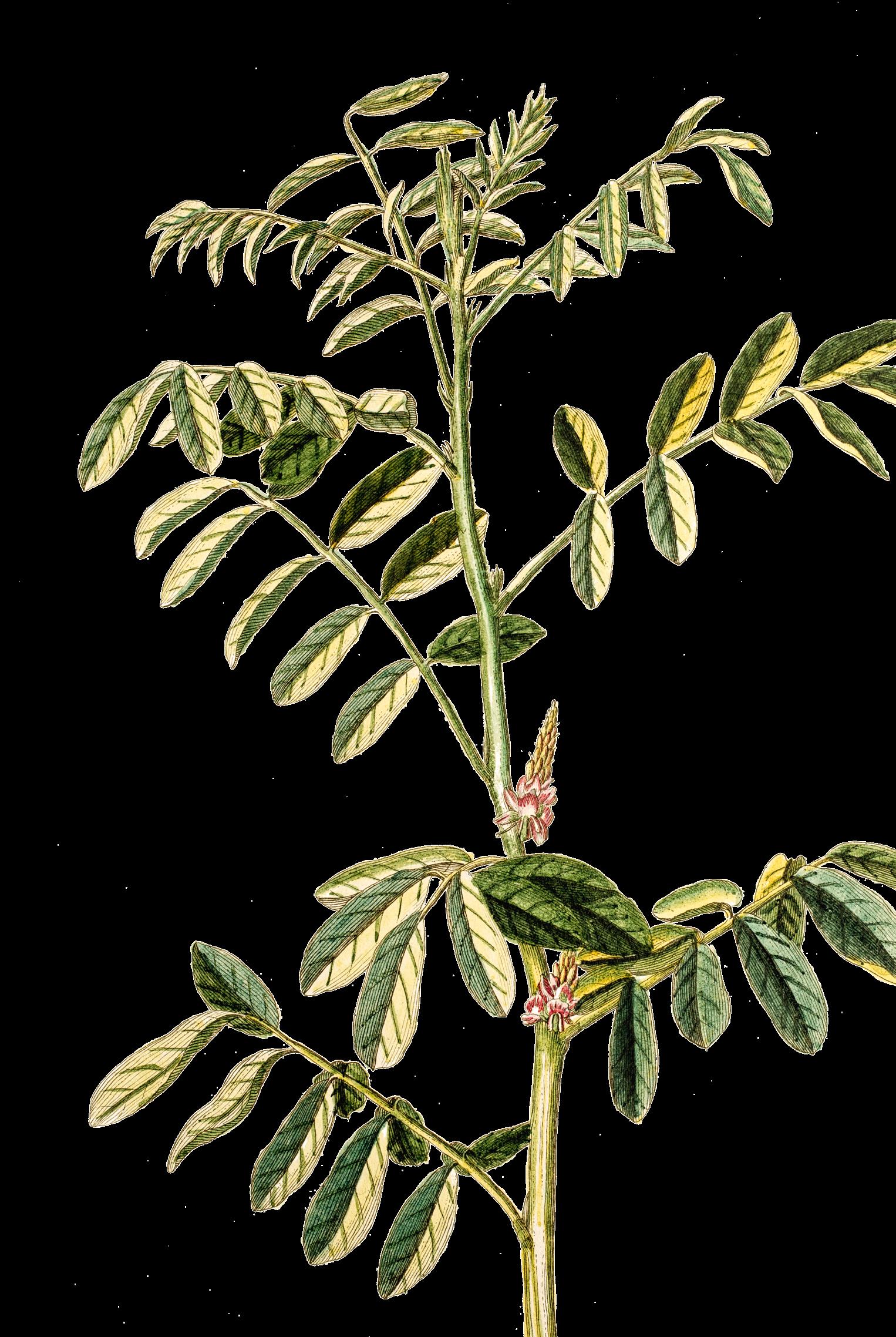
6 minute read
INDIGO: NATURAL VERSUS
from J'N'C 02/2021
INDIGO: NATURAL VERSUS SYNTHETIC
INDIGO: NATURAL VERSUS SYNTHETIC
Advertisement
Indigo dye is the key ingredient that gives your blue jeans their characteristic look. Even though it can be sourced naturally, it’s usually made synthetically these days – but both methods have their pros and cons. As conscious consumers, are we guilty of romanticising natural ingredients or is a greener indigo future with synthetics actually within reach? Let’s find out ...
