
4 minute read
Peter Hay Kitchens makes next move new edgebanding technology from HOMAG Group
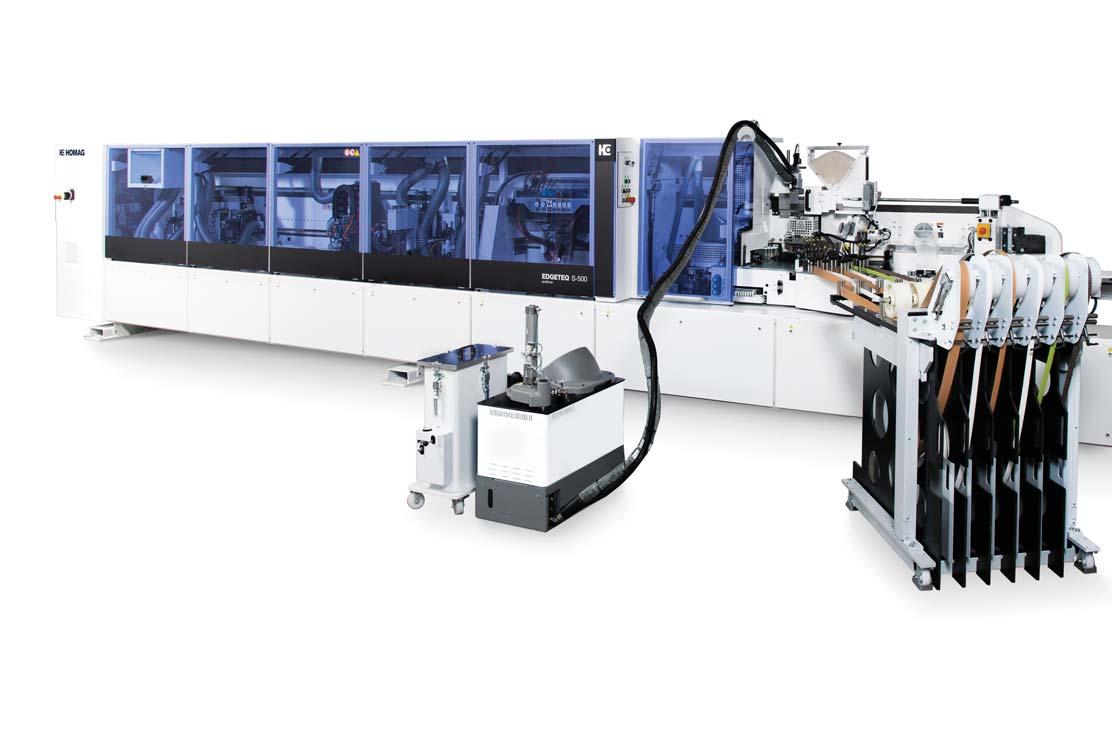
In forty eight years of operation Peter Hay Kitchens have always been at the forefront of the New Zealand kitchen manufacturing industry in the development of new processes and the use of technology. The recent purchase of three edgebanding lines from German machinery supplier HOMAG Group including the latest airTec technology has continued that tradition, keeping the company in touch with the marketplace and more importantly, expanding on their journey of creating the most advanced Batch One processing line for cabinet production, a process that started back in 2015. Bob Nordgren from JOINERS Magazine spoke with founder and owner Peter Hay and his Sales and Marketing Manager Karl O’Hanlon about this next step in the journey and what these edgebanding lines mean for Peter Hay Kitchens.
“The nature of the kitchen business has changed. We saw that back five years ago when we went through a major change in production theory: the move to Batch One production which enables us to effect large volume manufacturing of a one off product thereby meeting the emerging demand for customisation but at an economic cost.” says Peter.
“The move to HOMAG Group with the three new edgebanding processing lines is a significant next step: it allows us to keep pace, but more importantly expand on our 4.0 project which we see as market leading.” explains Peter. “We have invested a lot over the last few years but we have achieved a lot as well. We believe what we are doing is the right thing for this business, that’s why we bought not one, not two but three of the latest in edgebanding production line machines.”
The attitude and approach to this business is impressive as Peter comments “At Peter Hay Kitchens we have a great group of people developing and deploying this pathway forward. We all understand kitchens, where they are heading and how we fit into that. Technology, automation and software play an important role in that while the move to HOMAG Group brought synergy through not only factory processing but a strong connection through the integration of the Imos software that runs the design and production planning as well.”
