JOE RUSSELL
Selected works produced at the Bartlett School of Architecture, UCL
GRADUATE APPLICATION
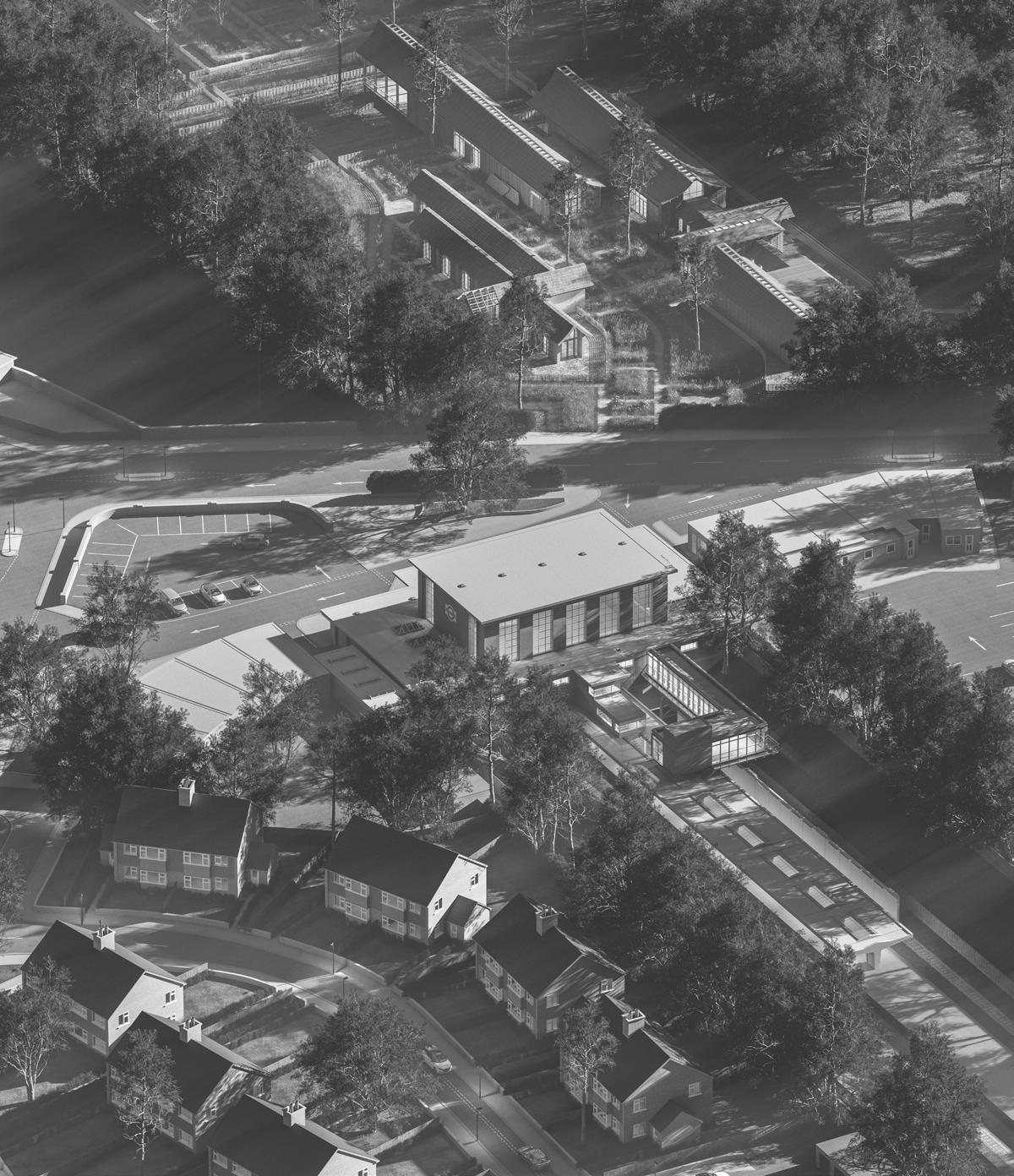
Selected works produced at the Bartlett School of Architecture, UCL
Individual Building Project, 2022
BSc Architecture, Bartlett School of Architecture
Tutors: Professor Murray Fraser and Michiko Sumi
Individual Design Project, 2021
BSc Architecture, Bartlett School of Architecture
Tutors: Professor Murray Fraser and Michiko Sumi
Individual Building Project, 2021
BSc Architecture, Bartlett School of Architecture
Tutors: Pascal Bronner and Thomas Hillier
Individual Design Project, 2020
BSc Architecture, Bartlett School of Architecture
Tutors: Pascal Bronner and Thomas Hillier
AJ Student Prize Winner 2022
Bartlett Medal Winner 2022
RIBA President’s Medal Nominee 2022
1st Class Honours
This project responds to the UK’s increasingly severe housing crisis by proposing a housing/community scheme as a precedent for socially and ecologically sustainable future developments within the Metropolitan Green Belt (MGB).
