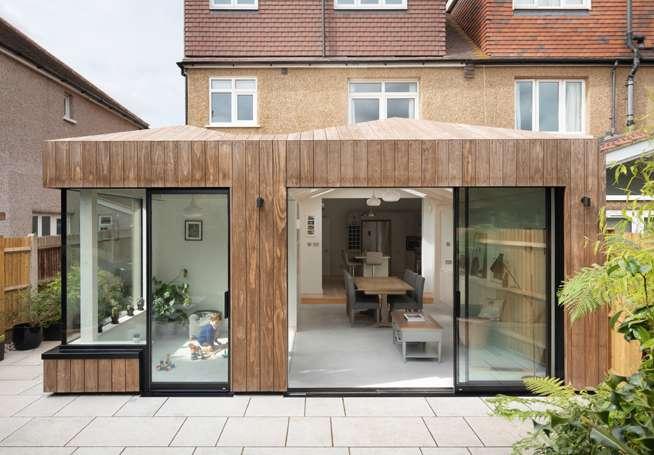
11 minute read
Paints
Widely recognised as one of London’s most perfect villages, full of beautiful shops, prime period properties and green open spaces, Wimbledon is an idyllic location for any family. Therefore, it came as no surprise to Up Architects when they were appointed by a young family, who required more space, to deliver the full refurbishment and extension of their existing home. Kebony, a global leader in the production of sustainable modified wood, was carefully selected by the architects for the exterior cladding of the extension to create something truly beautiful without being ostentatious.
After making the decision to stay in their house, rather than moving to a bigger property in the area, or moving away from the children’s school, the family recognised their pressing need for more space. Up Architects wanted to design an extension that stood out from the run-of-the-mill extensions in the area, and started with the idea of a single large space that could be adapted to suit the family’s needs over time, incorporating dining, living, a playroom, study area, TV room and guest room into the brief. Now their hectic family life could take place in a modern, light filled open-plan living space, all with an enhanced connection to the garden. In keeping with the client’s brief, the design is simple, un-assuming and honest with two simple roof forms sitting over the main space, formed from an exposed glulam timber structure with Kebony cladding used for the exterior walls and roof. The simple geometry of the twinhipped roofs breaks up the bulk seen from outside and defines the different spaces internally without a physical division. The timber Kebony cladding lines up across the walls and roof, with compound mitred joints, making the whole extension appear to be carved from one block of wood, with no visible gutters to compromise the sharp lines.
Advertisement
All the timber used was sustainably sourced and the Kebony cladding is guaranteed for 30 years. Developed in Norway, Kebony’s revolutionary technology is an environmentally friendly and patented process which modifies sustainably sourced softwoods by heating the wood with furfuryl alcohol - an agricultural by-product. By polymerising the wood’s cell wall, the softwoods permanently take on the attributes of tropical hardwood including high durability, hardness and dimensional stability. This unique process also provides Kebony with its characteristic appearance, which only grows more beautiful with time.
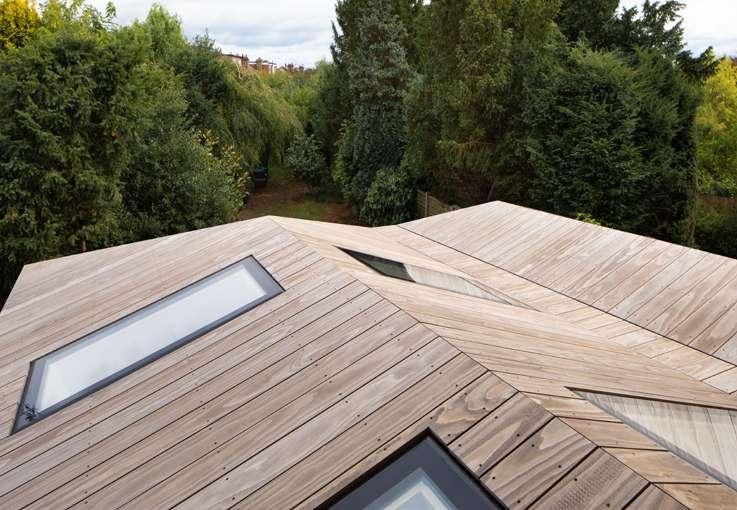
Marty McColl, Director at Up Architects commented: “Following our appointment for this project, it was essential that the family felt they had made the right decision in opting for an extension rather than moving house. We were able to create substantially more space, whilst ensuring the extension reflected the brief to build something that was beautiful in design without being ostentatious; we are thrilled with the final product and loved working with Kebony to transform this traditional suburban semi-detached house into a contemporary and more practical family home.”
