



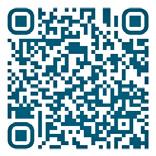
Steve Schofield, CEO at the British Pump Manufacturers’ Association, considers whether there is at last a change in attitudes towards energy efficiency amongst the general public. And if so, whether this can have a meaningful impact on decreasing the energy consumption across UK industry.
The subject of energy, or rather energy efficiency, has long been a topic of vague disinterest among the vast majority of households and billpayers. Energy, or rather the complex business sector that produces and delivers it, has historically struggled with engagement. Energy efficiency, in particular, has more often than not been misrepresented as simply a penny-saving exercise involving the change of lightbulbs for modern replacements, and switching lights off when rooms are unoccupied. Boiling the kettle less, another suggestion often heard.
However, with the huge global rise in the cost of energy, and its near constant headline coverage by the broadcast media, not to mention the financial pain we are all now enduring, perhaps 2023 has the potential to see a real change in attitudes. A change that could positively impact all aspects of energy use.
Of course, greater autonomy in our energy provision is now understood and acknowledged as a stand out
way to protect ourselves from market volatility caused by unstable regimes. But the drive for improved efficiency across all the avenues of energy use, will simply mean that the energy we do produce and secure as a country will go that much further. This will not only allow us to make big savings on our domestic bills and to ensure our homes stay warm through the winter months, it will also have a massive impact on the efficiency, and ultimately, the profitability of our commercial and industrial sectors.
The British Pump Manufacturers Association (BPMA) has been a longstanding advocate of not only the need for improved energy efficiency across the UK’s vast installed base of pumps and pump systems, but also the massive opportunity it presents for significant energy use reduction.
The operation of pumps and their associated systems accounts for around 20% of the world’s entire electrical energy consumption, and in some high-use industrial applications, this can be as much as 25-50% of the total electrical energy usage. Across
the European continent pumps are the single largest user of electricity within industry, consuming over 300 TWhpa of electricity, which in turn accounts for over 65 Mton of CO2 emissions.
Unfortunately, the vast majority of pump systems operating today were not originally designed with energy conservation as a major consideration. It is now well documented that rotodynamic pumps, which account for 80% of the installed base across Europe are between 20-30% oversized. This is usually due to an in-built ‘safety factor’ allowing for potential future uprates, or any wear in the pump or fouling of the system. But this simply means they are using far too much energy for the required duty. As such, there is huge potential to save massive amounts of energy if these pumps are properly sized, operated and maintained. In fact, if pump systems are initially designed with energy use in mind, and the pumps are optimised for efficiency, a saving up to 50% in electrical energy can be achieved.
In essence, it is important to know as much about the pump system as possible and to create a pressure/flow profile for the system, as the energy required to drive the pump is directly related to the flow and pressure required.
It is also important to carry out regularly energy audits to help determine where energy use reduction measures can be employed, and in turn how operating costs can be lowered. The government has estimated that most companies can reduce their energy consumption by 10-20%, and energy audits carried out in accordance with ISO 14414 have shown that savings of 30-50% are not unusual. By reviewing utility bills, you can get an indication of the savings to be made and the investment that you should be prepared to put into the auditing process.
Across most industrial sites, some two-thirds of the total energy consumption is used to power electric motors, an integral part of any pump system. The overall cost associated with operating these essential pieces of equipment throughout their entire life span can be broken down as follows; 5% accounts for the initial purchase/installation costs, 10% for ongoing maintenance and a massive 85% for the energy used to run them.
Clearly, any reduction in the energy consumed by electric motors is important, and with modern designs, that reduction can be as much as 30%. It is also evident that many pumps and motors are constantly
operated at full power, irrespective of process needs, something which can managed with the addition of variable speed drives, and so across Europe’s installed base there is the potential for significant energy savings; savings which can in turn drop to the bottom line and increase the profitability of any business.
Given the amount of energy consumed by pumps in their normal operation, and the potential for energy efficiency gains within pump systems, the BPMA has developed the Certified Pump System Auditor Scheme (CPSA).
Through the CPSA, pump engineers are being trained to correctly assess the efficiency of pump systems, and to provide appropriate recommendations in order to improve the efficiency of those systems. The CPSA accreditation is achieved by successfully completing a four-day residential course, followed by the satisfactory completion of a pump system audit. Only then can ‘Certified Pump System Auditor’ status be achieved.
Within the full ESOS Guidance document, the ISO/14414-Pump System Energy Assessment standard is referenced as an auditing methodology that can be accepted by “Lead Assessors” approved by the Environment Agency. Accordingly, it is hoped that CPSA accredited persons (who are trained according to the IS0 14414 standard) will be recommended
by Lead Assessors to undertake the pumping system elements of company-wide energy audits.