The Green Belt Act of 1938 constituted the first formal planning legislation to define the open space surrounding Greater London as protected land. Initially proposed to give access to the countryside, the MGB later became a physical constraint to the growth of London. The current policy is set out within the National Planning Policy Framework which states ‘the fundamental aim of Green Belt Policy is to prevent urban sprawl by keeping land permanently open.’
for MGB expansion in the 1950s, said that Green Belt land did not have to be ‘green’ or even particularly attractive, as its purpose was to stop urban development. Therefore, the ‘actual use or enjoyment of the Green Belt is clearly seen as an incidental benefit’ of the policy rather than its intended goal .
A 21st-Century Metropolitan Green Belt written by Dr Alan Mace of the London School of Economics, critiques current Green Belt policy and instead proposes urban planning solutions for sustainable future development within the MGB. This project – titled ‘Tightening the Green Belt: Oakwood Mews, Enfield’ – takes on these ideas and adapts them at the scale of an architectural scheme that relies upon locally sourced natural/recycled materials.
Finding a site was dictated by the parameters set out within Dr Mace’s A 21st Century Metropolitan Green Belt. I focused on Enfield in the North London area to conduct a ‘mini-expedition’ to find a site that would meet the requirements set out for the project.
The site eventually chosen was the land opposite Oakwood underground station near the northern end of the Piccadilly Line. The station was designed by renowned modernist architect Charles Holden, who designed a number of muchpraised stations along the Piccadilly Line. Oakwood is the penultimate stop, and being so close to this station means that there will be very easy public access for residents and visitors to my new housing/ community scheme.
The land ultimately provided the best opportunity to produce architectural design that most thoughtfully responded to the parameters proposed by Dr Mace for sustainable development:
“Development within the MGB should:
I. Limit environmental losses
II. Benefit existing residents
III. Limit private car usage
IV. Be close to public transport links”
The site stretches for approximately 200 meters in length and 50 meters in width. The topography of the site slopes down notably on its northern boundary, away from the road that passes in front of the underground station.
1. Two bedroom houses
2. Storage and delivery shed
3. Two bedroom houses II
4. Three bedroom houses
5. Stairs to upper level
6. One bedroom house
7. Three bedroom houses II
8. Cantilevered balcony
9. Lower level workspace
10. Multipurpose space
11. Toilets
12. Storage facility
.13. Main hall
14. Open plan nursery
15. Nursery toilets
16. Main lobby
17. Kitchen and storage
18. Cafe
The community center is located at the south end of the site where the land meets Bramley Road. Included within the larger built body (clad in stacked timber beams and roofed with reclaimed corrugated steel sheeting) is a cafe, workspace, hall, kitchen and lobby. The spaces are designed to be purposefully open with minimal interior walls. This allows for the building to easily adapt to the differing needs of a range of occupiers.
Opposite the main center is the nursery, equipped with white-washed, reclaimed brick walls and thatched roofing. The nursery is also very open plan which allows
the space to become an extension of the main center during out-of-school hours (such as evenings and weekends).
These public-serving components are deliberately oversized in comparison to the number of housing units within the scheme. This is to cater to both new residents and existing local residents.
The housing consists of a range of semidetached and terraced one-bedroom, two-bedroom and three-bedroom homes. The proposal is medium-density, with each property having its own small private garden. All residents have access to the large public gardens designed to enhance community engagement.
The three-bedroom houses are fitted with reclaimed corrugated steel sheet roofing, while the one and two-bedroom homes have natural thatched roofing.
In anticipation of a new fleet of underground trains being introduced to the Piccadilly Line in 2025, Transport for London (TfL) is undertaking major upgrades to the line’s maintenance depots. The upgrade will involve the complete demolition of its current Cockfosters depot.
My project therefore responds to this demolition by placing itself within this process of depot deconstruction. In doing so, my scheme gains an array of recycled building materials and prevents several hundred tonnes of embodied carbon from being dumped in landfill sites around London.
