
13 minute read
The Evolution of Cooperatives
Cooperatives remain a vital link in Iowa farmer’s supply chain
BY KRISS NELSON
In Iowa, cooperatives are a vital part of the agricultural landscape.
“Cooperatives were created to provide services and competitive pricing to the people that would benefit from that — their farmer members,” says Dave Holm, executive director of the Iowa Institute of Cooperatives. “That has not changed despite the evolution in the agricultural industry.”
Iowa Institute of Cooperatives: Guiding state cooperatives since 1951
The Iowa Institute of Cooperatives was organized in 1951 and operates under their mission of “enhancing member cooperative’s success.”
According to Holm, the institute helps its 155 members, comprising grain, electrical and credit union cooperatives through legislative lobbying and educational programming.
There are three cooperative statutes in Iowa that the Iowa Institute of Cooperatives works to ensure are up-to-date:
• Chapter 499: This chapter covers agricultural and utility cooperatives
• Chapter 501: This law provides the structure for “closed,” or “new generation” cooperatives owned by farmers
• Chapter 501a: This statute hybrid model allows outside investment into cooperatives
Protecting the Grain Indemnity Fund was a key priority for the Iowa Institute of Cooperatives during the 2024 legislative session, and this emphasis will persist in 2025, Holm says.
Educational programs are geared toward cooperative board members and staff, and they include business and leadership development.
Farmers Co-op Ottosen: ‘Small but mighty’
Farmers Co-op Elevator in Ottosen formed in 1920 and has remained a single location for 124 years.
Jess Welter, an Ottosen farmer, serves as secretary on the board of directors for Farmers Co-op in Ottosen.
He describes the co-op as “small and mighty” and credits the loyalty from their patron and customer base and employees’ dedication as the driver behind the success.
“People have always told us that bigger is better, that we need to expand or that we should be bought out to survive and have more buying power, but that is not the case,” Welter says. He’s served on the elevator’s board since 2005.
“Ottosen elevator is my preferred choice not only because of its proximity to where I live but also because I prefer the personal touch, as the cooperative has managed to run a successful business without needing multiple elevator locations,” Welter says.
It’s the personal touch that’s been the mainstay for 124 years, says Kevin Walker, the co-op's general manager of Farmers Co-op Ottosen.
“We have a very loyal customer base that wants to do business with us because we have close relationships, and they know the people they are dealing with,” says Walker. “We have a long-tenured group of employees with low turnover. Also, we operate with an open-door policy; a customer can come in and speak to me without an appointment, and I know them, and they know me.”
In addition to operating a propane location in Algona, Walker emphasizes their commitment to identifying profitable niche markets for their company. This includes a handling agreement with Scoular, in which they load railcars with organic corn bound for the West Coast.
“Some of our competitors do not want to enter into some things we do because they (the niche markets) are not large enough to do so profitably,” says Walker.
For the past 15 years, Farmers Co-op Ottosen has been working to replace all the company’s fuel delivery trucks and custom application equipment with the latest technology. They are also upgrading their grain receiving facility.
Since 2010, Farmers Co-op Ottosen has constructed a new corn dryer, added
1.5 million bushels of new grain storage and increased their grain receiving capacity to 42,000 bushels per hour. Upgrades also include a new liquid fertilizer and chemical complex along with a 9,000-ton dry fertilizer plant.
Walker assures farmers that the Ottosen elevator will be available to assist them in challenging times.
“We will continue to offer our customers the personalized service they expect,” says Walker. “Along with providing our goods and services at the lowest cost we can, and paying the most we can for their grain and returning dividends to them.”