The next CPSA Training Course is scheduled for 9th-12th May 2023. For more detailed information, please visit http://www.bpma-cpsa.co.uk
In conclusion, it is hoped that with the heightened publicity around the cost of energy, and society’s growing appreciation of its importance to our very existence, we will begin to see far greater urgency in the adoption of energy reduction measures across our commercial and industrial sectors.
Ultimately it’s a question of choice, and whether businesses are prepared to finally address the ‘Capex vs Opex’ argument and begin to enjoy the long term financial gains available through improved operational efficiency. The offer being; pay for the new equipment now, and recoup the cost through the energy savings made over its operational life. But either way, supported by the documented evidence that significant savings can be made through the correct selection and efficient operation of pumps and their related systems, the BPMA will continue its efforts to drive this clear and important message.
Further information on the work carried out by the BPMA can be found through the websitehttps://www.bpma.org.uk/ - or for any specific enquiries, please email s.smith@bpma.org.uk
In Weidmüller, you have a trusted and reliable partner with years of experience in cable preparation, processing and systemised marking. Our THM thermal transfer printer integrates cutting and perforation tasks into the printing process; it can divide endless materials into arbitrary lengths. The result is a noticeably simpler production of custom cuts with a respective inscription assignment.
Using the Mulitmark printer, you reduce the potential sources of error with complete data consistency. You will streamline timeconsuming work processes and increase your productivity.
Weidmüller UK
Klippon House, Centurion Court Office Park Meridian Business Park, Leicester, LE19 1TP
Tel: +44 1162 823470
Fax:+44 1162 893582
www.weidmuller.co.uk
At the forefront of digital marketing, Manufactuing Update strives to bring its readers the latest in industrial manufacturing, in a format that provides the best usability and ease of use for it’s readers.
www.manufacturing-update.co.uk
Publication & Managing Director
Jodie Little 01843 595818 jodie@jetdigitalmedia.co.uk
Publishing House
March 2023
Editorial Assistant
Laura Sharpe 01843 448 443 laura@engineering-update.co.uk
Jet Digital Media Ltd, Suite 1 & 2 Spratling Court Offices, Spratling Street, Manston, Kent CT12 5AN
www.jetdigitalmedia.co.uk
Editorial Assistant Leigh Little 01843 448 443 leigh@engineering-update.co.uk E-learning
Classroom based
For more information call 0121 601 6691 scan code for the training guide or email: training@bpma.org.uk
The Manufacturing Institute (TMI) has been trusted in delivering high-quality and impactful training since 1994. Offering courses that create impactful changes to a business such as Six Sigma, Lean Manufacturing, and Team Leadership. This year has started off with a bang for TMI, receiving City & Guilds assurance for the Team Leadership Development Programme (TLDP) and the Accelerated Route to Lean Manufacturing (ARTL). These are often the gateway onto the MSc in Manufacturing Leadership, or even larger continuous improvement consultancy projects and Shingo.
The City & Guilds Assured Benchmark is a quality assurance framework, which evaluates eight areas of programme design and delivery. It is the Benchmark Standard to confirm that an organisation has met the global quality standard set by City & Guilds. Lisa Riley, Executive Director at TMI reflected, “These programmes are so enduring that customers old and new refer to them by their acronyms. In the last 12-months, both programmes have been updated and refreshed. It felt like time to get them formally ratified by one of the Nation’s most familiar educational organisations – City & Guilds.”
Joe Bell, Strategic Commercial Manager at City & Guilds said, “City & Guilds is delighted to be able to work with organisations who value good quality skills development. The Manufacturing Institute has invested in developing these programmes to achieve the City & Guilds Assured benchmarks, which now evidences that the courses meet world-class quality standards on all aspects from planning and design, to delivery and evaluation. Congratulations TMI!”.
These programmes help build a coaching culture, giving employees the opportunity of personal development, which reflects on their business. TMI understands this culture and encourages delegates to continuously develop. Upon successful completion of the Programme, delegates receive a co-branded digital credential highlighting their personal development, which includes detailed information about the learner’s skills and achievements.
For more information about Leadership and Lean training, please visit www.manufacrutinginstitute.co.uk or telephone +44 (0)161 245 4845 for a prospectus.
A Highlands-based window and conservatory business has defied the cost-of-living crisis to shatter its annual sales target, securing more than £4.5m orders in a recordbreaking year.
ERG, which employs 45 people at its Clayton Court base in Invergordon, has overcome a turbulent economic climate to paint a hugely positive picture of its own courtesy of continued investment in products and service and the adoption of new sales and marketing practices.
Headed up by Ian Joy, the company has been helping homeowners since 1974, offering the design and installation of windows, doors, replacement roofs and contemporary living spaces, such as conservatories and orangeries.
Over the years it has built up a wideranging customer base covering an aera the size of Belgium, spanning from Fort William to Inverness, and as far north as Wick.
The management team doesn’t attribute ERG’s success to a single magic bullet, but instead prefers to focus on targeted inward investment and the support of its manufacturing partner, Conservatory Outlet.