One of that team is Karl O’Hanlon, Sales and Marketing Manager. Peter Hay Kitchens is the biggest business of its kind here in New Zealand. Operating from their 10,000 square metre site in the Auckland suburb of Manukau it produces up to a thousand kitchens a month. Karl comments “We have always struggled for benchmarking ideas and theories here in New Zealand as the scale of the business sets it apart a little. Because of this we have often looked overseas however I believe where we are now is truly world class.” Peter adds “It’s amazing how far we have come, but also where we are heading. It really is exciting and its that excitement that pushes the team and provides them unique opportunities to work on pathways forward which are not always possible in a lot of businesses. The funny thing was, when we sat down and finally made the purchase decision, it was those things that stood out with HOMAG Group as well.”
The objective has been to network the entire production process from board to finished product, to make it a more efficient, successful business. “HOMAG Group, in addressing the production issues we faced were genuinely interested in getting the process right: they bought new ideas to the table. This is these days an ‘intelligent” business where the efficiencies and gains made from automation for example are balanced against the realities of running a business of real size.” comments Karl.
This next step for Peter Hay Kitchens begins with the arrival and installation of the three edgebanding lines in the coming months. We will check on progress in a later issue.
Less material more sales
New features for cutting and nesting
Where do joinery and carpentry businesses lose the most time? Where is the most potential to save material and thus money? HOMAG has looked at these questions intensely. The result is practical solutions that make manual cutting and nesting processing more comfortable and that save more material
Reusing offcuts
In the intelliDivide cutting optimization, the employee defines an individual dimension that specifies the size from which an offcut should be reused. This offcut can be registered as available material with a simple click in the app. It is then included in the next optimization of the cutting patterns. Practical: the cutting assistant prints a special offcut label with all relevant information directly. This ensures that the offcut is clearly labeled and easy to find again.
Overview of the panel stock
The ‘Cutting Production Set’ now allows the user to manage both the stock location and the panel stock, including offcuts. As soon as a cutting pattern has been transferred to the tablet at the saw, the material required is reserved. Once a job has been processed, the assistant automatically deletes the panels used. An individual minimum stock level for each panel type informs the operator in good time when material needs to be reordered.
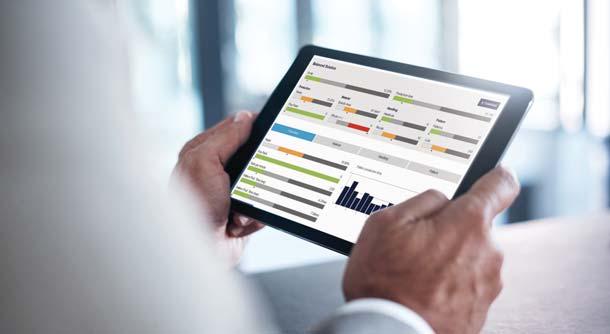
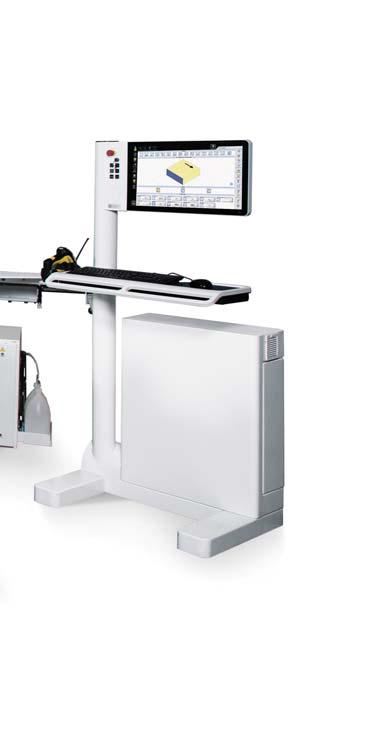
More flexibility with strip cutting
The assistant also supports those who cut their panels into strips first. The operator sees a graphical display of how wide the strips should be cut. Each strip can also be given a separate label, thus preventing them from being mixed up. The operator can therefore cut a large number of strips first and then process them later. Longer interruptions or continuing work the next day are no longer an issue.
Nesting assistant: Reduce costs and increase efficiency
The new ‘Nesting Production Set’ brings the advantages of the cutting assistant to your nesting machine. The assistant supports you in the automatic calculation of your nesting patterns. The optimization software places the individual components in the nest as close to each other as possible. This allows you to reduce material consumption and save costs. At the same time, you print an individual label for each nested part. This ensures that each workpiece has all the information required for the subsequent processing. The set is the ideal entry level solution for labeling your components and is perfect for retrofitting label printing on HOMAG nesting machines. You can thus create the basis for integrated processing data in your joinery during the nesting process.
What’s in a name?
The name Toitū was the result of a brainstorm at the company’s sales conference and was enthusiastically supported by the company’s manufacturing manager and a key account manager who represent different iwi – and ensured there was consultation with iwi around its usage in this context. Toitū has several interpretations, including 'enduring', 'untouched', 'kept pure', 'protected' – and also 'sustainable'.