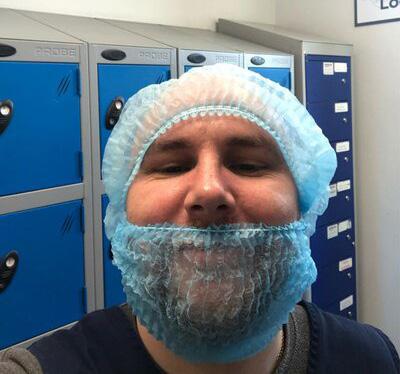
11 minute read
Roofing & Cladding
Roofing & cladding HOW LINKEDIN RANT LED TO FULL-TIME JOB FOR DAD
AN IMPROMTU LinkedIn rant has turned into a full-time job at leading Derbyshire roofing firm PermaRoof for dad-of-one Lee Moore.
Advertisement
The 36-year-old, from Kirkby in Ashfield, Nottinghamshire, was between jobs when he signed up to a temporary work agency and was placed on the 6am until 2pm shift at a local food packing manufacturer alongside four other workers. However, by 7am, Lee was the only agency staff member still standing, with the other four quitting in the first hour.
Shocked by what he saw, Lee took to LinkedIn to vent. His post ended up going viral, racking up more than 120,000 likes, 5,000 comments and hundreds of job offers – including one from Adrian Buttress, managing director at Alfreton-based PermaRoof.
Lee, who has a nineyear-old son, said: “I had been unemployed since mid-February and was in the middle of interviewing for a role at a company in Chesterfield. However, this got pushed back due to Covid, so the recruiter said they could sign me up for some temporary work with an agency.
“I couldn’t believe it when an hour into my shift, the four other temporary workers I’d arrived with had already given up – one refused to wear a hair net, another said they didn’t want to use a computer and the remaining two said the work was too boring. I was amazed that people out of work could be so picky; for me, a job is there to keep a roof over my family’s heads, pay the bills and provide food, so I was proud to wear my hair net!
“I vented my frustration on LinkedIn – it was only supposed to be a rant, but it ended up going viral. In fact, I am still getting notifications for it today, more than a month later. It was mindblowing to see how far it ended up travelling; I had hundreds of messages from people offering support and opportunities.
“One of them was from Adrian at PermaRoof saying he was interested in having a chat. I had a couple of interviews and he made me feel the most wanted. He was very transparent about where the company was heading and really went the extra mile, showing me around the PermaRoof headquarters, which ended up being just a few miles away from my home.”
Lee – who previously worked in sales for hire and construction companies – has now joined PermaRoof as a specialist products manager. As part of his new role, he will be working in the firm’s modular division, a sector PermaRoof expanded into during the pandemic after supplying fast flat roofing solutions to four emergency NHS projects during the first month of lockdown.
Lee Moore has joined PermaRoof as a specialist products manager after his LinkedIn post went viral
Adrian said: “I believe in hiring on attitude as everything else can be taught. When I came across Lee’s post on LinkedIn, I knew I had to speak to him. When I discovered he had previous sales experience and lived just down the road from our head office, it seemed like fate. Lee had hundreds of job offers, so I am truly delighted that he chose to come and join the PermaRoof team. We’re extremely happy to have him with us and know he’ll do a fantastic job building our customer base for the modular division.”
For more information on PermaRoof, please visit www.permaroof.co.uk or call 01773 608839.