TEXT JENNI KOUTNI
With its filigree leaves and soft pink blossoms, it’s hard to imagine that the indigo plant provides the vibrant dye that makes the blue jeans we know and love. But before it reaches the final indigo blue dye stage, there are quite a few steps in between – such as fermentation processes and oxidation – before the finished pigment can be used in its dried, powdered form. But does it really make sense for companies to go natural these days? Shouldn’t they opt straight for the less expensive synthetic pigment? The answer isn’t that simple.
A BRIEF HISTORY LESSON
As proven by the tiny remnant of dyed cotton that was found during excavations in Peru, people have been using the indigo plant to dye fabric for 6,000 years now. Sub-species of the indigo plant grow on different continents, but the chemical composition is identical in all of them. With natural indigo pigments, the dyeing process is based on what is called a reduction-oxidation process. As it’s barely water soluble on its own, it first has to be chemically converted with the use of a reducing agent like sodium hydrosulphite in order for it to dissolve in water. Only then can the dye penetrate the fibres of the fabric, giving them a yellow colour. Finally, the fabric is taken out of the liquid, where it oxidises when exposed to oxygen and turns blue. The indigo then returns to its insoluble state and remains within the fabric, even after years of washing. Until the end of the 20th century this plant-based dyeing technique was the only one in use. But the turn of the century brought about a revolution that would change the way indigo dye was used forever.
THE SYNTHETIC REVOLUTION
In 1897, German chemist and Nobel Prize winner Adolf von Baeyer succeeded in creating a synthetic form of indigo for the first time. By 1914, the natural indigo dyeing process only made up a mere four percent share of the global market. The fact that synthetic indigo couldn’t compete with the genuine natural indigo dyestuff didn’t seem to interest the mass market: the new pigment was received with great enthusiasm by the textile industry, mainly due to its cheap price. And that was possible because of a resource that, back then, seemed infinite: petroleum, which is still the main component of almost all synthetic dyestuffs to this day. From a chemical perspective, natural and synthetic indigo are identical. Only a special chemical test procedure can determine which method was used to dye a fabric. So as consumers, we have to rely on the word of the producers, as is so often the case.
