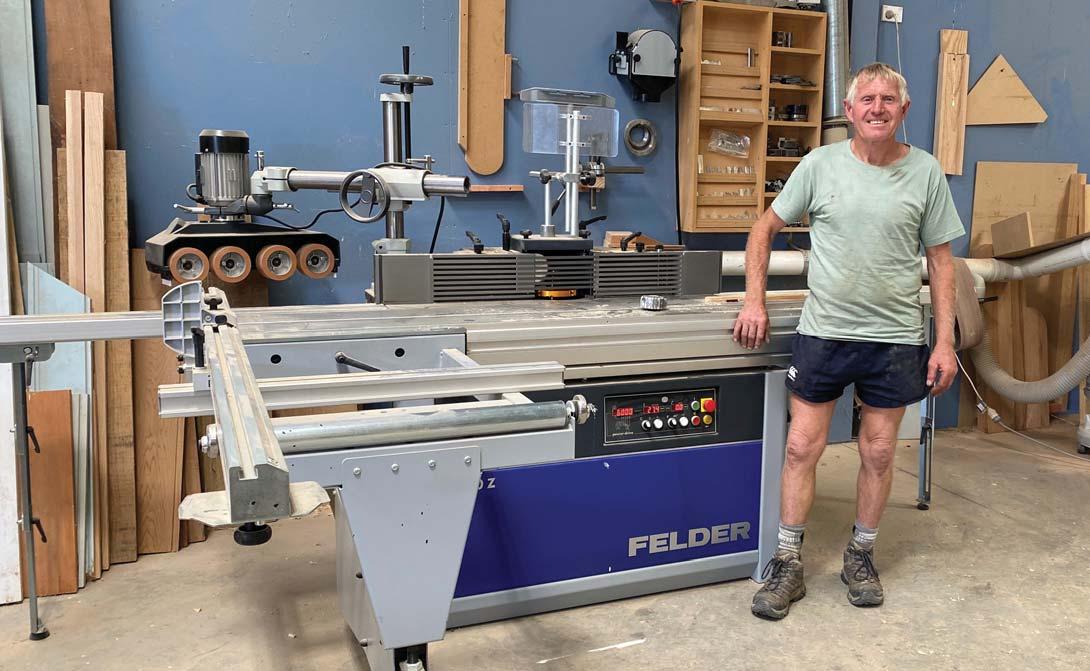
4 minute read
Better, safer, more comfortable
“I make stuff,” explains Peter Taylor, of Peter Taylor Builders near Ashburton. “I’ll give anything a go.” He’s not kidding. Peter’s workshop – a large farm shed near his home – is a treasure trove of some of the stuff Peter has made. Most noticeable is a full size Chuck Wagon – the field-kitchen of a wagon train from the US prairies – hand built, from scratch. Nearby is a beautifully crafted red-gum vanity unit, an oak table with timber fixings, and all sorts of other bespoke assorted furniture. There’s even a steam-bent coffin. The workshop is filled with hardwood, with racks and slabs of oak, blue and red gum, black poplar – all just waiting for the right project. The walls are lined with the tools of the trade, including templates for all manner of work. “You never make anything just once” says Peter.
Self-employed since aged 19, Peter gave up the dream of going farming in his 30s and has spent his working life building – mostly on farms. For decades he has run building crews working on all aspects of farm buildings across the Canterbury plains. Today, Peter Taylor Builders is the premium house-builder in town, constructing the multimillion dollar mansions successful farmers are building on retirement.
But woodworking isn’t just part of Peter’s day job. It’s also his hobby. “I spend about 35 to 40 hours a week in my workshop, making stuff,” says Peter. “Some of my time is setting up materials for the guys on site, or the joinery projects we have. But a lot of my day is doing my own projects –things that interest me.” Hence the Chuck Wagon, and many other horse-drawn conveyances. Peter has a wide interest and therefore lots of projects. The rocking horse, followed by rocking tractor, and rocking police car. Memorial seating for a local school. Furniture and chairs for pre-schools. Toys for those in need. At least 20% of Peter’s time is spent on charity projects.