In addition to salvaging the Cockfosters depot materials, My proposal is also to source local naturally occurring materials that can be sustainably harvested (i.e. timber from the plentiful pine/fir woodlands and straw bales grown on adjacent farmland). The combining of harvested material with recycled material presents an opportunity to develop an architectural design that tackles the restrictiveness of the reused component catalog balanced with the expansiveness of new building materials.
The drawing that I made of the existing site to the left outlines the location of horticultural land (straw bale), coniferous woodland (pine/fir trees), the Cockfosters depot and my chosen site in the center.
At the first stage of assessing what recycled materials would be available for reuse in my project, I carried out a detailed survey of the existing Cockfosters depot as the plans and sections were not publicly available. I then drew up the most accurate 3D model of the building so that I could calculate precisely which materials would become available and how much embodied carbon could be salvaged/saved from landfill.
NOTE: There are 2 sets of ‘A’ and 14 sets of ‘B’. The values on the following page give embodied carbon values for the entire depot. The visuals are not representative.
STAGE 0
Embodied carbon salvaged: 0 kgCO2e
Material types: n/a
Embodied carbon salvaged total: 0 tCO2e
STAGE 1
Embodied carbon salvaged:
27785.9 kgCO2e
Material types: Glass, Steel
Embodied carbon total: 27.8 tCO2e
STAGE 2
Embodied carbon salvaged:
69521.2 kgCO2e
Material types:
Concrete, Brick, Steel, Glass
Embodied carbon total: 97.3 tCO2e
STAGE 3
Embodied carbon salvaged: 121139.6 kgCO2e
Material types: Concrete, Brick, Steel, Glass
Embodied carbon total: 218.4 tCO2e
STAGE 4
Embodied carbon salvaged: 142985.2 kgCO2e
Material types: Brick, Steel
Embodied carbon total: 361.4 tCO2e
STAGE 5
Embodied carbon salvaged: 363071.6 kgCO2e
Material types: Brick, Steel
Embodied carbon total: 724.5 tCO2e
Component - B
Concrete - 0.930 m3
Mass of concrete = 2300kg/m3 x 0.930m3 = 2139.0kg
Concrete carbon coefficient = 0.143
Embodied carbon = 30.6 kgCO2e
Total (x14) = 428.4 kgCO2e
Brick 5.597 m3
Mass of Bricks = 1600kg/m3 x 5.597m3 = 8955.2kg
Brick carbon coefficient = 0.23
Embodied carbon = 2059.7 kgCO2e
Total (x14) = 28835.8 kgCO2e
Glass 0.163 m3
Mass of glass = 2500kg/m3 x 0.163m3 = 407.5kg
Glass carbon coefficient = 0.86
Embodied carbon = 350.5 kgCO2e
Total (x14) = 4907.0 kgCO2e
STAGE 3
Component - A
Concrete - 4.727 m3
Mass of concrete = 2300kg/m3 x 4.727 m3 = 10,872.1kg
Concrete carbon coefficient = 0.143
Embodied carbon = 1554.7 kgCO2e
Total (x2) = 3109.4 kgCO2e
Brick 19.783 m3
Mass of Bricks = 1600kg/m3 x 19.783m3 = 31652.1kg
Brick carbon coefficient = 0.23
Embodied carbon = 7280.0 kgCO2e
Total (x2) = 14560.0 kgCO2e
Steel beam - 0.756m3
Mass of steel = 7850kg/m3 x 0.756m3 = 5934.6kg
British steel EPD carbon coefficient = 2.45
Embodied carbon = 14539.8 kgCO2e
Total (x2) = 29079.6 kgCO2e
Glass 0.254 m3
Mass of glass = 2500kg/m3 x 0.254m3 = 635.0kg
Glass carbon coefficient = 0.86
Embodied carbon = 546.1 kgCO2e
Total (x2) = 1092.2 kgCO2e
Component - B
14,649.6kg
Brick carbon coefficient = 0.23
Embodied carbon = 3369.4 kgCO2e
Total (x14) = 47171.6 kgCO2e
STAGE 4
Component A
Steel beam - 0.433 m3
Mass of steel = 7850kg/m3 x 0.433m3 = 3399.1kg
British steel EPD carbon coefficient = 2.45
Embodied carbon = 8327.8 kgCO2e
Total (x2) = 16655.6 kgCO2e
Brick - 2.991 m3
Mass of Bricks = 1600kg/m3 x 2.991m3 = 4785.6kg
Brick carbon coefficient = 0.23
Embodied carbon = 1100.7 kgCO2e
Total (x2) = 2201.4 kgCO2e
Component B
Steel beam - 0.461 m3