“We’ve got an incredible team at ERG and our success – in the face of some turbulent times – is testament to their talent and hard work. We’re looking ahead and we’re aiming to break the £5m mark for the first time in 2023,” commented Ian, who has been with the business for 40 years.
“You could put our growth down to the theory of marginal gains because we have made modifications to the business, and they have all combined to help us reach this target.
“Crucially, we have invested in our own practices at a time when many other companies might well have tightened their belts. The strategic decision to do this was critical in our success and was reinforced when we finished 2022 with £337,000 of sales – our best-ever December.”
Ian admitted that ERG took a ‘step back’ from its daily operations and refocused the business in the broadest manner possible.
This included further investment in digital and social media and the rollout of a unique replacement roof campaign launched in conjunction with Conservatory Outlet’s in-house marketing team.
Meanwhile, the sales process was made more personable and bespoke, with ERG’s experienced sales co-ordinator adding a personal touch via follow-up calls.
Ian added: “We refocussed the sales team to make sure they understood the importance of clearing out the ‘sales pipeline’, adding in another client call by our lead booking sales co-ordinator post appointment to ensure the meeting went well and to see if any further information was required.
“Internally, we had regular team meetings via Zoom and provided daily target updates, making sure we didn’t lose focus on the overall end-goal. We knew that if we were to break our sales record, we would need to communicate
better internally and work as one team. To have done this gives me as much satisfaction as the sales figure itself.”
ERG sources its premium products from Yorkshire-based Conservatory Outlet, and its ‘Extreme Range’ represents the perfect solution for the unpredictable Highland climate.
“ERG’s success shows just what is possible, even in these difficult trading conditions,” continued Karen Clough, Group Marketing Director at Conservatory Outlet.
She concluded: “Ian and the team have invested in their marketing output and worked with our teams to develop and execute innovative, targeted campaigns and they’re seeing the fruits of this approach in leads and sales.
“Since joining the Conservatory Outlet Network in 2018 the company has grown by 26% and we look forward to supporting ERG as it continues on its ambitious growth plans.”
For further information, please visit www.ergscotland.co.uk or www.conservatoryoutlet.co.uk
Food processing plants must balance rigorous hygiene requirements with the need to improve productivity, leaving many plant managers unsure of the best investments regarding conveyor systems. Here Enrico Visconti, Head of Industry Segment Food at hygienic conveyor belt manufacturer Habasit, shares some advice on how to improve conveyor belt sanitation in food processing applications.
Conveyor belts in food processing are key focus areas for cleaning as they are in direct contact with food products. The biggest challenge they face is cross contamination, where food products are contaminated by foreign bodies. This can either be physical contamination or microbiological contamination, caused by biofilm build-up on the line.
Biofilms typically consist of water, lipids, proteins, polysaccharides, and microorganisms and are particularly challenging for food processing sanitation operators to remove. Essentially, biofilm structures create bacterial colonies and single-cell groups that adhere to surfaces. These are preserved by a protective dome of polysaccharide meshing, making them difficult to remove and clean. Therefore, hygienic design features that prevent biofilm build-up from occurring in the first place are crucial for ongoing hygiene in food processing plants.
A critical area for modular belting is the hinges, where, if not properly cleaned, product debris might accumulate and biofilm grows. Therefore, hygienic belt design must limit the surface area of hinges and provide easy access to belting from all sides, allowing sanitation workers to inspect, clean, and validate belts quickly and effectively. Belts must also facilitate the flow of water and cleaning agents to the most hidden parts and the rods connecting the belts, so they cannot become breeding grounds for harmful bacteria.
Overcoming this challenge led to the development of Super HyCLEAN, a plastic modular belting range designed to improve cleaning efficiency and food safety. These belts have a completely flat belt surface, including on the running side, where the hinge and rod area have been minimized. The hinges have been placed on the outer sides of the belt, resulting in a flat bottom surface, significantly reducing any areas at risk of debris collection and biofilm accumulation. Furthermore, the dynamic open hinge allows water flow to reach the hinges and the rods, facilitating debris removal.
Independent third-party testing and industrial trials in the most hygienically demanding applications in poultry, fish, and red meat processing concluded that
cleaning operation time and water usage can both be reduced by over 50 per cent because they trap less debris. Further testing using UV-tracers found that, after only five rinsing cycles, there was up to 4.1 times less soil residue on Super HyCLEAN compared to other commonly used hygienic plastic modular belts. Furthermore, microbiological swab tests and CFU testing showed the belts developed 20 times fewer bacterial colonies compared to commonly used hygienic modular belts.
The next way hygiene of food processing conveyors can be improved is by using modern cleaning in place (CIP) units - spray cleaning bars fitted to conveyor frames to increase cleaning effectiveness. The functional use of CIPs is clear, they improve cleanability and reduce the time required for cleaning, therefore improving productivity. However, most food conveyor systems are not equipped with CIP units and it is often overly complicated to install them as aftermarket.