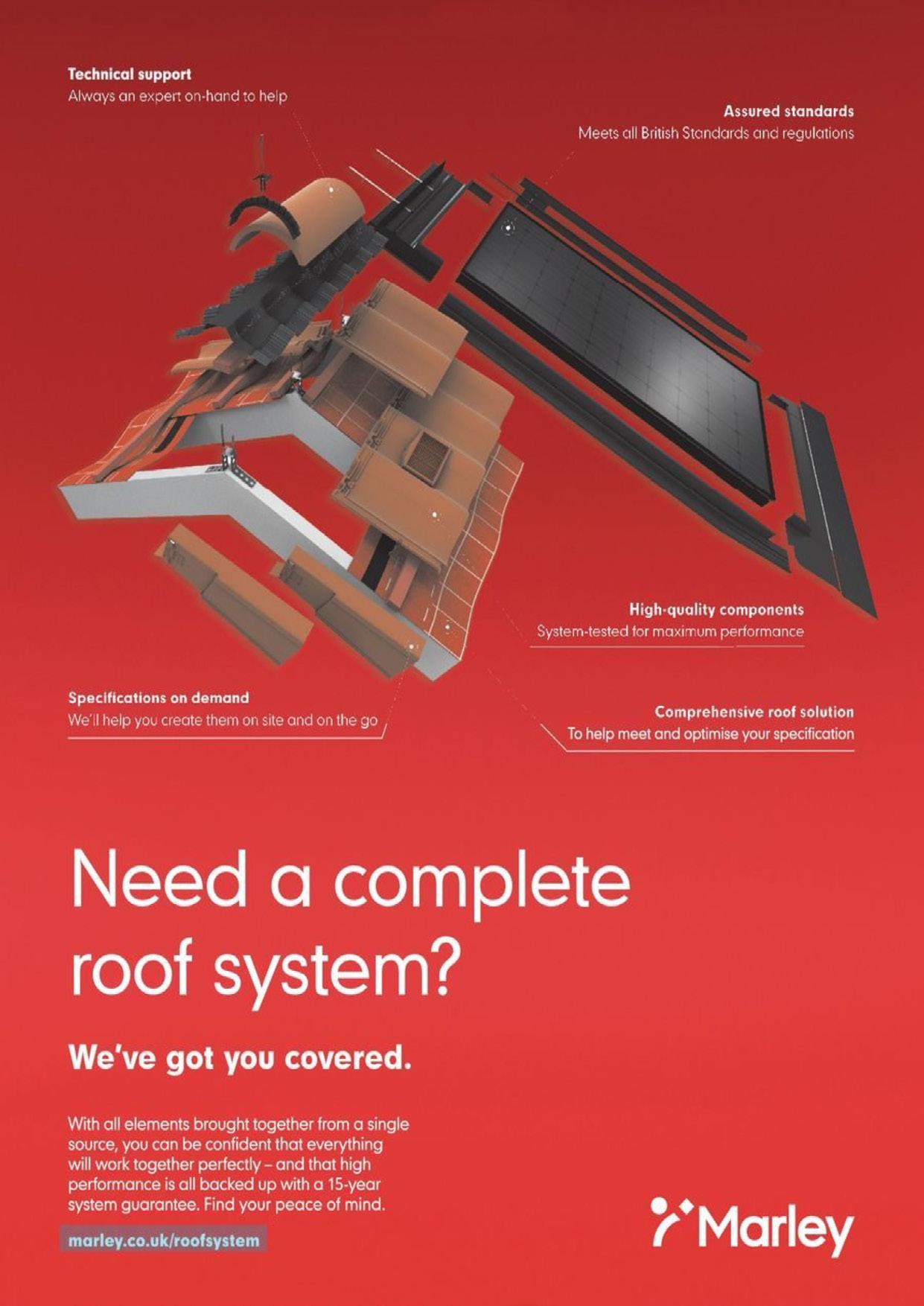
www.metalline.co.uk
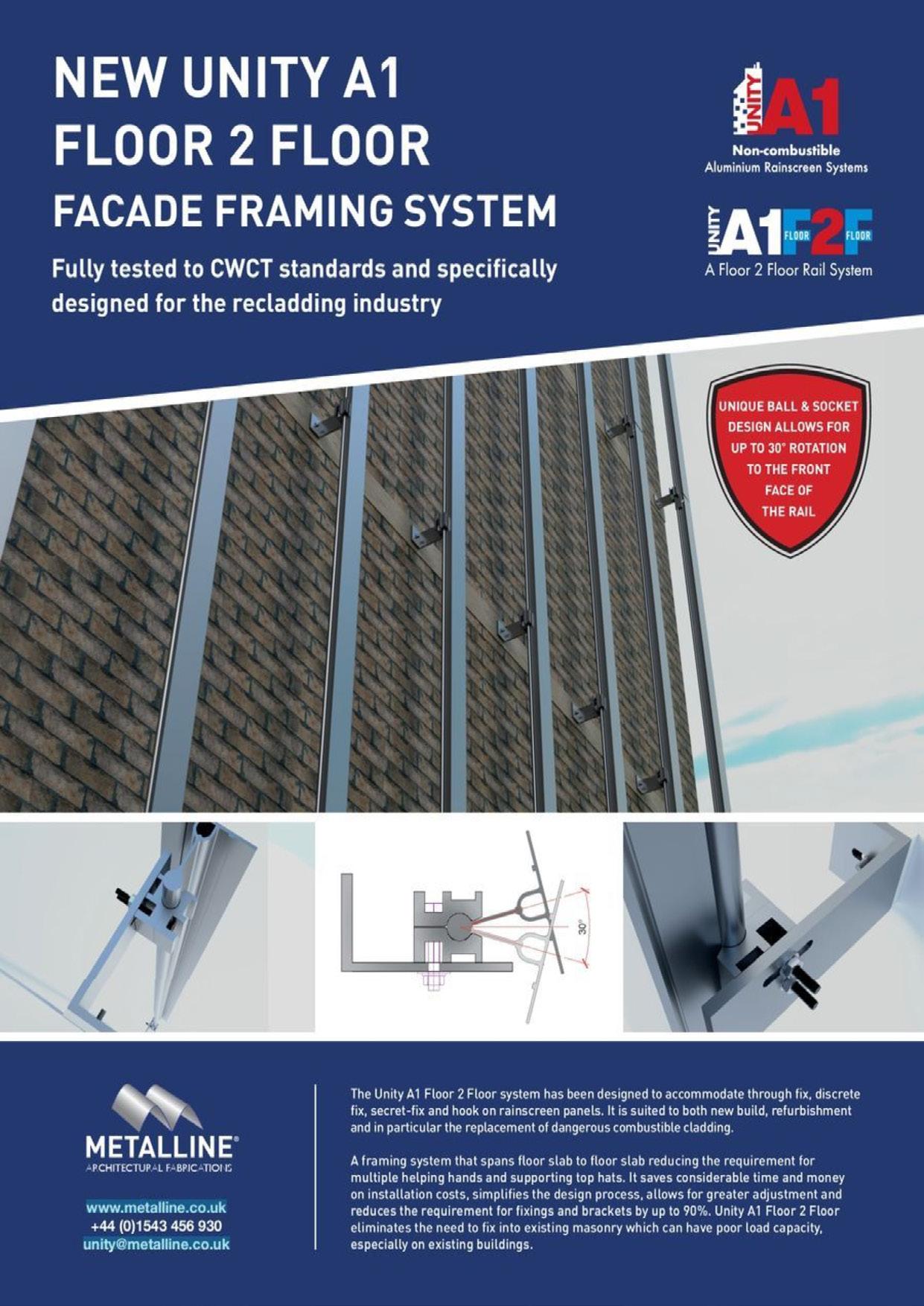
roofing & cladding West Fraser product application: Roofing (OSB)
Getting buildings wind and watertight is a priority on any construction site so choosing a quick, easy to install, reliable and versatile roofing system is vital.
H
igh quality roof decking or pitched roof sarking is an essential component and Oriented Strand Board (OSB) is now the preferred option for many. Unsurprisingly, given the product’s outstanding attributes, West Fraser’s SterlingOSB Zero OSB3 or SterlingOSB Zero T&G is frequently the first choice.
Ideal for structural use in load bearing dry or humid conditions, SterlingOSB Zero OSB3 offers great value and durability. Stronger than most softwood ply, thanks to its makeup of multiple layers of real wood strands pressed together, it is designed to withstand the toughest of conditions. Working with the boards is trouble free as they are uniform in quality with no knots, voids or delamination issues. Helping to cut waste, a range of panel sizes and thicknesses is available to suit all needs.
The boards are square-edged so butt together easily and cleanly. Panels are cut and installed on a roof using conventional roofing equipment and are easy to saw, drill, nail or plane. Nails can be driven as close as 8mm from the panel edge without causing splitting. SterlingOSB Zero’s smooth surface gives improved adhesion qualities for all flat roofing applications and no sanding is required, even for GRP finishes.
With all the advantages of the Sterling OSB Zero range, SterlingOSB Zero T&G is specifically designed for flat roofing and is BBA approved and fully compliant to BS 6229:2003. The panels are consistent and machined to exact tolerances. Reliable fixings are easily achieved across the board using 3mm diameter ring-shank nails or 50mm long screws at 100mm centres across the supporting joists. The tongue and groove profile helps increase the lifespan of the roof by reducing movement of the boards which could damage surface coverings.
Timber is a highly sustainable building product and, with the Sterling OSB Zero range, there is the added reassurance that the product’s environmental credentials are further enhanced. The panels are net carbon negative, responsibly sourced and FSC certified. They are manufactured in the UK from locally grown timber, cutting embodied carbon from transportation. In addition, all West Fraser mills have obtained the coveted environmental ISO 14001 accreditation. The Sterling OSB Zero range is also the first OSB product to be made in the UK with zero added formaldehyde, so it is an even ‘greener’ board that meets all standards with ease.