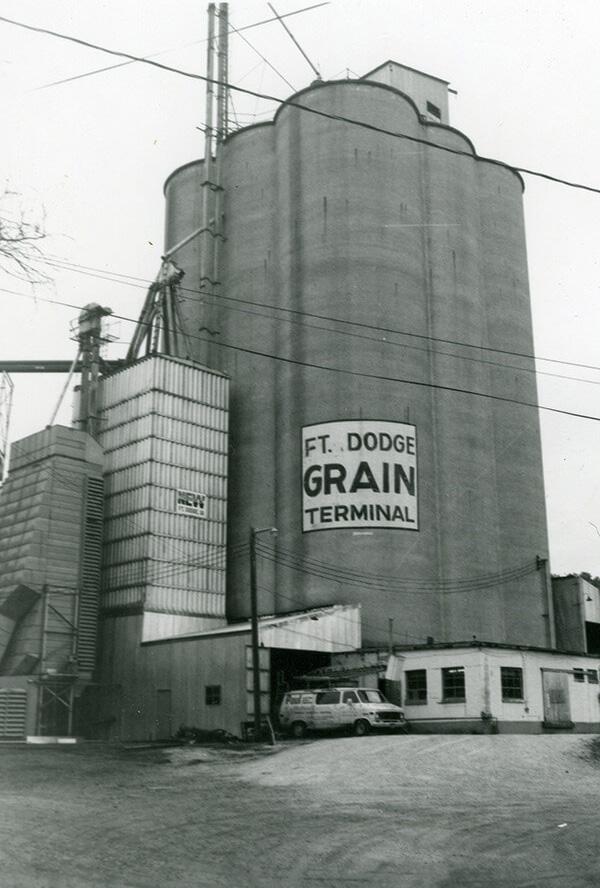
A look into the cooperative movement's history
As farming became more mechanized and markets expanded, Iowa farmers began organizing cooperatives to reduce their dependencies on middlemen and secure better prices for their products.
Farmers with rail access constructed elevators in the mid- to late 1800s and eventually formed stock companies. These facilities were first built for the purpose of importing coal and lumber, and exporting livestock. These locations often included a grain elevator, marking the start of the grain industry.
Soon, farmers began feeling they were being taken advantage of, Holm says, and in 1922, the federal government passed the Capper-Volstead Act to give farmers the same right to bargain collectively as corporations without violating anti-trust laws.
This spurred the cooperative growth in Iowa.
“A private investor would not have the amount of infrastructure cooperatives have built in this state,” says Holm. “The modernized grain facilities, rail access, agricultural inputs; none of that would be here if it was not for the cooperative system.”
There were 710 cooperatives in Iowa by the late 1940s. Currently, Iowa is home to 42 grain cooperatives.
While the cooperative model continues to evolve, the connections between cooperatives and their members remain unchanged, Holm says.
“Cooperatives have a relationship with their members which is often generational and they want their members to succeed,” he says. “That is the reason cooperatives exist.”
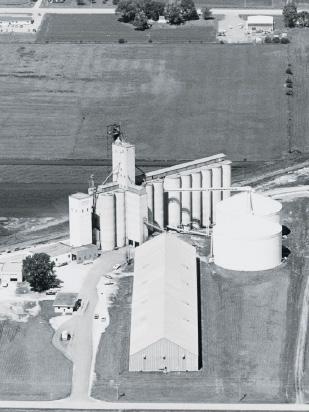
Landus: Focused on innovation
What began in 1888, with its earliest roots at Farmers Elevator and Livestock Company in Jordan, Landus now serves more than 5,500 farmers across 34 states and 16 countries.
“Over the years, dozens of elevators, grain companies, feed mills and suppliers, agronomy facilities and even a hardware store and energy company have merged, changed hands and banded together to remain relevant and strong in the global marketplace,” says Matt Carstens, president & CEO of Landus and Conduit. “At Landus, we support every link in the food chain, from seed to commodity, from product to feed and from cow to the kitchen table.”
Regardless of size, Carstens says Landus is committed to keeping the farmer at the center of everything.