This perception is changing thanks to new plug-and-play hygienic CIP units that can be easily installed on any conveyor system. This allows industry to retrofit CIP units onto any system without requiring costly and disruptive engineering work, improving plantwide cleanability and reducing the cleaning window, improving plant productivity.
Another way to improve hygiene in food processing is by installing components that allow removal of belts from conveyor frames without using tools, such as Saniclip. This facilitates easy cleaning of conveyor frames without requiring specialist engineers, drastically cutting the time required for cleaning and improving productivity.
To find out more about how Habasit can help improve sanitation programs in food processing plants, visit www.habasit.com/ en/Industries/Food-and–Beverage
The new compact conductivity sensors LDL100 and LDL200 from ifm impress with their fast and precise media differentiation.
This helps you to control CIP processes efficiently and to increase the availability of your system. The new LDLs are also simple to commission: They are ready for use out-of-the-box and transmit the conductivity and temperature of the medium via a single M12 connection - digitally and loss-free thanks to IO-Link. As there is no additional evaluation unit required, you also save system costs. So easy, so good.
ifm – close to you!
Linear motors are ideal for fast and accurate motion in a machine.
Linmot, the leading manufacturer of cylindrical linear motors, has made them even more suitable for demanding food and pharmaceutical applications. For these environments, any mechanism needs to have a high protection class and be easy to clean and require little maintenance.
The motors have been developed to be fully sealed and are made in High grade Stainless Steel. The cylindrical design allows the motor to be completely smooth and does not require seals. There are no food or particle traps and they can be fully washed down.
This is a big advantage over screw, belt actuators or pneumatic cylinders.
The motors are available in Linear modules with protection class IP64S and stainless steel linear modules with protection class IP69 consisting of a linear guide and an integrated LinMot linear motor.
Motor series in stainless steel (EN 1.4404/ AISI 316L) for wash down applications. The motors are characterised by their hygienic design and the high motor protection class IP69 according to DIN EN 60529. Perfectly suited for «inplace» cleaning processes like CIP and SIP.
LinMot linear motors have been used in the food industry for years. They score here with industry-
specific advantages, such as simple integration, flexible programmability, dynamics and hygienic design. The motors can be connected to common control platforms in synchronous operati on or simple point-to-point motion. The advantages of servo technology enable the gentle and dynamic processing of food. With the help of stored motion profiles, frequent product changes can be achieved simply by pressing a button. LinMot linear motors are available in stainless steel with a high protection class, meaning they can be cleaned under high pressure and with caustic cleaning solutions.
Users wishing to combine the advantages of dosing based on flow measurement with those of piston dosing in a rotary filling machine now have clean design LinMot motor options. Using LinMot stainless steel motors, the stroke movement of the filling needles can be mechanically decoupled from the movement of the carousel. Even highly dynamic needle raising applications are possible.
Unlike mechanical lifting curves, electrical direct drives do not exert any destructive forces on the bearing shafts.
www.quin.co.uk/linmot
Our laser marking system mp-LM 3 is characterized by high cost efficiency as well as abrasion-resistant and durable marking. Unique features are: The laser device can mark a wide variety of different materials and is unbeatable in terms of price-performance ratio.
The interaction of hardware, software and accessories provides real added value with our laser marking system. The high degree of automation allows users to focus on their core competences and save resources. For the customer, consistent system integration ensures optimum labeling quality as well as very high efficiency and cost-effectiveness in everyday operations.
Automated batch processing and marking software integration enable high output. The magazine filling aid mp-LM B enables a smooth and time-optimized labeling process due to parallel preparation of the magazine loading. The mp-LM carrier plates are used to flexibly hold various murrSystems labeling materials. They can be stacked directly in the labeling magazine. However, separator plates can also be inserted into the magazine. These allow mixed loading in one order. With the help of the mp-LM single-line adapters, individual lines of the plastic labels that have not yet been marked can be further processed in the laser marking device. No single lines remain.
The UniversalMarking software used with the mp-LM 3 can also operate other labeling technologies or devices: device-independent and process-optimized, time- and cost-saving, as well as intuitive and interactive.
The mp-LM 3 with high output requires no consumables. It is nearly service-free with low maintenance requirements.
Various materials in different thicknesses, shapes and colors for different applications can be labeled.
Permanent marketing
Because the lettering is extremely abrasionresistant and UV-resistant, it is durable and long-lasting.
Very good price-performance ratio
Our laser marking device impresses with low operating costs, high productivity and marking speed (up to 10,000 labels/hour).
The world of robotics grows ever larger and more diverse as the capability and flexibility of the technology advances, opening up new areas of application. The use of robots within manufacturing industry is well established and very much taken for granted, and it is not uncommon to find robots being used within the medical device and pharmaceutical sectors. However, robotics has now reached the stage where they are not only manufacturing the medicines we rely upon, they are now also now finding their way into the operating theatre, playing a crucial role in assisting surgeons with medical interventions. This article by Stäubli’s Simon Jenkins takes a look at the latest developments and advances in the company’s medical robots.