Samples of SterlingOSB Zero, and West Fraser’s other construction panels, can be ordered on the website Uk.westfraser.com. Head to the housebuilder page on the website to download a selection of tools including a fully-interactive guide to all West Fraser products and a checklist to make sure you have everything you need for your build.
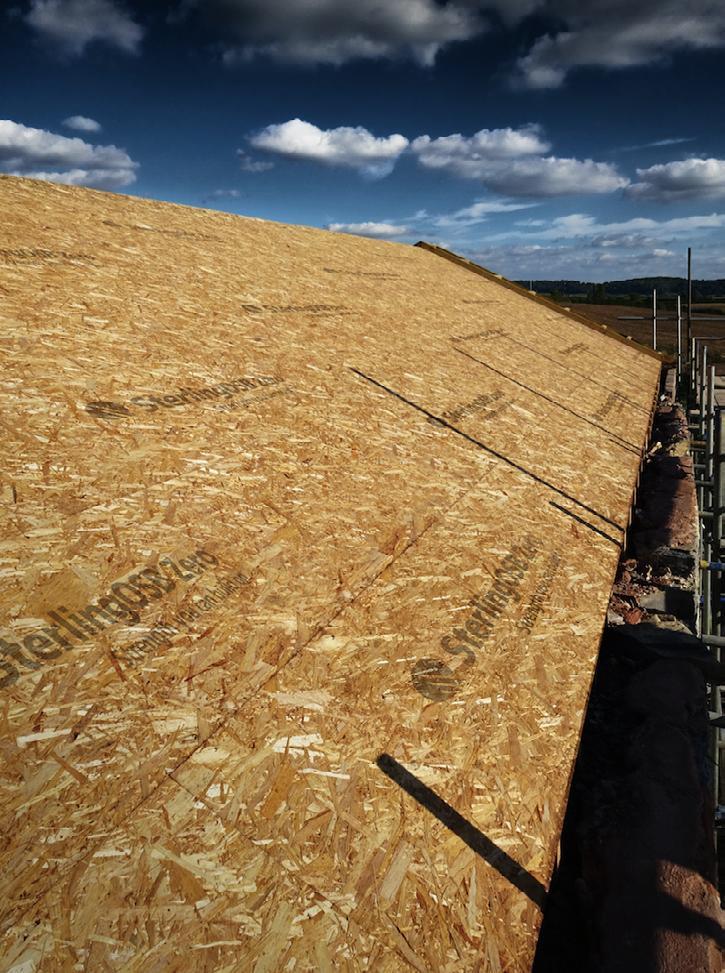
For further information, call 01786 812 921 or visit
Uk.westfraser.com
G
reen roofs are sometimes thought of as a specialist feature due to their innovative nature, meaning contractors are often not made aware in conversations with merchants that they could be offering them as an extra service.
Also known as “living roofs”, they have a visible top layer that consists of plant medium and can be crowned in a number of different ways depending on the tastes of the building owner, the purpose of the roof (whether it’s a flat roof on an extension or something smaller, such as the top of a bike store), and its weight-bearing capacity. Every layer is important
Green roofs are made up several layers of material with a base, waterproofing membrane at the bottom, protected from the drainage layers by isolation medium and a planting layer on top. Planting layers typically consist of ground covering, water-loving plants such as sedum and other succulents, moss and grasses.
Arguably, the most important layer to get right is the base membrane. Once you’ve determined that the structure will take the additional weight of a green roof, which a surveyor would be able to confirm, then choosing the right membrane is crucial.
Creating a green roof can be a costly, timeconsuming process for the client, therefore using a reliable, high-quality waterproofing membrane is essential for the base layer. If this base membrane fails and need to be replaced, not only does it mean a waste of time and money for homeowners, but it could also negatively impact a contractor’s reputation – particularly if regular failures occur. The ideal membrane
Your base layer must provide 100% waterproofing across the entire project and be effectively adhered directly onto the roof deck, which is what makes EPDM the perfect candidate for a long-term living roof.
EPDM membranes carry a life expectancy of more than 50 years, backed up and proven in the field all over the world across a wide range of climates. Because the planting medium absorbs rainfall so effectively, water is often consistently present and seeps through the drainage and protective insulation layers before reaching the membrane.
This is where the EPDM comes into its own as it removes this concern by protecting the flat roof deck from water ingress and offering the best protection over time when compared to any other flat roofing membrane.