MINOR DIFFERENCES
In general, dyeing with indigo is quite time-consuming. For example, you can’t just apply the entire dye onto the fabric in one go: it has to be done in layers, with lots of patience. And as we already know, that means dip-dyeing the fabric in a bath, air-drying it and then dipping it again. It can take as many as 12 dipping cycles until the desired blue tone is achieved. From an economic point of view, natural indigo also has other drawbacks: there may be contaminants in the dye and the results are less reliable than the chemical version from the laboratory. The colour results are also not as consistent as with the artificial variant. Under certain circumstances, these contaminants can lead to a rather dull-looking colour. Having said that, many people consider these characteristics to be exactly what makes naturally dyed jeans so special because each pair is truly unique. Another disadvantage: the scenario of global production shifting to natural indigo would mean much more agricultural land given up to the indigo plant. To cover the demand on the global fashion
SHUTTERSTOCK.COM — BENJAMAS PHOTOVEC PHOTO Before it reaches the final indigo blue dye stage, there are quite a few steps in between – such as fermentation processes and oxidation.
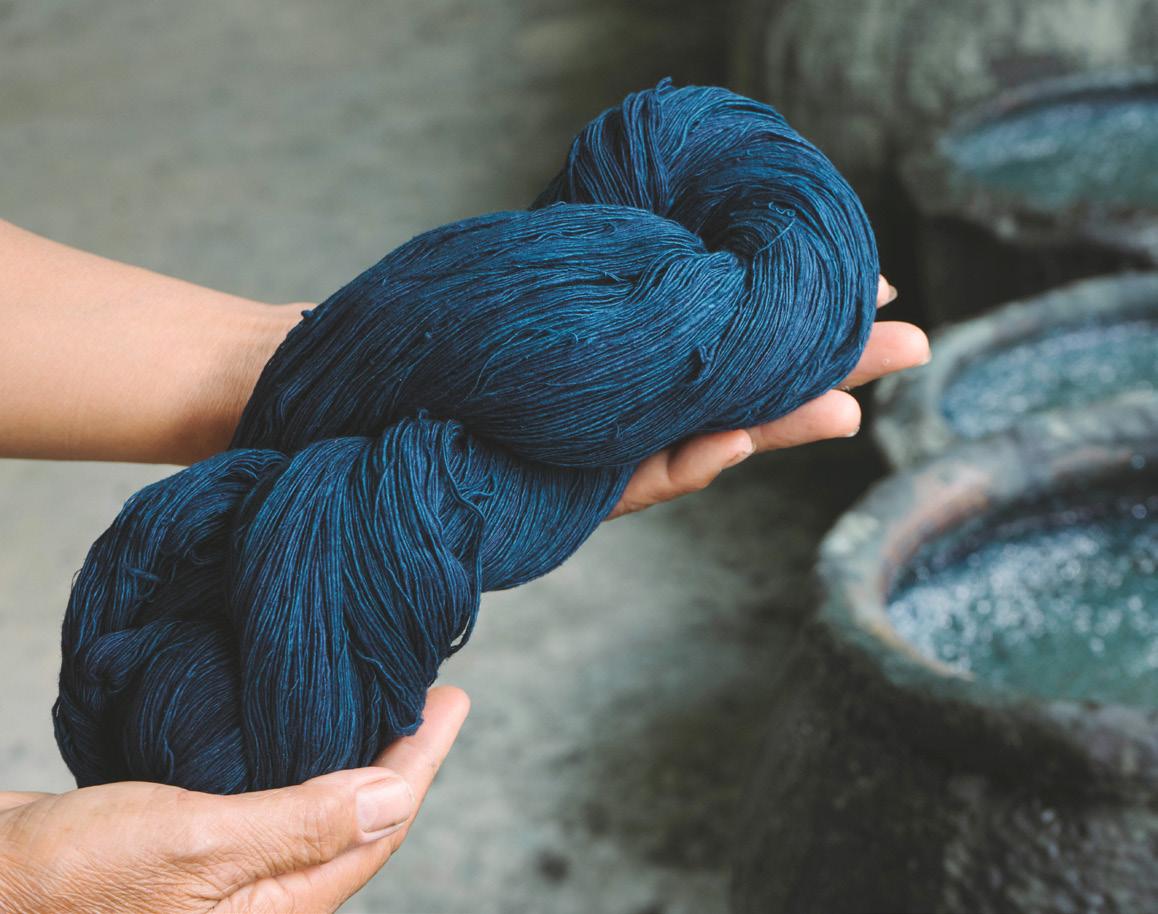

INDIGO: NATURAL VERSUS SYNTHETIC
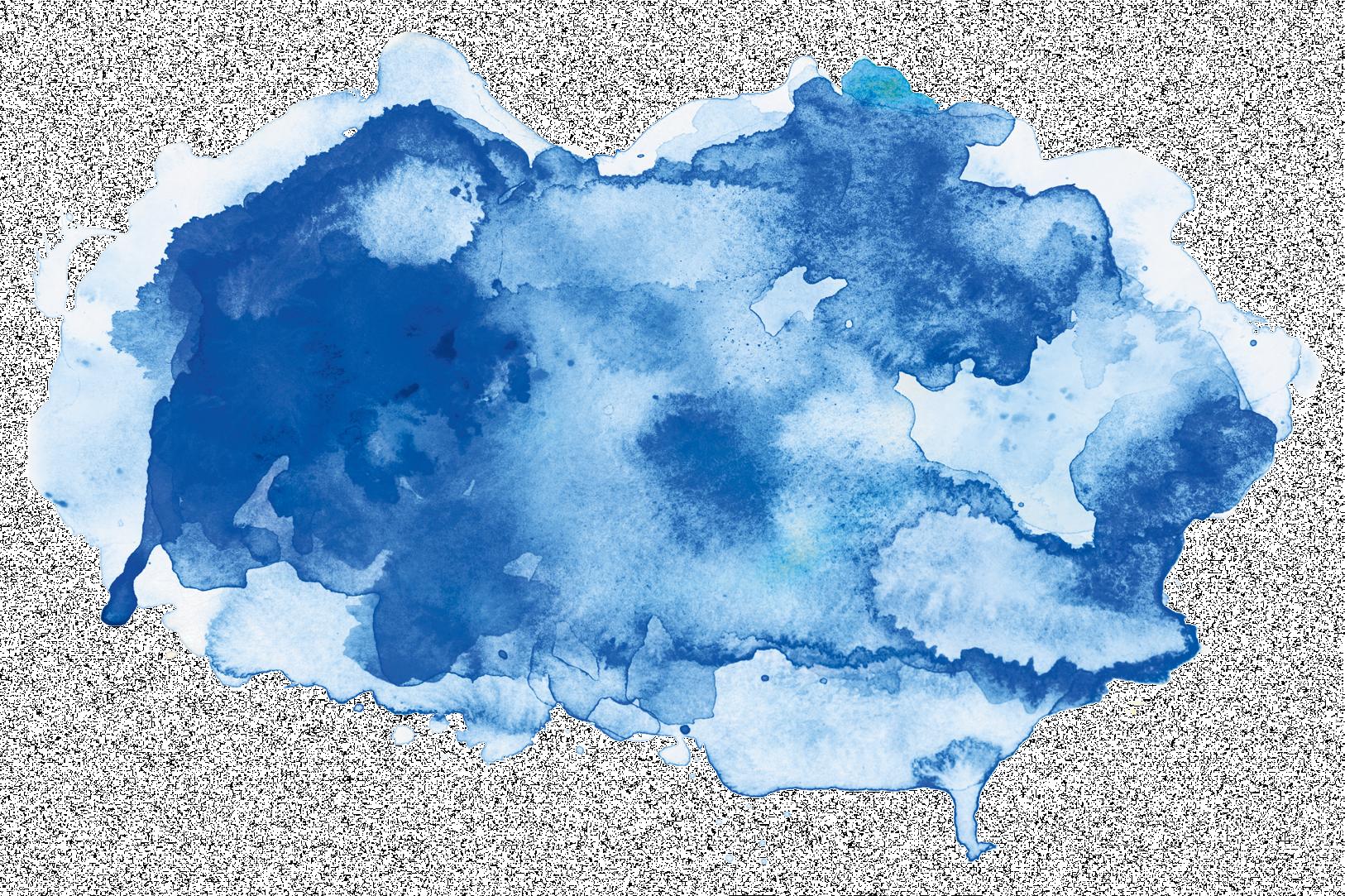
ISTOCKPHOTO.COM — STELLALEVI PHOTO
market, experts estimate that 70,000 tonnes of pure indigo would have to be produced annually, and that would require an estimated 10 million hectares of land.
INDIGO POWDER AS A HEALTH HAZARD
These are just some of the reasons why synthetic indigo is so dominant in today’s conventional denim production, with China as the main manufacturer. Although there are several different methods being used to create indigo, one particular method is preferred worldwide because it produces the maximum output with the minimum cost. It requires certain conditions and chemicals that have to be handled with the utmost care. In addition to aniline, formaldehyde and prussic acid (also known as cyanide), it uses ingredients like sodium amide that are at risk of exploding when they are brought into contact with oxygen. Environmentalists have already exposed many scandals where factories pollute the surrounding waters with the by-products of indigo production. As