Adrian Pye, International Sales Director at Kebony added: “We are delighted with the growing demand for Kebony extensions, the wood is extremely versatile and can be used for both traditional and modern properties as well as detached, semi-detached or terrace houses. It is evident that Up Architects have carefully considered the brief and created the perfect living space to meet the needs of this young family and the final product is a testament to their hard work.”
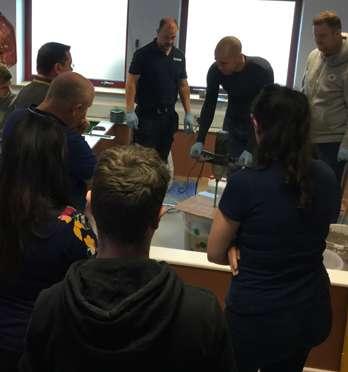
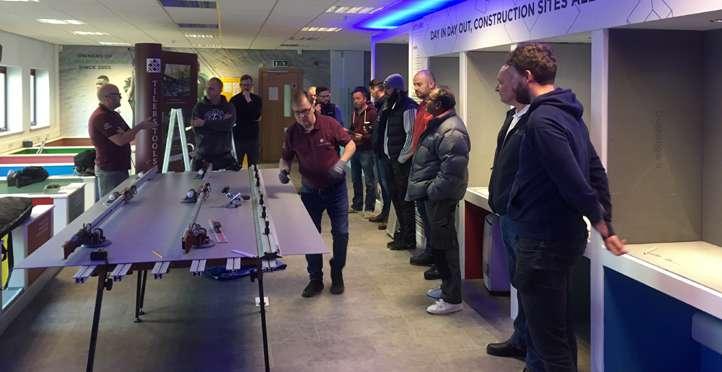
Mapei has unveiled its extensive list of training dates for 2020, as part of plans to continually utilise its impressive training facility based in Halesowen, West Midlands.
F
ollowing a successful first year of training courses at the facility situated at Mapei Academy, a total of 51 days have been dedicated to training, covering Ceramic Tiling, Resilient Flooring, EWI, Resin, Ultratop Loft, Concrete Repair and Basement Structural Waterproofing.
There will be 12 dates dedicated for each of the Ceramic Tiling and Resilient Flooring training courses, 6 dates for both EWI and Resin Flooring, and 5 dates each for Ultratop Loft, Concrete Repair, and Basement Structural Waterproofing. A team made up of Chris Myatt, Adrian Jennings, Neal Perryman, Adrian Jones and Jeremy Mann, as well as relevant product line experts, will be on hand to provide information and expertise at each tailored training course. Bookings from distributors, contractors, designers and engineers are welcomed, and can be tailored to specific needs and requirements. All training delegates will receive presentation notes, refreshments, a buffet lunch, a factory tour and Mapei goodies.