Stäubli Robotics has for many years, continued to develop robots for life science applications, and today the company’s robots are recognised as setting the benchmark for hygiene and safety. Whenever accuracy is a requirement, together with factors such as low particle emissions, and easyclean surfaces, Stäubli has long led the way in these areas.
Simon Jenkins explains: “Stäubli has developed a unique solution that meets a number of the constraints present in patient care. Just as in our industrial
focused solutions, the medical range of robots have been specially adapted to make them the perfect partner in patient care, addressing the specific demands within these high compliance and complex applications, whilst ensuring consistent performance, safety, and reliability.
Today, Stäubli robots help to relieve doctors of some of the strain they are under whilst performing operations that demand their full concentration. Our robots are also contributing to the development of innovative surgical techniques.”
For robots to interact with surgeons in the operating theatre, and perform the tasks demanded of them, they need to operate at the highest levels of safety. Robots within an Operating Theatre are effectively working in a collaborative manner alongside the Surgeon and other medical staff.
Stäubli robots use a unique set of modular SIL3-PLe safety functions including safe stop, safe speed, safe zone, etc. The latest TX2/CS9 systems are designed for collaborative applications with the highest levels of safety. In addition, reliable stopping and braking performance is ensured by a system embedded brake test.
Medical and patient care applications also require the highest levels of cleanliness and the company’s TX2 range of robots have a smooth, white, high-quality finish with sector specific surface preparation. This means that they are capable of meeting ISO Class 2 cleanroom standards, which demands fewer than 11 particles greater than 0.3 microns and no particles greater than 1.0 microns per cubic metre. The Stericlean range of H₂O₂ compliant robots also offer protection up to IP67 level.
Stäubli has been a key player in a series of collaborations and partnerships in recent years which has seen the company’s robots working alongside Doctors and Surgeons in a number of ways.
Based in San Sebastian, Spain, Cyber Surgery has developed a robotic system for spinal procedures. The solution guides the surgeon, making the procedure safer, more accurate and minimally invasive. The three main benefits of this system are: a reduction in reinterventions due to the levels of accuracy provided by the robot, postoperative time in hospital is shortened because the surgery is performed in a minimally invasive way producing less damage to soft tissues and subsequent bleeding, and reduced X-ray exposure thanks to the fact that the robot provides a guide for the surgeon.
The RoboticScope, developed in 2016 by BHS Technologies GmbH in Innsbruck comprises of a high-precision robot, a high-resolution 3D camera, and an innovative head-mounted display.
Using this technology, the surgeon looks directly into the operating field via a Head-Mounted-Display (HMD). The two digital micro-displays integrated within the HMD directly in front of the surgeon’s eyes, show high-resolution, real-time 3D images relayed by the dual camera lenses mounted on the robot head.
The position of the robot determines the visible image, allowing the surgeon to operate in a freely selectable and completely relaxed head position. The surgeon retains control over the exact image field and viewing angle, automatically steering the robot with contact-free head movements. Using this method, the surgeon can select the viewing angle of the 8x zoom lenses and even control a sophisticated menu from a micro-display, allowing the activation and control of further functions. Some 500 surgeons around the world have now used the RoboticScope, and the device is so intuitive that more than 90 percent of users master it after just ten minutes.
The robot technology behind the RoboticScope is a high-precision Stäubli TX2-60L robot which delivers the precise and jerk-free motion
(Stäubli robots help to relieve doctors of some of the strain they are under whilst performing operations that demand their full concentration.)
sequences of the RoboticScope. As with the entire range of the latest 6-axis robots, the enclosed structure allows for a protection class of IP65, with the wrist being IP67 compliant. With cleanroom class ISO 5 as a standard, the robot allows BHS to also save on the potential extra costs of upgrading to a cleanroom version.
Simon Jenkins concludes: “Stäubli’s unique robot portfolio, combined with decades of industry experience, and a strong customer focus make it a valued partner for many renowned life science companies around the globe. The examples illustrated in this article are but a few of the areas where our robots are making a valuable contribution to interactive patient care.”
Stäubli (UK) Limited
Hadley Park East
Hadley
Telford
TF1 6QJ
Email: robot.uk@staubli.com
Telephone: +44 (0)1952 671917
Web: www.staubli.com
Titan Enterprises is inviting visitors to explore their dynamic new website. Designed for the evolving scientific, engineering and measurement marketplace, Titan’s new enriched content-led website gives the visitor a step-up in user experience. This next generation website has improved navigation and functionality at its core while allowing visitors to explore the full liquid flow measurement product portfolio Titan offers.
Created to give a user-friendly experience, the site includes many new features to enable visitors to easily navigate their way around the site, find the flow measurement products applicable to their application or process, and discover rich technicalbased content.
