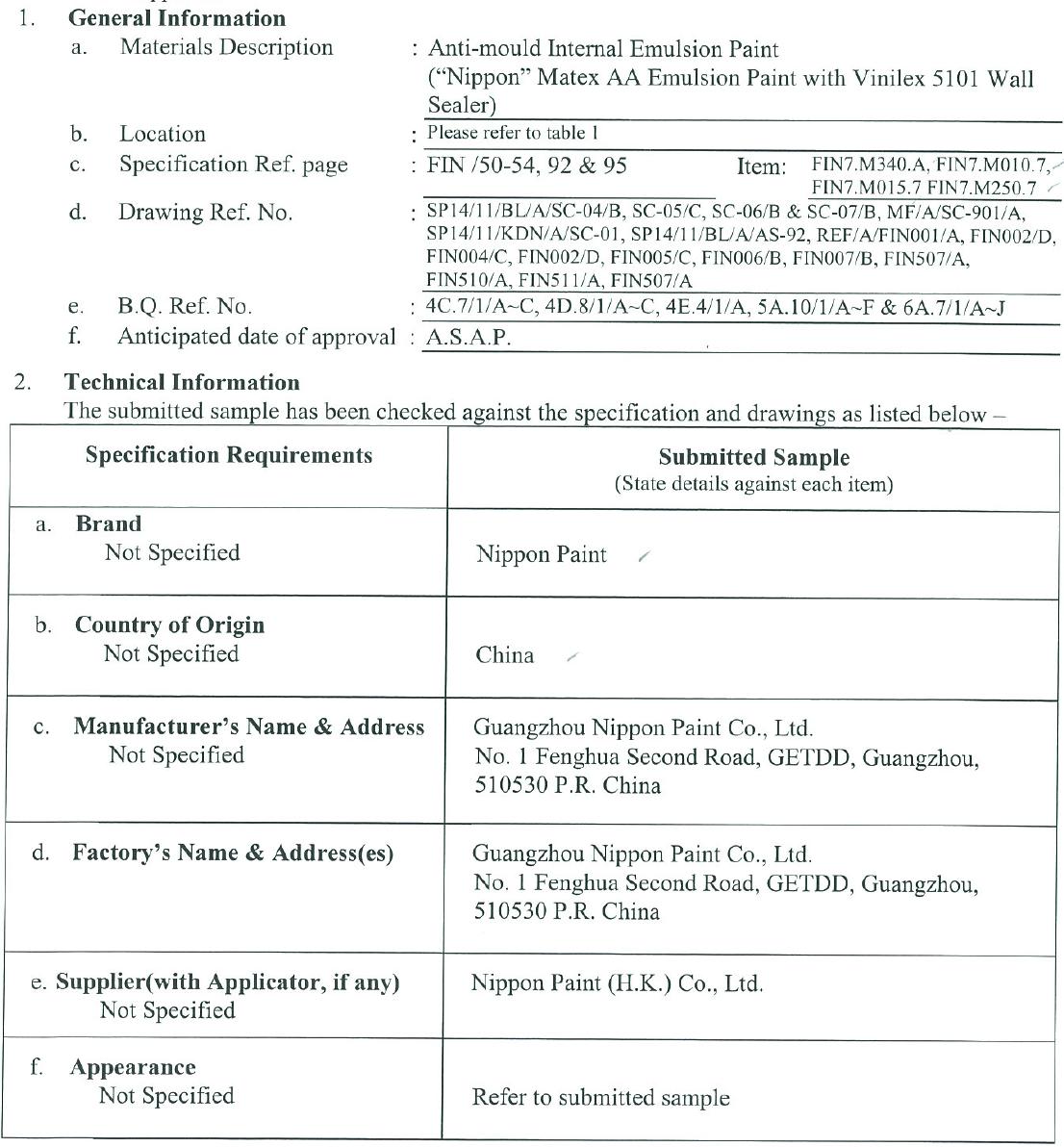


Specification lists the requirements of submission
Material Management
According to progress, the coordination team would choose the appropriate material for use. Before submission, I would check specification documents and drawing requirements. Then I would ask suppliers to provide needed information for approval. Only approved materials can be used on site.
There are four steps of material management: purchase, deliver, store and use. Every step has its own requirements of the materials.
PURCHASE
DELIEVER
STORE
USE
Four Steps of Material Management
Material Submission Schudule