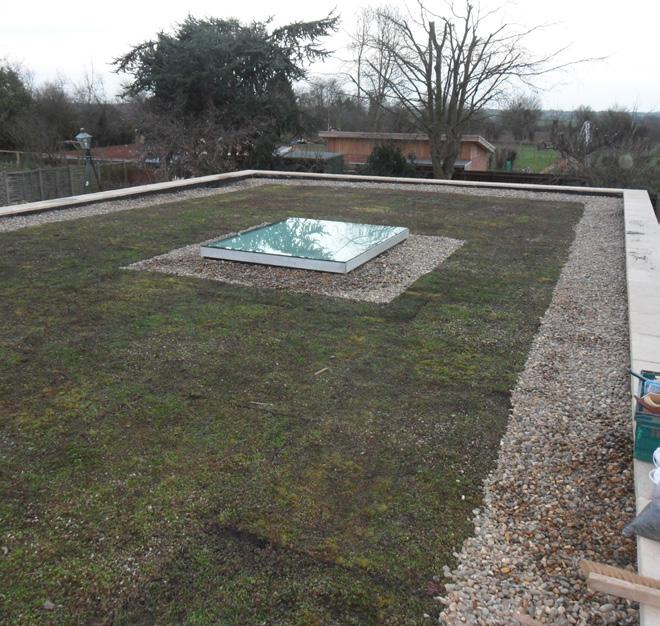
Three top tips
1. Use an isolation layer widely across the green roof Quite literally, cover all your bases. Make sure the base waterproofing membrane is completely protected from the gravel or other aggregates that may be used in the following drainage layers. While EPDM doesn’t damage easily, it still requires adequate protection to ensure the membrane doesn’t get punctured.
By simply covering the entire surface area with a suitable isolation layer – such as a geotextile fleece – you minimise this risk and will also contribute to making the home more energy efficient.
2. Consider maintenance aspects during the design process There are three different kinds of green roof design, which all require different levels of maintenance:
• Extensive: This is the lowmaintenance option; it’s often planted with mediums that are mostly self-sustaining and hardy against most weather conditions. The most successful plans for extensive green roofs are sedum, rough grasses, or moss. • Semi-intensive: This is often used in roofing that can be used and walked upon, such as roof terraces. Paths with planting that can be lightly maintained are the ideal candidate.
• Intensive: This is the most weight-bearing option, so advice from a surveyor or architect would be advised to ensure the current roof can support this additional weight. It offers more design ideas as a garden, such as the use of trees, shrubs or even the creation of patio areas and/or flower beds.
3. Add interest around the edges It’s a good idea to spend some time on the design of a living roof as mistakes can prove costly. For example, think carefully about how the green roof appears from the ground. If it’s a high roof, seeding around the edges with plants designed to overhang could be a nice additional design feature.
But above everything else, choose a supplier than can support the contractor’s design vision who has a dedicated knowledge of green roofs. This includes support of the design or aesthetic value of the intended roof as well as consideration of creating habitats for urban wildlife, surface water management, sound insulation, and energy efficiency.
Lightwell Restoration
– Brentwood, Essex
Delta Registered Installers, Renderseal Ltd were employed to provide a maintainable waterproofing solution to a problematic lightwell. The scope of the project was to facilitate a solution for water penetration and salt contamination without disturbing the existing garden patio or adding any additional pressure to the interior of the property.
Any below ground structure will require a robust waterproofing design. The same scenario applies to lightwells.
In this project scenario, the basement lightwell walls are earth retaining and are subject to lateral penetration from ground water subject to weather conditions and water table levels. The existing render finish, on inspection was very sandy in colour and failed to form a barrier/resistance to hold back any moisture/water.
An earth retaining wall is a structure designed and constructed to resist the lateral pressure of soil, when there is a desired change in ground elevation that exceeds the angle of repose of the soil.
Whether you are building a new home or doing a renovation, you can add plenty of light-filled luxury by simply including an architectural void or lightwell.
Voids and lightwells are large open interior spaces that contribute to natural light entering a property from outside.