The dynamic design and new features include:
• Flow Meter Product and Application filters that allow users to narrow down the product portfolio by selecting flow meter operational attributes
• Quote Requests are now easily processed online through a new ‘cart’ functionality.
• Concise product pages provide the user with easy access to the technical information and option to request a quote for specific flowmeter model types.
• Rapid Response Functionality allows the site to be compatible with all browsers and mobile devices.
• Site-wide Search tool helps users find information relating to a flow measurement device or technical aspect of interest.
Samantha Hannay, Titan’s Marketing Manager says: “The enhanced media pages give users a richer online content with press releases, case studies and technical papers.”
Samantha continues: “Valuable content is also contained in the " Guides and Tools " pages so the user is never far away from useful and pertinent information, particularly in regards to the installation of their selected flow meter device.”
Visitors to Titan’s new website can stay informed with the latest flowmeter technology and industry news by signing up to their fLowdown e-newsletter.
For further information on flow measurement devices to suit specific applications, please contact Titan Enterprises on +44 (0)1935 812790 or sales@flowmeters.co.uk
Is the photographer’s knowledge of your industry important?
“Carter Manufacturing is a global supplier of precision bearings and tooling to aerospace, medical, nuclear and defence. We require exceptional images to support our business and make it stand out across all the markets in which we are active. Having used various photographers in the past, we have a good idea of what we need in a photographer to achieve our desired images. Experience in all the sectors in which we are involved is not realistic but having knowledge of some plus the ability to adapt those to
Industrial photographer, Adrian Waine, is no stranger to the pages of Manufacturing Update. His imagery ranks amongst the best we feature. In this article we get a new perspective on what it takes to create stunning images in challenging environments – Mel Meader, Chief Operating Officer, of Carter Manufacturing, explains in this interview with editor Taylor Owens how Adrian provides the creative spark for their pictures.
What references do you seek before hiring a photographer?
“We discovered Adrian Waine through his images being credited in an associates website. For us, the work speaks for itself and having found these images we started to dig a little deeper. Once satisfied with the imagery, we set about talking with Adrian informally to get a feel for him and how he approaches each commission. His wider industry expertise and experience quickly shone through and gave us the confidence we were seeking.”
Does the photographer’s equipment or lack of it have any consequences?
“The right equipment is necessary, especially lighting. We strive to create original images to capture the imagination of our target audience. Ambient light alone is very limiting in this respect. With the equipment must come knowledge in how to use it for maximum creative effect. We discuss a shot list in advance which defines who needs to obtain what. Adrian supplies all photography and lighting equipment required to capture a shot. He also brings a time-served assistant with him and suggests must-haves in terms of relevant props. This makes the photography process much easier on the day as everything is to hand when needed.”
When the photographs are completed do you feel that the investment in time and money are worthy of the results?
“Without a doubt. We have had several uses from the imagery and expect more. They are being used in our website and have been used in exhibition stands, within our social media and marketing campaigns. The key to getting the most out of the time hinges on the advance preparation. The magical creative flair, if you like, is left to Adrian.”
Is organising a photographic shoot in a working factory disruptive?
“I know it sounds repetitive, but again preparation is key when commissioning a professional photographer like Adrian. Disruption is often minimal when you append time building a shot list, prop portfolio and select the people involved in advance. Adrian adapts where he can and will always adjust or generate an additional shot outside of the plan if he can and so maximise the useable shots taken on the day.”
Modern cameras and high-end phone cameras, pack a lot of punch these days, are you not tempted to try taking your own pictures?
“You cannot capture the images of this quality using a phone or personal camera. Attention to detail comes from experience and Adrian’s speaks for itself. Lighting, camera angles and feel cannot be re-created without using a time served photographer. Owning an oil painting set doesn’t make you an artist! Working at the forefront of emerging technologies you need to create the right feel when drawing in customers. Adrian achieves this well and we believe that it is well received by our customers, ‘a homemade shot’ will not do.”
Is building a long-term relationship with a photography important?
We began working with Adrian in 2020, and have already completed three shoots with him, with more in the pipeline. Adrian seems to keep well on top of trends. We see our future relationship with Adrian being a constant to keep our imagery fresh, current and eye-catching in an ever changing world.
Does photography help the business attract new talent?
Carter Manufacturing is a pioneering company and to inspire and attract a new generation of engineers to propel
our industry forward we need to show our workplaces for the centres of technological excellence that they are. Adrian’s images come together to tell that story.
www.carterbearings.co.uk
Mel Meader, Chief Operating Officer, Carter Manufacturing Limited
+44 1865 821 720
Mob 07859 879040
mel@carterbearings.co.uk
www.photographyforindustry.com
Photography : Adrian Waine
Tel 0151 356 3855
adrian@photographyforindustry.com
Adrian was formerly staff photographer with Saudi ARAMCO and was regularly commissioned within the oil processing facilities of Saudi Arabia.