“Everyone at Landus, including myself, are constantly listening to what matters most to farmers. Whether it be access to affordable healthcare, reliable logistics, competitive pricing or innovative solutions that can make their jobs easier and more efficient,” he says. Landus is dedicated to innovation and actively seeks new and creative solutions for the benefit of its farmers, he says.
Cooperatives were formed to help create value for their members. The initial focus was on grain shipping, sales, bulk pricing and chemicals.
“Today, we work to provide value in any way possible,” Carstens says. “From grain sales and chemicals to drones and the power of data to healthcare and e-commerce, we must keep the farmer at the center of everything we do. And that means we have to adjust to their needs and the problems they need help solving.”
An example of these innovations includes Landus Health and Conduit Health coverage; Landus Advantage, a new freight brokering division; Landus Energy, providing Landus farmers more efficient and cost effective ways to get fuel, gasoline and eventually adding propane, lubricants, DEF and other related products to fuel their operations; Conduit, a first-of-its-kind company that combines the best elements of a farmer owned cooperative and a technology company and AcreEdge, a lineup of agronomy products created by Landus agronomists and scientists.
The cooperative, in partnership with Talus Renewables, recently began producing green ammonia using renewable energy to remove hydrocarbons from traditional anhydrous ammonia manufacturing processes. Talus Renewables will soon be in operation for the fall fertilizer season.
“This innovative processing makes farming more sustainable, economical and efficient,” says Carstens. “Utilizing existing equipment and methods, farmers will alter the carbon intensity score of their operations by switching to green ammonia.”
Carstens realizes if their farmers do not succeed, the cooperative does not succeed.
“Those are words we live by at Landus,” he says. “No matter what economic uncertainties lay ahead, we will listen to our farmers and work alongside them as we face it together. At the end of the day, we would not be where we are today without the hard work and dedication from our 5,500plus farmers across the nation.”
NEW Cooperative: 51 years of serving their members
Fifty years ago, the idea of two local cooperatives merging was fresh. In 1973, a local cooperative with a 50-rail car capacity and another local cooperative with excess grain to market turned this idea into a reality. This venture was the beginning of NEW Cooperative. For more than 50 years, NEW Cooperative has stayed committed to farmers while being driven by its more than 12,000 members across 82 communities.
NEW Cooperative’s goal has since remained the same while evolving to ensure its customers and members have access to a sustainable rail market and markets beyond the rail.
“Since 1973, NEW Cooperative’s purpose has never wavered,” says Dan Dix, general manager of NEW Cooperative. “As times change, so do the needs of farmers. NEW Cooperative is devoted to evolving with them by providing the solutions they need in grain, agronomy, precision agriculture, energy and feed. By using leadingedge technologies and resources, we will continue to make their operations efficient and profitable.”
For NEW Cooperative, efficiency is a top priority when working toward strategically improving facilities so they can best serve members today and in the future, Dix says. Demand for additional agronomy and grain services in the Churdan area has yielded in the construction of two buildings, which will hold 1.25 million bushels of soybeans and 2.75 million bushels of corn. Increased grain receipts and demand for agricultural services have led to other construction projects in Belmond, Clearfield, Humeston and Osceola.
NEW Cooperative expanded its feed division by building the Pomeroy feed mill in 2017. Since then, NEW Cooperative built feed mills in Rowan and Cooper.
“It has been an exciting time of growth and opportunity for NEW Cooperative,” says Dix. “In the last ten years, NEW Cooperative has added 50 locations while also doubling in size over the last three years. While undergoing these changes, NEW Cooperative relied on its core principles and mission, which it has always followed: to serve its members.”
NEW Cooperative is known as one of the first Iowa ag retailers to offer variable-rate fertilizer applications and continues to offer precision ag, data management and precision hardware services through their SOILMAP software.
“Helping our members get the most out of their crop input dollars is another principle that has never wavered,” says Dix. “Our agronomists and precision ag team are vital partners of our member’s operations. Reviewing crop input plans and assisting members in managing their farm’s data are just a few of the ways they help to maximize customer’s potential.”