Mass of steel = 7850kg/m3 x 0.461m3 = 3618.9kg
British steel EPD carbon coefficient = 2.45
Embodied carbon = 8866.3 kgCO2e
Total (x14) = 124128.2 kgCO2e
STAGE 5
Component A
Steel - 0.569m3
Mass of steel = 7850kg/m3 x 0.569m3 = 4466.7kg
British steel EPD carbon coefficient = 2.45
Embodied carbon = 10943.4 kgCO2e
Total (x2) = 21886.8 kgCO2e
Brick - 7.327 m3
Mass of Bricks = 1600kg/m3 x 7.327m3 = 11723.2kg
Brick carbon coefficient = 0.23
Embodied carbon = 2696.3 kgCO2e
Total (x2) = 5392.6 kgCO2e
Component B
Steel -1.138m3
Mass of steel = 7850kg/m3 x 1.138m3 = 8933.3kg
British steel EPD carbon coefficient = 2.45
2.45
Embodied carbon = 12655.0 kgCO2e
Total (x2) = 25310.0 kgCO2e
Glass - 0.353 m3
Mass of glass = 2500kg/m3 x 0.353m3 = 882.5kg
Glass carbon coefficient = 0.86
Embodied carbon = 759.0 kgCO2e
Total (x2) = 1518.0 kgCO2e
Concrete - 5.674 m3
Mass of concrete = 2300kg/m3 x 5.674m3 = 13050.2kg
Concrete carbon coefficient = 0.143
Embodied carbon = 1866.2 kgCO2e
Total (x14) = 26126.8 kgCO2e
Brick 9.156 m3
Mass of Bricks = 1600kg/m3 x 9.156m3 =
Embodied carbon = 21886.8 kgCO2e
Total (x14) = 306415.2 kgCO2e
Brick - 5.667m3
Mass of Bricks = 1600kg/m3 x 5.667m3 = 9067.2kg
Brick carbon coefficient = 0.23
Embodied carbon = 2085.5 kgCO2e
Total (x14) = 29197.0 kgCO2e
Close up view of depot front elevation (component A)
Throughout the design development process a series of section-cut models were used to refine the proposal, exploring how the recycled/harvested materials could be combined elegantly and productively.
The models visualise the architectural qualities of key spaces such as the housing types (single storey - 1 bedroom house, double storey - 2 bedroom house and double storey - 3 bedroom house).
1. Reclaimed corrugated steel sheet roofing
2. Steam bent curved timber beam rafters
3. Rewelded steel support for roof beams
4. Steel beam framework
5. Wall insulation / straw bale
6. Exterior timber cladding / facade
7. Roof insulation / straw bale
8. Timber frame to hold insulation
9. Floor insulation
10. Reclaimed H-Beams as pile foundations
1. Roof insulation / straw bale
2. Rewelded steel support for roof beams
3. Reclaimed brick walls
4. Timber frame to hold insulation
5. Exterior timber cladding / facade
6. Wall insulation / straw bale
7. Reclaimed corrugated steel sheet roofing
8. Steam bent curved timber beam rafters
9. Primary roof support beams
10. Front entrance
11. Floor insulation
12. Brick footings
STAGE 1 - H-PILES
Net embodied carbon: -67.9 tCO2e
Saved from landfill:
67911.9 kgCO2e
Harvested material:
0 kgCO2e
STAGE 2 - RAMMED EARTH
Net embodied carbon: -85.4 tCO2e
Saved from landfill:
29502.7 kgCO2e
Harvested material:
11978.8 kgCO2e
STAGE 3 - PRIMARY FRAME
Net embodied carbon:
-118.7 tCO2e
Saved from landfill:
33266.2 kgCO2e
Harvested material: 0 kgCO2e
STAGE 4 - SECONDARY FRAME
Net embodied carbon: -150.0 tCO2e
Saved from landfill: 32265.8 kgCO2e
Harvested material:
1033.4 kgCO2e
STAGE 5 - INSULATION
Net embodied carbon: -156.4 tCO2e
Saved from landfill: 7246.7 kgCO2e
Harvested material: 785.6 kgCO2e
STAGE 6 - TERTIARY FRAME
Net embodied carbon: -155.8 tCO2e
Saved from landfill: 0 kgCO2e
Harvested material: 619.8 kgC02e
STAGE 7 - INSULATION
Net embodied carbon: -156.6 tCO2e
Saved from landfill:
1412.6 kgCO2e
Harvested material:
657.9 kgCO2e
STAGE 8 - ROOF SUPPORT
Net embodied carbon: -206.4 tCO2e
Saved from landfill:
51280.1 kgCO2e
Harvested material:
1479.0 kgCO2e
STAGE 9 - ROOF SUPPORT
Net embodied carbon: -205.7 tCO2e
Saved from landfill: 0 kgCO2e
Harvested material:
733.9 kgCO2e
STAGE 10 - RAFTERS
Net embodied carbon: -203.5 tCO2e
Saved from landfill: 0 kgCO2e
Harvested material: 2166.1 kgCO2e