ProSolv®5408e is a high-performance solvent cleaner used for sustainable and future proof vapour degreasing. Soft on the environment and safe for users, it offers improved cleaning at lower costs. Low boiling point, economical with energy with low solvent losses and faster production.
Vapour degreasing, with or with-out ultrasonics, is the oldest, simplest and most effective solvent degreasing and metal cleaning process used today. It has, until recently, been subject to little change since it was first invented in the early part of the last century. In the UK, Europe, United States and other advanced industrialized economies increasingly stringent legislation to control emissions of VOCs, Solvents with a high Global Warming Potential (GWP), or a high Ozone Depletion Potential (ODP), and those compounds associated with human health concerns has led to Envirotech Europe manufacturing new formulations for precision cleaning solvents with low or near zero potential.
Halogenated hydrocarbons are the solvents of choice for vapour degreasing and cleaning. The process is essentially simple. A tank with a sump to contain the solvent, heaters at the base and condensation coils around the top section to control the height of the vapour is all that is needed. When heated in the sump halogenated solvents produce, in most cases, a saturated vapour between 3 and 4 times heavier than air at a temperature greater than the ambient temperature of the parts to be cleaned.
This allows the solvent vapour to condense on the surface of the parts. The condensate dissolves the contaminants such as oil, greases, flux, and soils returning the used solvent into the sump of the machine for recycling into vapour which continuously condenses onto the parts until they have achieved vapour temperature when, with no further condensation, the process is complete. Parts removed from the cleaning machines are very clean, warm and dry.
The most common halogenated solvents, in use for commercial purposes, are non-flammable so present no risk in this process. Perchloroethylene, used mainly for dry cleaning, methylene chloride previously used widely in paint strippers, 1,1,1- trichloroethane and trichloroethylene used for vapour degreasing were the original materials used based on chlorine chemistry. However continuing concern about the environmental impact and danger to operators by exposure to chlorine-based solvents, especially trichloroethylene, has led to a continuing search for safer alternatives, such as ProSolv®5408e, a trans-1,2-Dichloroethylene based solvent mixture that is non-flammable.
The ProSolv®5408e vapour degreasing process gives the highest levels of economical cleaning with minimum energy
usage, low footprint on the factory floor, safety for the operator, and high production rates with low solvent usage or environmental impact.
With the new generation of sealed cleaning machines the future of vapour degreasing as the process of choice is assured.
Please visit our website for information about other uses and applications for ProSolv®5408e
For more advice, please telephone us on +44 (0) 20 8281 6370 or use our website contact form
All products are supplied and supported by EnviroTech Europe Ltd. Manufactured in the United Kingdom and available on short delivery times through our dedicated team of distributors worldwide.
Video animation of Solvac hermetically sealed equipment by kind permission of CC Hydrosonics Ltd.
Supplied and supported by
www.envirotech-europe.com
OAL is proud to announce its latest project with Worldwide Fruit to stop packaging errors with artificial intelligence and automation. Worldwide Fruit has scaled and improved its quality control processes, resulting in happier customers and reduced operational risk. Automation has helped find and prevent “hard-to-spot errors” whilst reducing the time it takes to complete quality control checks. They have also removed substantial paperwork from the business helping meet and surpass sustainability goals.
Previously manual human checks of product labels, date code and country of origin were undertaken, but these methods are susceptible to human error, especially in a high-complexity business like Worldwide Fruit. Their complex operations handle thousands of different product, grower, and packaging combinations. For one category like apples, there are many varieties of apples from different countries with different packaging and promotion requirements from each retailer.
For a production run, Worldwide Fruit must ensure the right product (apple), is in the right packaging with the right date code and country of origin. Any mistake in the process could result in a product recall and a fine from retailers. To address these challenges Worldwide Fruit turned to automation.
After a review of suppliers, Worldwide Fruit chose to work with OAL because of recommendations and previous experience implementing the OAL system. Furthermore, they wanted to work with a business that could integrate with their existing ERP system, which OAL could demonstrate.
The priority was implementing an “online” label and verification system across its packaging lines to accelerate its digital transformation. Online meaning, every product is verified as opposed to “offline” where a sample is verified.
Fran McNally, Quality Manager at Worldwide Fruit described the project: “The team at OAL are easy to work with, working together we have implemented a robust automated label and date code verification system. By introducing cutting edge artificial intelligence technology
we’ve futureproofed our packaging lines, enabling further automation. Crucially we’ve been able to customise the system to meet our unique requirements. The 247 support is quick, friendly, and efficient!”
The OAL solution has a number of elements to automate the process. A digital master product database was created containing all critical SKU information. OAL Line Terminals were installed on every line for operators to start and finish jobs and conduct quality checks related to the job. This includes online cameras to scan and verify packaging to ensure the right packaging is applied to the product. Each online printer was connected to the OAL system. The OAL system controls the printer and tells it the date code to print based on the date code rules in the master product database.The offline print room printers were also under the control of the OAL system to ensure offline printed labels were also correct.