Besides their grain and agronomy services, NEW Cooperative’s energy department has recently expanded. While previously meeting their member’s energy needs in northwest, north central, western and southern areas of the state, NEW Cooperative is now delivering their expanded propane and refined fuel energy services in Wright and Pocahontas Counties while establishing new services in Hamilton, Webster, Humboldt, Calhoun and Greene Counties.
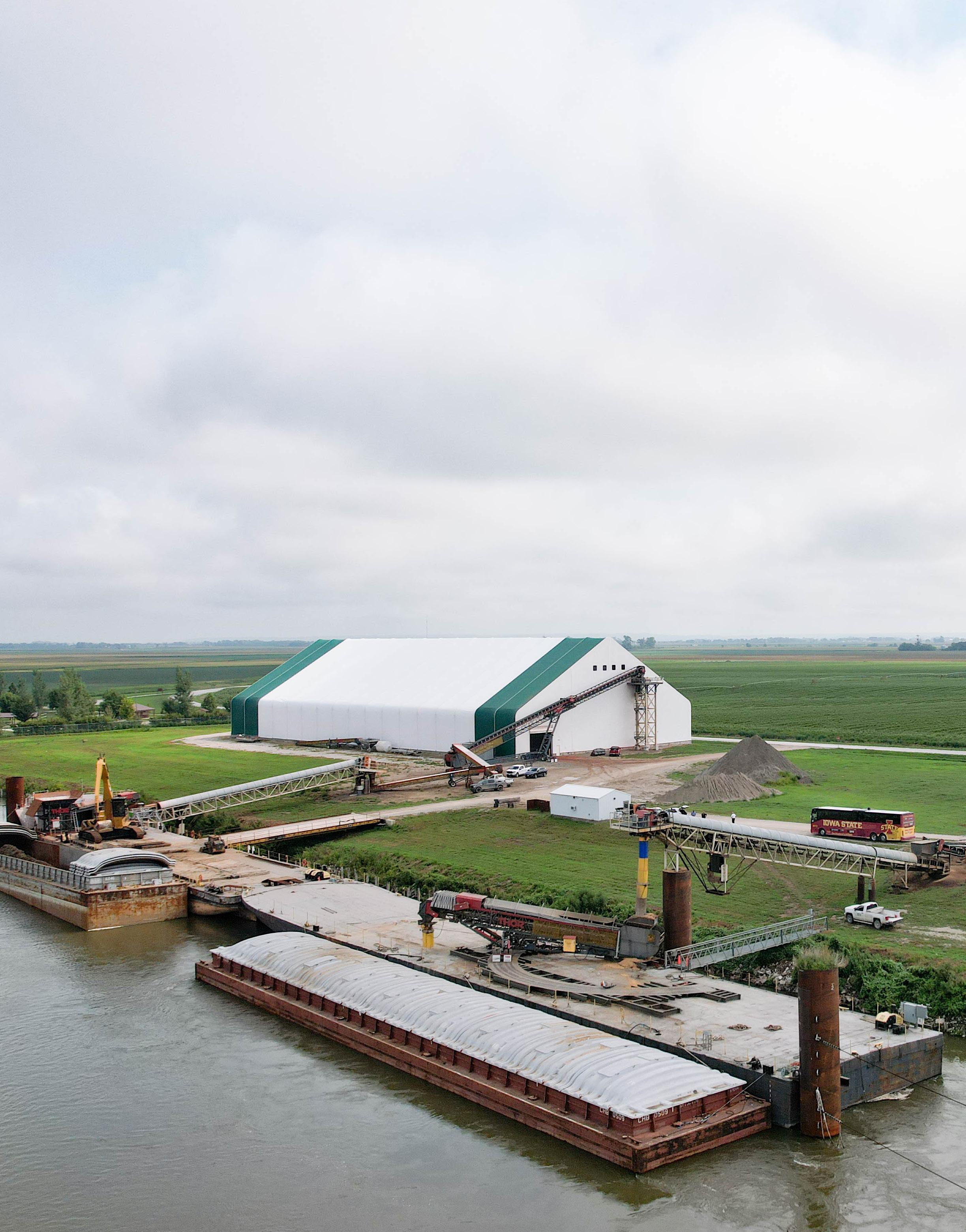
Port of Blencoe
Dubbed as a “gateway to the world market,” NEW Cooperative’s Port of Blencoe site is the cooperative’s only barge loading and unloading facility. Located halfway between Council Bluffs and Sioux City, the Port of Blencoe is the farthest stop north on the Missouri River and shifts high-volume freight from the road to the waterway.