STAGE 11 - INSULATION
Net embodied carbon: -202.7 tCO2e
Saved from landfill: 0 kgCO2e
Harvested material: 808.2 kgCO2e
STAGE 12 - CLADDING
Net embodied carbon: -209.9 tCO2e
Saved from landfill: 7156.0 kgCO2e
Harvested material: 0 kgCO2e
STAGE 1
Type - Reclaimed
Concrete - 3.456 m3
Mass of concrete = 2300kg/m3 x 3.456 m3 =
7948.8 kg
Concrete carbon coefficient = 0.143
Embodied carbon = 1136.7 kgCO2e
Steel - 3.472 m3
Mass of Steel = 7850kg/m3 x 3.472 m3 =
27255.2 kg
British steel EPD carbon coefficient = 2.45
Embodied carbon = 66775.2 kgCO2e
STAGE 2
Type - Reclaimed
Steel - 1.534 m3
Mass of Steel = 7850kg/m3 x 1.534 m3 =
12041.9 kg
British steel EPD carbon coefficient = 2.45
Embodied carbon = 29502.7 kgCO2e
Type - Harvested
Stabilised rammed earth - 129.641 m3
Mass of rammed earth = 1540kg/m3 x m3 =
199647.1 kg
Cement Stabilised Soil Carbon Coefficient =
0.060
Embodied carbon = 11978.8 kgCO2e
STAGE 3
Type - Reclaimed
Brick - 22.143 m3
Mass of Bricks = 1600kg/m3 x m3 = 35428.8 kg
Brick carbon coefficient = 0.23
Embodied carbon = 8148.6 kgCO2e
Steel - 1.306 m3
Mass of Steel = 7850kg/m3 x m3 = 10252.1 kg
British steel EPD carbon coefficient = 2.45
Embodied carbon = 25117.6 kgCO2e
STAGE 4
Type - Reclaimed
Brick - 18.379 m3
Mass of Bricks = 1600kg/m3 x m3 = 29406.4 kg
Brick carbon coefficient = 0.23
Embodied carbon = 6763.5 kgCO2e
Steel - 1.326 m3
Mass of Steel = 7850kg/m3 x m3 = 10409.1 kg
British steel EPD carbon coefficient = 2.45
Embodied carbon = 25502.3 kgCO2e
Type - Harvested
Timber - 10.742 m3
Mass of Timber = 370kg/m3 x m3 = 3974.5 kg
Timber carbon coefficient = 0.26
Embodied carbon = 1033.4 kgCO2e
STAGE 5
Type - Reclaimed
Brick 19.692 m3
Mass of Bricks = 1600kg/m3 x m3 = 31507.2 kg
Brick carbon coefficient = 0.23
Embodied carbon = 7246.7 kgCO2e
Type - Harvested
Straw Bale - 35.726 m3
Total lifespan carbon emission = 14.12 kgCO2e/ m3
Embodied carbon = 504.5 kgCO2e
Timber - 2.922 m3
Mass of Timber = 370kg/m3 x m3 = 1081.1 kg
Timber carbon coefficient = 0.26
Embodied carbon = 281.1 kgCO2e
STAGE 6
Type - Harvested
Timber - 6.443 m3
Mass of Timber = 370kg/m3 x m3 = 2383.9 kg
Timber carbon coefficient = 0.26
Embodied carbon = 619.8 kgCO2e
STAGE 7
Type - Reclaimed
Glass 0.657 m3
Mass of glass = 2500kg/m3 x m3 = 1642.5 kg
Glass carbon coefficient = 0.86
Embodied carbon = 1412.6 kgCO2e
Type - Harvested
Straw Bale - 46.592 m3
Total lifespan carbon emission = 14.12 kgCO2e/ m3
Embodied carbon = 657.9 kgCO2e
STAGE 8
Type - Reclaimed
Steel - 2.630 m3
Mass of Steel = 7850kg/m3 x m3 = 20645.5 kg
British steel EPD carbon coefficient = 2.45
Embodied carbon = 50581.5 kgCO2e
Glass - 0.285 m3
Mass of glass = 2500kg/m3 x m3 = 812.3 kg
Glass carbon coefficient = 0.86
Embodied carbon = 698.6 kgCO2e
Type - Harvested
Timber 15.374 m3
Mass of Timber = 370kg/m3 x m3 = 5688.4 kg
Timber carbon coefficient = 0.26
Embodied carbon = 1479.0 kgCO2e
STAGE 9
Type - Harvested
Timber 7.629 m3
Mass of Timber = 370kg/m3 x m3 = 2822.7 kg
Timber carbon coefficient = 0.26
Embodied carbon = 733.9 kgCO2e
STAGE 10
Type - Harvested
Timber 22.517 m3
Mass of Timber = 370kg/m3 x m3 = 8331.3 kg
Timber carbon coefficient = 0.26
Embodied carbon = 2166.1 kgCO2e
STAGE 11
Type - Harvested
Straw Bale 57.235 m3
Total lifespan carbon emission = 14.12 kgCO2e/
m3
Embodied carbon = 808.2 kgCO2e
STAGE 12
Type - Reclaimed
Steel sheet 0.268 m3
Mass of sheet = 7850kg/m3 x m3 = 2103.8 kg
British steel EPD carbon coefficient = 2.45
Embodied carbon = 5154.3 kgCO2e
Glass - 0.931 m3
Mass of glass = 2500kg/m3 x m3 = 2327.5 kg
Glass carbon coefficient = 0.86
Embodied carbon = 2001.7 kgCO2e