The dates are as follows:
Ceramic: January 7, February 4, March 3, April 7, May 5, June 2, July 7, August 4, September 8, October 6, November 3, December 1
Resilient: January 9, February 6, March 5, April 9, May 7, June 4, July 9, August 6, September 10, October 8, November 5, December 3 EWI: January 23, March 26, May 28, July 30, September 24, November 26
Resin: February 25, April 28, June 30, July 28, September 29, November 24
Ultratop Loft: January 21, March 24, June 23, August 25, October 27
Concrete Repair: March 17, May 12, July 2, September 15, November 10
Basement Structural Waterproofing: February 27, April 2, June 11, September 17, November 19

To book your place on one of Mapei’s coveted training courses, email ukmarketing@mapei.co.uk or call 0121 508 6970

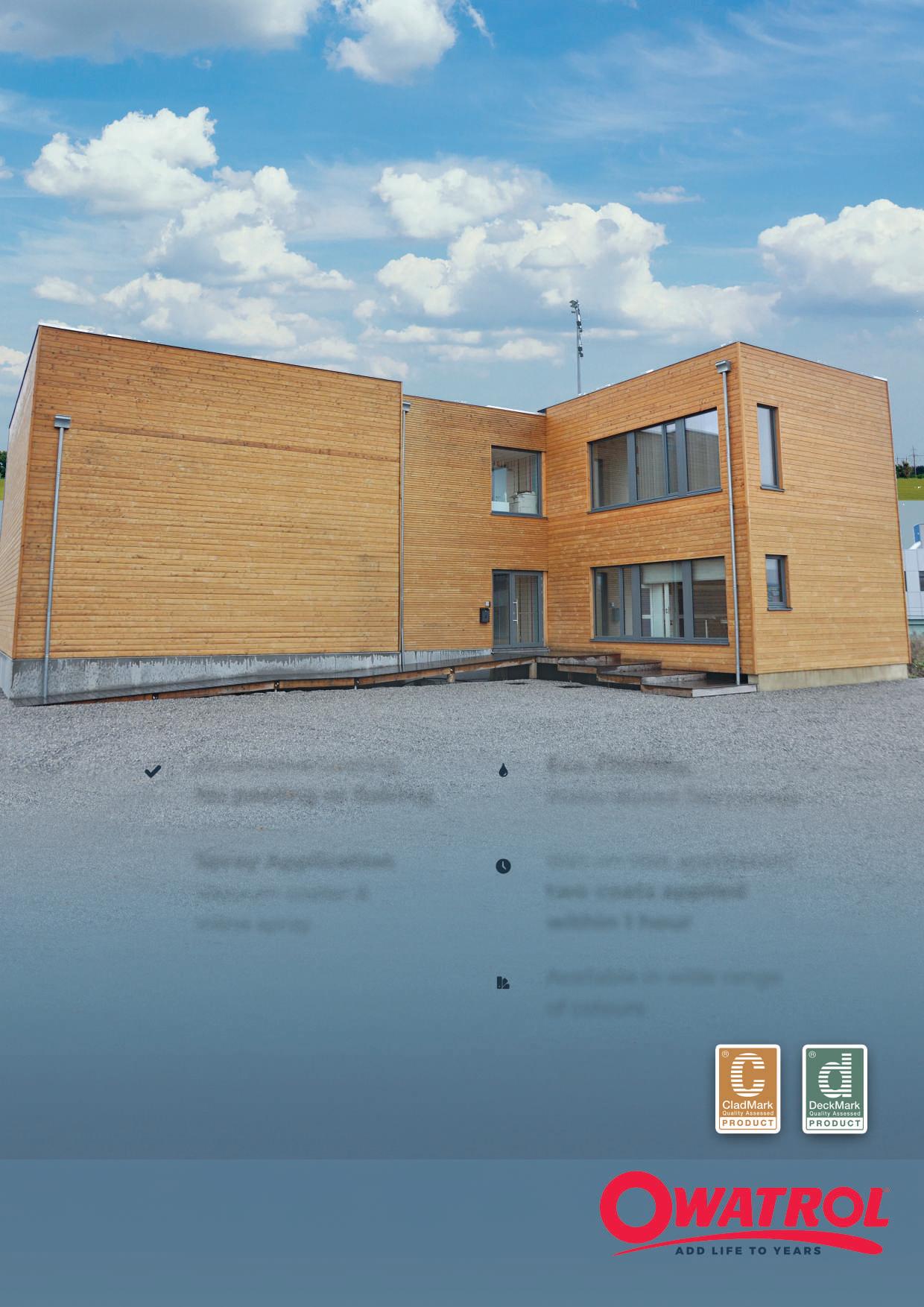
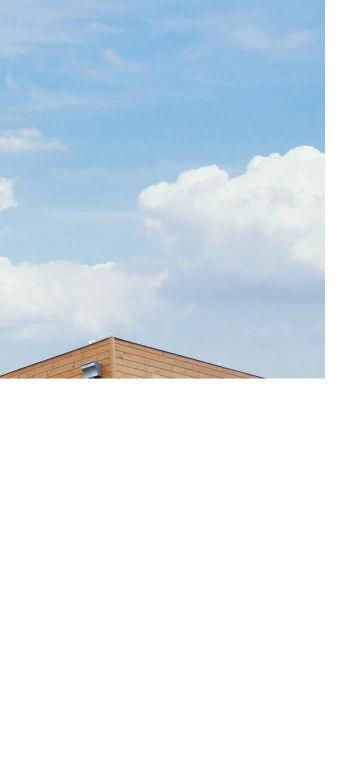
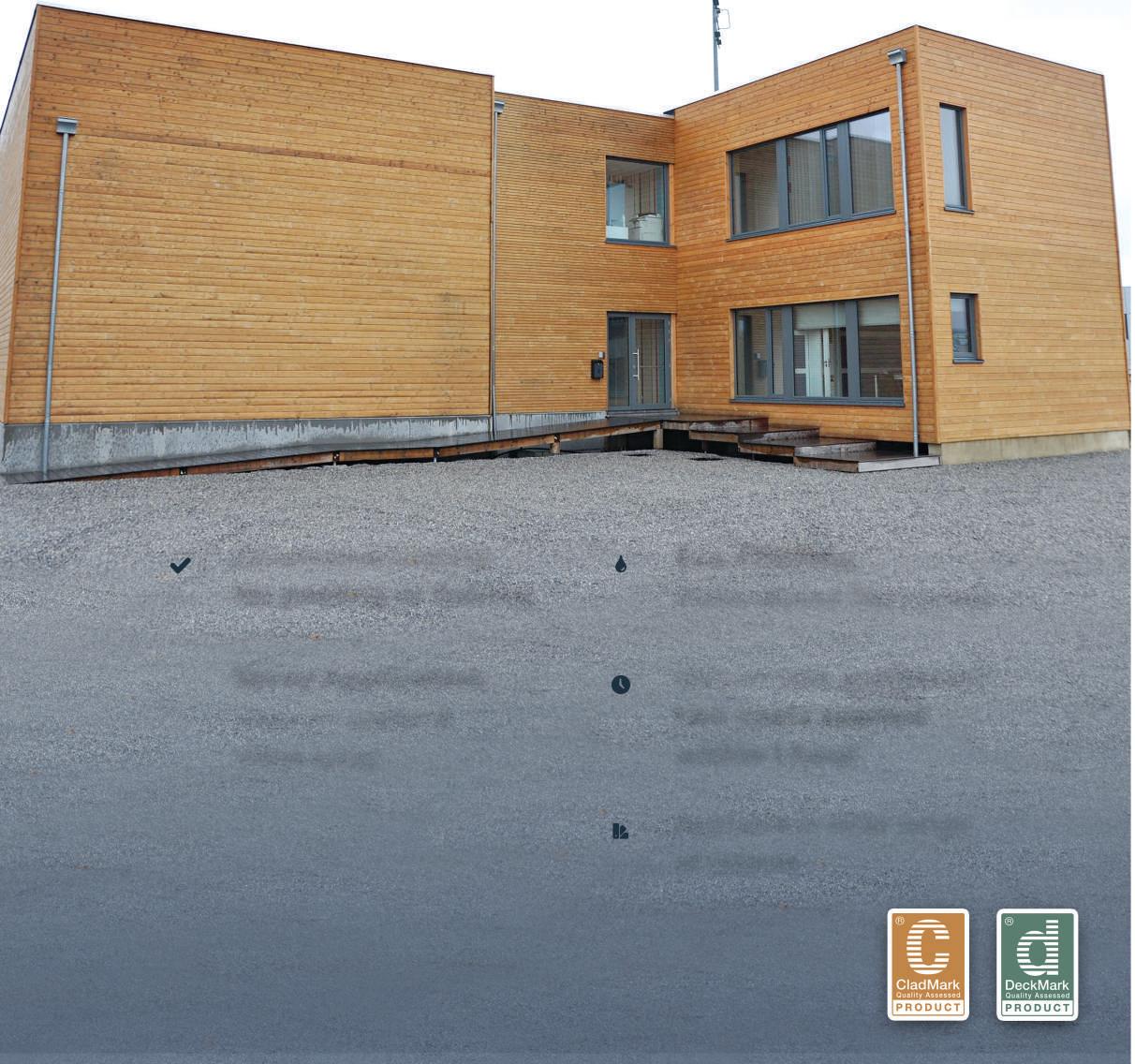
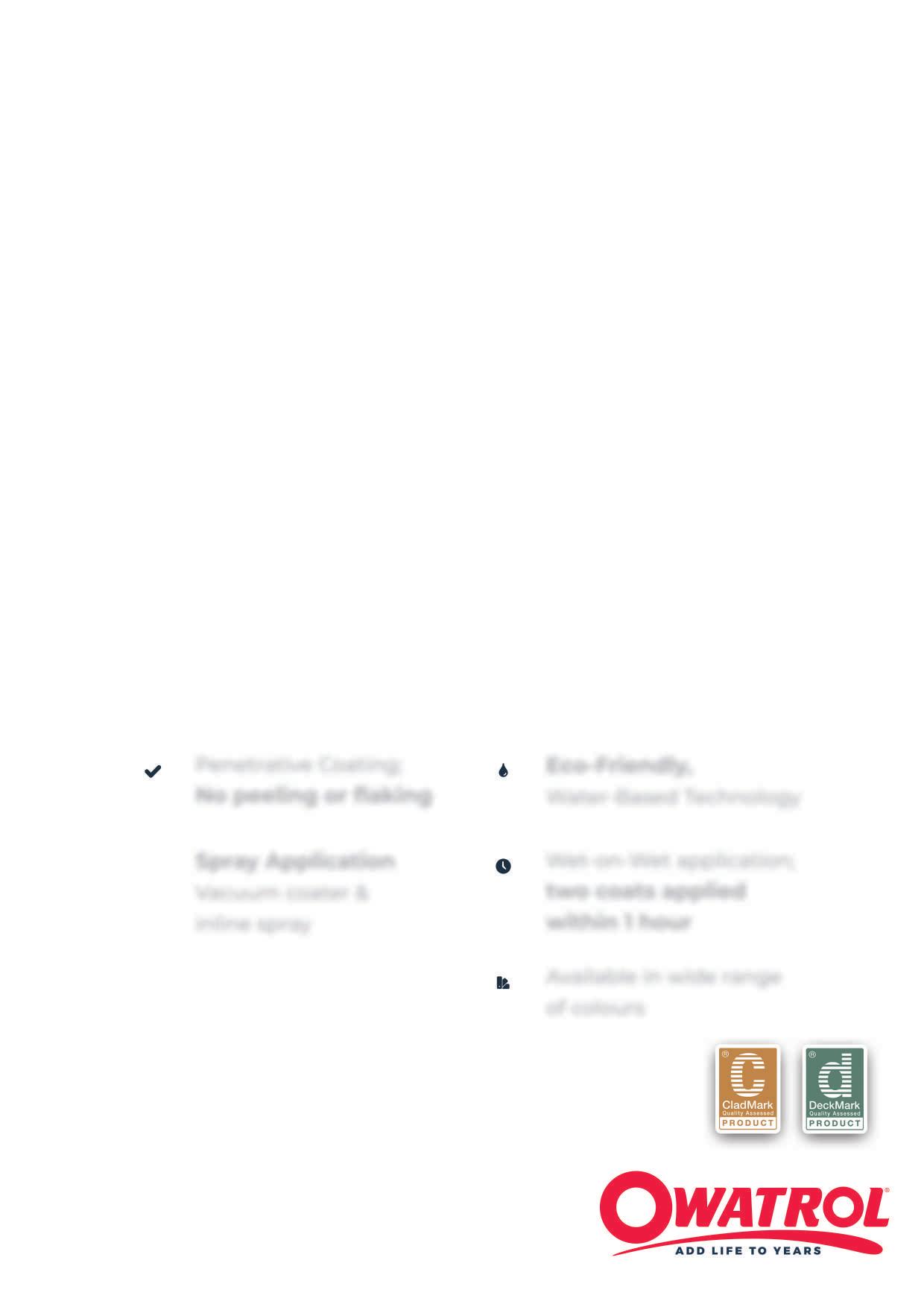

Paints BT1 - Ground-breaking technology in resisting E. coli and MRSA