The spring of 2021 marked the beginning of grain and fertilizer transportation to and from the port.
From an agronomy viewpoint, the Port of Blencoe puts NEW Cooperative in line to tap worldwide product availability and more attractive prices. In terms of grain marketing, farmers’ commodities can link to new destinations for increased market value.
The fertilizer storage building at the Port of Blencoe stores fertilizer for both wholesale and retail distribution and can hold 20,000 tons of product.
Besides fertilizer, the Port of Blencoe ships a variety of products including soybeans, soybean meal, corn and distillers dried grains.
AGP: Improving market opportunities for farmers
More than 40 years ago, Ag Processing Inc. (AGP) began with a focus on processing soybeans and has grown to be the world’s largest farmerowned soybean processor and leading supplier of soybean meal and refined vegetable oils.
Currently, AGP has 10 soybean crush plants in Iowa, Minnesota, Missouri, Nebraska and South Dakota; four soybean oil refineries and three biodiesel production facilities.
They also have a footprint in the Pacific Northwest with an export terminal used to market soybean meal to overseas customers.
What is unique about AGP is that it is a federated cooperative owned by approximately 150 local and regional farmer-owned cooperatives. AGP’s cooperative stockholders represent approximately 250,000 farmers through their membership.
More than 90% of the soybeans processed at AGP are from cooperative member-owners who purchase soybeans from their farmer-owners.
“AGP adds value to their soybeans by processing them into soybean meal, soybean oil and a variety of coproducts,” says Chris Schaffer, AGP’s CEO. “Unlike most of our competitors, as a cooperative, AGP’s earnings stay local. Profits are returned to our members, their farmer-owners and the communities we operate in.”
With renewable diesel (RD) production significantly increasing demand for soybean oil, AGP is seeing the need to crush more soybeans to meet the feedstock needs of the RD industry.
With predictions of the domestic soybean crush industry to increase production capacity by nearly 30%, this could mean more demand for U.S. soybeans — particularly in AGP’s trade territory.
To help meet this demand, AGP is constructing its 11th soybean crush facility located in David City, Nebraska, scheduled to become operational in 2025.
The company is also adding a second export terminal in the Pacific Northwest that will double their export capacity to benefit their current and future overseas customers and improve their ability to compete for business in the Pacific Rim.
Besides new facilities, AGP aims to re-invest in their current facilities. Currently, the company has plans to spend over a billion dollars on improvements within the next three years.
“Some of our plants have been in operation for over 40 years, but the company has always prioritized repairing, maintaining and upgrading all the plants to increase efficiencies, improve safety and to remain competitive,” says Schaffer. “We like to say for some of our older facilities, the only thing that remains original is the nameplate.”
Investments in Iowa include upgrades to AGP’s Eagle Grove facility, a new meal load out at the Sheldon plant, additional storage in Emmetsburg, and expanding the crush capacity at Sergeant Bluff.
“These investments will improve market opportunities for Iowa soybean farmers and sometimes, will reduce costs to producers by improving loading and unloading times,” says Schaffer. “These investments will also help AGP continue to add value to the producers’ crops and return value to our members and the local communities for years to come.”
Contact Kriss Nelson at knelson@iasoybeans.com