This project investigates the state of the architectural industry in terms of practice and labor. It addresses key issues such as underpayment and overwork, and argues that these are caused by companies putting financial gains before the treatment of, and working conditions for, employees. As such, the project concludes that this prioritization is a result of modern-day, capital-driven efficiency.
This modern-day efficiency first came to fruition during the industrial revolution, when production methods were mechanized and mass scaled. Arkwright’s spinning frame is a prime example of improved manufacturing efficiency during this period. However, it also highlights several of the problems caused by streamlined mass production such as child labor, deplorable working conditions, and severe underpayment. In recognizing this, the project communicates an unfavorable view toward striving for efficiency.
The project then investigates the efficiency of architectural labor and designer workflow. It assesses the certainty of
errors in hand drawing - a task that can never be completely efficient - and by using this concept as a foundation, argues that designers are innately inefficient. From here, I design an ‘inefficient’ drawing machine that bases its algorithm on human error probabilities to mimic human inefficiency in drawing production. I produce a typical office floor plan and incorporate the inefficient drawing machine into the design process to investigate how mistakes and ‘inefficiencies’ can create new uses for spaces.
Ultimately, the project proposes that architects should rethink the current emphasis on production efficiency as the principal dictator of how we design and inhabit space. Instead, we should incorporate mistakes and chances into our designs. This alternative design process could make architecture more in touch with human’s intrinsic inefficiency through the random errors and ‘inefficiencies’ it creates.
Raw output with initial errors from the drawing machine
Redrawing the plan - my intervention - in order to create closed wall forms
Refined vector-based composition - digital intervention - for 3D modelling
The project proposes a mental health revolution through an examination of the long-term effects of the Covid-19 pandemic on public mental health. Inspired by the Great Exhibition of 1851, a celebration of industry that was emblematic of the nineteenth century’s economic and technological advancements, this project aims to communicate a celebration of openness toward mental health. Thus, a celebration representative of the societal needs of the 21st century.
Located within the same footprint of Hyde Park as the original Great Exhibition, a monumental in scale, yet delicate, latticelike structure hangs above a sculpted landscape. The building performs as a clinic and public space, illustrating the themes of transparency and openness through both its framework and function. The structure aims to be a celebration of acceptance; a physical beacon of hope to the millions suffering in silence from mental illness every year.
This project is a short speculative investigation into how memories change and evolve over time. The project starts with reflecting on my memories of a trip to Camden Passage, an area in Islington, London, known for its antique shops and cafes. Using hand drawing as a chosen medium, the project investigates how my memories change and shift as new
experiences and memories are added as the project timeline progresses. The evolution of what is included in the drawings speaks to the changing nature of memory and how it shapes our understanding of the past. Overall, ‘A Memory Machine’ is a highly personal examination of memory’s complex and fluid nature.