In time of heightened health risks and being cautious of what we put into our homes, it is now the time take a more in depth look at BT1, the latest technology from CT1 and making sure we always use the healthiest choice in our homes and new builds.
I
n an era of uncertainty and high tension due to COVID-19, we are concerned about the health of our nation and home dwellers. Not only that, but those in clinics, schools and hospitals where the most vulnerable are.
CT1 which is the UK’s Number 1 Sealant and Adhesive, is the healthiest choice for the home. Boasting over 25 accreditations, this makes CT1 the healthiest choice for your home.
CT1 has an EC1 certification for the lowest emissions, A+ Green which is awarded for lowest indoor emissions green rated, Green ISO standard and the most unique accreditation and highly accredited, is The Norwegian Asthma and Allergy Association. The NAAF logo is highly sought after and one of the hardest accreditations to receive. The association test and awards products on their ability to reduce asthma and allergy attacks in the home, and CT1 The Snag List Eliminator has been awarded this. CT1 is the only sealant and adhesive globally to achieve this. A label recognised globally as the highest in its authority for advising and testing of products that reduce asthma and allergy in the home.
CT1 with a unique TRIBRID® formulation has no solvents and is also the most userfriendly sealant and adhesive to use with no odour. CT1 also has an ISEGA food certificate.
But never to rest on their laurels, CT1 who lead the way in research and development for the building industry, realised a massive gap in the market for a unique product for the bathroom only. One which creates a clinically clean bathroom! But on testing and developing the product, the lab tests came back with some unique results. BT1 Bathroom Sealant Number 1, which has been created to completely fight off bacteria, fungus and all pesticides. Ground-breaking technology formulated over 4-year period and vigorous testing has created the most high spec sealant on the market to date.
With a guarantee of colour retention, for up to 25 years. Scientifically formulated in a manner in which bacteria/microbes cannot survive, making it easier to maintain a more hygienic surface, is free from solvents and isocyanates making it ideal sanitaryware product and a product for all public health institutions and clinics.
The real breakthrough that is most prevalent at such a time of spread of infections and high risk level contagious disease, is that BT1 has also been proven to resist microbes such as MRSA, E. coli and Campylobacter. This has changed the way in which clinics and hospitals will now protect their surface areas and indeed for the construction of new builds!
Hospitals such as Solihull Hospital in Birmingham, Good Hope Hospital in Sutton amongst a few other institutions are now using BT1 for facility repair and maintenance work, for creating a healthier environment.
Many factories also in food processing and handling are also now using this groundbreaking product.
BT1 from the creators of CT1.