Methodology After surveying the condition of the lightwell and adjoining property, Renderseal Ltd proposed a solution to modify the lightwell to mitigate any future problems without significantly affecting the structure or surroundings. •40•
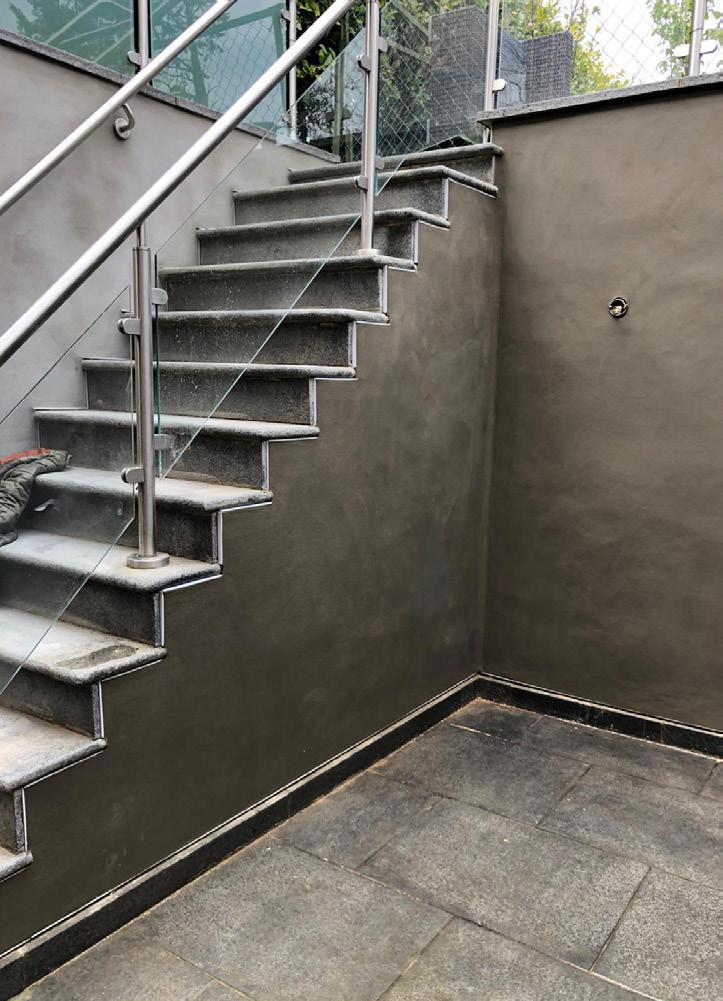

Delta’s PT membrane offers a fast and effective method for repairing and upgrading lightwells, whilst at the same time retaining the existing aesthetics of properties, making this approach particularly suited to repairs. Delta’s PT Membrane is a HDPE membrane which works as an impermeable damp proofing base for plaster or shotcrete (as a water control and drainage membrane).
Due to the “air gap” technology, Delta PT creates an effective barrier to the transmission of moisture, humidity, water vapour and salts, whilst assisting drainage by directing any water ingress to suitable drainage points. Once the Delta PT was installed, Renderseal incorporated vertical expansion joints to prevent the render from cracking, whilst installing a horizontal stainlesssteel stop bead base. They further applied a two-coat sand/cement to provide a surface ready for painting.
Products • Delta PT Membrane
• Delta PT Plugs with Grommets
• Delta Fleece Tape
• Delta PT Profile Case Study Results Renderseal Ltd were praised for the quality and speed of their refurbishment/installation, which was completed in just 5 days and within budget.
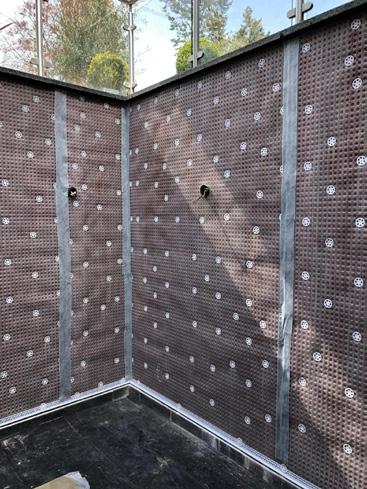
The owners of the property were delighted with the result and knowledge that their lightwell will remain fully protected against the long-term threat of water and salt ingress.
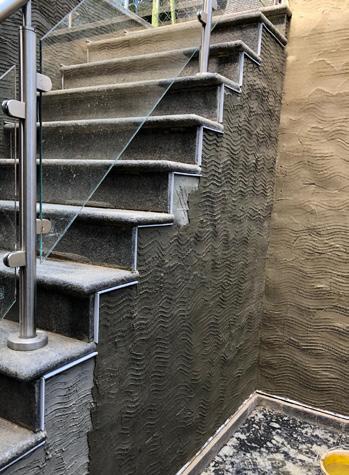