indigo power is sold in a highly concentrated form, the aniline contained in it is doubly dangerous: when workers tear open the packages containing the indigo powder, the air is filled with dust that can be carcinogenic if inhaled. This also poses a risk when dyeing clothes at home: indigo dyeing kits available on the internet or from drugstores can irritate the skin, eyes and airways.
ALTERNATIVES AND EXCEPTIONS
Hazardous ingredients like aniline aren’t a problem during the dyeing process with natural indigo. When carried out responsibly, traditional indigo production is therefore safer and less toxic for the environment and manufacturers. But that is currently not a realistic option for the mass market, which is why research is being done on many fronts to improve synthetic indigo production. For example, German company DyStar, which produces 30 percent of the world’s synthetic indigo, is working on a closed loop for all of their processes. That means that ingredients and by-products are safely redirected back into other manufacturing processes. The indigo dye used here is in liquid form, in order to protect workers from the toxic fumes of the powder. In addition, DyStar has come up with another method that completely eliminates the use of sodium hydrosulphite, instead using an organic and biodegradable reducing agent that is harmless when added to the wastewater system. After 11 years of research, the company Tejidos Royo has even succeeded in eliminating the use of water in their indigo dyeing process entirely. Their ‘Dry Indigo’ product uses foam to apply the dyes, which means it doesn’t produce any wastewater. Korean scientists have also recently discovered a way to create indigo with bacteria rather than petroleum, and a biotech start-up called Huue, based in California, has developed a way to make dye using microbes. So exciting progress is definitely being made.
WHO’S THE WINNER?
As is usually the case, the price is the decisive factor in determining the success of a product. The problem with bio-based technologies from natural sources is their scalability. The kilo price for synthetic indigo is noticeably cheaper than that of natural indigo. But in the price-driven denim industry, just a few cents can make or break a product. So it looks like the return to naturally dyed jeans lies in the hands of smaller fashion labels, whose environmentally conscious clientele is willing to pay a little more in exchange for authentic products.