Click Here for the BT1 Video
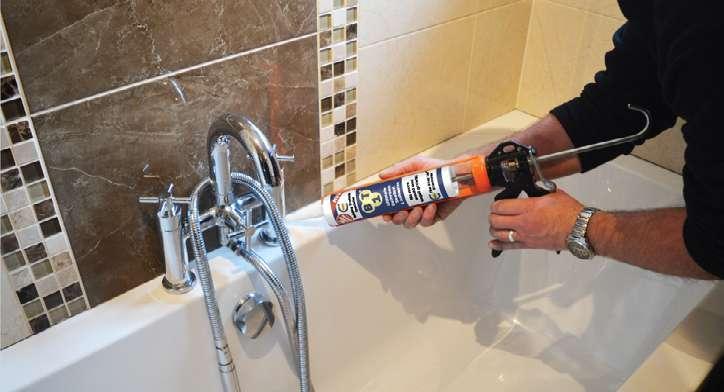
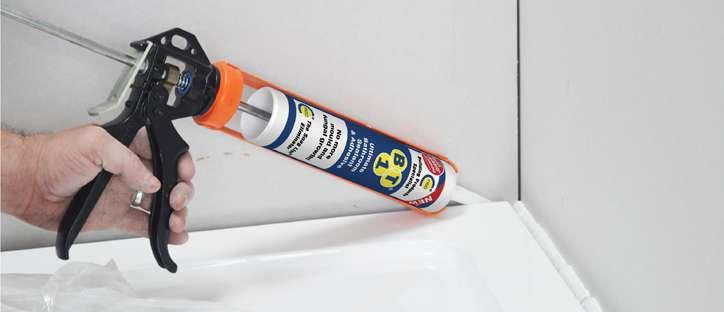
Delta Membranes
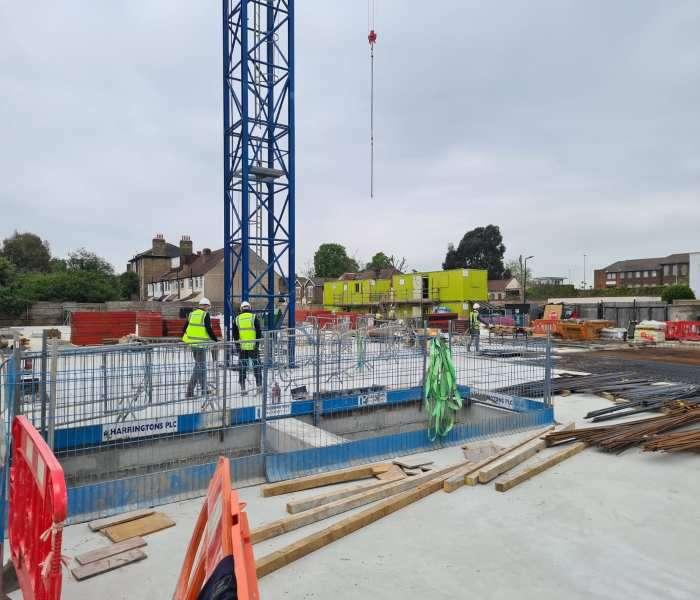
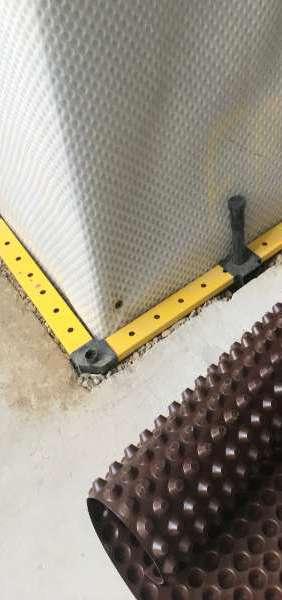
Overview
512/522 Streatham High Road is a new mixed-use development of storage and office space.
Delta’s Director David J. Symes was delighted to have been involved with this prestigious project from concept which involved a super basement with a footprint of an impressive 1500m2 (wall surface) and 2500m2 (floor surface).
Harmonix were appointed main contractor to create a five-storey structure which included a two-storey basement. Initially the area was excavated to approximately 13,700m3 using contiguous piling to form two basement levels. A new structural concrete slab was laid with three lift pits, with the piles having then been faced with a concrete lining wall.
The project required a robust and a meticulously detailed specification with Delta Registered Installers, Cemplas being appointed waterproofing contractor to guarantee a watertight basement.