Working almost exclusively in solid timber, Peter started decades ago with a 2nd hand Holytek and Wadkin machines from a local furniture maker closing down. As Peter’s projects got bigger, so did his workshop. And when COVID ended a long-planned overseas trip, Peter decided it was time to upgrade. Working with Mark from the Christchurch branch of Jacks, Peter’s invested in a package of Austrian machines from the Felder group. These include an A951L 510mm wide planer with 2.7m tables, and a D963 thicknesser – both with Silent-Power spiral cutter blocks. There’s a K740S sliding table saw and an F900Z spindle moulder with a 2m sliding table, along with a FAT 300S working table. Peter’s enthusiasm for the new machines is clear: “Hand on heart, I wish I’d bought them 20 years ago. I cannot tell you the difference these machines have made to my efficiency, and the enjoyment I get working with them.”
High on the list of workshop improvements Peter is enjoying is the FAT 300S table. “I use this for everything,” Peter says enthusiastically. “Infeed or outfeed table, laying up and assembly – the grandkids even push each other around the workshop on it!” With a capacity to hold up to 300kgs, height adjustment and lockable wheels, Peter uses the FAT 300S to move heavy slabs, table tops, doors, or any other heavy or bulky workpiece around his workshop. “Let’s be realistic. If I damaged my back trying to lug heavy slabs around my workshop, the medical bills alone would add up to more than I paid for this work table. I can’t understand why every workshop in the country hasn’t got two.”
Next for praise from Peter is Felder’s spiral Silent-Power cutterblock, which is in both his planer and thicknesser. “Why anyone wouldn’t invest in a spiral cutter block I have no idea,” he says. “It’s nearly silent. I used to be able to hear the old thicknesser from the other end of the farm! What’s more, the finish is almost as good as coming off a sander. And the longevity and cost-savings of the spiral tip knives is outstanding. It used to cost me $120 in sharpening every time I took a notch out of a single straight knife blade, whereas I’ve only ever turned one spiral knife in hundreds of hours of running.”
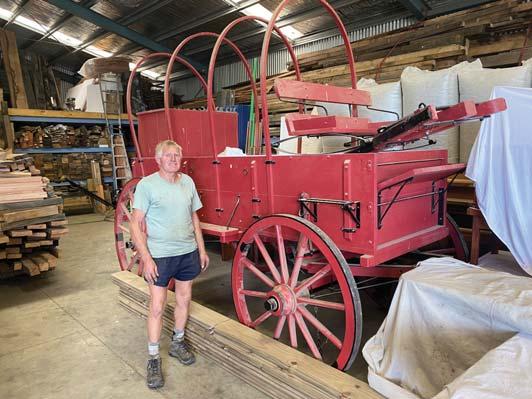
Peter also praises the smooth feeding when compared to a threeknife set up. “Perhaps it’s the combination of the spiral knives and the infeed roller that eases the resistance to the workpiece. I’m not sure but it’s so much less work than the sweat I used to work up feeding the old straight knife machine.”
Of all the machines in the workshop, Peter saves the most praise for this F900Z spindle moulder. A combination of timing and special manufacturer pricing meant he purchased a considerably higher spec than he originally intended. “This machine should get more promotion,” says Peter. “It’s undersold. With the long sliding table it does the work of several machines, and with the addition of fold-out table extensions it can cope with long workpieces – doors, table tops.
I’m using it for all my mortice and tenon work, grooving, rebates. I invested in new throwawayknife tooling and that’s a huge time-saver. Setting up for T&G, with digital readout I’m saving an hour over manual setting, for every set-up.”
Peter’s a positive guy, and has something positive to say about all his new machines – and in particular the labour-saving and safety benefits they feature. Remote start-stop buttons on sliding tables. Digital displays, enhanced guarding, and simplicity of use. But as a sole operator he keeps returning to the improved efficiency he’s found the new Felder machinery brings: “I’m alone in this workshop, so anything that can help my efficiency, my safety and my comfort are worth having. They just make life so much easier. I reckon Jacks should make customers choose to take these extra features off, not add them. Because until you’ve used many of these optional extras on a job, you don’t realise the value they add. Anyone who doesn’t believe me – come use my machines and find out for yourself!”