Finally, the site chose to add an extra layer of assurance with APRIL Eye date code verification. APRIL Eye gives the OAL system the functionality to read back and verify printed date codes in an image. This ensures the right date code is applied, it’s legible and in the right location.
At Worldwide Fruit, as part of start-up, interval and end-of-run checks the operator takes a picture of a finished pack with the OAL line terminal hand scanner. The system checks it’s correct and legible against the current job.
Finally, every check, scan and data point is recorded providing a complete digital audit trail to ensure BRC and retailer code of practice compliance.
As engineering managers come under pressure to meet demanding schedules, often with fewer skilled hands and tighter budgets, the benefits of professional tool storage and management become stronger than ever.
Snap-on Industrial’s Level 5™ automated total asset management system brings order to any workplace, enabling engineers and technicians to know exactly where to find every tool they need, when they need it, saving time and easing stress.
How useful would it be if all valuable tools could be tracked from one central point? Snap-on’s Level 5™ system makes that possible. It provides complete reports on everything
managers or supervisors need to keep an eye on.
And then there’s FOD. The threat of foreign object damage is a real and present danger in many engineering workplaces. Using Snap-on Level 5™ minimises the risk of human error, as automated tool control constantly tracks every tool and detects which tools have been removed or returned, ensuring greater protection against FOD.
Engineered to track individual tools by user, without bar codes, scanners, RFID tags or other add-ons, the system works at the speed its users demand. Other systems require additional steps to scan or log activity. The Snapon system does this automatically so users save time and don’t have to depend on other steps to ensure accurate results.
Snap-on’s Level 5™ ATC boxes are network ready, using either Ethernet or wireless connection. That enables users to review activity at all Level 5 boxes in their location from one central computer, avoiding the time consuming need to inspect each box.
Major benefits of the system include:
• No individual tool scanning required;
• No RFID tags to install or replace;
• No limitations on tool size: from ¼” screwdriver bit upwards;
• Intuitive interface, with an easy to use touchscreen
• Audible voice announcement of tool removal and replacement
• Automatic locking for maximum security
• Errors announced and displayed to indicate incorrect tool position or advise when a drawer is not closed.
Says Richard Packham, Director UK & Europe for Snap-on Industrial: “Snapon’s automated system takes asset management to an entirely new level. The ability to monitor several boxes from one central computer offers a huge advantage to engineering managers.”
For technical details visit: www.snaponlevel5.com call (01536) 413904 or e-mail: ukindustrialmarketing@snapon.com
MPW Precision reached a six-month traceability goal in just four weeks, earning the ISO 9001 without a single non-conformance.
MPW Precision was founded in December 2020 by father and son entrepreneurs Maurice and Paul Watson, who between them have over 60 years of combined experience in precision manufacturing. The company specialises in producing high-precision quality engineered components for use in larger fabrications and power generation.
With years of previous experience leading a manufacturing company, Paul knew that complex manufacturing needs a capable MRP system for efficient and well-organised operation.
Since all of MPW Precision’s clients require ISO 9001 and other quality assurance certifications, an important functionality that Paul required was end-to-end traceability. Being located over three manufacturing sites and two home offices, it was also important that the software be web-based and able to run on off-the-shelf PCs and tablets. A final determining factor was affordability.
After trialling several MRP systems, Paul demoed MRPeasy and felt it ticked all the boxes and seemed easy not just in name but also for day-to-day use and crucially – to implement.
Having prior experience with implementing manufacturing software, Paul decided to go at it himself. “I had a target to install MRPeasy and become ISO 9001 approved within 6 months,” he says. Using the wealth of resources on MRPeasy’s website he got the system up and running in just about 4 weeks.
“After 6 months of using MRPeasy, SGS (an industry-leading certification company) came in to undertake the certification audit and we passed without a single non-conformance. On the report, SGS also commented on how good MRPeasy was with traceability”, Paul explained.
Since MPW Precision opted for a day-one implementation, there were no metrics on how MRPeasy affected efficiency after going live. However, comparing with the MRP solution that Paul and Maurice had previously used, Priority Software, they can now do things like taking an order and getting it to the shopfloor in around 25% of the time. “There was approval and other stages involved and we had 40 employees instead of 8 but all-in-all, it’s around 70% more efficient.” says Watson.
Today, MPW Precision uses MRPeasy for pretty much everything, except for some ISO-specific QC processes, and benefits from having business-critical information all in one place and accessible from the shop floor, office, or any internet-enabled external location. The owners have also been praised by their customers for the speed at which the system makes documentation available to them. Meanwhile, the seamless QuickBooks integration ensures the accounts are well taken care of.
MRPeasy is a cloud-based ERP/MRP system for small manufacturers and distributors. For more information and a free trial, visit www.mrpeasy.com