The project requirement was for two forms of waterproofing which consisted of a Type B watertight concrete and Type C Cavity •54•

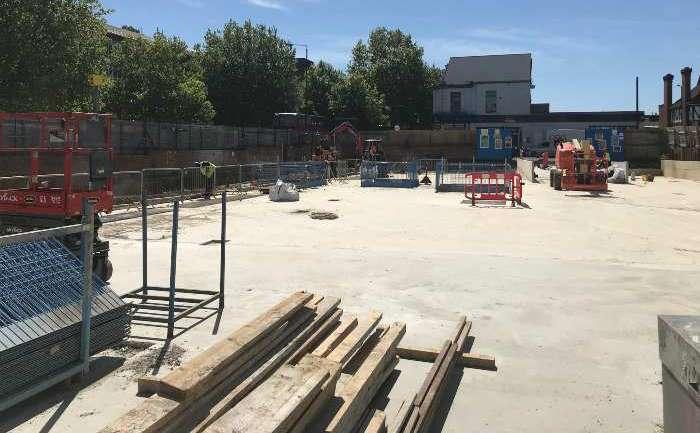
Drainage Membrane System which would meet all criteria of BS8102:2009 (Code of Practice for Protection of Below Ground Structures against Water from the Ground) and to provide a Grade 3 habitable environment.
Methodology
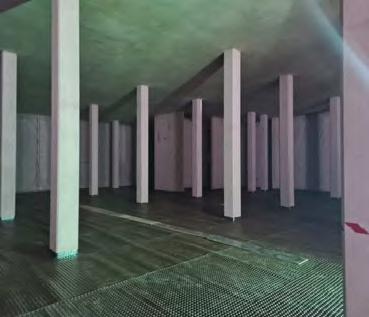
When designing a robust waterproofing solution, attention to detail is critical. The waterproofing design for any new build below ground structure should always be carried out by a CSSW (Certified Surveyor in Structural Waterproofing) or equally qualified surveyor.
When specifying a Type C cavity drainage membrane system, full consideration must be given to the drainage aspect, when installed below ground.
Prior to the installation of the Type C System, the lift pits and piling cap were encapsulated with Koster NB1 waterproof slurry. Koster NB1 active migratory crystalline slurry was applied over the capping beam and taken across the underside of the ground floor soffit to provide protection against the expectation of lateral capillary movement and down the front face of the concrete lining wall.
To reduce the risk of free lime leaching out of new concrete during the curing process, Koster Polysil TG 500 was applied to the face of the concrete lining wall.
After ensuring the structure water watertight Delta MS 500 Cavity drain membrane was installed to the walls and applied to the face of the concrete lining wall.
Cavity Drainage Systems manage water penetration, Delta drainage channel, a water collection conduit designed to control water ingress was bedded into a preformed recess/gully at the floor/ wall junction with incorporated inspection and maintenance points to comply with BS8102:2009.
Prior to the application of approx. 2500m2 of Delta MS20 membrane the basement slab was thoroughly flood tested which extended to the vertical cavity drain membrane and results recorded on the Delta/Cemplas site monitoring forms to ensure the free passage of water had unhindered access to the sumps. This is an important part of the testing where installing Type C systems and ensures that any debris behind the system is fully flushed away preventing issues in the future and designing out risk.
Locations of the sump pump units were suggested during the design phase. By incorporating sump pumps at the design stage, it allowed for project team to work together to create and share a range of project documentation with the benefit of interconnectivity which in turn created better project decisions during the correct stages of the project.
Products:
• Delta MS 20 • Delta MS 500 • Koster Polysil TG 500 • Koster NB1
Case Study Results
The project successful reflects the relationship between Delta and Cemplas. Highly accomplished project performance from concept with complete customer satisfaction. Cemplas have created a completely dry and habitable Grade 3 environment two-storey basement which fully complies with all criteria set in BS 8102:2009. It was a pleasure Cemplas and we look forward to the next project! •55•